Abstract
The chemical composition and solubility of metals in welding fumes is thought to be related to the welder health but is not well characterized. We quantified and compared the total (insoluble + soluble) and soluble metal contents in fumes from flux-cored arc welding using non-stainless steel (FCAW/NSS) and stainless steel (FCAW/SS) wire. Welding was performed in an American Welding Society standard fume collection chamber. The total content of 13 analyzed metals was significantly higher in FCAW/NSS fumes than in FCAW/SS fumes (51.6 ± 5.7 vs. 40.2 ± 5.2%, p < 0.001). Soluble metal content was significantly higher in FCAW/SS fumes than in FCAW/NSS fumes (15.5 ± 5.8 vs. 6.49 ± 2.4%, p < 0.001) due to the presence of potassium and sodium. Different proportions of each element were observed between welding types. Iron, magnesium, and aluminum were significantly higher in FCAW/NSS fumes, whereas chromium, nickel, and potassium were more common in FCAW/SS fumes. The metal composition of FCAW fumes was more similar to that of shielded metal arc welding fumes than that of gas metal arc welding fumes. It seems unnecessary to measure soluble iron, nickel, aluminum, and barium to compare with their soluble ACGIH-TLVs at the FCAW welding process. But chromium should be specified in terms of its valance and solubility.
INTRODUCTION
Welding fumes are generated by vapor condensation as well as microspatter ejection from the weld pool. Welding fumes are composed of various elements, most of which are metals, metal oxides, and other materials from welding electrode, base metal, coatings, or inner flux materials (CitationZimmer and Biswas 2001).
The fume composition and fume formation rates are influenced by various welding factors including welding types, welding alloy, arc voltage, arc current, shielding gas, evaporation heat of each component, interaction of each component, and transferring mode of electrode (AWS 1987; CitationVoitkevich 1995; CitationYoon et al. 2003).
Flux-cored arc welding (FCAW), growing in popularity as an alternative to SMAW because of its productivity and quality of welding, has characteristics of both shielded metal arc welding (SMAW) and gas metal arc welding (GMAW). FCAW is similar to SMAW in that they both use a flux. Flux are quite complex and include gas formers, deoxidizers, binders, slag formers, arc stabilizers, and alloying additions (AWS 1987). In FCAW, the flux is contained in the tubular wire, whereas it is applied to the outer sheath in SMAW. FCAW employs a spool of wire that feeds continuously, like GMAW, and can use shielding gas to supplement the gaseous shield produced by the flux component (CitationHewitt and Hirst 1993; CitationHarris 2002). Stainless-steel (SS) and mild-steel (MS), the most common types of outer tubular wire of FCAW electrodes, have different elemental constituents (CitationTaylor et al. 2003; CitationYoon et al. 2003).
It was reported that the primary source of fume is filler material rather than the base metal (CitationVoitkevich 1995; CitationTaylor et al. 2003). FCAW and SMAW generate more fumes than GMAW, and the flux component can be integrated into fumes. Thus, the composition of fumes generated from FCAW depends on the composition of the inner flux as well as tubular wire, and to a minor extent, on the base metal. Fumes from FCAW processes were reported to be large, complex and potentially multimodal because of flux complexity whereas fumes from GMAW were small, smooth, and unimodal (CitationZimmer and Biswas 2001; CitationHewitt and Gray 1983).
The chemical composition and size range of welding fumes have been investigated using complex techniques and expensive equipment, such as x-ray fluorescence spectrometry (XRF), neutron activation analysis (NAA), x-ray photoelectron spectrometry (XPS), x-ray diffraction (XRD), energy dispersive spectrometry with scanning and transmission electron microscopy (SEM-EDS and TEM-EDS), various types of impactor, aerodynamic particle sizer, electric aerosol analyzer (EAA), and differential mobility particle sizer (Voitkevich 1988; CitationKarlsen et al. 1992; CitationZimmer et al. 2002; CitationJenkins 2003; CitationJenkins and Eagar 2005).
Welding fumes are known to cause bronchitis, respiratory tract irritation, metal fume fever, chemical pneumonitis, lung function changes, and a possible increase in the incidence of lung cancer (NIOSH 1998; CitationAntonini et al. 1998). Health effects of welding fumes depend on the concentration, particle size, chemical composition, solubility (CitationAntonini et al. 1996; CitationAntonini et al. 1997; CitationAntonini et al. 1999).
The solubility of metals in fumes is not well characterized, and information on the solubility of metals in fumes is limited (CitationAshley 2001). The solubility of metals and metalloids depends on the extraction medium, time, temperature, and volume (CitationHewitt and Gray 1983; CitationFairfax and Boltzer 1994; CitationYoon et al. 2003). Despite several descriptions of solubility, the operational definition of solubility and the analytical methods used to measure it are so diverse that it is difficult to compare data from different studies. Furthermore, a very limited number of welding wires and/or welding rods in a given welding process have been used because the main purpose of studies on the solubility of welding fumes was not characterization of solubility itself, but toxicity testing in vitro (CitationButler and Howe 1999; CitationAntonini et al. 1999; CitationAntonini et al. 2001; CitationTaylor et al. 2003).
The solubility of FCAW fumes has not been thoroughly investigated, especially using the many flux-cored wires used in non-stainless (NSS) and SS wire commercial products. Also, material safety data sheets provided by welding consumable manufacturers usually provide not the fume compositions but consumable compositions which are different from airborne fume constituents. And there is no data on the solubility of metals in material safety data sheets.
The purposes of this study were to quantify the composition of 13 different metals and to determine their soluble fractions in FCAW non-stainless steel (FCAW/NSS) and stainless steel (FCAW/SS) fumes with nine commercial wire products.
METHODS
Welding Fume Generation
A summary of the welding conditions and analytical protocol is given in and , respectively. The fume collection chamber used here was described in detail in a previous paper (CitationYoon et al. 2003).This chamber was validated for stable welding conditions and retention of fumes during the welding and sampling periods (KIIT 1999). A base metal was mounted on the turntable and flux-cored wire was fed into the welding torch. Current, voltage, and welding time were monitored with an arc monitoring system (V4.1, O.I.S. Engineering Ltd., UK); both current and voltage were very stable (C.V. < 0.01).
TABLE 1 Welding conditions and materials for generating fumes
Five 1.2 mm diameter flux-cored wires were used for FCAW/SS and four for FCAW/NSS, with CO2 gas. To compare the results, the welding current, voltage, and shielding gas flow rate were fixed at 25 V, 180 A, and 20 L/min of CO2, respectively. These conditions were adopted from the values recommended by wire manufacturers.
Welding Fume Sampling
Welding was carried out for 120 sec, and fume sampling was conducted for 180 sec, including the 60 sec following welding. To collect the fumes, air was drawn through a pre-dried (< 20% RH, 105°C, > 1 h) glass fiber filter (pore size 0.6 um, 254 × 203 mm; Whatman, USA) with a flow rate of 2.3–2.8 m3/min from the top of the welding chamber. After sampling, fumes on the glass fiber were scraped carefully with a Teflon spatula and put into scintillation vials. Collected fumes were dried in auto-desiccators (< 20% RH, C-3B, SANPLATEC Corp., Japan) overnight and stored at–20°C until analysis.
Analysis
Pretreatments for the analyses of total and soluble contents of 13 metals were conducted according to the procedures in Annexes B (dissolution method for soluble metal and metalloids) and G (dissolution method in a microwave digestion system) of the International Organization for Standardization (ISO) 15202 method, respectively (ISO 2001). Fumes from nine FCAW samples were prepared as shown in ; three samples of each product were prepared to determine total (insoluble + soluble) metal content, three samples each for the insoluble fraction, and three samples for only the soluble fraction. All sample sets were prepared with reagent blanks or filter blanks.
To determine the total content of each of the 13 metals, six samples of each fume sample were prepared. Three samples were prepared directly from the fumes. The stored fumes were reconditioned in the auto-desiccator before weighing and weighed to about 2 mg on a 0.01 mg sensitivity balance (CP225-D, Sartorius, Germany). Three other samples were prepared from the remaining soluble filtrate residues on mixed cellulose ester (MCE) filters, which were added later to the insoluble fraction to calculate total content. These weighed fumes were put into microwave ovens (MDS2100, CEM Corp., USA) separately. Ashing acid (4 ml of nitric acid and 1 ml of perchloric acid; Sigma-Aldrich, USA) was added into microwave oven vessels, and the temperature was increased to 180°C by 10°C/min and was maintained at 180°C for 15 min. After the microwave digestion, the solution was poured into a pre-cleaned centrifuge tube and diluted with distilled water to 25 ml for analysis. If there was visible precipitate, the solution was filtered with a 0.45 μ m syringe filter (Millex HV 25 mm, 0.45 μ m PVDF, Millipore Corp., USA).
To determine soluble metal content, six 5 mg samples were weighed from nine reconditioned FCAW fume samples. After adding 10 ml of class I distilled water, samples were agitated for 60 min at 120 rpm in a 37 ± 2°C water bath. Three samples were filtered with a suction apparatus with MCE filters (0.45 μ m, Millipore), on which insoluble residue remained. The residue on the MCE filter was further processed by microwave oven digestion; the insoluble results were added to the insoluble fraction to calculate total metal content. The remaining three dissolution samples were filtered by syringe filters. Residues on syringe filters were not further digested because of their harness. The filtered solution was diluted to 40 ml with distilled water after adding 0.5 ml nitric acid for stabilization.
Soluble nickel is difficult to extract with distilled water (HSE 1998; CitationZatka et al. 1992). Thus, ammonium citrate solution was used, which was made from di-ammonium hydrogen citrate (Aldrich, USA) and citric acid monohydrate (Fluka, Switzerland) as designated in the ISO 15202-2 method.
An inductively coupled plasma atomic emission spectrometer (ICP-AES; Model Optima 3000 DV, Perkin-Elmer, USA) with a charge-coupled device (CCD) detector was tuned before analysis, according to the manufacturer's recommended protocol. A prepared sample solution was injected into the plasma torch at 1 ml/min. Thirteen metals were analyzed at 1300 W and the recommended emission wavelength for each metal: aluminum (396.152 nm), barium (233.527 nm), calcium (422.673 nm), chromium (205.560 nm), copper (324.754 nm), iron (238.204 nm), lithium (670.781 nm), magnesium (279.079 nm), manganese (257.610 nm), nickel (232.003 nm), potassium (766.491 nm), sodium (589.592 nm), and zinc (213.856 nm). All analytical results were corrected by reagent blanks or filter blanks.
Total contents and soluble fractions were calculated by dividing the analytical results by the total fume weight. Metals that were below 0.1% were summed and designated as “other” (barium, copper, lithium, zinc, and calcium, except in product D) as shown in and . Soluble nickel in was extracted by distilled water. Comparison of extraction results for soluble nickel between the distilled water and ammonium citrate solution are presented in . We used a t-test to test for significant differences between FCAW/NSS and FCAW/SS fumes.
TABLE 2 Total metal (insoluble + soluble) content in FCAW fumes
TABLE 3 Soluble metal content in FCAW fumes
TABLE 4 Comparison of soluble nickel content measured with different leaching solutions
RESULTS
Total Metal Content in FCAW Fumes
The total metal content in FCAW fumes is summarized in . FCAW/NSS fumes contained significantly more metal than FCAW/SS fumes (51.6 ± 5.69 vs. 40.2 ± 5.20%, p < 0.001).
The metal content profile of FCAW/NSS fumes was different from that of FCAW/SS fumes ( and ). In FCAW fumes, iron was most abundant, followed by magnesium, manganese, sodium, aluminum, and potassium. In FCAW/SS fumes, potassium was most abundant, followed by iron, manganese, sodium, chromium, and nickel.
FIG. 2 Total content (insoluble + soluble) of each metal in FCAW fumes with non-stainless steel (NSS, black bars) and stainless steel (SS, grey bars) wire. Error bars indicate one standard deviation.
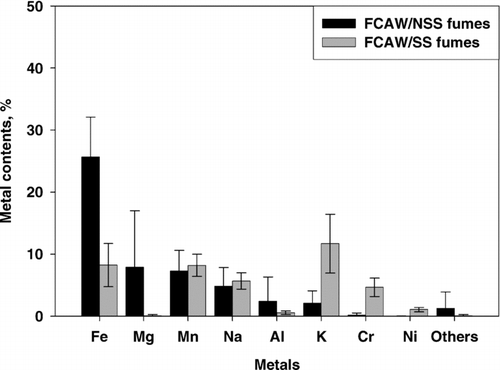
Individual metals had different patterns according to welding type. Iron, aluminum, and magnesium were significantly higher in FCAW/NSS fumes than in FCAW/SS fumes (Fe, 25.7 ± 6.41 vs. 8.22 ± 3.47%, p < 0.001; Al, 2.39 ± 3.91 vs. 0.54 ± 0.29%, p = 0.012; Mg, 7.89 ± 9.08 vs. 0.07 ± 0.17%, p < 0.001).
There was significantly more chromium, nickel, and potassium in FCAW/SS fumes than in FCAW/NSS (Cr, 4.65 ± 1.46 vs. 0.17 ± 0.31%, p < 0.001; Ni, 1.05 ± 0.34 vs. < 0.01%, p < 0.001; K, 11.67 ± 4.72% vs. 2.08 ± 2.00%, p < 0.001). Sodium and manganese had similar contents in both FCAW/NSS and FCAW/SS fumes (Na, 4.84 ± 3.01 vs. 5.66 ± 1.30%, p = 0.18; Mn, 7.24 ± 3.37 vs. 8.19 ± 1.79%, p = 0.19). Barium, copper, lithium, and zinc represented less than 0.1% of both FCAW/NSS and FCAW/SS fumes. Calcium was also less than 0.1%, except for one self-shielded wire (product D) that had 4.47% calcium.
Some metals had different patterns based on the characteristics of the welding wire. Fumes from heat-resistant steel wire (product B) had different characteristics than other FCAW/NSS fumes: the sodium content was somewhat higher but magnesium was much lower than in other wire fumes. Product B contained 0.7% chromium, whereas chromium was below 0.1% in other FCAW/NSS fumes. Self-shielded wire (product D) fumes had a unique pattern: manganese and sodium were 1.75 and 0.42%, respectively, whereas they were 9.10 and 6.15%, respectively, in other FCAW/NSS welding fumes. Iron and potassium amounts were somewhat lower in self-shielded wire fumes than in fumes from other products. Aluminum and magnesium were high (8.91 and 22.8%, respectively) in self-shielded wire fumes, whereas they were below 1.0 and 2.8%, respectively, in other FCAW/NSS welding fumes.
Soluble Metal Content in FCAW Fumes
The soluble metal content was significantly higher in FCAW/SS welding fumes than in FCAW/NSS welding fumes (15.5 ± 5.84 vs. 6.49 ± 2.37%, p < 0.001), in contrast to total metal content (40.2 vs. 51.6%), as shown in . Thus, the soluble fraction of the 13 analyzed metals was significantly higher in FCAW/SS fumes than in FCAW/NSS fumes (39.1 ± 16.46 vs. 12.9 ± 5.33%, p = 0.019).
Individual metals had different soluble content patterns than total metal patterns (). Soluble potassium and sodium were most abundant. Soluble potassium constituted 1.57% of FCAW/NSS fumes and 9.74% of FCAW/SS fumes, which were significantly different (p < 0.001). Soluble sodium constituted 3.59 and 4.70% in FCAW/NSS and FCAW/SS, respectively; these fumes were significantly different (p = 0.02) except when self-shielded FCAW fumes (product D) were excluded (p = 0.97). Soluble sodium constituted 0.23% in self-shielded FCAW fumes which was much lower than in other FCAW/NSS or FCAW/SS fumes.
FIG. 3 Soluble content of each metal in FCAW fumes with non-stainless steel (NSS, black bars) and stainless steel (SS, grey bars) wire. Error bars indicate one standard deviation but is distorted because of logarithmic scale of y-axis.
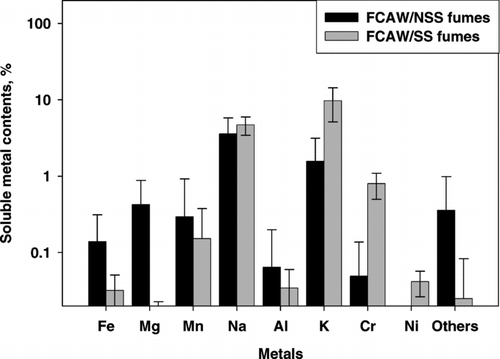
Except soluble potassium and sodium, all soluble metals were below 1%. Iron, aluminum, manganese, and magnesium were higher in FCAW/NSS fumes, but were well below 1%.
The content of soluble chromium was 0.80% in FCAW/SS fumes. Among the FCAW/NSS fumes, 0.20% soluble chromium was found in heat resistant FCAW fumes. Contents of soluble barium, lithium, zinc, and copper were less than 0.1% in both FCAW/NSS and FCAW/SS fumes, with the exception of soluble calcium (1.40%) in self-shielded FCAW fumes (product D).
Like the total metal content, heat resistant flux-cored wire (product B) and self-shielded flux-cored wire (product D) had different characteristics than other products. Mean contents of soluble iron and manganese were 0.42 and 0.98%, respectively, in heat resistant flux-cored wire welding fumes; these values were much higher than those in other FCAW fumes. Also, 0.20% soluble chromium was found in heat resistant flux-cored wire fumes. Contents of soluble potassium and magnesium were very low compared to other FCAW/NSS fumes. Self-shielded wire (product D) fumes contained very little soluble iron, manganese, and potassium, whereas soluble aluminum and magnesium contents were high compared to those in other welding fumes. Soluble nickel is barely leached by distilled water (ISO 2001; HSE 1998). Table IV compares the soluble nickel extracted with distilled water and with ammonium citrate leaching solution. Measured content of soluble nickel was 0.11–0.12% in FCAW/SS fumes with ammonium citrate solution leaching, whereas it was 0.04–0.05% with distilled water leaching.
DISCUSSION
Total Metal Content in FCAW Fumes
Most of the chemical components in welding fumes come from the consumable electrode, i.e., flux-cored wire in this study (CitationPalmer and Eaton 2001; CitationVoitkevich 1995). Metals such as sodium, potassium, calcium, and magnesium originate from the flux, whereas iron, manganese, chromium, and nickel originate from both the outer wire and the flux core (CitationVoitkevich 1995).
It should be emphasized that metal composition data on material safety data sheets provided by welding consumable manufacturers usually provide the consumable compositions which are different from fume constituents. Furthermore, detailed flux composition is the secret of the manufacturer.
We tried to analyze the outer tubular wire and inner flux separately, but digestion with the NIOSH 7300 (heating with nitric and perchloric acid) and ISO 15202-2 annex G (microwave digestion with nitric and perchloric acid) methods was unsuccessful (NIOSH 1994; ISO 2001). Instead, we attempted SEM analysis. The metal composition of the outer shell was similar regardless of analytical points, but the flux composition varied according to the analytical points (). Iron, chromium, nickel, and manganese were found consistently in the outer tubular wire (67.7, 21.6, 1.2, and 9.9%, respectively), but the metal composition of the inner flux varied. Alkali metals, like sodium and potassium, existed in the inner flux. These metals can form slag, which protects the weld pool and is easily evaporated. In addition to the 13 metals analyzed here, silica, titanium, and zirconium were found in flux. Thus, the total amount of metal in fumes was underestimated in this study. It is not clear why metal content is higher in FCAW/NSS fumes than in FCAW/SS fumes. One reason might be the higher iron content of FCAW/NSS. In this study, iron content was significantly higher in FCAW/NSS than in FCAW/SS. We can confirm that there is much more iron and magnesium in mild steel wire, whereas chromium and nickel are incorporated more into stainless steel wire. Another possibility is the contribution of unanalyzed elements such as silica, zirconium, titanium, and fluoride. To clarify their contribution, further studies should compare the contents of NSS and SS flux-cored wire.
FIG. 4 Illustration of the composition of the outer shell and the inner flux in flux-cored wire product E. (a) Cross-section of flux-cored wire and analytical spectra of several points. (b) Analytical spectrum of a cross-section of the flux. Cross sectional spectra are different from analytical spectra at point 3 and 4 because of non-homogenous distribution of flux material.
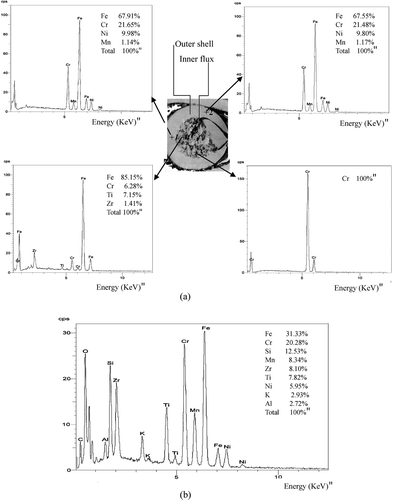
Fume composition by weight from FCAW used in this study might be less affected by vapor chemistry than GMAW. Genkins and Eagar (2005) reported that the inner flux has a greater chance to directly transfer to microspatter, so that about 30% of FCAW fumes are large-diameter (1–20 μ m) microspatter while GMAW fumes contain less than 10% microspatter. Flux material from the inner core of the electrode was reported richer in bulk fumes than metals from the tubular wire (CitationHewitt and Hirst 1991).
Although we could not quantify the inner flux composition, we found that fume composition might be influenced by the inner flux because there was a large difference between fume composition and the outer tubular wire. For example, in product E, chromium and nickel contents (4.85 and 1.00%, respectively) were lower in fumes than in the outer tubular wire (21.6 and 9.9%, respectively) because other metals in the flux contributed to the fumes.
SS welding fumes have lower levels of iron but more manganese, chromium, and nickel compared to MS fumes (CitationLees 1991; CitationCamner and Johansson 1992; CitationAntonini et al. 1999). In this study, iron, chromium, and nickel showed the same patterns as in previous studies (CitationLees 1991; CitationCamner and Johansson 1992), but there was no difference in manganese content between FCAW/SS and FCAW/NSS fumes. These metals are all cytotoxic and are associated with lung disease (CitationLees 1991; CitationCamner and Johansson 1992). Iron, chromium, nickel, and manganese are considered important due to their well known toxicity. The iron and manganese contents were 8.22 and 8.19%, respectively, in FCAW/SS, whereas they were 25.7 and 7.24% in FCAW/NSS. Chromium and nickel contents were 4.65 and 1.05%, respectively, in FCAW/SS, whereas they were negligible in FCAW/NSS (except chromium in heat-resistant wire, product B, 0.70%). Chromium and nickel contents are much higher in GMAW/SS fumes than in FCAW/SS fumes (CitationVoitkevich 1995), because FCAW fumes are affected by the inner flux as well as the outer tubular wire.
From , 48.4% of FCAW/NSS fumes and 59.8% of FCAW/SS fumes were not composed of the 13 metals analyzed. Other chemicals could be constituents in the remaining fumes. First, there could be some other metal constituents that were not analyzed here. Silica, titanium, and zirconium are possible metals in SS welding fumes (CitationJenkins 2003). Silica and titanium represent 4–25 and 0–2%, respectively, of FCAW/NSS (AWS 1987). CitationVoitkevich (1995) reported that the silica content was 2–4% of FCAW/NSS fumes and 3–6% of FCAW/SS fumes, whereas their fluoride contents were 8–15 and 5–10%, respectively. Because various welding variables such as current, voltage, and shielding gas can affect the fume generation rate (CitationYoon et al. 2003), the weight percentage of metal constituents can vary. Second, a considerable amount of fluoride and oxygen could be present in the fumes. Metal elements were presented here, but most metals in fumes exist as compounds that are more complicated when flux is used than in GMAW with solid wire (CitationVoitkevich 1995). Most metals exist as oxides and fluorides. Oxygen can form various metal oxide compounds in fumes such as Fe3O4, FeCr2O4, K2CrO4, K2FeO4,K2MnO4, MnFe2O4, Na2CrO4, and NiO (CitationVoitkevich 1995). The oxygen content of FCAW fumes were reported 36.4% (CitationVoitkevich 1995). Additionally, fluorine compounds and metal carbonates are possible in FCAW with CO2 gas. For example, potassium compounds such as KCrF3, KMnF3, K2NaCrF6, KFeF3, and K2CO3 can be formed in SMAW or FCAW (CitationVoitkevich 1995). The fluoride content of FCAW/NSS fumes ranges from 7 to 13% (AWS 1987). In an x-ray diffraction study of SMAW, which has the same chemistry as FCAW, metals in fumes were present as fluorides. Transmission electron micrographs with energy dispersive spectrometry of FCAW fumes indicate that metal oxides (e.g., Fe3O4) come from the inside core portions, whereas metal fluorides (e.g., K, Na, Ca, or MnF2) come from the outer shell (CitationJenkins 2003).
In fumes from self-shielded flux-cored welding (product D; ), the content of iron, manganese, and sodium was lower than in fumes from other products. This is partially because self-shielded flux-cored electrodes contain large amounts of calcium fluoride, known as fluorospar (CitationAntonini 2003). One reason why the iron content in product D fumes is lower than that of other FCAW/NSS fumes is that aluminum oxide is easily segregated from iron oxide, and these compounds are immiscible (CitationJenkins 2003). Calcium, which was included in “others” in , was 4.47% in product D, whereas it was less than 0.1% in other welding fumes.
Alkali metals (Na and K) are incorporated into the flux of the electrode to form slag, which protects the weld pool. Fluorides, which are also major constituents of flux, form alkali metal compounds if those metals are present and are much more volatile than alkali oxides (CitationJenkins 2003). Fluorides containing fumes were reported to cause more lung injury and inflammation in rats than other types of welding fumes (CitationAntonini et al. 1997).
Soluble Metal Content in FCAW Fumes
Because there has been some debate over the definition of solubility (CitationVoitkevich 1995; CitationWeast 1988; CitationBeliles 1994), it is important to provide an operational definition of solubility when measuring soluble metals in workplace air samples. In this study, double distilled water and ammonium citrate were used in the case of soluble nickel, as described in the ISO 15202-2 method. Possible media include 0.1–0.3 M HCl, 0.22% Na2CO3, 0.01 N lactic acid, and cell growth medium to mimic gastric juices, blood serum pH, or a real biomedium (CitationVoitkevich 1995).
Among the 13 metals analyzed here, four (Fe;1 mg/m3, Ni;0.1 mg/m3, Al;2 mg/m3, and Ba;0.5 mg/m3) have soluble threshold limit values (TLVs) of the American Conference of Governmental Industrial Hygienists (ACGIH). Also, hexavalent chromium is designated as both soluble form (0.05mg/m3) and insoluble form (0.01 mg/m3) (ACGIH 2008). In this study, soluble chromium was analyzed in place of soluble hexavalent chromium. CitationYoon et al. (2003) found that hexavalent chromium content increased from 0.15 to 1.08% with input energy and that soluble hexavalent chromium represented most (80–90%) of the total hexavalent chromium in FCAW/SS fumes.In SMAW, hexavalent chromium is almost entirely in soluble form because potassium or sodium in the flux reacts with chromium and forms K2CrO4, K2Cr2O7, Na2CrO4, and K2NaCrF6, which are all soluble (CitationKoponen et al. 1981; CitationVoitkevich 1995). In this study, the soluble portion of chromium averaged 17.2% (5.0–35.4%).
Soluble forms of iron and manganese are known to complex with fluorine (K3FeF6, FeF3, MnF2, and MnF3) and are found on particle surfaces, while their more insoluble oxide compounds are concentrated in the particle core in the form of Fe3O4 and MnFe2O4 (CitationAntonini et al. 2006). Potassium and sodium contribute to the solubility of other metals.
There was less soluble metal (3.10%) in self-shielded welding fumes (product D), although the total metal content of product D was similar to or above that of other welding fumes. The reason for this finding is that both potassium and sodium are less abundant in product D than in other products ().
Soluble contents of iron, nickel, aluminum, barium, which have soluble ACGIH-TLVs, in both FCAW/SS and FCAW/NSS fumes were very low (maximum 14%, 0.12%, 0.06%, < 0.01%, respectively) as shown in and . When we consider the low contents and soluble ACGIH TLVs for above 4 metals, we suggest that it is unnecessary to monitor the soluble metal concentrations of iron, nickel, aluminum, and barium at the FCAW welding process. But considering the toxicity and low ACGIH-TLVs, chromium in FCAW/SS should be specified in terms of its valance status (trivalent or hexavalent) and solubility (soluble or insoluble).
One major limitation of this study is that we did not take different particle sizes into account, so these results represent the bulk material only. Also, as discussed above, some elements like oxygen, fluorine, silica, titanium, and zirconium were not analyzed. Other limitation is that we did not specify the chromium valance status. Though CitationYoon et al. (2003) found that hexavalent chromium constitutes 0.15–1.08 % in fumes and 80–90% of hexavalent chromium in FCAW/SS fumes was existed as soluble forms in the previous study. We did not evaluate what amounts of hexavalent chromium existed in insoluble chromium and soluble chromium in FCAW/SS fumes in this study.
CONCLUSIONS
• | The metal content profile of FCAW/NSS fumes was different from that of FCAW/SS fumes. Total metal content was higher in FCAW/NSS than in FCAW/SS, whereas soluble metal content was higher in FCAW/SS. Potassium was most abundant in FCAW/SS fumes, followed by iron, manganese, sodium, chromium, and nickel. In FCAW/NSS fumes, iron was most abundant, followed by magnesium, manganese, sodium, aluminum, and potassium. | ||||
• | In FCAW/SS fumes, chromium, nickel, and potassium were significantly higher than in FCAW/NSS fumes. Iron, aluminum, and magnesium were significantly higher in FCAW/NSS than in FCAW/SS. | ||||
• | Fume composition and content were influenced by the inner flux. Proportions of major components of the outer tubular wire (e.g., iron, chromium, nickel, and manganese) were lower in FCAW fumes because inner flux components also contributed to the fumes. | ||||
• | Sodium and potassium, which originated from the inner flux, contributed to soluble metal content. |
The metal composition of FCAW fumes was similar to that of SMAW, whereas FCAW fumes were less similar to GMAW fumes, which is mainly due to the existence of flux in both FCAW and SMAW.
Acknowledgments
The author sincerely thank Dr. Kay Teschke, Professor of School of Environmental Health, University of British Columbia, Canada, for her consideration to finish this article during a stay in Canada and her valuable comments. This study was supported by Research Settlement Fund for the new faculty of SNU and a grant from LG yonam Foundation.
Notes
* Heat—resistant wire.
** Self—shielded wire.
* “Others” include Ba, Li, Cu, Ca, and Zn.
** Sum of metals includes Fe, Cr, Ni, Al, Ba, Mn, Li, Na, K, Mg, Zn, Cu, and Ca.
* Ni was extracted with distilled water. Results from the ammonium citrate extract for Ni are presented in .
** “Others” include Ba, Li, Cu, and Ca.
*** Sum of metals includes Fe, Cr, Ni, Al, Ba, Mn, Li, Na, K, Mg, Zn, Cu, and Ca.
REFERENCES
- American Conference of Governmental Industrial Hygienists (ACGIH) . 2008 . Threshold Limit Values for Chemical Substances and Physical Agents and Biological Exposure Indices , 10 – 61 . Cincinnati, OH : ACGIH .
- American Welding Society (AWS) . 1987 . “ Part II. Arc Welding Fumes and Gases ” . In Fumes and Gases in the Welding Environment , Edited by: Speight , F. Y. and Campbell , H. C. 73 – 86 . American Welding Society . reprinted, ISBN 0-87171-174-5
- Antonini , J. M. , Clarke , R. W. , Krishna Murthy , G. G. , Sreekanthan , P. , Jenkins , N. , Eagar , T. W. and Brain , J. D. 1998 . Freshly Generated Stainless Steel Welding Fume Induced Greater Lung Inflammation in Rats as Compared to Aged Fumes . Toxicol. Lett. , 98 : 77 – 86 .
- Antonini , J. M. , Krishna Murthy , G. G. , Rogers , R. A. , Albert , R. , Ulrich , G. D. and Brain , J. D. 1996 . Pneumotoxicity of and Pulmonary Clearance of Different Welding Fumes after Intratracheal Instillation in the Rat . Toxicol. Appl. Pharmacol. , 140 : 188 – 199 .
- Antonini , J. M. , Krishna Murthy , G. G. and Brain , J. D. 1997 . Responses to Welding Fumes: Lung Injury, Inflammation, and the Release of Tumor Necrosis Factor-Alpha and Interleukin-1b . Exp. Lung Res. , 23 : 205 – 227 .
- Antonini , J. M. , Lawryk , N. J. , Krishna Murthy , G. G. and Brain , J. D. 1999 . Effect of Welding Fume Solubility on Lung Macrophage Viability and Function In Vitro . J. Toxicol. Environ. Health. , 58 : 343 – 363 .
- Antonini , J. M. , Ebeling , A. R. and Roberts , J. R. 2001 . Highly Soluble Stainless Steel Welding Fume Slows the Pulmonary Clearance of a Bacterial Pathogen and Severely Damages the Lungs after Infection . Toxicol. Sci. , 60 : 424
- Antonini , J. M. 2003 . Health Effects of Welding . Critical Reviews in Toxicol. , 33 ( 1 ) : 61 – 103 .
- Antonini , J. M. , O'Callaghan , J. P. and Miller , D. B. 2006 . Development of an Animal Model to Study the Potential Neurotoxic Effects Associated with Welding Fume Inhalation . NeuroToxicol. , 27 : 745 – 751 .
- Ashley , K. 2001 . International Standard Procedure for the Extraction of Metal Compounds having Soluble Threshold Limit Values . Appl. Occup. Environ. Hyg. , 16 : 850 – 853 .
- Beliles , R. P. 1994 . “ The Metals ” . In Patty's Industrial Hygiene and Toxicology, , 4th ed. , vol. 2c , 1879 – 2317 . NewYork : Wiley .
- Butler , O. T. and Howe , A. M. 1999 . Development of an International Standard for the Determination of Metals and Metalloids in Workplace Air Using ICP-AES: Evaluation of Sample Dissolution Procedures Through an Interlaboratory Trial . J. Environ. Monit. , 1 : 23 – 32 .
- Camner , P. and Johansson , A. 1992 . The Reaction of Alveolar Macrophages to Inhaled Metal Aerosols . Environ. Health Perspect. , 97 : 185 – 188 .
- Fairfax , R. and Boltzer , M. 1994 . TLVs—Soluble and Insoluble Metal Compounds . Appl. Occup. Environ. Hyg. , 9 : 683 – 686 .
- Harris , M. K. 2002 . Welding Health and Safety: A Field Guide for OEHS Professionals , 17 – 40 . Fairfax, Virginia : American Industrial Hygiene Association Press .
- Hewitt , P. J. and Gray , C. N. 1983 . Some Difficulties in the Assessment of Electric Arc Welding Fume . Am. Ind. Hyg. Assoc. J. , 44 : 727 – 732 .
- Hewitt , P. J. and Hirst , A. A. 1991 . Development and Validation of a Model to Predict the Metallic Composition of Flux-Cored Arc-Welding Fumes . Ann. Occup. Hyg. , 35 : 223 – 232 .
- Hewitt , P. J. and Hirst , A. A. 1993 . A System Approach to the Control of Welding Fumes at Source . Ann. Occup. Hyg. , 37 : 297 – 306 .
- Health and Safety Executive (HSE) . 1998 . “ MDHS Method 42/2, Nickel and Inorganic Compounds of Nickel; and Method 46/2, Platinum Metal and Soluble Platinum Compounds ” . In Methods for the Determination of Hazardous Substances , Sheffield, UK : HSE .
- International Organization for Standardization (ISO) . 2001 . ISO 15202-2-2001, Work Place Air-Determination of Metals and Metalloids in Airborne Particulate Matter by Inductively coupled Plasma Atomic Emission Spectrometry-Part 2: Sample Preparation , Geneva, , Switzerland : ISO . www.iso.ch
- Jenkins , N. T. 2003 . Chemistry of Airborne Particles from Metallurgical Processing , Ph.D. dissertation Cambridge, Mass. : Massachusetts Institute of Technology .
- Jenkins , N. T. and Eagar , T. W. 2005 . Chemical Analysis of Welding Fume Particles . Welding J. , : 87s – 93s .
- Karlsen , J. T. , Farrants , G. , Torgrimsen , T. and Reith , A. 1992 . Chemical Composition and Morphology of Welding Fume Particles and Grinding Dusts . Am. Ind. Hyg. Assoc. J. , 53 : 290 – 297 .
- Korea Institute of Industrial Technology (KIIT) . 1999 . The Evaluation Techniques of Fume Generation Characteristics and Feedability During Arc Welding (Korean) , 34 – 70 . Seoul : KIIT .
- Koponen , M. , Gustafsson , T. , Kalliomäki , P. and Pyy , L. 1981 . Chromium and Nickel Aerosols in Stainless Steel Manufacturing, Grinding and Welding . Am. Ind. Hyg. Assoc. J. , 42 : 596 – 601 .
- Lees , P. S. J. 1991 . Chromium and Disease: Review of Epidemiologic Studies with Particular Reference to Etiologic Information Provided by Measures of Exposures . Environ. Health Perspect. , 92 : 93 – 104 .
- Palmer , W. G. and Eaton , J. C. 2001 . Effects of Welding on Health—XI , Miami, FL : American Welding Society .
- National Institute for Occupational Safety and Health (NIOSH) . 1988 . Criteria for a Recommended Standard Welding, Brazing, and Thermal Cutting , Cincinnati, OH : DHHS (NOSH) . Publication No. 88–110
- National Institute for Occupational Safety and Health (NIOSH) . 1994 . “ NIOSH Method 7300 Elements ” . In In NIOSH Manual of Analytical Methods , Edited by: Eller , P. M. Cincinnati, OH : DHHS (NOSH) .
- Taylor , M. D. , Roberts , J. R. , Leonard , S. S. , Shi , X. and Antonini , J. M. 2003 . Effects of Welding Fumes of Differing Composition and Solubility on Free Radical Production and Acute Lung Injury and Inflammation in Rats . Toxicol. Sci. , 75 : 181 – 191 .
- Voitkevich , V. G. 1995 . Welding Fumes—Formation, Properties and Biological Effects , 18 – 104 . Abington Publishing, Cambridge . England ISBN 1-85573-185-1
- Weast , R. C. 1988 . CRC Handbook of Chemistry and Physics, 1st student ed , Edited by: Weast , R. C. Boca Raton, FL : CRC Press .
- Yoon , C. S. , Paik , N. W. and Kim , J. H. 2003 . Fume Generation and Content of Total Chromium and Hexavalent Chromium in Flux-Cored Arc Welding . Ann. Occup. Hyg. , 47 : 671 – 680 .
- Zatka , V. J. , Warner , J. S. and Maskery , D. 1992 . Chemical Speciation of Nickel in Airborne Dusts: Analytical Method and Results of An Interlaboratory Test Program . Environ. Sci. Technol. , 26 : 138
- Zimmer , A. T. and Biswas , P. 2001 . Characterization of the Aerosols Resulting from Arc Welding Processes . J. Aerosol Sci. , 32 : 993 – 1008 .
- Zimmer , A. T. , Barona , P. A. and Biswas , P. 2002 . The Influence of Operating Parameters on Number-Weighted Aerosol Size Distribution Generated from a Gas Metal Arc Welding Process . J. Aerosol Sci. , 33 : 519 – 531 .