Abstract
The flame spray pyrolysis (FSP) synthesis of silica particles from two different precursors, tetraethylorthosilicate (TEOS) and silicic acid which have significantly different volatilities, was investigated. The size and morphology of the particles produced using various concentrations of precursors and flame temperatures were examined. Significantly different volatilities of the precursors affected the particle formation mechanism. Two different particle formation mechanisms, vapor phase reaction (VPR) and intradroplet reaction (IDR), are proposed based on the relative time scale for the evaporation of sprayed precursor droplets and for particle formation at the same process conditions. VPR resulted in silica agglomerates with small primary particles of around 10 nm sizes. IDR resulted in isolated and spherical silica particles with the sizes of around 650 nm from silicic acid.
INTRODUCTION
Silica (SiO2) particles have been widely used in various industrial applications such as catalysts, pigments, pharmaceuticals, electronic and thin film substrates, electronic and thermal insulators, and humidity sensors (CitationCaruso et al. 1998; CitationGiesche 1994). Silica powder has been synthesized by the various methods including the sol-gel technique (CitationLu et al. 1997), surfactant-mediated process (CitationInagaki et al. 2002), hydrothermal reaction (CitationTanev and Pinnavaia 1996), chemical vapor deposition (CitationLee et al. 2005), and flame synthesis (CitationJang 1999; CitationMadler et al. 2002).
Flame synthesis has been widely used for producing silica particles in industry. It produces large quantities of particles, provides a good control of the particle size and crystallinity, and is a continuous process without the need for further treatments like calcination (CitationPratsinis 1998). Flame synthesis processes can be divided into the flame vapor synthesis (FVS) and the flame spray pyrolysis (FSP). The precursor is introduced into the flame as a vapor phase in FVS. The important steps in FVS are chemical transformation from precursor to oxide, the nucleation of oxide vapors, the collisions of oxide particles, the condensation of oxide vapor onto oxide particles, and the sintering of oxide particles (CitationFriedlander 2000). However, FVS has the disadvantage of requiring volatile precursors. Also, it is not easy to control the concentration of each precursor during the synthesis of multi-component particles.
In FSP, the precursors are fed into the flame reactor as sprayed droplets. Important advantages of FSP over FVS is that it can easily synthesize multi-component particles and use wide ranges of precursors regardless of their volatility (CitationBickmore et al. 1996; CitationBickmore et al. 1998; CitationChang et al. 2006; CitationJang et al. 2004; CitationMadler et al. 2002; CitationMadler and Pratsinis 2002; CitationMueller et al. 2004; CitationPratsinis 1998; CitationSahm et al. 2004; CitationStrobel et al. 2004; CitationTani et al. 2002). In terms of particle formation mechanism, FSP is more complicated than FVS because the evaporation of the droplets has to be considered in addition to the process steps in FVS. Many precursors have been used to form silica particles by FSP including hexamethyldisiloxane (HMDSO) (CitationMadler et al. 2002), tetraethylorthosilicate (TEOS) (CitationJang et al. 2006), tetramethylsilane (TMS), tetramethylorthosilicate (TMOS), and tetrapropylorthosilicate (TPOS) (CitationJossen et al. 2005). However, these precursors have relatively low boiling points ranging from 27 to 275 °C. Hence, the morphology of silica particles made by FSP was similar to that made by FVS. The morphology of particles is an important issue in the application of particles. Aggregated particles are preferred for reinforcing polymers such as carbon black for tires. On the other hand, spherical particles are desirable for pigments in paint and carrier particles in drug delivery.
In this study, we synthesized silica particles by FSP from two precursors, TEOS and silicic acid ([SiOx(OH)4 - 2x]n), which have significantly different volatilization characteristics. We further present two mechanisms based on the consideration of the different evaporation and particle formation times to explain the different morphologies of the particles obtained from the two precursors.
EXPERIMENTAL DETAILS
Apparatus
Two liquid-phase precursor solutions were prepared for the synthesis of SiO2 particles. One was tetraethylorthosilicate (TEOS, 98%, ACROS Organics, USA) mixed with ethanol (DC Chemical Co., 99.5%) to several concentrations. The other was an aqueous silicic acid solution that was prepared from sodium silicate solution by an ion exchange process with cation exchange resin for the removal of Na+.
A schematic drawing of the experimental apparatus for the preparation of SiO2 powder is shown in . The experimental apparatus consisted of an ultrasonic nebulizer (Alfresa Pharma Co., UN-511), a diffusion flame burner, and a particle collector. The precursor solution was sprayed by a vibrator, operated with a frequency of 1.7 MHz, of the ultrasonic nebulizer. Droplets sprayed from the precursor solution were carried into the central tube of the diffusion burner by dry Ar gas (2 lpm) where the burner has an outer diameter of 36 mm and a length of 300 mm. The liquid flowrate was around 1.07 ml/min which varied somewhat depending on the viscosity of the liquid. Another Ar gas (1 lpm) was flowed through the second tube from the center of the burner for a stable and straight flow of the flame. H2 (99.995%, 5 lpm) was used as the fuel while O2 (99.95%, 6 lpm) and air (15 lpm) were used as oxidants. Temperature profile of the flame is shown in . It was measured by using a Pt-Rh R-type thermocouple (Omega Engineering) with a 0.5 mm diameter. In all the runs, the flame temperature was measured three times along the axial and radial directions of the burner without feeding the precursor. The particles generated in the flame were collected by thermophoresis on the surface of a water-cooled glass tube (100 mm in diameter and 300 mm in length) installed 150 mm above the top of the burner, unless otherwise specified.
Analysis
The particle morphology was characterized by a transmission electron microscope (TEM, Philips, CM 12). The specific surface area of the particles was measured by nitrogen adsorption at –196°C using a BET instrument (Micromeritics, Tristar 3000). Average particle diameter was calculated from the specific surface area of particles using the relationship between the specific surface area (A) and the particle diameter (d p ), d p = 6/ (ρ p · A), where ρ p is the density of particle (SiO2, ρ p = 2.2 g/cm3), assuming spherical particles. The chemical bonds of the particles were analyzed by a Fourier transform infrared spectroscopy (FT-IR, Thermo Electron, Nicolet 380). XRD and FT-IR data showed only silica peaks where the data were not reported in here. Hence, the synthesized particles can be deemed to be pure silica.
RESULTS AND DISCUSSION
The major difference between TEOS and silicic acid is volatility. The boiling point of TEOS is around 169°C. On the other hand, there is no boiling point of silicic acid because it readily forms silica when it loses water molecules. Hence, the volatilities of the two precursors are very different. The volatility can affect the evaporation rate of the precursors and the formation of particles in the flame. The precursor with the high evaporation rate in FSP forms particles similar to that in FVS. The precursor with the low evaporation rate might form particles different from that with the high evaporation rate.
Effect of Precursor Concentration
To see the effect of evaporation rate on the particle morphology, we first varied the concentration of the precursors from 0.1 to 0.5 M in solution. The maximum flame temperature was fixed at 1610°C. As the TEOS concentration in the precursor solution increased from 0.1 to 0.5 M, the specific surface area of silica powder by the BET method decreased from 285 to 81.4 m2/g and the average particle size calculated from the specific surface area increased from 9.6 to 33.5 nm (). These results reveal that the average particle size can easily be controlled by changing the precursor concentration in FSP. However, particles did not grow uniformly in proportion to increase in the precursor concentration. The average particle size increased 3.5 times when the precursor concentration increased 5 times. If one particle was generated from one precursor droplet, the average diameter of particles for a precursor concentration of 0.5 M would be 51/3 = 1.71 times of the average diameter of particles from a precursor concentration of 0.1 M (CitationMessing et al. 1993). Hence, the factor of 3.5 might indicate there are two different particle formation mechanisms depending on the concentration of the precursor. To elucidate this phenomenon, we qualitatively analyzed the particle morphology by TEM.
FIG. 3 (a) Specific surface areas and average particle sizes of silica particles made from TEOS at various concentrations at 1610°C. TEM micrographs of silica particles for (b) 0.1, (c) 0.3, and (d) 0.5 M. (e) Specific surface areas and average particle sizes of silica particles produced from TEOS at various heights from the top of the burner at 0.3 M and 1610°C.
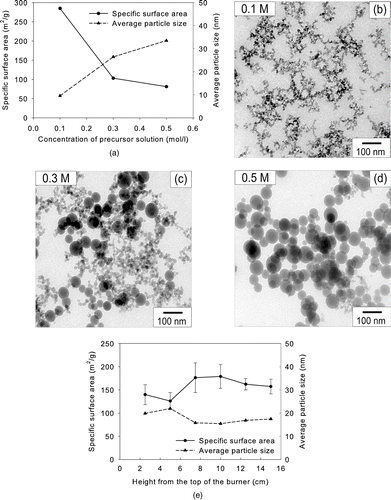
, , shows TEM micrographs of the silica particles as prepared by the FSP using TEOS solutions of various concentrations. The morphology of as-prepared silica nanoparticles was spherical and solid. There were almost no aggregated particles when the concentration of TEOS was 0.5 M. On the contrary, when the precursor concentration was 0.1 M, only chain-like aggregates were produced. Particles made by FVS generally form chain-like aggregates. When the precursor concentration was 0.3 M, both aggregated and dispersed particles coexisted. These results indicate that silica nanopowder from 0.1 and 0.5 M TEOS solutions was formed by different mechanisms. When the precursor concentration was 0.1 M, TEOS was completely evaporated in the flame. The evaporated precursor formed silica aggregates. When the precursor concentration was 0.5 M, TEOS droplets were 1.71 times larger than those generated from the 0.1 M solution. The evaporation time of droplets is proportional to the square of the droplet size (CitationHinds 1999). Hence, the evaporation time of the droplets formed from 0.5 M TEOS solution is 2.92 times longer than those from 0.1 M TEOS solution. The thermal decomposition of TEOS has previously been expressed as a first order reaction (CitationChu et al. 1991; CitationHerzler et al. 1997). The rate constant for thermal decomposition can be expressed as k[1/s] = k 0exp(-E/RT) where k 0 is the pre-exponential factor, E is the activation energy, R is the gas constant, and T is the droplet temperature. Since the droplet temperature is the same if there is no superheating, the particle formation time is the same regardless of the precursor concentration. Therefore, the increased evaporation time of droplets might not be long enough for TEOS to be completely evaporated, resulting in different particle morphologies.
We considered more carefully large and spherical particles shown in and . CitationWegner and Pratsinis (2003) obtained more and larger spherical particles at higher production rate of 25 g/h or lower temperature in flame vapor synthesis. They reported that those particles were formed by the fusion of agglomerates. We agree with their analysis, but our analysis on the formation of particles is somewhat different from their research because the droplet evaporation was not instantaneous in our system when the precursor concentration was high. If coalescence is the only mechanism for large and spherical particles, there should be larger spherical particles at longer residence time and higher temperature. shows the specific surface areas of silica sampled from various heights from the top of the burner at the TEOS concentration of 0.3 M. The result showed no correlation of particle size and residence time. Furthermore, the results obtained under various flame temperatures did not support coalescence for larger spherical particles. Based on the above analysis, we believe that particles were formed inside the droplets before the droplets evaporated completely, in the case of the higher-concentration TEOS solution.
Silica particles were also made from silicic acid under the same condition. The specific surface area values of as-prepared powders from aqueous silicic acid solutions having concentrations of 0.1, 0.3 and 0.5 M were 8.95, 5.78, and 4.10 m2/g, respectively. The average particle diameter calculated from them increased as 305, 472, and 665 nm, respectively (). The actual increase of particle diameter between the first and the third cases was 2.18 times which was very close to 1.71 compared to the case for TEOS. The difference in the increase factor may be due to the difference in droplet size. The droplet sizes were calculated from the particle size with the assumption of one particle formation from one droplet. They were 2.18, 2.34, and 2.78 μ m for 0.1, 0.3, and 0.5 M, respectively. The increase of droplet size with the concentration might be due to the increase of viscosity (CitationLefebvre 1989) and/or due to the polymerization of silicic acid (CitationIler 1979). The calculated sizes of the droplets were smaller than those measured (CitationWang et al. 2008). This was due to the disintegration of droplets in the flame. However, the sizes of disintegrated droplets were larger than those with acetate compounds in FSP (CitationJang et al. 2004). Polymerization of silicic acid might lessen the disintegration of the droplets. Unfortunately, kinetic data of the polymerization of silicic acid do not exist. , , shows TEM pictures of particles from aqueous silicic acid solutions having various concentrations. At all concentrations, spherical, non-hollow and isolated particles were formed. This implies that there was only one mechanism to form silica particles from silicic acid, unlike in the case of TEOS. As stated earlier, the evaporation time of silicic acid was infinitely long due to its low volatility. Hence, silicic acid formed one particle from one droplet resulting in only isolated particles regardless of its concentration.
FIG. 4 (a) Specific surface areas and average particle sizes of silica particles made from silicic acid at various concentrations at 1610°C. TEM micrographs of silica particles for (b) 0.1, (c) 0.3, and (d) 0.5 M.
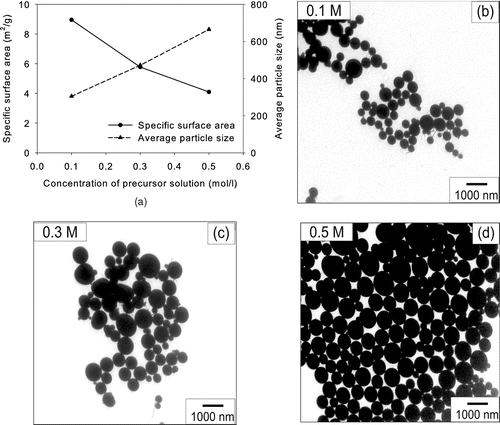
Different energy supplies by silicic acid and TEOS precursors did not affect the product properties. Energy supplied by H2 was 64 kJ/min that was same for both TEOS and silicic acid cases. Energy supplied by TEOS was negligible with 3.7 kJ/min even at 0.5 M compared to 64 kJ/min. Hence, there is few effect of energy addition by TEOS on the larger particles at 0.3 and 0.5 M of TEOS. Energy supplied by ethanol in the TEOS case was 25.1 kJ/min which might cause a difference in product properties. However, the specific surface area of the powders made from silicic acid in ethanol was within 15% from those made from silicic acid in water even with the maximum supplied energy of 20.7 kJ/mol. Hence, additional energy supply by ethanol did not affect the specific surface area data. Also, the flame height was maintained at 310 mm regardless of the ethanol and TEOS feeding at the H2 flowrate of 5 lpm. Therefore, the larger particles were not mainly formed by increased energy and residence time in the flame.
Effect of Flame Temperature
If the particles were made from the precursor vapor, an increase in the flame temperature promotes the particle growth due to higher coalescence rate resulting in larger primary particle size (CitationFriedlander 2000). But in the present study, we investigated another effect of evaporation time of the precursor on the particle morphology with respect to flame temperature when there was incomplete droplet evaporation at a high precursor concentration.
The maximum flame temperature in this work was varied from 1200 to 1710°C by controlling H2 flow rate from 3 to 6 l/min while the precursor concentration in the solution was held at 0.5 M. The average particle size made from TEOS decreased from 47.6 to 15.9 nm as the maximum flame temperature increased from 1200 to 1710°C (). TEM pictures of silica particles prepared from 0.5 M TEOS solution with different flame temperatures are shown in , , , . Although the flame temperature increased, the morphology of as-prepared particles remained spherical and non-aggregated when the maximum flame temperature was lower than 1610°C. However, when the maximum flame temperature was 1710°C, both non-aggregated particles and chain-like aggregates were formed, as shown in . The evaporation rate is proportional to the temperature (CitationFriedlander 2000). Hence, the evaporation time decreased as the temperature increased. The particle formation time inside the droplets, however, was similar because temperature of the droplets remained the same around the boiling point of TEOS. Therefore, as temperature increased, the evaporation was more pronounced than particle formation. At the higher flame temperature, precursor vapors converted to particles after the evaporation of precursor droplet. When the flame temperature was lower, particles formed inside the precursor droplet which did not evaporate completely. This is why the morphologies of particles were different at different temperatures when the precursor concentration was high. There was no effect of longer residence time on larger particles due to the increased energy supply by the increased H2 feeding. The flame height increased from 250 to 340 mm as the H2 flowrate increased from 3 to 6 lpm. However, the BET equivalent size of silica products made from TEOS decreased from 47.6 to 15.9 m2/g even though the residence time in the flame increased. This result also supports the intradroplet reaction instead of ordinary vapor phase reaction.
FIG. 5 (a) Specific surface areas and average particle sizes of silica particles made from TEOS at various temperatures and the precursor concentration of 0.5 M. TEM micrographs of silica particles obtained at (b) 1200, (c) 1350, (d) 1610, and (e) 1710°C.
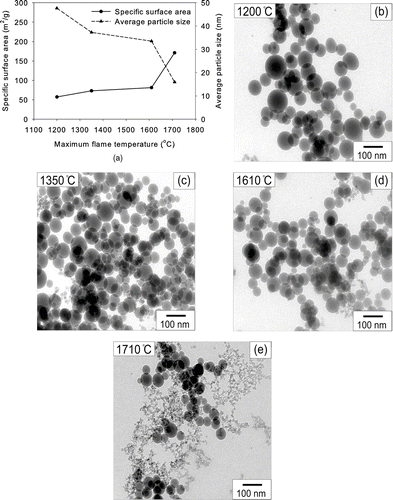
The specific surface area and average size of particles from a silicic acid solution were not changed noticeably with respect to the maximum flame temperature (). In addition, the morphologies of as-prepared silica particles were spherical, non-hollow and non-aggregated under all experimental conditions (, , , ). Temperature of 1710°C was still not enough to evaporate silicon compounds in silicic acid. Hence, silica particles were formed directly from the precursor droplets. That was the reason why the specific surface areas were independent of temperature. The crystalline phase of all silica particles from TEOS and silicic acid solutions was amorphous regardless of temperature.
Particle Formation Mechanisms
The generation and growth of SiO2 particles from sprayed droplets of precursors by the FSP are proposed to follow the paths illustrated in . Primary droplets are formed from the ultrasonic nebulizer. The average size of the droplets are around 6 μ m (CitationWang et al. 2008). These primary droplets are disintegrated in the flame due to a large temperature gradient (CitationJang et al. 2004). From the result of silicic acid, the size of disintegrated droplets was around 2 μ m. After the disintegration, the evaporation of solvents, such as water or ethanol, completed first, and only the precursor remains in the droplet because the solvents have lower boiling point than the precursor. Evaporated precursor by its partial vapor pressure during the complete solvent evaporation was followed by the ordinary vapor phase reaction process to form particles. For the remaining precursor droplets, there are two main mechanisms for particle formation and growth based on the evaporation time and particle formation time. Due to the limited data such as particle formation kinetics, vapor pressure at the droplet surface, and the diffusion coefficient of precursor vapor, the actual comparison of each time, however, could not be performed.
FIG. 7 Particle formation mechanisms. (A) vapor phase reaction (VPR), (B) mixture of VPR and intra-droplet reaction (IDR), and (C) IDR.
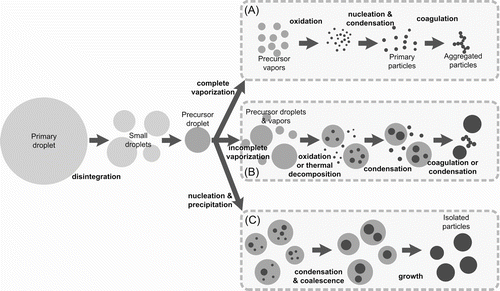
The first mechanism is the vapor phase reaction (VPR, (A) in ) for the case when the evaporation time of the precursor was much shorter than the particle formation time. For particle formation mechanisms, thermal decomposition and precipitation were considered important in this study. The kinetics of silica formation from precursor droplets is not well known, unlike from vapors (CitationChu et al. 1991). The kinetics of particle formation is not dependent on the flame temperature because the temperature of a burning droplet is fixed at its boiling point if there is no superheating. The concentration of precursors is also the same after the evaporation of solvents. Hence, the particle formation time is almost fixed. However, the evaporation time is dependent on the precursor concentration and flame temperature. In this first case, primary particles are generated after the complete evaporation of the precursor droplet. The experimental condition of low precursor concentration and high flame temperature (e.g., 0.1 M at 1610°C) of TEOS belong in this case. The primary particles generated from the precursor vapors typically grow into small and aggregated particles by nucleation, condensation and coagulation in the flame (CitationPratsinis 1998).
The second mechanism, involving intradroplet reaction (IDR, (C) in ), is for the opposite case when the evaporation time of the precursor is much longer than the particle formation time. It applies to all the cases for silicic acid. In the case of IDR, small seed particles are generated by the precipitation inside the precursor droplet before its evaporation. These small seed particles then form one spherical particle in the droplet by condensation and coagulation (CitationIler 1979). Finally, large and non-aggregated spherical particles are formed.
When the evaporation time and particle formation time are comparable, a combination of VPR and IDR occurs, as shown in . It occurs for a higher precursor concentration (e.g., higher than 0.3 M at 1610°C) and a lower flame temperature of TEOS (e.g., lower than 1710°C at 0.5 M). Particles form inside the droplets by thermal decomposition while the droplets are evaporating. This results in two types of particles. Small and aggregated particles are made by VPR, and larger and spherical particles are made by IDR. However, the particles size made from TEOS by IDR was much smaller than that from silicic acid by IDR due to the partial evaporation of TEOS. After particles are formed by VPR and IDR, they may experience coagulation.
CONCLUSIONS
Silica particles having different morphologies were synthesized by FSP from two precursors, TEOS and silicic acid, with different volatilities. The morphology of synthesized particles was dependent on the evaporation rate of the precursor. When the evaporation time was shorter than the particle formation time, aggregated particles were formed like in FVS. Spherical and isolated particles were formed under the opposite condition. Based on these cases, two types of particle formation mechanism, VPR and IDR, are proposed. By choosing an appropriate precursor, particle morphology as well as their crystallinity and size can readily be controlled by taking advantage of the knowledge of these different mechanisms.
Acknowledgments
This research was supported by the General Research Project of the Korea Institute of Geoscience and Mineral Resources (KIGAM) funded by the Ministry of Knowledge Economy.
REFERENCES
- Bickmore , C. R. , Waldner , K. F. , Treadwell , D. R. and Laine , R. M. 1996 . Ultrafine Spinel Powders by Flame Spray Pyrolysis of a Magnesium Aluminum Double Alkoxide . J. Am. Ceram. Soc. , 79 : 1419 – 1423 .
- Bickmore , C. R. , Waldner , K. F. , Baranwal , R. , Hinklin , T. , Treadwell , D. R. and Laine , R. M. 1998 . Ultrafine Titania by Flame Spray Pyrolysis of a Titanatrane Complex . J. Eur. Ceram. Soc. , 18 : 287 – 297 .
- Caruso , F. , Caruso , R. A. and Mohwald , H. 1998 . Nanoengineering of Inorganic and Hybrid Hollow Spheres by Colloidal Templating . Science , 282 : 1111 – 1114 .
- Chang , H. W. , Lenggoro , I. W. , Okuyama , K. and Jang , H. D. 2006 . Flame Spray Pyrolysis for Preparing Red-Light-Emitting, Submicron-Sized Luminescent Strontium Titanate Particles . Japanese Journal of Applied Physics Part 1—Regular Papers Brief Communications & Review Papers. , 45 : 967 – 973 .
- Chu , J. C. S. , Breslin , J. , Wang , N. S. and Lin , M. C. 1991 . Relative Stabilities of Tetramethyl Orthosilicate and Tetraethyl Orthosilicate in the Gas Phase . Mater. Lett. , 12 : 179 – 184 .
- Friedlander , S. K. 2000 . Smoke, Dust, and Haze , New York : Oxford University Press .
- Giesche , H. 1994 . Synthesis of Monodispersed Silica Powders II. Controlled Growth Reaction and Continuous Production Process . J. Eur. Ceram. Soc. , 14 : 205 – 214 .
- Herzler , J. , Manion , J. A. and Tsang , W. 1997 . Single-Pulse Shock Tube Study of the Decomposition of Tetraethoxysilane and Related Compounds . J. Phys. Chem. A. , 101 : 5500 – 5508 .
- Hinds , W. C. 1999 . Aerosol Technology , New York : John Wiley & Sons .
- Iler , R. K. 1979 . The Chemistry of Silica , New York : Wiley .
- Inagaki , S. , Guan , S. , Ohsuna , T. and Terasaki , O. 2002 . An Ordered Mesoporous Organosilica Hybrid Material with a Crystal-Like Wall Structure . Nature. , 416 : 304 – 307 .
- Jang , H. D. 1999 . Generation of Silica Nanoparticles from Tetraethylorthosilicate (TEOS) Vapor in a Diffusion Flame . Aerosol Sci. Technol. , 30 : 477 – 488 .
- Jang , H. D. , Seong , C. M. , Suh , Y. J. , Kim , H. C. and Lee , C. K. 2004 . Synthesis of Lithium-Cobalt Oxide Nanoparticles by Flame Spray Pyrolysis . Aerosol Sci. Technol. , 38 : 1027 – 1032 .
- Jang , H. D. , Chang , H. , Suh , Y. and Okuyama , K. 2006 . Synthesis of SiO2 Nanoparticles from Sprayed Droplets of Tetraethylorthosilicate by the Flame Spray Pyrolysis . Current Applied Physics , 6 : e110 – e113 .
- Jossen , R. , Pratsinis , S. E. , Stark , W. J. and Madler , L. 2005 . Criteria for Flame-Spray Synthesis of Hollow, Shell-Like, or Inhomogeneous Oxides . J. Am. Ceram. Soc. , 88 : 1388 – 1393 .
- Lee , M. H. , Cho , K. , Shah , A. P. and Biswas , P. 2005 . Nanostructured Sorbents for Capture of Cadmium Species in Combustion Environments . Environ. Sci. Technol. , 39 : 8481 – 8489 .
- Lefebvre , A. H. 1989 . Atomization and Sprays , London : Taylor & Francis .
- Lu , Y. , Ganguli , R. , Drewien , C. A. , Anderson , M. T. , Jeffrey Brinker , C. , Gong , W. , Guo , Y. , Soyez , H. , Dunn , B. , Huang , M. H. and Zink , J. I. 1997 . Continuous Formation of Supported Cubic and Hexagonal Mesoporous Films by Sol-Gel Dip-Coating . Nature. , 389 : 364 – 368 .
- Madler , L. , Kammler , H. K. , Mueller , R. and Pratsinis , S. E. 2002 . Controlled Synthesis of Nanostructured Particles by Flame Spray Pyrolysis . J. Aerosol Sci. , 33 : 369 – 389 .
- Madler , L. and Pratsinis , S. E. 2002 . Bismuth Oxide Nanoparticles by Flame Spray Pyrolysis . J. Am. Ceram. Soc. , 85 : 1713 – 1718 .
- Messing , G. L. , Zhang , S. C. and Jayanthi , G. V. 1993 . Ceramic Powder Synthesis by Spray Pyrolysis . J. Am. Ceram. Soc. , 76 : 2707 – 2726 .
- Mueller , R. , Jossen , R. , Pratsinis , S. E. , Watson , M. and Akhtar , M. K. 2004 . Zirconia Nanoparticles Made in Spray Flames at High Production Rates . J. Am. Ceram. Soc. , 87 : 197 – 202 .
- Pratsinis , S. E. 1998 . Flame Aerosol Synthesis of Ceramic Powders . Prog. Energ. Combust. , 24 : 197 – 219 .
- Sahm , T. , Madler , L. , Gurlo , A. , Barsan , N. , Pratsinis , S. E. and Weimar , U. 2004 . Flame Spray Synthesis of Tin Dioxide Nanoparticles for Gas Sensing . Sensor, Actuat. B—Chem. , 98 : 148 – 153 .
- Strobel , R. , Krumeich , F. , Stark , W. J. , Pratsinis , S. E. and Baiker , A. 2004 . Flame Spray Synthesis of Pd/Al2O3 Catalysts and Their Behavior in Enantioselective Hydrogenation . J. Catal. , 222 : 307 – 314 .
- Tanev , P. T. and Pinnavaia , T. J. 1996 . Mesoporous Silica Molecular Sieves Prepared by Ionic and Neutral Surfactant Templating: A Comparison of Physical Properties . Chem. Mater. , 8 : 2068 – 2079 .
- Tani , T. , Madler , L. and Pratsinis , S. E. 2002 . Homogeneous ZnO Nanoparticles by Flame Spray Pyrolysis . J. Nanopart. Res. , 4 : 337 – 343 .
- Wang , W. N. , Purwanto , A. , Lenggoro , I. W. , Okuyama , K. , Chang , H. and Jang , H. D. 2008 . Investigation on the Correlations Between Droplet and Particle Size Distribution in Ultrasonic Spray Pyrolysis . Ind. Eng. Chem. Res. , 47 : 1650 – 1659 .
- Wegner , K. and Pratsinis , S. E. 2003 . Scale-up of Nanoparticle Synthesis in Diffusion Flame Reactors . Chem. Eng. Sci. , 58 : 4581 – 4589 .