Abstract
Nano-structured sorbent injection is a promising technique for heavy metal capture in combustion systems. The importance of sorbent injection strategies, including the form of the sorbent and its injection location for metal capture and removal is investigated in this study. A multi-component tri-modal aerosol dynamic model was employed to understand the evolution of heavy metals and sorbents, as well as their interactions in the incineration system. Experiments were conducted to assess the performance of in-situ generated SiO2, compared with bulk Ti-PICL sorbent, in capturing lead and cadmium from a demilitarization incineration system. Nano-structured SiO2 generated in-situ was found to be more efficient than the bulk Ti-PICL sorbent because it offers a higher external surface area for condensation. The sorbent injection location is important as it affects the physical properties of the sorbent and the pathway for heavy metal capture. Extensive sintering and reduction in the surface area were observed when sorbent was injected into high temperature flue gas, i.e., directly into the combustor. However, when injected into much lower temperature flue gas, the pathway for heavy metal capture was altered from condensation to inter-particle coagulation due to the nucleation of heavy metal species. This study further revealed that new emission standards can be readily met with an optimal sorbent injection strategy.
1. INTRODUCTION
Heavy metal emissions are of great concern because of their toxicity to human health and the environment. In the past decades, heavy metal loading in the atmosphere has substantially increased from anthropogenic emission sources, such as coal-fired power plants and waste incinerators. To limit the emissions, in 1999 the U.S. Environmental Protection Agency (USEPA) issued the National Emission Standard for Hazardous Air Pollutants (NESHAP) from combustion sources. Due to the increased awareness of the potential hazards of the pollutants, in October 2005, the standards were tightened to further reduce the emissions. For example, the emission standards for semi-volatile metals (lead and cadmium) from incinerators were reduced from 240 μ g/m3 to 230 μ g/m3 for existing sources and from 24 μ g/m3 to 10 μ g/m3 for new sources. Similarly, the emission standard for mercury was reduced from 45 μ g/m3 to 8.1 μ g/m3 for new sources (Federal Register, 2005). The tightened emission standards call not only for a thorough evaluation of the performance of current control technologies, but also the development of new control techniques.
To effectively design a control methodology, it is important to understand the transformation of metallic species in the combustion environment. These metallic species are encountered both as a natural, trace constituent in fuels and as an industrially processed commodity. When introduced into a combustor, volatile heavy metals vaporize at high temperatures, undergo several reactions, and then nucleate in the cooler downstream regions to form aerosols which ultimately grow to submicrometer size ranges (CitationBiswas and Wu 1998; CitationLinak and Wendt 1994; CitationSuriyawong et al. 2006). Combustion sources are a major source of heavy metals in the atmosphere. Such sources are abundant, and conventional particle control devices typically have minimal collection efficiency in submicrometer size ranges, where toxic metals are predominant (CitationLinak and Wendt 1993; CitationSuriyawong et al. 2008).
Several control methodologies have been proposed for control of toxic metal emissions from combustion systems. In sorbent injection, which is both promising and widely used, sorbents are injected into the combustion system to chemically adsorb heavy metal vapors or scavenge fine-heavy metal particles (CitationYao et al. 2004; CitationGale and Wendt 2002). The former pathway for heavy metal capture is more effective, and thus is preferred. Several factors, such as the physical properties of the sorbent and the evolution of heavy metal size distribution in the system, play an important role in determining this pathway, and subsequently on the effectiveness and the efficiency of the sorbent. Bulk sorbent particles, typically in the micrometer or millimeter size range have been shown to be effective for capturing heavy metal species in combustion systems; however, they are hampered by several physico-chemical limitations (CitationGale and Wendt 2005; CitationUberoi et al. 1990; CitationUberoi and Shadman 1990). Once the metallic species has chemisorbed to the outer surface, the inner volume is rendered ineffective (CitationBiswas and Wu 1998; CitationBiswas, et al. 2005; CitationLee, et al. 2005). Thus, a large volume of bulk sorbent is required to capture trace metals.
In an alternative approach, a nano-structured sorbent agglomerate has demonstrated effectiveness in heavy metal capture with lower sorbent-to-heavy-metal ratios in comparison to bulk sorbents (CitationBiswas and Zachariah 1997; CitationChen, et al. 2007). Owen and Biswas (1996 a, b) reported the effective suppression of lead species nucleation using small quantities of sorbent materials, ratios as low as 5:1 for silica-lead reactions. CitationWu et al. (1998) applied the in-situ generated nano-structured sorbent technique using titanium-based precursors in conjunction with ultraviolet irradiation for mercury capture. They reported a low required mercury to titania ratio of 1:150, much less than mercury to bulk activated carbon ratio of 1:50,000 (CitationGranite, et al. 2000). The nano-structured sorbent consists of an agglomerate of nanometer-sized primary particles; thus, the agglomerate has a very high external surface area for adsorption, compared to spherical particles of the same volume. This external surface area is one of the key parameters governing the efficiency of the sorbent.
Nano-structured sorbents can be generated in-situ by injecting vapor-phase of the sorbent-precursors, such as tetramethyldisiloxane (TMDS) for silica (SiO2) or titanium tetra-isopropoxide (TTIP) for titania (TiO2) particles. At high temperatures, the precursor vapors decompose and form nanometer-sized particles. These particles grow by coagulation and sintering in the combustion system, resulting in agglomerates of nanometer-sized primary particles. CitationLee et al. (2005) reported 99% capture efficiency of cadmium species using in-situ generated nano-structured silica sorbent, with firm binding (less than 3% leaching of cadmium from cadmium-sorbent products). CitationJeong et al. (2007) demonstrated simultaneous removal of cadmium and lead species using in-situ generated nano-structured silica sorbent. These advantages make nano-structured sorbents a promising technique to meet the new emission standards with less additional cost and modifications to the facility.
While the effectiveness of nano-structured sorbents for heavy metal capture has been successfully demonstrated in many laboratory-scale experiments, its application in pilot- and full-scale facilities needs to be carefully designed. To minimize the cost, it is important to minimize mass loading while achieving desirable capture efficiencies. Understanding the evolution of heavy metal compounds, the growth dynamic of sorbent particles, and their interactions will allow optimal injection strategies to be developed. Using both experimental and numerical approaches, this study establishes an understanding of the evolution of heavy metals (lead and cadmium) and sorbent particles, as well as the interactions among them at different sorbent injection strategies in a demilitarization incineration system. The importance of the form of the sorbent and its injection location on the effectiveness and the efficiency of the sorbent for heavy metal capture is highlighted, and the optimal sorbent injection strategy for such a system is proposed.
2. METHODOLOGY
2.1. Test Plan
The overall objective is to demonstrate the importance of the sorbent injection strategy on the effectiveness and the efficiency for heavy metal capture in incineration systems. The test plan was designed as outlined in . In Set I, experimental measurements and numerical simulations were conducted to understand the transformation of the metallic species in a demilitarization incineration system. The particle size distributions and elemental analysis of particulate samples were measured from a slip-stream drawn from three different locations, shown in . The results of Set I provided a baseline for the sorbent injection strategy study in Set III. In Set II, experiments were conducted in a slip-stream system to evaluate the performance of a nano-structured sorbent and a bulk Ti-PICL sorbent, using flue gas from the full-scale incinerator. The slip-stream system allowed us to evaluate the effectiveness of the sorbent in flue gas from the full-scale system, while the key parameters influencing the effectiveness, i.e., residence time and flue gas temperature, were still under proper controlled. In Set III, a modeling study was carried out to determine the effects of sorbent injection strategy on the properties of the sorbent, including external surface area and eventual agglomerate size, and on the interaction of the sorbent and heavy metals in the incineration system. The optimal sorbent injection strategy was established based on the results from Set III.
FIG. 1 (a) A schematic diagram of a 250 kg/day munitions demilitarization incinerator, Tooele Army Depot, Tooele, UT. (b) Schematic diagram of the slip-stream system and the temperature-time history.
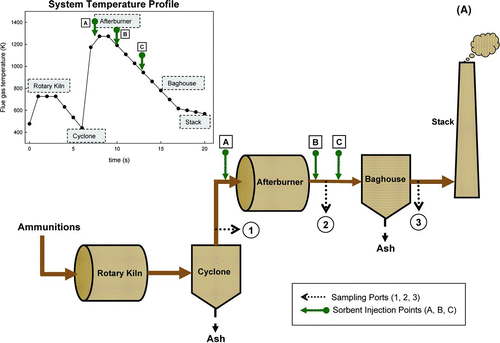
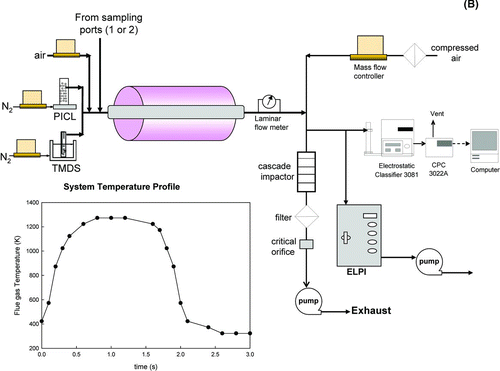
TABLE 1 Summary of experiments and simulations conducted
2.2. Experimental Method
Experiments were conducted on a 250 kg/day munitions demilitarization incinerator, APE1236, at Tooele Army Depot, Tooele, UT. The system, shown in , consisted of a rotary kiln combustor, a cyclone, an afterburner, and a ceramic baghouse. Munitions, including bullets, shell cases, primers, and powder, were introduced into a rotary kiln combustor where they were burnt or detonated. The large metal particle residues entrained in flue gas passed through a cyclone, where they were collected and recovered. The flue gas then traveled through the afterburner, combusting the organics and residues, and the ceramic baghouse, where particulate ash and heavy metals were removed from the exhaust stream before it was emitted into the atmosphere. In this particular system, the flue gas flow rate was approximately 113.3 m3/min, with a gas velocity of 4.2 m/s in the duct. A 2.5 lpm slip-stream was drawn from three locations: before the afterburner, at the baghouse inlet, and at the stack, as shown in . The aerosols entrained in the flue gas were measured by an electrical low pressure impactor (ELPI, Dekati Ltd.) and a real time Scanning Mobility Particle Sizer (SMPS, TSI Inc., Shoreview, MN, USA) to determine the particle size distribution ranging from 10 nm to 10 μ m. The coarse (particle diameter larger than 0.5 μ m) and fine (particle diameter smaller than 0.5 μ m) aerosols were separated using a cascade impactor (Mark III, Pollution Control System Corp., Seattle, WA) with a final stage 50% cut-off particle size of 0.5 μ m. Both coarse and fine particles were also collected on a glass fiber filter (Whatman, EPM 2000) for lead and cadmium species analysis. The analysis was carried out using the ASTM D6357- ICP-MS standard method. The procedure includes a complete digestion of the matrix in a microwave system with strong acids (HF, HNO3, and HCl), and analyses of the digested samples by inductively-coupled plasma mass spectroscopy (ICP-MS).
The experimental system for conducting sorbent capture experiments is shown in . The system consisted of a sorbent injection system, a tubular furnace (Lindberg/Blue M, Model HTF55342C, T max = 1200°C) with a stainless steel reactor tube (2.54 cm I.D. and 90.0 cm long), and a measuring system. A 2.5 lpm slip-stream drawn from the incinerator was introduced into the furnace with a sorbent, resulting in a residence time of 2 s inside the furnace. Two types of sorbents, a vapor phase silica precursor (1,1,3,3-Tetramethyldisiloxane ((CH3)2SiH)2O, Aldrich)-TMDS), and a solid phase titania-pillared clay (Ti-PICL) sorbent, were used. TMDS was introduced into the furnace using a bubbler with 0.1 lpm nitrogen as a carrier gas. The solid Ti-PICL powders were introduced into the furnace using a fluidized bed feeder. The furnace temperature was maintained at 1000°C. At the exit of the furnace, particle-free air at a flow rate of 11.5 lpm was added to reduce the flue gas temperature and quench the aerosol dynamics and chemical reactions. The resultant aerosol was measured by an ELPI and a SMPS to determine the particle size distribution. The coarse and fine aerosols were separated using a six-stage cascade impactor and collected on a glass fiber filter (Whatman, EPM 2000) for leachability testing. The leachability test based on the Toxicity Characteristic Leaching Procedure (TCLP, USEPA Method 1311), was conducted to determine how strongly lead and cadmium were bonded to the sorbent. The dissolution test was performed using 0.04 milli-Q water and 0.1 M acetic acid solution as the extraction fluids. The filters were placed in 50 ml Falcon™ tubes with the respective solutions. Each sample was fixed by an extraction vessel holder and agitated for 24 h at the rotating speed of 8 rpm (Agitator: Barnstead International, Model 4152110). After agitation, the samples were left for 24 h to allow the insoluble solids to settle. Then 10.0 ml of solution was sampled, filtered with a 0.45 μ m membrane filter, and analyzed by an ICP-MS for the concentrations of lead and cadmium species.
2.3. Modeling Approach
To understand the growth dynamics of sorbent particles and its effect on the interaction between metals and sorbent particles in the system, a generalized n-modal and m-species model for evolution of multi-component aerosol dynamics developed by CitationKim et al. (2007) was employed. This model describes particle formation and evolution of multi-component aerosols, and also accounts for the collisional growth of aggregate-liked particle morphology and the change in surface area due to both collisions and sintering.
2.3.1. Model Description
shows a schematic representation of metals and sorbent interaction via a generalized n-modal and m-species model for evolution of multi-component aerosol dynamics. While the model is generalized for any number of components (CitationKim et al. 2007), only the three-component model, representing the interaction of sorbent, lead and cadmium species, was used in this paper. In the three-component model, there are three monomer modes, representing the vapor phases of the two individual heavy metal species and the sorbent precursor, three nucleation modes (mode 1), representing lead, cadmium and sorbent particles formed via nucleation, and one accumulation mode (mode 2), representing the products of the collisions among particles and the condensation of vapor molecules on the particles; as illustrated in . Each mode of the model is considered to have a monodisperse size distribution from the viewpoint of particle volume, similar to a monodisperse model developed by CitationKruis et al.(1993), and a bi-modal model developed by CitationJeong and Choi (2003). The volume of the monomer balance of heavy metal species can be obtained by
FIG. 2 The three component model. Subscripts 1, 2, and 3 represent the three components (in this study, Pb species, Cd species and SiO2, respectively). The subscript “4” represents the accumulation mode that is obtained by the interaction of the species with the sorbent. The subscript “0” represents the initial condition. N is the number concentration, and v the respective particle size. The solid line represents a collisional growth pathway, and the dashed lines represent a condensation growth pathway.
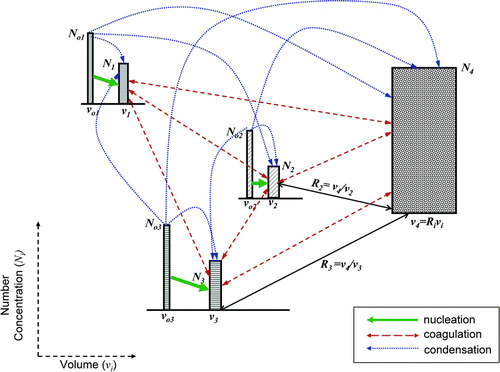
Considering the nucleation mode, the number concentration equation is described as
For the accumulation mode (mode 2), the conservation equations for number, volume, and area concentrations are given by
The collision diameter, d c , of the aggregates in the accumulation mode (mode 2) was adopted to consider the non-sphericity of aggregate particles as defined by CitationKruis et al. (1993):
2.3.2. Simulation Parameters
This study tested in-situ generated nano-structured silica (SiO2) sorbent and titania pillared clay (Ti-PILC) bulk sorbent. The in-situ generated SiO2was produced by the decomposition of sorbent vapor precursor (TMDS) in high temperature flue gas, resulting in molecular-sized SiO2 particles. Both nano-structured SiO2 and Ti-PILC bulk sorbent with a particle size of 100 μ m were modeled in this study, and their effectiveness on heavy metal removal was determined. It should be noted that the model assumes that the sorbent particles are spherical when they are first injected into the flue gas. Later when the particles undergo growth by collisions, they form agglomerates with a fractal dimension of 1.8. This study focused primarily on the capture of lead and cadmium species because they were the primary components of the incinerated munitions (CitationBoddu and Hay 2004). The concentrations of lead and cadmium, 4.16, and 2.0 mg/m3, respectively, used in the simulation were estimated based on the total amount of lead and cadmium in the particulate matter (reported in ), along with the percent enrichment of the metals and their species in the particulate matters, reported in the Emission Measurements Report from the facility (CitationBoddu and Hay 2003). This report indicated that more than 99.9% of the lead and greater than 95% of the cadmium were found in the particulate matter, and the major components of these metals existed in oxide forms, i.e., lead oxide (PbO) and cadmium oxide (CdO). The values of the important parameters used in the model are shown in . The properties of SiO2, CdO, and PbO, tabulated in , are obtained from the CRC Chemistry Handbook (1999–2000), unless otherwise indicated below .
TABLE 2 Parameters and constants used in simulations
TABLE 3 Analysis of lead and cadmium contents in the collected samples
The temperature profile of the flue gas plays an important role in the evolution of the heavy metal species as well as the changing properties of the sorbents. The temperature profile of the munitions demilitarization incinerator, shown in , was used in the simulation. According to the layout of the system, three sorbent injection locations were selected: (1) in the afterburner, (2) after the afterburner, and (3) before the baghouse filter. Sorbent injection prior to the cyclone was impractical since the sorbent would be removed in the cyclone, resulting in the ineffective heavy metal removal. All simulations were performed until the flue gas entered the baghouse.
3. RESULTS AND DISCUSSION
To effectively and efficiently implement a sorbent injection technique, it is important to understand the evolution of the heavy metal species in the combustion system as well as the interaction between heavy metal species and sorbents. The first part of this section discusses the evolution of the metal species in the demilitarization incineration system based on the on-site measurements and the subsequent modeling approach. The second part focuses on understanding the interaction between heavy metals and the nano-structured and bulk Ti-PICL sorbents for capturing lead and cadmium using flue gas in the incineration system. In the last part, the effects of sorbent injection strategy on the interactions among lead, cadmium, and sorbents in the incineration system are discussed.
3.1. Evolution of Heavy Metals in the Incineration System (Set I)
It has been well established that particle formation pathways dictate the eventual particle size (CitationBiswas et al. 2005; CitationLinak and Wendt 1994; CitationSuriyawong, et al. 2006). The particle size distributions were determined by sampling during detonation of munitions without any sorbent addition from three different locations: port 1, after the cyclone, port 2, at the exit of the afterburner, and port 3, at the stack (baghouse outlet). The results are shown in . A bimodal particle size distribution, centered at approximately 0.02–0.08 μ m and 0.2–0.5 μ m in diameter, was observed for flue gas from port 1, after the cyclone. This indicates that at least two particle formation mechanisms, nucleation and fragmentation, occurred in the system prior to the sampling location. In a rotary kiln, where ammunition was detonated, metallic compounds may vaporize or fragment. While large residues resulting from the fragmentation were collected and removed in the cyclone, some of the diminutive residues remained entrained in the flue gas along with the vaporized metallic species. As the flue gas cooled, the vaporized species nucleated or condensed onto the surface of existing particles. Because of different particle formation pathways, these diminutive residues and nucleated particles resulted in a bi-modal particle size distribution. The ultrafine particle mode (less than 100 nm in diameter) was formed via the vaporization-nucleation pathway, and the submicrometer particle mode (less than 1 μ m and greater than 100 nm in diameter) was formed by fragmentation.
FIG. 3 Measured particle size distributions at different locations in the munitions incinerator. Particles larger than 500 nm were measured using an electrical low pressure impactor (ELPI), and the particles less than 500 nm are measured using a scanning mobility particle sizer (SMPS).
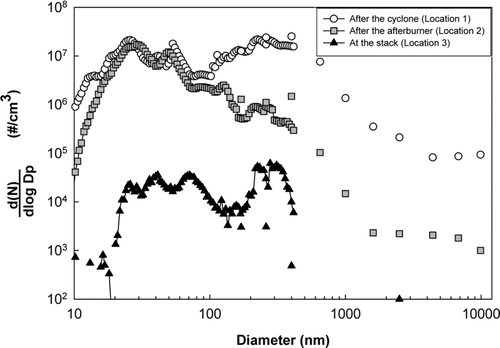
On comparison of the size distributions sampled from port 1 and port 2, no significant differences were apparent for the ultrafine particles. However, the particles in the submicrometer mode were significantly decreased at port 2 (at the exit of the afterburner). At the afterburner, the remaining residues generated by fine-fragmentation in the rotary kiln were vaporized at a temperature of approximately 1273 K. The metallic species that nucleated previously might also re-vaporize and re-nucleate, resulting in an ultrafine particle size distribution similar to that found in sampling location 1. On comparison of the resultant size distributions from port 2 (at the exit of the afterburner) and port 3 (at the stack), a significant reduction of particle numbers were observed, greater than 99% based on the total particle number concentration. Despite this high efficiency of the particle collection in the baghouse, considerable amounts of ultrafine- and submicrometer-sized particles still penetrated through, and were subsequently measured in the stack.
A multi-component tri-modal model was adopted to understand the evolution of PbO and CdO in the system. These simulations were conducted from the afterburner to the baghouse inlet. At the starting location at the afterburner, both PbO and CdO existed in vapor forms prior to injection of the sorbent. The results of the simulations, shown in , are reported as a function of the total residence time in the incineration system. The predicted concentrations of lead and cadmium vapor are shown in , and the particle number concentration and the geometric mean particle size are given in . At the total system residence time of 10 s, flue gas exited the afterburner and subsequently cooled, increasing the vapor concentrations of PbO and CdO, and the saturation ratios of the metals. At a residence time of approximately 11 s, the vapor concentration of PbO sharply decreased and the particle concentration of PbO drastically increased, due to nucleation. At a residence time of approximately 12 s, the vapor concentration of CdO started decreasing; however, no CdO particles were formed at this point, and there was no spike in the total particle concentration. This result implied that the nucleated PbO particles served as the seed for condensation of both PbO and CdO vapors. This prediction was consistent with the experimental observation by CitationJeong et al. (2007). The predicted geometric particle diameter of 38 nm was also in the range, which had been experimentally measured.
FIG. 4 (a) The variation of lead and cadmium vapor concentrations. (b) The evolution of the particle number concentration and the geometric mean particle diameter. Left axis is for the particle number concentration. Right axis is for the geometric mean particle size.
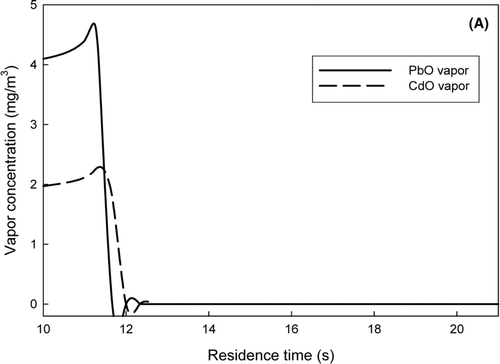
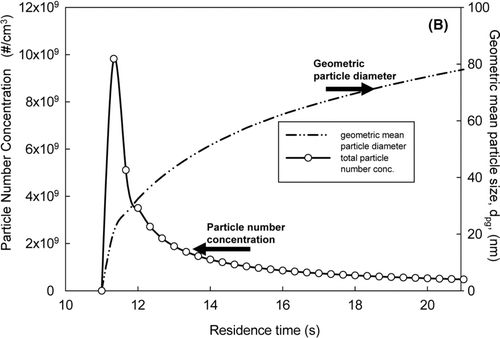
The evolution of PbO and CdO in the system suggested a possible scheme to effectively remove the metals from the system flue gas. Because the saturation ratio (S), the ratio of the metal vapor concentration to its saturation concentration, increases with decreasing temperature, nucleation and condensation are competitive mechanisms for the conversion to the aerosol phase. Nucleation occurs when the saturation ratio of the metal vapor exceeds its critical saturation ratio (S*) for nucleation, while condensation initiates when S is greater than 1. In the interim period, where the saturation ratio is between 1 and S*, the metal vapor is available for condensation on the existing particles. The presence of sorbent particles would allow the metallic vapor to condense out, which is an effective way of suppressing nucleation, reducing the formation of the submicrometer mode, and minimizing emissions of the metals.
3.2. Heavy Metals and Sorbent Interactions—A Slip Stream Test (Set II)
The performance of two different sorbents, in-situ generated SiO2 and bulk Ti-PICL, on capturing lead and cadmium species entrained in the incineration flue gas was evaluated using a slip-stream system. Flue gas, drawn from port 2, was passed through the furnace at 1000°C to mimic the condition at the afterburner. Sorbents were also introduced into the furnace, where they reacted with heavy metal species. and show the results of the in-situ generated SiO2 and bulk Ti-PICL for heavy metal capture. When the in-situ generated SiO2 was injected, the ultrafine particles did not form, as shown in . At a sorbent feed rate of 1.0 g/h, there were no particles smaller than 20 nm, and at a sorbent feed rate of 3.0 g/h, particles smaller than 70 nm were absent. Comparing the resultant size distributions of the sorbent with and without heavy metal species, little change in the particle size distributions toward the larger size was observed when heavy metals were present with the sorbent. The absence of ultrafine particles and the slight shift of the sorbent particle size distributions when the sorbent and heavy metals were present together indicate the condensation of the heavy metal species on the surface of the sorbent particles, and consequently the suppression of the formation of new particles by nucleation.
FIG. 5 Particle size distributions from slip-stream experiments. (a) using in-situ generated SiO2; (b) using bulk Ti-PICL.
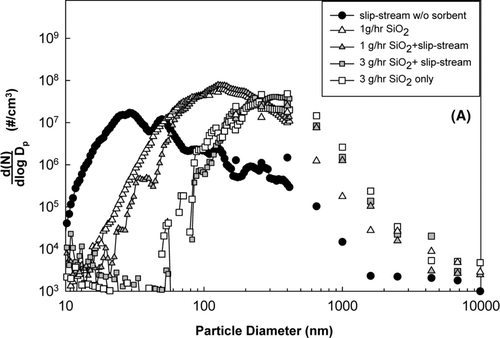
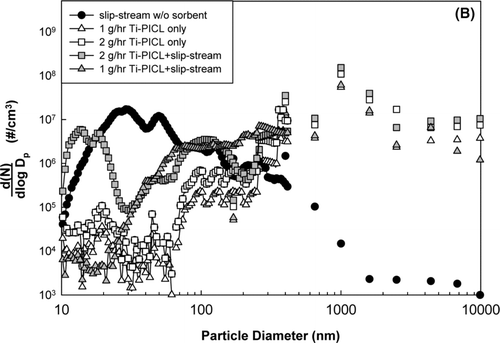
The effectiveness of bulk Ti-PICL on heavy metal capture was also evaluated. The particle size distribution results are shown in . The mean size of Ti-PICL particles was approximately 100 μ m at room temperature; however, when the particles were exposed to high temperature, the particle mean size dropped to around 1 μ m. When the sorbent was injected at feed rates of 1.0 and 2.0 g/h, some reduction in the number of ultrafine particles was observed. The particle size distributions of the sorbent and slip-stream co-feed tests lay between the sorbent only and the slip-stream tests for both sorbent feed rates. The reduction of fine particles indicated condensation of the vaporized metal species on the sorbent; however, the existence of fine particles also implied the nucleation of the remnant metal vapor. These results further suggested that all the metal species were not effectively captured by bulk Ti-PICL sorbent at these feed rates.
The effectiveness of both in-situ generated SiO2 and bulk Ti-PICL for lead and cadmium capture was also evaluated with leachability test (). The dissolution of Cd and Pb from the fine (< 1 μ m) and coarse (> 1 μ m) fractions of the entrained particles in the incinerator flue gas without sorbent injection were determined as a baseline. The dissolution of both metals in Milli-Q water was low, which is consistent with the low solubility of CdO and PbO. The dissolution of lead and cadmium species in 0.1 N acetic acid solution is much higher than in the milli-Q water since PbO and CdO are soluble in low pH solution (CRC 1999–2000). Similar dissolution tests were carried out for the particles collected from the sorbent injection experiments. At the same extraction condition, the dissolution of lead and cadmium from particles collected from sorbent injection experiments was less than the baseline. The in-situ generated SiO2 sorbent demonstrated effective immobilization of both lead and cadmium species, especially in comparison to the bulk Ti-PICL sorbent. The low leachability of metal species from in-situ generated SiO2 can be attributed to the formation of metal-sorbent complex, such as lead silicate and cadmium silicate, which has much lower leachability than that of PbO and CdO in the acetic acid solution (Owen and Biswas 1996a).
To understand the interactions among lead, cadmium, and sorbent particles, a tri-modal model was employed. The predicted concentrations of lead and cadmium vapor and the particle number concentration are reported in for in-situ generated SiO2 and 6B for Ti-PICL. When SiO2vapor precursor was injected into the reactor, it decomposed instantaneously and formed SiO2particles. The SiO2 particles then coagulated and formed aggregates of molecular-sized SiO2 particles, resulting in reduction of the total particle number concentration along the reactor. At a residence time of 1.6 s, the vapor concentrations of lead and cadmium in the flue gas increased as the flue gas cooled upon exiting the reactor. The simulation results at 1.0 g/h sorbent feed rate showed that the total particle number concentration flue gas did not increase significantly as the flue gas cooled. The large external surface area of the aggregates (45 m2/g), promoted condensation of cadmium and lead vapors, and subsequently suppressed nucleation of these metals. These predictions are consistent with the experimental results.
FIG. 6 The variation of lead and cadmium vapor concentrations and total particle number concentration in a slip-stream system. (a) with 1.0 g/h in-situ generated SiO2; (b) with 1.0 g/h bulk Ti-PICL; (c) with 2.0 g/h bulk Ti-PICL. Left axis is for the vapor concentration. Right axis is for the total particle number concentration.
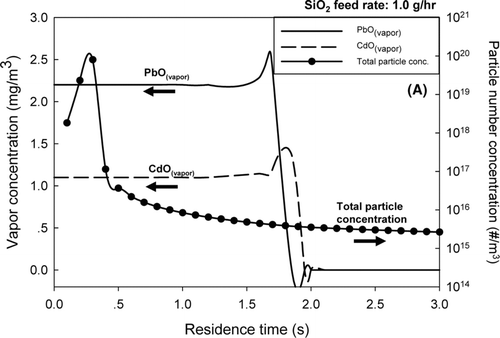
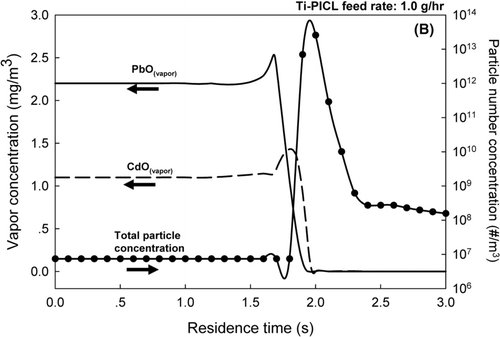
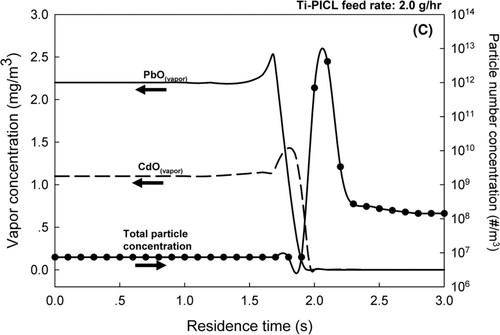
For the bulk Ti-PICL sorbent, results shown in and c, at both sorbent feed rates of 1.0 and 2.0 g/h, a drastic decrease in the vapor concentrations of both CdO and PbO were demonstrated, along with a sharp increase in the total particle number concentrations in the flue gas exiting the reactor. Because of the exponential dependence of the saturation metal vapor concentrations with on flue gas temperature, the saturation ratios of the metals rapidly increased as the flue gas temperature decreased, resulting in competitive mechanisms between particle formation via nucleation and particle growth by condensation. At the sorbent feed rate of 1.0 g/h, and a residence time of 1.7 s, the model prediction showed a spike in the total particle number concentration and a drastic decrease in the vapor concentration of PbO, indicating nucleation of PbO particles. Slightly after the nucleation of PbO, the vapor concentration of CdO also decreased; however, the total particle number did not increase. This result indicated the condensation of CdO vapor on the surfaces of the sorbent and the nucleated PbO particles. When the sorbent feed rate increased to 2.0 g/h, the simulation results showed that the vapor concentration of PbO decreased at a residence time of 1.7 s, followed by a decline in CdO vapor concentration and a sharp increase in the total particle number concentration at a residence time of approximately 1.9 s. These results implied that the increased sorbent feed rate promoted condensation of PbO vapor; however, the total surface area for condensation was still not enough to suppress the nucleation of PbO and CdO particles. The critical saturation ratios of the metals were quickly reached as the flue gas temperature sharply dropped after exiting the reactor. These simulation results were also consistent with the experimental results. At the sorbent feed rate of 1.0 g/h, the ultrafine particles, centered at approximately 30–100 nm, co-existed with the bulk particles. When the sorbent feed rate was increased to 2.0 g/h, an additional ultrafine mode particle, centered on 15 nm, was present, indicating the later nucleation of the remnant metal vapors.
The results of Set II suggested the metal oxides, PbO and CdO, were effectively captured by the in-situ generated SiO2for both tested sorbent feed rates. The bulk Ti-PICL sorbent did not capture the metallic compounds as effectively because the sorbent did not provide enough surface area to remove vapor by condensation and subsequently suppress nucleation of the metals when the saturation ratios were sharply increased as the temperature of the flue gas dropped. These results further underline the importance of the properties of the sorbent (e.g., surface area) the characteristics of heavy metals (e.g., saturation vapor pressure), and the system parameters (e.g., temperature gradient) on the interplay between particle formation and growth mechanisms. These factors greatly affect the performance of the sorbent in heavy metal capture.
3.3. Heavy Metal Capture—Effects of Sorbent Injection Strategy (Set III)
In pilot- and full-scale facilities, several factors, such as the growth dynamics of heavy metals and sorbents and the interactions among them in the system, play an important role in the effectiveness and the efficiency of the sorbent. To understand their effects, a tri-modal model was employed. Two sets of simulations were conducted to examine the effects of sorbent injection strategies, including the sorbent injection location and type of sorbent, on the performance of the sorbent. The first set was performed without heavy metal present. This set evaluated the effects of the sorbent injection strategy on the physical properties of the sorbent, including external surface area and eventual size. The second set was conducted to determine the required sorbent-to-metals-ratios in order to meet the new emission standard of 230 μ g/m3for lead and cadmium. It should be noted that the emitted concentrations of lead and cadmium were determined by the combined amount of vapor-phase and nucleated metal particles of the metal. The metals associated with sorbent particles were assumed to be removed from the flue gas at the particulate control device. According to the layout of the system, three sorbent injection locations were selected: (1) in the afterburner, (2) after the afterburner, and (3) before the baghouse, as shown in . Sorbent injection prior to the cyclone was impractical since the sorbent could be removed in the cyclone, resulting in ineffective heavy metal removal.
The influences of injection location on the key properties of the sorbent, including surface area per unit mass and eventual particle size are shown in . The simulations were conducted in the absence of heavy metals. For all injection locations, the in-situ generated SiO2 sorbent exhibited much higher external surface area per unit mass than that of bulk Ti-PICL particles. This is attributed to the primary size of the sorbent particles. In the in-situ generated process, the molecular-sized SiO2 particles sorbent were generated via the decomposition of the sorbent vapor precursor. Thus, they offered higher external surface area per unit mass than that of micrometer-sized particles. For the in-situ generated SiO2 particles, the surface-area-to-mass ratios instantaneously increased after the injection, then decreased due to sintering, and became constant afterwards, indicating complete decomposition of the vapor precursor for all injection locations. The Si-vapor precursor injected at location 3, exhibited the highest surface area to mass ratio, followed by injection locations 2 and 1. These differences are attributed to sintering. After rapid decomposition of the vapor precursor, the SiO2 particles coagulated and formed aggregates of molecular-sized SiO2 particles. Due to high temperature, the connected particles coalesced by solid-state diffusion, sintering, into more nearly spherical shapes, reducing the surface area and aggregate size. The temperature inside the injection location 1 (the afterburner) was much higher than those of injection location 2 (after the afterburner) and 3 (before the baghouse). Thus, it resulted in faster sintering rates. For bulk sorbent particles, the effects of sintering were also observed, as shown in . However, the effects were not as significant as that seen in the in-situ generated process because the required sintering time is proportional to the fourth power of the primary particle size (CitationKruis, et al. 1993). The initial size of the bulk Ti-PICL particles was much larger than that of the in-situ generated process, so less impact was observed.
FIG. 7 (a) The evolution of the total surface area for different sorbent injection locations. (b) The evolution of the geometric mean diameter for different sorbent injection locations. Left axis is for Ti-PICL sorbent with symbol legends. Right axis is for in-situ generated SiO2 with line legends.

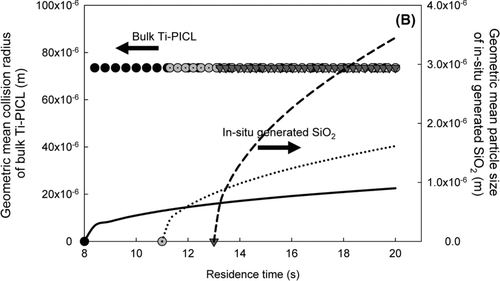
Another important property of the sorbent is its eventual size at the particulate control device. This parameter indicates the effectiveness with which metal-sorbent particle can be captured in a particulate control device. Results of the simulations are illustrated in . The in-situ generated sorbent injected at location 3 exhibited the largest agglomerate size, approximately 3.5 μ m, followed by injection locations 2 and 1. The differences are attributed to sintering, as discussed earlier. The eventual sizes of bulk sorbent particles are relatively the same as their initial size for all injection locations. From all simulation conditions, the eventual agglomerated sizes of SiO2 sorbent ranged between 0.9 to 100 μ m; hence they would be effectively captured by particulate control devices, such as baghouses and ESPs.
To determine the effects of sorbent injection strategy on the efficiency of the sorbent, Set II simulations were performed. The results, shown in , are presented as the required mass ratio of sorbent to heavy metal to meet the emission standard of 230 μ g/m3. The in-situ generated SiO2 was far more effective than the bulk Ti-PICL sorbent for all injection locations. These results are attributed to the key properties of the sorbent and the generation process. The in-situ generation offered higher surface area per unit mass and higher particle number concentration than the bulk sorbent. High surface area promotes condensation of metal oxide vapors, which subsequently suppresses nucleation to form the metal oxide particles. High particle number concentration increases coagulation rates of sorbent-metal products in the system. For the in-situ generated sorbent, the required sorbent-to-metal ratio decreased from injection location 1 to 2 and increased at injection location 3. The decrease was attributed to a higher surface area per unit mass when the sorbent precursor injected at location 2 than that of location 1, as previously discussed. The increase in the sorbent required at injection location 3 was attributed to the mechanism for capturing heavy metal species. According to the evolution of PbO and CdO in the system discussed in Section 3.1, PbO vapor nucleated prior to injection location 3; hence, inter-coagulation was the mechanism for removing PbO particles. Since the coagulation rate depends on particle number concentration, more sorbent was required (CitationFriedlander et al. 1989; CitationLee and Wu 2005). For bulk sorbent, there was no significant difference in the required amounts of sorbent between injection location 1 and 2; however, the required amount was substantially increased at injection location 3. The former results indicated that sintering was not significant for the bulk sorbent, which is consistent with the previous findings. The substantial increase of the required sorbent at injection location 3 resulted from the inter-coagulation mechanism. At the same mass concentration, the bulk sorbent offers much lower particle number concentration and external surface area, resulting in much more sorbent required.
FIG. 8 Required sorbent to metal mass ratio for different injection locations to meet the emission standard of 230 μ g/m3
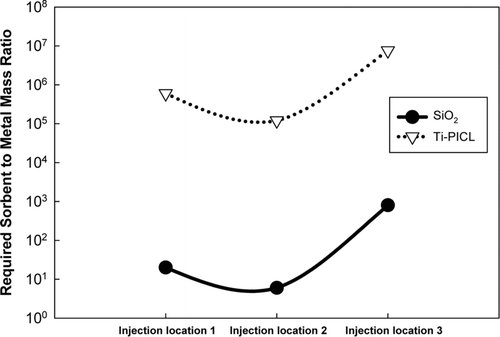
As cost is always important, an optimal sorbent injection strategy is needed. For this incineration system, the in-situ generated sorbent is more efficient, and the sorbent precursor should be injected after the afterburner. In this location, the precursor was completely decomposed, the metallic compounds existed in the vapor-phase, and surface area reduction was not significant, allowing for dominant capture by condensation.
4. CONCLUSIONS
Sorbent injection is one of the promising techniques to control heavy metal emissions from combustion sources. The evolutions of lead and cadmium compounds in a demilitarized incineration system were established. The performance of nano-structured SiO2 and bulk Ti-PICL sorbent was evaluated under the incinerator flue gas using a slip-stream system. The injection strategy, including the form of sorbent injected and the injection location, on the effectiveness and efficiency of the sorbent were demonstrated. An understanding of the evolution of heavy metal species, the growth dynamics of sorbent particles, and their interactions in the system is essential in optimizing the capture process. Sorbent injection should be carefully designed to ensure formation of high-surface-area agglomerates and suppression of nucleation of heavy metals. The new emission standards can be achieved using the sorbent injection technology in conjunction with a well-designed sorbent injection strategy.
Acknowledgments
This work was supported in part by a SBIR Phase II contract (DACA42-03-C-0029) from the U. S. Army Construction Engineering Research Laboratory (CERL) through Triton Systems, Inc. Discussions with Drs. Apoorva Shah, Triton Systems, Inc., and V. Boddu, CERL, Urbana−Champaign, IL, are gratefully acknowledged.
Notes
*sorbent injection location
*estimated from pure cadmium value.
**Gmelin, H. (1969).
REFERENCES
- Biswas , P. , Suriyawong , A. , Smallwood , M. , Noel , J. , Lee , M. and Giammar , D. E. 2005 . Nanostructured Sorbents for Heavy Metal Emission Control - A Review . Proceedings of the American Chemical Society , 229 : U869 – U869 .
- Biswas , P. and Wu , C. Y. 1998 . Control of Toxic Metal Emissions from Combustors Using Sorbents: A Review . J. Air & Waste Manage. Assoc. , 48 ( 2 ) : 113 – 127 .
- Biswas , P. and Zachariah , M. R. 1997 . In-situ Immobilization of Lead Species in Combustion Environments by Injection of Gas Phase Silica Sorbent Precursors . Environ. Sci. & Technol. , 31 ( 9 ) : 2455 – 2463 .
- Boddu , V. M. and Hay , K. J. 2003 . Characterization of Lead and Cadmium Species in Emissions from Deactivation Furnace at Tooele Army Depot , U. S. Army Engineer Research and Development Center .
- Boddu , V. M. and Hay , K. J. Characterization of Lead and Cadmium Species in Emissions from Deactivation Furnace . Proceedings of the 24th Army Sci. Conference . Washington , DC : Department of the Army .
- Chen , X. , Lee , M. H. , Jeong , S. K. , Kim , S. B. , Suriyawong , A. , Higginson , K. , Shah , A. and Biswas , P. Heavy Metal Formation in Munition Waste Incinerators and Nano-structured Sorbents for their Control . Proceedings of the American Chemical Society . Chicago , IL : CRC . (1999–2000). Handbook of Chemistry and Physics, 80th ed., 1999–2000. CRS-Press, Cleveland, OH
- Friedlander , S. K. , Koch , W. and Main , H. H. 1989 . Scavenging of a Coagulating Fine Aerosol by a Coarse Particle Mode . Aerosol Sci. Technol. , 20 : 887 – 890 .
- Friedlander , S. K. 2000 . Smoke, dust, and haze: fundamentals of aerosol dynamics , New York : Oxford University Press .
- Gale , T. K. and Wendt , J. O. L. 2002 . High-Temperature Interactions Between Multiple-Metals and Kaolinite . Combustion and Flame , 131 : 299 – 307 .
- Gale , T. K. and Wendt , J. O. L. 2005 . In-furnace capture of cadmium and other semi-volatile metals by sorbents . Proc. Combust. Ins. , 30 : 2999 – 3007 .
- Granite , E. J. , Pennline , H. W. and Hargis , R. A. 2000 . Novel sorbents for mercury removal from flue gas . Ind. Eng. Chem. Res. , 39 : 1020 – 1029 .
- Gmelin , H. 1969 . Der Anorganischen Chemie , 72 Weinheim/Bergstr. : Verlag Chemies, GmBH . Teil C-Lieferung, 1
- Jeong , I. J. and Choi , M . 2003 . A Simple Bimodal Model for the Evolution of Non-Spherical Particles Undergoing Nucleation, Coagulation and Coalescence . J. Aerosol Sci. , 34 : 965 – 976 .
- Jeong , S. K. , Kim , S. B. , Kim , S. S. , Chen , X. and Biswas , P. 2007 . Simultaneous Removal of Cd and Pb from Flue Gases Using in-situ Generated Nano-sized Sorbents . Ind. Eng. Chem. Res. , 13 ( 7 ) : 1154 – 1161 .
- Kim , S. B. , Jeong , S. K. , Kim , S. S. and Biswas , P. Trimodal Model for Multi-component Aerosol Dynamics, the European Aerosol Conference 2007 . September 9–14 2007 , Salzburg, Austria .
- Kruis , F. E. , Kusters , K. A. and Pratsinis , S. E. 1993 . A Simple Model for the Evolution of the Characteristics of Aggregate Particles Undergoing Coagulation and Sintering . Aerosol Sci. Technol. , 19 : 514 – 526 .
- Lee , M. H. , Cho , K. , Shah , A. P. and Biswas , P. 2005 . Nanostructured Sorbents for Capture of Cadmium Species in Combustion Environments . Environ. Sci. Technol. , 39 : 8481 – 8489 .
- Lee , S. R. and Wu , C. Y. 2005 . Size Distribution Evolution of Fine Aerosols due to Intercoagulation with Coarse Aerosols . Aerosol Sci. Technol. , 39 : 358 – 370 .
- Linak , W. P. and Wendt , J. O. L. 1993 . Toxic Metal Emissions from Incineration—Mechanisms and Control . Prog. Energy Combust Sci. , 19 : 145 – 185 .
- Linak , W. P. and Wendt , J. O. L. 1994 . Trace-metal Transformation Mechanisms during Coal Combustion . Fuel Processing Technol. , 39 : 173 – 198 .
- National Emission Standards for Hazardous Air Pollutants . 2005 . Final Standards for Hazardous Air Pollutants for Hazardous Waste Combustors (Phase I Final Replacement Standards and Phase II) . Federal Register , 70 : 59402
- Owens , T. M. and Biswas , P. 1996a . Reactions between Vapor Phase Lead compounds and In-situ Generated Silica Particles at Various Lead-silicon Feed Ratios: Applications to Toxic Metal Capture in Combustors . J. Air & Waste Manage. Assoc. , 46 : 530 – 538 .
- Owens , T. M. and Biswas , P. 1996b . Vapor Phase Sorbent Precursors for Toxic Metal Emission Control from Combustors . Ind. Eng. Chem. Res. , 35 : 792 – 798 .
- Suriyawong , A. , Gamble , M. D. , Lee , M. , Axelbaum , R. L. and Biswas , P. 2006 . Submicrometer Particle Formation and Mercury Speciation under O2-CO2 Coal Combustion . Energy & Fuels , 20 : 2357 – 2363 .
- Suriyawong , A. , Hogan , C. J. , Jiang , J. and Biswas , P. 2008 . Charged Fraction and Electrostatic Collection of Ultrafine and Submicrometer Particles Formed during O2-CO2 Coal Combustion . Fuel , 87 : 673 – 682 .
- Uberoi , M. , Punjak , W. A. and Shadman , F. 1990 . The Kinetics and Mechanism of Alkali Removal from Flue-Gases by Solid Sorbents . Prog. Energy Combust Sci. , 16 ( 4 ) : 205 – 211 .
- Uberoi , M. and Shadman , F. 1990 . Sorbents for Removal of Lead Compounds from Hot Flue-Gases . AIChE J. , 36 ( 2 ) : 307 – 309 .
- Wu , C. Y. , Lee , T. G. , Tyree , G. , Arar , E. and Biswas , P. 1998 . Capture of Mercury in Combustion Systems by In-situ generated Titania Particles with UV Irradiation . Environ. Eng. Sci. , 15 : 137 – 148 .
- Yao , H. , Mkilaha , I. S. N. and Naruse , I. 2004 . Screening of Sorbents and Capture of Lead and Cadmium Compounds during Sewage Sludge Combustion . Fuel , 83 ( 7–8 ) : 1001 – 1007 .
- Zhuang , Y. and Biswas , P . 2001 . Submicrometer Particle Formation and Control in a Bench-scale Pulverized Coal Combustor . Energy & Fuels , 15 ( 3 ) : 510 – 516 .