Abstract
We present a new flame-based aerosol reactor configuration that combines thermal decomposition and hydrogen reduction to produce metal nanoparticles. This approach uses a fuel-rich hydrogen flame as a source of low-cost energy to initiate particle synthesis, but separates the flame chemistry from the particle formation chemistry. Hot combustion products pass through a nozzle to produce a high-temperature reducing jet. A liquid precursor solution is rapidly atomized, evaporated, and decomposed by the expanding jet, initiating particle formation. In particular, here we have produced carbon-coated copper nanoparticles from an aqueous copper formate precursor solution and characterized them by aerosol mobility distribution measurements, electron microscopy, and x-ray diffraction. Copper serves here as a prototype for non-oxide materials that are generally difficult to produce in flame-based reactors. This work demonstrates that such materials can be produced in substantial quantities with particle diameters below 50 nm in this new process.
1. INTRODUCTION
Nanostructures, for centuries, have been known for their unique properties. Over the past decade many new nanomaterials have been developed, and they are continuously being applied in new technologies. However, with new applications come new challenges. One in particular is production scale. Most nanomaterial synthesis takes place at a laboratory scale, producing only milligrams of material at a time. Production of such materials must be scaled up, at low cost, for many potential applications. There are techniques available to mass produce nanostructures, including flame spray, plasma, and laser pyrolysis (CitationKammler et al. 2001; CitationSwihart 2003). However, these have limitations with respect to the material composition and sizes that can be achieved in each case.
Flame spray pyrolysis is a vapor-phase nanoparticle production process in which a liquid precursor is evaporated and decomposed in a flame. This process is the most widely used method for manufacturing commercial quantities of nanoparticles, as flame-based processes are almost always the most economical when compared to plasma, laser, or furnace-based processes. In flame synthesis, the input energy comes from a low-cost source (the precursor itself or an added fuel), and the heating rate can be extremely rapid (CitationAthanassiou et al. 2006; CitationHahn 1997; CitationKammler et al. 2001).
However, flame synthesis does have important limitations. It is generally difficult to produce non-oxide materials (other than carbon black) through conventional flame spray synthesis, because the particle formation chemistry is intermixed with, and coupled to, the flame chemistry. Furthermore, the residence time in this technique is highly dependent on the properties of the flame, including the flame height and turbulence intensity. Thus, when precise control of particle formation or production of non-oxidized particles is needed, other approaches, such as plasma synthesis or laser pyrolysis, are used. However, they require relatively expensive forms of energy input. Conventional heating via conduction and convection from a reactor wall is more economical and also decoupled from the chemistry, but cannot provide the rapid heating and cooling that can be achieved by methods that deliver energy directly into the gas (CitationKammler et al. 2001).
Praxair has developed a thermal nozzle technology, as described in several U.S. patents (CitationAnderson 1993; CitationAnderson et al. 2002; CitationAnderson et al. 2003; CitationBool et al. 2002), for providing a high-velocity, well-mixed hot gas stream that can be used to atomize a liquid precursor. In its simplest form, this device is a combustion chamber with separate fuel and oxidizer inlets and an engineered converging-diverging nozzle as an outlet. Acceleration of the gas through this nozzle converts some of the thermal energy of combustion into kinetic energy of the gas exiting the nozzle, resulting in a high velocity turbulent jet of hot gas. The gas reaches its sonic velocity at the throat of the nozzle (point of minimum diameter) and then continues to accelerate in the diverging portion. It exits the nozzle as a supersonic jet which must then recompress across a shock wave to return to subsonic flow downstream, converting some kinetic energy back to thermal energy. As demonstrated by CitationAnderson et al. (Anderson et al. 2002), mixing downstream of the nozzle is rapid, providing complete mixing of the hot gas jet with a surrounding gas stream on a sub-millisecond time scale. The high velocity gas jet is also very effective in atomizing a liquid injected around it (CitationAnderson et al. 2003; CitationBool et al. 2002). To exploit this for nanoparticle synthesis, we deliver a liquid precursor solution just downstream of such a nozzle, where the hot jet provides rapid heating and mixing, along with atomization of the precursor solution. The resulting droplets evaporate, the precursor decomposes, and particles nucleate and grow in a uniform environment.
This is similar to a flame spray pyrolysis process, except that combustion and particle formation occur in separate regions of the reactor system. This allows us to decouple the combustion chemistry from the particle formation chemistry. This decoupling is particularly advantageous for preparing metal nanoparticles that are prone to oxidation, and must therefore be produced in a reducing environment. If the thermal nozzle is operated with a fuel-rich hydrogen flame, the atmosphere downstream of the nozzle contains excess hydrogen and is free of oxygen. Use of hydrogen as the fuel eliminates the possibility of soot formation in the combustion zone upstream of the thermal nozzle, and gives water as the only combustion product. This is somewhat similar to plasma-based nanoparticle synthesis methods in which a precursor is injected into a thermal plasma torch downstream of the plasma itself (CitationGirshick 2008; CitationRao et al. 1995; CitationRao et al. 1998). However, hydrogen combustion provides a more efficient and lower-cost source of energy. Unlike a thermal plasma, which must run at very high temperature (>5000 K), the hydrogen flame can be diluted to provide only the minimum temperature needed for precursor decomposition and particle formation.
Furthermore, in conventional flame-spray pyrolysis, the enthalpy content of the precursor solution is a key consideration, and therefore precursors are dissolved in combustible organic solvents. Water-soluble precursors can sometimes be used in water-in-oil type emulsions. However, even then the presence of water can be a problem (CitationTani et al. 2003). Separation of the flame chemistry from the particle formation chemistry in our system allows us to use aqueous precursor solutions, an important advantage with respect to cost, environmental impact, and precursor flexibility.
Copper formate is an inexpensive copper precursor that has a high solubility in water and decomposes thermally to produce copper or copper oxide and gaseous byproducts (CO2 and CO). In the presence of excess hydrogen, any oxides produced (CuO or Cu2O) will be reduced to metallic copper. Here, as a first demonstration of the method, we have used copper formate to produce carbon-coated copper particles via the following overall reactions.
Carbon-coated nanomaterials, especially metals, are of significant interest, due to their stability against oxidation and degradation. Copper nanoparticles with a layer of carbon on the surface can be used to stabilize particles while maintaining electrical and thermal conductivity comparable to materials that are currently used in conductive inks. They therefore hold great promise as a lower-cost replacement for gold and silver particles in these applications. They also have potential for use in thermally conductive inks and pastes and in EMI shielding applications (CitationLuechinger et al. 2008). Aerosol methods such as arc-discharge techniques (CitationErmoline et al. 2002; CitationLiu et al. 2004) and flame-spray pyrolysis in a reducing atmosphere (CitationAthanassiou et al. 2006; CitationLuechinger et al. 2008) combine the synthesis of particles and carbon coating into one step, and provide the most economical routes to these materials. Stark and co-workers have prepared carbon-coated copper nanoparticles using a flame-spray pyrolysis approach and tested their performance in conductive inks and sensing applications (CitationAthanassiou et al. 2006; CitationLuechinger et al. 2008). Importantly, they showed good conductivity of printed patterns without a separate sintering step, as well as long-term stability of the carbon-coated copper at ambient conditions. However, in their conventional flame-spray pyrolysis approach (putting a flame-spray nozzle inside a nitrogen-filled glove box to achieve reducing conditions) Stark et al. used a relatively expensive organometallic precursor, Copper (II) 2-ethyl-hexanoate, dissolved in tetrahydrofuran. They also primarily produced much larger particles than those shown here. Thus, our simpler (no glove-box required) process with a low-cost aqueous precursor has the potential to achieve the same or better results at lower cost and with less environmental impact if it can be scaled up to appropriate production rates.
2. EXPERIMENTAL
2.1. High-Temperature-Reducing Jet Synthesis
Our prototype high-temperature-reducing jet reactor is shown schematically in . In it, a relatively small flow of oxygen (∼2 SLM) enters the combustion region through a central lance, with a larger flow of hydrogen and nitrogen (∼10 SLM total) entering through a surrounding concentric annular region. An inverted diffusion flame (oxidant on the inside, fuel on the outside) forms at the tip of the oxygen inlet lance. The flame temperature is controlled by varying the oxygen flow, while always using excess hydrogen. The hot combustion products are accelerated through a converging-diverging nozzle. The precursor is delivered into the diverging portion of the nozzle. Residence time in the particle nucleation and growth section (between the nozzle and the quench zone) can be varied by changing its length and diameter. This allows for residence times from a few milliseconds to at least a few hundred milliseconds. A residence time of about 50 ms was used here. Our system is designed for a total gas flow through the nozzle of about 10–20 SLM. Based on Praxair's operating experience with similar thermal nozzles, this is near the minimum scale at which the thermal nozzle performs well. At the exit of the reactor, the product particles are quenched by mixing with an excess of cold nitrogen (∼100 slm), very rapidly lowering the product temperature and ending particle growth. Rapid quenching minimizes formation of “hard agglomerates” of partially sintered particles. Additional dilution nitrogen (up to 100 slm) can be added at the filter inlet to provide further dilution and cooling.
Product particles are collected using a 293 mm diameter mixed-cellulose ester filter with 0.2 micron pore size. This provides efficient particle collection with minimal pressure drop at the flow rates used here. The particle-laden filter is subsequently dissolved in acetone. Particles are recovered by centrifugation and washed in acetone and acetic acid.
2.2. Nanoparticle Characterization
The copper nanoparticles were analyzed by a series of methods: x-ray diffraction (XRD) (Rigaku Ultima IV X-Ray Diffractometer), transmission electron microscopy (TEM) (JEOL JEM 2010 at an accelerating voltage of 200 KV), and scanning electron microscopy (Hitachi SU70 thermally assisted field emission SEM). A custom-built electrostatic sampler, similar to that described by (CitationDixkens and Fissan 1999), was used for collecting particles directly onto TEM grids for offline analysis.
The size distribution of particles (or agglomerates) was also measured downstream of the reactor using a scanning mobility particle sizing system. In this device, an electrostatic classifier (Differential Mobility Analyzer or DMA) separates particles by electrical mobility. The monodispersed aerosol exiting the DMA passes to a Condensation Particle Counter (CPC), which measures particle number concentration. Scanning the voltage applied to the electrostatic classifier while monitoring the particle concentration provides data that can be used to obtain the particle size distribution (CitationChen et al. 1998). Data inversion was carried out using our own codes (CitationTalukdar and Swihart 2003). The configuration used here (TSI 3776 CPC and TSI 3085 DMA) with 1.5 slpm sample flow provides measurements for particle diameters of about 2 to 100 nm. Bipolar charging was achieved using a home-built Po-210 neutralizer.
3. RESULTS AND DISCUSSION
In the experiments described here, we produced copper nanoparticles from copper formate. Copper formate is a low-cost copper salt that is highly soluble in water, sublimes above 150°C, and decomposes to give copper oxides and carbon oxides (CitationPatnaik 2003). Thus, upon rapid heating of copper formate, we expect evaporation of water from precursor droplets, leaving solid Cu(HCO2)2 particles that then sublime and decompose. This might lead to formation of CuO or Cu2O particles directly from Cu(HCO2)2, or to nucleation of Cu, CuO, or Cu2O from the gas phase. In any case, in the presence of hydrogen at elevated temperature, copper oxides are reduced to metallic copper. Simultaneously, at sufficiently high temperature, reduction of CO and CO2 produced as a by-product of precursor decomposition can lead to deposition of carbon on the surface of the newly formed copper particles. shows a scanning transmission electron microscope (STEM) image of particles produced in this system from copper formate and sampled directly onto a TEM grid using electrostatic deposition. In this case, the vast majority of particles (by number) are below 20 nm in diameter, but there is a small fraction of larger particles. The particles are mostly unagglomerated, in contrast to typical aerosol particles. This is a direct result of the short residence time within the reactor (∼50 ms) and in the lines leading to the electrostatic sampler (∼200 ms).
FIG. 2 Scanning transmission electron microscopy (STEM) image of copper particles produced from copper formate. Energy-dispersive x-ray spectroscopy showed that the particles were copper.
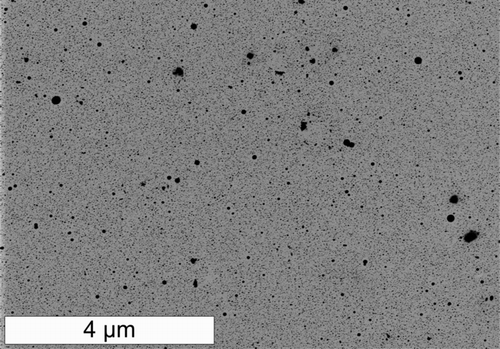
shows two high resolution TEM images of single copper nanoparticles, along with the corresponding selected area electron diffraction (SAED) pattern. The lattice fringes in the high-resolution images have a spacing of 2.09 Å, matching the expected 2.084 Å spacing of fcc copper (111) planes. Likewise, the SAED ring diameters are consistent with metallic copper. Each particle is coated with ∼2 nm of material that is presumed to be amorphous carbon. The wavy, layered appearance is typical of amorphous or partially graphitic carbon. shows a larger field-of-view of the copper carbon-coated particles. At higher magnification, each particle was similar to the one shown in , having a crystalline copper core and carbon shell. The particles shown in Figures and were collected from a sample stream that had been diluted with dry nitrogen.
FIG. 3 Transmission electron micrographs (a, b) and selected area electron diffraction pattern (c) of isolated copper nanoparticles. In (c) we have superimposed rings at the expected diameters for diffraction from the copper fcc lattice.
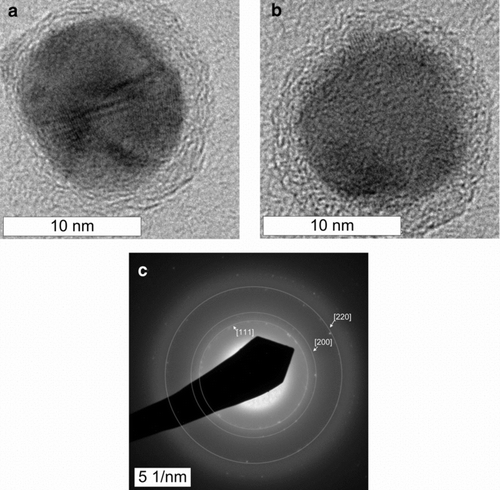
Powder x-ray diffraction, shown in , corroborated the presence of metallic copper, with peaks corresponding to the [1, 1,1], [2, 0,0], and [2, 2,0] planes of the copper fcc lattice. The XRD pattern displayed a broad peak around 10–40° indicating the presence of non-crystalline material. No peak attributable to graphite could be detected. Similar XRD patterns (broad peak at 10–40°) have been observed for amorphous carbon and multiwall carbon nanotubes (CitationGuo and Li 2005). These results are also similar to those observed for carbon-coated copper particles produced by other methods (CitationAthanassiou et al. 2006). The sharp peaks shown in the XRD data are probably due to a small minority of larger particles like the one shown in , which may dominate the x-ray diffraction. Samples used for XRD were obtained by collection on filter membranes, followed by dissolution of the membrane and washing with acetone and acetic acid. This washing may have also dissolved particles that had incomplete carbon coatings, biasing the size distribution of particles used in the XRD measurement toward larger particles. Further washing with acetic acid left behind many hollow carbon shells, as seen in . Particles with multiple internal planar defects, like the one shown in were also observed.
FIG. 6 Transmission electron micrographs of carbon coated copper nanoparticles (a, b) collected on membrane filters and recovered by dissolution of the filter and washing, (c) carbon shells remaining after washing in acetic acid.
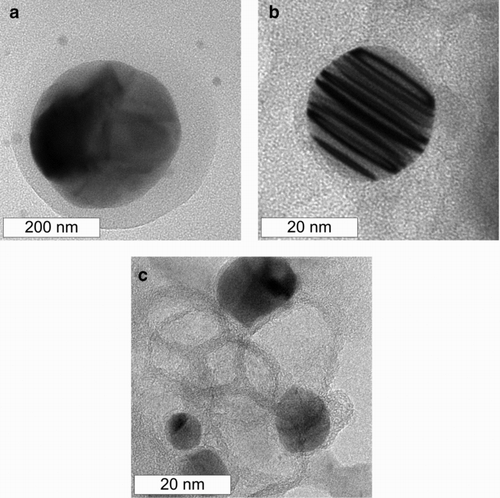
We have also made online aerosol size distribution measurements, using a scanning mobility particle sizer (SMPS). The SMPS provides a rapid (∼5 min) measurement of the size distribution of particles reaching it. This can be a valuable addition to more time-consuming analysis of size distributions based on electron microscopy. An example of measured size distributions is shown in , here the reproducibility of reactor conditions (temperature, pressure, and flows) between different runs resulting in reproducible size distributions. Some aggregation may occur in the sampling system, leading to a measured size distribution based on electrical mobility that is slightly larger than the primary particle size observed in TEM. This effect was more pronounced at higher precursor concentrations, where the apparent increase in particle size measured with the SMPS was much greater than the increase in primary particle size observed by TEM imaging.
FIG. 7 Example of size distributions measured using the SMPS, for five runs at nominally identical conditions. The geometric mean diameter and geometric standard deviation are 13.2 nm and 1.49, respectively.
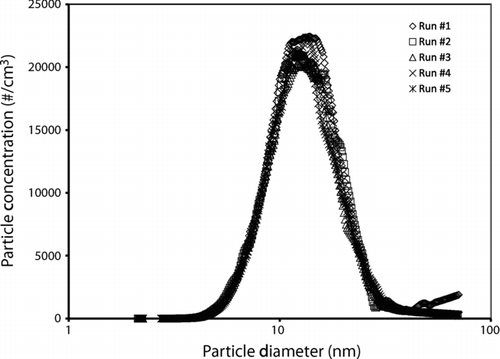
For baseline conditions of about 580–600°C and 4 psig in the particle formation zone, precursor flow of ∼5 ml/min (corresponding to ∼180 mg/h copper, as a 10 mM solution of copper formate), and gas flows as described above, we obtain a particle size distribution measured by the SMPS as shown in . This corresponds to a typical geometric mean particle diameter near 13 nm, with a size distribution typical of particles formed by aggregation and sintering (σ g = 1.49). It should be emphasized that this size distribution represents the electrical mobility diameter of particles or aggregates reaching the particle measurement system, and may be larger than the diameter of the primary particles produced in the reactor.
The particle size distribution can be influenced by many factors, including the pressure, temperature, gas, and precursor flow rates, and precursor concentration. However, at the current scale and with the current nozzle design, the operating window over which the nozzle provides stable (non-pulsatile) precursor delivery and uniform atomization of the precursor is relatively narrow. Combined results from TEM imaging and from the SMPS mobility-based measurements showed that the size distribution of primary particles did not vary dramatically within this range. Thus, a systematic study of the change of particle size and size distribution with operating conditions has not been presented here.
4. CONCLUSION
We have demonstrated here a new aerosol reactor configuration for production of non-oxide materials using flame-based heating. This unique millisecond-residence-time aerosol reactor has the important advantage of separating the flame chemistry from the particle nucleation and growth chemistry. This allows particle formation to occur entirely in a reducing environment. As a first demonstration of this approach, we have produced carbon-coated copper particles in this system using an aqueous copper formate precursor, demonstrating that this process can produce non-agglomerated metal nanoparticles. The particular choice of copper formate as a precursor for the work demonstrated here was based on its ability to generate a protective carbon coating in situ, along with its low cost, high water solubility, and decomposition to the desired product and environmentally benign byproducts. However, other precursors, such as copper nitrate and copper sulfate, can also be used, with different cost and by-product profiles without any changes to the reactor design. Likewise, for other metals, analogous low-cost water-soluble precursors are available (e.g., silver acetate or silver nitrate for producing silver nanoparticles). Thus, the HTRJ reactor is potentially a platform technology that can produce a broad range of metals that are oxidized in a conventional flame reactor, but that will not be oxidized in the presence of water and hydrogen. Moreover, it can do so using aqueous solutions of inexpensive precursors that decompose to produce the desired metal nanoparticles and environmentally benign by-products.
This work was partially supported by The National Science Foundation (CBET-0652042), and the University at Buffalo Integrated Nanostructured Systems Instrumentation Facility.
References
- Anderson , J. E. 1993 . “ Thermal Nozzle Combustion Method U.S.A. ” . Patent #5,266,024.
- Anderson , J. E. , Francis , A. W. , Wagner , M. L. and Leger , C. B. 2002 . “ Hot Gas Reactor and Process for Using Same U.S.A. ” . Patent #6,471,937.
- Anderson , J. E. , Bool , J. E. , Arnold , G. W. and Leger , C. B. 2003 . “ Hot Gas Atomization U.S.A. ” . Patent #6,565,010.
- Athanassiou , E. K. , Grass , R. N. and Stark , W. J. 2006 . Large-Scale Production of Carbon-Coated Copper Nanoparticles for Sensor Applications. . Nanotechnol. , 17 : 1668 – 1673 .
- Bool , J. E. , Anderson , J. E. , Arnold , G. W. and Leger , C. B. 2002 . “ Fuel and Waste Combustion System U.S.A. ” . Patent #6,450,108.
- Chen , D. R. , Pui , D. Y. H. , Hummes , D. , Fissan , H. , Quant , F. R. and Sem , G. J. 1998 . Design and Evaluation of a Nanometer Aerosol Differential Mobility Analyzer (Nano-DMA). . J. Aerosol Sci. , 29 : 497 – 509 .
- Dixkens , J. and Fissan , H. 1999 . Development of an Electrostatic Precipitator for Off-Line Particle Analysis. . Aerosol Sci. Technol. , 30 : 438 – 453 .
- Ermoline , A. , Schoenitz , M. , Dreizin , E. and Yao , N. 2002 . Production of Carbon-Coated Aluminium Nanopowders in Pulsed Microarc Discharge. . Nanotechnol. , 13 : 638 – 643 .
- Girshick , S. L. 2008 . Aerosol Processing for Nanomanufacturing. . J. Nanopart. Res. , 10 : 935 – 945 .
- Guo , D. J. and Li , H. L. 2005 . Highly Dispersed Ag Nanoparticles on Functional MWNT Surfaces for Methanol Oxidation in Alkaline Solution. . Carbon , 43 : 1259 – 1264 .
- Hahn , H. 1997 . Gas Phase Synthesis of Nanocrystalline Materials. . Nanostruct. Mater. , 9 : 3 – 12 .
- Kammler , H. K. , Mädler , L. and Pratsinis , S. E. 2001 . Flame Synthesis of Nanoparticles. . Chem. Eng. Technol. , 24 : 583 – 596 .
- Liu , Y. , Ling , J. , Wei , U. and Zhang , X. G. 2004 . Effective Synthesis of Carbon-Coated Co and Ni Nanocrystallites with Improved Magnetic Properties by AC Arc Discharge Under an N-2 Atmosphere. . Nanotechnol. , 15 : 43 – 47 .
- Luechinger , N. A. , Athanassiou , E. K. and Stark , W. J. 2008 . Graphene-stabilized Copper Nanoparticles as an Air-Stable Substitute for Silver and Gold in Low-Cost Ink-Jet Printable Electronics. . Nanotechnol. , 19 : 445201
- Patnaik , P. 2003 . Handbook of Inorganic Chemicals , New York : McGraw-Hill .
- Rao , N. , Girshick , S. , Heberlein , J. , McMurry , P. , Jones , S. , Hansen , D. and Micheel , B. 1995 . Nanoparticle Formation Using a Plasma Expansion Process. . Plasma Chem. Plasma Proc. , 15 : 581 – 606 .
- Rao , N. P. , Tymiak , N. , Blum , J. , Neiman , A. , Lee , H. J. , Girshick , S. L. , McMurry , P. H. and Heberlein , J. 1998 . Hypersonic Plasma Particle Deposition of Nanostructured Silicon and Silicon Carbide. . J. Aerosol Sci. , 29 : 707 – 720 .
- Swihart , M. T. 2003 . Vapor-Phase Synthesis of Nanoparticles. . Curr. Opin. Colloid Interf. Sci. , 8 : 127 – 133 .
- Talukdar , S. S. and Swihart , M. T. 2003 . An Improved Data Inversion Program for Obtaining Aerosol Size Distributions from Scanning Differential Mobility Analyzer Data. . Aerosol Sci. Technol. , 37 : 145 – 161 .
- Tani , T. , Watanabe , N. and Takatori , K. 2003 . Emulsion Combustion and Flame Spray Synthesis of Zinc Oxide/Silica Particles. . J. Nanopart. Res. , 5 : 39 – 46 .