Abstract
In this article, the influence of the water vapor concentration on structural changes of SiO2 aerosol nanoparticle agglomerates during tempering was studied. The presence of water vapor in the carrier gas was shown to strongly accelerate the kinetics of sintering. While dry sintering at temperatures between 1100°C and 1500°C generated aggregates only, the addition of water to the process yields individual, completely coalesced nanoparticles at a temperature of 1300°C. Furthermore, depending on the water vapor concentration and temperature of the process, evaporation and condensation processes could be observed, leading to bimodal size distributions. The results prove the significant role of the water concentration in high temperature synthesis of silica and may be used to improve the control over morphology and specific surface area in these processes.
1. INTRODUCTION
Owing to their favorable properties, the number of applications for SiO2 nanoparticles is steadily increasing. Examples for these are fillers in polymers (Muriel et al. Citation2007) and lacquers (Barna et al. Citation2005). Silica for these purposes is produced on a large scale by established aerosol processes, e.g., in flame reactors. Consequently, a large number of studies focused on the synthesis and growth of SiO2 nanoparticles in flames (e.g., Ulrich Citation1971, Citation1984; Ehrman et al. Citation1998; Mueller et al. Citation2004).
In the absence of growth species, the main mechanisms increasing the size of SiO2 particles in the gas phase are coagulation and sintering (Ulrich Citation1971). To describe these mechanisms, a number of models exist (Ulrich and Subramanian Citation1977; Koch and Friedlander Citation1990; CitationKruis et al. 1993; CitationXiong and Pratsinis 1993; CitationLehtinen et al. 1996; CitationSander et al. 2009).
To describe the kinetics of sintering, the characteristic sintering time is commonly used in these models. For silica a sintering mechanism based on viscous flow is usually assumed (e.g., CitationEhrman et al. 1998), for which the characteristic sintering time τ was given by CitationFrenkel (1945). An important influence parameter for τ is the viscosity, for which the temperature dependence is described by an Arrhenius approach (CitationKingery et al. 1976).
For a comparison of experimental data for flame synthesized silica with the model, CitationXiong et al. (1993) used the bulk values for the viscosity provided by CitationKingery et al. (1976) to calculate the characteristic sintering time. In a similar attempt, CitationEhrman et al. (1998) employed the data of CitationHetherington et al. (1964). The viscosities given by Kingery were determined for bulk silica in dry atmospheres.
Hetherington provided data for varied water content and showed a weakening of the network by the attack of siloxane bonds and the formation of hydroxyl groups, strongly decreasing the activation energy of the Arrhenius-type temperature dependence of the viscosity. The link between the breakage of siloxane bonds, viscous flow, and hydroxyl content in silica glass was supported by more recent work (CitationMalfait and Halter 2008; Goller et al. 2009). A similar effect was attributed to the presence of chlorine, leading to an approximate antiproportional dependence of viscosity on the mass fraction of water or chlorine (Hetherington et al. 1964).
The use of viscosity data provided by CitationKingery et al. (1976) in the work of CitationXiong et al. (1993) disregarding the influence of water leads to a gross underprediction of the sintering velocity in the temperature range below 1600°C.
FIG. 1 Experimental setup to study the influence of the water concentration of the carrier gas on the sintering process of SiO2 nanoparticles.
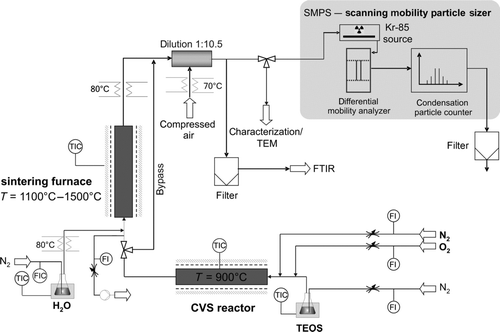
However, the use of Hetherington's data by CitationEhrman et al. (1998) also failed to deliver a model consistent with the experimental results. In this case, differences in the particle size between the experiments and a size dependence of the viscosity were assumed. This assumption was supported later by the work of CitationTsantilis et al. (2001), who again stated an underprediction of the sintering of silica in flames for primary particles in the lower single digit nanometer size range. The influence of the water content of the gas atmosphere during sintering as described for bulk materials (CitationHetherington et al. 1964) can also be expected to have an even stronger effect on nanoscale silica due to the large specific surface area. Other mechanisms of sintering such as surface diffusion may also play a role in agglomerates of amorphous silica agglomerates. In the initial stage of sintering however, when the primary particle size is only 4 nm and with a size of the monomeric silica tetrahedra of 0.4 nm (CitationEhrman 1999), the diffusion of OH within the solid, a mechanism assumed even for bulk glass melts (Goller et al. 2009), will certainly be rapid enough to influence viscosity throughout the particle and not only in a surface layer. The adsorption of water and the formation of terminating hydroxyl groups reduce the surface free energy and have been measured and simulated by different authors (CitationMurashov and Demchuk 2005; CitationPeng et al. 2009; CitationAl Akoum et al. 2010) and may have several effects. Considering the sinter mechanism of the particles, the driving force for coalescence, following the Koch and Friedlander (1990) model, would be lowered, potentially leading to a reduction of the sintering velocity. Since the cited literature mainly concentrates on the effects on the adsorption of desired molecules for subsequent functionalization in liquid phase processes and reliable data on the influence of the hydroxyl concentration on the surface energy and sintering of silica nanoparticles do not exist to the best of our knowledge, the extent of this effect remains unclear.
Apart from the influence of the gas atmosphere and the primary particle size, the agglomerate structure also influences the characteristic sintering time (CitationSchwade and Roth 2003; CitationKirchhof et al. 2009). Therefore, the comparison of existing experimental data to extract the influence of the gas atmosphere alone is inconclusive.
In flame synthesis (CitationPratsinis 1998) and gas-dynamically induced particle synthesis (CitationGrzona et al. 2009; CitationGoertz et al. in press, Kingery et al. 1976), methane is frequently used as the burning gas yielding water vapor as a reaction product. Hence, particle growth in most gas phase syntheses processes for nanopowders takes place in the presence of water vapor. The understanding of structure formation in these processes thus requires knowledge regarding the influence of water vapor concentration on the sintering of nano-sized particles. Surprisingly, however, there is no systematic investigation of this matter to this day.
The aim of this work is thus a first aerosol-based experimental investigation of the influence of the water vapor concentration of the carrier gas on the sintering process of SiO2 nanoparticles. Aerosol methods allow the synthesis and the sintering of the particles directly in-line, excluding exposure to ambient air, and the on-line and real-time characterization of structural changes.
2. EXPERIMENTAL
The setup used in the experiments is shown in . In a hot-wall aerosol reactor, the formation of silica nanoparticles by chemical vapor synthesis (CVS) takes place. In a second tube furnace directly in line with the reactor, sintering under variation of the water concentration of the carrier gas is studied.
Upstream of the first furnace, nitrogen (50 mL/min, Air Liquide, 99.99%) passes a bubbling system (water bath temperature 60°C), from where tetraethyl orthosilicate (TEOS) is transferred into the gas phase. In addition, the CVS reactor (T = 900°C, heated length 500 mm, d i = 19 mm) receives another nitrogen flow (500 mL/min) mixed with oxygen (60 mL/min, Air Liquide, 99.5%) for the oxidation reaction of the TEOS. The mean residence time in the CVS reactor is τ = 5.0 s under the given process conditions. In the CVS reactor, amorphous SiO2 aggregates with a primary particle size of 5.7 nm (geometric standard deviation of 1.2) are formed (). The synthesis conditions were kept constant in all experiments, such that the material used for subsequent analyses was always identical.
Before the aerosol flow enters the sintering furnace (Gero Hochtemperaturöfen GmbH, HTRV 70-715/16, heated length 750 mm, d i = 19 mm), a flow of 500 mL/min is branched off downstream of the CVS reactor and an equal flow of dry or humidified nitrogen is fed in further downstream. Water is introduced into the gas phase using a bubbling system again. The water bath temperature of the water bubbling system is set to 20°C and 60°C to adjust the water content in the carrier gas. To prevent water condensation, all lines downstream of the water bubbler are heated electrically to 80°C. In addition to that, the aerosol is diluted by the given ratio to avoid condensation on transmission electron microscopy (TEM) grids and in the scanning mobility particle sizer (SMPS) system. In the individual experiments, the sintering temperature was varied between 1100°C and 1500°C. The residence time depends on the process conditions selected and was experimentally determined to values of τ = 27.1 s and τ = 23.5 s at a sintering temperature of 1100°C and 1500°C, respectively.
FIG. 3 FTIR absorbance spectra of the particle filtered gas streams entering the sintering furnace before mixing. The lower black line presents the spectra resulting from TEOS decomposition at 900°C. The middle and upper black lines represent the spectra of added nitrogen loaded with water at a bubbler temperature of 20°C and 60°C, respectively.
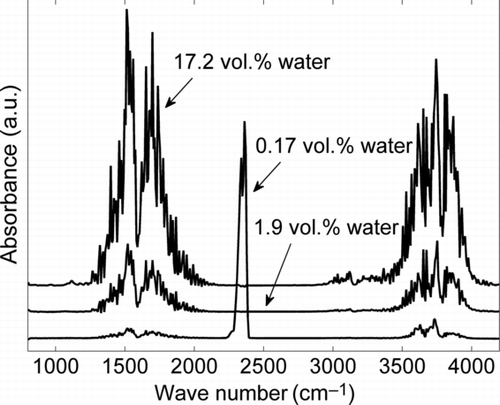
The water concentration of the carrier gas was measured by Fourier-transform infrared spectrometry (FTIR, ansyco GASMET DX2000). Calibration of the FTIR spectrometer was performed by a dew-point mirror hygrometer.
The structural changes of the silica agglomerates were monitored on-line by an SMPS (TSI DMA 3071A & TSI CPC 3775) and by sampling particles for TEM analysis (Philips CM12 120 keV) using a low-pressure impactor.
3. RESULTS AND DISCUSSION
3.1. Sintering of Silica Nanoagglomerates in Dry Air
To assess the impact of the water concentration of the carrier gas on the sintering process, a study of the sintering of SiO2 nanoparticle agglomerates in nearly dry air is prerequisite. Therefore no additional water vapor was added, but the water resulting from the TEOS decomposition remains in the gas phase, as shown in . The characteristic peak pattern for water vapor is clearly visible at 1300–1900 cm−1 and 3500–4000 cm−1. However, the FTIR absorbance spectra of the gas streams entering the sintering furnace show that the water amount resulting from TEOS decomposition (0.17 vol.%) is negligible in comparison to the additionally added water vapor (1.9 vol.% and 17.2 vol.%) for the experiments discussed in Sections 3.2 and 3.3. The additional peak at 2300 cm−1 in the spectra for TEOS decomposition (lower black line) belongs to CO2, resulting from the complete decomposition of TEOS in the oxygen–nitrogen mixture. No silica-related peaks could be observed in the spectra, because a high efficiency particulate air (HEPA) filter was placed before the FTIR to avoid deposition in the chamber. The initial size distribution and a TEM image of the particles generated in the CVS-process are displayed in . summarizes the structural changes indicated by the mobility equivalent diameter (from SMPS) and the primary particle size (from TEM) found for sintering temperatures between 1100°C and 1500°C. The first data points in the diagram represent the particle sizes and the number concentration of the freshly generated particles, upstream of the sintering furnace. The increased mobility diameter d M and the smaller particle number concentration c N at 1100°C, in comparison to the initial aerosol characteristics, are caused by the progressing coagulation of agglomerates in the sintering furnace, leaving the primary particle size unaffected. With increasing sintering temperature, however, an increase in the primary particle diameter can be detected, indicating coalescence of the SiO2 particles. As the viscosity of SiO2 decreases with increasing temperature, the coalescence time needed for particle growth is reduced as well. Up to 1400°C, the aggregate structure hardly changes. This is reflected by a nearly constant mobility diameter of the SiO2 aggregates downstream of the sintering furnace between 1100°C and 1400°C (). At 1500°C, SiO2 starts to form more compact structures and a strong increase of the primary particle diameter can be observed. However, the residence time of τ = 23.5 s is not sufficient for the SiO2 to sinter to completely spherical particles () in a dry gas atmosphere.
FIG. 5 TEM images of SiO2 nanoparticles downstream of the sintering furnace as a function of the sintering temperature T S and the water concentration of the carrier gas in the sintering furnace.
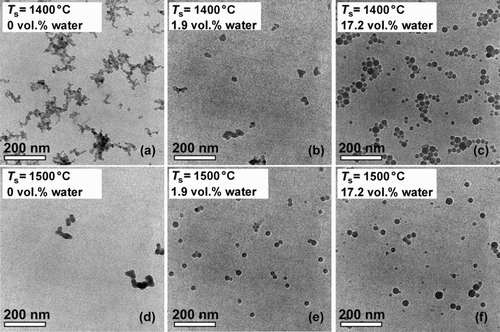
TABLE 1 Impact of the water concentration of the carrier gas on the aggregate structure when adding water vapor upstream of the sintering furnace
3.2. The Influence of Increased Water Vapor Concentration on the Sintering of Silica Nanoparticles
The influence of increased water concentration of the carrier gas on the sintering process was studied at two different water concentrations of 1.9 and 17.2 vol.%. Again, the sintering temperatures were varied from 1100°C to 1500°C. The aggregate structures obtained under these conditions are listed in . Representative TEM images of the SiO2 particles generated at 1400°C and 1500°C as a function of the water concentration of the carrier gas are shown in . At 1100°C and 1200°C, no restructuring of the aggregates can be detected at both water vapor concentrations. At a sintering temperature of 1300°C, first individual spherical, nonaggregated particles can be observed along with persisting aggregate structures at a water concentration of 17.2 vol.%. The same applies to 1400°C and a water concentration of 1.9 vol.% (). If the water concentration at 1400°C is increased to 17.2 vol.%, only spherical, nonaggregated particles exist (). At 1500°C, spherical, nonaggregated particles are found at both water concentrations of the carrier gas ( and f). The more pronounced restructuring of the particles at 1500°C and 1.9 vol.% water () compared with particles at 1400°C and 1.9 vol.% () can be explained by the lower viscosity of the SiO2 particles at higher temperatures and the corresponding decrease of τ.
TABLE 2 Median and geometric standard deviation of primary particle size distributions (lognormal fit) of silica agglomerates, sintered at 1400°C with different water concentrations in the carrier gas
FIG. 7 Influence of the water concentration of the carrier gas on the SMPS mobility size distributions downstream of the sintering furnace at T S = 1400°C.
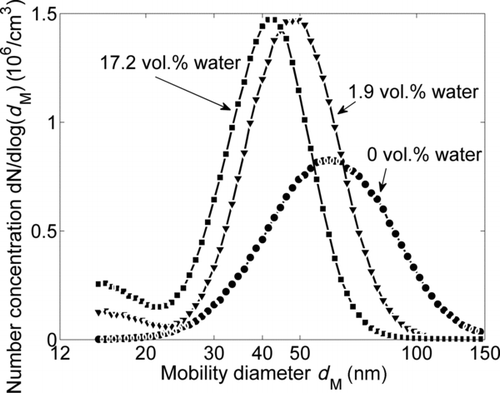
It is demonstrated by these observations that the presence of additional water in the carrier gas has a considerable influence on sintering kinetics. While all sintering temperatures and the respective residence time in the sintering furnace in dry air yielded aggregated structures only, the presence of additional water led to individual nanoparticles at 1300°C already. Hence, water reduces the sintering time needed for complete coalescence of particles in agreement with the findings for bulk materials (CitationHetherington et al. 1964; CitationLeko et al. 1973).
3.3. Effect of Increased Water Vapor Concentration on the Particle Size During Sintering
To assess the influence of increased water concentration in the carrier gas on the particle size during sintering, the size distributions of both the primary particles and the mobility diameters have to be considered.
Primary particle size distributions, approximated by lognormal distributions, determined downstream of the sintering furnace at 1400°C are shown in . The median values of the primary particle size distribution and the geometric standard deviation are given in . The increase in the primary particle diameter can be explained by the coalescence of the particles and again reflects the acceleration of sintering kinetics in the presence of additional water (Section 3.1). It can also be noticed that the primary particle size distribution broadens with increasing water concentration of the carrier gas.
The mobility diameter distributions measured with the SMPS at 1400°C are represented in with the water concentration as a parameter. As described above, an increased water concentration eases the restructuring of the agglomerates and the coalescence of the primary particles leading to a reduced mobility diameter. The increase in the particle number concentration in the presence of water can only be explained by evaporation and condensation processes, indicated by the formation of a small nuclei mode in the range of 15 nm (). This effect is more dominant for the higher water concentration but is still not sufficiently strong to be reflected in the primary particle size distribution (), which is dominated by the growth due to coalescence of the primary particles in the aggregates.
FIG. 8 Influence of the water concentration of the carrier gas on the primary particle size distributions downstream of the sintering furnace at T S = 1500°C, determined by TEM image analysis.
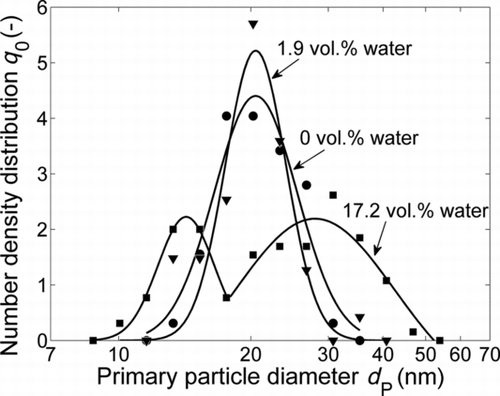
TABLE 3 Median and geometric standard deviation of primary particle size distributions (lognormal fit) of silica agglomerates, sintered at 1500°C with different water concentrations in the carrier gas
The formation of new particles is even more distinct at 1500°C. shows the primary particle size distributions at this temperature with the water concentration of the carrier gas as a parameter. In contrast to the results at 1400°C, no growth of the primary particle diameter can be observed at 1500°C when increasing the water concentration from 0 to 1.9 vol.% as shown in . However, the particle structure and morphology change quite dramatically under these conditions, as can be seen in and e, and also in the mobility diameter (). Therefore it is clear that not only restructuring and sintering of the agglomerates take place, but also additionally evaporation and condensation processes occur. The occurrence of evaporation and condensation is also confirmed again by the existence of a nuclei mode in the mobility distribution (). When increasing the water concentration to 17.2 vol.%, this effect is so dominant that a bimodal primary particle size distribution evolves (). The median values, resulting from two overlapping lognormal fits, are 14.3 and 27.8 nm ().
FIG. 9 Influence of the water concentration of the carrier gas on the SMPS mobility size distributions downstream of the sintering furnace at T S = 1500°C.
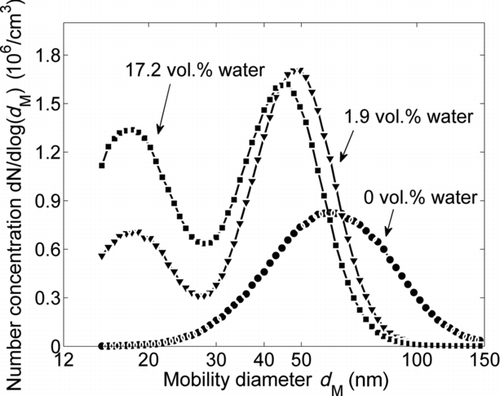
The evaporation and recondensation of silica were observed before. CitationWidiyastuti et al. (2009) used a methane flame to transform micron-sized silica particles into nanoagglomerates. Their experimental work was supported by modeling results by using solid evaporation and gas-to-particle conversion in the flame for the particle formation mechanism. CitationOpila et al. (1997) identified the gaseous reaction products from the decomposition of silica in water vapor at atmospheric pressure as Si(OH)4 and SiO(OH)2 using mass spectroscopy. The formation of volatile Si(OH)4 increases with increasing water vapor partial pressure.
The evaporation of silica observed in our experiments might be explained by the observations of CitationHetherington et al. (1964) discussed earlier, where the disintegration of silanol bonds and the weakening of the silica matrix were observed. Under extreme conditions regarding temperature and water vapor concentration, this process could lead to the formation of vaporous species like Si(OH)4 or SiO(OH)2. The formation of new particles then occurs when the aerosol is cooled off leaving the furnace.
4. CONCLUSIONS
It could be shown that the water concentration of the carrier gas has a significant influence on the structure of SiO2 nanoagglomerates during sintering. Beyond the considerable acceleration of coalescence, the formation of condensable species in the presence of water at high temperatures, leading to the generation of new particles, is a remarkable finding of these experiments.
The observed effects on sintering kinetics should therefore not to be neglected in theoretical work describing systems where water vapor is present. In product design for nanoscale silica powders, water concentration could also be an interesting parameter for the manipulation of the particle structure in synthesis processes. For both theory and application, however, more detailed studies on the nature of the discovered phenomena is needed.
ACKNOWLEDGMENT
We acknowledge the financial support from the Deutsche Forschungsgemeinschaft (DFG, no. PAK 75).
REFERENCES
- Al Akoum , R. , Vaulot , C. , Schwartz , D. , Hirn , M. P. and Bassel , H. 2010 . How Silanization of Silica Particles Affects the Adsorption of PDMS Chains on its Surface . J. Polym. Sci. Pt. B—Pol. Phys. , 48 ( 22 ) : 2371 – 2378 .
- Barna , E. , Bommer , B. , Kürsteiner , J. , Vital , A. , Trzebiatowski , O. v. , Koch , W. , Schmid , B. and Graule , T. 2005 . Innovative, Scratch Proof Nanocomposites for Clear Coatings . Compos. Pt. A—Appl. Sci. Manuf. , 36 : 473 – 480 .
- Ehrman , S. H. 1999 . Effect of Particle Size on Rate of Coalescence of Silica Nanoparticles . J. Coll. Interf. Sci., , 213 : 258 – 261 .
- Ehrman , S. H. , Friedlander , S. K. and Zachariah , M. R. 1998 . Characteristics of SiO2/TiO2 Nanocomposite Particles Formed in a Premixed Flat Flame . J. Aerosol Sci. , 29 : 687 – 706 .
- Frenkel , J. 1945 . Viscous Flow of Crystalline Bodies Under the Action of Surface Tension . J. Phys. (U.S.S.R.) , 9 : 385 – 391 .
- Goertz , V. , Korp , D. , Al-Hasan , N. , Giglmaier , M. and Nirschl , H. 2011 . Experimental Study of Gas-Dynamically Induced Nanoparticle Synthesis by Use of Adapted Sampling Probes . Chem. Eng. Process , (in press) doi: 10.1016/j.cep.2011.05.007
- Goller , D. D. , Philipps , R. T. and Sayce , I. C. 2009 . Structural Relaxation of SiO2 at Elevated Temperatures Monitored by in situ Raman Scattering . Journal of Non-Crystalline Solids , 355 : 1747 – 1754 .
- Grzona , A. , Weiss , A. , Olivier , H. , Gawehn , T. , Gülhan , A. , Al-Hasan , N. , Schnerr , G. H. , Abdali , A. , Luong , M. , Wiggers , H. , Schulz , C. , Chun , J. , Weigand , B. , Winnemöller , T. , Schröder , W. , Rakel , T. , Schaber , K. , Goertz , V. , Nirschl , H. , Maisels , A. , Leibold , W. and Dannehl , M. 2009 . Gas-Phase Synthesis of Non-Agglomerated Nanoparticles by Fast Gasdynamic Heating and Cooling . : 857 – 862 . in Shock Waves, 26th International Symposium on Shock Waves (Vol. 2)
- Hetherington , G. , Jack , K. H. and Kennedy , J. C. 1964 . The Viscosity of Vitreous Silica . Phys. Chem. Glasses , 5 : 130 – 136 .
- Kingery , W. D. , Bowen , H. K. and Uhlmann , D. R. 1976 . Introduction to Ceramics , Springer-Verlag . Hannemann, K., and Seiler, F., eds.
- Kirchhof , M. , Schmid , H.-J. and Peukert , W. 2009 . Three-Dimensional Simulation of Viscous-Flow Agglomerate Sintering . Phys. Rev. E , 80 : 026319
- Koch , W. and Friedlander , S. K. 1990 . The Effect of Particle Coalescence on the Surface Area of a Coagulation Aerosol . J. Colloid Interface Sci. , 140 : 419 – 427 .
- Kruis , F. E. , Kusters , K. A. , Pratsinis , S. E. and Scarlett , B. 1993 . A Simple Model for the Evolution of the Characteristics of Aggregate Particles Undergoing Coagulation and Sintering . Aerosol Sci. Technol. , 19 : 514 – 526 .
- Lehtinen , K. E. J. , Windeler , R. S. and Friedlander , S. K. 1996 . Prediction of Nanoparticle Size and the Onset of Dendrite Formation Using the Method of Characteristic Times . J. Aerosol Sci. , 27 : 883 – 896 .
- Leko , V. K. , Meshcheryakova , E. V. , Gusakova , H. K. and Lebedeva , P. B. 1973 . The Effect of Some Factors on the Viscosity of Vitreous Silica . Steklo i Keramika , 8 : 16 – 18 .
- Malfait , W. and Halter , W. E. 2008 . Structural Relaxation in Silica Glasses and Melts: High-Temperature Raman Spectroscopy . Phys. Rev. B , 77 : 014201
- Mueller , R. , Kammler , H. K. , Pratsinis , S. E. , Vital , A. , Beaucage , G. and Burtscher , P. 2004 . Non-Agglomerated Dry Silica Nanoparticles . Powder Technol. , 140 : 40 – 48 .
- Murashov , V. V. and Demchuk , E. 2005 . Surface Sites and Unrelaxed Surface Energies of Tetrahedral Silica Polymorphs and Silicate . Surf. Sci. , 595 ( 1–3 ) : 6 – 19 .
- Muriel , M. , Dubault , A. and Halary , J. L. 2007 . Plastic and Fracture Behavior of Nanosilica-Filled Poly(methyl methacrylate) . Polym. Int. , 56 : 214 – 223 .
- Opila , E. J , Fox , D. S. and Jacobson , N. S. 1997 . Mass Spectrometric Identification of Si-O-H (g) Species of Silica with Water Vapor at Atmospheric Pressure . J. Am. Ceram. Soc. , 80 : 1009 – 1012 .
- Peng , L. , Qisui , L. and Chaocan , Z. 2009 . The Molar Formation Enthalpy of Nano-SiO2 with Different Surface Area . J. Therm. Anal. Calorim , 95 ( 2 ) : 667 – 670. .
- Pratsinis , S. E. 1998 . Flame Aerosol Synthesis of Ceramic Powders . Prog. Energy Combust. Sci. , 24 : 197 – 219 .
- Sander , M. , West , R. H. , Celnik , M. S. and Kraft , M. 2009 . A Detailed Model for the Sintering of Polydispersed Nanoparticle Agglomerates . Aerosol Sci. Technol. , 43 : 978 – 989 .
- Schwade , B. and Roth , P. 2003 . Simulation of Nano-Particle Formation in a Wall-Heated Aerosol Reactor Including Coalescence . J. Aerosol Sci. , 34 : 339 – 357 .
- Tsantilis , S. , Briesen , H. and Pratsinis , S. E. 2001 . Sintering Time for Silica Particle Growth . Aerosol Sci. Technol. , 34 : 237 – 246 .
- Ulrich , G. D. 1971 . Theory of Particle Formation and Growth in Oxide Synthesis Flames . Combust. Sci. Technol. , 4 : 47 – 57 .
- Ulrich , G. D. 1984 . Flame Synthesis of Fine Particles . Chem. Engng. News , 62 : 22 – 29 .
- Ulrich , G. D. and Subramanian , N. S. 1977 . Particle Growth in Flames. III. Coalescence as a Rate-Controlling Process . Combust. Sci. Technol. , 17 : 119 – 126 .
- Widiyastuti , W. , Purwanto , A. , Wang , W. N. , Iskandar , F. , Setyawan , H. and Okuyama , K. 2009 . Nanoparticle Formation Through Solid-Fed Flame Synthesis: Experiment and Modeling . AIChE J , 55 : 885 – 895 .
- Xiong , Y. , Akhtar , M. K. and Pratsinis , S. E. 1993 . Formation of Agglomerate Particle by Coagulation and Sintering—Part II. The Evolution of the Morphology of Aerosol-Made Titania, Silica and Silica-Doped Titania Powders . J. Aerosol Sci. , 24 : 301 – 313 .
- Xiong , Y. and Pratsinis , S. E. 1993 . Formation of Agglomerate Particle by Coagulation and Sintering—Part I. A Two-Dimensional Solution of the Population Balance Equation . J. Aerosol Sci. , 24 : 283 – 300 .