Abstract
The aim of this study was to achieve a method to perform detailed characterization and human exposure studies of nanosized and nanostructured aerosol particles. The source chosen was mild steel, active gas, arc welding fume. The setup consisted of a generation chamber, where welding can be performed, connected to an airtight stainless steel 22 m3 exposure chamber. Instrumentation, consisting of a tapered element oscillating microbalance, a scanning mobility particle sizer, and a sampler for electron microscopy and particle-induced X-ray emission analysis was connected to the stainless steel chamber. The feasibility of the system for human exposure studies was evaluated by exposing 31 human volunteers, in groups of three, to a test aerosol containing 1 mg/m3 welding fumes and to conditioned, filtered air. The results show that an aerosol that accurately represents dilute welding fume exposures that occur in workplaces can be produced in a controlled manner, and that the experimental setup can be used for 6 h, double-blind, exposures of human subjects. Particle mass concentration levels could be varied from <5 μg/m3 to more than 1000 μg/m3. Fumes from metal active gas welding showed a unimodal size distribution with a mean mobility diameter of 160 nm, transmission electron microscopy showed aggregates with a clearly nanosized structure.
Copyright 2013 American Association for Aerosol Research
1. INTRODUCTION
The objectives of this research were to design a system for controlled characterization and human exposure studies of nanosized/nanostructured airborne particles from thermal processes, occurring in industrial workplaces, and to validate the system by comparison to real workplaces where welding occurs.
Numerous studies indicate that there is a correlation between exposure to airborne particles and health problems (Pope et al. Citation2002; Li et al. Citation2003; Brook and Rajagopalan Citation2010). People spend a major part of their time in the workplace, so the health effects of particle exposures in these environments are of special interest. Airborne nanosized (having one dimension <100 nm) and nanostructured particles are of particular concern, since their health effects and the mechanisms driving these effects are not fully understood (Gil et al. Citation2010). Some studies, though, provide a basis for better theoretical understanding of their exposure, uptake, and kinetics. A strong hypothesis is that the relatively large particle number and surface area per unit mass of these particles are likely to decrease the ability of the macrophages to phagocytose them, and increase their uptake by epithelial cells. The particles can, hence, end up in the interstitium and cause inflammation there (Donaldson et al. Citation1998). Comparing the inflammogenicity of carbon black with ultrafine carbon black when instilled into rat lungs, Brown et al. (Citation2000) found that the ultrafine carbon black particles induced more inflammation and suggested that the difference may be accounted for by increased surface area or particle number. Kreyling et al. (Citation2002) showed translocation of radiolabeled iridium particles (15 and 80 nm) within a week after inhalation to systemic circulation and liver, spleen heart, and brain in rats. The translocated fraction was one order of magnitude larger for the 15 nm particles than for the 80 nm particles. An inhalation study, using rats, by Oberdorster et al. (Citation2004) showed increasing particle levels of 36 nm 13C particles in the olfactory bulb throughout a 7-day postexposure period indicating that uptake via sensory nerve endings constitutes a clearance pathway to the central nervous system. Oberdorster et al. (Citation2011) also showed particle translocation to the blood compartment from the GI-tract of whole-body exposed rats. The cardiovascular effects of inhalation of nanosized particles have been studied by Pekkanen et al. (Citation2002), this study found a correlation between ultrafine particulate air pollution and ST segment depression during exercise (indicating increased risk of myocardial ischemia) in human test subjects.
There is a long tradition of exploring the health effects of dusts and fumes in industrial environments. Most exposure measurements in these studies, as well as threshold limit values, have been based on mass concentrations. Very often the mass of nanoparticles is insignificant compared to the mass of coarse particles in industrial workplaces, yet there can be very high number concentrations of nanosized and nanostructured particles present. There is an ongoing debate on what metric is most relevant for assessment of exposure risk. In addition to number concentration, size, shape, surface area, and composition are examples of measurable parameters which can be assumed to influence particle toxicity (Warheit et al. Citation2007; Trout and Schulte Citation2010). As the development of new instruments to analyze nanoparticles progresses, more extensive studies of nanoparticles in the workplace are becoming possible. Renewed study of these environments and exposures, using modern instrumentation, can give us better knowledge of the health effects of specific aerosol properties and characteristics. There is a need for well-designed toxicological studies of fine (<2.5 μm) and ultrafine (<100 nm) particle exposure in humans.
Welding is a major source of fine and ultrafine particles in working environments worldwide. In the United States, alone there are nearly 0.5 million people performing welding and cutting operations full-time, and an additional 1–2 million workers who weld intermittently (Jenkins Citation2003). In Europe 837,000 people work as full-time welders and 1 million more weld intermittently (Björn Hedlund 2011, General Manager of European Welding Association (EWA), personal communication). The total amount of smoke emitted from the welding industry worldwide is estimated to 5000 tons/year (Redding Citation2002). Very high exposure concentrations can be obtained when welding; levels of several mg/m3 are not uncommon as averages for personal exposures over a workday. Furthermore, particles from welding processes are enriched with metal oxides, which are potentially toxic. The significance of welding particles as examples of large-scale exposure to nanosized particles has previously been demonstrated by Bohgard et al. (Citation1979) where clear indications of particles from shielded metal arc welding washed with buffered water solution show disintegration of the agglomerates into numerous metal-containing “free” nanoparticles.
Welding fume particles are formed when molten metal at the end of an electrode emits vapor that mixes with the shield gas and is transported from the arc temperature of well above 3000 K (boiling point of iron) to room temperature (Jenkins Citation2003). Particles nucleate and grow by condensation to form primary particles (0.01–0.10 μm) followed by growth through coagulation. As the temperature of the plume decreases, the welding fume particles quickly form complex, chain, aggregates between 100 and 300 nm in length. The variations in both primary particle size and aggregate size can be large (Jenkins Citation2003).
The most frequently used welding methods are shielded metal arc welding (SMAW) and gas metal arc welding (GMAW). The latter can be divided in metal inert gas (MIG) and metal active gas (MAG), depending on the composition of the shielding gas. By creating a microclimate around the welding point, a flux or gas protects the molten metal from oxidation, thus shielding it from the oxygen in the surrounding atmosphere. The type of shielding gas depends on the substrate. However, a welding process is often optimized by using a mixture of the two types of gases (active and inert). The composition of the electrode is matched to that of the substrate, so that a welding joint with mechanical properties similar to the substrate is obtained. It has been shown that fume composition is reasonably independent of the substrate material itself and that the welding fumes are mainly composed of species from the electrode material (Antonini et al. 2006). The substrate seems to influence the fume composition only if covered with oil, paint, or any similar substance (Quimby and Ulrich 1999).
The emerging applications of nanotechnology require precautions with respect to inhalable nanosized and nanostructured particles. Some industrial processes, including welding, create air borne nanoparticles (Tabrizi et al. Citation2010). Particles from industrial environments like welding workplaces can be used to increase the understanding of toxicological mechanisms and in risk analysis.
2. THE METHODOLOGY
The methodology developed for this study can be divided into three parts: (i) measurement of welding fume aerosol in real world workplace environments and literature review, (ii) generation of an aerosol with similar properties in controlled laboratory settings, and (iii) creation of a chamber environment suitable for controlled characterizations and human exposure studies.
The study was approved by the local ethics committee according to the declarations of Helsinki and an informed consent was obtained from all subjects prior to exposure.
2.1. Aerosol Characterization in Workplaces
Welding aerosols were characterized by conducting extensive measurements in three welding workshops in the south of Sweden. A wide range of measurement instruments were used, described in detail in Isaxon et al. (Citation2009). Samples were taken at two different points in each of the workshops. The first sampling point was at a 2 m height, at least 5 m distance from the nearest known source of fine and ultrafine particles, using a PM10 inlet. The purpose of this was to sample the workshop background air. The second sampling point was in a freshly generated welding plume at a distance of 5–20 cm above the welding point using a sampling probe immediately connected to a two-stage ejector dilution system. These in-plume measurements provided the signature size distribution and composition of GMAW fumes. With these measurements, the mass and number concentrations, size distribution, and chemical composition in both the welding plume and in the background air were defined.
From the workplace measurements, it was found that welding and other activities were executed for periods of nonuniform length and frequency; hence, background concentrations fluctuated considerably during a workday. PM10 mass concentration in the background zone during working hours could typically vary throughout the day between 100 μg/m3 during periods of low activity to 3000 μg/m3 or above during intense periods. Average mass concentrations of 1–3 mg/m3 were common. The respirable dust, measured for selected welders by personal filter samplers (with a 50% cut-off at 4 μm) placed in the breathing zone, varied between 0.6 and 3.4 mg/m3. In particle-induced X-ray emission (PIXE) analysis of impactor samples, MAG welding typically showed a unimodal size distribution with a mass median aerodynamic diameter of around 200 nm (Isaxon et al. Citation2009). Chemical analysis showed that the elemental particle composition was dominated by iron, while the manganese fraction increased with size, suggesting that manganese condenses onto existing particles at lower temperatures in the formation process (Isaxon et al. Citation2009). Further, the fraction of nickel and chromium were very low, as expected for welding in mild steel.
2.2. Choice of Particle Concentrations for Controlled Exposure Studies
The welding fume generated by MAG welding in mild steel consists, in the size range between 150 and 500 nm, of approximately 20% (mass) of manganese (Isaxon et al. Citation2009). Manganese is toxic and has been linked to impaired motor skills and cognitive disorders. High exposure to airborne manganese has been shown to cause a form of neurodegeneration similar to Parkinson's disease called “manganism” among people working with metallurgical processes (Crossgrove and Zheng Citation2004). In Sweden, the 8 h occupational threshold limit value for manganese is 100 μg/m3. The target welding fume mass concentration for the human exposure study was set to 1000 μg/m3 as a mean which is equivalent to a manganese concentration of 85 μg/m3 for the selected electrode and welding technique.
2.3. Aerosol Generation for Human Exposure Studies
A laboratory generation system for welding fumes was developed using a welding system frequently utilized in the welding industry (Kemppi, Kempomig 350, Lahti, Finland) with a 1 mm electrode (ESAB, Aristorod 12.50, Gothenburg, Sweden), which is one of the most commonly used electrodes from this manufacturer for mild steel welding. The nozzle feeding rate was 3 cm/s. This electrode has relatively high levels of manganese and silicon (1.2% and 0.7%, respectively), making it useful for welding on clean mild steel but also for welding over moderate to high levels of rust and mill scale. As shielding gas an Ar/CO2 mixture (82% Ar, 18% CO2) (Air Liquide, Arcal MAG, Paris, France) at a flow rate of 12 lpm was used. Mild steel was chosen as the welding substrate because it is commonly used in the industry. Welding was performed at 125 A, 5.5 V. To create an average fume particle concentration of 1000 mg/m3, a welding pulse of 3 min was generated followed by a nonwelding period of 20 min. This kind of nonuniform exposure resembles real-life work situations. Continuous monitoring and averaging of the mass concentration with a custom-built computer program (written in Labview, version 8.2, National instruments, Austin, TX, USA) made it possible to increase or decrease the welding time of each welding pulse, and the pulse frequency, toward the desired mean concentration. The person performing the welding was trained by a professional welder. Welding was conducted in straight lines at a uniform pace. Care was taken not to let the welding joints cross each other, so that welding was always carried out on a clean mild steel surface.
The aerosol was generated in a 1.33 m3 chamber made of glass and stainless steel (bottom surface area 0.81 m2) placed in an adjacent room. An inlet for clean pressurized air, filtered by a high efficiency particle arrestor (HEPA) filter and an active carbon filter was placed in the bottom to provide a steady controlled flow through the generation volume. Welding fumes were captured by an extractor hood placed directly above (0.3 m) the aerosol source with an inlet area of 0.39 m × 0.16 m. The hood was connected to a copper pipe, 3 cm in diameter and 8.25 m in length, through which the aerosol by means of an air amplifier (Coval, M10C, Raleigh, NC, USA) was transported into the chamber. Pressurized air was injected in the amplifier, perpendicular to the aerosol flow. An air amplifier is constructed such that the pressurized airflow bends 90° to follow the interior surface of the amplifier (due to the Coanda effect), and thus creates a low pressure area in the amplifier volume. The low pressure entrains the aerosol and produces high velocity outlet flows. The amplifier drew 400 lpm of aerosol from the generation volume and delivered 500 lpm after dilution with filtered pressurized air at 4 Bar (400 kPa) of operating pressure. These flow rates could be varied by adjusting the operating pressure of the air amplifier. A muffler was placed after the air amplifier, just prior to the chamber inlet, so that the sound of the amplifier would not reveal if it was particle exposure or blank at a given exposure event. The welding fume was further diluted by air from the conditioning system (described in the next section) before entering the exposure chamber. The extractor hood and air amplifier were used to keep the residence time of the aerosol in the generation system at a minimum (approximately 2 s). By this, aerosol dynamic processes, mainly coagulation that easily occurs with high number concentrations and long residence time, could be avoided. Coagulation alters the number size distribution toward larger and fewer particles, neither of which is desired in these exposure experiments. In principle, efforts were made to achieve a dilution process (residence time and dilution ratio) relevant for that occurring in realistic industrial environments when the fume travels from generation point to breathing zone. A cyclone was placed just prior to the dilution of welding fume with air from the air conditioning unit, downstream the air amplifier, in order to avoid release of particles deposited in pipe bends and in the amplifier itself into the chamber. Such mechanically generated particles would mostly be larger than 2–3 μm, and are not desirable in the exposure chamber. The initial relative concentration fluctuations extracted from the hood could be monitored with an optical aerosol instrument (TSI, DustTrak 8520, Shoreview, MN, USA). By opening a valve in the extractor hood, the concentration of aerosol transported out of the generation volume could be varied. The generation volume was protected from contamination from the surrounding air by a hatch, which was kept closed at all times, except when welding was conducted. Calculations show that particles from ambient air that may leak into the generation volume during welding contributed to the exposure chamber particle concentration by less than 0.2 μg/m3.
The mean residence time of the diluted fume in the exposure chamber was 10 min (due to an air exchange rate of 5.8/h) and, therefore, the exposure is most relevant for relatively fresh background aerosol at a workplace.
2.4. The Exposure Chamber
The human exposure chamber () is a 21.6 m3 room where all interior surfaces except for a window of 0.8 m2 are made out of stainless steel. When the doors are closed, the system is under a slight positive pressure.
The room is entered via an antechamber (3.1 m3) with airtight doors. The chamber is supplied with air through a separate, custom-built air conditioning system by which airflow, temperature, and relative humidity are controlled. After being filtered inside the conditioning system, the chamber air supply passes through an additional activated carbon filter and an ultra-low penetration air filter, before entering the exposure chamber at roof level. The exposure aerosol is premixed with the supply air and diluted into the clean air stream just above the chamber inlet at roof level. The chamber air exhaust flow is controlled using a variable fan which is also used for achieving a desired slight overpressure (typically 10 Pa or just below) inside the chamber, to make sure no particles from the surrounding air penetrate into the chamber. When the chamber was validated (Isaxon 2008), in the absence of test subjects and at air exchange rates of approximately 4/h, trace gas measurements showed that spatial concentration gradients are less than 15% throughout the chamber volume. In the presence of test subjects, the degree of mixing improves due to thermal convection induced by the test subjects.
The chamber is suited for human exposures as well as for source characterization (Pagels et al. 2009) and aerosol transformation studies.
The conditioning system was started well before the human exposures to ensure that the chamber was filled with fresh clean air at the start of the experiment. The air exchange rate of 5.8/h was necessary to keep the CO2 level at comfortable values (not exceeding 1000 ppm) for human test subjects. The target chamber temperature was 23°C, since pilot tests with human volunteers showed that this was the temperature of highest comfort. The target RH was 25–30%, which was the range observed at the welding workplaces. Both the workplace measurements and the human exposure study took place during wintertime. Three human test subjects were in the chamber during each exposure event. The subjects were exposed while seated. The test subjects were visually monitored all the time by a medical doctor sitting outside the chamber by the window.
3. PARTICLE CHARACTERIZATION AND AIR MONITORING
During the exposures, PM2.5 particle mass concentration in the chamber was monitored with a Tapered Element Oscillating Microbalance (TEOM, Rupprecht & Patashnic Co. Inc., Albany, NY, USA), calibrated by the manufacturer, at 50°C and with a cyclone as a precollector for particles larger than 2.5 μm. The particle number concentration and mobility size distribution (10–650 nm) were measured using a Scanning Mobility Particle Sizer (SMPS) system, calibrated by polystyrene latex spheres and a reference condensation particle counter, consisting of a long column Hauke type differential mobility analyzer (DMA), with an aerosol flow rate of 0.5 lpm and a sheath airflow rate of 5 lpm and a CPC 3010 (TSI, Shoreview, MN, USA). Diffusion driers were installed in the sheath flow loop. The welding aerosol chemical composition was characterized by PIXE and X-ray energy dispersive spectroscopy (XEDS). Using a stacked filter unit (SFU), samples for PIXE analysis were collected for 260 min on 54 mm capillary pore (Nuclepore) filters at 4 lpm, with a PM2.5 cut-off. The SFU consists of two capillary pore filters connected in series, as described by Heidam (1981). The pore size in the first filter is 8 μm with high transmission of fine particles. The second filter has a pore size of 0.4 μm ensuring an effective collection of the fine particles (Pagels et al. Citation2003). At PIXE analysis, a proton beam of 2.55 MeV is focused on the 0.4 μm filter specimen, causing a vacancy in the inner shell of an atom, which put the atom in a state of high excitation. A transition to a state of lower energy quickly occurs, and a series of characteristic X-ray emission lines is obtained (Johansson Citation1989). The cross-section for the creation of an inner shell vacancy is very high using protons, and therefore the sensitivity is high—most elements except the very light ones (Z < 14) can be detected in concentrations below 1 ppb. Using an electrostatic precipitator, samples were collected for transmission electron microscopy (TEM) and XEDS onto carbon coated Cu TEM grids. The XEDS method detects characteristic X-rays, in ways similar to the PIXE method, with the difference that XEDS uses a high-energy electron beam to excite the atom. The detection limit of XEDS is around 1 atomic%, and the lightest detectable element is Be (Z = 4) (Messing Citation2011). Temperature, relative humidity (Swema Air 300, Swema, Stockholm, Sweden), and carbon dioxide levels (RI-411A, RKI Instruments, Union City, CA, USA) were monitored online in the chamber during the human exposures. The complete exposure system including welding fume generation is shown in .
4. RESULTS
illustrates how the number and mass concentrations in the chamber typically varied with time during an exposure event. The exposures started at 09:30 and finished at 16:00. The welding pulses resulted in rapid increases in particle concentration, which quickly declined, mostly due to the relatively high air exchange rate. It can be seen that the precision in peak mass and number concentration after each welding episode was within a factor of two, which illustrates a reasonable repeatability in the manual welding procedure. These concentration fluctuations are similar to what was noticed in the welding workshops.
FIG. 3 Temporal variations of number and mass concentrations in the chamber during a typical welding exposure event. During human exposures, the test subjects had lunch between 12:00 and 13:00 and no activities took place in the exposure chamber at this time.
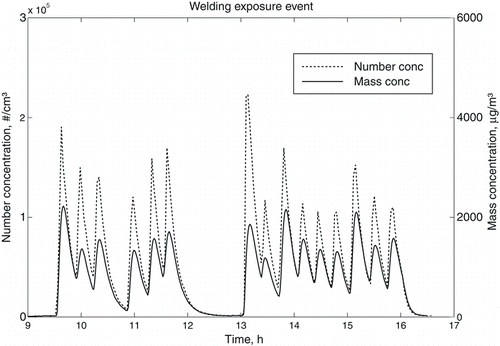
The aim to generate a mean mass concentration realistic for a workday, 1000 μg/m3, was achieved. The procedure proved to deliver reproducible results throughout the number of exposure events, as can be seen in , where the mean values are given with standard deviation showing the variations between the different exposure events. It was possible to vary the length of the pulses and their frequency so that a mean mass concentration of 1000 ± 70 μg/m3 could be maintained at every event. The number and mass concentrations as well as carbon dioxide, relative humidity, and temperature during the exposure events are shown in .
TABLE 1 Mean levels during the 13 welding exposure events
In , number size distribution of generated welding fume in the chamber and measured in the workplace is presented. The size distribution of the generated welding fume is typically a single mode with a geometric mean diameter of 160 nm. This corresponds well to what was seen at the in-plume measurements in the welding workshops (measured in a MAG welding plume) () and with what others have observed (Zimmer and Biswas Citation2001). The workshop size distribution is narrower partly because it was sampled closer to the welding point.
FIG. 4 MAG welding number distributions from laboratory and workshops. Workshop data have been normalized to fit the maximum value of the chamber number concentration. The number concentration is given as dN/dlogDp, indicating that the concentration in each size bin of the instrument has been normalized to the width of the bin.
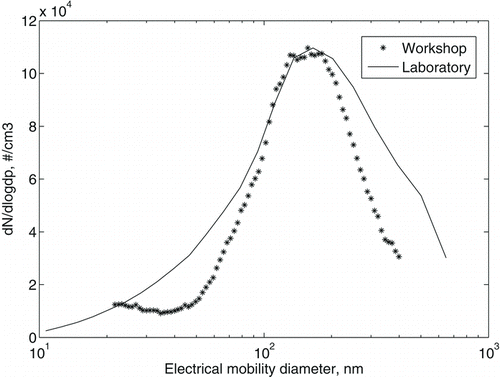
The geometric mean diameter did not vary by more than ±10 nm in-between exposure events.
shows the chemical composition of the generated welding fume compared to that measured in the plume in a welding workshop when MAG welding in mild steel was being conducted.
FIG. 5 The elemental composition in mass% measured with PIXE (elements heavier than aluminum) of welding smoke as measured in the welding workshop and during the exposure studies.
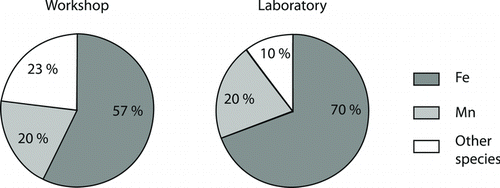
The major metal in the generated welding fume is iron. A fume fraction of 1/5 of manganese was seen in both the workshop measurements and during exposure events, and considerably larger in the fume than in the welding electrode (1.5% Mn in the Aristorod 12.50 used in the laboratory). This was likely due to the higher volatility of manganese compared to iron. In contact with the surrounding air, both iron and manganese form oxides. One can expect to find manganese in the oxidation states Mn2+ and Mn3+ and ferrous oxides such as FeO, Fe2O3, and Fe3O4 in the welding fume. The compounds among “other species” in the generated fume are summarized in .
TABLE 2 Amount of species, detectable with PIXE, other than iron and manganese in the generated welding fume
Compounds with concentrations below the PIXE detection limit were arsenic, bromine, chromium, nickel, phosphorus, rubidium, selenium, strontium, titanium, vanadium, and yttrium.
TEM images showed aggregates of varying size, composed of a few to several hundred primary particles (). The primary particle size was in the size range between 2 and 70 nm, depending on where along the temperature gradient from welding point to surrounding air they had been formed.
shows an example of the results from XEDS. In this specific image, three primary particles of different size were analyzed and found to be composed of similar proportions of oxygen, manganese, and iron.
The results of the particle characterizations also show that, despite the fact that the majority of the emitted particles are larger than 100 nm (), welding particles are agglomerates consisting of nanosize primary particles ( and ).
5. SUMMARY AND DISCUSSION
A method to perform detailed characterization and human exposure studies of nanosized and nanostructured welding fume has been developed and validated. The laboratory generated welding fumes were similar in composition and particle size distribution to the fumes measured in welding workshops. The generation method was reproducible at all exposure events throughout the duration of the study. The aimed target exposure mean concentration was obtained in each exposure event, ensuring that test subjects would be exposed to a manganese level well below the 8 h health limit value of 100 μg/m3.
The real-time instrumentation used for chamber air monitoring can give a clear overview of what the test subjects were exposed to at any given time. The SMPS system, which uses a DMA to sort particles into size bins based on their mobility in an electric field, was used primarily because there was a need for online number concentration and size distribution measurements during the human exposures. Welding fume particles are aggregated, however, sizing of particles according to their mobility diameter is expected to describe the deposition probability in the respiratory tract for the size fraction <0.5 μm, where diffusion is the dominating deposition mechanism (Rissler et al. Citation2012), which proposes an additional argument for using SMPS in human exposure studies. The SMPS data from the human exposures could, together with information of shape and primary particle size from TEM analysis and particle density, later on be used for calculating parameters other than mobility equivalent size distribution and number concentration if needed. For example, calculation of surface area of the agglomerates/aggregates as a function of mobility diameter can be done if additional characterization with an aerosol particle mass analyzer (APM) is done (as suggested by Rissler et al. Citation2012). The SMPS is frequently used in emission and exposure studies and, hence, the data from this system are valuable for comparison of results.
It is instructive to compare the mass concentration from the TEOM with the effective volume concentration from the SMPS (using the mobility size as diameter measure). From this the apparent density was found to be 1 g/cm3 for the welding aggregates, which is about half an order of magnitude lower than that of the bulk density of the expected iron oxides (5–6 g/cm3) present in the welding fume particles. Thus, a density much lower than the bulk density must be used if estimating the mass concentration from SMPS measurements of welding fumes. A similar argument holds when calculating aerodynamic diameters of the welding fume aggregates, as a density much lower than the bulk density of the material needs to be used. This effect could be seen in the workplace measurements where the mass median aerodynamic diameter (200 nm) was only marginally larger than the count median diameter of the SMPS (160 nm). The small aerodynamic diameter of the agglomerates also may have important implications for the respiratory tract deposition due to sedimentation of such larger particles.
FIG. 7 XEDS analysis of welding fume particles, showing the atomic percent of oxygen, manganese, and iron in three primary particles of different size.
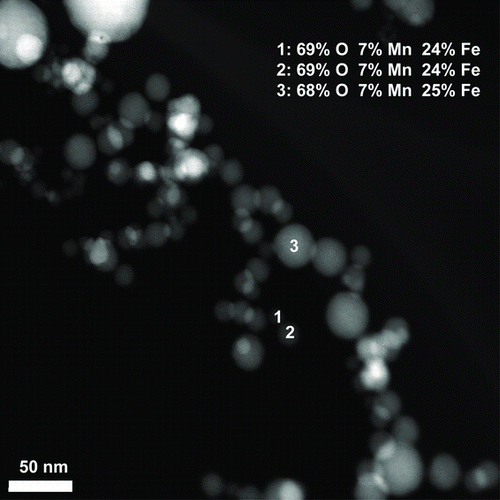
Detailed characterization of welding fume particles in this study showed that the majority of emitted particles are larger than 100 nm but are agglomerates of primary nanosize particles. These, upon contact with airway tissue, may disintegrate into numerous metal-containing particles (Bohgard et al. 1979). This suggests that particles from thermal processes in industrial workplaces could be used as reference or model particles in studies assessing potential health effects of nanosized particles from emerging applications of nanotechnology. The aim of this study was to examine the nanostructure of welding fume which have similarities (in generation mechanism—arc discharge, in structure/morphology, in size) with a variety of engineered nanoparticles. A large population of welders has been, and is being, exposed to these types of particles. Occupational exposure to engineered nanoparticles is expected to increase. The developed methodology can be used for studying the health effects of nanostructured particles from welding. This will also increase our understanding on how nanoparticles affect humans.
Human exposure studies can serve to bridge the gap between epidemiology and toxicology, and help in extrapolating the results from animal studies to the human system. The developed methodology described in this article is safe and efficient enough to be used for future human exposure studies. In the future, human exposure studies based on this protocol in principle can be carried out for engineered nanoparticles, such as carbon nanotubes, as well as other indoor sources. The generation chamber and the aerosol transport/dilution system into the exposure chamber are suitable for combustion-generated aerosols in general (e.g., candle smoke). When using the exposure chamber and monitoring/characterization instruments for other aerosols, the generation part of the system may need to be modified depending on type of aerosol and generation method.
Acknowledgments
The authors thank Swedish Council for Working Life and Social Research (FAS), Swedish Research Council for Environment, Agricultural Sciences and Spatial Planning (FORMAS), and Centre for Medicine and Technology for Working Life and Society (METALUND) for their support.
REFERENCES
- Antonini , J. M. , Afshari , A. A. , Stone , S. , Chen , B. , Schwegler-Berry , D. Fletcher , W. G. 2006 . Design, Construction and Characterization of a Novel Robotic Welding Fume Generator and Inhalation Exposure System for Laboratory Animals. . J. Occup. Environ. Hyg., , 3 ( 4 ) : 194 – 203 .
- Bohgard , M. , Jangida , B. L. and Akselsson , R. 1979 . An Analytical Procedure for Determining Chromium in Samples of Airborne Dust . Ann. Occup. Hyg. , 22 : 241 – 251 .
- Brook , R. D., and Rajagopalan , S. 2010 . Particulate Matter Air Pollution and Atherosclerosis. . Curr. Atheroscler. Rep. , 12 ( 5 ) : 291 – 300 .
- Brown , D. M. , Stone , V. , Findlay , P. , MacNee , W. and Donaldson , K. 2000 . Increased Inflammation and Intracellular Calcium Caused by Ultrafine Carbon Black is Independent of Transition Metals or Other Soluble Components. . Occup. Environ. Med. , 57 : 685 – 691 .
- Crossgrove , J. , and Zheng , W. 2004 . Manganese Toxicity upon Overexposure . NMR Biomed. , 17 : 544 – 553 .
- Donaldson , K. , Li , X. Y. and MacNee , W. 1998 . Ultrafine (Nanometre) Particle Mediated Lung Injury. . J. Aerosol. Sci. , 29 : 553 – 560 .
- Gil , P. R. , Oberdorster , G. , Elder , A. , Puntes , V. and Parak , W. J. 2010 . Correlating Physico-Chemical with Toxicological Properties of Nanoparticles: The Present and the Future . ACS Nano., , 4 ( 10 ) : 5527 – 5531 .
- Heidam , N. C. 1981 . Review: Aerosol Fractionation by Sequential Filtration with Nuclepore Filters . Atmos. Environ., , 15 ( 6 ) : 891 – 904 .
- Isaxon , C. 2008 . Controlled Human Exposures to Aerosol Particles . MSc thesis ISRN LUTMDN/TMAT-5118-SE, Lund University, Lund, Sweden
- Isaxon , C. , Pagels , J. , Gudmundsson , A. , Asbach , C. , John , A. C. Kuhlbusch , T. A. J. 2009 . Characteristics of Welding Fume Aerosol Investigated in Three Swedish Workshops, Conference Proceeding for Inhaled Particles X. . J. Phys. Conf. Ser. , 151(1)
- Jenkins , N. T. 2003 . Chemistry of Airborne Particles from Metallurgical Processing . Doctoral thesis, Massachusetts Institute of Technology, Cambridge, MA
- Johansson , S. A. E. 1989 . PIXE: A Novel Technique for Elemental Analysis . Endeavour, New series, , 13 ( 2 ) : 48 – 53 .
- Kreyling , W. G. , Semmler , M. , Erbe , F. , Mayer , P. , Takenaka , S. Schulz , H. 2002 . Translocation of Ultrafine Insoluble Iridium Particles from Lung Epithelium to Extrapulmonary Organs is Size Dependent but Very Low. . J. Toxicol. Environ. Health Part A , 65 : 1513 – 1530 .
- Li , N. , Sioutas , C. , Cho , A. , Schmitz , D. , Misra , C. Sempf , J. 2003 . Ultrafine Particulate Pollutants Induce Oxidative Stress and Mitochondrial Damage. . Environm. Health Perspect. , 111 : 455 – 460 .
- Messing , M. 2011 . Engineered Nanoparticles Generation, Characterization and Applications . Doctoral thesis, Lund University, Lund, Sweden
- Oberdorster , G. , Sharp , Z. , Atudorei , V. , Elder , A. , Gelein , R. Kreyling , W. 2004 . Translocation of Inhaled Ultrafine Particles to the Brain. . Inhal. Toxicol. , 16 : 437 – 445 .
- Oberdorster , G. , Sharp , Z. , Atudorei , V. , Elder , A. , Gelein , R. Lunts , A. 2011 . Extrapulmonary Translocation of Ultrafine Carbon Particles Following Whole-Body Inhalation Exposure of Rats. . J. Toxicol. Environ. Health Part A , 65 : 1531 – 1543 .
- Pagels , J. , Strand , M. , Rissler , J. , Szpila , A. , Gudmundsson , A. Bohgard , M. 2003 . Characteristics of Aerosol Particles Formed during Grate Combustion of Moist Forest Residue . J. Aerosol. Sci., , 34 : 1043 – 1059 .
- Pekkanen , J. , Peters , A. , Hoek , G. , Tiittanen , P. , Brunekreef , B. de Hartog , J. 2002 . Particulate Air Pollution and Risk of ST-Segment Depression during Repeated Submaximal Exercise Tests among Subjects with Coronary Heart Disease - The Exposure and Risk Assessment for Fine and Ultrafine Particles in Ambient Air (ULTRA) Study. . Circulation , 106 : 933 – 938 .
- Pope , C. A. , Burnett , R. T. , Thun , M. J. , Calle , E. E. , Krewski , D. Ito , K. 2002 . Lung Cancer, Cardiopulmonary Mortality, and Long-Term Exposure to Fine Particulate Air Pollution. . J. Am. Med. Assoc., , 287 : 1132 – 1141 .
- Quimby , B. J., and Ulrich , G. D. 1999 . Fume Formation Rates in Gas Metal Arc Welding. . Weld. J., , 78 ( 4 ) : 142 – 149 .
- Redding , C. J. 2002, June . Fume Model for Gas Metal Arc Welding. . Weld. J. , : 95 – 103 .
- Rissler , J. , Swietlicki , E. , Bengtsson , A. , Boman , C. , Pagels , J. Sandström , T. 2012 . Experimental Determination of Deposition of Diesel Exhaust Particles in the Human Respiratory Tract . J. Aerosol. Sci., , 48 : 18 – 33 .
- Tabrizi , N. S. , Xu , Q. , van der Pers , N. M. and Schmidt-Ott , A. 2010 . Generation of Mixed Metallic Nanoparticles from Immiscible Metals by Spark Discharge . J. Nanopart. Res. , 12 ( 1 ) : 247 – 259 .
- Trout , D. B. and Schulte , P. A. 2010 . Medical Surveillance, Exposure Registries, and Epidemiologic Research for Workers Exposed to Nanomaterials . Toxicology , 269 : 128 – 135 .
- Warheit , D. B. , Borm , P. J. A , Hennes , C. and Lademann , J. 2007 . Testing Strategies to Establish the Safety of Nanomaterials: Conclusions of an ECETOC Workshop . Inhal. Toxicol., , 19 : 631 – 643 .
- Zimmer , A. T., and Biswas , P. 2001 . Characterization of the Aerosols Resulting from Arc Welding Processes . J. Aerosol. Sci., , 32 : 993 – 1008 .