Abstract
In an effort to identify particle initial motion prior liftoff interactions of micrometer glass beads (10–100 μm) on glass, ceramic, and hardwood substrates were investigated experimentally. Particles were deposited on the lower surface of a 10 cm2 wind tunnel by gravitational settling. Air flows were imposed from an open entrance at average velocities up to 16 m/s. Individual particle trajectories obtained by high-speed imaging reveal three different types of motion: rolling/bouncing (saltation caused by the movement of hard particles over an uneven surface in a turbulent flow of air), immediate liftoff (particles completely leave the surface with no or minimal initial rolling/bouncing) and complex motion (particles travel with rolling/bouncing motion on the surface for a certain distance before final liftoff). Surface roughness significantly affects the particle initial motion prior to liftoff. The majority of particle trajectories from the glass substrate were parallel to the surface with complex motion. Hardwood substrates took the longest time for initial particle movement (t >1 s) causing a more rapid liftoff. The ceramic substrate showed the most rolling/bouncing motion, for 80% of the particles. The detachment percentage initially follows an exponentially increasing trend for a period of ∼1 s, followed by a plateau phase for a period of 5 s. Changing the velocity, substrate, and particle size significantly affects particle detachment. Incorporating the different types of particle motion prior to liftoff into detachment mode models, and understanding how their relative contributions change with different particle and substrate materials, can potentially yield improved predictive capabilities.
Copyright 2013 American Association for Aerosol Research
INTRODUCTION
Materials that have been deposited on a surface may subsequently detach and become resuspended from that surface. The major effects of the resuspension can include inhalation hazards and redeposition of particles resulting spread of the contamination (Nicholson Citation1993). Detachment of particles from a surface and their transport, away from that surface, is of interest in outdoor applications where the largest materials may be of significance in the spread of contamination (Nicholson, Citation1993; Hinds Citation1999) Therefore, knowledge of detachment processes is required if the full effects of a contamination event are to be assessed.
The resuspension process usually contains two regimes. The first regime (short-term resuspension) lasts for a brief period of time (e.g., about 1 min). During this period, the most easily resuspended particles (i.e., with less adhesion force) are removed either in groups or individually. The second regime has much lower resuspension rate(s) (Ibrahim Citation2004). In many of the currently reported experiments, almost half the material removed during the entire duration of those experiments was lost from the surface within the first 10 s (Nicholson Citation1993). However, most of the existing data were obtained months to years after initial deposition. These long-term data sets are poor surrogates for short-term emergency response scenarios (Kim et al. Citation2010).
The important factor in the handling of dust is the fact that the particles will adhere to each other and to solid surfaces. Jordan (Citation1954) raised the importance of changing the surface roughness for particle detachment. Qian and Ferro (Citation2008) concluded that hard floor could be a better choice than carpet for reducing particle resuspension. Lohaus et al. (Citation2008) found that air velocities of more than 5 m/s were required to resuspend 50% of 3.2 μm particles from linoleum and wood surfaces. In general, high turbulence and high velocity conditions minimized the differences between materials (Mukai et al. Citation2009). Goldasteh et al. (Citation2010) showed that detachment from wood flooring was easier than from linoleum flooring and they suggested that the difference in the adhesion force (surface energy) and the nature of the micro roughness is the main reason for such behavior.
Resuspension may involve rolling or sliding motion (Jordan Citation1954). Ibrahim et al. (Citation2003) indicated that the microspheres undergo pure rolling along the surface before possible entrainment and this sweeping motion plays a role in the detachment process. However, the effect of particle surface interaction remained unknown since only microscopic glass surfaces were used during his entire investigation. Similarly, the particle trajectory immediately before liftoff was not investigated.
Despite extensive detachment studies, there is still a significant lack of information regarding the path of particles very close to the surface (Harris and Davidson Citation2008). Such information is needed to provide insight in the micromechanism of particle removal (Zhang and Ahmadi Citation2000). This work presents an experimental investigation of the conditions under which a transient fluid flow causes spherical glass microparticles to detach from different surfaces. The general approach is to observe individual microparticle motion during short-term resuspension, and to focus on the basic detachment mechanisms of the resuspended particles to fully understand and quantify their behavior immediately before liftoff. In our experiments, we use a higher frame rate (up to 4000 frame/s) to precisely capture the trajectories of individual particles immediately before liftoff from different surfaces. These new observations can help provide a better understanding of particle–surface interactions prior to liftoff under different environmentally relevant conditions.
In this study, we follow the definition of detachment established by Ibrahim et al. (2008) referring to the process of overcoming adhesion forces between the microparticle and the surface. Detachment can be observed experimentally by monitoring the change in the number of particles remaining on the surface with time (Ibrahim et al. Citation2003). The microparticles are considered detached when they initially begin to move on the surface. To more precisely specify the type of initial motion, we have performed new studies to monitor individual particle trajectories from the side-view using a high-speed camera. Three main categories of initial motion were identified: rolling/bouncing (i.e., saltation) caused by the movement of hard particles over an uneven surface in a turbulent flow of air, immediate liftoff where the particles completely leave the surface with no or minimal initial rolling/bouncing, and complex motion where particles travel with rolling/bouncing motion on the surface for a certain distance before liftoff (in this case the liftoff will be donated as late liftoff to distinguish it from the immediate liftoff). The rolling bouncing motion was then divided into two classifications, either pure rolling/bouncing or rolling/bouncing potential liftoff where particles showed potential to liftoff in the later stages of motion. Three different substrates were considered.
METHODS AND MATERIALS
The experimental setup consists of a 10 cm2 duct that is 180 cm long (). The duct was divided into three sections: an entrance section of 91 cm length made from aluminum material, a 30 cm length of clear PC-300™ Polycarbonate (test section), and a final 61 cm length of aluminum material. A 2.5 cm thick layer of insulation material was added to the bottom of the setup to enable flush mounting the different substrates. The substrates were hardwood, ceramic, and glass slides. The substrates were cleaned with ethanol to neutralize the surface and reduce electrostatic charges (Boor et al. Citation2011). Atomic force microscopy (Veeco, Plainview, NY, USA) was used to scan the glass surfaces (Ibrahim et al. Citation2003). For the other substrates, the surface characteristics were analyzed using a Stylus Profilometer (Dektak 3, Veeco, Plainview, NY, USA), (Boor et al. Citation2011). In this study, results based on three different replicates show average Ra values of (0.536 ± 0.054) × 10−3 μm, 0.038 ± 0.020 μm, and 0.072 ± 0.002 μm for glass, ceramic, and hardwood substrates, respectively.
Glass beads (Polysciences, Inc., Warrington, PA, USA), spherical in shape with specific gravity of 2.48–2.52 g/cm3 were deposited on the top of each substrate by gravitational settling (Ibrahim Citation2004). A Coulter Counter (Beckmann Coulter, Inc., Fullerton, CA, USA) was used to verify the particle size distribution. The mean diameters corresponding to each particle size range are 26.41 μm for the 10–30 μm particles range, 36.24 μm for the 30–50 μm particles range, and 45.31 μm for the 50–100 μm particles range.
A high-speed camera (Photron, Fastcam Ultima APX Imager) was used to monitor the particles detached from the surface with respect to time either from the side or from the top. A telecentric lens (1–10x magnification [Moritex U.S.A., Inc. San Jose, CA, USA]) was mounted on the camera to capture individual particle motion using a halogen light source. A calibration frame taken before each experiment yielded a spatial resolution of 0.9 μm/pixel and 22 μm/pixel (512 × 1024 pixels and 512 × 512 pixels) for side and top view, respectively. The camera displacement was adjusted using a traverse system (BiSlide, Velmex, Inc., Bloomfield, NY, USA). Image acquisition was synchronized with the blowers to automatically trigger the camera while starting the airflow with a specially designed electric circuit. The circuit contains two relay switches (TE Connectivity Solid State Relays, TX, USA), a regulated power supply (Model PAD, Kikusui Electronics Corporation, Japan), and a pulse generator (Quantum Composers, Bozeman, MT, USA). The camera output is connected to a computer for image analysis.
A flow straightener was located at the entrance of the duct to eliminate swirl and to produce highly repeatable flow profile. Four adjustable speed blowers (Thermo Anderson, Smyrna, GA, USA) were connected to the setup. Each blower was connected to A/D glass fiber filters (8 × 10″, Pall Corporation, Ann Arbor, MI, USA) and a variable autotransformer (STACO Energy Product Co., Dayton, OH. USA). A freshly calibrated air velocity meter (VelociCalc, TSI, Inc., Shoreview, MN, USA) was placed in the test section downstream the substrate to simultaneously monitor the speed and the environmental conditions. All experiments were conducted at room temperature and RH of 24.1 ± 0.9°C with 0.03°C/°C uncertainty and 38.5 ± 3.0% with 0.2% RH/°C uncertainty, respectively. A single probe TSI IFA 300 constant temperature hot film anemometer (HFA) was used to verify the velocity profile. A calibration curve was developed based on King's Law with a mean square error of 0.997 × 10−3. Steady state velocities were reached within approximately 1 s. The turbulence intensity estimations were about (6.95 ± 0.34)%.
MEASUREMENT AND ASSOCIATED ERRORS
For the first set of experiments, image analysis was conducted to determine the paths followed by individual particles immediately before liftoff. The data recorded were analyzed using the MATLAB code developed by Estrada-Pérez and Hassan (Citation2010). The origin of coordinates obtained from the MATLAB code is the top left corner of the images recorded. However, the airflow was from the opposite direction (right to left). Accordingly, the following set of equations was assigned to avoid any negative trajectory values:
FIG. 2 Raw data images for the different type of motions of the glass bead particles obtained using 4000 frames/s. (a) rolling/bouncing motion, (b) rolling/bouncing potential liftoff motion, (c) complex motion (rolling/bouncing late liftoff), and (d) immediate liftoff (no rolling/bouncing).
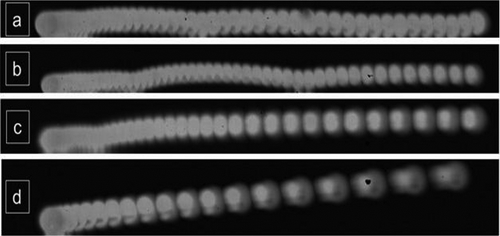
In the second set of experiments, the camera was positioned at the top of the test section to capture single layer particle detachment (not single particle as done in the first set of experiments) with respect to time, within a period of 0–5 s at 2000 frames/s. The number of deposited microparticles was large enough to achieve acceptable statistical accuracy but not too large to cause particle impacts on the surface. The particle single layer initially deposited was about 431 ± 170 particles/cm2 for the 10–30 μm glass bead particles, 360 ± 153 particles/cm2 for the 30–50 μm glass bead particles and, 194 ± 64 particles/cm2 for the 50–100 μm glass beads (Ibrahim et al. Citation2003). Additionally, particle collision results were excluded from the analysis by adjusting the code parameters to avoid any duplicate particles. The experiments were repeated three times for the thee different surfaces, the three different particle size ranges and at three different air velocity conditions. The air velocity started from zero to predicted speeds of 16 ± 1.4 m/s, 11 ± 1 m/s, and 9 ± 0.7 m/s (81 experiments in total). The analysis was based on detachment percentage defined as the number of particles detached from the surface at a certain time compared to the number initially deposited on the surface (Ibrahim et al. Citation2003).
Due to the triggering technique discussed earlier, the error associated with the time can be a maximum of 5 × 10−4 s for 2000 frame/s. The particle counting errors mainly depend on the accuracy of the code. Results showed an error of about (2 ± 2)% in the detachment percentage calculations. Very likely, the error arises from acceleration, whether due to a change in a particle's speed or its direction and/or random noise in the camera sensor and the finite size of pixels in the sensor as extensively discussed by Feng et al. (Citation2011). While it is possible to design an experiment to reduce these particles position uncertainties, they can never be eliminated.
ANOVA statistical analysis (three ways) was applied to verify the level of statistical accuracy for the detachment percentage results recorded at 5 s. The three factors were velocity, particle size, and substrate. The confidence level is taken as 95% (95 percent confidence indicates a significant difference between the parameters used in experiment, Lipson and Sheth Citation1973).
RESULTS AND DISCUSSION
Particle Trajectory
Results obtained from tracking 80 particle trajectories (20 particles for each surface) indicated that the glass beads (ranging from 20–45 μm) experienced three main types of motion ( and ): rolling/bouncing (saltation caused by the movement of hard particles over an uneven surface in a turbulent flow of air), immediate liftoff (particles completely leave the surface with no or minimal initial rolling/bouncing), and complex motion (particles travel with rolling/bouncing motion on the surface for a certain distance before liftoff). Analysis showed that the particle velocity in the x direction, u
p was dominant compared to the velocity in the z direction, w
p (see the online supplemental information; Figure S1). To investigate the significance of the particle vertical velocity fluctuation a parameter was developed. The parameter was used to compare the energy associated with the vertical velocity fluctuations caused by the up/down motion of the particles in the vertical direction, z, and the particle total kinetic energy (dominated by the velocity magnitudes, Equation (4)). The vertical velocity fluctuation energy, , was calculated from the area under the power spectrum curves of the particle vertical velocity data using a fast Fourier transform [FFT], EquationEquation (5)). To obtain the kinetic energy, the average values of the KEp data (Figure S2) were considered for each particle. The ratio of the vertical velocity fluctuation energy and the average particle total kinetic energy was scaled to obtain a quantity of order 1 that will be referred to as r (Equation (4)).
FIG. 3 Type of motion on glass, ceramic, and hardwood substrates for glass beads 20–45 μm in size range for air velocities 0–16 m/s (for more details, see Table S1–S3).
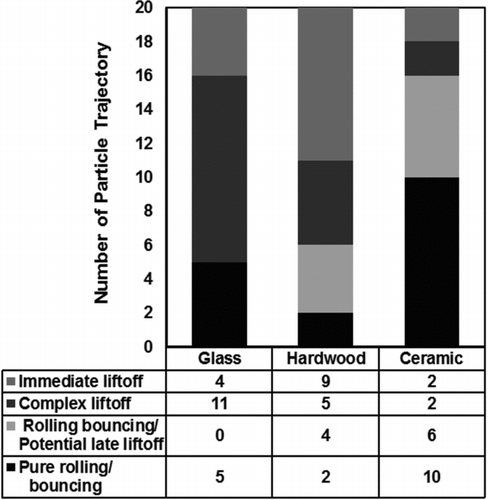
FIG. 4 Particle trajectory for the glass beads particles (20–45 μm in size range) on glass, hardwood, and ceramic substrate as a function of r.
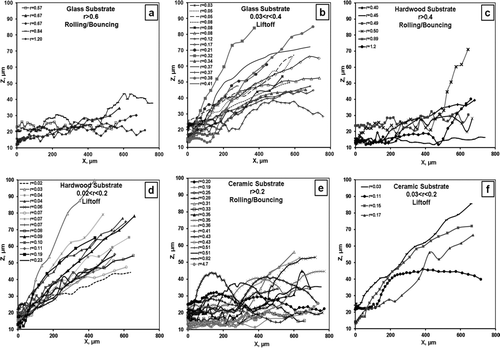
Surface roughness seems to significantly affect the particle initial motion prior to liftoff. Particles deposited on glass substrates, the smoothest roughness with 100x less roughness, needed about 50% less kinetic energy for liftoff motion to occur (, , and ). Additionally, about 70–75% of the particles from glass and hardwood substrates will eventually liftoff, compared to 20% liftoff from the ceramic substrate (Immediate and complex liftoff ). Although the majority of the particle trajectories from glass and hardwood substrates seem to eventually liftoff ( and ), a closer look reveals that the bigger the surface roughness (typically hardwood in this case), the longer it will take for the particle initial motion (t > 1 s) to cause a more rapid liftoff with minimum or no initial rolling/bouncing motion (Figure S3). In contrast, particle trajectories from the glass substrates seem to display a complex motion, as particles travel about 25% with a rolling/bouncing motion before completely leaving the surface. In this case, the majority of particle trajectories from the glass substrate tend to travel in the horizontal direction parallel to the surface after liftoff rather than the rapid increase liftoff as seen on the hardwood substrates. In other words, over the same recording time, the glass substrate is expected to have the highest resuspension percentage, as confirmed by the detachment percentage results presented in the next section. Particles on the ceramic substrate, however, seem to struggle to achieve liftoff as 80% of the particles recorded showed a rolling/bouncing motion (). A closer examination of the ceramic rolling/bouncing particles (80% of the total particles), shown in , reveals that about 40% of these particle trajectories show a potential of late liftoff after initial rolling/bouncing at traveling distances of about 40% of the recorded distance ().
FIG. 5 Time effect on particle trajectory for the glass beads particles on ceramic substrate, where the time, t, is the time it will take the particle to begin its initial movement since starting the camera and the blower simultaneous triggering.
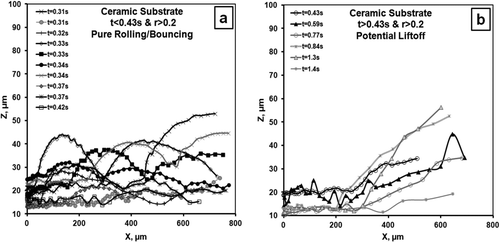
According to Wu et al. (Citation1992), when the particle relaxation time, EquationEquation (6), is much greater than the turbulent time scale, EquationEquation (7), the particle should eventually return to the surface under the influence of gravity.
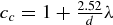
In our particle size range and flow conditions, the particle relaxation time, τp = (0.004–0.018) s, is at least 10x more than the turbulent time scale, tL = 0.0004 s. Hence, the particle trajectories will follow a parabolic path, each particle having a constant horizontal velocity as it moves downstream, but reaching a maximum height before returning to the surface under the influence of gravity (Wu et al. Citation1992).
FIG. 6 Time dependence of detachment percentage of different sizes glass beads particles on a glass substrate.
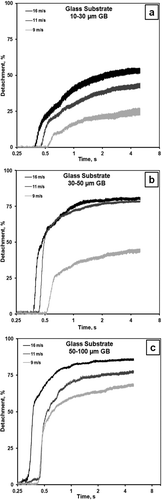
Although the average roughness values for the hardwood and the ceramic are close (within factor of 2). The ceramic is a glazed surface with top glass finish and appears extremely smooth and shiny compared to the hardwood's aluminum oxide finish. To further investigate roughness, scanning electron microscopy (SEM) was used to visualize the topographies. SEM images showed that the ceramic roughness is characterized by scattered bumps and larger non-uniformly distributed features, in contrast of the hardwood where the roughness was more homogeneous. Additionally, the hardwood surface used in this study contains an aluminum oxide surface finish. The coefficient of static friction for glass particles on hardwood is therefore estimated to be glass on aluminum, yielding a value of 0.17. For the ceramic substrate, glass on glass contact was assumed using a value of 0.9. Comparing the difference between glass particles on a glass surface (glass–glass), glass particles on a ceramic surface (glass–ceramic), and glass particles on a hardwood surfaces (glass–wood) shows that that (glass–glass) and (glass–ceramic) have the same coefficient of friction but different surface roughness. In this case, the difference in results shown in and is dominated the surface roughness effect only as seen in , 75% of the glass surface results liftoff after rolling for about 25% of the recorded distance only. In contrast, 80% of the particles on the ceramic substrate displayed rolling motion on the surface over the entire viewing window. Hence, surface roughness appears to delay the liftoff since the same particles experience liftoff on glass but not on ceramic. On the other hand, if we compare the (glass–wood) and (glass–ceramic) and disregard the 2x difference in surface roughness, we immediately notice the difference in the static coefficient of friction (0.17 and 0.9, respectively). It therefore appears that the interplay between particle–surface interactions, initial motion, and liftoff is more complex than previously thought. For example, previous models proposed that only one type of particle motion occurs, whereas our experiments reveal that a combination of motion can occur.
Particle Detachment and Resuspension Rate
The detachment percentage data initially follow an exponentially increasing trend for a period of ∼1 s, followed by a plateau phase during the remainder of the 5 s recording time, with higher detachment percentage observed on glass (, and Figures S4 and S5, available in the online supplementary information). Changing the velocity, substrate and particle size for the glass beads will significantly affect particle detachment with at least 97.5% confidence level using ANOVA statistical analysis at t = 5 s (Table S4; Figure S6). In general, less particle detachment was observed on hardwood flooring compared to the ceramic and glass substrates, especially for the larger particle size; the highest detachment was obtained by using glass substrate. Increasing the particle size will result in increased detachment, as very likely larger particles penetrate higher into the boundary layer and thus experience higher removal forces. As the particle size increases, removal forces increase more rapidly than adhesion forces. Larger surface roughness (such as hardwood in our case) provides more shielding, acting against particle detachment and resuspension.
Another term to quantify the resuspension is the resuspension rate, defined as the fraction of deposited particles resuspended per unit time (Slinn Citation1978), or the normalized resuspension flux (Loosmore Citation2000) where Λ is the resuspension rate, s
−1, Δt is a constant equal 1/frame rate, ΔN = N
i+1 – Ni, where i is the number of frames taken by the camera, N
i+1 and N
i were estimated by a curve fit to the experimental with R
2 valued around 0.95. In general, resuspension rates of particles from the surfaces change over time and range from 0 s−1 to 7 s−1 with three regimes to be considered, the first regime lasts for less than 0.5 s with zero values; the second regime is characterized by rapid exponential increase. However, the third regime exhibits opposite behavior of slower exponential decay that lasts until the end of the 5 s recording (Figures S7–S9). For resuspension to occur, the aerodynamic drag force must be greater than the adhesion force. Very likely, the adhesion forces were initially higher than the drag forces causing the particles to stick to the surface with zero resuspension rate in the first 0.5 s. However, the increase in air speed with time from the stationary state to the desired speed caused the rapid increase in the resuspension rate in the second regime due to the corresponding increase in drag force. Beyond this time, the particles most easily resuspended have been removed, resulting in a nonlinear decrease in resuspension rate (Loosmore Citation2003). In addition, resuspension occurs when particles acquire enough energy to escape from the adhesive potential well and deeper wells result in lower resuspension rates. Allowing for variations in the strength of adhesive force among the particles, resuspension rate is found to decrease approximately inversely with time. This is typically what we observed in the third regime of our experiments.
For comparison, the analytical model earlier developed by Kim et al. (Citation2010) was also used to verify the resuspension rate calculations, (EquationEquation (8)).






In this study, the microparticles are embedded completely within the viscous sublayer (z + < 5). The wall unit z + equal zu*/ν in which z is the physical height above the wall (in our study, at y = 50.5 μm, z + = 2.5). The turbulent boundary layer thickness can be calculated based on a formula given by Prandtl and Tietjens (Citation1934) as shown in Equation (9)

The resuspension rate experimental results were compared to predictions by Kim's analytical model (). In general, a ratio around 1 was obtained when the resuspension rates were compared for the glass substrate at the smaller particle size range, <50 μm (Figure S10). Such agreement is a reflection of the similarity of our experimental approach under these conditions with that of Ibrahim (2004) that was used to establish the correlations in the Kim model, since Ibrahim's experiments were performed using smooth glass substrates. In contrast, the analytical model tends to underestimate resuspension rates by a 10x factor in the ceramic and hardwood substrates. This seems to be consistent with previous observations that the roughest surfaces were the most under predicted by Kim's model (Kim et al. Citation2010).
FIG. 7 Comparison between our resuspension rate experimental results and Kim et al. (Citation2010) analytical model at t = 5 s.
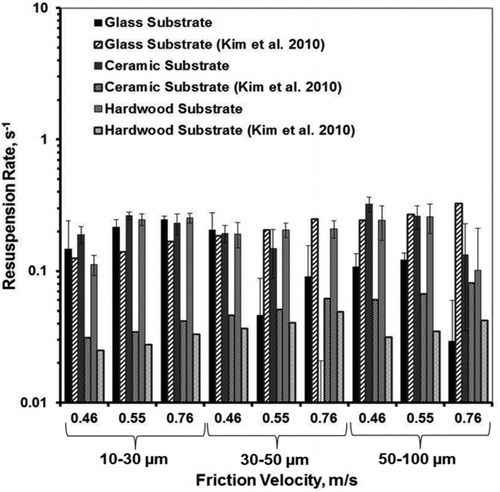
In our experiments, we observe that the Kim analytical model most accurately predicts resuspension phenomena in the smooth glass substrates, whose roughness is 100x less than the other surfaces we examined at smaller particle sizes. According to Fuller and Tabor (Citation1975) a roughness of only 1 μm is sufficient to reduce the adhesion to a small fraction of its value on a smooth surface. Since, the glass substrate is much smoother, the adhesion mechanism may be expected to be better represented by the Hamaker constant that is incorporated in the model. This mechanism may not fully capture what is happening in the other rougher substrates. These differences are supported by , where the “rolling/bouncing late liftoff” mechanism is seen only on the ceramic and hardwood surfaces. Therefore, in order to make more accurate predictions, our results suggest that resuspension models should be refined to incorporate the different types of particle motion prior to liftoff in order to better represent the particle–surface interactions associated with different substrates.
SUMMARY AND CONCLUSIONS
Resuspension may involve rolling or sliding (Jordan Citation1954; Hinds Citation1999). However, the rolling detachment is the dominant mechanism for particle removal in turbulent flows (Zhang and Ahmadi Citation2000; Ibrahim et al. Citation2003). Despite the extensive studies of resuspension phenomena, there is still a significant lack of information about the path of particles very close to the surface (Harris and Davidson Citation2008). Further data are needed to provide insight in the micromechanics of the particle removal process (Zhang and Ahmadi Citation2000). In this study, particle trajectories immediately before liftoff were investigated experimentally, using three different substrates representing different roughness characteristics. We found that glass beads (sizing ranging from 20–45 μm) experienced three different types of motion,
1. | Rolling motion without any liftoff as earlier reported in literature; however, our high-speed imaging studies reveal that the particles also experience vertical bouncing while rolling on the surface. | ||||
2. | Complex motion, where the particles simultaneously roll while bouncing up and down for a certain time before liftoff. | ||||
3. | Immediate liftoff with no initial rolling or bouncing. |
Particles experiencing rolling/bouncing motion seem to have stronger vertical velocity fluctuation energies compared to the total average kinetic energy. Conversely, rapid liftoff seems to be associated with higher kinetic energy. The longer it will take the particle to start its initial movement the more rapid is the liftoff once motion is initiated. Particle–surface interactions were varied by changing the surface roughness, significantly affecting initial motion prior to liftoff. Particles deposited on the smoothest substrate (100x less roughness for glass compared to hardwood and ceramic), required about 50% less particle kinetic energy/vertical velocity fluctuation to eventually liftoff. The greater the surface roughness (typically hardwood in our case), the longer it took the particle for initial motion to start (t > 1 s) causing a more rapid liftoff with a minimum or no initial rolling/ bouncing motion. In contrast, particle trajectories from the glass substrates seemed to have a complex motion, and the particle needs to travel about 25% with a rolling/bouncing motion before completely leaving the surface and lifting off. In this case, the majority of particle trajectories from the glass substrate tended to be directed parallel to the surface after liftoff. The ceramic substrate showed the most rolling/bouncing motion, for 80% of the particles recorded.
Changing the velocity, substrate and particle size for the glass bead particles significantly affects the detachment percentage with at least 97.5% statistical accuracy using ANOVA statistical analysis. The surface with the smallest roughness, glass, displayed the highest detachment over the entire particle size range tested. Very likely, larger particles penetrate higher into the boundary layer and thus experience higher removal forces. Larger surface roughness (such as hard wood in our case) provides more shielding, acting against detachment. Moreover, the detachment percentage data initially follow an exponentially increasing trend for a period of ∼1 s, followed by a plateau phase during the remainder of the 5 s imaging time.
Our experimental results point out the importance of identifying the different types of particle motion that occur prior to liftoff, and how their relative contributions change with different particle and substrate materials. Incorporating these insights into the representation of particle–surface interactions in existing detachment mode models will help improve their ability to accurately predict resuspension phenomena.
Supplementary Files.zip
Download ()Acknowledgments
[Supplementary materials are available for this article. Go to the publisher's online edition of Aerosol Science and Technology to view the free supplementary files.]
REFERENCES
- Bergström , L. 1997 . Hamaker Constants of Inorganic Materials . Adv. Colloid Interface Sci. , 70 : 125 – 169 .
- Boor , B. E. , Siegel , J. A. and Novoselac , A. 2011 . Development of an Experimental Methodology to Determine Monolayer and Multilayer Particle Resuspension from Indoor Surfaces . ASHRAE Transactions , 117 : 434 – 441 .
- Estrada-Pérez , C. E. and Hassan , Y. A. 2010 . PTV Experiments of Subcooled Boiling Flow Through a Vertical Rectangular Channel . Int. J. Multiphase Flow. , 36 : 691 – 706 .
- Feng , Y. , Goree , J. and Liu , B. 2011 . Errors in Particle Tracking Velocimetry with High Speed Cameras . Rev. Sci. Instrum. , 82 ( 053707 ) : 1 – 7 .
- Fuller , K. N. G. and Tabor , D. 1975 . The Effect of Surface Roughness on the Adhesion of Elastic Solids . Proc. R. Soc. Lond. A. , 345 : 327 – 342 .
- Goldasteh , I. , Ahmadi , G. and Ferro , A. 2010 . Effect of Air Flow on Dust Particles Resuspension from Common Floorings . Paper presented at Proceedings of ASME 2010 3rd Joint US-European Fluids Engineering Summer Meeting and 8th International Conference on Nanochannels, Microchannels, and Minichannels, August 1–5 Montreal, Canada
- Harris , A. R. and Davidson , C. I. 2008 . Particle Resuspension in Turbulent Flow: A Stochastic Model for Individual Soil Grains . Aerosol Sci. and Technol. , 42 : 613 – 628 .
- Hinds , W. C. 1999 . Aerosol Technology: Properties, Behavior, and Measurement of Airborne Particles (2nd ed.) , New York : John Willy & Sons .
- Ibrahim , A. H. 2004 . Microparticle Detachment from Surfaces by Fluid Flow. Ph.D. dissertation University of Notre Dame Notre Dame, IN
- Ibrahim , A. H. , Dunn and Qazi , M. F. 2008 . Experiments and Validation of a Model for Microparticle Detachment from a Surface by Trubulent Air Flow . J. Aerosol Sci. , 39 : 645 – 656 .
- Ibrahim , A. H. , Dunn , P. F. and Brach , R. M. 2003 . Microparticle Detachment from Surfaces Exposed to Turbulent Air Flow: Controlled Experiments and Modeling . J. Aerosol Sci. , 34 : 765 – 782 .
- Incropera , F. P. and DeWitt , D. P. 2002 . Fundamentals of Heat and Mass Transfer (5th ed.) , New York : John Wiley & Sons .
- Jordan , D. W. 1954 . The Adhesion of Dust Particles . Brit. J. Appl. Phys. , 3 : S194 – S197 .
- Kays , W. , Crawford , M. and Weigand , B. 2005 . Convection Heat and Mass Transfer (4th ed.) , New York : McGraw-Gill .
- Kim , Y. , Gidwani , A. , Wyslouzil , B. E. and Sohn , C. W. 2010 . Source Term Models for Fine Particle Resuspension from Indoor Surfaces . Build. and Environ. , 45 : 1854 – 1865 .
- Lipson , C. and Sheth , N. J. 1973 . Statistical Design and Analysis of Engineering Experiments , New York : McGraw-Hill .
- Lohaus , J. H. , Novoselac , A. and Siegel , J. A. 2008 . Particle Resuspension from Indoor Flooring Materials Paper Presented at Proceedings of the 11th International Conference: “Indoor Air and Climate,” August 17–22 Copenhagen, Denmark Paper ID: 342
- Loosmore , G. A. 2000 . Dust Resuspension and the Implications for Contaminant Transport. Ph.D. dissertation , Berkeley , CA : University of California .
- Loosmore , G. A. 2003 . Evaluation and Development of Models for Resuspension of Aerosols at Short Times after Deposition . Atmos. Environ , 37 : 639 – 647 .
- Miller , R. W. 1996 . Flow Measurement Engineering Handbook (3rd ed.) , New York : McGraw Hill .
- Mishulovich , A. and Evanko , J. L. 2003 . Lexington, KY , , USA : Paper Presented at International Ash Utilization Symposium, October 20–22 . Ceramic Tiles from High-Carbon Fly ash
- Moody , L. F. and Princeton , N. J. 1944 . Friction Factor for Pipe Flow . ASME Trans. , 66 : 671 – 684 .
- Mukai , C. , Siegel , J. A. and Novoselac , A. 2009 . Impact of Airflow Characteristics on Particle Resuspension from Indoor Surfaces . Aerosol Sci. and Technol. , 43 : 1022 – 1032 .
- Nicholson , K. W. 1993 . Wind Tunnel Experiments on the Resuspension of Particulate Material . Atmospheric Environment. , 27A : 181 – 188 .
- Prandtl , L. and Tietjens , O. G. 1934 . Applied Hydro and Aerodynamics (Engineering Society Monographs) McGraw-Hill, New York
- Qian , J. and Ferro , A. R. 2008 . Resuspension of Dust Particles in a Chamber and Associated Environmental Factors . Aerosol Sci. and Technol. , 42 : 566 – 578 .
- Slinn , W. G. N. 1978 . Parameterisations for Resuspension and for Wet and Dry Deposition of Particles and Gases for Use in Radiation Dose Calculations . Nucl. Safety. , 19 : 205 – 219 .
- Soltani , M. and Ahmadi , G. 1994 . On Particle Adhesion and Removal Mechanisms in Turbulent Flows . J. Adhes. Sci. and Technol. , 8 : 763 – 785 .
- Versteeg , H. K. and Malalasekera , W. 1995 . An Introduction to Computational Fluid Dynamics , Essex , NJ : Longman Scientific & Technical .
- Wu , Y. , Davidson , C. I. and Russell , A. G. 1992 . Controlled Wind Tunnel Experiments for Particle Bounceoff and Resuspension . Aerosol Sci. and Technol. , 17 : 245 – 262 .
- Zhang , H. and Ahmadi , G. 2000 . Aerosol Particle Transport and Deposition in Vertical and Horizontal Turbulent Duct Flows . J. Fluid Mech. , 406 : 55 – 80 .