Abstract
Simple modifications to widely available commercial-off-the-shelf (COTS) inkjet printers and cartridges enabled production of aerosols that were tunable in number, size, and size-distribution width. Aerosols generated from various solutions using an inkjet printer with varying control software settings were dehydrated into solid microparticles for characterization using an aerodynamic particle sizer (APS) to determine particle number and size. The duration of microdroplet and microparticle production using this method was adjustable by varying the size of the print job image sent from the control computer. The microparticles created using the inkjet printer were predominantly 1–5 μm in aerodynamic diameter. Tuning of the size of the created microparticle size-distribution was achieved by changing the solute concentration in the printed solution. The size of the dried particles increased monotonically with solute concentration as expected. The aerosol size-distribution width was customizable by varying the COTS inkjet printer control software settings. The highest quality programmed print modes produced a narrower size-distribution compared to the rapid, low quality print options available in the software. The morphology of the dehydrated microparticles was determined to be spherical using scanning electron microscopy (SEM). These experiments demonstrated the successful use of commonly accessible commercial inkjet printers and software to produce tunable and well-characterized aerosol size-distributions in an easily controlled manner. The customizable aerosols and microparticles produced using this method displayed diverse properties that may be tailored to a wide range of experimental applications.
Copyright 2013 American Association for Aerosol Research
INTRODUCTION
Microdroplets and microparticles find use in many diverse scientific applications. However, reproducible, controlled-size aerosol production is currently only achievable using commercial systems tailored for very specific applications. There is a need for a more accessible and universally applicable generation mechanism for controlled-size aerosols and microparticles using equipment already present in most laboratories. Here, we demonstrate the successful use of a widely available commercial-off-the-shelf (COTS) inkjet printer to produce tunable and well-characterized aerosol size-distributions in a rapid, easily controlled manner.
Historically, aerosols and microparticles have been used to investigate solute atomization in flames for analytical spectroscopic analyses (Hieftje and Malmstadt Citation1968; Seymour and Boss Citation1983; Childers and Hieftje Citation1986), spray combustion and fuel injection (Sangiovanni and Labowsky Citation1982), agricultural spraying drift and deposition (Threadgill et al. Citation1974), evaporation (Yang et al. Citation1997) and other physical properties related to weather (Magarvey and Taylor Citation1956), and for assessing performance of particulate control devices and the effects of particulate air pollutants (Berglund and Liu Citation1973). More recently, aerosols have been tailored for use in drug delivery (Jain et al. Citation1998; Hauschild et al. Citation2005), Raman spectroscopy of levitated droplets (Trunk et al. Citation1994), maskless lithography for microelectromechanical system (MEMS) fabrication (Wang et al. Citation2004), and as particle standards containing trace levels of molecules for ion mobility spectroscopy (Fletcher et al. Citation2008) and trace levels of elements for X-ray fluorescence spectrometry and laser ablation inductively coupled plasma mass spectrometry (Fittschen et al. Citation2006, Citation2008). Uniform microdroplets of ink for data recording applications were first developed by Sweet (Citation1965). This first inkjet droplet production system, as well as the several modified systems by others that followed (Kamphoefner Citation1972; Stemme and Larsson Citation1973; Carnahan and Hou Citation1977), formed the basis for the commercial inkjet printing industry (Buehner et al. Citation1977). These early studies all used custom-built aerosol generation systems that were unique and elaborate, requiring considerable time and effort to construct, and patience and skill to operate. In addition, an attempt to duplicate or improve upon an aerosol generator described in the literature proved difficult as often details were oversimplified or not provided.
Currently, there is a variety of commercially available aerosol generators designed to alleviate some of the drawbacks of using individual custom-built systems. The Vibrating Orifice Aerosol Generator (VOAG, TSI Inc., Shoreview, MN, USA) uses a piezoelectric cylinder to precisely control the breakup of a liquid jet into monodisperse microdroplets. The diameter of the microdroplets is tunable by varying the liquid flow rate and the vibration frequency of the nozzle. However, droplets are created one at a time, making the VOAG unsuitable for rapid, large-scale aerosol production (Berglund and Liu Citation1973). The Sono-Tek ultrasonic atomizer (Sono-Tek Corp., Milton, NY, USA; www.sono-tek.com) uses the piezoelectric transducer droplet production method as well, but produces a spray of polydisperse microdroplets with an atomizing surface at the end of the liquid feed tube instead of a nozzle. The resulting polydisperse microdroplets have the disadvantage of requiring sorting prior to use in some applications. Nebulizers are another commercially available aerosol production option. The aerosol production mechanism involves a rapidly flowing gas stream interacting with a relatively slowly flowing liquid stream, where the turbulent gas flow breaks the liquid into randomly sized droplets in a large range of sizes. More sophisticated nebulizers contain impingement surfaces to break up the larger droplets into smaller droplets, resulting in a narrower size-distribution. However, even with impingement surfaces, the resulting microdroplets are still polydisperse over a larger size-range than is appropriate for some aerosol applications (Rubinson and Rubinson Citation2000). Finally, commercial emulsion solvent extraction piezoelectric printing systems (SphereJet, MicroFab Technologies, Inc., Plano, TX, USA) can print microparticles composed of polymers, but cannot generate aerosols (Jain et al. Citation1998; Fletcher et al. Citation2008). Similar to the VOAG, the single monodisperse particle generation rates are not ideal for large-scale production. There are a range of other commercially available comprehensive aerosol and particle production and characterization systems based on inkjet printing technology that produce well-defined aerosols. However, most systems are tailored to a specific purpose and are unable to transition effectively to new applications.
Commercial inkjet printer systems (Hewlett-Packard DeskJet series, Hewlett-Packard Company, Palo Alto, CA, USA) are low-cost, typically less than $100 USD for the entire system (printer, cartridge, and operating software), widely available, and capable of rapid, large-scale, consistent size-distribution microdroplet production (Buskirk et al. Citation1988; Bohorquez et al. Citation1994; Shelley et al. Citation1997). Current COTS inkjet printers employ either a piezoelectric mechanism (discussed above) or a thermal bubble mechanism for microdroplet production. The basic components of a thermal inkjet printhead are resistors, ink channels, and exit nozzles. When the resistor is electrically heated, the nearby ink is vaporized to create a bubble, forcing an ink droplet out through the nozzle. The collapsing bubble and capillary force then draw ink from the channel to refill the nozzle (Buskirk et al. Citation1988; Chen et al. Citation1998). High-throughput, reproducible size-distribution microdroplet generation is achievable as some inkjet cartridges contain approximately 300 identical nozzles with concurrent nozzle firing rates of around 8 kHz (Bohorquez et al. Citation1994; Shelley et al. Citation1997). Compared to custom-built and commercially available systems, there is minimal time and money investment in applying these widely available COTS inkjet printer systems to aerosol and microparticle production applications.
The US Army's Edgewood Chemical Biological Center first demonstrated the potential for COTS inkjet-based aerosol generation. The Inkjet Aerosol Generator (IJAG) coupled a 12-nozzle thermal inkjet printhead from a desktop inkjet printer to a heated desiccation tube to dry the aerosol into microparticles, and was controlled using custom-built electronics and software. The uniformity of aerosols produced over time was demonstrated, and particles with tunable sizes in the range of 1–10 μm were generated (Bottiger et al. Citation1998). The Digital Aerosol Generator (DAG) was the second generation of the IJAG, utilizing COTS industrial-sized piezoelectric inkjet array printheads. The printed droplets were rapidly dried using a flow of warm air in a custom-built droplet conditioning module, and the system was controlled using custom software and electronics (Dougherty et al. Citation2007). Sergeyev and Shaw (Citation2006) also demonstrated the use of a COTS thermal inkjet cartridge operated using custom-built electronics to produce droplets in a constant size-distribution (17 ± 2 μm). The system was reproducible over several hours and the droplet generation rate was accurately controlled, however, no attempt was made to tune the size-distribution of the generated droplets. All of these custom-built microdroplet and microparticle production systems incorporated COTS inkjet cartridges, leveraging decades of droplet production technology to produce aerosols with desirable properties. However, the other components of the aerosol generation systems (e.g., the control electronics and printhead enclosures) and the software to control the cartridges were custom-built, making it difficult to transition the technology in a cost-effective manner to other researchers and consumers.
This article describes the use of widely available COTS inkjet printer systems, with the associated commercial control software, for universal aerosol and microparticle generation. Simple modifications to the inkjet printers and cartridges were added, but with retained functionality of the commercial software to easily control the printer and aerosol generation. Tunable and well-characterized microparticle size-distributions were simply and reproducibly produced with diverse properties suitable for many applications, including large-scale production, using this commonly accessible system.
MATERIALS AND METHODS
COTS inkjet printers and cartridges were purchased online from Hewlett-Packard (HP, http://www.shopping.hp.com). This work utilized HP Deskjet D1660 Printers and HP 60 Black and Tricolor ink cartridges. Hewlett-Packard printer systems use the thermal bubble mechanism of microdroplet production, which was better suited for this work compared to piezoelectric systems, as it is more robust to experimentation and modification due to the lack of moving mechanical parts in the printheads. The black ink cartridges contained 336 nozzles, 20 μm in diameter, arranged in two columns of staggered nozzles (determined using SEM, data not shown). Nozzles were spaced at 1/600 inch (600 dots per inch, or dpi, resolution), yielding a swath height of 0.56 inches. The nozzles have a reported firing rate of 8 kHz and generate 13.8 pL ink droplets, which equates to 30 μm in diameter (Bohorquez et al. Citation1994; Shelley et al. Citation1997).
FIG. 1 Schematic drawings of the experimental setup showing (a) the modified inkjet printer and stationary mounted cartridge carriage (top view) and (b) the droplet collection, dehydration, and microparticle characterization devices (side view).
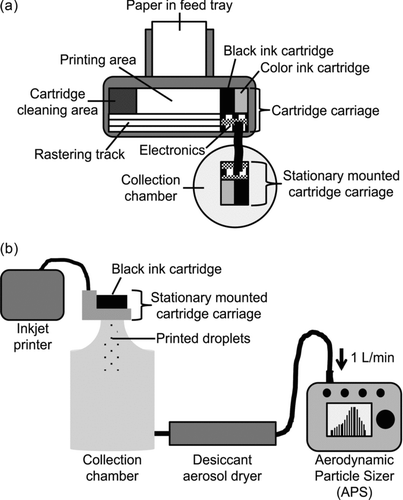
Both the printers and cartridges were modified to enable printing a variety of solutions and collecting and analyzing the printed aerosol droplets. The top cover of the printer was removed to allow access to the cartridge carriage assembly inside (). The cartridge carriage was removed from a second printer, electrically connected to the carriage in the intact printer, and stationary mounted over a large plastic collection chamber. This configuration allowed the cartridge carriage within the intact printer to raster back and forth normally as if printing an image on the paper, but the printed droplets issued from the stationary mounted cartridge carriage for collection. The inkjet cartridges were prepared for experiments by removing the tops and flushing out the ink with water. The solutions printed during experiments were always printed through clean black cartridges as they were more simply constructed compared to the tricolor cartridges. After the black cartridge was loaded with 500 μL of the solution to be printed, the top was replaced. The black cartridge was then placed in the stationary cartridge carriage over the initial collection chamber for production and collection of aerosol droplets.
Instead of striking paper to form an image, the droplets generated by the modified printer and stationary mounted black inkjet cartridge were collected in a five-gallon polycarbonate container and immediately drawn through desiccant aerosol dryers (built in-house) to dehydrate them (). This resulted in solid microparticles consisting of the nonvolatile dissolved substances from the printed aqueous solution. The microparticles (still suspended in the moving air stream) were then characterized using an aerodynamic particle sizer (APS, TSI model 3321, Shoreview, MN, USA) and Aerosol Instrument Manager Software (version 8.1, TSI). The APS drew air at a rate of 1 L/min through the system and was the means for transporting the generated microdroplets from the initial collection chamber through the desiccant dryers to the APS to be analyzed. The APS counted the microparticles and determined their aerodynamic diameter simultaneously, yielding size-distribution results for the microparticles collected during each experiment.
The generated microparticles were composed of glucono-delta-lactone (GDL, Purac America, Inc., Lincolnshire, IL, USA), a naturally-occurring food additive. GDL was chosen as it is nontoxic and water soluble, making it amenable for use in the thermal inkjet cartridges that are manufactured to print water-based black ink (Hall et al. Citation1994). Solutions of varying GDL concentration (% w/v) in sterile water (Teknova, Hollister, CA, USA) were tested in order to examine the tunability of the resulting microparticle size-distribution created using this inkjet printing method. lists some physical properties, namely density and viscosity, of the tested GDL solutions, as well as the values measured for the HP 60 black ink that was in the cartridges. The density of each solution was measured by weighing 1.000 mL of the solution using an analytical balance in triplicate. The kinematic viscosity of each solution was determined using a Cannon-Fenske opaque viscometer (size 50, Cannon Instrument Company, State College, PA, USA) in triplicate. Kinematic viscosity was converted to dynamic viscosity by multiplying by the density of the solution. Solution density and viscosity affect nozzle re-filling speed and droplet break-off time within the inkjet cartridge and are therefore expected to have an effect on expelled droplet size.
TABLE 1 Physical properties of aqueous GDL solutions used during experiments and HP 60 black ink for comparison (n = 3, mean ± one standard deviation)
TABLE 2 Paper type and print quality settings investigated for effect on printed aerosol characteristics (* indicates tested experimental condition, N/A indicates setting not available)
The image sent to the printer as the print job for all experiments was a solid black rectangle, 20.2 cm × 7.6 cm, created on a slide in Microsoft Office PowerPoint (Microsoft, Redmond, WA, USA). The slide was saved as a picture, and the picture was printed from the Preview application of a Mac OS X computer (Apple, Inc., Cupertino, CA, USA). The HP Deskjet D1660 printer driver was downloaded from the HP website and installed on the same computer. When the black rectangle image was printed from preview to the HP Deskjet D1660 printer, there were several customizable options available in the paper type/quality portion of the Advanced print menu that were expected to influence the generated aerosol. The customizable options included: paper type, quality, color, photo fix, and grayscale mode. The most interesting paper type and print quality option combinations available in the commercial software were investigated (). The color option was always set to grayscale, as solution was only loaded into the black inkjet cartridge to be printed. The photo fix option was always “off” to simplify the results. The grayscale mode suboptions were high quality (both tricolor and black cartridges used) and black print cartridge only. The black print cartridge only option was employed at all times that it was available, however, for higher quality settings the high quality grayscale mode was the only option available.
The microparticle APS size-distribution raw data collected during experiments was qualitatively compared to determine the effects of varying the generation parameters on the resulting microparticle size-distribution. The datasets were then treated more analytically by truncating them to only include the principal size-distribution data points containing the majority of the collected microparticles and applying standard chromatographic peak processing and analysis methods (e.g., gas or liquid chromatography data analysis methods). The truncated size-distribution data from all experiments was imported into MATLAB (version R2011b, MathWorks, Inc., Natick, MA, USA) and individually smoothed using the Savitzky–Golay algorithm with the best experimentally determined parameters for these data (data point span of seven, polynomial degree of three) (Savitzky and Golay Citation1964). The MATLAB Curve Fitting Toolbox was then used to fit a single Gaussian function to the smoothed data from each experiment. The resulting Gaussian equations that best fit the data were used to determine microparticle size-distribution maxima positions and full width at half maximum (FWHM) values in terms of aerodynamic diameter. Statistically significant differences in the generated microparticle size-distribution characteristics resulting from changing experimental conditions were evaluated using Student's t-tests and one-way analysis of variance (ANOVA) procedures using Microsoft Office Excel (null hypotheses were that the experimental means were the same). The resolutions of relevant size-distributions were also calculated using the conventional chromatographic theory equation (EquationEquation (1)) using Excel:
As the microparticle size-distribution data was collected in terms of aerodynamic diameter on the x-axis and particle counts on the y-axis, the resolution was calculated using measurements in micrometers (μm). The mean size-distribution standard deviations from the Gaussian best-fit equations multiplied by four were used as the baseline peak width values, W, and the mean size-distribution maximum positions were used as retention times, tR , in order to determine the resolution, Rs , of two microparticle size-distributions (Skoog et al. Citation1998; Rubinson and Rubinson Citation2000).
Finally, Scanning Electron Microscopy (SEM) was used to confirm the size and examine the morphology of the GDL microparticles produced using the COTS inkjet printer. Microparticles were collected on TeflonTM filter material (1.0 μm pore size, ZeflourTM supported PTFE, Pall Corp., Ann Arbor, MI, USA) using a four-stage Impactor Stack with a 9 L/min air flow rate (California Measurements, Inc., Sierra Madre, CA, USA). Samples were sputter coated with a thin layer of gold using a Hummer 6.2 Sputter Coater (Anatech, Union City, CA, USA) and were viewed using a Hitachi S-800 field emission scanning electron microscope (Hitachi, South San Francisco, CA, USA) and Quartz PCI imaging software (version 6.0, Quartz Imaging Corporation, Vancouver, BC, Canada). Images from SEM analysis were further analyzed using ImageJ software (National Institutes of Health, http://rsbweb.nih.gov/ij/) for measuring particle size and counting the particles in the images.
RESULTS AND DISCUSSION
Effect of Solute Concentration in Printed Solution on Microparticle Size-Distribution
The effect of varying the concentration of GDL in the printed solution on the resulting microparticle size-distribution was investigated by printing aqueous solutions ranging from 1–20% GDL in at least duplicate using the default inkjet printer software settings, namely plain paper and normal quality (1, 2.5, 5, 10, 12.5, 15, and 20% GDL n = 3; 7.5% GDL n = 5; 17.5% GDL n = 2). Aerosol generation took approximately 6.6 s using the default settings and was the same for all GDL solutions. The printed aerosol was drawn through desiccant dryers, and the resulting solid microparticles were characterized using an APS to yield both microparticle size and number collected. displays a representative subset of the mean microparticle APS size-distribution raw data results for the different GDL solutions. Very few particles were collected with aerodynamic diameters above 8 μm for all tested solutions. The majority of microparticles collected from all solutions were in the range of 1–5 μm in aerodynamic diameter. The APS results for the lower concentration GDL solutions displayed multiple size-distributions, possibly as a result of particle coalescence or abnormal inkjet cartridge operation. The solutions containing more than 7.5% GDL created single size-distributions of microparticles as expected. This result is likely due to the physical properties, such as density and viscosity, of the GDL solutions. The physical properties of the more concentrated GDL solutions were more similar to the aqueous black ink that the cartridges are designed to print compared to the lower concentration GDL solutions (). Due to the undesirable multi-modal operation of the inkjet cartridge when low concentration GDL solutions were printed, the data for the 1, 2.5, and 5% GDL solutions were not examined further. Overall, the particle size-distributions created by the modified inkjet printer were generally normal distributions, making them more similar to distributions generated using a nebulizer (log-normal size-distribution) and dissimilar from monodisperse droplets generated by the VOAG.
FIG. 2 Mean APS size-distribution results for microparticles created by printing aqueous solutions with varying GDL concentrations demonstrate particle size tunability by varying solute concentration (n ≥ 2, error bars are one standard deviation).
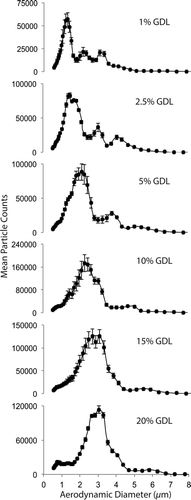
FIG. 3 Mean microparticle aerodynamic diameters generated using various GDL concentrations in the printed aqueous solutions in comparison to theoretical particle diameters from droplets 30 μm in diameter produced using the same GDL solutions (n ≥ 2, error bars are one standard deviation). Note separate y-axes for the experimental and theoretical results.
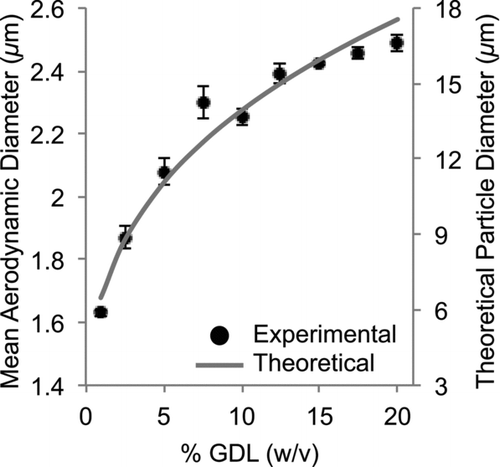
A trend in the microparticle size-distribution APS data indicated that as the GDL concentration in the printed solution increased, the size-distribution shifted towards larger microparticle aerodynamic diameters (). This was the anticipated result, as the dry microparticles measured by the APS were composed of the solute in the solution and should display a dependence on solution concentration according to:
where Dp is the dry particle diameter, C is the volumetric concentration of the nonvolatile solute in the volatile solvent, and Dd is the wet droplet diameter (Berglund and Liu Citation1973). A plot of the relationship between GDL concentration in the printed aqueous solution and the resulting mean microparticle aerodynamic diameter calculated from the APS results is displayed in , along with theoretical particle diameters resulting from droplets 30 μm in diameter containing the same concentrations of GDL (Bohorquez et al. Citation1994; Shelley et al. Citation1997). The expected power relationship according to the cube root of the solute concentration is present in both the theoretical and experimental datasets, indicating consistent droplet diameter generation despite modifications to the inkjet printer and cartridge. However, the microparticles generated using the modified inkjet printer system and aqueous GDL solutions were smaller than predicted (note the separate y-axes for the experimental and theoretical results in ). The experimental droplet diameters were calculated using the tested GDL concentrations, mean particle diameters measured using the APS, and EquationEquation (2), which yielded an average droplet diameter of approximately 5.3 μm issuing from the cartridge when aqueous GDL solutions were printed. This difference between the reported 30 μm ink droplet diameter and the observed 5.3 μm GDL solution droplet diameters is due to the lower viscosities of the tested GDL aqueous solutions (1.026–1.794 cP, ) compared to the black ink (2.918 cP). Higher viscosity solutions have longer break-off times of the exiting droplet from the solution remaining in the nozzle, resulting in more solution transferring to the droplet and therefore making the droplet larger compared to droplets of less viscous solutions (Chen et al. Citation1998).
FIG. 4 Mean microparticle size-distribution Gaussian fit results showing increasing distribution maximum positions with increasing GDL concentration and comparable size-distribution width for all GDL solutions (n ≥ 2). The mean particle counts for all samples are normalized to one for comparison. (Color figure available online.)
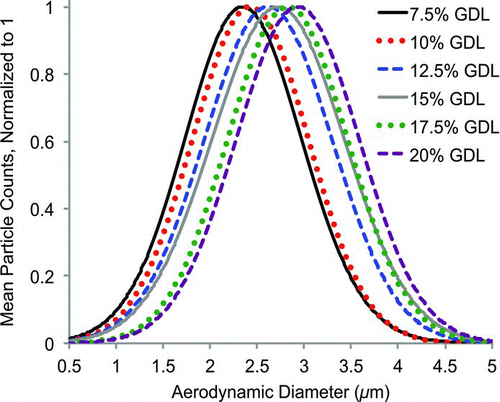
The raw APS size-distribution data from the microparticles produced using the different concentration GDL solutions were investigated further by applying the Savitzky-Golay smoothing algorithm and then fitting the smoothed data to Gaussian functions. The coefficients of determination (R 2) of the Gaussian best-fit equations to the data points were all above 0.97 for this dataset, indicating the Gaussian equations accurately represented the data (an R 2 of 1 indicates a perfect fit to the data) (Miller and Miller Citation2005). The resulting best-fit Gaussian equations, shown in , were used to determine mean microparticle size-distribution maximum positions and FWHM values for further analyses. The mean particle counts for all samples were normalized to one for more straightforward comparison, which had no effect on the size-distribution positions or FWHM values. The microparticle size-distribution maxima and FWHM values in terms of aerodynamic diameter were compared to determine statistically significant differences and solution concentration effects on the resulting microparticles. Mean size-distribution maximum values ranged from 2.35 μm (7.5% GDL) to 2.93 μm (20% GDL) aerodynamic diameter, demonstrating a 22% relative change within the dataset. One-way ANOVA determined that all GDL solution mean size-distribution maximum values differed significantly at greater than 99% confidence ( p < .01), meaning that the microparticle size-distribution significantly shifts to higher aerodynamic diameters when the GDL concentration in the printed solution is increased. Student's t-test results from pairwise comparisons of the mean size-distribution maxima of adjacent concentration GDL solutions (e.g., comparing 7.5% with 10%, 10% with 12.5%) showed that almost all solutions produced microspheres that were significantly different in size at 99% confidence ( p < .01) from the microspheres produced using other GDL solutions. The only exception was the 7.5 and 10% GDL size-distribution maxima comparison, which differed significantly at 86% confidence ( p = .137). These size-distribution results demonstrate the ability to tune the size of the microparticles created using the commercial inkjet printer by simply adjusting the solute concentration in the printed solution.
TABLE 3 Microparticle size-distribution resolutions for all tested GDL solutions, indicating considerable overlap among the different size-distributions
Mean microparticle size-distribution FWHM values in terms of aerodynamic diameter from the best-fit Gaussian equations to the data varied from 2.05 μm wide (10% GDL) to 2.34 μm wide (15% GDL), which corresponds to a 13% relative change in the dataset. One-way ANOVA analysis of the microparticle size-distribution FWHM results for each tested GDL solution determined that the means were not significantly different ( p = .103). There was no discernable trend in the FWHM results with respect to GDL concentration in the printed solution, so no pairwise statistical analyses were performed. The microparticle size-distribution resolutions (Rs ) were calculated for all possible GDL solution comparisons using EquationEquation (1), and the results are listed in . As in chromatographic peak analysis, a resolution value of 1.5 is considered complete separation, and a resolution of 1 indicates approximately 4% overlap between the two size-distributions (Skoog et al. Citation1998). The size-distributions in this dataset were not appreciably resolved, with all comparisons showing resolution values less than 0.16. This result was expected due to the large size-distribution widths relative to the change in size-distribution maximum positions between microparticles produced using different GDL solutions. The FWHM results showed that the microparticle size-distribution widths remained relatively constant despite significant changes in microparticle size due to varying GDL concentration in the printed solution. This suggested consistent printhead operation when different solutions were used for aerosol generation, which is a desirable characteristic of a system for use in generating tunable and diverse microdroplets and microparticles for a wide range of applications.
Effect of Printer Software Settings on Microparticle Size-Distribution
Different print media require different ink droplet characteristics to produce the same degree of optical density and image resolution. Therefore, the inkjet printer is programmed with several different print modes selectable within the commercial software that yield droplets with the desirable characteristics for the specified print media and image quality (Bohorquez et al. Citation1994). The availability of different paper type and printing quality options suggested that the printed droplet characteristics would be altered depending on which settings were chosen. The paper type and print quality software settings investigated to determine if tunable microparticle size-distributions could be produced are listed in . The time and number of cartridge carriage passes used by the printer to execute the same print job using the different software settings was measured () in order to characterize this novel aerosol generator. All printing times were less than 4 min, and most were less than 1 min, demonstrating the high-throughput capability of this aerosol generator. As expected, the printing was executed most rapidly when the fast draft setting was employed, and the highest quality print modes took the most time, with higher numbers of cartridge passes and longer drying times between passes.
TABLE 4 The number of cartridge carriage passes and time expended by the modified inkjet printer to execute the same print job to generate aerosols using various paper type and print quality software settings (n = 3, mean ± one standard deviation)
FIG. 5 Mean size-distribution results from APS measurements of microparticles generated by printing 15% GDL solution using (a) plain paper, (b) photo paper, (c) inkjet paper, and (d) transparency film settings along with the associated print quality settings available in the commercial printer software (n ≥ 3, error bars are one standard deviation).
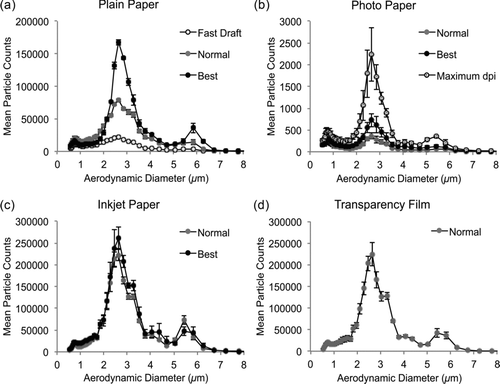
The 15% GDL solution was printed with the different paper type and print quality settings in at least triplicate (photo paper, normal quality n = 5; photo paper, best quality n = 4; all other settings n = 3), and a summary of the APS size-distribution results for the generated microparticles is shown in . The microparticles produced when the plain and photo paper settings were used displayed differences according to print quality setting. The plain paper results showed that the lowest quality setting (fast draft) produced the fewest number and smallest aerodynamic diameter microparticles, the moderate quality setting (normal) generated more and larger microparticles, and the highest quality setting (best) produced the most and largest microparticles. Similar results were observed when the photo paper setting was tested. When the print quality was increased from normal (lowest quality) to maximum dpi (highest quality), more and larger microparticles were produced. These results were expected, as the main differences between the programmed print modes for the inkjet printer are the number of cartridge carriage passes () and the optical density of the black ink, where higher quality print modes require more passes that deposit more and larger droplets compared to low-quality print modes (Hall et al. Citation1994). The number of microparticles produced was much lower overall when the photo paper setting was used compared to the plain paper setting, which was expected as the glossy photo paper should require much less ink to achieve the same optical density levels as on more porous plain paper when printing with black ink.
The microparticle size-distribution results for the remaining two paper settings tested, inkjet paper and transparency film, were similar for both paper settings and both quality settings (). The lack of difference in the produced microparticle characteristics when using the normal and best quality settings with inkjet paper indicated a common printing mechanism for the two conditions. These results agree with the timing data in , where the same number of cartridge passes were employed to generate droplets for the inkjet paper and transparency film, with the transparency film and best quality setting for the inkjet paper just taking longer with more drying time between passes. The number and aerodynamic diameter of the microparticles generated for inkjet paper and transparency film were both comparable to the results obtained when the plain paper, best quality setting was used, which was anticipated for the inkjet paper. It was expected that the size-distribution results for microdroplets printed onto transparency film would resemble the results for the photo paper setting. This was not observed, however, as the transparent media needs to be made opaque by the dense application of ink during printing, which requires a larger droplet number and size, similar to those generated for porous papers. Overall, the programmed print modes in the commercial software executed by the inkjet printer appeared to be achieving the desired printed droplet features based on the time for aerosol production and the characteristics of the generated microparticles. The number of particles generated using the various software settings indicated that the photo paper option is unsuitable for high-throughput applications, while all other print media options yield high-throughput aerosol generation.
The mean best-fit Gaussian equations to the smoothed data were used to determine microparticle size-distribution maximum positions and FWHM values for statistical evaluations of the effects of varying the commercial printer software settings. The Gaussian best-fit equations for this dataset all had R 2 above 0.90, with most greater than 0.95, indicating the equations were accurately representing the data (Miller and Miller Citation2005). Mean size-distribution maximum values for this dataset ranged from 2.57 μm (plain paper, fast draft quality) to 2.77 μm (plain paper, best quality), which represents an 8% relative change in the dataset. One-way ANOVA showed that the mean size-distribution maxima values varied significantly at 99% confidence ( p < .01) when the printer settings were varied. This result was due to small standard deviations within replicate analyses. Changing the printer settings had a lesser effect on the resulting microparticle size in comparison to the first dataset where the GDL concentration in printed solution was varied (22% relative change). When the experimental printer settings were ranked according to mean size-distribution maximum value, no trend relating the produced microparticle size to the printer settings was observed. Microparticle size-distribution maximum results were also compared within the individual paper types separately using one-way ANOVA. Significant differences were observed only for the plain paper type, where the mean size-distribution maxima produced using the different quality settings were significantly different at 99% confidence ( p < .01). Overall, these results indicate that while the produced microparticle size-distribution maxima may shift slightly (8%) when different printer software settings are employed, the size is more appreciably changed by modifying the solute concentration in the printed solution (22%), as demonstrated in the previous section. Any undesirable change in the size of the microparticles as a result of changing the printer software settings to tune the size-distribution width could easily be remedied by slightly adjusting the solute concentration.
FIG. 6 Mean microparticle size-distribution Gaussian fit results for 15% GDL solution printed using different paper type and print quality settings (n ≥ 3), arranged in ascending order according to mean FWHM value. The mean particle counts for all samples are normalized to one, and all size-distribution maxima are aligned to zero for comparison. These results demonstrate the ability to tune the width of the generated microparticle size-distribution by altering the commercial printer software settings used during production. (Color figure available online.)
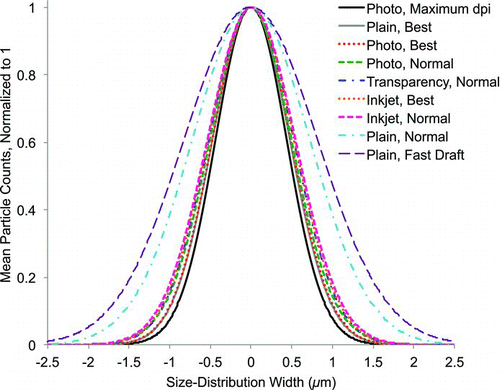
Figure 6 shows the mean best-fit Gaussian equations to the smoothed APS size-distribution data of microparticles generated using varying printer software settings. The number of particles generated for each sample was normalized to one and the size-distribution maximum positions are all aligned at zero for more straightforward comparison, as the size-distribution maxima remained relatively constant within this dataset. Mean size-distribution FWHM results spanned from 1.47 μm wide (photo paper, maximum dpi quality) to 2.74 μm wide (plain paper, fast draft quality), displaying a 68% relative change within the dataset. One-way ANOVA revealed significant differences in the mean FWHM values at 99% confidence ( p < .01) for the microparticles generated using varying printer software settings. Changing the printing parameters had a much larger effect on the resulting microparticle size-distribution width compared to changing the GDL concentration in the printed solution (13% relative change). This result was reasonable, as aiming to generate images on different media with varying degrees of perceived print quality requires changing the way the printhead functions, while simply adjusting the solute concentration is not expected to have a large effect on the way the droplets are generated. When the printer software settings were ranked according to mean size-distribution FHWM values, a trend was observed that was consistent with expectations based on printhead operation. The microparticles produced using the photo paper, maximum dpi quality setting had the narrowest size-distribution (smallest FWHM), and the widest size-distribution (largest FWHM) was produced using the plain paper, fast draft quality setting. Within each individual paper type, the higher quality settings produced narrower size-distributions, which was true for all paper types. Finally, the resolutions of all microparticle size-distributions from this dataset were calculated according to EquationEquation (1). The resolution results listed in show that the size-distributions were not appreciably resolved, with resolution values less than 0.06. This was expected, as the size-distribution maxima positions changed a relatively small amount within this dataset, and some of the printer settings produced relatively wide size-distributions. Overall, the ability to tune the size-distribution width of a generated aerosol by varying the commercial printer software settings was demonstrated. More monodisperse microparticle populations were generated using the highest quality print settings, which is often desirable. However, some applications require a more polydisperse but still controlled aerosol size-distribution, which is also achievable using the lowest quality print settings available in the COTS inkjet printer software.
TABLE 5 Size-distribution resolutions for microparticles created using various printer settings, indicating substantial overlap among the different size-distributions
The experiments discussed above demonstrated the ability to tune the size of microparticles produced using a commercial inkjet printer by varying the concentration of the solute in the printed solution, as well as the size-distribution width by changing the printer software settings. Changing these parameters also typically altered the number of microparticles collected during each experiment and the duration of microdroplet generation, which are also parameters of interest when generating an aerosol or microparticle population for an application. The number of microparticles generated during an experiment is easily managed by printing different images from the computer. More microdroplets will be produced over a longer timespan when a larger image is printed, as the printer needs to cover a larger area on the print media. Large-scale, high-throughput production is also achievable by printing multiple pages covered almost completely by large black rectangles as the printed image. The same image was printed for all experiments during this study for experimental consistency, but changing the image printed is a straightforward method to tune the number of microparticles produced and the duration of production.
The microparticles generated during all experiments in this study were polydisperse to a limited extent (± ∼1 μm), which was likely due to the mechanical capabilities of the COTS inkjet cartridges as well as the software designed to operate them. Inkjet cartridges are manufactured to produce droplets that fall within a specified volume range, so some variation is expected among the approximately 300 nozzles in the cartridge. For example, the size of the refill channel for each nozzle may vary slightly. Variability tends to increase when continuous printing is employed, as was the case in the present study where the goal was to create a large and representative microparticle population. When droplets are ejected in close succession, differences in the meniscus position over the exit nozzle due to rapid refilling may cause slight volume differences in the microdroplets produced. Also, as the printed solution is depleted, the backpressure in the cartridge decreases, yielding droplets with smaller volumes compared to the initially printed droplets, as the nozzles do not completely refill. Finally, as the temperature of the cartridge increases during continuous printing, the resulting droplet volumes also increase, an effect called thermal inkjet heating. The printhead is always heated to a designated temperature set-point customized for each printing mode before printing begins to correct for this effect, which is likely the source of the differing size-distribution widths when different printer software settings are used (Bohorquez et al. Citation1994).
FIG. 7 Micrographs taken during SEM analysis showing (a) the large number and overall uniformity of the GDL microparticles produced using the inkjet printer and (b) the size and morphology of individual microparticles, which agrees with the corresponding APS results (c).
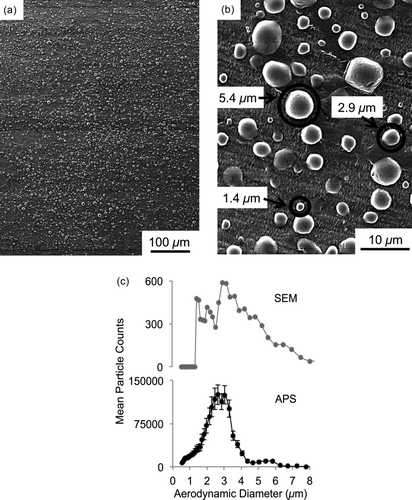
Apart from the effects of the inkjet cartridges, software control algorithms also create the controlled polydispersity observed in the generated microparticles. The firmware- and hardware-based algorithms for generating images using the inkjet printer can be used to enhance edge smoothness and generate sharper-looking images by placing dots between the basic grid points or by changing the dot size (Bohorquez et al. Citation1994). As the image printed for this study's experiments was a black rectangle, the edges may have been smoothed in this manner, resulting in microparticles with different sizes. Also, the cartridge thought it was printing overlapping swaths of solid black to achieve the printed image, so it is possible that the nozzles in the center of the printhead were programmed to produce more and larger droplets compared to the nozzles at the edges of the printhead so that the overlapping swath areas would not become oversaturated. These design components of the inkjet cartridges and software control algorithms led to controlled and reproducible polydispersities in the generated microparticle populations. The degree of microparticle polydispersity observed in these experiments for the COTS inkjet printhead is acceptable for many applications and was comparable to or better than the polydispersity observed using commercial aerosol production methods.
SEM of Generated Microparticles
SEM was used to confirm the APS size-distribution results by examining the morphology of the microparticles generated using the commercial inkjet printer. Microparticles created by printing 15% GDL solution using plain paper, normal quality (default) printer settings were collected on a filter using an impactor. Micrographs from SEM analysis are displayed in , along with a size-distribution comparison between the SEM and APS data from . The image on the left was obtained using relatively low magnification in order to observe the general characteristics of the collected microparticle population. The large number of microparticles created and collected was expected and confirmed the high-throughput capability of this aerosol and microparticle generating technique. There was a uniform variability of size and shape in the microparticle population, which demonstrated the consistency of the inkjet printer production method. There was also no evidence of particle aggregation, indicating that the solvent is sufficiently evaporated before collection and analysis, resulting in dry microparticles composed of the solute material.
The image on the right in was obtained using increased magnification SEM to more precisely visualize the size and shape of the microparticles. The morphology of the microparticles is generally spherical as anticipated, with some displaying slightly oval or cubic features. The microparticle sizes in the images were manually assessed using display features of the software. The collected sample contained microparticles approximately 1–5.5 μm in diameter, with the majority in the range of 1.5–4 μm in diameter. The size-distribution generated using the SEM images generally agrees with the APS data, although three orders of magnitude less particles were analyzed using the SEM method, leading to an exaggeration of the contribution of particles with diameters greater than 5 μm. Also, the SEM samples were made using an impactor with a stage cutoff of 0.7 μm, so no particles smaller than that were collected for imaging as they passed to the next impactor stage. Overall, these SEM results indicated that spherical microparticles were generated by dehydrating microdroplets produced using a commercial inkjet printer, and that the microparticle size-distribution characteristics measured using the APS were accurate.
SUMMARY AND CONCLUSIONS
This study demonstrated the successful use of widely available commercial inkjet printers and software to produce tunable and well-characterized aerosol size-distributions in an easily controlled manner. Simple modifications to COTS inkjet printers and cartridges facilitated cost-effective production of aerosols that were tunable in number, size, and size-distribution width. Aerosols generated using an inkjet printer with varying experimental parameters were dehydrated into solid microparticles for analysis using an APS to determine the size-distribution characteristics. The microparticles created using the inkjet printer were predominantly 1–5 μm in aerodynamic diameter, with the size-distribution maximum position and width depending on the printed solution concentration and the commercial software settings used to execute the print job. The morphology of the created microparticles was determined to be spherical using SEM, which also confirmed the APS size-distribution results.
Depending on the desired application, aerosols and microparticles with a variety of properties may be produced using the commonly available inkjet printer. When large microparticles are needed, higher solute concentrations in the printed solution should be used to generate the microparticles. If the goal is a narrow particle size-distribution, the highest quality print settings available in the commercial operating software should be employed. When high-throughput aerosol generation is necessary, the transparency, inkjet, or plain paper software settings will all yield the desired results. The customizable aerosols and microparticles produced using these commonly accessible inkjet printer systems displayed diverse properties suitable for a wide range of experimental applications in aerosol research and other fields of study.
Acknowledgments
This work was performed under the auspices of the U.S. Department of Energy by Lawrence Livermore National Laboratory under Contract DE-AC52-07NA27344 and was supported by the Defense Threat Reduction Agency (contract DTRA10027-4691) and the Lawrence Livermore National Laboratory Lawrence Scholar Program. LLNL release number: LLNL-JRNL-558133.
REFERENCES
- Berglund , R. N. and Liu , B. Y. H. 1973 . Generation of Monodisperse Aerosol Standards . Environ. Sci. Technol. , 7 : 147 – 153 .
- Bohorquez , J. H. , Canfield , B. P. , Courian , K. J. , Drogo , F. , Hall , C. A. E. Holstun , C. L. 1994 . Laser-Comparable Inkjet Text Printing . Hewlett-Packard J. , 45 : 9 – 17 .
- Bottiger , J. R. , Deluca , P. J. , Stuebing , E. W. and VanReenen , D. R. 1998 . An Ink Jet Aerosol Generator . J. Aerosol Sci. , 29 : S965 – S966 .
- Buehner , W. L. , Hill , J. D. , Williams , T. H. and Woods , J. W. 1977 . Application of Ink Jet Technology to a Word Processing Output Printer . IBM J. Res. Dev. , 21 : 2 – 9 .
- Buskirk , W. A. , Hackleman , D. E. , Hall , S. T. , Kanarek , P. H. , Low , R. N. Trueba , K. E. 1988 . Development of a High-Resolution Thermal Inkjet Printhead . Hewlett-Packard J. , 39 : 55 – 61 .
- Carnahan , R. D. and Hou , S. L. 1977 . Ink jet technology . IEEE T. Ind. Appl. , 13 : 95 – 104 .
- Chen , P. H. , Chen , W. C. , Ding , P. P. and Chang , S. H. 1998 . Droplet Formation of a Thermal Sideshooter Inkjet Printhead . Int. J. Heat Fluid Fl. , 19 : 382 – 390 .
- Childers , A. G. and Hieftje , G. M. 1986 . An Improved Uniform-Size-Droplet Generator . Appl. Spectrosc. , 40 : 688 – 691 .
- Dougherty , G. M. , Hadley , D. R. , O’Connor , P. R. and Bottiger , J. R. 2007 . “ Engineered Aerosol Production for Laboratory Scale Chemical/Biological Test and Evaluation ” . Report no. UCRL-TR-230829, Lawrence Livermore National Laboratory, Livermore, CA, USA. Available at https://e-reports-ext.llnl.gov/pdf/347374.pdf
- Fittschen , U. E. A. , Bings , N. H. , Hauschild , S. , Forster , S. , Kiera , A. F. Karavani , E. 2008 . Characteristics of Picoliter Droplet Dried Residues as Standards for Direct Analysis Techniques . Anal. Chem. , 80 : 1967 – 1977 .
- Fittschen , U. E. A. , Hauschild , S. , Amberger , M. A. , Lammel , G. , Streli , C. Forster , S. 2006 . A New Technique for the Deposition of Standard Solutions in Total Reflection X-Ray Fluorescence Spectrometry (TXRF) Using Pico-Droplets Generated by Inkjet Printers and its Applicability for Aerosol Analysis with SR-TXRF . Spectrochim. Acta B , 61 : 1098 – 1104 .
- Fletcher , R. A. , Brazin , J. A. , Staymates , M. E. , Benner , B. A. and Gillen , J. G. 2008 . Fabrication of Polymer Microsphere Particle Standards Containing Trace Explosives Using an Oil/Water Emulsion Solvent Extraction Piezoelectric Printing Process . Talanta , 76 : 949 – 955 .
- Hall , C. A. E. , Scandalis , A. R. , Broder , D. W. , Moore , S. I. , Movaghar , R. Rhoads , W. W. 1994 . Inkjet Printer Print Quality Enhancement Techniques . Hewlett-Packard J. , 45 : 35 – 40 .
- Hauschild , S. , Lipprandt , U. , Rumplecker , A. , Borchert , U. , Rank , A. Schubert , R. 2005 . Direct Preparation and Loading of Lipid and Polymer Vesicles Using Inkjets . Small , 1 : 1177 – 1180 .
- Hieftje , G. M. and Malmstadt , H. V. 1968 . A Unique System for Studying Flame Spectrometric Processes . Anal. Chem. , 40 : 1860 – 1867 .
- Jain , R. , Shah , N. H. , Malick , A. W. and Rhodes , C. T. 1998 . Controlled Drug Delivery by Biodegradable Poly(ester) Devices: Different Preparative Approaches . Drug Dev. Ind. Pharm. , 24 : 703 – 727 .
- Kamphoefner , F. J. 1972 . Ink Jet Printing . IEEE T. Electron Dev. , 19 : 584 – 593 .
- Magarvey , R. H. and Taylor , B. W. 1956 . Apparatus for the Production of Large Water Drops . Rev. Sci. Instrum. , 27 : 944 – 947 .
- Miller , J. N. and Miller , J. C. 2005 . Statistics and Chemometrics for Analytical Chemistry (5th Ed.) , 142 – 144 . Harlow , , UK : Pearson Education Limited .
- Rubinson , K. A. and Rubinson , J. F. 2000 . Contemporary Instrumental Analysis , 373 – 374 . Upper Saddle River , NJ : Prentice-Hall . 617
- Sangiovanni , J. J. and Labowsky , M. 1982 . Burning Times of Linear Fuel Droplet Arrays: A Comparison of Experiment and Theory . Combust. Flame , 47 : 15 – 30 .
- Savitzky , A. and Golay , M. J. E. 1964 . Smoothing and Differentiation of Data by Simplified Least Squares Procedures . Anal. Chem. , 36 : 1627 – 1639 .
- Sergeyev , A. V. and Shaw , R. A. 2006 . An Inexpensive Uniform-Size Aerosol Generator . Meas. Sci. Technol. , 17 : N41 – N44 .
- Seymour , R. J. and Boss , C. B. 1983 . Design Modification for a Uniform Droplet Generator System . Appl. Spectrosc. , 37 : 375 – 379 .
- Shelley , D. J. , Majewski , J. T. , Thackray , M. R. and McWilliams , J. L. 1997 . A Lower-Cost Inkjet Printer Based on a New Printing Performance Architecture . Hewlett-Packard J. , 48 : 6 – 11 .
- Skoog , D. A. , Holler , F. J. and Nieman , T. A. 1998 . Principles of Instrumental Analysis , 688 Pacific Grove , CA : Brooks/Cole Thomson Learning .
- Stemme , E. and Larsson , S. G. 1973 . The Piezoelectric Capillary Injector- a New Hydrodynamic Method for Dot Pattern Generation . IEEE T. Electron Dev. , 20 : 14 – 19 .
- Sweet , R. G. 1965 . High Frequency Recording with Electrostatically Deflected Ink Jets . Rev. Sci. Instrum. , 36 : 131 – 136 .
- Threadgill , E. D. , Williamson , R. E. and Miles , G. E. 1974 . Development of Controlled-Size Droplet Generators . T. ASAE , 17 : 837 – 840 .
- Trunk , M. , Lankers , M. , Popp , J. and Kiefer , W. 1994 . Simple and Inexpensive Design for a Uniform-Size Droplet Generator . Appl. Spectrosc. , 48 : 1291 – 1293 .
- Wang , Y. , Bokor , J. and Lee , A. 2004 . Maskless Lithography Using Drop-on-Demand Inkjet Printing Method . P. Soc. Photo-Opt. Ins. , 5374 : 628 – 636 .
- Yang , J. C. , Chien , W. , King , M. and Grosshandler , W. L. 1997 . A Simple Piezoelectric Droplet Generator . Exp. Fluids , 23 : 445 – 447 .