Abstract
A new primary standard method for calibrating optical particle counters (OPC) has been developed based on quantitative gravitational deposition on a silicon wafer and accurate counting of the particles by a wafer surface scanner (WSS). The test aerosol consists of 3-μm diameter monodisperse polystyrene latex (PSL) spheres at concentrations in the range of 0.1 cm−3 to 1 cm−3. A key element to the calibration is the ability to generate monodisperse PSL spheres without residue particles by use of a virtual impactor and differential mobility analyzer. The use of these devices reduced the percentage of residue particles from more than 99.98% to about 5%. The expanded relative uncertainty (95% confidence level) in the number concentration determined with a WSS for a deposition of 200 particles is 17.8%. The major uncertainty component arises from the Poisson fluctuations in the aerosol concentration because of the low concentration. This methodology has advantages of a fast scanning time by the WSS of minutes compared to hours or days by microscopy and of counting every particle deposited compared to often only a small fraction via microscopy.
The WSS was used in the calibration of an OPC based on 12 depositions with concentrations ranging from 0.1 cm−3 to 1 cm−3 for each deposition. Make-up air was added to the aerosol entering the OPC so that the lowest achievable concentration for the OPC measurement is about 0.01 cm−3 in this study. The detection efficiency of the OPC was measured to be 0.984 with an expanded uncertainty of 13.4%.
Copyright 2014 American Association for Aerosol Research
INTRODUCTION
Optical particle counters (OPCs) are widely used to measure aerosol size distribution and number concentration in the size range of approximately 0.1 μm to 30 μm by means of light scattering from single particles. The OPCs are applied to low-concentration measurements such as clean room or ambient particulate matter (PM) monitoring, and to high-concentration industrial aerosols, e.g., industrial filtration. There is also interest in the accurate calibration of OPCs at very low concentrations (0.01 cm−3 to 1 cm−3) of particles in the 1 μm–5 μm size range in terms of their use for measuring the concentration of virulent biological structures. For the U.S. military, there is an interest in having the calibration be traceable to SI units realized by the National Institute of Standards and Technology (NIST). This requirement is in support of current and future biological agent detectors.
The OPC operates by drawing a stream of aerosol through a focused light beam into the measurement region at a controlled flow rate. Light scattered from single particles are collected and directed to a photodetector, where they are converted into proportional voltage pulses to size the particles based on a calibration curve. Particle number concentration is derived by counting the pulses. The development and performance of OPCs is reviewed by Sorensen et al. (Citation2011) and the application of OPCs to atmospheric aerosols is reviewed by McMurry (Citation2000).
As described earlier, the operation of an OPC doesn't initially appear to require any calibration beyond the volumetric flow rate when determining number concentration. That is, if every particle flows through the intense portion of the focused beam, then each particle would be detected as a voltage pulse above the background. For particle concentrations below 1 cm−3, the probability of two particles being in the beam at the same time is negligibly small. How can the OPC fail? There can be a misalignment of the focused beam relative to the aerosol stream or particles in the scattering volume may be recirculated so that some of particles are not counted or some are double counted. There can also be a loss of the particles between the inlet and the focused beam. A failure of the electronic counting circuitry is also a possibility, but this has seldom been a problem in practice. It is also crucial that the flow be accurately known. For cases where there is a sheath flow, it is critical that the sheath flow keep the aerosol in the focused beam and that it not create any mixing. While these effects discussed earlier have a low probability, it is still essential to be able to verify the correct performance of the instrument. Ideally, this would be done with a measurement traceable to the SI units. Traceability to SI units through a calibration method is also necessary to fulfill regulatory requirements of institutions that require traceability.
One approach has been to calibrate OPCs using a standard OPC. Gebhart et al. (Citation1983) measured the counting efficiency of 11 OPCs using two aerosol-size spectrometers developed in their laboratory over the size range of 0.5 μm to 4 μm and concentration range of approximately 20 cm−3 to 500 cm−3. The measurements made with these instruments differed by at most 5% from parallel measurements with an independent method based on the electrostatic deposition of the particles. Peters et al. (Citation2006) used a time-of-flight instrument, Aerodynamic Particle Sizer or APS (TSI, Inc.), as their reference standard instrument. The APS was independently calibrated by collecting fluorescent polystyrene latex (PSL) spheres on a filter in parallel with the APS measurements (Volckens and Peters Citation2005). The size of the monodisperse PSL spheres ranged from 1 μm to 4 μm and the aerosol concentrations from 0.5 cm−3 to 50 cm−3. No statement of the uncertainty in the number concentration measurement is given; the error bars in the calibration plots indicate a 3% to 8% uncertainty.
While the calibration methods used by both Gebhart et al. (Citation1983) and by Volckens and Peters (Citation2005) are valid approaches, there is a lack of information to replicate the approach or to make a quantitative assessment of the uncertainty in the counting efficiency (number concentration). In addition, the minimum concentration is on the order of the maximum concentration of interest in the current study. Such a low concentration is below the limit for the fluorometric measurements by Volckens and Peters and may also be too low for the electrostatic deposition measurements of Gebhart et al. (Citation1983).
It is of interest that the condensation particle counter, which is also based on light scattering by particles, was calibrated by measuring the electrical current for singly charged particles (Liu and Pui Citation1974). This is a traceable calibration, since the current can be related to the standard ampere. Unfortunately, this calibration is only accurate for particle concentrations of at least 5000 particles/cm3.
In performing a primary calibration of a condensation particle counter, Fletcher et al. (Citation2009), in addition to measurements of electronic current for singly charged particles, deposited the calibration aerosol on a filter to determine the concentration. For each filter, a minimum of 600 particles were sized with a scanning electron microscope (SEM). The combined uncertainty in the filter collection method was about 3% including the uncertainties for the counting statistics, volumetric flow, the field of view area for the SEM, and the effective area of the collection filter.
Our new proposed concentration measurement is qualitatively similar to that of Fletcher et al. (Citation2009). The particles are first collected on a surface and then are counted. The difference is that the particles are collected on a silicon wafer in a deposition chamber via gravity rather than on a filter, and all of the particles are counted using a wafer surface scanner (WSS) instead of counting particles in selected fields of view using an electron microscope. This would likely be a very challenging task to do even once via microscopy let alone carried out for a large number of filters. This is why we elected to use WSS technology which is designed to scan and count all the particles on a 20-cm diameter wafer in about 1 min.
This calibration method is intended for primary calibration laboratories that would calibrate “references OPCs,” which would then be used to calibrate other OPCs. While there is a significant cost for the calibration system relative to the cost of an OPC, the calibration system provides a method to perform an absolute calibration of the OPC. Furthermore, the calibration can be made traceable to measurement standards realized at NIST or other national measurement institutes, which is a regulatory requirement for some institutions, e.g., the U.S. Army. Thus, the intended benefit is a measurement system that allows for legal or accredited calibration of the concentration measurement of an OPC, along with an improvement in the accuracy of OPC measurements by the community of OPC users.
This article focuses on developing a particle concentration measurement method with a quantitative uncertainty and applying this method to the calibration of an OPC with test aerosols in the concentration range of 0.1 cm−3 to 1 cm−3. The general approach for the calibration is to generate a monodisperse 3 μm PSL aerosol without residue particles and split the flow with half going to the OPC to be calibrated and half to the deposition chamber. The key topics of the article are the following: minimizing the number of residue particles, design and performance of the deposition chamber and flow splitter, performance of the wafer surface scanner, and uncertainty analysis.
METHODOLOGY
Generation of Monodisperse 3-μm Spheres Without Residue Particles
In our application, it is important that the aerosol be narrowly distributed 3-μm polystyrene latex (PSL) spheres without residue particles. If the residue particles were not eliminated, the WSS would be saturated by their presence. Residue particles result from the evaporation of droplets without PSL spheres. The nonvolatile impurities including the surfactant and salts from the PSL suspension create residue particles when the droplets evaporate. The concentration of the residue particles are on the order of 106 cm−3 to 107 cm−3, while the size of the residue particle can range from less than 10 nm to more than 1 μm for droplets of size 20 μm.
We used a three-prong approach to minimize the residue particles: centrifuge the particle suspension, pass the aerosol through a virtual impactor to concentrate the 3-μm particles prior to size classification, and then pass it through a differential mobility analyzer (DMA). The suspension was prepared by mixing 40 drops of a 0.5% by mass suspension of 3-μm PSL spheres (Thermo Scientific, 3.00-μm number average diameter with a standard uncertainty of 0.04 μm and a standard deviation of the size distribution equal to 0.03 μm) with 10 ml of filtered–deionized water. The suspension was centrifuged at 4500 rpm for 5 min. The clear liquid was poured off, and the concentrated particles were diluted with deionized water which had been passed through a 50-nm pore-size final filter. This procedure was repeated three times to reduce the size of the residue particles. The suspension was nebulized (HUDSON RCI, Cat. No. 1700) and the droplets then passed through two driers. As shown in , one Po-210 radioactive neutralizer was placed before the driers to reduce the highly charged nebulizer droplets and the second was placed after the drier to provide a Boltzmann charge distribution for the PSL spheres before entering the DMA. The nominal 3-μm particle concentration exiting the drier was on the order of 10 cm−3.
FIG. 1. Schematic of the system for calibrating an OPC by depositing 3-μm PSL spheres on a silicon wafer. Additional instrumentation used for optimizing the virtual impactor performance and for determining the reduction in residue particles by the DMA is indicated by the dashed lines.
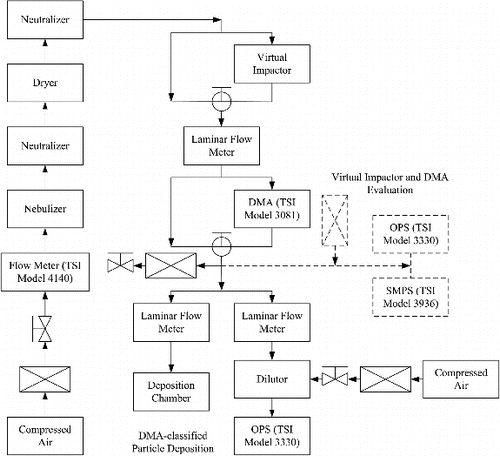
To select only the 3-μm spheres, a DMA (TSI Model 3081) was used downstream of the driers. The DMA was operated at a 23.3 cm3/s sheath flow rate and at a 5.0 cm3/s aerosol flow rate which was monitored by the laminar flow meter upstream of the DMA. A low flow is required because of the large particle size being selected. The doubly charged particles 3-μm spheres are selected for this flow condition with a 10,000 V (DMA) setting. The concentrations and size distributions of classified particles were then measured with an optical particle counter (TSI OPS 3330) to evaluate the performance of DMA classification for 3-μm PSL particles. A three-way valve was used to switch the aerosol stream upstream and downstream of the DMA. It was found that the concentration exiting the DMA was about a factor of 50 lower than the inlet concentration and had a value of about of about 0.2 cm−3 for the operating conditions described earlier.
To increase the concentration of 3-μm PSL spheres, a virtual impactor was inserted before the DMA. The design of the impactor shown in was based on the theoretical study by Marple and Chien (Citation1980) and the experimental study by Loo and Cork (Citation1988). The Reynolds number is 2357 based on a total flow of 50 cm3/s and a nozzle diameter of 0.18 cm and the Stokes number for the 3-μm PSL spheres with a density of 1.04 is 0.67. The 3 μm PSL spheres have sufficient inertia to “virtually impact” into the collection volume () where they are carried with the minor flow of 5.83 cm3/s to the DMA. The residue particles are carried away from the radial jet by the major air flow. Also, a fraction of the residue particles will be present in the minor air flow. A three-way valve was used to switch the air flow upstream and downstream of the virtual impactor. The aerosol stream bypassed the DMA and was introduced into the OPC for aerosol size distribution measurements. shows typical particle size distributions upstream and downstream of the virtual impactor for nebulized 3-μm PSL spheres. Downstream particle concentration of the 3-μm size channel was about eight times higher than the upstream. This was a significant increase.
FIG. 3. Particle concentration with respect to particle diameter for the aerosol upstream and downstream of the virtual impactor operated at a total flow rate of 50 cm3/s and a minor exit flow rate of 5.83 cm3/s.
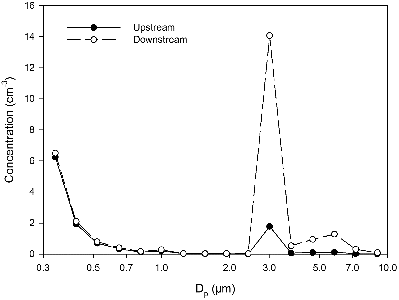
An attempt was also made to measure the size distribution of the residue particles with a scanning mobility particle sizer (SMPS) after the DMA at an aerosol generator flow of 50 cm3/s, but the number of counts for sizes ranging from 20 nm to 320 nm was at most 1 over a 20-min period. Our upper bound estimate of the residue particle concentration is 0.01 cm−3 compared to 3200 cm−3 without the DMA. With the virtual impactor and DMA in place, the concentration of 3-μm PSL spheres generated was in the range of 0.1 cm−3 to 1.0 cm−3, which exceeds the concentration of residue particles by a factor of 10 to 100. Without these components, the residue concentration was more than 100 times the concentration of 3-μm spheres.
Size distribution measurements of the 3-μm PSL spheres were also performed with and without centrifugation using the OPC. There is a single peak at 3 μm with centrifugation while without centrifugation there is a second peak near 2 μm presumably arising from a singly charged residue particle with the same mobility as the doubly charged 3-μm PSL sphere.
Gravitational Deposition Chamber
Electrostatic deposition of monodisperse calibration particles has been widely used for the calibration of WSS for particle sizes smaller than about 1 μm (Pui et al. Citation1990; Yook et al. Citation2008). For spheres 3 μm and larger, the gravitational settling velocity was estimated to be large enough to deposit all the spheres onto a silicon wafer without the need for an electric field. The key parameters for the estimate were a 20-cm diameter wafer, a gap of 5 mm between the cover plate and the wafer, and a flow of 1.67 cm3/s. shows a drawing of the settling chamber, including the cover plate, base plate, toggle clamps, and wafer tray. The aerosol containing the 3-μm PSL particles first enters the top inlet tube, which is located at the center of the cover plate and normal to the wafer. The base plate centers and supports the cover plate with a machined groove. This places the aerosol inlet directly over the center of the wafer tray so that the aerosol flows over the middle of the wafer. Four toggle clamps are placed on the corners of the base plate to allow for rapid insertion and removal of the wafer (20 s). This is important to minimize contamination from particles in the clean room. The chamber contains two exhaust ports on opposite sides of the chamber through which the airflow exits the deposition chamber. A notch in the wafer tray allows the operator to remove the silicon wafers with minimum contamination. Small tweezers allow the operator to slightly lift the wafer so a wafer wand may secure it for removal.
FIG. 4. Schematic of the deposition chamber. The outlets are indicated by the dotted lines near the two arrows.
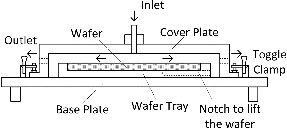
The volume of a deposition chamber increases as the radius squared; therefore, for a uniform radial flow (URF), the gas velocity decreases inversely with the radius squared. The largest settling radius, rmax, corresponds to the radius at which a particle entering the chamber just below the cover would settle to the wafer surface. For URF, one obtains the following expression for the largest settling radius:[1] where Q is the aerosol volumetric flow rate and vTS is the terminal gravitational settling velocity. At volumetric flow rates of 1.8 cm3/s and a settling velocity of 0.0286 cm/s, the settling radius is 4.5 cm.
Flow Splitter
also presents the experimental setup for the DMA-classified particle deposition using a settling chamber. The particle generation and classification sections were the same as described earlier for the virtual impactor and DMA evaluation. All the components in the setup were oriented vertically as much as possible with gradual bends when necessary.
Exiting the DMA, excess aerosol was bled off until approximately a 3.3 cm3/s flow was split into near-equal parts: one entered the settling chamber for particle deposition on a wafer for 3 min to 10 min, and the other combined with a sheath-flow of makeup air in the diluter () before flowing into the OPC at 16.7 cm3/s. The flow was split using a tee fitting followed by flexible tubing, with approximately equal bends to the laminar flow elements. The pressure drop was monitored with an electronic barometer with a nominal reading of 45 Pa for a flow rate of 1.67 cm3/s. The laminar flow elements were calibrated with a positive displacement flow meter (BIOS DryCal flow meter) with an uncertainty of 1.0% of the reading for the range of interest in this study.
The diluter consists of two coaxial flows, the inner aerosol flow and the outer sheath flow that confines the aerosol to the center of the diluter. Since the OPC samples all of the flow exiting the diluter, the key feature of the diluter is in delivering all of the particles into the OPC, as opposed to providing a known dilution factor and a well-mixed aerosol to the OPC. The sheath flow of clean air at a flow of about 15 cm3/s compared to an aerosol flow of about 2 cm3/s minimizes the deposition of the 3 μm spheres on the walls of the diluter and on the outlet tubing. Kesavan et al. (Citation2014) obtained an average wall loss of 0.7% for 2.7-μm aerodynamic fluorescein particles in a flow adapter with sheath flow and overall dimensions similar to our diluter. We expect our losses to also be less than 1%, which would have a negligible effect on our uncertainty.
Wafer Surface Scanner
The performance of wafer surface scanners (WSS) has been studied both for monodisperse PSL spheres (Lee et al. Citation1991) and for real-world particles (Liu et al. Citation1993) for particle sizes less than 1 μm. The WSS collects the scattered light from individual small particles. The coordinates and the light scattering intensity are recorded for each scattering event on the wafer surface. For the KLA-SP1 Wafer Surface Scanner used in this study, the intensity measurements are sorted into eight particle size bins ranging from 1 μm to 6.5 μm. These sizes are larger than are normally used by the WSS in semiconductor facilities. A calibration curve based on electromagnetic scattering theory and calibration particles are used by the manufacturer to relate the light scattering intensity to the particle diameter. The wafer is scanned in a helical manner by rotating the wafer and translating it in the x-direction. The WSS was operated in the high-throughput mode with an elliptical spot size oriented in the x direction with dimensions 340 μm by 20 μm and a pitch of 170 μm. For this operation mode, the overlap in the helical scan results in each particle being scanned twice. This feature is also used in eliminating false counts.
The performance of the scanner was tested by performing ten repeat scans for the same wafer with 212 particles sized with counts in three bins (2.75 μm – 3.25 μm, 3.25 μm – 3.75 μm, and 3.75 μm – 4.25 μm) on wafer 4, 6/26 and 277 particles on wafer 1, 6/12. The maximum change from scan to scan was two particles for each of the two wafers.
Optical Particle Counter
The OPC (TSI Model 3330) uses a focused laser diode and an elliptical mirror to focus the scattered light onto the photodetector. These pulses are then converted into an electrical signal which is then used to size and count the particles. We used the OPC in a configuration with 16 size bins logarithmically distributed over particle sizes from 0.3 μm to 10 μm. All of the aerosol entering the OPC flows thru the sensing volume and is detected. There is a sheath flow of 13.3 cm3/s in addition to the 13.3 cm3/s aerosol inlet flow.
Calibration Measurements
All the wafers are scanned before depositing particles onto the wafer and transported from the scanner site to the clean room in a specially designed wafer transport container. After allowing for warm-up time for the electronics, the inlet flow to the nebulizer is set at 50 cm3/s, the sheath aerosol flow at 23.3 cm3/s, the exit flow from the virtual impactor, which is also the inlet aerosol flow to the DMA, at 5.0 cm3/s, and the flows to both the deposition chamber and the OPC are set to 1.67 cm3/s. The concentration of the PSL solution in the nebulizer may be adjusted if the inlet OPC concentration is not in the desired range. At this time, the tube from the laminar flow element to the deposition chamber is connected to a HEPA filter. The wafer is then transferred from the transport container to the deposition chamber using a wafer wand which holds the wafer with suction. The quick disconnect clamps and the centering groove on the wafer tray allow the transfer to take place within about 20 s. The deposition tube is then connected to the deposition chamber and particles are collected for 120 s up to 600 s. This minimizes the possibility of contamination from particles in the clean room. After the deposition, the aerosol flow is redirected to the HEPA filter. Throughout the collection periods, the OPC size distribution and the pressure transducer readings are recorded. The wafer is then removed with the wand after slightly elevating the wafer by inserting a small tweezer in the notch in the wafer holder.
This same procedure was followed but with the DMA voltage off so that no 3-μm PSL spheres are deposited and the effect of background contaminants could be assessed. Also, between depositions, the splitter Tee was rotated by 180° and the tubes connected to the rotated end of the tee to assess the effect of splitter bias on the measurements. This procedure was done between the 3rd and 4th wafers on 6/12 to get a correction factor for this day's measurements. On 6/26, the splitter tee was rotated between the 7th and 8th wafers and between the 11th and 12th wafers to get a correction factor for the second day's measurements.
RESULTS
A map of the coordinates of 3-μm spheres deposited on Wafer 4 at a deposition flow of 1.83 cm3/s for 180 s is shown in . Because of the variation of the wafer scanning beam intensity with position, the 3-μm spheres correspond to the three bins extending from 2.75 μm to 4.25 μm. The deposition area is nearly enclosed by the 4.51-cm radius circle predicted by URF flow. A series of depositions were also carried out at an increased flow rate. The deposition pattern is also shown for Wafer 11 in for a flow of 2.35 cm3/s. The observed increase in area is consistent with a URF flow prediction.
FIG. 5. Map of the x–y coordinates and size for each particle deposited on the wafer. The 3-μm spheres (small circles) are deposited within a 4.51-cm radius dashed circle at the lower flow of 1.83 cm3/s for wafer 4, 6/12 (upper map) and within a 5.11-cm radius at the larger flow of 2.35 cm3/s for wafer 5, 6/26 (lower map). The dark marks on the lower wafers indicate scratches on the wafer surface.
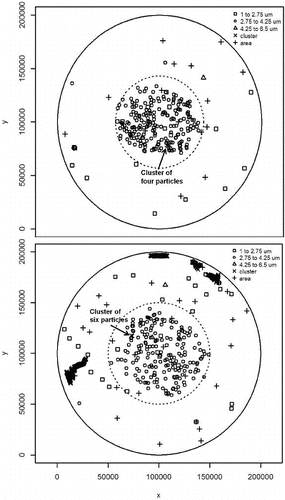
To assess the uniformity of the deposition, we define the radial density distribution ρ(r) from the center of the wafer as:[2] The averages of ρ(r) normalized by the total number of particles deposited are plotted in for nine low-flow depositions and three at a higher flow condition. There appears to be two peaks in the averaged reduced densities; however this is not a certainty because of the large value of the standard deviation for the repeat depositions. The predicted density based on URF is a constant density dropping to zero at 4.51 cm for low flow and 5.21 cm at high flow. The larger standard deviation for the first two data points is a result of only one to ten particles being deposited in a circle with a radius of 1 cm.
FIG. 6. Average fractional density of particles deposited on the wafer at lower flow (data indicated by circles) and higher flow (data indicated by squares). The error bars correspond to the standard deviations based on nine wafers for the lower flow and three wafers for the higher flow. Where the two sets of error bars overlap, the low flow error bars are larger except for the densities at 3.25 cm.
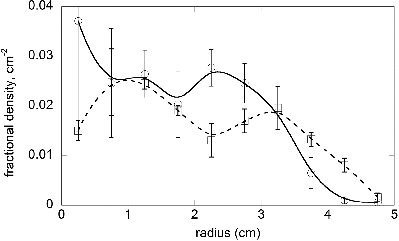
One can also obtain an estimate of the average distance between neighboring particles, , using the following expression:
[3] For Wafer 4,
, in the more uniform region between r = 1 cm and r = 3.5 cm, varied from 0.39 cm to 0.55 cm and from 0.46 cm to 0.58 cm for Wafer 11. The nearest neighbor spacing is important because if it is too small, then the scanner may count two particles as one.
The fact that the 3-μm spheres are deposited within a radius, a factor of two or less than the wafer diameter, and that the deposition area is similar to that predicted by URF gives us confidence that all the particles going through the inlet are deposited. Two 3-μm spheres are observed outside the circle for Wafer 4 and one for Wafer 11. By performing scans on bare wafers before and after being placed in the deposition chamber with no particles being generated, we find that contamination from the clean room is the likely source of these particles outside the circle.
From the scanner output of coordinates and size of each particle, we determine the total number of particles in the three bins (2.75 μm–3.25 μm, 3.25 μm–3.75 μm, and 3.75 μm–4.25 μm). For the scanner recipe that was used, each sphere in a cluster of closely spaced spheres was counted as a cluster. These are illustrated as crosses (×) in . In this case, the scanner software monitors the distance between scattering peaks and considers the structure a cluster if the peak spacing is within a few multiples of the beam size. For the set beam size with a diameter of 340 μm, particles spaced by 700 μm or less could be counted as clusters. This results in one grouping of three closely spaced particles being counted as three clusters. Thus in our analysis, we count each cluster as a single 3-μm sphere. As an example, from wafer 5, 6/26, the six-sphere cluster at x = 7.3 cm, y = 11.7 cm indicated by the cross symbol is recorded by the scanner as six clusters, which is actually one grouping of six 3-μm spheres. The separation between the spheres ranges from about 150 μm to 700 μm. Depositions with more than 15% clusters are excluded from the analysis. On some wafers such as wafer 5, 6/26, scratches appear near the edge as closely spaced clusters.
There are two other classes of particles: Particles just outside the three PSL size bins (1 μm to 2.75 μm and 4.25 μm to 6.5 μm) and “area” particles (particles larger than the largest size bin). The small and large particles each contribute about 5 or less to the 3 μm sum in the center of the wafer. These particles are distributed across the wafer and are observed on the “no deposit” wafer. These particles are considered contaminants and are not included in the count. The “area” particles, which have a scattering signal stronger than a 6-μm sphere, make up five or fewer particles in the center, are widely dispersed on the wafer, and are present in an almost equal amount on the “no deposit wafer.” These particles are not included in the count.
A summary of the deposition data is given in including the number of particles in each of the three bins centered on the 3 μm PSL sphere size for concentrations extending from about 0.1 cm−3 to 1.0 cm−3. The flow rate was determined from the average pressure drop through the laminar flow element. contains the OPC results, the splitter bias, and the corrected OPC concentration. The size distributions of the 3-μm PSL spheres measured by the WSS and OPC are shown in .
TABLE 1 Wafer surface scanner count distribution for 12 depositions
TABLE 2 Comparison of the OPC results with the wafer surface scanner results
FIG. 7. Bin distribution of 3-μm spheres for the WSS (three bins) and for the OPC (two bins), based on 180 s of deposition for Experiment 4. The total number of spheres counted, which is equal to the area under the curve, was 209 for the WSS and 213 for the OPC. The two narrowly spaced lines between the arrows correspond to ±1 standard deviation of the size distribution of the PSL spheres about the number mean size (3.00 μm) obtained by particle manufacturer, Thermo Scientific.
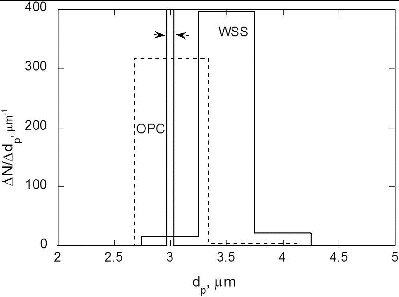
The tables include both the number of counts obtained by the WSS during the sampling interval and the number of counts obtained by the OPC during this same interval. If both instruments operated correctly and the flow rates were equal into the instruments, then the number of counts would be equal.
To determine the splitter bias, the concentration ratio of OPC to WSS was measured once with the splitter tee/sampling tube in its initial orientation and once with the assembly rotated by 180°. The sampling bias β is obtained using the following formula:[4] where the subscripts 1 and 2 refer to the initial and rotated orientations. Treating the WSS as the standard measurement, the bias-corrected value of the OPC reading is equal to β times the OPC reading. This is not a result of a defect in the OPC but is caused by a difference in the concentration in the two sampling lines resulting from a defect in the Tee or incomplete mixing resulting in a higher concentration on one side compared to the other.
The corrected OPC concentration and the corrected OPC-to-WSS ratio are given in . The mean and relative standard deviations of the mean of the ratios are 0.984 and 0.038 for the combined dataset. A graphical representation of these results in shows that the ratio is independent of the concentration. The results of linear regressions, with and without the intercept, for variation of the OPC concentration with that of the WSS are shown in . While the zero intercept with a slope of 1.022 provides an apparently good fit to the data, the nonzero intercept is equal to −0.033 and is statistically significant, suggesting a slight bias in the data.
FIG. 8. The WSS/OPC ratios are plotted with respect to the WSS concentrations. The solid line represents the average value of the concentration.
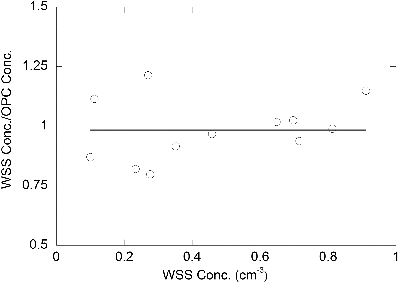
FIG. 9. Linear regression with intercept (solid line, slope = 1.075, intercept = −0.033) and without (solid line, slope = 1.022) for the OPC concentration versus deposition chamber inlet concentration. The error bars correspond to the 95% confidence interval for the linear regression with intercept.
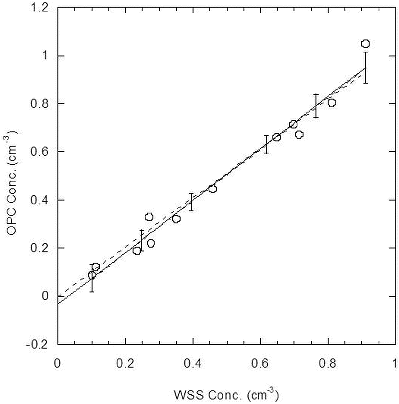
UNCERTAINTY
WSS/Deposition Measurements
The number concentration based on the WSS, CWSS, is obtained from the number of 3-μm PSL spheres deposited, N, the deposition flow rate, F, and the collection time, t,[5] The relative uncertainty in the concentration, uC, is related to the uncertainties in N, F, and t via the law of propagation of uncertainty (Taylor and Kuyatt Citation1994)
[6] The relative standard uncertainty is the ratio of the estimated standard deviation divided by the mean value. Next, the uncertainty for a single deposition is computed.
The three major components to the uncertainty in uN are random fluctuations, cluster particles, and incorrectly sized particles. For randomly distributed particles, the statistical distribution describing the probability of N particles in a volume V depositing on the wafer is given by the Poisson distribution[7] where Navg is the number of particles per volume V averaged over many volumes V. The volume V in our case corresponds to the fixed volume of gas flowing through the deposition chamber. The relative standard deviation for the Poisson distribution is given by:
[8] The random component of the relative uncertainty for the number of particles N deposited, u(N, random), is equal to σr(N).
In the preceding section, we explained why each cluster particle was counted as a single 3-μm sphere. To test this assumption, repeat scans were made with the area defect feature, which included cluster counts, disabled. This resulted in a 0.023 fractional change in the WSS counts for particles in the size bins from 2.75 μm to 4.25 μm, and was used to estimate the relative standard uncertainty arising from the cluster particles, u(N, cluster).
In the preceding section, we also described the presence of particles smaller and larger than the nominal 3-μm PSL spheres coating the wafer. These were not included in the count; however, there is an uncertainty associated with totally discounting them. We computed the increase of the off-size particles in the wafer center relative to the entire surface. It was assumed that the undersized particles were 3-μm PSL spheres but were incorrectly sized by being near the edge of the laser beam, leading to a smaller scattering signal. The oversized particles are assumed to occur from a stronger light scattering signal from two very closely spaced 3-μm PSL spheres (too close to be counted as two clusters). Carrying out this analysis, we find a fraction of 0.017 of undersized particles, 1.0 μm to 2.75 μm, and 0.005 oversized particles, 4.25 μm to 6.5 μm. The relative standard uncertainty associated with off-size particles, u(N, off-size), was conservatively estimated to be 0.022, the sum of the two fractions.
The maximum change in the number of counts obtained by the WSS for ten repeat scans for particles in the size range between 2.75 μm and 4.25 μm was 2 based on about 200 particles sized. We assume that the probability of the counting error is uniformly distributed over the interval of 198 to 202 leading to estimated standard deviation equal . The corresponding relative uncertainty u(N, repeat) associated with repeatability is given by:
[9] The final uncertainty term arises from the observation that on each of two “no deposition” wafers, one particle in the 3.0-μm bin range near the center of the wafer was observed. These wafers were exposed to the atmosphere in the clean room as they were placed in the deposition chamber and removed, but no PSL spheres were deposited. The uncertainty from these false PSL spheres, u(N, false), is equal 1/N.
The total relative standard uncertainty in the particle count is obtained as the sum of the squares of the individual components.[10] For N = 100, 200, and 800, the values of uN are 0.106, 0.078, and 0.048, respectively. For all three cases, the random fluctuation term dominates.
While many components of the uncertainty of the WSS have been investigated, the current study does not constitute a calibration of the WSS traceable to SI units. There is a need for the WSS to be tested based on an artifact with an accurately known number of particles.
The accurate determination of the low-deposition flow, about 1.5 cm3/s, is a challenge. The two major components of the flow uncertainty are the pressure transducer resolution, 0.025 relative to the nominal value, and the flow variation during a deposition, 0.034 relative to the nominal flow. The total flow standard uncertainty, uF = 0.042, is computed as the quadrature sum of the two components.
The time uncertainty is determined to be 3 s by the time to make and break the connection between the plastic tube and the inlet to the deposition chamber. The relative timing standard uncertainty, ut, based on a 240 s deposition is 0.013.
For N = 100, 200, and 800, the values of the combined concentration standard uncertainty uC are computed using Equation (6) to be 0.115, 0.089, and 0.065. The major uncertainty component results from the random fluctuations in the aerosol at low concentration.
Calibration of OPC with WSS
A primary interest regarding the calibration of the OPC with the WSS is the calculation of the OPC detection efficiency, η, and the associated uncertainty, uη:
[11] where COPC is the OPC concentration corrected for splitter bias, and CWSS is the deposition concentration. The detection efficiency uncertainty uη is calculated as the root sum of squares of the uncertainty in the WSS deposition measurement, uWSS, and the uncertainty in the repeatability of the measurement of η, uη (repeat).
[12] The uncertainty in the WSS is calculated by EquationEquations (6)
[6] and Equation(10)
[10] , where uWSS is equivalent to uC in EquationEquation (6)
[6] . To avoid double counting, the term u (N, random) is removed in EquationEquation (10)
[10] . The resulting uN was used in EquationEquation (6)
[6] to calculate uWSS. The resulting value of uWSS is 0.055 ignoring a variation of 0.002 as the number of particles varies from 100 to 800 particles. The quantity uη (repeat) is estimated as the relative standard deviation of the mean of the twelve η's and was calculated to be 0.038. From EquationEquation (12)
[12] , uη is calculated to be 0.067. The average detection efficiency and the relative expanded uncertainty (95% confidence interval) are found to be η = 0.984 ± 0.134.
In analyzing the data, the sampling bias β was measured by rotating the aerosol splitter. The value of β for the first six wafers was 1.048 and the value obtained for the second six was 1.066. There is no quantitative estimate of the uncertainty in the splitter bias. It could be as large as 10%. This term is not included in the uncertainty analysis and will be an area of future study.
SUMMARY AND DISCUSSION
A methodology was developed for generating residue free 3-μm spheres, depositing them on a wafer, and counting the particles. Using a virtual impactor and a DMA results in about 95% of the particles being 3-μm spheres, while without these devices, only about 0.005% of the particles are 3-μm spheres and the remainder are residue particles. The deposition requires from 100 s to 600 s and the scanning time is on the order of minutes. Doing the equivalent task via microscopy would require many hours. The lowest concentration for a deposition was about 0.1 cm−3.
The relative expanded uncertainty (95% confidence level, equal 2 × uc) in the number concentration determined with a WSS for a deposition of 200 particles is 17.8%. The uncertainty in the number of counts from the Poisson statistics dominates the uncertainty in the concentration. The second major component is the uncertainty in the flow to the deposition chamber. It is feasible to reduce these uncertainties by at least a factor of two by depositing more particles and by using a higher resolution pressure transducer for monitoring the flow.
One advantage of the WSS technology is that the wafer with deposited spheres can be stored and used at a later time to verify the performance of a second wafer scanner or of the same scanner used at a later date.
The WSS was used in the calibration of an OPC based on 12 depositions with concentrations ranging from 0.1 cm−3 to 1 cm−3 for each deposition. Make-up air was added to the aerosol entering the OPC, so that the lowest achievable concentration for the OPC measurement is about 0.01 cm−3 in this study. The detection efficiency of the OPC was measured to be 0.984 with an expanded uncertainty of 0.134.
While this study establishes the feasibility of using wafer deposition and particle counting as an accurate calibration method, further developments are needed before an accurate traceable calibration is possible. These include an accurate calibration of the WSS, reducing clean room contamination, and improving the flow splitter design. The improved flow splitter design is critical to obtaining a quantitative measure of the splitter bias and its uncertainty.
ACKNOWLEDGMENTS
The authors thank the support of members of the Center for Filtration Research, especially Dr. Seong Chan Kim and Huaping Wang from Entegris Inc. for their help on wafer inspection technique.
FUNDING
Funding for this project is provided by the office of the Joint Product Manager for Biological Detection Systems.
REFERENCES
- Fletcher, R. A., Mulholland, G. W., Winchester, M. R., King, R. L., and Klinedinst, D. B. (2009). Calibration of a Condensation Particle Counter Using a NIST Traceable Method, Aerosol Sci. Technol., 43:425–441.
- Gebhart, J., Blankenberg, P., Borman, S., and Roth, C. (1983).Vergleichsmessungen an Optischen Partiketzählem, Staub-Reinhalt. Luft 43, 439.
- Kesavan, J. S., Bottiger, J. R., Schepers, D. R., and McFarland, A. R. (2014). Comparison of Particle Number Counts Measured with an Ink Jet Aerosol Generator and an Aerodynamic Particle Sizer. Aerosol Sci. Technol., 48:219–227.
- Lee, H. S., Chae, S. K., Ye, Y., Pui, D. Y. H., and Wojcik, G. L. (1991). Theoretical and Experimental Particle Size Response of Wafer Surface Scanners. Aerosol Sci. Technol., 14(2):177–192.
- Liu, B. Y. H., Chae, S. K., and Bae, G. N. (1993). Sizing Accuracy, Counting Efficiency, Lower Detection Limit and Repeatability of a Wafer Surface Scanner for Ideal and Real-World Particles. J. Electrochem. Soc., 140(5):1403–1409.
- Liu, B. Y. H, and Pui, D. Y. H.(1974). A Submicron Aerosol Standard and the Primary Absolute Calibration of the Condensation Nuclei Counter. J. Colloid Interface Sci., 47:155–171.
- Loo, B. W., and Cork, C. P. (1988). Development of High Efficiency Virtual Impactors. Aerosol Sci. Technol., 9(3):167–176.
- Marple, V. A., and Chien, C. M. (1980). Virtual Impactors: A Theoretical Study. Environ. Sci. Technol., 14:976–985.
- McMurry, P. H. (2000). A Review of Atmospheric Aerosol Measurements, Atmos. Environ., 34:1959–1999.
- Peters, T. M., Ott, D., and O’Shaughnessy, P. T. (2006). Comparison of the Grimm 1.108 and 1.109 Portable Aerosol Spectrometer to the TSI 3321 Aerodynamic Particle Sizer for Dry Particles. Ann. Occup. Hyg., 50(8):84–850.
- Pui, D. Y. H., Ye, Y., and Liu, B. Y. H. (1990). Experimental Study of Particle Deposition on Semiconductor Wafers. Aerosol Sci. Technol., 12(4):795–804.
- Sorensen, C., Gebhart, J., O’Hern, T., and Rader, D. (2011). Optical Measurement Techniques: Fund- amentals and Applications. in Aerosol Measurement: Principles, Techniques, and Applications, P. Kulkarni, P. A. Baron, and K. Willeke, Eds., John Wiley and Sons, Hoboken, NJ, pp. 270–307.
- Taylor, B. N., and Kuyatt, C. E.(1994). Guidelines for Evaluating and Expressing the Uncertainty of NIST Measurement Results, NIST Technical Note 1297, U.S. Government Printing Office, Washington, DC; Available at http://physics.nist.gov/Pubs/. See also Guide to the Expression of Uncertainty in Measurement; ISBN 92-67-10188-9, 1st Ed., ISO, Geneva, Switzerland (1993).
- Volckens, J., and Peters, T. M. (2005). Counting and Particle Transmission Efficiency of the Aerodynamic Particle Sizer. J. Aerosol Sci., 36:1400–1408.
- Yook, S. J., Fissan, H., Engelke, T., Asbach, C., Zwaag, T., Kim, J. H., et al. (2008). Classification of Highly Monodisperse Nanoparticles of NIST-Traceable Sizes by TDMA and Control of Deposition Spot Size on a Surface by Electrophoresis. J. Aerosol Sci., 39(6), 537–548.