Abstract
The silicon carbide (SiC) ceramic filter is the most favorable component to remove particulate matter from hot flue gas due to its high filtration efficiency and high thermal durability. The effect of SiC powder size on the physical properties and filtration performance to prepare high-performance granular ceramic filter media was investigated in this study. Disk-type filter media were prepared by mixing ceramic components followed by physical compression and sintering. The porosity and average pore diameter in the filter media increased with increasing powder size. However, the mechanical strength decreased with increasing powder size, while it increased with increasing physical compressive force. The filter performance factor, qFM was introduced to evaluate the ceramic filter properties, and the SiC50 filter was the best of the ceramic filters prepared in this study. We also found that diffusion was a dominant collection mechanism for particles smaller than 0.7 μm, and direct interception and inertia were dominant collection mechanisms for particles larger than 0.7 μm in the SiC50 filter based on a single collector efficiency model. In addition, the predicted collection efficiencies showed reasonably good agreement with the experimental ones.
Copyright 2014 American Association for Aerosol Research
1. INTRODUCTION
Hot gas filtration has become a potential technology to remove particulate matter from dust-laden flue gas from coal-fired power plants, especially pressurized fluidized-bed combustion (PFBC) systems and integrated gasification combined-cycle (IGCC) systems (Kamiya et al. Citation2001; Al-Otoom et al. Citation2003). Moreover, it is becoming more important to protect heat exchangers, catalyst units and turbines from corrosion and fouling in a biomass combustion process (Pastila et al. Citation2001; Freitas et al. Citation2006; Heidenreich Citation2013; Nilsson et al. Citation2013).
Ceramic filters are widely used in hot gas filtration due to their high filtration efficiency and high thermal durability against corrosive hot flue gases (Freitas et al. Citation2006; Chi et al. Citation2009). Silicon carbide (SiC) is especially useful for the fabrication of ceramic filters because of its high temperature stability, thermal shock resistance, high corrosion resistance, and excellent mechanical properties (Alvin et al. Citation1991; Alvin Citation1996; Pastila et al. Citation2001; Li et al. Citation2011). Ceramic filters for hot gas cleaning can be classified into fibrous ceramic filters and granular ceramic filters on the basis of their fabrication materials. Fibrous ceramic filters have high collection efficiency and high permeability although they have low mechanical strength. In contrast, granular ceramic filters have good mechanical strength, and it is easy to control their filtration properties by varying the powder size. Furthermore, granular filters provide continuous cleaning performance and reusability, which is ideal for maintaining constant filter performance in terms of collection efficiency and pressure drop (Jo et al. Citation1997; Freitas et al. Citation2006; Kuo et al. Citation2010).
Many researchers have investigated the filtration characteristics of ceramic filters in hot gas filtration. However, most studies have focused on operational performance in terms of collection efficiency and pressure drop as well as its stability in practical applications. In addition, previous researches have been conducted with large-scale demonstration systems (Sasatsu et al. Citation2001; Hata et al. Citation2003). Lupion et al. (Citation2013) investigated the filtration performance and operating conditions in a filtration system with two types of commercial ceramic candle filters. Zhong et al. (Citation2013) studied the filtration efficiency and stability of a commercial ceramic filter in removing the organic aerosol from flue gas. As demonstrated above, recent studies have the limitation that they were performed with commercial ceramic candle filters to investigate their filtration performance in hot gas filtration.
Therefore, in the present study, we prepared disk-type ceramic filters with various sizes of SiC powders, and the effect of the powder size on filtration performance and physical properties (porosity, pore size distribution, and mechanical strength) were examined. In addition, the particle collection mechanisms in granular ceramic filter media were studied based on a single collector efficiency model (Tien Citation1989; Freitas et al. Citation2006; Kuo et al. Citation2010).
2. EXPERIMENTAL SETUP AND METHOD
2.1. Preparation of Ceramic Filters
The sintering temperature of pure SiC is above 2100°C due to its strong covalent bonds. The addition of bonding materials, such as boron (B compound), aluminum (Al compound), and carbon, to SiC powder is a possible way to improve its contraction kinetics (Sigl and Kleebe Citation1993; Li et al. Citation2011). shows the chemical compositions of the prepared ceramic filters and their intrinsic functional roles. Disk-type ceramic filters with a diameter of 47 mm were prepared by mixing all materials (total mass = 9 g) at the speed of 1200 rpm with a stirrer, followed by compression for 5 s under a pressure of 30 MPa using a hydraulic press (HHP-10, Hyundae Mechanic & Electric CO., LTD.). SiC powders of various sizes (10, 25, 50, 100, 200 μm) were used to determine the effect of powder size on filter performance. Prior to determining the suitable SiC powder size, we investigated the effect of the binder powder sizes (5, 10, 25, 50 μm) on the filter quality factor, which was obtained from particle collection efficiency and pressure drop in the prepared ceramic filters. As shown in , the filter quality factor was the highest in the binder powder with the size of 25 μm. Therefore, we decided that the most appropriate size of binder materials was 25 μm. The prepared filters were dried for 5 h at the temperature of 105°C and sintered for 2 h at 1450°C in a box-type furnace. The operating temperature of the sintering furnace was programmed as shown in . The temperature gradient ranged from 3.1 to 4.2 K/min, and a constant temperature was maintained intermittently until the sintering temperature reached 1450°C.
Table 1 Chemical composition of prepared ceramic filters
2.2. Characterization of Ceramic Filters
The pore properties of each ceramic filter, namely, porosity, average pore diameter and pore size distribution, were analyzed by a mercury porosimeter (Autopore IV, Micromeritics), and its mechanical strength was measured by a universal testing machine (UTM) (KDMT-156, Kyung Do Precision). However, the prepared filters were too thin for their mechanical strength to be measured with the jig that is generally used in a UTM. Therefore, a specialized jig with a diameter of 10 mm was prepared and used. The jig was designed to press the center of a ceramic filter at the speed of 0.5 mm/min. The thickness of each ceramic filter was measured with a micrometer at three points of the filter and averaged. The internal morphology of each filter was observed with a field emission scanning electron microscope (FE-SEM) (JSM-6701F, JEOL).
2.3. Measurement of Filtration Performance
shows the experimental setup to evaluate the filtration performance. Test particles were generated by supplying clean air in a magnetically stirred flask filled with fly ash powders, and provided in the filter test unit. The filtration velocity was adjusted from 1 to 3 m/min by supplying makeup clean air upstream of the filter test unit. The particle collection efficiency of a ceramic filter was determined by measuring the particle number concentration with an aerodynamic particle sizer (APS 3321, TSI Inc.) upstream and downstream of the filter media. Pressure drop across the filter medium was also measured with a U-tube-type manometer at the same time.
3. RESULTS AND DISCUSSION
3.1. Physical Properties of the Prepared Ceramic Filters
shows the internal morphologies of the prepared ceramic filters with various SiC powder sizes. A difference in relation to the powder size used is clearly observed in FE-SEM images, and binding among the SiC powders and other additives can also be seen. However, several pinholes and cracks were observed in the filters fabricated by SiC powders with diameters of 10 μm (SiC10) and 25 μm (SiC25). In addition, large holes were seen in the filter samples fabricated from large SiC powders. In contrast, the ceramic filter fabricated with 50 μm SiC powders (SiC50) was relatively uniform.
The pore size distributions of the fabricated filters were measured to check their uniformity, and the results are shown in . The pore size distribution in SiC50 was more uniform and narrower than those of other SiC powders. The measured physical properties of the prepared filters are summarized in . The thickness and the actual weight of a filter decreased with increasing SiC powder, even though it was prepared with the same amount of mass and under the same compressive force. The porosity and average pore diameter increased with increasing SiC powder size. Wen et al. (Citation2008) reported the same results. However, this tendency was not observed in the SiC powder size of 200 μm. The average pore diameter and porosity decreased for a ceramic filter made from 200 μm SiC, and these phenomena can be attributed to the inhomogeneity of the prepared filters.
Table 2 Physical properties of ceramic filters prepared with SiC powders of various sizes
The mechanical strengths of the prepared ceramic filters prepared with SiC powders of various sizes are shown in . The load required to break the prepared samples with a UTM decreased with increasing SiC powder size. However, we measured mechanical strength in the order of SiC200 < SiC100 < SiC10 < SiC50 < SiC25. We can infer that the ceramic filter prepared with SiC25 had the highest mechanical strength. Displacement, which means the compressed distance of a filter medium before breaking, also decreased with increasing SiC powder size.
3.2. Filtration Performance
The collection efficiencies of ceramic filters prepared with various SiC powder sizes are shown in . The experimental results showed that the collection efficiency increased with increasing test particle size and decreasing SiC powder size at the filtration velocity of 1 m/min. The collection efficiency generally increases with increasing test particle size due to higher inertial force (Hinds Citation1999). However, the collection efficiency of the ceramic filter prepared with SiC10 was lower than that of an SiC25 filter at particles sizes smaller than 1 μm. A possible explanation of the lower collection efficiency could be the formation of pinholes and cracks as seen in the FE-SEM images. Furthermore, the inhomogeneity of the filters using SiC100 and SiC200 might explain the drastic decrease in collection efficiency.
In general, pressure drop across a granular filter increases with increasing filtration velocity and depends on the physical properties of the filter (Larbot et al. Citation2003) shows the pressure drops of the ceramic filters prepared with SiC powders of various sizes and filtration velocities ranging from 1 to 3 m/min. The experimental pressure drop was compared with the pressure drop predicted by Kozeny-Carman's equation as shown in EquationEquation (1)[1] (Endo et al. Citation2002):
[1]
The prepared filter consisted of SiC powders and other additives. However, those powders were sintered at high temperature and their grain sizes were changed. We determined the grain sizes in the filter by measuring more than 100 grains observed with an FE-SEM. The grain sizes were 12.33 μm for SiC10, 28.39 μm for SiC25, 53.52 μm for SiC50, 111.65 μm for SiC100, and 209.7 μm for SiC200, respectively.
As shown in the figure, the predicted pressure drops of SiC10 and SiC25 were higher than the experimental pressure drop. This phenomenon can be attributed to the large hole and cracks in the prepared filters as shown in the FE-SEM images. We can also see the predicted pressure drops of SiC100 and SiC200 were clearly less than the experimental pressure drops. A possible explanation of this result is the occurrence of the channeling effect due to their inhomogeneity. However, the predicted result with SiC50 was in good agreement with the experimental one. This result means that the SiC50 filter had a homogeneous morphology as shown in a FE-SEM image.
As mentioned in the previous section, the inhomogeneity of the prepared filters, especially those made with SiC100 and SiC200 leads lower collection efficiency. To elucidate this result, we divided each prepared filter into four zones and measured the pressure drop in each zone using a stainless steel film with a hole of 5 mm as shown in . shows the pressure drop difference in each zone of the prepared filters (SiC10, SiC25, SiC50, SiC100, and SiC200). The pressure drop at each zone of SiC50 was constant at the same filtration velocity; however, those of other filters were not constant. This result reveals that SiC50 was uniform, and the other filters were not uniform. Therefore, the choice of proper powder size is very important in the fabrication of ceramic filters. In addition, the powder size affected the morphology, physical characteristics, and filtration performance in terms of collection efficiency and pressure drop.
The filter quality factor is a useful parameter to assess the filtration performance of various filter media. It is defined as the ratio of collection efficiency and pressure drop as shown in EquationEquation (2)[2] (Hinds Citation1999):
[2] where qF is the quality factor, P is the particle penetration, and △p is the pressure drop across the filter media. However, mechanical strength is a more critical parameter for a filter medium under the conditions of high temperature and corrosive exhaust gas. Therefore, the mechanical strength should be considered as a parameter for suitable evaluation of hot gas filtration performance. In this study, a new parameter, qFM, which stands for multiplication of qF and maximum mechanical strength, σM, is introduced. shows a calculated value of qFM with the prepared filters with various SiC powder sizes at a filtration velocity of 1 m/min. As shown in , the SiC50 filter had the highest value of qFM. This result demonstrated that the selection of a suitable powder size is very important in the fabrication of a granular ceramic filter, and SiC50 was found to be the most appropriate size in this study.
3.3. Filtration Mechanisms
Freitas et al. (Citation2006) investigated the particle collection mechanisms in a double-layered ceramic filter using the single collector efficiency model. Therefore, we referred to their work and investigated particle collection mechanisms in a prepared filter. The single collector efficiency of a granular filter is defined as the ratio of the number of captured particles to the number of particles introduced in a single collector (Gutfinger and Tardos Citation1979; Alvin et al. Citation1991; Kuo et al. Citation2010). The total collection efficiency, E, is an exponential function of the physical properties, namely: filter thickness (L), powder size (dc), porosity (s), and total single collector efficiency (ηT), as expressed in EquationEquation (3)[3] (Allen and Raabe Citation1985; Gal et al. Citation1985; Kuo et al. Citation2010):
[3]
[4]
Here, ηT can be calculated by EquationEquation (4)[4] summing the single collector efficiencies by individual collection mechanisms, i.e., ηD, the single collector efficiency due to diffusion, ηI, the single collector efficiency due to inertia, ηDI, the single collector efficiency due to direct interception and ηG, the single collector efficiency due to gravity. However, this assumption is limited to no interaction among collection mechanisms.
The diffusional collection mechanism arises from the Brownian movement of fine particles escaping from a streamline (Larbot et al. Citation2003; Freitas et al. Citation2006). The predicted equation of single collector efficiency, ηD, due to diffusion was proposed by Tien (Citation1989) and expressed as[5] where As is Happel's parameter, and Pe is the Peclet number, which are expressed as
[6]
[7] where D is the diffusivity of a particle.
Inertial force is a dominant collection mechanism at high filtration velocity, high particle density, and large particle size (Larbot et al. Citation2003). The single collector efficiency, ηI, is expressed in EquationEquation (8)[8] as suggested by Jung et al. (Citation1989) :
[8] where StkE is the effective Stokes number (D’Ottavio and Goren Citation1982), and R is the interception parameter, which are expressed as
[9]
[10]
Here Re is the Reynolds number and Stk is the Stokes number which are expressed as[11]
[12]
Direct interception is a collection mechanism in which a particle follows a fluid streamline and is captured on a collector. Paretsky et al. (Citation1971) suggested the following prediction equation:[13]
Gravitation is a dominant collection mechanism when a particle is large enough and filtration velocity is quite low. The prediction equation is given by (Paretsky et al. Citation1971; Larbot et al. Citation2003)[14] where vt is the terminal settling velocity of a particle, which is expressed as
[15]
compares the experimental collection efficiencies (symbols) and collection efficiencies by EquationEquation (3)[3] (solid line) in the prepared filter. As shown in the figure, the predicted collection efficiencies show good agreement with the experimental data at particle sizes larger than 0.7 μm; however, they showed disagreement at particle sizes smaller than 0.7 μm. The discrepancy can be attributed to the nonuniformity of filter porosity during sintering.
FIG. 12. Comparison of experimental collection efficiencies and predicted collection efficiencies in a granular ceramic filter.
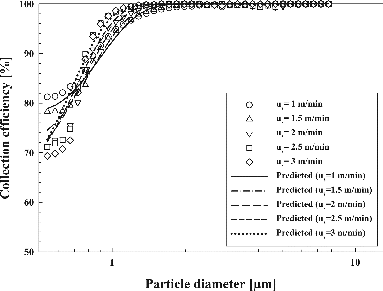
shows the collection efficiencies due to individual collection mechanisms in a SiC50 filter with various filtration velocities. Cleary, diffusion is a dominant collection mechanism at particle size smaller than 0.7 μm, and it is stronger with decreasing filtration velocity. Collection efficiency due to direct interception and inertial force drastically increase with increasing particle size. In addition, gravitational force readily increases with particle size and becomes an important collection mechanism at particle sizes larger than 2.5 μm.
The total collection efficiency summing up individual collection efficiencies increases with increasing filtration velocity and particle size. In particular, we could see that particle collection efficiency at a filtration velocity of 1 m/min and particle sizes smaller than 0.7 μm was higher than those at other filtration velocities and particle sizes. This tendency is clearly seen in the experimental data in .
4. CONCLUSION
Granular ceramic filters prepared with SiC powders of various sizes were prepared, and their physical and filtration characteristics were investigated in this study. The porosity and average pore diameter in the filter media increased with increasing powder size. However, the mechanical strength decreased with increasing powder size, while it increased with increasing physical compressive force. The prepared ceramic filters fabricated with SiC powders (SiC25 and SiC50) had excellent collection efficiencies for particles larger than 1 μm. However, the samples made with SiC100 and SiC200 powders had low collection efficiencies due to their inhomogeneity. We have also demonstrated that diffusion was a dominant collection mechanism for particles smaller than 0.7 μm, and direct interception and inertia were dominant collection mechanisms for particles larger than 0.7 μm in the SiC50 filter based on a single collector efficiency model. This result reveals that lower filtration velocity is efficient to remove fine particles and high filtration velocity for coarse particles with a granular ceramic filter.
Additional information
Funding
REFERENCES
- Allen, M. D., and Raabe, O. G. (1985). Slip Correction Measurements of Spherical Solid Aerosol Particles in an Improved Millikan Apparatus. Aerosol Sci. Technol., 4:269–286.
- Al-Otoom, A. Y., Ninomiya, Y., Moghtaderi, B., and Wall, T. F. (2003). Coal Ash Buildup on Ceramic Filters in a Hot Gas Filtration System. Energy Fuels., 17:316–320.
- Alvin, M. A. (1996). Advanced Ceramic Materials for Use in High-Temperature Particulate Removal Systems. Ind. Eng. Chem. Res., 35:3384–3398.
- Alvin, M. A., Lippert, T. E., and Lane, J. E. (1991). Assessment of Porous Ceramic Materials for Hot Gas Filtration Applications. Amer. Ceram. Soc. Bull., 70:1491–1498.
- Chi, H., Ji, Z., Sun, D., and Cui, L. (2009). Experimental Investigation of Dust Deposit Within Ceramic Filter Medium During Filtration-Cleaning Cycles. Chin. J. Chem. Eng., 17:219–225.
- D’Ottavio, T., and Goren, S. L. (1982). Aerosol Capture in Granular Beds in the Impaction Dominated Regime. Aerosol Sci. Technol., 2:91–108.
- Endo, Y., Chen, D. –R., and Pui, D. Y. H. (2002). Collection Efficiency of Sintered Ceramic Filters Made of Submicron Spheres. Filtr. Sep., 39:42–47.
- Freitas, N. L. D., Gonçalves, J. A. S., Innocentini, M. D. M., and Coury, J. R. (2006). Development of a Double-Layered Ceramic Filter for Aerosol Filtration at High-Temperatures: The Filter Collection Efficiency. J. Hazard. Mater., 136:747–756.
- Gal, E., Tardos, G., and Pfeffer, R. (1985). A Study of Inertial Effects in Granular Bed Filtration. AIChE J., 31:1093–1104.
- Gutfinger, C., and Tardos, G. I. (1979). Theoretical and Experimental Investigation on Granular Bed Dust Filters. Atmos. Environ., 13:853–867.
- Hata, M., Furuuchi, M., Kanaoka, C., Kurose, R., and Makino, H. (2003). Observation of Dust Release Behavior From Ceramic Filter Elements. Adv. Powder Technol., 14:719–734.
- Heidenreich, S. (2013). Hot Gas Filtration – A Review. Fuel, 104:83–94.
- Hinds, W. C. (1999). Aerosol Technology: Properties, Behavior, and Measurement of Airborne Particles, 2nd ed. Wiley, New York,
- Jo, Y. M., Hutchison, R. B., and Raper, J. A. (1997). Characterization of Ceramic Composite Membrane Filters for Hot Gas Cleaning. Powder Technol., 91:55–62.
- Jung, Y., Walata, S. A., and Tien, C. (1989). Experimental Determination of the Initial Collection Efficiency of Granular Beds in the Inertial-Impaction-Dominated Region. Aerosol Sci. Technol., 11:168–182.
- Kamiya, H., Deguchi, K., Gotou, J., and Horio, M. (2001). Increasing Phenomena of Pressure Drop During Dust Removal Using a Rigid Ceramic Filter at High Temperatures. Powder Technol., 118:160–165.
- Kuo, Y. -M., Huang, S. –H., Lin, W. –Y., Hsiao, M. –F., and Chen, C. –C. (2010). Filtration and Loading Characteristics of Granular Bed Filters. J. Aerosol Sci., 41:223–229.
- Larbot, A., Bertrand, M., Marre, S., and Prouzet, E. (2003). Performances of Ceramic Filters for Air Purification. Sep. Purif. Technol., 32:81–85.
- Li, J., Lin, H., and Li, J. (2011). Factors that Influence the Flexural Strength of SiC-Based Porous Ceramics used for Hot Gas Filter Support. J. European Ceram. Soc., 31:825–831.
- Lupion, M., Navarrete, B., Alonso-Fariñas, B., and Rodriguez-Galan, M. (2013). Hot Gas Filters for Coal-Based Power Generation Systems: Operating Experiences. Fuel, 108:24–30.
- Nilsson, P., Meng, X., Malik, A., De Jong, W., Gudmundsson, A., Verkooijen, A. H. M., and Sanati, M. (2013). Sampling and Characterization if Sub-Micrometer High-Temperature Particles Present in the Product Gas From a Circulating Fluidized-Bed Biomass Gasifier. Energy Fuels, 27:3290–3295.
- Paretsky, L., Theodore, L., Pfeffer, R., and Squires, A. M. (1971). Panel Bed Filters for Simultaneous Removal of Fly Ash and Sulfur Dioxide: II. Filtration of Dilute Aerosols by Sand Beds. J. Air Pollut. Control Assoc., 21:204–209.
- Pastila, P., Helanti, V., Nikkilä, A., and Mäntylä, T. (2001). Environmental Effects on Microstructure and Strength of SiC-Based Hot Gas Filters. J. European Ceram. Soc., 21:1261–1268.
- Sasatsu, H., Misawa, N., Shimizu, M., and Abe, R. (2001). Predicting the Pressure Drop Across Hot Gas Filter (CTF) Installed in a Commercial Size PFBC System. Powder Technol., 118:58–67.
- Sigl, L. S., and Kleebe, H. –J. (1993). Core/Rim Structure of Liquid-Phase-Sintered Silicon Carbide. J. Am. Ceram. Soc., 76:773–776.
- Tien, C. (1989). Granular Filtration of Aerosols and Hydrosols. Butterworths-Heinemann, Boston.
- Wen, Z. –H., Han, Y. –S., Liang, L., and Li, J. –B. (2008). Preparation of Porous Ceramics with Controllable Pore Sizes in an Easy and Low-Cost Way. Mater Charact., 59:1335–1338.
- Zhong, Z., Xing, W., Li, X., and Zhang, F. (2013). Removal of Organic Aerosols from Furnace Flue Gas by Ceramic Filters. Ind. Eng. Chem. Res., 52:5455–5461.