Abstract
Ultrasonic spray pyrolysis method to synthesize porous submicron particles of solid oxide fuel cell (SOFC) electrode materials was developed in which citric acid is added in a precursor solution. This citric acid-addition ultrasonic spray pyrolysis (CA-USP) method was then used to synthesize NiO-Gd0.1Ce0.9O1.95 (GDC) particles for SOFC anodes and La0.8Sr0.2Co3 (LSC) and La0.8Ca0.2MnO3 (LCM) particles for SOFC cathodes. The synthesized particles were submicron-sized, porous, and spherical, and had a sponge-like structure. Energy dispersive X-ray spectrometry images of the synthesized NiO-GDC particles revealed that Ni, Ce, Gd, and O were uniformly distributed within individual particles. NiO-GDC and LCM particles with sponge-like structure were not crushed by a 2-h ball mill grinding test. The formation process of the sponge-like structure was clarified by synthesizing GDC particles at various furnace temperatures between 473 and 1273 K.
Copyright 2014 American Association for Aerosol Research
INTRODUCTION
Solid oxide fuel cells (SOFC) convert chemical energy to electric energy and consist of an anode, a cathode, and a dense electrolyte sandwiched between these electrodes. To improve SOFC efficiency, most research effort focuses on reducing the operating temperature from 1273 K to 873–973 K (Haile Citation2003). Such reduction will require improvement in the conductivity at 973 K and in microstructure of both the cathode and anode. The microstructure affects the performance of these electrodes because they are in contact with oxygen and hydrogen gases and thus exchange reactions occur between the oxygen gas and electrons and between the hydrogen gas and oxide ions, respectively. Porous particles improve the microstructure in both cathodes and anodes. Anodes and cathodes of SOFCs are generally fabricated on a holding substrate by the printing method. Powders of the electrode materials are mixed mechanically with binder to prepare the printing inks (i.e., a slurry in which the material powder is suspended in the binder), which are then pressed on the holding substrate during the printing process. Particles of the electrode materials must not be crushed in this process, because to form the porous microstructure in both electrodes, the particles must be both porous and crush-resistant.
As highly conductive electrode materials, La0.8Sr0.2Co3 (LSC), La0.8Sr0.2MnO3 (LSM), and La0.8Ca0.2MnO3 (LCM) are commonly used as the cathode material because of their high catalytic activity for oxygen reduction and their thermal and chemical compatibility with yttria-stabilized zirconia (YSZ) as the electrolyte material (Yamamoto et al. Citation1987; Hammouche et al. Citation1989). Although a mixture of a ceramic and metal oxide, such as NiO-YSZ cermet, is generally used as a standard anode material, NiO-Gd0.1Ce0.9O1.95 (NiO-GDC) is highly active as an anode catalyst for hydrogen fuel and has a high conductivity (Brandon et al. Citation2004; Sun and Stimming Citation2007; Suzuki et al. Citation2008). Also, NiO-GDC has good thermal compatibility with GDC, which has recently attracted the attention of researchers as an electrolyte material due to its high conductivity at 873–973 K (Haile Citation2003; Brandon et al. Citation2004; Suzuki et al. Citation2008).
Ultrasonic spray pyrolysis (USP) is typically used to prepare submicron particles of complex oxides because this method can form highly crystalline oxides from a single solution in which three or four precursors are dissolved in stoichiometric ratios of the target synthesized complex oxides. USP has been used to synthesize various oxides such as zirconia (Messing et al. Citation1993; Djurado and Meunier Citation1998; Chen et al. Citation2008), YSZ (Messing et al. Citation1993; Gaudon et al. Citation2004), alumina/platinum composite (Messing et al. Citation1993), ZnO (Messing et al. Citation1993; Okuyama and Lenggro Citation2003), BaO (Messing et al. Citation1993), ceria (Okuyama and Lenggro Citation2003; Chen et al. Citation2008) and LiMn2O4 (Matsuda and Taniguchi Citation2004). Using USP, Suda et al. (Citation2006) synthesized NiO-Sm0.2Ce0.8O1.9 (NiO-SCO) composite particles from nitric acid solutions in which samarium oxide, cerium nitrate, and nickel acetate were dissolved for use as SOFC anode material, and Kawano et al. (Citation2011) prepared NiO-SCO particles from an aqueous solution of nickel nitrate, cerium nitrate, and samarium nitrate. Both of these composite particles showed high performance for use as anodes of SOFCs. Mesguich et al. (Citation2010, Citation2013) used USP to produce Nd2NiO4+δ particles for use as SOFC cathode material, and investigated the influence of the crystallinity and size of these particles on electrochemical properties of the cathode. Although Suda et al. (2006), Kawano et al. (2011), and Mesguich et al. (2010, 2013) successfully synthesized anode and cathode material particles with high electrochemical properties by the USP method, their particles were either solid or hollow but not porous. Although we previously successfully synthesized GDC, NiO-GDC composite, and LSC particles as electrolyte, anode, and cathode materials, respectively, by USP method (Kinoshita and Adachi Citation2014), the morphologies of these particles were either solid or hollow but not porous. Recently, we proposed a new USP method in which carbon nanoparticles are added in a precursor solution. This carbon nanoparticle-addition ultrasonic spray pyrolysis (CNA-USP) method produces crushable porous particles and can successfully synthesize porous GDC submicron particles that can be easily separated into nanoparticles by a tumbling ball milling (Kinoshita et al. Citation2014). Review of these previous reports involving USP reveals that hard, porous particles required to improve the microstructure of SOFC cathodes and anodes have not yet been produced.
The goal of this study was to synthesize crush-resistant, highly porous submicron particles of NiO-GDC, LSC, and LCM as SOFC cathode and anode materials. To produce these particles, we developed the spray pyrolysis method in which citric acid is added in the precursor solution. We call this the citric acid-addition ultrasonic spray pyrolysis (CA-USP) method. The addition of critic acid to source solution (spray solution) was tried independently by Dong et al. (Citation2011) of our research at a similar time when we investigated the method (Yoshida Citation2012). They have synthesized hollow PbWO4 particles from lead nitrate and ammonium metatungstate hydrate of HNO3 solution by USP method to use as a photocatalyst. Their objective material, used precursor solution, and morphology of synthesized particles are different from this research.
The morphology and interior structure of these synthesized particles were observed using a scanning electron microscopy and a transmission electron microscopy, respectively, their crystalline phases were characterized using powder X-ray diffraction, and their toughness was examined using liquid phase ball milling. The specific surface areas were measured by N2 adsorption isotherms method.
CA-USP METHOD
shows the concept of the CA-USP method. First, an aqueous solution of dissolved precursors and citric acid is atomized into micron-sized droplets by using an ultrasonic nebulizer. These droplets containing citric acid are sent to a furnace via a carrier gas. In the furnace, evaporation of the water causes the citric acid to precipitate before the complex of precursors, and thus the citric acid resides in the droplets due to its solubility being lower than that of the precursors. The precursors deposit in the residual space of the droplets where is not occupied by the citric acid, and thermal decomposition produces amorphous material from these precursors. The citric acid in these amorphous submicron particles is then removed by being oxidized to CO2 gas and H2O vapor by combustion, resulting in pores in the submicron particles. Finally, these amorphous porous particles are crystallized by further heating, thus forming porous crystalline submicron particles. Citric acid is used because (1) it precipitates faster than precursors due to its lower solubility than the precursors, and (2) it can be removed from particles by combustion to form pores before sintering because the thermal decomposition temperature of citric acid is lower (433 K) than the sintering temperature of complex oxides (Wyrzykowski et al. Citation2011).
EXPERIMENTS
The porous submicron particles of NiO-GDC, LSC, and LCM were synthesized by the same apparatus used in the CNA-USP method (Kinoshita et al. Citation2014), consisting of (1) an ultrasonic nebulizer to convert the precursor solution into micron-sized droplets, (2) a flow type cylindrical reactor to form complex oxide particles by thermal decomposition, and (3) an electrostatic precipitator to collect product particles. In the nebulizer, the precursor solution in which a citric acid at a concentration Cc = 0.2 mol L−1 was added was vibrated by six ultrasonic oscillators at a frequency of 2.4 MHz (Honda Electronics, HM-2412) and thus converted to mist droplets a few microns in diameter. The droplets were then carried into the cylindrical reactor (a ceramic tube of 50 mm inner diameter and 640 mm total length) with air at a flow rate Q = 5 L min−1 (at standard conditions). The reactor was heated by two electric furnaces; an upper flow side furnace (furnace 1; 130 mm in the length) kept at Tf1 = 673 K, and a lower flow side furnace (furnace 2; 400 mm in the length) set at various Tf2 from 873 to 1473 K. Both furnaces were set at an interval of 110 mm and the rector tube between both furnaces was covered by the insulator. The average residence time in the reactor was tr = 16 s at Q = 5 L min−1. The temperature profiles in the reactor are shown in . The gas temperatures increase linearly in both zones heated by the furnace 1 and covered with the insulator and attain to almost Tf2 in the zone heated by the furnace 2. We used the average residence time in the reactor of 640 mm total length, tr = 16 s, as the reaction time because the citric acid which has the thermal decomposition temperature of 433 K decompsed in the furnace 1 kept at Tf1 = 673 K. In the reactor, solid particles are produced by thermal decomposition of precursors after the evaporation of the solvent and precipitation of the solute in droplets. The synthesized particles were collected by using an electrostatic particle precipitator (EPP) (Okuyama et al. Citation1993) heated at 403 K using an electric heater to prevent condensation of water on EPP walls. Calculated from the volume of the sprayed precursor solution and the mass of the collected particles, the maximum production rate of the apparatus was about 3 g hr−1 and the yield was 70% at the synthesis condition of Q = 5 L min−1 and total concentration of metal ions Ctotal = 0.2 mol L−1.
FIG. 2. Temperature profiles in the reactor at Tf1 = 673 K, Tf2 = 873, 1073, and 1273 K, and Q = 5 L min−1.
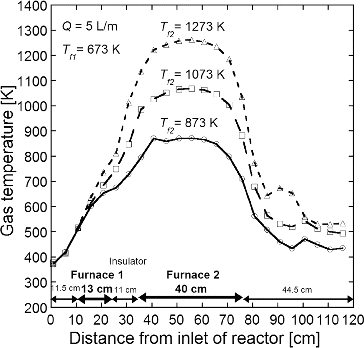
The crystalline phase of the synthesized particles was characterized by comparisons of powder X-ray diffraction patterns (XRD, RIGAKU RINT1500), data from the joint committee for powder diffraction standards (JCPDS), and the particle shape and size distribution obtained using scanning electron microscopy (SEM, Hitachi S-4500). The local distributions of metals in the particles were evaluated based on energy dispersive X-ray spectrometry (EDX) images. The inside morphologies of the particles were observed using transmission electron microscopy (TEM, Hitachi H-8100T). The specific surface areas Sw were determined by N2 adsorption using a volumetric adsorption measurement instrument (Bel Japan, Belsorp-18). The size distributions of particles suspended in pure water were measured using dynamic light scattering spectrophotometry (DLS, Otsuka Electronics, ELSZ-2ON) to evaluate the effects of particle grinding in a liquid phase on the size distribution.
In our experiments, the precursor solution for NiO-GDC was prepared by dissolving Ce(NO3)3·6H2O (Wako, 98%), and Gd(NO3)3·6H2O (Wako, 99.5%) in pure water at a stoichiometric ratio of GDC and adding Ni(NO3)2·6H2O (Wako, 98%) in the dissolving water at the molar ratio of NiO:GDC = 1:1. The precursor solution for LSC was prepared by dissolving La(NO3)3·6H2O (Wako, 99.9%), Sr(NO3)3 (Wako, 98%), and Co(NO3)2·6H2O (Wako, 98%) and that for LCM by dissolving La(NO3)3·6H2O, Ca(NO3)2·4H2O (Wako, 98%), and Mn(NO3)2·6H2O (Wako, 98%), in pure water at stoichiometric ratios of each complex oxide. The Ctotal was kept at 0.2 mol L−1. Finally, citric acid at a concentration Cc = 0.2 mol L−1 was added to these prepared precursor solutions.
Synthesized particles were then ground as follows using a tumbling ball mill to qualitatively estimate the toughness of the particles. Particles (200 mg) were suspended in pure water (200 mL) and then put in an alumina pot (100-mm deep, 72.25-mm inner diameter) together with alumina balls (20 balls of 10-mm-diameter, and 20 balls of 15-mm-diameter). The pot was then rotated at 164 rpm for 2 h. The shapes of the particles before and after grinding were observed using SEM and their size distributions using DLS.
RESULTS AND DISCUSSION
shows XRD patterns of synthesized particles of (a) GDC, (b) LSC, and (c) LCM with JCPDS 78-0643 of NiO and JCPDS 78-0161 of GDC, JCPDS 36-1392 of LSC, and JCPDS 44-1040 of LCM, respectively. Peaks of all XRD patterns agree with the JCPDS data, confirming successful synthesis of GDC, LSC, and LCM particles by the CA-USP method and revealing that the crystalline phases were not affected by the addition of citric acid. lists the average crystallite size Dcry calculated from the most intense reflection peak by using Scherrer's formula. The synthesized NiO-GDC, LSC, and LCM particles were highly crystalline as evidenced by Dcry = 11–43 nm. The addition of citric acid decreased Dcry of NiO, GDC, and LCM from 19 nm to 11 nm, from 20 nm and 17 nm, from 43 nm to 34 nm, respectively, but had no effect on the Dcry of LSC.
TABLE 1 Average crystallite sizes Dcry obtained from XRD patterns for NiO-GDC, LSC, and LCM particles shown in Figure 4
FIG. 3. XRD patterns of (a) NiO-GDC, (b) LSC, and (c) LCM powders synthesized at Ctotal = Cc = 0.2 mol L−1, Tf1 = 673 K, Tf2 = 1273 K, and tr = 16 s with JCPDS 78-0643 of NiO and JCPDS 78-0161 of GDC, JCPDS 36-1392 of LSC, and JCPDS 44-1040 of LCM (white and black bars).
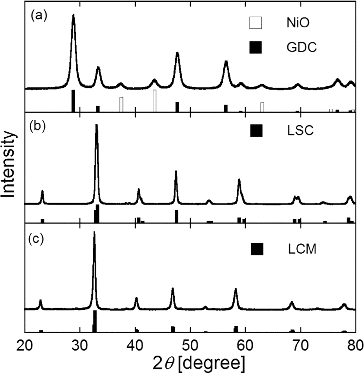
shows SEM images of NiO-GDC, LSC, and LCM particles synthesized without and with citric acid addition (Cc = 0 and Cc = 0.2 mol L−1, respectively). At Cc = 0 mol L−1, the synthesized NiO-GDC and LCM particles were spherical (), whereas LSC particles were not (). In contrast, at Cc = 0.2 mol L−1, the NiO-GDC, LSC, LCM particles were spherical (). lists the geometric mean diameter Dpg and geometric standard deviation σg of the synthesized particles determined by manually measuring (using a ruler) the diameters of 200 individual particles in the SEM images shown in . The error in Dpg between that obtained from 150 particles and that from 200 particles was less than 10%. Results indicate submicron particles with a narrow size distribution (475 ≤ Dpg ≤ 663 nm) and (1.21 ≤ σg ≤ 1.33), and Dpg increased with the addition of citric acid.
TABLE 2 Geometric mean diameters Dpg and geometric standard deviations σg obtained from SEM images of NiO-GDC, LSC, and LCM particles shown in Figure 5
FIG. 4. SEM images of (a) NiO-GDC, (b) LSC, and (c) LCM powders synthesized at Cc = 0 mol L−1 and (d) NiO-GDC, (e) LSC, and (f) LCM powders synthesized at Cc = 0.2 mol L−1. (Ctotal = 0.2 mol L−1, Tf1 = 673 K, Tf2 = 1273 K, and tr = 16 s.)
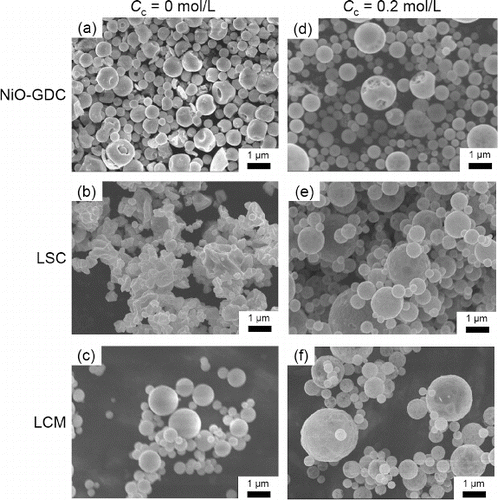
shows TEM images of NiO-GDC, LSC, and LCM particles synthesized with Cc = 0 and Cc = 0.2 mol L−1. At Cc = 0 mol L−1, all the particles had dense structure (). On the other hand, particles produced at Cc = 0.2 mol L−1 are sponge-like structure composed of numerous irregular-shaped pores with thin walls (). Such porous structure is required for both electrodes in SOFCs because exchange reactions between oxygen gas and electrons occur in the cathode and between hydrogen gas and oxide ions in the anode. At Cc = 0.2 mol L−1, sponge-like structures of NiO-GDC, LSC and LCM particles () indicate suitable particles for anodes and cathodes.
FIG. 5. TEM images of NiO-GDC, LSC, and LCM powders synthesized at Cc = 0 mol L−1 and Cc = 0.2 mol L−1. (Ctotal = 0.2 mol L−1, Tf1 = 673 K, Tf2 = 1273K, and tr = 16 s.)
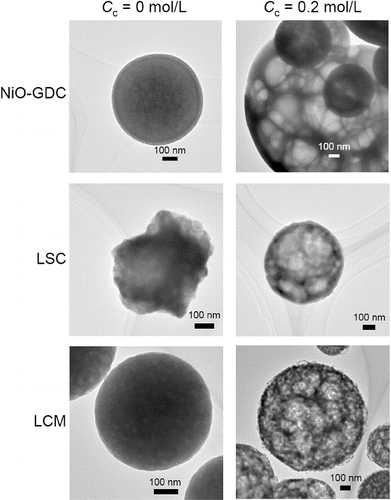
The formation mechanism of the sponge-like structure and the causes for the decrease in Dcry (with the exception of LSC particles; ) and the increase in Dpg () will be discussed later in this section.
shows the specific surface areas Sw obtained from BET analysis of N2 adsorption isotherms for NiO-GDC, LSC, and LCM particles. The addition of citric acid increased the Sw of the LSC and LCM particles from 39.0 m2 g−1 to 48.0 m2 g−1 and from 3.9 m2 g−1 to 22.7 m2 g−1, respectively, but had no effect on Sw of NiO-GDC. Differences in surface structure of the particles might explain this difference in effect of citric acid addition on Sw. shows high magnification SEM images of the surfaces of NiO-GDC, LSC and LCM particles synthesized at Cc = 0 mol L−1 and 0.2 mol L−1. At Cc = 0.2 mol L−1, numerous small pores are visible on the surface of the LSC and LCM particles (), whereas no pores are visible on the NiO-GDC particles (). At Cc = 0 mol L−1, no pores are visible on any of the particles (). The pores on LSC and LCM particles at Cc = 0.2 mol L−1 might be formed by the ejection of CO2 gas and H2O vapor. Therefore, the increase in Sw of LSC and LCM () are due to these pores. Conversely, the constant Sw of NiO-GDC particles was due to the absence of pores. This lack of such pores on NiO-GDC particles might be because pores close after the ejection of CO2 gas and H2O vapor. However, further experiments are necessary to confirm this hypothesis.
TABLE 3 Specific surface areas Sw obtained from N2 adsorption isotherms of NiO-GDC, LSC, and LCM particles
FIG. 6. High magnification SEM images of NiO-GDC, LSC, and LCM powders synthesized at Cc = 0 mol L−1 and Cc = 0.2 mol L−1. (Ctotal = 0.2 mol L−1, Tf1 = 673 K, Tf2 = 1273 K and tr = 16 s.)
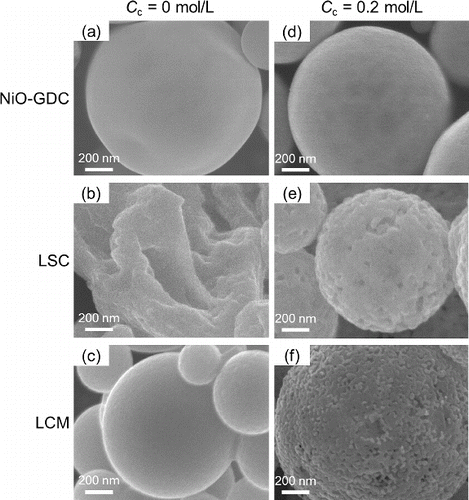
The performance of NiO-GDC as an anode depends strongly on the local distribution of NiO in individual NiO-GDC particles (Wang et al. Citation2008; Liu et al. Citation2008). shows EDX images to determine the local distribution of NiO in the NiO-GDC particles prepared at (a) Cc = 0 mol L−1 and (b) Cc = 0.2 mol L−1. At both Cc = 0 mol L−1 and Cc = 0.2 mol L−1, Ni, Ce, Gd, and O were distributed uniformly in the individual particles.
FIG. 7. EDX images of NiO-GDC particles synthesized at Cc = 0 mol L−1 and Cc = 0.2 mol L−1. (Ctotal = 0.2 mol L−1, Tf1 = 673 K, Tf2 = 1273 K, and tr = 16 s.)
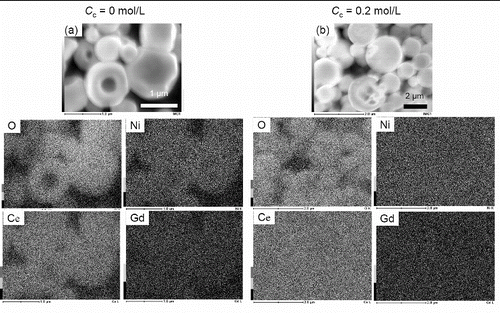
In the SOFC fabrication process, the powders of the SOFC anode and cathode materials are mixed mechanically with binder by using a tumbling ball mill to prepare the printing inks as described in the introduction. To confirm that the particles are not crushed by the ball milling, we tested the NiO-GDC and LCM particles for toughness as follows. Suspensions of NiO-GDC and LCM particles were ground by the tumbling ball mill for 2 h. The 2-h duration was selected because the preparation time of printing ink by a ball mill is 30 min to 2 h. shows the number-size distributions measured by DLS for NiO-GDC and LCM particles before (solid line) and after (dotted line) the 2-h ball milling. NiO-GDC particles show a main peak at about Dp = 500 nm and a secondary peak at about Dp = 3500 nm (), and LCM particles at about Dp = 600 nm and Dp = 3000 nm, respectively (). These main peaks are due to primary particles shown in because Dp = 500 and 600 nm of these main peaks are similar to the Dpg = 523 nm and 663 nm obtained from SEM images ( and ). For both the NiO-GDC and LCM particles, Dpg of the main peaks before and after grinding are similar, although the heights of secondary peaks reduce by the grinding. These results reveal that the sponge-like structured NiO-GDC and LCM particles are not crushed by the grinding, and that the secondary peaks are due to agglomeration of the primary particles (i.e., the porous submicron particles). These agglomerates can be easily separated into their primary particles by ball milling. Therefore, such agglomerates are not undesirable for the fabrication of SOFCs because the synthesized particles are mixed with binder (usually PEG) by the ball mill to prepare the printing ink. Thus, these particles synthesized by the CA-USP method are useful for printing inks of anode and cathode.
FIG. 8. Number size distributions of (a) NiO-GDC and (b) LCM particles measured by DLS before (solid lines) and after (dotted lines) a 2-h ball mill grinding. Particles were synthesized at Ctotal = Cc = 0.2 mol L−1, Tf1 = 673 K, Tf2 = 1273 K, and tr = 16 s.
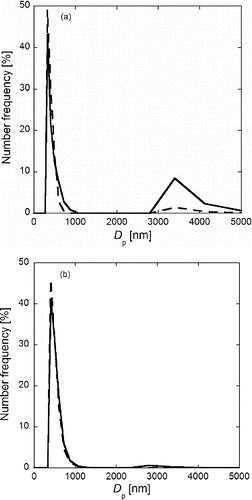
To clarify the formation process of the sponge-like structure, GDC particles were synthesized at various furnace temperatures Tf2 = 473, 673, 873, and 1072 K. Precursors of Ce(NO3)3·6H2O and Gd(NO3)3·6H2O were dissolved in pure water in the stoichiometric ratio of GDC at Ctotal = 0.2 mol L−1, Cc = 0.2 mol L−1, and tr = 16 s. shows the XRD patterns of the synthesized particles with the JCPDS 75-0161 of GDC, and shows the SEM images. The XRD patterns reveal that amorphous GDC particles formed at Tf2 = 673 K and crystallized at Tf2 ≥ 873 K. SEM images reveal that the sponge-like structures formed at Tf2 ≥ 673 K but not at Tf2 = 473 K. These results suggest that the sponge-like structures are already formed when particles are amorphous, that is, before the onset of crystallization.
FIG. 9. XRD patterns of GDC particles synthesized at Tf1 = 673 K, Tf2 = 473, 673, 873, and 1073 K (Ctotal = Cc = 0.2 mol L−1 and tr = 16 s) with JCPDS 78-0161 of GDC (black bars).
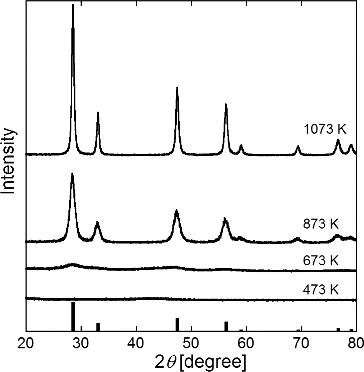
FIG. 10. SEM images of GDC particles synthesized at Tf1 = 673 K, Tf2 = (a) 473, (b) 673, (c) 873, and (d) 1073 K. Ctotal = Cc = 0.2 mol L−1, and tr = 16 s.
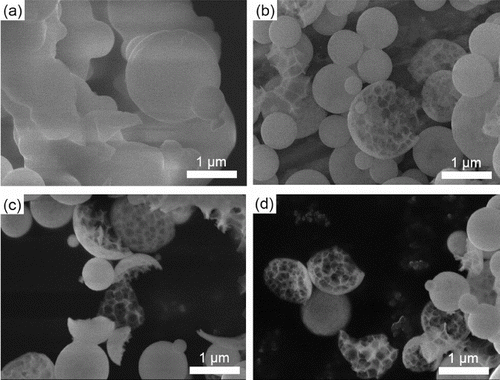
These results reveal the following mechanism in the formation of sponge-like particles by the CA-USP method. In the first step, the citric acid precipitates from the solution in the droplet at Tf2 < 473 K because its solubility is less than that of the precursors. After this precipitation, the precursors deposit in the other space where is not occupied by the precipitated citric acid. In the second step, amorphous GDC particles are produced from precursors by thermal decomposition, and the citric acid is removed from these amorphous particles by combustion at 473 K < Tf2 < 673 K. The result is porous particles. In the final step, sponge-like structured particles are crystallized and sintered at Tf2 > 873 K. Smaller reaction spaces formed by the precipitation of citric acid suppress the growth of crystallites and thus smaller crystallites are produced (NiO, GDC, and LCM; ) and the numerous pores formed in the amorphous particles increase the particle sizes (). This hypothesis of crystallite size does not explain why the crystallite size of LSC is unaffected by citric acid addition. Further experiments involving LSC particle synthesis are needed to propose a valid explanation. Similarly, more experimental data are needed to discuss the irregular morphology of LSC particles synthesized without citric acid.
CONCLUSIONS
Ultrasonic spray pyrolysis method to synthesize porous submicron particles of SOFC electrode materials was developed in which citric acid is added in a precursor solution. This citric acid-addition ultrasonic spray pyrolysis (CA-USP) method was used to synthesize NiO-GDC particles for SOFC anodes and synthesize LSC and LCM particles for SOFC cathodes at a furnace temperature of 1273 K, reaction time of 16 s, total metal ion concentration of 0.2 mol L−1 and citric acid concentration of 0.2 mol L−1. All three types of synthesized particles were submicron-size, spherical, highly porous, and had a sponge-like structure. EDX images for the NiO-GDC particles revealed that Ni, Ce, Gd, and O were uniformly distributed within the individual particles. The sponge-like structured NiO-GDC and LCM particles were not crushed by 2-h ball mill grinding in water.
GDC particles were synthesized at various furnace temperatures between 473 and 1073 K to clarify the formation process of the sponge-like structure. XRD patterns and SEM images revealed that the sponge-like structures were already formed when the particles were amorphous.
Additional information
Funding
REFERENCES
- Brandon, N. P., Blake, A., Corcoran, D., Cummimg, D., Duckett, A., El-Koury, K., et al. (2004). Development of Metal Supported Solid Oxide Fuel Cells for Operation at 500–600 C. J. Fuel Cell Sci. Technol., 1–1:61–65.
- Chen, C. Y., Tseng, T. K., Tsai, S. C., Lin, C. K., and Lin, H. M. (2008). Effect of Precursor Characteristics on Zirconia and Ceria Particle Morphology in Spray Pyrolysis. Ceram. Int., 34:409–416.
- Djurado, E., and Meunier, E. (1998). Synthesis of Doped and Undoped Nanopowders of Tetragonal Polycrystalline Zirconia (TPZ) by Spray-Pyrolysis. J. Solid State Chem., 141:191–198.
- Dong, F., Huang, Yu., Zou, S., Liu, J., and Lee, S. C. (2011). Ultrasonic Spray Pyrolisis Fabrication of Solid and Hollow PdWO4 Spheres with Structure-Directed Photocatalytic Activity. J. Phys. Chem. C, 115:241–247.
- Gaudon, M., Djurado, E., and Menzler, N. H. (2004). Morphology and Sintering Behavior of Yttria Stabilized Zirconia (8-YSZ) Powders Synthesized by Spray Pyrolysis. Ceram. Int., 30:2295–2303.
- Hammouche, A., Siebert, E., and Hammou, A. (1989). Crystallographic, Thermal and Electrochemical Properties of the System La1-xSrxMnO3 for High Temperature Solid Electrolyte Fuel Cells. Mater. Res. Bull., 24:367–380.
- Haile, S. M. (2003). Fuel Cell Materials and Components. Acta Material., 51:5981–6000.
- Kawano, M., Yoshida, H., and Inagaki, T. (2011). Synthesis of Anode Material for Solid Oxide Fuel Cell by Spray Pyrolysis and Its Cell Performance. J. Soc., Powder Technol. Japan, 48:376–380.
- Kinoshita, T., and Adachi, M. (2014). Submicron Particle Synthesis of Gd0.1Ce0.9O1.95, NiO-Gd0.1Ce0.9O1.95 and La0.8Sr0.2CoO3 by Ultrasonic Spray Pyrolysis. J. Chem. Eng. Jpn. (in press).
- Kinoshita, T., Arastoo, A., Maruco, H., and Adachi, M. (2014). Synthesis of Porous Submicron Gd0.1Ce0.9O1.95 Particles by Carbon Nanoparticle-Addition Ultrasonic Spray Pyrolysis (CNA-USP) and Nanoparticle Preparation by Ball Milling. Aerosol Sci. Technol., 48:1080–1088.
- Liu, Y., Hashimoto, S., Takei, K., Mori, M., and Funahashi, Y. (2008). Development and Characterization of Cathode-Supported SOFCs by Single-Step Cofiring Fabrication for Intermediate Temperature Operation. J. Fuel Cell Sci. Tech., 5:031209.
- Matsuda, K., and Taniguchi, I. (2004). Relationship Between the Electrochemical and Particle Properties of LiMn2O4 Prepared by Ultrasonic Spray Pyrolysis. J. Powder Sources, 132:156–160.
- Mesguich, D., Bassat, J.-M., Aymonier, C., Brüll, A., Dessemond, L., and Djurado, E. (2013). Influence of Crystallinity and Particle Size on the Electrochemical Properties of Spray Pyrolyzed Nd2NiO4+δ Powders. Electrochim. Acta, 87:330–335.
- Mesguich, D., Bassat, J. -M., Aymonier, C., and Djurado, E. (2010). Nanopowder Synthesis of the SOFC Cathode Material Nd2NiO4+δ by Ultrasonic Spray Pyrolysis. Solid State Ionics, 181:1015–1023.
- Messing, G. L., Zhang, S. C., and Jayanthi, G. V. (1993). Ceramic Powder Synthesis by Spray Pyrolysis. J. Am. Ceram. Soc., 76:2707–2726.
- Okuyama, K., and Lenggoro, I. W. (2003). Preparation of Nanoparticles via Spray Route. Chem. Eng. Sci., 58:537–547.
- Okuyama, K., Shimada, M., Adachi, M., and Tohge, N. (1993). Preparation of Ultrafine Superconductive Bi-Ca-Sr-Cu- Particles by Metalorganic Chemical Vapor Deposition. J. Aerosol Sci., 24:357–366.
- Suda, S., Takahashi, S., Kawano, M., Yoshida, H., and Inagaki, T. (2006). Effects of Atomization Conditions on Morphology and SOFC Anode Performance of Spray Pyrolyzed NiO-Sm0.2Ce0.8O1.9 Composite Particles. Solid State Ionics, 177:1219–1225.
- Sun, C., and Stimming, U., (2007). Recent Anode Advances in Solid Oxide Fuel Cells. J. Power Sources, 171:247–260.
- Suzuki, T., Yamaguchi, T., Fujishiro, Y., and Awano, M. (2006). Fabrication and Characterization of Micro Tubular SOFCs for Operation in the Intermediate Temperature. J. Power Sources, 160:73–77.
- Wang, Z., Lui, Y., Hashimoto, S., and Mori, M. (2008). Nanocomposite Ni-CGO Synthesized by the Citric Method as a Substrate for Thin-Film IT-SOFC. J. Korean Ceram. Soc., 45:782–787.
- Wyrzykowski, D., Hebanowska, E., Nowak-Wiczk, G., Makowski, M., and Chmurzynski, M. (2011). Thermal Behaviour of Citric Acid and Isomeric Aconitic Acids. J. Therm. Calorim, 104:731–735.
- Yamamoto, O., Takeda, Y., Kanno, R., and Anderson, H. U. (1987). Perovskite-Type Oxides as Oxygen Electrodes for Hifh Temperature Oxide Fuel Cells. Solid State Ionics, 22:241–246.
- Yoshida, T. (2012). Particle Synthesis of Solid Oxide Fuel Cell Materials by Citric Acid Addition-Ultrasonic Spray Pyrolysis. Master thesis at Osaka Prefecture University (in Japanese).