ABSTRACT
Particle size is a vital characterization for silicon nitride nanoparticle as its scale determines its application area. Particle size prediction for synthesis of silicon nitride nanoparticle by chemical vapor deposition (CVD) is much needed. In this study, a model is proposed for particle growth during silicon nitride nanoparticle synthesis by CVD in order to predict particle size. Comparison between modeling and experimental results validated the model. The modeling results showed that lower pressure in the condensation room would be an effective way of obtaining silicon nitride nanoparticles with smaller particle size. An expression is established to reveal the relation between the mean particle diameter of silicon nitride nanoparticle and pressure in the condensation room based on the modeling. The modeling method is capable of predicting the mean particle size of ultrafine silicon nitride powder to within 3.6% accuracy. Corresponding manufacturing thermal parameters are recommended for silicon nitride nanoparticle production with different mean particle sizes. Modeling and analysis in this article may provide theoretical guidance for production of silicon nitride nanoparticle by CVD.
© 2017 American Association for Aerosol Research
EDITOR :
1. Introduction
As efficient additives for improving the performance of conventional materials, nanoparticles are of great value in powder applications for many industries, such as chemical engineering, electronic engineering, and astronautics technology. Studies have shown novel characteristics of ultrafine powders in many aspects. For example, Hajmohammadi et al. (Citation2015) discovered that nano-particles (such as Cu and Ag) have advantages of enhancing thermal conductivities of fluids. Of all of the nanoparticles, silicon nitride nanoparticle has received more attention in recent decades due to its properties, such as thermal stability, a high of hardness, excellent high temperature properties, and corrosion resistance (Kshirsagar et al. Citation2011; Legut et al. Citation2014). Silicon nitride nanoparticle can be either an excellent additive or a great performance material in laboratory studies (Wananuruksawong et al. Citation2015; Yang et al. Citation2016).
In fact, in recent decades, several processes have been developed for laboratory-scale synthesis of silicon nitride nanoparticle, such as the direct nitridation of silicon, sol–gel methods, and chemical vapor deposition (CVD; Kavecky et al. Citation2000; Wang et al. Citation2006; Won et al. Citation2010; Yang et al. Citation2011; Li et al. Citation2012). In general, the processes could be divided into three categories: solid-state reaction method, liquid-state reaction method, and gas-state reaction method. Of all the methods to produce silicon nitride nanoparticle, CVD has attracted considerable attention in recent years. To begin with, CVD was used to deposit thin film, and it is still a common way to fabricate ultrathin film (Wright et al. Citation2008). Today CVD is attractive to researchers as an excellent way of producing ultrafine powders with narrow particle size distribution and high purity.
In fact, ultrafine silicon nitride powders can be used to manufacture composite materials, and the particle size of particles is a significant factor influencing the performance of composite materials. Any changes to particle size can greatly affect the size-determined nano-properties or potential nano-properties. This leads to the fact that particle performance and application areas vary in relation to particle size. Hence, it will benefit industrial production greatly once particle size can be accurately predicted in relation to given producing conditions.
A number of researchers have investigated synthesis of silicon nitride nanoparticle by conducting experimental studies. These studies focused on effects of preparation conditions on powder characteristic. Lu et al. (Citation1999) investigated the appearance and microscopic structure of silicon nitride powder activated by the shock waves of two different pressures (i.e., 15.7 and 25.6 GPa), where the results show that the bending strength of the sintered ceramics activated by the shock waves is also related to the sintering temperature. Pawelec et al. (Citation2002) obtained silicon nitride powders from the reaction of silicon dioxide powders with ammonia, and this method is economic and easy to perform. This article investigated the synthesis method as Pawelec et al. did in their research. Yang et al. (Citation2012) uncovered the effects of the pelletization of reactants and silicon nitride diluents on the combustion process parameters and the characteristics of products, where, as the content of the diluents was increased, the morphologies of the Si3N4 particles changed from short rods into equiaxed grains, and the residual Si in the final products obviously decreased. Hashimoto et al. (Citation2015) investigated the effect of deposition atmosphere on the phase composition and microstructure of silicon carbide film prepared by laser CVD, where the relationship between the reciprocal deposition temperature and deposition rate for SiC films was mapped using conventional CVD and laser CVD. These studies have explored a number of possible and convenient ways for synthesis of silicon nitride nanoparticle, and have investigated the effect of process parameters on synthesis of silicon nitride nanoparticle.
Modeling studies of CVD process are also an effective way to investigate nanoparticle formation mechanisms. Park et al. (Citation1999) predicted particle size distributions produced by the modified CVD process through solving two-dimensional aerosol dynamics equation, and investigated scope of application by one-dimensional analysis. Dang and Swihart (Citation2009) did a series work regarding computational modeling of silicon nanoparticle synthesis, and compared results predicted by different simulation methods. Hidayat et al. (Citation2010) used both experimental and computational methods to study droplet-to-particle formation of zinc oxide by low-pressure spray pyrolysis process, and concluded that the primary determinant of particle size during this process is pressure. Loeffler et al. (Citation2011) performed large eddy simulations to study formation and growth of titanium dioxide nanoparticles in turbulent jets, and predicted mean particle size well. Liu and Xiao (Citation2014) applied an Eulerian–Eulerian two-fluid model coupled with population balance equation to simulate the evolution of silicon particle growth by chemical vapor deposition of silane pyrolysis. They found that growth rate increased with the augmentation in silane concentration due to enhancement of surface deposition and cluster scavenging, and decreased with the decrease in fluidizing velocity due to poor solid distribution. These models paved the way for models of particle size prediction of silicon nitride nanoparticles prepared by CVD. Models of particle size prediction are needed for industrial application, and can help unravel mechanisms of particle formation by CVD method.
Theoretical study and experimental work is helping to develop an understanding of particle growth phenomena within the process, but much still remains to be done. The existing modeling studies concentrate on solutions either of fluid dynamics, or of aerosol dynamics. They have successfully revealed distributions of physical quantities (such as temperature, pressure, and gas flow velocity), and predicted particle size distribution. However, they can provide little information regarding details of particle micro-growth process. Few modeling concentrates on the micro-growth mechanism of the particle. A better understanding of the mechanism of nanoparticles production by CVD is much in need. Knowledge of how the process conditions affect particle sizes is still poor. This article intends to shed some light on the particle micro-growth by establishing a model based on the molecules collision theory and energy analysis of the particle. The behavior of particles during the CVD production process is very challenging as the particles grow extremely rapidly (within seconds). Under such circumstances, modeling can provide information that experimental measures cannot obtain. One of the principal objectives of this article is to give accurate prediction for the mean diameter of silicon nitride nanoparticle prepared by CVD. The other main objective of this article is to establish physical and mathematical models of the nanoparticle growth, and then reveal mechanisms of nanoparticle growth by CVD. The results will make it possible to predict the particle size of ultrafine silicon nitride powder produced by CVD accurately.
2. Methodology
This article discusses silicon nitride that was prepared by laser-driven thermochemical reactions between silane and ammonia. This is possible because the practical application of laser technique is well developed, and silane and ammonia are easily accessible industrial materials. Nanoparticles were attained by means of employing argon (whose boiling point is around 87.45 K) to cool silicon nitride gas rapidly. During the preparation procedure, there were four principal processes: thermochemical reaction, nucleation, condensation (/condensation nuclei growth), and deposition. There were energy variations throughout the four processes. A model for particle growth was developed, based on a detailed analysis of energy variations of reaction, nucleation, condensation, and deposition.
2.1. Modeling
Energy minimization and effective collision theory are the principal theoretical bases of modeling used in this article. When silicon nitride particles are under investigation, the four processes during the preparation procedure can be divided into two categories: energy generating and energy dissipating. Energy variation during the four processes is shown in Equation (Equation1
[1] ). A plus sign means that heat is generated through the process and needs to be dissipated; while a minus sign means that heat can be dissipated though the process:
[1] where
is the energy variation of the thermochemical reaction process, W;
is the energy variation during the condensation process, W;
is the energy transferred through radiation, W; and
is the energy transferred through convection.
The energy generating and energy dissipating processes can be analyzed separately since there are few coupling effects between these two kinds of processes. As energy dissipating processes are controllable by adjusting thermal parameters, they will be analyzed first.
2.1.1. Energy dissipating processes
There are two ways of transferring heat to dissipate energy in the ultrafine powder production process by CVD: radiative and convective heat transfer. Heat radiation does not require the presence of an intervening medium. On the other hand, convection only happens when there is an intervening medium. Radiation and convection are regarded as mutually independent processes, so the superposition of these two heat transfer processes is taken as the ultimate amount of heat dissipated by the condensation nuclei. Therefore, two energy dissipating models (the radiative heat transfer model and the convective one) are established, respectively, in the following section. A physical model of the two thermal processes is as shown in .
Figure 1. Physical model for radiation and convection in ultrafine silicon nitride production through CVD. This represents silicon nitride nucleation and the condensation process of cooling by argon. Silicon nitride molecules result from the thermal chemical reaction between silane and ammonia. is the energy dissipated though radiative heat transfer, and
is the energy dissipated though convective heat transfer.
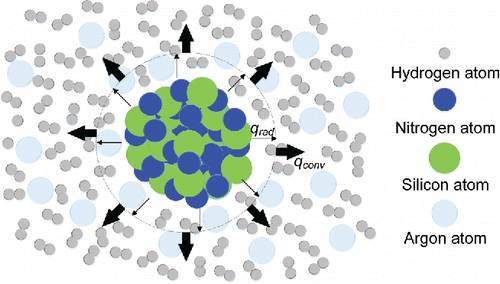
In the radiative heat transfer model, energy is released only by radiation. When silane vapor and ammonia vapor are in the reaction chamber, they are at the same temperature; so at this stage, radiation happens between the vapor and the reaction chamber wall. Radiation during this period is negligible because the temperature difference is relatively small. Inert gas is supplied after the reaction is completed. At this stage, the temperature difference between the condensation nuclei of silicon nitride and the inert gas atmosphere will be large. Therefore, the radiative heat transfer between them is analyzed here.
The third term in Equation (Equation1[1] ) describes energy variation through radiative heat transfer. Radiative heat transfer is a spontaneous process when there is temperature difference, so it depends mainly on the temperature of the condensation nucleus and that of reaction chamber. Based on the Stefan–Boltzmann law, surface radiative heat transfer in this case can be expressed as follows:
[2] where
is the molecule number in the silicon nitride condensation nucleus,
is the molecule density inside the silicon nitride condensation nucleus,
is the diameter of the silicon nitride molecule, m;
is the Stefan–Boltzmann constant, σb = 5.67 × 10−8 W/ (m2⋅K4);
is the surface emissivity of the condensation nucleus;
is the surface temperature of the condensation nucleus, K;
is the ambient temperature in the reaction chamber, K.
The last term in Equation (Equation1[1] ) is energy variation through convective heat transfer. In the convective heat transfer model, energy is released only by convection. Convection occurs only when the cooling medium (argon) is flowing in the reaction chamber. Convection involves the combined effects of conduction and fluid motion. The faster the fluid motion, the greater the convection heat transfers. From a micro perspective, fluid motion causes molecule collisions, and energy will be transferred as a result. In fact, micro-mechanisms of heat convection are heat transfer resulting from collisions between molecules/atoms. Therefore, the frequency of collisions between gas molecules and atoms and the energy exchanged through a collision will be analyzed below.
Equation (Equation3[3] ) shows the definition of temperature from thermodynamics:
[3]
Collisions between silicon nitride molecules and argon atoms will hardly cause bonding between them, so these collisions are regarded as perfectly elastic collisions in this study. The kinetic energy exchange rate in a perfectly elastic collision is one third. As the average translational kinetic energy of a molecule can be obtained from Equation (Equation3[3] ), kinetic energy exchange through a collision is
(that equals to
). shows the energy exchanges resulting from a series of collisions between heterogenous molecules and atoms.
Figure 2. Energy exchanges because of collisions between silicon nitride molecules and argon atoms. Solid spheres in this figure represent silicon nitride molecules, and hollow ones represent argon atoms. Changes in color show how energy is transmitted. Assume , and
represents the initial temperature of the silicon nitride vapor,
represents the initial temperature of the inert gas.
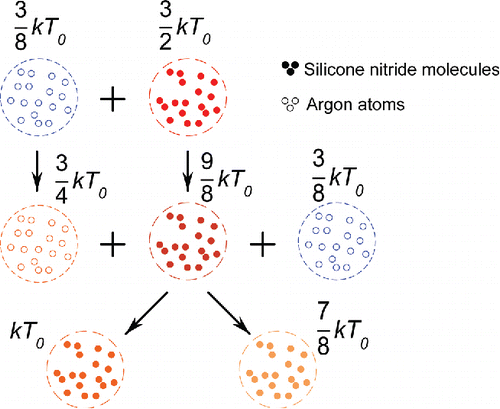
Heat convection is the heat transfer resulting from collisions between molecules and atoms. Therefore, unlike radiative heat transfer, convective heat transfer depends greatly on the frequency of collisions of gas molecules .
is different from
in the condensation process (
will be used in an energy analysis of the condensation process), because the collision object is different.
is the frequency of collisions between condensation nuclei and silicon nitride molecules, and
is the frequency of collisions between silicon nitride molecules and argon atoms.
can be expressed as follows (Maitland Citation1981; Mortimer Citation2008):
[4]
Based on the micro-mechanisms of the heat convection, the rate of heat convection for the condensation nucleus is obtained by Equation (Equation5[5] ):
[5] where
is the heat absorbed by the argon molecule when its temperature rises by a unit of temperature, J/K;
is the total collision frequency between the inert gas molecules and the vapor molecules, m−3 s−1;
is the number density of the vapor molecules, m−3;
is the number density of the inert gas molecules, m−3;
is the temperature increase of the argon vapor, K;
is the mean temperatures of the vapor molecules and condensation nuclei, K;
is the temperature of the inert gas, K; and
is the molecule mass of the inert gas, kg.
2.1.2. Energy generating processes
Energy generating processes in this study include thermochemical reaction process (since reaction between silane and ammonia is an exothermic reaction) and condensation process (which combines nucleation, condensation, and deposition). The two processes will be analyzed in detail.
The energy variation of the thermochemical reaction process can be denoted by the energy difference between the previous chemical bonds and the new ones. The chemical reaction equation is as follows:[6]
Energy variation can be obtained through energy difference between the bonding energy of the product and that of the reactant, as shown in the following Equation (Equation7[7] ):
[7]
Here represents the total bonding energy of all the products, J;
represents the total bonding energy of all the reactants, J.
In this article, assumption is made that the noncovalent bonds energy (including hydrogen bond N−–H+ and Van der Waals forces between polar molecules) are negligible. Only the chemical bond energy is considered in determining the energy variation of the thermochemical reaction process. Reasons are that, in the reaction shown as Equation (Equation6[6] ), order of the chemical bond energy is 106 J/mol, while orders of the hydrogen bond and Van der Waals forces are 104 J/mol and 103 J/mol, respectively. A hundredfold difference between orders of magnitude guarantees that noncovalent bonds energy has little effect on the accuracy of the results.
can be derived by
. The object of Equation (Equation1
[1] ) is a single particle, and the object of the
analyzed above is a large number of particles. So
is converted here. Hence, the coefficient
is multiplied by the
as shown in the following Equation (Equation8
[8] ):Here,
.
[8] where
is the molecule diameter, m;
is the density number of the vapor molecules, m−3;
is the Avogadro constant,
;
is Boltzmann's constant, k = 1.38 × 10−23 J/K;
is the mean temperature of the vapor molecules and condensation nuclei, K;
is the molecule mass of the vapor, kg.
Condensation and deposition are analyzed together because from the micro perspective, they are all related to the bonding of molecules caused by collisions resulting from attractive forces between molecules, and there are no chemical changes in these processes. Nucleation occurs when silicon nitride molecules collide and bond together, then to form nuclei. Condensation occurs when nuclei attract silicon nitride molecules to grow larger. The physical mechanisms of the three processes are identical, and involve the colliding and bonding together of the molecules. Therefore, they are expressed by the same equation in this article; and they are referred to as the condensation process.
In order to analyze the variation in energy before and after the molecules bond, the collision frequency between the condensation nuclei and the vapor molecules should be determined first. Then the probability of bonding taking place because of collision should be determined. is the variation in energy resulting from silicon nitride molecules bonding after collision. At a certain temperature and molecule density, molecules collide into each other at a certain frequency. However, not all collisions will lead to bonding. So Equation (Equation9
[9] ) shows the definition of
.
[9] where
is the probability of bonding as a result of collision between the condensation nuclei and the silicon nitride molecules;
is the total frequency of collisions between the condensation nuclei and the silicon nitride molecules, m−3 s−1;
is the energy released from each molecule when it condensates on the surface of a condensation nucleus, J.
is affected by the angle, velocity, and area of collision. The collision bonding probability decreases with the increase of collision velocity, while it increases with the increase of collision angle and collision area. Invalid collision is collision without bonding. When a condensation nucleus is small, as molecules inside this condensation nucleus increase, the collision area increases and collision velocity decreases. Therefore, collision-bonding probability between the condensation nucleus and the molecules in the space increases rapidly. When the condensation nucleus grows larger, as molecules inside this condensation nucleus increase, the collision bonding probability increases less rapidly. Invalid collision decreases with the increase of number of molecules inside the condensation nuclei. Collision bonding probability cannot exceed one. Therefore, collision-bonding probability between the condensation nuclei and vapor molecules in this article is determined as follows (Xia et al. Citation2014):
[10] where
is a constant,
is the number of molecules in one condensation nucleus. The second term on the right represents invalid collision probability.
, the frequency of collision between the condensation nuclei and vapor molecules, is then investigated. Condensation nuclei can be regarded as multi-molecular particles as they are small at the nucleation stage. The relationship between the volume of the molecules and that of condensation nuclei is as follows:
[11] where
is the number of molecules inside a condensation nucleus;
is the molecule diameter, m;
is the nucleus diameter, m; and
is the molecule compactness inside a condensation nucleus.
Based on the above analysis, can be obtained as follows:
[12] where
is the number density of the molecules of inert gas, m−3;
is the number density of the condensation nuclei, m−3;
is the molecule density inside the condensation nucleus;
is the molecule diameter, m;
is Boltzmann's constant, k = 1.38 × 10−23 J/K;
is the vapor temperature, K;
is molecule mass of the vapor, kg:
[13] where
is the pressure in the condensation room, Pa;
is the universal gas constant, R = 8.314 J/(mol. K); and
is temperature of the argon gas, K:
[14] where
is the reaction temperature in the condensation room, K.
So the energy variation during condensation process is as follows:
[15]
remains almost constant once all the conditions in the condensation room have been settled.
and
are determined by
. Therefore, there are two unknown variables in Equation (Equation15
[15] ), namely, the number of molecules number inside a condensation nucleus
and pressure in the condensation room
.
From the above analysis (Sections 2.1.1 and 2.1.2), the energy variation through the four processes can be obtained as in Equation (Equation16
[16] ):
[16] where
,
, and
.
,
, and
are used here to shorten the equation.
In Equation (Equation16[16] ), there are two unknown variables, the number of molecules inside a condensation nucleus
and the energy variation
. All the other parameters are fixed when the production conditions are established. Because the volume of the condensation room is fixed, its temperature is set at a certain level in these experiments. Therefore, from the physical and mathematical models established in this article, through changing the value of
, the relationship between
and
can be discovered.
2.2. Solution
Energy variation exists in every collision bonding; therefore, the state of the nucleus can be determined by analyzing the energy variation of every collision bonding. The stop condition of the calculation is based on the minimum energy minimization principle. When energy that needs to be dissipated is equal to energy that can be dissipated through radiation and convection, a balanced state is reached. This is the state when a condensation nucleus is about to deposit. Thus, the total variation in energy can be determined by computing integration from zero to for
. When the solution of Equation (Equation17
[17] ) is found, the calculation should be terminated, and the current
will be the number of molecules in the deposited powder.
[17]
The simulation process is as shown in . Molecules are uniform in the experiment chamber, so condensation nuclei grow uniformly in every direction. Hence, powder prepared by this method is approximate to sphere because of isotropy. In part 2.3, experiments will also verify that powder prepared by this method is approximate to sphere. After the number of molecules in the deposited powder is determined, the diameter of the powder
can be obtained by Equation (Equation18
[18] ):
[18]
2.3. Modeling verification
Because modeling results can provide continuous data at regular intervals for analysis, the modeling established in 2.1 will be used to discover the relation between the thermal parameter p (pressure in condensation room) and the characteristic (particle size) of particles prepared by CVD. Before this, the suitability of the modeling in 2.1 should be verified.
In order to test whether models established in 2.1 are reliable, three experiments were conducted, as shown in . Corresponding experimental parameters were as follows. Ratio of silane/ammonia was five to one. Gas flow of reactant was m3/s, and that of argon was
m3/s. Laser heating power was 1000 W. Three experiments were conducted under three different pressures. The three pressure values in these experiments were 35.5 kPa, 50.7 kPa, and 81.1 kPa.
Figure 4. Flow diagram of laser-driven CVD experiment; feed gas are silane and ammonia, inert gas is argon.

The purpose of this article is to study particle size, which will in turn be used as a criterion to test the modeling of part 2.1. The particles of the powders prepared are spherical, thereby conforming to modeling analysis. Hence, the characterization parameter of particle size is the diameter of the sphere. By inputting three pressure values into the models, particle diameters will be determined. In addition, the mean particle diameters of silicon nitride powder prepared in three experiments were recorded. In order to verify the results calculated by models established in this article, comparisons between calculated results and experimental results are made, as shown in .
As can be seen from , the data points of calculated mean powder diameters coincide perfectly with the experimental ones. All three relative errors of diameter calculations are less than 3.6% compared with experimental results. Considering experimental error, relative errors of less than 3.6% between calculations and experiments is low enough to be negligible. Therefore, the modeling results are validated as accurate, and can be used in the following analysis.
3. Results and discussion
As modeling in 2.1 has been verified to be reliable, it will be used to explore the relationship between pressure in the condensation room and the size of particles prepared by CVD, and mechanisms of the four processes (reaction, nucleation, condensation, and deposition). All the results obtained here are acquired from modeling established in the preceding part of the article.
3.1. Particle size
Under the experimental conditions established in this study, mean powder diameter is mainly affected by absolute pressure in the reaction/condensation room. Therefore, absolute pressure in the chamber is the main thermal parameter studied in this article. When sum of the heat radiation and the convection of the condensation nucleus (which are energy that can be dissipated) is equal to that of the energy that needs to be dissipated, this condensation nucleus will reach a steady state, and will then deposit. This is based on the energy minimization principle. One objective of this study is to unravel the impact of thermal parameters on the diameter of silicon nitride powder prepared by CVD method. The diameter of silicon nitride powder studied in this article is a mean diameter. The relation between particle diameter and pressure in the condensation room
is shown in .
Figure 6. Diameter of silicon nitride particle and molecule number in the particle as a function of pressure in the condensation room.
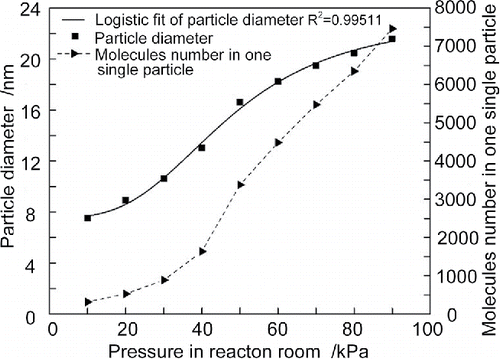
indicates an overall trend is the mean diameter of the particles increases with increase of pressure in the condensation room. The diameter of the particle increases slowly when pressure is lower than 30 kPa, and rapidly when pressure is between 30 kPa and 60 kPa, and then increases slowly again when pressure is higher than 60 kPa. However, the number of molecules in one single particle increases slowly at the lower pressure (<30 kPa), then continues to increase rapidly when pressure is higher than 50 kPa.
At the lower pressure (<30 kPa), the growth of condensation nuclei is slower and more difficult because the probability of molecules colliding and bonding is rather small. So at this point, the diameter of the particle increases smoothly and steadily with the increase of the pressure in the condensation room. When pressure is between 30 kPa and 60 kPa, the diameter of the particle increases rapidly with the increase of pressure in condensation room. This is because the probability of molecules colliding and bonding increases as pressure in the condensation room increases. At the higher pressure (>60 kPa), the number of molecules in one single particle increases rapidly, but the diameter of the particle increases slowly. Increasing regularities in the number of molecules in one particle and in particle diameter are clearly different. The reason is that, as the diameter increases, very many more molecules are needed for further diameter increase.
In order to quantify the relation between the diameter of the particle and pressure in the condensation room, a regression analysis is made using sigmoid function, as shown in . The relation function between the mean diameter of silicon nitride powder and the pressure in the condensation room can be expressed as the following equation:[19] where
is the mean diameter of silicon nitride powder prepared by CVD;
;
;
;
;
is the absolute pressure in the condensation room.
Rapid cooling is the principal means used in CVD to obtain nanometer scale powders. As can be derived from Equation (Equation19[19] ), a mean diameter
reaches its minimum value, which is 7.57, when absolute pressure
equals zero. This means that by means of rapid cooling, as absolute pressure in the condensation room decreases, the mean diameter of the powder cannot be smaller than 7.5 nm. Thus, it is not very meaningful to pursue the lowest pressure in the condensation room. In the meantime, Equation (Equation19
[19] ) indicates that a mean diameter
reaches its maximum value, which is 23.30, when absolute pressure
goes to infinity. This means that at atmospheric pressure (or higher pressure), by means of rapid cooling, powders with a minimum mean powder size of 23.3 nm can be prepared.
Equation (Equation19[19] ) can be applied as empirical equation of the relation between mean diameter and absolute pressure in the condensation room. When absolute pressure is below 100 kPa or the mean diameter of the powder is smaller than 22 nm, this empirical equation has an accuracy of up to 95%. In industrial application, when a certain powder diameter of silicon nitride is needed, absolute pressure in the condensation room can be determined according to Equation (Equation19
[19] ).
3.2. Energy analysis
In order to observe the effect of absolute pressure in the condensation room on energy variation
as a function of
, is obtained by employing known parameters in Equation (Equation16
[16] ). As can be seen in , when absolute pressure
is fixed,
decreases from greater than zero to less than zero; and
decreases as
decreases.
means the energy that can be dissipated by heat radiation and convection of the condensation nucleus is less than the energy of the condensation nucleus that needs to be dissipated by radiation and convection, while
means the opposite.
Figure 7. Energy variation of the condensation nucleus under different absolute pressure in the condensation room as a function of the number of molecules in the particle.
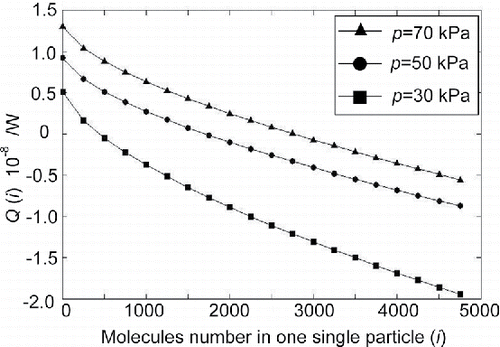
The tendency of energy variation as shown in explains why an increase of particle diameter fits to an S-shape curve (in ). At lower pressure (<50 kPa), energy that needs to be dissipated does not increase as rapidly as that which can be dissipated by radiation and convection, so energy variation
decreases sharply. Therefore, the condensation nucleus will deposit at a relatively early stage. This will lead to the mean powder diameter being relatively small. At higher pressure (>50 kPa), energy needing to be dissipated increases more rapidly than that which can be dissipated by radiation and convection, so energy variation
decreases relatively slowly. Hence, a steady state is not easy to reach, and the condensation nucleus will deposit at a relatively late stage. This means that the powder diameter will be relatively large.
3.3. Mechanisms
This article discusses silicon nitride prepared by laser-driven thermochemical reactions between silane and ammonia. Ultrafine silicon nitride powder then is obtained by rapid cooling of silicon nitride vapor using argon gas. Thermochemical reaction process, nucleation, condensation (condensation nuclei growth), and deposition process are the principal processes of preparing ultrafine silicon nitride powder by CVD in this article. shows the four processes.
Figure 8. Mechanisms of ultrafine silicon nitride powder prepared by CVD. (a) The thermochemical reaction process. (b) The nucleation and condensation nuclei growth process, and argon is employed for cooling. (c) The deposition process.
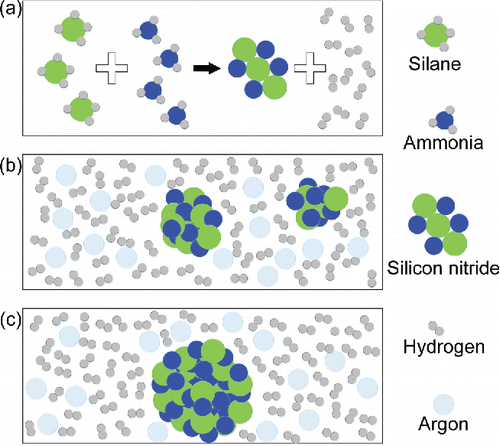
Gaseous thermochemical reaction occurs very rapidly because reactants in this article are both gaseous phase at ambient temperature and atmosphere pressure. The reaction temperature in this study is higher than the ambient temperature; and laser-induced, the reaction rate increases, which accounts for the considerable reduction in the time taken by the atoms to rearrange themselves. As heat transfers into the system, the thermal motions of the atoms are intensified, the molecules present become unstable, and energy needs to be released. Ruptures of present chemical bonds require energy, which can be released through breaks in the bonds, as a result of which ions appear. Suspensions of ions are inherently unstable, which leads to the formation of new chemical bonds. Thus, the thermal chemical reaction process in this study is simplified into an instantaneous energy release/absorption process. The essence of the chemical reaction is the ruptures of the present chemical bonds and the formations of new ones, so the energy difference between the old and new chemical bonds is the most important parameter in this process.
The chosen reactants are in gaseous phase because their intermolecular distances are large. Right after the reaction, the distances between the silicon nitride molecules are still large. This is of great significance for the production of silicon nitride powder with ultrafine diameter, because silicon nitride molecules will not aggregate to large particles immediately if they are far apart. Therefore, silicon nitride and hydrogen should all be in gas phase after the gaseous chemical reaction process. After the rearrangement of the atoms, there follows a transient state, where silicon nitride molecules are conducting gas-to-nuclei phase transition. Silicon nitride molecules collide because of the molecular thermal motion, and adhere because of attractive forces. Modeling results in part 3.1 show a minimum value of particle diameter, which is 7.5 nm. This supports the inference that because collisions between molecules and clusters are inevitable during CVD process, there should exist a minimum value of particle diameter.
The nucleation process can be described as silicon nitride molecules bonding together into nuclei through phase transition. Nuclei growth, the next process after nucleation, is essential for condensation. When a molecule collides with a nucleus, the molecule may bond with the nucleus, or it may bounce off. When molecules bond with nuclei, the outcome will generate energy; this is the condensation process. Energy needs to be released to reach a stable state during the condensation process. As nuclei develop into particles, particles grow into large particles. These large particles will deposit when their self-regulating energy system balances, so that the large particles achieve a stable state. This is the last process of particle growth.
4. Conclusions
Modeling was established to predict the mean particle size of ultrafine silicon nitride powder fabricated by CVD. Comparisons between calculated results and experimental ones showed that models established in this article could predict mean particle diameter by errors of less than 3.6%. The computational cost of the model developed in this article is much lower, and in simple system, the simulation results agree well with the experimental results.
Results show that lower pressure in the condensation room is an effective way of obtaining powders with smaller particle size. To obtain silicon nitride powders with a mean diameter of 20 nm, pressure in the condensation room must be controlled in the range of 75 kPa and 85 kPa. With pressure in condensation room in the range of 40 kPa and 50 kPa, silicon nitride powders with mean diameter of approximately 15 nm can be produced. Keeping lowering the pressure in condensation room, silicon nitride powders with smaller mean diameter could be obtained. However, when the pressure in the condensation room is under 10 kPa, it is meaningless to continue lowering the pressure, and silicon nitride powder with a mean particle diameter of 7–8 nm can be obtained.
The relation between mean diameter of ultrafine powder and pressure in the condensation room can be expressed by a sigmoid function. The relation function indicates that, by means of rapid cooling, as absolute pressure in the condensation room decreases, the mean diameter of the powder cannot be smaller than 7.5 nm. At atmospheric pressure (or higher pressure), by means of rapid cooling, a minimum mean powder size of 23.3 nm can be prepared.
By means of modeling and energy analysis of the energy generating and dissipating processes, the present work identifies microcosmic mechanisms of ultrafine silicon nitride powder by CVD method. Four processes during preparation by CVD are discussed: thermochemical reaction, nucleation, condensation, and deposition.
Nomenclature
Qreaction | = | energy variation of the thermochemical reaction process, W |
Qcondensation | = | energy variation during the condensation process, W |
Qradiation | = | energy transferred through radiation, W |
Qconvection | = | energy transferred through convection, W |
= | total collision frequency between the inert gas molecules and the vapor molecules, m−3 s−1 | |
= | total frequency of collisions between the condensation nuclei and the silicon nitride molecules, m−3 s−1 | |
= | total bonding energy of all the products, J | |
= | total bonding energy of all the reactants, J | |
= | energy released from each molecule when it condensates on the surface of a condensation nucleus, J | |
= | heat absorbed by the molecule when its temperature rises by a unit of temperature, J/K | |
= | diameter of the silicon nitride molecule, m | |
= | nucleus diameter, m | |
= | number density of the vapor molecules, m−3 | |
= | number density of the inert gas molecules, m−3 | |
= | molecule mass of the inert gas, kg | |
= | molecule mass of the vapor, kg | |
= | surface temperature of the condensation nucleus, K | |
= | ambient temperature in the reaction chamber, K | |
= | mean temperatures of the vapor molecules and condensation nuclei, K | |
= | Temperature of the inert gas, K | |
= | temperature increase of the argon vapor, K | |
= | pressure in the condensation room, Pa | |
= | probability of bonding because of collision between the condensation nuclei and the silicon nitride molecules | |
= | surface emissivity of the condensation nucleus | |
= | molecule number in the condensation nucleus | |
= | molecule density inside the condensation nucleus | |
= | Stefan–Boltzmann constant, σb = 5.67 × 10−8 W/ (m2⋅K4) | |
= | Avogadro constant, | |
= | Boltzmann's constant, k = 1.38 × 10−23 J/K | |
= | collision bonding probability constant | |
= | universal gas constant, R=8.314 J/(mol⋅K) |
Funding
This work was supported by the National Key Research and Development Program of China (grant number 2016YFB0601102).
References
- Dang, H., and Swihart, M. T. (2009). Computational Modeling of Silicon Nanoparticle Synthesis: I. A General Two-Dimensional Model. Aerosol Sci. Technol., 43:250–263.
- Hajmohammadi, M. R., Maleki, H., Lorenzini, G., and Nourazar, S. S. (2015). Effects of Cu and Ag Nano-particles on Flow and Heat Transfer from Permeable Surfaces. Adv. Powder Technol., 26:193–199.
- Hashimoto, R., Ito, A., and Goto, T. (2015). Effect of Deposition Atmosphere on the Phase Composition and Microstructure of Silicon Carbide Films Prepared by Laser Chemical Vapour Deposition. Ceram Int., 41:6898–6904.
- Hidayat, D., Widiyastuti, W., Ogi, T., and Okuyama, K. (2010). Droplet Generation and Nanoparticle Formation in Low-Pressure Spray Pyrolysis. Aerosol Sci. Technol., 44:692–705.
- Kavecky, T., Janeková, B., Madejová, J., and Ajgal, K. P. (2000). Silicon Carbide Powder Synthesis by Chemical Vapour Deposition from Silane/Acetylene Reaction System. J. Eur. Ceram Soc., 20:1939–1946.
- Kshirsagar, A., Nyaupane, P., Bodas, D., Duttagupta, S. P., and Gangal, S. A. (2011). Deposition and Characterization of Low Temperature Silicon Nitride Films Deposited by Inductively Coupled Plasma CVD. Appl. Surf. Sci., 257:5052–5058.
- Legut, D., Wdowik, U. D., and Kurtyka, P. (2014). Vibrational and Dielectric Properties of α-Si3N4 from Density Functional Theory. Mater. Chem. Phys., 147:42–49.
- Li, Y., Wang, L., Yin, S., and Yang, F. (2012). Rapid Crystallization of Amorphous Silicon Nitride Powder Accelerated by Liquid Si. Ceram Int., 38:5311–5314.
- Liu, S., and Xiao, W. (2014). Numerical Simulations of Particle Growth in a Silicon-CVD Fluidized Bed Reactor Via a CFD–PBM Coupled Model. Chem. Eng. Sci., 111:112–125.
- Loeffler, J., Das, S., and Garrick, S. C. (2011). Large Eddy Simulation of Titanium Dioxide Nanoparticle Formation and Growth in Turbulent Jets. Aerosol Sci. Technol., 45:616–628.
- Lu, F., Cai, Q., Zhou, X., and Xue, H. (1999). The study of shock-activation and sintering of silicon nitride powder materials. J. Mater. Process. Tech., 89–90:399–404.
- Maitland, G. C. (1981). Intermolecular Forces: Their Origin and Determination. Clarendon Press, Oxford.
- Mortimer, R. G. (2008). Physical Chemistry. Academic Press/Elsevier, Amsterdam.
- Park, K. S., Lee, B. W., and Choi, M. (1999). An Analysis of Aerosol Dynamics in the Modified Chemical Vapor Deposition. Aerosol Sci. Technol., 31:258–274.
- Pawelec, A., Strojek, B., Weisbrod, G., and Podsiad, O. S. A. (2002). Preparation of Silicon Nitride Powder from Silica and Ammonia. Ceram Int., 28:495–501.
- Wananuruksawong, R., Shinoda, Y., Akatsu, T., and Wakai, F. (2015). High-Strain-Rate Superplasticity in Nanocrystalline Silicon Nitride Ceramics Under Compression. Scripta Mater., 103:22–25.
- Wang, F., Jin, G., and Guo, X. (2006). Sol–gel Synthesis of Si3N4 Nanowires and Nanotubes. Mater. Lett., 60:330–333.
- Won, H. I., Won, C. W., Nersisyan, H. H., and Yoon, K. S. (2010). Salt-Assisted Combustion Synthesis of Silicon Nitride With High α-Phase Content. J. Alloy. Compd., 496:656–659.
- Wright, D. N., Marstein, E. S., Rognmo, A., and Holt, A. (2008). Plasma-Enhanced Chemical Vapour-Deposited Silicon Nitride Films; The Effect of Annealing on Optical Properties and Etch Rates. Sol. Energy Mater. Sol. Cells, 92:1091–1098.
- Xia, D., Wen, Y., Ren, L., and Hu, X. (2014). Mechanisms of Thermal Process of Zinc Ultrafine Powder Preparation by Inert Gas Condensation. Powder Technol., 257:175–180.
- Yang, J., Han, L., Chen, Y., Liu, G., Lin, Z., and Li, J. (2012). Effects of Pelletization of Reactants and Diluents on the Combustion Synthesis of Si3N4 Powder. J. Alloy. Compd., 511:81–84.
- Yang, J. H., Qiu, J. F., and Li, J. T. (2011). Preparation of Single-Phase Magnesium Silicon Nitride Powder by a Two-Step Process. Ceram Int., 37:673–677.
- Yang, Y., Kuang, J., Wang, H., Song, G., Liu, Y., and Tang, G. (2016). Enhancement in Thermal Property of Phase Change Microcapsules with Modified Silicon Nitride for Solar Energy. Sol. Energy Mater. Sol. Cells, 151:89–95.