With a high feeding rate of the precursor solution, highly porous spongelike lithium–cobalt–oxide films with bimodal pore structure and porosity over 90% were fabricated at 235°C by the electrostatic spray deposition (ESD) technique. The metal acetates were used as the precursors dissolved in a mixed solvent of ethanol and butyl carbitol. Scanning electron microscopy (SEM) and X–ray diffraction were used to analyze the structure of the as–deposited films. The growth rate was found to be 7.8 μm/h and 0.24 mg/(cm2 h). At a relatively long deposition time, this bimodal porous structure may evolve into a porous columnar structure. Other morphologies such as flattened reticular structure and rather dense structure can be obtained at deposition temperatures between 270 and 320°C.
INTRODUCTION
Porous ceramic films can find wide applications in catalysis, separation engineering, chemical reactors, and chemical sensing (CitationYang et al. 1996; CitationUhlhorn et al. 1992; CitationRitchie et al. 2001; CitationLin and Brown 1997). They can be prepared with a variety of fabrication techniques, including sol–gel (CitationBrinker et al. 1994), chemical vapor deposition (Lin and Burggraaf 1993), and spray deposition (CitationStudenikin et al. 1998). As a recently developed spray technique, electrostatic spray deposition (ESD) shows many advantages to prepare functional ceramic thin films of various controllable morphologies (CitationChen et al. 1996b;Su and Choy 2000; Nishizawa et al. 1998; CitationYoon et al. 2001). In particular, a unique film morphology, reticular or spongelike porous structure was successfully obtained by ESD technique for a number of functional ceramic materials including TiO2, CoO, MnO, LiCoO2, LiMn2O4, Li3PO4, and LaCoO3 (CitationChen et al. 1996a, 1997a; CitationTaniguchi and Schoonman 2002). Due to the high surface area and the 3D–crosslinking–pore structure, this morphology may lead to substantially improved properties of the ceramic films, for instance, largely enhanced ion transport rate and decreased interfacial resistance of electrochemical cells (CitationChen et al. 1997b; CitationShui et al. 2004). However, the formation mechanism of this special morphology is not well understood, although Chen et al. (1996a) proposed a possible schematic illustration. For example, that mechanism can only explain the formation of the reticular structure on the dense substrate. We were still puzzled by the formation of the reticular structure on the already formed porous “substrate,” which was in fact the previously deposited film. In this study, with the same precursors and substrate but greater feed rate and longer deposition time to deposit spongelike lithium cobalt oxide films compared with the conditions in the previous work (CitationChen et al. 1996a), we attempted to identify the formation mechanism by monitoring the evolution of the film structure with deposition time. During these investigations, we discovered a new spongelike porous morphology that has provided clues to the formation mechanism. This morphology has two levels of pore structure which results in a bimodal pore size distribution.
EXPERIMENTAL
The details of the ESD setup and its working principle were described in a previous paper (CitationChen et al. 1996b). Lithium acetate dehydrate (Li(CH3COO)2·4H2O) and cobalt acetate tetrahydrate (Co(CH3COO)2·4H2O) of analytical grade were dissolved in a mixture of ethanol (C2H5OH, 15vol%) and butyl carbitol (CH3(CH2)3OCH2OCH2CH2OH, 85vol%) to obtain one 0.005 M precursor solution. Aluminum disks (12 cm in diameter) were used as substrates and weighted before and after the deposition. A distance of 2.5 cm was kept between the nozzle and the substrate. The precursor solution was pumped through the metal capillary nozzle at an average rate of about 2 ml h−1 with a peristaltic pump. A DC voltage of 10.2 kV was applied between the orifice of the capillary nozzle and the substrate. The substrate temperature was controlled between 235 and 320°C. The film deposition took place under ambient.
The surface and cross–sectional morphologies of the deposited films were observed under a scanning electron microscope (SEM; HITACHI X–650), while the crystal structure was characterized using an X–ray diffractional meter (Philips X’Pert PRO SUPER) with Cu Kα radiation.
RESULTS AND DISCUSSION
The flow rate, Q, of the precursor solution is the most important parameter to determine the pore size dp of the deposited reticular films (CitationChen et al. 1996a); dp is proportional to Q in the case of low flow rate, roughly when Q ≤ 0.8 ml/h. However, there exists a minimum flow rate, Q min, of roughly 0.1 ml/h that is needed to obtain the reticular structure (CitationChen et al. 1997a). In addition, we have found that a low Q results in a small deposition area on the substrate. Therefore, we used a relatively high flow rate (about 2 ml/h) in this study. Nevertheless, due to the peristaltic pump used, the solution flow rate underwent periodic fluctuations as evidenced by different amounts of “steam” appeared alternately near the surface of the substrate during the deposition.
shows the SEMs of the cross sections and surfaces of lithium cobalt oxide films obtained after different deposition times. Obviously, the overall morphology of these films is spongelike porous, which is similar to the results observed previously. However, the porous surface structure here can be clearly divided into two levels of substructures. The first level of structure is composed of 3D–interconnected porous “tunnels” that are constructed with small round pores of a pore size around 5 μm. The local structure on the micrometer scale is almost same as the reticular structure found previously (CitationChen et al. 1996a). On the other hand, as the second level of the structure, the interconnection of these porous “tunnels” forms a larger porous structure with irregular pores of a pore size between 20 and 30 μm. Nevertheless, according to the cross–sectional images of the films (Figures ) reveal that this larger porous structure exists mainly on the planes parallel to the substrate but not in the direction of film thickness. As in our previous study (CitationChen et al. 1996a), the pore size of the reticular structure is determined by the flow rate of the precursor solution, this bimodal porous structure is obviously due to the two different flow rates alternately used in this study.
FIgure 1SEM micrographs of lithium–cobalt–oxide films with deposition time (a,b) 1 h, (c,d) 4 h, (e,f) 6 h, and (g,h) 11 h. The images (a, c, e, g) and (b, d, f, h) show the cross sections and surfaces of the films, respectively.
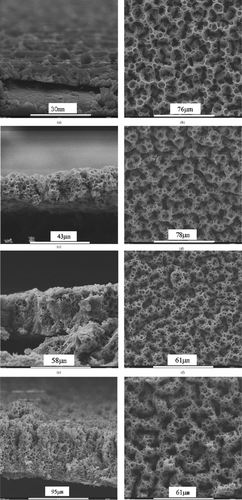
For the deposition of porous films via a spray technique, it is possible that the later–coming droplets might penetrate through the pores of the early–formed layer and fill into the bottom layer of the film so that the porosity in the bottom layer is greatly reduced. However, it can be seen from the micrographs of the spongelike films (), especially in the cross–sectional images, that the spongelike structure is indeed three–dimensional even when the deposition time is prolonged. This means that no or little droplet penetration through the pores takes place. We believe that this phenomenon is related to the preferential landing of the spray droplets. As we described previously (CitationChen et al. 1996b), the charged droplets generated in the ESD technique land preferentially on the surface sites where the opposite charge density is locally higher than their neighbor area. In the case of a conducting porous substrate, the density of opposite charges on the pore walls is obviously higher than in the pore voids under a high electrostatic field. Therefore, the spray droplets are attracted to the pore walls on the surface and discharge there rather than penetrating into the pores. This mechanism can explain the formation of three–dimensional spongelike films by means of ESD technique. Nevertheless, when the substrate or previously deposited layer has a nonuniform pore size distribution, this preferential deposition may lead to a discontinuous top porous layer. This is the case when a porous nickel foam substrate is used (CitationChen et al. 1996a) and the deposition time is relatively long (see below).
The film thickness at different deposition times can be determined directly from the cross–sectional images (). These results, together with the mass of the film as a function of deposition time, are shown in . Both the thickness and the mass of the film are roughly proportional to the deposition time; the growth rate is 7.8 μm/h or 0.24 mg/(cm2 h). Therefore, the film growth is controlled by the mass transport of the precursor solution.
shows the X–ray diffraction pattern of a lithium–cobalt–oxide film deposited at 235°C. In addition to the diffraction peaks from the aluminum substrate, three broad peaks at around 37°, 43°, and 62°, which can be assigned to cobalt oxide (CoO), are observed. Hence the as–deposited films appear to be composed of nanocrystalline CoO, amorphous Li2O, and small amount of organic components. As shown previously (CitationChen et al. 1996a), these films can be transformed to LiCoO2 films with the same morphology by annealing them at higher temperatures. On the other hand, from the measured film growth rates of 7.8 μm/h and 0.24 mg/(cm2 h), the density of the as–deposited films can be calculated to be 0.31 g/cm3. Under the assumption of absence of the organic components, the porosity of the lithium–cobalt–oxide films can be estimated to be about 93.5%.
FIgure 3X–ray diffraction pattern of an as–deposited lithium–cobalt–oxide film on Al substrate. The indexed peaks are from the diffraction of CoO.
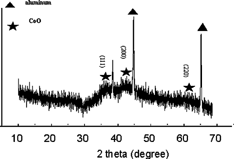
The left part of the cross–sectional image of the 11 h deposited film (g) shows that the film morphology may evolve into a columnar structure. This morphology evolution usually begins after a relatively long deposition time. This evolution may be attributed to the preferential landing of the charged spray droplets on a rough film surface. Depending on the deposition conditions, the appearance of the surface roughness could be the result of a slight change in these conditions. As shown in , a porous columnar structure is obtained on an 8 h deposited sample under the same nominal conditions (i.e., substrate temperature, concentration, and flow rate of the precursor solution, and nozzle–to–substrate distance) as for the films shows in . The early appearance of the columnar structure might result from a slight disturbance of the substrate temperature during the deposition process. With increasing the substrate temperature, the film morphology evolves from the bimodal porous structure at 235°C () to a flattened reticular structure at 270°C (a), a dense structure embedding floccules–like particles at 300°C, (b) and a rather dense particulate structure at 320°C (c). Based on these morphology changes, it can be speculated that when the spray droplets impinge on the substrate surface, they are still wet at 235 and 270°C, nearly dry at 300°C, and completely dry at 320°C. The various film morphologies obtained at different deposition temperatures provide wide opportunities for the application of ESD–derived ceramic films. 1
CONCLUSIONS
By feeding a precursor solution with periodically varied flow rates, highly porous spongelike lithium–cobalt–oxide films with a bimodal pore structure can be prepared by electrostatic spray deposition (ESD) technique at the substrate temperature of 235°C. Both the film thickness and the film mass are roughly proportional to the deposition time. At a relatively long deposition time, a columnar growth mode is followed. Other different film morphologies from flattened reticular to dense structures can be obtained at higher substrate temperatures.
Acknowledgments
This study was supported by National Science Foundation of China (grant No. 50372064) and National Education Council of China (grant No. 20030358057). C. H. Chen is also grateful for the support of 100 Talents Program of Acdemia Sinica.
REFERENCES
- Brinker , C. J. , Sehgal , R. , Hietala , S. L. , Deshpande , R. , Smith , D. M. , Loy , D. and Ashley , C. S. 1994 . J. Membrane Sci , 94 : 85
- Chen , C. H. , Kelder , E. M. and Schoonman , J. 1996a . J. Mater. Sci. , 31 : 5437 [CROSSREF]
- Chen , C. H. , Kelder , E. M. and Schoonman , J. 1997a . J. Electrochem. Soc. , 144 : L289
- Chen , C. H. , Kelder , E. M. and Schoonman , J. 1997b . J. Mater. Sci. Lett. , 16 : 1967 [CROSSREF]
- Chen , C. H. , Kelder , E. M. , van der Put , P. J. J. M. and Schoonman , J. 1996b . J. Mater. Chem. , 6 : 765 [CROSSREF]
- Lin , Y. S. and Burggraaf , A. J. 1993 . J. Membrane Sci. , 79 : 65 [CROSSREF]
- Lin , J. and Brown , C. W. 1997 . Trac-Trend Anal. Chem. , 16 : 200 [CROSSREF]
- Nishizawa , M. , Uchiyama , T. , Dokko , K. , Yamada , K. , Matsue , T. and Uchida , I. 1998 . Bull. Chem. Soc. Jpn. , 71 : 2011
- Ritchie , J. T. , Richardson and Luss , D. 2001 . AICHE J , 47 : 2092 [CROSSREF]
- Shui , J. L. , Jiang , G. S. , Xie , S. and Chen , C. H. 2004 . Electrochim. Acta , 49 : 2209 [CROSSREF] [CSA]
- Studenikin , S. A. , Golego , N. and Cocivera , M. 1998 . J. Appl. Phys. , 84 : 2287 [CROSSREF]
- Su , B. and Choy , K. L. 2000 . Thin Solid Films , 361 : 102 [CROSSREF] [CSA]
- Taniguchi , I. and Schoonman , J. 2002 . J. Mater. Synth. Proces. , 10 : 267 [CROSSREF] [CSA]
- Uhlhorn , R. J. R. , Keizer , K. and Burggraaf , A. J. 1992 . J. Membrane Sci. , 66 : 271 [CROSSREF]
- Yang , H. , Kuperman , A. , Coombs , N. , Mamiche-Afara , S. and Ozin , G. A. 1996 . Nature , 379 : 703 [CROSSREF]
- Yoon , W. S. , Ban , S. H. , Lee , K. K. , Kim , K. B. , Kim , M. G. and Lee , J. M. 2001 . J. Power Sources , 97-98 : 282 [CROSSREF] [CSA]