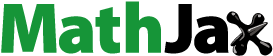
ABSTRACT
The low pH and high salinity of acid mine drainage (AMD) fundamentally complicates the sorption processes. We explored the selective removal of Cu, Ni and Co ions present in AMD from the excess of ferrous ions of using a chelating resins Lewatit® MonoPlus TP 220 and Lewatit® TP 208. Also, the recovery of metal copper from desorption solution using electrolysis was investigated. The results showed that the most effective sorption of metal ions was achieved with chelating sorbent Lewatit® TP 220. The dynamic capacity of the sorbent under the given conditions (pH= 2.5 ± 0.03, presence of Fe(II/III), Zn(II), Mn(II)) decreased in the following order: Cu(II) (43.3 ± 1.4 g/L) > Ni(II) (22.1 ± 2.1 g/L) > Co(II) (3.6 ± 0.4 g/L). Chelating resin Lewatit® TP 208 under the same conditions showed lower efficiency: Cu(II) (30.6 ± 1.3 g/L) > Ni(II) (9.1 ± 0.17 g/L) > Co(II) (1.3 ± 0.08 g/L). The weak base anion exchanger Purolite® A 832 was successfully used to take up Cu(II) from ammonia solution and easily regenerated with sulfuric acid. The sorption capacity for Cu(II) was calculated to be 19.2 ± 0.5 g/L. Electrolysis experiments were performed with a fluidized bed electrolysis reactor where metallic copper was regenerated from desorption solutions and purified sulfuric acid solutions were obtained.
GRAPHICAL ABSTRACT
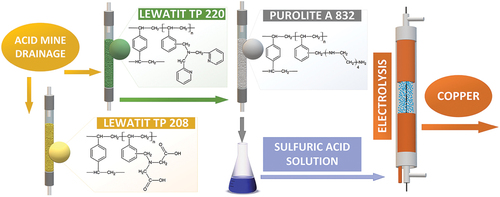
Introduction
Protecting water quality is one of the most important environmental challenges. Acid mine waters or acid mine drainage (AMD) pose a serious threat to natural ecosystems. Microbial oxidation of pyrite and other sulfide ores by chemolithotrophic acidophilic bacteria oxidizing iron (Leptospirillum ferrooxidans, Acidithiobacillus ferrooxidans) and sulfur oxidizing bacteria in the presence of water and air produces an extremely acidic solution (pH <2.5).[Citation1] The pyrite oxidation is represented by the reactions (1) – (4).[Citation2,Citation3]
The acidic pH of water has a toxic effect on biotic ecosystems and at the same time promotes the solubility of the metals such as Cu, Ni, Co.[Citation4] Even at low concentrations, these metals cause health hazards for aquatic organisms.[Citation5–8] Also, AMD contains a large amount of dissolved iron, which harms the fish population.[Citation9] The presence of these metals causes not only acute toxicity but also long-term accumulation and persistence.[Citation10–13]
Ion exchange (IX) is often used to remove toxic metals from waste waters or dilute streams. Recently, it has been increasingly used in hydrometallurgy.[Citation14] It is a selective, economically acceptable and very effective method of treatment. IX between the sorbent and the electrolyte solution occurs upon contact of the ion exchanger with the electrolyte solution. The reaction proceeds until an equilibrium is established between the ion concentration in the ion exchanger and in the solution.[Citation15–17] IX with chelating sorbents has been successfully demonstrated for Ni, Cu, and Zn removal from dilute streams.[Citation17–20] The chelating sorbents adsorb metal ions by a combination of ionic and coordination interaction instead of a simple electrostatic interaction in a conventional cationic or anionic exchange. The function of the chelating sorbent is based on the higher stability of the complex formed between the active groups of the sorbent and the metal compared to the stability of the original anionic metal complex in solution.[Citation21–23] One of the significant advantages of using chelating sorbents is the possibility of selective separation of metal ions and their subsequent desorption with a regenerating agent. Another advantage is the ability of effective sorption at low pH values, especially with resins having bis-picolylamine functional groups attached to a polystyrene divinylbenzene matrix.[Citation19,Citation24,Citation25] These properties are very beneficial for wastewater treatment, as it allows for reduced chemical consumption through the recycling of desorption solutions and opens up potential revenue streams through the recovery of metals from AMD. Recovery of metals from waste solutions is an important aspect of developing circular economy and will be necessary in the future with dwindling resources.[Citation26] The chelating sorbents adsorb metal ions by a combination of ionic and coordination interaction instead of a simple electrostatic interaction in a conventional cationic or anionic exchange. The function of the chelating sorbent is based on the higher stability of the complex formed between the active groups of the sorbent and the metal compared to the stability of the original anionic metal complex in solution.[Citation21–23]
Edebali and Pehlivan[Citation27] researched chelating resins with bis-picolylamine functional group – XUS 43,578 and iminodiacetic functional group in hydrogen form – CR11 for Cu(II) removal from synthetic effluents. The batch equilibrium experiments showed that the resins had a stronger affinity for Cu(II) ions. The optimum pH level for the Cu(II) removal from aqueous solution was 3 for both resin types. The monolayer saturation sorption capacity for Cu(II) was calculated at 30.7 mg/g for chelating resins with bis-picolylamine functional group and 46 mg/g for resin with iminodiacetic functional group.
Wołowicz and Hubicki[Citation28] studied the removal of the metals from acid solutions with Lewatit® MonoPlus TP 220. Using a batch method, it was found that chelating resin with bis-picolylamine functional group successfully removed tested metals. The series, from highest to lowest affinity, follows: Pd(II) > Au(III) > Pt(IV) > Cu(II) > Zn(II) > Co(II) > Ni(II).
The following studies about Cu(II), Ni(II) and Co(II) sorption on iminodiacetate chelating resins by Dinu and Dragan[Citation17] showed the calculated metal sorption capacities of the commercial resin Amberlite IRC-748, at pH 5, from highest to lowest was: Cu(II) > Ni(II) > Co(II).
Yuan-lai Xu et al.[Citation29] researched using tetraethylenepentamine modified bagasse for the Cu(II) recovery from metallurgical wastewater (pH = 4.5). Two tandem column experiments showed that amount of Cu(II) adsorbed on tetraethylenepentamine modified bagasse was 10.8 mg/g.
Mendes and Martins[Citation30] evaluated the use of chelating resin with bis-picolylamine functional group – Dowex M4195R for the selective removal of Ni(II) and Co(II) from acidic solutions. Even at pH 1, the bis-picolylamine resin had the best performance for nickel and cobalt sorption over the IDA (iminodiacetic acid) functional group sorbents (Amberlite IRC748R, Ionac SR-5 R and Purolite S930R).
Reig et al.[Citation24] investigated chelating resin with bis-picolylamine functional group Purolite S960 for the removal of Cu(II) and Zn(II) from hydrometallurgy effluents containing As(V) (batch and column experiments). It was found that the maximum retention of Cu(II) was reached at pH ≥1.0 (97 ± 1%), whereas the maximum Zn(II) retention of 60 ± 2% was obtained at pH values of 2.5–5.0. The sorption capacities for Cu(II) and Zn(II) recovery were 4.2 ± 0.5 mg/g resin and 0.4 ± 0.1 mg/g resin, respectively.
Vecino et al.[Citation31] studied two types of resins (Lewatit VP OC 1026, containing Bis-2-ethylhexylphosphoric acid (DEHPA) and Lewatit TP 207 – the cation ion exchange resin containing an iminodiacetic acid (IDA) group) for the sequential extraction of Cu(II) and Zn(II) from AMD (batch and column experiments). The best extraction of Zn(II) was obtained using resin with DEHPA – VP1026, being higher than 96% (pH = 2.6–2.8), whereas resin containing an iminodiacetic acid group – TP 207 was optimal for Cu(II) extraction (>99%) at pH = 3–4. In dynamic experiments, it was possible to separate and concentrate Zn(II) and Cu(II) using both resins.
The results of Diniz et al.[Citation32] indicate the ability of the chelating resins to extract from acidic solutions trace metals such as nickel(II), copper(II), cobalt(II) and lead(II) in the presence of high concentrations of iron, manganese, and chloride ions. The results also show that chelating ion exchange resins containing only nitrogen atoms under acidic conditions show high affinity for copper ions.[Citation28,Citation33]
The possibility of achieving separation of metals from mine waters at lower pH values using ion exchange resins provides single ion-rich streams that could be processed using electrowinning technologies.[Citation24,Citation31,Citation34–36]
The purpose of this work was to find the optimal conditions for the selective sorption and desorption of toxic metals, namely copper, from model acid mine drainage solutions with a high content of iron. We hypothesized that some metals such as copper, nickel, cobalt and zinc can be selectively recovered from very acidic solutions with a high iron content without adjustment of the pH and pretreatment, leaving majority of dissolved iron species in solution. Subsequent recovery of metallic copper and other valuable metals from the regenerant solutions would be possible by electrolysis. If iron needs to be removed by aeration and alkalization, resulting sludge will contain only trace amount of these toxic metals.
Materials and methods
Dynamic column studies
To compare individual sorbents, dynamic column experiments were performed. The selectivity of sorption of transition metals (Cu, Ni, Co and Zn) was monitored and compared. The sorption efficiency, desorption efficiency, sorption kinetics and sorbent capacity were determined. All sorption experiments were repeated at least three times. The results were calculated as average values and the standard deviations were estimated. Other experiments were repeated a maximum of two times. Single values or an average of two measurements were used as results. Therefore, standard deviations were not determined.
Solutions and resins
Model solutions simulating the conditions of real acid mine drainage waters were prepared. A stock AMD solution was made for all experiments with iron, zinc and manganese concentrations, 1000 ± 17.6 mgFe/L, 160.4 ± 6.3 mgZn/L and 44.6 ± 2.1 mgMn/L, respectively. The stock model AMD solution had a pH of 2.5 ± 0.03. This model solution composition corresponds with real mine waters present in metal mining areas.[Citation37] To simulate AMD from different mining environments, either copper, nickel or cobalt were added to the stock solution to provide concentrations of 50 ± 1.5 mgCu/L (solution 1), 51.5 ± 4.7 mgNi/L (solution 2), and 47.5 ± 5.9 mgCo/L (solution 3), respectively (detailed composition is described in ). The sulfate salts of the respective metals were used to prepare the solutions (CuSO4·5 H2O, NiSO4·6 H2O, CoSO4·7 H2O, FeSO4·7 H2O, ZnSO4·7 H2O, MnSO4·H2O). The pH was adjusted to 2.5 ± 0.03 with sulfuric acid. The initial concentration of copper was chosen based on the real mine water composition from the site Priest’s creek, Storwartz, Roros,[Citation38] below the sedimentation pond during 1995, as well as the concentrations of iron, zinc and manganese. The concentration of nickel and cobalt was chosen to better compare the sorption efficiency on individual sorbents. In real mine waters, nickel and cobalt concentrations are lower and its value depends on the region.[Citation39–44] Samples from the German (Ronneburg): Co − 12 mg/L, Ni 55 mg/L, Al − 234.5 mg/L, Zn − 12.5 mg/L, Fe − 21.1 mg/L, Mn − 500 mg/L, pH − 4.4.[Citation42] provides a summary of the experimental solution composition.
Table 1. Summary of the experimental solution composition.
A ferric salt (FeSO4·7 H2O) was used in the preparation of the model AMD solutions, as it is assumed that the AMD would be taken directly from the mine would contain mainly the ferrous form of iron. It was also assumed that during the experiments, Fe(II) would gradually oxidize into Fe(III).
The presence of Fe(III) in the model solutions was determined by thiocyanate colorimetry (at 500 nm in 50 mm cell) and compared with redox potential (Pt vs. Ag/AgCl 1 M KCl). Total iron concentration was measured by atomic absorption spectroscopy (AAS). provides data on the content of iron of different valences in the process of water oxidation. The fresh prepared AMD model solution and the same solution after 6 months standing in the laboratory were measured. The results show that in 6 months the Fe(III) content in the solution increased from 6.9% to 86.4%.
Table 2. Iron speciation data in model AMD solutions.
The chelating resin with a di-(2-picolyl)amine functional group Lewatit® MonoPlus TP 220 and the chelating resin with iminodiacetic functional group (IDA) Lewatit® TP 208 were studied during the dynamic column experiments to determine sorption and desorption efficiency of Cu(II), Ni(II) and Co(II) ions. The weak base anion exchanger Purolite® A 832 with tetraethylenepentamine (TEPA) functional group was studied for sorption of copper ions from spent ammonia regenerant solution. Properties of these sorbents are listed in .
Table 3. Properties of the studied resins[Citation45–47].
Lewatit® Monoplus TP 220 binds metals by coordination bonds with the nitrogen atom of pyridine. The sorbent is particularly suitable for the sorption of cobalt, nickel, copper and the separation of nickel from chromium(III) or ferric solution. Lewatit® Monoplus TP 220 has been shown to be able to selectively capture transition metal ions from extremely acidic solutions (pH <2).[Citation45]
Lewatit® TP 208 is an IDA-functional macroporous chelating cation that binds metals by electrostatic interaction and forms three coordination bonds between the metal and the free electron pairs of nitrogen and oxygen carboxyl groups. Therefore, it can be used even where metals in solution are bound by weak complexing agents. Lewatit® TP 208 removes the metal cations from aqueous solutions in the following order: Cu(II) > Pb(II) > Ni(II) > Zn(II) > Cd(II) > Fe(II).[Citation46]
Purolite® A 832 is ion exchange resin having tetraethylenepentamine (TEPA) functional group on macroporous polyacrylate matrix,[Citation23,Citation48] which is able to bond the copper from a copper-ammonia complex solution. Copper cations are taken up through coordination bonds to multiple N-atoms of the resin’s functional group in the free base form.[Citation22,Citation23]
Sorption and desorption experiments
Glass columns of inner diameter 10 mm and 25 cm tall were packed with 15 mL of purified and protonated sorbents for each experiment. The model AMD solution was pumped through the column by peristaltic pump at a specific flowrate 6 BV/h (1.5 mL/min). Effluent fractions were collected from the bottom of the column by automatic fraction collector Watrex DeltaChrom FC 500. The concentrations of metal ions were analyzed by atomic absorption spectrometer SpectrAA 220, VARIAN.
1 M H2SO4 and 2 M NH3 solutions were used to regenerate the chelating resins Lewatit® TP 220 and 1 M H2SO4 was used to regenerate Lewatit® TP 208. Regeneration was carried out in a co-current manner. Specific flowrate for all desorption experiments was 3 BV/h (0.75 mL/min). The dynamic column sorption/desorption processes are shown in .
The dynamic capacity cb was calculated by EquationEq. (5)(5)
(5) , where
is the inlet weight concentration (mg/L), where
is the outlet weight concentration (mg/L) V in fraction x, Vx volume of solution in fraction x (L) and V0 the volume of sorbent (L), n number of fractions till breakthrough.
Electrolysis studies
The resulting ammonia solution from Lewatit® MonoPlus TP 220 regeneration is not suitable for performing electrolysis due to NOx formation on the anode. For this reason, weak base anion exchanger Purolite® A 832 was used to take up copper from ammonia solution. The concentration of the ammonia solution after this step was measured by acid – base titration. Desorption of copper from the resin was achieved with H2SO4, allowing reuse of the ion exchange resin. The resulting copper sulfate solution can be electrolyzed to recover metallic copper.
The same glass column of inner diameter 10 mm was used. It was packed with 15 mL of exchange resin Purolite® A 832 with TEPA functional group. The resulting spent regenerant ammonia solution from Lewatit® MonoPlus TP 220 regeneration, containing 2.5 g/L of copper ions, was pumped through the column at a specific flowrate 3 BV/h (0.75 mL/min). Effluent fractions were collected by automatic fraction collector and were analyzed by atomic absorption spectrometer SpectrAA 220, VARIAN.
1 M H2SO4 solution was used to desorb copper ions from the exchange resin Purolite® A 832. The specific flowrate was set at 3 BV/h (0.75 mL/min).
Further experiments focused on the electrochemical recovery of copper from the used regeneration solutions. For the efficient recovery of copper, a tubular electrolyzer with a fluidized bed of inert particles was designed and constructed ()
A visual diagram of the design of the electrolysis reactor is shown in , where the left image shows the external structure of the reactor and the right image shows the internal structure of the reactor. The reactor column was made of poly(methyl methacrylate). It was 25 cm tall and had an inner diameter of 3 cm. The cathode function was performed by a sheet of copper with surface area of 230 cm2, which was located inside the column. A platinum wire served as the anode and was passed through the center of the reactor. A suspended layer was provided by inert spherical glass beads. The reactor was filled with 150 g of inert spherical glass beads (1/3 of the volume of the electrolyzer tube). The diameter of each glass bead was 0.5 mm. the inlet and outlet of the reactor column were equipped with a low pressure drop mesh. This detail prevented the beads from escaping from the reactor. The fluidized inert spheres enhanced mass transfer significantly to improve electrolysis performance.[Citation49] The fluidized bed of inert particles also continually compacted and polished the deposited copper onto the surface of the cathode. It allows to treat ten times lower metal concentration than traditional electro-winning cells.[Citation50] This concept with planar electrodes was successfully used previously where nitrate ions were reduced on electrode.[Citation51] Simple planar electrode configuration with open space will require longer operation time at low process intensity.
The copper electrolysis experiment was performed by adding 500 mL of regeneration solution after desorption of copper ions from Purolite® A 832 to the Erlenmeyer flask. The concentration of copper ions in this solution was 2.5 g/L. The acidic copper sulfate solution was pumped through the electrolysis reactor by peristaltic pump at a volumetric flowrate 25 mL/s, which provided the suspended layer in the cathode space. The power pack was set to a current value of 1 A. 0.5 mL samples of the electrolyte solution were taken every 30 minutes. The concentrations of Cu(II) were analyzed by atomic absorption spectrometer SpectrAA 220, VARIAN.
To optimize the electrolysis process, a series of experiments using different operating currents (0.5 A, 0.8 A, 1 A, 1.2 A, 1.5 A, 1.8 A, 2 A) were carried out. The goal of these tests was to establish the optimal current for obtaining a suitably purified solution, which could be reused for the desorption of copper from Purolite® A 832 resin. The maximum acceptable concentration of Cu(II) in the purified solution that will not impact the efficiency of the Purolite® A 832 was investigated (see Section 2.5).
A detailed diagram of the whole process from sorption of copper ions from AMD solution on Lewatit® MonoPlus TP 220 to electrolysis is shown in .
Figure 3. Diagram of copper removal and recovery process, where I - Sorption of Cu(II); II - Regeneration of Lewatit TP 220; a − 1 M H2SO4 regenerant solution; b − 2M NH3 regenerant solution; c – Cu(II) sorption on Purolite a 832; d − 2M NH3 recycling; III – Regeneration of Purolite A 832; e − 1M H2SO4 regenerant solution; IV – Electrolysis; f – regenerant solution after Cu(II) desorption; g − 1M H2SO4 recycling after electrolysis. Points I, II, III and IV were performed separately.
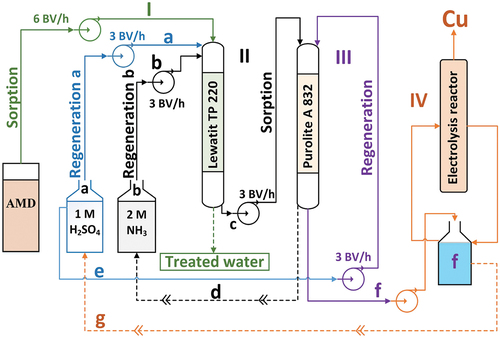
Batch sorption equilibrium tests with Purolite® A 832
The experiments were performed in four 200 mL flasks with 100 mL of solution of 1 M sulfuric acid with copper concentrations of 0.1, 0.3, 0.5 and 1 g/L, respectively. 2 mL of Purolite® A 832 resin was added to each flask. Samples were placed on a Unimax 1010 shaker. The mixing process of Unimax 1010 is based on horizontal, circular and vibrating motion with constant amplitude and with a continuously adjustable frequency, which was set at 315 revolutions per minute. The experiment lasted 24 hours at 25°С. The copper concentrations of each sample were analyzed by atomic absorption spectrometer.
The aim of the experiment was to model the amount of copper ions taken up during the regeneration of ion exchanger with the spent regenerant solution of 1 M H2SO4 that was treated with electrolysis and thus estimate the optimal concentration of copper at which the electrolysis can be terminated.
Column desorption tests with Purolite® A 832
To confirm the results of the batch sorption equilibrium tests (2.3) extra column desorption experiments were carried out using post electrolysis recycled sulfuric acid containing 0.5 g/L of Cu(II). The equipment, the amount of sorbent and the experimental conditions were the same as in the desorption experiment described in section 2.1.2.
Results and discussion
Sorption properties of Lewatit® MonoPlus TP 220 and Lewatit® TP 208 and their comparison
Lewatit® MonoPlus TP 220 resin exhibited the better sorption performance than Lewatit® MonoPlus TP 208. It is thought that the Lewatit® MonoPlus TP 220 performance was better due to the chelating sorbent containing di-(2-picolyl)amine functional groups. The breakthrough curves in represent the selectivity of Lewatit® MonoPlus TP 220 to Cu(II), Co(II), Ni(II). The sorption efficiency decreased in the following order: Cu(II) > Ni(II) > Co(II) (). The resin showed a very high affinity for sorption of copper ions. During the first 600 BV (9 L), the copper concentration at the column outlet was less than 0.8 mg/L. The sorption of nickel and cobalt ions was less efficient. The breakthrough of Ni(II) appeared at 100 BV, and of Co(II) already at 10 BV. The total dynamic capacity for Cu(II) was 43.31 ± 1.38 g/L, for Ni(II) − 22.09 ± 2.07 g/L, for Co(II) − 3.60 ± 0.35 g/L. This order is consistent with the findings of Diniz et al.[Citation19] where the similar macroporous polymer Dowex M-4195, with the chelating bispicolylamine functional group was investigated at the same pH.
Figure 4. Sorption of Cu(II), Co(II), Ni(II) on Lewatit® MonoPlus TP 220, where –●– Co(II), –□– Ni(II), –▲– Cu(II).
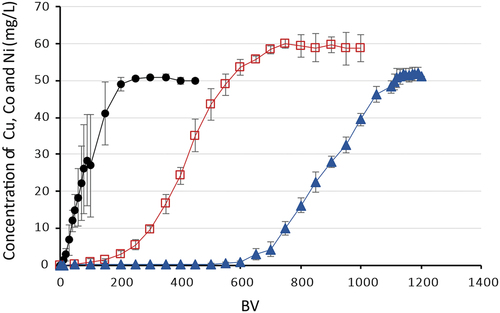
High sorption capacity for Cu(II) in the presence of sulfate ions have been also described by Kołodyńska et al.[Citation52] where sorption capacities of Lewatit ® MonoPlus TP 220 were studied at pH in the range of 2.0–2.6. The highest obtained sorption capacity for copper ions − 94.2 mg/g was slightly lower than the capacity described in this paper − 128.6 mg/g (43.31 g/L). The difference in the measured values can be explained by the different conditions of the experiments (solution without companion ions and batch equilibrium experiment).
Fe(II/III) and Mn(II) sorption was not observed in any of the experiments performed. During experiments with model mine waters containing copper and nickel, zinc was also not taken up. But as can be seen in experiments with cobalt AMD waters showed partial sorption of zinc ions, the total dynamic capacity for Zn(II) was calculated at 1.82 ± 0.09 g/L (). The ineffective sorption of Mn(II) compared to other metals during all sorption experiments can be connected with the fact that the Mn(II) ion is too large to interact with all three-donor nitrogens in the bis(2-pyridylmethyl) amine. The tridentate Mn(II)-bis(2-pyridylmethyl)amine complex has a low stability.[Citation19,Citation32,Citation53]
Figure 5. Sorption of Zn(II) on Lewatit® MonoPolus TP 220, where –●– AMD with Co(II), –□– AMD with Ni(II), –▲– AMD with Cu(II).
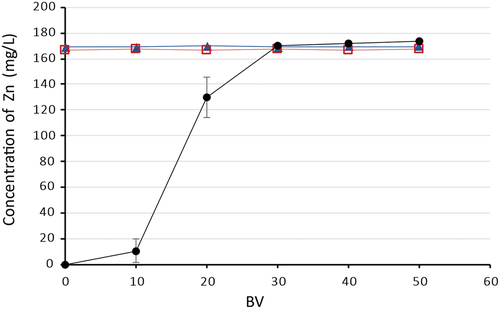
In the case of equilibrium sorption Fe(II/III), sorption of Fe(II) is negligible,[Citation54,Citation55] while affinity of Fe(III) towards the bis(2-pyridylmethyl) amine is higher than that of Mn(II) but lower than that of Cu(II), Ni(II) and Co(II).[Citation19,Citation53] Therefore, in the case of column sorption, other metals present such as copper, nickel or cobalt easily displace both Fe(II) and Fe(III).
In experiments with the resin with IDA functional groups – Lewatit® TP 208, it was found that the sorbent has a similar selectivity to the monitored metals as Lewatit TP 220 but shows a significantly lower dynamic capacity. The sorption efficiency decreased in the same order: Cu(II) > Ni(II) > Co(II). The total dynamic capacity for Cu(II) was calculated at 30.56 ± 1.30 g/L, for Ni(II) − 9.07 ± 0.17 g/L and for Co(II) − 1.30 ± 0.08 g/L ().
Figure 6. Sorption of Cu(II), Co(II), Ni(II) on Lewatit® TP 208 from model AMD solutions, where –●– Co(II), –□– Ni(II), –▲– Cu(II).
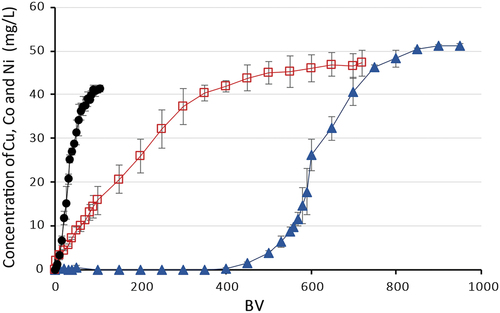
Sorption of zinc ions was also observed during all experiments. The total dynamic capacity depended on the composition of the AMD solution. Thus, in the case of AMD containing copper ions, the capacity for Zn(II) was calculated at 0.62 g/L, in experiments with AMD containing nickel ions − 2.40 g/L and with AMD containing cobalt ions − 6.11 g/L (). A decrease of Fe(II/III) concentration was also observed in the first 3–10 BV during sorption stages, which indicates the sorption of iron as well. The breakthrough curve of Fe does not provide accurate calculations of the total dynamic capacity, which is due to the high concentration of iron in the initial solution and the rapid saturation of the sorbent. Calculations were performed only after desorption of Fe(II/III) from the Lewatit® TP 208.
Figure 7. Sorption of Zn(II) on Lewatit® TP 208 from model AMD solutions, where –▲– AMD with Cu(II), –□– AMD with Ni(II), –●– AMD with Co(II).
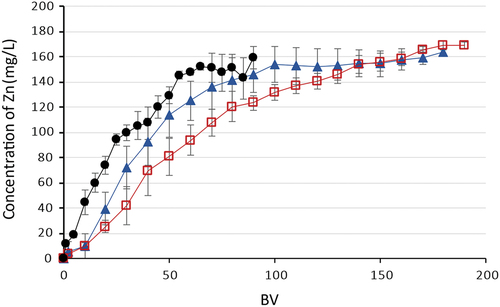
The capacity of the sorbent for accompanying ions is very different and depends on the composition of the input solution and the selectivity of resins to each ion. The differences in the capacities depending on the composition of the initial solution was studied by Jiang et al.[Citation18]
The sorption capacities obtained in this work reinforce previous studies by Park et al.,[Citation56] where Cu(II) sorption was studied by similar resin Lewatit® TP 207 (macroporous cation exchange resin with chelating iminodiacetate groups). The sorption capacity for Cu(II) with input solution containing 15.2 g Ni/L, 2 g Co/L, 512 mg Cu/L and 212 mg Fe/L at pH 2 was 68.7 mg/g. The sorption capacity is almost identical to the capacity obtained in this work − 65.02 ± 2.78 mg/g (30.56 ± 1.30 g/L).
Both chelating sorbents (Lewatit® MonoPlus TP 220 and Lewatit® TP 208) are suitable for sorption of selected metals from an acidic medium and both chelating resins show the highest affinity for Cu(II) ions. This is also supported by other studies.[Citation17,Citation19,Citation27,Citation28,Citation32]
The breakthrough curves of both resins were also monitored by changes of pH values (). In the case of monitoring the pH value of Lewatit® Monoplus TP 220 (), no influence of the pH values on the efficiency of ion removal was detected in the observed pH range. In some cases, a lower pH value was recorded in the first 3 BV. That can be explained by converting the resin into a protonated form before the sorption experiments using sulfuric acid solution. Further, during the sorption experiments, the pH value did not change. This phenomenon can be explained by the mechanism of ion binding by bispicolylamine. Bis(2-pyridylmethyl)amine is an uncharged tridentate ligand having the ability to form bidentate complexes with most divalent metals by coordination bonds.[Citation53,Citation57] Thus, in the first place, the formation of complexes occurs, and not ion-exchange processes, as with IDA resin such as Lewatit® TP 208. IDA is bonding divalent metals with a nitrogen and two oxygen atoms-three dentate ligands and by cation exchange process what affects the pH of the solution.[Citation27,Citation33] describes the metal retentions by Lewatit® TP 208 column dependence on pH values of effluent. The maximum retention of Cu(II) () was achieved at the beginning of the cycle, where the effluent pH was in the range of 1.9–2.2 and Cu(II) retention 99.9%. After that, Cu(II) concentration in the effluent began to gradually increase and a sharp retention decrease occurred after pH = 2.3 until the minimum was reached at pH 2.5, i.e. the pH of inlet solution. Zn(II) maximum retention (> 76.5%) was obtained at pH ˂2.0 and the minimum was observed at 2.2. The maximum retention of Fe(II/III) (75.4%) was achieved only in the first 2 column volumes when pH did not exceed 1.9. A similar course for retention of zinc and iron ions was noted for all experiments (). In all cases, the concentration of iron ions increased after 1.9 pH value was reached, as well as zinc, the retention started to decrease after pH value higher than 2. The maximum retention of Ni(II) took place at pH ˂ 2 (Re > 90%) and there is a rapid increase in concentration after pH = 2.2 (). Сo(II) shows a similar retention curve (Re > 80% at pH ˂ 2) (), but the process was twice faster, and it is also similar to retention of zinc in this AMD solution.
Figure 8. Retention (%) of each metal ion on (a) TP 220 and (b–d) TP 208 ion-exchange resins depends on pH value of effluent, where (a) –▲– Cu(II), –□– Ni(II), –●– Co(II), –x– Zn(II); (b) –▲– Cu(II), –x– Zn(II), –●– Fe(II); (c) –□– Ni(II), –x– Zn(II), –●– Fe(II); (d) –∆– Co(II), –x– Zn(II), –●– Fe(II).
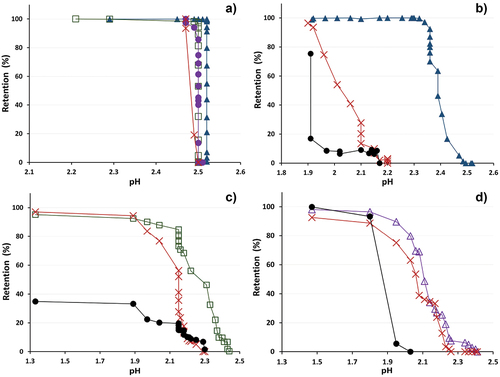
Course of desorption of Lewatit® MonoPlus TP 220 and Lewatit® TP 208
In attempts to regenerate the chelating sorbent Lewatit® MonoPlus TP 220, it was found that the use of a one molar sulfuric acid solution was insufficient to displace all entrapped copper ions. Desorption was performed with 1 M H2SO4 in the first step (10 column volumes − 150 mL), during which 25% efficiency was achieved and 2 M NH3 in the second step (10 column volumes − 150 mL), where virtually all trapped copper ions were displaced (98%) (). The results show () that the regeneration of Lewatit® MonoPlus TP 220 loaded with Cu(II) ions is very effective with 2 M ammonia solution, much more effective than using acid solutions. The maximum Cu(II) concentration achieved during the desorption step with 2 M NH3 was 20.1 g/l. To optimize the elution solutions, the volume can be reduced to 6–7 BV (90–105 ml) for ammonia solution and to 4 BV (60 ml) for sulfuric acid solution.
Figure 9. Desorption efficiency of Cu (II) for Lewatit® MonoPlus TP 220, desorption using BV 1M H2SO4 and 10 BV 2M NH3, where –▲– 1 M ammonia solution; –●– 1 M sulfuric acid solution.
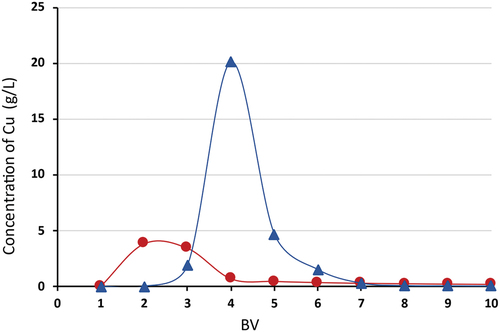
The first desorption step with 10 BV 1 M H2SO4 cannot be omitted due to the fact that during the experiments, small quantity of iron in the form of hydrated ferric oxide flakes formed a layer on the surface of the column. The hydrated ferric oxide flakes completely dissolved a given volume of sulfuric acid solution.
In contrast to copper ions, the desorption of nickel and cobalt ions from Lewatit® MonoPlus TP 220 was successfully achieved with 10 column volumes (150 mL) of 1 M H2SO4. The efficiency of desorption was equal to 95.5% for nickel and 90.6% for cobalt ions (). Also, during cobalt desorption, 98% of adsorbed zinc ions were displaced. 1 M sulfuric acid solution effectively eluate Ni(II), Co(II) and Zn(II) from TP 220 but shows very low efficiency for Cu(II). Mendes et al.[Citation30] suggest using 1 M NH4OH as the elution solution for Cu(II), with which it was achieved more than 80% efficiency. Compared to 1 M NH4OH for elution copper ions from bis-picolylamine resins 2 M NH3 showed a slightly higher result (> 98%).
Figure 10. Desorption efficiency of Ni(II), Co(II) and Zn(II) for Lewatit® MonoPlus TP 220, desorption using 1 M H2SO4, where –●– Ni(II), –⁎– Co(II), –▲– Zn(II).
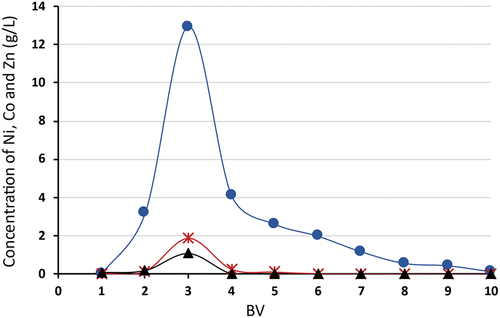
shows the desorption efficiency curves for Lewatit® TP 208 resin. It was found that 1 M sulfuric acid solution is effective for copper, nickel, cobalt and iron ion elution. The maximum Cu(II), Ni(II) and Co(II) () concentration achieved during the elution step was 18.9, 3.5 and 0.9 g/L, respectively. Using 10 BV (150 mL) of 1 M H2SO4 83–99% of trapped metals (Cu(II) − 97%, Ni(II) − 83%, Co(II) − 99%) was displaced. In the solution containing copper, the highest concentration of zinc in the elution step was only 6 mg/L and in the solution containing nickel it was measured at 26 mg/L, the desorption efficiency was 7 and 25% resp. This may be due to the fact that elution of zinc started at the sorption stage, when at first, all metals in the solution were sorbed by the resin, and then the metals with a higher selectivity such as copper and nickel displaced Zn(II). In the case of the solution with cobalt ions, the efficiency was high and amounted to 98%. The elution results obtained for TP 208 show a very high sorption capacity for iron (). The total dynamic capacity depends on the composition of the input solution. For copper containing AMD, the dynamic capacity for Fe(II/III) was 27.21 g/L (), for AMD with nickel () it was calculated to be 22.43 g/L, and for AMD with cobalt () the dynamic capacity was 18.68 g/L. It was found that the sorption process of iron ions on IDA resin is more effective than the sorption of other studied metals, except for copper. The resin presented a high selectivity for copper ions and iron is the second most sorbed metal. The final affinity series determined for the TP 208 can be presented in the order: Cu(II) > Fe(II/III) > Ni(II) > Zn(II) ≥ Co(II). The results presented in the other studies, which were conducted with divalent metal ions, differ only in the arrangement of the iron: Cu(II) > Ni(II) > Zn(II) > Co(II) > Fe(II).[Citation57,Citation58] The sorption of trivalent metal ions on IDA resins was not studied so extensively. The selectivity of IDA resin to trivalent metal ions in aqueous solutions was investigated by Yuchi et al.[Citation58] The affinity was presented in the order: Ga(III) > Fe(III)> In(III) > Sc(III)> Al(III) > Y(III)> La(III). From the results obtained in this work and comparison with other studies, it can be concluded that the IDA resin TP 208 has a much higher affinity for trivalent iron than for divalent iron ions. On the other hand, such a high affinity for Fe(II/III) may be due to its high concentration (1 g/L) compared to other metals in the model AMD solutions.
Figure 11. Regeneration of Lewatit® TP 208 using 1 M H2SO4, where (a) –○– Cu(II) and –∆– Fe(II/III) desorption (AMD with copper ions); (b) –□– Ni(II), –∆– Fe(II/III), and –x – Zn(II) desorption (AMD with nickel ions); (c) –●– Co(II), –∆– Fe(II/III), and –x – Zn(II) desorption (AMD with cobalt ions); (d) comparison of the effectiveness of –○– Cu(II), –□– Ni(II) and –●– Co(II) desorption.
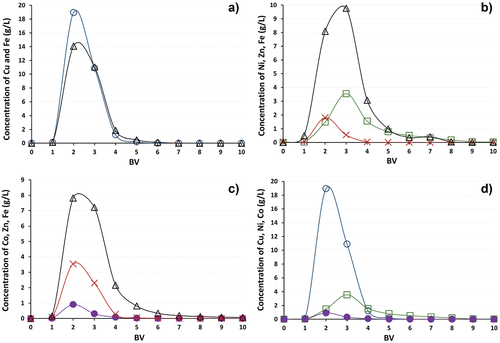
Both resins presented high capacity for copper ions, but Lewatit TP 208 does not provide the ability to selectively separate copper ions from other metal ions especially from iron ions. The advantage of the IDA resin is its efficient regeneration with sulfuric acid, which allows one-stage desorption. However, this desorption solution cannot be directly used for copper electrolysis due to the content of a large amount of iron. Lewatit TP 220 provides better separation of individual ions and selectively separates Cu(II) from Fe(II/III). However, two separate eluent solutions should be used (sulfuric acid to get rid of precipitated iron oxides, and ammonia to strip the copper) for regeneration. Also, ammonia solution is not suitable for subsequent electrolysis.
Sorption properties and desorption efficiency of Purolite® A 832
A macroporous weak base anion exchanger with a tetraethylenepentamine (TEPA) functional group was used for copper ion sorption from the regeneration copper ammonia solution. As observed in , the Cu(II) concentration at the outlet of the column against bed volumes, 80% of sorption efficiency was achieved up to 5 BV (75 mL), where the concentration of Cu(II) was 0.5 g/L, in the last sample taken (11 BV), the sorption efficiency was still more than 38%.
Figure 12. The sorption of Cu(II) on Purolite® A 832 from the regenerant ammonia solution, where –●– sorption of Cu(II).
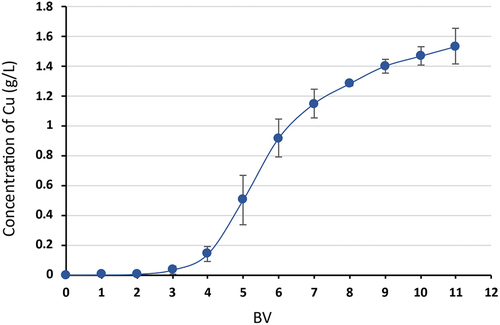
Regeneration of sorbents was carried out with 1 M H2SO4. shows the desorption curve, describing copper concentration vs bed volumes. The highest concentration of copper ions was about 12 g/L. From the overall balance, it was found that the use of 150 mL of 1 M sulfuric acid solution is enough to displace 87.8% Cu(II) from the resin. The total mass of copper desorbed by the resin in the column was 0.254 grams. The sorption capacity of Purolite® A 832 for copper ions was calculated at 19.2 ± 0.5 g/L.
Electrolysis studies
Almost all copper ions were removed from the desorption solution by the tubular fluidized bed reactor within first 60 minutes at a current density 8.7 mA/cm2 (2 A), the measured final concentration of Cu(II) in the electrolyte was 0.09 g/L.
A series of experiments with different operating currents (0.5–2 A) (2.1–8.7 mA/cm2) showed that the electrodeposition rate of copper increases with increasing current density. As can be seen in , the rate of electrodeposition of Cu(II) is directly proportional to the concentration of copper in the electrolyte solution. Linear decreasing trend indicates process limitation by set current density. Once the mass transfer limitation takes place, the exponential decrease is visible. It also follows that when the electrolysis process takes place at higher currents, less copper can be removed before moving into the ineffective mass transfer-controlled region. For the lowest current the concentration decrease trend indicates unusual behavior indicating the presence of other reactions.
Figure 14. Copper concentration vs time during electrolysis time for different operating currents, cathode area 230 cm2, where –○– 2 A; –X– 1.8 A; –♦– 1.5 A; –▬– 1.2 A; –▲– 1 A; –●– 0.8 A; –◊– 0.5 A.
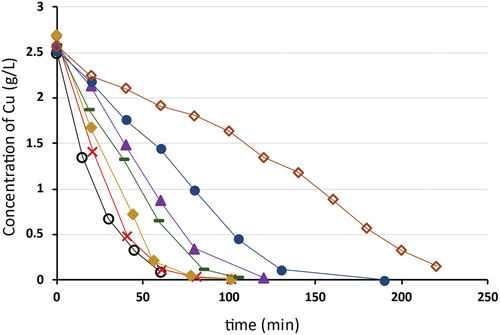
shows data of the electrolysis reactor operating limits.[Citation59] From the data it follows that the removal efficiency increases with increasing operating current, and the time required to remove copper decreases. Based on the results obtained at the operating limits of the electrolysis reactor, the optimum operating current to achieve different copper concentrations can be found by means of current efficiency (). The low efficiency at low current can be explained by reduction of dissolved oxygen (generated on anode) when the oxygen reduction is thermodynamically preferred than copper reduction. With increasing current, oxygen reduction is limited by its solubility and mass transfer; thus, current efficiency increases.
Table 4. The changing of the concentration of copper, current efficiency and removal time with operating current.
With respect to the parasitic reaction, it is better to operate at higher current density but to reach highest current efficiency only the limited time at mass transfer-controlled copper deposition is required.
To select an effective optimal current, the permissible residual concentration of copper in the electrolyte solution must be found. For this reason, batch sorption equilibrium and column desorption tests with the resin Purolite® A 832 were carried out.
Batch sorption equilibrium tests with Purolite® A 832
shows Cu(II) concentrations before and after experiments and the calculated absorbed mass of copper ions on Purolite® A 832. The practical solution’s initial Cu(II) concentrations were 0.110, 0.286, 0.463 and 0.939 g/L. As may be seen from , copper sorption took place in the solution with initial Cu(II) concentration − 0.939 g/L, when 2.96 g/L of Cu(II) were adsorbed. The amount of adsorbed copper ions was similar for the first three initial concentrations.
Table 5. Sorption equilibrium test results.
Based on sorption and electrolysis results, it was found that the initial Cu(II) concentration 0.5 g/L will be optimum and could be left in the 1 M sulfuric acid solution by considering both the energy consumption in electrolysis and effective desorption performance.
Column desorption tests with Purolite® A 832
To confirm the results (3.4.1) extra column desorption experiments were carried out using post electrolysis recycled sulfuric acid containing 0.5 g/L of Cu(II).
As may be seen in , desorption with post electrolysis recycled sulfuric acid containing 0.5 g/L of copper ions was slower than desorption with pure 1 M H2SO4. The intentional copper concentration in the last sample was 485.7 mg/L. The results also showed that 90.1% of the absorbed copper was displaced. This indicates the recycled solution suitable regeneration of the resin. To achieve the maximum possible copper desorption, the total bed volumes of the post electrolysis recycled sulfuric acid solution are higher compared with using pure H2SO4 increase. Another option could be a reduction of a specific flowrate from 6 BV/h to 3 BV/h to increase the contact time.
Figure 15. Comparison of desorption kinetic curves of Cu(II) using post electrolysis recycled 1 M H2SO4 0.5 g/L of Cu(II) and pure 1 M H2SO4, where –●– pure 1 M H2SO4; –▲– 1 M H2SO4 containing 0.5 g/L of Cu(II).
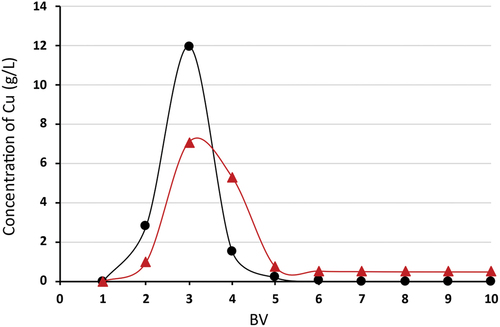
The ion exchangers were specifically selected so other metals, with significantly lower toxicity Fe, Al, Mn would not be taken up (large amounts of aluminum and manganese can also be found in some mine waters).[Citation5,Citation42] They can be removed in next step using simple precipitation. Thanks to the removal of toxic metal ions (e.g. Cu(II)) the toxicity of the precipitate (sludge) will be much lower and precise pH control would not be necessary. Lewatit TP 220 makes it possible to selectively remove copper without pre-treatment of mine water. However, on the other hand, regeneration of TP 220 is possible only with ammonia solution, which complicates the electrolysis process. It is necessary to add another sorption to the process with the help of TEPA resin. According to the proposed technology in this work, it will be possible to reuse elution solutions during the entire process. Recycling solutions should make this process cheaper. The purified sulfuric acid solution after electrolysis will be reused for the regeneration of Purolite A 832, and the purified ammonia after the sorption process on TEPA resin will be reused as a solution for elution of copper from Lewatit TP 220. The complete proposed process is shown in . This will make it possible to recycle sulfuric acid and ammonia solutions and significantly reduce costs. Optimization of sulfuric acid usage has been described in the work, but for ammonia, further research is needed. By acid – base titration it has been found that the concentration of ammonia after the whole process decreased from 2 mol/L to 1.9 mol/L, after four repetitions, the concentration was 1.5 mol/l. A decrease in the concentration can be ascribed both to evaporation of ammonia and its dilution with water during the sorption process (between repeated regenerations demineralized water was used to wash the Lewatit TP 220). The optimization of the process needs to be studied in more detail.
Conclusion
The aim of this work was to find optimal conditions for selective sorption and desorption of metals from acidic metal solutions using selected sorbents and to determine the possibility of subsequent recovery of metallic copper with electrolysis.
Two ion exchange resins were studied for selective removal of Cu(II), Ni(II) and Co(II) from synthetic solutions simulating acid mine drainage: chelating resin Lewatit® Mono Plus TP 220 containing a di-(2-picolyl)amine functional group and Lewatit® TP 208 – the chelating resin with IDA functional group. The most effective sorption was achieved using chelating resin Lewatit® Mono Plus TP 220. The calculated dynamic capacities of Lewatit® TP 208 were significantly lower: 30.6 ± 1.3 g/L for Cu(II), 9.1 ± 0.17 g/L for Ni(II) and 1.3 ± 0.08 g/L for Co(II). Also, the IDA resin was unsuitable for selective removal of copper ions, due to high affinity to Fe(II/III).
Lewatit® Mono Plus TP 220 shows a high selectivity to selected metals and sorption ability even at low pH values. The sorption efficiency decreased in the following order: Cu(II) > Ni(II) > Co(II). The total dynamic capacity for Cu(II) was 43.3 ± 1.4 g/L, for Ni(II) − 22.1 ± 2.1 g/L, for Co(II) − 3.6 ± 0.4 g/L. Sorption capacities for Lewatit® Mono Plus TP 220 and Lewatit® TP 208 were calculated for inlet solutions containing target metal ions and accompanying ions at pH of 2.5 ± 0.03.
During the Lewatit TP 220 sorption experiments due to the high iron content in AMD hydrated ferric oxide flakes formed a layer on the surface of the column. For that reason, it was necessary to use 1 M sulfuric acid in the first step to dissolve hydrated ferric oxide and 2 M ammonia solution in the second step for regeneration. By using a sulfuric acid solution, a high desorption efficiency of Co(II) (90.6%) and Ni(II) (95.5%) from Lewatit® MonoPlus TP 220 was also achieved. In other cases, high efficiency (> 90%) was achieved using an ammonia solution. The resulting ammonia solution after resins regeneration is not suitable for electrolysis process. Therefore, weak base anion exchanger having tetraethylenepentamine (TEPA) functional group Purolite® A 832 was used to take up copper from ammonia solution. After desorption of copper by sulfuric acid, a suitable electrolysis solution of 1 M H2SO4 containing Cu(II) was obtained. It was found that the resin Purolite® A 832 has a dynamic capacity for copper ions of 19.2 ± 0.5 g/L.
Another part of the work focused on the electrochemical recovery of copper from regeneration solutions. A fluidized bed electrolysis reactor, which was designed and constructed in the lab, has been successfully used to regenerate copper from desorption solutions.
By comparing the faradaic efficiency at different operating currents, it was found that 1.8 A (0.87, mA/cm2) was optimum to achieve a reduction in Cu(II) concentration from 2.5 g/L to 0.5 g/L. This post electrolysis sulfuric acid solution is suitable to be recycled and used again for effective regeneration of the Purolite® A 832.
The data obtained in this work indicate that the selective separation of copper, nickel and cobalt from iron and other metals, from acid mine drainage without pre-treatment can only be achieved using chelating resin with di-(2-picolyl)amine functional group (Lewatit® TP 220). Sorption of Fe(II/III) and Mn(II) was not observed in any of the experiments performed on TP 220. The resin with iminodiacetic acid functional group (Lewatit® TP 208) showed lower selectivity, resulting in high amount of iron(II,III) ions taken up.
As was demonstrated in this work at a lab scale, the two-step process, using di-(2-picolyl)amine and TEPA resins, does not require selective precipitation of iron(II/III) using alkaline industrial chemicals and does not need to adjust the value of pH as is necessary in other works.[Citation5,Citation31,Citation60–62] Another advantage of the process is the high selectivity that allowed recovery of pure copper in metallic form in the final electrolysis step. It should also be noted that regenerating solutions can be reused, greatly improving the economy of the process.
The application of this process has the potential to provide an effective AMD treatment step, with the added benefits of allowing for copper metal resource recovery from waste and the recycling of desorption solutions for reduced chemical consumption. The process is not limited to AMD treatment and could be utilized by industries that deal with wastewaters containing high copper concentrations.
Future studies
Further research is needed to optimize the ammonia solution process, as well as repeated electrolysis and regeneration tests for statistical analysis. It will be beneficial to carry out similar experiments with real mine waters to confirm the effectiveness of this technique.
Disclosure statement
No potential conflict of interest was reported by the authors.
Additional information
Funding
References
- Johnson, D.; Dziurla, M. A.; Kolmert, A.; Hallberg, K. B. The Microbiology of Acid Mine Drainage: Genesis and Biotreatment, 2002; Vol. 98.
- Bwapwa, J. K.; Jaiyeola, A. T.; Chetty, R. Bioremediation of Acid Mine Drainage Using Algae Strains: A Review. S. Afr. J. Chem. Eng. 2017, 24, 62–70. DOI: 10.1016/j.sajce.2017.06.005.
- Costello, C. Acid Mine Drainage: Innovative Treatment Technologies; U.S. Environmental Protection Agency, Office of Solid Waste and Emergency Response, Technology Innovation Office, 2003.
- Chen, T.; Yan, B.; Lei, C.; Xiao, X. Pollution Control and Metal Resource Recovery for Acid Mine Drainage. Hydrometallurgy 2014, 147-148, 112–119. DOI: 10.1016/j.hydromet.2014.04.024.
- Kefeni, K. K.; Msagati, T. A. M.; Mamba, B. B. Acid Mine Drainage: Prevention, Treatment Options, and Resource Recovery: A Review. J. Cleaner Prod. 2017, 151, 475–493. DOI: 10.1016/j.jclepro.2017.03.082.
- Anawar, H. Sustainable Rehabilitation of Mining Waste and Acid Mine Drainage Using Geochemistry, Mine Type, Mineralogy, Texture, Ore Extraction and Climate Knowledge. J. Environ. Manage. 2015, 158, 111–121. DOI: 10.1016/j.jenvman.2015.04.045.
- Fitzgerald, G. P.; Faust, S. L. Factors Affecting the Algicidal and Algistatic Properties of Copper. Appl. Microbiol. 1963, 11(4), 345–351. DOI: 10.1128/am.11.4.345-351.1963 (acccessed Sept 7, 2021).
- Kenefick, S. L.; Hrudey, S. E.; Peterson, H. G.; Prepas, E. E. Toxin Release from Microcystis Aeruginosa After Chemical Treatment. Water Sci. Technol. 1993, 27(3–4), 433–440. DOI: 10.2166/wst.1993.0387 (acccessed Sept 8, 2021).
- Bury, N. R.; Boyle, D.; Cooper, C. A. 4 - Iron. In Fish Physiology; Wood, C. M., Farrell, A. P., and Brauner, C. J., Eds.; Elsevier Inc. Amsterdam, Netherlands: Academic Press, 2011; Vol. 31, pp 201–251. doi:10.1016/S1546-5098(11)31004-7.
- Grosell, M.; Wood, C. Copper Uptake Across Rainbow Trout Gills. J. Exp. Biol. 2002, 205, 1179–1188. DOI: 10.1242/jeb.205.8.1179.
- Di Toro, D. M.; Allen, H. E.; Bergman, H. L.; Meyer, J. S.; Paquin, P. R.; Santore, R. C. Biotic Ligand Model of the Acute Toxicity of Metals. 1. Technical Basis. Environ. Toxicol. Chem. 2001, 20(10), 2383–2396. DOI: 10.1002/etc.5620201034 From NLM.
- Grosell, M. 2 - Copper. In Fish Physiology; Wood, C. M., Farrell, A. P., and Brauner, C. J., Eds.; Elsevier Inc. Amsterdam, Netherlands: Academic Press, 2011; Vol. 31, pp 53–133. doi:10.1016/S1546-5098(11)31002-3.
- Mendil, D.; Unal, O. F.; Tüzen, M.; Soylak, M. Determination of Trace Metals in Different Fish Species and Sediments from the River Yeşilirmak in Tokat, Turkey. Food. Chem. Toxicol. 2010, 48(5), 1383–1392. DOI: 10.1016/j.fct.2010.03.006 From NLM.
- Sole, K. C.; Mooiman, M. B.; Hardwick, E. Ion Exchange in Hydrometallurgical Processing: An Overview and Selected Applications. Sep. Purif. Rev. 2018, 47(2), 159–178, Review. DOI: 10.1080/15422119.2017.1354304 Scopus.
- Garg, B. S.; Sharma, R. K.; Bhojak, N.; Mittal, S. Chelating Resins and Their Applications in the Analysis of Trace Metal Ions. Microchem. J. 1999, 61(2), 94–114. DOI: 10.1006/mchj.1998.1681.
- Sparks, D. L. SORPTION | Metals. In Encyclopedia of Soils in the Environment; Hillel, D., Ed.; Newark, USA: Elsevier, 2005; pp 532–537. doi:10.1016/B0-12-348530-4/00554-3.
- Dinu, M. V.; Dragan, E. S. Heavy Metals Adsorption on Some Iminodiacetate Chelating Resins as a Function of the Adsorption Parameters. React. Funct. Polym. 2008, 68(9), 1346–1354. DOI: 10.1016/j.reactfunctpolym.2008.06.011.
- Jiang, J.; Ma, X.-S.; Xu, L.-Y.; Wang, L.-H.; Liu, G.-Y.; Xu, Q.-F.; Lu, J.-M.; Zhang, Y. Applications of Chelating Resin for Heavy Metal Removal from Wastewater. e-Polymers 2015, 15(3), 161–167. DOI: 10.1515/epoly-2014-0192.
- Diniz, C. V.; Doyle, F. M.; Ciminelli, V. S. T. Effect of pH on the Adsorption of Selected Heavy Metal Ions from Concentrated Chloride Solutions by the Chelating Resin Dowex M-4195. Sep. Sci. Technol. 2002, 37(14), 3169–3185. DOI: 10.1081/SS-120006155.
- Sharma, R. K.; Mittal, S.; Koel, M. Analysis of Trace Amounts of Metal Ions Using Silica-Based Chelating Resins: A Green Analytical Method. Crit. Rev. Anal. Chem. 2003, 33(3), 183–197. DOI: 10.1080/713609163.
- Platzer, N. Encyclopedia of Polymer Science and Engineering, H. F. Mark, N. M. Bikales, C. G. Overberger, and G. Menges, Wiley-Interscience, New York, 1985, 720 Pp. J. Polym. Sci., Part C 1986, 24(7), 359–360. DOI: 10.1002/pol.1986.140240720.
- Matejka, Z.; Zitkova, Z. The Sorption of Heavy-Metal Cations from EDTA Complexes on Acrylamide Resins Having Oligo(ethyleneamine) Moieties. React. Funct. Polym. 1997, 35(1), 81–88. DOI: 10.1016/S1381-5148(97)00052-7.
- Matějka, Z.; Weber, R. Ligand Exchange Sorption of Carboxylic and Aminocarboxylic Anions by Chelating Resins Loaded with Heavy Metal Cations. React. Polym. 1990, 13(3), 299–308. DOI: 10.1016/0923-1137(90)90098-O.
- Reig, M.; Vecino, X.; Hermassi, M.; Valderrama, C.; Gibert, O.; Cortina, J. L. Integration of Selectrodialysis and Solvent-Impregnated Resins for Zn(ii) and Cu(ii) Recovery from Hydrometallurgy Effluents Containing As(v). Sep. Purif. Technol. 2019, 229, Article. DOI: 10.1016/j.seppur.2019.115818 Scopus.
- Kołodyńska, D. The Effects of the Treatment Conditions on Metal Ions Removal in the Presence of Complexing Agents of a New Generation. Desalination 2010, 263, 159–169. DOI: 10.1016/j.desal.2010.06.053.
- Aderhold, D.; Williams, C. J.; Edyvean, R. G. J. The Removal of Heavy-Metal Ions by Seaweeds and Their Derivatives. Bioresour. Technol. 1996, 58(1), 1–6. DOI: 10.1016/S0960-8524(96)00072-7.
- Edebali, S.; Pehlivan, E. Evaluation of Chelate and Cation Exchange Resins to Remove Copper Ions. Powder Technol. 2016, 301. DOI: 10.1016/j.powtec.2016.06.011.
- Wołowicz, A.; Hubicki, Z. The Use of the Chelating Resin of a New Generation Lewatit MonoPlus TP-220 with the Bis-Picolylamine Functional Groups in the Removal of Selected Metal Ions from Acidic Solutions. Chem. Eng. J. 2012, 197, 493–508. DOI: 10.1016/j.cej.2012.05.047.
- Xu, Y.-L.; Song, S.-Y.; Chen, J.-D.; Chi, R.-A.; Yu, J.-X. Simultaneous Recovery of Cu2+ and Pb2+ from Metallurgical Wastewater by Two Tandem Columns Fixed Respectively with Tetraethylenepentamine and Phosphoric Acid Modified Bagasse. J. Taiwan Inst. Chem. Eng. 2019, 99, 132–141. DOI: 10.1016/j.jtice.2019.03.012.
- Mendes, F. D.; Martins, A. H. Selective Sorption of Nickel and Cobalt from Sulphate Solutions Using Chelating Resins. Int. J. Miner. Process. 2004, 74(1), 359–371. DOI: 10.1016/j.minpro.2004.04.003.
- Vecino, X.; Reig, M.; López, J.; Valderrama, C.; Cortina, J. L. Valorisation Options for Zn and Cu Recovery from Metal Influenced Acid Mine Waters Through Selective Precipitation and Ion-Exchange Processes: Promotion of On-Site/off-Site Management Options. J. Environ. Manage. 2021, 283, 112004. DOI: 10.1016/j.jenvman.2021.112004.
- Diniz, C. V.; Ciminelli, V. S. T.; Doyle, F. M. The Use of the Chelating Resin Dowex M-4195 in the Adsorption of Selected Heavy Metal Ions from Manganese Solutions. Hydrometallurgy 2005, 78(3), 147–155. DOI: 10.1016/j.hydromet.2004.12.007.
- Sengupta, A. K.; Zhu, Y.; Hauze, D. B. Metal (II) Ion Binding Onto Chelating Exchangers with Nitrogen Donor Atoms: Some New Observations and Related Implications. Environ. Sci. Technol. 1991, 25, 481–488. DOI: 10.1021/ES00015A016.
- Gorgievski, M.; Božić, D.; Stanković, V.; Bogdanović, G. Copper Electrowinning from Acid Mine Drainage: A Case Study from the Closed Mine “Cerovo”. J. Hazard. Mater. 2009, 170(2), 716–721. DOI: 10.1016/j.jhazmat.2009.04.135.
- Habashi, F. Copper Metallurgy at the Crossroads. J. Min. Metall. 2007, 43(1), 1–19. DOI: 10.2298/JMMB0701001H.
- Vecino, X.; Reig, M.; Valderrama, C.; Cortina, J. L. Ion-Exchange Technology for Lactic Acid Recovery in Downstream Processing: Equilibrium and Kinetic Parameters. Water (Switzerland) 2021, 13(11), Article. DOI: 10.3390/w13111572 Scopus.
- Motsi, T.; Rowson, N. A.; Simmons, M. J. H. Adsorption of Heavy Metals from Acid Mine Drainage by Natural Zeolite. Int. J. Miner. Process. 2009, 92(1), 42–48. DOI: 10.1016/j.minpro.2009.02.005.
- Paidar, M. Copper Remediation from Mine Waste Water in Flow-Through Cell Using a Graphite Felt Cathode; Institute of Chemical Technology Prague: Prague, 1997.
- Hedrich, S.; Johnson, D. B. Remediation and Selective Recovery of Metals from Acidic Mine Waters Using Novel Modular Bioreactors. Environ. Sci. Technol. 2014, 48(20), 12206–12212. DOI: 10.1021/es5030367.
- Brar, K. K.; Etteieb, S.; Magdouli, S.; Calugaru, L.; Brar, S. K. Novel Approach for the Management of Acid Mine Drainage (AMD) for the Recovery of Heavy Metals Along with Lipid Production by Chlorella Vulgaris. J. Environ. Manage. 2022, 308, 114507. DOI: 10.1016/j.jenvman.2022.114507.
- Sole, K. C.; Parker, J.; Cole, P. M.; Mooiman, M. B. Flowsheet Options for Cobalt Recovery in African Copper–Cobalt Hydrometallurgy Circuits. Mineral Process. Extr. Metall. Rev. 2019, 40(3), 194–206, Review. DOI: 10.1080/08827508.2018.1514301 Scopus.
- Grawunder, A.; Merten, D.; Büchel, G. Origin of Middle Rare Earth Element Enrichment in Acid Mine Drainage-Impacted Areas. Environ. Sci. Pollut. Res. 2014, 21(11), 6812–6823. DOI: 10.1007/s11356-013-2107-x.
- Richard, D.; Mucci, A.; Neculita, C. M.; Zagury, G. J. Comparison of Organic Materials for the Passive Treatment of Synthetic Neutral Mine Drainage Contaminated by Nickel: Short- and Medium-Term Batch Experiments. Appl. Geochem. 2020, 123, 104772. DOI: 10.1016/j.apgeochem.2020.104772.
- Ighalo, J. O.; Kurniawan, S. B.; Iwuozor, K. O.; Aniagor, C. O.; Ajala, O. J.; Oba, S. N.; Iwuchukwu, F. U.; Ahmadi, S.; Igwegbe, C. A. A Review of Treatment Technologies for the Mitigation of the Toxic Environmental Effects of Acid Mine Drainage (AMD). Process Saf. Environ. Prot. 2022, 157, 37–58. DOI: 10.1016/j.psep.2021.11.008.
- LANXESS. Products Information LEWATIT® MonoPlus TP 220. 2011. https://www.lenntech.com/Data-sheets/Lewatit-MonoPlus-TP-220-L.pdf ( accessed).
- LANXESS. Products Information LEWATIT® TP 208. 2011. https://www.lenntech.com/Data-sheets/Lewatit-MonoPlus-TP-208-L.pdf ( accessed).
- Purolite International Czech and Slovak Republics, org. sl.
- Zhao, X.; Höll, W. H.; Yun, G. Elimination of Cadmium Trace Contaminations from Drinking Water. Water Res. 2002, 36(4), 851–858. DOI: 10.1016/S0043-1354(01)00289-5.
- Walker, A. T. S.; Wragg, A. A. Mass Transfer in Fluidised Bed Electrochemical Reactors. Electrochim. Acta 1980, 25(3), 323–330. DOI: 10.1016/0013-4686(80)90013-4.
- Bouzek, K.; Palmer, J.; Rousar, I.; Wragg, A. A. Mass Transfer to Wall Electrodes in a Fluidised Bed of Inert Particles. Electrochim. Acta 1996, 41(4), 583–589. DOI: 10.1016/0013-4686(95)00345-2.
- Paidar, M.; Bouzek, K.; Jelínek, L.; Matějka, Z. A Combination of Ion Exchange and Electrochemical Reduction for Nitrate Removal from Drinking Water. Part II: Electrochemical Treatment of a Spent Regenerant Solution. Water Environ. Res. 2004, 76(7), 2691–2698. DOI: 10.1002/j.1554-7531.2004.tb00231.x.
- Kołodyńska, D.; Sofińska-Chmiel, W.; Mendyk, E.; Hubicki, Z. DOWEX M 4195 and LEWATIT® MonoPlus TP 220 in Heavy Metal Ions Removal from Acidic Streams. Sep. Sci. Technol. 2014, 49(13), 2003–2015. DOI: 10.1080/01496395.2014.908920.
- Sahni, S. K.; Reedijk, J. Coordination Chemistry of Chelating Resins and Ion Exchangers. Coord. Chem. Rev. 1984, 59, 1–139. DOI: 10.1016/0010-8545(84)85053-5.
- Grinstead, R. R. Selective Absorption of Copper, Nickel, Cobalt and Other Transition Metal Ions from Sulfuric Acid Solutions with the Chelating Ion Exchange Resin XFS 4195. Hydrometallurgy 1984, 12(3), 387–400. DOI: 10.1016/0304-386X(84)90009-4.
- Ajiboye, A. E.; Olasehinde, F. E.; Adebayo, O. A.; Ajayi, O. J. Recovery of Copper and Nickel from Polymetallic Sulphate Leach Solution of Printed Circuit Boards Using Dowex M 4195. Physicochem. Probl. Miner. Process. 2019, 55(5), 1156–1164. DOI: 10.5277/ppmp19038.
- Park, K. H.; Parhi, P. K.; Kang, N.-H. Studies on Removal of Low Content Copper from the Sea Nodule Aqueous Solution Using the Cationic Resin TP 207. Sep. Sci. Technol. 2012, 47(10), 1531–1541. DOI: 10.1080/01496395.2011.652285.
- Hubicki, Z.; Kołodyńska, D. Selective Removal of Heavy Metal Ions from Waters and Waste Waters Using Ion Exchange Methods; Kilislioğlu, A., Ed.; Ion Exchange Technologies: London, 2012. DOI: 10.5772/51040.
- Yuchi, A.; Sato, T.; Morimoto, Y.; Mizuno, H.; Wada, H. Adsorption Mechanism of Trivalent Metal Ions on Chelating Resins Containing Iminodiacetic Acid Groups with Reference to Selectivity. Anal. Chem. 1997, 69(15), 2941–2944. DOI: 10.1021/ac9612685.
- Wilson, R. Recovery of Copper from Acid Mine Drainage Using Chelating Ion Exchange and Electrolysis. Master’s Degree, University of Chemistry and Technology in Prague, University of Strathclyde, 2018.
- Akinwekomi, V.; Kefeni, K. K.; Maree, J. P.; Msagati, T. A. M. Integrated Acid Mine Drainage Treatment Using Mg(oh)2 or Mg(hco3)2 and Ca(oh)2: Implications for Separate Removal of Metals and Sulphate. Int. J. Miner. Process. 2016, 155, 83–90. DOI: 10.1016/j.minpro.2016.08.009.
- Watten, B. J.; Sibrell, P. L.; Schwartz, M. F. Acid Neutralization Within Limestone Sand Reactors Receiving Coal Mine Drainage. Environ. Pollut. 2005, 137(2), 295–304. DOI: 10.1016/j.envpol.2005.01.026.
- Olds, W. E.; Tsang, D. C. W.; Weber, P. A.; Weisener, C. G. Nickel and Zinc Removal from Acid Mine Drainage: Roles of Sludge Surface Area and Neutralising Agents. J. Min. 2013, 2013, 698031. DOI: 10.1155/2013/698031.