ABSTRACT
Entrained flow drying is an important fast drying tool in tobacco industry. This study used a drop tube reactor (DTR) as an entrained flow dryer to investigate drying process of flue-cured cut tobacco. Lab-scale cold and hot DTRs were set up to obtain drying kinetics for three types of cut tobacco using different drying gases and temperatures. The effective diffusion coefficients of cut tobacco in DTRs were compared with those in a general cylinder dryer. Moreover, the effects of different drying gases and temperatures on petroleum ether extract content were investigated. The results showed that the effective diffusion coefficients of cut tobacco in the DTRs were between 2.296 × 10−8 and 8–6.244 × 10−8 m2/s, which are two orders of magnitude higher than those in the cylinder dryer. Compared to hot air as a drying medium, superheated steam improved the effective diffusion coefficient of cut tobacco. The petroleum ether tobacco extract had a higher retention ratio when the superheated steam was used in the DTRs. An increase in the drying temperature resulted in a lower retention of the petroleum ether tobacco extract.
Introduction
Drying of cut tobacco to a suitable moisture content is an important operational step in tobacco primary processing. It has a significant effect on the physical and chemical properties of processed tobacco materials.[Citation1] Developing new drying technology to improve the quality of dried products has always been the focus of attention in the tobacco industry. The current drying methods for tobacco processing mainly include entrained flow drying and cylinder drying.[Citation2,Citation3] Entrained flow drying has a higher drying efficiency because of enhanced heat and mass transfer conditions.[Citation4,Citation5] In addition, it could improve the filling value of cut tobacco (a parameter describing a reduced apparent density of cut tobacco to achieve the same tobacco rod firmness), which is beneficial in reducing the tobacco consumption for cigarette making. For example, a riser dryer is one type of entrained flow dryer, which works based on gas–solid concurrent upward interaction. In doing so, solid transport is affected by the particle clustering and back-mixing[Citation6,Citation7] at different residence times and a high dispersion in the output solid properties can be achieved.[Citation8]
Over the last two decades, the gas–solid concurrent drop tube reactor (DTR) has been developed as a new type of fluidized reactors, which takes gas–solid concurrent with gravity field movement.[Citation9] Compared with the riser dryer, the DTR has several distinct advantages, such as narrow residence time distribution for particulate materials, low energy consumption, better product homogeneity, and high particles loads.[Citation7] In view of its advantages, the DTR has received wide attention in many industrial fields. For example, it has been used as a combustion reactor of different fuel characteristics.[Citation10] For petroleum catalytic cracking and biomass pyrolysis, the DTR was used as pyrolysis reactors to improve product yields.[Citation9,Citation11] In addition, the DTR has also been proposed as a fluidized dryer.[Citation8] However, the drying characteristics of particulate materials in a DTR, including drying kinetics and dried product quality, still requires further investigation and optimization. The objective of this work was to investigate the drying characteristics of cut tobacco materials in a DTR dryer. Both cold and hot DTRs were used in the present work to determinty -22 e the drying kinetics. The effect of drying gas atmosphere and temperature on the drying kinetics and dried leaf quality was systematically studied. The experimental results in this work could provide useful data for the design and application of this new type of dryer for tobacco processing.
Experimental platform
The cold DTR device in this work was designed to test the movement velocity and residence time of tobacco particles in a drop tube (). The device consisted of an air source, a charging unit, a drop tube, a discharge unit, and data acquisition system. The air source was either compassed air or bottled nitrogen. The charging unit consisted of an upper ball valve, a feed bin, and a lower ball valve. The drop tube was a 6-m long Polymeric Methyl Methacrylate (PMMA) tube with 150 mm diameter, in which 15 photoelectric detectors were uniformly distributed along its length. The data acquisition system collected signals from the photoelectric detectors.
Figure 1. A schematic diagram of the cold DTR. 1: Gas source; 2-1–2-2: stop valve; 3: pressure meter; 4: ball valve; 5: rotameter; 6: gas inlet; 7: flange; 8: drop tube; 9: gas outlet; 10: receiver; 11: data line; and 12: data acquisition system.
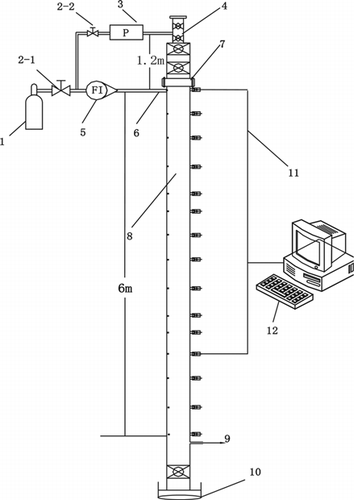
shows the hot DTR device, which consisted of an air source, a gas temperature and humidity control unit, a charging unit, a drop tube, a tube temperature control unit, and a discharge unit. As the drying medium, gas temperature and humidity control could be modified to produce superheated steam or hot air with different humidity levels, which was led through the drop tube from the gas inlet on the top of the DTR. The charging unit and the drop tube had the same structure and size with those of the cold device. The hot device has 15 uniformly set heating zones from the top to the bottom of the DTR to heat the drop tube. Correspondingly, 15 gas outlets were uniformly set at the bottom of each heating section of the drop tube. The discharge unit could collect the dried materials through a ball valve in the bottom of the DTR.
Figure 2. Diagram of the hot DTR. 1: Gas source; 2-1–2-4: stop valve; 3.1–3.2: rotameter; 4: flux pump; 5: pressure meter; 6: steam generator; 7.1–7.2: air preheater; 8: flange; 9: air inlet; 10–11: hygrometer; 12: drop tube; 13: blanking buffer; 14: receiver; 15: data line; and 16: temperature controller.
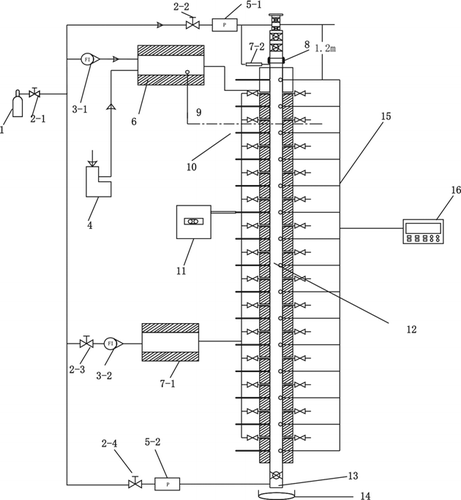
Materials and methods
Sample preparation
Three types of flue-cured tobacco were chosen as experimental materials, differing by the position along the tobacco plant (hence with different physical properties and chemical compositions), the upper tobacco leaf (coded B2F), middle tobacco leaf (coded C2F), and the lower tobacco leaf (coded X2F). All the tobacco leaves were cut into the width of approximately 0.8 mm. The initial moisture content of the tobacco was adjusted to 30% (on the wet basis) using an isothermal and constant humidity chamber with reference to normal operating conditions in tobacco primary processing (a stage of the tobacco processing where raw tobacco are cut and blended to achieve the right uniformity before being fed into a cigarette maker).
Drying experimental methods
The cold DTR device was used to measure the falling velocity of cut tobacco at different moisture contents, which was used to determine the drying kinetics in the hot DTR. The gas in the cold DTR was bottled nitrogen and supplied at a flow rate of 40 L/min Standard Temperature and Pressure (STP). Six levels of tobacco moisture contents were investigated, that is, 10, 15, 20, 25, 30, and 35%, covering the normal range experienced in tobacco processing. For each moisture level, 2 g sample was put into the feed bin of the charging unit. The lower ball valve of the charging unit was then opened, and the sample was fed into the drop tube. The corresponding falling time at the positions of each photoelectric detector was recorded. This allows the relationship of the drop height to the falling time of cut tobacco be calculated. In the cold DTR, the falling experiments were performed at three replicates at each condition to obtain an average result.
The drying experiments were then performed in the hot DTR. Two drying media were used, namely, the absolute dry air and superheated steam at five set temperatures, that is, 180, 210, 240, 270, and 300°C. The gas flow rate was set to the same level to that used in the cold DTR. The length of the heating section of the drop tube for each drying condition was set to different levels. The tobacco sample was dried and a sample of which was received at each level to measure its moisture content. In this way, the relationship between the falling height (i.e., length of the heating section of the drop tube) and the moisture content of the cut tobacco could be obtained under each drying condition. This relationship was then combined with that of the falling height vs. the falling time of the cut tobacco in the cold DTR to determine the drying kinetics in the hot DTR.
Sample analysis
The dried sample was collected from the receiver of the hot DTR. The moisture content of the samples from each drying test was detected by an oven method to determine the drying curves. Some samples were also used to determine the petroleum ether extract, which is an approximate parameter used in the tobacco industry to give an indication to the drying quality of cut tobacco.
The petroleum ether extract content in the dried sample was measured according to an industry standard method using a Soxhlet extractor. For this test, 2 g of dried sample was shred into tobacco power and placed in a Soxhlet extractor, into which petroleum ether was added. The extractor was hold in a water bath at 50°C for 8 h. The extraction solution was dried, and the resultant extract was weighted to determine the so-called petroleum ether extract content. The reproducibility was also determined by three repetitive extraction tests.
Data analysis
Matlab software (MathWorks, Inc., USA) was used for statistical analysis of experimental data obtained in both the cold and hot DTR. The velocity equation and moisture diffusion equation were solved by Matlab to obtain the drying kinetics parameters.
Results and discussion
Drop velocity of cut tobacco in cold DTR
The relationship between the falling time vs. the falling height of the cut tobacco at 10–35% moisture contents is presented in . A linear correlation between the falling time and the height was prominent, confirmed by the linear fitting of the experimental date achieving R2 > 0.999. This result indicated that the cut tobacco traveled in the cold DTR at a constant velocity, a higher moisture content tobacco particle fell more quickly than a lower moisture tobacco particle of otherwise equal properties. presents the numeric expressions between the falling time (t) and the falling height (H).
Table 1. Numeric equations obtained from cold DTR experiments.
The falling velocity (u) of the cut tobacco at a given moisture content in the cold drop tube can be expressed as follows:
shows the relationship between the velocity and the moisture content of the cut tobacco. The fitting result indicated that the velocity of the cut tobacco in the DTR had a linear relationship with the moisture content:
Drying curves: cut tobacco in hot DTR
The relationship of the drop height (i.e., the heated length of the drop tube) to the moisture content of the cut tobacco was obtained in the hot DTR. shows the experimental results of the C3F cut tobacco dried at different air temperatures.
In , it was shown that the moisture content of the cut tobacco gradually decreased at a given moment when it fell through the hot DTR. Hence, the falling velocity was not constant, and the movement greatly differed from that in the cold DTR. According to a previous study,[Citation12] an exponential decay equation [Eq. (3)] could be used to describe the relationship of the moisture content and the falling height of the cut tobacco.
By combining Eqs. (2) and (3):
According to Eq. (4), the falling height of the cut tobacco in could be used to derive the corresponding falling time (i.e., drying time). The drying curves of the cut tobacco in the hot DTR were thus obtained. show the drying curves of the three types of cut tobacco dried using hot air and superheated steam at different temperatures.
illustrate that the cut tobacco in the hot DTR underwent rapid drying: the moisture contents were reduced from the initial 30% to near or below 15% in less than 2 s. The higher temperature of the hot air or the superheated steam, the lower the final moisture content. The drying rate was in the order of: X2F > B2F > C3F, when the three types of cut tobaccos were compared. Superheated steam drying also seemed to be more effective than hot air drying at the same drying temperature.
Effective moisture diffusivity in DTR
When dropping in the dryer by gravity, cut tobacco particles were gradually dispersed along the vertical direction by collision and buoyance. Heat transfer to and from the cut tobacco through drying media mainly occurred by convection. Moisture in the cut tobacco was transferred out by vaporization to the hot air. The apparent moisture diffusion equation can be expressed according to Fick’s second law:
The analytical solution of Fick’s second law[Citation13] for the thin-layer material or stacked sheets can be resolved as follows:
While n is more than 3, the correlation coefficient tends to be stable, and the relative error is less than 5‰.[Citation14] Therefore, the first three terms were considered to calculate the effective diffusion coefficient. In the meantime, for the drying media of 99.99% nitrogen, Me can be approximately equal to 0. Hence, Eq. (3) can be simplified as follows without considering the shrinkage of the cut tobacco volume:
shows the experimental values of De for the three kinds of tobacco. The De of the lower tobacco leaves X2F in superheated steam significantly improved from 3.280 × 10−8 to 6.244 × 10−8 m2/s when the drying temperature increased from 180 to 300°C. The middle tobacco leaves C3F had the lowest De values, which varied from 2.296 × 10−8 to 4.942 × 10−8 m2/s. The De values of the cut tobacco in the absolute dry air were lower than those in the superheated steam. Compared to the reported results in the cylinder and fixed-bed dryers,[Citation15,Citation16] the effective moisture diffusivity of the cut tobacco in the DTR was significantly higher, that is, two orders of magnitude higher than those in the cylinder dryer.
Table 2. Effective moisture diffusivity of cut tobacco with different drying conditions.
Aside from the high drying temperature, the enhanced heat and mass transfer in the DTR were caused by its high gas/solid contact efficiency, thus the larger De values. When tobacco solids were transported in DTR, particles clustering were less obvious and the clusters are more unstable than those in the riser.[Citation7,Citation9] This means the solid particles could be dispersed more uniformly, and the uniform gas–solid flow structure of DTR is beneficial to heat and mass transfer. On the other hand, the superheated steam has high heat transfer coefficient when it is used as a drying medium. In the present DTR experiments, the drying temperatures were significantly higher than the reported inversion temperature,[Citation17] beyond which superheated steam drying was always faster than hot air drying. This could explain the higher moisture evaporation efficiency of superheated steam drying in .
Petroleum ether tobacco extract
The petroleum ether tobacco extraction mainly consists of volatile oil, resins, fatty acids, waxes, lipids, sterols, and pigments. Its content is often considered as an important index in estimating the quality of tobacco aroma. shows the effect of the drying temperature on the retention of the petroleum ether tobacco extracts for the three types of tobacco treated in superheated steam.
The 20°C sample depicted that the initial cut tobacco was balanced at room temperature before the drying process. The petroleum ether extract content was the highest in the upper tobacco leaf B2F. The C3F had a slight higher content compared to X2F. In comparison with the initial sample, dried products had relatively lower petroleum ether extract content. The higher the drying temperature, the lower the retention of the petroleum ether extracts. This result was related to the enhanced exposure of the cut tobacco to the heating environment. During drying in tobacco primary processing, flue-cured tobacco is heat sensitive and some of its volatile flavor components are subjected to evaporative, oxidative, or chemical cracking losses[Citation1,Citation3] which leads to noticeable quality degradation of dried tobacco materials.[Citation18,Citation19]
compares the effects of the drying media on the petroleum ether tobacco extracts at 210 and 270°C. The petroleum ether extract contents by superheated steam were significantly higher for the three types of tobacco, about 1.5 times of that was dried by absolute dry air. It seemed that the superheated steam drying improved the retention of functional components in tobacco leaves. Many research works also found that the atmospheric or low-pressure superheated steam drying resulted in the high retention of bioactive compounds, coloring materials, and proteins in different dried products.[Citation20Citation21Citation22] These findings could be related to the following two reasons. First, due to the oxygen-free atmosphere, the superheated steam drying could reduce the oxidation of some components in dried materials. Especially for the tobacco materials, their petroleum ether extract contains a large number of aldehydic and phenolic compounds, as were easily oxidized at high temperature. Second, the higher effective moisture diffusivity of cut tobacco in superheated steam shortened the exposure time of the sample to the heating environment, thus reducing the loss of heat-sensitive components in petroleum ether extract.
It can be seen that the tobacco drying in the DTR dryer showed significantly higher level of effective moisture diffusivity than the conventional cylinder drying used in tobacco processing. When compared with the riser dryer with gas–solid concurrent upward flow, due to the uniform gas–solid flow structure of DTR as reported in many fluidization literatures,[Citation6Citation7Citation8Citation9] the new type of dryer would provide the better product homogeneity. On the other hand, in the present work, the superheated steam as the drying medium showed a better effect on the retention of petroleum ether extract in tobacco than the conventional hot air drying. The DTR dryer combined with the superheated steam drying showed good application potential in tobacco industry.
Conclusion
Two lab-scale DTRs, namely a cold and hot drier, were used in this study as an entrained flow dryer for cut tobacco. The cold DTR was used to measure the relationship of the drop height to the residence time of the cut tobacco, whereas the hot DTR was used to measure the relationship between the cut tobacco’s drop height and moisture content. The drying kinetics of the cut tobacco in the DTR dryer was determined by combining the cold and hot experiments. The effect of the gas atmosphere and temperature on the drying kinetics was investigated. The petroleum ether tobacco extract in the dried products was also analyzed. The results showed that the effective diffusion coefficients of the cut tobacco in the DTR were between 2.296 × 10−8 and 6.244 × 10−8 m2/s, which was two orders of magnitude higher than those in the cylinder dryer. Compared to hot air, superheated steam could improve the effective diffusion coefficient of cut tobacco. The petroleum ether extract in tobacco had a higher retention ratio (i.e., 1.5 times of that dried by absolute dry air) when superheated steam was used in the DTR. The increasing drying temperature resulted in a lower retention ratio of the petroleum ether extract in tobacco.
Additional information
Funding
References
- Lai, W. L.; Liu, J. S.; Cai, G. H.; Lin, Y.; Li, Y. F.; Hong, W. L. Study on the Variety of Alkalis and Neutral Flavor Components During Key Cigarette Process. J. Instrum. Anal. 2004, 23(Suppl. 1), 272–273.
- Zhu, W. K.; Wang, L.; Duan, K.; Chen, L. Y.; Li, B. Experimental and Numerical Investigation of the Heat and Mass Transfer for Cut Tobacco During Two-Stage Convective Drying. Drying Technol. 2015, 33(8), 907–914.
- Zhu, W. K.; Wang, Y.; Chen, L. Y.; Wang, Z. G.; Li, B.; Wang, B. Effect of Two-Stage Dehydration on Retention of Characteristic Flavor Components of Flue Cured Tobacco in Rotary Dryer. Drying Technol. 2016, 34(13), 1621–1629.
- Kim, D. H. Simulation Study for Pneumatic Conveying Drying of Sawdust for Pellet Production. Drying Technol. 2014, 32(10), 1142–1156.
- Zhang, Y.; Zhou, F.; Xia, T.; Liu, C.; Wang, X. Experimental Investigation on Blockage Boundary for Pneumatic Conveying of Powders in Narrow Bifurcation Slits. Drying Technol. 2016, 34(9), 1052–1062.
- Bassi, A.; Briens, C.; Bergougnou, M. Short Contact Time Fluidized Reactors (SCTFRs). In Circulating Fluidized Bed Technology IV; Avidan, A. A., Ed.; AIChE, Newyork, 1994; pp 15–19.
- Cheng, Y.; Wu, C.; Zhu, J. Downer Reactor: From Fundamental Study to Industrial Application. Powder Technol. 2008, 183(3), 364–384.
- Alvarez, P. I.; Vega, R.; Blasco, R. Cocurrent Downflow Fluidized Bed Dryer: Experimental Equipment and Modeling. Drying Technol. 2005, 23(7), 1435–1449.
- Zhu, J. X.; Yu, Z. Q.; Jin, Y. Cocurrent Down Flow Circulating Fluidized Bed (Downer) Reactors—A State of the Art Review. Can. J. Chem. Eng. 1995, 73(5), 662–677.
- Yao, J. Coal Topping in a Fluidized Bed System. Fuel Energy Abstr. 2002, 43(4), 275.
- Deng, R.; Wei, F.; Jin, Y. Experimental Study of the Deep Catalytic Cracking Process in a Downer Reactor. Ind. Eng. Chem. Res. 2002, 41(24), 6015–6019.
- Wang, P. F.; Liu, C. X.; Li, B. Study on Rapid Drying Kinetics of Cut Tobacco in Gas–Solid Cocurrent Down Flow Fluidized Bed Dryer. Tob. Sci. Technol. 2014, 47(4), 5–9.
- Crank, J. Mathematics of Diffusion, 2nd ed.; Oxford University Press: London, 1975.
- Liu, Z.; Li, B.; Yu, C. F. Dynamics Analysis of Multiple Heat Transfer Impacts on Intensive Mass Transfer Daring Thin Layer Drying Processing of Cut Tobacco. Tob. Sci. Technol. 2009, 42(11), 5–10.
- Li, B.; Wang, P. F. An Experimental Study on Drying Kinetics of 15 Kinds of Cut Tobacco in the TG Drier. Ninth Asian Thermophysical Properties Conference, 19 October, Beijing, 2010.
- Pan, G. L.; Yu, C. F.; Shen, Y. J.; Zhang, E. Q.; Liu, Y. H.; Zhu, W. K. The Drying Characteristics of Cut Tobacco by Combining Radiation Heat Transfer and Vacuum. Tob. Sci. Technol. 2015, 48(Suppl. 1), 68–75.
- Johnson, P. W.; Langrish, T. A. G. Inversion Temperature and Pinch Analysis, Ways to Thermally Optimize Drying Processes. Drying Technol. 2011, 29(5), 488–507.
- Chin, S. K.; Law, C. L. Maximizing the Retention of Ganoderic Acids and Water-Soluble Polysaccharides Content of Ganoderma lucidum Using Two-Stage Dehydration Method. Drying Technol. 2014, 32(6), 644–656.
- Rodriguez, A.; Rodriguez, M. M.; Lemoine, M. L.; Mascheroni, R. H. Study and Comparison of Different Drying Processes for Dehydration of Raspberries. Drying Technol. 2016, 35(6), 689–698.
- Chalida, N.; Manop, C.; Pornpimon, M.; Sakamon, D. Bioactive Compounds and Bioactivities of Centella asiatica (L.) Urban Prepared by Different Drying Methods and Conditions. Drying Technol. 2013, 31(16), 2007–2015.
- Liu, J.; Zang, L.; Xu, Q.; Wang, R.; Li, Z. Drying of Soy Sauce Residue in Superheated Steam at Atmospheric Pressure. Drying Technol. 2017, 35, 1655–1662.
- Tungtrakul, P. Quality Attributes of Germinated High-Amylose and Waxy Rice in Superheated Steam and Hot Air Drying. Drying Technol. 2015, 33(7), 876–885.