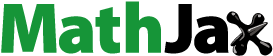
Abstract
Drying of paper during 2000–2018 is reviewed. The review includes new drying processes, multi-cylinder dryers, tissue and impingement drying, TAD-drying, infrared drying and energy use for drying of paper. It includes general aspects of infrared dryers but not drying of coated papers. Paper quality aspects, paper shrinkage and paper isotherms are not included. Impingement drying has been the most successful new technology with several applications while others such as impulse drying has not been commercialized mainly due to problems with paper quality parameters. One promising development is the introduction of steel instead of cast iron cylinders with increased heat transfer reducing the number of cylinders. Future research should focus on modeling the internal transport phenomena and to couple these phenomena to paper shrinkage and quality parameters. The influence of the fabric for the drying process needs more attention, understanding the drying process for new components such as microfibrillar cellulose in the stock and reducing energy use and increasing the amount of renewable energies for drying of paper.
Introduction
Worldwide about 410 million tons of paper were produced 2016[Citation1] and notwithstanding the internet era is still increasing year by year. Drying of the paper (printing paper, board, and tissue) is a major step on the paper producing machine requiring large amounts of energy and setting high demands on the quality for the produced paper grades. In small countries such as Sweden and Finland, the pulp and paper processes have a large share of the national economy and new developments are supported by national research funds. The multi-cylinder dryer is a large body of cast iron cylinders typically over 100 m long, and there are many incentives for reducing the length, increasing the speed and controlling all the different paper quality parameters. This review will cover the developments that have taken place in different paper drying technologies during 2000–2018.
Mujumdar published an early review about developments in the paper drying area.[Citation2] The review mentioned through drying, impingement drying and combinations of mechanical and thermal dewatering-drying of the paper web such as the Convac process as possible future industrial applications. Impingement drying has been a topic of considerable research during the years and a quite large number of different designs have been proposed. Convac drying, later called the Condebelt process, has resulted in two industrial installations. Wedel[Citation3] discussed different process configurations of the traditional multi-cylinder dryer as well as the possibilities with hot air impingement. Cross-directional shrinkage was mentioned as one challenge to achieve an even quality of the paper produced. Pikulik and Poirier[Citation4] in their review mainly focused on the high intensity dryer concept which is based on impingement drying on large diameter Yankee cylinders. The series Papermaking Science and Technology devotes book number 9[Citation5] to different paper drying aspects such as the multi-cylinder and other paper drying processes, steam and condensate systems, paper quality, and automation aspects for the dryers and should be consulted for information. A good chapter about drying of pulp and paper is also given by Polat and Mujumdar.[Citation6]
This review will cover published papers related to paper drying technologies from scientific journals and conferences during 2000 and 2018. The review includes new drying processes, multi-cylinder dryers, tissue, and impingement drying, TAD-drying, infrared drying and energy use for drying of paper. It will not include mechanical dewatering in the press section even if some processes such as impulse drying includes such phenomena as well. It will include general aspects of infrared dryers but not include drying of coated papers, paper quality aspects and paper isotherms. The reason for this is to limit the number of papers reviewed.
The technology for drying of pulp has not changed drastically during this period. The main development has been the introduction of two shoe presses to increase the dry matter content to around 50% before the pulp dryer. For this reason only a few publications related to the drying of pulp has been published during this period. Strømmen et al.[Citation7] studied heat pump drying in a fluidized bed dryer and Vieira et al.[Citation8] studied drying kinetics for recycled paper pulp. The best summary for drying of pulp is given by Larsson and Karlsson in Papermaking Science and Technology.[Citation9]
New drying processes
Condebelt
The Condebelt process was developed by Prof. Jukka Lehtinen and the first patent was issued already in 1975.[Citation10,Citation11] The idea is based on a heat pipe mechanism to achieve high drying rates and at the same improve several paper quality parameters such as surface smoothness, density, and Scott Bond values. The first industrial plant was started at the Pankakoski mill in Finland during 1996 and the second plant at the Dong Il mil in South Korea during 1999. The machines produce cardboard, linerboard, and fluting paper qualities. The machine in Finland is still in operation but due to change in ownership the machine in Korea will be taken out of production during 2019. Timofeev et al.[Citation12] used an experimental set-up to investigate different process parameters for the process. Temperatures inside a multi-layered sheet ranged between 100 and up to 160 °C for a hot plate temperature of 170 °C. Drying rates were 6–8 times higher compared to the multi-cylinder dryer. Clearly the motivation for this process is the large improvements in different paper strength parameters as well as the increased drying rates. The drawbacks are a rather complicated and expensive design involving moving steel bands at high velocities. A review of Condebelt, impingement, and impulse drying was presented by Talja et al.[Citation13] from the Metso company, presently the Valmet company.
Gas heated cylinder
Internally gas-heated cylinder dryers were developed during the 1980s by ABB in Canada and later the technology was sold to the Andritz company. There were 13 units installed in the US, Canada and Australia and today at least 4 of the US dryers are in operation,[Citation14] one installation is shown in . The idea is to increase the surface temperature by firing natural gas inside the cylinder either using an impingement design or an infrared design. In this way, the heat flux to the paper web increased resulting in drying rates 2–4 times higher compared with steam-heated cylinders. Lang et al.[Citation15] performed lab-scale experiments to study drying rates and changes in paper quality parameters. Using a surface temperature of 290 °C, the drying rate for a newsprint paper could be increased by 3 times compared to a surface temperature of 100 °C. The gas combustion and flue gases circulating unit is rather complex and exiting flue gases at high temperatures could result in lower energy efficiencies.
Figure 1. Tending side of a gas heated drying cylinder in the US [Citation14] (courtesy of Andritz Canada).
![Figure 1. Tending side of a gas heated drying cylinder in the US [Citation14] (courtesy of Andritz Canada).](/cms/asset/f0166d81-ad72-4e57-a3fb-8ddae979eb94/ldrt_a_1596949_f0001_c.jpg)
Impulse drying
The idea of impulse drying was initially developed during the 1980s at IPC in Appleton and the developments then moved to IPST in Atlanta, Georgia. It was said by one of the inventors that the idea came up when a heated hammer head was hit against a wet paper surface and it was found out that the paper area hit by the head had dried very significantly. Thus, the idea was to use temperatures in the range 250–450 °C, pressures 2–10 MPa and a very short residence times such as could be achieved in an extended press nip. Significant resources were spent on developing this technology among universities,[Citation16,Citation17] research institutes in Atlanta and Stockholm[Citation18,Citation19] and machine building companies. One main challenge has been to avoid delamination of the paper sheets, see .
Figure 2. Delamination of the paper web (reprinted from[Citation20], by permission from Tappi J.).
![Figure 2. Delamination of the paper web (reprinted from[Citation20], by permission from Tappi J.).](/cms/asset/62a47d38-fa63-4445-8d07-55cdb385f83f/ldrt_a_1596949_f0002_b.jpg)
Two heated extended nips were built at the EuroFEX pilot machine at Innventia in Stockholm which could operate at industrial machine speeds on a 300 mm wide paper web. Nilsson and Stenström[Citation21,Citation22] developed a model for the unsteady heat transfer in the press nip and compared the results with lab-scale experiments from an MTS-press[Citation23] as well as the EuroFEX pilot machine. The model only considered conductive heat transfer in the web and did not include compression of the web. Generally, the predictions from the model were too low, for both the MTS-press and the EuroFEX experiments, one result from the MTS-press operating at a dwell time of 50 ms and a peak pressure of 8 MPa is shown in . The main explanation for the differences was that no compression of the web was included.
Figure 3. Comparison of experimental[Citation23] and calculated data for an MTS-press.[Citation21]
![Figure 3. Comparison of experimental[Citation23] and calculated data for an MTS-press.[Citation21]](/cms/asset/72ea1ba9-8152-486c-b8ea-fa2e297e2274/ldrt_a_1596949_f0003_b.jpg)
Larsson and Orloff[Citation24,Citation25] performed experiments with an MTS laboratory platen press with longer press pulses in the range 32–64 ms. The moisture ratio change increased from 0.6 to 0.8 kgwater/kgdry matter when the press impulse was tripled. Also pilot-scale experiments were performed by Larsson and Stenström[Citation26,Citation27] at STFI in Stockholm. The length of industrial shoe-presses is limited to around 0.3 m so this technology needs further development if residence times longer than 30 ms are to be achieved for a web moving at 10 m/s. Martinez et al.[Citation28,Citation29] studied dryness and physical properties for a range of hot pressing parameters in a laboratory platen press. The platen press temperatures were in the range 23–380 °C, residence times between 25 and 500 ms and peak pressures 1–5 MPa. Either a positive or negative pressure profile was studied in order to avoid delamination phenomena and most of the experiments were performed with a TMP furnish. As expected, the temperature and the press impulse had a strong influence on the amount of water removed, but no differences were noted for different the shapes of the press pulse.
Riepen[Citation30] developed a model for hot pressing processes and validated the model at a pilot paper machine with press roll temperatures between 50 °C and 235 °C. The agreement with the experimental data was good, but the variation in the outgoing dryness of the web was not large in the experiments. Aguilar Ribeiro and Costa developed an extensive model that included densification of both the felt and the paper.[Citation17,Citation31–33] The prediction for the felt compression was compared with experimental data with fair agreement. Martin et al.[Citation34] evaluated data obtained from the EuroFEX machine in Stockholm from an energy cost perspective and found that the energy costs will increase by 5–20% due to the use of more expensive electricity. However, the higher energy costs were expected to be balanced by savings in pulp costs and increased productivity.
Nilsson and Norman used a slightly different approach with a thin metal band for transferring the energy to the paper in the press nip.[Citation35–37] The experiments were performed in laboratory set-up where the band was heated in a specially designed oven. Dewatering was highest for the steel bands and below a band thickness of 0.2 mm for steel and copper and 0.3 mm for aluminum the dewatering was reduced. The idea with using bands is to limit the energy transfer to the paper and thus reduce the problems with flashing of steam at the nip exit causing delamination. A 0.5 mm thick steel band could be heated to as high as 275 °C without any detectable decrease in the z-direction strength of the paper as measured by the Scott-Bond value. The backside of the band would need some insulation to reduce heat losses and increase energy efficiency for the process. The design using bands for the energy transfer is similar to the Condebelt approach and has been developed by Valmet in the so-called soft calendering concept, see . The purpose here is not dewatering but to improve the surface properties of the paper.
So far no industrial impulse drying processes have been installed due to paper quality issues and using electricity for heating to high temperatures which is more expensive than the traditional low-pressure steam in the multi-cylinder design.
Other new technologies
Drying using superheated steam is common for drying of beet pulp, wood particles, and bark.[Citation38] Research using this technology also for paper has been performed by McCall and Douglas who studied quality changes for the paper.[Citation39] No industrial units have been installed and one main challenge is to enter the web in the superheated steam atmosphere without entraining too much air. Also superheating the steam requires rather high steam pressures which will reduce the amount of backpressure power production at the mill increasing the cost for the process.
Microwave drying is an attractive technology where the energy is absorbed in the material where the water is. The technology has also been tested for drying of paper, Ahrens and Habeger[Citation40,Citation41] developed a model for the applicator so that it can be designed for web preheating and increased dewatering and drying. Challenges to be addressed are the energy efficiency of the microwave generator, high power levels are required, electricity is normally more expensive than steam and even distribution of the energy over the machine width. To authors knowledge, there are no industrial installations so far.
Pulsed combustion can be used to increase the heat and mass transfer rates during impingement drying. Wu et al.[Citation42] performed both experiments and CFD calculations to study the technology. Two of the main conclusions were that efficient drying extended up to three diameters of the tail pipe and that near the stagnation point heat transfer is governed by the impingement jet flow while outside this region the impingement vortex is of major importance. Patterson and Ahrens[Citation43] and Ahrens et al.[Citation44] studied the process both experimentally and by performing CFD calculations. The experiments were performed with three different prototype combustors; aerodynamic valve, pressurized combustion chamber and a multifunctional system. The results showed that the heat flux could be increased by 2.4 times compared to a standard impingement system.
Multi-cylinder dryer
The multi-cylinder dryer is the standard dryer for drying of all kinds of paper, newsprint, printing papers, linerboard, cardboard, and for the final drying of coated paper qualities. It is estimated that about 90% of the tonnage of papers produced are dried using the multi-cylinder design. This cast iron design was invented in the UK at the beginning of the 19th century when it was running very slow and heated by shoveling in coal on the one side and scraping out the ash on the other side. Typical data today are a cylinder 1.5–2.1 m in diameter (5, 6, and 7 feet), up to 10 m wide and rotating with speeds up to 2000 m/min. The number of steam-heated cylinders ranges between 20 and 170 arranged in different configurations. A modern machine which is to be started during 2019 at the Gruvön Billerud mill in Sweden is shown in . The machine is producing board and kraftliner and the dryer consists of 87 EvoDry steel drying cylinders.
The main advantages are the robust design resulting in small numbers of paper web breakages and thus a high productivity, flexibility for different paper qualities and that it is heated with low-pressure steam from the back-pressure turbine at the mill. Some disadvantages being relatively low drying rates resulting in a very long dryer section, large amounts of metal to be heated and cooled resulting in slow capacity or quality changes and that the secondary heat is produced at a dew point of only 50–60 °C. Despite this the design is still the favored technology for new machines, and it is not surprising that the majority of scientific papers from this period deals with this design.
Cylinder design
The steam condenses on the inside of the cast iron cylinder and at machine speeds of 2000 m/min the centrifugal force on the condensate will be up 150 times gravity resulting in a very stable and laminar condensate layer. This laminar layer will drastically reduce the heat flux to the paper and in spite of this importance, the number of papers dealing with this problem is not large. Stenström et al.[Citation45] studied the behavior of the condensate film in a laboratory cylinder with a diameter of 0.283 m that could be equipped with spoiler bars, a technology used to favor condensate movement and increased heat transfer coefficients. The water flow for a centrifugal force of 60 times gravity and a water depth of 2 mm is shown in .
Figure 6. Water flow with for a water depth of 2 mm and a centrifugal force of 60 times gravity.[Citation46]
![Figure 6. Water flow with for a water depth of 2 mm and a centrifugal force of 60 times gravity.[Citation46]](/cms/asset/313c4acf-b771-4737-9e62-65b5f78afd93/ldrt_a_1596949_f0006_c.jpg)
One conclusion from the project was to equip the cylinders with axial flanges that can conduct the heat through the condensate layer. Shin et al.[Citation47] developed a multi-port design essentially a double-walled cylinder with several flow channels and presented a heat transfer coefficient of 16 kW/m2°C for the condensate layer. This figure is around 10 times higher than for a traditional design using spoiler bars.
Heat conduction through the cylinder shell with a thickness of 25–32 mm is straightforward while the energy transfer from the outer side of the cylinder to the paper is more complex and depends on a number of variables such as the contact pressure, the moisture content and the composition of the paper and the surface characteristics. This resistance is normally modeled with a contact heat transfer coefficient often being a function of the paper moisture content. Milosavljevic et al.[Citation46] performed measurements in a pilot test rig and at a surface temperature of 120 °C the contact heat transfer coefficient was 1600 W/m2°C at a moisture content of 50%. Timofeev et al.[Citation48] performed computer simulations of a paper dryer using the contact heat transfer coefficient as the fitting parameter and found good agreement with the experimental data.[Citation46] Increasing the fabric tension from 2 to 6 kN/m increased the contact coefficient by 12%. Cameron and Tripathi[Citation49] also performed measurements in a laboratory dryer giving a contact heat transfer coefficient of around 800 W/m2°C in the constant rate period while for a dry paper it was only around 100 W/m2°C. Noboa and Seyed-Yagoobi[Citation50] performed measurements for uncoated and coated paper qualities. The increased contact conductance for a coated paper was explained by the improved conformation to the heated surface. Berg and Berg[Citation51] performed detailed calculations of the heat transfer between the heated surface and the paper and came to the conclusion that control of the boundary layer close to the cylinder is of importance for the contact coefficient.
The tasks for the fabric is to support the paper during the transport on and between the cylinders, achieve a good contact between the paper and the cylinder surface, aid ventilation in the pockets and drive the cylinders. The felt covers the paper during a large part of the drying process and acts as a resistance to mass transfer from the paper to the ventilation air. Smrtnik et al.[Citation52] measured this resistance using the cup method for eight different commercial felts resulting in mass transfer coefficients between 0.004 and 0.011 m/s. Felts are normally characterized with a permeability parameter and a good correlation was found between the mass transfer coefficients and the permeabilities. The measured data were used in a simulation program by Smrtnik et al.[Citation53–56] and showed that for a constant machine capacity the energy recovery could be increased from 43% to 73% for a fabric with a higher mass transport coefficient. The temperature of the fabric also influences the drying process, a parameter which can have potential for capacity increase in the paper dryer. Milosavljevic et al.[Citation57,Citation58] investigated the drying behavior of three felts with different of contact points and contact area in a laboratory simulator. The results showed that the number of contact points is more important than the contact area.
One recent development during the last years has been the introduction of steel instead of cast iron cylinders in the dryer, the EvoDry design from Voith is shown in .
The advantage with steel is the higher tensile strength resulting in a reduction of wall thickness, typically from 31 to 20 mm for a 1.8 m cylinder. Also the material has a higher thermal conductivity, both of these things resulting in an improved heat transfer reducing the number of drying cylinders.
Heat and mass transfer in the paper
Understanding the internal heat and mass transport phenomena are of course of utmost importance for calculations of the drying rate, the paper shrinkage and the development of paper quality parameters. Large efforts are thus spent on research in this area. Ramarao et al. presented a very extensive summary of moisture diffusion in paper materials.[Citation59] Permeabilities are important for pressure-driven transport during high intensity processes in paper, Lavrykov et al.[Citation60] used X-ray microtomography to determine permeabilities in the plane and in the thickness direction. Thermal conductivities and specific heats were measured for a large range of copy papers with different densities and ash contents by Lavrykov and Ramarao.[Citation61]
Baggerud developed a model for the heat and mass transfer phenomena during drying of paper which included both diffusive and convective fluxes and shrinkage of the paper.[Citation62–64] The calculations were compared with good agreement with experimental data, see .
Figure 8. Comparison of modelled and experimental paper temperatures.[Citation64]
![Figure 8. Comparison of modelled and experimental paper temperatures.[Citation64]](/cms/asset/be72daed-8230-4392-9153-bfb2fb823b6a/ldrt_a_1596949_f0008_b.jpg)
One interesting result was the description of the paper shrinkage during the drying process using triangular diagrams[Citation65–67] which has been applied also to other drying areas. The real drying process can be compared with no and ideal shrinkage represented by solid lines, one example is shown in .
Figure 9. Volume fractions during paper drying and shrinkage shown in triangular diagrams[Citation68]
![Figure 9. Volume fractions during paper drying and shrinkage shown in triangular diagrams[Citation68]](/cms/asset/1d524ec2-bdfb-4f2d-bb6d-ed98b1008b7e/ldrt_a_1596949_f0009_b.jpg)
The analogy between heat and mass transfer is needed to couple the external convective phenomena. Nilsson[Citation68] and Berg[Citation69] compared models at different dew points. Lu and Shen[Citation70] developed a model including convective and capillary transport of both liquid and gas in the paper with good agreement to experimental data. A similar model was developed by Hoshi et al.[Citation71] but did not include a comparison with experimental data.
Askfelt et al.,[Citation72] Alexandersson et al.[Citation73] and Alexandersson and Ristinmaa[Citation74] developed a very extensive model based on mixture theory for transport in cellulose networks. The model was used to study temperature and moisture changes during heating of wet paperboard as well as moisture and temperature dynamics for paperboard rolls. It is expected that more results will appear in the near future for different transport processes in paper.
Experimental data for the moisture distribution during drying of paper are of high importance for model development and fitting of adequate transport parameters. Magnetic resonance imaging (MRI) offers one possibility to acquire such data.[Citation75–79] Harding et al.[Citation76] achieved a resolution of 15 μm which was sufficient to follow the moisture gradients in a cardboard during drying. Leisen et al.[Citation78,Citation79] studied in moisture transport during drying of handsheets and paperboard using a 2 D MRI set-up. Both in-plane and through plane moisture transport were studied.
Dryer simulation models
Simulation models for the dryers are important tools in order to design and optimize the multi-cylinder dryer. Nissan and Hansen[Citation80] were among the first and they divided the cylinder into four phases which were repeated for each cylinder in the dryer. Today detailed calculations can be performed as the paper moves through the dryer and several computing tools have been developed. Karlsson et al.[Citation81–87] developed a dynamic model which could simulate processes such as capacity and paper quality changes and incorporated in the control algorithm for the dryer section. In this way, the time required for a quality change can be significantly reduced and the productivity on the machine increased. Nilsson studied data for four industrial paper dryers and developed a model for the drying process.[Citation88,Citation89] One interesting result was the introduction of two dimensionless Nilsson numbers:(1)
(1)
(2)
(2)
which compare the heat to the mass diffusivities for the external and internal processes.
Motta Lima et al.[Citation90–92] performed both experimental and modeling work using the concept of generalized drying rate curves. Initially, the paper[Citation90,Citation91] was not supported on the heated surface but later a dryer felt was also added.[Citation92] Good agreement was found between the experimental and modeled data. Motta Lima et al.[Citation93] used Nissan and Hansen’s model[Citation80]an industrial paper dryer, some deviations were noticed such as that the average paper temperature reached above 120 °C in the model.
Coumans and Ramakers[Citation94] calculated the internal temperature, moisture, and pressure gradients in a drying paper sheet. The calculated internal gas pressure reached 26 kPa over atmospheric pressure which could lead to delamination of the sheet. Gardner[Citation95] developed a model without taking internal transport phenomena into account which showed good agreement between measured and calculated sheet average moisture content. Ghodbanan et al.[Citation96] developed a model for a dryer on a corrugating paper machine. No internal transport was included and the model estimated the TAPPI drying rate with about an error of 2%. Reardon et al.[Citation97] presented the outlines of a model which was used to study two newsprint dryers. Sadeghi and Douglas[Citation98] included internal transport in a model that was validated against 12 industrial machines ranging from tissue to linerboard. The average error between the measured and calculated sheet temperatures was only +1 °C. However, no details were given about how the experimental average sheet temperature was measured. More details about the model are given by Sadeghi.[Citation99]
Perré et al.[Citation100] developed an extensive model for the multi-cylinder dryer including infrared dryers but no comparison with industrial data was presented. Paltakari[Citation101] studied internal temperature and moisture profiles in an experimental set-up for both single- and double-sided configurations. More details can be found in[Citation102]. Kong et al.[Citation103] developed a model for multi-cylinder dryer which included also the complex condensate system and heat recovery from the humid air. Good predictions were presented for both drying rate and the energy use for the dryer.
Tissue and impingement drying
Tissue
Tissue is dried on one single large drying cylinder, 5–7 m in diameter, often called a Yankee cylinder. The origin of the name Yankee is said to come from a Dutchman called Yonke who was working with the technology and when this technology was transferred to the US the name became Yankee.[Citation104] Energy for the drying process is transferred from the inside by condensing steam and on the outside by blowing heated air or combustion gases at high velocities against the paper surface. This completes the drying process during transport 2/3 of a revolution on the cylinder. Apart from developing higher temperatures and impingement velocities, this technology has not changed drastically. Nilsson et al.[Citation105] studied the consequences of a higher dew point in the hood and thus improved possibilities for energy recovery and Ottosson et al.[Citation106] developed a mathematical model for the process with good agreement between experimental and calculated final moisture contents.
Impingement drying
Impingement drying is used in very many different paper drying process; tissue drying, drying of coated paper qualities, and in multi-cylinder dryers for increased drying capacity. One recent vertical design from Valmet is shown in .
The local Nusselt number and thus the local heat transfer coefficient are of high importance for the impingement design and several authors have studied these phenomena[Citation107–111]. Shi et al.[Citation107] and Milosavljevic and Heikkilä[Citation108] obtained the Nusselt numbers and the heat transfer coefficients by computational fluid dynamic calculations while Heikkilä et al.[Citation109–111] used experimental techniques to obtain their data. One advantage with the impingement dryer over the multi-cylinder dryer is the possibility of relatively rapid machine changes provided that the control loops are adequately equipped and properly tuned. Kokko et al.[Citation112] studied a multivariable control and found faster response for the moisture content of the paper especially if feedforward control from the press section was used. Durán-Olivencia et al.[Citation113] developed a multifluid model for drying applications, essentially based on the previous work by Asencio.[Citation114] The model was tested with good agreement against impingement drying data.
Several advantages using the impingement dryer are mentioned by the industry[Citation115–118] such as that the vertical design increases the capacity for a fixed floor area, quick response enables faster grade changes and possibility to balance evaporation from both sides of the paper for a single-felted design.
Keränen[Citation119] studied impingement drying for a paper in contact with a hot surface and covered by a fabric. Both drying results and paper quality parameters were evaluated. Large increases in drying rates were recorded for the combined impingement and cylinder drying case. Hashemi et al.[Citation120,Citation121] studied combinations of impingement and multi-cylinder drying and one important conclusion from the study was that a good validated dryer simulator is important for the future development of the processes. Paprican in Canada has developed a new drying technique based on using large diameter cylinders covered with a high capacity impingement hood. The process is similar to a Yankee design and was called the PapridryTM process.[Citation122–124] Clearly, the capacity could be increased by replacing a number of multi-cylinders with this design and especially for low-basis weights such as newsprint the design would be attractive but to the authors knowledge no industrial machines have been installed. Liewkongsataporn et al.[Citation125] studied impingement drying in combination with a pulsating jet and achieved interesting results with up to doubled drying rates compared without the jet. The main drawback for the design is that the confinement plate has to be located a few centimeters from the paper. Vieira and Rocha[Citation126] and Motta Lima et al.[Citation127] performed convective drying experiments for recycled paper and filter paper.
TAD—through air drying
The principle for the TAD-process is to draw heated air through the sheet resulting in high heat and mass transfer coefficients and also high drying rates. This results in a product that has improved softness and a higher water absorbency. The drying process starts from a high moisture content of around 70% resulting in the use of large amounts of energy for evaporation. Also at high moisture content the pressure drop through the paper and the fabric is significant resulting in high electrical energy costs for the fans. The process is operated on one or two large diameter cylinders with a perforated honeycomb structure, the design from Valmet is shown in and . In most cases, it is followed by a Yankee cylinder for creping the product.
Figure 11. TAD Advantage Thru-Air®technology unit from Valmet with two TAD cylinders followed by one Yankee cylinder (photo courtesy of Valmet).
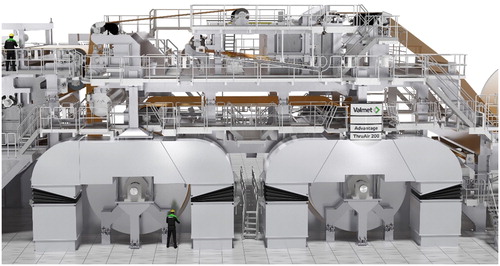
Most of the TAD plants have been installed in the US and Canada and today about 10 plants are in operation in Europe. Because of the high energy costs for the process a hybrid technology is developed where a structure is created using the traditional Yankee process producing a paper with some of the advantageous properties of the TAD-paper.
Weineisen et al.[Citation128–134] performed both experimental and modeling work related to the TAD process. Experimental work at industrial conditions for a tissue paper of 20 g/m2 with a drying time less than one second is challenging.[Citation132] One result from the study was that the exiting air was saturated at the adiabatic saturation temperature for the basis weights 30 and 40 g/m2 but not for the lowest basis weight studied 20 g/m2 which was explained by-pass effects for the lowest basis weight. A model based on a distribution of pore sizes showed good agreement with these experimental data.[Citation133] The energy use was evaluated for different process alternatives showing a thermal energy demand of around 4800 kJ/kg of water evaporated.
Ramaswamy et al.[Citation135–141] also studied the TAD process by performing experiments and developing models for the flow and the heat and mass transfer. The experiments were performed at air temperatures below 35 °C but the overall drying behavior was comparable with the results presented by Weineisen et al..[Citation132] One interesting result from the experiments was the acquisition of data for the local variation of temperature and velocity resulting in local non-uniformity of moisture.[Citation138] Modeling work used a characteristic dimension for the Forchheimer equation to describe the flow through the paper during drying.[Citation141]
Tysén et al.[Citation142–144] studied TAD in an equipment where sheets 9 × 9 cm were dried using air at room temperature. The drying process and the temperatures were followed using an infrared camera and thermocouples. Variation in local grammage has a large influence on the local air velocities and the surface temperature was used as an indicator for the non-uniformity in drying.[Citation143] The process was also studied by adding infrared radiation to the sheet resulting in reductions in drying time between 10% and 45% depending on the sheet basis weight and radiation power.
McGill University has also been active in developing the TAD technology.[Citation145–150] Several studies were focused on the variation in grammage and formation that will lead to uneven flow through the sheet, uneven drying and poor quality parameters. To quantify this a drying nonuniformity index was developed and measured for different parameters.[Citation147,Citation149] The moisture content for TAD drying of a 6-ply 180 g/m2 sheet was studied by interrupting the drying and separating the sheets.[Citation148] Sack paper with a basis weight of 100 g/m2 was dried in a TAD experimental rig but with a high pressure drop of 8 kPa.[Citation150] One conclusion from these studies was that in order to implement the TAD process and avoid high-pressure drops for drying of heavier grades would be to use the cylinder dryer for the first part of the drying and the TAD-process for the final stages of drying.[Citation145,Citation146] Etemoglu et al.[Citation151] developed a model for drying of paper with good agreement for TAD and impingement drying.
Infrared drying
Electrically and gas-heated infrared dryers are used for drying of coated papers, profiling of the paper web and for increased capacity in limited dryers. The advantages compared to the multi-cylinder design are high heat fluxes, absorption of radiation inside the wet web and profiling possibility, while disadvantages are the use of more expensive energy sources (electricity and gas) and a lower energy efficiency for the units. One gas-heated design is shown in .
Seyed-Yagoobi and Wirtz[Citation152,Citation153] and Seyed-Yagoobi et al.[Citation154,Citation155] performed experiments and developed a drying model for a gas heated unit. Pilot machine data were well predicted using the theoretical model. Seyed-Yagoobi and Husain[Citation156] further studied the absorption of radiation from a gas-heated unit and came to the conclusion that more data are needed for the optical properties of different papers. Seyed-Yagoobi and Noboa[Citation157] used a model to investigate the optimum location of two opposing gas-heated emitters, the conclusion was that for this specific case the best location for maximum speed increase was at the end of the multi-cylinder dryer. The electrical and gas-heated emitters have different spectral characteristics which will influence absorption and transport phenomena, Seyed-Yagoobi and Noboa.[Citation158] In this case, the heat flux from the electrical emitter was significantly higher making a comparison difficult.
Energy use
Energy use for drying of paper is a very important issue due to the large amounts used, increasing energy costs and the drive to change from fossil to renewable resources. In a country like Sweden with a large pulp and paper sector, the energy used for drying of these products is estimated to be about 20% of the total industrial energy use. The multi-cylinder design dominates for drying of paper and the main part of the supplied energy comes from low-pressure steam. The low-pressure steam is produced by burning lignin and hemicelluloses in the recovery boiler followed by electricity production in the back-pressure turbine. The specific energy use for a modern energy optimized design is around 3000 kJ/kg evaporated water and this figure cannot be lowered very much with existing technology. Instead improved energy efficiency should be aiming at increased mechanical dewatering in the press section and increased waste heat recovery from the exhaust moist air. As was mentioned earlier, heated shoe presses such as impulse drying, has however not been a way forward for increased dewatering due to paper quality issues. For a modern machine 60–70% percent of the supplied energy is recovered from the wet exhaust air and potential exist for further recovery, however at low temperatures below 50 °C. Possibly part of it can be delivered to nearby district heating networks. Increasing the solid content in sizing solutions will also contribute to a lower energy use for the total paper machine.
Heat recovery from the humid exhaust air to heat the ingoing air, the process water and the circulation water system was studied by Sivill et al.[Citation159] using a simulation program. The results were compared with three industrial machines. By increasing the exhaust air humidity the heat recovery could be increased by 300–1000 kW. Pettersson and Söderman[Citation160] also used mathematical methods to study how variations in the parameters could be accounted for to arrive at an optimal heat recovery system. Roonprasang[Citation161] developed a model for the multi-cylinder dryer with the goal to reduce the energy use but no direct industrial results were presented.
The energy use for the drying section in Chinese paper machine has been studied in a number of papers.[Citation162–167] Exergy analysis was use to increase waste heat recovery reducing the energy use by 4.6%,[Citation162] optimizing the process parameters for a newsprint machine reduced steam consumption by 8%,[Citation163] a detailed static model of the paper dryer showed that the air supply temperature could be reduced from 112 to 100 °C resulting in a specific heat reduction by 3.3%.[Citation164] Chen et al.[Citation165–167] performed a similar detailed analysis of the dryer section showing that the total steam consumption for one machine could be reduced from 1.82 to 1.50 ton of steam per ton of water evaporated. One reason for this rather large reduction is the high initial steam consumption indicating a nonenergy optimized paper dryer operation. By modifying a hood from semi-closed to closed, Yin et al.[Citation167] showed that the steam consumption could be reduced by 12.9% and the power consumption by 14.2% for a specific dryer.
Energy integration between different inlet and outlet air streams in the dryer and other streams at the mill is important and Lindell developed a modeling tool in order to study this with wet exhaust air from the hood, gas-fired hoods used for drying of tissue and impingement drying.[Citation168–171] Syngas from a gasification plant can be connected directly to the hood of a Yankee dryer or first used for electricity production in a gas turbine and then the flue gases fed to the Yankee dryer.[Citation170] A system using gas-heated impingement drying in combination with the traditional multicylinder dryer has higher energy costs compared with only using a traditional multicylinder design due to the higher cost for the natural gas compared with bark for the steam boilers.[Citation171]
Exhaust from impingement dryers offers good opportunities for energy integration and energy saving measures. Hytönen and Puumalainen[Citation172] proposed using an energy balance simulator for such studies and Di Marco et al.[Citation173] used detailed mass- and energy balances showing that energy savings of 4.5% should be possible. Laurijssen et al.[Citation174] showed that by increasing the dew point, increasing the process water temperature to 55 °C and increasing the starch solid content from 8% to 30%, energy savings of 32% could be accomplished. Efficient control is also very important for a good energy efficiency, startup times and quality changes should be minimized and process changes controlled. Bhutani et al.[Citation175] developed an energy fingerprint solution indicating that steam savings of 10–15% should be possible.
Thermodynamic analysis has also been used to analyze and optimize the paper drying processes with several advantages over traditional mass- and energy balances. Dincer and Sahin[Citation176] suggested using exergy efficiency to analyze drying processes. Zvolinschi et al.[Citation177] and Koper et al.[Citation178] used entropy production for optimizing the paper dryer and one conclusion was that the inlet air humidity should be increased to reduce entropy production[Citation177].
Conclusions and future work
The multicylinder design has not undergone drastic changes during these 20 years, perhaps use of impingement dryers for increased capacity and control of paper quality and the new steel cylinders are two of the most important developments. The scientific activity in this area was much higher during the first half of this period, the number of papers reviewed here per year is shown in .
One explanation for this decline can be that several research groups in Sweden, Canada, and the US are not active any more, another that the introduction of new technological developments has been limited reducing the industrial interest for research in this area.
However, several topics should need attention. The fabric is often neglected from a drying point of view. The temperature of the fabric also influences the drying process and impingement of the fabric has a significant effect on the drying behavior. Transfer of heat between the cylinder and the paper is normally modeled using a contact coefficient, a concept that should be replaced by a more physically based description. Despite numerous attempts to model the internal transport phenomena, more work is needed to couple these phenomena to paper shrinkage and quality parameters. Magnetic resonance imaging offers one possibility to measure moisture gradients at high resolution in time and space at realistic drying rates.
The biggest issue for the paper producing companies is to achieve the right quality and an even quality across the width and the length of the paper roll. Overdrying on the edges tends and shrinkage in the free draws are difficult to avoid. Machine-glazed paper (MG-paper) is produced using a multicylinder dryer in combination with a large Yankee-cylinder in the middle of the dryer. Previously, the development was towards replacing the Yankee-cylinder with a calendar design after the dryer but during the last years several new MG-machines have been built in Europe. Incorporating new materials such as microfibrillar cellulose in the stock could be a challenge for the existing paper dryer.
For an integrated mill, the multicylinder dryer is mainly based on renewable energy from the recovery boiler but impingement and Yankee dryers sometimes use large amounts of natural gas or liquefied petroleum gas. In this case, the companies are looking for biogas as a replacement. Old machines are not designed for the same energy efficiency and large improvements can often be achieved when analyzing these units.
An interesting collaboration between industry and academia has recently been established by Yagoobi in the US,[Citation179] Center for Advanced Research in Drying (CARD). The center is coordinated from Worcester Polytechnic Institute and University of Illinois and it is expected that interesting results will emerge from this collaboration.
Acknowledgments
The companies Andritz, Voith and Valmet are greatly acknowledged for providing the pictures of the industrial units.
References
- Paper Industry—Statistics & Facts. Retrieved February 25 2019 from www.statista.com/topics/1701/paper-industry/
- Mujumdar, A. S. Recent Developments in Paper Drying. Appita Journal 1982, 19, 72–76.
- Wedel, G. L. Progress in paper drying, 86th PAPTAC Annual Meeting, 2000. B13–B17.
- Pikulik, I.; Poirier, N. New developments in paper and board drying, www.researchgate.net/publication/229049928 (accessed Aug 30, 2018), first published 2003.
- Papermaking Science and Technology, 2nd ed.; Book 9, Papermaking Part 2 Drying, Editor Markku Karlsson, Helsinki: Paperi ja Puu Oy, 2009.
- Mujumdar, A. S. ed., Handbook of Industrial Drying, 3rd ed., Taylor and Francis: Boca Raton, 2007, 793–819.
- Strømmen, I.; Eikevik, T. M.; Alves-Filho, O.; Syverud, K. Heat pump drying of sulphate sulphite cellulose, Proceedings 14th International Drying Symposium (IDS 2004), Sao Paulo, Brazil, 2004, 1225–1232.
- Vieira, M. G. A.; Estrella, L.; Rocha, S. C. S. Energy Efficiency and Drying Kinetics of Recycled Paper Pulp. Drying Technology 2007, 25, 1639–1648. DOI: 10.1080/07373930701590806.
- Larsson, O.; Karlsson, I. Pulp Drying Applications, Papermaking Science and Technology, Book 6A, Chemical Pulping, Chapter 10, 666–685, Gullichsen, J., Fogelholm, C-J, Helsinki: Paperi ja Puu Oy, 2000.
- Retulainen, J. Key Development Phases of Condebelt: Long Journey from Idea to Commercial Product. Drying Technol. 2001, 19, 2451–2467. DOI: 10.1081/DRT-100108248.
- Retulainen, J. Key Development Phases of Condebelt: Long Journey from Idea to Commercial Product. Proceedings 12th International Drying Symposium (IDS 2000), Noordwijkerhout, the Netherlands, 2000, paper no. 295.
- Timofeev, O. N.; Ilomäki, J.; Kuusela, J. Effect of Process Parameters on Paper Temperature in Condebelt Drying. Proceedings 14th International Drying Symposium (IDS 2004), Sao Paulo, Brazil, 2004, 1327–1334.
- Talja, R.; Karlsson, M.; Malashenko, A. New Paper Drying Technologies – Present and Future. Presented at the 87th PAPTAC Annual Meeting, 2001, B229–B239.
- Private communication with Joseph Guadagno at the Andritz Paper Machinery division in Lachine Canada.
- Lang, I.; Smith, R.; Tawfik, R.; Poirier, N. A. High Temperature Gas-Heated Drying Cylinders: Potential Impact on Drying Rate and Product Quality. Pulp and Paper Canada 2001, 102, 34–39.
- Nilsson, J. Heat transfer mechanisms in high temperature pressing of paper, Licentiate thesis, Lund university, Lund, Sweden, 2001.
- Aguilar Ribeiro, H. Study of the rheology of deformable porous media: application to paper production, PhD thesis, University of Porto, Porto, Portugal, 2006.
- Lucisano, M. F. C. On the Mechanism of Heat Transfer with Phase Change During Impulse Pressing of Paper. Licentiate thesis, KTH Royal Institute of Technology, Stockholm, Sweden, 2000.
- Lucisano, M. F. C. On Heat and Paper: From Hot Pressing to Impulse Technology. PhD thesis, KTH Royal Institute of Technology, Stockholm, Sweden, 2002.
- Crouse, J. W.; Woo, Y. D.; Sprague, C. H. Delamination – a Stumbling Block to Implementing Impulse Drying Technology for Linerboard. Tappi J. 1989, 72, 211–215.
- Nilsson, J.; Stenström, S. Modelling of Heat Transfer in Hot Pressing and Impulse Drying of Paper. Drying Technol. 2001, 19, 2469–2485. DOI: 10.1081/DRT-100108249.
- Nilsson, J.; Stenström, S. Modelling of Heat Transfer in Hot Pressing and Impulse Drying of Paper. Proceedings 12th International Drying Symposium (IDS 2000), Noordwijkerhout, the Netherlands, 2000, paper no. 305.
- Krook, R.; Stenström, S. Temperature Gradients and Heat Flux Measurements in Hot Pressing of Paper. Experimental Heat Transfer 1998, 11, 221–240. DOI: 10.1080/08916159808946563.
- Larsson, H.; Orloff, D. I. Lab-scale Impulse Drying Experiments with Extension to Higher Impulse. Proceedings 12th International Drying Symposium (IDS 2000), Noordwijkerhout, the Netherlands, 2000, paper no. 304.
- Larsson, H.; Orloff, D. I. Lab-Scale Impulse Drying Experiments with Extension to Higher Impulse. Dry. Technol. 2001, 19, 2549–2558.
- Larsson, H.; Nilsson, J.; Stenström, S. Experiments in a Pilot-Scale Impulse Unit – Heat Transfer and Water Removal Rates. Nordic Pulp Paper Res. J. 2001, 16, 156–161. DOI: 10.3183/npprj-2001-16-02-p156-161.
- Larsson, H.; Stenström, S. Experiments in a Pilot-Scale Impulse Unit – Energy Efficiencies. Nordic Pulp Paper Res. J. 2001, 16, 162–167. DOI: 10.3183/npprj-2001-16-02-p162-167.
- Martinez, D. M.; Drotz, M.; Lai, R.; Martin, A. R. Dryness and Physical Properties of Paper Webs in Laboratory-scale Impulse Pressing. Proceedings 12th International Drying Symposium (IDS 2000), Noordwijkerhout, the Netherlands, 2000, paper no. 409.
- Martinez, D. M.; Drotz, M.; Lai, R.; Martin, A. R. Dryness and Physical Properties of Paper Webs in Laboratory-Scale Impulse Pressing. Dry. Technol. 2001, 19, 2435–2450. DOI: 10.1081/DRT-100108247.
- Riepen, M. An Inside View on Impulse Drying Phenomena by Modelling. Proceedings 12th International Drying Symposium (IDS 2000), Noordwijkerhout, the Netherlands, 2000, paper no. 113.
- Aguilar Ribeiro, H.; Costa, C. A. V. A Proposed Model in the Analysis of Impulse Drying of Paper. Int. Paper Phys. Conf. 2003, 305–309.
- Aguilar Ribeiro, H.; Costa, C. A. V. A Mechanical Model for Felt in Impulse Drying: A Cellular Materials Approach. I. Model Development and Simulation. Fibers Polym. 2008, 9, 55–62. DOI: 10.1007/s12221-008-0009-1.
- Aguilar Ribeiro, H.; Costa, C. A. V. A Mechanical Model for Felt in Impulse Drying: A Cellular Materials Approach. II. Experimental Validation. Fibers Polym. 2008, 9, 63–70. DOI: 10.1007/s12221-008-0010-8.
- Martin, A. R.; Drotz, M.; Talja, R.; Kaijaluoto, S.; Puumalainen, T. Energy Analysis of Impulse Technology: Research-Scale Experimental Papermaking Trials and Simulations of Industrial Applications. Appl. Thermal Eng. 2004, 24, 2411–2425. DOI: 10.1016/j.applthermaleng.2004.03.002.
- Nilsson, F.; Norman, B. Impulse Drying with Thin Metal Bands. Proceedings 12th International Drying Symposium (IDS 2000), Noordwijkerhout, the Netherlands, 2000, paper no. 255.
- Nilsson, F.; Norman, B. Impulse Drying Using a Thin Heated Metal Band with Backing Insulation. Part 1: Dewatering, Delamination and Temperature Events. Nordic Pulp Paper Res. J. 2002, 17, 326–332. DOI: 10.3183/npprj-2002-17-03-p326-332.
- Nilsson, F.; Norman, B. Impulse Drying Using a Thin Heated Metal Band with Backing Insulation. Part 2: The Influence of Thermal Energy on Dewatering and Delamination. Nordic Pulp Paper Res. J. 2002, 17, 333–339. DOI: 10.3183/npprj-2002-17-03-p333-339.
- Stenström, S. Drying of Biofuels from the Forest – a Review. Dry. Technol. 2017, 35, 1167–1181. DOI: 10.1080/07373937.2016.1258571.
- McCall, J. M.; Douglas, W. J. M. Enhancement of Properties of Diverse Grades of Paper by Superheated Steam Drying. Proceedings 14th International Drying Symposium (IDS 2004), Sao Paulo, Brazil, 2004, 1255–1262.
- Ahrens, F. W.; Habeger, C. C. Use of New Applicator Design Ideas to Improve Uniformity of Paper Drying Via Microwave Energy. Proceedings 12th International Drying Symposium (IDS 2000), Noordwijkerhout, the Netherlands, 2000, paper no. 298.
- Ahrens, F. W.; Habeger, C. C. Use of New Applicator Design Ideas to Improve Uniformity of Paper Drying via Microwave Energy. Dry. Technol. 2001, 19, 2531–2548. DOI: 10.1081/DRT-100108252.
- Wu, Z. H.; Mujumdar, A. S.; Liu, X. D.; Yang, L. Pulse Combustion Impingement to Enhance Paper Drying. Proceedings 15th International Drying Symposium (IDS 2006), Budapest, Hungary, 2006, 971–978.
- Patterson, T.; Ahrens, F. Development of Pulsed Air Drying (PAD) – a New Air Impingement Technology. Paper Technol. 2005, 46, 23–30.
- Ahrens, F.; Liewkongsataporn, W.; Patterson, T. Optimizing the Benefits of Pulse Combustion Impingement for Paper Drying. Proceedings 17th International Drying Symposium (IDS 2010), Magdeburg, Germany, 2010, 1317–1324.
- Stenström, S.; Ingvarsson, D.; Sundblom, T.; Älmqvist, A.; Jarl, M.; Lucisano, M. F. C. Condensate Heat transfer in Paper Drying Cylinders at High Centrifugal Forces. Proceedings 15th International Drying Symposium (IDS 2006), Budapest, Hungary, 2006, 1000–1006.
- Shin, J. H.; Hwang, K. S.; Jang, S. P.; Lee, K. W. Flow and Thermal Characteristics of Condensing Steam in a Single Horizontal Mini-Channel of a Multiport Cylinder Dryer. Dry. Technol. 2010, 29, 47–54. DOI: 10.1080/07373937.2010.482688.
- Milosavljevic, N.; Timofeev, O.; Rajala, P. Evaluation of Contact Heat Transfer Coefficient in Cylinder Drying: An Experimental Study. Proceedings 15th International Drying Symposium (IDS 2006), Budapest, Hungary, 2006, 946–950.
- Timofeev, O.; Milosavljevic, N.; Rajala, P. Evaluation of Contact Heat Transfer Coefficient in Cylinder Drying: A Simulation Study. Proceedings 15th International Drying Symposium (IDS 2006), Budapest, Hungary, 2006, 1007–1011.
- Cameron, J.; Tripathi, P. Measurement of Paper-Shell Contact Coefficients. Proceedings 12th International Drying Symposium (IDS 2000), Noordwijkerhout, the Netherlands, 2000, paper no. 293.
- Noboa, H. L.; Seyed-Yagoobi, J. Thermal Contact Conductance of a Coated Paper/Metal Interface. Drying Technology 2001, 19, 1125–1135. DOI: 10.1081/DRT-100104809.
- Berg, C.-G.; Berg, N.-C. A Study of the Contact Coefficient When Drying Paper, Proceedings 14th International Drying Symposium (IDS 2004), São Paulo, Brazil, 2004, 1209–1216.
- Smrtnik, S.; Nordström, S.; Hansson, R.; Stenström, S. Mass Transport Resistance of Paper Dryer Fabrics. Proceedings 15th International Drying Symposium (IDS 2006), Budapest, Hungary, 2006, 1034–1041.
- Smrtnik, S.; Karlsson, M.; Holmberg, P.; Stenström, S. The Importance of the Dryer Fabric for Cylinder Hood Humidity, Capacity and Energy Recovery. Proceedings 15th International Drying Symposium (IDS 2006), Budapest, Hungary, 2006, 957–962.
- Smrtnik, S.; Stenström, S. Modelling of Mass and Heat Transport in Dryer Fabric Structures. Part 1. Theoretical Model. Nordic Pulp and Paper Research Journal 2009, 24, 278–287. DOI: 10.3183/npprj-2009-24-03-p278-287.
- Smrtnik, S.; Stenström, S. Modelling of Mass and Heat Transport in Dryer Fabric Structures. Part 2. Model Validation and Industrial Implementation. Nordic Pulp and Paper Research Journal 2009, 24, 288–297. DOI: 10.3183/npprj-2009-24-03-p288-297.
- Smrtnik, S. Mass and Heat Transport in Dryer Fabrics, PhD thesis, Lund University, Lund, Sweden, 2009.
- Milosavljevic, N.; Heikkilä, P.; Ojanen, M.; Saari, J. Influence of Fabric Structure on the Drying Rate and Cylinder-Paper Contact Heat Transfer Coefficient, Proceedings 12th International Drying Symposium (IDS 2000), Noordwijkerhout, the Netherlands, 2000, paper no. 411.
- Milosavljevic, N.; Ojanen, M. New Aspects of Fabric Selection for Improved Drying and Runnability. Paper Technology 2004, 45, 47–51.
- Ramarao, B. V.; Massoquete, A.; Lavrykov, S.; Ramaswamy, S. Moisture Diffusion inside Paper Materials in the Hygroscopic Range and Characteristics of Diffusivity Parameters. Dry. Technol. 2003, 21, 2007–2056. DOI: 10.1081/DRT-120027044.
- Lavrykov, S.; Singh, S. K.; Ramarao, B. V.; Ramaswamy, S.; Pande, H. Analysis of the Permeability Tensor and the Correlating Length of Heterogeneities in Paper Using X-Ray Microtomography. Dry. Technol. 2016, 34, 871–882. DOI: 10.1080/07373937.2015.1057837.
- Lavrykov, S.; Ramarao, B. V. Thermal Properties of Copy Paper Sheets. Dry. Technol. 2012, 30, 297–311. DOI: 10.1080/07373937.2011.638148.
- Baggerud, E. Modelling of Mass and Heat Transport in Paper – Evaluation of Mechanisms and Shrinkage, PhD thesis, Lund University, Lund, Sweden, 2004.
- Baggerud, E. Modeling of Moisture Gradients for Convective Drying of Industrial Pulp Sheets. Proceedings 12th International Drying Symposium (IDS 2000), Noordwijkerhout, the Netherlands, 2000, paper no. 308.
- Baggerud, E.; Stenström, S. Diffusive Vapor and Liquid Transport during Convective Drying of Industrial Pulp Sheets. Proceedings of the Progress in Paper Physics Seminar, Finger Lakes/Syracuse, USA, 2002, 141–144.
- Baggerud, E.; Lindström, T.; Stenström, S. Measurement of Volume Fractions of Solid, Liquid and Gas in Kraft and CTMP Paper at Varying Moisture Content. Proceedings 2003 International Paper Physics Conference, Victoria, British Columbia, Canada, 2003, 157–163.
- Baggerud, E.; Stenström, S. Further Insight in the Web Consolidation Process. Part II. Triangular Phase Diagrams for Analysis of Paper Shrinkage. Nordic Pulp Paper Res. J. 2005, 20, 54–57. DOI: 10.3183/npprj-2005-20-01-p054-057.
- Baggerud, E.; Stenström, S. Further Insight in the Web Consolidation Process. Part III. Modelling of Paper Shrinkage. Nordic Pulp and Paper Research Journal 2005, 20, 58–63. DOI: 10.3183/npprj-2005-20-01-p058-063.
- Nilsson, L. On the Analogy Between Heat and Mass Transfer for High Dew Point Air. Proceedings 14th International Drying Symposium (IDS 2004), São Paulo, Brazil, 2004, 280–284.
- Berg, C.-G. A. Heat and Mass Transfer in Turbulent Drying Processes – Experimental and Theoretical Work. Dry. Technol. 2000, 18, 625–648. DOI: 10.1080/07373930008917729.
- Lu, T.; Shen, S. Q. Numerical and Experimental Investigation of Paper Drying: Heat and Mass Transfer with Phase Change in Porous Media. Appl. Thermal Eng. 2007, 27, 1248–1258. DOI: 10.1016/j.applthermaleng.2006.11.005.
- Hoshi, Y.; Kuno, H.; Takeshita, K.; Hashimoto, R.; Yanagi, K.; Yoshida, S. Prediction of Temperature and Moisture Content Profiles of Paper in a Drying Process. Heat Trans. Asian Res. 2001, 30, 77–94. DOI: 10.1002/1523-1496(200103)30:2<77::AID-HTJ1>3.0.CO;2-3.
- Askfelt, H.; Alexandersson, M.; Ristinmaa, M. Transient Transport of Heat, Mass and Momentum in Paperboard Including Dynamic Phase Change of Water. Int. J. Eng. Sci. 2016, 109, 54–72. DOI: 10.1016/j.ijengsci.2016.08.005.
- Alexandersson, M.; Askfelt, H.; Ristinmaa, M. Triphasic Model of Heat and Moisture Transport with Internal Mass Exchange in Paperboard. Transp. Porous Med. 2016, 112, 381–408. DOI: 10.1007/s11242-016-0651-9.
- Alexandersson, M.; Ristinmaa, M. Modelling Multiphase Transport in Deformable Cellulose Based Materials Exhibiting Internal Mass Exchange and Swelling. Int. J. Eng. Sci. 2018, 128, 101–126.
- Stenström, S.; Bonazzi, C.; Foucat, L. Magnetic Resonance Imaging for Moisture Profiles and Drying Curves. Modern Dry. Technol. 2009, 2, 91–142. Vol.
- Harding, S.; Wessman, D.; Stenström, S.; Kenne, L. Water Transport during the Drying of Cardboard Studied by NMR Imaging and Diffusion Techniques. Chem. Eng. Sci. 2001, 56, 5269–5281. DOI: 10.1016/S0009-2509(01)00197-X.
- Wessman, D.; Harding, S.; Stenström, S. Moisture Profiles During the Drying of Cardboard Measured by MRI. Proceedings 12th Int. Drying Symposium (IDS 2000), Noordwijkerhout, the Netherlands, 2000, paper no, 306.
- Leisen, J.; Hojjatie, B.; Coffin, D. W.; Beckham, H. W. In Plane Moisture Transport in Paper Detected by Magnetic Resonance Imaging. Drying Technology 2001, 19, 199–206. DOI: 10.1081/DRT-100001361.
- Leisen, J.; Hojjatie, B.; Coffin, D. W.; Lavrykov, S. A.; Ramarao, B. V.; Beckham, H. W. Through-Plane Diffusion of Moisture in Paper Detected by Magnetic Resonance Imaging. Ind. Eng. Chem. Res. 2002, 41, 6555–6565. DOI: 10.1021/ie0204686.
- Nissan, A. H.; Hansen, D. Heat and Mass Transfer Transients in Cylinder Drying: Part I. Unfelted Cylinders. AIChE J. 1960, 6, 606–611. DOI: 10.1002/aic.690060420.
- Karlsson, M. Static and Dynamic Modelling of the Drying Section of a Paper Machine, PhD thesis, Lund University, Lund, Sweden, 2005.
- Karlsson, M.; Stenström, S. Comparison of Two Modelling Approaches for a Multi-Cylinder Dryer. Proceedings 14th International Drying Symposium (IDS 2004), São Paulo, Brazil, 2004, 422–429.
- Karlsson, M.; Stenström, S.; Baggerud, E. Dynamic Simulation of the Steam Supply System for a Multi-Cylinder Dryer. Nordic Pulp Paper Res. J. 2002, 17, 66–70. DOI: 10.3183/npprj-2002-17-01-p066-070.
- Karlsson, M.; Slätteke, O.; Wittenmark, B.; Stenström, S. Reducing Moisture Transients in the Paper Machine Drying Section with the Midranging Control Technique. Nordic Pulp Paper Res. J. 2005, 20, 150–155. DOI: 10.3183/npprj-2005-20-02-p150-155.
- Karlsson, M.; Stenström, S. Static and Dynamic Modeling of Cardboard Drying Part 1: Theoretical Model. Dry. Technol. 2005, 23, 143–163. DOI: 10.1081/DRT-200047954.
- Karlsson, M.; Stenström, S. Static and Dynamic Modeling of Cardboard Drying Part 2: Simulations and Experimental Results. Dry. Technol. 2005, 23, 165–186. DOI: 10.1081/DRT-200047951.
- Karlsson, M.; Slätteke, O.; Hägglund, T.; Stenstrom, S. Feedforward Control in the Paper Machine Drying Section. Proceedings American Control Conference, Minneapolis, USA, 2006.
- Nilsson, L. Heat and Mass Transfer in Multicylinder Drying Part I. Anal. Mach. Data, Chem. Eng. Process. 2004, 43, 1547–1553. DOI: 10.1016/j.cep.2004.03.003.
- Nilsson, L. Heat and Mass Transfer in Multicylinder Drying Part II. Anal. Internal External Transp. Resistances, Chem. Eng. Process. 2004, 43, 1555–1560. DOI: 10.1016/j.cep.2004.03.002.
- Motta Lima, O. C.; Pereira, N. C.; Machado, M. A. L. S. Generalized Drying Rate Curves in Paper Drying. Proceedings 12th International Drying Symposium (IDS 2000), Noordwijkerhout, the Netherlands, 2000, paper no. 137.
- Motta Lima, O. C.; Stenzel, M.; Pereira, N. C. Drying Curves Generalization in Conductive/Convective Drying of Cellulose. Proceedings 14th International Drying Symposium (IDS 2004), São Paulo, Brazil, 2004, 1319–1326.
- Toffoli, C.; M.; Lima, O. C.; Sousa.; L.H.C.D, P.; N. C. Drying Kinetics Analysis of Contact (dryer felt) Paper (Cellulose) Drying. Proceedings 15th International Drying Symposium (IDS 2006), Budapest, Hungary, 2006, 995–999.
- Motta Lima, O. C.; Toffoli, C. M.; Ravagnani, M. A. S. S.; Pereira, N. C. Multicylinder Paper Drying Modelling and Simulation Using Generalized Correlations for the Material Drying Kinetics and the Contact Heat Transfer Coefficient. Proceedings 17th International Drying Symposium (IDS 2010), Magdeburg, Germany, 2010, 1371–1376.
- Coumans, W. J.; Ramakers, B. J. Microscopic Drying Behaviour of a Paper Sheet in a Multi-cylinder Dryer. Proceedings 12th International Drying Symposium (IDS 2000), Noordwijkerhout, the Netherlands, 2000, paper no. 404.
- Gardner, M. Computer Simulation of the Paper Machine Dryer Section. Proceedings 12th International Drying Symposium (IDS 2000), Noordwijkerhout, the Netherlands, 2000, paper no. 267.
- Ghodbanan, S.; Alizadeh, R.; Shafiei, S. Steady State Modelling of Multi-Cylinder Dryers in a Corrugating Paper Machine. Dry. Technol. 2015, 33, 1474–1490. DOI: 10.1080/07373937.2015.1020161.
- Reardon, S. A.; Davis, M. R.; Doe, P. E. Computational Modelling of Paper Drying Machines. Tappi J. 2000, 83, 58.
- Sadeghi, M.; Murray Douglas, W. J. From Tissue to Linerboard: Validation of Microscale Simulator for Single Technique and Hybrid Dryers. Proceedings 14th International Drying Symposium (IDS 2004), São Paulo, Brazil, 2004, 444–451.
- Sadeghi, M. Modeling and Simulation of Transport Phenomena in Paper Drying, PhD thesis, McGill University, Montreal, Canada, 2003.
- Perré, P.; Lescanne, Y.; Brocard, Y. Modelling of Paper Drying: A Comprehensive Computational Model Used by the Industry. Proceedings 14th International Drying Symposium (IDS 2004), São Paulo, Brazil, 2004, 1263–1270.
- Paltakari, J. Experimental Study of the Effect of Dryer Configuration on Internal Temperature and Moisture Profiles in the Sheet During Cyclic Contact Drying, Proceedings 12th International Drying Symposium (IDS 2000), Noordwijkerhout, the Netherlands, 2000, paper no. 314.
- Paltakari, J. Internal and External Factors Affecting the Paper Drying Process, PhD thesis, Helsinki University of Technology, Helsinki, Finland, 2000.
- Kong, L.; Tao, Z.; Liu, H.; Zhang, D. Effect of Operating Parameters on the Drying Performance of Multicylinder Paper Machine Dryer Section. Drying Technology 2016, 34, 1641–1650. DOI: 10.1080/07373937.2016.1139588.
- Corboy, W. G. Yankee dryers, Tappi Press, Paper Machine Operations, chapter XIV, 323–342, 1991.
- Nilsson, L.; Hauri, N.; Renström, R.; Gustavsson, C. Consequences of an Increased Dew Point in Yankee Drying of Tissue. Proceedings 15th International Drying Symposium (IDS 2006), Budapest, Hungary, 2006, 1012–1018.
- Ottosson, A.; Nilsson, L.; Berghel, J. A Mathematical Model of Heat and Mass Transfer in Yankee Drying of Tissue. Dry. Technol. 2017, 35, 323–334. DOI: 10.1080/07373937.2016.1170697.
- Shi, Y.; Ray, M. B.; Mujumdar, A. S. Effect of Large Temperature Differences on Local Nusselt Number under Turbulent Slot Impingement Jet. Dry. Technol. 2002, 20, 1803–1825. DOI: 10.1081/DRT-120015415.
- Milosavljevic, N.; Heikkilä, P. The Wall Jet-to Surface Heat Transfer in Impingement Drying. Proceedings 14th International Drying Symposium (IDS 2004), São Paulo, Brazil, 2004, 1287–1294.
- Heikkilä, P.; Milosavljevic, N. Investigation of Impingement Heat Transfer Coefficient at High Temperatures. Dry. Technol. 2002, 20, 211–222. DOI: 10.1081/DRT-120001375.
- Heikkilä, P.; Milosavljevic, N.; Jokioinen, I. Experimental Investigation of Impingement Heat Transfer Coefficient at High Temperatures. Proceedings 12th International Drying Symposium (IDS 2000), Noordwijkerhout, the Netherlands, 2000, paper no. 410.
- Heikkilä, P.; Milosavljevic, N. Influence of Impingement Temperature and Nozzle Geometry on Heat Transfer – Experimental and Theoretical Analysis. Dry. Technol. 2003, 21, 1957–1968. DOI: 10.1081/DRT-120026427.
- Kokko, T.; Lautala, P.; Huhtelin, T. Advanced Control Strategy for Impingement Drying. Dry. Technol. 2003, 21, 1969–1990. DOI: 10.1081/DRT-120026428.
- Durán-Olivencia, F. J.; Farzad, M.; Tilley, B. S.; Yagoobi, J. S. Multifluid Macroscopic Approach to Drying in Papermaking. Proceedings 21st International Drying Symposium (IDS 2018), Valencia, Spain, 2018, 1285–1292.
- Asensio, M. C. Transport Phenomena During Drying of Deformable Hygroscopic Porous Media: Fundamentals and Applications, PhD thesis, Texas A&M University, USA, 2000.
- Swietlik, F.; Juppi, K. Vertical Impingement Drying Unit for Dryer Sections. Preprints PAPTAC 92nd Annual Meeting, Montreal, Canada, 2006, B21–26.
- Tuomisto, M.; Juppi, K. Optidry Twin for Higher Paper Machine Speed and Efficiency. Preprints PAPTAC 93rd Annual Meeting, Montreal, Canada, 2007, A285–286.
- Hosemann, A. Impingement Drying-Tomorrow’s Drying Technology for Graphic Paper Grades!?! Preprints PAPTAC 92nd Annual Meeting, Montreal, Canada, 2006, B27–B32.
- Talja, R.; Timofeev, O.; Keränen, J.; Manninen, J. Impingement Drying in Papermaking. Proceedings 12th International Drying Symposium (IDS 2000), Noordwijkerhout, the Netherlands, 2000, paper no. 384.
- Keranen, J. Increasing the Drying Efficiency of Cylinder Drying, PhD thesis, University of Jyväskylä, Finland, 2011.
- Hashemi, S.; Sidwall, S.; Douglas, W. Paper Drying: A Strategy for Higher Machine Speed. II. Impingement Air Drying for Hybrid Dryer Sections. Dry. Technol. 2001, 19, 2509–2530. DOI: 10.1081/DRT-100108251.
- Hashemi, S. J.; Sidwall, S.; Douglas, W. J. M. Paper Drying: A Strategy for Higher Machine Speed. Part 2: Impingement air drying for hybrid dryer sections, Proceedings 12th International Drying Symposium (IDS 2000), Noordwijkerhout, the Netherlands, 2000, paper no. 423.
- Sadeghi, M.; Pikulik, I. Installation of PapridryTM System in Newsprint and Linerboard Machines. Proceedings 14th International Drying Symposium (IDS 2004), São Paulo, Brazil, 2004, 1279–1286.
- Sadeghi, M.; Poirier, N.; Pikulik, I. Pilot-Scale PapridryTM Drying of Linerboard. Preprints PAPTAC 91st Annual Meeting, Montreal, Canada, 2005, A39–A48.
- Pikulik, I. I.; Poirier, N.; Sadeghi, M. PapridryTM, a Novel and Rapid Technique for Paper Drying. Proceedings 15th International Drying Symposium (IDS 2006), Budapest, Hungary, 2006., 963–970.
- Liewkongsataporn, W.; Patterson, T.; Ahrens, F.; Loughran, J. Impingement Drying Enhancement Using a Pulsating Jet. Proceedings 15th International Drying Symposium (IDS 2006), Budapest, Hungary, 2006, 939–945.
- Vieira, M. G. A.; Rocha, S. C. S. Influence of Environmental Conditions on Natural Convective Drying Kinetics of Recycled Paper, Proceedings 15th International Drying Symposium (IDS 2006), Budapest, Hungary, 2006, 1048–1054.
- Motta Lima, O. C.; Ambrosio-Ugri, M. C. B.; Faria, S. H. B.; Pereira, N. C. Heat Transfer Analysis in the Convective Drying of Cellulose Materials. Proceedings 17th International Drying Symposium (IDS 2010), Magdeburg, Germany, 2010, 1396–1401.
- Weineisen, H. Through-Drying of Tissue Paper – Experiments and Modelling, PhD thesis, Lund University, Lund, Sweden, 2007.
- Weineisen, H.; Stenström, S. Modeling Through Drying of Tissue Based on Fundamental Correlations for Flow Through Cylindrical Conduits and Packed Beds. Proceedings 14th International Drying Symposium (IDS 2004), São Paulo, Brazil, 2004, 397–404.
- Weineisen, H.; Stenström, S. Modeling Through Drying of Tissue – Effect of Pore Size Distributions on Drying Characteristics. Dry. Technol. 2005, 23, 1909–1923. DOI: 10.1080/07373930500210317.
- Weineisen, H.; Parent, L.; Morrison, D.; Stenström, S. Experimental Study of Through Drying of Tissue at Industrial Conditions – Drying Results and Flow Analysis. Proceedings 15th International Drying Symposium (IDS 2006), Budapest, Hungary, 2006, 1026–1033.
- Weineisen, H.; Parent, L.; Morrison, D.; Stenström, S. Through-Drying of Tissue at High intensities – An Experimental Study. J. Pulp Paper Sci. 2007, 33, 1–8.
- Weineisen, H.; Stenström, S. A Model for through-Drying of Tissue Paper at Constant Pressure Drop and High Drying Intensity. Dry. Technol. 2007, 25, 1949–1958. DOI: 10.1080/07373930701727259.
- Weineisen, H.; Stenström, S. Modeling Drying and Energy Performance of Industrial through-Dryers. Dry. Technol. 2008, 26, 776–785. DOI: 10.1080/07373930802046443.
- Ramaswamy, S.; Ryan, M.; Huang, S.; Schneider, M. Through Air Drying Under Commercial Conditions. Proceedings 12th International Drying Symposium (IDS 2000), Noordwijkerhout, the Netherlands, 2000, paper no. 313.
- Ramaswamy, S.; Ryan, M.; Huang, S. Through Air Drying Under Commercial Conditions. Dry. Technol. 2001, 19, 2577–2592. DOI: 10.1081/DRT-100108255.
- Ryan, M.; Modak, A.; Zuo, H.; Ramaswamy, S.; Worry, G. Through Air Drying. Dry. Technol. 2003, 21, 719–734. DOI: 10.1081/DRT-120019059.
- Zuo, H.; Modak, A.; Ryan, M.; Ramaswamy, S. Experimental Analysis of the Effect of Local Non-uniformity on Convective Heat and Mass Transfer in Porous Media. Proceedings 14th International Drying Symposium (IDS 2004), São Paulo, Brazil, 2004, 1311–1318.
- Ryan, M.; Zhang, J.; Ramaswamy, S. Experimental Investigation of through Air Drying of Tissue and Towel under Commercial Conditions. Dry. Technol. 2007, 25, 195–204. DOI: 10.1080/07373930601161088.
- Modak, A.; Takagaki, S. S.; Ramaswamy, S. Integral Flow Parameters and Material Characteristics Analysis in Through Air Drying: Part I. Dry. Technol. 2009, 27, 672–684. DOI: 10.1080/07373930902827569.
- Modak, A.; Ryan, M.; Takagaki, S. S.; Ramaswamy, S. Mass Transfer Coefficients and Drying Rates in through Air Drying: Part II. Dry. Technol. 2009, 27, 685–694. DOI: 10.1080/07373930902827643.
- Tysén, A. Through Air Drying. Thermographic Studies of Drying Rates, Drying Non-uniformity and Infrared Assisted Drying, PhD thesis, Karlstad University, Karlstad, Sweden, 2018.
- Tysén, A.; Vomhoff, H. Method for the Quantification of in-Plane Drying Non-Uniformity. Nordic Pulp Paper Res. J. 2015, 30, 286–295.
- Tysén, A.; Vomhoff, H.; Nilsson, L. The Influence of Grammage and Pulp Type on through Air Drying. Nordic Pulp Paper Res. J. 2015, 30, 651–659.
- Hashemi, S. J.; Douglas, W. J. M. Paper Drying: A Strategy for Higher Machine Speed Part 1: Through Air Drying for Hybrid Dryer Sections. Proceedings 12th International Drying Symposium (IDS 2000), Noordwijkerhout, the Netherlands, 2000, paper no. 421.
- Hashemi, S. J.; Murray Douglas, W. J.; Paper, d. A Strategy for Higher Machine Speed. I: Through Air Drying for Hybrid Dryer Sections. Dry. Technol. 2001, 19, 2487–2507. DOI: 10.1081/DRT-100108250.
- Hashemi, S. J.; Murray Douglas, W. J. Moisture Nonuniformity in Drying Paper: Measurement and Relation to Process Parameters. Dry. Technol. 2003, 21, 329–347. DOI: 10.1081/DRT-120017754.
- Hashemi, S. J.; Roald, M.; Murray Douglas, W. J. Mechanism of Through Air Drying of Paper: Application in Hybrid Drying. Dry. Technol. 2003, 21, 349–368. DOI: 10.1081/DRT-120017755.
- Hashemi, S. J.; Murray Douglas, W. J. Comparative Techniques for Characterizing Drying Nonuniformity in Drying of Paper. Proceedings 14th International Drying Symposium (IDS 2004), São Paulo, Brazil, 2004, 1303–1310.
- Hashemi, S. J.; Sanguinetti, D.; Douglas, W. J. M. High Intensity Through Drying of Semi-permeable Paper. Proceedings 17th International Drying Symposium (IDS 2010), Magdeburg, Germany, 2010, 1343–1350.
- Etemoglu, A. B.; Can, M.; Avci, A.; Pulat, E. Theoretical Study of Combined Heat and Mass Transfer Process during Paper Drying. Heat Mass Transfer 2005, 41, 419–427. 128. DOI: 10.1007/s00231-004-0538-0.
- Seyed-Yagoobi, J.; Wirtz, J. W. An Experimental Study of Gas-fired Infrared Drying of Paper. Proceedings 12th International Drying Symposium (IDS 2000), Noordwijkerhout, the Netherlands, 2000, paper no. 364.
- Seyed-Yagoobi, J.; Wirtz, J. W. An Experimental Study of Gas-Fired Infrared Drying of Paper. Dry. Technol. 2001, 19, 1099–1112. DOI: 10.1081/DRT-100104807.
- Seyed-Yagoobi, J.; Sikirica, S. J.; Counts, K. M. Heating/Drying of Paper Sheet with Gas-fired Infrared Emitters – Pilot Machine Trials. Proceedings 12th International Drying Symposium (IDS 2000), Noordwijkerhout, the Netherlands, 2000, paper no. 319.
- Seyed-Yagoobi, J.; Sikirica, S. J.; Counts, K. M. Heating/Drying of Paper Sheet with Gas-Fired Infrared Emitters – Pilot Machine Trials. Dry. Technol. 2001, 19, 639–651. DOI: 10.1081/DRT-100103940.
- Seyed-Yagoobi, J.; Husain, A. N. Experimental and Theoretical Study of Heating/Drying of Moist Paper Sheet with a Gas-Fired Infrared Emitter. J. Heat Transfer 2001, 123, 711–718. DOI: 10.1115/1.1372324.
- Seyed-Yagoobi, J.; Noboa, H. Drying of Uncoated Paper with Gas-Fired Infrared Emitters – Optimum Emitters’s Location within a Paper Machine Drying Section. Dry. Technol. 2003, 21, 1897–1908. DOI: 10.1081/DRT-120026423.
- Seyed-Yagoobi, J.; Noboa, H. Heating/Drying of Uncoated Paper with Gas-fired and Electric Infrared Emitters – Fundamental Understanding. Proceedings 14th International Drying Symposium (IDS 2004), São Paulo, Brazil, 2004, 1217–1224.
- Sivill, L.; Ahtila, P.; Taimisto, M. Thermodynamic Simulation of Dryer Section Heat Recovery in Paper Machines. Appl. Thermal Eng. 2005, 25, 1273–1292. DOI: 10.1016/j.applthermaleng.2004.09.002.
- Pettersson, F.; Söderman, J. Design of Robust Heat Recovery Systems in Paper Machines. Chem. Eng. Process. 2007, 46, 910–917. DOI: 10.1016/j.cep.2007.05.018.
- Roonprasang, K. Thermal Analysis of Multi Cylinder Drying Section with Variant Geometry. PhD thesis, Technischen Universität Dresden, Dresden, Germany, 2008.
- Kong, L.; Liu, H.; Li, J.; Tao, J. Waste Heat Integration of Coating Paper Machine Drying Process. Dry. Technol. 2011, 29, 442–450. DOI: 10.1080/07373937.2010.506620.
- Li, Y.; Liu, H.; Li, J.; Tao, J. Process Parameters Optimization for Energy Saving in Paper Machine Dryer Section. Dry. Technol. 2011, 29, 910–917. DOI: 10.1080/07373937.2010.548617.
- Kong, L.; Liu, H. A Static Energy Model of Conventional Paper Drying for Multicylinder Paper Machines. Dry. Technol. 2012, 30, 276–296. DOI: 10.1080/07373937.2011.635253.
- Chen, X.; Li, J.; Liu, H.; Yin, Y.; Hong, M.; Zeng, Z. Energy System Diagnosis of Paper-Drying Process, Part 1: Energy Performance Assessment. Dry. Technol. 2016, 34, 930–943. DOI: 10.1080/07373937.2015.1087022.
- Chen, X.; Li, J.; Liu, H.; Yin, Y.; Zhang, Y. Energy System Diagnosis of Paper-Drying Process, Part 2: A Model-Based Estimation of Energy-Saving Potentials. Dry. Technol. 2016, 34, 1219–1230. DOI: 10.1080/07373937.2015.1095206.
- Yin, Y.; Li, J.; Liu, H.; Chen, X. An Energy-Saving Assessment Approach for Hood Retrofitting in Multi-Cylinder Dryer Sections. Dry. Technol. 2016, 34, 1868–1883. DOI: 10.1080/07373937.2016.1142452.
- Lindell, K. Strategies for Reduced Energy Use and Cost in Pulp and Paper Mills by Energy Integration of the Paper Drying Process, PhD thesis, Lund University, Lund, Sweden, 2007.
- Lindell, K.; Stenström, S. Assessment of Different Paper Drying Processes to Reduce the Total Energy Costs from a Mill Perspective. Proceedings 14th International Drying Symposium (IDS 2004), São Paulo, Brazil, 2004, 1233–1240.
- Lindell, K.; Stenström, S. Integration of Black Liquor Gasification with a Gas Fired Paper Drying Process. Proceedings 15th International Drying Symposium (IDS 2006), Budapest, Hungary, 2006, 931–938.
- Lindell, K.; Stenström, S. A Modular Process Modeling Tool for the Analysis of Energy Use and Cost in the Pulp and Paper Industry. Dry. Technol. 2006, 24, 1335–1345. DOI: 10.1080/07373930600951109.
- Hytönen, E.; Puumalainen, T. Simulation Based Analysis of the Influence of Impingement Drying on the Energy Concept of a Paper Mill Integrate. Proceedings 15th International Drying Symposium (IDS 2006), Budapest, Hungary, 2006, 987–994.
- Di Marco, P.; Frigo, S.; Gabbrielli, R.; Pecchia, S. Mathematical Modelling and Energy Performance Assessment of Air Impingement Drying Systems for the Production of Tissue Paper. Energy 2016, 114, 201–213. DOI: 10.1016/j.energy.2016.08.011.
- Laurijssen, J.; De Gram, F. J.; Worrell, E.; Faaij, A. Optimizing the Energy Efficiency of Conventional Multi-Cylinder Dryers in the Paper Industry. Energy 2010, 35, 3738–3750. DOI: 10.1016/j.energy.2010.05.023.
- Bhutani, N.; Lindberg, C.-F.; Starr, K.; Horton, R. Energy Assessment of Paper Machines. Energy Procedia 2012, 14, 955–963. DOI: 10.1016/j.egypro.2011.12.1039.
- Dincer, I.; Sahin, A. Z. A New Model for Thermodynamic Analysis of a Drying Process. Int. J. Heat Mass Transf. 2004, 47, 645–652. DOI: 10.1016/j.ijheatmasstransfer.2003.08.013.
- Zvolinschi, A.; Johannessen, E.; Kjelstrup, S. The Second-Law Optimal Operation of a Paper Machine. Chem. Eng. Sci. 2006, 61, 3653–3662. DOI: 10.1016/j.ces.2005.12.030.
- Koper, G. J. M.; Kjelstrup, S.; van de Ven, T.; Sadeghi, M.; Douglas, W. J. M. Entropy Production for Cylinder Drying of Linerboard and Newsprint. Int. J. Heat Mass Transf. 2007, 50, 1344–1355. DOI: 10.1016/j.ijheatmasstransfer.2006.09.006.
- Yagoobi, J. Center for Advanced Research in Drying – A US National Science Foundation Industry University Cooperative Research Center. Abstracts Second Nordic Baltic Drying Conference, Hamburg, Germany, 2017, 9.