ABSTRACT
Norway has seen an upsurge of interest in exploiting its mineral deposits during the last decade. One of the major areas of interest is a huge copper deposit, operated by Nussir ASA located in the Repparfjord tectonic window in the Caledonides of west Finnmark. Nussir ASA is evaluating the Nussir and Ulveryggen mineral resources that contain copper sulfides with a small amount of gold and silver bearing minerals. The performance of flotation operations is generally evaluated on the basis of degree of liberation of minerals or the surface interactions between the collector and mineral. Firstly, size-by-size mineralogical characterization of the flotation feed and cumulative final product using Zeiss automated mineralogy techniques (Mineralogic) revealed that mineral liberation heavily influenced the flotation behavior of the ore. Furthermore, in order to assess the role of pH, collector concentration and flotation time, bench scale flotation experiments were performed. The metallurgical results were maximum between pH 6 and 8 and at collector concentration 6 × 10−5 M. A correlation is established using the zeta potential and Hallimond flotation tests to assess the role of operating parameters in flotation. The distinctive role of process mineralogy and flotation chemical influence for copper mineral flotation of Nussir ore is presented in this article.
1. Introduction
The Nussir copper deposit is a sedimentary-hosted copper deposit located in the Kvalsund Municipality, Finnmark County, Norway, stretching from Repparfjorden in the east to the western part of the Nussir area. Moen et al. (Citation2014) confirmed the presence of chalcopyrite, chalcocite, bornite, covellite and digenite as the major copper minerals with small amounts of precious minerals, such as gold, silver and platinum group minerals in the ore. The latest mineral resource estimation is from July 2014, which states that Nussir consists of 5.8 million tons of indicated resources and 60.2 million tons of inferred resources, giving a total of 66 million tons of copper ore. This ore contains approximately 0.5–5% copper, which varies significantly based on geographical location.
The copper minerals found in many recent production operations frequently comprise low grade deposits requiring either multi stage flotation processing (including flotation at very alkaline pH to depress the iron sulfide gangue minerals), or concentration prior to smelting. However, Nussir copper ore is comprised within a relatively simple deposit with very high-grade copper minerals, and since the presence of other iron sulfides is negligible, processing is relatively uncomplicated. This research comprehends a detailed qualitative and quantitative analysis study of the mineralogical data of the ore sample, which includes methods viz. X-ray diffraction (XRD), X-ray fluorescence (XRF), LECO furnace sulfur analysis, inductively coupled plasma atomic emission spectroscopy (ICP-OES) characterization techniques, optical microscopy, scanning electron microscopy (SEM), and Zeiss automated mineralogy techniques (Mineralogic).
Process mineralogy is an integral part of mineral processing especially in the copper, gold, or silver mining industries where the process of beneficiation determines the difference between economic and uneconomic ventures. Process mineralogy comprises information and evaluation of mineral composition, size, and shape of mineral grains as well as mineral association, locking, and liberation data. The development of SEM and automated mineralogy techniques has been widely employed to find and classify copper mineralogy, finely disseminated minerals and associated sulfides–silicate phases, etc. In process mineralogy study, besides mineral characterization (Donskoi et al. Citation2007; Celik et al. Citation2010), detailed quantitative data are produced and interpreted with flotation operating conditions (Bahrami et al. Citation2019). The data are very useful particularly in plant design (Sant’agostino et al. Citation2001), flow sheet development (Nice and Brown Citation1995; Morizot et al. Citation1997), performance evaluation, and optimization studies (Frew and Davey Citation1993; Young, Pease, Johnson, and Munro Citation1997). The metallurgical results are usually assessed with the chemical analysis, which is relatively quick and straightforward. However, the data are not sufficient to keep the recovery/grade of the flotation stabilized and control the flotation performance. The metallurgical performance of a flotation process can be altered due to mineralogy, texture changes, and degree of liberation of the minerals in the ore. Young et al. (Citation1997) suggested a size-by-size mineralogical approach to identify and solve the problem related to ore quality and flotation performance in long term. In the literature, the information about the mineralization, texture, and liberation statements of the minerals are equally important for better recovery of skarn ores (Pangum et al. Citation2001), platinum group minerals (PGM), and gold with sulfide minerals (Cabri et al. Citation2005) and complex sulfide ores (Ecrola and Paloaari Citation1995; Ekmekc¸i et al. Citation2005; Lastra Citation2007; Gharai and Venugopal Citation2016). While implementing Isa Mills, besides circuit simplification, 20% of increase for zinc recovery, 5% of increase for lead recovery, and 7% of increase in liberation was achieved. There are many available examples, where mineralogic studies led to increase in production. The Cu-Pb selectivity was very low due to significant amounts of sphalerite and pyrite to the Cu-Pb bulk concentrate in a concentrator (Lastra Citation2007). It was found that reducing the feed size led to increase in liberation; but the gangue minerals sphalerite and pyrite were found in Cu-Pb concentrate in liberated form. Thus, the liberation analysis confirmed that the inability of the selective depression of sphalerite and pyrite was the major problem, but not the liberation.
Alternatively, the flotation collectors are responsible for the selective alterations of the hydrophobicities of a particular mineral/s in the ore. The metallurgical performance is highly dependent on the operating conditions during flotation (Wark et al. Citation1984; Woods and Richardson Citation1986; Deng and Chen Citation1991; Abramov and Forssberg Citation2005; Gül Citation2007; Bakalarz et al. Citation2015; Ataallah et al. Citation2018); thus, this study has been performed in order to judge the influence of these parameters on flotation results of similar ores.
The Nussir ore primarily contains three copper minerals: chalcopyrite, chalcocite, and bornite. The undesirable minerals are predominantly silicates and carbonates. Chalcopyrite is one of the abundant commercial sources of copper. However, chalcocite and bornite are also major copper minerals with higher percentages of copper. This study aims to find the possible reasons of copper losses to tail or dilution in the concentrate as a support to improve the metallurgy of the flotation circuits for the Nussir ore. The amounts of main minerals and mineral associations were size-by-size quantified by Zeiss mineralogic analysis and XRF analysis. Bench scale flotation tests were performed simultaneously in order to investigate the influence of residence time, collector concentration, and pH on flotation performance. The role of xanthate is also assessed with zeta potential and Hallimond flotation studies with respect to pH and xanthate concentration.
2. Materials and methods
2.1. Materials and reagents
The Nussir ore material was obtained from two different parts (panels) of the mine, Nussir North East (N-NE) and Nussir Old west (N-OW). Crushing and milling of these samples was performed in a jaw crusher with 3 mm opening. The material was then ground in a ball mill with 1 kg sample in each batch followed by screening into three different size fractions: – 250 + 150 µm, – 150 + 105 µm, – 105 + 75 µm, and – 75 µm for the mineralogical analysis. The samples were labeled S1, S2, S3, S4, respectively. On the basis of automated mineralogy results, size fraction S3 (–105 µm) was used for bench scale flotation to determine the recovery and grade as a function of pH, collector concentration, and flotation time. Additionally, six different size fraction samples were prepared in order to perform bench scale flotation experiments with respect to particle size in detail.
Approximately 50 g sample from each of the N-NE and N-OW panels was further ground to –10 µm as sample preparation for optical microscopy, SEM, XRD, XRF, LECO sulfur, ICP-OES characterization techniques.
The chalcocite, chalcopyrite, and bornite pure minerals were obtained from Cornwall (England), Falun (Sweden), and Virgen (Austria), respectively, in the form of small centimeter size rock pieces. The sulfide materials were first crushed and then ground in a ball mill to obtain the desired size range. In order to prepare the chalcocite, bornite, and chalcopyrite material for the various experiments, the samples were milled in a ball mill at 400 rpm for 10 min followed by sieving to obtain the size range of –150 + 50 µm for Hallimond flotation studies. For zeta potential experiments, the pure minerals were milled in a Fritsch pulverisette 6 planetary mono mill and the milled minerals were subsequently screened by ultrasound assisted wet screening to obtain –10 µm size particles. Dewatering was performed with the aid of a centrifuge and the remaining product was filtered using a 0.45 µm Millipore filter. Precautions were taken during the whole milling and sieving process until the initial conditioning phase for Hallimond flotation or zeta potential experiments to ensure that surface oxidation did not affect the results.
The sodium isobutyl xanthate (SIBX) used in these experiments was supplied by the Senmin LTD. The molecular weight of this collector was assumed to be 172.6 g mol−1, as specified by the manufacturer. Methyl isobutyl carbinol (MIBC) was employed as the frother. The pH was adjusted with dilute solutions of reagent grade milli Q water of HCl and NaOH. Deionized water was used in all the flotation tests and for the zeta potential experiments. Additionally, a standard quartz suspension was used for calibrating the zeta potential instrument. The BET surface areas for chalcopyrite, chalcocite, and bornite were 0.88, 1.11, and 1.31 m2 g−1.
2.2. Zeiss mineralogical mining method
All samples (S1-4) were initially examined by optical microscopy and SEM. Subsequent automated mineralogy analyses were performed before and after flotation with the Zeiss Mineralogic Mining System at the department of Matériaux et Environnement, Université de Liège, Belgium.
The Mineralogic Mining System is a new generation of Automated Mineralogy systems designed to provide information on the modal mineralogy (by area% and wt%), morphology of analyzed grains/particles, mineral liberation, locking characteristics, mineral association, chemical assay, and element deportment. Data acquisition by the Mineralogic was performed using a Zeiss Sigma 300 field emission gun equipped with two Bruker EDX detectors (XFlash® 630 SDD energy dispersive spectrometer). The operating conditions used for the data acquisition were 20 kV acceleration voltage, current of 20 nA, 8.5 mm working distance and a “full mapping” analytical mode. Analyses were conducted on selected representative areas of the whole specimen with a mapping step size of 3 µm and 0.025–0.03 s dwelling time.
For the microscopic observations, approximately 1 g representative sample was embedded in a mixture made with 0.4 g of PRINTEX® carbon black powder, 15 mL of epoxy resin and 2 mL of hardener to obtain blocks of 3 cm diameter. The addition of carbon black avoids the grain settlement by density into resin and allows a good spatial dispersion of particles (Bouzahzah et al. Citation2015).
2.3. Chemical analysis
Composite head samples were analyzed by ICP-OES, LECO sulfur analysis, XRF, XRD using standard methods. BRUKER AXS D-advanced diffractometer and BRUKER D8 advanced were used for the XRD and XRF analysis, respectively. Around 50 g from each N-NE and N-OW panels were further ground to –10 µm range using a Fritsch Pulverisette 6 planetary mono mill to prepare samples for these analyses.
2.4. Bench scale flotation tests
Bench scale flotation experiments were performed with 200 g (– 105 µm size fraction) of ore, ground in a ball mill with 1 kg steel grinding medium followed by flotation in a Maelgwyn bench scale flotation cell of 1 L capacity. The sequence of reagent addition was a pH regulator, collector and frother followed by flotation; the dosages of which varied according to the individual procedure details of experiments. In all the experiments, the impeller speed and airflow rate were fixed at 1200 rpm and 3 L min−1. The initial set of experiments were designed to reflect the particle size (d80), for samples from the panels N-NE, N-OW, and a mixture of both the samples. In the second set of experiments, the collector concentration was kept constant, i.e. 6 × 10−5 M and natural pH was maintained. The experiments were performed with sample S3 as a function of flotation time in two stages. In the third and fourth sets of experiments, flotation was performed as a function of pH and collector concentration, respectively. In both sets, the flotation was conducted in two stages and all concentrates and tailings were analyzed individually. In the third set, the flotation was performed with successive addition of collector concentration 5 × 10−5 M in the first stage followed by 1 × 10−5 M in the second stage. An additional fourth set of experiments were conducted in which reagent concentration was varied. Various flotation conditions along with results are presented in and . The resulting purified copper sulfide concentrates were filtered, dried, and then chemically analyzed with a Bruker AXS S8 Tiger Wavelength Dispersive XRF.
Table 1. Quantitative analysis of the ore sample using: ICP-OES, XRF, LECO Furnace S and XRD analysis.
Table 2. Bulk mineralogy of N-NE and N-OW samples obtained by Mineralogic AM.
Table 3. Modal analysis of cumulative flotation product stream (with respect to )).
Table 4. Grade and recovery results with respect to varying pH.
3. Results and discussions
3.1. Mineralogy
3.1.1. Chemical characterization techniques
The major copper mineralogy from the panel N-NE is dominated by bornite and chalcocite with a small amount of chalcopyrite, while the N-OW composite is rich in bornite and chalcopyrite with small amounts of chalcocite. The results of the XRD, XRF, LECO furnace sulfur, and ICP-OES analyses are presented in .
The data in show that the copper bearing minerals constitute 6–12% of the ore. The dominant sulfides were chalcopyrite, bornite, and chalcocite and the major gangue minerals in the ore are silicates and carbonates, eg. quartz, calcite, albite, and dolomite. Moreover, all sample composites consisted of considerable amounts of muscovite and clay (4–5%) which may cause issues in beneficiation and product handling. It is worthwhile to note that no other metal sulfides are present in any significant quantity in the ore. The sample from both panels contains mainly Ca (~9 to 11 wt. %) and Al (~5 wt. %), with less than 3 wt. % of Mg, K, Fe, and Na, in addition to traces of Mn, P, Ti, and Ba (<0.3 wt. %). These elements are mainly related to silicate and carbonate minerals as will be shown in the mineralogical characterization presented below. The S and Cu content of samples is approximately 4 and 7 wt. %, respectively for panels N-NE and N-OW corresponding to sulfide minerals. Very small quantities (in ppm) of gold, silver, and platinum group elements were detected by XRF analysis in a few samples.
The ore was further analyzed with a SEM and optical microscope. The Mineralogic analyses confirm that the Nussir ore has a significant amount of valuable minerals (Cu, Au, Ag) which are highly liberated below –105 µm. The bulk mineral percentage results () of the feed material from SEM and Mineralogic analysis were in agreement with the chemical analysis data and indicated that the major copper mineralogy in the ore is chalcopyrite, chalcocite, and bornite, contributing approximately 6–12% copper to the ore. Additionally, based on the SEM and Mineralogic analysis results it can be said that the economically interesting minerals (Au, Ag, PGM) were found to be primarily associated with the base copper sulfide minerals. The occurrence of PGM was not clearly understood with Mineralogic studies.
3.1.2. Process mineralogical evaluation
The samples of flotation feed and final products were prepared in narrow fractions to facilitate liberation analyses. A liberation criterion was selected as 95%, which means that if one particle consisted of a mineral higher than 95% of abundance, it was called a free particle even if that particle consisted two or more minerals. If two minerals existed in one particle less than 95% of abundance, it was termed a binary particle. Modal analysis showing locking statements of copper minerals with pyrite and gangue were also carried out for all fractions considering their quantity in whole stream. The examined main minerals were chalcopyrite (Cp), chalcocite (Cc), bornite (Bn) as copper minerals, and the rest were pyrite (Py), Feldspar (Fld), carbonates (dolomite, calcite), and silicates (Si) such as quartz (Qz) and so on.
3.1.3. Flotation feed
) shows the amount of copper sulfides liberated, locked, and middlings in the feed stream in four different size ranges. This figure shows that more than 75% of bornite is liberated for the S3 sample, while a large amount of this copper sulfide (17%) is present as middlings in both the panels (N-NE and N-OW). The majority of the chalcocite mineral is liberated in the S3 size fraction; there is no quantity of chalcocite midlings present in S3 and S4 size fraction of N-NE panel. In the S3 sample, chalcocite was often observed to be intergrown and locked with bornite. In N-OW panel, the liberation degrees of chalcopyrite increased to >80% in S2, S3, and S4 samples. In the S3 sample, chalcopyrite was often closely associated with bornite. Overall, it is also observed that, greater than 85% of the copper sulfides are liberated in the –75-µm size fraction. Further, there is a significant difference in the quantity of liberated particles between size S1 and S2. The degree of liberation of calcite and dolomite is significantly high (>85%) for S4 sample and the mean particle size (P80) is below ‒25 µ.
Figure 1. (a) Percentage of Liberated, middling and locked sulfides minerals in N-NE and N-OW samples. (b) Modal analysis of flotation product stream.
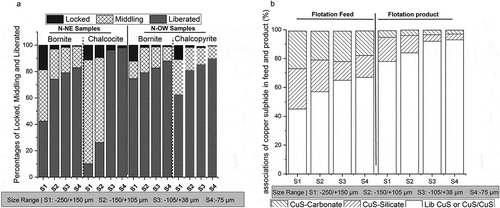
shows the modal analysis of the flotation feed and product. In the S3 sample, a significant percentage of flotation feed comprises of liberated copper sulfide/copper sulfide–copper sulfide associations, which indicates the chalcopyrite and chalcocite associations with bornite. However, sulfide associations shall pose less problems for selective flotation of valuable minerals, as no iron sulfide impurities are present in the ore. Modal analysis was calculated by considering all of the particles measured. As can be seen from the graph that copper sulfide was locked with silicates and carbonates particularly in coarse size fractions, which reduces with respect to decrease in size fractions. In sample S3 and S4, the chalcocite and chalcopyrite were mostly locked inside the bornite minerals.
3.1.4. Final concentrate
also shows the distribution of liberation and various association characteristics of copper sulfides in various size ranges after flotation. Same locking trend of chalcopyrite with chalcocite with bornite was observed in this product stream. Liberations of the copper minerals significantly increased in size fraction S3. The highest liberation degree values were obtained in the finest fraction, S4, cumulatively for all the three copper sulfides. The crucial point is that the amount and liberation statement of carbonates, which is the major contaminant increased significantly. Very high amount of calcite/dolomite was measured and most of calcite was in free form with a liberation degree of nearly 95% in all size. Thus, the best size fraction for Nussir ore flotation will be S3.
3.2. Bench scale flotation
Bench scale flotation tests with the Nussir sulfide ore were performed by varying particle size, flotation time, pH, and collector concentration with the S3 sample. Initial copper recovery for the samples from both the panels as a function of particle size is presented in . With increase in grind size from –150 µm to –250 µm, a substantial decrease in the copper recovery was observed for the N-OW sample. This is due to a decrease in the surface liberation of copper minerals beyond –150 µm. It is worth noting that the recovery of the mixed sample is essentially constant below the same size fraction (–150 µm,) while recovery steeply decreases with increasing size fraction sample due to insufficient degree of liberation. Hence, it can be concluded that reducing the overall size range to –105 µm, can result in increased recovery by 6–8%. The grade and recovery decreases again below 75 µm-size fraction which could be due to flotation of carbonate gangue minerals. The fine particles have low inertia and are therefore easily carried away by liquid streamlines around a bubble. Thus, the likelihood of collision with the bubble is minimal. Besides that, the fine particles lack the adequate kinetic energy to overcome the energy barrier to rupture the liquid film between particles and bubbles to form three-phase contact (Schulze Citation1989). Overall, the optimum grades were produced by samples from the –105 µm size fraction. This corroborates with the mineralogical study, which showed that the copper sulfides are mostly liberated in the –105 µm size fraction. However, the recoveries were marginally higher for lower size fractions; experiments were performed to improve the results for –105 µm size fraction in this study as the major associations in this size fraction is among Cu-sulfides. The remaining bench scale flotation experiments were performed with the S3 sample, which was regarded as the optimum sample due to the results previously considered. Thus, particle size is an essential parameter to optimize flotation processes (Hassanzadeh and Hasanzadeh Citation2017; Hassanzadeh Citation2017)
The grade-recovery results as a function of flotation time at collector concentration 6 × 10−5 M and at natural pH are presented in ). In all the tests, the flotation time for the second stage was kept at 1 min but the flotation time for the first stage varied. It is clearly observed that optimum grade and recovery for copper was achieved at 4 min flotation time; however, for other valuable minerals, the ideal flotation time was ca 3.5 min. Increasing flotation time to 10 min (1st stage– 9 min+ 2nd stage −1 min), reduces copper concentrate grade to 2.3% from 12.28%. shows the modal analysis of the cumulative flotation product stream; the middlings and locked particles begin to float along with the liberated particles with increasing time. There are significant differences between the liberated copper sulfide in the cumulative product stream while varying flotation time between 3.5 to 10 min. One possibility could be the increase in flotation of copper sulfides associated with carbonates and silicates. As the flotation time increase, the copper sulfide-carbonate/silicates midlings particles are more exposed and the probabilities to collide with the air-bubbles escalates. The explanation also substantiates the increase in recoveries and decrease in grade. ) depicts a comparison of the flotation performance of size fraction S3 and S4. It is clearly observed that the cumulative recovery of size fraction S4 relatively higher than size fraction S3; however, the grade decreased above 4.5 min flotation time. In order to improve the flotation results with lower size fractions, optimization of flotation time is essential.
Figure 3. (a) Cumulative recovery and grade of copper, gold and silver (size S3) as a function of flotation time. (b) Cumulative recovery and grade of copper of two size fractions S3 and S4.
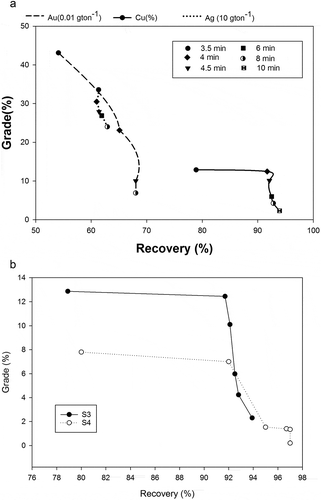
depicts the detailed stage wise grade and the recovery percentage of the concentrate 1, 2 and tailings as a function of pH. Results indicate that optimum recovery and grade were obtained at pH 8. The highest grade observed was 9.43% and the recovery was also 92.9% in the first stage at 6 × 10−5 M collector concentration and at pH 8(natural pH). The grade and recovery at pH 4 is significantly lower than at natural pH for the first stage experiment and the cumulative recovery of both concentrates is 73.89% at a grade of 2.63%. The chemical analysis shows at alkaline pH the recovery is high (91%), although the grade is moderate for pH 10 (9%), which further decreases at pH 12 (7%). The pure mineral flotation results showed decrease in recovery above pH 10 due to the formation of metal hydroxide at alkaline pH (metal hydroxides can lead to formation of metal xanthate precipitate) (Forssberg Citation1991; Ikumapayi and Rao Citation2013); it is later shown in the pure mineral studies. Overall, the combined recovery of both the concentrates is optimum in the pH range 6–9.
depicts the recovery and grade percentage of copper with respect to collector concentration and the modal mineralogy data is shown in . From , it can be observed that the recovery and grade percentage are low at 1 × 10−5 M. Several experiments were performed at collector concentration 6 × 10−5 M, varying the proportion of collector in both the stages. The results indicate that highest yield and grade of copper were produced with a collector concentration of 4 × 10−5 M and 8 g ton−1 MIBC in the first stage and subsequently adding 2 × 10−5 M reagent concentration in the second stage with 8 g ton−1 MIBC. Thus, the overall concentrate grade of copper was high when a higher proportion of SIBX was added in the first stage. indicates the modal mineralogy for the product stream and it is clearly observed that adding more collector dosage in the second stage increase the quantity of the locked particles leading to unselective flotation. A more detailed kinetic study is required to understand the variation of collector addition in different stages of flotation (similar to Ahmed and Jameson Citation1989; Hassanzadeh Citation2017).
Table 5. Grade and recovery results with respect to varying collector concentration.
Table 6. Modal analysis of cumulative flotation product stream (with respect to Table 6.).
Overall, optimum results were obtained when collector concentration of 4 × 10−5 M collector and 8 gton−1 MIBC is added in the first stage. After 1.5 min of flotation, another round of 5 min conditioning with collector concentration 2 × 10−5 M and frother 8 g ton−1 result in a cumulative concentration grade of 14% with approximately 91% recovery after two stages.
3.3. Explanation using pure mineral studies
3.3.1. Zeta potential studies
In order to explain the influence of xanthate on the five major minerals of the ore sample, zeta potential tests were conducted with respect to varying pH. The zeta potential of chalcopyrite, chalcocite, bornite, calcite, and quartz was determined as a function of pH in aqueous solution as shown in . The results show that the isoelectric point (IEP) of chalcopyrite is located at pH 4.2, chalcocite at pH 4.4 while bornite has two IEP values at pH 2.8 and pH 6 that are comparable to the previous results obtained by Kelebek and Smith (Citation1989) and Fullston and Ralston (Citation1999).
The IEP for calcite was at pH 8.2 (similar to Somasundaran Citation1986) and pH 2.1 for quartz. The influence of xanthate on the zeta potential values of these pure minerals was further studied. represents zeta potential of copper sulfides conditioned with 6 × 10−5 M xanthate as a function of pH. The zeta potential values of the copper sulfides were comparatively more negative in the presence of xanthate due to the adsorption of anionic collector. Hence, the adsorption mechanism could apparently be due to chemical interaction of xanthate on the sulfide surfaces. However, a marginal increase in negative potential is observed for the quartz and calcite minerals below pH 3 and pH 8.3, respectively. This indicates meagre adsorption of the collector on these gangue mineral surfaces due to electrostatic interactions. The meagre adsorption may lead to flotation of gangue minerals at high concentration of SIBX. In general, it is clearly observed that the collector chemically adsorbs on copper sulfides between pH 7 and pH 10, which well justifies our bench scale flotation results.
3.3.2. Hallimond flotation results
The hydrophobicity of the sulfide minerals in the reagent solutions were further assessed with Hallimond flotation experiments by varying pH and concentration of collector. The pH dependence on flotation of the major pure minerals of this ore was investigated at collector concentration 6 × 10−5 M and frother (MIBC) dosage 8 mmol L−1.
The Hallimond flotation results presented in confirm that it is possible to float the sulfides at the natural pH region, since the recovery of chalcopyrite is highest at pH 7, and that of chalcocite and bornite at pH 8. It is also notable that while the recovery of chalcocite and bornite is very low at acidic pH, recovery of chalcopyrite at pH 2–4 is approximately 80%. Nevertheless, recovery of chalcopyrite decreases with increasing pH value above pH 10, but no significant decrease is observed for chalcocite and bornite. Ackerman et al. (Citation1987) have also reported similar flotation results. However, a few researchers concluded that the recovery of sulfides, specifically chalcopyrite is highest between pH 9 and 10 which decreases above pH 10 (Hayes et al. Citation1987; Cheng and Iwasaki Citation1992; Ikumapayi and Rao Citation2013). This decrease in flotation response above pH 10 could be due to the hydrophilic ferrous hydroxides which are nearly absent in the acidic or neutral environment. The copper sulfide flotation results are consistent with the zeta potential results for the pH range 6–10. Calcite and quartz are not floating in the neutral pH regions due to xanthate as no significant adsorption was seen in the zeta-potential studies. However, at alkaline pH calcite floats marginally due to a meagre increase in the negative values of zeta potentials above pH 8.4. Metal activation is necessary for adsorption of anionic collector on quartz, therefore no significant recovery of quartz is observed. However at pH 2, 60% of the quartz is recovered which can be attributed to the electrostatic interaction between the positively charged quartz and negatively charged collector. The low grade of flotation product of Nussir ore at pH 4 could be explained with the high floatability of quartz at acidic pH region.
Copper sulfides are generally floated with thiol collectors at high pH value since pyrite can be depressed in this region. Pyrite or other iron sulfides are usually gangue sulfide minerals present in most of the copper sulfide ores. However, in the Nussir deposit, iron sulfides are not present and therefore beneficiation of this ore would be feasible in the natural pH region. Copper sulfides flotation at high pH values with sulfide ores using traditional collectors is economically beneficial but will at the same time, decrease the recovery of associated rare and precious metals, while disposal of alkaline water is another crucial issue. Thus, from the Hallimond flotation studies, the pure mineral flotation results also indicate that selective flotation of copper sulfides could be efficiently performed between pH 7 and 9.
4. Conclusion
Chalcopyrite, chalcocite and bornite are the primary copper minerals in Nussir copper ore. Microscopy analysis indicated that no other metal sulfide gangue is present in any significant quantity. The copper sulfides are mostly liberated (approx. >80%) in the −105 µm size fraction. Very small amounts of gold, silver, and PGM are found in the ore where these precious minerals also floated with copper sulfides. The performance of flotation results for Nussir ore was evaluated in terms of process mineralogy of the laboratory bench scale flotation data. First observation was, if the size fraction is further reduced below ‒105 µm, the liberation degree of carbonates increase significantly leading to reduction in selectivity. Consequently, the flotation grade of size fraction S4 was comparatively reduced as compared to the size fraction S3, in spite of increase in liberation degree of copper minerals.
Bench scale flotation results indicate that the ore is responsive and relatively quick to float. Gold and silver, attached with the base copper mineral were floated with the copper, but at lower recovery. Platinum did not follow the same trend and far little concentration was achieved. Increasing flotation time leads to flotation of the copper sulfide-carbonate middlings, which increases in the product stream due to higher probabilities of their collision with the air-bubbles escalates with respect to the flotation time. The results also indicate that at natural pH and collector concentration 6 × 10−5 M, the optimum cumulative concentrate grade obtained was 14.14% copper with a recovery of 92.1%. It should be noted that a lower proportion of collector concentration in stage1 resulted in higher cumulative recovery and grade. The pure mineral studies confirmed that SIBX could adsorb on the carbonates at higher pH and collector concentration which could be controlled by addition of certain depressant. Use of alternative more selective collectors or collector mixtures to improve flotation of copper minerals may be considered. In summary, the Nussir deposit should require uncomplicated processing in order to achieve recovery of copper and the other valuable minerals if the pH, residence time and collector concentration is controlled.
Acknowledgments
In addition, Laurentius Tijhuis and Torill Sørløkk at the Dept. of Petroleum and Geosciences, NTNU, Norway must be thanked for characterizing the samples by XRD and XRF. We would also acknowledge the Department of Matériaux et Environnement, Université de Liège, Belgium for their guidance when using the Zeiss Mineralogic mining equipment. One of the authors, Priyanka Dhar wishes to express her gratitude to Nussir ASA for providing the ore samples for this work.
Disclosure statement
The authors report no conflicts of interest. The authors alone are responsible for the content and writing of the article.
Additional information
Funding
References
- Abramov, A., and Forssberg, K. S. E., 2005, “Chemistry and optimal conditions for copper minerals flotation: theory and practice.” Mineral Processing and Extractive Metallurgy Review, 26(2). pp. 77–143. doi:10.1080/08827500590883197
- Ackerman, P. K., Harris, G. H., Klimpel, R. R., and Aplan, F. F., 1987, “Evaluation of flotation collectors for copper sulphides and pyrite, I. Common sulfhydryl collectors.” International Journal of Mineral Processing, 21. pp. 105–140. doi:10.1016/0301-7516(87)90009-3
- Ahmed, N., and Jameson, G. J., 1989, “Flotation Kinetics.” Mineral Processing and Extractive Metallurgy Review, 5(1–4). pp. 77–79. doi:10.1080/08827508908952645
- Ataallah, B., Yousef, G., Mohammad, R. H., Fatemeh, K., Morteza, A., and Abolfazl, D., 2018, “Combined effect of operating parameters on separation efficiency and kinetics of copper flotation.” Mining, Metallurgy & Exploration, 36(2). pp. 409–421.
- Bahrami, A., Mirmohammadi, M., Ghorbani, Y., Kazemi, F., Abdollahi, M., and Danesh, A., 2019, “Process mineralogy as a key factor affecting the flotation kinetics of copper sulfide minerals.” International Journal of Minerals, Metallurgy, and Materials, 26(4). pp. 430–439. doi:10.1007/s12613-019-1733–9
- Bakalarz, A., Gloy, G., and Luszczkiewicz, A., 2015, “Flotation of sulfide components of copper ore in the presence of n-dodecane.” Mineral Processing and Extractive Metallurgy Review, 36(2). pp. 103–111. doi:10.1080/08827508.2014.898301
- Bouzahzah, H., Benzaazoua, M., Mermillod-Blondin, R., and Pirard, E., 2015, “A novel procedure for polished section preparation for automated mineralogy avoiding internal particle settlement.” 12th International Congress for Applied Mineralogy (ICAM). Istanbul (Turkey), 10–12 August 2015.
- Cabri, L. J., Beattie, M., Rudashevsky, N. S., and Rudashevsky, V. N., 2005, “Process smineralogy of Au, Pd and Pt ores from the skaergaard intrusion, greenland, using new technology.” Minerals Engineering, 18. pp. 887–897. doi:10.1016/j.mineng.2005.01.021
- Celik, B., Can, N. M., and Sherazadishvili, J., 2010, “Influence of process mineralogy on improving metallurgical performance of a flotation plant.” Mineral Processing and Extractive Metallurgy Review, 32(1). pp. 30–46. doi:10.1080/08827508.2010.509678
- Cheng, X., and Iwasaki, I., 1992, “Pulp potential and its implications to sulfide flotation.” Mineral Processing and Extractive Metallurgy Review, 11(4). pp. 187–210. doi:10.1080/08827509208914206
- Deng, T., and Chen, J., 1991, “Treatment of oxidized copper ores with emphasis on refractory ores.” Mineral Processing and Extractive Metallurgy Review, 7(3–4). pp. 175–207. doi:10.1080/08827509108952671
- Donskoi, E., Suthers, S. P., Fradd, S. B., Young, J. M., Campbell, J. J., Raynlyn, T. D., and Clout, J. M. F., 2007, “Utilization of optical image analysis and automatic texture classificationfor iron ore particle characterization.” Minerals Engineering, 20. pp. 461–471. doi:10.1016/j.mineng.2006.12.005
- Ecrola, P. I., and Paloaari, V., 1995, “Developments in selective flotation of complex copper-lead-zinc.” Mineral Processing and Extractive Metallurgy Review, 15(1–4). pp. 47. doi:10.1080/08827509508936950
- Ekmekc¸i, Z., Can, M., Ergu¨, N., . S. L., Gu¨ Lsoy, O. ¨. Y., Benzer, H., and C, Elik, I˙. B., 2005, “Performance evaluation of C¸ BI˙ flotation plant using mineralogical analysis.” The 19th International Mining Congress and Fair of Turkey. Izmir (Turkey), 9–1(June). pp. 233–240. http://www.maden.org.tr/resimler/ekler/a4488c177d9dc8c_ek.pdf
- Forssberg, K., 1991, Flotation of Sulphide Minerals 1990, Amsterdam: Elsevier.
- Frew, J. A., and Davey, K. J., 1993, “Effect of liberation on flotation performance of a complex ore.” XVIII International Mineral Processing Congress, Sydney. pp. 905–911.
- Fullston, F., and Ralston,, 1999, “Zeta potential study of the oxidation of copper sulfide minerals.” Colloids and surfaces A: physicochemical and engineering aspects, 146(1). pp. 113–121. doi:10.1083/jcb.146.1.113
- Gharai, M., and Venugopal, R., 2016, “Modeling of flotation process—an overview of different approaches.” Mineral Processing and Extractive Metallurgy Review, 37(2). pp. 120–133.
- Gül, A., 2007, “The role of Na2S2O5 and activated carbon on the selective flotation of chalcopyrite from a copper ore using a dithiophosphine-type collector.” Mineral Processing and Extractive Metallurgy Review, 28(3). pp. 235–245. doi:10.1080/08827500601141750
- Hassanzadeh, A., and Hasanzadeh, M., 2017, “Chalcopyrite and pyrite floatabilities in the presence of sodium sulfide and sodium metabisulfite in a high pyritic copper complex ore.” Journal of Dispersion Science and Technology, 38(6). pp. pages 782–788. doi:10.1080/01932691.2016.1194763
- Hassanzadeh, F. K., 2017, “The kinetics modeling of chalcopyrite and pyrite, and the contribution of particle size and sodium metabisulfite to the flotation of copper complex ores.” Particulate Science and Technology, 35(4). pp. 455–461.
- Hayes, R. A., Price, D. M., Ralston, J., and Smith, R. W., 1987, “Collectorless flotation of sulphide minerals.” Mineral Processing and Extractive Metallurgy Review, 2(3). pp. 203–234. doi:10.1080/08827508708952606
- Ikumapayi, F., and Rao, K., 2013, “Recycling process water in complex sulphide ore flotation: effect of calcium and sulphate on sulphide minerals recovery.” Mineral Processing and Extractive Metallurgy Review, 36(1). pp. 45–64. doi:10.1080/08827508.2013.868346
- Kelebek, S., and Smith, G. W., 1989, “Electro-kinetic properties of a galena and chalcopyrite with a collectorless flotation behaviour.” colloids and surfaces, 40. pp. 137.
- Lastra, R., 2007, “Seven practical application cases of liberation analysis.” International Journal of Mineral Processing, 84. pp. 337–347. doi:10.1016/j.minpro.2006.07.017
- Moen, A. K., Sletten, A., and Berg Larsen, R., 2014, Geological and Mineralogical Investigation of the Western Part of the Nussir Copper Deposit - with Focus on the Geological Relationship between the Upper- and the Lower Mineralized Horizon. Internal report, NTNU.
- Morizot, G., Conil, P., Durance, M. V., and Gourram Badri, F., 1997, “Liberation and its role in flotation-based flowsheet development.” International Journal of Mineral Processing, 51. pp. 39–49. doi:10.1016/S0301-7516(97)00017-3
- Nice, R. W., and Brown, P. J., 1995, “The design of a base metals separation process.” Proc XIX IMPC, San Francisco, Calif., 3. pp. 137–143.
- Pangum, L. S., Glatthaar, J. W., and Manlapig, E. V., 2001, “Process mineralogy of fluorosilicate minerals in OK tedi ores.” Minerals Engineering, 14(12). pp. 1619–1628. doi:10.1016/S0892-6875(01)00180-7
- Sant’agostino, L. M., Alves, P. R., Shimabukurob, N., and Bonas, T. B., 2001, “Applied mineralogy as a tool for mine planning of phosphate rock.” Minerals Engineering, 14(12). pp. 1649–1657. doi:10.1016/S0892-6875(01)00183-2
- Schulze, H. J., 1989, “Hydrodynamics of bubble-mineral particle collisions.”Mineral Processing and Extractive Metallurgy Review, 5(1–4). pp. 43–76. doi:10.1080/08827508908952644
- Somasundaran, P., Ed., 1986, Advances in Mineral Processing, Littleton, Colo: SME, pp. 154–170.
- Wark, I., Jones, M., and Woodcock, J., 1984, Principles of Mineral Flotation: The Wark Symposium Parkville, Vic: Australasian Institute of Mining and Metallurgy, Vol. 40.
- Woods, R., and Richardson, P. E., 1986, The flotation of sulfide minerals - electrochemical aspects of sulphide minerals.
- Young, M. F., Please, J, Johnson, N. W., Munro, P. D., 1997, “Developments in Milling Practice at the Lead/Zinc Concentrator of Mount Isa Mines Limited from 1990.” AusIMM Sixth Mill Operators Conference. Madang, Papua New Guinea, 6–8 October.