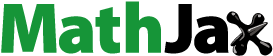
ABSTRACT
This review addresses the recovery of metals from all the main types of spent batteries (including Li-based, Zn-based, and Ni-based batteries) using bioleaching processes. Traditional processes are based on pyrometallurgical and hydrometallurgical methods and can be costly and, in some cases, cannot effectively recover the metals used in battery manufacture. Biobased hydrometallurgy may circumvent some of these drawbacks. This review presents a classification of batteries based on chemical composition from a recycling point of view. The bacterial and fungal leaching for each type of battery is reviewed. The research outputs are compared in each section, and chemical and biological mechanisms are presented. In addition, the catalytic effect of metals on the bioleaching process is reviewed for each battery. The results indicated that the main bioleaching mechanisms are the reactions of metals with metabolites, acid dissolution, and their combinations with oxidation-reduction reactions. The reactions presented in the literature are assessed and modified thermodynamically. The advantages and disadvantages of batteries bioleaching are discussed, and a future perspective is drawn. Although battery bioleaching has high efficiency and is an environmentally friendly method, with no gas emission and low energy consumption, slow kinetics and low pulp densities are among the major limiting factors hindering bioprocessing development from pilot to commercial scale.
1. Introduction
With the increasing use of mobile and cordless electronics, the disposal of spent batteries has also risen considerably. Batteries contain toxic metals such as Li, Co, Ni, Cd, Mn, Zn, and organic components (e.g. ethylene carbonate, dimethyl carbonate, diethyl carbonate) (Bal, Ghosh, and Das Citation2019; Li et al. Citation2010; Lopez, Akizu-Gardoki and Lizundia Citation2021). Thus, spent batteries pose a disposal hazard if discarded in the environment or landfills. Some batteries contain critical metals that are not abundantly available in the global market. The limited availability of these critical metals justifies the development of efficient metal recycling processes for spent batteries.
Two main approaches to metal recovery from batteries have been proposed: pyrometallurgical and hydrometallurgical methods. In the pyrometallurgical approach, high-temperature processes are used to recover metals from battery waste. This method can be applied to recover Co, Ni, Cu, and Fe, but not Li (Chandra et al. Citation2022; Huang et al. Citation2018; Liu et al. Citation2019; Meshram and Pandey, Citation2019). Hydrometallurgical techniques involve metal dissolution in inorganic or organic acids, followed by solvent extraction, precipitation, or electrochemical deposition (Asadi Dalini et al. Citation2021; Le and Lee Citation2021; Meng et al. Citation2021; Rezaei et al. Citation2022; Zheng et al. Citation2018). It was documented that bioleaching is cost-effective compared to the hydro/pyrometallurgical process. It was indicated although biological routes have similar total capital investment costs to chemical routes, the total operational costs of chemical and typical hybrid routes are substantially higher than bioprocess (Borja et al. Citation2016; Esmaeili et al. Citation2020; Moazzam et al. Citation2021; Pollmann et al. Citation2016). Technology transfer makes it possible to adopt these bioprocesses for recovering metals from spent batteries, an emergent field of bioprocessing. This review addresses microorganisms, thermodynamic and kinetic analysis of reaction mechanisms, and the advantages and disadvantages of these bioprocesses.
2. Classification of batteries
Batteries are classified as non-rechargeable (primary disposable batteries) and rechargeable (secondary batteries). Based on their metal content, batteries are grouped as Li-ion batteries, Zn-Mn dry and alkaline batteries, Pb-acid batteries, Ni-Cd batteries, and nickel-metal hydride (NiMH) batteries (Bernardes, Espinosa, and Tenório Citation2004; Provazi et al. Citation2011; Rogulski and Czerwiński Citation2006; Zeng, Li and Singh Citation2014). Disposable batteries are recyclable and classified into three groups: Li-based, Zn-based, and Ni-based batteries (). There is no research on the bioprocessing of Pb-based and Hg-batteries to date.
2.1. Li-based batteries
Common components in Li-ion batteries are the cathode, anode, electrolyte separator, and casing. Li-ion batteries typically contain Li (5–7%), Co (5–20%), Ni (5–10%), 5–10% other base metals (e.g. Cu, Fe, Al), 15% organic compounds, and 7% plastic components (Ordoñez, Gago, and Girard Citation2016). Interest in metals recycling in Li-ion batteries is focused on Co, Ni, and Li (Ghassa et al. Citation2020a; Saneie et al. Citation2022).
The cathode is made of an Al foil covering with electroactive materials that mainly consist of a lithiated metal oxide or phosphate (Yun et al. Citation2018). Common cathode materials are lithium cobalt oxide (LiCoO2), lithium manganese oxide (LiMn2O4), lithium nickel manganese cobalt oxide (LiNiMnCoO2), lithium vanadium oxide (LiV2O3), and lithium nickel cobalt aluminum oxide (LiNiCoAlO2) (Ellis, Lee, and Nazar Citation2010; Fergus Citation2010; Zeng, Li, and Singh Citation2014). LiCoO2 is the most common cathode due to its high discharge capacity and stability (Ghassa et al. Citation2021).
The anode is a Cu foil usually coated with graphite as the electroactive material (Golmohammadzadeh, Faraji and Rashchi Citation2018). The common electrolytes for Li batteries are mixtures of Li-salts (LiAsF6, LiClO4, LiPF6, LiCF3SO3, Li(SO2CF3)2, and LiBF4) and organic solvents (dimethyl sulfoxide, diethyl carbonate, propylene carbonate, and ethylene carbonate). These electrolytes are designed for ionic transport between the electrodes (Golmohammadzadeh, Faraji, and Rashchi Citation2018; Zeng, Li and Singh Citation2014). The components of Li batteries are wrapped up and inserted into a cylindrical case filled with an electrolyte (Chagnes and Pospiech Citation2013).
EquationEquations (1)(1)
(1) and (Equation2
(2)
(2) ) show the half-cell reactions at the anode and cathode of a common Li-ion battery, respectively. During discharge, Li released from lithiated graphite (LiC6) moves from the anode to the cathode through electrolyte, while the electrons reach the cathode in an external route to form LiCoO2. Thus Co4+ is reduced to Co3+. Based on the cohesive and bond free energy energies and the Gibbs free energy of formation, Li in the cathode is stable as LiCoO2 (reactions 1 and 2), and the reaction is not reversible to LiC6. However, during battery charging, the reverse reactions transfer Li to the thermodynamically less favorable LiC6 (Klaus Citation2018).
Different processing routes in pyrometallurgy, hydrometallurgy, and their combinations are employed to recycle Li-batteries. In the pyrometallurgical method, spent batteries are fed into a shaft furnace with three different temperature zones: evaporation of electrolyte (~300° C), plastic pyrolysis to incinerate plastic components (700° C), and smelting, which produces an alloy containing Cu, Co, Ni, and Fe, as well as waste slag. The slag also contains Al, Si, Ca, and Fe (King and Boxall Citation2019). However, the process is suitable for recycling other metals (Co especially) but not Li.
Hydrometallurgical processes have been developed and implemented to recover Li from spent batteries. These processes require mechanical pretreatments such as shredding, milling, and screening to reduce and separate organic from inorganic materials. Metals are dissolved from sorted Li-battery electrodes in organic or inorganic acid solutions. Oxidants or reductants may be used to increase the metal recovery and leaching rates, especially for Co. Liu et al. (Citation2019) showed inorganic acid solutions outperformed organic acids in the leaching cathodes for Co and Li recovery. The process’s cost, energy consumption, and CO2 emissions also favored the dissolution of inorganic acids. Dissolved metals can be recovered by various combinations of precipitation, solvent extraction, ion exchange, and electrowinning, all established in conventional hydrometallurgy.
2.2. Zn-based batteries
Zn-based batteries, including alkaline Zn-Mn and Zn-C batteries, usually supply power for small, low-energy devices such as radios, remote controls, toys, and watches. Zn-Mn batteries are not rechargeable and run out of power in a relatively short period. They contain Hg, Cu, Zn, and Mn (Calin et al. Citation2021), and the 12–28% Zn and 26–45% Mn increase their recycling potential (Sayilgan et al. Citation2009).
A typical Zn-Mn cathode contains 79–90% MnO2, acting as an oxidizing component, and 2–10% graphite for electronic conductivity. The electrolyte is 7–10% aqueous KOH. The main composition of the anode includes 55–70% Zn, 25–35% aqueous KOH (in the form of a solution with 35–52% potassium hydroxide), and 0.4–2% gelling agent. Reaction 3 shows that MnO2 is reduced to MnOOH when discharge occurs. The reaction is not reversible, and Zn batteries are not rechargeable.
Pyrometallurgical processes include selective metal volatilization and condensation. They are widely used to recycle Zn, Mn, and steel alloys (Belardi et al. Citation2012; Mocellin et al. Citation2017; Sun et al. Citation2016). Evaporation and reduction at 750-1500°C of Zn-Mn battery scrap are also practiced in the battery recycling industry (Hu et al. Citation2021).
Comminution and separation of steel and plastic are necessary to minimize impurities (Sayilgan et al. Citation2009). Sulfuric acid leaching can be used to dissolve Zn, Cu, Ni, Cd, and Hg, followed by solvent extraction for Zn recovery and selective ion exchange for other metals. In principle, this can be used to process spent Zn-C, alkaline Mn, and Ni-Cd batteries (Lannoo et al. Citation2019). Electrochemical techniques are also available to recover metals from solvents. Other products from the sulfuric acid process are MnCO3 obtained by precipitation and a mixture of manganese oxide and carbon black (Fröhlich and Sewing Citation1995).
2.3. Ni-based batteries
The Ni-Cd batteries are rechargeable and used in a wide range of applications, including portable equipment for wireless communication and computing devices (Bajpai and Dash Citation2012; Mahandra, Singh, and Gupta Citation2018). The main component of the cathode is Ni-oxyhydroxide (NiOOH), which is reduced to nickel hydroxide (Ni(OH)2) during the discharge (EquationEquation (4)(4)
(4) ). Graphite in the cathode improves conductivity, and Co (and other metals) in metallic and hydroxide forms increases the cathode life and capacity. Metallic Cd in the anode becomes cadmium hydroxide during discharge (EquationEquation (3)
(3)
(3) ). Ni is used in the anode to improve conductivity and prevent crystal growth and agglomeration during battery charge (Dewulf et al. Citation2010; Morioka Citation2001). KOH solution has been used as an electrolyte to wet internal cell components (Chakankar, Jadhav, and Hocheng Citation2017). The overall reaction of discharge and charge is presented in EquationEquation (4)
(4)
(4) :
Ni-Cd batteries cathode contain 47% Ni and 48% Cd (Cerruti, Curutchet, and Donati Citation1998). NiMH batteries are comprised of approximately ~40% Ni and Co (~3%) and rare earth metals (8–10% of La, Ce, Pr, and Nd) (Müller and Friedrich Citation2006).
Dumping and incineration of Ni-Cd batteries pose environmental health risks (Shi et al. Citation2019; Soria et al. Citation2001). Pyrometallurgical processes have been developed for Ni-Cd batteries based on Cd distillation in a closed furnace to yield metallic Cd powder, and Ni can be reduced and smelted in an electric furnace to produce metallic nickel (Espinosa et al. Citation2004). Hydrometallurgical methods can process mixtures of spent Ni-Cd, Zn-C, alkaline Mn, and Li batteries. Physical separation is first employed for size reduction, iron scrap separation, and separation of organic matter from metals. Sulfuric acid selectively dissolves non-Mn metals and non-carbon materials. Zn is recovered by solvent extraction and Cu, Ni, and Cd by ion exchange. Zn, Cu, Ni, and Cd are then recovered by electrolysis and Mn by precipitation (Tanong et al. Citation2017).
3. Bioleaching of batteries
Numerous acidophilic iron- and sulfur-oxidizing microorganisms have been identified and characterized from acidic mine water samples and acid bioleaching processes (Chen et al. Citation2016; Ghassa et al. Citation2015). Fe3+ acts as a chemical oxidant, and is reduced to Fe2+ in the reaction with a sulfide mineral. Microbial re-oxidation of Fe2+ to Fe3+ ensures continuing Fe3+-mediated oxidation and leaching capacity. The oxidation of sulfur compounds produces sulfuric acid and helps maintain acid conditions. Under ambient conditions, the chemical oxidation of Fe2+ to Fe3+ at low pH is too slow, but acidophilic microorganisms increase rates by 105–106 times (Ghassa et al. Citation2017). Redox reactions of metals and sulfur are central in microbial bioleaching (EquationEquations (5)(5)
(5) –(Equation7
(7)
(7) )).
Heterotrophs, mostly Aspergillus and Penicillium spp., have also been tested in bioleaching processes (Asghari et al. Citation2013; Pathak et al. Citation2021; Shah et al. Citation2020). Dissolution of metals from minerals by fungi is attributed to three reactions: (i) acidolysis of the mineral, (ii) metal sequestration and complex formation, and (iii) metal redox reactions. In acidolysis, metals dissolve due to a proton attack on the metal. In sequestration, organic acid metabolites (especially carboxylic acids) dissolve metals by forming stable complexes (EquationEquation (8)(8)
(8) ). Metal complexes are formed on the surfaces by ligand exchange, polarizing critical bonds (Brandl, Bosshard, and Wegmann Citation2001). In the redox reactions, the solubility of metals increases due to electron exchange between metals (EquationEquation (9)
(9)
(9) ).
M = metal
The target metals vary with the battery through the bioleaching of waste batteries. The solubilities vary with the target metals and their redox states. Bioleaching conditions are acidic to increase the solubilities, and in some cases, the metal dissolution is based on an H+ attack. Thus, the process may promote microorganisms that oxidize S0 to sulfuric acid. Spent batteries and battery waste exhibit acid demand, which should be satisfied for an acid bioleaching process. When the battery waste contains Co and Mn, these metals must be first reduced (Co3+ + e- → Co2+, Mn4+ +2e- → Mn2+) to soluble redox states. In comparison, Ni is directly oxidized to Ni2+ by proton attack. This oxidation requires a reductant, which may be an intermediate in the pathway of sulfur oxidation or Fe2+ which is oxidized to Fe3+ in reaction. High concentrations of Fe3+ provide an oxidative environment. Fe2+ is oxidized to Fe3+ by iron-oxidizing acidophiles, considered fundamental in the bioleaching of sulfide minerals.
3.1. Bioleaching of Li-based batteries
3.1.1. Bacterial leaching
Mishra et al. (Citation2008) used Acidithiobacillus ferrooxidans (A. ferrooxidans) with S0 and Fe2+ as the energy sources to leach LiCoO2 cathodes. At pH 2.5 and 0.5% pulp density, the metals recoveries were 65% Co and 10% Li in 25 d. Increasing the pulp density to 1% decreased the Co leachability to 56%. The mode of the bacterial action in the process was not clear in this study. Iron oxidation clearly enhanced Li dissolution (). The dissolution of Co required a reduction of Co3+ to Co2+.
Figure 2. The negative effect of mixed pulp density on the extraction of Co and Li from spent Li-ion batteries. The box-and-whisker plots show the median concentration, the 25th, and 75th quartiles.
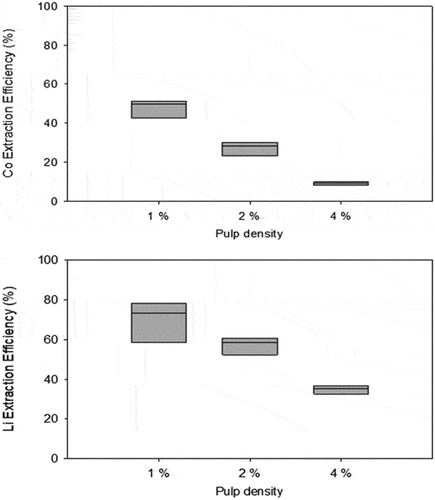
For cobalt leaching from LiCoO2 cathodes, Zeng et al. (Citation2012) used a Cu-catalyzed bioleaching process with A. ferrooxidans and Fe3+. The bacteria were first subcultured to adapt them separately to Cu2+ (10 g/L) and 1% spent LiCoO2 cathodes. 99.9% of Co was leached with 750 mg/L Cu2+ in 6 d. In the absence of Cu2+, 43% of Co leached in 10 d. Dissolution of Li was not specifically determined, but the residual was <1% of the original weight. The Cu catalyst effect of copper was explained by the exchange of Cu for Li in LiCoO2, forming a putative intermediate CuCo2O4, in which Fe3+ reduced the trivalent cobalt to the soluble Co2+ form (EquationEquations (10)(10)
(10) –(Equation12
(12)
(12) )) However, it is not clear whether the Cu-intermediate is stable because it has not been confirmed analytically. In addition, in the suggested reaction (EquationEquation (11)
(11)
(11) ), both Fe3+ and Co3+ are reduced, which means that this reaction cannot be correct. The correct reactions for different ions will be suggested in section 3.4.4, based on thermodynamic modeling.
Zeng et al. (Citation2013) investigated the Ag-catalyzed bioleaching of LiCoO2 cathodes with A. ferrooxidans cultures. With 20 mg/L Ag+, cobalt leached to 98% in 7 d at 1% pulp density, compared to 43% without Ag. Ag+ was proposed to form an intermediate AgCoO2 on LiCoO2 surfaces, with subsequent decay-causing a release of Ag+ and dissolution of Co2+ (EquationEquations (13)(13)
(13) –(Equation14
(14)
(14) )) (Zeng et al. Citation2013). A polytype of AgCoO2 is an efficient catalyst of Co oxidation (Dey et al. Citation2018), and several modifications of physical and chemical properties of this complex with delafossite (copper iron oxide mineral) formula have been described (Iwase et al. Citation2011; Muguerra et al. Citation2008). Like EquationEquations (11)
(11)
(11) and (Equation14
(14)
(14) ) also cannot be correct. Again, correct reactions will be suggested in section 3.4.4.
Although the catalytic role of Cu+ and Ag+ in the Fe3+-mediated dissolution of LiO2 is yet to be elucidated, these catalysts seem to enhance the release of Li+ from the Co complex, resulting in reductive leaching of Co, with iron-oxidizing microorganism maintaining a Fe3+ surplus.
Mixtures of A. ferrooxidans and Acidithiobacillus thiooxidans have also been tested for Li, Co, and Ni dissolution from spent Li-ion batteries. Initially, the cathodic and anodic layers from spent batteries, ground to −200 mesh (<75 µm), were inhibitory to the mixed culture, but this was alleviated through successive subcultures at increasing pulp densities of up to 40 g/L (Heydarian et al., Citation2018). In general, inhibition may be caused by multiple factors such as (i) toxic metals or organics affecting the oxidation activity; (ii) the pulp decreasing the transfer rate of oxygen in culture, affecting the aerobic activity and CO2 fixation negatively; (iii) collision of particles with cells, causing shearing cell membranes. At 4% pulp density and pH of 1.5, recoveries were 99% Li, 50% Co, and 89% Ni after 16 d in the mixed adapted culture. Co and Ni dissolved through reductive leaching involving the Fe redox couple, whereas Li dissolved through a proton attack.
Boxall et al. (Citation2018) used A. ferrooxidans and A. thiooxidans to produce Fe2(SO4)3 and H2SO4 solutions used to leach Li-ion battery waste, separately and in combination, at 25°C Experiments lasted to 2 h. 82% Mn, 74% Cu, 60% Li, 49% Ni, and 53% Co leached at optimum conditions. The initial pH in the range of 1.1–2.5 increased by 2 to 4 pH during the leaching.
Xin et al. (Citation2012) used a mixed culture of iron- and sulfur-oxidizing microorganisms to leach cathode and anode mixtures of Li-ion batteries. They used S, FeS2, or a combination as substrates. The leaching of Li was enhanced with S becoming of H2SO4. Co dissolution was improved when the culture received both S and FeS2 as the substrates, thus indicating the role of Fe as a redox carrier for the leaching of Co.
Zhao et al. (Citation2008) evaluated a two-step biological leaching: one reactor with S or FeSO4 to produce the bioleaching solution, another to leach anodic and cathodic materials obtained from spent Ni–Cd batteries. The consuming acid (dissolution of oxides and hydroxides) was occurred by acid produced by microorganisms. Ni and Cd dissolved more slowly in the second phase than in the first. In general, Cd-containing anodes dissolved faster than Ni-containing cathodes. Individual sources and reactions are difficult to determine because the leach solution was municipal sludge, and the batteries were processed without comminution or disassembly.
Xin et al. (Citation2016) examined the dissolution of Li, Co, Mn, and Ni from cathodes of spent batteries types LiFePO4, LiMn2O4, and LiNixCoyMn1-x-yO2. Li leached with acid, and Co, Mn, and Ni leached with Fe3+ (Fig. S1, please refer to the supplementary materials file). Xin et al. (2009) suggested that contact was required between cathodes and microorganisms for leaching Co, Ni, and Mn, but not for leaching Li. 92% Li, 93% Mn, 43% Co, and 38% Ni were dissolved in a mixed culture of A. thiooxidans and Leptospirillum ferriphilum (L. ferriphilum). The leaching of all metals was >95% at an initial pH of 1.5.
Extracellular polymeric substances (EPS) of iron-oxidizing microorganisms have also been associated with bioleaching processes (Wang et al. Citation2018; Wu et al. Citation2019). EPS facilitates cellular attachment and biofilm formation. Wu et al. (Citation2019) purified EPS from A. thiooxidans, A. ferrooxidans, and L. ferriphilum to evaluate it for bioleaching of spent battery type LiNixCoyMn1-x-yO2. Fe3+/Fe2+ cycle was formed in the EPS resulting in Li, Co, Ni, and Mn dissolution (Wu et al. Citation2019).
Ghassa et al. (Citation2020a, Citation2020b) tested a consortium of moderate thermophiles, including Acidithiobacillus caldus, L. ferriphilum, Sulfobacillus spp., and Ferroplasma spp. for bioleaching of Li-ion batteries. The consortium received S, Fe2+, and Fe scrap. Bioleaching of Co and Ni was two days because of fast Fe and S oxidation in thermophilic bioleaching. Li dissolution was not affected by these substrates. The addition of ferrous iron could be replaced with iron scrap, decreasing the leaching kinetic.
3.1.2. Fungal leaching
Organic acids, such as carboxylic acids, are biodegradable and less corrosive compared to inorganic acids (Asadi et al. Citation2018; Bahaloo-Horeh and Mousavi Citation2017). Based on their pKa values, dilute solutions of carboxylic acids have moderately acidic pH values in the range of 3–5. Organic acids are available through chemical synthesis (Karaffa, Sándor, and Fekete Citation2001) and as metabolites from central metabolic pathways. Fungi can grow over a wide pH range and tolerate toxic metals (Santhiya and Ting Citation2005).
Carboxylic acids were produced by Aspergillus niger cultures grown with sucrose and tested for bioleaching of Li-ion batteries (Bahaloo-Horeh et al. Citation2017). Spent media contained citric, oxalic, malic, gluconic, and oxalic acid. Oxalic acid had the highest concentration in A. niger cultures. 100% Cu, 95% Li, 45% Co, 38% Ni, 70% Mn, and 65% Al was leached in 8 d. Citric acid efficiently sequestered metals. Oxalic acid forms soluble complexes with Li and Al, whereas Ni- and Co-oxalates are practically insoluble. Subcultures of A. niger at increasing pulp density up to 1%, increased the metal tolerance. Acclimation increased biomass yields, organic acid production, and metal dissolution. The tolerance of A. niger culture was limited to 1% pulp density (Bahaloo-Horeh and Mousavi Citation2017; Bahaloo-Horeh, Mousavi, and Shojaosadati Citation2016), and at higher pulp densities spent medium method should be employed.
3.2. Bioleaching of zinc-batteries
3.2.1. Bacterial leaching
Zn-based batteries contain metals with relatively low economic values as compared to Li- and Ni-based batteries. The anodic and cathodic formulations of these batteries generally contain ZnO and soluble salts such as Zn5(OH)8Cl2·H2O (zinc chloride hydroxide monohydrate) and Zn(NH3)2Cl2 (zinc ammonium chloride), and Mn insoluble phases such as MnO2 (manganese dioxide) and tetragonal spinel ZnMn2O4 (Lobos, Citation2017; Mishra et al. Citation2008).
Xin et al. (Citation2012) investigated the bioleaching of Zn and Mn from spent Zn-Mn batteries with a mixed culture of Alicyclobacillus spp. and Sulfobacillus spp. The culture was inhibited at increasing pulp density. By increasing the pulp density from 1 to 8%, the bioleaching of Zn and Mn decreased from 100 to 30%, and from 94 to 2.5%, respectively. The recovery loss was attributed to the uncontrolled pH, which increased with pulp density. Sulfur oxidation or sulfuric acid addition could control pH and thus promote Zn and Mn dissolution, and additional Fe2+ could augment the dissolution of MnO2 to Mn2+. Niu et al. (Citation2016) evaluated the effect of pulp density on the bioleaching of spent Zn-Mn spent batteries using a mixed culture. Sulfuric acid addiction instead of biogenic acidity via sulfur oxidation was the most efficient and fastest method for pH control necessary for Zn and Mn recoveries at 8–9.7% pulp densities. Recoveries were >50% for both Zn and Mn at 8.0–9.7% pulp densities after 9 d. Niu et al. (Citation2016) proposed the following reaction for ZnMn2O4 dissolution:
The cathodic and anodic half-reactions will be presented in section 3.4.4.
Niu et al. (Citation2015) examined metal ion catalysis to enhance the leaching of Zn-Mn batteries in the Alicyclobacillus-Sulfobacillus mixed culture (). Cu2+ had the most catalyst effect in bioleaching compared to Co2+, Ni2+, and Ag+. The dissolution of Zn increased from 48% to 62% and Mn from 31% to 62% with 0.8 g Cu2+/l in the culture. They proposed a sequence of reactions for the dissolution (EquationEquations (16)(16)
(16) and (Equation17
(17)
(17) )). The effect of silver was particularly low, but this was expected because AgCl precipitation; the solution phase contained 5.1% Cl- from the dissolution of Zn5(OH)8Cl2.H2O and Zn(NH3)2Cl2) (). However, these reactions’ stoichiometry and redox shuttling are unconfirmed (Niu et al. Citation2015).
Figure 4. Effect of metallic ions as a catalyst (Copper and Silver) on the bioleaching of Co, Mn, and Zn from spent Li-ion and Zn-Mn batteries. The box-and-whisker plots show the median concentration, the 25th and 75th quartiles (Niu et al. Citation2015; Zeng et al. Citation2012, Citation2013).
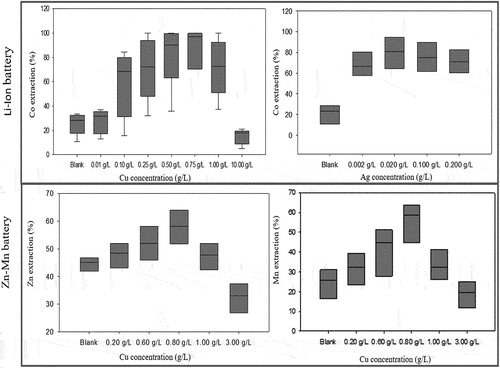
Xin et al. (Citation2012) evaluated mixed and single cultures (Alicyclobacillus and Sulfobacillus spp.), energy source (elemental sulfur, pyrite, elemental sulfur + pyrite), and initial pH values for contact or non-contact leaching of Zn-Mn spent alkaline and Zn-C-batteries (Xin et al. Citation2012). In the non-contact mode with a dialysis membrane separation, 96% Zn was leached in 1 d with acid regardless of test culture. MnIIO dissolves at low pH, whereas dissolution of MnIII2O3 and MnIII,IV3O4 requires a reductant (Sayilgan et al. Citation2009). Up to 97% Mn was leached reductively with Fe2+ as the reductant by the mixed culture in 13 d. Reductive dissolution of Mn could be coupled with microbial oxidation of pyrite as the source of sulfuric acid and dissolved iron. Dialysis membrane experiments demonstrated that bioleaching of Mn required microbial contact (×in et al. 2012b).
A flowsheet for Zn-Mn-ferrite production from spent Zn-Mn batteries was proposed by Song et al. (Citation2015). The proposed process was comprised of bioleaching, co-precipitation, and boiling reflux. A mixed culture with S and FeS2 was used for the bioleaching at 4% pulp density, with 100% Zn and 89% Mn dissolution in 13 d. For synthesizing Zn-Mn ferrite, various molar ratios of Mn:Zn:Fe (6:4:20, 5:5:20, and 4:6:20) and alkalis (NaOH, NaHCO3, and NH4HCO3) were tested. The high saturation magnetization of 102 emu/g and a uniform particle size of ferrite was obtained using 2 M each of Mn2+, Zn2+, and Fe2+, followed by co-precipitation with NaOH and reflux at 100°C (Song et al. Citation2015).
3.2.2. Fungal leaching
Kim et al. (Citation2016) employed six Aspergillus strains with various substrates sources to dissolve metals from spent Zn-Mn batteries. The strains produced predominantly citric and oxalic acid when sucrose and malt extract were used as substrates, respectively. Zn and Mn were leached with citric acid. Oxalic acid precipitates Zn2+ as Zn-oxalate (Sayer and Gadd Citation1997; Sayilgan et al. Citation2010; Xin et al. Citation2012), suggesting that oxalic acid concentrations should be minimized or citric acid should be separated from spent culture medium for use as a lixiviant.
3.3. Bioleaching of Ni-based batteries
3.3.1. Bacterial leaching
Cerruti, Curutchet and Donati (Citation1998) reported two-step bioleaching with A. ferrooxidans for spent Ni-Cd batteries. H2SO4 production from S oxidation reached 80 mmol H+ kg−1d−1 at pH 1.0 after 3 d. 1 kg of S0 produced sufficient acidity to maintain the pH at 1.0 for leaching ~25 g of spent batteries. After 93 d, nine successive steps of fresh leach solution replacement and various hydraulic retention times yielded 100% Cd, 96% Ni, and 95% Fe dissolution from spent Ni-Cd batteries (). The process involved Ni oxidation to Ni2+ followed by acid dissolution, and reduction of Ni-oxyhydroxide to Ni2+ and further acid dissolution. For the reductive step, intermediate sulfur compounds formed by S0 oxidation were proposed as electron donors.
Figure 5. Effect of HRT on the extraction of Co, Cd, and Ni from spent Ni-Cd batteries. The box-and-whisker plots show the median concentration, the 25th, and 75th quartiles.
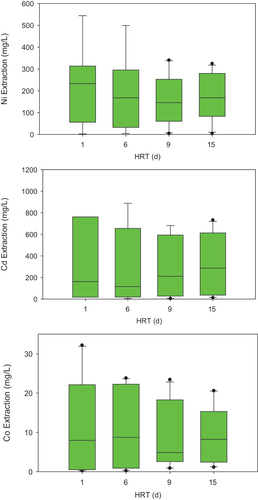
Sewage sludge has been evaluated as a substrate for bioleaching Ni-Cd batteries (Zhao et al. Citation2007, 2008a; Zhu et al. Citation2003). Zhao et al. (2008b) showed that Cd, Co, and Ni bioleaching was enhanced if Fe2+ instead of S0 was used. Ni and Cd bioleached rapidly with Fe2+ and sulfur at pH 1.2. Increasing the sewage sludge residence time from 1 to 4 d increased H2SO4 production to pH 1.9 and dissolution of Ni and Cd. Zhao et al. (2008a) reported 100% dissolution of Ni, Cd, and Co, at the ~25–40 d at pulp densities of 0.2, 0.4, and 0.8%, respectively (). Acid attack was the main dissolution mechanism, followed by microbial contact for oxidation (Zhao, Yang and Zhu Citation2008). Dissolution of Cd and Co was faster than Ni with sewage sludge because Cd and Co dissolutions occur at pH ~ 3–4.5, compared to pH 2.5–3.5 for Ni.
Response surface methodology was used to optimize the bioleaching of metals from Ni-Cd and NiMH batteries (Ijadi Bajestani, Mousavi, and Shojaosadati Citation2014a). Cd dissolution was independent of the initial Fe3+ concentration, enhanced at the pH range of 1.4 to 2.6. Cd formed a surface complex FeOCdOH2+ with hydrous ferric oxide (Dzombak and Morel Citation1986), which decreased Cd dissolution and precipitated ferric iron as jarosite (KFe₃(SO₄)₂(OH)₆) in sulfate-rich solutions. Co dissolution was dependent on the Fe3+ concentration and pH. Ni dissolution was enhanced at high redox potential and low pH values. Thus, the conditions of Ni and Cd dissolution were not comparable. Recoveries were 87% Ni, 67% Cd, and 94% Co at the 15 d (Ijadi Bajestani, Mousavi, and Shojaosadati Citation2014b).
Velgosová et al. (2013, 2014) reported that Cd completely dissolved from Cd-Ni batteries in acidic Fe3(SO4)2 solutions. Leaching was faster in the presence of iron-oxidizing microorganisms. Ni dissolution was 45% by bioleaching and 56% by the chemical leaching with Fe3(SO4)2. Cd dissolution was dependent on H2SO4 and Fe3+. A process flowsheet for the bioleaching Ni-Cd battery waste is shown in Fig. S2, comprising (i) an acidifying step to meet the acid demand and (ii) an aerated leaching reactor, Both steps need recycling settling basins as well as dewatering before disposal of solids.
3.3.2. Fungal leaching
Kim et al. (Citation2016) used several Aspergillus spp. to produce oxalic and citric acid for dissolution up to 95% Ni and Cd in 8 d. Citric acid formation are preferred because metal oxalates are relatively poorly soluble in aqueous solutions. The carbon source, fungal strain selection, and growth conditions are key to producing citric acid over oxalic acid.
3.4. Thermodynamic assessments
Assessing thermodynamic conditions in the bioleaching of spent batteries gives insight into the process.
3.4.1. Catalyst selection for bioleaching
Bioleaching processes are usually disadvantaged by slow leaching rates of both primary and secondary resources. Modified microbial cultures, surfactants, and catalyst metal ions such as Ag+, Cu2+, Hg2+, Co2+, Ru3+, As5+, Bi3+, Sn2+, Ni2+, activated carbon, and light illumination has been tested to enhance slow kinetics of bioleaching (Niu et al. Citation2015; Zeng et al. Citation2012, Citation2013). Increasing the difference in standard potential between the catalyst metal and the more noble metal led to faster kinetics and higher recovery (Ballester et al. Citation1992; Escudero et al. Citation1993; Guo et al. Citation2011). shows the Gibbs free energy for potential catalysts and target metals. Table S-1 (Supplementary Materials) is a list of the data presented in . A low Gibbs free energy shows better conditions for substituting the catalyst for the noble metal. Therefore, in the case of Li-ion batteries, the decreasing order of efficacy of catalysts are Bi3+, Ru3+, Hg2+, Cu2+, Sn2+, Ni2+, Co2+, and Ag+. For Zn-Mn batteries, the order decreased from Bi3+, Ru3+, Hg2+, Ag+, Cu2+, Sn2+, to Ni2+. There is consistency between the data in and the bioleaching data reported by Ballester et al. (Citation1990). However, catalyst recycling and price, environmental and health effects, and toxicity are factors that may overrule the usefulness of catalysts on a commercial scale.
3.4.2. Potential reactions
3.4.2.1. Li-ion batteries
The Gibbs free energy of formation for CuCo2O4 and AgCoO2 (reactions 10 and 13) is required to assess the thermodynamics of Co dissolution. And, there is no data for the Gibbs free energy of formation for the CuCo2O4 and AgCoO2 compounds based on the literature. Since reactions 9 and 12 proceed to completion, we could assume that the lowest Gibbs free energy of reaction could be 0 to find an approximation for the Gibbs free energy of other species. The Gibbs free energy was calculated to be −578 and −245 kJ/mol for CuCo2O4 and AgCoO2, respectively. The Gibbs free energy of reactions 11 and 14 is + 90 and +45 kJ/mol, calculated using . EquationEquation (18)(18)
(18) indicating that these reactions are not thermodynamically favorable. Alternatives for reactions 10 and 13 are proposed.
Based on the Gibbs free energies of alternative reactions (−265 and −133 kJ/mol), reactions 23 and 24 could describe Co dissolution in metal-catalyzed bioleaching, casting doubt on the reactions proposed by Zeng et al. (Citation2013). Co is trivalent in both intermediate complexes, and it is plausible that Fe2+ is the reductant for Co3+ to Co2+ reaction. The ORP increased over time, consistent with formation of Fe3+ (Zeng et al. Citation2012, Citation2013). Thus, the Fe redox cycle involved the microbial oxidation of Fe2+ as, well as the coupling between Fe2+ and Co3+ (Fe2+ → Fe3+ + e- and Co3+ + e → Co2+).
3.4.2.2. Zn-Mn batteries
The leaching of Mn3+ and Mn5+ requires reductive dissolution as Mn2+. The reaction by Niu et al. (Citation2016, Citation2015) cannot describe dissolution. The correct reactions and calculated Gibbs free energy for Cu-catalyst bioleaching of Zn-Mn batteries can be suggested as follow:
4. Perspectives on the bioleaching of batteries
Research indicates that bioleaching can be used for recovering metals from spent batteries, but low recovery, slow kinetics, and lack of optimization remain. Continuous H2SO4 and Fe2+/Fe3+ cycle may prove an efficient approach, but batch testing is indispensable for testing process parameters. The very low pulp densities are a major obstacle to piloting. Fungi produce carboxylic acids are tolerant to metals, and some can grow over a wide pH range. Many acidophilic bacteria and archaea are noted for extreme pH and resistance to metals. They produce acid from pyrite, other Fe-sulfides, or S0. In contrast, fungi require organic substrates. Mixed bacterial cultures may be the best. Extreme thermophiles have not been investigated. They have faster metabolism compared to mesophiles and moderate thermophiles, but fast reactions may not offset the energy required to maintain temperature. Fungal culture conditions for bioleaching are incompatible with bacteria and archaea. Culture control, exclusion of contaminants, and aseptic and sterile conditions are not feasible. Research to date is still exploratory, and some proposed reaction sequences are putative at best. Battery bioleaching has yet to test reactor configuration and develop design and control of upstream and downstream processes, scale-up, operating expenses, capital expenditures, and product recovery.
Supplemental Material
Download MS Word (348.8 KB)Disclosure statement
No potential conflict of interest was reported by the author(s).
Supplementary material
Supplemental data for this article can be accessed online at https://doi.org/10.1080/08827508.2022.2095376.
References
- Asadi, M., M. R. T. Mohammadi, F. Moosakazemi, M. J. Esmaeili, and M. Zakeri. 2018. Development of an environmentally friendly flowsheet to produce acid grade fluorite concentrate. Journal of Cleaner Production 186:782–98. doi:10.1016/J.JCLEPRO.2018.03.118.
- Asadi Dalini, E., G. Karimi, S. Zandevakili, and M. Goodarzi. 2021. A review on environmental, economic and hydrometallurgical processes of recycling spent lithium-ion batteries. Mineral Processing and Extractive Metallurgy Review 42 (7):451–72. doi:10.1080/08827508.2020.1781628.
- Asghari, I., S. M. Mousavi, F. Amiri, and S. Tavassoli. 2013. Bioleaching of spent refinery catalysts: A review. Journal of Industrial and Engineering Chemistry 19 (4):1069–81. doi:10.1016/J.JIEC.2012.12.005.
- Bahaloo-Horeh, N., and S. M. Mousavi. 2017. Enhanced recovery of valuable metals from spent lithium-ion batteries through optimization of organic acids produced by Aspergillus niger. Waste Management 60:666–79. doi:10.1016/j.wasman.2016.10.034.
- Bajpai, P., and V. Dash. 2012. Hybrid renewable energy systems for power generation in stand-alone applications: A review. Renewable and Sustainable Energy Reviews 16 (5):2926–39. doi:10.1016/J.RSER.2012.02.009.
- Bal, B., S. Ghosh, and A. P. Das. 2019. Microbial recovery and recycling of manganese waste and their future application: A review. Geomicrobiology Journal 36 (1):85–96. doi:10.1080/01490451.2018.1497731.
- Ballester, A., F. González, M. L. Blázquez, and J. L. Mier. 1990. The influence of various ions in the bioleaching of metal sulphides. Hydrometallurgy 23 (2–3):221–35. doi:10.1016/0304-386X(90)90006-N.
- Ballester, A., F. González, M. L. Blázquez, C. Gómez, and J. L. Mier. 1992. The use of catalytic ions in bioleaching. Hydrometallurgy 29 (1–3):145–60. doi:10.1016/0304-386X(92)90010-W.
- Belardi, G., R. Lavecchia, F. Medici, and L. Piga. 2012. Thermal treatment for recovery of manganese and zinc from zinc–carbon and alkaline spent batteries. Waste Management 32 (10):1945–51. doi:10.1016/J.WASMAN.2012.05.008.
- Bernardes, A., D. C. Espinosa, and J. A. Tenório. 2004. Recycling of batteries: A review of current processes and technologies. Journal of Power Sources 130 (1–2):291–98. doi:10.1016/J.JPOWSOUR.2003.12.026.
- Borja, D., K. A. Nguyen, R. A. Silva, J. H. Park, V. Gupta, Y. Han, Y. Lee, and H. Kim. 2016. Experiences and future challenges of bioleaching research in South Korea. Minerals 6 (4):128. doi:10.3390/min6040128.
- Boxall, N. J., K. Y. Cheng, W. Bruckard, and A. H. Kaksonen. 2018. Application of indirect non-contact bioleaching for extracting metals from waste lithium-ion batteries. Journal of Hazardous Materials 360:504–11. doi:10.1016/j.jhazmat.2018.08.024.
- Brandl, H., R. Bosshard, and M. Wegmann. 2001. Computer-Munching microbes: Metal leaching from electronic scrap by bacteria and fungi. Hydrometallurgy 59 (2–3):319–26. doi:10.1016/S0304-386X(00)00188-2.
- Calin, L., A. Catinean, M. Bilici, and A. Samuila. 2021. A corona-electrostatic technology for zinc and brass recovery from the coarse fraction of the recycling process of spent alkaline and zinc–carbon batteries. Journal of Cleaner Production 278:123477. doi:10.1016/j.jclepro.2020.123477.
- Cerruti, C., G. Curutchet, and E. Donati. 1998. Bio-Dissolution of spent nickel–cadmium batteries using Thiobacillus ferrooxidans. Journal of Biotechnology 62 (3):209–19. doi:10.1016/S0168-1656(98)00065-0.
- Chagnes, A., and B. Pospiech. 2013. A brief review on hydrometallurgical technologies for recycling spent lithium-ion batteries. Journal of Chemical Technology & Biotechnology 88 (7):1191–99. doi:10.1002/jctb.4053.
- Chakankar, M., U. Jadhav, and H. Hocheng. 2017. Assessment of bio-hydrometallurgical metal recovery from Ni-Cd batteries. 115:539–45. doi:10.2991/eesed-16.2017.75.
- Chandra, M., D. Yu, Q. Tian, and X. Guo. 2022. Recovery of cobalt from secondary resources: A comprehensive review. Mineral Processing and Extractive Metallurgy Review 43 (6):679–700. doi:10.1080/08827508.2021.1916927.
- Chen, L., L. Huang, C. Méndez-García, J. Kuang, Z. Hua, J. Liu, and W. Shu. 2016. Microbial communities, processes and functions in acid mine drainage ecosystems. Current Opinion in Biotechnology 38:150–58. doi:10.1016/j.copbio.2016.01.013.
- Dewulf, J., G. Van der Vorst, K. Denturck, H. Van Langenhove, W. Ghyoot, J. Tytgat, and K. Vandeputte. 2010. Recycling rechargeable lithium ion batteries: Critical analysis of natural resource savings. Resources, Conservation and Recycling 54 (4):229–34. doi:10.1016/J.RESCONREC.2009.08.004.
- Dey, S., G. C. Dhal, D. Mohan, and R. Prasad. 2018. Synthesis and characterization of AgCoo2 catalyst for oxidation of CO at a low temperature. Polyhedron 155:102–13. doi:10.1016/j.poly.2018.08.027.
- Dzombak, D., and F. M. M. Morel. 1986. Sorption of cadmium on hydrous ferric oxide at high sorbate/sorbent ratios: Equilibrium, kinetics, and modeling. Journal of Colloid and Interface Science 112 (2):588–98. doi:10.1016/0021-9797(86)90130-X.
- Ellis, B. L., K. T. Lee, and L. F. Nazar. 2010. Positive electrode materials for Li-ion and libatteries. Chemistry of Materials 23 (3):691–714. doi:10.1021/cm902696j.
- Escudero, M. E., F. González, M. L. Blázquez, A. Ballester, and C. Gómez. 1993. The catalytic effect of some cations on the biological leaching of a Spanish complex sulphide. Hydrometallurgy 34 (2):151–69. doi:10.1016/0304-386X(93)90032-9.
- Esmaeili, M., S. O. Rastegar, R. Beigzadeh, and T. Gu. 2020. Ultrasound-Assisted leaching of spent lithium ion batteries by natural organic acids and H2O2. Chemosphere 254:126670. doi:10.1016/j.chemosphere.2020.126670.
- Espinosa, D. C. R., A. M. Bernardes, and J. A. S. Tenório. 2004. An overview on the current processes for the recycling of batteries. Journal of Power Sources 135:311–19. doi:10.1016/J.JPOWSOUR.2004.03.083.
- Fergus, J. W. 2010. Recent developments in cathode materials for lithium ion batteries. Journal of Power Sources 195 (4):939–54. doi:10.1016/J.JPOWSOUR.2009.08.089.
- Fröhlich, S., and D. Sewing. 1995. The BATENUS process for recycling mixed battery waste. Journal of Power Sources 57 (1–2):27–30. doi:10.1016/0378-7753(95)02234-1.
- Ghassa, S., Z. Boruomand, M. Moradian, H. Abdollahi, and A. Akcil. 2015. Microbial dissolution of Zn-Pb sulfide minerals using mesophilic iron and sulfur-oxidizing acidophiles. Mineral Processing and Extractive Metallurgy Review 36 (2):112–22. doi:10.1080/08827508.2014.898302.
- Ghassa, S., M. Noaparast, S. Z. Shafaei, H. Abdollahi, M. Gharabaghi, and Z. Boruomand. 2017. A study on the zinc sulfide dissolution kinetics with biological and chemical ferric reagents. Hydrometallurgy 171. doi:10.1016/j.hydromet.2017.06.012.
- Ghassa, S., A. Farzanegan, M. Gharabaghi, and H. Abdollahi. 2020a. The reductive leaching of waste lithium ion batteries in presence of iron ions: Process optimization and kinetics modelling. Journal of Cleaner Production 262:121312. doi:10.1016/j.jclepro.202s0.121312.
- Ghassa, S., A. Farzanegan, M. Gharabaghi, and H. Abdollahi. 2020b. Novel bioleaching of waste lithium ion batteries by mixed moderate thermophilic microorganisms, using iron scrap as energy source and reducing agent. Hydrometallurgy 197:105465. doi:10.1016/j.hydromet.2020.105465.
- Ghassa, S., A. Farzanegan, M. Gharabaghi, and H. Abdollahi. 2021. Iron scrap, a sustainable reducing agent for waste lithium ions batteries leaching: An environmentally friendly method to treating waste with waste. Resources, Conservation and Recycling 166:105348. doi:10.1016/j.resconrec.2020.105348.
- Golmohammadzadeh, R., F. Faraji, and F. Rashchi. 2018. Recovery of lithium and cobalt from spent lithium ion batteries (LIBs) using organic acids as leaching reagents: A review. Resources, Conservation and Recycling 136:418–35. doi:10.1016/j.resconrec.2018.04.024.
- Guo, P., G. Zhang, J. Cao, Y. Li, Z. Fang, and C. Yang. 2011. Catalytic effect of Ag+ and Cu2+ on leaching realgar (As2s2). Hydrometallurgy 106 (1–2):99–103. doi:10.1016/J.HYDROMET.2010.12.006.
- Heydarian, A., S. M. Mousavi, F. Vakilchap, and M. Baniasadi. (2018). Application of a mixed culture of adapted acidophilic bacteria in two-step bioleaching of spent lithium-ion laptop batteries. Journal of Power Sources, 378 19–30. 10.1016/j.jpowsour.2017.12.009
- Horeh, N. B., S. M. Mousavi, and S. A. Shojaosadati. 2016. Bioleaching of valuable metals from spent lithium-ion mobile phone batteries using Aspergillus niger. Journal of Power Sources 320:257–66. doi:10.1016/J.JPOWSOUR.2016.04.104.
- Hu, X., A. Robles, T. Vikström, P. Väänänen, M. Zackrisson, and G. Ye. 2021. A novel process on the recovery of zinc and manganese from spent alkaline and zinc-carbon batteries. Journal of Hazardous Materials 411:124928. doi:10.1016/j.jhazmat.2020.124928.
- Huang, B., Z. Pan, X. Su, and L. An. 2018. Recycling of lithium-ion batteries: Recent advances and perspectives. Journal of Power Sources 399:274–86. doi:10.1016/j.jpowsour.2018.07.116.
- Ijadi Bajestani, M., S. M. Mousavi, and S. A. Shojaosadati. 2014a. Bioleaching of heavy metals from spent household batteries using Acidithiobacillus ferrooxidans: Statistical evaluation and optimization. Separation and Purification Technology 132:309–16. doi:10.1016/J.SEPPUR.2014.05.023.
- Ijadi Bajestani, M., S. M. Mousavi, and S. A. Shojaosadati. 2014b. Bioleaching of heavy metals from spent household batteries using Acidithiobacillus ferrooxidans: Statistical evaluation and optimization. Separation and Purification Technology 132:309–16. doi:10.1016/j.seppur.2014.05.023.
- Iwase, K., K. Sakaki, J. Matsuda, Y. Nakamura, T. Ishigaki, and E. Akiba. 2011. Synthesis and crystal structure of a Pr 5 Ni 19 superlattice alloy and Its hydrogen absorption–Desorption property. Inorganic Chemistry 50 (10):4548–52. doi:10.1021/ic200253w.
- Karaffa, L., E. Sándor, and E. Fekete. 2001. The biochemistry of citric acid of accumulation by aspergillus niger (A review). Acta Microbiologica Et Immunologica Hungarica 48 (3–4):429–40. doi:10.1556/AMicr.48.2001.3-4.11.
- Kim, M.-J., J.-Y. Seo, Y.-S. Choi, and G.-H. Kim. 2016. Bioleaching of spent Zn–Mn or Ni–Cd batteries by aspergillus species. Waste Management 51:168–73. doi:10.1016/J.WASMAN.2015.11.001.
- King, S., and N. J. Boxall. 2019. Lithium battery recycling in Australia: Defining the status and identifying opportunities for the development of a new industry. Journal of Cleaner Production 215:1279–87. doi:10.1016/J.JCLEPRO.2019.01.178.
- Klaus, S.-R. 2018. How batteries store and release energy: explaining basic electrochemistry. Journal of Chemical Education 95 (10):1801–10. doi:10.1021/acs.jchemed.8b00479.
- Lannoo, S., A. Vilas-Boas, S. M. Sadeghi, J. Jesus, and H. M. V. M. Soares. 2019. An environmentally friendly closed loop process to recycle raw materials from spent alkaline batteries. Journal of Cleaner Production 236:117612. doi:10.1016/j.jclepro.2019.117612.
- Le, M. N., and M. S. Lee. 2021. A review on hydrometallurgical processes for the recovery of valuable metals from spent catalysts and life cycle analysis perspective. Mineral Processing and Extractive Metallurgy Review 42 (5):335–54. doi:10.1080/08827508.2020.1726914.
- Li, L., J. Ge, F. Wu, R. Chen, S. Chen, and B. Wu. 2010. Recovery of cobalt and lithium from spent lithium ion batteries using organic citric acid as leachant. Journal of Hazardous Materials 176 (1–3):288–93. doi:10.1016/J.JHAZMAT.2009.11.026.
- Liu, C., J. Lin, H. Cao, Y. Zhang, and Z. Sun. 2019. Recycling of spent lithium-ion batteries in view of lithium recovery: A critical review. Journal of Cleaner Production 228:801–13. doi:10.1016/J.JCLEPRO.2019.04.304.
- Lobos, A. 2017. Bioleaching potential of filamentous fungi to mobilize lithium and cobalt from spent rechargeable Li-Ion batteries. USF Tampa Graduate Theses and Dissertations.
- Lopez, S., O. Akizu-Gardoki, and E. Lizundia. 2021. Comparative life cycle assessment of high performance lithium-sulfur battery cathodes. Journal of Cleaner Production 282:124528. doi:10.1016/j.jclepro.2020.124528.
- Mahandra, H., R. Singh, and B. Gupta. 2018. Recycling of Zn-C and Ni-Cd spent batteries using cyphos IL 104 via hydrometallurgical route. Journal of Cleaner Production 172:133–42. doi:10.1016/j.jclepro.2017.10.129.
- Meng, F., J. McNeice, S. S. Zadeh, and A. Ghahreman. 2021. Review of lithium production and recovery from minerals, brines, and lithium-Ion batteries. Mineral Processing and Extractive Metallurgy Review 42 (2):123–41. doi:10.1080/08827508.2019.1668387.
- Meshram, P., Abhilash, and B.D. Pandey. 2019. Advanced review on extraction of nickel from primary and secondary sources. Mineral Processing and Extractive Metallurgy Review 40 (3):157–93. doi:10.1080/08827508.2018.1514300.
- Mishra, D., D.-J. Kim, D. E. Ralph, J.-G. Ahn, and Y.-H. Rhee. 2008. Bioleaching of metals from spent lithium ion secondary batteries using Acidithiobacillus ferrooxidans. Waste Management 28 (2):333–38. doi:10.1016/J.WASMAN.2007.01.010.
- Moazzam, P., Y. Boroumand, P. Rabiei, S. S. Baghbaderani, P. Mokarian, F. Mohagheghian, L. J. Mohammed, and A. Razmjou. 2021. Lithium bioleaching: An emerging approach for the recovery of Li from spent lithium ion batteries. Chemosphere 277:130196. doi:10.1016/j.chemosphere.2021.130196.
- Mocellin, J., G. Mercier, J. L. Morel, P. Charbonnier, J. F. Blais, and M. O. Simonnot. 2017. Recovery of zinc and manganese from pyrometallurgy sludge by hydrometallurgical processing. Journal of Cleaner Production 168:311–21. doi:10.1016/j.jclepro.2017.09.003.
- Morioka, Y. 2001. State-Of-The-Art of alkaline rechargeable batteries. Journal of Power Sources 100 (1–2):107–16. doi:10.1016/S0378-7753(01)00888-6.
- Muguerra, H., C. Colin, M. Anne, M.-H. Julien, and P. Strobel. 2008. Topotactic synthesis, structure and magnetic properties of a new hexagonal polytype of silver cobaltate(iii) AgCoo2+δ. Journal of Solid State Chemistry 181 (11):2883–88. doi:10.1016/j.jssc.2008.07.031.
- Müller, T., and B. Friedrich. 2006. Development of a recycling process for nickel-metal hydride batteries. Journal of Power Sources 158 (2):1498–509. doi:10.1016/j.jpowsour.2005.10.046.
- Niu, Z., Q. Huang, J. Wang, Y. Yang, B. Xin, and S. Chen. 2015. Metallic ions catalysis for improving bioleaching yield of Zn and Mn from spent Zn-Mn batteries at high pulp density of 10%. Journal of Hazardous Materials 298:170–77. doi:10.1016/j.jhazmat.2015.05.038.
- Niu, Z., Q. Huang, B. Xin, C. Qi, J. Hu, S. Chen, and Y. Li. 2016. Optimization of bioleaching conditions for metal removal from spent zinc-manganese batteries using response surface methodology. Journal of Chemical Technology & Biotechnology 91 (3):608–17. doi:10.1002/jctb.4611.
- Ordoñez, J., E. J. Gago, and A. Girard. 2016. Processes and technologies for the recycling and recovery of spent lithium-ion batteries. Renewable and Sustainable Energy Reviews 60:195–205. doi:10.1016/J.RSER.2015.12.363.
- Pathak, A., R. Kothari, M. Vinoba, N. Habibi, and V. V. Tyagi. 2021. Fungal bioleaching of metals from refinery spent catalysts: A critical review of current research, challenges, and future directions. Journal of Environmental Management 280:111789. doi:10.1016/j.jenvman.2020.111789.
- Pollmann, K., S. Kutschke, S. Matys, S. Kostudis, S. Hopfe, and J. Raff. 2016. Novel biotechnological approaches for the recovery of metals from primary and secondary resources. Minerals 6 (2):54. doi:10.3390/min6020054.
- Provazi, K., B. A. Campos, D. C. R. Espinosa, and J. A. S. Tenório. 2011. Metal separation from mixed types of batteries using selective precipitation and liquid–liquid extraction techniques. Waste Management 31 (1):59–64. doi:10.1016/J.WASMAN.2010.08.021.
- Rezaei, H., S. Ziaedin Shafaei, H. Abdollahi, A. Shahidi, and S. Ghassa. 2022. A sustainable method for germanium, vanadium and lithium extraction from coal fly ash: Sodium salts roasting and organic acids leaching. Fuel 312:122844. doi:10.1016/j.fuel.2021.122844.
- Rogulski, Z., and A. Czerwiński. 2006. Used batteries collection and recycling in Poland. Journal of Power Sources 159 (1):454–58. doi:10.1016/J.JPOWSOUR.2006.02.034.
- Saneie, R., H. Abdollahi, S. Ghassa, D. Azizi, and S. Chehreh Chelgani. 2022. Recovery of copper and aluminum from spent lithium-Ion batteries by froth flotation: A sustainable approach. Journal of Sustainable Metallurgy 8 (1):386–97. doi:10.1007/s40831-022-00493-0.
- Santhiya, D., and Y.-P. Ting. 2005. Bioleaching of spent refinery processing catalyst using Aspergillus niger with high-yield oxalic acid. Journal of Biotechnology 116 (2):171–84. doi:10.1016/J.JBIOTEC.2004.10.011.
- Sayer, J. A., and G. M. Gadd. 1997. Solubilization and transformation of insoluble inorganic metal compounds to insoluble metal oxalates by Aspergillus niger. Mycological Research 101 (6):653–61. doi:10.1017/S0953756296003140.
- Sayilgan, E., T. Kukrer, G. Civelekoglu, F. Ferella, A. Akcil, F. Veglio, and M. Kitis. 2009. A review of technologies for the recovery of metals from spent alkaline and zinc–carbon batteries. Hydrometallurgy 97 (3–4):158–66. doi:10.1016/J.HYDROMET.2009.02.008.
- Sayilgan, E., T. Kukrer, N. O. Yigit, G. Civelekoglu, and M. Kitis. 2010. Acidic leaching and precipitation of zinc and manganese from spent battery powders using various reductants. Journal of Hazardous Materials 173 (1–3):137–43. doi:10.1016/J.JHAZMAT.2009.08.063.
- Shah, S. S., M. C. Palmieri, S. R. P. Sponchiado, and D. Bevilaqua. 2020. Environmentally sustainable and cost-effective bioleaching of aluminum from low-grade bauxite ore using marine-derived Aspergillus niger. Hydrometallurgy 195:105368. doi:10.1016/j.hydromet.2020.105368.
- Shi, J.-J., Y. Shi, Y.-L. Feng, Q. Li, W.-Q. Chen, W.-J. Zhang, and H.-Q. Li. 2019. Anthropogenic cadmium cycles and emissions in Mainland China 1990–2015. Journal of Cleaner Production 230:1256–65. doi:10.1016/j.jclepro.2019.05.166.
- Song, Y., Q. Huang, Z. Niu, J. Ma, B. Xin, S. Chen, J. Dai, and R. Wang. 2015. Preparation of Zn–Mn ferrite from spent Zn–Mn batteries using a novel multi-step process of bioleaching and co-precipitation and boiling reflux. Hydrometallurgy 153:66–73. doi:10.1016/J.HYDROMET.2015.02.007.
- Soria, M. L., J. Chacón, J. C. Hernández, D. Moreno, and A. Ojeda. 2001. Nickel metal hydride batteries for high power applications. Journal of Power Sources 96 (1):68–75. doi:10.1016/S0378-7753(00)00677-7.
- Sun, M., Y. Wang, J. Hong, J. Dai, R. Wang, Z. Niu, and B. Xin. 2016. Life cycle assessment of a bio-hydrometallurgical treatment of spent Zn-Mn batteries. Journal of Cleaner Production 129:350–58. doi:10.1016/j.jclepro.2016.04.058.
- Tanong, K., L.-H. Tran, G. Mercier, and J.-F. Blais. 2017. Recovery of Zn (II), Mn (II), Cd (II) and Ni (II) from the unsorted spent batteries using solvent extraction, electrodeposition and precipitation methods. Journal of Cleaner Production 148:233–44. doi:10.1016/j.jclepro.2017.01.158.
- Wang, J., B. Tian, Y. Bao, C. Qian, Y. Yang, T. Niu, and B. Xin. 2018. Functional exploration of extracellular polymeric substances (EPS) in the bioleaching of obsolete electric vehicle LiNixcoymn1-x-yO2 Li-ion batteries. Journal of Hazardous Materials 354:250–57. doi:10.1016/j.jhazmat.2018.05.009.
- Wu, W., X. Liu, X. Zhang, X. Li, Y. Qiu, M. Zhu, and W. Tan. 2019. Mechanism underlying the bioleaching process of LiCoo2 by sulfur-oxidizing and iron-oxidizing bacteria. Journal of Bioscience and Bioengineering 128 (3):344–54. doi:10.1016/J.JBIOSC.2019.03.007.
- Xin, B., W. Jiang, H. Aslam, K. Zhang, C. Liu, R. Wang, and Y. Wang. 2012. Bioleaching of zinc and manganese from spent Zn–Mn batteries and mechanism exploration. Bioresource Technology 106:147–53. doi:10.1016/j.biortech.2011.12.013.
- Xin, Y., X. Guo, S. Chen, J. Wang, F. Wu, and B. Xin. 2016. Bioleaching of valuable metals Li, Co, Ni and Mn from spent electric vehicle Li-ion batteries for the purpose of recovery. Journal of Cleaner Production 116:249–58. doi:10.1016/J.JCLEPRO.2016.01.001.
- Yun, L., D. Linh, L. Shui, X. Peng, A. Garg, M. L. P. LE, S. Asghari, and J. Sandoval. 2018. Metallurgical and mechanical methods for recycling of lithium-ion battery pack for electric vehicles. Resources, Conservation and Recycling 136:198–208. doi:10.1016/j.resconrec.2018.04.025.
- Zeng, G., X. Deng, S. Luo, X. Luo, and J. Zou. 2012. A copper-catalyzed bioleaching process for enhancement of cobalt dissolution from spent lithium-ion batteries. Journal of Hazardous Materials 199-200:164–69. doi:10.1016/j.jhazmat.2011.10.063.
- Zeng, G., S. Luo, X. Deng, L. Li, and C. Au. 2013. Influence of silver ions on bioleaching of cobalt from spent lithium batteries. Minerals Engineering 49:40–44. doi:10.1016/J.MINENG.2013.04.021.
- Zeng, X., J. Li, and N. Singh. 2014. Recycling of spent lithium-ion battery: A critical review. Critical Reviews in Environmental Science and Technology 44 (10):1129–65. doi:10.1080/10643389.2013.763578.
- Zhao, L., L. Wang, D. Yang, and N. Zhu. 2007. Bioleaching of spent Ni-Cd batteries and phylogenetic analysis of an acidophilic strain in acidified sludge. Frontiers of Environmental Science & Engineering in China 1 (4):459–65. doi:10.1007/s11783-007-0073-6.
- Zhao, L., D. Yang, and N. W. Zhu. 2008. Bioleaching of spent Ni–Cd batteries by continuous flow system: Effect of hydraulic retention time and process load. Journal of Hazardous Materials 160 (2–3):648–54. doi:10.1016/j.jhazmat.2008.03.048.
- Zheng, X., Z. Zhu, X. Lin, Y. Zhang, Y. He, H. Cao, and Z. Sun. 2018. A mini-review on metal recycling from spent lithium Ion batteries. Engineering 4 (3):361–70. doi:10.1016/j.eng.2018.05.018.
- Zhu, N., L. Zhang, C. Li, and C. Cai. 2003. Recycling of spent nickel–cadmium batteries based on bioleaching process. Waste Management 23 (8):703–08. doi:10.1016/S0956-053X(03)00068-0.