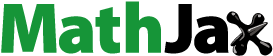
ABSTRACT
Accidental contact between hot melt and cold water poses fatal hazard in several industries. Vapor explosion during melt-water contact in nuclear power plant accident can result in catastrophic containment failure. The fast transient phenomena as vapor explosion is not comprehensively understood despite several advances in research. It is not clear why certain parameters of melt and water exhibit differences in fragmentation behavior. To examine the influential parameters, we perform a series of experiments. The interactions between melt and water is visualized by high-speed video and X-ray radiograph.
Introduction
Interaction between a hot liquid and a cold liquid may lead to intense vaporization of the cold (volatile) medium at a rapid pace, ultimately forming a vapor explosion. The disruptive potential of a vapor explosion is at the epicenter of safety assessment in various industries including, metallurgical industries, paper production industries, nuclear reactor industries, smelting industries, and liquid natural gas industries. More specifically, in nuclear power plants, during the late stages of a severe accident, it is considered that a large mass of molten corium (which in general case represents a mixture of molten fuel ((U, Zr) O2-x) and structure materials (steel)) may relocate into a subcooled water pool, raising the risk of vapor explosion. For instance, upon failure of the reactor pressure vessel (RPV) during a severe accident, molten corium is expected to discharge in the form of a melt jet into a subcooled water pool under the RPV. The melt jet undergoes breakup as result of interfacial Rayleigh-Taylor and Kelvin-Helmholtz instabilities into molten droplets typically in the range of several millimeters forming a so-called premixture, as illustrated in . The melt droplets undergo film boiling which restricts direct contact between melt and water. Following a triggering event (exposure to a pressure wave or spontaneous-triggering due to transition in boiling regimes) the vapor film surrounding a melt droplet is destabilized and melt-water direct contact is established (), leading to an initial vapor explosion and fine fragmentation of the melt droplet. The vapor explosion and subsequent rapid heat transfer between the fine fragments and water produces a high pressure shock wave that destabilizes the vapor films surrounding the adjacent melt droplets in the premixture thereby escalating the process. () [Citation1].
Figure 1. Sequential visuals depicting (a) melt jet penetrating into water pool, (b) jet breakup into droplets, (c) explosion triggering, (d) explosion propagation, and (e) escalation [Citation1].
![Figure 1. Sequential visuals depicting (a) melt jet penetrating into water pool, (b) jet breakup into droplets, (c) explosion triggering, (d) explosion propagation, and (e) escalation [Citation1].](/cms/asset/1a05a43e-7a00-41eb-96be-f27c13826f56/ueht_a_1505786_f0001_oc.jpg)
In general, the fine fragmentation of a droplet could be the result of either hydrodynamic or thermal mechanism. The hydrodynamic mechanism is jointly driven by surface tension and shear force due to the relative flow of the droplet with respect to surrounding water, typically limited by a critical Weber number:
Whereis the density of water,
is the melt-water relative velocity,
is the droplet diameter, and σ is the surface tension of the droplet. The thermal mechanism is largely related to the destabilization of the vapor film that surrounds the melt droplet so that direct contact between water and melt is established, driving the fine fragmentation of the melt droplet [Citation2].
The phenomena of melt and water interaction (FCI) is extensively investigated to understand the conditions that could trigger a vapor explosion during melt and water contact, the mechanism related to the fine fragmentation of melt and the influential parameters that promote or inhibit vapor explosion. Notably, several insights are achieved, for example, the KROTOS tests [Citation3] have shown that melt materials can influence the strength of vapor explosion. Alumina (Al2O3) seemed to produce violent explosions compared to that of a prototypic composition of corium (UO2–ZrO2). Further alumina melt exhibited a characteristic of spontaneous triggering for vapor explosion while the corium melt had to be externally triggered to initiate a vapor explosion. The TROI tests [Citation4] have also shown that Zirconia (ZrO2) melt can also undergo a strong spontaneously triggered vapor explosion. Due to the complex mechanisms involved in such a fast transient phenomena it is hard to interpret the reasons why certain materials exhibit a characteristic of spontaneous triggering for vapor explosion and the low energetics of a prototypic corium composition. Ultimately, an understanding of material influence on vapor explosion is necessary. The KROTOS and TROI experiments performed at a relatively large scale is also complemented by small scale experiments that allow to develop an in-depth understanding on the various mechanisms involved in vapor explosion [Citation2, Citation5–Citation7]. Analysis of the experimental data points out to deformation of melt surface as a result of Rayleigh-Taylor instabilities followed by the fine fragmentation of melt. The actuality of perceiving small-scale experimental observations in large-scale experiments is however not logical where the droplets existing in the flow stochastically have different sizes and therefore considerable differences in heat transfer rates.
It is clear from the aforementioned that the understanding of vapor explosion is insufficient, due to difficulties in experimentation and instrumentation. Further research on melt-water interaction is a necessity to better understand the phenomena and provide complementary knowledge useful to interpret the observations in large-scale experiments. The present study developed a well-controlled test approach to obtain the sequential anatomy of a vapor explosion, which provided high-quality data on the intense vaporization and melt disintegration during an explosive melt-water interaction. Followed by a brief introduction of the test facility and experimental methodology, we show the dynamic behavior of a melt droplet and its surrounding vapor film during the process of the droplet falling into a water pool. Further, we discuss the importance of influential parameters that affect the course of the explosion and fragmentation mechanisms.
Experimental techniques
shows the schematic of the test facility named as Micro Interactions in Steam Explosion Experiments (MISTEE). The melt generation system is an induction furnace (260 V, 40 A). Around ≈ 1 to 2 g of the mixture of binary oxides (WO3-CaO or WO3-ZrO2) is loaded in a tungsten crucible which consists of a hole at the center of the bottom of the crucible. The crucible is housed inside a chamber where argon gas is purged to maintain inert conditions. A well-controlled pneumatic plug system is utilized to cover the bottom hole of the crucible during melt preparation. A C-type thermocouple is mounted from the inside of the crucible to measure the melt-temperature. On achieving desired temperature of WO3-CaO or WO3-ZrO2 melt in the crucible, the pneumatic plug is released to uncover the bottom hole in the crucible so that the droplet falls by gravity into a rectangular plexi-glass tank (180 mm × 130 mm × 150 mm) containing water. A weak pressure pulse generated by an external triggering system aligned underneath the water tank disturbs the discharged melt droplet underwater. The pressure wave generating system is a piston set-up. A trigger hammer driven by rapid discharge of a capacitor bank (three capacitors of 400 Vdc and 4700 mF each) impacts on the piston to generate the pressure pulse. The interactions between the melt and water is recorded by a fast synchronous visualization system that is aligned with a capability to record simultaneously X-ray and photographic image. It consists of a CMOS digital camera (Redlake HG50LE), with an acquisition rate up to 20,000 fps for photography; and a continuous X-ray source tube (Philips MCN 321 – max. 320 keV), an X-ray converter and an image intensifier coupled to a high speed camera (Lightning RDTPlus camera), for radiographic imaging with an acquisition rate up to 8000 fps. Binary mixtures of WO3-CaO (75:25 mol %) and WO3-ZrO2 (74:26 mol %) at eutectic mass composition with a melting point of 1135°C and 1231°C, respectively, were chosen as the melt materials for MISTEE tests. The materials were selected considering the relatively high temperatures achievable in MISTEE furnace and also based on the resemblance in debris morphology between the simulant and prototypic materials after fragmentation in water [Citation8]. , presents the thermophysical properties of the materials used in the current work compared to that of prototypic corium (UO2–ZrO2).
Table 1. Thermal and physical properties of binary oxide simulant materials compared to corium composition.
Experimental results and discussion
Visual analysis of the dynamic behavior of melt interaction with water
A series of experiments with molten binary oxide mixture of WO3-CaO at eutectic composition is performed (). Driven by gravity a molten droplet of WO3-CaO or WO3-ZrO2 falls into a transparent tank filled with water. Once the melt droplet penetrates the water pool surface it emerges with a long trail of non-condensable gas which detaches from the droplet rear completely by 38 ms (). After an initial acceleration into the water pool, the droplet starts to decelerate and attains terminal velocity at ≈ 100 ms (). As the droplet descends further into the water pool, the vapor bubble enshrouding the droplet remains wobbly, but no detachment of bubbles from the droplet rear is observed. However, the vapor film thickness seems to undergo periodic oscillations which can be inferred from the aspect ratio (the ratio of the distance between the vertical peripheries and the horizontal peripheries) of the bubble over the quench period (). Hydrodynamic fragmentation is expected to occur for a Weber number above the value of 18 [Citation10]. With a Weber number ≈ 50 during the initial stages of quenching (for current experiments), it can be assumed that development of oscillations and hydrodynamic decomposition of the melt droplet into a few larger fragments is probable. However, within 45 ms into the water pool, the droplet attains a Weber number range of ≤ 7 and seems to be stable without any decomposition. A droplet elliptical in shape with a wobbling interface is observed to evolve in the water pool (). To investigate the thermal explosion phenomena, the droplet is exposed to the pressure wave only after ≈ 300 ms at a Weber number range of ≤ 10.
Table 2. Test parameters for WO3-CaO melt.
Figure 4. Molten WO3-CaO droplet: (a) displacement and velocity and (b) aspect ratio during quench in water pool. (Mmelt ≈ 1.3 g, ∆Tsup ≈ 115 K, and ∆Tsub ≈ 79 K).
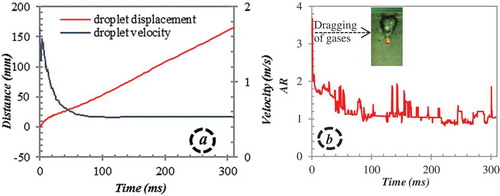
Figure 5. Simultaneous images of videography and X-ray radiography recorded for a single droplet of WO3-CaO undergoing explosion in water (Mmelt ≈ 1.2 g, ∆Tsup ≈ 116 K, and ∆Tsub ≈ 77 K).
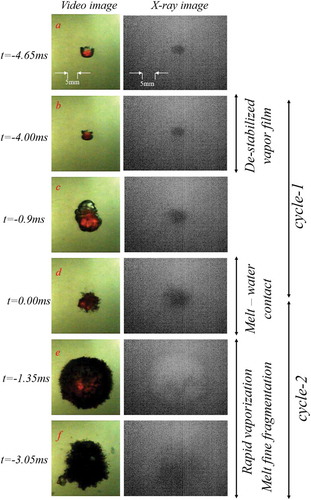
At ≈ 200 mm into the water pool the vapor film (black colored region in surrounding the melt droplet (red-colored region in ) is destabilized by an external pressure wave (). Upon destabilization of the vapor film a partial melt-water contact is initiated at the surface of the melt droplet resulting in melt swelling and subsequent vapor film growth during a period of up to 3.2 ms (-c). The over grown vapor film then collapses within 0.8 ms due to condensation leading to complete melt-water contact () followed by fine fragmentation of the melt droplet and subsequent explosive evaporation of water (-f). Such a fine fragmentation mechanism (commonly referred to as thermal fragmentation) can be related only to a hydrodynamic mechanism in the order of a catastrophic breakup, which can possibly occur at high Weber numbers typically at the range > 1300. Droplet displacement in the water pool as well as the aspect ratio of the droplet exposed to pressure wave is depicted in (-b). The average velocity of the droplet is 0.56 m/s and the droplet seems to be nearly spherical prior to the disturbance by pressure wave.
Figure 6. Dynamic characteristics of WO3-CaO melt droplet on exposure to a pressure wave: (a) droplet displacement, (b) droplet aspect ratio, (c) vapor and melt interrelated diameter history, (d) vapor interface acceleration, (e) pressure inside the vapor bubble, and (f) work done by the expanding vapor bubble (Mmelt ≈ 1.2 g, ∆Tsup ≈ 116 K, and ∆Tsub ≈ 77 K).

A process of bubble growth and collapse can be observed in . The equivalent diameter (D) of the vapor bubble projected area shows an initial growth rate of up to 2 times the initial diameter (D0) of the droplet on submission to the pressure pulse (−2.5 ms < t < 0 ms). On direct contact of water with melt (t = 0 ms) the diameter of the vapor bubble increases up to four times the initial diameter (0 ms < t < 1 ms). During this period, the vapor bubble interface accelerates at a of 170 000 m/s2 (). After this period, the bubble starts to decelerate (1 ms < t < 3 ms). A qualitatively similar pattern for the melt interrelated dynamics is observed. A process of initial melt deformation or melt swelling on submission to the pressure pulse (−2.5 ms < t < 0 ms), followed by an intense increase in the melt surface area (t > 0 ms) where the melt droplet is disintegrated into several micrometer sized fragments and dispersed in the water pool. Further, an estimation of the pressure inside the vapor bubble can be made using the classic Rayleigh-Plesset equation (Equation 2) for bubble dynamics [Citation6]. Pressure peaks in the range of 1.8 MPa during the period of melt disintegration (1 ms < t < 3 ms) is thus estimated ().
The work done by the expanding bubble (W) can be estimated by calculating the internal pressure using the Rayleigh-Plesset equation (Equation 3). The accumulative work is thus estimated as approximately 1.4J ().
Where, is the bubble radius,
the bubble velocity,
the bubble acceleration,
the density,
the surface tension, and
the dynamic viscosity. An experimental quantification of the mechanisms that initiate the fine fragmentation of melt during the thermal process is far from realization considering the short time spans. However, by utilizing the unique features of simultaneous visualization capabilities at MISTEE facility, it is substantiated in [Citation6] that the explosion energy conversion efficiency depends upon the rate at which the melt droplet can deform during the initial phase of the interaction or in other words the ability of the melt droplet to deform on exposure to a pressure wave. The insight was based on the data acquired by performing several experiments with single droplets of molten tin that underwent an explosive interaction. A rationale to the observation of melt deformation is the growth rate of instabilities on the melt surface due to the dynamic pressure differences. To explore further the melt deformation mechanism during the initial phase of the interaction we compare results obtained from current experiments. Here we define the melt deformation rate (MD*) as the ratio of melt projected area prior exposure to pressure wave (e.g. see , t = −4.65 ms) to the melt projected area during the initial phase of melt-water direct contact (e.g. see , t = 0 ms). The specific observation is made possible by acquisition of simultaneous X-ray visuals that show the evolution of melt during the intense interactions. The effect of melt deformation rate on the estimated thermal to mechanical conversion ratio (
) for current experiments with WO3-CaO is presented in . The results indicate an increased conversion ratio for conditions related to an increased melt deformation rate. Here, the thermal to mechanical conversion ratio is represented by:
Where, the total available thermal energy () within the melt drop is estimated by:
Thermal fragmentation theory
The mechanism of thermal fine fragmentation has been extensively studied in the past decades. Considering the complexities involved with such fast transient multiphase phenomena, visual information of the process is predominantly required to understand the mechanisms involved. Based on the visual evidences, obtained by flash X-ray and regular photography, it is proposed in [Citation11] that, on destabilization of the vapor film, fine filaments of melt protrude and the drop surface becomes highly convoluted establishing quasi contact between water and melt at localized region driving the fine fragmentation process (). Another classical fragmentation theory, assumes that, that the vapor film surrounding the melt droplet collapses on exposure to a pressure wave and as a result of Rayleigh-Taylor instabilities that arise on the interface, micro jets of water penetrate into the melt droplet and vaporize causing disintegration of the melt droplet similar to what can be observed in cavitation phenomena [Citation12]. ().
Figure 8. Thermal fragmentation models proposed in [Citation11] (a) and [Citation12] (b).
![Figure 8. Thermal fragmentation models proposed in [Citation11] (a) and [Citation12] (b).](/cms/asset/6d651de2-c614-4e2f-8951-3b847e1e1ab2/ueht_a_1505786_f0008_b.gif)
According to [Citation12] the water micro jets penetration depth (P*) into liquid melt due to the occurrence of Rayleigh-Taylor instabilities on the vapor-melt interface can be estimated by:
where the penetration velocity () can be estimated from Bernoulli’s equation for invicid fluid:
The penetration time scale can be associated with the fastest growing wavelength for the Rayleigh-Taylor instability (
) and hence can be estimated by:
Hence, by combining Equations 7 and 8, the penetration depth (P*) can be estimated by:
Based on Equation 10, penetration depth of water jets into melt as a result of the Taylors instabilities caused by transient pressure difference in the vapor-melt interface is shown in for WO3-CaO melt. For a vapor bubble pressure of 370 KPa, a penetration depth of up to 0.3 mm and a jet velocity of up to 3 m/s can be estimated. An experimental quantification of the mechanisms that initiate the fine fragmentation of melt during the thermal process is far from realization considering the short time spans.
Figure 9. Penetration depth for water jets induced by Rayleigh-Taylor instabilities on the melt droplet as a function of the pressure difference when subject to an external pressure wave based on Equation 10.
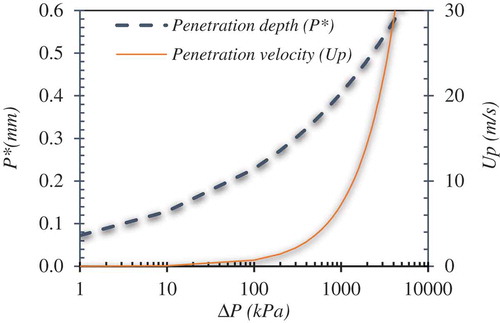
Effect of binary-oxide material
The use of different binary oxide materials have shown important differences in debris formation behavior during melt and water interactions without explosion [Citation13]. The experiments with small scale melt jets of WO3- ZrO2 have shown significant stress relief characteristics that the material can avoid fracture during solidification. This characteristic is largely speculated to be a result of material properties including a larger degree of thermal expansion (). It is instructive to note that the material physical properties are not comprehensively available elsewhere except for density and surface tension [Citation9]. However, since it could be worthwhile to compare the materials WO3-CaO and WO3-ZrO2 with almost similar ranges of melt density and surface tension experiments were conducted with WO3-ZrO2 (). Time sequence snapshots of molten WO3-ZrO2 undergoing vapor explosion in subcooled water is shown in . A mechanistically similar process of multiple growth and collapse of the vapor film is observed (). The diameter of the vapor bubble and the rates of melt deformation when exposed to a pressure wave seem to be well within the range predicted for WO3-CaO under similar conditions. In general, the results seem to be consistent with the results obtained with WO3-CaO melt ( and ). Since the material properties needed to estimate the internal thermal energy of WO3-ZrO2 is not comprehensively measured, the energy conversion ratio is not estimated at this point. However, it can be qualitatively seen that the mechanism of fine fragmentation is similar to that of the observations with WO3-CaO melt.
Table 3. Test parameters for WO3-ZrO2 melt.
Figure 10. Density (a) and surface tension (b) of WO3-CaO and WO3-ZrO2 melt as a function of melt temperature [Citation9].
![Figure 10. Density (a) and surface tension (b) of WO3-CaO and WO3-ZrO2 melt as a function of melt temperature [Citation9].](/cms/asset/8f5fa8e7-3eb9-437e-94cb-81e17927e418/ueht_a_1505786_f0010_oc.jpg)
Effect of melt superheat
The general notion in vapor explosion research is that a higher melt superheat can result in a stronger vapor explosion. A larger melt droplet superheat implies a larger thermal energy available within the droplet that can induce high heat transfer rates. However, the model implemented for thermal fragmentation in the vapor explosion code such as Texas does not include the effect of melt superheat [Citation14]. Here the rate of melt fine fragmentation on exposure to a pressure wave is given by:
where, is the mass of the initial melt droplet,
is the ambient pressure,
is the threshold pressure required to induce vapor film collapse,
is the melt droplet initial radius,
is the factor for coolant void fraction,
is the available fragmentation time, and C is a constant.
Further, to include the effect of melt surface solidification during vapor explosion triggering, a correlation for fragmentation rate is developed in [Citation15] by taking into account the effect of the melting point of the material and the rigidity of the melt surface to neutralize the growth of instabilities. Here, the fragmentation rate (ΓSS) is estimated by:
Where, is the Biot number,
is the Young’s modulus, and
is the coefficient for thermal expansion. For the improvement and validation of the existing models, an experimental analysis of separate effects is essential.
In general, the melt surface tension or the solidification trends (formation of crust layer) exhibited by the droplet prior exposure to pressure wave are important parameter that determine the growth rate of instabilities on the melt interface. To explore the effect of melt superheating on the mechanism of melt deformation during the initial phase of the interaction, we compare results obtained from the experiments with varied degree of superheating. Current experimental results show that the melt deformation ratio decreases at a lower melt superheat indicating that the growth of instabilities on the melt interface could be inhibited (). Furthermore, the role of melt superheat on the growth of instabilities deems support from the significant changes observed in the time scale for bubble deformation (∆tdeformation: time difference between initial bubble deformation and direct melt-water contact) () as a function of melt superheat. Given the differences in the melt properties specifically melt surface tension in the range of ≈ 16% for a change in melt superheat of ≈ 200 K (). The rationale is increased viscosity at low melt superheat that results in a lower heat flux and resilience to interface instabilities.
The thermal fragmentation time scale (∆tfragmentation) which corresponds to the time difference between the initiation of melt water mixing and completion of fine fragmentation into several sub micrometer size fragments is shown as a function of melt superheat in . Since it can be rather inconsistent when we consider the time at which cloud of fragments are observed, we consider here the time difference between initiation of melt-water mixing (t = 0 ms in ) and the time required for the completion of second cycle of bubble growth and collapse (t = 2.3 ms in ). A wide spectrum in the fragmentation time scale of ≈ 1.2 to 2.5 ms can be inferred from the results which is rather higher than the fragmentation time scale of 0.6 ms to 1.2 ms inferred from Ciccareli-Frost experiments with tin drops at varied melt-water relative velocities [Citation2]. However, a general trend of an increase in fine fragmentation time at an increased superheat is observed which is also consistent with the observations made in [Citation16], where a larger superheat tends to involve multiple cycles of explosion. The observations indicate that a larger fraction of the melt can be involved in the vapor explosion at a higher degree of melt superheat.
Fragment analysis
The particles collected from the experiments with WO3-CaO melt experiments were sieved for size distribution by subjecting to a set of sieve screens in the range between 38 µm and 1700 µm. Considering the very micron size range of the debris it was not possible to collect the debris appropriately in most of the cases. However, it was obtained for some experiments (Run ID# STe 126 and Run ID# STe 130). Typical, mass averaged size distribution of fragmented debris is shown in . Here the mass median particle diameter is approximately 200 µm, which in general depicts the extensive fragmentation rates of melt droplet. According to the data from hydrodynamic fragmentation experiments with gallium (Tmp = 30°C, ρ ≈ 6095 kg/m3) drops, a mean fragment diameter of ≈ 200 µm is achieved only at an initial Weber number range > 2500 [Citation17]. Data on debris size acquired from single droplet thermal fragmentation experiments is rather scarce. However, the data available from [Citation18] for molten silicon (Tmp = 1414°C, ρ ≈ 2600 kg/m3) droplets and from [Citation5] for molten tin (Tmp = 272°C, ρ ≈ 6734 kg/m3) which underwent fine fragmentation in high subcooling conditions, is compared with the current experimental data. Remarkably a close agreement between the debris sizes of molten silicon and WO3-CaO can be inferred though the density of WO3-CaO is much higher compared to silicon. Molten tin however seemed to generate larger fragments (mean particle diameter ≈ 600 µm). An examination of KROTOS – alumina (Tmp = 2072°C, ρ ≈ 2800 kg/m3) debris (fine fragmented particles) has shown that the mean diameter is in the range of ≈ 75 µm [Citation3]. A comparatively smaller mean particle diameter of alumina melts can plausibly be related to the larger internal energy available within the droplets. Furthermore, the debris samples acquired from WO3-CaO melt experiments were subject to scanning electron microscopy (SEM) analysis. The micro-structural view of the debris collected after thermal fragmentation of the melt droplet shows spherical, sharp edged and elongated morphologies (). Micro porosity is observed at localized regions of the debris indicating solidification shrinkage effects and failure of the interdendritic feeding.
Concluding remarks
In this article, the mechanism of vapor explosion is experimentally investigated. A series of experiments with a binary oxide melt composition of WO3-CaO and WO3-ZrO2 to simulate the system of UO2-ZrO2 has been conducted at the MISTEE facility at a relatively high temperature. The simultaneously acquired high resolution video as well as X-ray images reveal several insights on the melt droplet deformation mechanisms due to various instabilities and the disintegration of the melt droplets into fragments ranging between a few micrometers. Based on this visual investigation, it is observed that the use of different binary oxide materials have shown qualitative similarities in the progress of a vapor explosion. It is also identified that the melt superheat can have substantial effect on the fine fragmentation of melt. At a higher melt superheat the intensity of explosion can be expected to increase. At a low melt superheat, the surface tension forces resiliate the growth of instabilities on the melt interface. Very fine fragments of melt are produced as result of the vapor explosion. A mass median fragment diameter of ≈ 200 µm is estimated by conventional sieving of the fine fragments acquired after the interaction. Spontaneously triggered vapor explosions have not been observed even with experimental conditions involving a high melt superheat up to 350 K and a high subcooling up to 85 K. The results indicate the stochastic nature of spontaneously triggered vapor explosions. The use of different materials as corium simulants in vapor explosion research clearly indicates the difference in vapor explosion triggering mechanisms. To clarify the triggering mechanism it is critical to perform FCI experiments with a range of materials at higher melt temperatures (> 2000°C). It is thus important to exploit the unique features of the MISTEE facility to explore the explosion behavior of high temperature melts.
Acknowledgments
This study was made possible by the supports from Swedish research program APRI, and Swiss nuclear authority ENSI. The authors thank Per Skold, Technician at the KTH-NPS Laboratory for his technical support in the experimental setup. The discussions with the MSWI team members are gratefully acknowledged.
References
- L. Manickam, P. Kudinov, W. Ma, S. Bechta, and D. Grischenkov, “On the influence of water subcooling and melt jet parameters on debris formation,” Nucl. Eng. Des., vol. 309, pp. 265–276, 2016.
- H. S. Park, R. C. Hannson, and B. R. Sehgal, “Fine fragmentation of molten droplet in highly subcooled water due to vapor explosion observed by X-ray radiography,” Exp. Thermal Fluid Sci., vol. 29, pp. 351–361, 2005.
- I. Huhtiniemi and D. Magallon, “Insight into steam explosions with corium melts in KROTOS,” Nucl. Eng. Des., vol. 204, pp. 391–400, 2001.
- J. H. Song, J. H. Kim, S. W. Hong, B. T. Min, and H. D. Kim, “The effect of corium composition and interaction vessel geometry on the prototypic steam explosion,” Ann. Nucl. Energy, vol. 33, pp. 1437–1451, 2006.
- Y. Abe, H. Nariai, and Y. Hamada, “The trigger mechanism of vapor explosion,” J. Nucl. Sci. Technol., vol. 39, pp. 845–853, 2002.
- R. C. Hannson, H. S. Park, and T. N. Dinh, “Simultaneous high-speed digital cinematographic and X-ray radiographic imaging of an intense multi-fluid interaction with rapid phase changes,” Exp. Thermal Fluid Sci., vol. 33, pp. 754–763, 2009.
- R. C. Hannson, T. N. Dinh, and L. Manickam, “A study of the effect of binary oxide materials in a single droplet vapor explosion,” Nucl. Eng. Des., vol. 264, pp. 168–175, 2013.
- P. Kudinov, A. Karbojian, W. Ma, and T. N. Dinh, “The DEFOR-S experimental study of debris formation with corium simulant materials,” Nucl. Technol., vol. 170, pp. 219–230, 2010.
- C. Journeau, “PLINIUS FP6 transnational access to the prototypic corium platform PLINIUS,” Research Report of EURATOM 6th Framework Programme, Contract Number FP6-036403. Cadarache, France, 2010.
- E. Matsuo, Y. Abe, K. Chitose, K. Koyama, and K. Itoh, “Study on jet breakup behavior at core disruptive accident for fast breeder reactor,” Nucl. Eng. Des., vol. 238, pp. 1996–2004, 2008.
- G. Ciccarelli and D. L. Frost, “Fragmentation mechanisms based on single drop steam explosion experiments using flash X-ray radiography,” Nucl. Eng. Des., vol. 146, pp. 109–132, 1994.
- M. L. Corradini and B. J. Kim, “Modeling of small-scale single droplet fuel coolant interactions,” Nucl. Sci. Eng., vol. 98, pp. 16–28, 1988.
- L. Manickam, S. Bechta, and W. Ma, “On the fragmentation characteristics of melt jets quenched in water,” Int. J. Multiphase Flow, vol. 91, pp. 262–275, 2017.
- J. Tang and M. L. Corradini, Modeling of the Complete Process of One-Dimensional Vapor Explosions, Madison: University of Wisconsin, 1993.
- X. Cao, Y. Tobita, and S. Kondo, “A thermal fragmentation model induced by surface solidification,” J. Nucl. Sci. Technol., vol. 39, pp. 628–636, 2002.
- E. Kouraytem, Q. Li, and S. T. Thoroddsen, “Formation of microbeads during vapor explosion of fields metal in water,” Phys. Rev. E, vol. 93, pp. 1–6, 2016.
- B. E. Gelfand, “Droplet breakup phenomena in flows with velocity lag,” Prog. Energy Combustion Sci., vol. 22, pp. 201–265, 1996.
- L. S. Nelson, et al., “Steam explosions of single drops of molten silicon rich alloys,”. Proceedings of the Ninth International Ferro alloys Congress (INFACON 9), Quebec City, June 3–6, 2001.