ABSTRACT
This paper investigates the effect of the combined passive technique on heat transfer enhancement, friction factor, and thermal performance of a double-tube heat exchanger fitted with differently configured turbulators and using Alumina nanofluid. The performance parameters are studied for fixed flow rate (Re = 2500) of water at constant heat flux in the inner tube (hot fluid) and varying flow rates (500≤ Re≤5000) of Alumina nanofluid (volume concentrations: 0.05–0.15%) flowing in the outer tube (cold fluid). The configurations tested are a peripherally V-cut twisted tape (Twist Ratio = 20, 13.3, and 9.8) and a propeller turbulator (Number of propellers: 6, 8, and 10). The results show increased Nusselt number by 22.4% and 29.43%, increased Thermal Performance Factor by 1.25 and 1.33, respectively, for decreased twist ratio and increased number of propellers and volume concentration of Alumina nanofluid. The peripherally V-cut twisted tape (TR = 9.8) and propeller turbulator (Number of propellers = 10) with 0.15% volume concentrations of Alumina nanofluid combination give better performance, with a slight penalty in pressure drop. The correlations for the Nusselt number and friction factor are developed from the experimental data, which are fairly in good agreement with the experimental data.
Graphical abstract
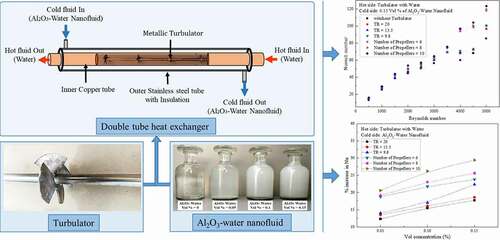
Acknowledgments
This work is supported by the Vision Group on Science and Technology (VGST), State Government of Karnataka, India, for the funding granted under the KFIST-L1 scheme (GRD No: 476).
Nomenclature
Cp | = | Specific heat, J kg−1K−1 |
d | = | Diameter, m. |
D | = | Tape width, m |
f | = | friction factor |
h | = | heat transfer coefficient, W m−2 k−1 |
H | = | Pitch length of tape, m |
K | = | Thermal conductivity, W m−1k−1 |
L | = | Length, m. |
n | = | Sample size |
Nu | = | Nusselt number |
Pr | = | Prandtl number |
Q | = | Heat transfer |
Re | = | Reynolds Number |
T | = | Temperature, O.C. |
U | = | Uncertainty |
V | = | Velocity, m s−1 |
X | = | Sample mean |
ΔP | = | Pressure Drop, psi or bar |
Greek/Roman/Latin Letters | = | |
Ρ | = | Density, kg m−3 |
μ | = | Dynamic viscosity, kg-m s−1 |
ϕ | = | Volume concentration |
σ | = | Standard deviation |
Subscripts | = | |
i | = | inlet |
o | = | outlet |
c | = | cold fluid |
h | = | hot fluid |
f | = | fluid |
m | = | mass |
nf | = | nanofluid |
P | = | Particle |
W | = | Water |
fhot | = | hot side friction factor |
fcold | = | cold side friction factor |
NP | = | Number of propellers |
Abbreviations | = | |
DTHE | = | Double Tube Heat Exchanger |
ID | = | Inner Diameter |
LMTD | = | Logarithmic Mean Temperature Difference |
OD | = | Outer Diameter |
TPF | = | Thermal Performance Factor |
TR | = | Twist Ratio |