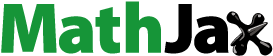
ABSTRACT
Embrittlement of steels and alloys in contact with hydrogen gas under pressure is a key problem in metallurgy with important implications for a future energy economy based on hydrogen. Here we report stress–strain measurements recorded under 200 MPa (∼30,000 PSI) hydrogen gas pressure to evaluate the resistance of MP35N to embrittlement. We find that MP35N with a tensile strength of more than 1800 MPa does not suffer any strength loss, retains a significant amount of ductility and hence appears to be highly resistant to hydrogen embrittlement even under elevated stress when exposed over a time-scale of hours. This exceptional resistance to H-embrittlement seems to be unique among all high-performance steels and alloys of comparable strength and bears on the use of this material for high pressure H2 research devices and storage applications.
It has become evident that hydrogen gas (H2) will be a key component in a future carbon-free energy economy. It is the most abundant element in universe, it is the cleanest fuel one can imagine since it produces only water, and it can be stored in large quantities and transported over large distances. However, one of the most serious handicaps is its reaction with common construction materials: In contact with H2, the vast majority of conventional steels and alloys undergoes serious embrittlement which degrades severely their mechanical properties and leads to important safety issues [Citation1–3]. To reduce its specific volume, most of the hydrogen gas is handled under high pressure at some point in the production and delivery chain. The metallic elements of the associated equipment (pipes, fittings, valves, compressors, etc.) have to withstand embrittlement under severe conditions of pressure and stress over an extended period of time. This problem is well known and the current solutions employ a very limited number of alloys known to resist H-embrittlement such as the austenitic stainless steels of the 300-series, in particular 316 and A286 as well as certain Cu-based alloys [Citation4,Citation5]. However, a common feature of all these alloys is their limited strength: the yield strength of these steels is well below 1000 MPa and at most 1300 MPa for the copper beryllium alloy. Also, the vast majority of research on embrittlement by H2 gas has focused on pressures below 70 MPa (10,000 psi) [Citation4,Citation5], i.e. data on the behavior of construction metals above this pressure are very sparse. To conclude, there is an urgent need for identifying high-performance steels and alloys which can withstand mechanical stresses well beyond 1000 MPa under H2 pressures in the multi-kbar range.
Here we present data on a commercially available alloy known as ‘MP35N’ which reveal an exceptional resistance to H2-embrittlement. This alloy could become a key material for components under severe mechanical stress and very high gas pressure to beyond 200 MPa (2 kbar, 30,000 PSI). MP35N is a nickel–cobalt-chromium-molybdenum alloy and a trademark of SPS Technologies [Citation6]. Its typical composition is 35% Ni, 35% Co, 20%Cr and 10% Mo. The material is known for its high strength combined with elevated toughness, ductility and corrosion resistance in sour environment [Citation6] as well as to H2 gas compressed to 34 MPa [Citation7]. Work-hardened and aged material can reach an ultimate tensile strength (UTS) of 2000 MPa and a 0.2% yield strength (0.2YST) of 1800 MPa whilst still retaining an elongation of 10%. This qualifies MP35N as a high-performance superalloy. The material we used in this study was purchased from Advanced Alloys Inc (New York, USA) and was produced by Carpenter/Latrobe Specialty Steel Company (Latrobe, PA, USA). It had the chemical composition given in . One can note the very low content of secondary elements Si, Mn, B, S, P and C as a result of the vacuum-induction and vacuum-arc remelting (VIM and VAR, respectively). Test specimens were machined from a rod of 1 inch diameter. The traction tests were carried out with pristine samples (i.e. solution annealed at 1038–1052°C and work hardened according to AMS 5844) as well as samples which were additionally aged for 4 h at 580°C (following AMS 5845) and cooled in air. Measurements on the pristine specimens gave a hardness of 48–49 HRC and 51 HRC for the aged samples. The initial characterization of the material at normal conditions was carried out on a commercial instrument (Schenk Trebel RMC100). For the pristine material it gave UTS = 1750 MPa, 0.2YST ≈ 1300 MPa and elongation e = 16%; for the aged material UTS = 1980 MPa, 0.2YST ≈ 1750 MPa and e = 11%. These data compare reasonably well with mechanical properties for the aged material quoted in the metallurgical certificate of the provider: UTS: 1940–1970 MPa, 0.2YST 1800–1850 MPa, elongation at 4d: 11–14%, hardness 50 HRC (no data for pristine material).
Table 1. Chemical composition (in mass%) of test specimens used in this work (from material certificate).
The traction machine (tensometer) developed for this work uses a 300 MPa hydrogen-compatible vessel which was previously part of a gas loader for neutron scattering measurements [Citation8], see . Test specimens were in form of ‘dog bones’ with 6.25 mm diameter ((a)). A typical stress–strain curve for a high-tensile steel (ISO 34NiCrMo16) is given in (b), illustrating the effect of embrittlement and loss in strength under 200 MPa hydrogen pressure.
Figure 1. Traction machine for measuring strain-stress curves under hydrogen gas pressure to 200 MPa. Not shown are the gas compressor, the hydraulic syringe pump and the data collection unit. (1) 10 kN hydraulic ram (ENERPAC), (2) 300 MPa stainless steel vessel with CuBe liner, (3) test specimen, (4) load frame, (5) pull rod, (6) pull adaptor (7) pull shaft, (8) electronic linear gauge (1 μm resolution), (9) O-ring seals, (10) wiper seal, (11) gas inlet, (12) spacer.
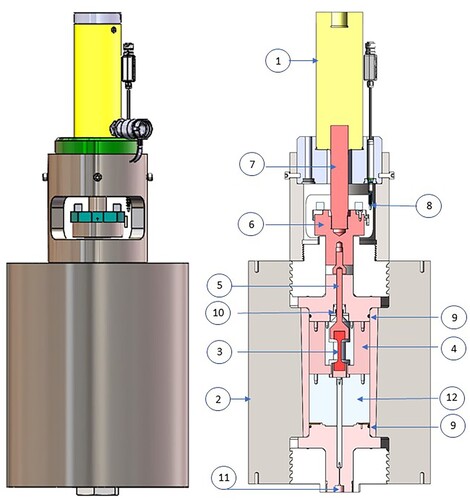
Figure 2. Picture of a test specimen (a) and example of a stress–strain curve (b) for a typical high-tensile steel (ISO 34NiCrMo16, Wst. no. 1.6773), with circles and dots/stars for measurements in air and ∼ 200 MPa H2 gas, respectively. Vertical errors indicate fracture. 0.2YST is the 0.2% yield strength, UTS the ultimate tensile strength and E the elongation. We used cylindrical specimens of 6.25 mm diameter according to ASTM standard A370-08a, length of reduced section 32, 72 mm total length, with an M20 thread at the ends. The central 32 mm were polished to have a surface roughness of less than 10 μm and cleaned with alcohol before each measurement.
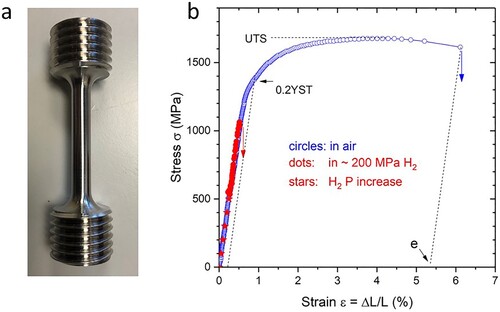
Stress across the test specimens is entirely given by the oil pressure in the ram (σ = 4890 Poil), except for a correction of 8% (at 200 MPa gas pressure) due to friction of the seal which was determined in an independent measurement. The strain is more difficult to measure and was determined by the following procedure. A linear gauge ((b)) with 1 μm resolution measures the total elongation ΔL under load which is the sum of the elongation of the specimen Δl plus the other elements ΔlT in the traction chain (essentially the pull rod and the pull adaptor), i.e. ΔL = Δl + ΔlT. Since the elements responsible for ΔlT are always in an elastic regime, ΔlT = α × Poil with some coefficient α. Below the elastic limit of the specimen, Δl = l × σ/E = l × 4890 Poil/E where E is the Young modulus and l the length of the test specimen. Therefore:
which allows to determine the coefficient α in a calibration run to typically 500 MPa stress, i.e. in the fully elastic regime, at atmospheric pressure. In practice, data up to typically 50 MPa have to be ignored since in the initial part of the traction the elongation is not exactly linear due to the presence of slack and threads in the traction elements. It should be noted that a gas pressure Pgas in the vessel generates unavoidably a pull onto the specimen and hence a stress σ = 2.65 Pgas, given a cross section of 78.5 mm2 of the pull rod. With 200 MPa H2 pressure, the initial stress (i.e. even before applying a pull with the ram) is therefore 530 MPa which is not negligible but still below the elastic limit of all materials we tested so far.
After mounting the test specimen an initial ‘training’ pull at atmospheric pressure up to ∼500 MPa stress was carried out. The load was then released and a full pull was carried out up to fracture. These measurements in air served as reference for the behavior in the absence of hydrogen and can be compared to the data provided by the producer of the test material. At least two pulls were carried out with the test specimen under ∼200 MPa hydrogen pressure. In a few cases the gas pressure was somewhat lower due to problems with the compressor. We used hydrogen gas type ‘N55’ with a purity of 99,9995% from Air Liquide. After assembling, the entire system was purged at least 3 times at 10 MPa gas pressure.
In general, our procedure follows as close as possible guidelines given by ASTM G142-98 [Citation9], i.e. (1) waiting time of at least 10 min at final H2 pressure, (2) strain rate of ca. 5 × 10−5 sec−1 up to UTS which is usually classified as ‘slow strain rate’ (SSR). All stress data presented here refer to engineering stress.
shows stress–strain curves for MP35N in air and under high H2 pressure. In total five runs were carried out, three with pristine (non-aged) test specimens (measurements in air, 183 MPa H2 and 200 MPa H2), and two with a specimen which was aged at 565°C for 4 h. In the 183 MPa run the increase in H2 pressure was longer than usual, i.e. 15 min to 100 MPa and 1 h to 183 MPa, due to a low performance of the compressor. The time in contact with H2 was hence considerably longer than in the other two runs. The curve obtained in air on the pristine sample indicates a tensile strength of 1700 MPa and ΔL/L at rupture of ca. 11%. These values are in reasonable agreement with the values obtained on a commercial device (see above), but with a slightly smaller elongation. The stress–strain curve for the sample at 183 MPa H2 pressure indicates no significant reduction in yield and tensile stress. The material conserves a considerable ductility (ΔL/L = 8%) though about 30% lower than in air. A second run (not shown) to 200 MPa (increase in 20, 15 min waiting time) gave very comparable results, i.e. 1700 MPa and 7% elongation. The fourth and fifth runs was carried out on the aged test specimen under 206 MPa H2 pressure (), giving UTS = 1980 MPa and YST = 1700 MPa with an elongation at rupture of e = 6%. The numbers on UTS and 0.2YTS are within precision and statistical error identical to the measurements carried out on the aged material in air using the commercial tensiometer (see above), as well as the material specifications from the provider. The only significant difference appears to be a reduction of the elongation e from typically 11–15% to 6%, i.e. by 50%.
Figure 3. Stress–strain curves for MP35N, pristine (i.e. non-aged) and aged specimens. Circles and squares correspond to data obtained in air and high H2-gas pressure. The inset shows an enlarged view of the low-ϵ data. For the runs with H2, no data are recorded below 550 MPa which corresponds to the pressure increase in the vessel.
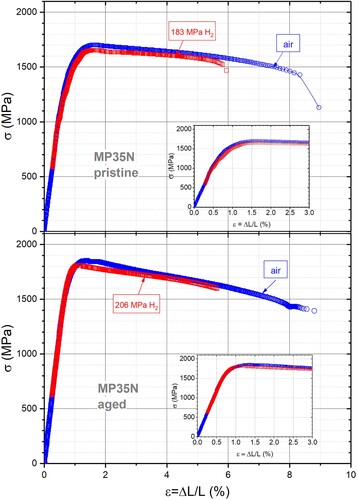
In conclusion, MP35N does not seem to suffer a reduction of strength under high H2 pressure and severe stress, even in contact with H2 over timescales of an hour, and this applies to pristine as well as to aged material. The only significant effect is a reduction of ductility in terms of elongation and reduced area to a level that may be acceptable for many applications.
shows scanning electron micrography images of the fracture surface of a MP35N sample, one after a test in air (left panels), the other after 183 MPa of H2 gas (right panels). The image from the air-exposed sample shows all characteristics of a typical ductile fracture mechanism, i.e. a cup-and-cone fracture surface with shallow and homogeneous dimples of typically 10–30 μm diameter in the central part. The image from the H2-exposed sample shows a less developed cup-and-cone morphology and for ∼90% of the fracture surface, still the same microstructure with shallow dimples of the same size as observed in the air-pulled sample. The remaining 10% which are located at the periphery shows a rougher surface, absence of dimples and probably some evidence for intra-granular fracture. These are microstructural features which point to fragile fracture and might hence be caused by some penetration of hydrogen. From these images it is unclear if fracture has started at these locations.
Figure 4. Scanning electron microscopy images of the fracture surface of MP35N samples tested in air (left) and in 183 MPa H2 gas (right). The insets give a global view across the specimen of 6.25 mm diameter, labels ‘a’ and ‘b’ correspond to enlarged views of spots marked in the insets. Measurements were carried out with a Zeiss ULTRA55 instrument with with a FEG-Schottky electronic source and equipped with the Gemini® ultra-high resolution electron column.
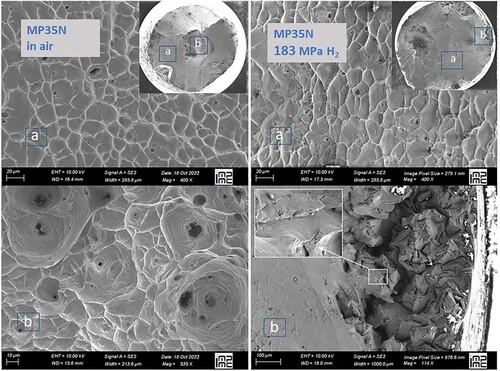
Samples of pristine and aged material as well as the specimen tested under 206 MPa H2 pressure were also x-rayed to observe potential structural modifications caused by the heat treatment and/or the contact with hydrogen (). All reflections can be indexed with the well-documented face-centred cubic structure (space group Fm3m, no. 225) with lattice parameter 3.585(5) Å and no indication of a potential hexagonal martensite produced by cold-working [Citation10]. Neither annealing nor high pressure hydrogen leads to additional reflections, and we cannot detect any significant change in lattice parameter (the slight shift visible at high 2-theta angles is not significant since it might be due to 0.05 mm difference in sample hight). Since the additional hardening during aging is produced by precipitation of secondary phases, possibly Co3Mo platelets [Citation11], the size of the nano-particles has to be smaller than 1–2 nm to remain undetected in these measurements, an estimate based on Scherrer’s formula. The observation that the specimen tested at 206 MPa H2 has no significantly different lattice parameter and no new Bragg reflections compared to the raw material suggests that all hydrogen which might have entered during the test has left the specimen without any permanent chemical interaction, such as the formation of metal hydrides.
Figure 5. X-ray diffraction patters of MP35N. Main figure: pristine (lower pattern, blue) and aged (upper pattern, red) material which was never in contact with H2. Inset: patterns from the aged specimen tested under 206 MPa H2 pressure. Numbers are Miller-indices of reflections. The differences in peak intensities are due to texture (preferred orientation of grains). Patterns in the main figure were displaced vertically to avoid overlap. λ = 1.79 Å. Data were collected with a counting time of 300 ms per step using an X’Pert Pro instrument from PANalytical equipped with a parallel beam X-ray mirror for Co radiation.
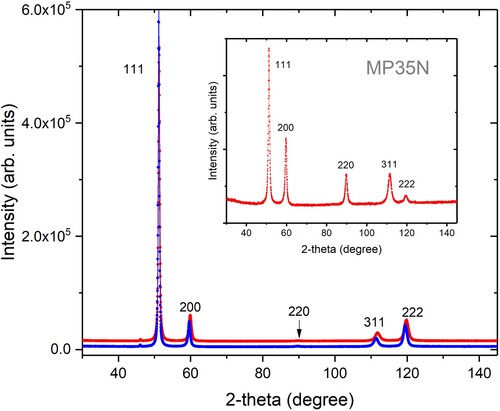
In conclusion, all measurements presented here demonstrate that MP35N has an exceptional resistance to hydrogen gas under pressures in the multi-kbar range and under severe stress during the contact with H2, when observed over an extended exposure time in the range of hours. For a comparison with other high-performance alloys and steels a useful parameter is the hydrogen environment embrittlement (HEE) index [Citation7], defined by:
Measurable properties in our case are the upper tensile stress UTS, elongation e and reduced area RA, which give the HEE indices for UTS, e and RA in . The table also contains data cited by Lee [Citation7] for MP35N exposed to 6 times lower H2 pressure (34.5 MPa) but no further detailed information given. We have also included in this table data of other high-performance steels (including PH stainless steels and highly Co/Ni-alloyed steel Aermet100) as well as CuBe, obtained by us following the same experimental procedure (ASTM G142-98b with dwelling time at 200 MPa ca. 10–15 min, see above). This allows hence a meaningful comparison on the effect of high pressure H2 between these materials. Copper beryllium (CuBe) serves as a reference for the alloy with known full resistance to hydrogen embrittlement, a finding which is confirmed by our measurements to 200 MPa. The table contains also data on other Ni-based superalloys INCONEL718 and RENE 41, as well as on the Fe-based A-286 alloy which is widely used for hydrogen applications. It is seen that among all steels we tested and which have comparable strength, none can compete with MP35N in terms of H2-resistance. Published HEE values obtained at 34.5 MPa for INCONEL and RENE41 are considerably lower and are likely even much lower at 200 MPa. The A-286 alloy can compete with MP35N in terms of HEE indices, but its strength is ∼60% lower for material with comparable HEE, i.e. wrought and un- aged specimens. As for CuBe, safety regulations make the use of CuBe more and more difficult, and the availability of alternative H2-resistant high-strength alloys would be very desirable.
Table 2. Mechanical characteristics of MP35N compared to other high-tensile steels and alloys of comparable strength, tested in this work or from the literature [Citation7]. The hydrogen environment embrittlement (HEE) index [Citation7] is defined in the main text, typical errors of this quantity are +/−0.03. All material of our work was in form of wrought bars. Alloy designations correspond to their commercial names. 819B: 35NiCrMo16, 819AW: 35NiCrMo16 remelted by consumable electrodes. MARVALX12: X1CrNiMoAITi12-9. MLX17: X1CrNiMoAlTi12-11-2. Data for A-286 correspond to wrought material without aging.
In conclusion, MP35N appears to be interesting for applications in a future hydrogen economy. Due to its low density, a large amount of hydrogen gas will need to be handled under high pressure on the way between the production site and the end consumer. Although in most cases the gas pressure will rarely exceed several hundred bars, certain elements in the delivery chain will locally be well beyond the limit where current construction materials withstand hydrogen embrittlement. The sealing areas in high pressure cone-to-cone fittings, for example, are usually stressed to close to plasticity (0.2YST) and in contact with H2 hence prone to catastrophic failure. A similar situation exists in highly stressed mechanical parts of hydrogen compressors. Finally, MP35N might find applications in future H2 storage containers which work beyond the current standard of 70 MPa/10,000 psi [Citation12], thereby allowing an increased autonomy in H2-powered vehicles.
A remaining important question to be addressed is long-time exposure to high pressure hydrogen, i.e. considerably longer than investigated in this study (1 h at most) which followed guidelines according to ASTM G142-98b [Citation8]. If we assume the diffusion coefficient in MP35N being similar to other austenitic Ni-Co alloys, i.e. 10−9–10−10 cm2/s at 300 K [Citation7,Citation13], the current time-scale (1 h) probes diffusion depths of a fraction of a mm. For technical applications with objects in the mm to cm range, tests over at least 100 times longer timescales, i.e. exposure during several days, would be highly desirable and are currently carried out by the authors.
Disclosure statement
No potential conflict of interest was reported by the author(s).
Data availability statement
The data that support the findings of this study are available from the corresponding author upon reasonable request.
Correction Statement
This article has been corrected with minor changes. These changes do not impact the academic content of the article.
Additional information
Funding
References
- Nagumo M. Fundamentals of hydrogen embrittlement. Heidelberg: Springer Verlag; 2016.
- Gibala R, Hehemann RF. Hydrogen embrittlement and stress corrosion cracking. Russell Township (OH): American Society of Metals; 1984.
- Alefeld G, Völkl J, editors. Hydrogen in metals. Heidelberg: Springer Verlag; 1977.
- San Marchi C, Somerday BP. Technical reference for hydrogen compatibility of materials. Sandia National Laboratory; 2012. (SANDIA Report SANSD2012-7321).
- Jewett RP, Walter RJ, Chandler WT, et al. Hydrogen environment embrittlement of metals. In: National Aeronautics and Space Administration, editors. NASA Contractor Report CR-2163. Washington (DC): National Aeronautics and Space Administration; 1973. p. 1–243.
- Williams TC. MP35N: a superalloy for critical oil and gas applications. Carpenter Technology White paper (CRS Holdings). 2019. Available from: https://www.carpentertechnology.com/hubfs/PDFs/MP35NASuperalloyforCriticalOilandGasApplications.pdf.
- Lee JA. Gaseous hydrogen embrittlement of materials in energy technology. RP Gangloff, BP Somerday, editors. Sawston, UK: Woodhead Publishing Ltd; 2012. p. 624–667. doi:10.1533/9780857093899.3.624
- Klotz S, Philippe J, Bull CL, et al. A 3 kbar hydrogen-compatible gas loader for Paris Edinburgh cells. High Press Res. 2013;33:214–220. doi:10.1080/08957959.2013.773323
- Standard test method for determination of susceptibility of metals to embrittlement in hydrogen containing environments at high pressure, high temperature, or both. G142-98 (reapproved 2016). West Conshohocken (PA): ASTM International; 2016.
- Prasad MJNV, Reiterer MW, Kumar KS. Microstructure and mechanical behavior of an as-drawn MP35N alloy wire. Mater Sci Eng A. 2014;610:326–337. doi:10.1016/j.msea.2014.05.046
- Ishmaku A, Han K. Characterization of cold-rolled and aged MP35N alloys. Mater Charact. 2001;42:139–148. doi:10.1016/S1044-5803(01)00162-0
- Durbin DJ, Malardier-Jugroot C. Review of hydrogen storage techniques for on board vehicle applications. Int J Hydrogen Energy. 2013;38:14595–14617. doi:10.1016/j.ijhydene.2013.07.058
- Hagi H. Diffusion coefficients of hydrogen in Ni-Cu and Ni-Co alloys. Trans Jpn Inst Met. 1986;27:233–240. doi:10.2320/matertrans1960.27.233