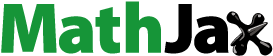
ABSTRACT
We have developed an oxide reactive sputtering technique aiming at rapidly sputtering high-quality oxide films on a diamond surface, providing excellent thermal insulation in high-pressure and temperature experiments using a laser-heated diamond anvil cell (LH-DAC). We identified conditions for rapid deposition of an alumina layer on diamond anvils, showing deposition rates as high as 0.67 um/hr. We also investigated the deposition conditions of zirconia, which have lower thermal conductivity than alumina. Laser-heating tests were performed at high pressures and temperatures to evaluate the thermal insulation of the oxide film deposited on the diamond anvils. The heating efficiency of zirconia-deposited anvils was higher than that of the alumina-deposited ones. Our zirconia-sputtered anvils were capable of generating up to 2580 K at around megabar pressure without additional thermal insulation, demonstrating the potential of this technique for ultra-high temperature generation.
1. Introduction
Diamond anvil cell (DAC) is a useful apparatus for generating high pressure corresponding to the Earth and planetary interior conditions [Citation1] and for understanding material properties such as melting [Citation2,Citation3] and phase transitions [Citation4,Citation5], and is a powerful tool for the synthesis of novel materials [Citation6]. High-temperature experiments using DACs are combined with heating techniques such as (1) external resistive heating (EH) that Joule-heats a microheater surrounding the gasket or the entire cell, (2) internal resistive heating (IH) that heats inside of the sample chamber by Joule heating [Citation7], and (3) laser heating (LH) that heats the sample by lasers. EH-DAC enables spatially and temporally stable heating [Citation8,Citation9], but the reported temperatures have been limited to 1700K [Citation10] due to the graphitization of diamond anvils. IH-DAC pushes the available temperatures up to the Earth’s core conditions [Citation3], and technical improvement has been made [Citation11], but its use is limited because of the high technical requirements. On the other hand, LH-DAC can conveniently generate high temperatures to several thousands of kelvins. Improvements in LH-DAC, such as flat-top laser optics, have made better spatial–temporal stability of laser heating [Citation12]. The sample needs to be thermally insulated from diamond anvils with high thermal conductivity (κ = ∼1000 W/m/K). Pellets of alkali halides or oxides, or noble gases such as argon and helium, have conventionally been used for thermal insulation in LH-DAC experiments. However, when compressed to extremely high pressure of over 100 GPa, such thermal insulation layer generally becomes thin due to an unavoidable plastic flow of the sample chamber in a DAC, which weakens the insulation. As a consequence, extremely high laser power is often required to generate the target temperature at megabar pressures, which is prone to causing diamond failure. Alternatively, a thin film deposited on a diamond anvil can also act as a thermal insulator [Citation13,Citation14]. The idea here is that such deposited thermal insulation layer is fixed to the diamond anvil, so the layer would not be thinned due to the lateral plastic flow of the sample chamber. They sputtered an alumina (κ = ∼25 W/mK) layer on a diamond anvil and generated up to 35 GPa and 3450 K without using additional insulation. However, after these reports, the alumina sputtering techniques have not been practically used in DAC experiments, which may be due to the lack of providing details of their sputtering conditions [Citation13,Citation14]; the quality of the sputtered oxide layer and its sputtering rate would critically be affected by many parameters such as the chamber size, distance of target and sample, substrate temperature, vacuum pressure before sputtering, the total pressure in the chamber during sputtering, and O2:Ar partial pressure ratio. The oxidation state of the sputtering target surface (called ‘oxide mode’ and ‘metal mode') is also essential information since it controls the deposition speed of the film [Citation15] (see Supplemental note 1 for details), but this information has not been provided either. This study aims to determine and share the sputtering conditions of alumina and zirconia on diamond anvils that shows a high sputtering rate with high-quality deposited films. We also evaluated the heating efficiencies of these oxide thermal insulation layers at high pressures in an LH-DAC.
2. Experimental method
A. Sputtering conditions of alumina and zirconia on diamond anvils
A radiofrequency magnetron sputtering machine KS-701MS-TE1 (K. Science Corp.) was used to sputter oxides on diamond anvils. Details of the sputtering machine are summarized in and . We used Al2O3 or metallic Al as a target to sputter alumina (run A1-A9) and a metal Zr target in a zirconia sputtering experiment (run A10). The sputtering conditions of each experimental run are shown in . We used a diamond (100) plane or a SiO2 slide glass cleaned with ethanol as a substrate. We did not chemically etch or heat the substrates before sputtering. After evacuating the chamber to <4e-3 Pa, we introduced Ar gas to increase the chamber pressures to ∼1 Pa, then activated glow discharge by applying voltage to the target and maintained the discharge for 10–20 min at 0.6 Pa, which is called pre-sputtering, to remove any oxide on the surface of the sputtering metallic target. During the pre-sputtering procedure, we covered the substrate with a shield to avoid an accumulation of metallic Al or Zr layer. After the pre-sputtering, we introduced oxygen gas controlling the O2:Ar ratio and then removed the shield to start sputtering on the substrate. We recorded the changes in the chamber pressure during sputtering, which was used as an indicator of whether the gettering effect was working (Figure S2; see Supplemental note 1 for details of the gettering effect). The oxygen flow ratio rO2 and change in chamber pressure rP are defined as follows:
(1)
(1)
(2)
(2) where fO2 and fAr indicate the mass flow of oxygen and argon gas to the chamber, respectively, and Pbefore and Pafter are the total pressure of the vacuum chamber at the beginning and the end of sputtering, respectively. The sputtering duration was 30 min to 11 h (). After sputtering, the substrate was observed under an optical microscope to check the quality of the sputtered layer ((a)). Then, we milled it with a focused ion beam (FIB) (VERSA 3D, FEI) to make a cross section of the accumulated layer and measured the thickness using a scanning electron microscope ((b,c)). Deposition rates for each condition were calculated from the sputtering time and film thickness.
Figure 2. (a) Optical microscope image of the deposited alumina layer on the diamond anvil surface in run A8 with a scale of 100 μm. The bright spot on the left side of the culet is due to the oblique incident light from the optical microscope. (b,c) Secondary electron microscope image of cross-sections of (b) alumina and (c) zirconia layers on a single crystal diamond substrate milled by focused ion beam in run A9 and A10, respectively. Gold was deposited on top of the ZrO2 layer to prevent charge-up.
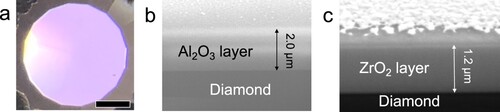
Table 1. Size of the radiofrequency magnetron sputtering machine.
Table 2. Conditions and results of alumina and zirconia sputtering.
In runs A8-A10, we covered the metal target with an aperture with a 17 mm hole (), also used in a previous study [Citation16], to create a difference in oxygen partial pressure between the area near the metal target and the substrate. When the target is covered with an aperture, it is expected that the oxygen around the target will be adsorbed by the gettering effect of the metal film deposited on the inner wall of the aperture, which keeps the target surface in a reductive (metal) state even when the chamber has a high O2/Ar ratio. Keeping the target surface non-oxidized is key to having a high sputtering rate since the sputtering rate of the metallic target is generally several to twenty times faster than that of the oxide target [Citation17]. On the other hand, outside the aperture would be oxidative, so the metallic particles sputtered out from the target would be oxidized and form oxides on the substrate ().
First, in runs A1-A6, we gradually increased the rO2 value to seek the sputtering conditions that can rapidly sputter an alumina layer using a metallic Al target that was not covered with an aperture. The total chamber pressure remained constant during sputtering with an rO2 value below 18%; above this value, the chamber pressure increased discontinuously (Figure S2), which intimates that the gettering effect caused by the metal film deposited on the inner wall of the chamber no longer have worked, resulting in oxidation of the Al target surface. However, we found that not oxide but metallic film would be sputtered to the substrate below the critical oxygen flow ratio. This suggests that sputtering an Al target without an aperture cannot deposit alumina films on the substrate under metallic mode. In run A7, we sputtered an Al2O3 target for 11 h in an oxygen-rich atmosphere to avoid forming AlOx (x < 1.5) [Citation17]; however, we observed a mosaic alumina layer sputtered on a diamond surface (see Supplemental note 2 and Figure S3), and it was too fragile to be used as a thermal insulation layer for DAC experiments.
On the other hand, when sputtering with an aperture attached to the Al target in runs A8 and A9, a homogeneous alumina film was deposited on the diamond anvil ((a)). Three hours of sputtering have produced a 2.0 µm-thick alumina ((b)), which gives a deposition rate of 0.67 µm/hr. Such a rate is much faster than the deposition rate of alumina sputtered by the oxide mode shown in the previous study [Citation18], indicating that the depositions in runs A8 and A9 were performed under the metallic mode. We emphasize that sputtering a few microns of oxides took only a few hours. Next, in run A10, we changed the target to metallic Zr and sputtered with an aperture and conditions similar to runs A8 and A9. As a result, a 1.2 µm-thick zirconia was produced by sputtering for 2 h and 40 min ((c)), which yields a deposition rate of 0.45 µm/hr. The sputtering rate of zirconia was the same order of magnitude as that of our alumina sputtering in the metallic mode, indicating that zirconia sputtering was also under the metallic mode in run A10. We conducted X-ray diffraction (XRD) measurements on zirconia film, which was sputtered for 5 h under identical conditions to run A10, at BL10XU, SPring-8. The measurements were carried out using the Perkin Elmer digital X-ray flat panel detector with an acquisition time of 10 s and 5 times integration. We found that the zirconia sputtered on a diamond was polycrystalline monoclinic ZrO2 (baddeleyite) (Figure S4).
B. DAC experiments
To evaluate the performance of the deposited thermal insulation layers, we conducted high-pressure laser-heating experiments using a symmetric LH-DAC (runs B1−B2). Run B1 compared the thermal insulation efficiency of alumina and zirconia thin films, while run B2 was conducted to evaluate the availability of the zirconia layer for LH-DAC experiments at higher pressures. We used a pair of beveled diamond anvils with a cullet size of 200 and 120 μm depending on the target pressure. A Re gasket with an initial thickness of 250 µm was pre-indented, and then a hole with a diameter half of the culet size was drilled using a UV laser drilling machine at the center of the indentation. A pellet of alumina powder was sandwiched with 10 μm thick iron foils as a heated sample in runs B1 and B2. We loaded the samples into the gasket hole after sputtering alumina and/or zirconia on the diamond anvils in the condition shown in . The pressure was measured before laser heating using the Raman shift of the diamond anvils [Citation19]. We heated the sample by applying a given laser power for a few seconds and then quenched it. Such heating cycles were repeated by increasing the laser power. We adopted the peak temperature in the sample as the sample temperature. Uncertainty of pressure and temperature may be both ±5%. In runs B1 and B2, we first compressed the sample to 15 and 91 GPa, respectively, and heated the sample from both sides using a couple of 100 W single-mode Yb fiber lasers (YLR-100, IPG Photonics Corp.) with flat-top beam-shaping optics at the University of Tokyo [Citation12]. In run B2, we then decompressed the pressure to 60 GPa and performed an additional laser heating experiment. We measured the pressure after heating in run B2; the pressure increased from 91 to 93 GPa in the first experiment and decreased from 60 to 56 GPa in the second one. The temperature of the sample was determined by a spectro-radiometric method collected on the IsoPlane160 Spectrometer equipped with ProEM-HS:512BX3 EMCCD (Teledyne Princeton Instruments) [Citation12]. The collected thermal radiation spectra from the sample were fitted by Planck’s grey body radiation law to calculate temperatures. The laser-heated spot was 20–30 μm.
3. Results and discussion
Laser-heating experiments were performed with thermal insulation only by the alumina and zirconia layers sputtered on diamond anvils in an LH-DAC. In run B1, a pair of diamond anvils were sputtered with 2 µm-thick alumina and zirconia on one side each (). For heating, we applied laser only to one side of the sample at a time, i.e., either alumina- or zirconia-side. First, we heated the iron foil sample placed on the alumina-sputtered diamond anvil. As we increased the laser power from 45 W to 60 W, the temperature rose from 1570 K to 2200 K showing a linear relationship between laser power and temperature ((a)). We then reduced the laser power to 50 W and increased it again to 65 W. The temperature followed the temperature dependence of the first heating cycle, rising from 1760K to 2230 K. Next, we heated the zirconia-side sample with increasing laser power from 35 W to 54 W. The sample temperature increased from 1810K to 2390 K linearly with increasing laser power. The generated temperature using a zirconia insulation layer was about 220 K higher than that of alumina with identical laser power ((a)). Given an order of magnitude lower thermal conductivity of zirconia over alumina at ambient conditions, it is reasonable that zirconia exhibits a higher heating efficiency. To verify the heating efficiency of the zirconia thermal insulating layer at higher pressures, we performed additional experiments at pressures of 91 and 60 GPa in run B2. We used double-sided laser heating to simultaneously heat the samples placed on both sides of the sputtered anvils. We first heated the iron foils placed on both sides of the zirconia-sputtered diamond anvils with an alumina pressure medium at 91 GPa by increasing the laser power stepwise from 21 W to 29 W. The temperature increased linearly from 1810K to 2580 K ((b)), indicating that zirconia thermal insulation works effectively even at ∼megabar pressure. We then performed another laser heating after reducing the pressure to 60 GPa in a similar manner. The temperature increased linearly with increasing laser power from 12 W to 16 W, which increased the temperature from 2010K to 2570 K. The heating efficiency in run B2 was higher than in run B1, which is likely due to the use of double-sided laser heating. The negative correlation between pressure and heating efficiency in run B2 may be due to thinning and increased thermal conductivity of the thermal insulation layer at higher pressure. Run B2 shows that the zirconia sputtering provides effective thermal insulation at megabar pressures in LH-DAC experiments.
Figure 3. The laser power-temperature relations when sputtered (a) 2 μm-thick alumina and zirconia layers in run B1, and 2.3 μm-thick zirconia layer in run B2 at (b) 91 GPa, and (c) 60 GPa.
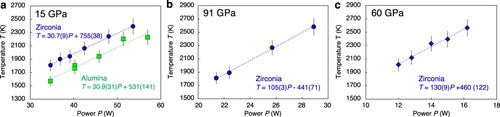
It is worth noting that the sputtered zirconia layer on the diamond anvil’s culet mostly remained after LH-DAC experiments and could be reused multiple times. Also, the sputtered zirconia layer at high pressures, which should have a cotunnite (PbCl2)-type structure at high pressures [Citation20], did not give significant peaks in the in-situ XRD pattern (Figure S5). This demonstrates that the sputtered zirconia insulation layer would not interfere with diffractions from the DAC sample, which is an additional advantage of the usage of sputtered zirconia in LH-DAC experiments.
4. Conclusion
We developed a thermal insulation layer sputtering technique suitable for LH-DAC. The following summarizes our findings.
We found the sputtering conditions that would rapidly deposit high-quality alumina and zirconia layers on diamond anvil by metal mode.
Laser heating with a zirconia insulation layer shows a higher heating efficiency than alumina.
The sputtered zirconia layer can be used for laser-heating experiments at ultrahigh pressures and temperatures of at least around megabar pressure and 2580 K, significantly extending the achievable P−T conditions using sputtering thermal insulation techniques [Citation13,Citation14].
The present thermal insulation technique by oxide sputtering, capable of generating several thousand K without additional insulation, can be applied to any LH-DAC experiments aiming for high-temperature generation. This technique can even generate high pressures and temperatures without the use of a conventional thermal insulator. This can increase the DAC sample thickness, which benefits high-pressure in situ synchrotron X-ray diffraction measurements that require thicker samples for stronger sample diffractions at megabar pressures. A recently reported high-P−T impedance measurement technique in LH-DAC was limited to 51 GPa since the two electrodes in the sample chamber easily create a short circuit at further compression [Citation21]. The present technique may expand the measurable pressure in impedance measurement, again, by maximizing the sample thickness. We believe there are further rich applications of this technique.
Supplemental Material
Download MS Word (4.6 MB)Acknowledgments
We thank two anonymous reviewers for their helpful comments. We acknowledge Shoh Tagawa for valuable discussion.
Disclosure statement
No potential conflict of interest was reported by the author(s).
Additional information
Funding
References
- Tateno S, Hirose K, Ohishi Y, et al. The structure of Iron in earth’s inner core. Science. 2010;330(6002):359–361. doi: 10.1126/science.1194662
- Anzellini S, Dewaele A, Mezouar M, et al. Melting of iron at earth’s inner core boundary based on fast X-ray diffraction. Science. 2013;340(6131):464–466. doi: 10.1126/science.1233514
- Sinmyo R, Hirose K, Ohishi Y. Melting curve of iron to 290 GPa determined in a resistance-heated diamond-anvil cell. Earth Planet Sci Lett. 2019;510:45–52. doi: 10.1016/j.epsl.2019.01.006
- Kim M, Oka K, Ahmed S, et al. Evidence for superionic H2O and diffusive He–H2O at high temperature and high pressure. J Phys: Condens Matter. 2022;34(39):394001. doi: 10.1088/1361-648X/ac8134
- Oka K, Tateno S, Kuwayama Y, et al. A cotunnite-type new high-pressure phase of Fe2S. Am Mineral. 2022;107(7):1249–1253. doi: 10.2138/am-2022-7959
- Drozdov AP, Kong PP, Minkov VS, et al. Superconductivity at 250 K in lanthanum hydride under high pressures. Nature. 2019;569(7757):528–531. doi: 10.1038/s41586-019-1201-8
- Suehiro S, Wakamatsu T, Ohta K, et al. High-temperature electrical resistivity measurements of hcp iron to Mbar pressure in an internally resistive heated diamond anvil cell. High Press Res. 2019;39(4):579–587. doi: 10.1080/08957959.2019.1692008
- Okuda Y, Kimura S, Ohta K, et al. A cylindrical SiC heater for an externally heated diamond anvil cell to 1500 K. Rev Sci Instrum. 2021;92(1):015119. doi: 10.1063/5.0036551
- Okuda Y, Oka K, Hikosaka K, et al. Novel non-Joule heating technique: Externally laser-heated diamond anvil cell. Rev Sci Instrum. 2023;94(4):043901. doi: 10.1063/5.0122111
- Yan J, Doran A, MacDowell AA, et al. A tungsten external heater for BX90 diamond anvil cells with a range up to 1700K. Rev Sci Instrum. 2021;92:013903. doi: 10.1063/5.0009663
- Geballe ZM, Holtgrewe N, Karandikar A, et al. Latent heat method to detect melting and freezing of metals at megabar pressures. Phys Rev Mater. 2021;5(3):033803. doi: 10.1103/PhysRevMaterials.5.033803
- Oka K, Hirose K, Tagawa S, et al. Melting in the Fe-FeO system to 204 GPa: implications for oxygen in Earth’s core. Am Mineral. 2019;104(11):1603–1607. doi: 10.2138/am-2019-7081
- Li M, Gao C, Ma Y, et al. New diamond anvil cell system for in situ resistance measurement under extreme conditions. Rev Sci Instrum. 2006;77(12):123902. doi: 10.1063/1.2400669
- Li M, Gao CX, Ma YZ, et al. In situ HPHT resistance measurement of (Fe0.125,Mg0.875)2SiO4 in a designed laser heated diamond anvil cell. J Phys: Condens Matter. 2007;19(42):425210. doi: 10.1088/0953-8984/19/42/425210
- Hata T, Matsuda H, Ando RAR, et al. Studies on positive ion behavior in reactive sputtering of yttria-stabilized zirconia (YSZ). Jpn J Appl Phys. 1994;33:L455. doi: 10.1143/JJAP.33.L455
- Hata T, Sasaki K, Ichikawa Y, et al. Yttria-stabilized zirconia (YSZ) heteroepitaxially grown on Si substrates by reactive sputtering. Vacuum. 2000;59(2-3):381–389. doi: 10.1016/S0042-207X(00)00291-8
- Abe Y, Kawamura M, Sasaki K. Target mode transition for reactive sputtering—Effect of gettering by Chamber Wall—. J Vac Soc Jpn. 2014;57(1):1–8. doi: 10.3131/jvsj2.57.1
- Maniv S, Westwood WD. Oxidation of an aluminum magnetron sputtering target in Ar/O2 mixtures. J Appl Phys. 2008;51(1):718–725. doi: 10.1063/1.327332
- Akahama Y, Kawamura H. High-pressure Raman spectroscopy of diamond anvils to 250GPa: Method for pressure determination in the multimegabar pressure range. J Appl Phys. 2004;96(7):3748–3751. doi: 10.1063/1.1778482
- Ohtaka O, Andrault D, Bouvier P, et al. Phase relations and equation of state of ZrO2 to 100|GPa. J Appl Crystallogr. 2005;38(5):727–733. doi: 10.1107/S0021889805018145
- Okuda Y, Oka K, Kubota Y, et al. High-P–T impedance measurements using a laser-heated diamond anvil cell. Rev Sci Instrum. 2022;93(10):105103. doi: 10.1063/5.0097883