Abstract
The catalytic properties of Cu–ZnO catalysts for glycerol hydrogenolysis to 1,2-propanediol (1,2-PDO) were tested in a fixed-bed reactor at 250 °C and 2.0 MPa H2. The relation between composition, surface properties, and catalytic performance of glycerol hydrogenation of Cu–ZnO catalysts was studied using nitrogen adsorption (BET methods), XRD, H2 temperature-programmed reduction, and N2O chemisorptions. It was found that there was a close link between the surface CuO amount of Cu–ZnO catalyst and the reactivity for glycerol hydrogenation. The Cu–ZnO catalyst (Cu/Zn = 1.86) which had the highest surface Cu amount showed the best catalytic activity for glycerol hydrogenolysis. Furthermore, Cu–ZnO catalyst presented good stability and remarkable catalytic activity for glycerol hydrogenolysis to 1,2-PDO using raw glycerol derived from the fat saponification as feedstock.
Graphical abstract
Glycerol hydrogenolysis to 1,2-PDO on Cu–ZnO catalyst in fixed-bed reactor.
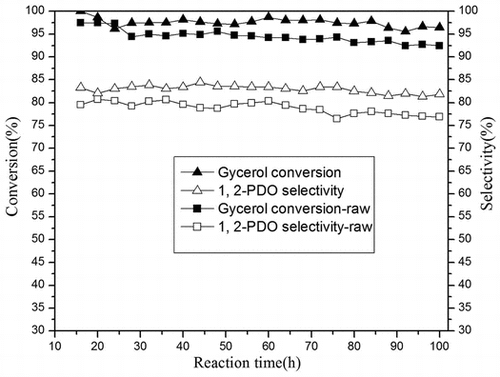
Key words:
Biodiesel is a new type of clean and environmentally friendly fuel, as it contains very little sulfur and can substitute for fossil fuel thus reducing the emission of carbon dioxide. Every 9 kg of biodiesel produced, around 1 kg of crude glycerol will be obtained as a by-product. Therefore, large amount of glycerol becomes surplus as a result of the rapid expansion of biodiesel manufacture. Also, glycerol can be produced by other industries, such as fat saponification and alcoholic beverage production units. In order to maintain the balance of glycerol in chemical industry chain, as well as to avoid environmental issues associated with its disposal, converting this very biodiesel by-product to other chemical products has become highly decisive.
By now, glycerol utilization has received extensive attention and been widely studied. Some important chemical intermediates, such as 1,3-propanediol (1,3-PDO),Citation1) citric acid,Citation2) succinic acidCitation3) can also be obtained under milder conditions via biotechnological processes. Besides, acrolein,Citation4,5) an important intermediate for manufacturing acrylic resin, and olefin can be produced by catalytic conversion of glycerol. However, more effortsCitation6–9) have been devoted to the conversion and utilization of glycerol to economically value-added product, 1,2-propanediol (1,2-PDO), which is widely used as biodegradable functional fluids such as deicing reagents, antifreezes and coolants, and precursors in the syntheses of polyester resins.
The hydrogenolysis of glycerol to 1,2-PDO is suggested to proceed via dehydration of glycerol to acetol by acid catalysis followed by catalytic hydrogenation, which has been supported by the observation of acetol in the reaction products and its selective hydrogenation to 1,2-PDO.Citation6,10) Some investigations have implied that acidity of catalyst supportsCitation11–13) or of reaction systemCitation14,15) should be a positive factor to improve the reaction activity during the hydrogenolysis of glycerol to 1,2-PDO. In the published works, Cu–ZnO bifunctional catalyst showed good performance in glycerol hydrogenolysis.Citation16,17) It was found that ZnO catalyzed the reaction by dehydrating the glycerol and further hydrogenolysis took place on the CuO site.Citation17)
Although there are numerous reports demonstrating a high yield of 1,2-PDO using batch reactors, just a few reports have evaluated the feasibility of raw glycerol as a substitute for 1,2-PDO production. In this study, raw glycerol derived from the fat saponification process was utilized without any purification to produce 1,2-PDO. Pure glycerol was also tested under the same conditions. The catalytic performances of Cu–ZnO catalysts in glycerol hydrogenolysis to 1,2-PDO were investigated. Fixed-bed flow reactor was chose for glycerol hydrogenolysis, as it was more economic and efficient for continuous and large-scale production compared to batch reactor. The relation between composition, surface properties, and catalytic performance of glycerol hydrogenation of Cu–ZnO was discussed. Important reference information of a suitable and industrial catalyst for catalytic hydrogenation of glycerol to 1,2-propanediol was also provided.
Materials and methods
CuO–ZnO oxide samples were prepared via co-precipitation method. A series of copper zinc hydroxycarbonate precursors were prepared by adding ammonium carbonate solution (3 M) to aqueous solutions of calculated amounts mixed solution of Cu(NO3)2·3H2O and Zn(NO3)2·6H2O at room temperature. Precipitation reagent ((NH4)2CO3, 3 M) was controlled to adjust the desired pH 7 in the mother liquor. The resulting precipitates were aged 3 h in the mother liquor, followed by filtration and washing with distilled water and then dried overnight at 100 °C and calcined at 673 K for 3 h. CuO–ZnO samples were measured by ICP analysis to get accurate Cu/Zn molar ratio (0.39, 1.08, 1.86, 3.01, 4.03, 4.88, respectively). For comparison, pure CuO and ZnO were also prepared by precipitation method.
The catalytic activity was carried out in a fixed-bed stainless steel reactor consisting of a stainless steel tube with an internal diameter of 6 mm and a coaxially centered thermocouple with its tip located in the middle of the bed using 0.9 g Cu–ZnO oxide catalysts (20–40 mesh). Prior to activity test, oxide catalysts were reduced in H2 flow at 300 °C for 3 h under atmospheric pressure and then dropped to reaction temperature. The following reaction conditions were employed during activity test: T = 250 °C; H2, p = 2.0 MPa, flow rate = 90 ml/min; glycerol water solution (40 wt%) flow rate = 3 or 6 ml/h. The liquid products were condensed and collected each 2 h under the fixed-bed reactor after reaction system was steady-going. The collected liquid products mainly included acetol, 1,2-propanediol, methanol, ethanol, 1-propanol, ethylene glycol were analyzed using a gas chromatograph with a PEG capillary column (50 m × 0.32 mm) and a flame ionization detector. Glycerol conversion and selectivity of the products were calculated on a carbon basis. Raw glycerol (98 wt%) was derived from the fat saponification process.
Powder X-ray diffraction patterns were recorded on a Philips X′pert diffractometer (Cu Ka radiation, 40 kV, 40 mA, scanning range: 5°–60°). The average crystallite sizes of Cu and ZnO were calculated from XRD patterns using Scherrer equation. For H2-TPR (Hydrogen Temperature-programmed reduction) measurement, 50 mg catalyst (20–40 mesh) was loaded in a quartz tube reactor and then treated with 5 mol% H2 in Ar at a heating rate of 5 °C/min from room temperature to 500 °C. The amount of the consumed hydrogen was determined by a thermal conductivity detector. For comparison, the TPR experiments of pure CuO and ZnO samples were also carried out in the same way. The copper surface dispersion was determined by N2O decomposition (N2O + 2Cus → N2 + Cus–O–Cus) at 90 °C followed by TPR.Citation9) Cu–ZnO oxide samples were reduced at 300 °C for 3 h and then flushed with Ar and cooled to 90 °C, afterward they were flushed with 25 vol % N2O in N2 for 30 min. Finally, the samples were again flushed with Ar and cooled to room temperature followed by TPR. TPR run was carried out in a 5% H2/Ar mixture at heating ramp rate of 10 °C/min. The amount of chemisorbed O atoms was calculated from the TPR peak area of pure CuO. The specific surface area of the metallic copper was calculated assuming a reaction stoichiometry of two Cu atoms per oxygen atoms, a Cu surface density of 1.46 × 1019 Cu atoms/m2.
Results and discussion
Cu–ZnO catalysts with varying Cu/Zn molar ratio were studied to optimize the catalyst composition for the glycerol hydrogenolysis in a fixed-bed reactor at the reaction conditions of 2 MPa H2 and 250 °C. Fig. shows glycerol conversion and main products selectivity of the Cu–ZnO catalyst (Cu/Zn = 4.03) are stable after 10-h reaction. Glycerol hydrogenolysis activity of Cu–ZnO catalysts with different composition in reaction time 10 h is presented in Table . With increasing of Cu content, the selectivity of 1,2-PDO increased, and the glycerol conversion initially increased and then decreased with a further increase in Cu composition. The optimum conversion recorded for the catalyst with Cu/Zn = 1.86. The product distributions over the Cu–ZnO catalysts suggest that the selectivity toward the formation of 1,2-PDO increased with increasing of Cu content (or decreasing of ZnO content).
Table 1. Effect of Cu/(Cu + Zn) ratio on the glycerol hydrogenolysis activity.
XRD patterns of the catalysts are presented in Fig. . CuO–ZnO oxide sample with Cu/Zn = 1.86, as shown by XRD results, contained merely ZnO and CuO crystallites. CuO in CuO–ZnO oxide sample was reduced to CuO after H2 300 °C 3-h pre-reduction, as proved by the concurrent appearance of CuO crystallite diffraction peaks at 43.3°, 50.6°, and 74.2°, etc. and disappearance of CuO diffraction peaks at 35.1°, 38.7°, 48.8°, etc. Compared to the fresh pre-reduced sample, CuO crystallite size became bigger after reaction, since Cu crystallite diffraction peaks became sharp and narrow distinctly. Fig. showed the XRD patterns of all Cu–ZnO catalysts after pre-reduction. CuO and ZnO crystallite diffraction peaks were clearly observed in all samples after pre-reduction. With the Cu content increase in Cu–ZnO catalysts (from curve a to curve f), CuO crystallite diffraction peaks intensity increased while ZnO crystallite diffraction peaks intensity decreased. Also, the FWHM (full width at half maximum) of CuO crystallite diffraction peaks decreased with the increasing of Cu loadings which indicated the increasing of CuO crystal particle size. It was discussed in detail in Table .
Table 2. Physicochemical properties of Cu–ZnO catalysts.
The H2-TPR profiles of CuO–ZnO samples are reported in Fig. . The TPR profile of CuO shows a wide peak with maximum at 343 °C. Pure ZnO did not reduce under the same experimental conditions. Integrated hydrogen consumption demonstrated that a complete reduction of Cu(II) to Cu(0) was always achieved at the final temperature of each TPR run. With the Cu content decrease in CuO–ZnO samples, the obvious shift of the CuO reduction temperature to lower level demonstrated the promoting effect of ZnO in copper dispersion and reducibility was caused by the strong interaction between ZnO and copper components. All the reduction peaks were wide, and even showed a shoulder-peaks (curve b and c), which could be assigned to the different CuO speciesCitation16) formed during the catalyst preparation process.
In order to discuss regular changes of Cu–ZnO catalysts activity with different Cu/Zn ratio, those catalyst measures characterized by XRD, N2O chemisorption, and BET were employed, and the results are listed in Table . CuO crystallite sizes calculated from the XRD data increased while surface amount of CuO by N2O adsorption decreased after the reaction, indicating that CuO crystallites agglomerated during the reaction process. Thus, we will discuss the stable surface CuO amount based on the data after reaction. When Cu content was low, the glycerol conversion showed remarkable increase with Cu content increasing. When Cu content exceeded Cu/Zn = 1.86 and continued to increase, it led to glycerol conversion decrease. The stable surface CuO amount of Cu–ZnO catalyst reached the highest level while Cu/Zn = 1.86, which resulted in the optimum conversion of glycerol.
Fig. illustrates glycerol reaction routes over copper catalyst surface. The mechanism to produce 1,2-PDO from glycerol via acetol intermediate was proposed and validated by Dasari et al.Citation6) Relative low H2 pressure and short contacting time in our fixed-bed reactor led to incomplete conversion of the acetol, which was dehydrated from glycerol, into 1,2-PDO, therefore relatively low 1,2-PDO selectivity was detected in our work than others.Citation7,17,18) Some condensation products, such as 2,4-dimethyl-1,3-dioxolane-2-methanol, formed by aldol reaction of acetol with 1,2-PDO, was detected by GC-MS measurement, which was reported in glycerol hydrogenation for the first time. Prior researchersCitation17,18) considered that glycerol was dehydrated to acetol and glycidol intermediates on acidic ZnO surfaces, followed by their hydrogenation on Cu surfaces. In our work, that CuO afforded the hydrogenation function as well as hydrogenolysis function was proved by catalytic ability of CuO reduced from pure CuO in continuous fixed-bed reactor, though the conversion (9.8%) was relatively low. Most researchers also thought reduced copper catalyst was effective for dehydration of glycerol to produce acetol but maybe in different reaction pathway. Sato et al.Citation19) proposed that dehydration of glycerol directly occurred on reduced copper catalyst while Liu et al.Citation16,20) thought dehydrogenation of glycerol directly occurred first on reduced copper catalyst, as shown in Fig. and Equations (1) and (2), respectively.
Raw glycerol from fat saponification and pure glycerol hydrogenolysis results are shown in Fig. . It indicated that formed Cu–ZnO catalyst pellet still maintained a good stability after 200-h reaction. Using the saponification by-product glycerol as raw material, Cu–ZnO catalyst pellet showed a good application prospects with 93 mol% glycerol conversion and 79 mol% 1,2-PDO selectivity, although slightly lower than using pure glycerol (glycerol conversion 96%, 1,2-PDO selectivity 83%). Also, the main by-product acetol selectivity was 13.6% higher than using pure glycerol (10.6%). The sum of all other by-products including condensations, 1-propanol, ethanol, methanol, and ethylene glycol was about 7%.
The optimum conversion and condensations selectivity were recorded for the catalyst with Cu/Zn = 1.86 in a fixed-bed reactor with reaction conditions of 2 MPa H2 pressure, 250 °C, reaction time of 12 h. In the Cu–ZnO catalyst for glycerol hydrogenation, CuO functioned as the dehydration as well as the hydrogenation. There is a close link between the Cu amount in Cu–ZnO catalyst and the reactivity for glycerol hydrogenation. Furthermore, Cu–ZnO catalyst presented good stability and remarkable catalytic activity for glycerol hydrogenolysis to 1,2-PDO using raw glycerol derived from the fat saponification as feedstock.
Authors contribution
FY and XB conceived and designed the study. GQ, XB, and TQ performed the experiments.GQ and XB wrote the paper. GQ and XB reviewed and edited the manuscript. All authors read and approved the manuscript.
Disclosure statement
No potential conflict of interest was reported by the authors.
Funding
This work was supported by the Specialized Research Fund for the Doctoral Program of Higher Education [grant number SRFDP-2012009111001]; Natural Science Foundation of Jiangsu Province [grant number BK2010304].
References
- Jun SA, Moon C, Kang CH, et al. Microbial fed-batch production of 1,3-propanediol using raw glycerol with suspended and immobilized Klebsiella pneumoniae. Appl. Biochem. Biotechnol. 2010;161:491–501.10.1007/s12010-009-8839-x
- Rymowicz W, Rywinska A, Gladkowski W. Simultaneous production of citric acid and erythritol from crude glycerol by Yarrowia lipolytica Wratislavia K1. Chem. Pap. 2008;62:239–246.
- Scholten E, Renz T, Thomas J. Continuous cultivation approach for fermentative succinic acid production from crude glycerol by Basfia succiniciproducens DD1. Biotechnol. Lett. 2009;31:1947–1951.10.1007/s10529-009-0104-4
- Tao L-Z, Chai S-H, Zuo Y, et al. Sustainable production of acrolein: acidic binary metal oxide catalysts for gas-phase dehydration of glycerol. Catal. Today. 2010;158:310–316.10.1016/j.cattod.2010.03.073
- Chai SH, Wang HP, Liang Y, et al. Sustainable production of acrolein: gas-phase dehydration of glycerol over Nb2O5 catalyst. J. Catal. 2007;250:342–349.10.1016/j.jcat.2007.06.016
- Dasari MA, Kiatsimkul PP, Sutterlin WR, et al. Low-pressure hydrogenolysis of glycerol to propylene glycol. Appl. Catal. A. 2005;281:225–231.10.1016/j.apcata.2004.11.033
- Yuan ZL, Wang JH, Wang LN, et al. Biodiesel derived glycerol hydrogenolysis to 1,2-propanediol on Cu/MgO catalysts. Bioresource Technol. 2010;101:7088–7092.10.1016/j.biortech.2010.04.016
- Yuan ZL, Wu P, Gao J, et al. Pt/solid-base: a predominant catalyst for glycerol hydrogenolysis in a base-free aqueous solution. Catal. Lett. 2009;130:261–265.10.1007/s10562-009-9879-0
- Huang ZW, Cui F, Kang HX, et al. Highly dispersed silica-supported copper nanoparticles prepared by precipitation−gel method: a simple but efficient and stable catalyst for glycerol hydrogenolysis. Chem. Mater. 2008;20:5090–5099.10.1021/cm8006233
- Kusunoki Y, Miyazawa T, Kunimori K, et al. Highly active metal-acid bifunctional catalyst system for hydrogenolysis of glycerol under mild reaction conditions. Catal. Comm. 2005;6:645–649.10.1016/j.catcom.2005.06.006
- Alhanash A, Kozhevnikova EF, Kozhevnikov IV. Hydrogenolysis of glycerol to propanediol over Ru: polyoxometalate bifunctional catalyst. Catal. Lett. 2008;120:307–311.10.1007/s10562-007-9286-3
- D’Hondt E, de Vyver SV, Sels BF, et al. Catalytic glycerol conversion into 1,2-propanediol in absence of added hydrogen. Chem. Comm. 2008;45:6011–6012.
- Guo LY, Zhou JX, Mao JB, et al. Supported Cu catalysts for the selective hydrogenolysis of glycerol to propanediols. Appl. Catal. A. 2009;367:93–98.10.1016/j.apcata.2009.07.040
- Miyazawa T, Koso S, Kunimori K, et al. Development of a Ru/C catalyst for glycerol hydrogenolysis in combination with an ion-exchange resin. Appl. Catal. A. 2007;318:244–251.10.1016/j.apcata.2006.11.006
- Furikado I, Miyazawa T, Koso S, et al. Catalytic performance of Rh/SiO2 in glycerol reaction under hydrogen. Green Chem. 2007;9:582–588.10.1039/b614253b
- Wang SA, Zhang YC, Liu HC. Selective hydrogenolysis of glycerol to propylene glycol on Cu–ZnO composite catalysts: structural requirements and reaction mechanism. Chem. Asian J. 2010;5:1100–1111.10.1002/asia.200900668
- Wang S, Liu HC. Selective hydrogenolysis of glycerol to propylene glycol on Cu–ZnO catalysts. Catal. Lett. 2007;117:62–67.10.1007/s10562-007-9106-9
- Balaraju M, Rekha V, Prasad PSS, et al. Selective hydrogenolysis of glycerol to 1,2 propanediol over Cu–ZnO catalysts. Catal. Lett. 2008;126:119–124.10.1007/s10562-008-9590-6
- Sato S, Akiyama M, Takahashi R, et al. Vapor-phase reaction of polyols over copper catalysts. Appl. Catal. A. 2008;347:186–191.10.1016/j.apcata.2008.06.013
- Wang S, Yin KH, Zhang YC, et al. Glycerol hydrogenolysis to propylene glycol and ethylene glycol on zirconia supported noble metal catalysts. ACS Catal. 2013;3:2112–2121.10.1021/cs400486z