Abstract
High-entropy alloys (HEAs) are a relatively new class of materials that have gained considerable attention from the metallurgical research community over recent years. They are characterised by their unconventional compositions, in that they are not based around a single major component, but rather comprise multiple principal alloying elements. Four core effects have been proposed in HEAs: (1) the entropic stabilisation of solid solutions, (2) the severe distortion of their lattices, (3) sluggish diffusion kinetics and (4) that properties are derived from a cocktail effect. By assessing these claims on the basis of existing experimental evidence in the literature, as well as classical metallurgical understanding, it is concluded that the significance of these effects may not be as great as initially believed. The effect of entropic stabilisation does not appear to be overarching, insufficient evidence exists to establish the strain in the lattices of HEAs, and rapid precipitation observed in some HEAs suggests their diffusion kinetics are not necessarily anomalously slow in comparison to conventional alloys. The meaning and influence of the cocktail effect is also a matter for debate. Nevertheless, it is clear that HEAs represent a stimulating opportunity for the metallurgical research community. The complex nature of their compositions means that the discovery of alloys with unusual and attractive properties is inevitable. It is suggested that future activity regarding these alloys seeks to establish the nature of their physical metallurgy, and develop them for practical applications. Their use as structural materials is one of the most promising and exciting opportunities. To realise this ambition, methods to rapidly predict phase equilibria and select suitable HEA compositions are needed, and this constitutes a significant challenge. However, while this obstacle might be considerable, the rewards associated with its conquest are even more substantial. Similarly, the challenges associated with comprehending the behaviour of alloys with complex compositions are great, but the potential to enhance our fundamental metallurgical understanding is more remarkable. Consequently, HEAs represent one of the most stimulating and promising research fields in materials science at present.
1. Introduction
High-entropy alloys (HEAs) are alloys that contain multiple principal alloying elements, often in near-equiatomic ratios. They are, therefore, compositionally very different from classical engineering alloys, in that they are not based on one majority component into which minority additions are made. First brought to the attention of the academic community in 2004 through the work of Yeh et al. Citation1 and Cantor et al.,Citation2 their design is based around the concept that their high configurational entropies of mixing should stabilise solid-solution phases relative to the formation of potentially-embrittling intermetallic phases. As a result, HEAs should exhibit special microstructural stability, as well as a variety of other unique and unusual properties arising from their complex compositions.
The majority of the HEA research and discourse has been influenced notably by the original and subsequent publications of Yeh and co-workers.Citation1, Citation3–8 From their work, four core effects have been proposed, which are as follows:
The high configurational entropy of HEA solid solutions has a dominant effect on phase Gibb's energy, and stabilises solid solutions relative to intermetallic phases.
The lattices of HEAs are severely strained, because of the size mismatch between alloying elements. This, in turn, has a range of different effects on the physical and mechanical properties of HEAs.
HEAs exhibit sluggish diffusion kinetics since atomic diffusion is more difficult through solid solutions with high concentrations of many elements, principally due to fluctuations in the bonding environment through their lattices.
The complexity of HEA compositions gives rise to a so-called ‘cocktail effect’ in which inter-element interactions give rise to unusual behaviours, as well as average composite properties (rule-of-mixtures).
The importance of these core effects has since been echoed by numerous HEA studies, and they have played a significant role in instigating and directing a great deal of HEA research.
Interest in HEAs is increasing dramatically at present, see Fig. , and a number of reviews of the HEA literature have been made over the past 5 years.Citation5, Citation6, Citation8, Citation10–13 These have been in the form of comprehensive and detailed summaries, such as the review by Zhang et al.,Citation14 as well as shorter critical assessments, such as the recent work of Miracle.Citation15 However, none of these have critically assessed the evidence for the four core effects described above – this is one, and the most important, of the three key aims of this review, and is tackled to begin with. The second aim of this review is to examine the opportunities and challenges associated with developing HEAs for use as new structural materials. Particular focus will be given to the development of methods that can be used to rapidly predict HEA microstructures and select alloys for experimental evaluation. The final aim is to highlight the exciting opportunity that the study of HEAs represents in terms of progressing our fundamental understanding of the behaviours of alloys. It should be noted that this review does not seek to detail the particular microstructures, processing and properties of each HEA system that has been explored – this has been achieved to a significant extent through some of the previous reviews.
1 The publication rate for HEA literature since 2004. Data gathered from ScopusCitation9 by searching for ‘HEAs’ in the keywords field and limiting the subject area to ‘Materials Science’
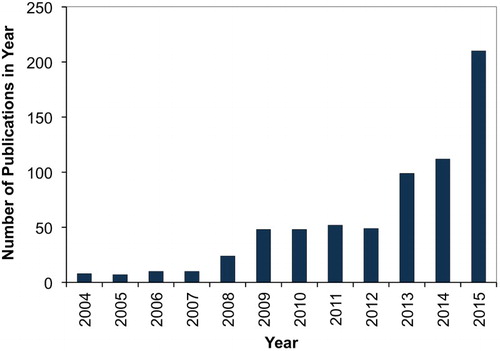
2. Entropic stabilisation
The original and most commonly reported compositional definition of HEAs is that they contain at least five alloying elements with concentrations in the range 5–35 at.-%.Citation1 These criteria were chosen as they were considered to define the compositional range in which the configurational entropies of alloys would be high enough to overcome the enthalpies of formation of intermetallic phases, resulting in stable solid solutions.Citation4 For a solution comprising n components, each with mole fractions , the configurational entropy,
, is as follows:
An alternative definition, which draws on the same principle of maximising configurational entropy, is that HEAs have a configurational entropy of mixing,
R.Citation5,
Citation16 For equiatomic alloys, this is only achievable for alloys with five or more components, and the two definitions coincide for majority of HEAs considered to date.
The entropic stabilisation of solid solutions in HEAs is fundamental to their design philosophy, and many reports have championed its effectiveness, particularly early HEA studies and reviews.Citation1,
Citation3,
Citation4 However, recently there have been a number of challenges to the notion that configurational entropy has such an overarching influence on phase stability in HEAs.Citation17–26 Importantly, these challenges have been supported by experimental experience – there appear to be very few HEAs that are stable as solid solutions at all temperatures up to melting. At present the only HEAs thought to be stable as a single solid-solution phase are the equiatomic refractory body-centred cubic (bcc) HEA VNbMoTaW,Citation27,
Citation28 and perhaps members of the TiVZrNbMo
Citation29 and Al
CrFeCoNiCitation30–32 systems for low values x and y. To the authors' knowledge, all other HEAs investigated have been found to decompose into more than one solid phase given the correct heat treatment.
A recent prominent example of phase instability reported in HEAs is that seen in the equiatomic HEA CrMnFeCoNi.Citation33–35 CrMnFeCoNi is widely considered to be the examplar HEA; first studied by Cantor et al.
Citation2 in their pioneering work on equiatomic multicomponent alloys, it has been the focus of numerous investigations, with a particular focus on its mechanical properties and processing.Citation33,
Citation36–57 Reports have often upheld CrMnFeCoNi as being stable as a single solid-solution phase, a characteristic that has made its mechanical properties of great interest, and a number of studies with a focus on phase stability have confirmed this.Citation19,
Citation22,
Citation58–60 However, it has recently been shown that exposures below 800C trigger precipitation in the alloy, most notably of the Cr-rich σ phase.Citation33–35 Hence, CrMnFeCoNi can no longer be thought of as stable as a single face-centred cubic (fcc) phase below its solidus.
A similar story has emerged for the HEA AlCrFeCoNiCu.Citation3,
Citation21,
Citation61–74 Part of the Al
CrFeCoNiCu series of alloys, which have received a great deal of attention,Citation1,
Citation64,
Citation73,
Citation75–86 initial reports appeared to suggest that Al
CrFeCoNiCu was stable as a single face-centred cubic (fcc) solid-solution phase.Citation3,
Citation62–64,
Citation75,
Citation76,
Citation78 Subsequent studies, however, found that this not the case, and have shown that it decomposes into multiple phases, including intermetallic Ni–Al-based B2, Ni–Al-based L1
and Cr-Co-Fe-based σ precipitates.Citation21,
Citation70–74,
Citation86 Indeed, a survey of the literature suggests that the addition of significant amounts of Al, Ti and/or Cu (
at.-%) almost always results in the formation of more than one phase in HEAs,Citation18,
Citation21,
Citation30,
Citation69–72,
Citation77–83,
Citation87–133 and that the incorporation of significant amounts of Cr increases the likelihood of σ phase formation in non-refractory alloys.Citation17,
Citation31,
Citation35,
Citation62,
Citation69,
Citation73,
Citation85–87,
Citation97,
Citation107,
Citation113,
Citation125,
Citation128,
Citation134–143
One of the most persuasive studies demonstrating the limited influence of configurational entropy on the phase stability of HEAs was that of Otto et al. Citation19 In this work, elements were substituted into CrMnFeCoNi that had the same crystal structure and a comparable size and electronegativity as the atoms they replaced, in an attempt to maximise the chance of solubility through the Hume-Rothery rules.Citation144, Citation145 Critically, this study found that in every case of substitution, the resulting alloy was not stable as a single solid-solution phase. Other compelling results were presented by Senkov et al. Citation24, Citation25 and Troparevsky et al.,Citation26 who have predicted, contrary to the HEA design philosophy, that the formation of intermetallic phases becomes more likely as the number of alloying elements increases, see Fig. . This conclusion is supported by the original work by Cantor et al.,Citation2 in which it was found that equiatomic alloys with 16 and 20 alloying elements were not stable as single phases (although these alloys were only assessed in the as-cast state).
2 The fraction of alloys with N components predicted to exist as solid solutions (SS), as intermetallics (IM), and as mixtures of solid solutions and intermetallics () at (a)
and (b)
C. Reprinted fromCitation25 with permission from Elsevier
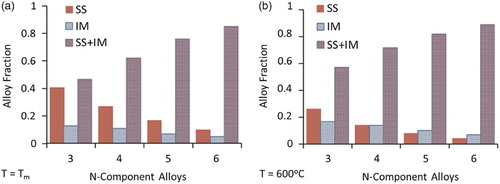
It has been suggested that because HEAs typically appear to comprise far fewer phases than the Gibb's phase rule would allow, configurational entropy is providing a significant stabilising effect even in multiphase alloys. However, when assessing this statement, the following three points must be considered. First, it must be recognised that Gibb's phase rule states the maximum number of equilibrium phases that can be present at any one point in a phase diagram, not the number that can be expected in general. For example, for binary combinations of elements at ambient pressure, the maximum of phases that can co-exist at any temperature is three. However, only at invariant reaction points, such as eutectic or peritectic points, are the maximum number of phases observed. Furthermore, in systems which show complete miscibility in both the liquid and solid state, such as the Ag–Cu system, three phases do not co-exist at any point. Second, it is clear that enthalpic factors have overcome entropic effects in multiphase HEAs, and that there is no guarantee that any solid solutions remaining after decomposition contain significant fractions of many components (i.e. have high values). Third, very careful assessment of HEA stability is required before claims are made about the particular number of phases present, and this has not been achieved in many studies.
Experimentally proving the absolute thermodynamic stability of an alloy is, of course, an impossible task, but there are two salient features that studies assessing HEA stability should include. First, appropriate heat treatments must be selected to homogenise as-cast material, and then promote phase decomposition. Focus should be away from as-cast microstructures, which have received a great deal of attention in many HEA studies,Citation1–3, Citation27, Citation30, Citation61–64, Citation76, Citation79, Citation87–91, Citation94, Citation96, Citation102, Citation109, Citation111, Citation113, Citation120, Citation122, Citation123, Citation126, Citation130, Citation133–136, Citation141, Citation146–165 since although their examination is useful to assess elemental partitioning tendencies (microsegregation), their analysis is not appropriate for assessment of phase stability. The importance of heat-treating as-cast HEAs to produce nearer-equilibrium microstructures has been highlighted, see for instance [Citation166] and [Citation167]. Following homogenisation, precipitation and phase separation should be probed by using low homologous temperatures that might typically be expected to act as aging treatments, where the effect of entropy on Gibb's free energy is less pronounced. The high temperatures used to homogenise materials following casting are not suitable for this purpose. Many HEA studies have used aging heat treatments effectively to induce precipitation, see for instance.Citation34, Citation35, Citation65, Citation66, Citation69, Citation93, Citation101, Citation103–105, Citation110, Citation168, Citation169
Second, high-resolution techniques should be used to determine whether phase decomposition has occurred at the small scale. Straightforward low-resolution SEM analysis is not usually sufficient to achieve this, since nanoscale precipitation and phase separations have often been reported.Citation1,
Citation18,
Citation20,
Citation21,
Citation34,
Citation62,
Citation72,
Citation73,
Citation75,
Citation86,
Citation91,
Citation93,
Citation99,
Citation104,
Citation114,
Citation123,
Citation127, Citation131,
Citation133,
Citation160,
Citation170–174 Techniques such as atom-probe tomography (APT) or scanning transmission electron microscopy (STEM) are required, see, for example, Fig. . The use of X-ray diffraction (XRD) in HEA studies is commonplace. However, care must be taken as the presence of phases with low volume fractions may not be detected using this technique. For example, SEM analysis revealed the presence of σ precipitates in AlCrFeCoNiCu at significantly shorter thermal exposure times than XRD,Citation74 highlighting the need to combine a number of techniques when characterising HEA microstructures. Careful consideration of diffraction peak profiles is also required, since what may at first appear to be a single peak could in fact be a result of multiple phases with similar structures and lattice parameters, see Fig. .Citation21,
Citation72 Such assessments need to be made at high diffraction angles, where there is greater sensitivity to small variations in lattice spacing.
3 STEM energy-dispersive X-ray (EDX) elemental composition maps of dendritic material in the HEA AlCrFeCoNiCu in the as-cast state, showing a spinodally-decomposed structure, and Ni–Al-rich L1
phase precipitates. Reprinted from Citation72
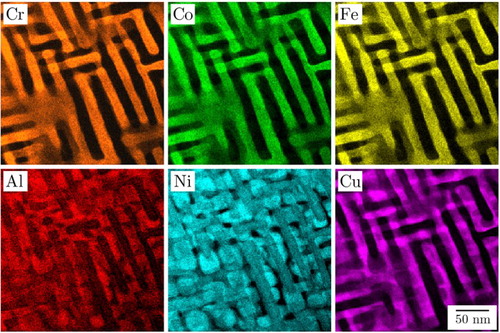
4 XRD peak profile analysis for the HEA AlCrFeCoNiCu, in which three separate phases with similar lattice parameters were shown to be present. Reprinted from Citation72
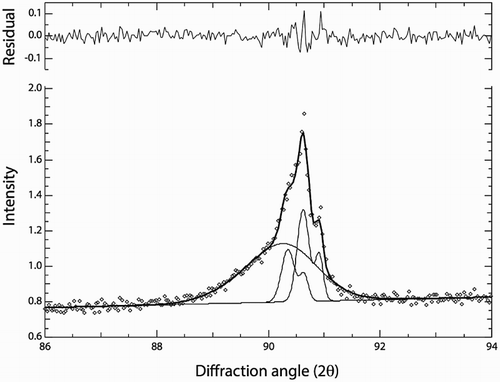
In summary, there is limited evidence to suggest that entropic stabilisation has an overarching effect on the microstructural stability of HEAs. It can be proposed that in the rare cases that HEAs have been found to be stable as a single solid-solution phase, it is not the effect of high configurational entropy that leads to their stability per se, since so many HEAs are evidently unstable. Rather, it seems that the enthalpy term associated with solution separation or intermetallic formation has not been significant in these cases. The influence of enthalpy, not entropy, is predominant. Evidence has yet to be presented that demonstrates configurational entropy can play a significant role in the stabilisation of solid solutions in multiphase HEAs, and that it does so to a greater extent than for conventional alloys, including concentrated alloys like Ni-base superalloys and twinning-induced plasticity (TWIP) steels. Careful experimental characterisation of HEAs is necessary before statements can be made about their stabilities.
2.1. Aside: naming conventions
Given the conclusions reached above, it is debatable whether the name ‘HEAs’ remains appropriate, particularly given the inherent association with the concept of entropic stabilisation. Recently, there have been some discussions of alternative naming conventions, for instance in the critical assessment by Miracle.Citation15 ‘Compositionally complex alloys’ has found some support, but in our opinion this is not ideal as many existing materials, such as Ni-base superalloys, are arguably more compositionally complex than many HEAs. ‘Multi-principal element’ or ‘complex concentrated alloys’ are perhaps more suitable in this respect. However, the authors believe that since the ‘HEA’ terminology is so embedded in the discourse, that a change in the naming convention would only lead to confusion. What is important is that the underlying metallurgical characteristics of HEAs are addressed and clarified, and that these principles are associated appropriately with the HEA designation.
At this point, it is also worth discussing the convention, or lack thereof, for describing HEA compositions. For instance, the same alloy has been studied in referencesCitation33–35,
Citation37–39,
Citation51,
Citation57 and described in no fewer than eight different ways: FeCoNiCrMn,Citation33 FeCoCrNiMn,Citation38 FeCrNiCoMn,Citation39 FeNiCoCrMn,Citation57 CrMnFeCoNi,Citation35 CoCrFeMnNi,Citation34 CoCrFeNiMn,Citation51 and NiFeCrCoMn.Citation37 This makes searching for a particular alloy composition unnecessarily difficult, and also increases the likelihood of confusion and mistaken identification. Although alphabetical order represents a possible solution to this problem, the authors believe that ordering by atomic number is the most suitable option when expressing HEA compositions as atomic ratios. In addition, we believe that the order should not be influenced by the particular concentrations of the elements, for example, CrMnFeCoNi and AlCrFeCoNiCu. Importantly, this convention transcends potential language barriers and, therefore, is likely to prove the most consistent internationally. We believe that establishing a systematic convention for naming different HEAs is far more important than renaming the whole alloy field.
3. Severely distorted lattices
It is well known that the introduction of substitutional solute atoms into a solvent matrix causes the displacement of neighbouring atoms from their ideal lattice positions, generating a strain field, and that it also induces a change in bulk lattice parameter. The localised distortions around the solute atom will interact elastically with dislocations moving through the material, resulting in solid-solution strengthening.Citation175, Citation176 Well-established models for solution strengthening have been produced for both dilute and concentrated alloys,Citation177–179 and their modification for HEAs is discussed in Section 8 of this article. A number of studies have suggested that severe lattice distortion contributes significantly to HEA properties,Citation3, Citation65, Citation75, Citation84, Citation85, Citation97, Citation165, Citation180–186 most notably with respect to increasing alloy strength, see for instanceCitation165, Citation187. Importantly, however, it is apparent that the strengthening effect of precipitates may have been overlooked in some cases.
A schematic of the proposed localised lattice distortion effect in HEAs is reproduced in Fig. . It has been suggested that these distortions arise not only from atomic size misfit, but also differences in the crystal structure and bonding preferences of alloying elements present.Citation8 It has been proposed that decreased XRD peak intensity in HEAs is evidence of lattice straining of this type,Citation3, Citation8, Citation65, Citation75, Citation97, Citation180 since it should result in increased diffuse scattering. It is true that diffraction peak intensity should decrease with increasing lattice strain around solute atoms, and that these localised static displacements have a similar effect on intensity as thermal vibrations.Citation188–193 Typical lattice strains from solute atoms are not thought to generate significant levels of peak broadening,Citation190, Citation191 as is observed in alloys with high dislocation densities or small crystallite sizes. However, it should be noted that a number of effects can influence the peak intensity and diffuse scattering observed in a diffraction pattern, including crystallographic texture, thermal vibrations and fluorescence. Hence, attentive assessment of high-quality experimental data is needed before any comment can be made on the magnitude of lattice distortions.Citation189–194 In addition, the levels of strain considered historically have been small, allowing for particular estimations to be made, and the effects of severe lattice distortions may be different.
Attempts have been made to assess the lattice distortion effect in HEAs by using pair distribution function (PDF) analysis. A PDF study of AlCrFeCoNiCu has been conducted using neutron scattering data, and it was proposed that evidence of lattice distortion was found.Citation85 Nevertheless, Al
CrFeCoNiCu comprises at least three phases at low temperatures, and a complex analysis would have been necessary to account for the effect of this in PDF measurements. A separate study used both neutrons and X-rays to produce PDFs of the ternary alloy ZrNbHf, which was described as being predominantly a single phase.Citation183 However, ZrNbHf is not an HEA by definition, and significant discrepancies between X-ray and neutron PDFs were recorded.
5 Schematic representation of strained lattices in HEAs. Reprinted fromCitation5 with permission from Springer
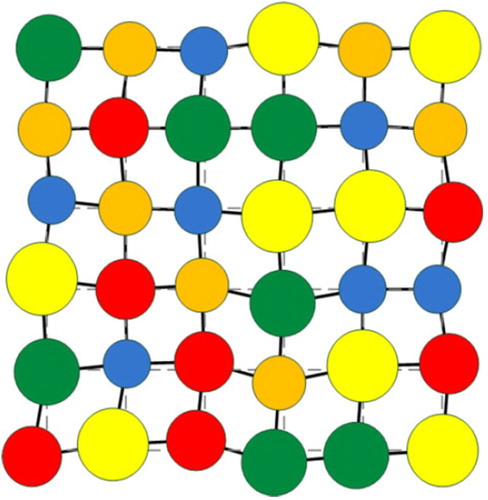
One might assume that evidence of severe lattice distortion could be found using high-resolution STEM – looking in cross section, atomic columns might look more blurred in a highly strained lattice than in an unstrained one, and atomic planes may also look distorted in the image plane. However, careful analysis accounting for phonon effects and other artefacts would be necessary before such conclusions were reached. Although it has been suggested that high-resolution TEM (HRTEM) images can show lattice distortion,Citation195 the gentle long-range distortions due to the presence of defects such as dislocations are not consistent with the localised strain proposed by Yeh et al. Citation3, Citation8, Citation65, Citation75, Citation97, Citation180
Toda-Caraballo and Rivera-Diáz-del-CastilloCitation185 have recently predicted lattice strains in HEAs using both a density function theory (DFT) approach, and a spring model based on quadratic potentials. Their article provides details of useful models for the prediction of lattice parameters and lattice strain in HEAs. Critically, however, their study predicted localised strains in nearest-neighbour bonds in bcc HEA VNbMoTaW of no more than of lattice parameter. This level of strain is no greater than those predicted and measured in both dilute and concentrated binary alloys.Citation189,
Citation190,
Citation196–201 Indeed, the displacements are of similar size to those expected from thermal vibrations around room temperatureCitation185,
Citation190,
Citation196 and, therefore, cannot be described assevere.
Besides assessment of experimental evidence and prediction results, qualitative arguments based on the phase energetics can be made to explain why severely distorted lattices are not likely to exist. As noted by Hume-Rothery, solid solutions tend to be unstable if the mismatch in size between solvent and solute atoms is large enough.Citation144, Citation202 Studies that have assessed the effect of atomic size mismatch, for example by the inclusion of Al in alloys, have indeed found that a larger mismatch makes the formation of solid solutions in HEAs less likely,Citation152, Citation203–208 as will be discussed in more detail in Section 7. It seems clear that even in HEAs, any strains would inherently increase the free energy of the lattice, at least partially offsetting any stabilisation to solid solutions delivered by increasing configurational entropy. One can argue that it is possible to have a severely strained lattice that is unstable, or have a stable solid solution that is not very strained, but it seems unlike that both stability and severe strain can be achieved simultaneously. There are, of course, many reasons besides strain that solid solutions decompose to mixtures of phases, but it is clear that strain would only decrease stability. In summary, there is no clear evidence to date that demonstrates that lattice distortions in HEAs are much greater than 5% of the lattice parameter, although there is some uncertainty as to how severe distortions would manifest themselves in diffraction data. This topic requires further investigation, and is likely to contribute significantly to our understanding of concentrated alloys.
4. Sluggish diffusion kinetics
Closely associated with the severely distorted lattice effect is the proposal that diffusion kinetics in HEAs are anomalously slow or sluggish.Citation4–6, Citation8, Citation209 This has been used to explain particular experimental observations in a number of studies.Citation1, Citation52, Citation53, Citation55, Citation65, Citation69, Citation75, Citation100, Citation124, Citation166, Citation181, Citation205, Citation210–214 Yeh et al. Citation5, Citation6, Citation8, Citation209 have suggested that anomalously slow diffusion in HEAs originates from fluctuations in the potential energies of lattice sites that are met by diffusing species, Fig. . In a pure element or dilute solid solution, the potential energy associated with each lattice site is approximately equal, whereas in an HEA there will be sites in which the bonding configuration will be more preferable for a diffusing species than others, and these act as temporary traps, slowing the rate of diffusion. Others have suggested that lattice distortions are also associated with slow diffusion in HEAs,Citation69, Citation181 and it seems reasonable to expect fluctuations in the potential energies of sites in a distorted lattice.
6 Schematic representation of the proposed difference in lattice potential energy profile along an atomic diffusion path in a pure element or dilute solid solution (top) and an HEA lattice (bottom). Note it is assumed that the distance between atomic sites is constant. A similar schematic for the HEA energy profile was given in reference Citation8
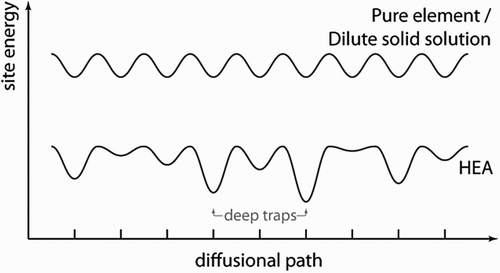
To date, only one study has published measured values for self-diffusion coefficients in HEAs, that by Tsai et al.
Citation209 They examined the diffusion of each constituent element in the equiatomic HEA CrMnFeCoNi, and found that values for the scaled activation energy, (Q being the activation energy and
the alloy melting point), were universally higher in the HEA than in selected fcc binary alloys and austenitic steels. Indeed, the values for
are also higher than any of those presented by Brown and AshbyCitation215 for fcc binary alloys – Tsai et al.
Citation209 measured a value of 0.1975 kJ mol−1 K−1 for Ni in CrMnFeCoNi, Fig. , while the maximum value found by Brown and AshbyCitation215 was 0.1933 kJ mol−1 K−1, and on average it was
kJ mol−1 K−1. Of course, diffusivity (D) depends exponentially on
, and hence even small variations in
can lead to order-of-magnitude changes in D. However, it must be recognised that D also depends on the value of the pre-exponential factor (
), and this can vary significantly, more than compensating for changes in
. For instance, the melting-point D values for Pt diffusion in Cu and W diffusion in Ni recorded by Brown and AshbyCitation215 are below the lowest values measured for D in CrMnFeCoNi by Tsai et al.
Citation209
7 Normalized activation energies of diffusion for Cr, Mn, Fe, Co and Ni in different matrices. Reprinted fromCitation209 with permission from Elsevier
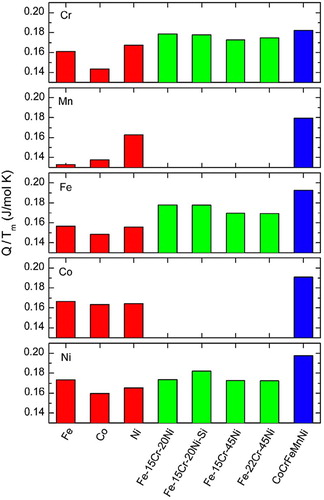
Aside from direct measurements of diffusivities, there is a great deal of experimental evidence that implies that atomic movement in HEAs is not unusually sluggish. Of particular prominence are observations of precipitation in many as-cast HEA samples,Citation1,
Citation21,
Citation62,
Citation70–72,
Citation75,
Citation91,
Citation99,
Citation100,
Citation114,
Citation121,
Citation123,
Citation127,
Citation147,
Citation172 including those subjected to very rapid cooling,Citation73,
Citation132,
Citation170,
Citation171 as well as in those quenched from high temperature heat treatments.Citation31,
Citation72,
Citation174 Indeed, it has recently been revealed that Ni–Al-based B2 precipitates are able to form on air cooling the HEA AlCrFeCoNiCuCitation74 from high temperatures. These results are in direct contrast to the suggestion that, because diffusion is so slow in HEAs, furnace cooling can be equated to a rapid quenching operations.Citation69,
Citation124
It should be recognised that care must be taken when relating rates of precipitation to values for D, since atomic fluxes are not only influenced by D, but also by gradients in concentration and chemical potential. Nevertheless, it is atomic fluxes that are the principal concern for metallurgists in practice, and rapid precipitation suggests that these fluxes are high. If we consider the possibility that the D values are abnormally low in HEAs, then in cases of rapid precipitation it must be that gradients in chemical potential are remarkably severe. Such cases could then be seen as confirmation of the fluctuations in lattice potential energy proposed by Yeh et al. Citation5, Citation6, Citation8, Citation209 – the changes in energy are simply so large that the ordering or clustering of species is unavoidable. Observations of rapid precipitation cannot be aligned with both the entropic stabilisation and sluggish diffusion effects simultaneously.
It has also been suggested that the recrystallisation resistance observed in some HEAs provides evidence for their sluggish diffusion kinetics.Citation52, Citation53, Citation55, Citation65, Citation212, Citation214 It is true that slow atomic diffusion does inhibit recrystallisation, but rates will also depend on other variables such as dislocation concentrations and distributions, prior grain size, and the presence of second phases or other inhomogeneities.Citation216 Hence, careful investigation is needed before recrystallisation kinetics are related to diffusion kinetics. In summary, the evidence considered here suggests that atomic diffusion in HEAs is unlikely to beanomalously slow, and that it is certainly not so in a generalised sense across all HEAs.
5. The cocktail effect
The cocktail effect is perhaps the most abstract of the core HEA effects, and it is difficult to determine precisely what is meant by it and what makes it particularly special. It appears to have been derived from the piece by RanganathanCitation217 entitled ‘Alloyed pleasures: Multimetallic cocktails’, which describes the mixing of elements in a ‘muti-metallic cocktail’ to produce HEAs. Recently, Lu et al. have described it as the ‘overall effect resulted from mutual interactions among composing elements, which would bring excess quantities to the average values simply predicted by the mixture rule’, while YehCitation8 has described it as ‘the overall effect from composition, structure, and microstructure’. The authors of this review assume that an example of a property derived from the rule of mixtures might be the lattice parameter (e.g. Vegard's law,Citation218 at least at low concentrations), while an ‘excess’ property might be increased wear resistance due to the development of a hard microstructure through precipitation.
It is not clear from the descriptions of the cocktail effect in what way it is unique to HEAs. Rules of mixtures apply to conventional alloys, and special properties can be obtained through elemental additions – this is fundamentally why so many elements are added into engineering alloys such as steels and Ni-base superalloys. The properties of all alloys, not just HEAs, depend critically on composition and microstructure. Perhaps it is best to use this term in relation to the surprising and exotic properties than can arise in HEAs due to their complex compositions. Otherwise, it could be argued that this effect should be dismissed.
6. A route for alloy development
To the authors' knowledge, HEAs have yet to be exploited commercially. However, a number of potential applications have been highlighted in the literature. These include their use as protective coatings owing to their good corrosion and wear resistanceCitation1, Citation80, Citation84, Citation115, Citation170, Citation171, Citation219–231 (see review of laser-deposited HEA coatings by Zhang et al. Citation232), as alloys for bulk metallic glasses,Citation11, Citation233–236 and even as materials for hydrogen storageCitation237 and diffusion barriers.Citation1, Citation181, Citation182 There has also been interest in their magneticCitation1, Citation10, Citation97, Citation238–243 and thermoelectric properties.Citation244 These properties and applications, and others, are discussed in more detail in the reviews by Zhang et al. Citation14 and Tsai et al. Citation6 The authors consider one of the most promising potential applications for HEAs is as structural materials, and this is addressed specifically in the following text.
It has been suggested that specific HEAs demonstrate some exceptional mechanical properties in comparison to conventional alloys, which might make them attractive in structural applications. Examples include the impressive fatigue resistance of AlCrFeCoNiCu,Citation67,
Citation68,
Citation174 the wear resistance of Al
CrFe
MnNi
,Citation92,
Citation245 Al
CrFeCoNiCu,Citation246 Al
Ti
CrFeCo
Ni
Citation106 and derivatives,Citation61–63 as well as the exceptional toughness and strength of CrFeMnCoNi at cryogenic temperatures,Citation36,
Citation40,
Citation41 which will be examined in particular detail below. It is not appropriate to talk about the properties of HEAs in general terms, since their different compositions can deliver very different properties, arguably to an greater extent than that which can be expected across alloys systems like steels. However, what does seem to be clear is that a great number of the HEAs examined to date are simply too brittle to be considered useful as engineering materials.
While low ductility is certainly not desirable for structural alloys, neither is the low yield strength observed in alloys comprising simple solid solutions, particularly when service conditions involve high temperatures. Almost all successful engineering alloys are based upon strengthening precipitates or interfaces that act as strong athermal obstacles to dislocation motion. This fact was highlighted by Miracle,Citation16 who proposed to switch the focus of HEA research away from achieving single-phase microstructures, to developing mixed solid-solution/intermetallic microstructures akin to those found in Ni-base superalloys. We would certainly advocate this approach. However, as Miracle highlighted, this represents a significant challenge, since careful control of the sizes and volume fractions of strengthening intermetallic phases is required to achieve the correct balance of properties. The idea of a balance in properties is a key one – it has been suggested that HEA studies have too often focussed on one property of interest, rather than the combination of properties required for most applications.Citation15, Citation247 Typically, good corrosion resistance, toughness and microstructural stability will be required alongside strength. With respect to corrosion resistance in particular, it can be foreseen that HEAs could offer a potential advantage over conventional alloys – if their solid solutions are even marginally stabilised by entropic effects, then higher additions of protective elements like Al and Cr into solution may be possible, boosting the likelihood of forming protective oxide layers.
The scale of the challenge of developing HEAs for structural applications is realised when we account for the enormous range of possible HEA alloy compositions. The number of equiatomic compositions alone is vast, but when non-equatomic compositions are considered,Citation211, Citation248 as well as the possibility of incorporating minor alloying additions,Citation128 then the potential compositional space becomes extraordinarily large. It must be recognised that the selection of promising alloy compositions is a formidable obstacle, which is at least partly responsible for the lack of compositional variety across many HEA studies.
Experimental exploration of the entire HEA compositonal space, whether it be in a random or ill-guided systematic fashion, is simply inconceivable. Decisions must be made about potential systems of interest, and they must be educated and well-informed. Too often, HEA studies have related the addition of an element directly to the resulting mechanical properties – an example might be the idea that the addition of Al improves strength. Without qualifying this statement using knowledge of how Al influences the microstructure of the material, little progress can be made. Some useful understanding of this type has already been developed through HEA studies – for instance, it is well known that the addition of increased levels of Al to AlCrFeCoNiCu, Al
CrFeCoNi and similar derivatives leads to the formation of bcc (and related ordered variants) over fcc structures,Citation30,
Citation75,
Citation76,
Citation78,
Citation79,
Citation95–97,
Citation99,
Citation102,
Citation112,
Citation129,
Citation130,
Citation160,
Citation249,
Citation250 which boosts the hardness of these alloys, but makes them more brittle.Citation96,
Citation117,
Citation246,
Citation251 However, laborious experimental characterisation cannot be relied upon in the face of overwhelming compositional possibility. Powerful predictive methods are required.
7. Phase prediction and alloy selection in HEAs
The prediction of the stability of solid solutions in HEAs has been a key area of interest to the HEA community, and is a topic of great importance with respect to the direction of future HEA studies. A common approach has been to utilise the empirical rules of Hume-RotheryCitation144, Citation145 and/or accessible thermodynamic quantities to form parametric criteria for the stability of HEA solid solutions, which are fitted to experimental results.Citation152, Citation159, Citation163, Citation173, Citation203–205, Citation207, Citation252–267 These phase-selection rules for as-cast HEAs were recently reviewed by Wang et al. Citation258 and Guo,Citation208 and are discussed briefly here.
The most common thermodynamic quantities used have been and
.
is evaluated through equation 1 given above (i.e. is approximated as
), and
through the following expression:
where
and
are the mixing enthalpies of binary A–B alloys, as calculated using Miedema's semi-empirical model.Citation268,
Citation269 The Hume-Rothery rules for the stability of alloy solid solutions are based around three parameters: (1) the atomic size misfit between solvent and solute, δ, which tends not to exceed ≈15% for stable solid solutions (this is known as the 15% rule, the argument being based on strain energy), (2) the electronegativity difference between two alloy components,
, which tends to be larger in alloys that contain intermetallic compounds and (3) the electron concentration, which is often taken to be the valence electron concentration (VEC). For HEAs, in which there are no clear solvent or solute components, the formulation of the Hume-Rothery parameters requires modification. For δ, the following expression has been employed:Citation203,
Citation270
where n is the total number of components i, each which have concentration
(atomic percentage) and atomic radius
.
is the average atomic radius of the alloy:
.Citation203,
Citation270 For
:Citation152,
Citation270
where the average electronegativity
. Finally, the VEC is as follows:Citation152
Zhang et al.
Citation203 were the first to produce a parametric study of HEA stability. They plotted HEAs of known stability in the 3D space defined by
,
and δ, and hence defined regimes of this space where stable solid solutions were expected to form, see Fig. . Many others have since followed this methodology, using the same parameters or others that provide measures of the same key effects.Citation163,
Citation204,
Citation252,
Citation253,
Citation255,
Citation258,
Citation263–266,
Citation271 Studies have indicated that plots of
vs. δ
Citation204–206,
Citation255,
Citation258 and
vs
Citation256 are most useful. Others have used alternative means of comparison – for instance, Singh et al.
Citation173 have suggested the use the parameter
, while Wang et al.
Citation266,
Citation271 replaced δ with a new parameter for the measure of atomic size mismatch, arguing that δ does not distinguish effectively enough between systems that form only solid solutions and those that decompose to give intermetallic compounds. Yang et al.
Citation252 introduced a new parameter incorporating both
and
, and used this in conjunction with δ to form a predictive criterion.
8 A plot of vs. δ showing the distribution of HEAs that form only solid solutions, that contain intermetallic compounds (alongside solid solutions), and that are amorphous. According to this treatment, only solid solutions form when 5 kJ mol
kJ mol−1 and
.Citation258 The red and blue areas represent the regions in which amorphous phases and solid solutions are found, respectively. The green oval encompasses the HEAs comprising intermetallic compounds. Reprinted fromCitation258 with permission from Springer
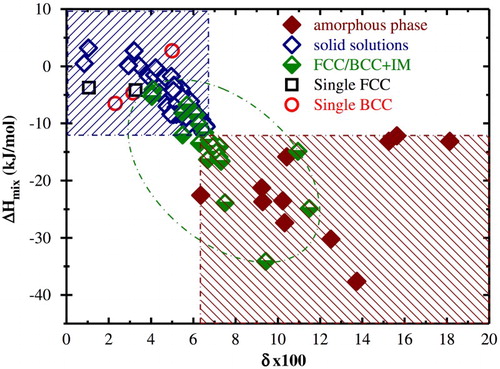
It has been argued that and δ are the critical parameters of interest with respect to solid-solution stability,Citation20,
Citation204–206,
Citation257 which has been reflected in the form of most of the criteria used. VEC appears to correlate well with the crystal structures of HEAs, with fcc structures consistently associated with high VEC values, and low VEC values delivering bcc structures.Citation152,
Citation159,
Citation258–260 Tsai et al.
Citation138,
Citation272 have used VEC alongside compositional considerations to predict σ formation in HEAs, while others have compared instances of ordered phase formation (including topologically close-packed phases, TCPs) against the average value of the d-orbital energy levelCitation262,
Citation273 and
.Citation274 It has been suggested that
it is also an indicator of elemental segregation on casting.Citation257
is not particularly useful differentiator, since it is uniformly high for HEAs.Citation208
Despite the widespread use of parametric studies, there are some significant limitations that must be recognised. First, their particular forms do not necessarily have a sound physical basis – there is no fundamental explanation for why specific ranges of particular parameters have been chosen or plotted against each other, aside from their correlation with experimental results. Singh et al.
Citation20 have suggested that the limits for the various parameters set in the literature are somewhat unsatisfactory for the understanding of the formation of solid solutions. Second, there is significant difficulty associated with accounting for the tendency of an HEA to form intermetallic phases. As has been highlighted by a number of authors, the estimation of the formation enthalpies of intermetallic compounds, , is inherently important for this,Citation16,
Citation19,
Citation267,
Citation275 and it is clear that the use of δ and
as proxies for
is limited. The regular use of
as an indicator of
can be criticised. It is understandable that
and
will be related in some way, since both involve the favourability of bonding between alloying elements, but the formation of intermetallic compounds an alloy typically involves bonding between particular subset of species, and this effect may be lost by estimating the magnitude of
using
values calculated for bulk compositions. Several studies have recognised this, and instead of calculating
for full alloy compositions; they have evaluated it for binary combinations known or suspected to form intermetallics, used other methods to evaluate
directly, or used experimentally measured
values.Citation16,
Citation26,
Citation267,
Citation275 For instance, King et al.
Citation275 estimated
using binary Miedema data to generate a parameter comparing the maximum Gibb's free energy change obtained from any clustering or intermetallic formation to the free energy change for the formation of a disordered solid solution. They assessed over 180 000 candidate HEAs to find compositions which were predicted to exist as single solid-solution phases. Notably, however, they found significant discrepancies between predictions using Miedema's model (which has been widely used in parametric studies) and DFT calculations and experimental results. This further highlights the uncertainty associated with parametric studies due to their use of certain assumptions and semi-empirical models to calculate thermodynamic quantities. Another example of such difficulties is that associated with evaluating the influence of the entropic term on the Gibb's free energies of solid solutions – which temperature should be used to compute
? The melting point of the alloy? The temperature of service? Or a wider temperature range indicative of that which an alloy might conceivably experience during its lifetime?
Perhaps the most critical weakness of the parametric approaches, however, is that almost all are fitted to experimentally obtained data. This is an issue since, as highlighted in previous sections, a significant proportion of the data used for validation have been taken from as-cast microstructures. These non-equilibrium microstructures are not indicative of phase stability, not least because their constituents can change with cooling rate. Even the use of as-homogenised results, which were exclusively assessed by Wang et al. recently,Citation258 is not ideal, since they also do no adequately inform us of alloy stabilities, see Fig. . Essentially, the parametric criteria are only as good as the data that are used to generate them, and they continue to predict stable solid solutions in CrMnFeCoNi and other non-refractory HEAs, which are now known to be unstable.
9 A plot of vs. δ in the same style as Fig. , but this time plotted using results from alloys heat treated in the range
. The red and blue areas represent the regions in which intermetallic phases and solid solutions are found, respectively. The green oval encompasses the HEAs comprising an addition of Al. Reprinted fromCitation258 with permission from Springer
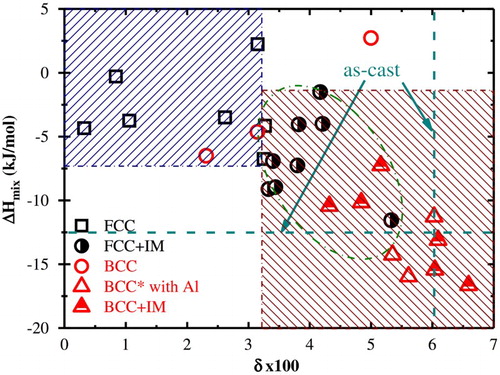
In theory, first-principle prediction techniques like DFT should be more robust than empirical or semi-empirical approaches, since they have a more solid grounding in physics and are less reliant on experimental inputs and empirical approximations. A number of studies have applied such techniques to the prediction of phase stability and ordering in HEAs,Citation23,
Citation250,
Citation275–283 as well as magnetic properties.Citation242 See the review by Troparevsky et al.
Citation284 for further discussions of applying ab initio methods to predict HEA properties. Troparevsky et al.
Citation26 themselves assessed HEA stability using values for binary compounds computed through DFT. Stable solid solutions were assumed to exist where
was neither too negative (intermetallic formation) or too positive (indicating incompatibility of constituent elements). Excellent agreement with experiment was claimed, but the range of
used was influenced by experimental results, and hence their model cannot be viewed as truly independent. In general, the effectiveness of first-principal models in predicting the formation of complex multi-component TCP phases and other intricate features of HEA microstructures has yet to be demonstrated, and is likely be limited by the number of atoms such models can assess.
The CALPHAD methodCitation285 is a well-utilised approach to predict phase equilibria in alloys, which does not suffer from limitations associated with the size of the system being modelled like first-principle methods do (although they arguably suffer from system complexity). However, CALPHAD methods should be applied to HEAs with caution, since extrapolation from our knowledge of common binary and ternary systems cannot be realised with great confidence. Studies that have used CALPHAD for direct phase predictions have often met with rather limited success.Citation118, Citation253, Citation286–288 The challenges associated with using CALPHAD for HEAs have been discussed in Refs. [Citation166] and [Citation167]. They have used CALPHAD by examining binary databases for ‘matching elements’ that could then be combined to predict phases in HEAs. They were able to successfully predict the major phases in three HEAs, but it was acknowledged that CALPHAD cannot be used to predict the formation of new unknown phases in the high-order HEA systems. Their approach did not predict the formation of σ in CrMnFeCoNi at the temperatures at which it has been observed. The formation of σ in CrMnFeCoCu, VCrMnCoNi and VMnFeCoNi is also not well predicted by CALPHAD.Citation19, Citation167, Citation213 Indeed, the accurate prediction of intermetallic phases, the formation of which is of great importance to engineering alloys, appears to be problematic for CALPHAD methods in general.
Although CALPHAD methods are by no means ideal candidates for the phase prediction in HEAs at present, there is arguably a lot of merit in using them to rationalise the results obtained from experimental investigations.Citation19, Citation213 There is even more potential in using it as a guide for alloy selection,Citation16, Citation213 particularly when the parametric criteria discussed above are the only alternative option. Perhaps the most important work on the topic of HEA selection has been carried out by Miracle, Senkov and co-workers.Citation16, Citation24, Citation25 Their seminal work has evolved around the recognition that the compositional space of HEAs is essentially limitless, and hence there must be a focus on the rapid selection and evaluation of alloying elements and HEA compositions if progress is to be made. The methodology, detailed in their 2014 article,Citation16 begins with the selection of a ‘palette’ of potential alloying elements based on fundamental properties such as melting point, elastic modulus and density – the justification being that an alloy tends to take on the properties of their constituent elements (the cocktail effect). A three-stage process is then initiated: The first stage (‘Stage 0’) is a screening assessment using CALPHAD to eliminate alloys that do not meet specific criteria, and hence select promising equimolar alloys. For instance, alloys with solidus temperatures below the temperature of intended use should be eliminated, as will those predicted to exhibited a first-order phase transition that could result in property changes during service. Alternatively, alloys could be eliminated if their matrices do not include the required levels of Cr, Al or Si for oxidation resistance. As with all alloy design, the criteria imposed at this first screening stage will be dependent on the intended application. The second stage involves rapid experimental evaluation of microstructure and elementary mechanical and environmental properties, using samples containing gradients in composition such that chemistries around the equimolar one selected can be sampled – the importance of sampling such space has been stressed recently by Pradeep et al.,Citation211 who have also examined rapid-through-put screening of HEAs. The production of compositionally gradiented samples can be achieved, for example, by the use of physical vapour deposition (see work of Ludwig et al. Citation289, Citation290), and microstructural characterisation can be accomplished through the use of simultaneous EDX analysis and electron back-scatter diffraction (EBSD) in the SEM. The third stage involves rapid experimental evaluation of the mechanical properties of candidate alloys using samples containing gradients in microstructure (for instance, grain size).
However, it should be stressed that rapid-through-put screening methods for both microstructure and mechanical property selection are not without their limitations at present. The sample preparation and measurement techniques have yet to be fully developed. The heat treatment of samples can be difficult, and can result in the debonding of the films from their substrates, or film-substrate reactions. Measured mechanical properties can be influenced by substrate interactions and residual stresses. Furthermore, the complexities of the heat treatments and their influence on microstructure and mechanical properties means there is a danger that promising alloys could be too easily dismissed. The link between heat treatment, microstructure and properties can be very complex and is not readily predictable, particularly for unknown systems. One can envisage that rapid approaches might dismiss most steels (had they not yet been discovered), due to their polymorphism and tendency to form brittle martensite when cooled quickly. Given these issues, care must be taken to validate the results of rapid-through-put methods against those obtained from conventional ‘bulk’ samples.
One of the key features of Miracle et al.'sCitation16 approach is that experimental results are fed back into the CALPHAD stage to improve predictive capability. Critically, at no point does the design process eliminate alloys that are predicted to form intermetallic compounds alongside a solid-solution phase. Instead, a special effort has been made to try and identify such systems, in recognition that the microstructures of most successful engineering alloys comprise a hard obstacle phase. In a recent paper,Citation24 they reported that they had evaluated 130 000 alloy systems using the CALPHAD stage of their methodology, and have identified 51 new equimolar alloy systems comprising between three and six base elements as candidates for experimental assessment. The ultimate success of their scheme has yet to be proven, and there are various obstacles to overcome (not least the issues with rapid-through-put techniques described above), but it currently represents one of the most progressive and promising activities in the HEA field. It would be interesting to critically compare the results of the high-throughput methods produced using CALPHAD, Miedema's model, and DFT to high-quality experimental observations. As yet, practical issues such as cost,Citation128, Citation248 as well as issues associated with the production of alloys, have not played a strong role in alloy selection. However, they will need to accounted for if HEAs are to be commercially successful.
It has been suggested that much of the experimental HEA research to date has focussed on too a narrow range of alloy compositions (typically using Al, Ti, Cr, Mn, Fe, Co, Ni and Cu), when in fact a major attraction of HEAs should be the scope for developing novel alloys with many different compositions.Citation1, Citation2, Citation5, Citation15, Citation16 Perhaps only the introduction of HEAs based on refractory metals,Citation29, Citation118–120, Citation156, Citation158, Citation163, Citation164, Citation281, Citation287, Citation291–301 instigated by Senkov, Miracle et al. Citation27, Citation28, Citation302 have provided a notable step change in this respect. The alloying screening methods discussed above are not limited in terms of potential alloying elements, and are hence to be viewed favourably in this respect. However, it can also be argued that the number of HEAs that have been assessed historically has in fact been too great, given the accuracy of characterisation that has been carried out. There have been too many alloys produced through too many processes leading to too many different conditions, such that we have not gained very much useful information, i.e. the sort of information that can be fed back into CALPHAD models. The challenge, then, is not just to predict alloy compositions with high potential, but also experimentally characterise candidate alloys to the extent that useful data are produced and promising alloys are not dismissed. The search for alloys should not be limited in terms of its scope, but it may be wise to restrict the number of candidate HEAs that are examined if the quality data gathered from large numbers of alloys is somewhat lacking. Quality should take some precedent over quantity.
8. Improved understanding
It is undoubtable that the task of HEA selection will add immeasurably to our understanding of phase formation in exotic systems, and to our ability to predict complex microstructures in multicomponent systems. Outside of this pursuit, however, the study of HEA behaviours also has the potential to contribute significantly to our fundamental understanding of alloys. It has often been claimed that HEAs display unusual characteristics, and while in some cases these may have been observed in other systems of alloys, they have yet to be fully understood.
Perhaps the most prominent example of an HEA displaying rather unique behaviour is CrMnFeCoNi. It has already been discussed that CrMnFeCoNi is not thermodynamically stable as a single phase at all temperatures. However, it can be readily heat treated to exist as a single fcc solid solution, and when tested in this condition it demonstrates some remarkable properties. Its yield strength is a strong function of temperature, increasing markedly with decreasing temperature.Citation36, Citation38, Citation40, Citation41, Citation303 This in itself is not unexpected, since although such temperature dependence is rare in pure fcc metals, it is observed in a number of fcc alloy solid solutions.Citation179, Citation304–309 What is unusual, however, is that this increase in yield stress at lower temperatures is accompanied by significant increases in ductility, toughness and ultimate-tensile strength (UTS). Indeed, at cryogenic temperatures, the ductility and toughness values attainable are quite exceptional: εf,eng > 0.7, KJIc > 200 MPa m1/2 and σUTS > 1GPa,Citation36, Citation40, Citation41 see Fig. .
10 Engineering stress vs. strain curves of the HEA CoCrFeMnNi at different temperatures in the (a) fine-grained (grain size 4.4 μm) and (b) coarse-grained (grain size 155 μm) condition. The inset in (a) shows a small load drop after yielding for a fine-grained sample tested at 473 K. Reprinted fromCitation36 with permission from Elsevier
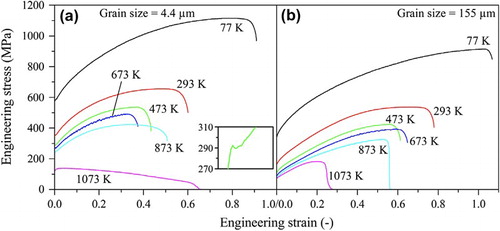
The impressive ductility and toughness is thought to be due to a high work-hardening rate, which is facilitated by high levels of deformation-induced nanotwinning at very low temperatures.Citation36, Citation40, Citation41, Citation46 The prevalence of this twinning can be attributed to a particularly low stacking-fault energy.Citation37, Citation43, Citation47, Citation310 However, while the ductility increase with decreasing temperature can be readily interpreted, the temperature dependence of yield stress in this compositionally complex alloy, and other HEAs is less well understood. This point was highlighted recently in the study by Wu et al.,Citation42 which assessed the temperature dependence of yield stress in a number of equiatomic ternary and quaternary alloys based on CrMnFeCoNi. They highlighted that a key issue associated with modelling solute effects in HEAs is that there is no clear distinction between solute and solvent species. This is particularly pertinent for equiatomic HEAs like CrMnFeCoNi.
It has been recommended that instead of envisaging dislocations being impeded by discrete solute atoms in a matrix, they should be viewed as moving through an effective medium in which the resistance is created by an average effect. To this end, Wu et al. Citation42 used a modified Peierls-Nabarro lattice resistance to model the yield behaviour of CrMnFeCoNi, which accounted for thermal activation through the effect of temperature on dislocation width.Citation311–313 Recently, a more advanced Peierls-Nabarro model, which accounted for segregation to stacking faults among other complexities, was successfully applied to CrMnFeCoNi by Patriarca et al. Citation57
This Peierls-Nabarro approach is in contrast to that taken by Toda-Caraballo and Rivera-Diáz-del-Castillo,Citation314 who modified Labusch's model for solid-solution strengthening in concentrated alloys.Citation178, Citation315 Labusch's treatment not only accounts for the effect of local strain fields around solute atoms, but also local changes in elastic modulus caused by their presence. This treatment was extended to HEAs, despite there being no clear distinction between solute or solvent, by estimating local changes in lattice spacing using the multicomponent model proposed by Moreen.Citation316 Good agreement was claimed between modelled and experimentally measured hardness values for many HEAs. However, the analysis used to reach this conclusion is questionable, since almost all the HEAs that were considered do not appear to have been measured in a single-phase solid-solution state. The difficulty is that alloys with larger atomic size misfits, which should in theory see increased solid-solution strengthening, tend to be unstable as single-phase solid solutions (Hume-Rothery) and instead appear hard due to the formation of extra phases. Hence, the lack of suitable case studies for solute strengthening in concentrated alloys is not surprising.
Even when suitable solid solutions can be made, the effects of short-range ordering (SRO) on mechanical behaviour could provide yet more complication.Citation309,Citation317,Citation318 SRO is also of particular interest to those modelling thermodynamic stability, since any ordering or clustering in a solid solution inherently reduces the configurational entropy of the system – equation 1 is only valid for an ideal solution, in which mixing is truly random. This point was highlighted recently by Bhadeshia.Citation247 Measuring SRO involves complex analyses of neutron or X-ray diffuse scattering data, as for the lattice strains discussed above. It is unlikely that SRO can be probed easily using atomic-probe tomography,Citation247 since the resolution of the technique is not sufficient.
Further interesting topics and questions have arisen from observations of other phenomena in HEA studies. For instance, a number of studies have observed serrations in the stress–strain curves of HEAs,Citation42, Citation319, Citation320 see Fig. . Classically, such serrations have been associated with dynamic strain aging (also known as the Portevin Le Chatilier effectCitation321, Citation322), and it is not clear where they are derived from in complex alloys like HEAs. It is possible that the diffusion of one set of solute atoms is causing this effect, but a more elaborate mechanism could also be at work.
11 Stress v. displacement curves of the HEA AlCr
Fe
Mn
Ni
in tension at temperatures of 573 and 673 K at a strain rate of
s−1. Reprinted fromCitation319 with permission from Springer

9. Concluding remarks
Based on the evidence that has been presented in the literature to date, it appears that the influence of the HEA core effects associated with entropic stabilisation, lattice distortion and sluggish diffusion may not be as significant as was first proposed. There are very few examples of HEAs that are believed to exist as entropically stablised solid solutions, and both experiment and theory suggest that the addition of more components to an alloy is likely to result in intermetallic formation or phase separation. Limited evidence exists as to the extent of lattice strain in the HEAs, and it can be argued that severe distortions would lead to rapid intermetallic formation (Hulme-Rothery). Normalised activation energies for diffusion in CrMnFeCoNi do appear to be higher than in conventional alloys, but the effect of variations in values must also be accounted for. In addition, there have been several reports of rapid precipitation in HEAs, indicating that diffusion kinetics in many HEAs are not slow. It is unclear what precisely the so-called cocktail effect refers to, and how it applies to HEAs to a greater extent than conventional alloys.
Nevertheless, HEAs offer a new and exciting approach to alloy design, with one of their most promising applications being structural materials. To this end, research focus should move away from trying to obtain single-phase HEAs, and instead develop alloys that posses the correct balance of mechanical properties. The possible number of candidate HEA compositions is huge, and educated sampling of compositional space is needed if research effort is to be expended efficiently. While parametric studies may be able to give some indication of the likelihood of solid-solution stability, and CALPHAD can give reasonable predictions of the majority phases in HEAs, both have limited success in predicting the formation of intermetallic compounds, which are of critical importance for the development of structural materials. However, they can be cleverly exploited as first-approximation guides in frameworks for alloy selection.
Rapid-throughput screening methods will likely be required to vet potential HEA compositions after predictive screening, but there are significant issues associated with their practical implementation. There is also a danger that promising alloys could be dismissed too early by these approaches, since they are less likely to explore the complex links between heat treatment, microstructure and properties. Indeed, careful experimental assessment of HEAs in general is necessary before conclusions are drawn about the characteristics and stabilities of their microstructures. Nanoscale precipitates and phase separations have often been observed, which necessitate the use of high-resolution techniques. Accurate and rapid microstructural measurement techniques are key if alloy selection initiatives are to be successful. The data they produced must be of sufficient quality to feed back into selection models.
Despite the conclusions drawn with respect to the founding principles of HEAs, we do not believe that changing the name of the research field would be helpful moving forwards. What is required is a change in the underlying science associated with the name. In our opinion a far more important matter is the adoption of a consistent alloy naming convention within the community. With that in mind, we suggest that when expressing HEA compositions as atomic ratios, the elements are listed by atomic number, and that the order is not influenced by the relative concentrations of each species.
In a recent review,Citation8 it was proposed that the traditional principles of physical metallurgy that have been developed over the past century need to be modified in light of HEA behaviour. We do not believe this is the case – although some HEAs do exhibit unusual behaviour, it is likely that this is derived from the same processes already acting in conventional alloys. Nonetheless, the study of HEAs does offer tremendous potential to improve our fundamental understanding of the mechanical and thermodynamic behaviour of alloys, as well as develop useful new materials.
HEAs have thrust us out of an age of limitation, where alloys were designed around one principal element, and into a new world of seemingly endless possibility. However, careful and educated alloying is required, such that we focus our attention on key features of the compositional landscape presented by HEAs, rather than wander somewhat aimlessly in its limitless expanse.
Acknowledgements
The authors would like to acknowledge L.R. Owen, Dr H.J. Stone, Dr K.A Christofidou and Prof. I. Todd for useful discussions and suggestions in reference to this work. The authors would also like to thank the reviewers of the original version of this manuscript for their exceptionally insightful and useful comments. One of the authors (NGJ) would like to acknowledge the EPSRC/Rolls-Royce Strategic Partnership for funding under EP/M005607/1.
ORCID
E. J. Pickering http://orcid.org/0000-0002-7516-868X
N. G. Jones http://orcid.org/0000-0002-1851-2261
References
- J. W. Yeh, S. K. Chen, S. J. Lin, J. Y. Gan, T. S. Chin, T. T. Shun, C. H. Tsau and S. Y. Chang: ‘Nanostructured high-entropy alloys with multiple principal elements: novel alloy design concepts and outcomes’, Adv. Eng. Mater., 2004, 6, 299–303.
- B. Cantor, I. T. H. Chang, P. Knight and A. J. B. Vincent: ‘Microstructural development in equiatomic multicomponent alloys’, Mater. Sci. Eng. A, 2004, 375–377, 213–218.
- J. W. Yeh, S. K. Chen, J. Y. Gan, S. J. Lin, T. S. Chin, T. T. Shun, C. H. Tsau and S. Y. Chang: ‘Formation of simple crystal structures in Cu–Co–Ni–Cr–Al–Fe–Ti–V alloys with multiprincipal metallic elements’, Metall. Mater. Trans. A, 2004, 35, 2533–2536.
- J. W. Yeh: ‘Recent progress in high-entropy alloys’, Ann. Chim. – Sci. Mater., 2006, 31, 633–648.
- J. W. Yeh: ‘Alloy design strategies and future trends in high-entropy alloys’, JOM, 2013, 65, 1759–1771.
- M. H. Tsai and J. W. Yeh: ‘High-entropy alloys: a critical review’, Mater. Res. Lett., 2014, 2, 107–123.
- B. S. Murty, J. W. Yeh and S. Ranganathan: ‘High-entropy alloys’, 1st edn; 2014, London, Butterworth-Heinemann.
- J. W. Yeh: ‘Physical metallurgy of high-entropy alloys’, JOM, 2015, 67, 2254–2261.
- http://www.scopus.com/ (accessed 16 January 2016).
- M. H. Tsai: ‘Physical properties of high entropy alloys’, Entropy, 2013, 15, 5338–5345.
- B. Cantor: ‘Multicomponent and high entropy alloys’, Entropy, 2014, 16, 4749–4768.
- Y. F. Ye, Q. Wang, J. Lu, C. T. Liu and Y. Yang: ‘High-entropy alloy: challenges and prospects’, Mater. Today, 2015, doi:10.1016/j.mattod.2015.11.026.
- A. T. Samaei, M. M. Mirsayar and M. R. M. Aliha: ‘The microstructure and mechanical behavior of modern high temperature alloys’, Eng. Solid Mech., 2015, 3, 1–20.
- Y. Zhang, T. T. Zuo, Z. Tang, M. C. Gao, K. A. Dahmen, P. K. Liaw and Z. P. Lu: ‘Microstructures and properties of high-entropy alloys’, Prog. Mater. Sci., 2014, 61, 1–93.
- D. B. Miracle: ‘Critical assessment 14: high entropy alloys and their development as structural materials’, Mater. Sci. Technol., 2015, 31, 1142–1147.
- D. B. Miracle, J. D. Miller, O. N. Senkov, C. Woodward, M. D. Uchic and J. Tiley: ‘Exploration and development of high entropy alloys for structural applications’, Entropy, 2014, 16, 494–525.
- S. Praveen, B. S. Murty and R. S. Kottada: ‘Alloying behavior in multi-component AlCoCrCuFe and NiCoCrCuFe high-entropy alloys’, Mater. Sci. Eng. A, 2012, 534, 83–89.
- K. G. Pradeep, N. Wanderka, P. Choi, J. Banhart, B. S. Murty and D. Raabe: ‘Atomic-scale compositional characterization of a nanocrystalline AlCrCuFeNiZn high-entropy alloy using atom probe tomography’, Acta Mater., 2013, 61, 4696–4706.
- F. Otto, Y. Yang, H. Bei and E. P. George: ‘Relative effects of enthalpy and entropy on the phase stability of equiatomic high-entropy alloys’, Acta Mater., 2013, 61, 2628–2638.
- A. K. Singh and A. Subramaniam: ‘On the formation of disordered solid solutions in multi-component alloys’, J. Alloys Compd., 2014, 587, 113–119.
- N. G. Jones, J. W. Aveson, A. Bhowmik, B. D. Conduit and H. J. Stone: ‘On the entropic stabilisation of an Al0.5CrFeCoNiCu high entropy alloy’, Intermetallics, 2014, 54, 148–153.
- C. C. Tasan, Y. Deng, K. G. Pradeep, M. J. Yao, H. Springer and D. Raabe: ‘Composition dependence of phase stability, deformation mechanisms, and mechanical properties of the CoCrFeMnNi high-entropy alloy system’, JOM, 2014, 66, 1993–2001.
- D. Ma, B. Grabowski, F. Körmann, J. Neugebauer and D. Raabe: ‘Ab initio thermodynamics of the CoCrFeMnNi high entropy alloy: importance of entropy contributions beyond the configurational one’, Acta Mater., 2015, 100, 90–97.
- O. N. Senkov, J. D. Miller, D. B. Miracle and C. Woodward: ‘Accelerated exploration of multi-principal element alloys with solid solution phases’, Nature Commun., 2015, 6, 6529.
- O. N. Senkov, J. D. Miller, D. B. Miracle and C. Woodward: ‘Accelerated exploration of multi-principal element alloys for structural applications’, Calphad, 2015, 50, 32–48.
- M. C. Troparevsky, J. R. Morris, P. R. C. Kent, A. R. Lupini and G. M. Stocks: ‘Criteria for predicting the formation of single-phase high-entropy alloys’, Phys. Rev. X, 2015, 5, 011041-1–011041-6.
- O. N. Senkov, G. B. Wilks, D. B. Miracle, C. P. Chuang and P. K. Liaw: ‘Refractory high-entropy alloys’, Intermetallics, 2010, 18, 1758–1765.
- O. N. Senkov, G. B. Wilks, J. M. Scott and D. B. Miracle: ‘Mechanical properties of Nb25Mo25Ta25W25 and V20Nb20Mo20Ta20W20 refractory high entropy alloys’, Intermetallics, 2011, 19, 698–706.
- Y. D. Wu, Y. H. Cai, X. H. Chen, T. Wang, J. J. Si, L. Wang, Y. D. Wang and X. D. Hui: ‘Phase composition and solid solution strengthening effect in TiZrNbMoV high-entropy alloys’, Mater. Design, 2015, 83, 651–660.
- W. R. Wang, W. L. Wang, S. C. Wang, Y. C. Tsai, C. H. Lai and J. W. Yeh: ‘Effects of Al addition on the microstructure and mechanical property of AlxCoCrFeNi high-entropy alloys’, Intermetallics, 2012, 26, 44–51.
- W. R. Wang, W. L. Wang and J. W. Yeh: ‘Phases, microstructure and mechanical properties of AlxCoCrFeNi high-entropy alloys at elevated temperatures’, J. Alloys Compd., 2014, 589, 143–152.
- D. Li and Y. Zhang: ‘The ultrahigh Charpy impact toughness of forged AlxCoCrFeNi high entropy alloys at room and cryogenic temperatures’, Intermetallics, 2016, 70, 24–28.
- J. Y. He, C. Zhu, D. Q. Zhou, W. H. Liu, T. G. Nieh and Z. P. Lu: ‘Steady state flow of the FeCoNiCrMn high entropy alloy at elevated temperatures’, Intermetallics, 2014, 55, 9–14.
- B. Schuh, F. Mendez-Martin, B. Volker, E. P. George, H. Clemens, R. Pippan and A. Hohenwarter: ‘Mechanical properties, microstructure and thermal stability of a nanocrystalline CoCrFeMnNi high-entropy alloy after severe plastic deformation’, Acta Mater., 2015, 96, 258–268.
- E. J. Pickering, R. Muñoz-Moreno, H. J. Stone and N. G. Jones: ‘Precipitation in the equiatomic high-entropy alloy CrMnFeCoNi’, Scr. Mater., 2016, 113, 106–109.
- F. Otto, A. Dlouhý, Ch. Somsen, H. Bei, G. Eggeler and E. P. George: ‘The influences of temperature and microstructure on the tensile properties of a CoCrFeMnNi high-entropy alloy’, Acta Mater., 2013, 61, 5743–5755.
- A. J. Zaddach, C. Niu, C. C. Koch and D. L. Irving: ‘Mechanical properties and stacking fault energies of NiFeCrCoMn high-entropy alloy’, JOM, 2013, 65, 1780–1789.
- C. Zhu, Z. P. Lu and T. G. Nieh: ‘Incipient plasticity and dislocation nucleation of FeCoCrNiMn high-entropy alloy’, Acta Mater., 2013, 61, 2993–3001.
- W. H. Liu, Y. Wu, J. Y. He, T. G. Nieh and Z. P. Lu: ‘Grain growth and the Hall–Petch relationship in a high-entropy FeCrNiCoMn alloy’, Scr. Mater., 2013, 68, 526–529.
- A. Gali and E. P. George: ‘Tensile properties of high- and medium-entropy alloys’, Intermetallics, 2013, 39, 74–78.
- B. Gludovatz, A. Hohenwarter, D. Catoor, E. H. Chang, E. P. George and R. O. Ritchie: ‘A fracture-resistant high-entropy alloy for cryogenic applications’, Science, 2014, 345, 1153–1158.
- Z. Wu, H. Bei, G. M. Pharr and E. P. George: ‘Temperature dependence of the mechanical properties of equiatomic solid solution alloys with face-centrede cubic crystal structures’, Acta Mater., 2014, 81, 428–441.
- P. P. Bhattacharjee, G. D. Sathiaraj, M. Zaid, J. R. Gatti, C. Lee, C. W. Tsai and J. W. Yeh: ‘Microstructure and texture evolution during annealing of equiatomic CoCrFeMnNi high-entropy alloy’, J. Alloys Compd, 2014, 587, 544–552.
- F. Otto, N. L. Hanold and E. P. George: ‘Microstructural evolution after thermomechanical processing in an equiatomic, single-phase CoCrFeMnNi high-entropy alloy with special focus on twin boundaries’, Intermetallics, 2014, 54, 39–48.
- Y. Wu, W. H. Liu, X. L. Wang, D. Ma, A. D. Stoica, T. G. Nieh, Z. B. He and Z. P. Lu: ‘In-situ neutron diffraction study of deformation behavior of a multi-component high-entropy alloy’, Appl. Phys. Lett., 2014, 104, 051910-1–051910-5.
- N. Stepanov, M. Tikhonovsky, N. Yurchenko, D. Zyabkin, M. Klimova, S. Zherebtsov, A. Efimov and G. Salishchev: ‘Effect of cryo-deformation on structure and properties of CoCrFeNiMn high-entropy alloy’, Intermetallics, 2015, 59, 8–17.
- G. Laplanche, O. Horst, F. Otto, G. Eggeler and E. P. George: ‘Microstructural evolution of a CoCrFeMnNi high-entropy alloy after swaging and annealing’, J.Alloys Compd., 2015, 647, 548–557.
- G. Laplanche, P. Gadaud, O. Horst, F. Otto, G. Eggeler and E. P. George: ‘Temperature dependencies of the elastic moduli and thermal expansion coefficient of an equiatomic, single-phase CoCrFeMnNi high-entropy alloy’, J. Alloys Compd., 2015, 623, 348–353.
- A. Haglund, M. Koehler, D. Catoor, E. P. George and V. Keppens: ‘Polycrystalline elastic moduli of a high-entropy alloy at cryogenic temperatures’, Intermetallics, 2015, 58, 62–64.
- B. Gludovatz, E. P. George and R. O. Ritchie: ‘Processing, microstructure and mechanical properties of the CrMnFeCoNi high-entropy alloy’, JOM, 2015, 67, 2262–2270.
- W. Ji, W. Wang, H. Wang, J. Zhang, Y. Wang, F. Zhang and Z. Fu: ‘Alloying behavior and novel properties of CoCrFeNiMn high-entropy alloy fabricated by mechanical alloying and spark plasma sintering’, Intermetallics, 2015, 56, 24–27.
- G. D. Sathiaraj and P. P. Bhattacharjee: ‘Effect of cold-rolling strain on the evolution of annealing texture of equiatomic CoCrFeMnNi high entropy alloy’, Mater. Charact., 2015, 109, 189–197.
- G. D. Sathiaraj and P. P. Bhattacharjee: ‘Effect of starting grain size on the evolution of microstructure and texture during thermo-mechanical processing of CoCrFeMnNi high entropy alloy’, J. Alloys Compd., 2015, 647, 82–96.
- G. D. Sathiaraj, C. Lee, C. W. Tsai, J. W. Yeh and P. P. Bhattacharjee: ‘Evolution of microstructure and crystallographic texture in severely cold rolled high entropy equiatomic CoCrFeMnNi alloy during annealing’, IOP Conf. Ser.: Mater. Sci. Eng., 2015, 82, 012068.
- G. D. Sathiaraj, M. Z. Ahmed and P. P. Bhattacharjee: ‘Microstructure and texture of heavily cold-rolled and annealed fcc equiatomic medium to high entropy alloys’, J. Alloys Compd., 2016, 664, 109–119.
- Z. Zhang, M. M. Mao, J. Wang, B. Gludovatz, Z. Zhang, S. X. Mao, E. P. George, Q. Yu and R. O. Ritchie: ‘Nanoscale origins of the damage tolerance of the high-entropy alloy CrMnFeCoNi’, Nat. Commun., 2015, DOI 10.1038/ncomms10143.
- L. Patriarca, A. Ojha, H. Sehitoglu and Y. I. Chumlyakov: ‘Slip nucleation in single crystal FeNiCoCrMn high entropy alloy’, Scr. Mater., 2016, 112, 54–57.
- G. A. Salishchev, M. A. Tikhonovsky, D. G. Shaysultanov, N. D. Stepanov, A. V. Kuznetsov, I. V. Kolodiy, A. S. Tortika and O. N. Senkov: ‘Effect of Mn and V on structure and mechanical properties of high-entropy alloys based on CoCrFeNi system’, J. Alloys Compd., 2014, 591, 11–21.
- M. Laurent-Brocq, A. Akhatova, L. Perrière, S. Chebini, X. Sauvage, E. Leroy and Y. Champion: ‘Insights into the phase diagram of the CrMnFeCoNi high entropy alloy’, Acta Mater., 2015, 88, 355–365.
- N. D. Stepanov, D. G. Shaysultanov, G. A. Salishchev, M. A. Tikhonovsky, E. E. Oleynik, A. S. Tortika and O. N. Senkov: ‘Effect of V content on microstructure and mechanical properties of the CoCrFeMnNiVx high entropy alloys’, J. Alloys Compd., 2015, 628, 170–185.
- C. Y. Hsu, J. W. Yeh, S. K. Chen and T. T. Shun: ‘Wear resistance and high-temperature compression strength of Fcc CuCoNiCrAl0.5Fe alloy with boron addition’, Metall. Trans. A, 2004, 35, 1465–1469.
- M. R. Chen, S. J. Lin, J. W. Yeh, S. K. Chen, Y. S. Huang and M. H. Chuang: ‘Effect of vanadium addition on the microstructure, hardness, and wear resistance of Al0.5CoCrCuFeNi high-entropy alloy’, Metall. Mater. Trans. A, 2006, 37A, 1363–1369.
- M. R. Chen, S. J. Lin, J. W. Yeh, S. K. Chen, Y. S. Huang and C. P. Tu: ‘Microstructure and properties of Al0.5CoCrCuFeNiTix (x=0-2) high-entropy alloys’, Mater. Trans., 2006, 47, 1395–1401.
- C. C. Tung, J. W. Yeh, T. T. Shun, S. K. Chen, Y. S. Huang and H. C. Chen: ‘On the elemental effect of AlCoCrCuFeNi high-entropy alloy system’, Mater. Lett., 2007, 61, 1–5.
- C. W. Tsai, Y. L. Chen, M. H. Tsai, J. W. Yeh, T. T. Shun and S. K. Chen: ‘Deformation and annealing behaviors of high-entropy alloy Al0.5CoCrCuFeNi’, J. Alloys Compd., 2009, 486, 427–435.
- C. W. Tsai, M. H. Tsai, J. W. Yeh and C. C. Yang: ‘Effect of temperature on mechanical properties of Al0.5CoCrCuFeNi wrought alloy’, J. Alloys Compd., 2010, 490, 160–165.
- M. A. Hemphill, T. Yuan, G. Y. Wang, J. W. Yeh, C. W. Tsai, A. Chuang and P. K. Liaw: ‘Fatigue behavior of Al0.5CoCrCuFeNi high entropy alloys’, Acta Mater., 2012, 60, 5723–5734.
- M. A. Hemphill: ‘Fatigue behavior of high-entropy alloys’, PhD thesis, The University of Tennessee, Knoxville, 2012.
- C. Ng, S. Guo, J. Luan, S. Shi and C. T. Liu: ‘Entropy-driven phase stability and slow diffusion kinetics in an Al0.5CoCrCuFeNi high entropy alloy’, Intermetallics, 2012, 31, 165–172.
- N. G. Jones, A. Frezza and H. J. Stone: ‘Phase equilibria of an Al0.5CrFeCoNiCu high entropy alloy’, Mater. Sci. Eng. A, 2014, 615, 214–221.
- N. G. Jones, K. A. Christofidou and H. J. Stone: ‘Rapid precipitation in an Al0.5CrFeCoNiCu high entropy alloy’, Mater. Sci. Technol., 2015, 31, 1171–1177.
- E. J. Pickering, H. J. Stone and N. G. Jones: ‘Fine-scale precipitation in the high-entropy alloy Al0.5CrFeCoNiCu’, Mater. Sci. Eng. A, 2015, 645, 65–71.
- X. D. Xu, P. Liu, S. Guo, A. Hirata, T. Fujita, T. G. Nieh, C. T. Liu and M. W. Chen: ‘Nanoscale phase separation in a FCC-based CoCrCuFeNiAl0.5 high-entropy alloy’, Acta Mater., 2015, 84, 145–152.
- N. G. Jones, R. Izzo, P. M. Mignanelli, K. A. Christofidou and H. J. Stone: ‘Phase evolution in an Al0.5CrFeCoNiCu high entropy alloy’, Intermetallics, 2016, 71, 43–50.
- C. J. Tong, Y. L. Chen, S. K. Chen, J. W. Yeh, T. T. Shun, C. H. Tsau, S. J. Lin and S. Y. Chang: ‘Microstructure characterization of AlxCoCrCuFeNi high-entropy alloy system with multiprincipal elements’, Metall. Mater. Trans. A, 2005, 36A, 881–893.
- J. M. Wu, S. J. Lin, J. W. Yeh, S. K. Chen, Y. S. Huang and H. C. Chen: ‘Adhesive wear behavior of AlxCoCrCuFeNi high-entropy alloys as a function of aluminum content’, Wear, 2006, 261, 513–519.
- L. H. Wen, H. C. Kou, J. S. Li, H. Chang, X. Y. Xue and L. Zhou: ‘Effect of aging temperature on microstructure and properties of AlCoCrCuFeNi high-entropy alloy’, Intermetallics, 2009, 17, 266–269.
- W. Y. Tang and J. W. Yeh: ‘Effect of aluminum content on plasma-nitrided AlxCoCrCuFeNi high-entropy alloys’, Metall. Mater. Trans. A, 2009, 40A, 1479–1486.
- S. Singh, N. Wanderka, B. S. Murty, U. Glatzel and J. Banhart: ‘Decomposition in multi-component AlCoCrCuFeNi high-entropy alloy’, Acta Mater., 2011, 59, 182–190.
- X. Ye, M. Ma, Y. Cao, W. Liu, X. Ye and Y. Gu: ‘The property research on high-entropy alloy AlxFeCoNiCuCr coating by laser cladding’, Phys. Procedia, 2011, 12, 303–312.
- A. V. Kuznetsov, D. G. Shaysultanov, N. D. Stepanov, G. A. Salishchev and O. N. Senkov: ‘Tensile properties of an AlCrCuNiFeCo high-entropy alloy in as-cast and wrought conditions’, Mater. Sci. Eng. A, 2012, 533, 107–118.
- R. Sriharitha, B. S. Murty and R. S. Kottada: ‘Phase formation in mechanically alloyed AlxCoCrCuFeNi (x = 1/4, 0.45, 1, 2.5, 5 mol) high entropy alloys’, Intermetallics, 2013, 32, 119–126.
- R. Sriharitha, B. S. Murty and R. S. Kottada: ‘Alloying, thermal stability and strengthening in spark plasma sintered AlxCoCrCuFeNi high entropy alloys’, J. Alloys Compd., 2014, 583, 419–426.
- Z. F. Wu, X. D. Wang, Q. P. Cao, G. H. Zhao, J. X. Li, D. X. Zhang, J. J. Zhu and J. Z. Jiang: ‘Microstructure characterization of AlxCo1Cr1Cu1Fe1Ni1 (x=0 and 2.5) high-entropy alloy films’, J. Alloys Compd., 2014, 609, 137–142.
- L. J. Santodonato, Y. Zhang, M. Feygenson, C. M. Parish, M. C. Gao, R. J .K. Weber, J. C. Neuefeind, Z. Tang and P. K. Liaw: ‘Deviation from high-entropy configurations in the atomic distributions of a multi-principal-element alloy’, Nat. Commun., 2015, doi:10.1038/ncomms6964.
- C. Y. Yu, X. D. Xu, M. W. Chen and C. T. Liu: ‘Atomistic mechanism of nano-scale phase separation in fcc-based high entropy alloys’, J. Alloys Compd., 2016, doi:10.1016/j.jallcom.2015.12.004.
- Y. J. Zhou, Y. Zhang, Y. L. Wang and G. L. Chen: ‘Microstructure and compressive properties of multicomponent Alx(TiVCrMnFeCoNiCu)100-x high-entropy alloys’, Mater. Sci. Eng. A, 2007, 454–455, 260–265.
- U. S. Hsu, U. D. Hung, J. W. Yeh, S. K. Chen, Y. S. Huang and C. C. Yang: ‘Alloying behavior of iron, gold and silver in AlCoCrCuNi-based equimolar high-entropy alloys’, Mater. Sci. Eng. A, 2007, 460–461, 403–408.
- X. F. Wang, Y. Zhang, Y. Qiao and G. L. Chen: ‘Novel microstructure and properties of multicomponent CoCrCuFeNiTix alloys’, Intermetallics, 2007, 15, 357–362.
- F. J. Wang and Y. Zhang: ‘Effect of Co addition on crystal structure and mechanical properties of Ti0.5CrFeNiAlCo high entropy alloy’, Mater. Sci. Eng. A, 2008, 496, 214–216.
- Y. P. Wang, B. S. Li, M. X. Ren, C. Yang and H. Z. Fu: ‘Microstructure and compressive properties of AlCrFeCoNi high entropy alloy’, Mater. Sci. Eng. A, 2008, 491, 154–158.
- W. Y. Tang, M. H. Chuang, H. Y. Chen and J. W. Yeh: ‘Microstructure and mechanical performance of brand-new Al0.3CrFe1.5MnNi0.5 high-entropy alloys’, Adv. Eng. Mater., 2009, 11, 788–794.
- T. T. Shun and Y. C. Du: ‘Microstructure and tensile behaviors of FCC Al0.3CoCrFeNi high entropy alloy’, J. Alloys Compd., 2009, 479, 157–160.
- Y. J. Zhou, Y. Zhang, F. J. Wang, Y. L. Wang and G. L. Chen: ‘Effect of Cu addition on the microstructure and mechanical properties of AlCoCrFeNiTi0.5 solid-solution alloy’, J. Alloys Compd., 2008, 466, 201–204.
- K. B. Zhang, Z. Y. Fu, J. Y. Zhang, J. Shi, W. M. Wang, H. Wang, Y. C. Wang and Q. J. Zhang: ‘Nanocrystalline CoCrFeNiCuAl high-entropy solid solution synthesized by mechanical alloying’, J. Alloys Compd., 2009, 485, L31–L34.
- K. B. Zhang, Z. Y. Fu, J. Y. Zhang, W. M. Wang, H. Wang, Y. C. Wang, Q. J. Zhang and J. Shi: ‘Microstructure and mechanical properties of CoCrFeNiTiAlx high-entropy alloys’, J. Alloys Compd., 2009, 485, L31–L34.
- H. P. Chou, Y. S. Chang, S. W. Chen and J. W. Yeh: ‘ Microstructure, thermophysical and electrical properties in AlxCoCrFeNi (0 ≤ x ≤ 2) high-entropy alloys ’, Mater. Sci. Eng. B, 2009, 163, 184–189.
- S. T. Chen, W. Y. Tang, Y. F. Kuo, S. Y. Chen, C. H. Tsau, T. T. Shun and J. W. Yeh: ‘Microstructure and properties of age-hardenable AlxCrFe1.5MnNi0.5 alloys’, Mater. Sci. Eng. A, 2010, 527, 5818–5825.
- K. B. Zhang, Z. Y. Fu, J. Y. Zhang, J. Shi, W. M. Wang, H. Wang, Y. C. Wang and Q. J. Zhang: ‘Annealing on the structure and properties evolution of the CoCrFeNiCuAl high-entropy alloy’, J. Alloys Compd., 2010, 502, 295–299.
- T. T. Shun, C. H. Hung and C. F. Lee: ‘Formation of ordered/disordered nanoparticles in FCC high entropy alloys’, J. Alloys Compd., 2010, 493, 105–109.
- T. T. Shun, C. H. Hung and C. F. Lee: ‘The effects of secondary elemental Mo or Ti addition in Al0.3CoCrFeNi high-entropy alloy on age hardening at 700°C’, J. Alloys Compd., 2010, 495, 55–58.
- C. Li, J. C. Li, M. Zhao and Q. Jiang: ‘Effect of aluminum contents on microstructure and properties of AlxCoCrFeNi alloys’, J. Alloys Compd., 2010, 504S, S515–S518.
- C. M. Lin, H. L. Tsai and H. Y. Bor: ‘Effect of aging treatment on microstructure and properties of high-entropy Cu0.5CoCrFeNi alloy’, Intermetallics, 2010, 18, 1244–1250.
- C. M. Lin and H. L. Tsai: ‘Equilibrium phase of high-entropy FeCoNiCrCu0.5 alloy at elevated temperature’, J. Alloys Compd., 2010, 489, 30–35.
- C. M. Lin and H. L. Tsai: ‘Evolution of microstructure, hardness, and corrosion properties of high-entropy Al0.5CoCrFeNi alloy’, Intermetallics, 2011, 19, 288–294.
- M. H. Chuang, M. H. Tsai, W. R. Wang, S. J. Lin and J. W. Yeh: ‘Microstructure and wear behavior of AlxCo1.5CrFeNi1.5Tiy high-entropy alloys’, Acta Materialia, 2011, 59, 6308–6317.
- C. Y. Hsu, C. C. Juan, W. R. Wang, T. S. Sheu, J. W. Yeh and S. K. Chen: ‘On the superior hot hardness and softening resistance of AlCoCrxFeMo0.5Ni high-entropy alloys’, Mater. Sci. Eng. A, 2011, 528, 3581–2588.
- B. Ren, Z. X. Liu, B. Cai, M. X. Wang and L. Shi: ‘Aging behavior of a CuCr2Fe2NiMn high-entropy alloy’, Mater. Design, 2012, 33, 121–126.
- P. Jinhong, P. Ye, Z. Hui and Z. Lu: ‘ Microstructure and properties of AlCrFeCuNix (0.6 ≤ x ≤ 1.4) high-entropy alloys’, Mater. Sci. Eng., 2012, 534, 228–233.
- L. C. Tsao, C. S. Chen and C. P. Chu: ‘Age hardening reaction of the Al0.3CrFe1.5MnNi0.5 high entropy alloy’, Mater. Design, 2012, 36, 854–858.
- Y. Wang, S. Ma, X. Chen, J. Shi, Y. Zhang and J. Qiao: ‘Optimizing mechanical properties of AlCoCrFeNiTix high-entropy alloys by tailoring microstructures’, Acta Metall. Sin. (English Lett.), 2013, 26, 277–284.
- B. Li, K. Peng, A. Hu, L. Zhou, J. Zhu and D. Li: ‘Structure and properties of FeCoNiCrCu0.5Alx high-entropy alloy’, Trans. Nonferrous Metals Soc. Chin., 2013, 23, 735–741.
- C. Y. Hsu, C. C. Juan, T. S. Sheu, S. W. Chen and J. W. Yeh: ‘Effect of aluminum content on microstructure and mechanical properties of AlxCoCrFeMo0.5Ni high-entropy alloys’, JOM, 2013, 65, 1840–1847.
- M. H. Tsai, H. Yuan, G. Cheng, W. Xu, K. Y. Tsai, C. W. Tsai, W. W. Jian, C. C. Juan, W. J. Shen, M. H. Chuang, J. W. Yeh and Y. T. Zhu: ‘Morphology, structure and composition of precipitates in Al0.3CoCrCu0.5FeNi high-entropy alloy’, Intermetallics, 2013, 32, 329–336.
- X. W. Qiu, Y. P. Zhang, L. He and C. G. Liu: ‘Microstructure and corrosion resistance of AlCrFeCuCo high entropy alloy’, J. Alloys Compd., 2013, 549, 195–199.
- X. W. Qiu: ‘Microstructure and properties of AlCrFeNiCoCu high entropy alloy prepared by powder metallurgy’, J. Alloys Compd., 2013, 555, 246–249.
- Z. Fu, W. Chen, S. Fang, D. Zhang, H. Xiao and D. Zhu: ‘Alloying behavior and deformation twinning in a CoNiFeCrAl0.6Ti0.4 high entropy alloy processed by spark plasma sintering’, J. Alloys Compd., 2013, 553, 316–323.
- O. N. Senkov, S. V. Senkova and C. Woodward: ‘Effect of aluminum on the microstructure and properties of two refractory high-entropy alloys’, Acta Mater., 2014, 68, 214–228.
- O. N. Senkov, C. Woodward and D. B. Miracle: ‘Microstructure and properties of aluminum-containing refractory high-entropy alloys’, JOM, 2014, 65, 2030–2042.
- C. M. Liu, H. M. Wang, S. Q. Zhang, H. B. Tang and A. L. Zhang: ‘Microstructure and oxidation behavior of new refractory high entropy alloys’, J. Alloys Compd., 2014, 583, 162–169.
- U. Roy, H. Roy, H. Daoud, U. Glatzel and K. K. Ray: ‘Fracture toughness and fracture micromechanism in a cast AlCoCrCuFeNi high entropy alloy system’, Mater. Lett., 2014, 132, 186–189.
- Y. Sun, G. Zhao, X. Wen, J. Qiao and F. Yang: ‘Nanoindentation deformation of a bi-phase AlCrCuFeNi2 alloy’, J. Alloys Compd., 2014, 608, 49–53.
- J. Y. He, W. H. Liu, H. Wang, Y. Wu, X. J. Liu, T. G. Nieh and Z. P. Lu: ‘Effects of Al addition on structural evolution and tensile properties of the FeCoNiCrMn high-entropy alloy system’, Acta Mater., 2014, 62, 105–113.
- C. Ng, S. Guo, J. Luan, Q. Wang, J. Lu, S. Shi and C. T. Liu: ‘Phase stability and tensile properties of co-free Al0.5CrCuFeNi2 high-entropy alloys’, J. Alloys Compd., 2014, 584, 530–537.
- L. Jiang, Y. Lu, Y. Dong, T. Wang, Z. Cao and T. Li: ‘Annealing effects on the microstructure and properties of bulk high-entropy CoCrFeNiTi0.5 alloy casting ingot’, Intermetallics, 2014, 44, 37–43.
- H. F. Sun, C. M. Wang, X. Zhang, R. Z. Li and L. Y. Ruan: ‘Study of the microstructure and performance of high-entropy alloys AlxFeCuCoNiCrTi’, Mater. Res. Innovations, 2015, 19, S8-89–S8-93.
- D. Choudhuri, T. Alam, T. Borkar, B. Gwalani, A. S. Mantri, S. G. Srinivasan, M. A. Gibson and R. Banerjee: ‘Formation of a Huesler-like L21 phase in a CoCrCuFeNiAlTi high-entropy alloy’, Scr. Mater., 2015, 100, 36–39.
- Z. P. Lu, H. Wang, M. W. Chen, I. Baker, J. W. Yeh, C. T. Liu and T. G. Nieh: ‘An assessment on the future development of high-entropy alloys: summary from a recent workshop’, Intermetallics, 2015, 66, 67–76.
- H. R. Sistla, J. W. Newkirk and F. F. Liou: ‘Effect of Al/Ni ratio, heat treatment on phase transformations and microstructure of AlxFeCoCrNi2-x (x=0.3,1) high entropy alloys’, Mater. Design, 2015, 81, 113–121.
- C. Chen, S. Pang, Y. Chen and T. Zhang: ‘Microstructure and mechanical properties of Al20-xCr20+0.5xFe20Co20Ni20-x high entropy alloys’, J. Alloys Compd., 2016, 659, 279–287.
- J. Y. He, H. Wang, H. L. Huang, X. D. Xu, M. W. Chen, Y. Wu, X. J. Liu, T. G. Nieh, K. An and Z. P. Lu: ‘A precipitation-hardened high-entropy alloy with outstanding tensile properties’, Acta Mater., 2016, 102, 187–196.
- P. F. Yu, H. Cheng, L. J. Zhang, H. Zhang, M. Z. Ma, G. Li, P. K. Liaw and R. P. Liu: ‘Nanotwin's formation and growth in an AlCoCuFeNi high-entropy alloy’, Scr. Mater., 2016, 114, 31–34.
- T. Borkar, B. Gwalani, D. Choudhuri, T. Alam, A. S. Mantri, M. A. Gibson and R. Banerjee: ‘Hierarchical multi-scale microstructural evolution in an as-cast Al2CuCrFeNi2 complex concentrated alloy’, Intermetallics, 2016, 71, 31–42.
- C. Y. Hsu, T. S. Sheu, J. W. Yeh and S. W. Chen: ‘Effect of iron content on wear behavior of AlCoCrFexMo0.5Ni high-entropy alloys’, Wear, 2010, 268, 653–659.
- C. Y. Hsu, W. R. Wang, W. Y. Tang, S. W. Chen and J. W. Yeh: ‘Microstructure and mechanical properties of new AlCoxCrFeMo0.5Ni high-entropy alloys’, Adv. Eng. Mater., 2010, 12, 44–49.
- T. T. Shun, L. Y. Chang and M. H. Shiu: ‘Microstructure and mechanical properties of multiprincipal component CoCrFeNiMox alloys’, Mater. Charact., 2012, 70, 63–67.
- C. C. Juan, C. Y. Hsu, C. W. Tsai, W. R. Wang, T. S. Sheu, J. W. Yeh and S. K. Chen: ‘On microstructure and mechanical performance of AlCoCrFeMo0.5Nix high-entropy alloys’, Intermetallics, 2013, 32, 401–407.
- M. H. Tsai, K. Y. Tsai, C. W. Tsai, C. Lee, C. C. Juan and J. W. Yeh: ‘Criterion for sigma phase formation in Cr- and V-containing high-entropy alloys’, Mater. Res. Lett., 2013, 1, 207–212.
- M. H. Tsai, H. Yuan, G. Cheng, W. Xu, W. W. Jian, M. H. Chuang, C. C. Juan, A. C. Yeh, S. J. Lin and Y. Zhu: ‘Significant hardening due to the formation of a sigma phase matrix in a high entropy alloy’, Intermetallics, 2013, 33, 81–86.
- Y. Dong, L. Jiang, H. Jiang, Y. Lu, T. Wang and T. Li: ‘Effects of annealing treatment on microstructure and hardness of bulk AlCrFeNiMo0.2 eutectic high-entropy alloy’, Mater. Design, 2015, 82, 91–97.
- H. Jiang, L. Jiang, K. Han, Y. Lu, T. Wang, Z. Cao and T. Li: ‘Effects of tungsten on microstructure and mechanical properties of CrFeNiV0.5Wx and CrFeNi2V0.5Wx high-entropy alloys’, J. Mater. Eng. Perform., 2015, 24, 4594–4600.
- A. J. Zaddach, R. O. Scattergood and C. C. Koch: ‘Tensile properties of low-stacking fault energy high-entropy alloys’, Mater. Sci. Eng. A, 2015, 636, 373–378.
- P. Wang, H. Cai and X. Cheng: ‘Effect of Ni/Cr ratio on phase, microstructure and mechanical properties of NixCoCuFeCr2-x (x=1.0, 1.2, 1.5, 1.8 mol) high entropy alloys’, J. Alloys Compd., 2016, 662, 20–31.
- W. Hume-Rothery, R. E. Smallman and C. W. Haworth: ‘The structure of metals and alloys’, 5th edn; 1969, London, The Institute of Metals.
- T. B. Massalski: ‘ Structure of solid solutions’, in ‘Physical metallurgy’ (ed. R. W. Cahn), 4th edn, 135–204; 1996, Amsterdam, Elsevier Science.
- Y. J. Zhou, Y. Zhang, Y. L. Wang and G. L. Chen: ‘Solid solution alloys of AlCoCrFeNiTix with excellent room-temperature mechanical properties’, Appl. Phys. Lett., 2007, 90, 181904-1–181904-3.
- Y. J. Zhou, Y. Zhang, T. N. Kim and G. L. Chen: ‘Microstructure characterizations and strengthening mechanism of multi-principal component AlCoCrFeNiTi0.5 solid solution alloy with excellent mechanical properties’, Mater. Lett., 2008, 62, 2673–2676.
- C. Li, M. Zhao, J. C. Li and Q. Jiang: ‘B2 structure of high-entropy alloys with addition of Al’, J. Appl. Phys., 2008, 104, 113504-1–113504-6.
- B. S. Li, Y. P. Wang, M. X. Ren, C. Yang and H. Z. Fu: ‘Effects of Mn, Ti and V on the microstructure and properties of AlCrFeCoNiCu high entropy alloy’, Mater. Sci. Eng. A, 2008, 498, 482–486.
- C. Li, J. C. Li, M. Zhao and Q. Jiang: ‘Effect of alloying elements on microstructure and properties of multiprincipal elements high-entropy alloys’, J. Alloys Compd., 2009, 475, 752–757.
- Z. Liu, S. Guo, X. Liu, J. Ye, Y. Yang, X. L. Wang, L. Yang, K. An and C. T. Liu: ‘Micromechanical characterization of casting-induced inhomogeneity in an Al0.8CoCrCuFeNi high-entropy alloy’, Scr. Mater., 2011, 64, 868–871.
- S. Guo, C. Ng, J. Lu and C. T. Li: ‘Effect of valence electron concentration on stability of fcc or bcc phase in high entropy alloys’, J. Appl. Phys., 2011, 109, 103505-1–103505-5.
- L. Liu, J. B. Zhu, C. Zhang, J. C. Li and Q. Jiang: ‘Microstructure and the properties of FeCoCuNiSnx high entropy alloys’, Mater. Sci. Eng. A, 2012, 548, 64–68.
- S. Guo, C. Ng and C. T. Liu: ‘Anomalous solidification microstructures in co-free AlxCrCuFeNi2 high-entropy alloys’, J. Alloys Compd., 2013, 557, 77–81.
- L. Liu, J. B. Zhu, L. Li, J. C. Li and Q. Jiang: ‘Microstructure and tensile properties of FeMnNiCuCoSnx high entropy alloys’, Mater. Design, 2013, 44, 223–227.
- J. P. Couzinie, G. Dirras, L. Perriere, T. Chauveau, E. Leroy, Y. Champion and I. Guillot: ‘Microstructure of a near-equimolar refractory high-entropy alloy’, Mater. Lett., 2014, 126, 285–287.
- Q. C. Fan, B. S. Li and Y. Zhang: ‘Influence of Al and Cu elements on the microstructure and properties of (FeCrNiCo)AlxCuy high-entropy alloys’, J. Alloys Compd., 2014, 614, 203–210.
- L. Lilensten, J. P. Couzinié, L. Perrière, J. Bourgon, N. Emery and I. Guillot: ‘New structure in refractory high-entropy alloys’, Mater. Lett., 2014, 132, 123–125.
- L. Asensio Dominguez, R. Goodall and I. Todd: ‘Prediction and validation of quaternary high entropy alloys using statistical approaches’, Mater. Sci. Technol., 2015, 31, 1201–1206.
- T. Yang, S. Xia, S. Liu, C. Wang, S. Liu, Y. Zhang, J. Xue, S. Yan and Y. Wang: ‘Effects of AL addition on microstructure and mechanical properties of AlxCoCrFeNi high-entropy alloy’, Mater. Sci. Eng. A, 2015, 648, 15–22.
- Y. Yu, J. Wang, J. Li, H. Kou and W. Liu: ‘Characterization of BCC phases in AlCoCrFeNiTix high entropy alloys’, Mater. Lett., 2015, 138, 78–80.
- P. H. Wu, N. Liu, W. Yang, Z. X. Zhu, Y. P. Lu and X. J. Wang: ‘Microstructure and solidification behavior of multicomponent CoCrCuxFeMoNi high-entropy alloys’, Mater. Sci. Eng. A, 2015, 642, 142–149.
- M. C. Gao, C. S. Carney, O. N. Dogan, P. D. Jablonski, J. A. Hawk and D. E. Alman: ‘Design of refractory high-entropy alloys’, JOM, 2015, 67, 2653–2669.
- B. Zhang, M. C. Gao, Y. Zhang and S. M. Guo: ‘Senary refractory high-entropy alloy CrxMoNbTaVW’, CALPHAD, 2015, 51, 193–201.
- C. Li, Y. Xue, M. Hua, T. Cao, L. Ma and L. Wang: ‘Microstructure and mechanical properties of AlxSi0.2CrFeCoNiCu1-x high-entropy alloys’, Mater. Design, 2016, 90, 601–609.
- C. Zhang, F. Zhang, S. Chen and W. Cao: ‘Computational thermodynamics aided high-entropy alloy design’, JOM, 2012, 64, 839–845.
- F. Zhang, C. Zhang, S. L. Chen, J. Zhu, W. S. Cao and U. R. Kattner: ‘An understanding of high entropy alloys from phase diagram calculations’, CALPHAD, 2014, 45, 1–10.
- C. M. Lin and H. L. Tsai: ‘Effect of annealing treatment on microstructure and properties of high-entropy FeCoNiCrCu0.5 alloy’, Mater. Chem. Phys., 2011, 128, 50–56.
- Y. X. Zhuang, H. D. Zue, Z. Y. Chen, Z. Y. Hu and J. C. He: ‘Effect of annealing treatment on microstructures and mechanical properties of FeCoNiCuAl high entropy alloys’, Mater. Sci. Eng. A, 2013, 572, 30–35.
- H. Zhang, Y. Pan, Y. He and H. Jiao: ‘Microstructure and properties of 6fenicosicralti high-entropy alloy coating prepared by laser cladding’, Appl. Surf. Sci., 2011, 257, 2259–2263.
- H. Zhang, Y. Pan and Y. Z. He: ‘Synthesis and characterization of FeCoNiCrCu high-entropy alloy coating by laser cladding’, Mater. Design, 2011, 32, 1910–1915.
- K. Zhang and Z. Fu: ‘Effects of annealing treatment on phase composition and microstructure of CoCrFeNiTiAlx high-entropy alloys’, Intermetallics, 2012, 22, 24–32.
- A. K. Singh, N. Kumar, A. Dwivedi and A. Subramaniam: ‘A geometrical parameter for the formation of disordered solid solutions in multi-component alloys’, Intermetallics, 2014, 53, 112–119.
- Z. Tang, T. Yuan, C. W. Tsai, J. W. Yeh, C. D. Lundin and P. K. Liaw: ‘Fatigue behavior of a wrought Al0.5CoCrCuFeNi two-phase high-entropy alloy’, Acta Mater., 2015, 99, 247–258.
- W. Rosenhain: ‘The hardness of solid soutions’, Proc. R. Soc. London, 1921, 99, 196–202.
- F. R. N. Nabarro: ‘The mechanical properties of solid solutions’, Proc. Phys. Soc., 1946, 58, 669–676.
- J. Friedel: ‘Dislocations’; 1964, New York, Pergamon Press.
- R. Labusch: ‘A statistical theory of solid solution hardening’, Physica Status Solidi, 1970, 41, 659–669.
- P. Haasen: ‘Mechanical properties of solid solutions’, in ‘Physical metallurgy’ (ed. R. W. Cahn), 4th edn, 2009–2073; 1996, Amsterdam, Elsevier Science.
- J. W. Yeh, S. Y. Chang, Y. D. Hong, S. K. Chen and S. J. Lin: ‘Anomalous decrease in X-ray diffraction intensities of Cu–Ni–Al–Co–Cr–Fe–Si alloy systems with multi-principal elements’, Mater. Chem. Phys., 2007, 103, 41–46.
- S. Y. Chang and D. S. Chen: ‘10-nm-Thick quinary (AlCrTaTiZr)N film as effective diffusion barrier for Cu interconnects at 900°C’, Appl. Phys. Lett., 2009, 94, 231909-1–231909-3.
- S. Y. Chang, Y. C. Huang, C. E. Li, H. F. Hsu, J. W. Yeh and S. J. Lin: ‘Improved diffusion-resistant ability of multicomponent nitrides: from unitary TiN to senary high-entropy (TiTaCrZrAlRu)N’, JOM, 2013, 65, 1790–1796.
- W. Guo, W. Dmowski, J. Y. Noh, P. Rack, P. K. Liaw and T. Egami: ‘Local atomic structure of a high-entropy alloy: an x-ray and neutron scattering study’, Metall. Mater. Trans. A, 2013, 44, 1994–1997.
- R. S. Mishra, N. Kumar and M. Komarasamy: ‘Lattice strain framework for plastic deformation in complex concentrated alloys including high entropy alloys’, Mater. Sci. Technol., 2015, 31, 1259–1263.
- I. Toda-Caraballo, J. S. Wrobel, S. L. Dudarev, D. Nguyen-Manh and P. E. J. Rivera-Diaz del Castillo: ‘Interatomic spacing distribution in multicomponent alloys’, Acta Mater., 2015, 97, 156–169.
- M. Komarasamy, N. Kumar, R. S. Mishra and P. K. Liaw: ‘Anomalies in the deformation mechanism and kinetics of coarse-grained high entropy alloy’, Mater. Sci. Eng. A, 2016, 654, 256–263.
- F. J. Wang, Y. Zhang and G. L. Chen: ‘Atomic packing efficiency and phase transition in a high entropy alloy’, J. Alloys Compd., 2009, 478, 321–324.
- K. Huang and H. H. Wills: ‘X-ray reflexions from dilute solutions’, Proc. R. Soc. London, 1947, 190, 102–117.
- B. E. Warren, B. L. Averbach and B. W. Roberts: ‘Atomic size effect in the x-ray scattering by alloys’, J. Appl. Phys., 1951, 22, 1493–1496.
- F. H. Herbstein, B. S. Borie and B. L. Averbach: ‘Local atomic displacements in solid solutions’, Acta Crystallogr., 1956, 9, 466–471.
- B. Borie: ‘X-ray diffraction effects of atomic size in alloys’, Acta Crystallogr., 1957, 10, 89–96.
- B. Borie and C. J. Sparks: ‘The interpretation of intensity distributions from disordered binary alloys’, Acta Crystallogr., 1971, 27, 198–201.
- B. D. Butler, R. L. Withers and T. R. Welberry: ‘Diffuse absences due to the atomic size effect’, Acta Crystallogr., 1992, 48, 737–746.
- G. E. Ice and C. J. Sparks: ‘Modern resonant x-ray studies of alloys: local order and displacements’, Annu. Rev. Mater. Sci., 1999, 29, 25–52.
- Y. Zou, S. Maiti, W. Steurer and R. Spolenak: ‘Size-dependent plasticity in an Nb25Mo25Ta25W25 refractory high-entropy alloy’, Acta Mater., 2014, 65, 85–97.
- F. H. Herbstein and B. L. Averbach: ‘The structure of lithium-magnesium solid solutions - I: measurements on the Bragg reflections’, Acta Metall., 1956, 4, 407–413.
- S. Froyen and C. Herring: ‘Distribution of interatomic spacings in random alloys’, J. Appl. Phys., 1981, 52, 7165–7173.
- G. Renaud, N. Motta, L. Lancon and M. Belakhovsky: ‘Topological short-range disorder in Au1-xNix solid solutions: an extended X-ray-absorption fine-structure spectroscopy and computer-simulation study’, Phys. Rev. B, 1988, 38, 5944–5964.
- U. Scheuer and B. Lengeller: ‘Lattice distortion of solute atoms in metals studied by X-ray-absorption fine structure’, Phys. Rev. B, 1991, 44, 9883–9894.
- N. Papanikolaou, R. Zeller, P. H. Dederichs and N. Stefanou: ‘Lattice distortion in cu-based dilute alloys: a first-principles study by the KKR green-function method’, Phys. Rev. B, 1997, 55, 4157–4167.
- T. Uesugi and K. Higashi: ‘First-principles studies on lattice constants and local lattice distortions in solid solution aluminum alloys’, Comput. Mater. Sci., 2013, 67, 1–10.
- W. Hume-Rothery, G. W. Mabbott and K. M. Channel Evans: ‘The freezing points, melting points, and solid solubility limits of the alloys of silver and copper with the elements of the B sub-groups’, Philos. Trans. R. Soc. London, 1934, 233, 1–97.
- Y. Zhang, Y. J. Zhou, J. P. Lin, G. L. Chen and P. K. Liaw: ‘Solid-solution phase formation rules for multi-component alloys’, Adv. Eng. Mater., 2008, 10, 534–538.
- S. Guo and C. T. Liu: ‘Phase stability in high entropy alloys: formation of solid-solution phase or amorphous phase’, Prog. Natural Sci.: Mater. Int., 2011, 21, 433–446.
- S. Guo, Q. Hu, C. Ng and C. T. Liu: ‘More than entropy in high-entropy alloys: forming solid solutions or amorphous phase’, Intermetallics, 2013, 41, 96–103.
- S. Guo and C. T. Liu: ‘Phase selection rules for complex multi-component alloys with equiatomic or close-to-equiatomic compositions’, Chin. J. Nat., 2013, 35, 85–96.
- S. Guo, C. Ng, Z. Wang and C. T. Liu: ‘Solid solutioning in equiatomic alloys: limit set by topological instability’, J. Alloys Compd., 2014, 583, 410–413.
- S. Guo: ‘Phase selection rules for cast high entropy alloys: an overview’, Mater. Sci. Technol., 2015, 31, 1223–1230.
- K. Y. Tsai, M. H. Tsai and J. W. Yeh: ‘Sluggish diffusion in CoCrFeMnNi high-entropy alloys’, Acta Mater., 2013, 61, 4887–4897.
- S. G. Ma, P. K. Liaw, M. C. Gao, J. W. Qiao, Z. H. Wang and Y. Zhang: ‘Damping behavior of AlxCoCrFeNi high-entropy alloys by a dynamic mechanical analyzer’, J. Alloys Compd., 2014, 604, 331–339.
- K. G. Pradeep, C. C. Tasan, M. J. Yao, Y. Deng, H. Springer and D. Raabe: ‘Non-equiatomic high entropy alloys: approach towards rapid alloy screening and property-oriented design’, Mater. Sci. Eng. A, 2015, 648, 183–192.
- S. G. Ma, J. W. Qiao, Z. H. Wang, H. J. Yang and Y. Zhang: ‘Microstructural features and tensile behaviors of the Al0.5CrCuFeNi2 high-entropy alloys by cold rolling and subsequent annealing’, Mater. Design, 2015, 88, 1057–1062.
- D. Ma, M. Yao, K. G. Pradeep, C. C. Tasan, H. Springer and D. Raabe: ‘Phase stability of non-equiatomic CoCrFeMnNi high entropy alloys’, Acta Mater., 2015, 98, 288–296.
- T. Uddin, K. Biswas and N. P. Gurao: ‘Deciphering micro-mechanisms of plastic deformation in a novel single phase Fcc-based MnFeCoNiCu high entropy alloy using crystallographic texture’, Mater. Sci. Eng. A, 2016, 657, 224–233.
- A. M. Brown and M. F. Ashby: ‘Correlations for diffusion constants’, Acta Metall., 1980, 28, 1085–1101.
- R. W. Cahn: ‘ Recovery and recrystallisation’, in ‘Physical metallurgy’ (ed. R. W. Cahn), 4th edn, 2399–2500; 1996, Amsterdam, Elsevier Science.
- S. Ranganathan: ‘Alloyed pleasures: multimetallic cocktails’, Curr. Sci., 2003, 85, 1404–1406.
- L. Vegard: ‘Die Konstitution der Mischkristalle und die Raumfuellung der Atome’, Z. Physik, 1921, 5, 17–26.
- T. K. Chen, T. T. Shun, J. W. Yeh and M. S. Wong: ‘Nanostructured nitride films of multi-element high-entropy alloys by reactive dc sputtering’, Surf. Coatings Technol., 2004, 188–189, 193–200.
- P. K. Huang, J. W. Yeh, T. T. Shun and S. K. Chen: ‘Multi-principal-element alloys with improved oxidation and wear resistance for thermal spray coating’, Adv. Eng. Mater., 2004, 6, 74–78.
- W. Y. Tang, M. H. Chuang, H. Y. Chen and J. W. Yeh: ‘Microstructure and mechanical performance of new Al0.5CrFe1.5MnNi0.5 high-entropy alloys improved by plasma nitriding’, Surf. Coat. Technol., 2010, 204, 3118–3124.
- L. M. Wang, C. C. Chen, J. W. Yeh and S. T. Ke: ‘The microstructure and strengthening mechanism of thermal spray coating NixCo0.6Fe0.2CrySizAlTi0.2 high-entropy alloys’, Mater. Chem. Phys., 2011, 126, 880–885.
- H. Zhang, Y. Z. He, Y. Pan and L. Z. Pei: ‘Phase selection, microstructure and properties of laser rapidly solidified FeCoNiCrAl2Si coating’, Intermetallics, 2011, 19, 1130–1135.
- H. Zhang, Y. Pan and Y. Z. He: ‘Grain refinement and boundary misorientation transition by annealing in the laser rapid solidified 6FeNiCoCrAlTiSi multicomponent ferrous alloy coating’, Surf. Coat. Technol., 2011, 205, 4068–4072.
- X. W. Qiu and C. G. Liu: ‘Microstructure and properties of Al2CrFeCoCuTiNix high-entropy alloys prepared by laser cladding’, J. Alloys Compd., 2013, 553, 216–220.
- L. Liu, J. B. Zhu, C. Hou, J. C. Li and Q. Jiang: ‘Dense and smooth amorphous films of multicomponent FeCoNiCuVZrAl high-entropy alloy deposited by direct current magnetron sputtering’, Mater. Design, 2013, 46, 675–679.
- X. W. Qiu, Y. P. Zhang and C. G. Liu: ‘Effect of Ti content on structure and properties of Al2CrFeNiCoCuTix high-entropy alloy coatings’, J. Alloys Compd., 2014, 585, 282–286.
- X. T. Liu, W. B. Lei, J. Li, Y. Ma, W. M. Wang, B. H. Zhang, C. S. Liu and J. Z. Cui: ‘Laser cladding of high-entropy alloy on H13 steel’, Rare Metals, 2014, 33, 727–730.
- H. Zhang, Y. Z. He, Y. Pan and S. Guo: ‘Thermally stable laser cladded CoCrCuFeNi high-entropy alloy coating with low stacking fault energy’, J. Alloys Compd., 2014, 600, 210–214.
- T. M. Yue, H. Xie, X. Lin, H. O. Yang and G. H. Meng: ‘Solidification behaviour in laser cladding of AlCoCrCuFeNi high-entropy alloy on magnesium substrates’, J. Alloys Compd., 2014, 587, 588–593.
- Y. Yu, J. Wang, J. Li, H. Kou, H. Duan, J. Li and W. Liu: ‘Tribological behavior of AlCoCrCuFeNi and AlCoCrFeNiTi0.5 high entropy alloys under hydrogen peroxide solution against different counterparts’, Tribol. Int., 2015, 92, 203–210.
- H. Zhang, Y. Pan, Y. Z. He, J. L. Wu, T. M. Yue and S. Guo: ‘Application prospects and microstructural features in laser-induced rapidly solidified high-entropy alloys’, JOM, 2014, 65, 2057–2066.
- X. Q. Gao, K. Zhao, H. B. Ke, D. W. Ding, W. H. Wang and H. Y. Bai: ‘High mixing entropy bulk metallic glasses’, J. Non-Cryst. Solids, 2011, 357, 3557–3560.
- A. Takeuchi, N. Chen, T. Wada, Y. Yokoyama, H. Kato, A. Inoue and J. W. Yeh: ‘Pd20Pt20Cu20Ni20P20 high-entropy alloy as a bulk metallic glass in the centimeter’, Intermetallics, 2011, 19, 1546–1554.
- A. Takeuchi, N. Chen, T. Wada, W. Zhang, Y. Yokoyama, A. Inoue and J. W. Yeh: ‘Alloy design for high-entropy bulk glassy alloys’, Procedia Eng., 2012, 36, 226–234.
- H. Y. Ding and K. F. Yao: ‘High entropy Ti20Zr20Cu20Ni20Be20 bulk metallic glass’, J. Non-Cryst. Solids, 2013, 364, 9–12.
- Y. F. Kao, S. W. Chen, J. H. Sheu, J. T. Lin, W. E. Lin, J. W. Yeh, S. J. Lin, T. Z. Liou and C. W. Wang: ‘Hydrogen storage properties of multi-principal-component CoFeMnTixVyZrz alloys’, Int. J. Hydrogen Energy, 2010, 35, 9046–9059.
- M. S. Lucas, L. Mauger, J. A. Muñoz, Y. Xiao, A. O. Sheets, S. L. Semiatin, J. Horwath and Z. Turgut: ‘Magnetic and vibrational properties of high-entropy alloys’, J. Appl. Phys., 2011, 109, 07E307-1–07E307-3.
- Y. F. Kao, S. K. Chen, T. J. Chen, P. C. Chu, J. W. Yeh and S. J. Lin: ‘Electrical, magnetic and hall properties of AlxCoCrFeNi high-entropy alloys’, J. Alloys Compd., 2011, 509, 1607–1614.
- M. S. Lucas, D. Belyea, C. Bauer, N. Bryant, E. Michel, Z. Turgut, S. O. Leontsev, J. Horwath, S. L. Semiatin, M. E. McHenry and C. W. Miller: ‘Thermomagnetic analysis of FeCoCrxNi alloys: magnetic entropy of high-entropy alloys’, J. Appl. Phys., 2013, 113, 17A923.
- Y. Zhang, T. T. Zuo, Y. Q. Cheng and P. K. Liaw: ‘High-entropy alloys with high saturation magnetization, electrical resistivity, and malleability’, Sci. Rep., 2013, 3, 1455.
- F. Körmann, D. Ma, D. D. Belyan, M. S. Lucas, C. W. Miller, B. Grabowski and M. H. F. Sluiter: ‘“Treasure maps” for magnetic high-entropy-alloys from theory and experiment’, Appl. Phys. Lett., 2015, 107, 142404-1–142404-5.
- S. Huang, Á. Vida, D. Molnár, K. Kádas, L. Károly, E. Holmström and L. Vitos: ‘Phase stability and magnetic behavior of FeCrCoNiGe high-entropy alloy’, Appl. Phys. Lett., 2015, 107, 251906-1–251906-4.
- S. Shafeie, S. Guo, Q. Hu, H. Fahlquist, P. Erhart and A. Palmqvist: ‘High-entropy alloys as high-temperature thermoelectric materials’, J. Appl. Phys., 2015, 118, 184905-1–184905-10.
- M. H. Chuang, M. H. Tsai, C. W. Tsai, N. H. Yang, S. Yi. Chang, J. W. Yeh, S. K. Chen and S. J. Lin: ‘Intrinsic surface hardening and precipitation kinetics of Al0.3CrFe1.5MnNi0.5 multi-component alloy’, J. Alloys Compd., 2013, 551, 12–18.
- C. J. Tong, M. R. Chen, S. K. Chen, J. W. Yeh, T. T. Shun, S. J. Lin and S. Y. Chang: ‘Mechanical performance of the AlxCoCrCuFeNi high-entropy alloy system with multiprincipal elements’, Metall. Mater. Trans. A, 2005, 36A, 1263–1271.
- H. K. D. H. Bhadeshia: ‘Editorial: high entropy alloys’, Mater. Sci. Technol., 2015, 31, 1139–1141.
- D. Raabe, C. C. Tasan, H. Springer and M. Bausch: ‘From high-entropy alloys to high-entropy steels’, Steel Res., 2015, 86, 1127–1138.
- Z. Tang, M. C. Gao, H. Diao, T. Yang, J. P. Liu, T. Zuo, Y. Zhang, Z. Lu, Y. Cheng, Y. Zhang, K. A. Dahmen, P. K. Liaw and T. Egami: ‘Aluminum alloying effects on lattice types, microstructures, and mechanical behavior of high-entropy alloys systems’, JOM, 2013, 65, 1848–1858.
- K. Jasiewicz, J. Cieslak, S. Kaprzyk and J. Tobola: ‘Relative crystal stability of AlxFeNiCrCo high entropy alloys from XRD analysis and formation energy calculation’, J.Alloys Compd., 2015, 648, 307–312.
- W. Chen, Z. Fu, S. Fang, Y. Wang, H. Xiao and D. Zhu: ‘Processing, microstructure and properties of Al0.6CoNiFeTi0.4 high entropy alloy with nanoscale twins’, Mater. Sci. Eng. A, 2013, 565, 439–444.
- X. Yang and Y. Zhang: ‘Prediction of high-entropy stabilized solid-solution in multi-component alloys’, Mater. Chem. Phys., 2012, 132, 233–238.
- R. Raghavan, K. C. Hari Kumar and B. S. Murty: ‘Analysis of phase formation in multi-component alloys’, J. Alloys Compd., 2012, 544, 152–158.
- J. Pi and Y. Pan: ‘Thermodynamic analysis for microstructure of high-entropy alloys’, Rare Metal Mater. Eng., 2013, 42, 232–237.
- M. X. Ren, B. S. Li and H. Z. Fu: ‘Formation condition of solid solution type high-entropy alloy’, Trans. Nonferrous Metals Soc. Chin., 2013, 23, 991–995.
- A. Takeuchi, K. Amiya, T. Wada, K. Yubuta, W. Zhang and A. Makino: ‘Entropies in alloy design for high-entropy and bulk glassy alloys’, Entropy, 2013, 15, 3810–3821.
- Z. S. Nong, J. C. Zhu, Y. Cao, X. W. Yang, Z. H. Lai and Y. Liu: ‘Stability and structure prediction of cubic phase in as cast high entropy alloys’, Mater. Sci. Technol., 2014, 30, 363–369.
- Z. Wang, S. Guo and C. T. Liu: ‘Phase selection in high-entropy alloys: from nonequilibrium to equilibrium’, JOM, 2014, 66, 1966–1972.
- M. G. Poletti and L. Battezzati: ‘Electronic and thermodynamic criteria for the occurrence of high entropy alloys in metallic systems’, Acta Mater., 2014, 75, 297–306.
- F. Tian, L. K. Varga, N. Chen, J. Shen and L. Vitos: ‘Empirical design of single phase high-entropy alloys with high hardness’, Intermetallics, 2015, 58, 1–6.
- M. G. Poletti, G. Fiore, B. A. Szost and L. Battezzati: ‘Search for high entropy alloys in the X-NbTaTiZr systems (X = Al, Cr, V, Sn)’, J. Alloys Compd., 2015, 620, 283–288.
- S. Sheikh, U. Klement and S. Guo: ‘Predicting the solid solubility limit in high-entropy alloys using the molecular orbital approach’, J. Appl. Phys., 2015, 118, 194902-1–194902-8.
- Y. F. Ye, C. T. Liu and Y. Yang: ‘A geometric model for intrinsic residual strain and phase stability in high entropy alloys’, Acta Mater., 2015, 94, 152–161.
- Y. F. Ye, Q. Wang, J. Lu, C. T. Liu and Y. Yang: ‘Design of high entropy alloys: a single-parameter thermodynamic rule’, Scr. Mater., 2015, 104, 53–55.
- Y. F. Ye, Q. Wang, J. Lu, C. T. Liu and Y. Yang: ‘The generalized thermodynamic rule for phase selection in multicomponent alloys’, Intermetallics, 2015, 59, 75–80.
- Z. Wang, Y. Huang, Y. Yang, J. Wang and C. T. Liu: ‘Atomic-size effect and solid solubility of multicomponent alloys’, Scr. Mater., 2015, 94, 28–31.
- O. N. Senkov and D. B. Miracle: ‘A new thermodynamic parameter to predict formation of solid solution or intermetallic phases in high entropy alloys’, J. Alloys Compd., 2016, 658, 603–607.
- F. R. deBoer, R. Boom, W. C. M. Mattens, A. R. Miedema and A. K. Niessen: ‘Cohesion in metals: transition metal alloys’; 1988, Amsterdam, North-Holland.
- A. Takeuchi and A. Inoue: ‘Classification of bulk metallic glasses by atomic size difference, heat of mixing and period of constituent elements and its application to characterization of the main alloying element’, Mater. Trans., 2005, 46, 2817–2829.
- S. Fang, X. Xiao, L. Xia, W. Li and Y. Dong: ‘Relationship between the widths of supercooled liquid regions and bond parameters of Mg-based bulk metallic glasses’, J. Non-Cryst. Solids, 2003, 321, 120–125.
- Z. Wang, W. Qiu, Y. Yang and C. T. Liu: ‘Atomic-size and lattice-distortion effects in newly developed high-entropy alloys with multiple principal elements’, Intermetallics, 2015, 64, 63–69.
- M. H. Tsai, K. C. Chang, J. H. Li, R. C. Tsai and A. H. Cheng: ‘A second criterion for sigma phase formation in high-entropy alloys’, Mater. Res. Lett., 2015, doi:10.1080/21663831.2015.1121168.
- Y. Lu, Y. Dong, L. Jiang, T. Wang, T. Li and Y. Zhang: ‘A criterion for topological close-packed phase formation in high entropy alloys’, Entropy, 2015, 17, 2355–2366.
- Y. Dong, Y. Lu, L. Jiang, T. Wang and T. Li: ‘Effects of electro-negativity on the stability of topologically close-packed phase in high entropy alloys’, Intermetallics, 2014, 52, 105–109.
- D. J. M. King, S. C. Middleburgh, A. G. McGregor and M. B. Cortie: ‘Predicting the formation and stability of single phase high-entropy alloys’, Acta Mater., 2016, 104, 172–179.
- M. F. del Grosso, G. Bozzolo and H. O. Mosca: ‘Determination of the transition to the high entropy regime for alloys of refractory elements’, J. Alloys Compd., 2012, 534, 25–31.
- M. F. del Grosso, G. Bozzolo and H. O. Mosca: ‘Modeling of high entropy alloys of refractory elements’, Phys. B, 2012, 407, 3285–3287.
- W. P. Huhn and M. Widom: ‘Prediction of A2 to B2 phase transition in the high-entropy alloy Mo-Nb-Ta-W’, JOM, 2013, 65, 1772–1779.
- F. Tian, L. K. Varga, N. Chen, L. Delczeg and L. Vitos: ‘Ab initio investigation of high-entropy alloys of 3d elements’, Phys. Rev. B, 2013, 87, 075144-1–075144-8.
- M. Widom, W. P. Huhn, S. Maiti and W. Steurer: ‘Hybrid monte carlo/molecular dynamics simulation of a refractory metal high entropy alloy’, Metall. Mater. Trans. A, 2014, 45, 196–200.
- F. Tian, L. K. Varga, N. Chen, J. Shen and L. Vitos: ‘Ab initio design of elastically isotropic TiZrNbMoVx high-entropy alloys’, J. Alloys Compd., 2014, 599, 19–25.
- S. C. Middleburgh, D. M. King, G. R. Lumpkin, M. Cortie and L. Edwards: ‘Segregation and migration of species in the CrCoFeNi high entropy alloy’, J. Alloys Compd., 2014, 599, 179–182.
- D. M. King, S. C. Middleburgh, L. Edwards, G. R. Lumpkin and M. Cortie: ‘Predicting the crystal structure and phase transitions in high-entropy alloys’, JOM, 2015, 67, 2375–2380.
- M. C. Troparevsky, J. R. Morris, M. Daene, Y. Wang, A. R. Lupini and G. M. Stocks: ‘Beyond atomic sizes and Hume-Rothery rules: understanding and predicting high-entropy alloys’, JOM, 2015, 67, 2350–2363.
- N. Saunders and A. P. Miodownik: ‘CALPHAD: calculation of phase diagrams – a comprehensive guide’, 1st edn; 1998, New York, Pergamon.
- A. Durga, K. C. Hari Kumar and B. S. Murty: ‘Phase formation in equiatomic high entropy alloys: CALPHAD approach and experimental studies’, Trans. Indian Inst. Metall., 2012, 65, 375–380.
- O. N. Senkov, F. Zhang and J. D. Miller: ‘Phase composition of a CrMo0.5NbTa0.5TiZr high entropy alloy: comparison of experimental and simulated data’, Entropy, 2013, 15, 3796–3809.
- Z. Cai, G. Jin, X. Cui, Y. Li, Y. Fan and J. Song: ‘Experimental and simulated data about microstructure and phase composition of a NiCrCoTiV high-entropy alloy prepared by vacuum hot-pressing sintering’, Vacuum, 2016, 124, 5–10.
- A. Ludwig, R. Zarnetta, S. Hamann, A. Savan and S. Thienhaus: ‘Development of multimunctional thin films using high-throughput experimentation methods’, Int. J. Mater. Res., 2008, 99, 1144–1149.
- R. Zarnetta, P. J. S. Buenconsejo, A. Savan, S. Thienhaus and A. Ludwig: ‘High-throughput study of martensitic transformations in the complete Ti–Ni–Cu system’, Intermetallics, 2012, 26, 98–109.
- O. N. Senkov, J. M. Scott, S. V. Senkova, F. Melsenkothen, D. B. Miracle and C. F. Woodward: ‘Microstructure and elevated temperature properties of a refractory TaNbHfZrTi alloy’, J. Mater. Sci., 2012, 47, 4062–4074.
- Y. D. Wu, Y. H. Cai, T. Wang, J. J. Si, J. Zhu, Y. D. Wang and X. D. Hui: ‘A refractory Hf25Nb25Ti25Zr25 high-entropy alloy with excellent structural stability and tensile properties’, Mater. Lett., 2014, 130, 277–280.
- E. Fazakas, V. Zadorozhnyy, L. K. Varga, A. Inoue, D. V. Louzguine-Luzgin, F. Tian and L. Vitos: ‘Experimental and theoretical study of Ti20Zr20Hf20Nb20X20 (X = V or Cr) refractory high-entropy alloys’, Int. J. Refract. Metals Hard Mater., 2014, 47, 131–138.
- B. Gorr, M. Azim, H. J. Christ, H. Chenand, D. V. Szabo, A. Kauffmann and M. Heilmaier: ‘Microstructure evolution in a new refractory high-entropy alloy W-Mo-Cr-Ti-Al’, Metall. Mater. Trans. A, 2016, 47, 961–970.
- Z. Han, X. Liu, S. Zhao, Y. Shao, J. Li and K. Yao: ‘Microstructure, phase stability and mechanical properties of Nb-Ni-Ti-Co-Zr and Nb-Ni-Ti-Co-Zr-Hf high entropy alloys’, Prog. Nat. Sci.: Mater. Int., 2015, 25, 365–369.
- N. D. Stepanov, D. G. Shaysultanov, G. A. Salishchev and M. A. Tikhonovsky: ‘Structure and mechanical properties of a light-weight AlNbTiV high entropy alloy’, Mater. Lett., 2015, 142, 153–155.
- S. Maiti and W. Steurer: ‘Structural-disorder and its effect on mechanical properties in single-phase TaNbHfZr high-entropy alloy’, Acta Mater., 2016, 106, 87–97.
- M. Heidelmann, M. Feuerbacher, D. Ma and B. Grabowski: ‘Structural anomaly in the high-entropy alloy ZrNbTiTaHf’, Intermetallics, 2016, 68, 11–15.
- A. Takeuchi, K. Amiya, T. Wada and K. Yubuta: ‘Dual HCP structures formed in senary ScYLaTiZrHf multi-principal element alloy’, Intermetallics, 2016, 69, 103–109.
- L. Rogal, F. Czerwinski, P. T. Jochym and L. Litynska-Dobrzynska: ‘Microstructure and mechanical properties of the novel Hf25Sc25Ti25Zr25 equiatomic alloy with hexagonal solid solutions’, Mater. Design, 2016, 92, 8–17.
- N. N. Guo, L. Wang, L. S. Luo, X. Z. Li, R. R. Chen, Y. Q. Su, J. J. Guo and H. Z. Fu: ‘Hot deformation characteristics and dynamic recrystallization of the MoNbHfZrTi refractory high-entropy alloy’, Mater. Sci. Eng. A, 2016, 651, 698–707.
- O. N. Senkov, J. M. Scott, S. V. Senkova, D. B. Miracle and C. F. Woodward: ‘Microstructure and room temperature properties of a high-entropy TaNbHfZrTi alloy’, J. Alloys Compd., 2011, 509, 6043–6048.
- W. Woo, E. W. Huang, J. W. Yeh, H. Choo, C. Lee and S. Y. Tu: ‘In-situ neutron diffraction studies on high-temperaturee deformation behavior in a CoCrFeMnNi high entropy alloy’, Intermetallics, 2015, 62, 1–6.
- G. W. Ardley and A. H. Cottrell: ‘Yield points in brass crystals’, Proc. R. Soc., 1953, 219, 328–341.
- P. Feltham and C. J. Copley: ‘Yielding and work-hardening in alpha-brass’, Acta Metall., 1960, 8, 542–550.
- A. A. Hendrickson and M. E. Fine: ‘Solid solution strengthening of Ag by Al’, Trans. TMS AIME, 1961, 221, 967–974.
- Ch. Schwink and H. Traub: ‘The active slip volume and the temperature-dependent processes in stage I of single crystals of Cu alloys’, Phys. Status Solidi, 1968, 30, 387–397.
- H. Traub, H. Neuhäuser and Ch. Schwink: ‘Investigation of the yield region of concentrated Cu-Ge and Cu-Zn single crystals – I. Critical resolved shear stress, slip line formation and the true strain rate’, Acta Metall., 1977, 25, 437–446.
- M. Z. Butt and I. M. Ghauri: ‘Effect of short-range order on the temperature dependence of plastic flow in α-brasses’, Phys. Status Solidi, 1988, 107, 187–195.
- S. Huang, W. Li, S. Lu, F. Tian, J. Shen, E. Holmström and L. Vitos: ‘Temperature dependent stacking fault energy of FeCrCoNiMn high entropy alloy’, Scr. Mater., 2015, 108, 44–47.
- R. Peierls: ‘The size of a dislocation’, Proc. R. Soc., 1940, 52, 34–37.
- F. R. N. Nabarro: ‘Dislocations in a simple cubic lattice’, Proc. R. Soc., 1947, 59, 256–272.
- H. D. Dietze: ‘Die Temperaturabhaengigkeit der Versetzungsstruktur’, Zeitschrift fuer Physik, 1952, 132, (1), 107–110.
- I. Toda-Caraballo and P. E. J. Rivera-Diaz del Castillo: ‘Modelling solid solution hardening in high-entropy alloys’, Acta Mater., 2015, 85, 14–23.
- R. Labusch, G. Grange, J. Ahearn and P. Haasen: ‘Rate processes in plastic deformation of materials’; 1975, Ohio, ASM.
- H. A. Moreen, R. Taggart and D. H. Paulonis: ‘A model for the prediction of lattice parameters of solid solutions’, Metall. Trans., 1971, 2, 265–268.
- J. C. Fisher: ‘On the strength of solid solution alloys’, Acta Metall., 1954, 2, 9–10.
- P. A. Flinn: ‘Solute hardening of close-packed solid solutions’, Acta Metall., 1958, 6, 631–635.
- J. Antonaglia, X. Xie, Z. Tang, C. W. Tsai, J. W. Qiao, Y. Zhang, M. O. Laktionova, E. D. Tabachnikova, J. W. Yeh, O. N. Senkov, M. C. Gao, J. T. Uhl, P. K. Liaw and K. A. Dahmen: ‘Temperature effects on deformation and serration behavior of high-entropy alloys (HEAs)’, JOM, 2014, 66, 2002–2008.
- R. Carroll, C. Lee, C. W. Tsai, J. W. Yeh, J. Antonaglia, B. A. W. Brinkman, M. LeBlanc, X. Xie, S. Chen, P. K. Liaw and K. A. Dahmen: ‘Experiments and model for serration statistics in low-entropy, medium-entropy, and high-entropy alloys’, Sci. Rep., 2015, 5, (16997), 0–0.
- A. Portevin and F. Le Chatilier: ‘Sur un Phénomène Observé lors de l'Essai de Traction d'Alliages en Cours de Transformation’, Comptes Rendus de l'Académie des Sciences Paris, 1923, 176, 507–510.
- A. H. Cottrell: ‘A note on the Portevin-Le Chatilier effect’, Philos. Mag., 1953, 44, 829–832.