Abstract
Intentional weld defect or flaw specimens can be required for training purposes, developing new non-destructive testing techniques, qualifying non-destructive testing procedures, and obtaining mechanical property data in support of safety cases. The single most important criterion in producing defects or imperfections is that they must accurately simulate flaws which can occur in welded components and structures. For this reason, in certain applications, saw cuts or machined slots which are more easily detected may not be considered acceptable as planar imperfections/defects for the purpose of NDT training or validation. Therefore, TWI has developed techniques for producing realistic imperfections/defects and, in the case of cracks, the desired morphology, including roughness, angles of tilt and skew to the surface. This paper describes the techniques used to obtain the above-mentioned defects and, for the most commonly required defect types, the qualification procedure used by TWI. This consists of inspecting by testing of surface crack detection, ultrasonic or radiographic inspection and/or sectioning to demonstrate that the dimensional tolerance of the simulated imperfections (i.e. actual size of the imperfection vs required size) can be generally guaranteed within ± 0.5 mm in through-wall extent and ± 1 mm in length.
Acknowledgements
The authors wish to thank their colleagues, Nigel Allison, Mark Tiplady, Rita Banks, Ivan Pinson, Nathan Decourcelle, Capucine Carpentier, Bill Lucas and all TWI clients who gave their permission for the use of data and images from various confidential projects.
Notes
Paper presented at the ‘Giornate Nazionali di Saldatura 6’ (National Welding Days) during the workshop ‘Diagnostics and Non-destructive Testing’ – Genoa 26–27 May 2011.
Additional information
Notes on contributors

M. Consonni
Marcello Consonni was awarded a degree in Materials Engineering in 2002 at the Milan Polytechnic. From 2002 to 2006 he worked for Ansaldo Camozzi in Milan (now Mangiarotti Nuclear) in the Department of Materials and Metallurgy; this firm is specialized in the construction of pressure equipment for the nuclear and oil & gas sectors. In 2006 he qualified as International Welding Engineer at the IIS in Genoa. Since the end of 2006 he has been working at the Welding Institute (TWI) in Cambridge (UK), initially in the Fracture Integrity Management Department and currently in the Welding Engineering Department.

D. Howse
David Howse joined TWI in 1994. He is now a member of the Arcs Process, Fabrication and Welding Engineering team as Consultant Welding Engineer. This group provides industrial consultancy services, carries out research projects and development activities and provides training at world level. He has specific experience in a vast range of arc and laser-welding processes and their application in many industrial sectors and has knowledge of the most important international codes and regulations. Before joining TWI, he worked in the offshore construction sector and in the civil construction field as supervisor of steel-structure construction projects throughout the UK. He then worked for an important European steel manufacturer, supporting the commercial business unit as regards welding activities. He was awarded a degree in metallurgy at the University of Leeds and a research doctorate in engineering at the University of Warwick.
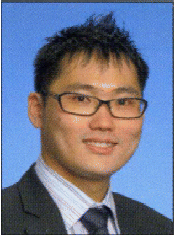
C. Fun Wee
Chen Fun Wee has been working at TWI since 2007 as Project Engineer in the TWI Department in Malaysia, where he has carried out risk-based inspection activities within the framework of risk management relating to chemical plants and energy production. He has also conducted qualification of welding procedures, in accordance with Standard BS EN 15614-2, for the fabrication of a storage tank and for a monorail project. He has applied QA/QC software for the management of fabrication by means of welding for a shipyard in Malaysia and has held courses in metallurgy for the training of instructors at university level.
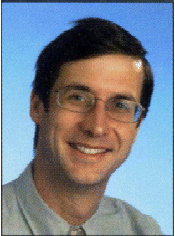
C. Schneider
Charles Schneider, who holds a degree in mathematics, joined the NDT Division of TWI in 1997. He is a specialist in the development of statistical models for the reliability of radiographic inspection and in their use for the extrapolation of data relating to the mapping of corrosion in components in large-size plants. He has also been President of an Independent Qualification Body that supervises phased-array ultrasonic testing of corner welds for Magnox components under pressure.