Most readers will be familiar with five standard types of manufacturing organisation: project, jobbing, batch, flow line or cells, and volume or mass production. The general rule seems to be that in most circumstances we try to organise our resources so that products can flow through them, with the most efficient flow being achieved in mass production where little or no work needs to be done between successive components and products. Jack Burbidge taught us about the grouping of products and processes into families for this purpose. When product variety means that unbroken flow cannot be achieved, we do the best we can with flow lines: groups or cells being better than batches, and batches being better than jobbing. In project manufacture the products, whether power stations or bridges, are often not capable of movement and the production is organised around them. In general, when we talk about products, we organise to save time when we can, by repeating actions as much as possible. When the product cannot flow, because each product is different or because we don't even make a complete product, we organise our resources according to their function, so that whatever girders must be rigged, we have riggers who can do it; whatever casting is to be made, our foundry can cast it. In these situations it is the skill that gives us the basis for our organisation; in fact a whole company might be specialist in offering its skill with no products and no catalogue.
Recent ideas on business processes extend the ideas of flow into the office areas. We understand the links between the stages of manufacture so that we can re-engineer the flow from order to delivery and payment to avoid hold-ups and to save time and cost. John Parnaby identified the idea of cells in office areas, and Mike Hammer launched a massive change in thinking with his ideas on re-engineering business processes into process flows. As an idea that grew quickly and was quickly attacked, the radical type of BPR was soon out of favour, but the concept of process flow still governs the organisation of operations in many companies in manufacturing and service industries. What happens though, where a skill is delivered rather than a process? Burbidge's group technology would allow service areas such as heat treatment to be separated from the normal flow; items would need hardening or annealing (etc) at many different points in the process flow, so the answer was to send them from any point to a single resource whose aim was to deliver a specialist service in a short and reliable time so that the item could return to the process flow without control being lost or time wasted. It would never be economical to install a heat treatment plant at every point where one could be needed; this is a logical exception to the process flow concept, based on the delivery of a specialist service.
So is the answer to organising services to place them in specialist areas? Those who operate heat treatment plants certainly have their own routines, but their process flow must differ in terms of volume, variety and timing from the order fulfilment process they support. There may be only one product going through the factory, but its ten components might require fifty different heat treatments, and the operations may take hours rather than minutes. These flows are not the same as the flow of orders though the main stream of operations. Operating on a different basis, it is convenient to think of them as “black boxes” that do their magic in their own way.
Viewed from the baseline of the well-understood order fulfilment process, activities such as “set strategy” or “recruit staff” operate to different timescales and different levels of volume and variety. They are difficult to link into flow models because their flows operate to different rhythms. So is it right to describe them as “management processes” or “support processes”? It might be better to think of them as specialist functions that provide services.
Where there is a repetitive flow of similar items, we can optimise time and cost by organising to repeat the activities as orders or products flow through. Where each activity is different, because the product (project?) in question is different from the last and the next, perhaps the best way to organise is not to look for flows but for collections of skills that can meet whatever demands may occur. Even if we can identify flows within these areas, the timescales make them quite different to the operational, revenue generating cycles so that a different, or at least a separate analysis is needed. Perhaps we should not lose the concepts of business functions that served so well before we started to re-engineer our processes.
Functions and processes have to be dealt with by all companies, and the management concepts we use to describe and analyse them are still in many ways unsatisfactory and incomplete. Production Planning & Control would welcome papers dealing with any aspect of the organisation of functions and processes in the manage, operate and support areas of manufacturing and service companies.
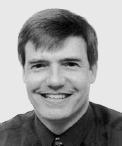
Stephen J Childe
Editor