Abstract
This paper deepens the understanding of the lead factory concept by examining how the lead factory role is operationalised and what challenges are associated with it. The research is based on an explorative case study of eight Swedish lead factories in the manufacturing industry. The empirical findings suggest that the understanding of the lead factory concept should be extended as it is not restricted to one type of set-up. The findings show a spectrum ranging from an entire manufacturing plant, parts of a plant, to a virtual plant considered to be the lead factory. The research also shows a broad range of challenges experienced by lead factories. Several of these are related to and originate from unclear role, responsibility and mandate of the lead factory. The lack of dedicated resources for lead factory activities, specifically long-term development and difficulties in measuring the benefits of the role, were other challenges faced.
1. Introduction
Managing an international manufacturing network effectively and efficiently is an increasingly important task for global manufacturing companies in order to gain competitive advantages (Bartlett and Ghoshal Citation2002; Ferdows Citation1997a; Rudberg and West Citation2008; Shi and Gregory Citation1998). Cheng, Farooq, and Johansen (Citation2014) emphasise that networks with dispersed plants enhance the possibilities of achieving higher flexibility and offer managers better conditions for responding to current business challenges. However, in order to benefit from the possible competitive advantages of being located globally, manufacturing companies must consider all plants as part of an integrated global network, rather than a collection of single production plants dispersed internationally (Ferdows Citation1997b), as coordination between the plants in the network is as important as their strategic location (Feldmann et al. Citation2013). Thus, manufacturing networks should be managed as expanded manufacturing systems (Shi and Gregory Citation1998). This requires a shift in the focus of manufacturing companies, from a plant focus to an international manufacturing network focus (Ferdows Citation1989; Nassimbeni and Sartor Citation2005; Rudberg and Olhager Citation2003; Shi Citation2003).
An important element in the management of international manufacturing networks is the role assignment for the different plants in the network. Production plants in international manufacturing networks often have different responsibilities and therefore different strategic roles in the network (Feldmann and Olhager Citation2013; Ferdows Citation1997a, Citation1997b; Thomas et al. Citation2015; Vereecke, Van Dierdonck, and De Meyer Citation2006, etc.). The classification of foreign subsidiaries generally relates to plant-specific capabilities (Cheng, Farooq, and Johansen Citation2011; Vereecke and Van Dierdonck Citation2002) and has resulted in several proposals for classifying subsidiaries (Bartlett and Ghoshal Citation2002; Birkinshaw and Morrison Citation1995; Cantwell and Mudambi Citation2005; Enright and Subramanian Citation2007; Hogenbirk and van Kranenburg Citation2006; Rugman and Verbeke Citation2001). One model that has gained much recognition is the framework presented by Ferdows (Citation1989, Citation1997a). On the basis of site competence and the primary strategic reason for the site, Ferdows (Citation1997a) differentiates between six generic strategic roles for factories of which the highest is the lead factory. According to Ferdows (Citation1997a), the lead factory is a global hub for product or process knowledge and creates new processes, products and technologies for the entire company. It is an important and strategic role for the lead factory to possess and for creating value in the network. This role or similar is also referred to as master plant/master function (Bengtsson, Niss, and Von Haartman Citation2010; Rudberg and West Citation2008), main plant (Feldmann et al. Citation2013), centre of excellence (Frost, Birkinshaw, and Ensign Citation2002) or hosting or active network factory (Vereecke, Van Dierdonck, and De Meyer Citation2006).
The main purpose of Ferdows’ model is to classify plants, while the roles and the operationalisation of them have not been emphasised. There is a need to describe the role of the plant from multiple dimensions, such as its responsibilities and the scope of its operations (Enright and Subramanian Citation2007; Thomas et al. Citation2015). Further, the majority of previous research related to the lead factory role focuses on strategic plant roles from a network perspective (for example, Colotla, Shi, and Gregory Citation2003; Miltenburg Citation2009; Thomas et al. Citation2015) and not from the perspective of the lead factory. Previous research focusing on the typology of plants provides some insights into the critical capabilities and characteristics of the actual lead factory (Feldmann and Olhager Citation2013; Ferdows Citation1997a; Maritan, Brush, and Karnani Citation2004; Meijboom and Vos Citation2004; Vereecke and Van Dierdonck Citation2002; Vereecke, Van Dierdonck, and De Meyer Citation2006). However, neither in academia or in the industry is there a common understanding of what the role of the lead factory fully entails, which creates uncertainty for manufacturing practices. Specifically, very limited research has been conducted on the operationalisation of the lead factory role, i.e. the realisation and execution of the lead factory role and on how it affects operations at the lead factory. It is not known what challenges are associated with the operationalisation of the lead factory role and how these should be addressed to enable the lead factory to contribute to increased network performance and create value in the overall network. Managers are therefore left with limited support concerning the management and operationalisation of lead factories in international manufacturing networks. Thus, scientific and industrial knowledge of lead factory operationalisation is required. Consequently, the purpose of this paper is to deepen the understanding of the lead factory role by (1) examining how it is operationalised, (2) what challenges are associated with it and, from this, identify future research opportunities.
2. Literature review
2.1. The strategic role of the manufacturing plant
The ability to manage conflicting demands from the business environment has become a key factor in the area of international strategy literature (Vereecke and Van Dierdonck Citation2002). Accordingly, global manufacturing companies with multiple plants that work in a global context need to adopt a structure and an organisation that allows them to respond to the competitive environment. This includes a clear understanding of the strategic role of the manufacturing plant and its relationship with the headquarters, R&D and other manufacturing plants, as well as an understanding of the activities carried out at the manufacturing plant. One level down, from the plant’s perspective, the challenge is to understand and adopt the assigned role and organise in a way that allows proper execution of the role in the network.
In the literature, multiple ways of classifying the different strategic roles of manufacturing plants have been proposed. One aspect of the role of a manufacturing plant relates to its strategic capabilities. In the study presented by Bartlett and Ghoshal (Citation2002), three competitive dimensions or capabilities were considered: global integration (cost competitiveness), national responsiveness (flexibility) and worldwide learning (innovation and learning). The authors concluded that in today’s highly competitive environment, companies need to aim at combining all three capabilities simultaneously in a so-called transnational organisation (Bartlett and Ghoshal Citation2002). A means to achieving a transnational organisation is a decentralised network of ‘mini-factories’ (Reichwald, Stotko, and Seifert Citation2003). Thus, the dispersed manufacturing plants should contribute to the development of a transnational organisation and need to be integrated in a network of diverse manufacturing plants with differentiated roles and allocated responsibilities.
As mentioned in the introduction, manufacturing plants play different strategic roles within a company and there are several proposals for classifying subsidiaries based on different aspects and dimensions. Jarillo and Martíanez (Citation1990) characterise subsidiaries based on the degree of localisation and the degree of integration. The degree of localisation implies the extent to which R&D, purchasing, manufacturing and marketing, for example, are performed in one plant, while the degree of integration implies the extent to which activities performed in another plant are integrated with the same activities in other plants in the network.
Our work mainly builds on the framework presented by Ferdows (Citation1989, Citation1997a), which has received much attention. Ferdows’ model transfers the general classification models, including the entire supply chain, into a system of classifying manufacturing plants (Vereecke and Van Dierdonck Citation2002). Based on the two dimensions of site competence and the primary strategic reason for the site, Ferdows (Citation1997a) differentiates between six generic manufacturing plant types: offshore, source, server, contributor, outpost and lead factory (Ferdows Citation1997a). An offshore plant is characterised as a low-competence site primarily established for reasons related to low-cost production, while a lead factory holds a wide range of competencies and managerial responsibilities. In the lead factory, new processes, products and technologies are developed for the entire company. Ferdows’s classification has been tested and verified on a general level by a variety of researchers who have made further contributions to the original model (e.g. Cheng, Farooq, and Johansen Citation2011; Feldmann and Olhager Citation2013; Meijboom and Vos Citation2004; Vereecke and Van Dierdonck Citation2002). For example, the findings of Feldmann, Olhager, and Persson (Citation2009) show that in Sweden, no pure-cost oriented plant was found, while the primary reason to locate manufacturing in Sweden was the high level of competence.
The main purpose of Ferdows’ model is classification of plants; role operationalisation or network coordination issues have not been emphasised. Over the past decades, research has shown the need to also consider the relationship between different plants, i.e. coordination of the different plants in the network (Cheng, Farooq, and Johansen Citation2015; Shi and Gregory Citation1998; Thomas et al. Citation2015). The analysis presented by Vereecke, Van Dierdonck, and De Meyer (Citation2006) leads to the identification of a third dimension that focuses on the various types and intensities of relationships between other plants and the headquarters. Accordingly, research on the strategic role of plants should consider more dimensions than the two dimensions identified by Ferdows. There is a need to describe the role of the plant from multiple dimensions, such as its responsibilities, the scope of its operations, its competence level and the importance of the markets, as all these factors impact the network structure and strategic role of the different plants (Enright and Subramanian Citation2007; Thomas et al. Citation2015).
To sum up, global manufacturing companies usually have a range of factories in their production network. At one end of the spectrum, it is possible to find plants that are characterised by low competence that are primarily established for reasons related to low-cost production, while at the other end of the spectrum, it is possible to find plants that hold a wide range of competencies and managerial responsibilities, i.e. lead factories designated to create value for the overall network.
2.2. The lead factory concept and its challenges
Ferdows (Citation1997a) describes the lead factory as having a high level of competence and being a global hub for product or process knowledge and its role is to create new processes, products and technologies for the entire company. In order to improve manufacturing, the lead factory should develop verified manufacturing processes that can then be ‘cloned’ to the other plants in the network, i.e. transferred to subsidiaries that implement the standardised process and manufacture the product for other markets (Bengtsson and Berggren Citation2008). It is important that the lead factory learns from its own experiences based on, for example, previous ramp-up processes and that it makes the required modifications to the subsequent design processes that enable products to be manufactured in a simpler and more cost-effective way (Ferdows Citation1997a). Learning should not only take place in the lead factory, but also in the network. The relative absorptive capacity, i.e. the ability to learn from the past experiences of others and absorb and learn from other processes to develop as a lead factory, is critical (Bengtsson, Niss, and Von Haartman Citation2010; Tsai Citation2001).
A lead factory should continually transfer knowledge and information about product modifications and changes in the production systems to the subsidiaries for which it is responsible (Rudberg and West Citation2008). Local adjustments may be needed that could cause a major challenge when trying to find a balance between maintaining central control and giving the subsidiaries a degree of autonomy that allows them to develop into independent subsidiaries (Pogrebnyakov and Kristensen Citation2011). This is in line with Shi (Citation2003), who highlights that the real challenge is how to balance global integration and local responsiveness.
Previous research points out that different plants might have different specialisations depending on the different stages of the product and process lifecycle. The role of the lead factory usually includes responsibilities related to process development and the introduction of new production (Hayes and Wheelwright Citation1979), which includes developing secure and efficient manufacturing processes, as well as organising a supply chain. Thus, the lead factory role usually entails early involvement in both product and process lifecycles. However, a lead factory should not only be effective in process development and new product introduction, it should also maintain the manufacturing capabilities and performance at globally competitive levels in serial production (Prajogo and Sohal Citation2004).
Lead factory specialisation can also be differentiated between being process focused or product focused, a differentiation already made by Hayes and Schmenner (Citation1978). A process-focused plant usually takes responsibility for a few manufacturing processes for many products and is only responsible for a few steps in the value chain. The product-focused plant, on the other hand, has responsibility for the manufacturing processes of the entire product, but only for a limited number of products with similar attributes. Thus, there can be several lead plants in one company but with different areas of responsibility.
Since lead factories do not work in isolation, but in a network comprising several subsidiaries, there is also a need to consider the interdependencies between the other sites in the network and also between the lead factory and the network itself (Miltenburg Citation2009; Riis et al. Citation2007). For example, Cheng, Farooq, and Johansen (Citation2015) point out that it is not sufficient to study plants as separate units, as an international manufacturing network is generally described as a plant network with matrix connections. Jaehne et al. (Citation2009) suggest an extended supply chain model, but for global production networks, a value network. Accordingly, there is a need to take a broad perspective that should include highlighting interdependent coordination since each plant in the network affects the other plants and therefore cannot be managed in isolation.
In addition, previous research shows that the role of the company is not static. Slepniov, Waehrens, and Johansen (Citation2014) demonstrate that the idea of transferring ‘only’ strategically neutral parts of production and retaining strategically important production activities at the home base may be difficult to implement. By contrast, it has been shown that subsidiaries are strategically expansive, i.e. the role of offshored sites is likely to be upgraded and could entail new capabilities (Adeyemi et al. Citation2014; Feldmann et al. Citation2013; Ferdows Citation1997a, Citation2006). Consequently, the relocation of certain production activities to other sites may eventually lead to the relocation of the remaining production activities to the upgraded offshore site and a loss of production capabilities at the home base, as well as a geographic separation between production and innovation activities (Slepniov, Waehrens, and Johansen Citation2014). However, a perceived or actual loss of competence in manufacturing would result in an almost instantaneous loss of this status (Prajogo and Sohal Citation2004).
Since companies today not only offshore manufacturing activities more than they used to (Cheng, Farooq, and Johansen Citation2014; Søndergaard, Oehmen, and Ahmed-Kristensen Citation2016), the increasing globalisation of manufacturing networks is continually changing and constitutes a severe risk for lead plants. When increasingly more manufacturing activities, including knowledge-intensive and proprietary manufacturing tasks, can be mobile or relocated, an increasing number of countries have become viable contenders for a company’s production operations and the number and significance of location decisions has increased (Porter and Rivkin Citation2012). As a result, subsidiaries and production plants that do not have a lead plant role in the manufacturing network have started to change their roles by increasing the scope of their activities and by seeking more autonomy in order to reduce the control of lead factories and the headquarters in their operations (Adeyemi et al. Citation2014). If one plant changes its role in the network it will have an impact on other plants in the network (Cheng, Farooq, and Johansen Citation2011; Feldmann et al. Citation2013) and Cheng, Farooq, and Johansen (Citation2011) demonstrate how a plant role might evolve in a network. Accordingly, it is even more challenging to uphold the lead plant role in today’s global and rapidly-changing networks. On top of this has been an evolution in the role of the lead factory in the network, which creates uncertainties regarding the meaning and scope of the lead factory role.
To sum up, while the above-discussed research provides important insights into the lead factory concept, it primarily addresses the lead factory role at a network level and there is little research concerning the operational level and the operationalisation of the lead factory role. Current literature does not elaborate on different lead factory set-ups and the different challenges the lead factory role can entail depending on the lead factory set-up in relation to the rest of the network.
3. Research design
In order to investigate the application of the role of the lead factory and its inherent challenges, a multiple-case study of eight cases was carried out. The case study approach enabled an in-depth study of the operationalisation of lead factories and the challenges related to the role in the real-life context of the manufacturing network (Yin Citation2009). The selection of cases was based on an assessment of the company’s responsibilities and actions in the network and if, according to previous literature, they were to be classified as lead factories, as some companies did not have a clear structure with formal role appointments (or called it something else) but still had acting lead plants. Each case comprises one or more lead factories in the company’s global manufacturing network and was selected based on their willingness to better manage the lead factory role. Two of the cases (Cases E and F) belonged to the same division in their company but were lead factories in different product areas. Each case company and its lead factory set-up are described in more detail in Section 4.
Data were gathered through interviews, questionnaires, collected documents, informal discussions and workshops. The primary source of data was gathered through 57 semi-structured interviews. The interviews lasted from between 22 and 133 minutes and were primarily single face-to-face interviews. A few telephone and Skype interviews were conducted due to the respondents being far away, and a small number of group interviews were conducted because of planning issues or requests from the interviewees. The number of interviews per case varied with a minimum of two respondents per case (see ). The variation in the number of interviews conducted was due to access and time/resource limitations, which prevented all the case companies being studied to the same extent. The interviews were, however, not the sole source of data, as questionnaires and informal discussions and workshops were also employed to help build an understanding of the cases and their narrative.
Table 1. Overview of the interviews conducted.
The respondents in the interviews were chosen based on their involvement in the lead factory management and execution. As the study focuses on the operationalisation of the lead factory role, the majority of respondents were organisationally positioned at the lead factories but had some element of global responsibility. Cases B, D, E, F, G and H also included respondents from central organisations or top management and Cases B, D, G and H also included respondents from the subsidiaries to widen the perspective of the lead factory role and the execution of it.
An interview guide was used in regard to the respondents’ organisational positions. For respondents at the lead factory, central organisations and top management, the questions covered the respondents’ roles and background information, manufacturing network structure and prerequisites, role of the lead factory, and its responsibilities and inherent challenges. For respondents at the subsidiaries, the questions covered the respondents’ roles and background information, subsidiary plant structure and prerequisites, and the relationship to and expectations towards the lead factory. All interviews were recorded and transcribed. Due to the exploratory nature of the research, the interview guides were slightly altered during the process of data collection in order to apply new insights and relevant aspects that emerged.
The interviews were complemented by two written questionnaires for all case companies. One of the questionnaires covered the experienced position of the lead factories in the network and their part in decision making, while the other questionnaire focused on the value created in the network by applying a lead factory concept and the follow up of the created value. The questionnaires were answered by persons with key positions with respect to the lead factory responsibility and role fulfilment at each case company. To add to the insights derived from the interviews and questionnaires, documents were also studied, including documents describing the network structure, role of the lead factory in the network and other company-specific information. Furthermore, informal discussions and workshops with managers and engineers at the lead factories were held and observations were made with respect to the concept of the lead factory’s role and the challenges as encountered.
The multiple-case study analysis was conducted in two stages: a within-case analysis followed by a cross-case analysis (Merriam Citation1998). During the within-case analysis, data were analysed to create a narrative that was used to describe and develop an understanding of the application and operationalisation of the lead factory role in each case and the inherent challenges in each case context. Summaries of these narratives are presented in Section 4. The cross-case analysis aimed at building theory across the cases to create a general explanation of the study of the lead factory role and its inherent challenges. The cross-case analysis was conducted in four stages including coding, clustering, categorising and subsuming the data into patterns (Saunders, Lewis, and Thornhill Citation2012). First, each interview was coded separately by two researchers according to pre-set categories: capabilities, structure, identity, interaction, challenges, created value and miscellaneous. The two codings were compared and compiled. Following this, similar entities were clustered and categorised. The categories were of a data-driven nature and addressed different types of lead factory set-ups, prerequisites and challenges related to the lead factory role. The coded and clustered data were then analysed and patterns across the cases were searched for in relation to the different set-ups identified. To further strengthen the data set concerning challenges, a second round of data collection was conducted in which the compiled list of identified challenges from the interviews, document collection and questionnaires were sent out to one or two key representatives at each case company to record which of the identified challenges they primarily experienced and also rank the top five most experienced challenges. The respondents were also asked to add challenges if they felt the list was incomplete. From this, the identified challenges were ranked based on the weighted average.
4. Operationalisation of the lead factory role
In the following sections, the eight cases are described with a focus on the operationalisation of the lead factory role. The case descriptions include general introductions to the companies and their networks, a summary of the application of the lead factory role and responsibility and a description of the lead factory’s relationship to the subsidiaries, other lead factories within the network and/or the management. The lead factory set-ups are summarised in .
Table 2. Overview of the lead factory set-ups and its responsibilities.
4.1. Case A
Company A is a large global pharmaceutical company with 27 manufacturing sites distributed across 16 countries. The lead factory is located in Sweden and has a long manufacturing tradition. With 3800 employees distributed over two plants, the lead factory is recognised as the largest high-tech manufacturing site in the network and manufactures around 35% of the company’s total production volume. The company has several lead factories in its production network that are responsible for different product segments. The lead factory being studied has officially been assigned the responsibility for two main areas: (1) supply and manufacturing of the products in its product segment of responsibility and (2) new product introduction of all products launched in the product segment’s market.
The lead factory is currently the only plant in the network that can manufacture the full range of products in its product segment and for different markets. The other plants solely manufacture a few products or are responsible for packaging for the regional market. As the lead factory is the designated launch site for new products, it is highly involved in new product development processes. This requires close collaboration with R&D, which is located in another Swedish city. The lead factory is responsible for conducting the company’s audit work but has no assigned responsibility nor any formal mandate to make the subsidiaries comply with standards or develop other plants in the network.
The collaboration between the different plants in the network is generally considered to be good and is usually based on a mutual exchange between all involved parties so that everyone can learn from each other and improve their performance. After merging with another company, the company’s headquarters were transferred from Sweden to another country. As a result, the lead factory lost its close relationship with the top management and all important strategic decisions are now taken at a higher level.
4.2. Case B
Case company B manufactures products for the rail industry. The company’s division comprises three product segments. The Swedish plant being studied specialises in manufacturing parts of the products in one of these segments. The plant has around 200 employees and the direct production network they belong to includes five plants, although the entire network is much larger. R&D of the specific product segment is located in the same city, while the company’s headquarters are located in North America.
A few years ago, the plant initiated an attempt to become a lead factory. As there is extensive experience of development of assembly systems and manufacturing technologies at the plant, as well as the introduction of new products, the plant wanted to change its role from a high-volume manufacturing plant to a lead factory, including a focus on being an introduction plant for new products in its segment. However, shortly after receiving approval for the plant to become a lead factory, there was a larger restructuring and the top management was replaced. This led to new organisations in which new business models are to be introduced. However, the lack of clarity regarding the aforementioned new business models and the absence of a clear mandate has caused confusion. There is no clear directive on how the lead factory concept should be established in the network, nor is there a clear description of the lead factory’s role, responsibility, budget or resources. While the new organisation is being established, the plant currently acts as a lead factory by supporting other plants in its network.
4.3. Case C
Case company C is part of a company in the automotive industry with eight manufacturing or assembly plants distributed over three countries. The lead factory belongs to a segment of the company that manufactures one of the key components of the final product.
In the business segment in question, the aspiration with the lead factory concept is a virtual lead factory. The idea is that the master processes should be developed virtually and then implemented at the physical factories. This desired lead factory set-up is new and has only recently been started due to a change in ownership. Currently, the direct network of the lead factory comprises two physical plants, one located at the site at which the virtual development takes place and one located in a different country. The staff at the plant located at the same site as the virtual development has extensive manufacturing experience, while the other plant started its manufacturing only two years ago.
The majority of R&D and management are located in another city than the physical plant. Although the company management is located in another city, the relationship is considered to be close as there are continuous interactions between different functions and persons. Nevertheless, the distance slows down the decision-making process. Furthermore, since the company is part of a larger company with several brands, the general management is located on another continent.
4.4. Case D
Case D is part of a global manufacturing company in the heavy vehicle industry. The company has 15 manufacturing sites located in nine countries. As a result of a previous merger between two companies, the headquarters are located in a ‘neutral’ country where no manufacturing is carried out.
The company has several lead factories in the network; each is assigned the lead factory role for a specific product segment, at either component or final product level. The study focused on a lead factory at the component level. The lead factory, located in Sweden, has approximately 500 employees. The lead factory being studied has a long tradition of manufacturing in the specific product segment. The lead factory is located at a larger site, at which other organisations and functions in the company, such as product development, sales and aftermarket are represented. Due to its role and because the plant is geographically close to product development, it actively contributes at an early stage in product development projects to ensure high manufacturability.
At the lead factory, all new products are introduced and ramped up to full production. The verified manufacturing and assembly processes are then transferred to the subsidiaries. Furthermore, to assist in the development of the subsidiaries, their employees are educated and trained at the lead factory.
Currently, the lead factory’s direct network includes two subsidiaries, one that has been part of the network for several years and one that was recently established. The new plant is rather inexperienced and requires a significant amount of support from the lead factory. The establishment of the new plant was heavily influenced by the lead factory and the lessons learned are based on its current production set-up. As a result, the new plant has a more efficient layout and newer production technology compared to the lead factory. The lead factory has recently started to follow up the work at the subsidiaries through audits in order to ensure a common manufacturing process across the network and to share best practices. There are also area-specific networks led and coordinated by the lead factory to enable the sharing of best practices.
To handle support to the subsidiaries and to manage transfer projects, the plant has a specific department comprising four employees responsible for project management and global support. However, the department is not responsible for general long-term production development in the company. This has led to conflicts and misunderstandings at the lead factory, as many employees outside this department have assumed that the entire lead factory responsibility only lies with the global support department and not at factory level, even though the department has been assigned only part of the entire responsibility of the lead factory.
Although the lead factory’s role is officially assigned by the top management, the lead factory does not have a strong voice when decisions are taken regarding where components should be manufactured. Each plant develops its own business case, although it is the lead factory that provides all the input in terms of estimated production data and calculations, as the subsidiaries do not have this specific knowledge. However, the lead factory has no insight into how the subsidiaries apply these figures when developing their business cases. For example, there are instances in some business cases where the subsidiaries have overestimated their own capability or underestimated the complexity and risks related to the product transfer.
4.5. Cases E and F
Cases E and F are both parts of a large global manufacturing company in the automotive industry with 45 manufacturing sites and 55 distribution centres. The company started its operations in Sweden and has expanded by acquiring several brands for different markets; the headquarters are still located in Sweden. The company has a central operations department, which is not directly linked to the plants, designed to support long-term development and to be responsible for the master processes. The manufacturing sites are grouped into manufacturers of the final product or of the components. Accordingly, the company has assigned the lead factory role to several plants depending on the specific product manufactured at the respective plant. The study includes four lead factories, all located in Sweden, responsible for different product segments in their areas. Due to differing lead factory roles in the network structure and how the lead factory concept was organised, the findings are differentiated into two cases, E and F.
4.5.1. Case E
The two plants in Case E belong to the final assembly network and have four and six manufacturing sites in their respective direct networks. They also have a number of distribution centres (DCs). Both plants in Case E have designated a physical area as their lead factory, labelled ‘pilot plant’. The lead factories are responsible for the development and validation of new processes and methods before these are implemented in serial production. The serial production plants, in which the lead factories are located, have a long tradition and experience of manufacturing their respective product segments.
One of the lead factories is located close to the headquarters and all central functions, including R&D and central development departments. Furthermore, there is a difference regarding the introduction of new products. For one of the lead factories, the newly-developed processes and methods can be implemented at any assembly plant in the manufacturing network and are not necessarily implemented at the site at which the lead factory is located. Contrary to this, for the other lead factory, the introduction of new products always takes place in the plant at which the lead factory is located. Both lead factories also support other plants around the globe and provide a training as well as a meeting arena for the entire network.
4.5.2. Case F
The direct network of Case F includes eight component manufacturing plants distributed across five countries. The two lead factories have around 1500 and 2800 employees, respectively, and are the largest plants in their product segments. Both plants have a high degree of advanced manufacturing technology and a long manufacturing tradition. However, they have only recently been assigned lead factory responsibility.
The component manufacturing lead factories have a different structure compared to those that manufacture the final product. In these lead factories, the entire plants are considered the lead factory. The lead factories are responsible for long-term production development in accordance with the technology roadmap, giving support to the subsidiaries and being representatives in new product development projects. The technology roadmaps include the identified future production development requirements that are developed centrally with input from assigned specialists at the lead factories. These specialists are, in turn, responsible for production development. Production development activities are, however, strongly affected by the central organisation, in which all development activities are coordinated, resources prioritised and decisions regarding investments made. In this central forum, all plants are represented and the ambition is to reach a common agreement.
The lead factories are at the same level as the other plants in the network and final decisions are taken centrally. However, when it comes to new product development projects, the lead factories represent all sites. R&D is not located in the same city as either of the plants. There are also examples where the lead factories are responsible for maintaining knowledge and development activities of manufacturing processes related to products that are manufactured at subsidiaries but not at the lead factory itself.
4.6. Case G
Case company G belongs to a large global company in the aerospace industry. The company network has grown extensively during the last decade by acquiring existing plants. The business sector to which the case company belongs comprises 12 plants in four different countries. The case company is part of the largest production site in the network with 2000 employees. Besides this, the production plant site also hosts parts of R&D, central development functions and large parts of management.
The lead factory is not only by far the largest, but also one of the oldest plants in the network. Based on its size in terms of personal resources, its wide-ranging and deep level of competence and extensive production experience, the plant has a lead factory role in the network and, from both top management as well as from the other sites, is expected to assist and support the other plants, although there is no official lead factory structure. Many of the other plants in the network turn to the lead factory for assistance with different types of production-related matters such as operations and the development of manufacturing technology, production, processes or quality improvements and system support. The lead factory often supports the subsidiaries, both remotely and by sending personnel, on both a long-term and a short-term basis. Most often, and especially for larger/longer initiatives, the receiving plant has to pay for the supporting resources assigned from the lead factory, as it does not have any extra or dedicated resources for global support. The lead factory also plays a leading role in new product development and is the speaking partner and link to R&D for the majority of the subsidiaries. Only a few of the other plants have direct contact with R&D.
The case company is also a driving force in different types of strategic decisions. For example, a second R&D site was established and initiated by the lead factory to relieve the pressure on the current site. The lead factory is also a driver in strategic decisions, such as where to locate manufacturing and engineering activities, as well as in deciding on the way of working.
4.7. Case H
Company H is a very large global manufacturer of precision steel products. The plants in the network are divided into clusters based on product types. The cluster that the case company belongs to includes four other plants. With its 1000 employees, the lead factory, located in Sweden, is the largest plant in its direct network and also one of the largest plants in the entire company.
In each product cluster is a lead factory expected by both management and the other plants to take a leading role in development activities and provide support to the other plants in the network. This role is usually assigned to the largest plant due to its size in terms of resources, and also experience and competence level. The lead factory being studied was the first plant in the entire network and has a long tradition of production in its segment. Due to its size, it also has a wide and deep array of competencies and is considered a natural lead factory. This plant is also the only plant in its network that manufactures all types of products within its segments, while the subsidiaries only produce parts of the product range. New products and variants are initially introduced at the lead factory and new production processes are initially developed and/or implemented and tested at the lead factory. The lead factory also provides production-related support to its subsidiaries and takes the lead in production development activities. It also gives recommendations in development projects and prepares the basis for investment decisions at the network level. However, as the lead factory role is not an official role in the network, there is no separate function or resources, but the department of process development is primarily involved in the lead factory-related work. The plant is, however, working towards an official structure to clarify its responsibility and be able to organise itself accordingly.
The lead factory is located at the same site as R&D, company headquarters and other central development and support functions. Thus, the subsidiaries in the network sometimes find it difficult to separate the plant from the entire site, including R&D and headquarters.
There is some collaboration between the different acting lead factories in the extended network, but there is also a perceived difference in the openness and willingness to share and assist others. This difference was also highlighted by the subsidiaries that had engaged in collaborations with several of the acting lead factories.
5. Challenges related to the lead factory role and its operationalisation
In this section, the empirical findings on the challenges associated with the lead factory role and operationalisation are presented.
5.1. The lead factory role, responsibilities and mandate
A challenge that all the case companies faced to some extent was uncertainty related to the lead factory role and its responsibilities. Understandably, the plants from companies at which the lead factory structure was not fully formalised and the role appointment was more unspoken than official – such as in Cases B, C, G and H – experienced uncertainty regarding what was expected of them. However, the fact that there were expectations for the plant acting as a lead factory was confirmed by the respondents outside of the lead factory (at subsidiary, central function and/or management/headquarter level). As the lead factory structure was not formalised, there was no clear directive to relate to, which caused confusion. Also, at formally - appointed lead factories, such as in Cases D–F, it was unclear what the lead factory’s roles fully entailed and what responsibilities came with it. To extend this challenge, respondents in several of the cases also raised the question of what was not included in the lead plant role. The Process development manager in Case H expressed it thus: ‘We don’t know if or when we can say no.’, for example, when subsidiaries ask for support, as it was not evident what actually falls outside the lead factory’s responsibilities. In the case Company C, for example, the new virtual lead factory structure, its meaning, what it involves and what formal responsibilities it includes was unclear. Despite an existing lead factory role description in Case D, there was also a high level of uncertainty as it was not clear if the lead factory responsibilities rested on the department, plant or site level. Also, in Cases G and H, similar problems were experienced, but by the subsidiaries, as the lead factory was located at a larger site that contained R&D and headquarters and the interfaces between them was blurred.
With regard to the unclear responsibilities or role description, there was, in all cases, also the challenge of an unclear mandate or lack of a mandate to be able to fulfil the lead factory responsibilities, e.g. connected to the standardisation of the working methods. Case companies D and E, which were formally appointed and responsible for developing standards, pointed out that they had no mandate to make the subsidiaries follow them. In Cases A and D, the case company was, for example, auditing the subsidiaries’ way of working, but without a mandate to control it. In several cases, it was stated that it desired a mandate to make the subsidiaries comply with new procedures and standards for it to be able to fulfil its lead factory role. It clearly emphasised that it was hard to make the subsidiaries accept directives from the lead factory and it often experienced a ‘not invented here’ mentality. One of the lead factory managers in Case E expressed this frustration, stating: ‘Why don’t they just do as I tell them?’ A senior advisor in Case A stated: ‘We have a pilot plant where, for example, we test new technologies but I don’t know how much of this is transferred within the network’.
5.2. Standardisation and subsidiary diversity
The challenge of resistance by the subsidiaries in complying with directives from the lead factory relates to different aspects of another common challenge, that of standardising. In all cases, the plants in the network differed in their prerequisites, such as size, competence/experience, product range, local regulations and customer requirements, which made it difficult to collaborate, and also for the lead factory to exchange developed knowledge between the plants. The differences not only limited the possibilities and effects of fruitful collaboration but also made it difficult to standardise solutions or working methods. The majority of the lead factories had difficulty making trade-offs between the degrees of global standards and required local adoptions. As expressed by the product engineering manager in Case C: ‘We want to make major purchasing decisions globally […] in the same time we want to find the optimal solution for each plant’. In Cases E and H, the respondents pointed out that, for example, investment decisions were not centrally coordinated to the desired extent but were instead influenced by a high degree of local development. There were even examples in which similar development activities took place at different plants, thus bypassing the entire lead plant structure.
Physical prerequisites such as plant layouts, type, level of equipment and degree of automation also made it difficult for the lead plant to be a physical ‘role model’. In Case D, this became evident as the lead factory supported the development of a new plant in the network. This resulted in a subsidiary with a more efficient layout and newer production technology compared to the lead factory. Also, in Case H, the unfeasibility of the lead factory always having the latest technology or systems in every aspect was discussed, as the lead factory could help a subsidiary invest in the most advanced up-to-date equipment, which would make a significant improvement. The same investment for the lead factory might only involve an incremental improvement instead and is, therefore, not feasible. In Case C, this problem was avoided to some extent by having a virtual lead factory concept that could always be kept up to date with the latest equipment, etc. It did, however, experience other challenges. As the virtual plant was considered to be a master plant in terms of its production processes, it was extremely important to use updated information and ensure that the virtual plant was continuously updated as soon as changes were implemented in any of the physical plants. However, this required changes at the physical plants to be continuously registered in a consistent manner.
One major impact on the execution of the lead factory role appears to be the product types and range at the plants in the network. In Cases E and F, this became clear as the lead factory role took very different forms, despite being part of the same company. In Case E, as an assembler of the end product, the collaboration was considered challenging, since all plants in the network handled different brands and their organisational affiliation related to different markets. Thus, the lead factories had to collaborate with a vast range of stakeholders with differing directives. Furthermore, there was ambiguity relating to governance and how the lead factory should work and communicate with the diverse stakeholders in the development process. This was considered challenging. It can be reflected that this might be one of the main reasons why its lead factory set-up was strongly focused on creating a meeting arena. The situation was not the same in Case F, as the manufacturing of components was much more standardised among the brands, i.e. the same components were supplied to internal customers irrespective of brand. Therefore, its lead factory role was much more focused on long-term production development activities, as there were greater opportunities to standardise the production in its network.
In Case B, all the subsidiaries had different product variants and models and it was not clear how much knowledge of all products was required by the lead factory. In several of the cases, such as A, D and H, one of the motivations for the lead factory appointment was that the plant had the ability to manufacture the whole product segment, although this was not always the case. Thus, one major challenge for lead factories is to be responsible for manufacturing products outside the lead factory’s own scope and this includes competence in both products and production processes.
The difference in experience, competence and resources at the subsidiaries also affected the type and level of support required from the lead factory. In Case D, this was clear, as one of the recently established subsidiaries required a lot of support at all levels, while the well-established subsidiary had a much higher level of autonomy, i.e. it worked independently and had its own development initiatives, which were rarely coordinated with the lead factory. Similar experiences were expressed by several other lead factories. The lead factory must deal with and manage a large range of different requirements and adjust its way of working to fit each subsidiary.
5.3. The network perspective
Another challenge was that development initiatives were still carried out in other plants without the involvement of the lead factory. In Case A the lead factory was responsible for spreading best practices in the network. If a particular solution was developed in one of the smaller plants in the network without the oversight of the lead factory, it may work well in that particular setting, but it was unclear how it might work in a large-scale manufacturing environment or in other plants in the network. Thus, there is always a risk that the proposed solutions become a global standard for the entire company, even though this might have a negative impact on the other plants. More specifically connected to the operationalisation of the lead factory role was the challenge of putting the benefit of the network before the benefit of the plant. The need of a shift in mindset from putting what is best for the network before what is best for the plant in acting as a lead factory was understood, but still had its challenges. This was expressed by the head of manufacturing engineering in Case B thus: ‘There is a challenge in people’s mindsets here […] from thinking that we need to optimise our plant, we should optimise our business unit or competitive advantage and build a spirit of comradeship’. Some respondents, however, considered this to be an ethical dilemma concerning loyalty to the plant at which they work versus loyalty to the network as a whole.
As discussed above, one of the key points of the lead factory role is to put the benefit of the network first, as the lead factory is expected to be a knowledge creator for the entire network. To be able to accomplish this, a good understanding of the subsidiaries’ prerequisites and requirements is a key lead factory capability. As pointed out by one of the respondents in Case F: ‘We have to understand that our needs are not always their [the subsidiaries’] needs’. However, as discussed in the previous section, the diversity of the subsidiaries makes this task challenging. In Case D, the interviewees considered it particularly challenging to have knowledge of and represent the local needs and conditions of all subsidiaries in the product development projects. In Cases E and F, engaging the subsidiaries in development work and making them feel involved and motivated and avoiding the ‘not invented here’ syndrome were highlighted as challenging. One of the main ways of overcoming this was to make the subsidiaries understand the benefits of having a lead factory structure; however, this was not always the case. Some emphasised that this was a management issue and did not rest on the lead factory. Nonetheless, these internal politics were considered a challenge in which subsidiaries did not respect or accept the lead factory structure in itself or the plant that was appointed the role. In Cases B and H, internal competition, specifically for the lead factory role, was described as a challenge, while in Cases B, D, E, F, G and H, the internal competition for production volumes was also considered to be challenging and a background to the resistance towards a lead factory structure. In Case D, the case company also felt that the other plants had a tendency to ‘oversell’ themselves and did not take risks into account properly when it came to making business cases, for example, when considering new products. This was one of the reasons why it also wanted the lead factory to weigh in more strongly on certain decisions by having a neutral voice that protected the best for the network.
5.4. Lead factory operations
One challenge when it comes to operationalising the lead factory role related to the lack of formalised processes and structures for carrying out the lead factory responsibilities. For example, only a few lead factories conducted continuous or structured audits or follow up of subsidiaries. The lack of follow-up not only made it difficult to understand their needs but also made it hard to identify current best practices and promote them within the network.
In Cases A and B, the lack of an established working method in the network raised issues about how to achieve an efficient organisation that ensures the transfer of knowledge to the proper functions among the plants in the network. In Case C, the respondents described themselves as beginners in respect of having global production in more than one location. Thus, responsibilities, procedures and ways of collaborating with the subsidiaries were not entirely established at a detailed level. Lack of formalised processes and routines to carry out the lead factory responsibility was mentioned by most of the case companies. In Case F, it was stated difficult to acquire knowledge of the needs of the plants in the network as there was only a limited number of collaboration activities in the global network. Both lead factories were well established locally, but relatively new in their global role. Currently, network activities only take place to a limited extent and fully taking lead factory responsibility was considered difficult, as the subsidiaries work quite independently. In, for example, Cases B and H, there was also a lack of coordination and collaboration between the different lead factories in the company as a whole. This was considered a challenge, especially when a subsidiary had to relate to several lead factories that all worked in different ways. At several of the lead factories, such as G and H, the lack of processes for handling the subsidiaries’ requests for assistance was also apparent. This often took place on an ad hoc basis and to a large extent depended on individuals, as the subsidiaries most often contacted someone they knew at the lead factory, usually, someone they had received assistance from before or that they knew possessed the required skills. Also, in cases where there were actual guidelines for handling requests from subsidiaries, contact was often initially made in an ad hoc way and then subsequently processed through official channels.
One of the main reasons for the lack of formalised processes and structures, and a major challenge to the lead factory operationalisation, in general, is a lack of or insufficient dedicated resources at the lead factory to perform the role. The level to which the lead factory role structure was formalised in the network played a large part in this, but the relationship between having no formal responsibility and no resources and vice versa was not conclusive. As the lead factories had different approaches to where the responsibility lay, for example, at the plant, pilot plant or virtual level, this rather influenced whether or not there were clearly dedicated resources. In Case D, a dedicated department for coordinating the lead factory role was no guarantee of receiving enough dedicated resources, as there was confusion as to where the lead factory responsibility really lay, i.e. at department, site or plant level. The need for, and often the lack of, dedicated resources at the subsidiaries to support global development activities was also considered a challenge. However, at the lead factories, the lack of resources mainly took the form of a challenge in balancing long-term development and daily operations, which made this another major challenge. In Case D, it was difficult to work with long-term production development outside specific new product development projects due to shortages in resources, as well as the absence of a training and development centre at the plant. Even in Case E, in which long-term production development was an explicit lead factory responsibility, this could not be avoided, as there were also demands on the Pilot Plant to carry out serial production, which limited the time it could work on long-term production development. In such cases, the lead factory resources could usually also support serial production at the respective plants hosting the Pilot Plant. Also, because these employees are highly experienced, they are also highly sought after by these plants.
In Case F, the specialists had a limited amount of time dedicated to long-term development work tasks. This could be conflicting as the specialists were also involved in daily operations and had to prioritise between long-term development and the daily needs of the plants. The challenges also involved resource planning. In cases F, G and H it was emphasised that it was hard to prepare and plan for the plant resources if the subsidiaries’ current and future needs were unknown as these change rapidly and also vary over time. In Case H, during the time of the interview, as much as 50% of the resources at the lead factory’s department of process development was currently involved in global support or in development activities.
Having the right types of resources and competencies to execute the lead factory role was also challenging. In Case C, it was not enough to only understand the needs required to build a virtual plant. To be employed at the virtual lead factory, traditional production engineering knowledge of production processes was also necessary to make the most optimal decisions about the future production set-up.
As the majority of the lead factories being studied were responsible for providing support to the subsidiaries, this often resulted in lead factory staff travelling to assist on-site at the subsidiaries on both short and long-term initiatives. Besides this, there were challenges regarding having resources with the right competencies and personalities to spare and also, on a personal level, it had to be someone who was able and willing to do this, as it most often did not form part of that person’s normal job description. Aspects such as personal preferences and family situations were considered to be underestimated as a challenge by, for example, Case companies D, G and H.
Furthermore, the lead factory role could also involve disturbances in the daily operations at the lead factory. In Case D, the training of staff from the entire network was carried out in running operations, which created disturbances and interruptions in the production at the lead factory.
5.5. Management aspects and relationships
In relation to a lack of a mandate, several companies also stated that a strained relationship with management and poor insight into, and influence on, management decisions was a challenge. Many of the lead factories contributed to decision making by preparing a basis for decisions, by offering suggestions or by performing evaluations. When it came to strategic decisions for the network, such as the localisation of development or production activities, investments and purchasing standards, Cases A, D and E found it challenging to not be involved in decision making and wanted a more prominent role in decision making to be able to fulfil their lead factory role. The challenge of not being properly part of decision making appears to be related to a significant geographical distance from the company’s headquarters, as this was the situation in cases where this was highlighted as being problematic. At the lead factories located on the same site as the company’s headquarters, this was not mentioned to the same extent, but instead, there were more often, especially from the subsidiaries difficulties in separating the lead factory from the rest of the site. This could, in some cases, create confusion but also, as in Case H, increasing tension between the sites in the network, as some felt they were being even more overlooked. Several case companies also pointed out the challenge of the lead factory structure or role not being static but changing in line with organisational or management changes. This was, for example, very clear in Case B, where the company had to make organisational changes several times to adjust the lead factory role to suit the new organisation and the new management ideas.
Also, the geographical distance to the R&D department and other central development functions were challenging for the execution of the lead factory role in cases where these were not located at the same site as, for example, in Case C. The virtual lead plant set-up in Case C and the creation of a meeting arena in Case E were measures designed to deal with these geographically distributed networks.
All lead factories being studied (with the partial exception of Case E) were required, apart from their lead factory responsibilities, to maintain an efficient serial production and were compared on the same general production-related KPIs as the other plants. This was viewed by the case companies as being unfair or even unreasonable, particularly as they often had no extra resources to perform the lead factory role. Lead factory activities often took up a substantial part of the lead factory’s resources, which were otherwise only being directed towards improving the performance of its serial production. Also, virtually all of the companies considered it difficult to measure or in other ways show the benefits of the lead factory role and the value it created in the network to warrant lower KPI levels. In particular, one of the main KPIs discussed was cost per produced unit or similar, which is understandably higher in a lead factory that is responsible for resources for the long-term development and global support of the entire network. As expressed in Case F, the company’s global development is financed by the lead factories, and they need to ensure that the competencies and resources are available. Thus, the need for appropriate cost models was strongly emphasised by some, but identifying and/or applying them was considered challenging.
5.6. Summary and ranking of challenges
Based on the analysis, challenges related to the lead factory role and its operationalisation were compiled and listed in a survey. summarises the results showing each companies’ ratings of the most prominent challenges marked X and the five main experienced challenges ranked from 1 to 5 (with 1 being the greatest challenge). The challenges in the table are listed in order of weighted average. The ten highest ranked challenges and their implications are discussed in the next section.
Table 3. Summary and ranking of identified challenges.
6. Discussion and implications
The purpose of this paper was to deepen the understanding of the lead factory role by examining how it is operationalised and what challenges are associated with it. In this section the findings and its implications are discussed and, based on this, possible future research areas have been highlighted as a contribution to the field.
6.1. Need for diverse views on the lead factory concept
In the paper, the applied lead factory set-ups of eight cases are described and summarised in . It can be concluded that the cases strongly differ in regard to how the lead factory role is operationalised and what the lead factory set-up looks like. In these eight cases, the set-ups range from companies that use the entire manufacturing plant as their lead factory, to those that have dedicated physical areas separated from the traditional production plant, to those at which a plant functions as a launch site for new products, to those at which a virtual plant is considered the lead factory. The dimensions and elements identified in earlier research, therefore, appear to be insufficient in covering the entire picture of the lead factory concept, as they do not show the extent to which the concept can be applied. It could also be concluded that there are differences in what the lead factory role involves in terms of the responsibilities associated with it. Few lead factories covered the entire spectrum of responsibilities mentioned by, for example, Ferdows (Citation1997a). This, however, is not surprising as previous studies point out that lead factories can be adapted to certain areas of responsibilities and that there are often several lead factories with different responsibilities in the same network (Feldmann and Olhager Citation2013, Hayes and Schmenner Citation1978). The majority of the lead factories in the study were what Hayes and Schmenner (Citation1978) called ‘product-focused plants’, i.e. the lead factory had been assigned for a certain product segment. As a result, it was responsible for the manufacturing processes related to its product segment and also responsible for the development of these processes. Giving support to subsidiaries also seems to be one of the most common denominators when it comes to lead factory responsibility, but there were also other aspects of responsibilities and different combinations in the cases studied, some of which were not mentioned in previous research, such as creating a meeting arena. Another distinct difference is the extent to which the lead factory role was a formal responsibility or not. It is argued that all the companies in the study are to be considered as lead factories, as they not only assume the role with its associated responsibilities, but also by virtue of the fact that their management and other plants in the network expected them to, even though there was no formalised structure for different plant roles in the network. Also, the non-formally appointed lead factories in the study are expected to play a leading role in development and to provide support to the subsidiaries. This could indicate that the lead factory role and structure is, instead, something that is formed by actions and expectations rather than formal organisational structures. These two findings emphasise the need to expand previous studies of plant roles (Ferdows Citation1997a; Meijboom and Vos Citation2004; Vereecke and Van Dierdonck Citation2002) and to take a multi-dimensional approach when defining site roles in order to provide a more realistic picture that is in line with those of recent studies (Cheng, Farooq, and Johansen Citation2015 and Thomas et al. Citation2015). This could include future studies to identify different lead factory types and concepts.
6.2. Managing the lead factory responsibilities
In the paper, a number of challenges associated with the lead factory role and its operationalisation are described and summarised in . In the following sections, the 10 highest ranked challenges and their implications are discussed.
The highest ranked challenge identified in the study was a lack of dedicated resources, or the right type of resources at the lead factory for lead factory activities. The implications of lack of resources were that serial production and associated development activities at the lead factory were suffering due to the lead plant role demanding a lot of resources, or that it was not possible to fulfil the lead plant responsibility to the desired extent. Few of the case companies were assigned extra or dedicated resources for lead plant activities and regarded this as unfair or impossible to assume the role as there were a lot of responsibilities and activities associated with the lead factory role that demanded extensive resources. By central management, this was often motivated by the lead factory already being the largest plant and therefore having more resources than the other plants. At the lead factories it was also considered hard to balance resources between daily operations and the lead factory-related activities, such as providing support to subsidiaries, as those activities often fluctuated significantly over time and were thus difficult to plan for. The lack of resources was also reflected in – and the main reason for the second highest ranked challenge – the difficulty of balancing long-term development and daily operations. Despite realising the importance of having a long-term perspective and continuously driving new development, it was difficult for the lead plant representatives to realise this in practice as serial production was always prioritised over development activities when resources were scarce. However, this, in turn, was recognised as being a symptom of not having enough dedicated resources for development activities. A basic motivation for the lead factory structure is that the total amount of resources in the network can be reduced if competencies and development activities are concentrated in one place and not redundant or recreated at each plant. For reasons of competitiveness and sustainability, resources should be kept to a minimum. However, for the successful utilisation of the lead plant structure in a production network, it is important to find appropriate levels of resources distributed over the plants and dedicated to different types of activities. Also, the management of lead factories must make it clear what activities should be prioritised.
6.3. Identifying lead factory capabilities and measuring lead factory performance
The third most highly ranked challenge was a difficulty in measuring or showing the benefits created by the lead factory in the network. As evident during the interviews, this is partly related to the fourth ranked challenge of an unclear lead factory role and responsibilities. As it is not clear what is expected of the lead factory and what responsibilities the role entails in practice it is, in turn, also difficult to both act the role and know or show if you are fulfilling it. However, this also partially relates to the seventh most common challenge, the fact that the lead factory is compared on the same KPIs or goals as the other plants and subsidiaries. This created a lot of frustration at the lead factories as they dedicated extensive resources to development activities such as developing new technology or processes. These were after they were properly functioning and fully debugged, with assistance from the lead factory, later implemented at the other plants in the network, which were then able to use the new solutions but without putting in much effort in their development. It is not performing the development work in itself that is considered unfair or problematic but rather the fact that the performance of all plants is only evaluated on KPIs such as cost per part or similar which, of course, is higher for the lead plant if it bears all the costs and resources for development activities, even though it is of benefit to all the plants in the network. So, while it is important to realise that the lead factory role is not static, as the role of offshored sites is likely to be upgraded and entail new capabilities (Adeyemi et al. Citation2014; Feldmann et al. Citation2013; Ferdows Citation1997a, Citation2006), the lead factory role is, and should be, subject to ongoing evaluation. The lead factory must, therefore, be able to motivate its appointment by showing the value it creates in the network. However, as the empirical evidence indicated, the current performance measurement systems do not support this. Being a key player in multiple areas of production development, with a focus on the exploration of future opportunities, while also being judged according to similar KPIs as their subsidiaries, is a struggle for lead factories. Accordingly, there is a risk that critical lead factory capabilities are not being developed and maintained as the role is both unclear and limits the possibility of achieving the network targets set by management. The ability to absorb and learn from others was one capability regarded as critical both in previous research (Bengtsson, Niss, and Von Haartman Citation2010; Tsai, Citation2001) and according to this study. However, there is a need to further investigate what lead factory capabilities are required to execute the role and also to develop and maintain it over time. Further research is proposed both on KPIs related to the lead factory role and its critical capabilities to measure and show its performance as well as on appropriate cost models in order to share the cost of development work that benefits the entire network.
6.4. Defining the lead factory role and how to fulfil it
The empirical evidence indicated that many of the challenges are strongly interrelated with each other and it can be concluded that many originate from uncertainties regarding the lead factory role, responsibilities and mandate as this was considered more or less unclear and problematic in all cases. A clear lead factory role description is necessary, as this would guide the lead factory management in what is required to fulfil the role and also clarify what falls outside it. Based on the role description, guidelines and processes for fulfilling the lead plant responsibilities should also be created as these were most often lacking, as indicated by challenge number six. This is to support the execution of the lead factory role and create value in the network. Clear guidelines and processes could also be a way of overcoming the challenge of putting the benefit of the network before the benefit of own plant if a global rather than a local perspective is adopted to encompass all development work activities. However, in order to create these guidelines and be able to follow them to fulfil the lead factory role, proper and dedicated resources are a necessity.
Also, as indicated by challenge number five, the empirical findings show that many of the subsidiaries work more or less autonomously and the lead factory has the role of an advisor or a supporter rather than having a mandate over the subsidiaries. Furthermore, there was often agreement in the network or a strong desire from the subsidiaries that they should be able to make adjustments in order to respond to the needs of their particular environment and customers. Nevertheless, local adjustments make it difficult for lead factories to control, revise and update central standards that could be shared in the network. Also, previous research has shown the difficulties in finding a balance between the control and autonomy of subsidiaries (Shi Citation2003; Pogrebnyakov and Kristensen Citation2011). More research is therefore required into how to balance this difficulty and, more specifically, how the global perspective can be successfully secured during production development as this is one of the basic motivations behind a lead plant structure: to consolidate development activities at one location to create higher value for the entire network with fewer resources.
6.5. Future research
The sections above have highlighted the managerial implications of the challenges identified and addressed a number of potential areas for further research connected to them. In summary, these areas address further studies on the following: the lead factory role and its responsibilities, particularly different lead factory types and concepts and how they can be realised, KPIs related to the lead factory role and critical capabilities for measuring and showing its performance, cost models to share the cost of development work that benefits the entire network and, finally, how to balance and successfully secure the global perspective during development work.
The findings are not without limitations. The limitations particularly originate in the research method applied. Firstly, the samples of lead factories are located in Sweden and are active in the manufacturing industry. Accordingly, the findings could be of limited use in other contexts. Secondly, while case studies are useful in facilitating the understanding of the phenomenon studied (Voss, Tsikriktsis, and Frohlich Citation2002), the approach applied has been explorative in nature. Therefore, although the generality of the findings is aided by the number and diversity of the cases used, as the cases provide the possibility to show the differences, the results could with benefit be further verified in studies that adopt an even broader empirical base. Thus, a promising avenue for further research is to study the lead factory role in more organisations and in different environments to ascertain whether or not the lead factory set-ups and identified challenges are context specific. However, this study does provide a previously lacking empirical insight into the operationalisation of the lead factory role. Thus, by pursuing a selection of the identified potential research areas, we aspire in the future to even further strengthen the field with academic as well as practical relevance and contributions.
Acknowledgements
The authors gratefully acknowledge the participation and contributions from the case companies that made this work possible.
Disclosure statement
No potential conflict of interest was reported by the authors.
Additional information
Funding
Notes on contributors
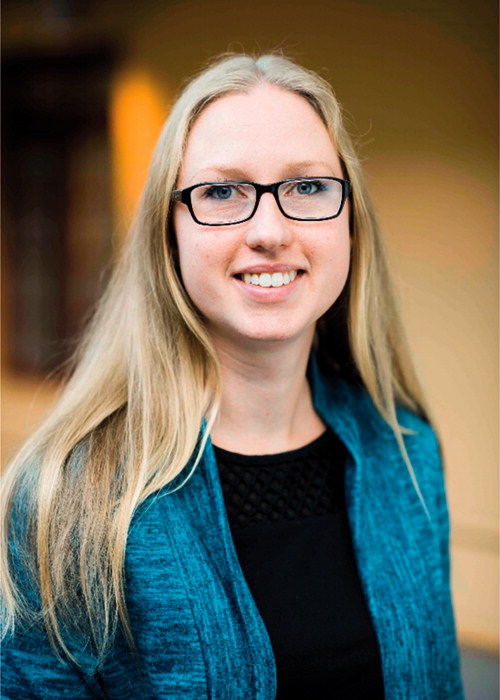
Anna Granlund
Anna Granlund is employed as Senior Lecturer at the division of Product Realisation at Mälardalen University in Sweden. She earned her Ph.D. in Innovation and Design from Mälardalen University in 2014. Anna’s research interest is connected to production system development on global as well as local level and her research is carried out in close collaboration with industry. Her previous research has focused on managing automation development on strategic and operational level. Current research interests include the management of international manufacturing networks, supplier involvement and information handling in manufacturing industry.
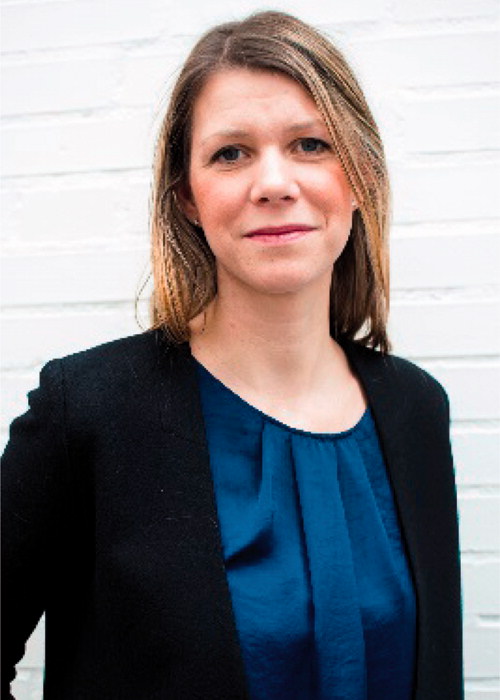
Carin Rösiö
Carin Rösiö is an assistant professor at School of Engineering, Jönköping University in Sweden. She earned a Ph.D. degree in Innovation and Design from Mälardalen University. Her research interest includes production system design within global production networks with a focus on reconfigurability, flexibility and the ability to handle change. The research addresses both technological and organizational aspects related to production system design on a strategic as well as operational level within a company.

Jessica Bruch
Jessica Bruch is a professor in Production Systems at Mälardalen University, Sweden. She holds a M.Sc. in Industrial Engineering and a Ph.D. in Innovation and Design. Her research interest concerns various aspects of production development and addresses both technological and organizational aspects on the project, company and interorganizational level. Current research interests include the management of international manufacturing networks, the fuzzy front end in production development and process development capabilities and strategies. Her research is carried out in close collaboration with industry.
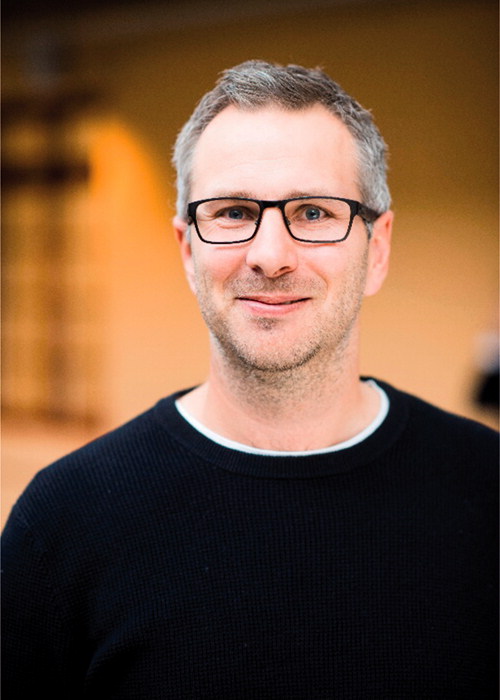
Peter E. Johansson
Peter E. Johansson is associate professor in Innovation science at Mälardalen University in Eskilstuna in Sweden, and part of the research group Workplace Innovation and Quality Management, WIQM. He received his PhD in Education in 2011 at Stockholm University; specialized in the fields of workplace learning, learning organisations and organization pedagogics. Peter has been involved in several research projects, and his current research interests are cross-disciplinary, and positioned in the intersection between operations management and innovation management research.
References
- Adeyemi, O., D. Slepniov, B. Vejrum Waehrens, H. Boer, and X. Wu. 2014. “Exploring the Changing Roles of Western Subsidiaries in China: Balancing Global Priorities with Local Demands.” In International Operations Networks, edited by John Johansen, Sami Farooq and Yang Cheng, 67–80. London: Springer.
- Bartlett, C. A., and S. Ghoshal. 2002. Managing Across Borders: The Transnational Solution. 2nd ed. Boston, MA: Harvard Business School Press.
- Bengtsson, L., and C. Berggren. 2008. “The Integrator’s New Advantage – The Reassessment of Outsourcing and Production Competence in a Global Telecom Firm.” European Management Journal 26 (5): 314–324. doi:10.1016/j.emj.2008.05.001.
- Bengtsson, L., C. Niss, and R. Von Haartman. 2010. “Combining Master and Apprentice Roles: Potential for Learning in Distributed Manufacturing Networks.” Creativity and Innovation Management 19 (4): 417–427. doi:10.1111/j.1467-8691.2010.00578.x.
- Birkinshaw, J. M., and A. J. Morrison. 1995. “Configurations of Strategy and Structure in Subsidiaries of Multinational Corporations.” Journal of International Business Studies 26 (4): 729–753. doi:10.1057/palgrave.jibs.8490818.
- Cantwell, J., and R. Mudambi. 2005. “MNE Competence‐Creating Subsidiary Mandates.” Strategic Management Journal 26 (12): 1109–1128. doi:10.1002/smj.497.
- Cheng, Y., S. Farooq, and J. Johansen. 2011. “Manufacturing Network Evolution: A Manufacturing Plant Perspective.” International Journal of Operations and Production Management 31 (12): 1311–1331. doi:10.1108/01443571111187466.
- Cheng, Y., S. Farooq, and J. Johansen. 2014. “Operations Network Deelopment: Internationalisation and Externalisation of Value Chain Activities.” Production Planning and Control 25 (16): 1351–1369. doi:10.1080/09537287.2013.839064.
- Cheng, Y., S. Farooq, and J. Johansen. 2015. “International Manufacturing Network: Past, Present, and Future.” International Journal of Operations and Production Management 35 (3): 392–429. doi:10.1108/IJOPM-03-2013-0146.
- Colotla, I., Y. Shi, and M. J. Gregory. 2003. “Operation and Performance of International Manufacturing Networks.” International Journal of Operations and Production Management 23 (10): 1184–1206. doi:10.1108/01443570310496625.
- Enright, M. J., and V. Subramanian. 2007. “An Organizing Framework for MNC Subsidiary Typologies.” Management International Review 47 (6): 895–924. doi:10.1007/s11575-007-0057-6.
- Feldmann, A., and J. Olhager. 2013. “Plant Roles: Site Competence Bundles and their Relationships with Site Location Factors and Performance.” International Journal of Operations and Production Management 33 (6): 722–744. doi:10.1108/IJOPM-03-2011-0077.
- Feldmann, A., J. Olhager, and F. Persson. 2009. “Designing and Managing Manufacturing Networks–A Survey of Swedish Plants.” Production Planning and Control 20 (2): 102–109. doi:10.1080/09537280802705252.
- Feldmann, A., J. Olhager, D. Fleet, and Y. Shi. 2013. “Linking Networks and Plant Roles: The Impact of Changing a Plant Role.” International Journal of Production Research 51 (19): 5696–5710. doi:10.1080/00207543.2013.778429.
- Ferdows, K. 1989. “Mapping International Factory Networks." In Managing International Manufacturing, edited by Kasra Ferdows, 3–21. Amsterdam: Elsevier Science Publishers.
- Ferdows, K. 1997a. “Making the Most of Foreign Factories.” Harvard Business Review 75 (2): 73–88. doi:10.1225/97204
- Ferdows, K. 1997b. “Made in the World: The Global Spread of Production.” Production and Operations Management 6 (2): 102–109. doi:10.1111/j.1937-5956.1997.tb00418.x
- Ferdows, K. 2006. “Transfer of Changing Production Know‐How.” Production and Operations Management 15 (1): 1–9. doi:10.1111/j.1937-5956.2006.tb00031.x.
- Frost, T. S., J. M. Birkinshaw, and P. C. Ensign. 2002. “Centers of Excellence in Multinational Corporations.” Strategic Management Journal 23 (11): 997–1018. doi:10.1002/smj.273
- Hayes, R. H., and R. W. Schmenner. 1978. “How Should You Organize Manufacturing?” Harvard Business Review 56 (1): 105–118.
- Hayes, R. H., and S. C. Wheelwright. 1979. “Link Manufacturing Process and Product Life Cycles.” Harvard Business Review 57 (1): 133–140.
- Hogenbirk, A. E., and H. L. van Kranenburg. 2006. “Roles of Foreign Owned Subsidiaries in a Small Economy.” International Business Review 15 (1): 53–67. doi:10.1016/j.ibusrev.2005.09.005.
- Jaehne, D. M., M. Li, R. Riedel, and E. Mueller. 2009. “Configuring and Operating Global Production Networks.” International Journal of Production Research 47 (8): 2013–2030. doi:10.1080/00207540802375697.
- Jarillo, J. C., and J. I. Martíanez. 1990. “Different Roles for Subsidiaries: The Case of Multinational Corporations in Spain.” Strategic Management Journal 11 (7): 501–512. doi:10.1002/smj.4250110702.
- Maritan, C. A., T. H. Brush, and A. G. Karnani. 2004. “Plant Roles and Decision Autonomy in Multinational Plant Networks.” Journal of Operations Management 22 (5): 489–503. doi:10.1016/j.jom.2004.05.007.
- Meijboom, B., and B. Vos. 2004. “Site Competence Dynamics in International Manufacturing Networks: Instrument Development and a Test in Eastern European Factories.” Journal of Purchasing and Supply Management 10 (3): 127–136. doi:10.1016/j.pursup.2004.09.001.
- Merriam, S. B. 1998. Qualitative Research and Case Study Applications in Education. 2nd ed. San Francisco, CA: Jossey-Bass.
- Miltenburg, J. 2009. “Setting Manufacturing Strategy for a Company’s International Manufacturing Network.” International Journal of Production Research 47 (22): 6179–6203. doi:10.1080/00207540802126629.
- Nassimbeni, G., and M. Sartor. 2005. “The Internationalization of Local Manufacturing Systems: Evidence from the Italian Chair District.” Production Planning and Control 16 (5): 470–478. doi:10.1080/09537280500110912.
- Pogrebnyakov, N., and J. D. Kristensen. 2011. “Building Innovation Subsidiaries in Emerging Markets: The Experience of Novo Nordisk.” Research-Technology Management 54 (4): 30–37.
- Porter, M. E., and J. W. Rivkin. 2012. “Choosing the United States.” Harvard Business Review 90 (3): 81–93.
- Prajogo, D. I., and A. S. Sohal. 2004. “Transitioning from Total Quality Management to Total Innovation Management: An Australian Case.” International Journal of Quality and Reliability Management 21 (8): 861–875. doi:10.1108/02656710410551746.
- Reichwald, R., C. M. Stotko, and S. Seifert. 2003. “Internationalizing Mass Customization – Minifactories as a Transnational Solution.” In Proceedings of the 2nd Interdisciplinary World Congress on Mass Customization and Personalization, October 6–8, Munich.
- Riis, J. O., J. Johansen, B. Vejrum Waehrens, and L. Englyst. 2007. “Strategic Roles of Manufacturing.” Journal of Manufacturing Technology Management 18 (8): 933–948. doi:10.1108/17410380710828262.
- Rudberg, M., and J. Olhager. 2003. “Manufacturing Networks and Supply Chains: an Operations Strategy Perspective.” Omega 31 (1): 29–39. doi:10.1016/S0305-0483(02)00063-4.
- Rudberg, M., and B. M. West. 2008. “Global Operations Strategy: Coordinating Manufacturing Networks.” Omega 36 (1): 91–106. doi:10.1016/j.omega.2005.10.008.
- Rugman, A. M., and A. Verbeke. 2001. “Subsidiary‐Specific Advantages in Multinational Enterprises.” Strategic Management Journal 22 (3): 237–250. doi:10.1002/smj.153.
- Saunders, M., P. Lewis, and A. Thornhill. 2012. Research Methods for Business Students. 6th ed. Harlow, UK: Pearson.
- Shi, Y. 2003. “Internationalisation and Evolution of Manufacturing Systems: classic Process Models, New Industrial Issues, and Academic Challenges.” Integrated Manufacturing Systems 14 (4):357–68. doi:10.1108/09576060310469734.
- Shi, Y., and M. Gregory. 1998. “International Manufacturing Networks – To Develop Global Competitive Capabilities.” Journal of Operations Management 16 (2-3): 195–214. doi:10.1016/S0272-6963(97)00038-7.
- Slepniov, D., B. V. Waehrens, and J. Johansen. 2014. “Dynamic Roles and Locations of Manufacturing: Imperatives of Alignment and Coordination with Innovation.” Journal of Manufacturing Technology Management 25 (2): 198–217. doi:10.1108/JMTM-10-2013-0142.
- Søndergaard, E., J. Oehmen, and S. Ahmed-Kristensen. 2016. “Extension of Internationalisation Models: Drivers and Processes for the Globalisation of Product Development – A Comparison of Danish and Chinese Engineering Firms.” Production Planning and Control 27 (13): 1112–1123. doi:10.1080/09537287.2016.1186849.
- Thomas, S., M. Scherrer-Rathje, M. Fischl, and T. Friedli. 2015. “Linking Network Targets and Site Capabilities: A Conceptual Framework to Determine Site Contributions to Strategic Manufacturing Network Targets.” International Journal of Operations and Production Management 35 (12): 1710–1734. doi:10.1108/IJOPM-10-2014-0464.
- Tsai, W. 2001. “Knowledge Transfer in Intraorganizational Networks: Effects of Network Position and Absorptive Capacity on Business Unit Innovation and Performance.” Academy of Management Journal 44 (5): 996–1004. http://www.jstor.org/stable/3069443.
- Vereecke, A., and R. Van Dierdonck. 2002. “The Strategic Role of the Plant: Testing Ferdows’s Model.” International Journal of Operations and Production Management 22 (5): 492–514. doi:10.1108/01443570210425147.
- Vereecke, A., R. Van Dierdonck, and A. De Meyer. 2006. “A Typology of Plants in Global Manufacturing Networks.” Management Science 52 (11): 1737–1750. doi:10.1287/mnsc.1060.0582.
- Voss, C., N. Tsikriktsis, and M. Frohlich. 2002. “Case Research in Operations Management.” International Journal of Operations and Production Management 22 (2): 195–219. doi:10.1108/01443570210414329.
- Yin, R. K. 2009. Case Study Research: Design and Methods. 4th ed. Thousand Oaks, CA: SAGE.