Lean thinking was proposed by Womack and Jones (Citation1996) as an interpretation of the way Toyota was successfully approaching its production system. The body of knowledge around the lean philosophy has been built over the years by practitioners and scholars from around the world and an interesting example of a conceptual model of lean tools and principles was proposed by Hodge et al. (Citation2011). The implementation of lean principles, concepts and tools is quite popular in many types of organisation around the world but not always with success (Negrão, Godinho Filho, and Marodin Citation2017). Lean training is referred to frequently in the literature as playing an important role in the success of lean implementation and in continuous improvement programmes. Shrimali and Soni (Citation2017) reported that one of the limitations observed for successful implementations of lean in SMEs was the poor training. Another study (Netland Citation2016) shows that after management commitment and involvement comes training, and education as the most commonly reported critical success factor in the improvement programme literature. Similar results were also reported by Yamchello et al. (Citation2014).
Lean in education and training can be divided into two distinctive areas of knowledge and work. One area can be called Lean Teaching and the other area can be called Teaching Lean. The Teaching Lean area can be described as the way students and professionals can be effectively trained on Lean principles, concepts and tools so they can apply Lean in real contexts such as factories and other organisations. This area is quite a large subject with fast growing interest in recent years. The other area, Lean Teaching, can be described as how lean principles and concepts can be effectively applied in learning/training activities. There is a very interesting book on the subject published by Emiliani (Citation2015) but this subject remains little explored by academic authors with very few articles published. Another closely-related area sometimes with confusing interpretation as Lean Teaching is the use of lean in schools and universities. In these cases the use of Lean is mainly applied in offices and other service areas that exist in academic organisations.
The Lean philosophy can be described as having two main sides: the visible side of Lean and the invisible side of Lean. The visible part is mainly related to the “Just In Time” and “Jidoka” pillars of the Toyota Production System (TPS), (Ohno Citation1988) while the invisible part is related to the second of the two key basic concepts of TPS “…treat the workers as human beings and with consideration” (Sugimori et al. Citation1977). The visible part of lean is quite easy to grasp and teach with help of games and simulations (Bicheno Citation2015) and normally some success is achieved. The main challenges for lean educators are first of all to fully understand this invisible part of Lean and then how to coach managers and organisations leaders so they understand and apply these concepts in their organisations. This invisible part of lean is almost impossible to implement without the commitment of the top leader in the organisation. That is the reason why the main challenge for lean educators is to find a way of attracting top managers for training in this invisible part of lean.
Lean Teaching, also called Lean Training, is gaining popularity very fast both in university courses as well as in training practitioners in companies. The need to involve all employees and managers in continuous improvement processes with lean vision requires ways of training that effectively change the routines and culture in a company. One popular concept that must be addressed here is the concept of the Learning Factory that can be described as an environment that closely reproduces a manufacturing process with its production conditions, which facilitates problem- and action-oriented learning (Abele Citation2016). The Learning factory is a very effective tool in improving the effectiveness of Lean Training both in academic environments as if in a real context.
University-Industry Collaboration (UIC) can be an effective platform to support Lean teaching and training for the benefit of students, professionals and consequently the economy and society. UIC can be classified in the following way (Ankrah and AL-Tabbaa Citation2015): (1) research support, (2) cooperative research, (3) knowledge transfer and (4) technology transfer. In UIC context the lean education can be included in the knowledge transfer class where knowledge can be transferred both ways and new knowledge can be created from this type of collaboration. An interesting example of university-industry collaboration with lean education is putting student teams in a real industry context by trying to solve problems and implement improvement actions using principles, concepts and lean tools (Lima et al. Citation2017). In this example the companies where students carry out their projects benefit from new solutions and new ways of looking at their problems while students effectively develop lean competencies in real context.
Another important tool that is explored in this special issue is the use of gaming and simulation in teaching lean and training. Lean games and simulations can be viewed as a lighter version of learning factory and are also very effective in helping trainees in capturing lean concepts and principles with the advantage of being applied in a normal classroom.
This special issue collects relevant work addressing the way lean training and learning is related to lean implementation success and in the sustainability of lean programmes. It also identifies some alignment of the objectives of the lean community players such as managers and facilitators in organisations with consultants, teachers and researchers in their common role as lean educators.
The organisation and management model that emerged from the Toyota Production System in many different forms and designations, here called Lean philosophy, although having a great potential in improving the performance of organisations and the quality of life of their employees, still calls for much to be done. Lean Educators play an important role in this process but for many reasons they are still failing in giving their learners the necessary skills to help organisations in implementing this philosophy with success. One of the problems is that in many educational institutions as other types of organisations the existing management and leadership culture is not yet prepared to accept Lean type philosophies. In other words most organisations are not open to the necessary participation and commitment of every employee in the problem solving and local management decision responsibilities that is supposed to exist in effective continuous improvement environments. Lean educators in many educational institutions are trying to teach Lean principles, concepts and tools in an environment where most of those principles and concepts are yet to be implemented. The main reason is that the managers/leaders in their institutions have yet to understand the potential benefits that their institutions could gain from this management philosophy. Most teachers in management and engineering schools have yet to understand the potential of this philosophy when effectively applied in different organisations as well as in the effectiveness of the education itself. We hope the papers presented here from a range of international researchers will go some way to help develop the field of Lean Training.
Disclosure statement
No potential conflict of interest was reported by the author(s).
Additional information
Funding
Notes on contributors
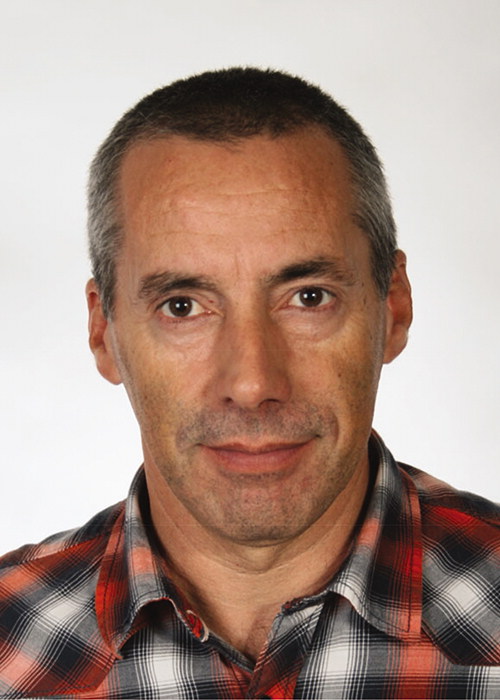
José Dinis-Carvalho
José Dinis-Carvalho is an Associate Professor at the University of Minho. Degree in Production Engineering in 1989 at the University of Minho. MSc in Computer Integrated Manufacturing in 1992 at Loughborough University. Ph.D. at the University of Nottingham in 1997 on Scheduling and Process Planning Integration. Main research interests are in Lean Approaches to any type of operating environment such as industry, hospitals, construction, offices, design, teaching, etc.. Stable and Sustainable Continuous Improvement systems is one of the main focus at the moment. Other research interests are Teamwork, Scrum and Active Learning approaches in engineering education.
References
- Abele, E. 2016. “Learning Factory.” In CIRP Encyclopedia of Production Engineering, edited by The International Academy for Produ, L. Laperrière, and G. Reinhart, 1–5. Berlin, Heidelberg: Springer Berlin Heidelberg.
- Ankrah, S., and O. Al-Tabbaa. 2015. “Universities-Industry Collaboration: A Systematic Review.” Scandinavian Journal of Management 31 (3): 387–408. doi:10.1016/j.scaman.2015.02.003.
- Emiliani, B. 2015. Lean Teaching: A Guide to Becoming a Better Teacher. Wethersfield, CT: The CLBM.
- Hodge, G. L., K. Goforth Ross, J. A. Joines, and K. Thoney. 2011. “Adapting Lean Manufacturing Principles to the Textile Industry.” Production Planning & Control 22 (3): 237–247. doi:10.1080/09537287.2010.498577.
- Bicheno, John. 2015. The Lean Games and Simulations Book. Picsie Books.
- Lima, R. M. M., J. Dinis-Carvalho, R. M. M. Sousa, P. Arezes, and D. Mesquita. 2017. “Development of Competences While Solving Real Industrial Interdisciplinary Problems: A successful Cooperation with Industry.” Producao 27. doi:10.1590/0103-6513.230016.
- Negrão, L. L. L., M. Godinho Filho, and G. Marodin. 2017. “Lean Practices and Their Effect on Performance: A Literature Review.” Production Planning & Control 28 (1): 33–56. doi:10.1080/09537287.2016.1231853.
- Netland, T. H. 2016. “Critical Success Factors for Implementing Lean Production: The Effect of Contingencies.” International Journal of Production Research 54 (8): 2433–2448. doi:10.1080/00207543.2015.1096976.
- Ohno, T. 1988. “Toyota Production System.” International Journal of Operations and Production Management 4 (1): 3–11. doi:10.1108/eb054703.
- Shrimali, A. K., and V. K. Soni. 2017. “A Review on Issues of Lean Manufacturing Implementation by Small and Medium Enterprises.” International Journal of Mechanical and Production Engineering Research and Development 7 (3): 283–300. doi:10.24247/ijmperdjun201729.
- Sugimori, Y., K. Kusunoki, F. Cho, and S. Uchikawa. 1977. “Toyota Production System and Kanban System Materialization of Just-in-Time and Respect-for-Human System.” International Journal of Production Research 15 (6): 553–564. doi:10.1080/00207547708943149.
- Womack, J., and D. Jones. 1996. Lean Thinking: Banish Waste and Create Wealth in Your Corporation. New York: Free Press. ISBN: 0-7432-4927-5
- Yamchello, H. T., R. Samin, A. Tamjidyamcholo, P. Bareji, and A. Beheshti. 2014. “A Review of the Critical Success Factors in the Adoption of Lean Production System by Small and Medium Sized Enterprises.” Applied Mechanics and Materials 564 (June): 627–631. doi:10.4028/www.scientific.net/AMM.564.627.