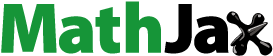
Abstract
Among the main fault locations of wind turbines, downtime accidents caused by bearing faults account for the majority. Therefore, it is of practical significance to detect the fault signal of the fan bearing as early as possible, and to arrange the maintenance plan reasonably, which is of practical significance to reduce the maintenance cost and increase the power generation time. Therefore, this paper proposes an early fault vibration detection and analysis model for wind power transmission based on deep neural networks and sensors. First of all, this paper studies the failure mechanism, vibration mechanism and signal characteristics of common failures of rolling bearings, combined with sensor technology, summarises and designs various bearing failures and failure signal detection models. Secondly, the deep neural network algorithm is used for the interference situation of rolling bearing vibration signal and the process of data re-analysis. The experimental and simulation results verify the adaptability of the early fault vibration detection model of wind power transmission in the early fault processing results, which can provide a reference for the early weak fault signal processing of wind turbine bearings.
1. Introduction
As a clean, renewable, and widely distributed new energy source, wind energy is gradually being developed and utilised to a certain extent, attracting more and more attention from various countries. With the development of wind power, wind farms are increasing day by day (Abdel-Khalik et al., Citation2013; Egea-Alvarez et al., Citation2013). The poor operating conditions of wind turbines and the complex and changeable loads make the unit failure rate high, resulting in low wind turbine utilisation and utilisation hours, and high operation and maintenance costs (Farahmand et al., Citation2015). With the increasing share of wind power in the power market and the steady increase in the single-unit capacity of wind turbines, failures and shutdowns of wind turbines will have a greater impact on grid security and the national economy, and improve the reliability and efficiency of wind power generation. There is no time to delay (Gorman et al., Citation2019; Paula et al., Citation2020; Ruddy et al., Citation2016). However, the current maintenance of wind farms generally adopts regular maintenance and fault maintenance methods. Such maintenance is difficult to comprehensively and timely understand the operation status of the equipment, which often results in long-term maintenance absenteeism and heavy losses (Elmitwally et al., Citation2016; Pang & Guo, Citation2019). In order to reduce the cost of wind power operation and maintenance, a new maintenance method has received extensive attention. Condition monitoring and fault diagnosis of wind turbines can ensure the safe operation of the wind turbines and improve the economy and market competitiveness of wind power.
As the carrier of the fault characteristic information of the transmission chain, the vibration signal can effectively reflect most of the fault information of the transmission chain of the wind turbine (Garg & Dahiya, Citation2016; Kocewiak et al., Citation2019; Rahmann & Palma-Behnke, Citation2013). Xiang J used the SCADA signal including vibration, temperature, power, and other signals and the power, speed, and wind speed signals sampled at the intermediate frequency as the basis, and applied Morlet wavelet transform, FFT and RMS technology to predict the transmission chain of wind turbines. (Xiang et al., Citation2009). In addition, based on the statistics and energy analysis of discrete wavelet transform, related scholars have realised the fault detection of the wind turbine transmission chain by monitoring the stator current of the doubly-fed wind turbine. In addition, other scholars based on a variety of data mining techniques, based on the measured signals of S CADA to predict the fault, and divided the judgment results into three progressive fault severity levels for warning (Haehne et al., Citation2018; Hong et al., Citation2018).
The above research results show that the introduction of the signal sparse decomposition method provides a new and effective method for the extraction of wind power transmission fault characteristics (Du et al., Citation2019; Li et al., Citation2017; Vargas et al., Citation2015). However, what we need to know is that although many sparse decomposition algorithms have been successfully applied to the process of wind power transmission fault feature extraction, some research on this aspect is still at the primary level (Chen et al., Citation2020; Purwins et al., Citation2019). Therefore, it is necessary to use other methods to realise the separation and extraction of wind power transmission composite fault characteristics (Ning et al., Citation2020; Ning et al., Citation2021; Zhang et al., Citation2021). Therefore, it is of practical significance to detect the fault signal of the fan bearing as early as possible and arrange the maintenance plan reasonably, which is of practical significance to reduce the maintenance cost and increase the power generation time. In recent years, deep neural network has been widely used in face recognition (Wang et al., Citation2019; Yan et al., Citation2021), person re-identification (Bai et al., Citation2021; Wang et al., Citation2020), sensing image recognition (Du et al., Citation2020; You et al., Citation2021), three-dimensional vision (Cai et al., Citation2021; Ugranli et al., Citation2016) and so on. Therefore, this paper proposes an early fault vibration detection and analysis model for wind power transmission based on deep neural networks and sensors. Before the failure occurs, the failure failure will have some corresponding weak signs (Bai et al., Citation2017; Mehrabi et al., Citation2019; Zhang et al., Citation2016). If online monitoring can be used to find the corresponding method to find the weak signs of the early failure of the gearbox, the maintenance and replacement of the gearbox will be avoided, and the economic benefits of the wind farm will be improved.
2. Sensor-based vibration detection of wind power transmission
Rolling bearing has the advantages of high transmission efficiency, low friction resistance, convenient assembly, and easy lubrication. It is one of the main components of wind power transmission. During operation, rolling bearings will be affected by various factors such as load, installation conditions, lubrication status, etc., so that various failures will occur after a period of use (Wu et al., Citation2019). Rolling bearings are a relatively weak component in the work of rotating machinery. Especially when the load of wind turbines is constantly changing and working conditions are bad, bearing failures are more frequent. In the initial stage of bearing failure, the degree of failure is relatively small, has no effect on the operation of the work, and is not easy to be found (DaR et al., Citation2020; Qi et al., Citation2021).
Compared with other fault diagnosis methods, the vibration of the gearbox is currently recognised as the best extraction of fault signs, which can quickly and comprehensively reflect the nature and scope of most gears, rolling bearings and shafting faults, and there are many advanced analyses (Chandra & Rolland, Citation2015; Davila-Chacon et al., Citation2015). The main basis of the vibration method is to analyze according to the frequency spectrum characteristics of the vibration signal, detect whether there are certain specific frequencies, and then determine whether a certain type of fault or vibration component occurs (Aragon-Calvo, Citation2019; Dong et al., Citation2019). For gears, these specific frequencies are called the characteristic frequencies of the gears. The characteristic frequency of the gear mainly includes the meshing frequency and the failure frequency of the gears at all levels, and the input speed of the frequency is related to the specific structure of the gear. Therefore, this article uses sensors to detect the vibration signal (Song et al., Citation2021). Figure shows a schematic diagram of the monitoring structure of a wind power transmission vibration sensor.
For the condition monitoring of the transmission chain of wind turbines, effectively obtaining suitable monitoring signals is a prerequisite for correctly judging the equipment operating conditions (Hb & Na, Citation2020). The correct acquisition of the vibration signal of the monitoring point involves many factors such as the location of the monitoring point and the selection and installation of sensors (Lu et al., Citation2014; Mendez et al., Citation2019). Figure shows a schematic diagram of the specific structure of a doubly-fed wind turbine sensor with a “one planet, two parallel” structure gearbox.
Among the large-capacity grid-connected wind turbines that have been put into production, horizontal-axis, three-bladed, upwind, and doubly-fed wind turbines still occupy a dominant position, which is also the mainstream technology of international wind turbines (Chakraborty et al., Citation2021; Zhao et al., Citation2020). Doubly-fed wind turbines usually use gearboxes to achieve power transmission between wind turbines and generators. The transmission system mainly includes blades, wheels, main shaft (low-speed shaft), gearbox, high-speed shaft, and generator (Song et al., Citation2021; Xue et al., Citation2016). The flexible characteristics of the above components will cause the unit to produce torque oscillations in the transient process, thereby affecting the operation and life of the transmission components. Therefore, the research on the transient operating performance of the grid-connected doubly-fed wind turbine and the flexible equivalent model of the transmission chain appears to be very important (Chapain & Aly, Citation2021; Zhou et al., Citation2019). The sensors in the vibration monitoring system are distributed on the transmission chain of the wind turbine, and the collected vibration signals are transmitted to the collection module. The acquisition module transmits the signal to the field server through the optical fibre, and the server transmits to the remote diagnosis centre through the Internet (Chen & Ahn, Citation2020). The distribution positions of sensors on different transmission structures are different.
3. Vibration signal processing based on deep neural network
3.1. Vibration characteristics of wind power system
Doubly-fed wind turbines still occupy a dominant position in large-scale wind turbines. The gearbox of the horizontal-axis three-blade doubly-fed wind turbine connected to the wind turbine and the doubly-fed generator provides a suitable transformation ratio for the speed of the two (Chen et al., Citation2020). The stator of the doubly-fed generator is directly connected to the grid through the transformer, and the rotor through the back-to-back double The PWM converter is connected to the grid. This chapter establishes the coordinate system shown in Figure below, where OP is the catenary, the origin O is the starting point of the catenary, the X-axis direction is the horizontal direction in the catenary plane, and the Y-axis direction is the vertical direction. Figure shows the schematic diagram of the force analysis of the gear node.
The force analysis of the OP segment catenary is carried out, and the force balance equation is obtained:
(1)
(1)
Among them, is the thread tension, so
.
(2)
(2)
Among them, is the line density of the line, that is, the mass per unit length of the line. Therefore,
(3)
(3)
The inner ring of the bearing of the planetary gear train is fastened to the shaft of the planetary gear, while the outer ring is closely matched with the planetary gear and moves together with the planetary gear. Therefore, during the operation of the planetary gearbox, the inner ring of the bearing only revolves around the sun gear axis with the planet carrier. The bearing cage and the outer ring of the bearing not only revolve with the planet carrier, but also rotate with the planet wheel around the axle of the planet. The moving drum of the bearing rolling elements is complicated.
(4)
(4)
The wind speed is intermittent and random, so the aerodynamic torque acting on the three blades of the wind turbine is often different. However, in the previously discussed models, only the six-mass model can simulate and analyze the unbalanced aerodynamic torque distribution of the blades. The reliability of the low-level model will be greatly compromised. Figure shows a schematic diagram of the force analysis of the wheel hub.
Analyze the force on the section line and get the force balance equation:
(5)
(5)
Expand to get:
(6)
(6)
(7)
(7)
At the same time, we can see that the system parameters will affect the best signal-to-noise ratio of stochastic resonance. Only when the system parameters reach a certain state of coordination with noise and weak signals, the global best stochastic resonance will occur, and the noise reduction effect at this time is the most ideal. If the unbalanced aerodynamic torque distribution has a great influence on the transient response of the wind turbine, it is less than the six-mass model.
(8)
(8)
Where .
In the end:
(9)
(9)
Since the outer ring of the planetary wheel rotates with the planetary wheel, when the outer ring of the planetary wheel bearing has a local failure, the position of the fault point relative to the planet carrier changes with the rotation of the outer ring. At this time, the load distribution intensity at the damage point and the direction of the gear meshing force will also change, which will have an amplitude modulation effect on the vibration signal.
3.2. Vibration signal processing
The characteristic of a deep belief network is that each layer of it captures the complex hidden nodes associated with higher commands in the layer below it. The Deep Boltzmann machine is very interesting in many ways. First of all, like deep belief networks, deep Boltzmann machines have the potential to learn more and more complex statements inside the model, which is a very promising way to solve problems such as objective things and speech recognition. Secondly, the in-depth statement can be from a large supply of unrepresented sensory input data and very limited data that has been identified, and these data can only be slightly changed later, a good model is established, and then go immediately Complete some special tasks. The most fundamental feature of a deep neural network is its own topological organisation. The weight update of the neurone subset formed by topological correlation is very similar. In addition, the neurones in the subset derived from the learning process are also different. Figure depicts the signal-to-noise ratio as a function of noise intensity.
It can be seen from Figure that in the second-order stochastic resonance system, no matter how the system parameter a changes, the change trend of the signal-to-noise ratio of the first-order stochastic resonance system with the noise intensity is consistent. The signal-to-noise ratio will first increase with the increase of the noise intensity, that is, the stochastic resonance phenomenon occurs at this time, and then the best stochastic resonance under this set of parameters is reached. Among the large-capacity grid-connected wind turbines that have been put into production, horizontal-axis, three-bladed, upwind, and doubly-fed wind turbines still occupy a dominant position, which is also the mainstream technology of international wind turbines. So the improved system model can theoretically generate stochastic resonance. System parameters will affect the best signal-to-noise ratio of stochastic resonance. When the system parameters reach a certain state of coordination with noise and weak signals, the global best stochastic resonance will occur, and the noise reduction effect at this time is the most ideal. Therefore, when the noise and signal are constant in practical applications, the maximum noise reduction effect can be achieved by adjusting the parameters of the stochastic resonance system. The following simulation compares the detection effects of the first-order stochastic resonance system and the improved second-order stochastic resonance system.
4. Verification of actual case of wind power transmission
Vibration signal is the carrier of fault characteristic information of the transmission chain of offshore wind turbines, and can effectively reflect most of the fault information of the transmission chain of wind turbines. Analyzing and processing vibration signals to extract fault information is the basis and key of fault diagnosis for the transmission chain of wind turbines. This chapter mainly focuses on simulation test research on vibration signal processing and fault diagnosis methods.
The wave load is the main source of the disturbance force that the mooring system receives during the working process. The mooring system will produce more complex motions under the excitation of wave loads, and the load it receives during the work process changes dynamically. In this paper, the design wave method is adopted, the wave height and wave period are selected through the working environment, the wave force is calculated by the hydrodynamic method, and the mooring system is analyzed in the time domain.
Regardless of the ocean current factor, taking the velocity potential of the deep-water travelling wave, the velocity and acceleration of the two-dimensional flow field caused by the wave are:
(23)
(23)
In the formula, a——wave amplitude; ω——angular frequency; k——wave number, k = 2π/L, L is the wavelength.
Normally, the wave period is mostly 6-12s, and the wavelength ranges from tens to hundreds of metres. In the numerical simulation, take a = 0.5 m, w = 0.628 rad/s, L = 20 m, k = 0.314. Using wave theory, after obtaining the velocity of the velocity field, the drag force calculation formula can be obtained:
(24)
(24)
The wave force received by the surface buoy in the travelling wave is slightly different from the force received by the components below the water surface. The surface buoy is subjected to wave pressure in the vertical direction and drag force of the water current in the horizontal direction. he bearing cage and the outer ring of the bearing not only revolve with the planet carrier, but also rotate with the planet wheel around the axle of the planet. Among them, the calculation formula of wave pressure is:
(25)
(25)
In the formula, is the area of the bottom of the buoy; y is the ordinate of the bottom of the buoy.
The wind speed is intermittent and random, so the aerodynamic torque acting on the three blades of the wind turbine is often different. However, in the previously discussed models, only the six-mass model can simulate and analyze the unbalanced aerodynamic torque distribution of the blades. The unbalanced aerodynamic torque distribution has a great influence on the transient response of the wind turbine, and the reliability of the low-level model will be greatly reduced. Therefore, based on the six-mass model, a comparative study of the transient response of the wind turbine transmission chain under balanced and unbalanced aerodynamic torque is carried out, and the four-mass model is combined to investigate the feasibility of replacing the high-order model with a low-order model. Set simulation conditions: a three-phase grounding short circuit occurs at the output of the doubly-fed generator in 0.5 s, and the fault is removed after 0.25 s. During operation, rolling bearings will be affected by various factors such as load, installation conditions, lubrication status, etc., so that various failures will occur after a period of use. The simulation results are applied to Lun Yi’s wind turbine to synthesise aerodynamic torque and main shaft (low-speed shaft) torque and high-speed shaft torque. Figure shows the effect of unbalanced torque distribution on the transmission response of the unit.
It can be seen from Figure that the torque curves output by the six-mass model or the four-mass model under balanced and unbalanced aerodynamic torque basically overlap and coincide. This means that the unbalanced aerodynamic torque distribution has little effect on the transient operating performance of the six-mass transmission chain model, and it is assumed that the synthetic aerodynamic torque of the wind turbine acting on Lun Yi is equal to three acting on the blades. Since the buoy is above the sea surface for a long time, the load of wind, waves and currents is greater than that of other parts, so the buoy is the research object. Under the premise of total aerodynamic torque, it is reasonable to replace the six-mass model with a reduced-order four-mass model, thereby simplifying the simulation model and improving the simulation efficiency.
The drag force of the buoy under the excitation of the regular wave fluctuates, the tension is zero at some moments, and the tension value at some moments is greater than 25000N, indicating that the anchor chain will relax-the change of tension state, resulting in greater impact tension, this phenomenon It is easy to cause fatigue damage of the anchor chain and shorten the service life of the system. The main basis of the vibration method is to analyze according to the frequency spectrum characteristics of the vibration signal, detect whether there are certain specific frequencies, and then determine whether a certain type of fault or vibration component occurs. The response image of the pressure wave shows that under the determined wave excitation, the system will produce a certain attitude deviation in the horizontal and vertical directions. After reaching the maximum deviation position, the buoy makes approximately simple harmonic motion in the longitudinal direction. That is, the draft of the buoy will fluctuate up and down within the predicted range, and the floating value is less than 0.01 m.
5. Conclusion
Vibration monitoring and fault diagnosis of wind turbines are of vital importance to the normal operation of wind turbines. At present, although the importance of wind turbine vibration monitoring and fault diagnosis technology has attracted the attention of wind power equipment manufacturers and operators, there are still technical problems in practical applications. Therefore, this paper proposes an early fault vibration detection and analysis model for wind power transmission based on deep neural networks and sensors. The experimental and simulation results verify the adaptability of the early fault vibration detection model of wind power transmission in the early fault processing results, which can provide a reference for the early weak fault signal processing of wind turbine bearings. Aiming at the problems in wind turbine transmission chain vibration monitoring and fault diagnosis, this paper studies the morphological filtering signal processing method combined with EMD decomposition for anti-electromagnetic interference, and the cyclic coherence method for extracting gearbox bearing fault features combined with cestrum editing. There is also a fault feature quantification method based on SOM neural network and Kalman filtering. Although the above methods have achieved certain practical results, the limitations of the research content and methods lead to some content that needs to be improved and studied in depth in this article. How to find out the cause of vibration signal fluctuation and eliminate the fluctuation can be the content of follow-up research.
Disclosure statement
No potential conflict of interest was reported by the author(s).
References
- Abdel-Khalik, A., Massoud, S., & Ahmed, M. (2013). Optimum power transmission-based droop control design for multi-terminal hvdc of offshore wind farms. IEEE Transactions on Power Systems, 28(3), 3401–3409. https://doi.org/10.1109/TPWRS.2013.2238685
- Aragon-Calvo, M. A. (2019). Classifying the large-scale structure of the universe with deep neural networks. Monthly Notices of the Royal Astronomical Society, 484(4), 5771–5784. https://doi.org/10.1093/mnras/stz393
- Bai, L., Li, F., Jiang, T., & Jia, H. (2017). Robust scheduling for wind integrated energy systems considering gas pipeline and power transmission n-1 contingencies. IEEE Transactions on Power Systems(2), 1–1. https://doi.org/10.1109/TPWRS.2016.2582684
- Bai, X., Wang, X., Liu, X., Liu, Q., & Kim, B. (2021). Explainable deep learning for efficient and robust pattern recognition: A survey of recent developments. Pattern Recognition, (2), 108102. https://doi.org/10.1016/j.patcog.2021.108102
- Cai, W., Liu, D., & Ning, X. (2021). Voxel-based three-view hybrid parallel network for 3D object classification. Displays, 69(1), 102076. https://doi.org/10.1016/j.displa.2021.102076
- Chakraborty, A., Mitra, A., Sarkar, S., & Das, S. (2021). Sway vibration control of floating horizontal axis wind turbine by modified spar-torus combination. Ocean Engineering, 219, 108232. https://doi.org/10.1016/j.oceaneng.2020.108232
- Chandra, R., & Rolland, L. (2015). Global-local population memetic algorithm for solving the forward kinematics of parallel manipulators. Connection Science, 27(1), 22–39. https://doi.org/10.1080/09540091.2014.948385
- Chapain, S., & Aly, A. M. (2021). Vibration attenuation in wind turbines: A proposed robust pendulum pounding tmd. Engineering Structures, 233, 111891. https://doi.org/10.1016/j.engstruct.2021.111891
- Chen, Z., & Ahn, H. (2020). Item response theory based ensemble in machine learning. International Journal of Automation and Computing, 17(5), 621–636. https://doi.org/10.1007/s11633-020-1239-y
- Chen, Z., Zhong, S., Chen, J., & Zhao, Y. (2020). DeepPursuit: Uniting Classical Wisdom and Deep Reinforcement Learning for Sparse Signal Recovery.
- DaR, S., Özbey, M., Çatlı, A. B., & Çukur, T. (2020). A transfer-learning approach for accelerated mri using deep neural networks. Magnetic Resonance in Medicine, 84(2), 663–685. https://doi.org/10.1002/mrm.28148
- Davila-Chacon, J., Wermter, S., & Bauer, J. (2015). Modeling development of natural multi-sensory integration using neural self-organisation and probabilistic population codes. Connection Science, 27(4), 358–376. https://doi.org/10.1080/09540091.2014.971224
- Dong, X., Lian, J., & Wang, H. (2019). Vibration source identification of offshore wind turbine structure based on optimized spectral kurtosis and ensemble empirical mode decomposition. Ocean Engineering, 172(JAN.15), 199–212. https://doi.org/10.1016/j.oceaneng.2018.11.030
- Du, X., Tang, S., Lu, Z., Wu, J., & Hung, P. (2020). A novel data placement strategy for data-sharing scientific workflows in heterogeneous edge-cloud Computing environments. IEEE ICWS. IEEE.
- Du, X., Xu, J., Cai, W., Zhu, C., & Chen, Y. (2019). Oprc: An online personalized reputation calculation model in service-oriented computing environments. IEEE Access, PP(99), 1–1. https://doi.org/10.1109/ACCESS.2019.2925778
- Egea-Alvarez, A., Bianchi, F., Junyent-Ferre, A., Gross, G., & Gomis-Bellmunt, O. (2013). Voltage control of multiterminal vsc-hvdc transmission systems for offshore wind power plants: Design and implementation in a scaled platform. IEEE Transactions on Industrial Electronics, 60(6), 2381–2391. https://doi.org/10.1109/TIE.2012.2230597
- Elmitwally, A., Eladl, A., & Abdelkader, S. (2016). Algorithm for transmission loss allocation in market-based power systems with wind generation. Journal of Energy Engineering, 142(4), 04016004. https://doi.org/10.1061/(ASCE)EY.1943-7897.0000341
- Farahmand, H., Jaehnert, S., Aigner, T., & Huertas-Hernando, D. (2015). Nordic hydropower flexibility and transmission expansion to support integration of north european wind power. Wind Energy, 18(6), 1075–1103. https://doi.org/10.1002/we.1749
- Garg, H., & Dahiya, R. (2016). Current signature analysis and its application in the condition monitoring of wind turbine for rotor faults. Energy Systems, 8(3), 495–510. https://doi.org/10.1007/s12667-016-0208-6
- Gorman, W., Mills, A., & Wiser, R. (2019). Improving estimates of transmission capital costs for utility-scale wind and solar projects to inform renewable energy policy. Energy Policy, 135(Dec.), 110994.1–110994.21. https://doi.org/10.1016/j.enpol.2019.110994
- Haehne, H., Schmietendorf, K., Tamrakar, S., Peinke, J., & Kettemann, S. (2018). Propagation of wind-power-induced fluctuations in power grids. Physical Review E, 99(5), 050301. https://doi.org/10.1103/PhysRevE.99.050301
- Hb, A., & Na, B. (2020). Vibration modeling of wind turbine shaft as rigid shaft supported by ehl contact ball bearings with overhung disc system. Tribology International, 151, 106481. https://doi.org/10.1016/j.triboint.2020.106481
- Hong, D., Zheng, J., Wu, Q., & Yang, X. (2018). Wind power forecast with error feedback and its economic benefit in power system dispatch. IET generation. Transmission Distribution, 12(21), 5730–5738. https://doi.org/10.1049/iet-gtd.2018.5635
- Kocewiak, L. H., Aristi, I. A., Gustavsen, B., & Holdyk, A. (2019). Modelling of wind power plant transmission system for harmonic propagation and small-signal stability studies. IET Renewable Power Generation, 13(5), 717–724. https://doi.org/10.1049/iet-rpg.2018.5077
- Li, X., Zhang, X., Wu, L., Lu, P., & Zhang, S. (2017). Transmission line overload risk assessment for power systems with wind and load-power generation correlation. IEEE Transactions on Smart Grid, 6(3), 1233–1242. https://doi.org/10.1109/TSG.2014.2387281
- Lu, Y., Yan, D., Zhang, J., & Levy, D. (2014). Direct back propagation neural dynamic programming-based particle swarm optimisation. Connection Science, 26(4), 367–388. https://doi.org/10.1080/09540091.2014.931355
- Mehrabi, M., Mohammadkarimi, M., Ardakani, M., & Jing, Y. (2019). Decision directed channel estimation based on deep neural network k-step predictor for mimo communications in 5 g. IEEE Journal on Selected Areas in Communications, 37(11), 2443–2456. https://doi.org/10.1109/JSAC.2019.2934004
- Mendez, G., Hervas, R., Gervas, P., Martin, A., & Julca, F. (2019). Dynamic emphatical narration for reduced authorial burden and increased user freedom in interactive storytelling. Connection Science, 31(1), 33–59. https://doi.org/10.1080/09540091.2018.1454891
- Ning, X., Duan, P., & Zhang, S. (2020). Real-time 3d face alignment using an encoder-decoder network with an efficient deconvolution layer. IEEE Signal Processing Letters, 27, 1944–1948. https://doi.org/10.1109/LSP.2020.3032277
- Ning, X., Gong, K., Li, W., Zhang, L., & Tian, S. (2021). Feature refinement and filter network for person re-identification. IEEE Transactions on Circuits and Systems for Video Technology, PP(99), 1–1. https://doi.org/10.1109/TCSVT.2020.3043026
- Pang, N., & Guo, W. (2019). Uncertain hybrid multiple attribute group decision of offshore wind power transmission mode based on thevikor method. Sustainability, 11(21), 6183. https://doi.org/10.3390/su11216183
- Paula, A., Oliveira, E., Oliveira, L. W., & Moraes, C. A. (2020). Reliability-constrained dynamic transmission expansion planning considering wind power generation. Electrical Engineering(1), 1–11. https://doi.org/10.1007/s00202-020-01054-y
- Purwins, H., Li, B., Virtanen, T., Schluter, J., Chang, S. Y., & Sainath, T. N. (2019). Deep Learning for audio signal processing. IEEE Journal of Selected Topics in Signal Processing, 13(2), 206–219. https://doi.org/10.1109/JSTSP.2019.2908700.
- Qi, S., Ning, X., & Yang, G. (2021). Review of multi-view 3D object recognition methods based on deep learning. Displays, 69(1), 102053. https://doi.org/10.1016/j.displa.2021.102053
- Rahmann, C., & Palma-Behnke, R. (2013). Optimal allocation of wind turbines by considering transmission security constraints and power system stability. Energies, 6(1), 294–311. https://doi.org/10.3390/en6010294
- Ruddy, J., Meere, R., & O’Donnell, T. (2016). Low frequency ac transmission for offshore wind power: A review. Renewable & Sustainable Energy Reviews, 56, 75–86. https://doi.org/10.1016/j.rser.2015.11.033
- Song, Z., Zhao, X., Hui, Y., & Jiang, H. (2021). Progressive back-projection network for COVID-CT super-resolution. Computer Methods and Programs in Biomedicine, 208, 106193. https://doi.org/10.1016/j.cmpb.2021.106193
- Ugranli, F., Karatepe, E., & Nielsen, A. H. (2016). Milp approach for bilevel transmission and reactive power planning considering wind curtailment. IEEE Transactions on Power Systems, 32(1), 652–661. https://doi.org/10.1109/TPWRS.2016.2562258
- Vargas, L. S., Bustos-Turu, G., & Larraín, F. (2015). Wind power curtailment and energy storage in transmission congestion management considering power plants ramp rates. 2015 IEEE Power & Energy Society General Meeting. IEEE, 30(5), 2498–2506. https://doi.org/10.1109/TPWRS.2014.2362922
- Wang, C., Bai, X., Wang, S., Zhou, J., & Ren, P. (2019). Multiscale visual attention networks for object detection in vhr remote sensing images. IEEE Geoence and Remote Sensing Letters, 16(2), 310–314. https://doi.org/10.1109/LGRS.2018.2872355
- Wang, J., Liu, B., Zhou, Y., Zhao, J., & Ming, L. M. (2020). Semisupervised multiscale generative adversarial network for semantic segmentation of remote sensing image. IEEE Geoscience and Remote Sensing Letters, PP(99), 1–5. https://doi.org/10.1109/LGRS.2020.3036823
- Wu, Y., Rosca, M., & Lillicrap, T. (2019). Deep Compressed Sensing.
- Xiang, J., Watson, S., & Liu, Y.. (2009). Smart monitoring of wind turbines using neural networks. In (pp. 1-8). In Sustainability in Energy and Buildings (pp. 1–8). Springer.
- Xue, B., Zhang, M., Su, N., & Binh, T. (2016). Investigation on particle swarm optimisation for feature selection on high-dimensional data: Local search and selection bias. Connection Science, 28(3), 270–294. https://doi.org/10.1080/09540091.2016.1185392
- Yan, C., Pang, G., Bai, X., Liu, C., & Zhou, J. (2021). Beyond triplet loss: Person re-identification with fine-grained difference-aware pairwise loss. IEEE Transactions on Multimedia, PP(99), 1–1. https://doi.org/10.1109/TMM.2021.3069562
- You, H., Yu, L., Tian, S., Ma, X., & Cai, W. (2021). Mc-net: Multiple max-pooling integration module and cross multi-scale deconvolution network. Knowledge-Based Systems, (4), 107456. https://doi.org/10.1016/j.knosys.2021.107456
- Zhang, L., Li, W., Yu, L., Sun, L., & Ning, X. (2021). Gmface: An explicit function for face image representation. Displays, 68(1), 102022. https://doi.org/10.1016/j.displa.2021.102022
- Zhang, Y., Ravishankar, J., Fletcher, J., Li, R., & Han, M. (2016). Review of modular multilevel converter based multi-terminal hvdc systems for offshore wind power transmission. Renewable & Sustainable Energy Reviews, 61, 572–586. https://doi.org/10.1016/j.rser.2016.01.108
- Zhao, Y., Pan, J., Huang, Z., Miao, Y., Jiang, J., & Wang, Z. (2020). Analysis of vibration monitoring data of an onshore wind turbine under different operational conditions. Engineering Structures, 205(Feb.15), 110071.1–110071.15. https://doi.org/10.1016/j.engstruct.2019.110071
- Zhou, L., Li, Y., Liu, F., Jiang, Z., Yu, Q., & Liu, L. (2019). Investigation of dynamic characteristics of a monopile wind turbine based on sea test. Ocean Engineering, 189(Oct.1), 106308.1–106308.17. https://doi.org/10.1016/j.oceaneng.2019.106308