Abstract
Solutions of water-soluble polymers have been used to stabilise deep excavations such as pile bores and diaphragm wall trenches since the 1970s. When compared with conventional bentonite slurries, these engineered fluids are recognised as bringing a number of benefits including smaller site footprint, lower environmental impact and lower construction costs. However, despite the years of use, too little has been published about their material properties and optimal methods of use, so problems still occur. To promote the best practice with these engineered fluids, this paper summarises the lessons that may be drawn from a number of published case histories of polymer use in the Far East. It is concluded from the review that the use of biodegradable polymers in deep excavations can be problematic unless a biocide is used. In contrast, synthetic polymers tend not to suffer from microbial degradation but do require the use of special pumping equipment to minimise shear degradation. In coarse soils, both types of polymer fluid can show excessive fluid loss. This can be remedied by adding bentonite, superabsorbent gel particles or proprietary fines that are dispersible in polymer fluids. Finally, soft pile bases have been reported which can be linked to the use of low fluid viscosity coupled with long waiting times between the end of excavation and concreting. This can be minimised by rigorous fluid and base cleaning. Overall, the case histories show that polymer fluids cannot be managed as if they were simply bentonite slurries. Their usage require different procedures, which, in turn, require different skills and experience from a contractor. This paper concludes with an analysis of future challenges and opportunities with these innovative construction fluids.
Introduction
In Hong Kong, as in many other parts of the world, bored piles are commonly constructed using either a full-length casing or a support fluid to stabilise the excavation until concrete is cast. Since the pioneering work of Veder [Citation1] in the early 1950s, bentonite clay slurry has been the support fluid of choice for an uncountable number excavation projects around the world. A wealth of knowledge and experience now exist for these slurries,[Citation2] though unfortunately problems do still occur from time to time. Bentonite clay is a natural and finite resource and in a search for more effective and sustainable alternatives, over the last 40 years or so, foundation engineers have investigated natural biodegradable water-soluble polymers such as xanthan and guar gums with varying degrees of success.[Citation3] A major breakthrough came in the early 1990s, when synthetic polymers based on the chemistry of partially hydrolysed polyacrylamides (PHPAs or HPAMs) became available to the foundation industry. PHPAs can be engineered to have long-chain molecules of correspondingly very high molecular weight. They are available as dry granular powders and as more rapidly dispersible liquid emulsions.
Today, the use of PHPA polymer fluids for deep excavations has spread from first applications in North America to many other countries including those of the Far East. There are many reasons for this, including (i) a smaller site plant footprint, (ii) reduced environmental impact, (iii) lower construction costs and (iv) a better foundation performance.[Citation3,Citation4] However, despite these potential benefits, many practitioners are still treading cautiously; reasons cited include the lack of documented case histories and the lack of official guidance.[Citation5] For example, the reference document Foundation design and construction published by the Geotechnical Engineering Office in Hong Kong only has a brief mention of polymer fluids and provides little guidance on their usage.[Citation6] The Code of practice for foundations published by the Buildings Department in Hong Kong does not mention polymer solutions as possible support fluids, though it does refer to the use of bentonite.[Citation7] The same situation prevails in many other countries.[Citation8,Citation9] Although a number of documented case histories do exist, they are scattered through the literature and some are not easily accessible. As stated in the Introduction, to help promote the best practice in foundation design and construction, this paper summarises the lessons that can be drawn from the available Far Eastern case histories. The choice of a limited geographic area makes the task more manageable and the results more relevant to a region. Where appropriate, laboratory results are cited to supplement the identified field experience, but the focus is on the latter. In the following sections, case histories from Japan, Hong Kong, Taiwan, Thailand and Singapore are discussed. It is hoped that these discussions will help those involved in foundation works to better understand and exploit this innovative and yet still poorly documented construction technology.
Case histories from Japan
Japan was probably one of the first countries to adopt the polymer fluid technology for deep excavation works. According to Ikuta [Citation10] and Xanthakos,[Citation11] a polymer product known as Telmarch was used for diaphragm walling in Japan in the 1970s. About 30 tons of Telmarch were produced every month in 1974 and about the same amount were used. Although little has been reported about the chemistry of this polymer, there is a certain amount of information about its physical properties in the literature.[Citation10,Citation11] shows the funnel viscosity curve for polymer concentrations ranging from 0.8% to 1.6% w/w, which correspond to 8–16 kg of polymer per m3 of mix water (note that a funnel with a capacity of 500 ml was used and the time recorded for the full discharge of 500 ml. The more commonly used Marsh funnel has a capacity of 1500 ml and the time is recorded for the discharge of 946 ml or 1000 ml [Citation12]). Concentrations of 8–16 kg/m3 are much higher than those used for currently available natural water-soluble polymers such as xanthan and guar gums (typically about 0.3% w/w), but are still considerably lower than those used for bentonite (30–60 kg/m3). It can be seen from that a considerable increase in fluid viscosity, over that of water, was achieved at these concentrations. This viscosity enabled the fluid to be used to stabilise deep excavations as it reduced the seepage losses to the ground. It may also be noted that the Telmarch fluid was much less sensitive to cement contamination from fresh concrete than conventional bentonite slurry.[Citation10]
Figure 1. Marsh funnel viscosity of Telmarch polymer fluid at different concentrations.[Citation11]
![Figure 1. Marsh funnel viscosity of Telmarch polymer fluid at different concentrations.[Citation11]](/cms/asset/bb57e44a-a75d-4502-a4b7-d29e53cae4ea/thie_a_970749_f0001_b.gif)
Despite the desirable physical properties of the Telmarch fluid, its usage appears to have been short-lived as no further information can be found in the literature. A recent enquiry to the supplier Telnite Co. Ltd has, however, revealed the reason for the decline in use. According to Telnite (email correspondence with K. Kodama; unreferenced), Telmarch was produced for use in the Japanese construction market in the 1970s. Its ease of mixing and application led Japanese companies to extend its usage to overseas projects. However, it was found that for deep excavations which took longer to complete, the fluid degraded in use with a loss of fluid properties. As a result, the use of Telmarch gradually declined and sales of this product ceased later. Based on this description of the problems, it is believed that Telmarch was a biodegradable natural polymer. Probably as a result of the problems encountered with Telmarch, in the early 1980s, Hori and Mori [Citation13] from Japan undertook a laboratory study of biodegradation and its prevention by increasing pH and the use of biocides. They concluded that a high pH alone was not sufficient to prevent biodegradation as indicated by the loss of fluid viscosity and they identified an organic nitrogen-based biocide that was effective in maintaining the fluid properties over a 60-day test period. Despite these findings, the use of polymer fluids does not appear to have revived in Japan as inferred from the lack of further publications. A recent literature search including that in the Japanese language did not reveal any papers on polymer fluids, though it did identify a 2013 patent application discussing the use of superabsorbent polymer for the control of fluid loss in coarse, highly permeable soils such as gravels.[Citation14] This specific application will be discussed with the case histories from Thailand.
Case histories from Hong Kong
Tuen Mun Station
In Hong Kong, the first approved use of polymer fluids was for the construction of part of the West Rail's Tuen Mun Station (Contract CC213) between 2001 and 2002. Information on this project has not been published, but the first author was involved during the construction period. The work involved the construction of nine rock-socketed bored piles ranging from 1.5 m to 1.8 m in diameter and up to 51 m in length to support a new railway viaduct crossing the Tuen Mun River. Part of the river was diverted so that during construction, the piling rigs operated on a platform built in the original riverbed. The polymer used for this project was SlurryPro CDP® which was supplied in granular form. The polymer material was mixed with fresh water at a concentration of at least 0.7 kg/m3 to form a viscous solution with a Marsh funnel viscosity of over 65 seconds. shows the mixing tanks and the pumps used in the fluid circuit. It can be seen from the photograph that a screw pump and a centrifugal pump were used. The former was used to pump the polymer fluid from the tanks to the excavation, and the latter was used to return the used fluids to the tanks during concreting. The rationale for this arrangement is that polymer fluids are prone to damage by the high shear stresses induced by centrifugal pumps,[Citation15] hence the lower shear screw pump was used to preserve the properties of the fluid when delivered to the excavations. However, as the screw pump was unable to deal with the high flow rate required during concreting, the centrifugal pump was used to return the fluid to storage. This arrangement was in accordance with the polymer supplier's recommendation, but the authors regard it as less than ideal since the potentially soil-laden used fluid is subjected to shear in the centrifugal pump which will tend to disperse the soil into the fluid and so promote the loss of active polymer by sorption onto the soil.[Citation16]
Prior to the excavation, a 10 m long temporary casing was inserted into the ground at each pile location to support the soft alluvial clay at the top. The pile bore was excavated dry to the bottom of the casing and then under the support of polymer fluid. During the excavation process, the support fluid level was maintained near the top of the casing to provide a high stabilising pressure to maintain the stability of the pile bore. At the end of the excavation, the pile base was cleaned by the air-lifting method as shown in . Although this base-cleaning method produced satisfactory results, Viana da Fonseca et al. [Citation17] recently noted that soil particles in polymer fluids can be settled to the base of the excavation very quickly, so that air lifting is generally not necessary and a mechanical cleaning bucket can be used instead. Indeed, a mechanical cleaning bucket may be preferred for large-diameter piles to ensure full sweeping of the base area.
At each pile location, the support fluid was tested for pH, viscosity, density and sand content. The test results were assessed against the fluid specifications proposed by the contractor, which is reproduced in . It is interesting to note that only pH and viscosity were controlled before the excavation, and that only density and sand content were controlled after the excavation. The density and sand content of the fluid will rarely exceed the upper limit before the excavation and thus the omission of these tests from the specification is of no great significance. However, in the authors' opinion, the pH and viscosity of the fluid should have been tested after the excavation to detect any loss of fluid activity due to sorption onto the soil or contamination by groundwater.[Citation4,Citation16] Finally, it is worth noting that although the completed piles were not load tested, their structural integrity was checked by cross-hole ultrasonic logging and no problems were identified. The piles have now been supporting the viaduct for more than 10 years and no problems have been reported. The first use of polymer support fluids in Hong Kong, therefore, can be considered a success.
Table 1. Test methods and polymer fluid specifications for the Tuen Mun Station project in Hong Kong.
Case histories from Taiwan
Taiwan high-speed rail – contracts 260 and 270
In Taiwan, Bustamante and Boato [Citation18] and Corbet et al. [Citation19] reported the use of polymer fluids for Contracts 260 and 270 of the Taiwan High-Speed Rail (THSR) project. Large-diameter bored piles were required to support the railway viaducts which run along much of the route for the two Contracts. The ground conditions consisted of alluvial sand, gravel and clay with the depth exceeding 100 m at some locations. Standard penetration test (SPT) blow counts (N) ranged from less than 10 for the first several metres to over 100 at depth.
Trials of different pile construction methods were undertaken at the beginning of the project. A 2 m diameter test pile was first constructed using a grab for the excavation and water to counterbalance the groundwater which lay at about 3 m below the ground level. The resulting 30 m long pile was tested using a single Osterberg cell (O-cell) set at about 20 m below the pile head. The test results showed that the mobilised skin friction (unit shaft resistance) was lower than the values used in the tender design. Polymer fluid was therefore used for a second test pile which was excavated using a rotary auger (Bustamante and Boato [Citation18] stated that granular SlurryPro CDP® polymer was used at a concentration between 0.4 kg/m3 and 0.6 kg/m3 to obtain a Marsh funnel viscosity between 52 seconds and 65 seconds). However, side-wall profile measurements using an ultrasonic technique showed very large amounts of over-break which were considered unacceptable. A third trial pile was therefore constructed using the reverse circulation drilling (RCD) rig with polymer fluid. Another 22 test piles with lengths ranging between 25 m and 72 m were later constructed by the same technique. Bustamante and Boato [Citation18] did not explain why drilling with the RCD technique produced better results than that with the rotary auger. However, given the ground conditions consisting mainly of sand and gravels, the soil on the side wall was probably disturbed by the auger during its repeated entry into and exit from the pile bore.
All the 22 test piles were load tested for either axial or lateral capacities at not less than 28 days after concreting. The results showed that the unit shaft resistance in clay was higher than the original design value, but no improvement in shaft resistance was found for the sand and gravel. A weaker-than-expected unit base resistance (end bearing) was also found from the back analyses, and this prompted a revision of the design equations (based on SPT results) and more careful base cleaning for the working piles. The calibrated design equations were given in Corbet et al. [Citation19] and were not repeated here. During the works, the piling contractor reported that 8200 working piles, 2 m in diameter and up to 60 m deep, were constructed using polymer fluids and RCD.[Citation20] These piles remain some of the largest constructed using polymer fluids. This would appear to be because contractors around the world are still cautious about using polymer fluids to support large excavations, especially in coarse soils.
THSR – contract 291
Duann et al. [Citation21] and Chin and Chen [Citation22] reported the pile loading test programme for another section of the THSR project delivered under Contact 291. The ground conditions at the test site consisted of alluvial deposits of interbedded sand and silty clay followed by mudstone at greater depth. A total of six test piles were constructed: TP-1, TP-1B, TP-2, TP-3, TP-3B and TP-4. As on Contracts 260 and 270, the test piles were drilled by the RCD method but only two of them, TP-1B and TP-3B, were under polymer fluids. All test piles were toe-grouted, but the two piles drilled under polymers also received multi-stage grout injections. All piles were tested from the top down using a steel loading frame. From the load test results, it was found that the two piles constructed using polymer fluids coupled with multi-stage toe-grouting showed very stiff, near-linear load-settlement response – a behaviour which was not seen in the other test piles. Although the stiff response must have been due, in part, to the multistage toe-grouting operation, it was concluded by the original authors that higher shaft resistance could be achieved when using polymers to stabilise the pile bores.
Case histories from Thailand
Bangkok elevated road and train system
Littlechild and Plumbridge [Citation23] reported what is probably the first use of polymer fluids for deep excavation works in Thailand. The project was the Bangkok Elevated Road and Train System (BERTS) which required 16,000 bored piles with a diameter of 1.5 m. Due to the large number of piles to be constructed, a number of instrumented trial piles were first constructed using different techniques including bentonite and polymer fluids and base grouting. Bangkok is located at the southern end of the Chao Phraya alluvial plain and the ground conditions in Bangkok comprise interbedded layers of medium dense to very dense sand (SPT N = 50 to >100 blows/300 mm) and firm to very stiff clay (Su = 50 to >200 kPa) to significant depth. The top 12–18 m is covered by a layer of marine clay known as Bangkok Soft Clay (Su = 10 kPa to 25 kPa). A temporary casing was used to support the Bangkok Soft Clay. Polymer support fluids were used for the excavation below the casing.
An interesting feature of this project, and indeed of all the identified Bangkok case histories, is that the polymer fluids were not prepared with water but with a dilute bentonite slurry. In the BERTS project, high fluid loss into the sand layers had been observed in the initial trial bores stabilised with pure polymer fluids, thus making the use of pure polymers uneconomic. However, it was found that the volume of fluid loss could be significantly reduced if the polymer fluid was mixed into water pre-loaded with bentonite at a concentration of 5 kg/m3. The piling contractor had already carried out two successful loading tests on piles elsewhere in Bangkok (Asoke and Worajack) using polymer–bentonite fluids. However, as the construction time for these test piles was relatively short (14 hours and 16 hours), two additional piles (C21 and C22) were constructed using bentonite–polymer fluids on the BERTS project site to assess the effect of construction time. The construction details and the load test results are summarised in . For comparison, the results of five piles constructed using bentonite (C5, C8, C10, SRT1 and SRT3) at the same site are given in the table. To aid the interpretation of these results, the ratios of actual to predicted shaft resistance have been plotted against construction time () and viscosity (). The predicted shaft resistances were based on the actual geology at each trial pile location and the design approach adopted by Littlechild et al. [Citation24] for plain piles.
Figure 4. Effects of support fluid type and construction time on bored pile performance in Bangkok, Thailand.
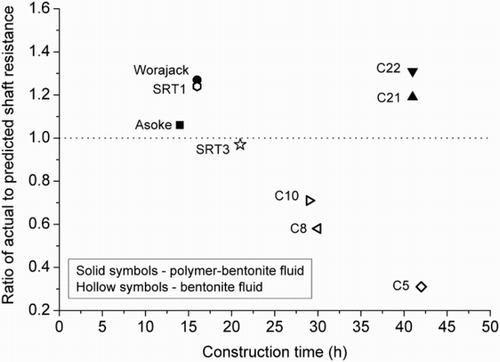
Figure 5. Effects of support fluid type and viscosity on bored pile performance in Bangkok, Thailand.
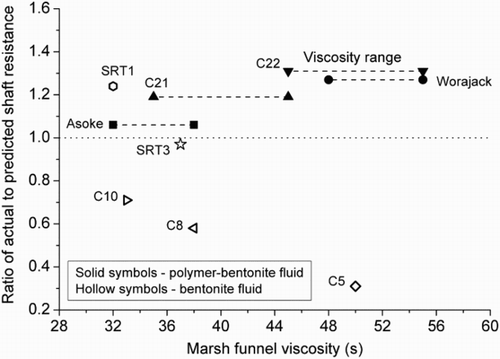
Table 2. Construction details and load test results for four trial piles constructed using polymer–bentonite mixes and bentonite fluids in Bangkok, Thailand.[Citation23]
shows that construction time up to 42 hours does not appear to have had any adverse effect on the shaft resistance of piles constructed using polymer–bentonite fluids (C21, C22, Asoke and Worajack). However, a significant reduction in shaft resistance can be seen with increasing construction time for the piles constructed using pure bentonite fluid (C5, C8, C10, SRT1 and SRT3). This latter finding confirms that of Thasnanipan et al. [Citation25] for piles constructed elsewhere in Bangkok and also laboratory evidence recently produced by Lam et al.[Citation26] The better performance of polymer–bentonite fluids may be due to the thinner filter cake formed on the excavation side wall, thus leading to better interfacial resistance between the soil and the pile concrete. As regards fluid viscosity, shows that increasing fluid viscosity had a slight positive effect on the load capacity of piles constructed under polymer–bentonite fluids, but a strong negative effect on the capacity of those constructed under bentonite alone. The slight beneficial effect with polymers was probably due to the better excavation stability when fluids of higher viscosity were used and possibly further reduced filter cake thickness. The reduction in pile performance observed when using bentonite may be due to a thicker filter cake formed on the side-wall surface. However, Thasnanipan et al. [Citation25] examined the effect of bentonite fluid viscosity, but did not find any noticeable trend.
Despite the apparent advantages found in Bangkok of using mixed polymer–bentonite fluids over bentonite alone, the authors have reservations about this practice. This is because even though the bentonite dosage is small (5 kg/m3), soft filter cakes can still form on the excavation side walls to reduce pile shaft resistance. In fact, this is confirmed by the results of some interface shear box tests presented in Thasnanipan et al.[Citation27] Their results showed that the interfacial shear resistance between cement mortar (simulating the pile concrete) and sand was reduced by both pure bentonite and polymer–bentonite fluids, although the degree of reduction was lower for the latter. In the authors' opinion, to overcome the high losses of polymer fluids to coarse soil zones, it may be preferable to use non-cake forming fluid-loss additives that are specially designed for polymer fluids, such as superabsorbent gel particles and non-reactive fines. shows the superabsorbent gel particles which are cross-linked polyacrylamides. When added to water, this material can absorb many hundred times its own weight to form a crystalline gel. In coarse formations such as those encountered in Bangkok, these gel particles can block the pores of the side walls and so reduce bulk fluid loss. Guidance on the use of swollen gel particles to reduce fluid loss typically can be found in polymer suppliers' literature and in Akagi et al.[Citation14]
Bangkok city case histories
Thasnanipan et al. [Citation28,Citation29] reported two other case histories of polymer used in Bangkok. Probably because of the experience on the BERTS project, a dilute bentonite fluid was used as the mix fluid for polymers in these two projects, again to reduce the volume of fluid loss into the sand layers. Thasnanipan et al. [Citation28] presented the results for 11 test piles (TP-1 to TP-11) with diameters ranging from 0.6 m to 1.8 m and lengths ranging from 24 m to 62 m. For the construction of these test piles, the support fluids were prepared using 5–12 kg of bentonite and 0.5 kg of polymer per m3 of water. The piles were load tested axially and were found to show less settlement than predicted. For the three piles (TP-1 to TP-3) that were instrumented with strain gauges, the measured shaft resistance was found to be significantly higher than the predicted values, giving a measured to predicted shaft resistance ratio between 1.41 and 1.58. These values are slightly higher than those given by Littlechild and Plumbridge (; Figures and ), but this may be because the predictions made by Thasnanipan et al. [Citation28] were more conservative. Based on back analysis of the test results, Thasnanipan et al. [Citation28,Citation29] proposed design (=
) values for bored piles in Bangkok constructed using polymer and bentonite fluids. Their suggested
values for polymer fluids are 0.1–0.15 higher than those for bentonite fluids; the exact value is depending on the internal friction angle of the sand. As discussed, it is believed that even better performance could have been achieved if pure polymer fluids and superabsorbent polymer additives () had been used to manage the fluid-loss problem. However, further research is required to confirm this.
Case histories from Singapore
Barrettes in Old Alluvium
Ho and Tan [Citation30] discussed the performance of a test barrette (a rectangular pile) constructed for a two-level basement in Tampines, Singapore. The site is underlain by Old Alluvium, which is a medium dense to dense sand with a significant amount of gravel, silt and clay. At the test location, the SPT blow counts (N) increased from less than 10 near the surface to over 100 blows/300 mm at 17 m depth. The dimensions of the test barrette were 0.8 m (width) × 2.8 m (length) × 17 m (depth). It was excavated with a hydraulic grab. Strain gauges and rod extensometers were installed at different levels down the barrette. The type of the polymer used for the excavation is not stated in the paper, but some properties of the used fluids from the trench are given. In particular, the Marsh funnel viscosity of the fluids is reported to have been in the range from 28 seconds to 32 seconds. These are very low viscosity values for any excavation fluid as the time for water is 26 seconds. Despite the low fluid viscosity, no excavation support problems were reported for the barrette.
The completed barrette was load tested by the maintained load method 26 days after casting. For each stratum, the measured unit skin friction (fs) was normalised by the corresponding SPT N value. The ratios were then compared with those previously obtained from bored piles constructed using full-length casings at other comparable sites, and little difference was found. However, the load test result showed that the base resistance of the test barrette did not pick up until a toe displacement of 4.8 mm had been reached. Thereafter, the observed base response was found to represent more closely the consolidation of weak debris under the test load rather than the in situ soil. The reason given by Ho and Tan for the poor base response is that the long waiting period (4.5 hours) between completion of the desanding process and concrete placement allowed soil particles to settle and collect as a soft sediment at the base of the barrette. Significant deposition of sediment from a desanded slurry is unexpected, especially as the reported sand content of the used fluid was relatively low ranging from 0.2% and 1.0% (which may be compared with the upper limit of 3% previously reported for the Tuen Mun Station project in Hong Kong; see ). However, given that the viscosity of the polymer fluid was very low and the waiting period was long, it is perhaps less surprising that a “soft toe” was able to form.
Because of the issue with the quality of the base, the working barrettes, which were constructed in the same way as the test barrette, were designed without reliance on end resistance, that is, they were designed for friction alone. In the authors' opinion, cost savings might have been achieved if the barrettes had been constructed using higher viscosity fluids and/or if it had been possible to manage the desanding and base-cleaning processes to avoid a build-up of spoil at the toe. Alternatively, the fluid could be exchanged after the excavation and the base mechanically cleaned before concreting. This would allow the end resistance to be considered in the final design. A UK case history illustrating the importance of fluid and base cleaning in polymer-supported pile bores is given in Lam et al.[Citation31]
Bored piles in residual soil
Ho et al. [Citation32] presented load test results for an instrumented bored pile constructed using polymer fluid for a housing project at Choa Chu Kang, Singapore. The ground conditions were 25 m of residual soil overlying 5 m of weathered granite followed by bedrock. The SPT N value was less than 10 blows/300 mm in the residual soil and 50–100 blows/300 mm in the weathered granite. A 5 m long temporary casing was used and excavation below the casing was carried out under a polymer fluid, for which no information is given. The pile was instrumented with strain gauges and rod extensometers at different levels and was tested by the maintained load method. The load test results showed that the end resistance suddenly dropped when the toe displacement reached 49 mm. A check on the installation records revealed that the measured depth of the pile bore reduced by 200 mm during the period between the end of boring and just before lowering the reinforcing steel cage. This was taken to indicate the accumulation of soft sediment at the bottom of the bore during the waiting period. The soft sediment was suspected by the original authors to have mixed with the fresh concrete during casting, and the sudden drop was believed to be the result of overstressing and crushing of the weak concrete. As for the first Singaporean case history discussed earlier, the peak unit shaft resistance was expressed as the ratio fs/N and compared with data obtained from piles constructed under bentonite. No significant difference was found between the two fluids, although the data appear quite scattered.
Conclusions
Lessons learned
The early 1970s' work with polymer fluids in Japan was successful but take-up of the polymer concept was limited. This was because the polymers then available (natural polymers) suffered biodegradation in deep excavations that required longer times for completion. Furthermore, it was found that high pH alone was not sufficient to prevent biodegradation. Laboratory trials demonstrated that the working life of natural polymers could be extended with biocides, but it has not been possible to identify whether they were actually employed on site. These early experiences showed that understanding the fundamental properties of polymer fluids is important.
Experience from Hong Kong showed that polymer fluids can be used to reduce the excavation fluid plant footprint and that with appropriate selection of polymer, they can be used near environmentally sensitive receptors such as rivers. The correct selection of pumps (screw as opposed to centrifugal where possible) and the adoption of appropriate fluid-testing and base-cleaning procedures can be seen to have contributed to the success of the projects such as the Tuen Mun Station project.
The experience from Taiwan demonstrated that polymer fluids are compatible with RCD drilling and indeed on that project pile performance was apparently improved by its usage. It also showed that polymer fluids can stabilise coarse soils containing sand and gravels in pile bores up to 2 m in diameter. Very stiff load-settlement response has been demonstrated for piles which were constructed using polymer fluids and toe-grouted.
Although they had been used in coarse soils in Taiwan, the experience from Bangkok highlighted the possible fluid-loss problem when pure polymer fluids are used in highly permeable grounds. The use of mixed polymer–bentonite fluids was found to give satisfactory results as shown by the high measured shaft resistance over a range of construction times and fluid viscosities. These benefits have been translated by some into higher
values to be used for routine pile design. The authors would not normally recommend the use of mixed bentonite–polymers slurries without conducting site-specific load tests and believe that the use of specially formulated fluid-loss additives can produce further benefits, but further research is required to confirm this.
The two cases from Singapore highlighted the potential “soft toe” problem due to the accumulation of sediment at the base of the excavation. The use of polymer fluids with low viscosity and long waiting periods between the end of excavation and concreting can both contribute to the problem even when the sand content of the fluid is low (<1%).
Future challenges and opportunities
As shown by these Far Eastern case histories, the use of polymer solutions for pile construction can offer many benefits but can also bring new problems unless these are recognised and managed. The future success of the polymer technology, as for bentonite before, will depend on the development of industry-wide specifications for polymer use. Ignoring the particular polymer-specific properties of polymer fluids, many of which can be very simply managed if recognised in time, may lead to problems such as those experienced by the Japanese contractors in the 1970s. If properly managed, the innovative polymer systems now available have the potential to improve on conventional bentonite slurries for bored pile construction.
Although thus far the use of polymer fluids has been largely limited to pile construction, in the future they may also replace bentonite in diaphragm walling and slurry tunnelling works. As civil engineers around the world increasingly have to build in congested urban cities, polymer fluids will become an attractive option for engineers as they do not require bulky ancillary equipment (hydrocyclones, filter presses, shaker screens, decanting centrifuges, etc.) for the removal of suspended soils. Due to their ease of mixing, polymer fluids are also expected to gain wider acceptance in water-well and site-investigation drilling. In addition, although it was not mentioned previously, polymer fluids also possess good lubricating characteristics and hence may be useful for pipe and pile jacking works.
ORCID
Carlos Lam http://orcid.org/0000-0003-3269-1638
Funding
The case histories discussed in this paper were studied as part of three research projects funded by the UK Engineering and Physical Sciences Research Council (EPSRC) [Grants EP/C537815/1 (Industrial CASE Award), EP/H50026X/1 (Knowledge Transfer Secondment) and EP/K503782/1 (Impact Acceleration Account)].
Additional information
Ir Dr Carlos Lam graduated from The Hong Kong Polytechnic University, Imperial College London and the University of Oxford in 2001, 2003 and 2011, respectively. He is a Chartered Civil Engineer and a Registered Ground Engineering Specialist in the UK. He has been conducting research on the use of polymer fluids for geotechnical construction since 2007 and has published extensively on this topic. Prof Stephan A. Jefferis and Ir Dr Lam are the authors of a technical book entitled “Polymer Support Fluids in Civil Engineering”, which will be published by ICE Publishing in 2015.
Prof Stephan A. Jefferis is the Director of Environmental Geotechnics Ltd, a Visiting Professor at the University of Oxford, an Emeritus Professor of the University of Surrey and currently the Vice Chairman of the British Geotechnical Association. He has over 40 years of experience in research and consultancy on geotechnical processes. He has worked extensively and internationally on the application of bentonite, bentonite-cement and polymer slurries in piling, diaphragm walling, tunnelling and cut-off walls. He is the author of over 100 papers and is regularly invited as a keynote speaker.
References
- Veder C. Procédé de construction de diaphragms imperméables à grande profondeur au moyen de boues thixotropiques [Method for the construction of impermeable diaphragms at great depth by means of thixotropic muds]. Proceedings of the 3rd international conference of soil mechanics and foundation engineering; 1953 Aug 16–27; Switzerland; p. 91–94. French.
- Federation of Piling Specialists. Bentonite support fluids in civil engineering. 2nd ed. Kent: Federation of Piling Specialists; 2006.
- Jefferis SA, Troughton V, Lam C. Polymer systems for fluid supported excavations. In: Geotechnical issues in construction: short paper series and proceedings of 2nd conference; report no. X513. London: CIRIA; 2011; p. 7–12.
- Jefferis SA, Lam C. Polymer support fluids: use and misuse of innovative fluids in geotechnical works. Proceedings of the 18th international conference of soil mechanics and geotechnical engineering; 2013 Sep 2–6; Paris. Paris: Presses des Ponts; p. 3219–3222.
- Wheeler P. Piles unlock polymer potential. Ground Eng. 2003;36(supp):8–9.
- Geotechnical Engineering Office. Foundation design and construction; GEO publication no. 1/2006. Hong Kong: Civil Engineering and Development Department, the HKSAR Government; 2006.
- Buildings Department. Code of practice for foundations. Hong Kong: Buildings Department, the HKSAR Government; 2004.
- Institution of Civil Engineers. ICE specification for piling and embedded retaining walls. London: Thomas Telford; 2007.
- Canadian Geotechnical Society. Canadian foundation engineering manual. 4th ed. Richmond, BC: Canadian Geotechnical Society; 2006.
- Ikuta Y. Diaphragm walling in Japan. Ground Eng. 1974;7:39–44.
- Xanthakos P. Slurry walls. New York: McGraw-Hill; 1979.
- Marsh HN. Properties and treatment of rotary mud. Trans AIME. 1931;92:234–251. doi: 10.2118/931234-G
- Hori Y, Mori K. [A study on prevention of polymer degradation in slurry for trench excavation: in case of polymer based slurry]. Summaries of technical papers of annual meeting (structures). Tokyo: Architectural Institute of Japan; 1983; p. 345–346. Japanese.
- Akagi H, Kondoh Y, Uehara S, Asano H, Ukegawa M. [Stable liquid composition of swollen superabsorbent polymer for ground excavation and construction method using same]. PCT (Patent Cooperation Treaty) application WO 2013024878 A1. 2013 Feb 21. Japanese.
- Lam C, Jefferis SA, Goodhue KG Jr. Observations on viscosity reduction of PHPA polymer support fluids. Proceedings of sessions of the GeoShanghai 2010 International Conference; 2010 Jun 3–5; Shanghai. Reston (VA): American Society of Civil Engineers; p. 184–191.
- Lam C, Martin PJ, Jefferis SA, Goodhue KG Jr. Determination of residual concentration of active polymer in a polymeric support fluid. Geotech Test J. 2014;37:46–59. doi: 10.1520/GTJ20130019
- Viana da Fonseca A, Buttling S, Coutinho RQ. Foundations: shallow and deep foundations, unsaturated conditions, heave and collapse, monitoring and proof testing. In: Huat BBK, Toll DG, Prasad A, editors. Handbook of tropical residual soils engineering. Leiden: CRC Press; 2012. p. 283–412.
- Bustamante M, Boato R. Les polymères: application au forage des pieux de grands diamètres [Polymer slurry in large diameter pile drilling – case histories]. Proceedings of the 16th international conference on soil mechanics and geotechnical engineering; 2005 Sep 12–16; Osaka. Amsterdam: Millpress; p. 2083–2086. French.
- Corbet SP, Peters M, Huppert F, Seitz J. Taiwan High Speed Railway – contracts 260 & 270 – geotechnical aspects and pile testing. Proceedings of the 16th international conference on soil mechanics and geotechnical engineering; 2005 Sep 12–16; Osaka. Amsterdam: Millpress; p. 2095–2098.
- Bilfinger Spezialtiefbau GmbH [Internet]. Taiwan High Speed Rail bored piles. Taichung, Taiwan [cited 2014 Jan 4]. Available from: http://www.spezialtiefbau.bilfinger.com/
- Duann SW, Chen MS, Seah TH, Fujita M. Optimization of pile foundation design through full-scale pile load tests in Taiwan High Speed Rail project. Proceedings of the 15th Southeast Asian geotechnical society conference; 2004 Nov 22–26; Bangkok. Thailand: Southeast Asian Geotechnical Society; p. 223–230.
- Chin CT, Chen JR. Foundation engineering practice in Taiwan – high speed rail experiences. Proceedings of a seminar on the state-of-the-practice of geotechnical engineering in Taiwan and Hong Kong; 2006 Jan 20; Hong Kong. Hong Kong: The Hong Kong Institution of Engineers; p. 28–51.
- Littlechild B, Plumbridge G. Effects of construction technique on the behaviour of plain bored cast in situ piles constructed under drilling slurry. Proceedings of the 7th international conference and exhibition on piling and deep foundations; 1998 Jun 15–17; Vienna. Hawthorne (NJ): Deep Foundations Institute; p. 1.6.1–1.6.8.
- Littlechild B, Plumbridge G, Free MW. Shaft grouted piles in sand and clay in Bangkok. Proceedings of the 7th international conference exhibition on piling and deep foundations; 1998 Jun 15–17; Vienna. Hawthorne (NJ): Deep Foundations Institute; p. 1.7.1–1.7.8.
- Thasnanipan N, Baskaran G, Anwar MA. Effect of construction time and bentonite viscosity on shaft capacity of bored piles. Proceedings of the 3rd international geotechnical seminar on deep foundations on bored and auger piles; 1998 Oct 19–21; Ghent. Rotterdam: Balkema; p. 171–177.
- Lam C, Jefferis SA, Martin CM. Effects of polymer and bentonite support fluids on concrete-sand interface shear strength. Géotechnique. 2014;64:28–39. doi: 10.1680/geot.13.P.012
- Thasnanipan N, Aye ZZ, Boonyarak T. Behaviour of polymer-based slurry for deep-seated bored piles in multi-layered soil of Bangkok. Proceedings of the 4th international geotechnical seminar on deep foundations on bored and auger piles; 2003 Jun 2–4; Ghent. Amsterdam: Millpress; p. 267–274.
- Thasnanipan N, Aye ZZ, Submaneewong C, Teparaksa W. Performance of wet-process bored piles constructed with polymer-based slurry in Bangkok subsoil. Proceedings of the international deep foundations congress 2002; 2002 Feb 14–16; Orlando. Geotechnical Special Publication No. 116. Reston (VA): American Society of Civil Engineers; p. 143–157.
- Thasnanipan N, Aye ZZ, Boonyarak T, Arayasiri M, Intraratchaiyakit C. The contest on the prediction of capacity of a bored pile constructed under polymer-based slurry in Bangkok subsoil. Proceedings of the DFI/EFFC 10th international conference on piling and deep foundations; 2006 May 31–Jun 2; Amsterdam. Hawthorne (NJ): Deep Foundations Institute; p. 387–396.
- Ho CE, Tan CG. Barrette foundation constructed under polymer slurry support in Old Alluvium. Proceedings of the 12th Southeast Asian geotechnical conference, 1996 May 6–10; Kuala Lumpur. Thailand: Southeast Asian Geotechnical Society; p. 379–384.
- Lam C, Troughton V, Jefferis SA, Suckling T. Effect of support fluids on pile performance – a field trial in east London. Ground Eng. 2010;43(10):28–31.
- Ho CE, Tan CG, Lim CH. An instrumented polymer slurry bored pile in weathered granite. Proceedings of the 52nd Canadian geotechnical conference, 1999 Oct 25–27; Regina, Saskatchewan. Richmond, British Columbia: The Canadian Geotechnical Society; p. 211–218.