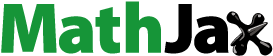
ABSTRACT
Bitumen ageing has a significant impact on the mechanical performance of asphalt concrete. This study utilises dynamic mechanical tests (frequency sweep, fatigue, and relaxation) to investigate the effect of ageing on the viscoelastic characteristics of bitumen. As ageing progressed, a shift of the Black diagrams curves towards lower phase angles was observed; at the same time the shape of the curves changed to a straight line and the curvature reduced. Interestingly, based on the standard fatigue analysis criteria, ageing appears to have a positive effect on bitumen fatigue life. Consequently, it occurs that studying only the stiffness and fatigue behaviour of bitumen cannot directly characterise ageing-induced degradation. The stress relaxation test was found to be more suitable to characterise ageing of bitumen. Aged bitumen had higher residual stresses and longer relaxation times. Hence, aged bitumen was found to be more susceptible to stress accumulation and thus cracking. A linear relationship was established between the crossover modulus and the stress relaxation ageing indices for the studied bitumen. This relationship suggests that crossover modulus has the potential to be used as a parameter to characterise the bitumen relaxation properties by means of routine tests such as the DSR frequency sweep tests.
1. Introduction
Ageing of bituminous materials is believed to be one of the major causes of pavement ravelling and cracking. The mechanical properties of bitumen, as of all organic substances, evolve with time. It is well known that as bitumen ages its ductility and penetration index are reduced while the softening point is increased (Siddiqui and Ali Citation1999, Gawel and Baqinska Citation2004, Lesueur Citation2009). Ultimately, the viscosity of the bitumen is increased and bitumen becomes stiffer. This may cause the mixture to become excessively brittle and susceptible to fatigue damage and cracking at lower temperatures (Kliewer et al. Citation1995, Isacsson and Zeng Citation1997, Hofko et al. Citation2016).
The process of ageing includes different mechanisms, such as physical hardening, loss of volatile components, photo-oxidation and thermal-oxidation (Lu et al. Citation2008). Physical hardening changes the rheological properties of bitumen due to a change in the orientation of molecules. This process is reversible because it alters the physical properties of bitumen without changing its chemical composition (Struik Citation1977, Ferry Citation1980). Evaporation causes the loss of volatile components of bitumen (Petersen Citation1984, Nie et al. Citation2018) during production, laying, and compaction as the asphalt mixture is subjected to higher temperatures. Moreover, UV radiation is associated with bitumen ageing because it activates photo-oxidation reactions which are degradation reactions at the bitumen surface in the presence of oxygen or ozone (Lesueur Citation2009, Hu et al. Citation2018). Generally, photo-oxidation takes place only within the top 5 μm of the exposed binder film (Durrieu et al. Citation2007). On the other hand, thermal oxidation is regarded as a chemical reaction process that leads to the transformation of one set of chemical substances to another. As such, this process is irreversible and is caused by physical–chemical changes in the individual bitumen components (Petersen Citation2009, Soenen et al. Citation2016). It is generally recognised that thermal oxidation is probably a key ageing mechanism of asphalt pavements and can cause an increase in bitumen stiffness, which can ultimately lead to cracking.
In the past, research has shown that typical bitumen properties such as viscosity, penetration, softening point and ductility had a good correlation with ageing (Kandhal and Koehler Citation1984). At that time the level of ageing was expressed as a reduction in penetration, an increase in softening point or as the ratio of viscosities, always in relation with the unaged (fresh) condition. Over the past a few years, however, rheology has been extensively used in order to classify and evaluate bituminous binders according to their performance properties (Mastrofini and Scarsella Citation2000). Rheology involves the study and evaluation of the time-temperature dependent response of materials that are stressed or subjected to an applied force. Rheological characterisation of bitumen includes testing for age hardening, temperature susceptibility, shear susceptibility, stiffness and viscosity (Miró et al. Citation2015). Because of that, more researchers currently use the dynamic shear rheometer (DSR) to determine the effect of ageing on the rheological and fatigue properties of bitumen. The results of these studies have shown that the mechanical properties of aged bitumen become more solid-like, as indicated by increased complex modulus and decreased phase angle (Lu and Isacsson Citation2002, Saoula et al. Citation2013, Moreno-Navarro et al. Citation2018). Studying only the stiffness and fatigue behaviour of bitumen cannot directly characterise the degradation of its properties due to ageing, because both stiffness and fatigue life increase with ageing. For instance, at equal stress levels, ageing increases the fatigue life of the bituminous material; however, the result of the fatigue test is in that case unreliable (Van den bergh and Van de Ven Citation2012, Fernández-Gómez et al. Citation2016, Lopez-Montero and Miro Citation2017). However, mangy agencies in US and Europe use only stiffness-based criteria and fatigue tests to classify bitumen for its cracking performance at fresh (unaged) and aged conditions. The stress relaxation ability of bitumen can be considered as an indicator of loss of bitumen durability due to ageing. Stress relaxation is essentially a pointer of bitumen cracking, as a decrease in the ability to relax stress (induced by traffic or thermal loading) due to ageing (Othman et al. Citation1995, Daniel et al. Citation1998, Raad et al. Citation2001) will ultimately lead to pavement cracking.
2. Objectives
The main objective of this study is to investigate the effects of oxidative ageing on the linear viscoelastic material properties, the fatigue and relaxation characteristics of bitumen. An attempt is also made to correlate the crossover modulus of bitumen with its relaxation properties; such a relation could be used to classify bitumen for its ability to resist crack formation by means of routine tests such as the DSR frequency sweep tests.
3. Materials, ageing protocol and experimental method
3.1. Materials
A bitumen with penetration grade 70/100 (1/10 mm), which is one of the most commonly used for the construction of asphalt pavements in the Netherlands, was selected for this study. The bitumen has no polymer or other chemical additive and was supplied from Q8 Kuwait Oil. shows the main physical and rheological properties of the studied bitumen.
Table 1. Specifications of PEN 70/100 at fresh (unaged) state.
3.2. Ageing method
In this study, bitumen films with 2 mm thickness were aged by using two different ageing protocols: oven ageing and PAV (Pressure Ageing Vessel) ageing. Part of the samples were aged in the oven for 20, 40, 80, 160, 320 h at 100°C and atmospheric pressure. To investigate the effect of temperature, other subsets of the samples were oven aged at 50 and 150°C for 40 h. Moreover, the PAV protocol was applied for 40 h and at 100°C and at four different ageing pressures of 5, 10, 15, 20 atm. summarises the various ageing processes that were considered.
Table 2. Ageing programme.
3.3. Experimental methods
An Anton Paar MCR 502 device was used to analyse the linear rheological, fatigue and relaxation properties of the bitumen due to oxidative ageing. At least three repetition tests were done for each ageing condition. Initially, the linear viscoelastic (LVE) strain range of the bitumen samples was determined using amplitude sweep tests.
The rheological properties of bitumen were characterised by means of DSR tests according to NEN-EN 14770. The bitumen samples were tested using a parallel-plates configuration at a stress-controlled model. The frequency sweep tests were performed at five different temperatures (0, 10, 20, 30 and 40°C). During the tests, the frequency varied in a logarithmic manner from 50 to 0.01 Hz. The complex shear modulus and phase angle values were collected during the tests. Master curves of the dynamic shear modulus and phase angle were constructed, in order to determine the viscoelastic behaviour in a wider range of frequencies, at the reference temperature of 20°C.
Considering that the selected control modes in a DSR tests can have a significant influence on the damage behaviour of bitumen (Monismith and Deacon Citation1969, Kim et al. Citation1997, Shen and Carpenter Citation2007, Masad et al. Citation2008), fatigue tests were conducted by applying dynamic shear loading at the temperature of 20°C and at a frequency of 10 Hz under two different control modes, stress-controlled and strain-controlled. The bitumen samples were tested using the parallel-plates configuration with 8 mm plate diameter and 2 mm gap. Based on the results of the amplitude sweep tests, six different stress amplitudes (0.04, 0.05, 0.10, 0.15, 0.20 and 0.25 MPa) and five different strain amplitudes (0.5, 1, 2, 3 and 4%) were applied for each control mode.
The relaxation tests were performed with 1% shear strain in a very short time period (0.04 s) at the beginning, followed by a relaxation period of 100 s. The bitumen samples were tested using the parallel-plates configuration with 8 mm plate diameter and 2 mm gap at 0°C. The shear stress values were collected during the tests. Since the relaxation rate is very fast at the beginning of the test, the frequency of data collection is 100 points every second.
4. Results and discussion
4.1. Frequency sweep tests
At least three replicates at each condition were considered for the frequency sweep tests. The effect of ageing is seen as an increase in the complex shear modulus and a reduction in the phase angle, . Overall, it has been shown that bitumen ageing (as expressed through the complex shear modulus and phase angle) increased for a higher ageing time, temperature and pressure. Nevertheless, temperature was found to be the most influential parameter for ageing, probably because the ageing rate coefficient increases exponentially with temperature based on the Arrhenius equation. Detail on the effect of the ageing parameters on the rheology of the studied bitumen type are discussed in previous studies (Jing et al. Citation2018, Tarsi et al. Citation2018).
Black diagrams, , were plotted to present the rheological changes of bitumen with ageing. Black diagrams are graphs of the complex shear modulus versus the phase angle, in which the frequency and the temperature are eliminated, hence, the data can be presented in one plot without the need to apply the Time–Temperature Superposition (TTS) principle (Airey Citation2002). As ageing progresses, a shift of the Black diagram curves towards lower phase angles is observed; at the same time the shape of the curves changes to a straight line and the curvature reduces. These changes denote a tendency towards a stiffer and less viscous material, which could result to failures such as brittle fracture at low temperatures.
Another interesting observation in is that the glassy modulus () and the equilibrium modulus (
) remains constant for the bitumen at different ageing states. Glassy modulus represents the response at high frequencies or low temperatures, whereas the equilibrium modulus represents the response at low frequencies or high temperatures. These results may indicate that ageing has no effect on the mechanical response of bitumen at extreme conditions (such as extreme high or low temperature conditions). In addition, the value of glassy modulus is in the order of 109, while the equilibrium modulus is in the order of 102, resulting in a difference of seven in their magnitude. This result points out that the typical assumption that the value of
is zero for bituminous materials in the Christensen–Anderson–Marasteanu (CAM) model (Equation (1)) is reasonable (Marasteanu and Anderson Citation1996, Li et al. Citation2006, Cholewinska et al. Citation2018).
(1)
(1) where
is the equilibrium modulus representing the minimum modulus when
,
is glassy modulus representing the maximum modulus when
,
is the crossover frequency at which the elastic component is approximately equal to the viscous component, and
and
are fitting parameters.
To understand deeper the effect of ageing on the Black diagrams, the crossover modulus is studied in this work. Crossover modulus is the complex shear modulus corresponding to the phase angle of 45°, , which denotes that the storage shear modulus is equal to the loss shear modulus. When the phase angle is below 45°, the material has more solid behaviour; when it is higher than 45°, the materials have more fluid behaviour. As shown in , under the same test conditions, more data points appear in the region with phase angle below 45° after ageing, which denotes bitumen has more solid behaviour (elastic response) and less fluid behaviour (viscous response) due to ageing.
The crossover modulus is a special point on the material’s viscoelastic spectrum, which does not depend on the test frequency and temperature. However, ageing has a significant influence on crossover modulus as shown in , as the crossover modulus decreases with ageing. In addition, the dispersion intervals among the replicate samples appear to increase with ageing. This can be attributed to the higher non-homogeneity of the samples as the ageing process evolved. Laboratory ageing was performed by placing the samples in PAV pans and therefore oxygen was diffusing from top downwards, creating thus a stiffness gradient inside the sample. Then, the bitumen was stirred to form a homogeneous sample before it is poured into the DSR disk moulds. As the stiffness gradient is higher at more severe ageing states, the homogeneity of the samples could possibly be poorer and it could explain the higher differences among the tested replicates.
In order to quantify the ageing effect on the crossover modulus (CM) of bitumen, an ageing index is proposed and expressed as the ratio of the CM of the fresh bitumen over the CM of the aged (because of the reduction in crossover modulus with ageing), Equation (2).(2)
(2) where
is the ageing index of crossover modulus,
and
are the crossover modulus of fresh and aged bitumen, respectively. By using Equation (2), the
values of all samples were obtained and plotted in . The results show that the CM ageing index increases with ageing.
4.2. Fatigue tests
Cyclic tests were conducted on three samples at each stress/strain level and ageing state to evaluate the fatigue performance of bitumen. For the fresh bitumen, the results of complex shear modulus vs number of cycles in both control modes are shown .
Figure 6. Complex shear modulus vs number of cycles for bitumen at fresh conditions (unaged state): stress-controlled mode (left) and strain-controlled mode (right).
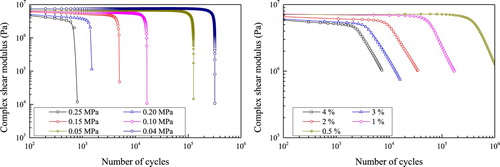
There is an obvious difference between the results of the stress-controlled and strain-controlled modes, as shown in . After certain cycles of loading in the stress-controlled test the complex shear modulus suddenly drops, while the modulus decreases more gradually for the strain-controlled tests. The fatigue criterion is defined as a 50% reduction in the value of the complex shear modulus. Then, based on the concepts of viscoelastic continuum damage (VECD) theory (Jafari and Babazadeh Citation2016), the fatigue life of bitumen can be fitted by Equations (3) and (4).(3)
(3)
(4)
(4)
where is the shear stress,
is the shear strain,
and
are the number of cycles to failure in stress-controlled and strain-controlled respectively, and
,
and
,
are the fitting parameters derived from the experiment of stress-controlled and strain-controlled, respectively. The experimental results of the aged bitumen at various ageing times are fitted according to Equations (3) and (4). The results of the fatigue tests are shown in and the fitting parameters for both control modes are reported in .
Figure 7. Fatigue results of bitumen with various ageing time: stress-controlled mode (left) and strain-controlled mode (right).
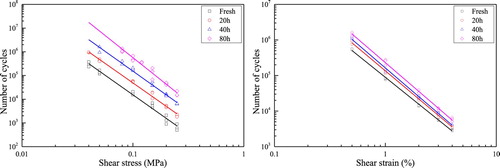
Table 3. Fitting parameters for fatigue results.
shows that the fatigue life increases with ageing. Specifically, as shown in , the fitting parameters and
increase significantly, while the parameters
and
change slightly or not at all with ageing. Based on the VECD concept, when there is no change in the value of the parameter
(or
), larger values of the parameter
(or
) denote that bitumen has better fatigue properties. The fact that ageing seems to increase the bitumen fatigue life is in conflict with the common view that a pavement becomes susceptible to fatigue cracking because of ageing (Airey and Rahimzadeh Citation2004, Ouyang et al. Citation2006, Liu et al. Citation2014, Villegas-Villegas et al. Citation2018). One reason may be that the fatigue damage of a pavement due to ageing is not only due to the cohesive damage within the bitumen but also due to the loss of adhesion between the aggregate and the bitumen. Ageing increases the fatigue life of bitumen itself but it may reduce the adhesive bond strength with the aggregates. Another reason may be the definition of the fatigue criterion as the 50% reduction in the values of complex shear modulus, is not suitable for data analysis of fatigue (Ghuzlan and Carpenter Citation2000, Bonnetti et al. Citation2002, Bhasin et al. Citation2009). It is recommended to develop new methodologies for analysing the fatigue data.
4.3. Relaxation tests
Similarly to the frequency tests, a minimum of three replicate samples for each ageing condition were tested for stress relaxation using the DSR. (left-side graphs) shows the relationship between shear stress and relaxation time with increased ageing time, temperature and pressure. By standardising the initial shear stress to a value of 100%, the residual stress vs relaxation time at different ageing conditions is plotted in (right-side graphs).
Figure 8. Relaxation curves (left) and residual stress curves (right) of PEN 70/100 at different ageing conditions.
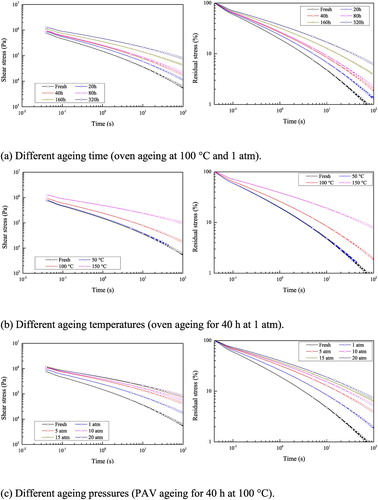
(left) shows that a power law can describe well the relationship between the shear stress and the relaxation time. The relaxation curves move up with ageing, indicating that at the same relaxation time the shear stress of bitumen increases with ageing. In other words, the relaxation modulus increases with ageing. It is obvious, (right), that bitumen ageing decreases the stress relaxation and increases the residual stress. For the fresh bitumen, only 1.03% of the initial shear stress remained after 100 s relaxation, however, more than 6% of initial shear stress remained in the aged sample after relaxation. Especially, for the sample aged at 150°C, about 8% of initial shear stress remained after relaxation. The results show that aged bitumen results to higher residual stresses, suggesting that bitumen will accumulate higher stresses at the same loading level.
In order to further analyse the relaxation properties of aged bitumen, the absolute values of shear stress at 0 and 100 s are plotted in , which denote the stress state of bitumen at the initial and end time of relaxation.
In , the initial shear stress (shear stress at 0 s) of bitumen samples subjected different ageing conditions are in the order of 1000 kPa. The initial shear stress of the most highly aged sample (320 h, 150°C or 20 atm) is about 1.4 times larger than that of fresh bitumen. However, after a relaxation period of 100 s, the shear stress of the 320 h aged sample, the 150°C aged sample and the 20 atm aged sample were still 68.73, 97.29 and 80.63 kPa, respectively, which is more than 10 times higher than that of fresh bitumen. Hence, the residual stresses after the same relaxation time are higher for the aged samples. Due to the fact that there is continuous traffic loading, the relaxation time of bitumen needs to be short to prevent stress accumulation in the pavement. shows the relaxation time when the shear stress got reduced to 50% or 25% of the initial stress.
The relaxation time, at which shear stress reduces to 50% and 25% of the initial stress, increases with ageing. An increase of the relaxation time can be explained by the fact that the viscosity of bitumen increases due to ageing (Rigg et al. Citation2017). For fresh bitumen, the shear stress reduces to 25% of its initial value within one second. However, this time increases for the 320 h and 20 atm aged samples, for which it is 3.28 and 3.76 s, respectively. For the oven-aged bitumen samples 150°C, the relaxation time to reach a 25% decay in stress is 4.58 s. Longer relaxation times denote materials that are more susceptible to accumulate stresses.
To quantify the ageing effect on the relaxation properties of bituminous materials, a relaxation ageing index is calculated as the ratio of relaxation time between aged and fresh bitumen, Equation (5).(5)
(5) where
is the ageing index of relaxation that corresponds to the relaxation time when shear stress reduces to 50% of initial stress,
and
are the relaxation time at which the shear stress gets reduced to 50% of initial stress of aged and fresh bitumen, respectively. By using Equation (3), the
for all samples were plotted in . The results show that the relaxation ageing index increases with ageing.
4.4. Relationship between crossover modulus and relaxation time
A frequency sweep test is the most commonly used rheological characterisation method in the laboratory. It is, therefore, of paramount importance to deduce as many information possible from the master curves or black diagrams to characterise the rheological properties of bitumen, apart from the stiffness and phase angle of the material, such as the stress relaxation of bitumen. For this purpose, an attempt to correlate the crossover modulus of bitumen with its relaxation properties was made, by plotting the against
, as presented in .
shows that there is a good linear relationship between these two parameters for the studied bitumen. The points move from the position of to the top right corner along the blue line due to ageing. Interestingly it appears that this relationship does not depend on the ageing protocol. In other words, different ageing protocols have the same influence on the ageing indexes
and
. Similar observations were made for the relationship between the crossover modulus and the ageing index (Jing et al. Citation2019). Based on Equation (3), the values of
was obtained and the relationship between
and
was added in .
Figure 13. Relationship between the crossover modulus and the stress relaxation
ageing indices at shear stress levels of 50% and 25% of the initial stress.
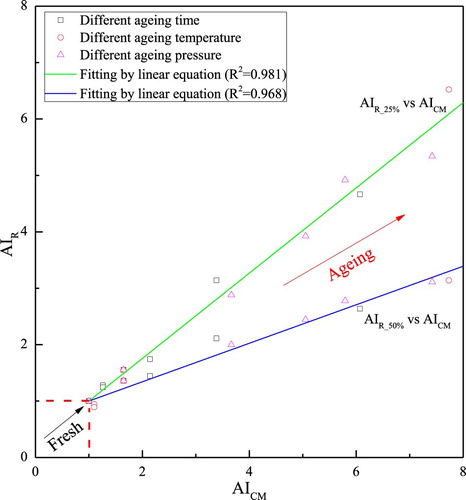
As shown in , although the slope of the fitting line changes depending on the shear stress level, the linear relationship between the ageing index of crossover modulus and stress relaxation remains. This relationship suggests that the reduction in the crossover modulus denotes a reduction in the relaxation properties of the bitumen. Therefore, the crossover modulus obtained through the frequency sweep test can be used as a parameter to express the relaxation properties of bituminous materials.
In this study, however, the established relationship between the crossover modulus and the stress relaxation is based on the experimental results for only one bitumen type. The universality of this relationship and the conditions under which it is valid and can be used for determining the relaxation properties of bitumen still needs to be investigated. The preliminary data for the studied bitumen are promising and more bitumen types will be analysed in the future to validate these findings.
5. Conclusions
The work presented in this paper shows the preliminary results of a broad study on the effect of ageing on the mechanical properties of bitumen and asphalt concrete. This study specifically focuses on the linear viscoelastic material properties, the fatigue and relaxation characteristics of aged bitumen. A series of ageing experiments were performed on 2 mm thickness bitumen films at different ageing time intervals, temperatures and pressures. DSR tests were carried out to determine the changes in the response of aged bitumen.
The results show that studying only the stiffness and fatigue behaviour of bitumen cannot directly characterise the degradation of its properties due to ageing because both stiffness and fatigue life, increase with ageing. The effect of ageing is seen as a shift of the Black diagram curves towards higher stiffness and lower phase angles. Interestingly, both the glass modulus and the equilibrium modulus do not change with ageing; in contrast the crossover modulus reduces with ageing. According to the standard fatigue analysis criteria, it appears that ageing has a positive effect on the fatigue life of bitumen. This observation contradicts field observations and raises questions about the suitability of such criteria. It appears that the fatigue tests can give a false impression of the effects of ageing on bitumen viscoelastic properties.
The relaxation test, however, appears to be more relevant to characterise the ageing effect on bitumen and it is proposed as an indicator of loss of bitumen durability due to ageing. Higher residual shear stresses and longer relaxation times were found for aged bitumen in comparison to those for fresh (unaged) bitumen. Therefore, the relaxation test results suggest that aged bitumen is more susceptible to stress accumulation, as its ability to relax stress decreases, and consequently is more sensitive cracking. Moreover, the values of the relaxation properties increased for extended ageing times and for higher temperatures and pressure. Among the various ageing parameters, temperature appears to be the most influential for ageing.
On the basis of the relaxation and the frequency sweep test results, a linear relationship is found between the crossover modulus ageing index and the relaxation ageing index for the studied bitumen. Such a relation has potential to be used to classify bitumen for its ability to resist crack formation by means of routine tests such as the DSR frequency sweep tests. This study was limited in terms of the bitumen types used; only one bitumen was tested. As a result, more bitumen types will be analysed in the future to validate the established relationships and the findings of this study.
Disclosure statement
No potential conflict of interest was reported by the authors.
Additional information
Funding
References
- Airey, G. D, 2002. Use of black diagrams to identify inconsistencies in rheological data. Road Materials and Pavement Design, 3 (4), 403–424. doi: 10.1080/14680629.2002.9689933
- Airey, G. D., and Rahimzadeh, B., 2004. Combined bituminous binder and mixture linear rheological properties. Construction and Building Materials, 18 (7), 535–548. doi: 10.1016/j.conbuildmat.2004.04.008
- Bhasin, A., et al., 2009. Quantitative comparison of energy methods to characterize fatigue in asphalt materials. Journal of Materials in Civil Engineering, 21 (2), 83–92. doi: 10.1061/(ASCE)0899-1561(2009)21:2(83)
- Bonnetti, K., Nam, K., and Bahia, H., 2002. Measuring and defining fatigue behaviour of asphalt binders. Transportation Research Record, 1810, 33–43. doi: 10.3141/1810-05
- Cholewinska, M., Iwański, M., and Mazurek, G., 2018. The impact of ageing on the bitumen stiffness modulus using the CAM model. Baltic Journal of Road and Bridge Engineering, 13 (1), 34–39. doi: 10.3846/bjrbe.2018.386
- Daniel, J. S., Kim, Y. R., and Lee, H. J., 1998. Effects of aging on viscoelastic properties of asphalt-aggregate mixtures. Transportation Research Record, 1630, 21–27. doi: 10.3141/1630-03
- Durrieu, F., Farcas, F., and Mouillet, V., 2007. The influence of UV aging of a Styrene/butadiene/Styrene modified bitumen: comparison between laboratory and on site aging. Fuel, 86 (10), 1446–1451. doi: 10.1016/j.fuel.2006.11.024
- Fernández-Gómez, W. D., et al., 2016. Effects of environmental aging and ultra violet radiation on asphalt mixture dynamic modulus, permanent deformation and fatigue life. Revista Facultad de Ingeniería Universidad de Antioquia, (80), 89–96.
- Ferry, J.D, 1980. Viscoelastic properties of polymers. Toronto, Canada: John Wiley & Sons.
- Gawel, I. and Baqinska, K., 2004. Effect of chemical nature on the susceptibility of asphalt to aging. Petroleum Science and Technology, 22 (9), 1261–1271. doi: 10.1081/LFT-200034074
- Ghuzlan, K. and Carpenter, S., 2000. Energy-derived, damage-based failure criterion for fatigue testing. Transportation Research Record: Journal of the Transportation Research Board, 1723, 141–149. doi: 10.3141/1723-18
- Hofko, B., et al., 2016. Effect of short-term ageing temperature on bitumen properties. Road Materials and Pavement Design, 18, 108–117. doi: 10.1080/14680629.2017.1304268
- Hu, J., et al., 2018. Effect of ultraviolet radiation in different wavebands on bitumen. Construction and Building Materials, 159, 479–485. doi: 10.1016/j.conbuildmat.2017.10.117
- Isacsson, U. and Zeng, H., 1997. Relationships between bitumen chemistry and low temperature behaviour of asphalt. Construction and Building Materials, 11 (2), 83–91. doi: 10.1016/S0950-0618(97)00008-1
- Jafari, M. and Babazadeh, A., 2016. Evaluation of polyphosphoric acid-modified binders using multiple stress creep and recovery and linear amplitude sweep tests. Road Materials and Pavement Design, 17 (4), 859–876. doi: 10.1080/14680629.2015.1132631
- Jing, R., et al., 2018. Chemo-mechanics of ageing on bitumen materials. Transportation Research Board 97th Annual Meeting: Washington DC, United States, 7–11 Jan.
- Jing, R., et al., 2019. Ageing effect on chemo-mechanics of bitumen. RILEM Bookseries, 20, 71–76. doi: 10.1007/978-3-030-00476-7_12
- Kandhal, P. S. and Koehler, W. C., 1984. Significant studies on asphalt durability: Pennsylvania experience. Transportation Research Record, 999, 41–50.
- Kim, Y.R., Lee, H. J., and Little, D.N., 1997. Fatigue characterization of asphalt concrete using viscoelasticity and continuum damage theory (with discussion). Journal of the Association of Asphalt Paving Technologists, 66, 520–569.
- Kliewer, J. E., Bell, C. A., and Sosnovske, D. A., 1995. Investigation of the relationship between field performance and laboratory aging properties of asphalt mixtures, engineering properties of asphalt mixtures and the relationship to their performance. ASTM International, 3–20.
- Lesueur, D., 2009. The colloidal structure of bitumen: consequences on the rheology and on the mechanisms of bitumen modification. Advances in Colloid and Interface Science, 145, 42–82. doi: 10.1016/j.cis.2008.08.011
- Li, X., et al., 2006. Evaluation of field aging effects on asphalt binder properties. Road Materials and Pavement Design, 7 (sup1), 57–73. doi: 10.1080/14680629.2006.9690058
- Liu, X., et al., 2014. Fatigue properties of layered double hydroxides modified asphalt and its mixture. Advances in Materials Science and Engineering, 2014, 1–6.
- Lopez-Montero, T. and Miro, R., 2017. Ageing and temperature effect on the fatigue performance of bituminous mixtures. Materiales de Construcción, 67, 327.
- Lu, X. and Isacsson, U., 2002. Effect of ageing on bitumen chemistry and rheology. Construction and Building Materials, 16 (1), 15–22. doi: 10.1016/S0950-0618(01)00033-2
- Lu, X., Talon, Y., and Redelius, P., 2008. Ageing of bituminous binders-laboratory tests and field data. in Proceedings of the 4th Eurasphalt & Eurobitume Congress, Copenhagen: 21–23.
- Marasteanu, M. and Anderson, D., 1996. Time temperature dependency of asphalt binders- an improved model. Journal of the Association of Asphalt Paving Technologists, 65, 407–448.
- Masad, E., et al., 2008. A unified method for the analysis of controlled-strain and controlled-stress fatigue testing. International Journal of Pavement Engineering, 9 (4), 233–246. doi: 10.1080/10298430701551219
- Mastrofini, D. and Scarsella, M., 2000. The application of rheology to the evaluation of bitumen ageing. Fuel, 79 (9), 1005–1015. doi: 10.1016/S0016-2361(99)00244-6
- Miró, R., et al., 2015. Effect of ageing and temperature on the fatigue behaviour of bitumen. Materials and Design, 86, 129–137. doi: 10.1016/j.matdes.2015.07.076
- Monismith, C.L. and Deacon, J.A., 1969. Fatigue of asphalt paving mixtures. Transportation Engineering Journal of ASCE, 95 (2), 317–346.
- Moreno-Navarro, F., et al., 2018. Fatigue cracking in asphalt mixtures: the effects of ageing and temperature. Road Materials and Pavement Design, 19 (3), 561–570. doi: 10.1080/14680629.2018.1418717
- Nie, F., et al., 2018. Oil sand pyrolysis: Evolution of volatiles and contributions from mineral, bitumen, maltene, and SARA fractions. Fuel, 224, 726–739. doi: 10.1016/j.fuel.2018.03.069
- Othman, A., Figueroa, L., and Aglan, J., 1995. Fatigue behaviour of styrene-butadiene-styrene modified asphaltic mixtures exposed to low-temperature cyclic aging. Transportation Research Record, 1492, 129–134.
- Ouyang, C., et al., 2006. Improving the aging resistance of asphalt by addition of zinc dialkyldithiophosphate. Fuel, 85 (7), 1060–1066. doi: 10.1016/j.fuel.2005.08.023
- Petersen, J.C, 1984. Chemical composition of asphalt as related to asphalt durability: state of the art. Transportation Research Record, 999, 13–30.
- Petersen, J.C, 2009. A review of the fundamentals of asphalt oxidation: chemical, physicochemical, physical property, and durability relationships. Transportation Research E-Circular (E-C140), 1–78.
- Raad, L., Saboundjian, S., and Minassian, G., 2001. Field aging effects on fatigue of asphalt concrete and asphalt-rubber concrete. Transportation Research Record, 1767, 126–134. doi: 10.3141/1767-16
- Rigg, A., et al., 2017. Non-isothermal kinetic analysis of reversible aging in asphalt cements. Road Materials and Pavement Design, 18, 185–210. doi: 10.1080/14680629.2017.1389070
- Saoula, S., et al., 2013. Analysis of the rheological behavior of ageing bitumen and predicting the risk of permanent deformation of asphalt. Materials Sciences and Applications, 4, 312–318. doi: 10.4236/msa.2013.45040
- Shen, S. and Carpenter, S., 2007. Development of an asphalt fatigue model based on energy principles. Asphalt Paving Technology-Proceedings, 76, 525.
- Siddiqui, M. N. and Ali, M. F., 1999. Investigation of chemical transformations by NMR and GPC during the laboratory aging of Arabian asphalt. Fuel, 78 (12), 1407–1416. doi: 10.1016/S0016-2361(99)00080-0
- Soenen, H., Lu, X., and Laukkanen, O.-V., 2016. Oxidation of bitumen: molecular characterization and influence on rheological properties. Rheologica Acta, 55 (4), 315–326. doi: 10.1007/s00397-016-0919-6
- Struik, L.C.E., 1977. Physical aging in amorphous polymers and other materials (doctoral thesis). Delft University of Technology.
- Tarsi, G., et al., 2018. Effects of different aging methods on chemical and rheological properties of bitumen. Journal of Materials in Civil Engineering, 30 (3), 04018009. doi: 10.1061/(ASCE)MT.1943-5533.0002206
- Van den bergh, W. and Van de Ven, M. F. C., 2012. The influence of ageing on the fatigue and healing properties of bituminous mortars. Procedia-Social and Behavioral Sciences, 53, 256–265. doi: 10.1016/j.sbspro.2012.09.878
- Villegas-Villegas, R. E., et al., 2018. Analysis of asphalt oxidation by means of accelerated testing and environmental conditions. Transportation Research Record, 2672 (28), 244–255. doi: 10.1177/0361198118777630