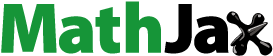
ABSTRACT
High modulus asphalt concrete (HMAC) mixtures are produced using hard grade binders or modified bitumen and are known to have exceptional resistance towards rutting and fatigue. Due to the similarity between hard binder and aged reclaimed asphalt (RA) binder, HMAC mixtures have great potential to incorporate higher percentages of RA material. Here we present a study evaluating the performance of HMAC mixtures incorporating high content of RA material. Both hard grade binder and polymer modified bitumen (PMB) were used for all the mixtures with RA content varying from 0% to 70%. The laboratory performance of mixtures was examined using wheel tracking test, semi-circular bend test, thermal stress restrained specimen test, water sensitivity test and four-point bending test. The results demonstrated that it is possible to develop HMAC mixtures with satisfactory performance using RA content up to 70%, by using PMB binder. The mixtures produced using PMB binder outperformed conventional hard grade binder mixtures especially for use in regions with extremely cold winters.
1. Introduction
High modulus asphalt concrete (HMAC) originated in France in the eighties, where it was known as Enrobés a Module Élevé (EME) [AFNOR Citation1999a] when used in base/binder course and known as Bitumineux Beton Module Élevé [AFNOR Citation1999b] when used as thin layer in wearing course. HMAC mixtures are either produced using a hard grade bitumen (Capitão and Picado-Santos Citation2006, Espersson Citation2014, Lee et al. Citation2007, Miró et al. Citation2011, Sybilski et al. Citation2010) or using modified binders (Geng et al. Citation2013, Ma et al. Citation2015, Zou et al. Citation2017). The binders required for HMAC mixtures show much higher complex modulus and viscosity at elevated temperatures compared to conventional bitumen (Espersson Citation2014). The high content of bitumen and smaller air voids structure in HMAC assure better workability, fatigue durability and water resistance (Sybilski et al. Citation2010). HMAC mixtures are normally required to have a dynamic modulus higher than 14,000 MPa at 15°C test temperature and 10 Hz frequency as per French specification (Capitão and Picado-Santos Citation2006, Ma et al. Citation2015). The SPENS Citation2009 specifications for HMAC mixtures require a minimum stiffness of 14,000 MPa at 10°C test temperature and 10 Hz frequency.
Due to its high dynamic modulus, HMAC pavements can reduce the thickness of the entire road structure by 30–35% (Brosseaud et al. Citation2013) and thickness of base layer by around 25% (Espersson Citation2014). The binders used in HMAC have stiffness similar to that of aged binder in reclaimed asphalt (RA) material. For this reason, the HMAC mixtures are expected to incorporate higher percentages of RA material. Inclusion of RA material into AC (asphalt concrete) type mixtures has often been reported to increase the resistance to rutting, because of the aged binder present in the RA material (Zaumanis et al. Citation2018, Rathore et al. Citation2019). This benefit might not be present for HMAC mixtures as it already offer better resistance towards rutting failure (Espersson Citation2014, Ma et al. Citation2015, Zou et al. Citation2015, Zou et al. Citation2017) and thus RA bitumen might not necessarily increase the viscosity of the final binder blend.
The hard grade binder makes HMAC mixtures highly susceptible to low temperature cracking failure (Geng et al. Citation2013, Rys et al. Citation2017). The incorporation of RA material into HMAC mixtures can further reduce the thermal and fatigue cracking resistance especially for regions with cold winters. The studies have also reported a reduction in thermal and cracking resistance on incorporation of RA material (Miró et al. Citation2011, Ma et al. Citation2016). Polyolefin modifiers have been used in the past to improve the low temperature cracking resistance and fatigue resistance in HMAC mixtures (Judycki et al. Citation2015, Zou et al. Citation2017). The HMAC mixture containing polymer modified bitumen (PMB) have also shown rutting resistance superior to hard grade binders (Haritonovs et al. Citation2016). In general, significant efforts have been made in past to study the performance of HMAC mixtures containing RA material. However, the current state of art indicates the concern towards low-temperature cracking and fatigue cracking of HMAC mixtures especially for regions with cold winters. To address the above concerns and considering the variability of RA material source and binder, the performance of HMAC needs to be evaluated on a mixture to mixture basis. Moreover, the benefits of polymer modified binders compared to hard grade binders, in enhancing the performance of HMAC and ability to incorporate high RA percentages in mixture needs to be investigated.
2. Objective
The overall objective of this study was to evaluate the performance of high modulus asphalt concrete mixtures containing high content of reclaimed asphalt material and to examine the effect of PMB compared to conventional hard grade binder on mixture properties. The scope of this study included:
Design of high modulus asphalt concrete mixtures containing various percentages of reclaimed asphalt material using SBS (styrene-butadiene-styrene) modified binder and conventional hard grade binder.
Evaluating the effect of adding RA material on rutting and fatigue resistance of mixtures using wheel tracking test and four point bending test, respectively.
Determination of water sensitivity of mixtures using indirect tensile strength test.
Investigation of low temperature and intermediate temperature cracking resistance of HMAC mixtures using thermal stress restrained specimen test and semi-circular bend test respectively.
3. Material and methods
In this study, eight different mixtures were produced by considering four contents of RA material (0%, 25%, 50% and 70%) and using two types of binders (PMB25/55-80 and B20/30). The rutting behaviour of mixtures was evaluated using the wheel tracking test. To determine the low and intermediate temperature cracking resistance, thermal stress restrained specimen test and semi-circular bend test were conducted. In addition, water sensitivity evaluation was also carried out for all the mixtures using indirect tensile strength test.
3.1. Materials
RA material originating from Latvia was collected after processing at the asphalt plant. This particular RA material had a binder content of 4.85% and penetration of 23 × 0.1 mm. The angularity of fine aggregates (ECS) for RA material determined according to EN 933-6 was 28. Four sizes of granite aggregates along with one natural sand and filler material were obtained from a local supplier. The angularity of fine aggregates (ECS) for the granite and natural sand were 38 and 27, respectively. Two binder types, including one conventional hard grade binder (B20/30) and one polymer modified bitumen (PMB 25/55-80) were used in this study. The PMB binder was produced using SBS (styrene-butadiene-styrene) modifier and the polymer content was in range of 6.5–7.0% by mass of bitumen. As shown in , the properties of RA binder are similar to B20/30 binder, which indicates that RA binder could be used to replace the high modulus binder in HMAC mixtures.
Table 1. Recovered RA binder and virgin binder properties.
3.2. Methods
3.2.1. Mix design
All mixtures were designed to target the HMAC-16 aggregate grading requirements according to SPENS Citation2009 specifications as shown in . The description of all the mixtures produced as part of this study is described in . for simplification. The components of virgin aggregates were adjusted to maintain the gradation of all the RA content mixtures as shown in . HMAC mixtures containing 0%, 25% and 50% RA content were designed with 4.8% binder content while 70% RA mixtures were designed with 4.5% binder content. The RA content is expressed as weight % of total aggregates. In this study, full RA binder activation was assumed, and accordingly the amount of the virgin binder was added to each mixture.
Table 2. Description of all the mixtures produced in this study.
Table 3. Various components of mix design and their proportion in mixtures.
To prepare the mixtures in the laboratory, all the materials were heated to a temperature of 150°C in the oven. The materials were then mixed for 5 min in the laboratory mixer. The marshall samples were compacted at 145°C using a standard impact hammer by applying a compaction effort of 50 blows on each side. The volumetric properties of each mixture were determined according to EN 12697-8. Marshall test was conducted to determine marshall stability and flow value following the procedure of EN 12697-34. The volumetric properties and marshall test results are given in . The air voids observed in marshall specimens were used targeted for slabs prepared using roller compactor according to EN 12679-33.
Table 4. Volumetrics analysis and marshall test results.
3.2.2. Wheel tracking test
The incorporation of RA material had generally increased the rutting resistance of mixtures due to presence of stiff binder. Though, this benefit might not be observed for HMAC mixtures as here already a hard grade binder is used. Hence, wheel tracking test was conducted for mixtures according to EN 12679-22. A load of 700 N was applied using rubber tire of 200 mm diameter and 50 mm width. A testing temperature of 60°C was selected for the rutting test to fulfil the requirements of SPENS Citation2009 specifications. The test was run for 10,000 load cycles and rut depth was measured using two linear variable deformation transducers (LVDT). A single specimen was tested for each mixture type. The wheel tracking slope was also calculated according to EN 12679-22 as follows:
(1)
(1) where WTSAIR is the wheel-tracking slope per 103 load cycles in mm, d5000, d10,000 are the rut depths in mm after 5000 and 10,000 load cycles, respectively.
3.2.3. Thermal stress restrained specimen test (TSRST)
HMAC mixtures are highly susceptible to low temperature cracking and incorporation of RA material can further increase the thermal cracking tendency. Therefore, it becomes extremely important to evaluate the low-temperature performance of HMAC mixtures especially for countries like Latvia, where the winters are extremely cold. In this study, thermal stress restrained specimen test (TSRST) was conducted according to EN 12697-46 to evaluate the low temperature cracking performance of mixtures. The principal of the test is to keep the length of the specimen constant during the cooling process until the sample cracks due to thermal tensile stress. The prismatic specimens were obtained by sawing the compacted slabs to a final height of 160 mm and a width of 50 mm. For conducting the test, the prismatic specimens were glued to two aluminium plates and mounted in a load frame in the environmental chamber. The test starts at 20°C and the temperature is lowered at a rate of 10°C/hour until failure. Two repetitive samples were tested for each mixture type and the average value of two was reported.
3.2.4. Semi-circular bending test
The highly stiff RA material may increase the tendency of fracture failure in the HMAC mixtures. Therefore, the semi-circular bending (SCB) test was used to investigate the artificial crack propagation mixtures and compare the cracking resistance of asphalt mixtures produced with different binder and RA contents. This test is used as a performance indicator of intermediate temperature cracking resistance. SCB test was performed according to EN 12697-44 at 0°C temperature. For the preparation of sample, 150 mm cores were drilled from slabs and were sliced into half to obtain semi-circular samples polished to the required height of 50 mm. A notch of 10 mm length was cut at the centre using the saw to control the crack initiation point. The specimens were loaded at a constant deformation rate of 5 mm/min until the fracture failure and the load vs deflection curve is recorded. Fracture toughness is then calculated from Equationequation 2(2)
(2) . Four repetitive samples were utilized for each of the mixtures.
(2)
(2) where KIc – fracture toughness, N/mm3/2 W– height of specimen, mm σmax – maximum stress, N/mm2 f (a/W) – geometric factor of specimen (5.956).
3.2.5. Water sensitivity
The water sensitivity of the mixtures was determined according to EN 12697-12. In this test, 100 mm diameter cylindrical samples were produced using marshall compactor by applying 35 blows from each side. The set of specimens were divided into two equally sized subsets. Half of the samples were kept dry at room temperature and the other half were conditioned in water bath at 40°C for 72 h. The samples were conditioned for 3 h at 22°C before the actual test. The indirect tensile strength test was conducted according to EN 12697-23 at a loading speed of 50 mm/min and maximum load was recorded. The indirect tensile strength ratio (ITSR) was calculated as the ratio of wet to dry specimen and expressed in percentage.
3.2.6. Four point bending test
The higher content of high modulus binder used in HMAC mixtures makes these mixtures resistant towards fatigue cracking. However, the inclusion of high content of RA material may reduce the fatigue resistance of asphalt mixtures. To evaluate the fatigue performance of HMAC mixtures, the four-point bending test was performed according to EN 12697-24. For this test, prismatic shaped specimens were obtained by sawing the laboratory compacted slabs to the required dimensions. This test was conducted in strain-controlled mode tests at the loading frequency of 10 Hz. The specimens were subjected to a sinusoidal loading at strain amplitude in the range of 50–400 µm/m. Before testing, all the specimens were conditioned at testing temperature for at least 2 h and the test was conducted at 10°C. The fatigue cycles cause microcracking of the specimen and decrease in stiffness modulus of the beam. The test is run until the stiffness modulus reached half of its initial value or until the specimen broke. Fatigue life (Nf) is defined as the number of cycles required to reach the stiffness modulus in a specimen to 50% of its initial value. The test was also run at 50 µm/m amplitude for all the mixtures until 1000 cycles to measure the stiffness modulus of HMAC mixtures as required in SPENS Citation2009 specifications. The fatigue line was drawn by plotting the number of fatigue cycles to failure corresponding to different strain amplitudes. The strain amplitude corresponding to 106 cycles was also computed from the fatigue line.
4. Results and discussion
4.1. Rutting
Wheel tracking test results are of high importance for HMAC mixtures, because they are generally intended for high traffic intensity roads. . demonstrates wheel tracking slope results and all the mixes fulfil the requirement of maximum 0.1 mm rut depth per 1000 load cycles as per SPENS Citation2009 specifications. For PMB binder, an increase in RA content resulted in reduced resistance towards rutting for PMB mixtures. For B20/30 binder, B25 and B70 mixtures showed higher resistance than B0 and B50 mixtures, respectively. However, the difference is only slight and can be attributed to test variability. Overall, the addition of RA material reduced the rutting resistance of the mixtures. As shown in , the flow coefficient of fine aggregates did not differ much for all RA% mixtures. Therefore, it is hypothesized that the main reason for the worse rutting resistance of the RA mixtures could be the composition of aggregates in RA material which include gravels, dolomites and granites.
Proportional rut depth in wheel tracking test is shown in . Overall, it can be seen in that all the mixtures fall slightly outside the minimum requirement of 3% as per SPENS Citation2009 specifications. The ranking of the mixtures in proportional rut depth is the same as that in the wheel tracking slope. PMB0 is the closest to passing the requirement while the PMB70 mixture showed the poorest performance.
The proportional rut depth demonstrates the total rut depth at the end of the test including both the compaction and rutting phases of the test while the slope is calculated based on the development of the rut between 5000 and 10,000 load cycles. Since the slope satisfies the requirement for all the mixtures while the proportional rut depth does not, it can be inferred that the consolidation characteristics at the beginning of the test are not satisfactory for all mixtures. In other words, the development of the rut until 5,000 load cycles is too rapid. It can be stated that mixtures are subject to excessive compaction at the beginning of the test before the aggregates interlock and then a satisfactory wheel tracking resistance is achieved (measured as WTT slope). The possible reason for this behaviour could be insufficient compacting effort of slabs that failed to form a dense aggregate interlocking. In this case, an increased slab compaction effort in laboratory may reduce the initial consolidation due to lower air voids. Another option could be to change the gradation of aggregates in the mixture.
4.2. Fracture toughness
Fracture toughness of the mixtures was determined using Semi-circular bend test. The test results are depicted in . There is no formal fracture toughness requirement for HMAC mixtures, but an earlier study determined that a typical fracture toughness for AC-16 mixtures used in Latvia is between 28 N/mm3/2 for mixtures with unmodified bitumen and 43 N/mm3/2 for PMB modified mixtures (Zaumanis & Valters Citation2020). The AC-16 grading curve requirements are the same as HMAC-16, thus it can be reasonably assumed that aggregate grading does not play a crucial role in comparing the AC and HMAC mixture fracture resistance and the main impact would come from the bitumen. It can be observed in . that the results for the HMAC are in a relatively similar range as those of the earlier tested AC mixtures.
Figure 4. SCB fracture toughness of HMAC mixtures. The error bars report one standard deviation from mean.
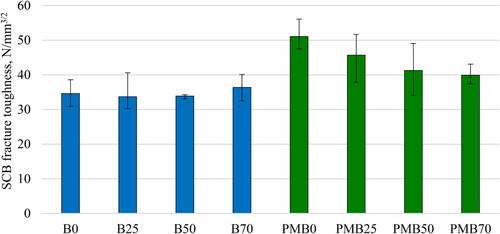
For the mixtures comprising of B20/30 bitumen the fracture toughness does not change with an increase in RA content. A one-way analysis of variance was conducted using a level of significance (α = 0.05). The p-values < 0.05 indicate a significant difference between means of test results. The analysis shows that B0 and PMB0 were found to be statistically different (p-value = 0.001) from each other along with B25 and PMB25, which had significant difference in fracture toughness (p-value = 0.021). Clearly, the addition of PMB binder significantly increased the fracture toughness for 0% and 25% RA content mixture. As stated earlier, this situation was similar to the previous study on AC mixtures where the use of PMB resulted in increased fracture toughness of mixtures (Zaumanis & Valters Citation2020). For 50% and 70% RA content mixtures, there was no significant difference between the conventional binder and PMB binder (p-values > 0.05). This is because these mixtures contain very low virgin binder content and most of the binder requirement is fulfilled by RA binder. It seems obvious that the results are most sensitive to the PMB content in the mixtures when all other things are equal. Since the RA does not contain any polymers, the proportion of PMB is reducing in these mixtures and along with it – the fracture toughness. If the target would be to maximize the fracture toughness, the best option would be to use even higher polymer content for the high RA content mixtures.
4.3. Low temperature cracking
This study was carried out in Latvia which is a relatively cold country and therefore low temperature cracking resistance of such mixtures is extremely important. Recently, a requirement for TSRST cracking resistance has been introduced in the SPENS Citation2009 specifications. The minimum required value for base and binder courses is −20°C.
Low temperature cracking test results for HMAC mixtures are summarized in . It can be seen that none of the mixtures with B20/30 bitumen reach the minimum low temperature cracking resistance requirement, even the 0% RA mixture. The mixtures with PMB bitumen, on the other hand, fulfilled the requirement in all cases. The cracking temperature decreases on incorporation of polymer modified binder with PMB0 showing a cracking temperature of −27.3°C which is 10°C lower than that of conventional binder which is −17.3°C. Even at 70% RA content, PMB mixture outperformed the conventional binder, improving the cracking resistance by −7.1°C. Therefore, it is clear that HMAC mixtures with unmodified hard bitumen are not suitable for regions with extremely cold winters like Latvia.
Figure 5. TSRST cracking temperatures for HMAC mixtures. The error bars report the range of cracking temperature.
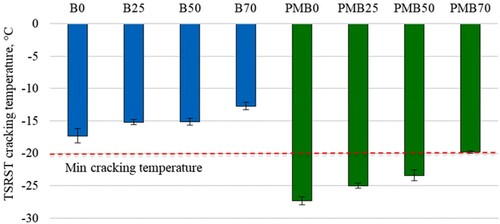
For countries with extremely cold winters, such as Latvia and Poland, it is strongly recommended to use PMB in the design of HMAC mixtures. Another observation from the TSRST cracking test results is that the increase in RA content reduces the resistance to low temperature cracking regardless of the type of bitumen. It is for these reasons that it is recommended to include TSRST cracking resistance requirement as part of the HMAC specifications in Latvia.
4.4. Water sensitivity
The water sensitivity test results for all samples are illustrated in . The requirement in Latvia and most other countries for indirect tensile strength ratio is 80%. It can be seen that all the mixtures pass this requirement. The samples containing RA on average have somewhat higher water sensitivity compared to the reference samples without RA. This has been reported in many studies (Al-Swailmi and Terrel Citation1992, Mogawer et al. Citation2012). The likely reason is that the RA is coated with bitumen twice – once during the original mixture preparation and for the second time during recycling. If the pavement from which RA is milled did not have any moisture damage, it is likely that also the new mixture will not have any moisture damage problems.
In some counties experiencing extreme winters, the water sensitivity test is modified to include freeze-thaw cycles. Though, this study did not consider the freeze-thaw cycles, this could be evaluated for future studies.
The change in RA content did not significantly affect the dry indirect tensile strength in both B20/30 binder mixtures (p-value = 0.07) as well as PMB binder mixture (p-value = 0.651).
4.5. Fatigue cracking
4.5.1. Fatigue life
This is an important test for HMAC mixtures as incorporation of a high amount of RA material may be reducing the fatigue cracking resistance. The results of the four-point bending test at different strain amplitudes were used to develop a relationship between the number of fatigue cycles and strain amplitude as illustrated in . Clearly, all the PMB mixtures show higher cycles to fatigue failure compared to the mixtures with B20/30 binder, except for the 70% RA. An increase in RA content showed a significant reduction in fatigue resistance for the PMB mixtures. The increased fatigue life in PMB0, PMB25 and PMB50 mixtures may be a result of highly elastic PMB binder. For the 70% RA mixture, the amount of virgin binder was low and therefore the effect of PMB binder was not significant. It can be inferred that upto 50% RA content, PMB binder can offer significant advantages over conventional binder by increasing the fatigue life of pavement. It is recommended to use higher polymer content bitumen when increasing RA content above 50% in order to observe significant benefits from elastic PMB binder.
The fatigue equations were developed by making a linear regression between the natural logarithm of number of fatigue cycles (Nf) and natural logarithm of initial strain amplitudes (ϵ) at 100th cycle. A typical fatigue relationship can be expressed as Equation (3).
(3)
(3) where a1 and a2 are regression coefficients.
The fatigue relationships developed in all mixtures along with R2 values and regression coefficients are shown in . A good correlation (R2 > 0.93) was observed for all the mixes except the PMB25 mixture. The lower R2 coefficients in this mixture could be due to the variability of test results. The slope of the fatigue curve is represented by the constant a1 and the intercept is represented by a2. These fatigue equations from were used to compute the strain level corresponding to 106 cycles (ϵ6). The SPENS Citation2009 specification requires a minimum ϵ6 value of 130 µm/m for HMAC mixtures. . shows that all the mixtures fulfilled the minimum requirement of ϵ6 value. The ϵ6 values for all PMB mixes were significantly higher than the B20/30 mixtures. Moreover, with an increase in RA content, ϵ6 value was found to be reduced. For 70% RA mixture, the benefit of PMB binder could not be observed as a result of low virgin binder content. Overall, it can be inferred that the incorporation of RA material reduces the fatigue resistance of HMAC mixtures. However, PMB binder can be used to increase the resistance towards fatigue cracking especially for regions with cold winters where this type of failure is predominant.
Table 5. Fatigue equations with R2 values and constants.
4.5.2. Stiffness modulus
The four-point bending test was carried out at 50 µm/m amplitude to determine the stiffness modulus of mixtures at 10°C temperature and loading frequency of 10 Hz. This test was run up to 1000 fatigue cycles and the stiffness modulus obtained at 100th cycle was determined as shown in . The minimum stiffness modulus requirement for HMAC mixtures is 14,000 MPa according to the SPENS Citation2009 specification and in most of the countries. The stiffness modulus results show that all the mixtures, except the PMB without RA, comply with this requirement. The PMB mixture without RA material is thus not stiff enough for use as an HMAC and the addition of RA in fact serves to increase the stiffness modulus to the desirable level. The effect of increasing RA content was not observed on stiffness modulus values for B20/30 mixes. For PMB mixtures, stiffness modulus increased with an increase in RA content due to hard binder available from RA material.
5. Conclusions
In this study, the laboratory performance of high modulus asphalt mixtures containing high content of RA material was evaluated. Four RA contents (0%, 25%, 50% and 70%) and two binders including, one polymer modified bitumen (PMB 25/55-80) and one conventional hard grade binder (B20/30) were considered. The mixtures were evaluated using the wheel tracking test, thermal stress restrained specimen test, water sensitivity test, semi-circular bend test and four point bending test. Based on the analysis of results, the following conclusions were drawn:
The HMAC-16 gradation and volumetric requirements were fulfilled for all contents of reclaimed asphalt (RA) material. The RA binder properties were similar to the B20/30 virgin binder properties and therefore high RA contents can be used to fulfil the hard binder requirement for HMAC mixtures.
The wheel tracking test showed that wheel tracking slopes were satisfactory for all mixtures, but all the mixtures failed in the proportional rut depth criteria. The rutting resistance of PMB mixtures was found to be superior to B20/30 binder mixtures. The addition of RA material reduced the rutting resistance of HMAC mixtures due to the presence of round aggregates in the RA material.
Thermal stress restrained specimen test results demonstrated that none of the mixtures containing B20/30 bitumen fulfil the low-temperature cracking requirement. Therefore, conventional hard grade bitumen type is not recommended for use in HMAC mixtures produced in regions with cold winters. On the other hand, all the PMB mixtures outperformed B20/30 bitumen mixtures by considerably reducing the thermal cracking temperature.
All the mixtures satisfied the water sensitivity minimum requirements. The RA mixtures even had slightly higher resistance to moisture damage than the virgin mixtures. The tensile strength was found to be similar for all the mixtures.
The results of the semi-circular bend test of HMAC mixtures were similar to AC type mixtures used in Latvia. The incorporation of PMB binder increased the fracture toughness for 0% and 25% RA content mixtures, however, the effect of PMB binder was found to be negligible for 50% and 70% RA content mixtures.
All the HMAC mixtures passed the minimum requirement in fatigue criteria. The addition of RA material reduced the fatigue resistance of HMAC mixtures. The incorporation of PMB binder significantly improved the fatigue resistance for mixture up to 50% RA content. This indicates PMB binder can be used in HMAC mixtures where fatigue cracking is a predominant form of failure.
All mixtures, except the PMB mixture without RA, passed the stiffness modulus requirement. Addition of RA increased the stiffness modulus, which is favourable since because it allowed to fulfil the requirements for HMAC mixtures. The increased stiffness modulus may also be able to reduce the thickness of asphalt base layer due to lower stress levels in the pavement.
This study demonstrated that it is possible to use high contents of RA material with confidence to develop HMAC mixtures that provide satisfactory performance. For RA content above 50%, significant benefits could be observed by using PMB binder with high polymer content. It is also recommended to use PMB binder for HMAC mixtures in regions with cold winters to ensure increased resistance towards low temperature and intermediate temperature cracking. A combination of conventional hard binder and PMB could be investigated in future studies as it may help to fulfil the stiffness modulus requirements for HMAC mixtures.
Disclosure statement
No potential conflict of interest was reported by the author(s).
Additional information
Funding
References
- Al-Swailmi, S. and Terrel, R.L., 1992. Evaluation of water damage of asphalt concrete mixtures using the environmental conditioning system (ECS). Asphalt Paving Technology, 61, 405–445.
- Brosseaud, Y., et al., 2013. High modulus asphalt mixes with high rate of RA : what does it happen ? Congrès Eurobitume Eurasphalt, (EE2012).
- Capitão, S. and Picado-Santos, L., 2006. Applications, properties and design of high modulus bituminous mixtures. Road Materials and Pavement Design, 7 (1), 103–117. doi:https://doi.org/10.1080/14680629.2006.9690029.
- Espersson, M., 2014. Effect in the high modulus asphalt concrete with the temperature. Construction and Building Materials, 71, 638–643. doi:https://doi.org/10.1016/j.conbuildmat.2014.08.088.
- Geng, H., Clopotel, C.S., and Bahia, H.U., 2013. Effects of high modulus asphalt binders on performance of typical asphalt pavement structures. Construction and Building Materials, 44, 207–213. doi:https://doi.org/10.1016/j.conbuildmat.2013.03.035.
- Haritonovs, V., Tihonovs, J., and Zaumanis, M., 2016. Performance evaluation of high modulus asphalt concrete mixes. IOP Conference Series: Materials Science and Engineering, 123 (1), 0–6. doi:https://doi.org/10.1088/1757-899X/123/1/012055.
- Judycki, J., et al., 2015. Investigation of low-temperature cracking in newly constructed high-modulus asphalt concrete base course of a motorway pavement. Road Materials and Pavement Design, 16 (April), 362–388. doi:https://doi.org/10.1080/14680629.2015.1029674.
- Lee, H.J., Lee, J.H., and Park, H.M., 2007. Performance evaluation of high modulus asphalt mixtures for long life asphalt pavements. Construction and Building Materials, 21 (5), 1079–1087. doi:https://doi.org/10.1016/j.conbuildmat.2006.01.003.
- Ma, T., et al., 2015. Laboratory performance characteristics of high modulus asphalt mixture with high-content RAP. Construction and Building Materials, 101, 975–982. doi:https://doi.org/10.1016/j.conbuildmat.2015.10.160.
- Ma, T., et al., 2016. Experimental study of recycled asphalt concrete modified by high-modulus agent. Construction and Building Materials, 128, 128–135. doi:https://doi.org/10.1016/j.conbuildmat.2016.10.078.
- Miró, R., et al., 2011. Evaluation of high modulus mixture behaviour with high reclaimed asphalt pavement (RAP) percentages for sustainable road construction. Construction and Building Materials, 25 (10), 3854–3862. doi:https://doi.org/10.1016/j.conbuildmat.2011.04.006.
- Mogawer, W., et al., 2012. Performance characteristics of plant produced high RAP mixtures. Road Materials and Pavement Design, 13, 183–208. doi:https://doi.org/10.1080/14680629.2012.657070.
- P. l’Association Français de Normalisation (AFNORa), 1999. La Défense, Norme Français NF-P-98-140, Couches d’assise: Enrobés module élevé.
- P. l’Association Français de Normalisation (AFNORb), 1999. La Défense, Norme Français NF-P-98-141, Couches de roulement et couches de liaison: bétons bitumineux à module élevé.
- Rathore, M., Haritonovs, V., and Zaumanis, M., 2019. Asphalt recycling technologies: a review on limitations and benefits. IOP Conference Series: Materials Science and Engineering, 660, 012046. doi:https://doi.org/10.1088/1757-899X/660/1/012046.
- Rys, D., et al., 2017. Comparison of low-temperature cracks intensity on pavements with high modulus asphalt concrete and conventional asphalt concrete bases. Construction and Building Materials, 147, 478–487. doi:https://doi.org/10.1016/j.conbuildmat.2017.04.179.
- SPENS, 2009. Laboratory and field implementation of high modulus asphalt concrete. Requirements for HMAC mix design and pavement design. Sustainable Pavements for European New Member States. European Commision DG Research.
- Sybilski, D., Bańkowski, W., and Krajewski, M., 2010. High modulus asphalt concrete with limestone aggregates. International Journal of Pavement Research & Technology, 3 (2), 96–101. doi:https://doi.org/10.6135/ijprt.org.tw/2010.3(2).96.
- Zaumanis, M., Poulikakos, L.D., and Partl, M.N., 2018. Performance-based design of asphalt mixtures and review of key parameters. Materials and Design, 141, 185–201. doi:https://doi.org/10.1016/j.matdes.2017.12.035.
- Zaumanis, M. and Valters, A, 2020. Comparison of two low-temperature cracking tests for use in performance-based asphalt mixture design. International Journal of Pavement Engineering, 21 (12), 1461–1469. doi:https://doi.org/10.1080/10298436.2018.1549323.
- Zou, X., et al., 2015. Modification mechanism of high modulus asphalt binders and mixtures performance evaluation. Construction and Building Materials, 90, 53–58. doi:https://doi.org/10.1016/j.conbuildmat.2015.04.048.
- Zou, X., et al., 2017. Effects of modifier content on high-modulus asphalt mixture and prediction of fatigue property using Weibull theory. Road Materials and Pavement Design, 18, 88–96. doi:https://doi.org/10.1080/14680629.2017.1329864.