ABSTRACT
In this experimental work, homogeneous nanotube layers were successfully formed by anodization on titanium wires with diameters lower than 200 µm employing an aqueous anodizing solution composed of carboxymethylcellulose and sodium fluoride. Homogeneous nanotube layers were formed only when the titanium wires were electropolished. After heat treatment at 350 and 600°C, the nanotubes were transformed from amorphous phase into anatase phase or a mix between anatase and rutile phases. After both heat treatments, the nanotube coatings remained uniform; namely, no apparent cracks, critical defects, or coating delamination were seen. To the best of our knowledge, a homogeneous nanotube coating composed of anatase or a mix between anatase and rutile phases on titanium wires with diameters lower than 200 µm has not been reported. These coatings may be potentially useful in a variety of fields, including biomedicine, sensing, and catalysis.
Introduction
Several mechanical and chemical properties have been observed on titanium-based materials, such as low density, chemical stability, and high mechanical properties.[Citation1,Citation2] Besides those characteristics, the titanium can spontaneously form a layer of TiO2; however, this coating could be modified using an electrochemical process called anodization.[Citation3,Citation4] The anodization process allows the growth of TiO2 layers with controlled morphological physical characteristics, namely, pores,[Citation5] grooves[Citation5] and nanotubes.[Citation6,Citation7] The TiO2 nanotubes have been attractive to scientists due to the combination of the commonly known properties of TiO2 combined with the higher specific area of the nanotubular geometry.[Citation8–10] Through the anodizing technique, it is possible to coat pieces with complicated geometries; thus, TiO2 nanotubular structures can be produced on the surface of thin titanium wires. From the literature review, several authors[Citation11–16] recently reported non-homogeneous nanotubular structures made on titanium wires; namely, coatings with apparent cracks, important defects, and coating delamination. Most of those papers employed titanium wires with diameters higher than 300 µm. In a previous work,[Citation17] we produced homogeneous TiO2 nanotubes in titanium wires with diameters around 800 µm. However, additional research is necessary to produce homogeneous nanotubular structures on titanium wires with diameters lower than 200 µm. This experimental work aimed to evaluate the relationship between the electropolishing procedure and pH value with the morphologic characteristics of TiO2 nanotubes produced on titanium wires with diameters lower than 200 µm, using an anodizing solution of sodium fluoride (NaF), carboxymethylcellulose (CMC) and distilled water. Furthermore, to analyze heat treatment effect on TiO2 nanotubes to convert the amorphous phase into TiO2 polymorphs as anatase or rutile phases without affecting their homogeneity. It is worth highlighting that homogeneous TiO2 nanotubes on titanium wires with diameters lower than 200 µm were produced in this research work. As far as we are aware, homogeneous TiO2 nanotubes on titanium wires with diameters lower than 200 µm composed of anatase or a mix between anatase and rutile phases have not been reported. A possible application of these homogeneous nanotubular layers composed of anatase or anatase/rutile mix is photocatalysis; due to the high specific area of TiO2 nanotubes combined with high photocatalytic properties of anatase and rutile phases. Another possible application is in the biomedical field, specifically in biomedical devices such as stems or controlled drug release devices.
Materials and methods
The electropolishing process consisted of submerging wires of titanium grade 1 (ø:0.2032 millimeters) in a solution made of CH₃COOH, HF, and H2SO4 (60:25:15 volume/volume %) utilizing a current of 200 milliamperes per square centimeter for 160 s. Wires both electropolished and without electropolishing, were anodized by employing the exact procedure utilized during our earlier paper.[Citation18] Titanium wires were immersed in an aqueous solution containing NaF and CMC; the anodization solution pH was established using phosphoric acid. The anodization procedure was implemented for 5 h at 20 V, utilizing platinum netting as a cathode and the titanium wires as the anode. After completing the anodization, the titanium wires were washed with filtered water and dried up with air. A scanning electron microscopy equipment (JEOL JSM 6940 LV) was employed to evaluate the anodic coatings; the cross-view images were captured by scraping the surface and sloping the sample holder (about 30°) until taking the chosen image. The measurements for internal diameter and thickness of TiO2 nanotubes were estimated utilizing two SEM micrographs for every kind of sample; 10 measurements were done for each image. The heat treatment temperatures selected were 350 and 600°C, and the ramps employed will be presented later on. Once the heat treatment finishes, the samples were gradually cooled inside the furnace. The experimental conditions for every sort of anodic sample obtained are displayed in .
Table 1. Anodizing conditions of produced layers.
Results and discussion
Morphologic characterization of as anodized anodic coatings
reveals the SEM micrographs of anodized Ti wires with and without electropolishing, employing anodizing solutions with pH values of 2.5 and 4. From , it is observed that TiO2 nanotubes were obtained only in the electropolished samples. The SEM pictures at low magnifications (below 10000X) of S3 and S4 samples revealed a higher homogeneity in the coatings; namely, no apparent cracks, important defects, or coating delamination were perceived. From the SEM images at higher magnifications (above 10000X) of S3 and S4 samples, it is observed that the nanotubes produced have high packability; no cracks or spaces between nanotubes can be seen. From , it is clear that the titanium wires without electropolishing, after anodization reduced their diameter to approximately 150 µm. On the other hand, the diameter of the electropolished titanium wires after anodization was in the range of 100–130 µm. Furthermore, the nanotubes internal diameter value was 101,87 ± 13,67 and 107,39 ± 9,05 nm for the S3 and S4 samples, respectively. displays the SEM images (transversal view) of the electropolished titanium wires after anodization (S3 and S4 samples). From , the length of the nanotubes was 2037,19 ± 31,75 and 1551,21 ± 49,67 nm for the S3 and S4 samples, respectively.
Figure 2. SEM micrographs (transversal view) of anodized titanium wires. S3 (a) and (b), S4 (c) and (d).
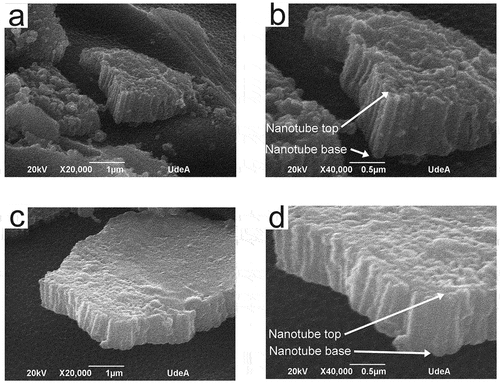
Recently various authors[Citation13,Citation14,Citation19–23] reported that TiO2 nanotubes produced on titanium wires presented defects such as delamination, cracks, coral like structures among others. Delamination could be a critical drawback for the real application of TiO2 nanotubes created on titanium wires by anodization as the properties added to the Ti surfaces by the nanotubes would be lost. Isa et al.[Citation14] made TiO2 nanotubes onto titanium wires using an electrolyte of ethylene glycol and NH4F for photocatalytic applications. These authors stated that reusability and stability are important characteristics of a catalyst in real situations. They also reported that photocatalytic properties dramatically decreased due to delamination after a second cycle of reuse; after a third cycle of reuse, the coating was peeled off and the photocatalytic properties were very low.
The internal diameter values of the TiO2 nanotubes produced in this experimental work were similar to those measured in our previous papers on flat surfaces[Citation18] and titanium wires with diameters around 800 µm,[Citation17] at identical anodizing conditions. However, the length of TiO2 nanotubes produced in this experimental work was shorter than those made on flat surfaces[Citation18] and bigger than those grown on titanium wires with diameters around 800 µm.[Citation17] The TiO2 nanotube length differences between S3 and S4 samples are related to the electrolyte pH effect. The relationship between electrolyte pH value and nanotube length has been reported in preceding experimental works,[Citation18,Citation24–26] and our results are congruent with those articles.
Heat Treatment
To obtain nanotubular coatings composed of anatase or rutile phases or a mixture of them, on the surface of titanium wires, two heat treatments were employed using temperatures of 350 and 600°C. shows the ramp used for the heat treatments utilizing temperatures of 350 and 600°C for S3 and S4 samples. From , the ramps used slowly increased and the temperature was maintained at specific values for about 1 hour; however, the final temperature (either 350 or 600 °C) was held for 2 h. This ramp was designed to prevent the nanotube coating delamination and the appearance of cracks or defects in the nanotube layer. displays the Raman spectra of S3 and S4 samples both heat-treated (350 and 600 °C) and in the absence of heat treatment. From , the coatings without heat treatment have a distinctive Raman spectra form with wide peaks nearly at 152, 451, and 610 cm−1 as described in earlier research papers for amorphous TiO2 nanotubes.[Citation7,Citation27,Citation28] Since , the predominant phase in the 350°C heat-treated samples S3 and S4 was anatase. Samples S3 and S4 heat-treated at a temperature of 600°C were composed of rutile and anatase, as shown in . Images of anodized titanium wires (S3 and S4 samples) later heat treatment at 350°C are shown in . The uniformity of the coatings is preserved in both S3 and S4 samples heat-treated at a temperature of 350°C. Furthermore, the nanotubes preserve the high packability observed in the nanotube coatings without heat treatment. displays the SEM micrographs of anodized titanium wires (S3, S4 and S5 samples) later heat treatment at 600°C. Coating delamination has been seen in the heat-treated S3 samples at a temperature of 600°C since (a)-(6). Heat-treated S4 samples at a temperature of 600°C maintained the coating uniformity found in the nanotube coatings without heat treatment, as shown in (f)-(6); thus, cracks, defects or delamination was not seen in these samples. From (j)-(6), S5 samples heat-treated at 600°C retained the coating homogeneity, noted in the same nanotube coatings in the absence of heat treatment.
Figure 4. Raman spectra of anodized titanium wires (S3 and S4 samples) before heat treatment (a), with heat treatment at 350°C (b) and with heat treatment at 600 °C (c).
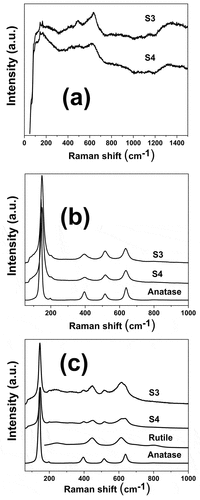
Figure 6. SEM micrographs of heat-treated at 600°C anodized titanium wires. S3 (a)-(e), S4 (f)-(i), S5 (j)-(l).
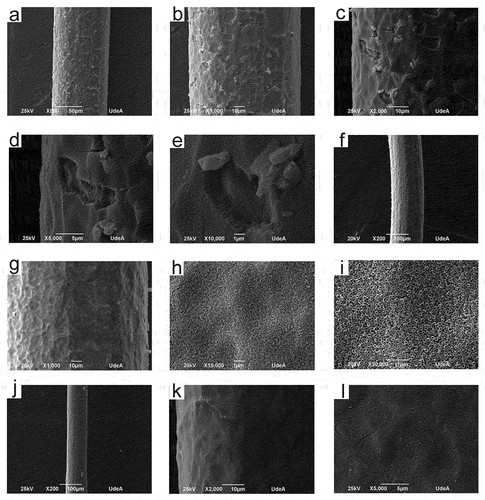
The temperature ramp was designed based on our previous works[Citation7,Citation17,Citation27] to prevent the occurrence of delamination, cracks or imperfections in the nanotube coatings. However, the coating stability after heat treatment depends on the layer characteristics in some cases. From the results section (), the S3 samples later heat treatment at 600°C presented coating delamination and cracks; however, the S4 samples after the same heat treatment maintained the coating uniformity observed in the nanotube coatings without heat treatment. An explanation of this behavior can be based on the nanotube length; from , the length of TiO2 nanotubes of S3 samples is about 2000 nm compared with 1500 nm of those in the S4 samples. Thus, the integrity of the TiO2 nanotubes heat-treated at a temperature of 600°C depends on the length of the nanotubes. The length of the TiO2 nanotubes in the S5 samples (pH 3.5) was smaller than those in the S3 samples (pH 4) but larger than the nanotubes in the S4 samples (pH 2.5). From , the S5 samples show a higher coating uniformity than the S3 samples after heat treatment; thus, from our results, nanotubes with lengths shorter than 2000 nm maintain the coating uniformity after heat treatment at 600°C. Shivaram et al[Citation29] produced TiO2 nanotubes in flat surfaces with different lengths (300 and 950 nm) to study the heat treatment effect on the nanotube integrity. Shivaram et al. found that, after heat treatment, longer nanotubes were thermally more unstable than those with lower lengths. The results of Shivaram et al. are in accord with our results.
According to the literature review, some authors[Citation11,Citation30–32] reported TiO2 nanotubes produced on titanium wires composed of anatase or anatase and rutile phases. However, those authors did not report the impact of heat treatment on the integrity of the nanotubular structures of TiO2. Furthermore, the authors of those experimental works reported that TiO2 nanotubes produced on titanium wires without heat treatment had problems such as delamination, cracks, and defects. Thus, the heat treatment could increase those problems by detaching a high percentage of the coating.
Some authors[Citation11,Citation33,Citation34] reported that the photocatalytic properties are enhanced when the TiO2 is constituted of a combination of anatase and rutile. Thus, the homogeneous TiO2 nanotubes consisting of a mix of anatase and rutile produced in this work could be used in photocatalytic applications.
Conclusions
TiO2 nanotubes were successfully produced on titanium wires with diameters smaller than 200 µm, employing an aqueous anodizing solution of NaF and CMC. Based on the results, the subsequent could be concluded:
Homogeneous nanotube coatings were made only in the titanium wires with electropolishing pretreatment.
The internal diameter values of TiO2 nanotubes produced were similar to those measured in flat surfaces and titanium wires with diameters around 800 µm.
The length of TiO2 nanotubes produced was shorter than those made on flat surfaces and longer than those grown on titanium wires with diameters of around 800 µm.
After both heat treatments, homogeneous nanotube composed of anatase or a mix between anatase and rutile phases were produced without apparent cracks, critical defects, or coating delamination.
Disclosure statement
No potential conflict of interest was reported by the author(s).
Additional information
Funding
References
- Meng, Y.; Li, X.; Li, Z.; Liu, C.; Zhao, J.; Wang, J.; Liu, Y.; Yuan, X.; Cui, Z.; Yang, X. Surface Functionalization of Titanium Alloy with MiR-29b Nanocapsules to Enhance Bone Regeneration. ACS Appl. Mater. Interfaces. 2016, 8(9), 5783–5793. DOI: 10.1021/acsami.5b10650.
- Gui, N.; Xu, W.; Abraham, A. N.; Shukla, R.; Qian, M. Osteoblast Responses to Titanium-Coated Subcellular Scaled Microgrooves. ACS Appl. Bio Mater. 2019, 2(6), 2405–2413. DOI: 10.1021/acsabm.9b00094.
- Aguirre Ocampo, R.; Echeverry-Rendón, M.; Robledo, S.; Echeverría Echeverría, F. Effect of TiO2 Nanotubes Size, Heat Treatment, and UV Irradiation on Osteoblast Behavior. Mater. Chem. Phys. 2022, 275(Jan 2022), 125137. DOI: 10.1016/j.matchemphys.2021.125137.
- Demetrescu, I.; Ionita, D.; Pirvu, C.; Portan, D. Present and Future Trends in TiO2 Nanotubes Elaboration, Characterization and Potential Applications. Mol. Cryst. Liq. Cryst. 2010, 521(1), 195–203. DOI: 10.1080/15421401003715918.
- Echeverry-Rendón, M.; Galvis, O.; Aguirre, R.; Robledo, S.; Castaño, J. G.; Echeverría, F. Modification of Titanium Alloys Surface Properties by Plasma Electrolytic Oxidation (PEO) and Influence on Biological Response. J. Mater. Sci. Mater. Med. 2017, 28(11), 11. DOI: 10.1007/s10856-017-5972-x.
- Aguirre Ocampo, R.; Echeverría Echeverría, F. Antibacterial and Biological Behavior of TiO2 Nanotubes Produced by Anodizing Technique. Crit. Rev. Biomed. Eng. 2021, 49(1), 51–65. DOI: 10.1615/critrevbiomedeng.2021037758.
- Aguirre, R.; Echeverry-Rendón, M.; Quintero, D.; Castaño, J. G.; Harmsen, M. C.; Robledo, S.; Echeverría, E. F. Formation of Nanotubular TiO 2 Structures with Varied Surface Characteristics for Biomaterial Applications. J. Biomed. Mater. Res. Part A. 2018, 106(5), 5. DOI: 10.1002/jbm.a.36331.
- Chan, C. M. N.; Ng, A. M. C.; Fung, M. K.; Cheng, H. S.; Guo, M. Y.; Djurišić, A. B.; Leung, F. C. C.; Chan, W. K. Antibacterial and Photocatalytic Activities of TiO2 Nanotubes. J. Exp. Nanosci. 2013, 8(6), 859–867. DOI: 10.1080/17458080.2011.616540.
- Chen, X.; Mao, S. S. Titanium Dioxide Nanomaterials: Synthesis, Properties, Modifications and Applications. Chem. Rev. 2007, 107(7), 2891–2959. DOI: 10.1021/cr0500535.
- Liu, Y.; Tong, Z.; Wang, C.; Xia, R.; Li, H.; Yu, H.; Jing, J.; Cheng, W. TiO2 Nanotubes Regulate Histone Acetylation Through F-Actin to Induce the Osteogenic Differentiation of Bmscs. Artif. Cells Nanomed Biotechnol. 2021, 49(1), 398–406. DOI: 10.1080/21691401.2021.1910282.
- Bao, R.; Zhao, Y.; Ma, F.; Wu, J.; Xia, J.; Li, H. 3D-Tnas Composite Electrodes with Enhanced Visible-Light Photoelectrocatalytic Performance and Stability. J. Phys. Chem. Solids. 2022, 161(June 2021), 110435. DOI: 10.1016/j.jpcs.2021.110435.
- Selli, G. I.; Bonatto, F.; Oliveira, A. E. R. T. P.; Kopp Alves, A.; Aguzzoli, C.; Ten Caten, C. S.; Bergmann, C. P. Chelating Agents Effects in Nanoengineered Silver Structures Over TiO2 Nanotubes on Ti Wires and Their Rhodamine B Detection Activity. Mater. Chem. Phys. 2021, 258(May 2020), 123887. DOI: 10.1016/j.matchemphys.2020.123887.
- Jian, X.; Xu, J.; Wang, Y.; Zhao, C.; Gao, Z.; Song, Y. Y. Deployment of MIL-88b(fe)/tio2nanotube-Supported Ti Wires as Reusable Electrochemiluminescence Microelectrodes for Noninvasive Sensing of H2o2from Single Cancer Cells. Anal. Chem. 2021, 93(32), 11312–11320. DOI: 10.1021/acs.analchem.1c02670.
- Isa, N.; Mohamad nor, N.; Wan Kamis, W. Z.; Tan, W. K.; Kawamura, G.; Matsuda, A.; Lockman, Z. Anodized TiO2 Nanotubes Using Ti Wire in Fluorinated Ethylene Glycol with Air Bubbles for Removal of Methylene Blue Dye. J. Appl. Electrochem. 2021. DOI: 10.1007/s10800-021-01644-z.
- Ali, G.; Maqbool, M. Field Emission Properties of TiO2 Nanotubes Fabricated on Ti Wire. Mater. Chem. Phys. 2019, 233(July 2018), 21–26. DOI: 10.1016/j.matchemphys.2019.05.026.
- Sugiawati, V. A.; Vacandio, F.; Galeyeva, A.; Kurbatov, A. P.; Djenizian, T. Enhanced Electrochemical Performance of Electropolymerized Self-Organized TiO2 Nanotubes Fabricated by Anodization of Ti Grid. Front. Phys. 2019, 7(November), 1–8. DOI: 10.3389/fphy.2019.00179.
- Aguirre Ocampo, R.; Echeverría Echeverría, F. TiO2 Nanotubes Produced on Curved Titanium Surfaces Using Aqueous Electrolytes with Carboxymethyl Cellulose. Phys. E Low-Dimensional Syst. Nanostructures. 2021, 125(January), 114391. DOI: 10.1016/j.physe.2020.114391.
- Aguirre Ocampo, R.; Echeverría Echeverría, F. Effect of the Anodization Parameters on TiO2 Nanotubes Characteristics Produced in Aqueous Electrolytes with CMC. Appl. Surf. Sci. 2019, 469, 994–1006. DOI: 10.1016/j.apsusc.2018.11.097.
- Bao, R.; Geng, J.; Sullivan, J. A.; Xia, J.; Wang, W.; Wong, W. Y.; Li, H. Hierarchical 3D TiO2 Nanotube Arrays Sensitized by Graphene Oxide and ZnxCdys for High Performance Photoelectrochemical Applications. Phys. Status Solidi Appl. Mater. Sci. 2018, 215(24), 1–7. DOI: 10.1002/pssa.201800436.
- Alivov, Y.; Funke, H.; Nagpal, P. Air-Gating and Chemical-Gating in Transistors and Sensing Devices Made from Hollow TiO2 Semiconductor Nanotubes. Nanotechnology. 2015, 26(29), 295203. DOI: 10.1088/0957-4484/26/29/295203.
- Lashkov, A. V.; Fedorov, F. S.; Vasilkov, M. Y.; Kochetkov, A. V.; Belyaev, I. V.; Plugin, I. A.; Varezhnikov, A. S.; Filipenko, A. N.; Romanov, S. A.; Nasibulin, A. G., et al. The Ti Wire Functionalized with Inherent TiO2 Nanotubes by Anodization as One-Electrode Gas Sensor: A Proof-Of-Concept Study. Sens. Actuators B Chem. 2020, 306(October 2019), 127615.
- Yang, L.; Zheng, X.; Liu, M.; Luo, S.; Luo, Y.; Li, G. Fast Photoelectro-Reduction of CrVi Over MoS2@tio2 Nanotubes on Ti Wire. J. Hazard. Mater. 2017, 329, 230–240. DOI: 10.1016/j.jhazmat.2017.01.045.
- Saboo, T.; Tavella, F.; Ampelli, C.; Perathoner, S.; Genovese, C.; Marepally, B. C.; Veyre, L.; Quadrelli, E. A.; Centi, G. Water Splitting on 3D-Type Meso/macro Porous Structured Photoanodes Based on Ti Mesh. Sol. Energy Mater. Sol. Cells. 2018, 178(November 2017), 98–105. DOI: 10.1016/j.solmat.2018.01.007.
- Aguirre, O. R.; Echeverría, E. F. Effects of Fluoride Source on the Characteristics of Titanium Dioxide Nanotubes. Appl. Surf. Sci. 2018, 445, 308–319. DOI: 10.1016/j.apsusc.2018.03.139.
- Lai, C. W.; Sreekantan, S. Photoelectrochemical Properties of TiO2 Nanotube Arrays: Effect of Electrolyte PH and Annealing Temperature. J. Exp. Nanosci. 2014, 9(3), 230–239. DOI: 10.1080/17458080.2011.654276.
- Sreekantan, S.; Lockman, Z.; Hazan, R.; Tasbihi, M.; Tong, L. K.; Mohamed, A. R. Influence of Electrolyte PH on TiO2 Nanotube Formation by Ti Anodization. J. Alloys Compd. 2009, 485(1–2), 478–483. DOI: 10.1016/j.jallcom.2009.05.152.
- Ocampo, R. A.; Echeverry‐Rendón, M.; DeAlba‐montero, I.; Robledo, S.; Ruiz, F.; Echeverría Echeverría, F. Effect of Surface Characteristics on the Antibacterial Properties of TiO2 Nanotubes Produced in Aqueous Electrolytes with Carboxymethyl Cellulose. J. Biomed. Mater. Res. Part A. 2021, 109(1), 104–121. DOI: 10.1002/jbm.a.37010.
- Hardcastle, F. Raman Spectroscopy of Titania (TiO2) Nanotubular Water-Splitting Catalysts. J. Ark. Acad. Sci. 2011, 65, 43–48. DOI: 10.54119/jaas.2011.6504.
- Shivaram, A.; Bose, S.; Bandyopadhyay, A. Thermal Degradation of TiO2 Nanotubes on Titanium. Appl. Surf. Sci. 2014, 317, 573–580. DOI: 10.1016/j.apsusc.2014.08.107.
- Qiu, L.; Wang, Q.; Liu, Z.; Zhao, Q.; Tian, X.; Li, H.; Gao, S. Preparation of 3D TiO2 Nanotube Arrays Photoelectrode on Ti Mesh for Photoelectric Conversion and Photoelectrocatalytic Removal of Pollutant. Sep. Purif. Technol. 2018, 207(June), 206–212. DOI: 10.1016/j.seppur.2018.06.050.
- Liao, J.; Lin, S.; Zhang, L.; Pan, N.; Cao, X.; Li, J. Photocatalytic Degradation of Methyl Orange Using a TiO 2/ti Mesh Electrode with 3D Nanotube Arrays. ACS Appl. Mater. Interfaces. 2012, 4(1), 171–177. DOI: 10.1021/am201220e.
- Ru, Y.; Yang, L.; Li, Y.; Jiang, W.; Li, Y.; Luo, Y.; Yang, L.; Li, T.; Luo, S. Photoelectrocatalytic Reduction of CO2 on Titania Nanotube Arrays Modified by Pd and RGO. J. Mater. Sci. 2018, 53(14), 10351–10362. DOI: 10.1007/s10853-018-2319-z.
- Suhadolnik, L.; Krivec, M.; Žagar, K.; Dražić, G.; Čeh, M. A TiO2-Nanotubes-Based Coil-Type Microreactor for Highly Efficient Photoelectrocatalytic Degradation of Organic Compounds. J. Ind. Eng. Chem. 2017, 47, 384–390. DOI: 10.1016/j.jiec.2016.12.009.
- Lau, K. S.; Lai, C. W.; Lim, Y. S.; Hamid, S. B. A. Electrochemical Growth of Self-Organised Anodic TiO 2 Nanotubes for Better Photocatalytic Degradation Reaction. Mater. Res. Innov. 2014, 18(sup6), SS6–464. DOI: 10.1179/1432891714Z.000000000998.