ABSTRACT
This work presents an updated overview of waste lubricant oil (WLO) management practices in Europe to promote a circular economy. The characteristics of virgin and waste oil, their hazardous properties and the impacts of improper disposal are addressed. Current treatment routes and regeneration technologies adopted in Europe are presented. An overview of life cycle assessment (LCA) of WLO management strategies are summarized. Finally, future developments and concerns about the regeneration process are discussed. The current objectives of European Union toward a circular economy represent a challenge for Member States which must maximize the collection and recycling rates. EU management indicators show an overwhelming trend for recycling. However, there is a competition between recycling by regeneration to produce base oil and reprocessing for energy recovery. EU legislation states that priority should be given to options that provide better overall environmental outcome. However, LCA studies, are not unanimous about regeneration being the soundest environmental option. Other factors such as lubricant market, energy consumption, distance to treatment facilities, operation costs and product quality should be accounted for. Selective segregation of WLO is extremely important to increase the regeneration rate and obtain high-quality base-stocks. However, this means a significant increase in the collection costs.
Graphical abstract
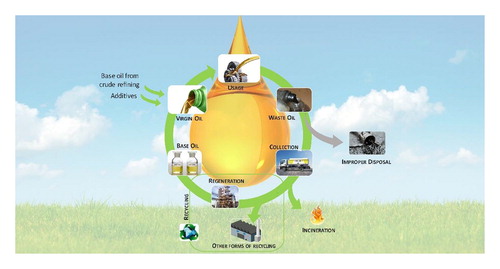
1. Introduction
Some products are essential for humans to sustain living standards and comfort. Lubricant oil is one of those products. Their main function is to reduce friction and wear of metal surfaces, extend the service life of the equipment and save resources and energy. Scientific research has shown that the direct costs of friction and wear phenomena may be responsible for nearly 10% of the gross national product (GNP) in many industrialized countries (Stachowiak & Batchelor, Citation2014). In addition, it is estimated that 1% of GNP could be saved in terms of energy if current tribological knowledge (the science of friction) was applied to lubricated systems (Bronshteyn & Kreiner, Citation1999).
In 2017, the world lubricant market was estimated at around 35.7 Mt. Accounting for 43% of the global market, Asia-Pacific has the highest share and is the region with the fastest growth in the consumption of lubricants. Europe is responsible for 19% of lubricants demand, consuming 6.8 Mt of lubricating oil every year (Fuchs, Citation2017). The world demand by geographic area in 2017 and 2007 (shown between brackets) is presented in .
Figure 1. Lubricant demand by region in 2017 (2007). Adapted from Fuchs (Citation2018).
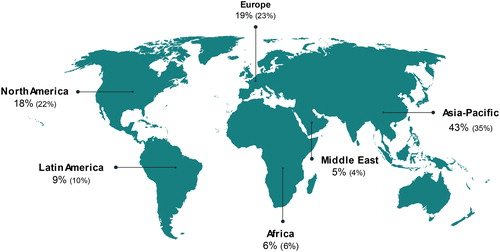
According to the application, lubricants may be classified into automotive, industrial, process, and marine oils. Indeed, the automotive segment accounted for 57% in 2016 (Fuchs, Citation2017). Industrial lubricants are sub-divided into industrial oils and industrial specialties (metalworking fluids and greases). The term lubricant has been loosely applied to many other fluids that do not specifically perform the main function of reducing friction and wear. Some examples include power and heat transmission fluids, hydraulic fluids, dielectric fluids, specific process oils, and others. Process oils correspond to raw materials, for instance used as plasticizers agents in plastic and rubber industries. Process oils are only linked with lubricants because they are mineral oil products resulting from the refining of crude (Totten et al., Citation2003).
Lubricants are generally subjected to degradation and contamination from several sources during its long-term operation (Mortier et al., Citation2010). Contamination can have serious adverse effects on the physical and chemical properties of lubricants. The loss of crucial properties, which are central to the useful service life can result in inefficient system performance, accelerated mechanical and chemical wear processes, shorten the service life of the equipment, and cause premature failures (Gustavsson, Citation2013; Speight & Exall, Citation2014). Thus, lubricants have a lifespan, after which they require replacement. However, some oils are consumed during service, and some are partly lost by combustion processes, evaporation, residues remaining in the containers, etc. Therefore, about 50% of the fresh lubricants consumed will generate waste and, consequently, a huge amount of waste lubricant oil (WLO) is produced every year all over the world (Monier & Labouze, Citation2001).
Nowadays, the sustainability principles are considered a driving force for the industry, and thus saving energy, resources and cutting emissions have become central issues. Also, lubricants production and its recovery are increasingly drawing public attention, since good practices may contribute to the sparing use of resources and sustainable development. With ever-growing global environmental awareness, many countries have developed regulations for guiding the management of hazardous waste. In the European Union (EU), demanding regulations led to the employment of the best available techniques (BAT) regarding waste oil management and to increasing collection and recycling rates over the years in several countries (GEIR, Citation2016). However, some Member States still need to improve the performance of the integrated waste oil management systems to reach the goals of the EU directives (Pinheiro, Ascensão, Cardoso, et al., Citation2017). Other countries around the world have also been trying to implement reliable management practices. As an example, El-Fadel and Khoury (Citation2001) reported the situation in Lebanon, and Jhanani and Joseph (Citation2011) in Indian automotive industries.
In this context, this work aims to provide an updated overview of the management strategies for the WLO currently adopted in Europe. The physicochemical characteristics of both virgin and waste lubricating oil, their hazardous properties and the impact of the disposal on the environment and human health are addressed. The current treatment routes adopted in Europe and an overview of life cycle assessment studies regarding the different WLO management strategies are presented. Finally, a discussion on future developments and concerns about the regeneration process is also examined.
2. Physicochemical characteristics of virgin and waste lubricant oils
Virgin lubricants are a blend of base oil and additives added to adjust the properties to meet specifications and desired service life (Rudnick, Citation2013). The base oil is typically defined as oil from refining crude oil (mineral base oil) or obtained by chemical synthesis (synthetic base oil) with a boiling point range between 300 °C and 565 °C, consisting of hydrocarbons from C18 to C40 (Speight & Exall, Citation2014).
Lubricants based on mineral oils are still widely used due to their low cost, availability, and overall acceptable performance (Mang & Dresel, Citation2017). Mineral oils can be classified as paraffinic, naphthenic or aromatic based on the predominant type of structure in the crude, as illustrated in (Totten et al., Citation2003). Paraffinic hydrocarbon fractions are saturated linear (n-paraffin) or branched (iso-paraffin) alkanes (Robinson, Citation2006). Paraffins have good viscosity-temperature characteristics, which leads to better performance for applications such as for engine oils (Rudnick, Citation2013). On the other hand, iso-paraffins present significant physicochemical differences as the degree of branching increases. Linear alkanes exhibit good viscosity-temperature properties, but their high melting point causes crystallization as wax. Waxy paraffins have exceptionally high pour point (the minimum temperature at which a lubricant is still able to flow) which hamper their use at low temperatures. In contrast, highly branched alkanes have poor viscosity/temperature properties (Lynch, Citation2007; Mang & Dresel, Citation2017; Sequeira, Citation1994). Paraffinic base stocks are the most widely used base oil for lubricant applications comprising about 85% of world supply (Lynch, Citation2007).
Figure 2. Classes of mineral hydrocarbons present in base oils. Adapted from Mang and Dresel (Citation2017).
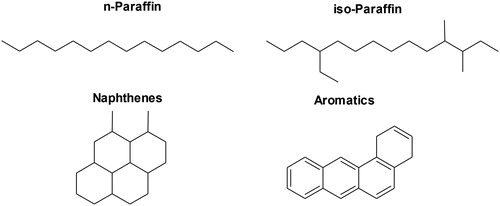
Alicyclic hydrocarbons, known as naphthenes are saturated cyclic structures based on more than one and up to six-membered rings (Totten et al., Citation2003). Naphthenes tend to have low pour point, providing outstanding low-temperature properties. Furthermore, its high solvency power contributes not only to the dilution of additives, but also to dissolve deposits and debris during use. These characteristics improve the seal compatibility, which is of great importance in many applications, such as in hydraulic fluids and gear oils (Mang & Dresel, Citation2017; Speight & Exall, Citation2014). The main disadvantages of naphthenic oils are low oxidation stability and viscosity-temperature characteristics (Mang et al., Citation2011; Pirro et al., Citation2001).
Aromatic oils are cyclic unsaturated hydrocarbons comprising one or more benzene rings (Robinson, Citation2006). Aromatic oils have poor oxidative stability and pour viscosity-temperature properties that limit its use for lubricant formulations. However, they have the best solvency power for additives, making their combination with paraffins advantageous (Robinson, Citation2006; Totten et al., Citation2003).
Nowadays, the variety of lubricants has grown to meet the increasing technological requirements of modern machines, which operate under severe conditions and challenging environments. Global synthetic lubricant demand represented 8–10% of total lubricant demand in 2014 and it is expected to grow at an annual growth rate of 2.9% from 2014 to 2020 (HIS Markit, Citation2015). Unlike mineral base stocks derived from crude, synthetics have well-defined molecular structures with well-defined molecular weight distributions. In general, it provides superior mechanical and chemical properties than traditional mineral oil (Lugt, Citation2013; Speight & Exall, Citation2014). The worldwide demand for synthetic base oil is dominated by three main components – polyalphaolefins (PAO), synthetic esters and polyalkylene glycols (PAG) (Mortier et al., Citation2010). Their market share in 2014 was nearly 90% of total synthetic base stock demand, where PAO accounted for 44%, followed by 30% esters and 13% PAG (HIS Markit, Citation2015).
Polyalphaolefins (PAO) are saturated olefin polymers belonging to a class of high performance synthetic base stocks (Benda et al., Citation1996). The alkyl groups present in the polymer backbone chain can have several molecular conformations (), which prevents the orderly alignment of the molecules. This characteristic provides excellent low-temperature properties since the molecules do not crystallize at low temperatures (Ray et al., Citation2012). PAO are also characterized by a high thermal and oxidation stability, high viscosity index and low volatility for higher molecular weight polymers. On the other hand, the low polarity of these compounds leads to lower solvency power, which affects the miscibility with polar additives and can cause sealing problems (Mang & Dresel, Citation2017; Rudnick, Citation2013).
Figure 3. Typical polyalphaolefin oligomers. Adapted from Mang and Dresel (Citation2017).
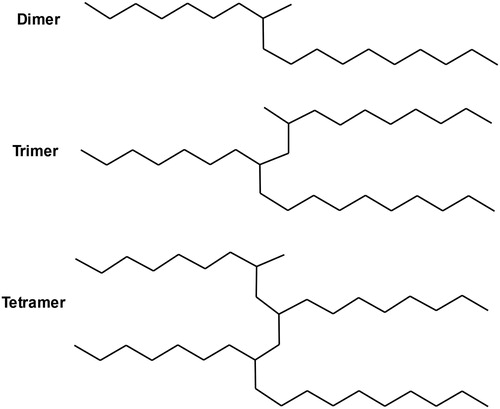
Ester-based lubricant oils are a broad family of high performance synthetic base oil, used in severe environment applications due to their custom-tailored properties (). The composition is based mainly on branched hydrocarbons in the presence of oxygen in the form of ester groups that convey polarity to the base oil (Rudnick & Shubkin, Citation1999). The polarity provides characteristics such as low volatility, high flash point, thermal stability, high solvency, high detergency and dispersion, and biodegradability (Rudnick, Citation2013). However, the main disadvantages are related to the seal compatibility and the fact that esters are hygroscopic. Water can catalyze the reverse reaction of esterification (acid hydrolysis of the ester to give carboxylic acids), affecting hydrolytic stability (Rudnick & Shubkin, Citation1999).
Figure 4. Several families of synthetic ester base oils (Rudnick, Citation2013).
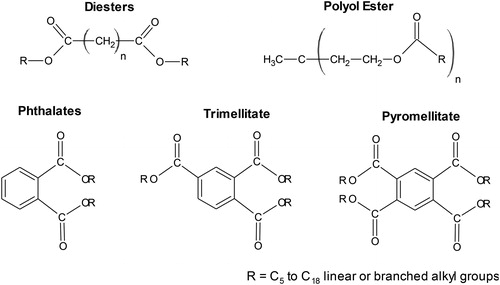
Polyalkylene glycols (PAGs), , are produced by polymerization of ethylene oxide (EO) and/or propylene oxide (PO) in different ratios (Rudnick, Citation2013). PAG can have a wide range of viscosity grades and can reach very high viscosities and VI, which is related to the molecular weight of the polymers (Harnoy, Citation2003). High polarity and a low coefficient of friction are the most important characteristics of PAG. In addition, PAG-based oils offer low volatility and have desired properties at high and low temperatures (Laing & Thomas, Citation2014). They also are fire-resistant and have high loading capacity to withstand high pressures (Rudnick, Citation2013). However, one of the most relevant limiting characteristics is its incompatibility with other base oils and additives due to their limited miscibility (Mang & Dresel, Citation2017).
Figure 5. Polyalkylene Glycol general structure (Rudnick, Citation2013).
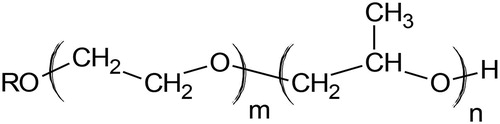
In general, synthetic base oils are incorporated into petroleum distillate feedstocks to enhance the properties of the finished product (Rizvi, Citation2009). summarizes a comparison between synthetic and mineral oil.
Table 1. Comparison between mineral and synthetic base oil (Rizvi, Citation2009).
Both minerals or synthetic lubricants are subject to degradation and contamination during its operation (Mortier et al., Citation2010). The chemical changes and accumulation of contaminants increases with the oil use and depends on the original base oil, refining process used, additives package, application type, time of service, etc. (Totten et al., Citation2003). The elemental contamination can be caused by the base oil and additives deterioration, and external contaminants.
Besides the contamination associated with specific elements, lubricant oils may lose their performance due to water, chlorine and polychlorinated biphenyls (PCB), polycyclic aromatic hydrocarbons (PAH) and particulate metals (Audibert, Citation2006).
Water may be in three different forms: dissolved, emulsified and free, depending on the temperature, pressure and the type of oil. Water may arise from several sources, including rain leakage, infiltrations, condensation of air, cooling system leaks, antifreeze agents, fuel combustion by-product or process water, etc. (Day & Bauer, Citation2007). The concentration of water in the WLO can vary up to 15 wt.% ().
Table 2. General characteristics of virgin and waste lubricant oil (Pinheiro, Ascensão, Cardoso, et al., Citation2017; Pinheiro, Ascensão, Reis, et al., Citation2017).
Chlorine is part of some metalworking, hydraulic, insulating or heat transfer fluids as chlorinated hydrocarbons with specific characteristics such as chemical stability and fire-resistance (Speight & Exall, Citation2014). Organochlorides such as PCB are contaminants of special concern which arise mainly from transformer oils (Jahromi et al., Citation2014). The production and use of PCB were banned in most countries in the 80 s due to their persistent and toxic properties, but some contamination is still detected in WLO (Jahromi et al., Citation2014).
PAH can be added intentionally to some transformer oils, due to their capacity to absorb potentially explosive gases produced during operation and to extend the lifetime of the oil by acting as natural oxidation inhibitors (Pillai et al., Citation2005). Additionally, PAH can derive from mineral base oils which were not removed during crude refining or can also be formed by the combustion of fossil fuels during engine operation. In fact, the concentration of PAH in used crankcase oil may be 3 times higher than that in virgin oil (Zakaria et al., Citation2002).
Contamination of WLO with metals may arise from the additives, the wear of metals, such as engine bearing or bushings, and from fuel containing metals. Metals are found in WLO as particulate matter or elemental form (Speight & Exall, Citation2014).
Other contaminants in WLO may comprise i) soot and carbon from incomplete combustion, which are responsible for the characteristic black color of WLO; ii) sludge, varnish, corrosive organic acids from oxidation, nitration, sulfonation and other undesirable reactions; iii) unburnt fuel that leaks into the lubricant; iv) dust and dirt composed of silicates from the surrounding environment; v) solvents, antifreeze agents, coolants, brake fluid that result from mishandling of the WLO producer; vi) remaining additives that were not depleted during use, etc., and several other miscellaneous debris (Audibert, Citation2006).
lists some characteristics of virgin lubricants for different applications (cut fluids, gear oils, hydraulic oils, motor oils, marine, and others), and of WLO collected in Portuguese generators (garage, industry, and others).
3. Impact of waste oils on human health and the environment
According to the European List of waste (LoW), which intends to provide harmonization of waste classification in the EU, all WLO are absolute hazardous entries in the list. Therefore, regardless of its composition and/or source, WLO, exhibit at least one hazardous properties (HP) listed in the Commission Regulation (EU) No. 1357/2014. WLO typically display HP5 (Specific Target Organ Toxicity/Aspiration Toxicity), HP7 (carcinogenic) and/or HP14 (ecotoxic) (UK Environment Agency, Citation2015). The HP may be due to metals, chlorine, PCB, or even polychlorinated terphenyls (PCT) and polybrominated biphenyls (PBB). In addition, unburned fuel and by-products from fuel combustion may cause the accumulation of compounds such as PAH. These compounds consisting of multiple rings such as benzo[a]pyrene are classified as carcinogenic to humans by the International Agency for Research on Cancer (IARC, Citation2018).
Since lubricant oils are usually toxic and not readily biodegradable, the indiscriminate disposal of WLO into the environment may create serious problems for ecosystems, posing a high risk of damage to the soil, water, and air (Speight & Exall, Citation2014).
The assessment of the biodegradability and microbial toxicity of lubricants has been a demand to meet the criteria of ecolabelling schemes aiming at environmental protection. Although it is not an easy procedure, there are some approaches to assess biodegradability in different conditions, namely aerobic, anaerobic, freshwater and marine ambient (Battersby, Citation2000).
Stringent regulations on the use, handling, and disposal of these materials are imposed by several government regulators to alleviate the potential hazards to the environment. However, due to the difficulty to mitigate spills and discharges of lubricants, mainly mineral-based oils, the United States Environmental Protection Agency (EPA) introduced a new class of raw materials to produce lubricants. These are named environmentally acceptable (EA) materials, which are not toxic and biodegradable, unlike mineral-based oils (US EPA, Citation2011). The three most common categories of biodegradable base oils that constitute an EA are from renewable resources: vegetable oils, synthetic esters, and polyalkylene glycols. The aquatic toxicity exhibited by lubricants formulated from EA components is low when compared to mineral oil.
The next sections describe the environmental effects of WLO on the soil, water and the air. Some of the characteristics of WLO responsible by the environmental contamination can be seen in , where the concentration range of polychlorinated biphenyls, benzo[a]pyrene, benzo[a]anthracene and potentially toxic metals (Zn, Cr, Pb, etc.) are reported.
3.1. Soil
Soil contamination with WLO is derived from leaks and losses of engines, indiscriminate dumping into sewers, or into the ground. The consequences of WLO in the soil functions can be devastating since normal physical, chemical and microbiological properties may be significantly hampered.
The fate of the oil released into the soil is mainly controlled by the nature, porosity and organic matter of the soil. In case of high organic content, soil tends to absorb the oil and prevent its flow downward, whereas permeable soil with little organic matter allows migration of the oil and contamination of groundwater (Klamerus-Iwan et al., Citation2015). The portion that remains in the soil undergoes slow volatilization due to low vapor pressures (<0.001 mm Hg at 25 °C), slow hydrolysis and/or microbial degradation (Speight & Exall, Citation2014).
The presence of WLO in the soil induces substantial changes in the living organisms, mainly the ones involved in the nitrogen cycle. It fills the pores between the particles hindering the access of oxygen, inducing a significant number of anaerobic zones, and thus also to metabolic activity by anaerobic microorganisms (John et al., Citation2011).
The heavy metals can strongly inhibit primary production in soil, carbon mineralization, nitrogen transformations and mineralization of sulfur and phosphorus (Srivastava et al., Citation2017). The pollution with WLO leads to the accumulation of essential (e.g. K, Mg, Ca, Fe, Co, Ni, Cu, Zn, etc.) and non-essential elements (e.g. Al, Pb, and Cd) and its possible translocation into plant tissues (Vwioko et al., Citation2006). High concentrations of toxic metals can cause metabolic and growth inhibition for most plant species, and can have a harmful effect on the food chain (Morkunas et al., Citation2018). A study performed using Vigna unguiculata and Zea mays revealed that engine oil has inhibitory effects on the growth and early seedling performance (Kayode et al., Citation2009).
Moreover, plants may uptake PAH present in the soil, especially the low molecular weight molecules, which are rapidly translocated to the above-ground tissues (Klamerus-Iwan et al., Citation2015). The oral toxicity of these compounds varies from very toxic to moderately toxic (50 to 1000 mg/kg body weight) in rats. Other effects on terrestrial organisms may include adverse effects on reproduction and immunity systems (Jahromi et al., Citation2014).
3.2. Water
Lubricants can contaminate water due to illegal dumping into watercourses or dragging through rainwater from streets, roads, and vehicle-parks. The most significant source of hydrocarbons in runoff waters is motor oil from automobile traffic (Vazquez-Duhalt, Citation1989). Lubricants in contact with water form a low-density organic film, preventing the oxygenation of living beings in the aqueous medium. The different constituents undergo slow different processes of volatilization, emulsification, agglomeration, photodegradation and biodegradation (Özbay, Citation2016).
Bioavailability of hydrocarbons is dependent on the solubility of saturated and aromatic hydrocarbons in water (Swigert et al., Citation2014). Studies on alkanes indicate that the solubility of carbon chains ≥ C10 in water is limited (<1 mg/L) to cause toxicity (ECHA, Citation2008).
As in the soil, the main effect of hydrocarbons in aquatic environment is the stress and then the change in the community of microorganisms. Typically, organisms may be inhibited by the presence of specific contaminants (e.g. metals) (Kapoor et al., Citation2015) although an increase of microorganisms capable of biodegrading low molecular weight hydrocarbons may occur (Deshpande et al., Citation2018).
Few studies have evaluated the toxic potential of lubricant oil for ecosystems. However, a recent study investigated the photooxidation effects on lubricant oil in an in situ mesocosm over 4 days. Morphological defects were evaluated on olive flounder (Paralichthys olivaceus) embryos in a control group (without radiation exposure) and exposure group (submitted to UV radiation). Especially tail fin fold defects were found to be significantly elevated in both the control and exposed groups to photooxidation, suggesting the toxic potential of lube oil in un-weathered conditions (Shankar et al., Citation2020).
It was found that the WLO is one of the most important mutagenic agents in the aquatic environment (Salam, Citation2016). Indeed, hydrocarbons have greater resistance to biodegradation, compared with other organic substances existing in typical wastewater treatment plants. Degradation rates vary depend on environmental conditions and decrease with increasing hydrocarbon complexity. In general, short-chain alkanes and alkenes are the most easily degraded, followed by branched alkanes and then aromatics (Xue et al., Citation2015). Contaminated water, can ultimately reach water receptors, causing adverse effects on human health and natural ecosystems (Speight, Citation2017).
3.3. Air
WLO has a heat of combustion similar to petroleum fuels (∼42,500 kcal/kg), but it is much less expensive (Arpa et al., Citation2010). For this reason, it can be used as a primary or supplemental fuel for industrial boilers, domestic oil burners, rotary cement kilns, waste disposal incinerators, among others. However, as aforementioned, WLO accumulates large amounts of metals and other contaminants, that can be released through the gases if the combustion and air pollution control units do not operate properly (Speight & Exall, Citation2014).
The indiscriminate burning of WLO, without a demetallization pretreatment, generates significant emissions of metals. The combustion of 1 L of WLO may results in 800 mg of Zn and 30 mg of Pb to the air, which corresponds to an 50–100 times increase comparing to crude-derived fuel oils (Boughton & Horvath, Citation2004). In addition, the combustion produces other harmful compounds such as dioxins, sulfur oxides, nitro compounds, hydrochloric acid, nitrogen oxides, phosphates, among others. High concentrations of HCl are formed during the combustion of WLO such as cutting oil and metal processing oil, which may contain up to 5% chloride (Audibert, Citation2003).
Burning WLO release more than 50% of lead, cadmium, chromium and zinc contained therein in the form of particles (U.S. Department of Energy, Citation2006). Besides these particulate emissions, it has been reported the presence of carcinogenic hydrocarbons of polycyclic type, which were not destroyed in the combustion (ATSDR, Citation2007).
4. A circular economy waste management approach
The current objectives of the EU toward a more circular economy represent an essential element to foster a sustainable, resource efficient and competitive economy within planetary boundaries (Geissdoerfer et al., Citation2017). This concept supports the deviation from the present mode that remains strongly based on the linear principles of production and consumption (Kirchherr et al., Citation2017). The circular economy is based on the idea that materials and products value must be kept in circulation for as long as possible, instead of being discarded or destroyed. In fact, the Waste Framework Directive (WFD) aims to avoid waste generation in line to the waste hierarchy, where prevention is the best option, followed by the re-use, recycling and other forms of recovery (European Commission, Citation2017). illustrates the concept of a circular economy applied to lubricant oils. Aspects of economy activity since the design of lubricant oil, crude refining to yield base oil, production of virgin lubricants, usage/consumption, generation of WLO, ending with the collection and recycling are covered. The disposal must be minimized (zero if possible) since it corresponds to a negative externality.
It must be highlighted that the application of the circular economy concept is to a large degree driven by local legislation (Heshmati, Citation2015). Kapustina and Horttanainen (Citation2016) reviewed the existing management systems in the EU focusing on the main stakeholders, subsidies, governmental support and treatment methods. In the scope of the circular economy, it is fundamental to develop appropriate metrics (Parchomenko et al., Citation2019). To the best of our knowledge, no systematic metrics were applied yet to the management of WLO, and thus further efforts are required.
The following sections describe the management of WLO in Europe, from the handling, storage, and collection phases, to the treatment routes applied in Europe. Particular attention will be given to regeneration, since it is of paramount importance for the circular economy concept applied to WLO.
4.1. Handling, storage, and collection of WLO
With ever-growing global environmental awareness, many countries have developed regulations for guiding the management of hazardous waste. In the EU Member States, the Waste Framework Directive (WFD) 2008/98/EC amended by the Directive (EU) 2018/851, establishes the framework for the management of WLO. Thus, guidelines to protect the environment and human health are proposed for preventing or reducing the negative impacts of WLO, as well as for reducing consequences of resources use and improving the efficiency of such practice. The framework defines the ambitious goal of bringing the EU closer to a “society of recycling.” Thus, the management of WLO should be conducted in accordance with the waste hierarchy (1 – prevention, 2 – reuse, 3 – recycling, 4 – energy recovery and 5 – disposal). The amended Article 21 states that the Member States shall take measures to guarantee that:
waste oils are collected separately unless this is not technically feasible;
waste oils are treated, giving priority to regeneration or alternatively to other equivalent recycling operations;
waste oils of different characteristics are not mixed, and waste oils are not mixed with other kinds of waste or substances, if such mixing hamper regeneration or another recycling operation;
Consequently, the handling and storage of WLO by the generators is of paramount importance for the proper management of this hazardous waste.
illustrates the typical paths of the lubricant’s life cycle, since their production from base oil and additives, generation of waste, handling, storage, collection, and finally the treatment. After use, the WLO should be stored by the generators in containers. The management systems in the EU countries typically includes a network of operators that collect WLO from generators across national territory and transport to the treatment units. Prior to collection, a quality control is carried out to confirm the technical requirements for further management (Pires & Martinho, Citation2013).
In 2016, the EU-28 generated 4,200 kt of WLO (waste category 01.3 according to Commission Regulation 849/2010). However, the quantities of WLO treated achieved just 2,370 kt (Eurostat, Citation2019) which means that there is still room for improvement of the management systems.
Besides the correct storage in proper containers to prevent leakage and spills, it is necessary to ensure that other contaminants (e.g. water, solvents, gasoline, antifreeze) are not mixed with WLO, which decrease the potential of WLO for regeneration. Indeed, external contaminations can cause the noncompliance of WLO with technical specifications defined by Member State local regulations. As a precautionary measure, waste management companies should inform waste oil generators of the consequences of mixing oils with other contaminants (e.g. water, solvents, etc.), through awareness-raising actions. In addition, specific containers must be provided to WLO generators for implementing the segregated collection. For example, shows the technical specifications established in Portugal for monitoring WLO quality at several stages of the management system, including collection, pretreatment, as well as after regeneration. The guidelines for environmentally sound management of used oils in the Mediterranean reported that in general, WLO should be accepted for regeneration if water < 2000 ppm, chlorine < 2000 ppm, PCB < 50 ppm, and flashpoint >150 °C (UNEP, Citation2015).
Table 3. Technical specifications of WLO defined by the Portuguese Environmental Agency (APA, Citation2015).
In case of the collection operator receive a contaminated WLO load, for instance with chlorine >2000 ppm, then all the tank truckload may be contaminated. A container contaminated with chlorine >2000 ppm must be disposed of as chlorinated waste and is not recycled. Thus, WLO generators must adopt suitable storage practices of different types of wastes, avoiding non-conformities. Additionally, WLO regeneration operators shall ensure that the base oil resulting from such operation do not have on their composition dangerous substances, according to the applicable legislation. WLO containing PCB/PCT with concentrations greater than 50 ppm are generally excluded from the regular management of WLO. In this case, the wastes contaminated with PCB must be destroyed by incineration (Jahromi et al., Citation2014).
4.2. Treatment and disposal routes
There are several routes for the treatment and disposal of WLO, each subject to local regulations. Currently, the most relevant disposal routes available in Europe are regeneration, laundering, reclaiming, direct burning, mild and severe reprocessing, and thermal cracking ().
Figure 8. Treatment and disposal routes available in Europe (European Commission, Citation2018).
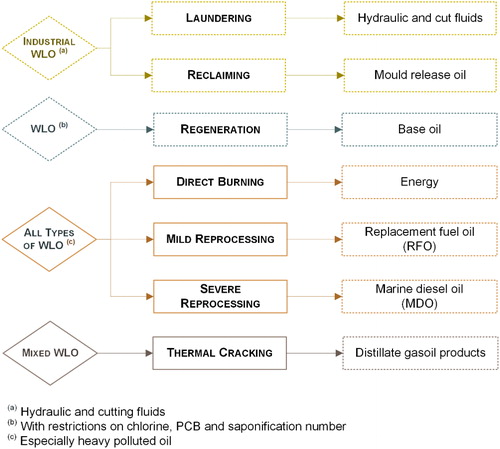
Laundering and reclaiming are suitable for recovery industrial lubricants. Laundering is a closed-loop treatment especially for hydraulic and cut fluids. The process involves the removal of solids by filtration, de-watering by vacuum distillation and the addition of fresh additives. The treated oil returns to the same company for reuse (Totten & De Negri, Citation2017). Hydraulic fluids can also be treated by reclaiming, where the lubricant is centrifuged and/or filtered and then reused (Monier & Labouze, Citation2001).
Direct burning of WLO without any pretreatment can be employed for energy recovery. This route depends greatly on local regulations and varies in popularity across Europe. The combustion can occur in cement kilns, space heaters or waste incinerators (Speight & Exall, Citation2014).
Mild reprocessing is a simple treatment process to remove water and sediments from heavy polluted WLO. After this treatment the oil can still contain metals, halogen, and sulfur but can be further used as replacement fuel oil (RFO) for combustion in road stone plants, blended into fuel oil or in power stations (Monier & Labouze, Citation2001). Severe reprocessing aims at separating the combustible portion of heavy polluted WLO from less desirable bottom fractions containing metals, noncombustible ash, and dirt. Chemical or thermal treatments are applied to produce a demetallized heavy fuel oil (HFO), also called heavy distillate, which can be used as marine diesel oil (MDO), etc. (Audibert, Citation2006).
Regeneration involves the production of base oil from WLO after the removal of contaminants, oxidation products, and additives, for further manufacture of lubricant products. The process is more complex than those described above and involves several treatment technologies to achieve a base oil with similar quality to those from crude oil refining (Audibert, Citation2006). Depending on local regulations, WLO contaminated with chlorine, PCB or with a chemical composition that hinders the treatment by regeneration must be managed using other treatment or disposal route.
Thermal cracking is based on the principle of breaking the larger hydrocarbon molecules with about 30 carbon atoms to obtain hydrocarbons with 10 – 18 carbon atoms through heating in a pressurized vessel. High-quality products such as demetallized HFO and gasoil products are obtained (Monier & Labouze, Citation2001).
In this scope, it is important to clarify that according to the Directive 2008/98/EC, recycling refers to “any recovery operation by which waste materials are reprocessed into products, materials or substances whether for the original or other purposes.” It includes laundering, reclaiming, reprocessing, and regeneration of WLO, but excludes energy recovery.
As illustrated in , the main products obtained from the several treatment options vary. However, the generation of by-products must also be considered. The most difficult stream to handle from the regeneration or fuel production facilities is the one containing heavy metals and other contaminants that are separated from the waste oil, called “asphalt flux.” The asphalt flux may be used as an asphalt component, or mixed with liquid fuels and burned or incorporated in building materials such as bricks or concrete building blocks. The leaching of contaminants from finished asphalt roads and roofs is considered unexpressive (Speight & Exall, Citation2014). The gaseous emissions from energy recovery plants have to be monitored and treated to ensure that potentially harmful compounds are not emitted in dangerous levels to the environment (Boughton & Horvath, Citation2004).
According to GEIR – the European re-refining industry group, in 2016, 42% of the WLO was used directly to regeneration within the EU countries where it was collected and 13% was regenerated after exporting to other EU countries, . The second preferred pathway is reprocessing to produce fuel oil, which accounts for 31% of the collected WLO. depicts the treatment and disposal options of some Member States reported in 2016 (Eurostat, Citation2019). EU-28 reported 85% of recycling (including regeneration and reprocessing to fuel), which is comparable to GEIR values. However, difficulties were faced for extracting reliable information from Eurostat database. The comparison between management systems across the EU countries is still very difficult despite the Directive (EU) 2018/851 indications that Member States shall report to the Commission the data on lubricants placed on the market and WLO treated each year.
Figure 9. WLO treatment/disposal routes applied in Europe in 2016 according to (a) GEIR (Citation2016) and (b) Eurostat (Citation2019). (c) Treatment routes adopted in Portugal from 2006 to 2016.
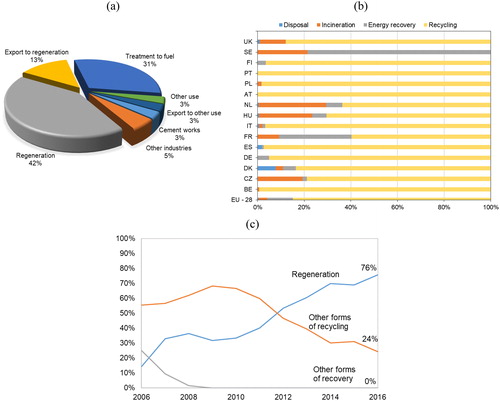
shows the management indicators for Portugal, which are disclosed by SOGILUB (company responsible for the management system). Data from SOGILUB for Portugal is reliable and therefore is used in this review as a reference to confirm the information from GEIR and Eurostat. The information reported in Eurostat for Portugal is consistent with SOGILUB’s data, which means that 100% of the WLO was recycled by regeneration or other forms of recycling in 2016. Comparing to other countries (namely SE, NL, HU, FR) Portugal did not favor incineration and energy recovery.
The EU regulations clearly identify the preference for regeneration over other forms of recycling/recovery. In fact, Directive (EU) 2018/851 states that the Commission should propose measures to expand regeneration, and that attention should be paid to the quality and final use of the regenerated and recycled products. On the one hand, the treatment option selected is forced by legislation and depends on the compliance of WLO characteristics with the established technical specifications, namely the WLO chemical composition, including type and level of contamination, base oil properties, etc. On the other hand, the choice between the various options depends on economic aspects including recovery operation costs, price of the recovered resource and market conditions.
The competition between energy recovery and regeneration of WLO hinders the regeneration across Europe. Market demand for burning waste oil directly in small-scale space heaters and in industrial-scale processes is potentially very much greater than the supply since the energy consumption from industry can be high (GEIR, Citation2016). Consequently, depending upon local environmental regulations, the price of waste oil is close to its nearest substitute of coal or medium to heavy fuel oil, and can be even lower (Speight & Exall, Citation2014). In addition, the economics affecting the relative attractiveness of the various disposal options invariably change with time and location. For instance, in some countries, the proximity between the waste oil collection centers to regeneration or other waste oil treatment/disposal facilities can save substantial costs in transportation. Therefore, alternative disposal methods to regeneration can become economically attractive depending also on the local collection/transportation costs
4.3. Regeneration technologies
According to the WFD 2008/98/EC, regeneration “means any recycling operation whereby base oils can be produced by refining waste oils, in particular by removing the contaminants, the oxidation products and the additives contained in such oils.” The obtained base oil has the potential to produce lubricating oils with similar properties as virgin base oils (Kajdas, Citation2014). Additionally, other useful by-products such as fuels, asphalt, gas oil, etc., can be recovered a limitless number of times by regeneration. In the EU, about 13% of the base oil consumed is obtained from regenerated WLO, which strongly contributes to the circular economy (reducing the dependence on natural resources) and environmental protection (GEIR, Citation2016).
The earliest and widely adopted regeneration technology in the past was the acid/clay process (Audibert, Citation2006). The treatment involved mixing WLO with concentrated sulfuric acid as an extraction medium for the removal of undesired contaminants, forming acid sludge. The acid treated oil was then mixed with clay and filtered (Dang, Citation1997). Satisfactory quality base stocks were produced by this simple technology. However, problems associated with the disposal of spent clay and acid sludge and the low yield (45–65%) discouraged the use of this process which was banned in the early 1970s (Awaja & Pavel, Citation2006; Kajdas, Citation2014).
Alternative technologies were developed based on similar separation units as the refining of crude oil for base oil production. These processes include a pretreatment, dewatering and defueling, deasphalting, finishing and fractioning steps (Gary et al., Citation2007; Hsu et al., Citation2009; Robinson, Citation2006). The regeneration plants are based on the combination of a sequence of processes using different operating conditions and producing diverse types of base oil (Pinheiro et al., Citation2018). Modern regeneration technologies can produce high-quality base oil that correspond to the group I or even group II according to the American Petroleum Institute (API) classification of base oils (Madanhire & Mbohwa, Citation2016). shows the regeneration plants in operation across Europe in 2016 (European Commission, Citation2018; GEIR, Citation2016). The total European waste oil regeneration capacity is about 1,980 kt/year (Speight & Exall, Citation2014).
Figure 10. Regeneration plants in Europe, 2016 (European Commission, Citation2018; GEIR, Citation2016).
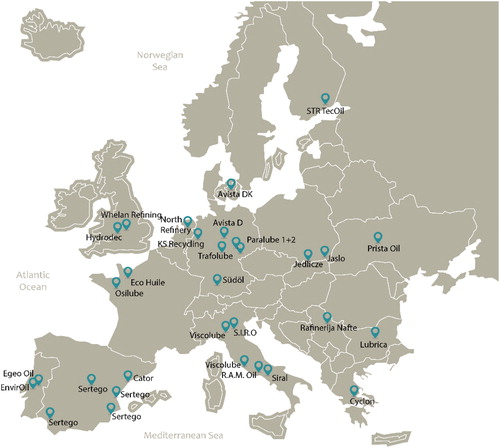
shows an overview of the technologies applied at an industrial scale. Typically, key components of the process include the deasphalting and finishing steps, which make industrial plants different from each other (Awaja & Pavel, Citation2006). A sequence of simple distillation processes can be used to separate the contaminants from the WLO. This is the case of the EcoHuile or Sotulub process, which is employed in a regeneration plant in France (Speight & Exall, Citation2014). However, low-quality base oils are obtained with this technology. Processes involving distillation and clay treatment such as the Viscolube technology, used in regeneration plants in Italy, allow to achieve a final product with acceptable quality, but a significant amount of by-products are generated (Audibert, Citation2006). Coupling distillation with solvent extraction processes using propane is also an alternative for the regeneration of WLO. This is the case of the Interline process (applied in plants in the UK and Spain) and the Snamprogetti (Italy). More sophisticated technologies involve distillation processes such as thin film evaporators (TFE) or thermal deasphalting units (TDA) coupled with hydrogenation such as the case of the KTI process, (Greece), Revivoil (Italy), CEP Process (Finland) and Mineraloel-Raffinerie Dollbergen GmbH (MRD) Process (Germany).
Table 4. Waste oil regeneration technologies.
More complex regeneration processes involving hydrotreating can deliver products that are safer (without PAH, and PCB) and with reliable performance. However, the energy usage of those modern regeneration processes is higher than that of their simpler predecessors. presents the qualitative comparison of energy requirements and operating costs for different regeneration processes. Therefore, increasing complexity of the regeneration process in order to achieve high quality products that meet market requirements increases the energy requirements and operating costs. This fact can make the economics of regeneration not so attractive for investors, preferring energy recovery as a route for the disposal of WLO.
Table 5. Comparison of energy requirements and operating cost for various regeneration processes (Hsu & Liu, Citation2011).
5. Life cycle assessment of WLO management strategies
The Waste Framework Directive establishes that WLO should be treated following the waste hierarchy, and options that deliver the best overall environmental outcome should be preferred. Life cycle assessment (LCA) studies have been used to identify the best overall environmental outcome. summarizes LCA studies that addressed WLO management in the last 15 years regarding the benefits of regeneration and other recovery options.
Table 6. Summary of life cycle assessments (LCA) for WLO disposal and treatment routes.
The LCA studies comparing the regeneration process with primary production of virgin base oil from crude, showed clearly that regeneration decreases the environmental impacts (Abdalla & Fehrenbach, Citation2017; Botas et al., Citation2017). However, LCA comparing WLO treatment options are not in agreement about the best environmental outcome. In fact, only 2 out of 7 studies indicate clearly that regeneration is the best environmentally sound treatment option (Abdalla & Fehrenbach, Citation2017; Kanokkantapong et al., Citation2009). The study of Kanokkantapong et al. (Citation2009) refers the preference for the regeneration process using the acid clay technology. For some developing countries, the use of acid remains a simple and inexpensive process that makes WLO recycling possible, but that causes problems concerning the acid sludge formed (Audibert, Citation2006). However, nowadays the acid clay process is no longer applied in Europe.
The other LCA studies have shown that while regeneration offers great benefits regarding in some impact categories, it is not possible to conclude that regeneration is the best option. Collins et al. (Citation2017) determined that no single disposition showed consistently lower impacts. Their results indicated that maximizing collection is the best policy to reduce either crude oil or energy consumption and could achieve higher natural resource savings than focusing on differences between disposal options. Pires and Martinho (Citation2013) compared 16 management alternatives, indicating that none of the management alternatives showed better environmental performance. The tested systems included combinations of various mild processing techniques and recovery options adopted in Portugal, namely recycling during expanded clay production, recycling and electric energy production, re-refining, energy recovery during cement production, and energy recovery in the production of expanded clay. Kalnes et al. (Citation2006) also indicated that depending on the impact categories assessed, burning WLO in cement kilns or the regeneration process have different impacts on the environment. Boughton and Horvath (Citation2004) showed that the recovery options by regeneration and production of MDO are both favorable in terms of environmental impacts than combustion of WLO as fuel with no pollution controls (Boughton & Horvath, Citation2004).
Therefore, the current emphasis placed by the European Commission on regeneration of WLO over other recovery options may not be justified by the LCA studies in the literature. It is important to note that there is uncertainty associated with different impact assessment methods. LCA results must be seen in the light of the inherent assumptions in the modeling phase to reach the goal and scope of the study.
Nevertheless, it is recommended that further studies must be undertaken regarding not only environmental aspects. Considering also economic and social issues and using transparent criteria and assumptions could provide a strong basis for an unbiased assessment of the relative merits of the alternative recycling processes under the assumed conditions. Other factors such as the lubricants and fuels market, market uses, taxation rates, power production, industrial energy consumption, distance between collection and treatment, and ongoing technological development should be accounted for the selection of the proper treatment
6. Future major developments and concerns regarding regeneration
The EU seeks to accelerate the transition to a circular economy, where resources are re-used or re-introduced in production processes, instead of being discarded after use (Ghisellini et al., Citation2016; Gregson et al., Citation2015). Directive (EU) 2018/851 states that by 31 December 2022, the Commission shall examine data on waste oils provided by the Member States with a view to considering the feasibility of adopting measures for their treatment, including quantitative targets on regeneration and any further measures to promote their regeneration. According to (GEIR, Citation2004), the introduction of regeneration targets would better support the objectives toward a circular economy, encouraging the separate collection. This goal represents a challenge for most of the Member States, including countries with already well-established management practices.
The improvement of the WLO management system and compliance with regeneration targets are closely related to the chemical characteristics of the WLO generated. Nowadays, new technologies enable lower oil consumption and the formulation of advanced lubricants can lead to longer periods between oil changes, thus decreasing the generation of waste. Besides that, largely due to difficulties and costs of segregation during collection of WLO, regenerated base stocks may not comply with the performance requirements for advanced lubricants. In order to produce high quality lubricants, more sophysticated processes are required, which can only be achieved with significant energy inputs. In addition, the incorrect handling of WLO by generators through the mixing with wastes of different characteristics such as brake fluids, antifreeze and other solvents, can hamper further regeneration or recovery. Moreover, the type of WLO generated is dependent on the original composition of the virgin oil. The influence of the type of base oil on the regeneration process is one issue that is seldom addressed in the literature and is a key factor for the increase of the WLO regeneration rate.
The lubricant industry uses several ways to classify lubricants. From the consumer’s point of view, it is important that the essential information is provided on the label for the selection of the correct virgin oil for a specific application. Therefore, in most cases, the classification given on the packaging or in the safety data sheet is based on viscosity grade, application (engine oil, gear oil, hydraulic fluid, etc.), and sometimes the stock source is also provided (mineral versus synthetic). In the EU Member States, when the lubricant oil becomes waste, the generator must assign a code number according to the European List of waste (LoW). This list accounts for lubricants from several main applications () within which the stock source must be specified (mineral-based chlorinated or non-chlorinated, synthetic, readily biodegradable or others). Nevertheless, the virgin oil producer is not obliged to provide information about the chemical composition of the base oil, even because this information is often unknown.
Figure 11. Virgin oil classification commonly adopted by manufacturers and waste lubricant oil categories available in the European list of waste that may be used to select a treatment.
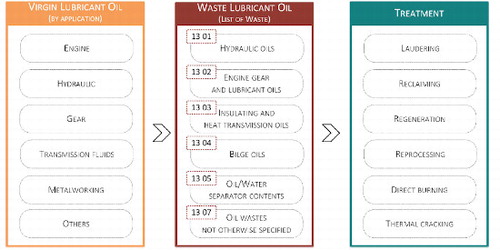
Regarding the segregation of WLO, the WFD states that waste oils of different characteristics should not be mixed, if such mixing impedes their regeneration. In addition, the mixing of WLO with different characteristics also decreases the market value of the finished base stock product, which is a critical aspect for the success of regeneration. However, there is no recommendation in the legislation or in the literature on exactly what types of WLO should not be mixed/segregated. According to the LoW there are more than 30 entries for WLO divided between applications ( only shows the main categories of LoW codes for WLO). This makes impossible to segregate the different types of WLO during storage and collection phases based on those codes. Therefore, in most of the cases, all WLO is mixed and forwarded to treatment. This makes the regeneration more difficult and costly, and some of WLO must be directed to other forms of recycling.
The regeneration industry has been struggling with the fact that after the alkaline treatment and in stages that require a substantial temperature increase such as distillation, some WLO form a gel type oil that can cause plugging of the plant. A recent study reported that this phenomenon is mostly related to the use of synthetic lubricants based on esters, which increase the amount of saponifiable matter present in the WLO (Pinheiro, Ascensão, Reis, et al., Citation2017). Synthetic ester-based oils will give rise to the coagulation phenomena responsible for blocking regeneration plants using alkaline treatments, hampering the regeneration process (Pinheiro et al., Citation2020). Consequently, WLO with synthetic ester and phosphate ester base oil should be segregated at the source (Kupareva et al., Citation2013). This problem is likely to be aggravated in the next years due to developments in the lubricants market. In 2015 the global demand for synthetic oils was 8–10% of the total lubricant. Of these, about 30% were of ester type oils, with an upward trend expected for the forthcoming years (HIS Markit, Citation2015).
One opportunity for the improvement of the management systems is a more in-depth knowledge of the chemical characteristics of WLO that can or cannot be mixed. More specific indications could be given to the generators on the correct practices for the segregation of WLO. In addition, virgin oil producers should provide more specific information on the chemical composition (e.g. ester type, silicone oil, etc.) of the base oil to allow the correct segregation. This would support the fulfillment of regeneration targets in Europe, but will increase significantly the collection and segregation costs.
7. Conclusions
The disposal of WLO into the environment may pose a high risk of damage to ecosystems. The good practices of a waste management system must be based on a holistic circular economy approach, which includes the design and production of lubricants, usage/consumption, generation of WLO, ending up with the collection and recycling. Regarding the management of waste generated, EU countries show a trending for recycling WLO, with a competition between regeneration and energy recovery. In the face of market pressure for the usage of WLO as fuel, EU legislation suggests the introduction of policies to promote regeneration in preference to direct burning or production of fuels. According to LCA studies, regeneration reduces the environmental impacts, comparing with the production of virgin base oil from crude. However, not all LCA studies confirm that regeneration is the best option regarding all impact categories. The selection of the treatment route should consider lubricant market, energy consumption, distance to treatment facilities, operation costs, final product quality and technological development.
Abbreviations | ||
ADP | = | abiotic depletion potential |
AP | = | acidification potential |
API | = | American Petroleum Institute |
AT | = | Austria |
BAT | = | best available techniques |
BE | = | Belgium |
CA | = | carcinogens |
CC | = | climate change |
CED | = | cumulative energy demand |
CZ | = | Czechia |
DE | = | Germany |
DK | = | Denmark |
EP | = | eutrophication potential |
ES | = | Spain |
ET | = | ecotoxicity |
EU-28 | = | European Union - 28 countries |
FAEP | = | freshwater aquatic ecotoxicity potential |
FFD | = | fossil fuel depletion |
FI | = | Finland |
FR | = | France |
FSEP | = | freshwater sedimental ecotoxicity potential |
GEIR | = | Groupement Européen de l’Industrie de la Régénération |
GNP | = | gross national product |
GWP | = | global warming potential |
HFO | = | heavy fuel oil |
HH | = | human health |
HM | = | heavy metals |
HP | = | hazardous property |
HTP | = | human toxicity potential |
HU | = | Hungary |
IT | = | Italy |
LCA | = | life cycle assessment |
LoW | = | list of waste |
LU | = | land use |
MDO | = | marine diesel oil |
Mi | = | minerals |
NL | = | Netherlands |
NMP | = | N-methyl-2-pyrrolidone |
ODP | = | ozone depletion potential |
PAG | = | polyalkylene glycols |
PAH | = | polycyclic aromatic hydrocarbon |
PAO | = | polyalphaolefins |
PCB | = | polychlorinated biphenyl |
PCT | = | polychlorinated terphenyl |
PL | = | Poland |
PM | = | particulate matter |
POCP | = | photochemical oxidation potential |
PT | = | Portugal |
QC | = | quality control |
RA | = | radiation |
RD | = | resource depletion |
RFO | = | replacement fuel oil |
RI | = | respiratory inorganics |
RO | = | respiratory organics |
SE | = | Sweden |
STOT | = | specific target organ toxicity |
TDA | = | thermal deasphalting |
TEP | = | terrestrial ecotoxicity potential |
TFE | = | thin film evaporation |
TPH | = | total petroleum hydrocarbons |
UK | = | United Kingdom |
VGO | = | vacuum gas oil |
WFD | = | waste framework directive |
WLO | = | waste lubricant oil |
Acknowledgements
The authors gratefully acknowledge the financial support from SOGILUB – Sociedade de Gestão Integrada de Óleos Lubrificantes Usados, Lda.
References
- Abdalla, N., & Fehrenbach, H. (2017). Updating the study Ecological and energetic assessment of re-refining waste oils to base oils Substitution of primarily produced base oils including semi-synthetic and synthetic compounds. ifeu – Institut für Energie. https://bva-altoelrecycling.de/files/uploads/2017/10/oekobilanz_ifeu_2017.pdf
- APA. (2015). Especificações Técnicas dos Óleos Usados. https://www.apambiente.pt/_zdata/Politicas/Residuos/FluxosEspecificosResiduos/OU/Especific%0Aacoes_Tecnicas_Oleos_usados-Aprovado.pdf
- Arpa, O., Yumrutas, R., & Demirbas, A. (2010). Production of diesel-like fuel from waste engine oil by pyrolitic distillation. Applied Energy, 87(1), 122–127. doi:10.1016/j.apenergy.2009.05.042
- ATSDR. (2007). Toxicological profile for lead. https://www.atsdr.cdc.gov/toxprofiles/tp13.pdf
- Audibert, F. (2003). Les huiles usagées: Reraffinage et valorisation énergétique. Edition Technip.
- Audibert, F. (2006). Waste engine oils: Rerefining and energy recovery. Elsevier.
- Awaja, F., & Pavel, D. (2006). Design aspects of used lubricating oil re-refining. Elsevier.
- Battersby, N. S. (2000). The biodegradability and microbial toxicity testing of lubricants-some recommendations. Chemosphere, 41(7), 1011–1027. doi:10.1016/S0045-6535(99)00517-2
- Benda, R., Bullen, J., & Plomer, A. (1996). Synthetics basics: Polyalphaolefins — base fluids for high-performance lubricants. Journal of Synthetic Lubrication, 13(1), 41–57. doi:10.1002/jsl.3000130105
- Borza, M., Leoncini, S., & Modenesi, A. (1983). Spent oil recovery process (U.S. Patent No. 4406778 A). U.S. Patent and Trademark Office.
- Botas, J. A., Moreno, J., Espada, J. J., Serrano, D. P., & Dufour, J. (2017). Recycling of used lubricating oil: Evaluation of environmental and energy performance by LCA. Resources, Conservation and Recycling, 125(1), 315–323. doi:10.1016/j.resconrec.2017.07.010
- Boughton, B., & Horvath, A. (2004). Environmental assessment of used oil management methods. Environmental Science & Technology, 38(2), 353–358. doi:10.1021/es034236p
- Bronshteyn, L. A., & Kreiner, J. H. (1999). Energy efficiency of industrial oils. Tribology Transactions, 42(4), 771–4694. doi:10.1080/10402009908982281
- Collins, M., Schiebel, K., Dyke, P. (2017). Life cycle assessment of used oil management. https://www.api.org/∼/media/Files/Certification/Engine-Oil-Diesel/Publications/LCA-of-Used-Oil-Mgmt-ERM-10012017.pdf
- Dang, G. S. (1997). Rerefining of used oils — a review of commercial processes. Tribotest, 3(4), 445–457. doi:10.1002/tt.3020030407
- Day, M., Bauer, C. (2007). Water contamination in hydraulic and lube systems. https://www.machinerylubrication.com/Read/1084/water-contamination-lube
- Deshpande, R. S., Sundaravadivelu, D., Techtmann, S., Conmy, R. N., Santo Domingo, J. W., & Campo, P. (2018). Microbial degradation of Cold Lake Blend and Western Canadian select dilbits by freshwater enrichments. Journal of Hazardous Materials, 352, 111–120. doi:10.1016/j.jhazmat.2018.03.030
- ECHA. (2008). Support document for identification of alkanes, C10-13, chloro as a substance of very high concern. https://echa.europa.eu/documents/10162/2edcfedb-ec53-4754-8598-e787a8ff7a58
- El-Fadel, M., & Khoury, R. (2001). Strategies for vehicle waste-oil management: A case study. Resources, Conservation and Recycling, 33(2), 75–91. doi:10.1016/S0921-3449(01)00058-1
- European Commission. (2017). Towards a circular economy - Waste management in the EU. http://www.europarl.europa.eu/RegData/etudes/STUD/2017/581913/EPRS_STU%282017%29581913_EN.pdf
- European Commission. (2018). Best available techniques (BAT) reference document for waste treatment industrial. Emissions Directive 2010/75/EU (Integrated Pollution Prevention and Control). European Commission.
- Eurostat. (2019). Treatment of waste by waste category, hazardousness and waste management operations. http://appsso.eurostat.ec.europa.eu
- Fuchs. (2017). Fuchs group - setting standards worldwide. https://www.fuchs.com/fileadmin/Home/Praesentation/2017/FUCHS_Investor_May.pdf
- Fuchs. (2018). Future challenges of the lubricants industry. https://www.fuchs.com/fileadmin/Home/Praesentation/2018/180618_FCMD_CTO.pdf
- Gary, J. G., Handwerk, G. E., & Kaiser, M. J. (2007). Petroleum refining: Technology and economics. (5th ed.). CRC Press.
- GEIR. (2004). An environmental review of waste oils regeneration. http://www.geir-rerefining.org/documents/PositionpaperGEIR161104.pdf
- GEIR. (2016). Waste framework directive revision: European waste oil re-refining industry position. https://www.geir-rerefining.org/wp-content/uploads/GEIRpositionpaperWFD_2016_FINAL.pdf
- Geissdoerfer, M., Savaget, P., Bocken, N. M. P., & Hultink, E. J. (2017). The circular economy – A new sustainability paradigm? Journal of Cleaner Production, 143, 757–768. doi:10.1016/j.jclepro.2016.12.048
- Ghisellini, P., Cialani, C., & Ulgiati, S. (2016). A review on circular economy: The expected transition to a balanced interplay of environmental and economic systems. Journal of Cleaner Production, 114, 11–32. doi:10.1016/j.jclepro.2015.09.007
- Gregson, N., Crang, M., Fuller, S., & Holmes, H. (2015). Interrogating the circular economy: The moral economy of resource recovery in the EU. Economy and Society, 44(2), 218–243. doi:10.1080/03085147.2015.1013353
- Gustavsson, F. (2013). Triboactive component coatings. Tribological testing and microanalysis of low-friction tribofilms [Doctoral Thesis]. Digitala Vetenskapliga Arkivet. Uppsala University. http://www.diva-portal.org/smash/record.jsf?pid=diva2%3A585099&dswid=1213
- Harnoy, A. (2003). Bearing design in machinery: Engineering tribology and lubrication. Marcel Dekker, Inc.
- Heshmati, A. (2015). A review of the circular economy and its implementation. Heshmati, Almas. IZA Discussion Paper No. 9611. https://ssrn.com/abstract=2713032
- Hsu, Y.-L., Lee, C.-H., & Kreng, V. B. (2009). Analysis and comparison of regenerative technologies of waste lubricant. WSEAS Transactions on Environment and Development, 5(3), 295–309.
- Hsu, Y. L., & Liu, C. C. (2011). Evaluation and selection of regeneration of waste lubricating oil technology. Environmental Monitoring and Assessment, 176(1-4), 197–212. doi:10.1007/s10661-010-1576-3
- HIS Markit (2015). Synthetic lubricants - specialty chemicals update program. https://ihsmarkit.com/products/chemical-synthetic-lubricants-scup.html
- IARC. (2018). List of classifications, Volumes 1–120. http://monographs.iarc.fr/ENG/Classification/latest_classif.php
- Jafari, A. J., & Hassanpour, M. (2015). Analysis and comparison of used lubricants, regenerative technologies in the world. Resources, Conservation and Recycling, 103, 179–191. doi:10.1016/j.resconrec.2015.07.026
- Jahromi, F. A., Kannan, N., Zakaria, M. P., & Aris, A. Z. (2014). Persistent contaminants in waste oils: A short review on PCBs and PAHs as main contaminants. In A. Z. Aris, T. H. Tengku Ismail, R. Harun, A. M. Abdullah, & M. Y. Ishak (Eds.), From sources to solution (pp. 107–110). Springer.
- Jhanani, S., & Joseph, K. (2011). Used oil generation and management in the automotive industries. International Journal of Environmental Sciences, 2(2), 638–648.
- John, R. C., Itah, A. Y., Essien, J. P., & Ikpe, D. I. (2011). Fate of nitrogen-fixing bacteria in crude oil contaminated wetland ultisol. Bulletin of Environmental Contamination and Toxicology, 87(3), 343–353. doi:10.1007/s00128-011-0320-1
- Kajdas, C. (2014). Re-refining technologies. In T. Mang (Ed.), Encyclopedia of lubricants and lubrication (pp. 1554–1568). Springer-Verlag.
- Kalnes, T. N., Shonnard, D. R., & Schuppel, A. (2006). LCA of a spent lube oil re-refining process. Computer Aided Chemical Engineering, 21, 713–718. doi:10.1016/S1570-7946(06)80129-X
- Kanokkantapong, V., Kiatkittipong, W., Panyapinyopol, B., Wongsuchoto, P., & Pavasant, P. (2009). Used lubricating oil management options based on life cycle thinking. Resources, Conservation and Recycling, 53(5), 294–299. doi:10.1016/j.resconrec.2009.01.002
- Kapoor, V., Li, X., Elk, M., Chandran, K., Impellitteri, C. A., & Santo Domingo, J. W. (2015). Impact of heavy metals on transcriptional and physiological activity of nitrifying bacteria. Environmental Science & Technology, 49(22), 13454–13462. doi:10.1021/acs.est.5b02748
- Kapustina, V., & Horttanainen, M. (2016). A review of the existing waste oil management systems. Journal of Solid Waste Technology & Management, 42(1), 948–961.
- Kayode, J., Olowoyo, O., & Oyedeji, A. (2009). The effects of used engine oil pollution on the growth and early seedling performance of Vigna uniguiculata and Zea mays. Research Journal of Soil Biology, 1(1), 15–19. doi:10.3923/rjsb.2009.15.19
- Kentonm, K. J. (1998). Oil re-refining method and apparatus (U.S. Patent No. 5,759,385). U.S. Patent and Trademark Office.
- Kirchherr, J., Reike, D., & Hekkert, M. (2017). Conceptualizing the circular economy: An analysis of 114 definitions. Resources, Conservation and Recycling, 127, 221–232. doi:10.1016/j.resconrec.2017.09.005
- Klamerus-Iwan, A., Błońska, E., Lasota, J., Kalandyk, A., & Waligórski, P. (2015). Influence of oil contamination on physical and biological properties of forest soil after chainsaw use. Water, Air, and Soil Pollution, 226(11), 389. doi:10.1007/s11270-015-2649-2
- Kupareva, A., Mäki-Arvela, P., & Murzin, D. Y. (2013). Technology for rerefining used lube oils applied in Europe: A review. Journal of Chemical Technology & Biotechnology, 88(10), 1780–1793. doi:10.1002/jctb.4137
- Laing, D., & Thomas, H. (2014). Food and pharma industry lubrication. In T. Mang (Ed.), Encyclopedia of lubricants and lubrication (pp. 645–679). Springer-Verlag.
- Lugt, P. M. (2013). Grease lubrication in rolling bearings. Wiley.
- Lynch, T. R. (2007). Process chemistry of lubricant base stocks. CRC Press.
- Madanhire, I., & Mbohwa, C. (2016). Mitigating environmental impact of petroleum lubricants. Springer.
- Magnabosco, L. M., & Rondeau, W. A. (1993). Improved process for the production of base stock oils from used oil (EP Patent No. 0574272 A2). European Patent Office.
- Mang, T., Bobzin, K., & Bartels, T. (2011). Industrial tribology: Tribosystems, friction, wear and surface engineering, lubrication. Wiley-VCH.
- Mang, T., & Dresel, W. (2017). Lubricants and lubrication. Wiley.
- Mannetje, L., & Laghate, A. (1990). Process for re-refining spent lube oils (U.S. Patent No. 4941967 A). U.S. Patent and Trademark Office.
- Minana, J., Schieppati, R., & Dalla, F. (1994). Process to re-refine used oils (EP Patent No. 0618959 A1). European Patent Office.
- Monier, V., Labouze, E. (2001). Critical review of existing studies and life cycle analysis on the regeneration and incineration of waste oils. http://ec.europa.eu/environment/waste/studies/oil/waste_oil.pdf
- Morkunas, I., Woźniak, A., Mai, V. C., Rucińska-Sobkowiak, R., & Jeandet, P. (2018). The role of heavy metals in plant response to biotic stress. Molecules, 23(9), 2320. doi:10.3390/molecules23092320
- Mortier, R. M., Fox, M. F., & Orszulik, S. T. (2010). Chemistry and technology of lubricants (3rd ed.). Springer.
- Özbay, H. (2016). The effects of motor oil on the growth of three aquatic macrophytes. Acta Ecologica Sinica, 36(6), 504–508. doi:10.1016/j.chnaes.2016.08.005
- Parchomenko, A., Nelen, D., Gillabel, J., & Rechberger, H. (2019). Measuring the circular economy - A multiple correspondence analysis of 63 metrics. Journal of Cleaner Production, 210, 200–216. doi:10.1016/j.jclepro.2018.10.357
- Pillai, I., Ritchie, L., Heywood, R., Wilson, G., Pahlavanpour, B., Setford, S., & Saini, S. (2005). Development of an improved analytical method for the determination of carcinogenic polycyclic aromatic hydrocarbons in transformer oil. Journal of Chromatography A, 1064(2), 205–212. doi:10.1016/j.chroma.2004.12.066
- Pinheiro, C. T., Quina, M. J., Gando-Ferreira, L. M., & Cardoso, C. M. (2020). Effect of chemical additives on the regeneration of waste lubricant oil. In C. Vilarinho et al. (Ed.), Wastes: Solutions, treatments and opportunities (Vol. 3, pp. 13–18). CRC Press – Taylor & Francis Group.
- Pinheiro, C. T., Ascensão, V. R., Cardoso, C. M., Quina, M. J., & Gando-Ferreira, L. M. (2017). An overview of waste lubricant oil management system: Physicochemical characterization contribution for its improvement. Journal of Cleaner Production, 150, 301–308. doi:10.1016/j.jclepro.2017.03.024
- Pinheiro, C. T., Ascensão, V. R., Reis, M. S., Quina, M. J., & Gando-Ferreira, L. M. (2017). A data-driven approach for the study of coagulation phenomena in waste lubricant oils and its relevance in alkaline regeneration treatments. Science of the Total Environment, 599–600, 2054–2064. doi:10.1016/j.scitotenv.2017.05.124
- Pinheiro, C. T., Pais, R. F., Quina, M. J., & Gando-Ferreira, L. M. (2018). Regeneration of waste lubricant oil with distinct properties by extraction-flocculation using green solvents. Journal of Cleaner Production, 200, 578–587. doi:10.1016/j.jclepro.2018.07.282
- Pires, A., & Martinho, G. (2013). Life cycle assessment of a waste lubricant oil management system. The International Journal of Life Cycle Assessment, 18(1), 102–112. doi:10.1007/s11367-012-0455-2
- Pirro, D. M., Daschner, E., & Wessol, A. A. (2001). Lubrication fundamentals (2nd ed.). CRC Press.
- Pöhler, J., Mödler, M., Bruhnke, D., & Hindenberg, H. (2004). Method for reprocessing waste oils (U.S. Patent No. 6712954 B1). U.S. Patent and Trademark Office.
- Ray, S., Rao, P. V. C., & Choudary, N. V. (2012). Poly-α-olefin-based synthetic lubricants: A short review on various synthetic routes. Lubrication Science, 24(1), 23–44. doi:10.1002/ls.166
- Rizvi, S. Q. A. (2009). A comprehensive review of lubricant chemistry, technology, selection, and design. ASTM International.
- Robinson, P. R. (2006). Petroleum processing overview. In C. S. Hsu & P. R. Robinson (Eds.), Practical advances in petroleum processing (Vol. 1, pp. 1–76). Springer.
- Rudnick, L. (2013). Synthetics, mineral oils, and bio-based lubricants: Chemistry and technology. CRC Press.
- Rudnick, L., & Shubkin, R. (1999). Synthetic lubricants and high-performance functional fluids (2nd ed.). CRC Press.
- Salam, L. B. (2016). Metabolism of waste engine oil by Pseudomonas species. 3 Biotech, 6(1), 98. doi:10.1007/s13205-016-0419-5
- Sequeira, A. (1994). Lubricant base oil and wax processing. Marcel Dekker, Inc.
- Shankar, R., Jung, J. H., Loh, A., An, J. G., Ha, S. Y., & Yim, U. H. (2020). Environmental significance of lubricant oil: A systematic study of photooxidation and its consequences. Water Research, 168, 115183. doi:10.1016/j.watres.2019.115183
- Speight, J. G. (2017). Environmental organic chemistry for engineers. Butterworth-Heinemann.
- Speight, J. G., & Exall, D. I. (2014). Rerefining of used lubricating oils. CRC Press.
- Srivastava, V., Sarkar, A., Singh, S., Singh, P., de Araujo, A. S. F., & Singh, R. P. (2017). Agroecological responses of heavy metal pollution with special emphasis on soil health and plant performances. Frontiers in Environmental Science, 5, 64. doi:10.3389/fenvs.2017.00064
- Stachowiak, G. W., & Batchelor, A. W. (2014). Engineering tribology (4th ed.). Elsevier.
- Swigert, J. P., Lee, C., Wong, D. C. L., & Podhasky, P. (2014). Aquatic hazard and biodegradability of light and middle atmospheric distillate petroleum streams. Chemosphere, 108, 1–9. doi:10.1016/j.chemosphere.2014.02.028
- Totten, G. E., & De Negri, V. J. (2017). Handbook of hydraulic fluid technology (2nd ed.). CRC Press.
- Totten, G. E., Westbrook, S., & Shah, R. (2003). Fuels and lubricants handbook: Technology, properties, performance, and testing. ASTM International. doi:10.1520/MNL37WCD-EB
- U.S. Department of Energy. (2006). Used oil re-refining study to address energy policy Act of 2005 Section 1838. https://fossil.energy.gov/epact/used_oil_report.pdf
- UK Environment Agency. (2015). Technical guidance WM3: Waste classification - Guidance on the classification and assessment of waste. https://www.gov.uk/government/uploads/system/uploads/attachment_data/file/427077/LIT_10121.pdf
- UNEP. (2015). Guidelines for environmentally sound management of used oils in the Mediterranean. UNEP.
- US EPA. (2011). Environmentally acceptable lubricants (Report No. EPA 800‐R‐11‐002). Washington, DC: United States Environmental Protection Agency Office of Wastewater Management.
- Vazquez-Duhalt, R. (1989). Environmental impact of used motor oil. The Science of the Total Environment, 79(1), 1–23. doi:10.1016/0048-9697(89)90049-1
- Vwioko, D. E., Anoliefo, G. O., & Fashemi, S. D. (2006). Metal concentration in plant tissues of Ricinus communis L. (Castor oil) grown in soil contaminated with spent lubricating oil. Journal of Applied Sciences and Environmental Management, 10(3), 127–134. doi:10.4314/jasem.v10i3.17331
- Williams, M. R., & Krzykawski, J. (2001). Method for obtaining base oil and removing impurities from used oil products (U.S. Patent 6174431 B1). U.S. Patent and Trademark Office.
- Xue, J., Yu, Y., Bai, Y., Wang, L., & Wu, Y. (2015). Marine oil-degrading microorganisms and biodegradation process of petroleum hydrocarbon in marine environments: A review. Current Microbiology, 71(2), 220–228. doi:10.1007/s00284-015-0825-7
- Zakaria, M. P., Takada, H., Tsutsumi, S., Ohno, K., Yamada, J., Kouno, E., & Kumata, H. (2002). Distribution of polycyclic aromatic hydrocarbons (PAHs) in rivers and estuaries in Malaysia: A widespread input of petrogenic PAHs. Environmental Science & Technology, 36(9), 1907–1918. doi:10.1021/es011278