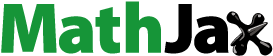
ABSTRACT
Mg coating is one of the viable options for Ti to enhance its bioactivity. However, the rapid corrosion of Mg coating in physiological conditions has delayed their introduction for therapeutic applications to date. In this study, a ceramic layer between Ti substrate and Mg coating was prepared and heat treatment was also carried out to improve the corrosion resistance of the Mg coating. The in vitro test revealed that the ceramics layer decreased the galvanic corrosion between the Mg coatings and substrate, improved the corrosion resistance and wear properties. Furthermore, the post-heat treatment of Mg coating on Ti had a significant effect on the surface morphology and microstructure of the coating. The heat-treated Mg coatings on Ti at 400 °C for 10 min substrates showed an improved corrosion resistance compared with the untreated substrate. The heat treatment significantly influenced the hardness, adhesion, friction coefficient, and wear resistance of the coating.
Introduction
Due to excellent biocompatibility and advanced mechanical properties, Ti and its alloy have been widely used in dentistry and orthopaedic surgery to enhance, support or replace an existing biological structure [Citation1]. However, Ti-based metal has still some shortcomings yet to be resolved. The major challenge for titanium is to improve the osteointegration and enhance the bioactivity of the implants with bone regeneration and healing [Citation2]. 3D printed porous structure is the common approaches to improve bone growth and enhance the bioactivity of Ti. While the mechanical strength of 3D printed Ti is too low to satisfy completely the clinical demands. To improve the mechanical strength, implant efficiency, bioactivity and osseointegration, a variety of surface treatment has been explored. Surface modifications such as CaP coating and the double-layer coatings composed of Sr and Mg can accelerate bone growth, and the physicochemical changes of the implant induced a firm bonding with the bone [Citation3,Citation4].
Recently, Mg-based metals have shown great potential to be used as biocompatible and biodegradable materials due to their excellent properties, including relatively close elastic modulus and density (41–45 GPa, 1.7–2.0 g/cm3) to the human bones (10–40 GPa, 1.8–2.1 g/cm3) [Citation5–8]. And the corrosion resistance of magnesium and its alloy can be improved by heat treatment and severe plastic deformation techniques [Citation9–12]. Furthermore, Mg has a positive effect on bone tissue, which could improve the reconstruction and healing of the associated bone. Witte et al. reported that Mg-based materials showed a positive effect on the bone tissue and high Mg ion activates the surrounding bone cell [Citation13,Citation14]. However, Mg and its alloy with low mechanical property (compared with Ti alloy) cannot be applied to implants with high mechanical requirements. Therefore, many studies dedicate to improve the bioactivity of Ti alloy by constructing Mg coating. Xiaohui et al. reported that the surface modification of Ti via plasma electrolytic technique to fabricate a Mg-TiO2 coatings can significantly enhance the biological activity of Ti. The pores structure of Mg-TiO2 coating improved the adhesion and proliferation of bone marrow cells and showed good cytocompatibility and no cytotoxicity [Citation15]. Mg was coated on porous titanium scaffolds to enhance their osteointegration properties in our previous study, the results demonstrated improved osteogenesis and angiogenesis ability in vitro and in vivo [Citation4,Citation16].
However, the rapid corrosion of Mg coating in physiological conditions due to the severe galvanic corrosion and loose coating morphology has delayed their introduction for therapeutic applications to date [Citation17]. Therefore, a ceramic layer was prepared on the Ti substrate before the Mg coating preparation to decrease the direct contact of the Mg coating and Ti substrate and the galvanic corrosion of the Mg coating. Furthermore, heat treatment on the Mg coating was also carried out to improve the compactness of the coating and enhance its corrosion resistance.
Experimental methods
Materials preparation
In this study, two ceramic layers (the micro-arc oxidation (MAO) layer, and the TiO2 layer) were prepared on the surface of Ti substrates, respectively, for comparison. For the MAO layer preparation, a pulsed bipolar electrical source (WHD-20) with a power of 2 kW was used, the main electrolyte ingredients were 8 g/L KF, 4 g/L(NaPO3)6 and 1.2 g/L Ca(OH)2, and the working voltage, frequency, duty cycle, and preparation time were 360 V, 1000 Hz, 40%, and 5 min, respectively. The TiO2 layer was prepared in a furnace at 945°C for 50 min and then cooled in the furnace.
After the MAO or TiO2 layer preparation, samples were cleaned with absolute ethanol and dried in the air. Then, pure Mg coating was prepared by physical vapour deposition (PVD) with 700 °C Mg target and 100 °C Ti substrate for 40 min at a typical vacuum pressure of 10−5 Torr. Pure Mg-coated samples were then heat-treated at different temperatures up to 400°C for 10 min to evolve a dense surface. Scanning electronic microscopy (SEM) was employed to investigate the surface morphology of the coating. XRD was employed to characterise the phases of the coatings.
Immersion test
Samples were immersed in D-Hank’s solution with a solution ratio of 1.25 cm2/mL for three weeks at 37°C according to the standard GB/T 16886 method [Citation18]. Hank’s solution was refreshed every day. Five parallel samples were used, and the pH values of Hank’s solution were monitored.
Electrochemical experiment
The electrochemical test was performed at 37°C in D-Hank’s solution by Gamry 600 plus instrument [Citation19]. Samples with a surface area of 0.785 cm2 (Φ10 mm) were moulded in epoxy resin for the electrochemical test. The three-electrode cell used in this experiment consists of the samples as the working electrode, saturated calomel electrode (SCE) as the reference electrode and platinum as the counter electrode. The test started after the 1800 s at an open-circuit potential (OCP). Then, the electrochemical impedance spectroscopy (EIS) test was carried out at the OCP with a frequency from 100 kHz to 10 mHz. The potentiodynamic polarisation test started from −0.25 V to 0.35 V with reference to OCP and the scan rate was 0.5 mV/s. The test was repeated three times for each coating.
Adhesion strength measurement
The adhesion strength of Mg coatings was assessed using an Instron 5582 mechanical testing device (Instron Corporation, Norwood, United States of America). The cylindrical samples (n = 3) with a diameter of 20 mm were employed by the ISO 13779–4 standard. The loading fixtures were adhered to the Mg-coated surface with adhesive glue and dried for 3 hours in a 100 °C oven. The fixtures were tensile tested till failure at a constant cross-head speed of 1.0 ± 0.01 mm/min.
Wear test
The wear test was carried out by a Kearns Model VHX6000, Friction and wear testing UTM-2 M machine, with an applied horizontal force of 5 N, covering a distance of 5 mm in the forward and backward directions. No lubrication was used during the test. Silicon nitride ball/coated Mg sliding couple were adopted to study the influence of different treatments on the wear property. The highest speed and frequency of the electric motor were 12.5 cm/s and 2 Hz respectively. The test was carried out three times for each coating. The wear volume loss V was calculated as follows [Citation20]:
where A is the cross-section area (mm2) of the wear track which is measured by using a surface profile measurement instrument (AlphaStep IQ) and L is the length of the track.
Hardness test
A Nano Indenter (Nano instruments) fitted with a Berkovich probe was used to detect the hardness change along with the depth of a coated sample. A calibrator was used to calibrate the Nano indenter. The force used in the experiments was 20 mN, and the distance between two adjacent indentations was at least 10 µm. To assess the hardness, the load/displacement data collected after the first unloading were studied using the Oliver/Pharr method [Citation21].
Results
Microstructure characterisation
) shows an SEM micrograph and elemental analysis of the TiO2 layer. It is found that a compact TiO2 layer exists on the Ti substrate. The XRD patterns of Mg coating and Ti substrate are shown in ). Only the Mg peaks were visible in the Mg coating. According to PDF#35-0821, the (101) peak at 26.6° should be the strongest, while in this study the (002) peak at 40.4° became the strongest peak, and the (004) peak at 72.5° was also increased, implying that the coating may preferentially expand in the (00 l) direction.
The effect of ceramic layer on Mg coating
Biodegradation study
) represents the pH trend of the Mg coating on bare Ti, TiO2 and MAO treated Ti immersed in D-Hank’s solution for 21 days. The trend shows that on the first day, the pH of all coatings was almost 10.7. After day 1, the pH for all the samples was descending except for a platform between day3 and day9. Furthermore, the pH of Mg coating on pure Ti was still higher than ceramics treated samples up to day 9. After 9 days of immersion, the pH of Mg coating on pure Ti abruptly decreased and approached 7.5 on day 21, while the pH of ceramics treated and TiO2 samples are still higher than Mg coating on pure Ti substrate.
shows the electrochemical results of Mg coated on bare Ti, TiO2 and MAO treated Ti. The potentiodynamic polarisation curves in ) reveal that both Mg-coated on Ti with MAO and TiO2 acquired higher corrosion resistance as compared to Mg-coated pure Ti. The Tafel fitting was performed with the potentiodynamic polarisation curves, and the results are shown in [Citation22]. The corrosion rate of Mg coating on Ti with MAO ceramics and TiO2 layers are 3.721 mm/year and 4.106 mm/year, respectively. Mg coatings on MAO-treated Ti acquired the highest corrosion resistance, and Mg-coated bare Ti showed the highest degradation rate (4.634 mm/year). ) represents the Nyquist curve of the coatings. Usually, a larger diameter of the capacitive loop in Nyquist curves shows a higher impedance value. It was found that Mg coating on MAO treated Ti behaved better corrosion resistance relatively.
Figure 3. Potentiodynamic polarisation curve (a), Nyquist curve (b) of ceramics layered Mg coated Titanium (c) Equivalent circuits of Mg coating with and without treatment in D-Hank’s solution.
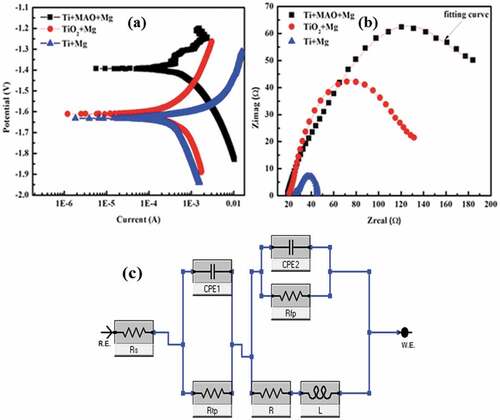
Table 1. The Tafel fitting results were based on potentiodynamic polarisation tested in D-Hank’s solution (Icorr represented the corrosion current and Ecorr represented the corrosion potential).
To further analyse the corrosion behaviour of Mg coatings, the circuit model in ) was applied to fit the EIS results. ZSimpWin software was used to fit the data. In this equivalent circuit, there are primarily two components. The solution resistance is denoted by Rs. Rtp and CPE1 are the first two parts. Rtp is the film resistance, which links to the coating’s protective effect. CPE1 stands for continuous constant phase element, which is used to characterise the film capacity. Rfp and CPE2 make up the second portion. CPE2 is the electric double-layer capacity between the coating matrix and D-Hank’s solution, and Rpf is the charge transfer resistance of the degrading process. The Rfp value of TiO2+ Mg (123 Ωcm−2) and Ti+MAO+Mg (119 Ωcm−2) is higher than that of Ti+Mg (108 Ωcm−2) coating according to the fitting results (). When the film resistance Rtp of the three coatings was compared, the film resistance of Pure Mg coating, MAO coating, and TiO2 treated Mg coating was found to be around 2200 cm−2, 2280 cm−2, and 2341 cm−2, respectively.
Table 2. Fitting results of EIS curves for Mg, MAO+Mg, and TiO2+ Mg coating immersed in D-Hank’s solution.
Wear property
showed the wear test results of Mg coating on bare Ti and Ti treated by TiO2 and MAO ceramics. It was found that, before the coatings were destroyed, the friction coefficients for Ti+Mg, TiO2+ Mg, and Ti+MAO+Mg coatings were 0.440, 0.329, and 0.370, respectively. showed their cross-section profile. For MAO and TiO2 treated Ti, the wear volume loss is less than samples without treatment. This indicated that both MAO and TiO2 treated samples have also better wear properties as compared to those without treatment. When the coatings were damaged, a considerable change in the friction coefficient was detected. The big shift change point can be used to estimate the sliding distance and damage regions before the coating was entirely damaged. The Mg coating on Ti substrate had the more destructive region as compared to those on MAO and TiO2 treated Ti substrate shown in .
The effect of heat treatment on Mg coating
Microstructural characterisation
Typical microstructures of the Mg coatings with different heat treatments are shown in . As we can see in ), the Mg coating (without treatment) has equiaxed grains structures with an average particles size of 4.6 µm. After heat treatment of the sample for 10 min, Mg particles tend to fuse. The particles grew up with the increased temperature, and the average particle size grew from 4.6 µm to 194 µm. As previously reported [Citation22,Citation23], the block-like particle is identified in three different orientation and size relationships with the three different temperatures of Mg coating. As the treatment temperature extends to 400 °C, the size of the particles slightly changed compared with 300 °C. For the untreated coating, there are many micro-holes in the coating, in which corrosion easily occurred. For the heat-treated samples, the micro-holes decreased and the particles grew together. Thus, grains did not disintegrate easily from the matrix as the immersion time increased.
Immersion test
The pH variation (short-term and long-term) of heat-treated and untreated Mg coated Ti immersed in D-Hank’s solution is shown in . It can be seen that heat treatment could improve the corrosion resistance of the coating and maintain the pH values lower than those of untreated samples. As the immersion time prolonged, the destruction of the coating on the 7th day occurred, as shown in . It can be seen that the heat-treated coatings at 400 °C and 300 °C coating are better than 200° C and untreated coatings. The coating was severely corroded in the untreated and low-temperature heated treated conditions because of the loose deposition, which could not prevent infiltration of the solution. The surfaces of samples were optically detected to investigate their degradation morphologies after the degradation products were removed. Without heat treatment, the Mg coating was nearly peeled off as shown in ). The integrity became better with the increasing temperature, due to the thick and dense coating.
Electrochemical polarisation
The heat treatment of Mg-coated samples was carried out at up to 400 °C for 10 min to alter their corrosion behaviour. The corrosion potential of heat-treated Mg-coated Ti (10 min up to 400 °C) shifted in a more negative direction as compared to untreated samples, as shown in ). The corrosion current density of samples before and after heat-treated was calculated by Tafel fitting from the potentiodynamic polarisation curves. shows that the corrosion current of untreated Mg coatings was higher than that of treated Mg coatings and that the corrosion current increased from 0.311 ± 0.201 to 0.521 ± 0.020 µA/cm2as the treatment temperature decreased. As a result, the degradation is increasing with decreasing temperature.
Figure 9. Potentiodynamic polarisation (a) and Impedance curves (b) of the coatings with and without heat treatment in D-Hank’s solution.
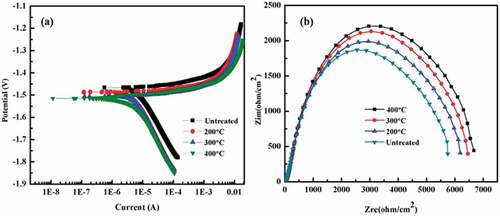
Table 3. Tafel fitting results based on potentiodynamic polarisation tested in D-Hank’s solution.
Electrochemical impedance spectroscopy
The corrosion behaviour of Mg coatings was further analysed by the EIS test. The EIS results are plotted in the Nyquist format, as shown in ). The heat-treated coating exhibited a higher corrosion resistance compared to untreated conditions, which is presented by the larger diameter of the semicircle on the Nyquist plot. As the heat treatment temperature increased, the diameter of the semicircle became larger. The EIS results are found consistent with the potentiodynamic polarisation.
shows the results of the EIS fitting results by the circuit model in . As the heat treatment temperature increased, the Rtp (Film resistance) of the coatings increased. Hence, heat treatment increase the quality of Mg coatings, and the Mg coating heat-treated at 400°C acquired the best corrosion resistance. Meanwhile, the Rfp (Charge transfer resistance) value of 400 °C coating is also higher than that of the other coatings. As a result, the degradation resistance of the coating after heat-treated is significantly higher than the untreated.
Table 4. Fitting results of Mg (treated) and Mg (untreated) coatings immersed in D-Hank’s solution.
Adhesion strength
Considering the adhesion strength is one of the most important factors for the coating performance. The coating with insufficient adhesive strength may delaminate from the substrate resulting in implant failure and medical consequences. The adhesion strength test was performed on Mg-coated samples before and after heat treatment. shows the adhesion strength for the Mg, coating samples before and after heat treatment at 200°C, 300°C, and 400°C After 10 minutes of heat treatment, the average adhesion strength of Mg coatings was 20 ± 2.11 MPa, 21 ± 2.11 MPa, and 23 ± 2.48 MPa, respectively.
Hardness and wear resistance
The hardness variation of the Mg coatings before and after heat-treated is shown in . The heat-treated coatings behaved an obvious age-hardening characteristic. As the temperature rose, the hardness of coatings was rapidly improved. Among all the coatings, the Mg coating heat-treated at 400°C acquired the highest hardness. The friction coefficient of Mg coatings was also detected before and after heat-treated at a different temperature, as shown in . It was found that the friction coefficient of Mg coatings decreased after heat-treated, which might have a close relationship with the increase of hardness of the treated Mg coatings. The decrease in friction coefficient and improvement in wear resistance for the treated samples may be due to an increase in hardness of the coated surface when compared to the untreated sample. As well known, both hardness and friction properties of the coating were determined by the quality of the coatings.
Discussions
Effect of ceramics layers on the Mg coating
The surface coating is one of the viable options for Ti implants to enhance their bioactivity. The purpose of ceramics treatment for Ti substrate was to reduce galvanic corrosion because of the ceramics insulator between Mg coating and Ti substrate.
Normally, faster degradation of Mg bulk means higher pH due to the release of more OH−. But in the case of coating, this situation is different. In the early stage of degradation, the quantity of Mg is abundant, so the Mg coating without ceramics insulator showed a higher pH value which means worse anticorrosion property whose behaviour was consistent with Mg bulk. However, in the final stage, as shown in ), the Mg coating without ceramics insulator was lower. The consumption of degradation resulted in severe magnesium deficiency, and insufficient OH− cannot raise pH anymore, and that just proved the faster degradation of Mg coating without ceramics insulator. This result was consistent with a previous report [Citation24]. An abrupt decrease in pH for all samples after 12 days confirmed the Mg coating’s peeling off as shown in . The possible reason was that Mg coated on ceramics treated Ti samples has the absence of galvanic corrosion between the coating and substrate, which decreased the degradation rate. The existence of ceramics and TiO2 played an important role to stabilise the coating and decrease the degradation process.
Usually, high-frequency capacitive loops, with larger diameters present high impedance value and better corrosion resistance [Citation25]. Therefore, Ceramics treated Ti and TiO2 exhibited better corrosion resistance in ). Similarly, from potentiodynamic polarisation ceramics treated Mg-coated Ti and TiO2 have a higher corrosion resistance as compared to Mg coated bare Ti in ).
For all kinds of coating having the same length, the weight volume loss was calculated according to Equationequation 1(1)
(1) . The weight volume loss for TiO2+ Mg, MAO+Mg, and Ti+Mg coating was 0.064 mm3, 0.0886 mm3, and 0.052 mm3, respectively. MAO coating has many micro-pores, which causes cracks when the force was applied for a longer period. However, it exhibited better wear properties as compared to pure Mg coating because of the highest thickness .
Effect of heat treatment on Mg coatings
Over fast degradation rate of Mg implant was still an urgent problem that needs to be solved for clinical application, especially for Mg coating who was lack of effective surface anti-corrosion method. Therefore, their anti-corrosion performance became vital.
The corrosion resistance of the coating increased as the treatment temperature was raised, owing to high adhesion and less crevice corrosion. Only a few dispersed particles were present in ), while the residual amount of coating increased as the treatment temperature increased as shown in ). Heat treatment can redistribute the coating particles and modify the microstructure. As a result, heat treatment was frequently utilised to change the microstructure and corrosion behaviour of coating materials [Citation26]. The shape, size, and distribution of coating particles, significantly influence the mechanical behaviour and corrosion properties of the coating [Citation27]. As shown in the shape and the distribution of the coating were significantly influenced by the heat treatment. The denser surface at higher temperature heat treatment presented higher hardness as shown in . The wear properties of the coating were normally related to the hardness. It was noticed from the results in , that the heat treatment of coating reduced the friction coefficient and larger wear rate.
The heat-treated samples showed a lower corrosion current density as compared to the samples without heat treatment as shown in . Different heat-treatment settings and deposition processes have also been shown to alter the bonding strength of coatings in previous research [Citation28]. The hardness was enhanced from 38 to 50 GPa after treatment at 400°C, a nearly 24% increase. The hardness was further increased by heat treatment to the highest possible level.
In the case of a stainless steel stylus sliding on a coating, the friction force was primarily due to the force required to distort the ploughed surface plastically. As a result, the treated sample’s friction coefficient was lower than that of the untreated sample . At the same time, ploughing and micro-cutting create less wear volume loss than the original sample under the lower load. Under the same load of 5 N, the treated sample exhibits fewer cracks than the original sample. The current findings clearly showed an increase in the coating’s friction and wear properties of the treated surface.
Conclusion
1) In this study, Mg was successfully coated on Ti with MAO ceramics layer and TiO2 treated samples. The ceramics layer, as well as TiO2, treated samples could slow down the degradation rate of Mg coating, and enhanced their wear properties. On the contrary, Pure Mg coating showed the fastest degradation rate due to the existence of galvanic corrosion between Mg coating and Ti substrate.
2) The heat treatment for Mg coatings on Ti alloy significantly improved their corrosion resistance; decrease the friction of coefficient, enhancing the wear properties of the Mg coating. As a result, the treated coating has a lot of potential in biomedical applications that demand greater adhesion, corrosion control, and wear resistance.
Acknowledgments
This work was financially supported by the National Key Research and Development Program of China (No. 2020YFC1107501), National Natural Science Foundation of China (No. 51971222), STS program (No.20201600200042) and DongGuan Innovative Research Team Program (No. 2020607234007).
Disclosure statement
No potential conflict of interest was reported by the author(s).
Additional information
Funding
References
- Liu X, Chu PK, Ding C. Surface modification of titanium, titanium alloys, and related materials for biomedical applications. Mater Sci Eng R. 2004;47(3):49–11.
- Drago C, Howell K. Concepts for designing and fabricating metal implant frameworks for hybrid implant prostheses. J Prosthodont. 2012;21(5):413–424.
- Praharaj R, Mishra S, Misra R, et al. Biocompatibility and adhesion response of magnesium-hydroxyapatite/strontium-titania (Mg-HAp/Sr-TiO2) bilayer coating on titanium. Mater Technol. 2022;37(4):230–239.
- Li XK, Gao P, Wan P, et al. Novel bio-functional magnesium coating on porous Ti6Al4V orthopaedic implants: in vitro and in vivo study. Sci Rep. 2017;7:154.
- Staiger MP, Pietak AM, Huadmai J, et al. Magnesium and its alloys as orthopedic biomaterials: a review. Biomaterials. 2006;27(9):1728–1734.
- Sun Y, Zhang B, Wang Y, et al. Preparation and characterization of a new biomedical Mg–Zn–Ca alloy. Mater Design. 2012;34:58–64.
- Witte F, Fischer J, Nellesen J, et al. In vitro and in vivo corrosion measurements of magnesium alloys. Biomaterials. 2006;27(7):1013–1018.
- Kraus T, Fischerauer SF, Hänzi AC, et al. Magnesium alloys for temporary implants in osteosynthesis: in vivo studies of their degradation and interaction with bone. Acta Biomater. 2012;8(3):1230–1238.
- Luan Y, Mao P, Tan L, et al. Optimising the mechanical properties and corrosion resistance of biodegradable Mg-2Zn-0.5 Nd alloy by solution treatment. Mater Technol. 2022;37(8):663–672.
- Chen J, Yang Y, Xu Y, et al. Effects of heat treatment on degradation, mechanical properties and cytocompatibility of Mg-1.5 Zn-0.5 Y-0.5 Zr alloy. Mater Technol. 2022;37(11):1825–1836.
- Gao M, Jia C, Ni D, et al. Influence of microstructure modification on corrosion resistance of friction stir processing biodegradable Mg-Zn-Nd alloy. Mater Technol. 2022;37(1):57–62.
- Shen Y, Chen J, Wang G, et al. Effects of ECAP extrusion on the mechanical and biodegradable properties of an extruded Mg-1.5 Zn-0.5 Y-0.5 Zr alloy. Mater Technol. 2022;37(2):135–142.
- Ni X, Zhao Q, Pan X, et al. Biocompatibility of a magnesium coating on a titanium surface and its effects on BMSCs. Mater Technol. 2022;37(14):3129–3139.
- Witte F. Reprint of: the history of biodegradable magnesium implants: a review. Acta Biomater. 2015;23:S28–S40.
- Wang J, Witte F, Xi T, et al. Recommendation for modifying current cytotoxicity testing standards for biodegradable magnesium-based materials. Acta Biomater. 2015;21:237–249.
- Gao P, Fan B, Yu X, et al. Biofunctional magnesium coated Ti6Al4V scaffold enhances osteogenesis and angiogenesis in vitro and in vivo for orthopedic application. Bioactive Mater. 2020;5(3):680–693.
- Ibrahim M, Yu X, Tan L, et al. Influence of strontium phosphate coating on the degradation of physical vapor deposition sprayed Mg coating on Ti6Al4V substrate to promote bone tissue healing. Front Mater. 2020. 10.3389/fmats.2020.583240
- Liu XW, Sun JK, Zhou FY, et al. Micro-alloying with Mn in Zn-Mg alloy for future biodegradable metals application (vol 94, pg 95, 2016). Mater Design. 2016;96:377.
- Zong Y, Yuan GY, Zhang XB, et al. Comparison of biodegradable behaviors of AZ31 and Mg-Nd-Zn-Zr alloys in Hank’s physiological solution. Mater Sci Eng B-Adv. 2012;177(5):395–401.
- Wang ZB, Tao NR, Li S, et al. Effect of surface nanocrystallization on friction and wear properties in low carbon steel. Mater Sci Eng A. 2003;352(1):144–149.
- Pharr G, Oliver W. Measurement of thin film mechanical properties using nanoindentation. Mrs Bull. 1992;17(7):28–33.
- Fu PH, Peng LM, Jiang HY, et al. Zr-containing precipitates in Mg-3wt% Nd-0.2 wt% Zn-0.4 wt% Zr alloy during solution treatment at 540° C, Materials science forum. Trans Tech Publ. 2007;2007:97–100.
- Ng K, Ngan A. Deformation of micron-sized aluminium bi-crystal pillars. Philosoph Magazine. 2009;89(33):3013–3026.
- Yu X, Ibrahim M, Lu S, et al. MgCu coating on Ti6Al4V alloy for orthopedic application. Mater Lett. 2018;233:35–38.
- Chen J, Lu S, Tan L, et al. Comparative study on effects of different coatings on biodegradable and wear properties of Mg-2Zn-1Gd-0.5Zr alloy. Surf Coat Technol. 2018;352:273–284.
- Li W, Wang X, Liu C, et al. Effect of heat treatment on the bio-corrosion properties and wear resistance of antibacterial Co-29Cr-6Mo-xCu alloys. J Mater Sci. 2019;30(10):112.
- Ram GJ, Esplin C, Stucker B. Microstructure and wear properties of LENS® deposited medical grade CoCrMo. J Mater Sci. 2008;19(5):2105–2111.
- Tsui Y, Doyle C, Clyne T. Plasma sprayed hydroxyapatite coatings on titanium substrates Part 1: mechanical properties and residual stress levels. Biomaterials. 1998;19(22):2015–2029.