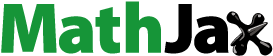
ABSTRACT
In this paper, molecular dynamics simulation method was used to establish the atomic model of high entropy alloy. The effect of strain rate on the microstructure evolution and dislocation motion of FeNiCoCrCu high entropy alloy was studied by applying tension and compression loads at different strain rates. The results show that the stress–strain curve of FeNiCoCrCu high entropy alloy presents three stages of elastic deformation, yield and plastic deformation under high strain rate. Under tensile load, Frank dislocation causes plastic deformation of the material, and the dislocation reaction between Shockley dislocation and Hirth dislocation generates Stair-rod dislocation. The mechanism of stress relaxation of materials under compression load is the formation of stacking faults. One of the mechanisms of strain hardening of materials is the formation of twins. In addition, stacking faults intersect with each other to produce dislocation reactions, which generate Stair-rod dislocations, maintaining the development of strain hardening effect.
Introduction
In recent years, the appearance of high entropy alloy provides a new way to break the restriction relationship between strength and toughness of metal materials [Citation1,Citation2]. The multi-principal element alloy design concept and high mixed entropy effect of high entropy alloy break through the traditional single principal element design concept of alloy [Citation3–5]. Researchers can meet different application needs by changing the element type, composition ratio, processing and heat treatment and other processes. High entropy alloys have attracted much attention in the industrial field due to their excellent mechanical properties [Citation6–8], such as high strength and toughness, which are different from traditional alloys [Citation9–11]. N. Gong et al. [Citation12] provide a glimpse of recent advances in Laser-cladding (LC) of high entropy alloys in terms of design fundamentals, metallurgical phase and microstructure, specific properties for advanced coating applications and the effect of ceramic particle reinforcement in LC deposition of high entropy alloy coatings. Gali et al. [Citation13] prepared CrMnFeCoNi and CrFeCoNi high entropy alloys and studied their deformation behaviour at −196 to 1000°C. It was found that both alloys exhibit strong temperature dependence and weak strain rate dependence. Senkov et al. [Citation14] studied a typical BCC WNbMoTa refractory high entropy alloy. From the quasi cleavage fracture of the surface cracking along almost parallel to the compression direction, it can be determined that the fracture occurs under tensile stress, and the brittle ductile transition temperature of the BCC refractory high entropy alloy is higher than room temperature. Wang et al. [Citation15] demonstrated through experiments that MoNbTi significantly deviates from the dislocation behaviour of traditional BCC, and the alloy exhibits good strength at both low and normal temperatures. Among them, FeCoCrCuNi high entropy alloy has been proved by experiments to have excellent mechanical properties [Citation16–18] and has potential and application value in industrial field.
The traditional mechanical properties of materials are usually obtained by measuring the macro-stress–strain relationship of samples with Hopkinson bars and light gas guns, and the fracture morphology is observed by scanning electron microscopy. However, the macro-phenomenon is the collective representation of the movement of micro-atoms. It is difficult to obtain the microstructure evolution mechanism of plastic deformation of FeCoCrCuNi high entropy alloy through macroscopic experimental method, which seriously restricts the design and application of high entropy alloy.
Molecular dynamics simulation can be used as an effective tool to make up for the lack of experiments because of its atomic tracking ability. Therefore, using molecular dynamics method to simulate the dynamic mechanical response process of materials can obtain the microscopic configuration and dislocation evolution law at atomic scale [Citation19,Citation20].
Unfortunately, up to now, there is little research on the micro-dynamic mechanical response of FeCoCrCuNi high entropy alloy. Most of the research focuses on the effects of preparation processes on material properties and macroscopic physical properties. In terms of the impact of preparation processes on material properties, Ding et al. [Citation21] prepared AlFeCoCrCuNi high entropy alloy by plasma arc method. The crystal structure, morphology and element distribution of the high entropy alloy were studied by scanning electron microscopy, transmission electron microscopy and inductively coupled atomic emission spectroscopy. Lin et al. [Citation22] studied the phase transformation process of FeCoCrNiCu0.5 high entropy alloy with as cast structure and heat treatment structure, analysed the relationship between the microstructure and hardness of the sample, observed the FCC peak from the X-ray diffraction of the as cast sample, and there were precipitates in the sample heated to 950ºC. Park et al. [Citation23] studied the recrystallization behaviour of cold rolled FeCoCrNiCu high entropy alloy and found that the microhardness decreased with the increase of recrystallization fraction. Based on the ultra-fine grain size and the two-phase structure in FeCoCrNiCu high entropy alloy, the reasons for the higher hardness were discussed. Tan et al. [Citation24] prepared CoCrFeNi high entropy alloy films by magnetron sputtering with simple splicing targets under different substrate bias voltages. The hardness, elastic modulus and creep properties of the films were measured by nanoindentation. In terms of macroscopic physical performance research, Li et al. [Citation25] studied the tensile yield strength and plasticity of FeCoCrCuNi high entropy alloy with different copper content and found that the addition of copper made the alloy change from a single BCC structure to FCC structure, which improved the tensile strength and plasticity of the alloy. Zhang et al. [Citation26] studied the micromechanical response of FeCoCrCuNi high entropy alloy using nanoindentation system and found that the yield strength of the high entropy alloy under uniaxial compression is related to size but is not too sensitive to typical nanostructures. By comparing the nanoindentation behaviour of nanotwin FeCoCrCuNi high entropy alloy and single crystal high entropy alloy, Tian et al. [Citation27] revealed the influence of twin boundary on the plastic deformation of high entropy alloy from the perspectives of defect structure, shear strain and surface morphology. Feng et al. [Citation28] prepared AlCoCrCuFeNix high entropy alloy coatings with different nickel content on 45 # steel surface by cold spray assisted induction remelting technology and obtained coating properties with different Ni content. Based on the existing research results, it can be found that the research on the microstructure evolution mechanism of dynamic mechanical properties of FeCoCrNiCu high entropy alloy under high strain rate tension and compression loading is still lacking.
In this paper, the atomic model of FeCoCrCuNi high entropy alloy under tension and compression was established by molecular dynamics simulation method. The evolution of atomic configuration and dislocation motion of materials under different loading strain rates was studied, and the micro-plastic deformation mechanism of FeCoCrCuNi high entropy materials under high strain was revealed innovatively. The research results provide a theoretical basis for the application of FeCoCrCuNi high entropy alloys in extreme environments.
Modelling
The dynamic tension and compression model of FeNiCoCrCu high entropy alloy is established, as shown in . Five kinds of atoms are randomly distributed on the lattice points of FCC structure in a proportion of 20%. The lattice constant of FeNiCoCrCu high entropy alloy is the maximum lattice constant of five single crystals: Fe, Ni, Co, Cr and Cu. The [100], [010] and [001] directions of the crystal are selected as the x, y and z directions of the model, respectively. The model size is 20a × 20a × 40a (a is the lattice constant), and it contains 6.4 × 104 atoms. Periodic boundary conditions are applied in all three directions of the model, which are consistent under NVT relaxation and tensile or compression loading. The simulation time step is 1 fs. EAM embedded atomic potential function [Citation29] is used to describe the interaction between FeNiCoCrCu. The form of embedded atomic potential function is as follows [Citation29]:
where U is the total potential energy of the system, F is the embedded energy function, and is the function of the atomic electron density, ρi is the sum of the electron cloud density generated at atom i by all atoms except atom i, Ф is the pair potential term, and rij is the distance between the atom i and the atom j.
High entropy alloys are not simply piled up by several elements, but undergo a strict preparation process. In order to restore the state of the high entropy alloy more truly, it is necessary to simulate the experimental preparation process of the model before loading. At present, the commonly used experimental preparation method of high entropy alloy is vacuum arc melting casting. The prepared materials are added into the electric arc furnace, then melted and cast into the high temperature mould, cooled and annealed, and finally cut into products. Therefore, in this paper, the conjugate gradient method is firstly used to minimize the energy and make the system reach the lowest potential energy. Then, the model is heated and melted, all atoms in the system are heated to 1500 K at the rate of 0.06 K/fs, and relaxation reaches equilibrium under the NVT ensemble. Then, the quenching process is simulated from 1500 K to 300 K at the rate of 0.024 K/fs, and the relaxation is carried out under the NVT ensemble. The molecular dynamics integral equation is solved by using the Verlet integral method.
The molecular dynamics software LAMMPS [Citation30] was used to simulate the above processes. The tensile and compressive loads with strain rate of 108 ~ 1011 s−1 were applied to the y direction of the atomic model, respectively, and the pressure in the other two directions was controlled to zero. The stress–strain change law of FeNiCoCrCu high entropy alloy was analysed. The visual analysis of atomic morphology used OVITO [Citation31] software to identify dislocation types and measure dislocation lengths.
Results and discussion
Dynamic tensile mechanical properties
The stress–strain curve of FeNiCoCrCu high entropy alloy under tensile loading at room temperature (300 K) at different strain rates is shown in . No plastic deformation occurs under low strain rate load. There are obviously three stages of elastic deformation, yield and plastic deformation when the strain rate reaches e11s−1. Before the strain reaches 0.2, the stress–strain relationship basically obeys Hooke’s law, and the stress changes linearly with the strain. By fitting the slope of the 0.1 ~ 0.2 strain segment in the stress–strain curve, it can be obtained that the Young’s modulus E in the tensile direction is 82.4 GPa, which is consistent with the range of 56.5 ~ 82.5 GPa [Citation26] obtained by other scholars in mechanical experiments. After the elastic stage, the stress–strain curve drops rapidly, and the material enters the yield stage. With the increase of the loading to 0.3 strain, the decreasing trend of the stress slows down significantly, and the material enters the stage of non-uniform plastic deformation. With the increase of strain rate, the elastic stages of FeNiCoCrCu high entropy alloy basically coincide. Young’s modulus remains unchanged; however, the yield strength increases gradually.
In order to explore the mechanism of the influence of tensile strain rate on the mechanical properties of FeNiCoCrCu high entropy alloy, the micro-configuration of atomic model and the evolution law of dislocation movement under different strain rates are analysed. shows the micro-configuration diagram of material fracture at different strain rates, shows the comparison of dislocation length at different strain rates, and shows the evolution diagram of dislocation structure at strain rates of 1011 s−1.
Figure 3. Micro-configuration of material fracture at different strain rates (FCC phase are coloured in green, HCP phase are coloured in red, BCC phase are coloured in blue, disordered atoms are coloured in white).
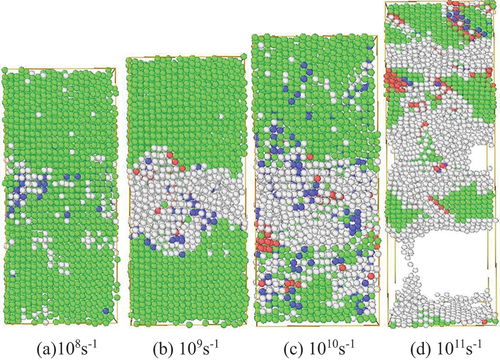
Figure 5. Dislocation structure evolution at strain rate of 1011 s−1 (The serial number in the figure is consistent with that in the Fig. 2. The 1/2 perfect dislocations are coloured in blue, the 1/6 Shockley partial dislocations are coloured in green, the 1/3 Hirth dislocations are coloured in yellow, the 1/6 Stair rod dislocations are coloured in purple, and the 1/3 Frank dislocations are coloured in cyan.).
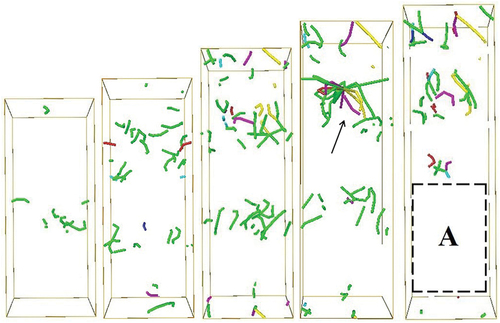
With the increase of strain rate, the atoms of amorphous phase and HCP phase gradually increase, as shown in , and the newly formed HCP phase atoms form stacking faults, which prevent the sliding and improve the strength of the material. The strain at fracture also increases with the increase of strain rate, which makes the plasticity increase gradually. The total dislocation length increases significantly with the increase of strain rate as shown in . When the strain rate is lower than 1010 s−1, the strain corresponding to the peak value of the total dislocation length is consistent with the yield point in the stress–strain curve in ; When the material reaches the yield point at strain rate of 1011 s−1, the dislocation length increases significantly, making the material enter the yield and plastic deformation stages. Therefore, the formation of dislocation has a decisive influence on the yield strength and plasticity of the material.
The dislocation structure of each strain node is extracted at a strain rate of 1011 s−1, as shown in . Only a small amount of Shockley partial dislocations are formed when the material reaches the yield point on 1 #. As the strain continues to increase, perfect dislocation slip needs to overcome the continuous energy barrier caused by high lattice friction. Slow moving slip bands of perfect dislocations will block partial dislocations, which require additional force to overcome the block. Therefore, when reaching the lower yield point of 2 #, the number of Shockley partial dislocations gradually increases as the strain increases, leading to slippage. A small number of Frank dislocations also occur at this time. Frank dislocations belong to immovable dislocations, which are fixed on the boundary line between the main slip surface and the conjugate slip surface, thus preventing the fracture of the region with the increase of strain, making the material enter the plastic deformation stage. When the original slip plane and the cross slip plane intersect at an obtuse angle, the leading part of the extended dislocation decomposes in the original slip plane, forming a small amount of Hirth disloc
ations. As the strain continues to increase, the cross-slip process continues and the number of Hirth dislocations increases. When two Shockley dislocations meet on the intersection line on the slip plane, dislocation reaction occurs to generate a Stair-rod dislocation, which prevents further slip of Shockley dislocations, so that the material does not fracture (as shown by the arrow in 4)). During the whole plastic deformation stage, the Shockley dislocation and the Hirth dislocation achieve a dynamic balance of decomposition and synthesis, which explains the phenomenon that the stress decreases slightly with the increase of strain at this stage. When the strain reaches a certain threshold, the dynamic equilibrium is broken, and the Shockley dislocation is no longer decomposed in some areas (area a in the dislocation diagram of 5 # fracture point).
Dynamic compression mechanical properties
The stress–strain curve of FeNiCoCrCu high entropy alloy under compression loading at room temperature (300 K) at different strain rates is shown in . In the elastic stage of the curve, the stress does not increase linearly strictly with the increase of strain but appears a wave trough of stress decline in the curve with strain of 0.22, and then increases. When the strain rate is 108, 109 s−1, there is only elastic deformation stage, and the fracture occurs near the strain of 0.3; when the strain rate is 1010 s−1, the stress–strain curve shows three stages: elastic deformation, yield and plastic deformation. After going through the yield stage, the material did not break, and the stress at point 7 # rebounded reversely, entering the plastic deformation stage.
In order to further explore the influence mechanism of compressive strain rate of 1010 s−1 on the dynamic mechanical properties of FeNiCoCrCu high entropy alloy, the micro-configuration of atomic model and dislocation movement evolution law under different strain rates are analysed. shows the length variation of different types of dislocations when the compression strain rate is 1010 s−1. shows the evolution of different strain microstructures. shows the evolution of dislocation structures under different strains.
Figure 7. The length change rule of different types of dislocations at the compression strain rate of 1010 s−1 (the number in the figure is consistent with the number of the characteristic points of the stress strain curve in Fig. 6).
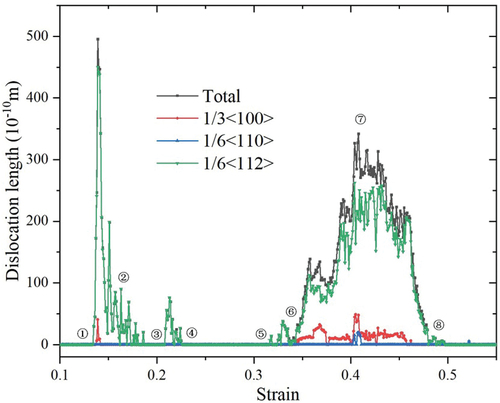
Figure 8. Evolution of micro-configurations under different strains (FCC phase are coloured in green, HCP phase are coloured in red, BCC phase are coloured in blue, disordered atoms are coloured in white).
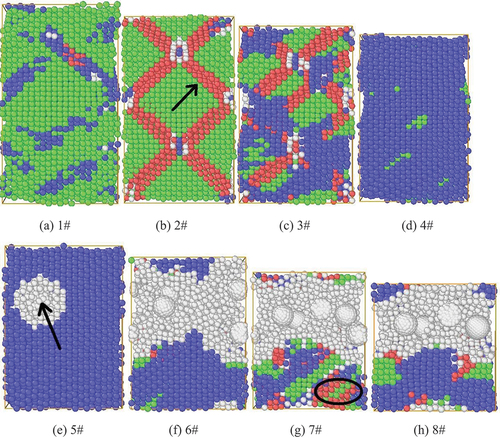
Figure 9. Structural evolution diagram of dislocation under different strains (the number in the figure is consistent with that in Fig. 6. The dislocation type is consistent with Fig. 5.).
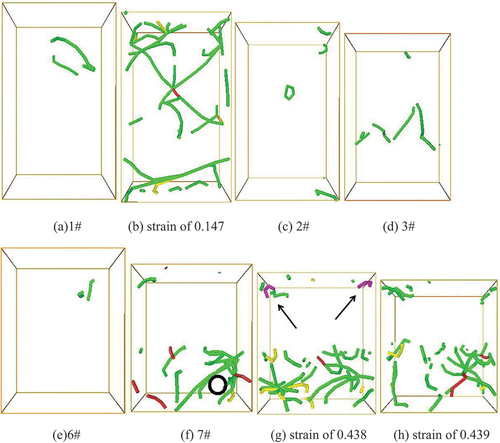
Most of the dislocations are 1/6 Shockley partial dislocations as shown in . At the elastic stage, 1/3 Hirth dislocations appear at the platform and after the yield point, and 1/6 Stair-rod dislocations appear at point 7#, indicating that the Stair-rod dislocations are one of the mechanisms of strain hardening effect.
Most atoms are FCC phase at the beginning of elastic phase by comparing . With the increase of strain, more FCC phases are transformed into BCC phase, becoming dislocation nucleation sources. At point 1 # of the stress–strain curve, layered BCC phase atoms begin to appear and are arranged in 45º and 135º directions. As the strain continues to increase, the nucleation dislocations slip and expand, generating a large number of Shockley partial dislocations. The BCC phase atoms gradually transform into more than three layered HCP phases, forming stacking faults, as indicated by the arrow in . The occurrence of stacking faults leads to stress relaxation, so the stress between point 1 # and point 2 # on the curve does not increase significantly. The stacking fault causes some dislocations to decompose in the original slip plane, forming a small amount of Hirth dislocations, which makes the Shockley partial dislocations continuously reduce. When the strain reaches 2 # point, the Shockley partial dislocations almost disappear. Similarly, there are a large number of HCP stacking faults between point 3 # and point 4 # on the curve, and local faults pass through the stacking fault interface without being blocked, resulting in stress relaxation. Therefore, the material is easy to deform, causing the stress to fall like a cliff. The stacking fault interface disappears with the increase of compression load, and a large number of FCC phase atoms are transformed into BCC.
When the HCP phase at point 4 # is completely transformed into BCC phase, the elastic deformation stage of the material resumes. When subjected to continuous strong compression, the atom is far away from the initial position. After the first spherical amorphous cluster appears in the BCC phase atom (as indicated by the arrow in ), the material reaches the yield strength at point 5 #. As the strain continues to increase, the disordered spherical amorphous clusters gradually increase, the material enters the yield stage, and the stress rapidly decreases with the increase of strain. When the strain reaches point 7 #, a twin structure of two layers of HCP phase atoms sandwiched with one layer of FCC phase atoms appears, as shown in the circles in (f). The local dislocations cannot pass through the twin interface, which blocks the slip of the dislocations and forms the strain hardening effect. Therefore, the stress–strain curve shows a significant upward trend from point 7 #. With the continuous increase of strain, the stacking faults at the upper part of the atomic model intersect with each other, and a dislocation reaction as shown in Formula (3) occurs, forming a Stair-rod dislocation, as indicated by the arrow in . The Stair-rod dislocations block the further movement of dislocations in the upper part of the model, so that the dislocations are confined outside the amorphous cluster, maintaining the development of strain hardening effect.
Compared with the micro-configuration diagram at the yield point and fracture point at the strain rates of 108 s−1 and 109 s−1 shown in , the common point is that there are stacking faults that significantly reduce the stress. The difference is that no twins are found at low strain rates, indicating that twins are an important mechanism for strain hardening after the yield point at high strain rates.
Conclusion
In this paper, the dynamic mechanical properties of FeNiCoCrCu high entropy alloy in tension and compression were studied by molecular dynamics simulation, and the mechanism of the influence of strain rate on the microstructure evolution and dislocation movement of FeNiCoCrCu high entropy alloy was obtained. The following specific conclusions can be drawn:
FeNiCoCrCu high entropy alloy has no plastic deformation under low strain rate loading. When the strain rate reaches e11s−1, it obviously presents three stages of elastic deformation, yield and plastic deformation. The yield strength increases with the increase of strain rate. In the stage of compression elasticity, the stress does not increase linearly with the increase of strain strictly.
Under high tensile strain rate, stacking faults are formed in the material, which prevent the sliding, thus improving the strength of the material. The formation of Frank dislocation makes the material enter the stage of plastic deformation. The dynamic equilibrium of Shockley dislocation and Hirth dislocation maintains the plastic deformation. The dislocation reaction between the Shockley dislocation and the Hirth dislocation generates the Stair rod dislocation, which prevents the further sliding of the Shockley dislocation and the fracture of the material.
The mechanism of stress relaxation of materials under high strain rate compression load is the formation of stacking faults. The mechanism of strain hardening is the formation of twins. In addition, stacking faults intersect with each other to produce dislocation reaction, which generates strut dislocations and maintains the development of strain hardening effect.
Acknowledgments
We acknowledge the guidance given by Key Laboratory of Science and Technology on Materials on dynamic deformation.
Disclosure statement
No potential conflict of interest was reported by the authors.
Data availability statement
The raw/processed data required to reproduce these findings cannot be shared at this time due to legal and ethical reasons.
Additional information
Funding
References
- Chen HH, Zhang XF, Liu C, et al. Research progress on impact deformation behavior of high-entropy alloys. Explosion and Shock Waves. 2021;41:30–10.
- George EP, Curtin WA, Tasan CC. High entropy alloys: a focused review of mechanical properties and deformation mechanisms. Acta Materialia. 2020;188:435–474.
- Li JG, Huang RR, Zhang Q, et al. Mechnical properties and behaviors of high entropy alloys. Chinese J Theor App Mech. 2020;52:333–359.
- Hui JL, Feng YC, Yang C, et al. Progress in theoretical modeling and simulation on strengthening and toughening of high-entropy alloys. Chinese J Solid Mech. 2020;41:93–108.
- Lu ZP, Lei ZF, Huang HL, et al., Deformation behavior and toughening of high-entropy alloys, Acta Metallurgica Sinica. 54(2018) 1553–1566.DOI:10.11900/0412.1961.2018.00372.
- Zhang ZR, Zhang H, Tang Y. Microstructure, mechanical properties and energetic characteristics of a novel high-entropy alloy HfZrTiTa0.53. Mater Des. 2017;133:435–443.
- Zhang ZR. Microstructure and mechanical properties of Hf Zr Ti tax high-entropy alloys energetic structural materials. Changsha, Hunan, P.R.China: National University of Defense Technology; 2017.
- Chen HH, Zhang XF, Xiong W, et al., Dynamic mechanical behavior and penetration performance of WFeNiMo high-entropy alloy, Chinese Journal of Theoretical and Applied Mechanics. 52(2020)1443–1453. DOI: 10.6052/0459-1879-20-166.
- Senkov ON, Wilks GB, Scott JM. Mechanical properties of Nb25Mo25Ta25W25 and V20Nb20Mo20Ta20W20 refractory high entropy alloys. Intermetallics. 2011;19:698–706.
- Chen H, Kauffmann A, Laube S. Contribution of lattice distortion to solid solution strengthening in a series of refractory high entropy alloys. Metall Mater Trans A. 2018;49:772–781.
- Liu ZQ, Qiao JW. Research progress of refractory high-entropy alloys. Mater China. 2019;38:767–774.
- Gong N, Meng TL, Cao J, et al. Laser-cladding of high entropy alloy coatings: an overview. Mater Technol. 2022;38. DOI:10.1080/10667857.2022.2151696.
- Gali A, George EP. Tensile properties of high-and medium-entropy alloys. Intermetallics. 2013;39:74–78.
- Senkov ON, Wilks GB, Miracle DB, et al. Refractory high-entropy alloys, Intermetallics. 18(2010)1758–1765. DOI: 10.1016/j.intermet.2010.05.014.
- Wang FL, Balbus GH, Xu SZ, et al. Multiplicity of dislocation pathways in a refractory multiprincipal element alloy. Science. 2020;370:95–101.
- Liu Y, Chen M, Li YX, et al. Microstructure and mechanical performance of AlxCoCrCuFeNi high-entropy alloys. Rare Metal MaterEng. 2009;38:1602.
- Li BY, Peng K, Hu AP. Structure and properties of FeCoNiCrCu0. 5Alx high- entropy alloy. Trans Nonferrous Met Soc China. 2013;23:735.
- Dong B, Wang XM, Zhu ZL. Study on the mechanical performance and microstructure of FeCoCrCuNi high-entropy alloy with crack and void by molecular dynamics simulations. J Atomic Mol Phys. 2020;37:591–595.
- Ruestes CJ, Alhafez IA, Urbassek HM, Atomistic studies of nanoindentation a review of recent advances, Crystals. 7(2017)293. DOI: 10.3390/cryst7100293.
- Iaa A, Cjr B, Embc D. Indentation and scratching of iron by a rotating tool – a molecular dynamics study. Comput Mater Sci. 194. DOI:10.1016/j.commatsci.2021.110445
- Ding BB. Preparation and properties research of Al-Co-Cr-Cu-Fe-Ni multiprincipal alloys powders, Anhui: Ma Anshan. Anhui, Ma Anshan: Anhui University of Technology; 2018.
- Lin CM, Tsai HL. Equi librium phase of high-entropy FeCoNiCrCu0.5 alloy at elevated temperature. J Alloys Compd. 2010;489:30–35.
- Park N, Watanabe I, Terada D, et al., Recrystallization behavior of CoCrCuFeNi high-entropy alloy, Metall Mat Trans A. 46(2015)1481–1487. DOI:10.1007/s11661-014-2594-5.
- Tan SY, Liu XD, Wang ZZ. Nanoindentation mechanical properties of CoCrFeNi high entropy alloy films. Mater Technol. 2022;37:1097–1108.
- Li JM. Study on the Al-Co-Cr-Fe-Ni-Cu of high entropy alloys. Guangxi Nanning: Guangxi University for Nationalities; 2018.
- Zhang H, Siu KW, Liao W, et al. In situ mechanical characterization of CoCrCuFeNi high-entropy alloy micro/nano-pillars for their size-dependent mechanical behavior. Mater Res Express. 2016;3:094002. DOI:10.1088/2053-1591/3/9/094002.
- Tian Y, Fang Q, Li J, Molecular dynamics simulations for nanoindentation response of nanotwinned FeNiCrCoCu high entropy alloy. Nanotechnology. 31(2020)465701. DOI:10.1088/1361-6528/ab.
- Feng L, Yang WJ, Li WS, Microstructure and properties of cold spraying AlCoCrCuFeNix HEA coatings synthesized by induction remelting, Materials technology. 37(2022)2567–2579. DOI10.1080/10667857.2022.2046929.
- Farkas D, Caro A, Model interatomic potentials and lattice strain in a high-entropy alloy, J. Mater Res. 33(2018)3218–3225. DOI:10.1557/jmr.2018.245.
- Plimpton S, Fast parallel algorithms for short-range molecular dynamics, J.Comput Phys. 117(1995)1–19. DOI:10.1006/jcph.1995.1039.
- Stukowski A, Visualization and analysis of atomistic simulation data with OVITO – the open visualization tool, Model Simul Mater Sci. Eng. 18(2010)15012. DOI:10.1088/0965-0393/18/1/015012.