ABSTRACT
Recently, the application of flexible sensors in mechanical equipment has attracted widespread attention. However, the design of vibration sensor materials and structures for complex mechanical environments still faces challenges. Hence, we proposed an annular structure CCTO/PDMS-based triboelectric nanogenerator (CP-TENG) as self-powered triboelectric automotive bolt tightness sensor. Due to the high dielectric properties of CCTO/PDMS film, the CP-TENG device can obtain high electrical output performance to achieve high sensitivity sensing. Through the annular structure design, CP-TENG devices can be integrated into bolt fittings with good structural compatibility. The output voltage and current of CP-TENG can monitor the different accelerations borne by the bolts from 9 to 60 m/s2. Moreover, by installing on the gasket, the CP-TENG device can also monitor bolt looseness to achieve early warning of the safety status of automotive components. This research can promote the development of self-powered sensor in the field of automotive bolt vibration monitoring.
Introduction
Recently, vehicle driving safety has become a research hotspot [Citation1,Citation2]. The main factor affecting vehicle driving safety comes from the looseness and detachment of components [Citation3]. Therefore, sensor systems for monitoring the looseness of automotive bolts are crucial. Conventional monitoring methods rely on manual detection of abnormal bolts in assembly, which is difficult and cumbersome, and has a high rate of misjudgement [Citation4,Citation5]. It is noteworthy that the rapid development of flexible electronic devices is gradually merging with the development of sensors [Citation6,Citation7], energy storage devices [Citation8,Citation9], and energy harvesters [Citation10,Citation11]. Sensor components based on flexible materials typically have good flexibility and tensile properties, and can be well adapted to complex environments [Citation12]. In particular, sensors used for vibration monitoring of mechanical equipment require materials with strong compatibility and structural design with high sensitivity sensing effects [Citation13–15]. Also, because long-term vibration of mechanical equipment can cause components to heat up, it is important to have sensors with good heat resistance. The most important point is that the structural design of the sensor device needs to be able to integrate with the monitored equipment without affecting the original mechanical equipment and avoiding additional negative interference. Generally, based on the signal amplitude, frequency, and signal shape characteristics of the vibration sensor, the vibration of the monitored equipment can be fed back to achieve fatigue monitoring of mechanical equipment, especially commonly used vehicles such as automobiles. In the past, vibration sensors were mainly based on the principle of piezoresistance [Citation16], capacitive effect [Citation17], and piezoelectric effect [Citation18], and triboelectric effect [Citation19]. It is worth noting that triboelectric electrical sensors are the best choice for vibration monitoring of mechanical equipment due to their high response rate and independence from external power sources.
Recently, triboelectric nanogenerators (TENGs) based on triboelectric effects have been extensively studied, and many self-powered vibration sensors have been developed based on TENG devices [Citation20–36]. Xiao et al. designed a self-powered vibration sensor based on a spring assisted structure [Citation37]. When the sensor device is subjected to mechanical impact, the slider located at the spring section will move, generating a voltage output signal to achieve structural health monitoring. However, due to the structural design of the sensor, the oscillator will produce resonance characteristics during use, which will affect the resolution of the sensor. Xiao et al. proposed a new vibration monitoring structure TENG based on plastic balls, which has good frequency self-adaptability [Citation38]. However, it is worth noting that contact and collision between rigid triboelectric materials can cause severe wear and noise. According to this, Cheng et al. used a soft sphere filled with liquid as a vibrator, but this soft sphere can cause complex deformation during the collision process, and the manufacturing cost is on the high side [Citation39]. In addition, liquid metal is also used to manufacture vibrators for frictional electrical sensors, which has good practical value. Zhang et al. proposed a triboelectric vibration sensor based on liquid metal, which can achieve acceleration sensing [Citation40]. However, this liquid metal vibration triboelectric electrical sensor is toxic, and this oscillating structure is difficult to match with automotive bolts. Improving the dielectric constant of triboelectric materials is an important way to improve the output performance of TENG devices. Although researchers have been striving to improve the dielectric constant of polymer dielectrics without losing their flexibility, processability, and other inherent properties, no significant results have been achieved. Significantly, the covalently bonded calcium copper titanate (CaCu3Ti4O12, CCTO) can enhanced dielectric constant (e) and low dielectric loss of polydimethylsiloxane (PDMS), which brings a new provides a new approach to improving the output performance of TENG devices based on PDMS. To achieve the goal of monitoring vibration of automotive bolts, efforts should be made to design flexible triboelectric materials and related matching structures.
In this work, we proposed an annular structure CCTO/PDMS-based triboelectric nanogenerator (CP-TENG) as self-powered triboelectric automotive bolt tightness sensor. The CCTO/PDMS film and copper was used as the triboelectric pairs. Due to the high dielectric properties of CCTO/PDMS film, the CP-TENG device can obtain high electrical output performance to achieve high sensitivity sensing. Through the annular structure design, CP-TENG devices can be integrated into bolt fittings with good structural compatibility. The output voltage and current of CP-TENG can monitor the different accelerations borne by the bolts from 9 to 60 m/s2. Moreover, by installing on the gasket, the CP-TENG device can also monitor bolt looseness to achieve early warning of the safety status of automotive components. In detail, when the vehicle bolts are tightened, the CP-TENG installed on the gasket will generate a periodically stable voltage signal. When a bolt is loosened, CP-TENG can produce a high impact pulse signal to achieve monitoring of loose bolts. CP-TENG can still maintain good reliability under nearly 10,000 working times. In addition, due to the excellent temperature stability of the CP-TENG electrical output, it is very suitable for monitoring complex mechanical vibration environments such as automobiles.
Experiments
The detailed preparation process of CCTO/PDMS film is shown in ). Firstly, add mineral oil and CCTO particles into PDMS mixture (10:1) for mechanical mixing, and control the mass ratio of CCTO to PDMS at 20%. Besides, silica gel and curing agent (10:1.2) are used to accelerate the curing and stability of PDMS. A ring structure Kapton film is used as the material substrate, as present in ). Then, paste copper foil on the surface of the annular structure Kapton film, as shown in . Apply the mixed colloid on the surface of copper foil to form CCTO/PDMS film, and then cure the sample at 100°C for 1 hour, as illustrated in . After complete curing, CCTO/PDMS composite film is obtained, and a triboelectric pair is formed with conductive copper foil, as shown in ). The the annular structure CP-TENG can be installed on the gasket. shows the picture of gasket with copper foil attached, and illustrates the picture of gasket with CCTO/PDMS film attached. Furthermore, shows the scanning electron microscope (SEM) image of CCTO/PDMS film surface. Besides, we provided the XRD patterns of CCTO, PDMS, and CCTO/PDMS, as illustrated in Figure S1. For CCTO/PDMS, the patterns are the same as that of CCTO, manifesting the intact crystal structure without being broken by the linkage with the combination with PDMS.
Figure 1. (a) Conceptual diagram of bolts in automobiles. (b1, b2) the schematic of inserting the TENG sensor into the loose bolt. (c1-c6) the fabrication process of CCTO/PDMS film and CP-TENG device. (d) the picture of gasket with copper foil attached. (e) the picture of gasket with CCTO/PDMS film attached. (f) the SEM image of CCTO/PDMS film surface.
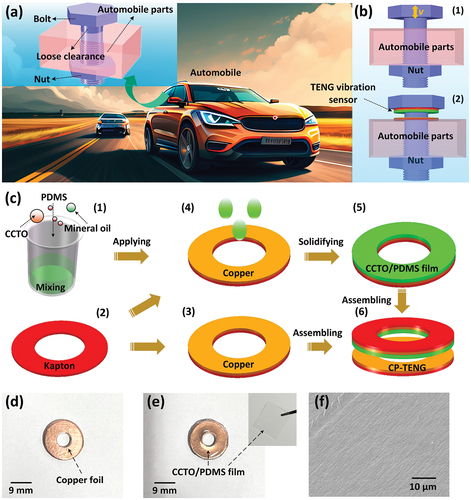
Results and discussion
To evaluate the sensing performance of CP-TENG device from a quantitative perspective, we use linear motors to provide mechanical excitation with different vibration frequencies, vibration amplitudes, and accelerations, thereby driving CP-TENG to generate electrical output signals. As shown in , fix the gasket attached to the CCTO/PDMS film on the moving end, and then fix the gasket attached to the copper foil on the fixed end. The electrometer 6514 was installed in the circuit to test for Voc and Isc of CP-TENG. Furthermore, depicts the detailed output signal waveform of Voc and Isc of CP-TENG device. The mechanical vibration state of CP-TENG can be fed back from the peak value and frequency of the output waveform. presents the CP-TENG working principle driven by external forces. During the collision between CCTO/PDMS film and copper, electrons migrate from the copper foil surface to the CCTO/PDMS film surface. When the two pads move with each other, driven by the potential difference between CCTO/PDMS film and copper foil, the driving electrons periodically flow between the two copper electrodes, generating an induced current. Due to the fact that mechanical equipment can generate heat between bolts and gaskets during vibration, it is crucial to study the effect of temperature on the output performance of CP-TENG. ) illustrates the Voc and Isc of CP-TENG under different temperature. It can be observed that the output performance of CP-TENG remains stable despite temperature changes. In addition, the thickness of CCTO/PDMS film is also a key factor affecting the output performance of CP-TENG. Therefore, we also investigated the output performance of CP-TENG with different thicknesses of CCTO/PDMS films under different accelerations, as shown in ). The CP-TENG device with thicker CCTO/PDMS film will produce high output performance, but the Voc of CP-TENG device tends to stabilize as the acceleration increases. Also, we measured the output voltage of CP-TENG (size: 2 cm × 2 cm), as shown in Figure S4. Furthermore, according to Ohm’s law, we calculated the output current and power of CP-TENG under different loads. From the results, when the resistance of the load increases, the output voltage increases and the output current decreases. Besides, when the resistance value of the external load is 20 MΩ, the output power of CP-TENG reaches its maximum value of 175 μW.
Figure 2. (a) Structural diagram of mechanical system for CP-TENG device. (b) the output signal waveform of Voc and Isc of CP-TENG device. (c1, c2) the working principle of CP-TENG device. The (d) Voc and (e) Isc of CP-TENG under different temperature. (f, g) the influence of CCTO/PDMS film thickness on CP-TENG output performance under different acceleration conditions.
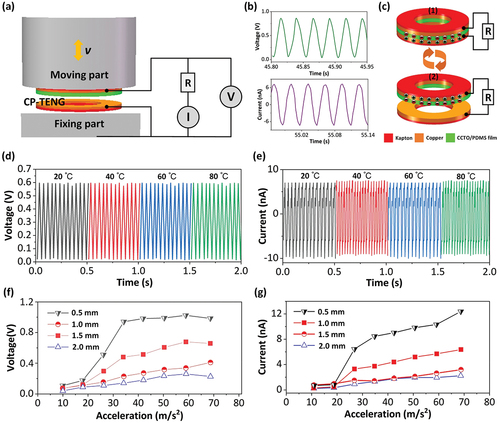
Considering the influence of the thickness of CCTO/PDMS film on the CP-TENG sensing performance, we chose CCTO/PDMS film with a thickness of 1.5 mm as the experimental object. ) shows the output signal waveform of the Voc and Isc of CP-TENG device. It can be observed that as the acceleration increases, the output performance of CP-TENG gradually increases, and its output performance signal can be used as a sensor signal to monitor the acceleration received by the device. During the driving process of a vehicle, the fastening of bolts is very important, which will directly affect the safety factor of the vehicle. The monitoring of bolt tightness and impact force by CP-TENG can effectively prevent the failure of important components. Furthermore, considering the long-term reliability of CP-TENG, we have tested its output performance stability of CP-TENG under continuous operation. ) illustrates the Voc and Isc of CP-TENG under continuous working conditions of nearly 10,000 times. It can be observed that the output performance of CP-TENG is very stable under multiple consecutive operating conditions. Moreover, we developed the output performance of CP-TENG under various humidity (from 30% to 50%), as shown in Figure S2. From the results, the changing humidity did not have a significant impact on the output performance of CP-TENG. Furthermore, we also measured the electrical output of CP-TENG under long-term continuous working conditions (frequency: 10 Hz, time: 6000 s), as illustrated in Figure S3.
Figure 3. (a) the Voc of CP-TENG under different acceleration. (b) the Isc of CP-TENG under different acceleration. (c, d) the reliability testing of CP-TENG device.
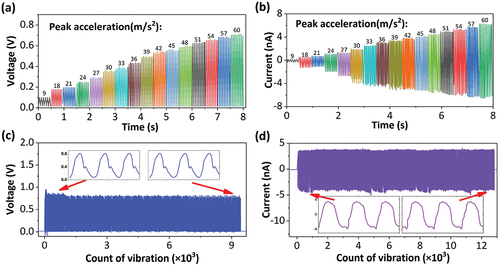
To simulate the bolt vibration monitoring scenario, we fixed the bolts on the prefabricated components, and arranged the gaskets with CP-TENG devices between the bolts and the components to maintain a certain gap, as shown in . illustrates that after the vibration system is started, the vibration amplitude of the CP-TENG device gradually increases, and its voltage signal also increases, reflecting the loosening information of the bolt. Furthermore, presents a bolt vibration scenario, where it can be observed that two CP-TENG mounted gaskets are arranged between the nut and the component. To visually evaluate the rapid response of CP-TENG to acceleration, we use a linear motor to provide shock vibration, and feedback the vibration effect through the output signal of CP-TENG. The fast Fourier transform (FFT) spectrum of the output voltage signal of the CP-TENG device clearly shows that the natural frequency varies from 23 Hz to 35 Hz, as present in .
Figure 4. (a) System overview diagram of CP-TENG device for vibration monitoring. (b) the output voltage signal of CP-TENG device during vibration process. (c) the picture of bolt vibration test scenario. (d) the time domain signal and FFT spectrum of the CP-TENG device.
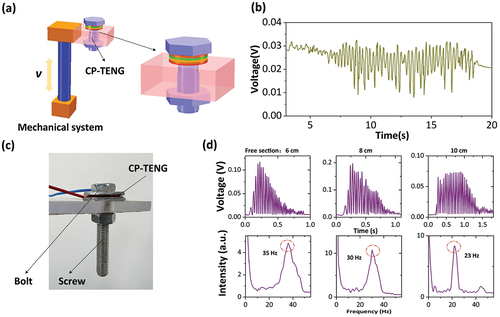
In addition to monitoring different accelerations, CP-TENG can also monitor sudden loosening of bolts and evaluate equipment safety. As shown in , when the vibration system is started, CP-TENG will generate a small stable voltage signal due to the existence of small gaps between the shims. When the bolt loosens significantly, the output voltage of CP-TENG will produce abrupt spikes, as shown in . When the vehicle is running, the overall vibration can be very large, leading to damage and detachment of components. Real-time monitoring of bolt vibration information will help to solve automotive safety issues. shows the output voltage signal of the PC-TENG device under the normal vibration state of the bolt, and a stable periodic waveform can be observed. When the bolts become loose, there will be a gap between the shims, as shown in . Under the action of component vibration, CP-TENG generates a relatively high output voltage, which can be used to evaluate the pre-tightening effect of bolts. shows the output signals of PC-TENG subjected to low-frequency shock vibration under different bolt loosening states.
Figure 5. (a) the output voltage signal of CP-TENG under normal operation. (b) the output voltage signal of CP-TENG under breakdown state. The output voltage signal of CP-TENG under (c) compression state and (d) loose state. (e) the output voltage signal of CP-TENG under low-frequency impact conditions.
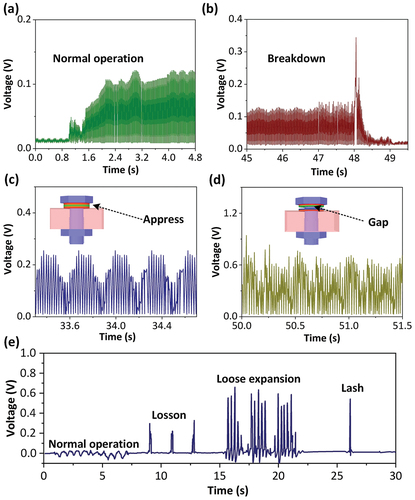
Conclusion
In summary, we designed an annular structure CP-TENG as self-powered triboelectric automotive bolt tightness sensor. The CCTO/PDMS film and copper was used as the triboelectric pairs. Through the annular structure design, CP-TENG devices can be integrated into bolt fittings with good structural compatibility. The output voltage and current of CP-TENG can monitor the different accelerations borne by the bolts from 9 to 60 m/s2. Moreover, by installing on the gasket, the CP-TENG device can also monitor bolt looseness to achieve early warning of the safety status of automotive components. CP-TENG can still maintain good reliability under nearly 10,000 working times. In addition, due to the excellent temperature stability of the CP-TENG electrical output, it is very suitable for monitoring complex mechanical vibration environments such as automobiles.
Supplemental Material
Download MS Word (3.1 MB)Disclosure statement
No potential conflict of interest was reported by the authors.
Supplementary Material
Supplemental data for this article can be accessed online at https://doi.org/10.1080/10667857.2023.2214775
References
- Jia Y, Wang S, Peng J, et al. Evaluation of pavement rutting based on driving safety of vehicles. Int J Pavement Res Technol. 2022;15(2):457–7. DOI:10.1007/s42947-021-00032-2
- Zhou X, Sun F, Zhang C, et al. Stochastically predictive co-optimization of the speed planning and powertrain controls for electric vehicles driving in random traffic environment safely and efficiently. J Power Sources. 2022;528:231200.
- Ahmed MM, Khan MN, Das A, et al. Global lessons learned from naturalistic driving studies to advance traffic safety and operation research: a systematic review. Accid Anal Prev. 2022;167:106568.
- Parekh D, Poddar N, Rajpurkar A, et al. A review on autonomous vehicles: progress, methods and challenges. Electronics. 2022;11(14):2162. DOI:10.3390/electronics11142162
- Hang P, Huang C, Hu Z, et al. Driving conflict resolution of autonomous vehicles at unsignalized intersections: a differential game approach. IEEE ASME Trans Mechatron. 2022;27(6):5136–5146. DOI:10.1109/TMECH.2022.3174273
- Li WD, Ke K, Jia J, et al. Recent advances in multiresponsive flexible sensors towards E‐skin: a delicate design for versatile sensing. Small. 2022;18(7):2103734. DOI:10.1002/smll.202103734
- Zhao C, Wang Y, Tang G, et al. Ionic flexible sensors: mechanisms, materials, structures, and applications. Adv Funct Mater. 2022;32(17):2110417. DOI:10.1002/adfm.202110417
- Zhao S, Ran W, Lou Z, et al. Neuromorphic-computing-based adaptive learning using ion dynamics in flexible energy storage devices. Natl Sci Rev. 2022;9(11):nwac158. DOI:10.1093/nsr/nwac158
- Liu M, Li X, Shao C, et al. Synchronous-ultrahigh conductive-reactive N-atoms doping strategy of carbon nanofibers networks for high‐performance flexible energy storage. Energy Storage Mater. 2022;44:250–262.
- Ansari MA, Somdee P. piezoelectric polymeric foams as flexible energy harvesters: a review. Adv Energy Sustain Res. 2022;3(9):2200063.
- Venkatesan M, Chen WC, Cho CJ, et al. Enhanced piezoelectric and photocatalytic performance of flexible energy harvester based on CsZn0. 75Pb0. 25I3/CNC–PVDF composite nanofibers. Chem Eng J. 2022;433:133620.
- Pavel IA, Lakard S, Lakard B. Flexible sensors based on conductive polymers. Chemosensors. 2022;10(3):97.
- Peng S, Guo Q, Thirunavukkarasu N, et al. Tailoring of photocurable ionogel toward high resilience and low hysteresis 3D printed versatile porous flexible sensor. Chem Eng J. 2022;439:135593.
- Nie Y, Yue D, Xiao W, et al. Anti-freezing and self-healing nanocomposite hydrogels based on poly (vinyl alcohol) for highly sensitive and durable flexible sensors. Chem Eng J. 2022;436:135243.
- Qin T, Liao W, Yu L, et al. Recent progress in conductive self‐healing hydrogels for flexible sensors. J Polym Sci. 2022;60(18):2607–2634. DOI:10.1002/pol.20210899
- Shen Z, Liu F, Huang S, et al. Progress of flexible strain sensors for physiological signal monitoring. Biosens Bioelectron. 2022;114298.
- Ma Z, Zhang Y, Zhang K, et al. Recent progress in flexible capacitive sensors: structures and properties. Nano Mater Sci. 2022. DOI:10.1016/j.nanoms.2021.11.002
- Mirjalali S, Mahdavi Varposhti A, Abrishami S, et al. A review on wearable electrospun polymeric piezoelectric sensors and energy harvesters. Macromol Mater Eng. 2023;308(1):2200442. DOI:10.1002/mame.202200442
- Qu X, Liu Z, Tan P, et al. Artificial tactile perception smart finger for material identification based on triboelectric sensing. Sci Adv. 2022;8(31):eabq2521. DOI:10.1126/sciadv.abq2521
- Pu X, An S, Tang Q, et al. Wearable triboelectric sensors for biomedical monitoring and human-machine interface. iScience. 2021;24(1):102027. Iscience.
- Xiang H, Zeng Y, Huang X, et al. From triboelectric nanogenerator to multifunctional triboelectric sensors: a chemical perspective toward the interface optimization and device integration. Small. 2022;18(43):2107222. DOI:10.1002/smll.202107222
- Kim DW, Lee JH, Kim JK, et al. Material aspects of triboelectric energy generation and sensors. Npg Asia Mater. 2020;12(1):6. DOI:10.1038/s41427-019-0176-0
- Fang Y, Zou Y, Xu J, et al. Ambulatory cardiovascular monitoring via a machine‐learning‐assisted textile triboelectric sensor. Adv Mater. 2021;33(41):2104178. DOI:10.1002/adma.202104178
- Yao X. A flexible triboelectric nanogenerator based on soft foam for rehabilitation monitor after foot surgery. Mater Technol. 2022;37(10):1516–1522.
- Wang S, Zhang Y. A functional triboelectric nanogenerator based on the LiCl/PVA hydrogel for cheerleading training. Mater Technol. 2022;37(13):2752–2757.
- Lu Y, Tian H, Cheng J, et al. Decoding lip language using triboelectric sensors with deep learning. Nat Commun. 2022;13(1):1401. DOI:10.1038/s41467-022-29083-0
- Zhu M, Sun Z, Chen T, et al. Low cost exoskeleton manipulator using bidirectional triboelectric sensors enhanced multiple degree of freedom sensory system. Nat Commun. 2021;12(1):2692. DOI:10.1038/s41467-021-23020-3
- Han G, Wu B, Pu Y. High output triboelectric nanogenerator based on scotch tape for self-powered flexible electrics. Mater Technol. 2022;37(4):224–229.
- Yan Z, Wang L, Xia Y, et al. Flexible high-resolution triboelectric sensor array based on patterned laser‐induced graphene for self-powered real-time tactile sensing. Adv Funct Mater. 2021;31(23):2100709. DOI:10.1002/adfm.202100709
- Gao Q, Cheng T, Wang ZL. Triboelectric mechanical sensors—Progress and prospects. Extreme Mech Lett. 2021;42:101100.
- Ren L. A triboelectric nanogenerator based on foam for human motion posture monitoring. Mater Technol. 2022;37(9):1140–1145.
- Liu R, Li M. A textile-based triboelectric nanogenerator for long jump monitoring. Mater Technol. 2022;37(12):2360–2367.
- Wang Z, Gao W. A wave structure triboelectric nanogenerator for race walking motion sensing. Mater Technol. 2022;37(13):2637–2643.
- Kojčinović J, Sahu M, Hajra S, et al. Nanocrystalline triple perovskite compounds A3Fe2BO9 (A= Sr, Ba;B= W, Te) with ferromagnetic and dielectric properties for triboelectric energy harvesting. Mater Chem Front. 2022;6(9):1116–1128. DOI:10.1039/D1QM01565F
- Sahu M, Hajra S, Panda S, et al. Waste textiles as the versatile triboelectric energy-harvesting platform for self-powered applications in sports and athletics. Nano Energy. 2022;97:107208.
- Hajra S, Panda J, Swain J, et al. Triazine skeletal covalent organic frameworks: a versatile highly positive surface potential triboelectric layer for energy harvesting and self-powered applications. Nano Energy. 2022;101:107620.
- Xiao X, Zhang X, Wang S, et al. Honeycomb structure inspired triboelectric nanogenerator for highly effective vibration energy harvesting and self‐powered engine condition monitoring. Adv Energy Mater. 2019;9(40):1902460. DOI:10.1002/aenm.201902460
- Cheng P, Guo H, Wen Z, et al. Largely enhanced triboelectric nanogenerator for efficient harvesting of water wave energy by soft contacted structure. Nano Energy. 2019;57:432–439.
- Zou H, Zhang Y, Guo L, et al. Quantifying the triboelectric series. Nat Commun. 2019;10(1):1427. DOI:10.1038/s41467-019-09461-x
- Zhang B, Wu Z, Lin Z, et al. All-in-one 3D acceleration sensor based on coded liquid–metal triboelectric nanogenerator for vehicle restraint system. Mater Today. 2021;43:37–44.