ABSTRACT
The pursuit of low-cost superalloys with excellent creep property is of great importance for practical engineering application. In this study, the creep performance, microstructure evolution and deformation mechanism of a low-cost Fe-Ni-based superalloy under the condition of 750°C/130 MPa and 700°C/200 MPa were investigated. The creep rupture life reached 14,715 h and 12,716 h, respectively, under the aforementioned conditions. After long-term creep, carbides and γ′ particles (Ni3(Al,Ti)) with spherical shape grew gradually due to the Ostwald ripening. Abnormal coarse needle-like γ′ phase presented at grain boundaries and grew along preferred orientation under the synergy effect of grain boundary migration, stress, and diffusion. Influence of precipitate-free zones, carbides, and coincidence site lattice (CSL) boundary on the creep properties were discussed. The creep deformation mechanism of the Fe-Ni-based superalloy were dominated by dislocations slip. Dislocations moved via by-passing the γ′ phase and formed dislocation bows around the precipitates.
Introduction
In order to reduce greenhouse gas emission and improve the thermal efficiency of power plants, the ultra-supercritical (USC) power generation technology is developing towards higher steam temperatures (~700°C) and pressures (35 MPa) [Citation1]. This requires materials can withstand the harsh working environment and provide long-term reliability. However, widely used heat-resistant austenitic stainless steel, e.g. Super304H, TP310, cannot meet the requirements about creep and corrosion properties at higher temperatures. Apart from creep fracture failure, breakaway oxidation also may occur for chromia forming alloys after long time expose to water vapour containing environment [Citation2,Citation3]. Therefore, there is an urgent need to develop high-performance superalloys. Ni-based superalloys with excellent high-temperature performance but costly, which limited their large-scale use. Considering the cost, performance, and service life, Fe-Ni-based superalloys are promising materials for the next-generation USC thermal power plants.
The mechanical properties of metals are generally influenced by composition, grain size and precipitates [Citation4–9]. Alloying elements, such as Ti, Al, W, are widely used to improve the strength of alloys through solid solution and/or precipitation strengthening effect [Citation10–13]. Alloying elements segregate in the vicinity of grain boundaries or exist in the form of precipitates at grain boundaries all can hinder the migration of grain boundary, therefore, maintaining the stability of microstructure [Citation14,Citation15]. Various superalloys are designed based on this concept to obtain excellent high-temperature strength and creep property. For Fe-Ni-based superalloys, γ′ phase and carbides are usually introduced as strengthening phases [Citation1,Citation16]. γ′ phase has ordered face centred cubic crystal structure and often with the chemical formula Ni3Al and Ni3(Al,Ti,Nb). It can impede the motion of dislocations, thereby increasing the resistance to deformation of superalloys and improving high-temperature strength. The crystal structure of carbides same to γ′ phase and usually present in the form of (Nb,Ti)C or Cr23C6. Carbides in Fe-Ni-based superalloys can interact with other phases, such as γ matrix and γ′ precipitates. These interactions can influence the strength, ductility, and creep resistance. Moreover, the shape, size, and stability of precipitates in superalloys also have a significant influence on their performance. In general, precipitates with spherical shape and smaller size are beneficial to improve the mechanical properties of superalloys. However, the morphology of precipitates in superalloys usually varies with the extension of service time, which in turn change their performance at elevated temperatures [Citation1,Citation17,Citation18]. The reduction of the γ/γ′ interface area, lattice mismatch strain of the γ/γ′ interface and modulus misfit all can provide driving force for the γ′ phase coarsening [Citation19]. Moreover, precipitate-free zone (PFZ) may present in the proximity of grain boundaries and lead to the creep damage after long time service under stress and elevated temperature [Citation20]. Controlling PFZ in the vicinity of grain boundaries is vital to obtain a superior balance between creep strength and ductility and improve creep properties.
The creep life of superalloys is sensitive to the temperature and stress exerted on them, which dominate different creep mechanism [Citation21]. Dislocations cannot be activated easily at low temperatures and the generation and propagation of dislocations in the matrix are suppressed [Citation22]. When the applied stress exceeds the threshold stress for creep, dislocations sweep across the γ/γ′ microstructure with forming the anti-phase boundaries (APBs) and eventually shear the γ′ precipitates [Citation23,Citation24]. However, the creep behaviour and dislocations movement mechanism at high temperatures are striking different from that at low temperature. Dislocations are easily emitted and propagate in matrix under low external stress. The pronounced dislocations present at γ/γ′ interface form interfacial dislocation networks, which can hinder subsequent dislocations motion and promote dislocation climbing [Citation25]. High-density dislocations also occur annihilation phenomenon simultaneously, which causes the softening of matrix. As a result, the strain hardening and recovery softening caused by dislocation blockage coordinate with each other, which is helpful to creep property [Citation26]. Moreover, precipitates size also play a significant role on the movement of dislocations. The deformation may change from stacking fault shearing to Orowan bypassing with the increase in precipitate size [Citation27]. Therefore, the evolution of γ′ phase and its interaction with dislocations under different creep conditions deserve further investigation.
In this study, the creep property of the Fe-Ni-based superalloy at 700°C/200 MPa and 750°C/130 MPa is tested. Moreover, the evolution of γ′ phase in grains and grain boundary carbides are investigated in detail. The formation mechanism of precipitate-free zone (PFZ) and its influence on creep property is discussed. Finally, the interaction between precipitates and dislocations related creep mechanism are analysed.
Experimental methods
The chemical composition of the studied Fe-Ni-based superalloy is shown in . Before creep experiments, the received superalloy plates experienced four-step heat treatment. The heat treatment process is depicted in . Plates were solution treated at high temperatures to minimise the compositional heterogeneity. Subsequently, these plates were fast cooled to room temperature by water to avoid harmful precipitates formation. After ageing treatment at 650°C and 800°C, pronounced γ′ precipitates are expected to form in the matrix. Considering the practical service environment of the Fe-Ni-based superalloy, creep experiments were conducted under the conditions of 750°C/130 MPa and 700°C/200 MPa, which were named as T1 and T2, respectively. Creep specimens were machined to gauge length of 100 mm and diameter of 10 mm. Standard creep tests were conducted under aforementioned conditions using computerized creep testing machine.
Table 1. The chemical composition of the fe-ni-based superalloy (wt.%).
After creep experiments, specimens with size of 6 mm × 8 mm × 3 mm were cut from the uniform deformation region of the creep samples, which perpendicular to the tensile axis. All specimens were metallographically polished using standard metallographic procedure and ultrasonically cleaned by ethanol. Then, these specimens were etched using etching reagent (4 g CuSO4 +20 ml HCl +20 ml H2O) before microstructure observation. Microstructure and fracture morphology characterisation were carried out using scanning electron microscope (SEM, ZEISS ULTRA 55) in conjunction with electron back scatter diffraction (EBSD) operated at voltage of 15 kV. Samples were vibration polished and the step size of 10 μm was chosen for EBSD analysis. Precipitates and dislocations analysis were performed using transmission electron microscopy (TEM, FEI Tecnai G2 F20) equipped with an energy dispersive X-ray analysis system (EDS). Thin foils of 3 mm diameter for TEM studies were mechanical polished to ~50 µm thickness, then twin-jet polished in an electrolyte of 8% perchloric acid and 92% alcohol in volume at a potential of 28 V and −30°C. TEM was operated at an accelerating voltage of 200 kV.
Results and discussion
Microstructure of the heat-treated alloy
shows the morphology of carbides and γ′ precipitates in the matrix of the heat-treated Fe-Ni-based superalloy. Carbides that existed in Fe-Ni-based superalloys usually with MC or M23C6 type carbides. MC carbides with large size generally distributed in grain interior or in the vicinity of grain boundaries. Small size M23C6 carbides preferred to precipitate at grain boundaries in a chain structure [Citation28]. shows carbides precipitated at grain boundaries with near spherical shape. The large size carbide reached ~7 μm in diameter existed at grain boundaries. Some small carbides sparsely distributed in the grain interior. High-density fine spherical γ′ particles were observed at high magnification. γ′ particles in the present alloy were uniform with size of ~26 nm. EDS mapping results indicate the large size carbides and γ′ particles should be TiC and Ni3(Al, Ti), respectively.
Creep properties
shows the strain-creep time and strain rate-creep time curves of the Fe-Ni-based superalloy under the test conditions of 750°C/130 MPa, and 700°C/200 MPa. The creep life of the samples under these conditions reached 14,715 h and 12,716 h, respectively. The creep curves of the experimental alloy can be divided into three stages: slow accelerating stage, steady-state stage, and rapid accelerating stage. For sample crept at 750°C/130 MPa, the proportion of every stage were about 29%, 28%, and 43%, respectively. Similarly, the proportion of every stage accounted for 28%, 25%, and 47%, respectively, when crept at 700°C/200 MPa. The sample displayed slightly longer creep rupture life also exhibited greater elongation after fracture. Although the creep life discrepancy between the two samples was about 15%, the overall creep behaviour of these two samples was similar under the given creep conditions. Moreover, the creep strain rate of the sample before rupture was less than 2 × 10−3s−1 under the condition of 750°C/130 MPa, which was also less than that under 700°C/200 MPa. On balance, the new developed low-cost exhibited good creep property under these conditions.
Microstructure of carbides after creep fracture
The morphology of carbides after creep test under various conditions is portrayed in . show carbides with large size mainly distributed along grain boundaries. These large size carbides were identified as TiC carbides by EDS mapping (), which unevenly precipitated along grain boundaries. For the sample crept at 750°C/130 MPa, large size MC carbides tended to agglomerate together (, indicated by red rectangle). In contrast, carbides more likely to exist in the form of carbide bands (, indicated by blue rectangle) and the length of carbide bands even exceeded 500 μm. After long-term creep, most carbides with rod shape (). The large one can reach ~5 μm in width and ~25 μm in length. The EDS mapping results in confirmed small Cr-rich carbides presented in the vicinity of large size TiC carbides. These small size carbides were identified as Cr23C6 carbides, which mainly discontinuously precipitated along grain boundaries.
Figure 4. Morphology of the carbides after creep test under the conditions of (a–c) 750°C/130 MPa and (d-f) 700°C/200 MPa.
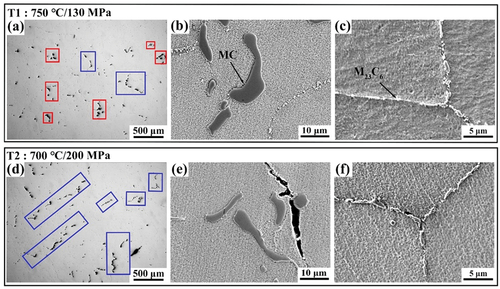
Figure 5. The elemental mapping images of TiC and Cr23C6 carbides in the experimental alloy under the creep condition of 700°C/200 MPa.
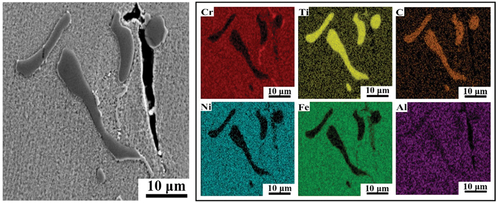
Carbides as one of the main strengthening phases in superalloys, which randomly distribute in the matrix or discontinuously precipitate at GBs all can improve the strength of superalloy. However, carbides experience dissolution, re-precipitation and coarsening during the creep process. Large size MC carbides presented in grain interior or at grain boundary may lead to stress concentration at the carbides/matrix interface, which increased the risk of crack nucleation. Carbide is a kind of embrittlement phase, which continuously precipitates at grain boundaries may cause intergranular embrittlement [Citation29]. In the present study, Cr23C6 carbides exhibited continuous network structure at GBs may increase intergranular embrittlement tendency of the Fe-Ni-based superalloy. shows microcrack presented at grain boundary after creep test, where both TiC and Cr23C6 carbides existed in the adjacent region.
The evolution of γ′ precipitates and creep fracture mechanism
shows the morphology of γ′ phase after long-term creep under the conditions of 750°C/130 MPa and 700°C/200 MPa. γ′ phase still exhibited near spherical shape and the average size of the precipitates after creep under the aforementioned conditions were about 139 nm and 69 nm, respectively. It indicates the coarsening rate of γ′ phase was sensitive to creep temperature. The driving force for coarsening of γ’ precipitates mainly comes from the reducing of specific free energy at the interface of γ′/γ [Citation30]. shows the bright-field image of the experimental alloy and corresponding selected area electron diffraction (SAED) pattern. The SAED pattern confirmed the presence of γ′ phase. depicts the elemental mapping results of the region that corresponding to . These spherical precipitates uniformly distributed in the matrix and enriched in Ni, Ti, and Al elements, implying these precipitates were Ni3(Al, Ti).
Figure 6. SEM images showing the morphology of γ′ precipitates under the creep condition of (a) 750°C/130 MPa and (b) 700°C/200 MPa. (c) TEM bright-field image and corresponding (d) EDS elemental analysis results of the experimental alloy under the creep condition of 700°C/200 MPa.
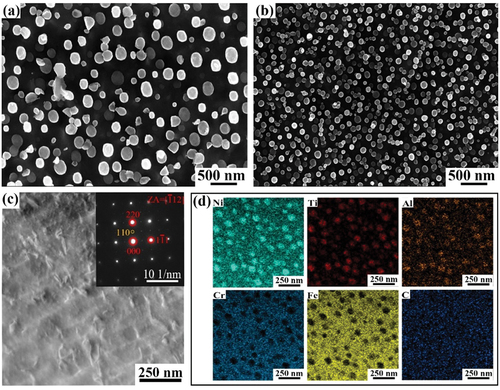
It should be noted that ‘abnormal’ microstructure presented in the region along grain boundaries after long-term creep, as shown in . Precipitates-free zones (PFZs) and discontinuous coarsening zones (DCZs) were observed. γ′ precipitates cannot be observed in the PFZs due to dissolution during the creep process. Grain boundary migration phenomenon will occur when stress is exerted. In order to maintain the strain compatibility of adjacent grains, grain boundary migration is a better choice from energy consideration [Citation31]. During the creep process, the accumulation of dislocations in the vicinity of grain boundaries increased the concentration of vacancy, which promoted the dissolution of γ′ precipitates. Moreover, elements redistribution during long-term exposure to high-temperature environment also can result in the formation of PFZs [Citation32]. Moreover, discontinuous coarse precipitates with needle-like or irregular shape were observed in the vicinity of PFZs. shows the EDS mapping results of the coarse precipitates in the grain boundary of the sample after creep at the condition of 700°C/200 MPa. These precipitates were confirmed enriched with Ni, Al, and Ti elements, indicating they were discontinuous coarse γ′ phase. The size of the coarse γ′ phase was 10–50 times larger than the regular γ′ phase in the matrix. The great consumption of Ni, Al and Ti for precipitation of coarse γ′ phase should be one of the reason for the formation of γ′ phase PFZs in the adjacent regions. In general, the strength of PFZs is lower than the matrix due to lacking of γ′ precipitates and the relative lower concentration of alloying elements, which act as precipitate strengthening and solid solution strengthening role, respectively. If the width of PFZs exceeds a well-defined limit, they lower the yield strength drastically [Citation33]. Therefore, PFZs more likely be the crack nucleation and propagation sites and lead to intergranular fracture during creep.
Figure 7. SEM and EDS mapping images of PFZs/DCZs in samples after creep at (a, b) 750°C/130 MPa and (c, d) 700°C/200 MPa. (e) elemental mapping of the coarse precipitates in the sample crept at 700°C/200 MPa.
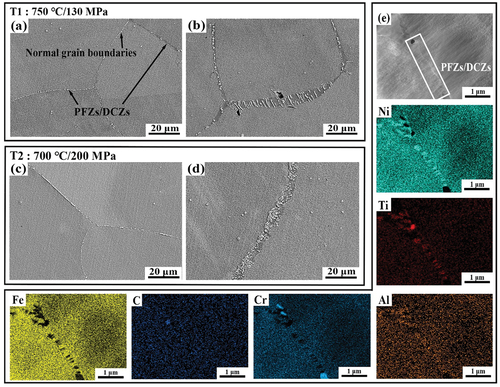
shows the fracture morphology of the Fe-Ni-based superalloy after creep rupture. Although the fracture surface occurred oxidation phenomenon due to fractured at high temperatures, it was clearly the fracture surface was of cleavage fracture character (). The phenomenon of intergranular fracture usually caused by the presence of brittle second phase at grain boundaries or the weakened grain boundaries. In the present study, both coarse γ′ phase and PFZs occurred along grain boundaries, which should be one of the reasons for the intergranular fracture during the creep test.
Strain distribution and grain boundary characteristics
shows the EBSD analysis results the experimental alloy after creep under the conditions of 750°C/130 MPa and 700°C/200 MPa. The inverse pole figures () show the grain orientation of the grains were random, without preferential orientation. The average grain size of the samples after creep under the aforementioned conditions were about 232 μm and 221 μm, respectively. Fine grains were observed in the vicinity of large grains. Twins formed in most of the coarse grains which can be distinguished from orientation. The kernel average misorientation (KAM) figures () reflect the strain distribution of samples after creep experiments, which also corresponding to the distribution of dislocations density. The distribution of the strain in the crept samples were uneven. Stain more likely to concentrate in small grains or around grain boundaries. Moreover, small grain boundaries were observed in the high strain regions. It is well-known dislocations can transform into low-angle grain boundaries through dislocation climb. This climb can occur due to the presence of vacancies or interstitial atoms that provide a pathway for dislocation motion. During high-temperature creep process, atoms diffusion together with dislocations movement promoted the low-angle grain boundaries formation, which can reduce the overall energy associated with the dislocation network. The proportion of different degree of strains in the samples was counted, as shown in . In general, strain that higher than 1% is regarded as the high strain. Therefore, the fraction of high strain in the sample that crept under the condition of 700°C/200 MPa was higher than that under 750°C/130 MPa. The relative lower fraction of high strain in the sample maybe one of the reasons for its longer creep life.
Figure 9. EBSD analysis results of the alloy after creep at of 750°C/130 MPa and 700°C/200 MPa. (a, d) inverse pole figure (IPF), (b, e) kernel average misorientation (KAM) figure (red lines: low angle grain boundary (2°–15°); black lines: high angle grain boundary (>15°)), (c, f) coincidence site lattice (CSL) boundary figure, (g) strains calculated by KAM results, (h) the proportion of various coincidence site lattice (CSL) grain boundaries.
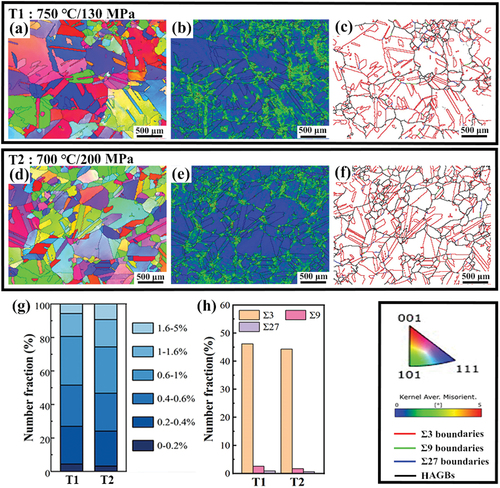
shows the statistical results of the representative coincidence site lattice (CSL) boundaries, which include ∑3, ∑9, and ∑27 boundaries. CSL boundaries are special grain boundaries that possess a high degree of atomic coincidence between adjacent grains, which tend to have higher interfacial strength compared to random grain boundaries. This increased strength can impede dislocation motion and grain boundary sliding, reducing the rate of creep deformation. The presence of CSL boundaries can effectively act as barriers to dislocation movement, leading to a longer creep life [Citation34,Citation35]. In the present study, the statistical results show the proportion of ∑3, ∑9, and ∑27 boundaries in the sample that crept at 750°C/130 MPa were 46.2%, 2.57%, and 0.93%, respectively. In contrast, these values were 44.3%, 1.72%, and 0.62%, respectively, when crept at 700°C/200 MPa. It is obvious the CSL boundary was dominated by ∑3 boundary and the sample with higher fraction of CSL boundary corresponded to longer creep life. Therefore, higher fraction of ∑3 boundary in the superalloy is beneficial to improve its creep life.
Creep deformation mechanism
Dislocation slip is the primary mechanism that responsible for the creep deformation of superalloys. Under high temperatures and applied stress, dislocations in the crystal lattice move and glide, causing plastic deformation. The movement and interaction of dislocations contribute to the time-dependent deformation observed in creep. Therefore, high number density of near spherical shape γ′ particles in the matrix plays a significant role in the creep deformation of the Fe-Ni-based superalloy. shows the TEM bright-field images of the sample after creep at 750°C/130 MPa and 700°C/200 MPa. The length and density of dislocations in the samples exhibited striking different morphology. Dislocations with lower density and longer length were observed in the sample crept at 750°C/130 MPa. These dislocations were pinned by precipitates and bowed. In contrast, dislocation in the sample that crept at 700°C/200 MPa were characterized with high density and short length. These dislocations were also pinned by precipitates. The different morphology of dislocations in the crept samples should be the combined effect of different factors, such as, precipitates, temperature, and stress.
Figure 10. TEM bright-field images showing the interaction between dislocations and γ′ particles when crept at (a) 750°C/130 MPa and (b) 700°C/200 MPa.
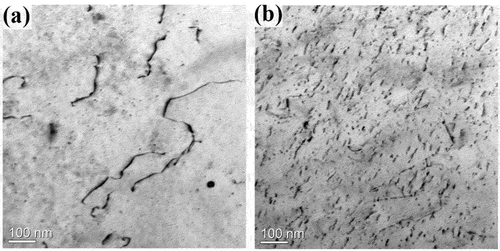
The γ′ particles size and interparticle spacing were different in the samples that crept under various conditions, as shown in . Large interparticle spacing is beneficial for dislocations bypass precipitates. Dislocation loops can expand through the narrow matrix channels between rod-shape precipitates, which have a ~ 30–40 nm interparticle spacing [Citation36]. The mechanisms about dislocations move across precipitates include cutting and by-passing based on the interparticle spacing. In this study, the interparticle spacing of the two samples were large, especially for the sample crept at 750°C/130 MPa (). Therefore, dislocations slipped through the γ′ particles of the two samples were dominated by by-passing mechanism. also shows dislocations bypassed the precipitates when encountered these precipitates. Due to the coarsening of γ′ particles during long-term creep, the size of γ′ particles and interparticle spacing in the sample that crept at 750°C/130 MPa were almost twice as big as that in the sample crept at 700°C/200 MPa. Moreover, higher temperatures generally promote the formation and movement of dislocations in superalloy. But the relative lower applied stress reduces dislocation generation and multiplication. also shows the higher density of dislocations existed in the sample crept under higher stress. Therefore, the combination of γ′ particles, temperature and stress affect the dislocation behaviour during creep. The relative fewer dislocations movement in the sample crept at 750°C/130 MPa should be one of the reasons for its longer creep life.
Conclusions
In this study, the microstructure evolution and creep deformation mechanism of a low-cost Fe-Ni-based superalloy under the creep conditions of 750°C/130 MPa and 700°C/200 MPa were systematically analysed. The following conclusions can be drawn:
The creep life of the Fe-Ni-based superalloy that crept at 750°C/130 MPa and 700°C/200 MPa reached 14,715 h and 12,716 h, respectively. The creep property of the experimental alloy can satisfy the requirement about the materials used for 700°C ultra-supercritical power plant.
Carbides in the vicinity of grain boundaries increased obviously after long-term creep, especially crept at 700°C/200 MPa. Large size TiC carbides were distributed in band along grain boundaries, which may lead to stress concentration at the carbides/matrix interface and promote crack nucleation. Cr23C6 carbides exhibited continuous network structure at GBs may increase intergranular embrittlement tendency of the Fe-Ni-based superalloy.
Ni3(Al,Ti) type γ′ particles increased from ~26 nm to ~139 nm and ~69 nm, respectively, after crept at 750°C/130 MPa and 700°C/200 MPa. Coarse needle like γ′ phase, carbides, and precipitates-free zones (PFZs) occurred along grain boundaries, which weakened the grain boundary strength and led to the intergranular fracture of the samples during creep test.
The distribution of the strain in the crept samples were uneven. Stain more likely to concentrate in small grains or around grain boundaries. The relative lower fraction of high strain and higher fraction of ∑3 boundary in the sample that crept at 750°C/130 MPa should be one of the reasons for its longer creep life.
The creep deformation of the experimental alloy was dominated by dislocations slip through bypassing precipitates. The combination of γ′ particles, temperature and stress affect the dislocation behaviour during creep.
Author contribution
L.L. Wei: Conceptualization, Methodology, Formal analysis, Investigation, Writing – original draft, Funding acquisition. B.K. Pan: Investigation, Data processing. Y.G. Wang: Investigation. B. Li: Investigation. X.S. Jia: Conceptualization, Supervision, Resources, Project administration, Writing – review & editing, Funding acquisition.
Acknowledgments
This work is funded by Guangdong Basic and Applied Basic Research Foundation (No. 2021A1515110151).
Disclosure statement
The authors declare that they have no known competing financial interests or personal relationships that could have appeared to influence the work reported in this paper.
Data availability statement
The raw/processed data required to reproduce these findings cannot be shared at this time as the data also forms part of an ongoing study
Correction Statement
This article has been republished with minor changes. These changes do not impact the academic content of the article.
Additional information
Funding
References
- Huang Y, Zhang R, Zhou Z, et al. Effect of long-term aging on microstructural stability and tensile deformation of a Fe–Ni-based superalloy. Mater Sci Eng A. 2022;847:143298. doi: 10.1016/j.msea.2022.143298
- Wei LL, Chen LQ, Ma MY, et al. Oxidation behavior of ferritic stainless steels in simulated automotive exhaust gas containing 5 vol.% water vapor. Mater Chem Phys. 2018;205:508–11. doi: 10.1016/j.matchemphys.2017.11.051
- Wei L, Zheng J, Chen L, et al. High temperature oxidation behavior of ferritic stainless steel containing W and ce. Corros Sci. 2018;142:79–92. doi: 10.1016/j.corsci.2018.07.017
- Ning H, Li X, Meng L, et al. Effect of Ni and Mo on microstructure and mechanical properties of grey cast iron. Mater Technol. 2023;38(1):2172991. doi: 10.1080/10667857.2023.2172991
- Niu G, Zurob HS, Misra RDK, et al. Superior fracture toughness in a high-strength austenitic steel with heterogeneous lamellar microstructure. Acta Mater. 2022;226:117642. doi: 10.1016/j.actamat.2022.117642
- Misra RDK. Enabling manufacturing of multi-axial forging-induced ultrafine-grained strong and ductile magnesium alloys: a perspective of process-structure-property paradigm. Mater Technol. 2023;38(1):2189769. doi: 10.1080/10667857.2023.2189769
- Misra RDK, Challa VSA, Injeti VSY. Phase reversion-induced nanostructured austenitic alloys: an overview. Mater Technol. 2022;37(7):437–449. doi: 10.1080/10667857.2022.2065621
- Wei LL, Gao GH, Kim J, et al. Ultrahigh strength-high ductility 1 GPa low density austenitic steel with ordered precipitation strengthening phase and dynamic slip band refinement. Mater Sci Eng A. 2022;838:142829. doi: 10.1016/j.msea.2022.142829
- Misra RDK. On the relationship between the grain boundary bio-physical attributes with the cells in the physiological environment. Mater Lett. 2023;344:134453. doi: 10.1016/j.matlet.2023.134453
- Yang C, Xu H, Wang Y, et al. Hot tearing analysis and process optimisation of the fire face of al-cu alloy cylinder head based on MAGMA numerical simulation. Mater Technol. 2023;38(1):2165245. doi: 10.1080/10667857.2023.2165245
- Guo L, Su X, Dai L, et al. Strain ageing embrittlement behaviour of X80 self-shielded flux-cored girth weld metal. Mater Technol. 2023;38(1):2164978. doi: 10.1080/10667857.2023.2164978
- Li Q, Zuo H, Feng J, et al. Strain rate and temperature sensitivity on the flow behaviour of a duplex stainless steel during hot deformation. Mater Technol. 2023;38(1):2166216. doi: 10.1080/10667857.2023.2166216
- Wang L, Li J, Liu ZQ, et al. Towards strength-ductility synergy in nanosheets strengthened titanium matrix composites through laser power bed fusion of MXene/Ti composite powder. Mater Technol. 2023;38(1):2181680. doi: 10.1080/10667857.2023.2181680
- Wei L, Chen L, Liu H, et al. Significant grain refinement in the simulated heat affected zone (HAZ) of ferritic stainless steels by alloying with tungsten. Metall Mater Trans A. 2020;51(6):2719–2723. doi: 10.1007/s11661-020-05767-4
- Wei L, Chen L, Liu H, et al. Precipitation behavior of laves phase in the vicinity of oxide film of ferritic stainless steel: selective oxidation-induced precipitation. Oxid Met. 2020;93(1–2):195–213. doi: 10.1007/s11085-019-09955-5
- Fatriansyah JF, Suhariadi I, Fauziyyah HA, et al. Prediction and optimization of mechanical properties of Ni based and FeeNi based super alloys via neural network approach with alloying composition parameter. J Mater Res Technol. 2023;24:4168–4176. doi: 10.1016/j.jmrt.2023.04.065
- Huang YS, Wang XG, Cui CY, et al. The effect of coarsening of γ′ precipitate on creep properties of Ni-based single crystal superalloys during long-term aging. Mater Sci Eng A. 2020;773:138886. doi: 10.1016/j.msea.2019.138886
- Peng T, Yang B, Yang G, et al. Microstructural evolution and mechanical properties of nimonic 105 alloy aged at 750 °C. J Alloys Compd. 2019;798:375–385. doi: 10.1016/j.jallcom.2019.05.289
- Acharya MV, Fuchs GE. The effect of long-term thermal exposures on the microstructure and properties of CMSX-10 single crystal Ni-base superalloys. Mater Sci Eng A. 2004;381(1):143–153. doi: 10.1016/j.msea.2004.04.001
- Yonemura M, Semba H, Igarashi M. Development of microstructural damage in Ni-based alloys during creep. Metall Mater Trans A. 2016;47(4):1898–1905. doi: 10.1007/s11661-016-3346-5
- Xia W, Zhao X, Yue L, et al. Microstructural evolution and creep mechanisms in Ni-based single crystal superalloys: a review. J Alloys Compd. 2020;819:152954. doi: 10.1016/j.jallcom.2019.152954
- Tang Y, Huang M, Xiong J, et al. Evolution of superdislocation structures during tertiary creep of a nickel-based single-crystal superalloy at high temperature and low stress. Acta Mater. 2017;126:336–345. doi: 10.1016/j.actamat.2016.12.072
- Zhang P, Yuan Y, Shen SC, et al. Tensile deformation mechanisms at various temperatures in a new directionally solidified Ni-base superalloy. J Alloy Comp. 2017;694:502–509.
- Geng P, Li W, Zhang X, et al. A theoretical model for yield strength anomaly of Ni-base superalloys at elevated temperature. J Alloy Comp. 2017;706:340–343. doi: 10.1016/j.jallcom.2017.02.262
- Cui L, Yu J, Liu J, et al. The creep deformation mechanisms of a newly designed nickel-base superalloy. Mater Sci Eng A. 2018;710:309–317. doi: 10.1016/j.msea.2017.11.002
- Lv P, Liu L, Zhao G, et al. Creep properties and relevant deformation mechanisms of two low-cost nickel-based single crystal superalloys at elevated temperatures. Mater Sci Eng A. 2022;851:143561. doi: 10.1016/j.msea.2022.143561
- Wang X, Han G, Cui C, et al. The dependence of portevin–Le châtelier effect on the γ′ precipitates in a wrought Ni-base superalloy. Metall Mater Trans A. 2016;47(12):5994–6003. doi: 10.1007/s11661-016-3718-x
- Iwamaru A, Hisazawa H, Terada Y. Microstructure evolution of Fe–Ni-based alloy HR6W during isothermal aging. Mater Trans. 2019;60(5):824–829. doi: 10.2320/matertrans.M2019032
- Cheng H, Li Z, Leng B, et al. Intergranular diffusion and embrittlement of a Ni–16Mo–7Cr alloy in te vapor environment. J Nucl Mater. 2015;467:341–348. doi: 10.1016/j.jnucmat.2015.09.053
- Unocic KA, Shingledecker JP, Tortorelli PF. Microstructural changes in Inconel® 740 after long-term aging in the presence and absence of stress. JOM. 2014;66(12):2535–2542. doi: 10.1007/s11837-014-1208-4
- Bechetti DH, DuPont JN, Barbadillo JJ, et al. Microstructural evolution of INCONEL® alloy 740H® fusion welds during creep. Metall Mater Trans A. 2014;46(2):739–755. doi: 10.1007/s11661-014-2682-6
- Hou K, Ou M, Wang M, et al. Precipitation of η phase and its effects on stress rupture properties of K4750 alloy. Mater Sci Eng A. 2019;763:138137. doi: 10.1016/j.msea.2019.138137
- Krol T, Baither D, Nembach E. The formation of precipitate free zones along grain boundaries in a superalloy and the ensuing effects on its plastic deformation. Acta Mater. 2004;52(7):2095–2108. doi: 10.1016/j.actamat.2004.01.011
- Thaveeprungsriporn V, Was GS. The role of coincidence-site-lattice boundaries in creep of Ni-16Cr-9Fe at 360 °C. Metall Mater Trans A. 1997;28(10):2101–2112. doi: 10.1007/s11661-997-0167-6
- Lall A, Bowen P, Rabiei A. A study on the creep behavior of alloy 709 using in-situ scanning electron microscopy. Mater Charact. 2022;183:111587. doi: 10.1016/j.matchar.2021.111587
- Gutierrez-Urrutia I, Raabe D. High strength and ductile low density austenitic FeMnAlC steels: simplex and alloys strengthened by nanoscale ordered carbides. Mater Sci Technol. 2014;30(9):1099–1104. doi: 10.1179/1743284714Y.0000000515