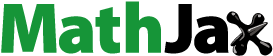
Abstract
Frequent donning and doffing of filtering facepiece respirators (FFRs) can reduce their effectiveness due to the residual deformation of their elastic head straps. This study investigates the loss of elasticity of head straps during repeated use. Five elastomeric tapes were tested as FFR head straps, and their tensile strength was measured using a DU-100 dynamometer after repeated donning and doffing cycles. After eight consecutive uses, the protection factor drops significantly, requiring strap length adjustments to guarantee the specified level of user protection. The maximum tensile force of the elastomeric head straps causes residual elongation, which remains consistent after eight cycles. The study also establishes how strap elongation depends on the force and number of donning and doffing cycles. This knowledge is vital for designing better FFRs. Additionally, the research explores alternative materials for FFR construction to address strap elongation and its effects on performance and comfort.
1. Introduction
Filtering facepiece respirators (FFRs) play a crucial role in safeguarding workers’ respiratory systems from harmful aerosols or industrial dust during their professional activities. Moulded half masks are among the most common type (Figure ). Their widespread use is attributed to the adequate protection they provide, their simplistic design and ease of use. Recently, they have become an essential tool for medical professionals caring for patients with COVID-19 [Citation1].
Figure 1. Design of the typical filtering facepiece respirator. Note: 1 = nose clip; 2 = elastomeric head straps; 3 = exhalation valve; 4 = inner seal; 5 = filtering material (filtering facepiece). The full colour version of this figure is available online.
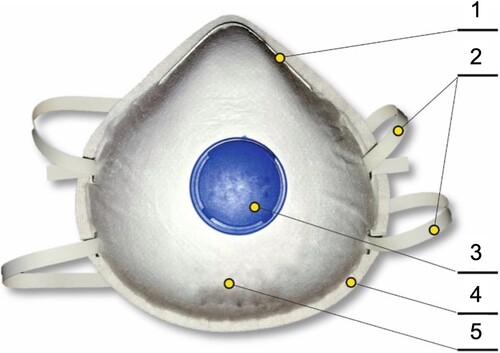
The key to ensuring the safety of FFR users lies in the tight fit of the facepiece against the user’s face [Citation2]. This largely depends on two factors: the extent to which the facepiece design aligns with the user head’s anthropometric dimensions and the amount of force applied by elastomeric head straps to secure the facepiece to the user’s face. Often, issues surrounding adequate FFR protection arise in maintaining the necessary tension in the head strap, as inadequate tension can lead to gaps that permit the ingress of polluted air into the breathing zone, thereby diminishing the FFR’s protective properties.
Disposable FFRs, marked as ‘NR’ (non-reusable) according to the European standards [Citation3], are advised to be discarded after one work shift or 4–8 h of use. However, FFRs marked as ‘R’ (reusable) can be used multiple times. Real-world practice often sees FFRs being repeatedly removed and put on during work shifts, potentially leading to a loss of elasticity in the elastomeric head straps due to frequent stretching, which can cause deformation and even breakage. Unfortunately, during the laboratory tests of FFRs, the quality of elastomeric head straps is typically only assessed during practical performance tests, and there is no provision for determining residual deformation following multiple donning and doffing cycles of the FFR [Citation3].
Hence, for FFR manufacturers, the development of suitable methods and results for such studies is pertinent for choosing elastomeric straps materials, which would provide the specified level of protective properties of the FFRs throughout their intended service life.
Certain studies have also evaluated the impact of respiratory protective equipment (RPE) storage time on the properties of its elastomeric straps, demonstrating how tension forces change when the FFR is worn infrequently [Citation4]. It was also discovered that the upper strap has a more significant impact on the FFR’s leak-tightness than the lower strap, suggesting that different materials could be utilized in their manufacture [Citation5].
The results of the study were later substantially enhanced through the application of three-dimensional imaging apparatus. This enabled determination of the sealing interface established between the user’s facial contour and the perimeter of the FFR as well as the spatial distribution of the compressive forces exerted behind the seal. A noteworthy observation was recorded post the ultraviolet disinfection procedure applied to the straps, a process shown to compromise their inherent tensile strength [Citation6].
The hygienic and ergonomic properties of RPE, including the mechanical pressure exerted by the facepiece on the human face, play a significant role in the potential adverse effects on users [Citation7–9]. Limited use of RPE is often reported in workplaces due to local pain or discomfort caused by the device. At the same time, the pressure applied by the front part of the FFR facepiece ensures a tight fit around the sealing strip. Studies indicate that this pressure can range from 5 to 30 N, depending on the tension of the head strap [Citation10–12]. Such a wide pressure range is attributed to some workers’ attempts to secure the FFR more tightly against the face to prevent the penetration of unfiltered air into the breathing zone. This leads to facial pressure sores or skin irritation, often leading to the removal of the FFR and subsequent degradation of the elastomeric head straps, as demonstrated by Pires et al. [Citation13]. The researchers showed that the deterioration of elastic properties occurred after 10–14 days of use of the reusable FFR. Some studies have shown how the environmental conditions and temperatures can affect the preservation of the properties of such materials [Citation14]. In other works, the hypothesis that the respirator can be used up to five times was tested [Citation15–17]. To validate this, the authors presented the outcomes of determining the fit after 20 wearing cycles. However, the investigation did not draw any correlations or conclusions related to the elongation of the FFR’s elastomeric head straps.
Consequently, a task emerged to establish the dependence between the relative elongation of the elastomeric strap, the applied force and the number of donning and doffing cycles, to elucidate any potential degradation in the FFR’s protective properties.
This article seeks to identify the lifespan of the elasticity of elastomeric head straps of the FFR. To achieve this aim, we have ascertained the relative elongation of the elastomeric head straps in response to tension, which could be interpreted into technical specifications for FFR production. We have also investigated the strap elongation following multiple cycles of donning and doffing and evaluated the impact of this elongation on the FFR’s fit. We have also explored strategies for improving the overall performance of the strap. One such option included the integration of specialized plastic inserts into the head harness of the FFR.
2. Materials and methods
2.1. Filtering facepiece respirators
Five different types of elastomeric tapes were selected for this experimental study (Figure ). Their corresponding technical specifications are presented in Table . The selected tapes are among the most commonly used in FFR designs and are readily available on the market. Each tape was used to construct the head straps for the Standard 213 FFP2 NR model of FFR, which is mass-produced by LLC SPE Standart (Ukraine). All straps were affixed to the facepiece through ultrasonic welding. The length of each strap was consistently 320 mm, a measurement that was determined based on the anthropometric dimensions of the users.
Figure 2. Types of elastomeric tapes used in design of the filtering facepiece respirator (FFR). Note: 1 = round thin; 2 = round large; 3 = wide rectangular; 4 = narrow rectangular; 5 = ordinary.
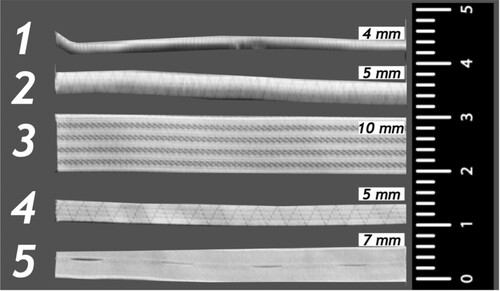
Table 1. Technical specifications of elastomeric tapes.
Each strap was marked at 5-mm intervals, allowing for precise measurement of their elongation due to applied force. A TOPEX 50-cm 31C050 metal ruler (TOPEX, Poland), with an uncertainty of U = 0.1 mm, was used for these measurements. The markings on the straps were made manually using a ‘pigment liner 0.5’ marker from STA Company (China), with a rod thickness of 0.5 mm.
Experiments were performed with human participants, as a head model cannot provide the required tightness of the facepiece, and the use of sealants (e.g., adhesive tape or latex glue) could affect the test results by reducing the breathing surface and interfering with the head straps. The participants in the study were selected based on medical factors and an absence of facial hair and scars to ensure consistency. A total of five individuals (three men and two women) were chosen as test subjects. Prior to the tests, the test subjects provided their written consent for the processing of collected data and underwent initial instruction on the proper use of the FFRs.
The FFR was then put on the face of the participant according to the manufacturer’s instructions (lower strap on the neck, upper strap on the back of the head). A seal check was performed before each round of tests to avoid leakage. If necessary, the FFR was readjusted.
2.2. Tensile strength of the elastomeric head strap
The tension of elastomeric head straps was measured with the DU-100 dynamometer (PromTechniMashPrylad, Ukraine). The accuracy of the force measurements was equal to 0.5 N, with a deviation from the measured value of 0.04 N.
The tensile strength of the FFR’s head strap was gradually increased. To achieve this, a dynamometer was attached to the headband, positioning the straps at the centre to ensure they stretched uniformly. The tensile force was applied perpendicular to the axis of the facepiece (Figure ). The test operator carried out the stretching and meticulously adjusted the tension of the elastomeric straps by monitoring the dynamometer’s scale. All data gathered were documented in the work records.
Figure 3. General view of laboratory tests. Note: 1 = respirator model Standard 213 FFP2 NR (LLC SPE Standart, Ukraine); 2 = elastomeric head straps; 3 = dynamometer DU-100 (PromTechniMashPrylad, Ukraine); 4 = differential pressure gauge Testo 512 (TESTO AG, Germany). The full colour version of this figure is available online.
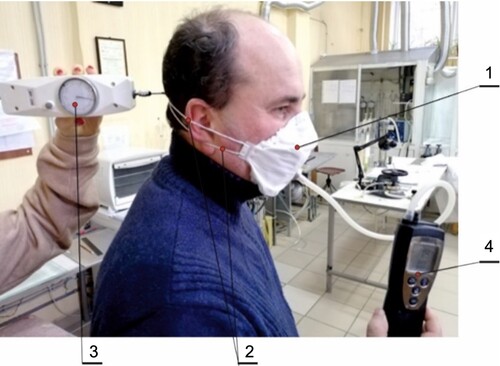
2.3. Pressure drop and protection factor
The change in the pressure drop across the respirator was also evaluated using the differential Testo 512 pressure gauge (U = 0.1 Pa; TESTO AG, Germany) with an accuracy of 1 Pa (Figure ). The pressure drop data were also monitored and recorded in the working records, which allowed calculation of the protection factor of the FFR according to the following equation [Citation18]:
(1)
(1) where Ki = airflow coefficient in the obturation strip; ηc =penetration coefficient of the filtering material of the FFR; ηn = leakage coefficient through the slits in the obturation strap of the FFR.
Ki is determined by the following equation [Citation18]:
(2)
(2) where Δpr = pressure drop in the FFR (Pa); Rf = aerodynamic drag of the filtering material (N·s / m5); Δpf = pressure drop on the filtering material of the FFR (Pa); Rr = aerodynamic drag of the FFR (N·s / m5).
The filtration efficiency and leakage coefficient of the FFR were determined according to the method described by Cheberiachko et al. [Citation19]. The FFR used in the study is manufactured using the filtering material ELEFLEN, which has a penetration coefficient ranging between 0.01 and 0.05% [Citation11]. Furthermore, the leakage coefficient through any gaps between the user’s face and the FFR was found to be 0.005%. The determination of the air flow resistance of the ELEFLEN filtering material was conducted according to the method described by Cheberyachko et al. [Citation20].
2.4. Simulated wearing
According to ‘Simulated wearing treatment’ of Standard No. EN 149:2001 + A1:2009 [Citation3,para.8.3.1], the donning and doffing procedure should be repeated 20 times. In our experiment, the donning and doffing procedure was repeated until the elastomeric strap was elongated and the ‘equilibrium state’ was reached, i.e., the state when the elastomeric strap was no longer elongated. Usually, during the initial period (approximately five iterations), a rapid increase in residual deformation was observed, leading to a deterioration in the fit of the FFR to the user’s face. However, after 10–12 iterations, due to the ordering of the material structure, the increase ceased and the elastomeric strap reached a state of equilibrium. A total of 10 samples of the FFR were tested. The testing sample was only used by one tester, and was disposed of after the experiment.
2.5. Relative elongation
The relative elongation of the elastomeric straps was determined by measuring the force of tension using a PM-3-1 tensile machine with the accuracy of 0.1 N (LLC SPE Ukrintech, Ukraine). Marked sections of elastomeric straps of 50 mm each were vertically firmly fixed in the clamps of the PM-3-1 tensile machine. Next, the tensile machine was turned on, which stretched the tested samples at 100 mm/min speed, so there was no stress on the elongation. The tensile force and relative elongation were recorded. Upon reaching the force at which the fixed specimens were no longer stretched, the tensile machine automatically stopped and the tests ended. In cases where slippage did occur at the stretching phase, the test was repeated with a new sample to ensure accurate and consistent measurements. Four samples of each type of tested elastomeric straps were prepared. Each testing sample was used only once and disposed of afterwards.
2.6. Calculations
The data analysis was performed using Microsoft Excel version 2010. For statistical analysis, a significance level of p < 0.05 was considered to determine statistical significance.
3. Results and discussion
In the initial phase, the relative elongation of the elastomeric head straps of the FFR under the impact of tensile forces was evaluated (Figure ). This was done to verify compliance with the requirements of the technical conditions for the manufacture of FFRs. In particular, the elastomeric tapes of the head strap could sustain a 20 N load for a duration of 10 s without any failure.
Figure 4. Dependence of relative elongation, Δl / l (%), of elastomeric straps on tension force, FT (N). Note: 1 = round thin; 2 = round large; 3 = wide rectangular; 4 = narrow rectangular; 5 = ordinary. The full colour version of this figure is available online.
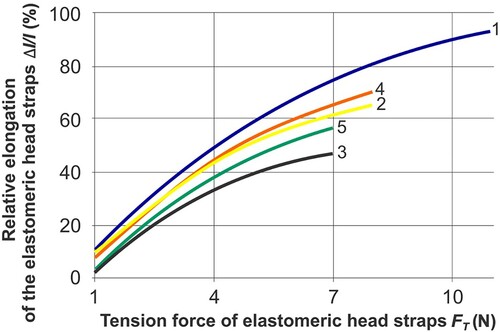
The thin round tape (tape no. 1, Figure ) exhibited the highest relative elongation, whereas the lowest was found for the wide rectangular tape (tape no. 3, Figure ). The strap’s relative elongation diminished as the tape’s width increased. Tapes with lower surface density demonstrated higher relative elongations.
The subsequent phase examined the elongation of the elastomeric head straps of the FFR due to repeated cycles of donning and doffing (Table ). This allowed us to determine the residual elongation of the FFR’s elastomeric head straps, which subsequently helped assess the deterioration of protective properties. Specifically, we calculated the protection coefficient, which is affected by a reduction in pressing force and an increase in unfiltered air suction through gaps between the face and the facepiece.
Table 2. Elongation of elastomeric head straps due to repeated donning and doffing of the FFR.
In all tested types of elastic straps, elongation increased with the rising number of donning and doffing cycles. The highest relative elongation was observed for the narrowest tape (tape no. 1, Figure ), and the lowest for the widest tape (tape no. 3, Figure ). Towards the end of the experiment, the relative elongation decreased with an increase in surface density.
Elongation of the elastomeric head straps, caused by repeated donning and doffing of the FFR, resulted in weakened pressing force of the half mask against the user’s face The average measured values are presented in Table .
Table 3. Residual tensile strength of elastomeric head straps after multiple procedures of donning and doffing the FFR.
One can conclude that the poorest results were obtained for elastomeric tape no. 1 (Figure ), which is characterized by the minimum technical parameters, as presented in Table .
To ascertain the change in the FFR’s protection factor due to the stretching of the elastomeric straps, we determined the pressure drop loss resulting from leaks between the user’s face and the FFR, as presented in Table . Table presents the calculation of the protection factor for the ‘Standard’ FFR, considering harmful aerosol leakage caused by gaps between the user’s face and the FFR. These gaps are due to the weakening of the tension force of the head harness resulting from the stretching of the elastomeric straps.
Table 4. Pressure drops on the FFR due to multiple donning and doffing cycles.
Table 5. Changes in protection factor due to multiple donning and doffing cycles for different elastomeric tapes.
Experimental study results demonstrate that simulating multiple rounds of donning and doffing of FFRs leads to a gradual decrease in the tensile strength and internal restorative properties of the elastomeric material from which they are made. The degree of tensile strength deterioration in the elastomeric head straps depends on the type of material and its technical specifications, including width, elongation and surface density (see Table ).
It is assumed that the inner structural elements of elastomeric tapes have a spiral shape, which expands with increasing force and eventually becomes linear. This transformation impacts the tape’s ability to restore its original size (in the case of elastomeric tape no. 1, it extended almost 2 cm from 35 cm after five stretches). This change in shape from spiral to linear is due to weak secondary connections, while the recovery of the original structure is facilitated by transverse ligaments. Residual deformation occurs only when the polymer stretches beyond the elastic deformation limit, leading to the rupture of transverse ligaments [Citation15,Citation16].
To enhance the protection level for FFR users when repeated removal is necessary, we propose reducing the size of the elastomeric straps by adding plastic inserts to the head harness construction (see Figure ). These plastic inserts are positioned at the back of the user’s head and neck, where the elastomeric straps are attached on both sides. This modification would increase the tension force of the head harness, on the one hand, and reduce the volume of strap stretching on the other.
Figure 5. General view of laboratory tests of a respirator with a modernized headband: (a) general view; (b) side view; (c) back view. Note: 1 = respirator model Standard 213 FFP2 NR (LLC SPE Standart, Ukraine); 2 = elastomeric head straps; 3 = dynamometer DU-100 (PromTechniMashPrylad, Ukraine); 4 = plastic insert. The full colour version of this figure is available online.

To verify this hypothesis, an experiment was conducted following the previously described procedure to calculate the change in protection factor of the FFR due to several donning and doffing cycles. Three variants were considered, each differing in the length of the elastomeric straps fixed on the respective grips of the 100-mm plastic insert. The results are presented in Table .
Table 6. Changes in protection factor due to multiple donning and doffing cycles.
Note that the length of the elastomeric straps was determined by the value of the pressing forces, which should ideally be within a comfortable range (4–6 N). We observed less elongation of the straps and a minor increase in the FFR protection factor during multiple donning and doffing procedures. These results suggest the potential applicability of such a structural solution to enhance user safety.
Since the results of our experimental measurements show an escalating decrease in the forces produced by elastomeric straps under continuous stretching, we can infer that some cross-links in the elastomeric material layer are rapturing. Consequently, the FFR facepiece must be equipped with adjustable straps to provide the necessary tension ensuring a leak-tight fit to the user’s face. In many available models, such an element is absent, leading to a decrease in the facepiece’s pressure forces against the face and increasing suction on the obturation strip, which significantly compromises its protective properties [Citation21]. Additionally, it is crucial to monitor the stretch level of the elastomeric strap so that it can be tightened to the appropriate degree in a timely manner.
Studying the relative elongation of the FFR’s elastomeric straps is crucial for determining the effort required to ensure a proper fit of the FFR facepiece to the user’s face. Note that excessive tension results in stretching (structural deformation) of the filtering material, potentially increasing the entry of contaminants into the FFR’s breathing zone [Citation22]. In some FFR models, elastomeric straps can be attached directly to the half mask’s surface. These straps also affect the comfort of wearing protective equipment – they may pull hair, irritate the skin and exert excessive pressure on the face [Citation23].
To improve the comfort of FFRs without compromising their effectiveness and safety, there are several alternatives to traditional rubber straps. Elastic fabric straps made from materials like nylon and spandex offer a balance of a secure fit and comfort, providing a softer and more flexible option. Silicone straps are hypoallergenic, durable and comfortable against the skin, making them another viable alternative. Velcro straps are also a convenient option, allowing for easy adjustments to ensure a perfect fit and enhancing user comfort and safety. For those with sensitive skin, breathable materials such as cotton or poly-cotton blends can minimize skin irritation and enhance comfort. It is important to note that the choice of strap material significantly influences user comfort and overall compliance with FFR use. Therefore, designers and manufacturers should consider these alternatives, but they must undergo rigorous testing to ensure they meet necessary safety standards and do not compromise the FFR’s protective properties.
Furthermore, there are also other changes in FFR construction that could be explored. One of these could be the incorporation of viscoelastic seals in the design of FFRs, which can potentially improve leak-tightness without unnecessary increases in pressure needed for proper facepiece fit [Citation8,Citation9].
A limitation of this study is that it was conducted without additional laboratory tests recommended by Standard No. EN 149:2001 + A1:2009 [Citation3]. Additionally, the study examined only one model of FFRs. This restricts the extrapolation of the results to other models of RPE, especially given the current proliferation of diverse and unique models [Citation24]. These various models may have different methods of attaching elastomeric head straps to the half mask.
4. Conclusions
We have developed a method to determine the impact of elastic forces from elastomeric head straps of FFRs on their protective properties. This allowed us to establish a relationship between the relative elongation of elastomeric straps and the protection factor of FFRs. The developed method differs from existing ones as it determines the reduction in the FFR protection factor by the difference in pressure drops on the FFR and its filter, which results from a decrease in the tension of the head straps.
We discovered that after eight cycles of donning and doffing the FFR, the protection factor significantly deteriorates, and the mask can no longer guarantee the manufacturer’s stated level of protection without additional adjustment to the length of the FFR’s elastomeric head strap. Furthermore, we found that the maximum tensile force of the elastomeric head straps leads to residual elongation, which virtually remains unchanged after eight donning and doffing cycles. The deterioration of the protection factor occurs due to the stretching of the FFR’s elastomeric head strap (from 10 to 210%), underscoring the necessity for laboratory testing of its protective properties following repeated donning and doffing. The results of our study also suggest that it would be advantageous to equip FFR designs with elastomeric head straps and additional structural elements that either control the pressure force or allow for their tightening to increase tension. The inclusion of additional sealing on the facepiece’s rim could also be beneficial to ensure that tight-fitting respirators do not compromise user comfort.
Acknowledgements
This article is partially published and based on the results of a research task carried out within the scope of the fifth stage of the National Programme ‘Improvement of Safety and Working Conditions’ supported by the resources of the National Centre for Research and Development task no. III.PB.14 entitled ‘Development of Self-fitting Seal for Respiratory Protective Devices’. The Central Institute for Labour Protection – National Research Institute is the Programme’s main coordinator.
All test subjects gave informed consent for inclusion before participating in the study. Tests were performed on the study group taking part in the routine assessment of respiratory protective devices according to the European standards.
Disclosure statement
No potential conflict of interest was reported by the authors.
Additional information
Funding
References
- Kim K, Zhao L. Filtering facepiece respirator supply chain management framework in a disaster such as COVID-19. Societies. 2021;11:136. doi:10.3390/soc11040136
- Peters MDJ. N95 respirators for health care workers: the importance of fit, comfort, and usability. Med J Aust. 2022;217:83–84. doi:10.5694/mja2.51618
- European Committee for Standardization. Respiratory protective devices - Filtering half masks to protect against particles. Requirements: testing, marking. Standard No. EN 149:2001+A1: 2009.
- Roberge R, Niezgoda G, Benson S. Analysis of forces generated by N95 filtering facepiece respirator tethering devices: a pilot study. J Occup Environ Hyg. 2012;9:517–523. doi:10.1080/15459624.2012.695962
- Roberge RJ, Palmiero AJ, Liu Y, et al. Effect of upper strap downward displacement on N95 filtering facepiece respirator fit factors: a pilot study. J Occup Environ Hyg. 2014;11:338–341. doi:10.1080/15459624.2013.866716
- Lindsley WG, Martin SB, Thewlis RE, et al. Effects of ultraviolet germicidal irradiation (UVGI) on N95 respirator filtration performance and structural integrity. J Occup Environ Hyg. 2015;12:509–517. doi:10.1080/15459624.2015.1018518
- Graveling R. The ergonomics of respiratory protection. In: L Racz, DP Yamamoto RME, editors. Handbook of Respiratory Protection. Safeguarding Against Current and Emerging Hazards. Boca Raton: CRC Press; 2017. p. 119–128.
- Okrasa M, Leszczyńska M, Sałasińska K, et al. Viscoelastic polyurethane foams for use in seals of respiratory protective devices. Materials. 2021;14:1600. doi:10.3390/ma14071600
- Okrasa M, Leszczyńska M, Sałasińska K, et al. Viscoelastic polyurethane foams with reduced flammability and cytotoxicity. Materials. 2021;15:151. doi:10.3390/ma15010151
- Bazaluk O, Cheberiachko S, Cheberiachko Y, et al. Development of a dust respirator by improving the half mask frame design. Int J Environ Res Public Health. 2021;18:5482. doi:10.3390/ijerph18105482
- Bazaluk O, Ennan A, Cheberiachko S, et al. Research on regularities of cyclic air motion through a respirator filter. Appl Sci. 2021;11:3157. doi:10.3390/app11073157
- De Genova DC, McInnes-Ledoux P, Weinberg R, et al. Force degradation of orthodontic elastomeric chains – a product comparison study. Am J Orthod. 1985;87:377–384. doi:10.1016/0002-9416(85)90197-6
- Pires BU, de Souza RE, Filho MV, et al. Force degradation of different elastomeric chains and nickel titanium closed springs. Brazilian J Oral Sci. 2011;10:167–170.
- Araujo FdC, Ursi WdS. Estudo da degradação da força gerada por elásticos ortodônticos sintéticos [Study of force degradation produced by synthetic orthodontic elastics]. Rev Dent Press Ortod e Ortop Facial. 2006;11:52–61. Spanish. doi:10.1590/S1415-54192006000600008
- Jang JY, Kim SW. Evaluation of filtration performance efficiency of commercial cloth masks. Korean J Environ Heal Sci. 2015;41:203–215. doi:10.5668/JEHS.2015.41.3.203
- Bergman MS, Viscusi DJ, Zhuang Z, et al. Impact of multiple consecutive donnings on filtering facepiece respirator fit. Am J Infect Control. 2012;40:375–380. doi:10.1016/j.ajic.2011.05.003
- Roberge RJ, Kim J-H, Benson S. N95 filtering facepiece respirator deadspace temperature and humidity. J Occup Environ Hyg. 2012;9:166–171. doi:10.1080/15459624.2012.660428
- Golinko V, Cheberiachko S, Cheberiachko Y, et al. Improving the protective efficiency of elastomeric filter respirators. Eastern-European J Enterp Technol. 2015;2:60. doi:10.15587/1729-4061.2015.41210
- Cheberiachko S, Cheberiachko Y, Radchuk D, et al. Calculation of the protection factor taking into consideration leaks between the face and the half-mask of the filter respirator. J Donetsk Min Inst. 2020;1(46):232–239. Russian. doi:10.31474/1999-981x-2020-1-232-239.
- Cheberyachko S, Radchuk D, Cheberyachko Y, et al. Evaluation of respirator reliability. Geo-Technical Mech. 2013;4556:72–83.
- Yang J, Dai J, Zhuang Z. Simulating the interaction between a respirator and a headform using LS-DYNA. Comput Aided Des Appl. 2009;6:539–551. doi:10.3722/cadaps.2009.539-551
- Roberge RJ, Monaghan WD, Palmiero AJ, et al. Infrared imaging for leak detection of N95 filtering facepiece respirators: a pilot study. Am J Ind Med. 2011;54:628–636. doi:10.1002/ajim.20970
- Lei Z, Yang J, Zhuang Z. Headform and N95 filtering facepiece respirator interaction: contact pressure simulation and validation. J Occup Environ Hyg. 2012;9:46–58. doi:10.1080/15459624.2011.635130
- Cheberiachko S, Knysh I, Pustovoi D, et al. Research of operational properties of household fabrics for production of protective masks. Mater Sci Forum. 2021;1038:221–232. doi:10.4028/www.scientific.net/MSF.1038.221