Abstract
A number of activated carbons derived from waste tires were further impregnated by gaseous elemental sulfur at temperatures of 400 and 650 °C, with a carbon and sulfur mass ratio of 1:3. The capabilities of sulfur diffusing into the micropores of the activated carbons were significantly different between 400 and 650 °C, resulting in obvious dissimilarities in the sulfur content of the activated carbons. The sulfur-impregnated activated carbons were examined for the adsorptive capacity of gas-phase mercuric chloride (HgCl2) by thermogravimetric analysis (TGA). The analytical precision of TGA was up to 10−6 g at the inlet HgCl2 concentrations of 100, 300, and 500 μg/m3, for an adsorption time of 3 hr and an adsorption temperature of 150 °C, simulating the flue gas emitted from municipal solid waste (MSW) incinerators. Experimental results showed that sulfur modification can slightly reduce the specific surface area of activated carbons. High-surface-area activated carbons after sulfur modification had abundant mesopores and micropores, whereas low-surface-area activated carbons had abundant macropores and mesopores. Sulfur molecules were evenly distributed on the surface of the inner pores after sulfur modification, and the sulfur content of the activated carbons increased from 2–2.5% to 5–11%. After sulfur modification, the adsorptive capacity of HgCl2 for high-surface-area sulfurized activated carbons reached 1.557 mg/g (22 times higher than the virgin activated carbons). The injection of activated carbons was followed by fabric filtration, which is commonly used to remove HgCl2 from MSW incinerators. The residence time of activated carbons collected in the fabric filter is commonly about 1 hr, but the time required to achieve equilibrium is less than 10 min. Consequently, it is worthwhile to compare the adsorption rates of HgCl2 in the time intervals of <10 and 10–60 min.
Waste tires constitute potential carbonaceous materials for the production of activated carbons, which is a typical control technology for removing HgCl2 from municipal solid waste (MSW) incinerators. The adsorption of HgCl2 with sulfur-impregnated activated carbons has seldom been investigated in regard to the variation in HgCl2 adsorption with a specific surface area and pore size distribution of the activated carbons during the HgCl2 adsorption process. In this work, sulfur-impregnated activated carbons were produced from waste tires and then examined for their adsorptive capacities of HgCl2 using thermogravimetric analysis (TGA).
Introduction
A number of harmful substances are produced and emitted into the atmospheric environment during the incineration of municipal solid wastes (MSWs). Heavy metals in MSWs are the most difficult to remove; in particular, mercury, as a global air pollutant, has been paid considerable attention due to its hazardous effect on the environment and human health (CitationHsi et al., 2001). Elemental mercury (Hg0) and its derivates (e.g., HgCl2 and HgO) have a relatively high vapor pressure, and are easily emitted from MSW incinerators if they have not been effectively removed by air pollution control devices (APCDs) (CitationKrishnan and Anirudhan, 2002).
There are three typical control technologies for removing HgCl2 from MSW incinerators: activated carbon injection, sodium sulfide injection, and wet scrubbing (CitationAmes et al., 1998). Of these, activated carbon injection has been widely used due to its high removal efficiency of HgCl2. Activated carbons have become increasingly interesting because of their excellent adsorbent properties. At present, powdered activated carbons (PACs) used in MSW incinerators are for the most part produced from coconut shells, wood, coal, and other carbon-containing raw materials either by physical or chemical activation (CitationChen et al., 2009). However, a major problem associated with the use of activated carbons for HgCl2 flue gas control is the high cost; thus, the investigation of alternative low-cost adsorbents continues (CitationFan and Brown, 2001). Waste tires constitute a ready source of potential carbonaceous materials for the production of activated carbons.
Commonly, the treatment technologies for waste tires both here and abroad include renovation, reusage, auxiliary fuel, incineration, pyrolysis, etc. (CitationBarbooti et al., 1989). Of these, pyrolysis technology dealing with waste tires has the advantage of not only treating large quantities of waste tires, but also producing value-added by-products (such as combustible gas, pyrolysis oil, and carbon black) (CitationCannon et al., 1996). At present, only a small portion of carbon black is used as an additive to plastic, rubber, etc., whereas the larger portion is disposed of as waste (CitationBiswas and Wu, 1998). In this work, carbon black produced from the pyrolysis of waste tires has been used as the raw material in the production of activated carbons with various operating parameters at high temperature and in an anaerobic environment. The virgin and sulfurized activated carbons can be further applied to adsorb HgCl2 in the flue gas emitted from MSW incinerators.
The adsorptive capacities of organic substances and heavy metals with activated carbons tend to decrease with the adsorption temperature. However, adding certain chemicals to activated carbons can change the surface characteristics of activated carbons, which can enhance the adsorptive capacity of specific air pollutants (CitationCarey et al., 1998). Previous studies have shown that sulfur-impregnated activated carbons can be used to remove elemental mercury (Hg0) from coal-fired power plants and MSW incinerators. The reagent most used for sulfur modification of activated carbon is sodium sulfide (Na2S) (CitationGalbreath and Zygarlicke, 2000; CitationLin et al., 2008). However, the major species of gaseous mercury contaminants emitted from MSW incinerators are oxidized mercury in which HgCl2 accounts for 60–65% of total mercury pollutants (CitationBrown et al., 1999; CitationYuan et al., 2004). Unfortunately, the adsorption of HgCl2 with sulfur-impregnated activated carbons has seldom been investigated in regard to the variation of HgCl2 adsorption with a specific surface area and pore-size distribution of the activated carbons during the HgCl2 adsorption process (CitationChen et al., 2007). Previous investigations have reported that sulfur molecules diffused into the inner pores of activated carbons at high temperatures conductively enhanced the chemisorption of activated carbons, hence, the adsorptive capacity of mercury, although sulfur may plug the inner micropores and thus reduce the specific surface area of the activated carbons (CitationIoannidou and Zabaniotou, 2007).
Furthermore, most studies conducted for the adsorption of heavy metals commonly utilized adsorption columns, with only a few using thermogravimetric analysis (TGA). TGA has significant advantages in its continuous recording of the weight variations of the activated carbons and the drawing of their adsorption curves (CitationSalvador et al., 2005). In this work, TGA was applied to replace the adsorption column experiments for the removal of gas-phase HgCl2 with sulfur-impregnated activated carbons derived from waste tires. The effects of pore structure and surface characteristics on sulfur-impregnated activated carbons have also been investigated. An innovative aspect of the present study is that the pyrolysis of waste tires and the sulfur modification of activated carbons were successfully developed under several conditions. It is hoped that the results obtained from this study will provide a more realistic approach for the adsorption process, as well as more useful information on feasible applications. Since waste tires are made of rubber and negatively impact the environment, their reuse for producing activated carbons would be rewarding. Some of the obtained activated carbons, such as those derived from waste tires with an activation of 4 hr at 900 °C, demonstrated similar BET (Brunauer-Emmett-Teller isotherm) surface areas and HgCl2 adsorptive capacity to those of commercial products (usually more than 700 m2/g) (CitationSkodras et al., 2007). Thus, the application of sulfur-impregnated activated carbons could be considered as a potential solution for reducing the hazards of HgCl2.
Materials and Methods
Sample preparation and characterization
Activated carbons used in this study included three kinds of surface area (high, medium, and low) and all were produced from waste tires with different water injection rates and activation times (). Nitrogen was used as the protective gas to create an anaerobic or anoxic condition for the pyrolysis of waste tires, with a nitrogen flow rate of 0.5 L/min. First, waste tires were scissored into fragments of approximately 0.5–1.0 cm, and then cleaned and dried in a drying cabinet. Next, several pieces of the waste tires, with a total mass of about 20 g, were placed in a crucible and then into a high-temperature furnace for pyrolysis at a set temperature by adjusting various water injection rates to prepare activated carbons with different specific surface areas.
Table 1. Activated carbons produced from waste tires under different pyrolysis, activation, and sulfurization conditions
The conventional method for the sulfur modification of activated carbons uses aqueous sodium sulfide (Na2S) impregnation. However, this study utilized vapor-phase elemental sulfur (S0)-containing gas stream to modify activated carbons at high temperatures. The virgin activated carbons (about 1 g) derived from the waste tires was granulated and uniformly mixed with elemental sulfur (about 3 g). The mixture was then heated in a sulfur modification reactor at 400 or 650 °C for 3 hr by passing nitrogen gas at 100 mL/min. The capabilities of the elemental sulfur diffusing into the mesopores and macropores of the activated carbons were significantly different at temperatures of 400 and 650 °C, resulting in a clear dissimilarity in the sulfur content of the activated carbons. Moreover, some studies have reported a mass ratio of carbon and sulfur of 1:4 (CitationHladíková et al., 2001); however, the aforementioned research showed that the adsorptive capacity of sulfur-impregnated activated carbons produced at the carbon-to-sulfur mass ratio of 1:3 was superior to 1:0.5, 1:1, 1:2, and 1:4 (CitationLin et al., 2006). Thus, the experiments conducted in this study used sulfur-impregnated activated carbons produced at the carbon-to-sulfur mass ratio of 1:3.
In this work, the physical characteristics of various activated carbons, including the BET surface area, pore volume, and the average pore radius, were analyzed with a BET surface analyzer (Model ASAP 2000; Micrometritics Instrument Corporation). The sulfur content of the activated carbons was measured with an elemental analyzer (Model EA 1108; Fisons). In addition, the physical and chemical characteristics of the activated carbons were analyzed by an environmental scanning electron microscopy (ESEM) with an energy dispersal spectrum (EDS).
Bench-scale HgCl2 adsorption tests
The schematic diagram of a bench-scale HgCl2 adsorption unit is shown in . First, activated carbon samples (about 30 mg) were placed on the scale of a TGA (Mettler Toledoto, model TGA/SDTA 851e) and nitrogen gas was added at about 10 mL/min for 24 hr to avoid the spoiler phenomenon and ensure the stability of the experimental system. The TGA measurement was as precise as 10−6 g. At the startup of the HgCl2 adsorption experiments, nitrogen gas was mixed with HgCl2 generated from an HgCl2 permeation tube (VICI Metronics; xx, xx) by adjusting the temperature and carrier gas flow rate. The operating parameters investigated included the inlet HgCl2 concentrations of 100, 300, and 500 μg/m3, with an adsorption time of 3 hr and an adsorption temperature of 150 °C, which simulated the condition of flue gas emitted from MSW incinerators. Then, the adsorptive capacity of HgCl2 was investigated with the BET surface area and the sulfur content of the sulfur-impregnated activated carbons.
Results and Discussion
Pore structure characteristics of activated carbons
Sulfur-impregnated activated carbons are composed of a large number of micropores, and a high sulfur content enhances the adsorptive capacity of HgCl2 by activated carbons (CitationOllero et al., 2002). Micropores usually possess the majority of active sites for HgCl2 adsorption, whereas macropores and mesopores act as transportation routes (CitationWu et al., 2006). illustrates the ESEM images of sulfur-impregnated activated carbons with magnification of 5000, 10,000, and 20,000, respectively. As shown in , macropores larger than 500 Å were found mainly on the surface of the activated carbons, with mesopores and micropores hiding inside the activated carbons. Sulfur molecules can diffuse and deposit on the micropores of activated carbons after sulfur impregnation, and possibly plug the transitional paths.
summarizes the physical properties of activated carbons, including BET surface area (S BET), micropore surface area (S micro), total pore volume (V total), and micropore volume (V micro). The BET surface areas of three virgin activated carbons derived from waste tires were 713 (NH), 534 (NM), and 242 (NL) m2/g, respectively. After sulfur modification at 400 and 650 °C, the BET surface areas of the activated carbons were reduced to 645 (H-400S), 415 (M-400S), and 201 (L-400S) m2/g and 673 (H-650S), 430 (M-650S), and 217 (L-650S) m2/g, respectively. The aforementioned surface area data showed that the sulfur modification process could reduce the BET surface area of activated carbons. The higher the sulfur content of the activated carbons, the lower the BET surface area. The surface area of micropores accounted for 10.0–59.7% of BET surface areas. The micropore surface areas of sulfur-impregnated activated carbons were 166 (H-400S), 168 (M-400S), and 120 (L-400S) m2/g at 400 °C, which decreased little. The micropore surface areas of the sulfur-impregnated activated carbons were 79 (H-650S), 43 (M-650S), and 59 (L-650S) m2/g at 650 °C, which decreased dramatically. In summary, the activated carbons with a high surface area had abundant mesopores and micropores after sulfur modification, whereas the activated carbons with low surface area were dominated by macropores and mesopores after sulfur modification.
Table 2. Pore structure characteristics of virgin and sulfur-impregnated activated carbons
illustrates the pore-size distribution of activated carbons with a high surface area (NH, H-400S, and H-605S) modified by elemental sulfur at temperatures of 400 and 650 °C. The elemental sulfur was initially gasified and mainly composed of chain sulfur molecules at a temperature of 400 °C, which diffused with relative ease into the mesopores and macropores of activated carbons. Correspondingly, the elemental sulfur was completely gasified and mostly composed of ring sulfur molecules at the temperature of 650 °C, which was relatively difficult to diffuse into the mesopores and macropores of activated carbons (CitationFlora et al., 1998; CitationSandra and Roberto, 1999). The sulfur molecules partially blocked the mesopores and macropores acting as passages to micropores. Consequently, the BET surface area of transitional pores decreased slightly, whereas the BET surface area of micropores decreased significantly after sulfur modification of the activated carbons. In addition to different sulfur molecule shapes at 400 and 650 °C, the amount of sulfur adsorbed on the surfaces of the mesopores and macropores in the activated carbons caused significant reduction of micropore surface area at 650 °C, compared with that at 400 °C. As HgCl2molecules passed through the main paths of macropores and mesopores into micropores, the amount of macropores and mesopores highly influenced the adsorption of HgCl2 by the activated carbons.
Surface chemistry characteristics of activated carbons
The sulfur contents of the activated carbons before and after sulfur modification, measured with an elemental analyzer (EA), are shown in . It was found that the sulfur-impregnation process at temperatures of 400 and 650 °C clearly increased the sulfur content of the activated carbons from 2% to 10% and 6%, respectively. The higher the temperature of sulfur modification, the lower the sulfur content of the activated carbons.
Table 3. Sulfur contents of virgin and sulfur-impregnated activated carbons
illustrates the chemical composition of the activated carbons after sulfur modification, as measured with an energy dispersive spectrometer (EDS). It was evident that sulfur crystals existed on the surface of the sulfur-impregnated activated carbons whether the magnification was 5000, 10,000, or 20,000. The sulfur content of 10.9% measured with the EDS was close to that of 11.1% measured with an EA, suggesting that the sulfur was evenly distributed both on the outside surface and in the inner pores of the activated carbons. In addition, sodium and silicon were also found to exist in the activated carbons. As sodium sulfide is added in the tire manufacturing process (CitationXiong et al., 2003), only a few sodium elements were attached on the surface of the activated carbons. Furthermore, some silicon residue was found on the activated carbons from the use of quartz asbestos during the sulfur modification process.
Mercuric chloride adsorption results
illustrates the adsorption of HgCl2 by activated carbons with a high surface area. The saturated adsorptive capacity of HgCl2 for virgin activated carbons (only about 0.07 mg/g) was achieved in a short time of 7 min. The HgCl2 adsorption curves for high-sulfur activated carbons impregnated at 400 °C with the inlet HgCl2 concentration are illustrated in . The results indicated that the saturated adsorptive capacities of HgCl2 were 1.557 (H-400S), 1.165 (M-400S), and 0.950 (L-400S) mg/g for the inlet HgCl2 concentration of 500 μg/m3; 1.132 (H-400S), 0.992 (M-400S), and 0.752 (L-400S) mg/g for the inlet HgCl2 concentration of 300 μg/m3; and 0.848 (H-400S), 0.686 (M-400S), and 0.558 (L-400S) mg/g for the inlet HgCl2 concentration of 100 μg/m3, respectively.
Figure 5. HgCl2 adsorption curve of virgin activated carbons derived from waste tires at the inlet HgCl2 concentration of 500 μg/m3.
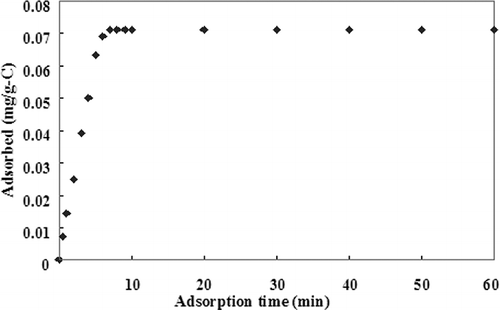
Figure 6. HgCl2 adsorption curves of activated carbons sulfur-impregnated at 400 °C with the inlet HgCl2 concentration of (a) 500, (b) 300, and (c) 100 μg/m3.
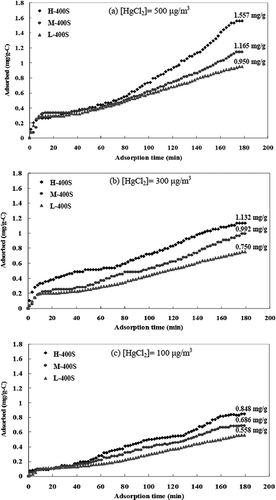
The sulfur modification process efficiently raised the saturated adsorptive capacity of HgCl2, with activated carbons with a high surface area reaching 1.557 mg/g (approximately 22 times higher than virgin activated carbons); even those with a low surface area reached 0.950 mg/g (more than 13 times higher than virgin activated carbons). Moreover, at the same inlet HgCl2 concentration, the saturated adsorptive capacity of HgCl2 by sulfur-impregnated activated carbons increased with the activated carbons' surface area, which was similar to the physical adsorption trend mentioned in the literature (CitationGonzález et al., 2006). Therefore, the BET surface area of sulfur-impregnated activated carbons played an important role in the saturated adsorptive capacity of HgCl2.
HgCl2 adsorption curves can be divided into two adsorption stages. The adsorptive capacity of HgCl2 by virgin activated carbons commonly achieves its saturation status in less than 10 min. Consequently, it was worthwhile comparing the adsorption rates of HgCl2 for time intervals of <10 and 10–60 min. At the first adsorption stage (within 10 min), the HgCl2 adsorption rate rose quickly and steadily regardless of the inlet HgCl2 concentration, since HgCl2 molecules could diffuse into macropores and mesopores due to physical adsorption. At the second adsorption stage (after 10 min), the adsorption of HgCl2 became slower, since HgCl2 molecules gradually diffused into mesopores and micropores. Furthermore, the adsorptive capacity of HgCl2 by sulfur-impregnated activated carbons with a high surface area was much higher than that for medium or low surface area, since the activated carbons with a high surface area had abundant mesopores and micropores, and contained more sulfur in the transitional pores. The lower inlet HgCl2 concentration, the lower amount of HgCl2 molecules diffused into micropores and the lower HgCl2 adsorption gaps between different activated carbons. Thus, the BET surface area of activated carbons slightly affected the adsorption of HgCl2 at a low inlet HgCl2 concentration. In addition, the adsorptive capacity of HgCl2 by activated carbons increased with the inlet HgCl2 concentration due to the increase of driving force of molecular diffusion. At the same adsorption temperature, the increase of the inlet HgCl2 concentration enhanced the HgCl2 diffusion rate and shortened the saturated adsorption time (CitationWu et al., 2006), which allowed HgCl2 molecules to easily enter into the inner micropores of activated carbons and, thus, increase the adsorptive capacity of HgCl2.
illustrates the HgCl2 adsorption curves for low-sulfur activated carbons impregnated at 650 °C with various inlet HgCl2 concentrations. At the inlet HgCl2 concentration of 500 μg/m3, the saturated adsorptive capacities of HgCl2 were 0.971 (H-650S), 0.895 (M-650S), and 0.774 (L-650S) mg/g, respectively; at the inlet HgCl2 concentration of 300 μg/m3, the saturated adsorptive capacities of HgCl2 were 0.829 (H-650S), 0.750 (M-650S), and 0.670 (L-650S) mg/g, respectively; and at the inlet HgCl2 concentration of 100 μg/m3, the HgCl2 saturated adsorption capacities were 0.687 (H-650S), 0.605 (M-650S), and 0.523 (L-650S) mg/g, respectively. Compared with high-sulfur activated carbons, there was a significant decrease of the saturated adsorptive capacity of HgCl2 by activated carbons for different inlet HgCl2 concentrations, which demonstrated that the sulfur content of the activated carbons played an important role in the saturated adsorptive capacity of HgCl2. Moreover, as with high-sulfur-content activated carbons, the saturated adsorptive capacity of HgCl2 increased with the surface area of the activated carbons, and HgCl2 was also adsorbed by two adsorption stages with a turning point at 10 min.
Figure 7. HgCl2 adsorption curves of activated carbons sulfur-impregnated at 650 °C with the inlet HgCl2 concentration of (a) 500, (b) 300, and (c) 100 μg/m3.
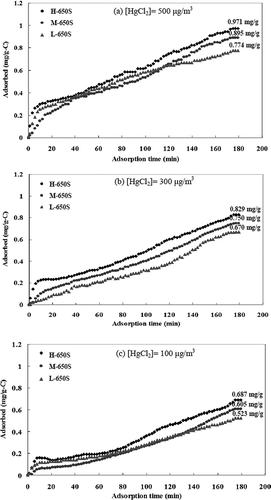
The control technology of powdered activated carbon injection followed by fabric filtration is commonly used to remove HgCl2 from MSW incinerators. Powdered activated carbon injection into the ducts requires a very short time and the residence time of powdered activated carbons collected in the fabric filter is about 1 hr (CitationPavlish et al., 2003). Accordingly, this present work only studied the adsorption rate of HgCl2 for activated carbons with a high surface area. shows that the adsorption rates of HgCl2 by sulfur-impregnated activated carbons (H-400S and H-650S) within 10 min were in the range of 0.0089–0.0299 μg/g·min, and that the adsorption rates of HgCl2 increased with the inlet HgCl2 concentration. However, the adsorption rates of HgCl2 by low-sulfur activated carbons were higher than those by high-sulfur activated carbons, since low-sulfur activated carbons had abundant macropores and mesopores. Furthermore, the HgCl2 adsorption rates of activated carbons (H-400S and H-650S) for between 10 and 60 min were in the range of 0.0007–0.0041 μg/g·min, which was obviously lower than those in the first stage. This result indicated that there was no penetration of HgCl2 within 1 hr when powdered activated carbons remained in the fabric filter, and that high-sulfur activated carbons possessed the highest saturated adsorptive capacity of HgCl2. The results indicated that the sulfur-impregnated activated carbons had relatively high absorption rates within 60 min as compared with the virgin activated carbon. Consequently, the feasibility of applying sulfur-impregnated activated carbons derived from waste tires to remove HgCl2 from MSW incinerators was confirmed.
Table 4. HgCl2 adsorption rates of sulfur-impregnated activated carbons
Conclusions
Activated carbons derived from waste tires demonstrate similar surface areas to commercial tires, and sulfur modification of activated carbons efficiently enhanced the saturated adsorptive capacity of HgCl2. The sulfur-impregnated activated carbon with a high surface area achieved a maximum adsorptive capacity up to 1.557 mg/g (approximately 22 times higher than for virgin activated carbons). The saturated adsorptive capacity of HgCl2 by sulfur-impregnated activated carbons at 400 °C was obviously higher than that at 650 °C due to the chemisorption of HgCl2 by the sulfur-impregnated activated carbons. Additionally, the sulfur content of activated carbons at 400 and 650 °C obviously increased from 2% to 10% and 6%, respectively.
The HgCl2 adsorption curves were divided into two adsorption stages. In the first stage (within 10 min), the HgCl2 adsorption rate increased dramatically regardless of the inlet HgCl2concentration, since the HgCl2 molecules entered into the macropores and mesopores due to physical adsorption. As a result, the HgCl2 adsorption rates for low-sulfur activated carbons were higher than those for high-sulfur activated carbons, since low-sulfur activated carbons had abundant macropores and mesopores. The HgCl2 adsorption rates of activated carbons were in the range of 0.0089–0.0299 μg/g·min. In the second stage (after 10 min), the HgCl2 adsorption rate became lower, since HgCl2 molecules gradually diffused into mesopores and micropores. The HgCl2 adsorption rates of activated carbons were in the range of 0.0007-0.0041 μg/g·min, which was obviously lower than those in the first stage. However, there was no penetration of HgCl2 within the whole process. Thus, the feasibility of applying sulfur-impregnated activated carbons derived from waste tires to remove HgCl2 from MSW incinerators was confirmed.
Acknowledgments
This study was partially supported by National Science Council of Republic of China (NSC-96-2221-E-110-017-MY2) and the National Natural Science Foundation of the People's Republic of China (grant no. 51008106). The authors would like to express their sincere appreciation for the financial support to accomplish this study. The authors thank especially Mr. Iau-Ren Ie, Mr. Yi-Hsiu Jen, Mr. Hsieh-Hung Tsai, and Mr. Sheng-Han Xue from the Institute of Environmental Engineering, National Sun Yat-sen University, for their assistance in chemical analyses.
References
- Ames , M. , Gullu , G. and Olmez , I. 1998 . Atmospheric mercury in the vapor phase, and in fine and coarse particulate matter at Perch River. New York . Atmos. Environ. , 32 : 865 – 872 .
- Barbooti , M.M. , Hassen , E.B. and Issa , N.A. 1989 . Thermogravemetric and pyrolytic investigation of scrap tires . J. Petro. Res. , 8 : 229 – 242 .
- Biswas , P. and Wu , C.Y. 1998 . Control of toxic metal emissions from combustors using sorbents: A review . J. Air Waste Manage. Assoc , 48 : 113 – 127 .
- Brown , T.D. , Smith , D.N. , Hargis , R.A. Jr. and O'Dowd , W.J. 1999 . Mercury measurement and its control: What we know, have learned, and need to further investigate . J. Air Waste Manage. Assoc , 49 : 628 – 640 .
- Cannon , F.S. , Dusenbury , J.S. , Paulsen , J. , Sigh , D.W. and Maurer , D.J. 1996 . Advanced oxidant regeneration of granular activated carbon for controlling air-phase VOCs . Ozone Sci. Eng. , 18 : 417 – 441 .
- Carey , T.R. , Hargrove , O.W. Jr. and Richardson , C.F. 1998 . Factors affecting mercury control in utility flue gas using activated carbon . J. Air Waste Manage. Assoc , 48 : 1166 – 1174 .
- Chen , W.C. , Lin , H.Y. , Yuan , C.S. and Hung , C.H. 2009 . Kinetic modeling on the adsorption of mercury chloride vapor on spherical activated carbon by thermogravimetric analysis . J. Air Waste Manage. Assoc , 59 : 227 – 235 . doi: 10.3155/1047-3289.59.2.227
- Chen , W.C. , Syue , S.H. , Lin , H.Y. and Yuan , C.S. Desorption of mercuric chloride from spent powdered activated carbons via thermogravimetric analysis . Proceedings of the 14th IUAPPA World Congress . September 9–13 2007 . pp. 1414 – 1417 . Brisbane , , Australia
- Fan , M. and Brown , R.C. 2001 . Comparison of the loss-on-ignition and thermogravimetric analysis techniques in measuring unburned carbon in coal fly ash . Energy Fuels , 15 : 1414 – 1417 .
- Flora , J.R.V. , Vidic , R.D. , Liu , W. and Thurnau , R.C. 1998 . Modeling powdered activated carbon injection for the uptake of elemental mercury vapors . J. Air Waste Manage. Assoc , 48 : 1051 – 1059 .
- Galbreath , K.C. and Zygarlicke , C.J. 2000 . Mercury transformations in coal combustion flue gas . Fuel Proc. Technol. , 65 : 289 – 310 .
- González , J.F. , Encinar , J.M. , González-García , C.M. , Sabio , E. , Ramiro , A. , Canito , J.L. and Gañán , J. 2006 . Preparation of activated carbons from used tyres by gasification with steam and carbon dioxide . Appl. Surf. Sci. , 252 : 5999 – 6004 .
- Hladíková , V. , Petrík , J. , Jursa , S. , Ursínyová , M. and Kočan , A. 2001 . Atmospheric mercury levels in the Slovak Republic . Chemosphere , 45 : 801 – 806 .
- Hsi , H.C. , Rood , M.J. , Rostam-Abadi , M. , Chen , S. and Chang , R. 2001 . Effects of sulfur impregnation temperature on the properties and mercury adsorption capacities of activated carbon fibers . Environ. Sci. Technol. , 35 : 2785 – 2791 .
- Ioannidou , O. and Zabaniotou , A. 2007 . Agricultural residues as precursors for activated carbon production—A review . Renew. Sustain. Energy Rev. , 11 : 1966 – 2005 .
- Krishnan , A.K. and Anirudhan , T.S. 2002 . Uptake of heavy metals in batch systems by sulfurized steam activated carbon prepared from sugarcane bagasse pith . Ind. Eng. Chem. Res. , 41 : 5085 – 5093 .
- Lin , H.Y. , Yuan , C.S. and Hung , C.H. 2008 . Surface functional characteristics (C, O, S) of carbon black before and after steam activation . J. Air Waste Manage. Assoc , 58 : 78 – 84 .
- Lin , H.Y. , Yuan , C.S. , Wu , C.H. and Hung , C.H. 2006 . The adsorptive capacity of vapor-phase mercury chloride onto powdered activated carbon derived from waste tires . J. Air Waste Manage. Assoc , 56 : 1558 – 1566 .
- Ollero , P. , Serrera , A. , Arjona , R. and Alcantarilla , S. 2002 . Diffusional effects in TGA gasification experiments for kinetic determination . Fuel , 81 : 1989 – 2000 .
- Pavlish , J.H. , Sondreal , E.A. , Mann , M.D. , Olson , E.S. , Galbreath , K.C. , Laudal , D.L. and Benson , S.A. 2003 . Status review of mercury control options for coal-fired power plants . Fuel Proc. Technol. , 82 : 89 – 165 .
- Salvador , F. , ánchez-Montero , M.J. S , Salvador , A. and Martín , M.J. 2005 . Study of the energetic heterogeneity of the adsorption of phenol onto activated carbons by TPD under supercritical conditions . Appl. Surf. Sci. , 252 : 641 – 646 .
- Sandra , V. and Roberto , P. 1999 . Deposition of sulfur from H2S on porous adsorbents and effect on their mercury adsorption capacity . Geothermics. , 28 : 341 – 354 .
- Skodras , G. , Diamantopoulou , Ir. , Zabaniotou , A. , Stavropoulos , G. and Sakellaropoulos , G.P. 2007 . Enhanced mercury adsorption in activated carbons from biomass materials and waste tires . Fuel Proc. Technol. , 88 : 749 – 758 .
- Wu , S. , Uddin , M.A. and Sasaoka , E. 2006 . Characteristics of the removal of mercury vapor in coal derived flue gas over iron oxide sorbents . Fuel , 85 : 213 – 218 .
- Xiong , Y.H. , Jiang , T. and Zou , X. 2003 . Automatic proximate analyzer of coal based on isothermal thermogravimetric analysis (TGA) with twin-furnace . Thermochim. Acta , 8 : 97 – 101 .
- Yuan , C.S. , Lin , H.Y. , Wu , C.H. and Liu , M.H. 2004 . Preparing of sulfurized powdered activated carbon from waste tires using an innovative compositive impregnation process . J. Air Waste Manage. Assoc , 54 : 862 – 870 .