Abstract
Stone processing sludge (SPS) is a by-product of stone-processing wastewater treatment; it is suitable for use as a raw material for making artificial lightweight aggregates (ALWAs). In this study, boric acid was utilized as a flux to lower sintering temperature. The formation of the viscous glassy phase was observed by DTA curve and changes in XRD patterns. Experiments were conducted to find the optimal combination of sintering temperature, sintering time, and boric acid dosage to produce an ALWA of favorable characteristics in terms of water absorption, bulk density, apparent porosity, compressive strength and weight loss to satisfy Taiwan's regulatory requirements for construction and insulation materials. Optimal results gave a sintering temperature of 850 °C for 15 min at a boric acid dosage of 15 % by weight of SPS. Results for ALWA favorable characteristics were: 0.21 % (water absorption), 0.35 %(apparent porosity), 1.67 g/cm3 (bulk density), 66.94 MPa (compressive strength), and less than 0.1% (weight loss).
Artificial lightweight aggregates (ALWAs) can be produced from stone processing sludge. A cost-effective, efficient production procedure is possible after fluxing with boric acid and sintering at 850°C for 15 min. At this temperature, the physical properties of the lightweight aggregate meet Taiwan's regulatory standards for construction or heat insulation material.
Introduction
Stone processing is a major industry in eastern Taiwan. Processing includes cutting, carving, and polishing of granite, marble, or serpentine. Great amounts of water and lime are used for cooling saws. The sludge derived is termed stone processing sludge (SPS) and is made up of approximately 25% stone (CitationChang et al., 2010). According to the Industrial Waste Control Center in Taiwan, 52,008 tons of such sludge was produced in 2010. Typically, sludge disposal involves transferring the sludge to make it suitable as cement filler for use in construction.
Artificial lightweight aggregate (ALWA) production is a suitable alternative method of SPS recycling. ALWAs can be used as replacements for natural granular materials, and typically have a bulk density of less than 2.0 g/cm3 (CitationGonzález-Corrochano et al., 2009). ALWAs have the capacity to decrease loading on building structures and provide thermal insulation (CitationCheeseman and Virdi, 2005). However, despite these advantages, the manufacture of ALWAs can be prohibitive because of the large energy budget needed to produce them. Previous studies have revealed sintering temperatures of higher than 1000°C being necessary to create bloating within aggregates. This favorable characteristic reduces bulk density. CitationTay et al. (2003) used industrial sludge and marine clay to produce aggregates at a sintering temperature of 1135°C. CitationMun (2007) used sewage sludge as a raw material, and samples were sintered at 1050°C to 1150°C. CitationChen et al. (2010) incorporated fly ash derived from municipal solid waste (MSW) incineration with reservoir sediment, and the mixtures were sintered at 1100 to 1200°C. CitationFakhfakh et al. (2007) used smectite-rich marlstone to manufacture ALWAs with samples preheated at 600 to 800°C for 2 hr before sintering at 1180°C. CitationKourti et al. (2010) studied the effect of glass dosage on processing, physical properties, and the microstructure of lightweight aggregates made from the fly ash of lignite coal. The mixture was rapidly sintered at temperatures between 1040 and 1120°C in a rotary furnace. The physical properties of the aggregates produced from the studies just described varied widely. In summary, water absorption was between 1% and 47%, particle density from 0.7 g/cm3 to 2.15 g/cm3, and compressive strength between 0.5 MPa and 8 MPa. In general, favorable ALWA characteristics such as lower water absorption, lower bulk density, and higher compressive strength were obtained if a sufficient sintering temperature was applied.
CitationRiley (1951) has shown that the lightweight properties of ALWAs are due to clays bloating during sintering. The two major bloating parameters governing bloating are (1) materials producing an adhesive glassy phase to trap gases, and (2) substances being present that can produce gases while the glass phase forms. Fluxes are a means of reducing sintering temperature to achieve bloating at lower temperatures. In ceramic processes, boric agents are commonly used as fluxes to reduce sintering temperatures. For example, in steatite ceramics production, boron oxide lowers the densification temperature (CitationSoykan, 2007). In anorthite ceramics, the single anorthite phase is achievable at 950°C when boron oxide is used; however, the single anorthite phase is not observed in boron-free samples even at a sintering temperature of 1100°C (Mergen and Aslanoğlu, 2007). In other cases where borax has been used as a fluxing agent, sintering temperatures have been reduced from 1500°C (borax-free samples) to 1200°C (borax flux samples) (CitationYang et al., 2009). In this study, boric acid is chosen as the fluxing agent in the sintering of ALWA because it is cheaper than boron trioxide and boron trioxide can be formed by dehydration of boric acid. The dehydration of boric acid is shown in Equationeqs 1 and Equation2 (CitationKocakuşak et al., 1996):
Accordingly, it is expected that boron trioxide can lower the formation temperature of the adhesive glassy phase as well as the sintering temperature of the manufactured ALWAs. The glassy phase should seal the outer surface pores trapping pockets of gas within the aggregate's structure during sintering. The physical property tests show that the manufactured ALWAs are suitable for use as construction or heat insulation materials.
Materials and Methods
Analysis of stone processing sludge (SPS) characteristics
The sludge utilized in this study is from a wastewater treatment system of a stone processing factory in eastern Taiwan. The sludge sample was dried at 110°C, and its characteristics were analyzed by atomic absorption spectrometry, ignition loss, and x-ray diffraction.
Accordingly, a 0.2-g sample mixed with 16 mL aqua regia and 8 mL hydrofluoric acid was heated at 180°C for 3 hr for chemical analysis of SPS. The filtrate was diluted and analyzed by atomic absorption spectroscopy (AAS). For ignition loss testing, the SPS was ground until the particle size was less than 1 mm. Five grams (W1) of SPS were heated at 800°C for 3 hr. The weight (W2) of the residue was recorded while the sample was cooled. The results of ignition loss were calculated according to Equationeq 3:
Chemical analysis
Chemical analysis was carried out with Varian atomic spectroscopy, AA240. The powdered sample was mixed with 16 mL aqua regia and 8 mL hydrofluoric acid before heating at 180°C for 3 hr. The resultant solution was cooled, filtered, and diluted. The concentrations of elements including Si, Fe, Al, K, Ca, Na, and Mg were then determined.
Experimental procedures for ALWA formation
SPS was mixed with boric acid to control the weight ratio of boric acid versus sludge from 0 to 15%. The mixtures were rolled on a ball mill for 4 hr. Each homogeneous mixture was shaped in a mold at 3.5 MPa for 1.5 min; then the shaped sample (cylindrical with a 2-cm diameter) was sintered from 800 to 900°C with times being maintained from 5 to 60 min. After sintering, the synthetic aggregates were tested for water absorption, bulk density, apparent porosity, compressive strength, and weight loss (after rinsing with Na2SO4 solution) to determine optimal synthesis parameters.
Analysis of ALWAs' characteristics
Water absorption testing
This testing was done according to Chinese National Standard (CNS) code 488 of Taiwan. The ALWA was weighed (W3), and then soaked for 24 hr. After soaking, the surface of the synthetic aggregate was dried with a clean cloth, and its weight (W4) was recorded. The water absorption data were from Equationeq 4.
Bulk density testing
The ALWA was weighed in water, and the weight (W5) was read. The volume and bulk density were calculated with Equationeqs 5 and Equation6:
Apparent porosity testing
This testing was done according to Chinese National Standard (CNS) code 619 of Taiwan. The value of the apparent porosity of ALWA was calculated by Equationeq 7:
Compressive strength testing
ALWA was tested by a single-axis compression instrument, and the value was calculated from Equationeq 8:
Weight loss after rinsing with Na2SO4 solution
The testing procedure is described in Chinese National Standard (CNS) code 3618, and the results are used to assess weight loss from ALWAs. The aggregate sample was weighed (W3) and put into a saturated solution of sodium sulfate for 16 hr at room temperature. Then the sample was dried at 105°C until the sample weight was constant. The regimen mentioned above was repeated 5 times, and the sample cleaned with distilled water of 43 ± 6°C after the final drying. The filtrate was examined with a solution of barium chloride to ensure that the sodium sulfate was removed completely. The sample was then dried again to constant weight and recorded (W6). Weight loss was calculated from Equationeq 9:
X-ray diffraction (XRD) analysis
An x-ray diffractometer (XRD, Rigaku) was used to examine and scan the crystalline phases of SPS and ALWAs from 10° to 80° (2θ) at a scan rate of 4 degrees per minute with voltage and current at 30 kV and 50 mA, respectively.
Differential thermal analysis (DTA)
Differential thermal analysis (DTA) was carried out with TeckMax TG/DTA 6300. SPS was mixed with different doses (7.5%, 15%, and 20%) of boric acid and loaded into an Al2O3 ceramic crucible for each test. All samples were tested under 100 mL/min of airflow. Different heating rates were adopted: the first was heating from 30°C to 1000°C at 5°C per minute and the other was heating from 600°C to 900°C at 2.5°C per minute.
Scanning electron microscope (SEM) analysis
A (JEOL, JSM6360) high-resolution scanning electron microscope (SEM) was used to observe surface and cross-section morphology of the sample. The size of the specimen was about 0.2 × 0.2 cm2 and was sprinkled for gilding in platinum by vacuum deposition.
Results and Discussion
Characteristics analysis of SPS
The SPS used in these experiments was a by-product of wastewater treatment during stone processing at factories in eastern Taiwan. The major elements of the SPS were Si, Fe, Al, K, Ca, Na, and Mg (see ). Si, Al, K, Na, and Mg came from the offcuts of raw stone, while Fe probably came from the diamond-edged saw blades. After testing, ignition loss of SPS was 2.88. This was probably due to the existence of a polymer used in wastewater treatment. From , the major phases of SPS were SiO2, (Na,Ca)(Si,Al)4O8, and KAlSi3O8. The results of chemical analysis should be helpful in explaining why the major minerals were quartz and aluminosilicate.
Table 1. Chemical analysis and loss on ignition (LOI) of SPS
Effect of boric acid in ALWA production
In a metallic or ceramic system, a eutectic system commonly forms in which a mixture of chemical compounds or elements has a specific chemical composition that solidifies at lower temperatures than other products composed of the same ingredients. The critical temperature for solidification or melting is called the eutectic point. In ceramic fabrication, a low-melting-point ingredient is usually added to the matrix as flux to lower the melting point. The glass transition temperature also decreases in accordance with the new melting point. During sintering, boric acid dehydrates to boron trioxide. It has a low melting point (450°C) and melts early the sintering process. Correspondingly, it has been found that increased addition of boric acid as flux reduces the melting point of sintered compunds and the temperature at which glass transition occurs. ALWAs of varying characteristics were sintered using SPS mixed with different dosages of boric acid in this study. The ALWAs were then analyzed using differential thermal analysis (DTA) curves, SEM and XRD techniques. The formation of a viscous glassy phase at the surface of the ALWA is essential for reducing water absorption, apparent porosity, and bulk density. In this study, it was found boric acid promotes glassy phase formation. When boric acid dosage increased from 0 wt% to 20 wt%, the values of water absorption decreased from 27.6% to 0.43% and apparent porosity and bulk density changed from 45.7% to 0.65% and 2.17 g/cm3 to 1.0 g/cm3, respectively (see ). High boric acid usage at 20 wt% of sludge resulted in bulk melting, and a loss of shape among ALWAs formed. However, SEM analysis of ALWA cross-sections showed that dosing at 15 wt% boric acid produces ALWAs with spherical inner pores containing trapped gases (). On the other hand, there was relatively low formation of the glassy phase for the 7.5 wt% flux dosage sample and gasses escaped before the surface pores sealed. This left an irregular distribution of small pores inside the aggregates. The formation of the viscous glass phase could also be observed at the glass transition region on the DTA curve and altered XRD pattern of SPS. The results of DTA are shown in . In , different boric acid dosage of samples were tested from 30 to 1000°C (at a heating rate of 5°C per minute) to find the glass transition region. It is evident that the transition region is between 600 and 800°C. To restrain the transition region more precisely a heating rate of 2.5°C per minute over a narrower temperature band (600 to 900°C) was chosen. The results are shown in . The drop in height of the DTA curve with temperature for glass transition relates to boric acid dosing. The results indicated that higher boric acid dosing promoted the formation of the glass phase and made the glass transition region more apparent. XRD analysis also gave evidence of the glass-phase formation. If the amorphous glassy phase occurred, the intensity of the XRD peak for the mineral phase (SiO2 or feldspar) of SPS should decline. In , the XRD results of ALWA-surface structures derived from different boric acid dosages were tested and compared with the original SPS. The results showed that the intensity of SiO2 of ALWA samples was much lower than that of SPS and the XRD peak for feldspar disappeared. In ceramic sintering, feldspar is considered a flux for improving sintering reactions. CitationMedvedovski (2001) mentioned melting of feldspar promoting the liquid phase in liquid-phase sintering. CitationAlves et al. (2012) mentioned porcelain tile staining being caused by the presence of pores, and these pores could be eliminated during sintering through liquid-phase sintering. Feldspar is the most important raw material available for promoting the liquid phase during sintering. CitationDas et al. (2003) mentioned feldspar reacting with silica and the formation of eutectic system in the temperature range of 950–1000°C for a clay–quartz–feldspar system. In our experiments, feldspar within the SPS also melted to help form the viscous glassy phase. Its peak is not evident in the final XRD pattern. In the sintering process, the crystallinity of ALWAs' surfaces declined and the amorphous glassy phase formed so that open pores at the surface were sealed, improving ALWA characteristics of low water absorption and apparent porosity. The results of DTA and XRD indicate that boric acid addition can promote glass-phase formation and improve the physical characteristics of ALWAs (i.e., low water absorption, low apparent porosity, and low bulk density).
Figure 2. Characteristics of ALWAs with different boric acid dosages (sintering temperature: 900°C, sintering time: 30 min).
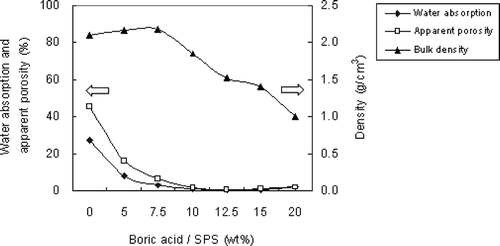
Figure 3. Cross-section SEM images of aggregates sintered from SPS with different dosage of H3BO3 (sintered at 900°C for 30 min): (a) 7.5 wt%; (b) 15 wt%.
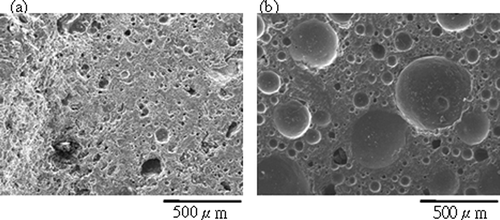
Figure 4. Differential thermal analysis of SPS with different dosage of H3BO3: (a) 5°C per min from 30 to 1000°C; (b) 2.5°C per min from 600 to 900°C.
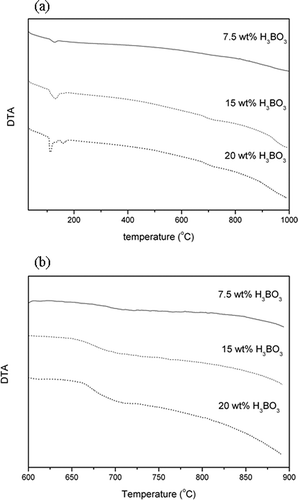
During stone cutting, water and lime are used. Lime is a source of calcium in our SPS samples. During sintering, Ca(OH)2 decomposes to CaO at 512°C (CitationHalstead and Moore, 1957; CitationGonzález-Corrochano et al., 2010). CaO is regarded as a flux according to Riley's diagram. Riley's diagram describes the effects of chemical composition on clay bloating and the phase diagram includes SiO2, Al2O3, and flux materials Na2O, K2O, Fe2O3, FeO, MgO, and CaO (CitationRiley, 1951). CitationLiao and Huang (2011) reported CaO as being a glass-forming oxide that can promote bloating behavior to form porous structures. CitationMun (2007) reported CaO acting as a flux and affecting the viscosity of raw materials at high temperature but sewage sludge not having sudden changes in viscosity even at high temperature because its CaO and MgO contents were 10% or less. Although CaO has a positive effect on the formation of the glassy phase, CaO is only 5% in our SPS sample, limiting its influence on our study.
Effect of sintering temperature on ALWAs
Water is produced by the dehydration of boric acid during sintering. When the sample is heated, water evaporates and pores are left on the surface or inside the aggregate. If the sintering temperature is high enough to form the glassy phase, surface pores are sealed, and both water absorption and apparent porosity of the ALWA decrease. Temperature is a driving force in sintering reactions, and three temperatures (i.e., 800, 850, and 900°C) were chosen to find the optimal sintering temperature at a sintering time of 0.5 hr. The effect of sintering temperature on water absorption, bulk density, and apparent porosity was also estimated. In , these three parameters are shown to decrease with increased sintering temperature, which means a well-formed glassy phase existed after high-temperature sintering. The values of water absorption and apparent porosity were less than 1% for sintering temperatures greater than 850°C. To meet Taiwan's national standards, ALWA bulk density needs to be less than 2.0 g/cm3. The respective values of bulk density for ALWAs sintered at 800, 850, and 900°C were 2.0, 1.5, and 1.4 g/cm3. Therefore, a sintering temperature of 850°C was chosen as optimal. SEM images () show surface pores disappearing gradually and inner pores becoming larger and more spherical with increased temperature. The formation of inner pores depends on gas production and the viscous glassy phase forming. In the sintering process, certain compounds liberate gas and a simultaneous viscous glassy phase traps this gas. The trapped gases cause bloating and reduced bulk density.
Figure 5. Characteristics of ALWAs with different sintering temperatures (boric acid dosage: 15 wt%, sintering time: 30 min).
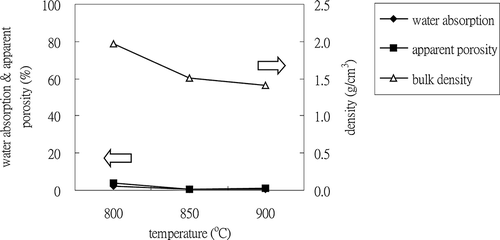
Figure 6 SEM images of aggregates sintered from SPS with 15 wt% H3BO3 at different temperatures for 0.5 hr: (a) surface, 800°C; (b) surface, 850°C; (c) surface, 900°C; (d) cross-section, 800°C; (e) cross-section, 850°C; (f) cross-section, 900°C.
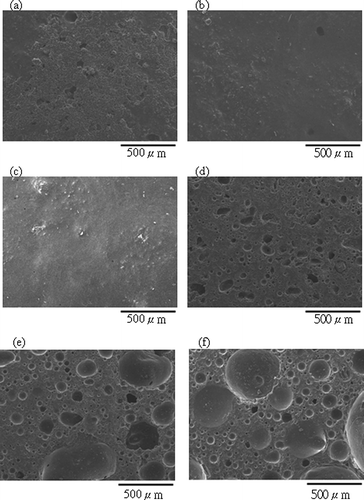
Our SPS sample contains organic compounds because flocculant polymers were added to wastewater to improve sedimentation. The organic compounds and boric acid decompose in the sintering process to release CO2 and H2O adding to the porous nature of the aggregate. High-temperature sintering results in the viscous glassy phase forming and sealing open pores at the aggregate's surface. Any trapped gases result in the aggregate being more porous. For this to occur, a balance must be achieved between the viscosity of the molten matrix and gas pressure (Mun, 2002). High sintering temperatures lower the viscosity of the glassy phase, leading to larger inner pores. As the cross-section images show (), inner pores of the ALWA sintered at 900°C were bigger than those of the 800°C aggregate.
Effect of sintering time on ALWAs
SPS was mixed with 15% boric acid and sintered at 850°C for 5 min, 15 min, 30 min, and 60 min. CitationHuang et al. (2007) mentioned that the specific gravity of ALWAs is affected by sintering duration. The highest specific gravity of ALWA occurred when there was insufficient time (5 min) for gas pocketing to occur in the inner pores. On the other hand, if the sintering temperature was prolonged (60 min), a high degree of melting occurred and increased specific gravity resulted from the glassy phase engulfing the whole of the aggregate. In this study, for sintering times of 15 and 30 min, the following respective results were obtained for water absorption, apparent porosity, and bulk density: 0.21%, 0.35%, and 1.67 g/cm3, and 0.39%, 0.59%, and 1.52 g/cm3 (see ). Evidently, the values of water absorption and apparent porosity increased slightly with increased sintering time, but bulk density was reduced due to larger inner pores being formed within the ALWA. For a sintering time of 60 min, bulk density increased to 1.62 g/cm3. SEM cross-section imaging shows that large inner pores formed in the sample (see ); however, its bulk density was greater than that of the sample sintered at 30 min. Why did such large inner pores not lead to lower bulk density? To answer this question, the volume of the ALWA before and after sintering was measured and it was found that the volume of the 60-min sample shrank 5.5% during sintering but expanded 3% for the 30-min sample. Therefore, while there were several large inner pores in the 60 min sample, the higher bulk density resulted from overall volume shrinkage. Volume shrinkage resulted from prolonged melting over the longer sintering period. Prolonged sintering reduced the viscosity of the glassy phase allowing for more gasses to bubble off or recombine with trapped gasses to form largish inner pores. In fact, the value of apparent porosity increased from 0.59% (sintered at 30 min) to 2.04% (sintered at 60 min). Finding the optimal combination of flux and energy conservation is one of the goals of this study. The results of these experiments indicate that 15% boric acid SPS sintered at 850°C for 15 min gave an ALWA of low water absorption and apparent porosity with a bulk density of just 1.67 g/cm3.
Compressive strength of ALWAs
Compressive strength of ALWA is influenced by boric acid dosage, sintering temperature, and sintering time. The results of compressive strength are shown in . Boric acid dosage affects the formation of a sealed surface in ALWAs. If the dosage is inadequate, the surface pores are not sealed completely at 900°C and ALWAs have high water absorption, apparent porosity, and low compressive strength. On the other hand, if dosage is too great, ALWAs melt to a point where they cannot keep their cylinder shape for compressive strength testing. Therefore, in our study there is no available result for SPS sintered at 900°C for 30 min with more than 20 wt% boric acid. However, the ALWA produced from SPS with 15 wt% boric acid has high compressive strength. This boric acid dosage level is considered optimal.
Table 2. Results of compressive strength and weight loss after rinsing with Na2SO4 solution of ALWAs
The value of compressive strength decreases with increased sintering temperature. This may be due to higher sintering temperatures reducing the mechanical strength of ALWAs due to larger inner pores (CitationDucman and Mirtič., 2009). In this study, the compressive strengths of ALWAs sintered at 800, 850, and 900°C for 30 min are 59.3, 35.5, and 27.3 MPa, respectively. Although the ALWA sintered at 800°C has the highest compressive strength, its bulk density was 1.96 g/cm3, meaning that it could not be classified as a lightweight aggregate. This likely occurred due to the surface not being completely sealed. The most suitable sintering temperature for conserving energy while producing favorable strength characteristics in the ALWA is 850°C.
Sintering time also affects compressive strength. For boric acid dosage of 15 wt% and sintering temperature of 850°C, the product with the highest compressive strength (66.94 MPa) had a sintering time of 15 min. SEM images of ALWAs sintered for different times are shown in . Inner pores become larger when a longer sintering time is used. The decrease in compressive strength relates to large inner pores worsening the mechanical properties of ALWAs.
Weight loss after rinsing with Na2SO4 solution of ALWAs
ALWAs sintered at 850°C for different times were tested for weight loss after rinsing with Na2SO4 solution; the results are shown in . This test is supposed to simulate the effect of ice crystallization in saturated aggregates (CitationChiou et al., 2006). The expansion of Na2SO4 during the soaking–drying process can crumble an ALWA, causing weight loss. In this study, weight loss after rinsing with Na2SO4 solution for all tested samples was less than 0.1% (far less than the regulatory limit of 12 %). The low weight loss resulted from the vitrified surface of the ALWA having low porosity; thus, expanding Na2SO4 could not create ALWA surface damage. In sum, all the ALWAs sintered at 850 °C met Taiwan's regulatory limit.
Comparing the characteristics of all ALWAs, those aggregates sintered at 850°C for 15 min showed the most appropriate characteristics with highest compressive strength (66.94 MPa) and good values for water absorption, apparent porosity, and bulk density, 0.21%, 0.35%, and 1.67 g/cm3. This ALWA is suitable for use as a construction and insulation material.
The advantages of boric acid application
Boric acid is dehydrated to form boron trioxide in the sintering process; boron trioxide is a useful flux in ceramic fabrication. The addition of boric acid can improve the physical properties of lightweight aggregates greatly at lowered sintering temperatures. According to a study by CitationHojamberdiev et al. (2011), water absorption, density, and compressive strength of ceramic tiles sintered with muscovite granite waste at 1150°C for 1 hr were 3.66–4.22%, 2.1–2.16 g/cm3, and 44.27–54.24 MPa, respectively. CitationMenezes et al. (2005) used granite sawing waste to produce ceramic bricks and tiles. The sample was sintered between 1150 and 1200°C, and a low water absorption sample (<1%) could only be obtained when the sintering temperature was 1200°C. Additionally, the modulus of rupture of all sample was less than than 36 MPa. By comparision, in our study, the values of water absorption, bulk density, and compressive strength were 0.21%, 1.67 g/cm3, and 66.94 MPa for ALWA with 15% boric acid sintered at 850°C for 15 min. Our ALWA had lower bulk density and higher compressive strength than the already-mentioned ceramic tiles. Furthermore, the ALWA in our study has much lower water absorption and higher compressive strength than the existing commercial ALWA Lytag. Lytag is produced from pulverished-fuel ash at 1200–1300°C (CitationSwamy and Lambert, 1981), and its water absorption, density and compressive strength are 10–17%, 1.35–1.5 g/cm3, and 5–9 MPa, respectively (CitationCheeseman and Virdi, 2005).
There are 1727 kilowatt-hours of energy saved when 1 ton of SPS is sintered at 850°C compared to 1150°C. In a recent comparative study of energy use efficiency (CitationHu et al., 2012), we showed that the prices of electricity, heavy oil, and coal are NT$2.365, 2.03, and 0.543 per kilowatt-hour so that NT$4084.4, 3506, and 938 in energy costs is saved for the respective energy sources. The cost of boric acid is NT$3552 for the treatment of 1 ton of SPS. If the water content of SPS is 20%, 1 ton of SPS contains 800 kg of dry SPS. For boric acid dosing at 15 wt%, the amount of boric acid needed is 120 kg. Since the price of boric acid is NT$29.6/kg, a factory using electricity as its heating source to sinter ALWAs could save $432.4 per ton SPS. In addition, the cost of boric acid is close to that of the energy savings when heavy oil is used as an energy source. Furthermore, boric acid as a fluxing agent produces superior quality ALWAs regardless of energy savings. This paper, therefore, concludes that boric acid is a highly suitable cost-effective fluxing agent in the production of ALWAs for factories using electricity or heavy oil as heating source in the sintering process.
Conclusion
Stone processing sludge (SPS) is a by-product of stone-processing wastewater treatment. This paper tests the use of boric acid as a flux to reduce the sintering temperature required to produce an artificial lightweight aggregate (ALWA) from SPS suitable for use as a construction and insulation material in accordance with Taiwan's regulations. The optimal fluxing ratio, sintering temperature, and duration times were tested to find an aggregate that had appropriate weight loss, water absorption, apparent porosity, bulk density, and compressive strength. A boric acid ratio of 15% for a sintering temperature of 850°C at 15 min gave an aggregate with water absorption, apparent porosity, bulk density, and compressive strength of 0.21%, 0.35%, 1.67 g/cm3, and 66.94 MPa. Na2SO4 solution testing for ALWA weight loss after rinsing gave a result of less than 1%. Producing such an aggregate is not only energy efficient but it also meets the regulatory requirements of Taiwan for construction materials.
References
- Alves , H.J. , Melchiades , F.G. and Boschi , A.O. 2012 . Effect of feldspar particle size on the porous microstructure and stain resistance of polished porcelain tiles . J. Eur. Ceram. Soc , 32 : 2095 – 2102 . doi: 10.1016/j.jeurceramsoc.2012.03.019
- Chang , F.C. , Lee , M.Y. , Lo , S.L. and Lin , J.D. 2010 . Artificial aggregate made from waste stone sludge and waste silt . J. Environ. Manage , 91 : 2289 – 2294 . doi: 10.1016/j.jenvman.2010.06.011
- Cheeseman , C.R. and Virdi , G.S. 2005 . Properties and microstructure of lightweight aggregate produced from sintered weage sludge ash . Resources Conserv. Recycling , 45 : 18 – 30 . doi: 10.1016/j.resconrec.2004.12.006
- Chen , H.J. , Wanga , S.Y. and Tang , C.W. 2010 . Reuse of incineration fly ashes and reaction ashes for manufacturing lightweight aggregate . Constr. Build. Mater , 24 : 46 – 55 . doi: 10.1016/j.conbuildmat.2009.08.008
- Chiou , I.J. , Wang , K.S. , Chen , C.H. and Lin , Y.T. 2006 . Lightweight aggregate made from sewage sludge and incinerated ash . Waste Manage , 26 : 1453 – 1461 . doi: 10.1016/j.wasman.2005.11.024
- Das , S.K. and Dana , K. 2003 . Differences in densification behaviour of K- and Na-feldspar-containing porcelain bodies . Thermochim. Acta , 406 : 199 – 206 . doi: 10.1016/S0040-6031(03)00257-0
- Ducman , V. and Mirtič , B. 2009 . The applicability of different waste materials for the production of lightweight aggregates . Waste Manage , 29 : 2361 – 2368 . doi: 10.1016/j.wasman.2009.02.013
- Fakhfakh , E. , Hajjaji , W. , Medhioub , M. , Rocha , F. , López-Galindo , A. , Setti , M. , Kooli , F. , Zargouni , F. and Jamoussi , F. 2007 . Effects of sand addition on production of lightweight aggregates from Tunisian smectite-rich clayey rocks . Appl. Clay Sci , 35 : 228 – 237 . doi: 10.1016/j.clay.2006.09.006
- González-Corrochano , B. , Alonso-Azcárate , J. and Rodas , M. 2009 . Production of lightweight aggregates from mining and industrial wastes . J. Environ. Manage , 90 : 2801 – 2812 . doi: 10.1016/j.jenvman.2009.03.009
- González-Corrochano , B. , Alonso-Azcárate , J. , Rodas , M. , Luque , F.J. and Barrenechea , J.F. 2010 . Miacrostructure and mineralogy of lightweight aggregates produced from washing aggregate sludge, fly ash and used motor oil . Cement Concrete. Comp , 32 : 694 – 707 . doi: 10.1016/j.cemconcomp.2010.07.014
- Halstead , P.E. and Moore , A.E. 1957 . The thermal dissociation of calcium hydroxide . J. Chem. Soc , : 3873 – 3875 . doi: 10.1039/jr9570003873
- Hojamberdiev , M. , Eminov , A. and Xu , Y. 2011 . Utilzation of muscovite granite waste in the manufacture of ceramic tiles . Ceram. Int , 37 : 871 – 876 . doi: 10.1016/j.ceramint.2010.10.032
- Hu , S. , Hu , S.H. , Fu , Y.P. and Sie , S.F. 2012 . Lowered temperature resource recycling of paper sludge using a co-melting technology . Bioresources , 7 ( 3 ) : 2766 – 2783 .
- Huang , S.C. , Chang , F.C. , Lo , S.L. , Lee , M.Y. , Wang , C.F. and Lin , J.D. 2007 . Production of lightweight aggregates from mining residues, heavy metal sludge, and incinerator fly ash . J. Hazard. Mater , 144 : 52 – 58 . doi: 10.1016/j.jhazmat.2006.09.094
- Kocakuşak , S. , Akçay , K. , Ayok , T. , öroğlu , H.J. K , Koral , M. , Savaşçi , Ö.T. and Tolun , R. 1996 . Production of anhydrous, crystalline boron oxide in fluidized bed reactor . Chem. Eng. Process , 35 : 311 – 317 .
- Kourti , I. and Cheeseman , C.R. 2010 . Properties and microstructure of lightweight aggregate produced from lignite coal fly ash and recycled glass . Resources Conserv. Recycling , 54 : 769 – 775 . doi: 10.1016/j.resconrec.2009.12.006
- Liao , Y.C. and Huang , C.Y. 2011 . Effects of CaO addition on lightweight aggregates produced from water reservoir sediment . Constr. Build. Mater , 25 : 2997 – 3002 . doi: 10.1016/j.conbuildmat.2010.12.034
- Medvedovski , E. 2001 . Liquid-phase sintering from the high-temperature corrosion process standpoint . Mater. Chem. Phys , 67 : 32 – 36 . doi: 10.1016/S0254-0584(00)00416-8
- Menezes , R.R. , Ferreira , H.S. , Neves , G.A. , Lira , H.L. and Ferreira , H.C. 2005 . Use of granite sawing wastes in the production of ceramic bricks and tiles . J. Eur. Ceram. Soc , 25 : 1149 – 1158 . doi: 10.1016/j.jeurceramsoc.2004.04.020
- Mergen , A. and Aslanoğlu , V.Z. 2003 . Low-temperature fabrication of anorthite ceramics from kaolinite and calcium carbonate with boron oxide addition . Cerma Int , 29 : 667 – 670 . doi: 10.1016/S0272-8842(02)00215-8
- Mun , K.J. Constr . 2007 . Development and tests of lightweight aggregate using sewage sludge for nonstructural concrete . Build. Mater , 21 : 1583 – 1588 . doi: 10.1016/j.conbuildmat.2005.09.009
- Riley , C.M. 1951 . Relation of chemical properties to the bloating of clays . J. Am. Ceram. Soc , 34 : 121 – 128 . doi: 10.1111/j.1151-2916.1951.tb11619.x
- Soykan , H.Ş. 2007 . Low-temperature fabrication of steatite ceramics with boron Oxide addition . Cerma Int , 33 : 911 – 914 . doi: 10.1016/j.ceramint.2006.02.001
- Swamy , R.N. and Lambert , G.H. 1981 . The microstructure of Lytag aggregate . Int. J. Cement Compos. Lightweight Concrete , 3 : 273 – 282 . doi: 10.1016/0262-5075(81)90038-5
- Tay , J.H. , Show , K.Y. , Hong , S.Y. , Chien , C.Y. and Lee , D.J. 2003 . Thermal stabilization of iron-rich sludge for high strength aggregates . J. Mater. Civil Eng , 15 : 577 – 585 . doi: 10.1061/(ASCE)0899-1561(2003)15:6(577)
- Yang , J. , Xiao , B. and Boccaccini , R. 2009 . Preparation of low melting temperature glass-ceramics from municipal waste incineration fly ash . Fuel , 88 : 1275 – 1280 . doi: 10.1016/j.fuel.2009.01.019