Abstract
Coal fly ash (CFA) was used as a raw material for the synthesis of zeolite molecular sieve. The synthesis began with the pretreatment of CFA to remove impurities (e.g., Fe2O3, CaO, etc.) under various acid types (HCl, H2SO4, and HNO3) and acid/CFA ratios (5–25 mLacid/gCFA). High product purity (up to 97%) was achieved with HCl (20%wt), and acid/CFA ratio of 20 mLHCl/gCFA. The treated CFA was then converted to zeolite by the fusion reaction under various Si/Al molar ratios (0.54–1.84). Zeolite type A was synthesized when the Si/Al molar ratios were lower than 1, whereas sodium aluminum silicate hydrate was formed when the Si/Al molar ratio were higher than 1. The highest water adsorption performance of the zeolite product, i.e., the outlet ethanol concentration of 99.9%wt and the specific adsorption capacity of 2.31 × 10−2 gwater/gzeolite, was observed with the Si/Al molar ratio of 0.82. The zeolite was tested for its water adsorption capacity repeatedly 10 times without deactivation.
Implications:
This work evaluated the technical feasibility in the conversion of CFA to zeolite, which would help reduce the quantity of waste needed to be landfilled. This adds value to the unwanted material by converting it into something that can be further used. The synthesized products were shown to be quite stable as water adsorbent for the dehydration of ethanol solution.
Introduction
The world energy crisis has become severe due to the depletion of fossil fuels. A blend of ethanol and gasoline can be used as alternative fuel for spark-ignition engines. Moreover, ethanol can also be used as an additive to diesel fuels (Satge et al., Citation2001). Biogenic ethanol is produced from the fermentation of feedstocks such as molasses, cassava, and corn. Generally, the concentration of ethanol from fermentation is in the range of 9–10% and it needs to be purified prior to the utilization as fuel additive. The distillation technology is usually applied for the ethanol purification. Nevertheless, due to its azeotropic nature, dehydration of the remaining water after distillation is required to raise ethanol concentration to above 95%wt. This is typically achieved through the use of molecular sieve water adsorption.
Coal fly ash (CFA) is an important by-product of coal combustion in the power plant. It was officially reported that Thailand generated approximately 6 million tons per year of CFA (reported in 2011) with a rising trend (Energy Policy and Planning of Thailand, Citation2011). The management of CFA therefore becomes both economic and environmental issues. Several technological options have been proposed for the disposal of fly ash such as the use as a raw material substitute in the cement production. As the major component of CFA is amorphous aluminosilicate (approximately 80%) (Molina and Poole, Citation2004), the conversion of CFA to zeolite has been proposed as a viable method. This is not only to generate a useful adsorbent but also to increase the value of industrial waste CFA. Many types of zeolite can be synthesized from CFA (Moise et al., Citation2001; Querol et al., Citation2002), and among these, zeolite A and faujasite are known as the most valuable forms, as they have a uniform pore size and a high cation exchange capacity (CEC), which makes them interesting adsorbents, catalyst, catalyst supports, and high-cation-exchange materials (Querol et al., Citation2002; Izidoro et al., Citation2013; Sapawe et al., Citation2013). Large-scale ethanol/water separation processes utilize molecular sieve that preferentially adsorbs water while ethanol molecules are excluded. Furthermore, the pressure swing adsorption and the temperature swing adsorption with molecular sieve types 3A and 4A are currently becoming the option for the production of anhydrous ethanol (Lalik et al., 2009; Mario and Martin, Citation2009). Nevertheless, the reports relevant to synthesis of high-purity zeolite from CFA and its water adsorption properties remain limited.
Due to the presence of high impurities in raw CFA, acid-washing pretreatment has been proposed as a purification option prior to the synthesis process. This work evaluated the technical feasibility in the conversion of local CFA to zeolite. Various acid-washing pretreatment conditions were carried out in order to determine the suitable conditions for removing impurities from CFA. The influence of Si/Al molar ratio of the CFA source on physical and chemical properties of the synthesized zeolite was investigated. After converting CFA to zeolite, the synthesized samples were tested as water sorbent from 95%wt ethanol solution where its adsorption capacity was compared with the commercial-grade molecular sieve.
Experimental
Raw materials
CFA was obtained from the combustion of sub-bituminous coal at the local coal-fired combined power plant in Prachinburi, Thailand. CFA was collected nine times during December 2010 to December 2011. The average and standard deviation values of the chemical compositions of the CFA samples were evaluated by X-ray fluorescence and reported in (XRF; model PW2400; Philips, The Netherlands). According to the analysis of variance (ANOVA) using the two-way ANOVA method calculated at 95% confidence level, it can be concluded that there is no significant difference regarding the compositions of CFA among the seasons.
1. Chemical composition of original CFA samples analyzed by XRF
Acid-washing pretreatment procedure
Various pretreatment conditions (i.e., acid volume, acid types, and acid reuse) were carried out for the treatment of CFA. Firstly, CFA (20 g) was initially added to HCl, H2SO4, or HNO3 with 10–30%w/w acid concentration under the acid/CFA ratios of 5, 10, 15, 20, and 25 mLacid/gCFA. The mixture was stirred constantly at the rate of 300 rpm at 80 °C for 2 hr. After that, the solid sample was filtered off from the acid solution and washed repeatedly with deionized water until the solution reached neutral pH and then dried overnight at 105 °C in a kiln. The acid solution, once the solid sample was filtered off, was used in next pretreatment batches. The concentration and the volume of the filtered acid were determined and adjusted before being used in next pretreatment batches.
Zeolite synthesis procedure
For this work, the method developed by Ruen-ngam et al. (Citation2009) (the fusion method followed by the hydrothermal method) was employed. First, the pretreatment sample was mixed with sodium hydroxide (NaOH anhydrous; Sigma-Aldrich) to make a NaOH/CFA mass ratio of 2.25. Next, the mixture was then burnt at 550 °C for 1 hr in a tubular furnace. After cooling down, the product was crushed, mixed in deionized water (85 mL), and stirred constantly at the rate of 300 rpm at room temperature for 12 hr. The mixture was subsequently crystallized in a kiln (80 °C) for 4 hr. The crystal was separated and washed several times with deionized water until the pH of the solution went down to 10–11 and dried overnight at 105 °C. The flow diagram of the synthesis process is shown in .
Characterization
Several physical characterizations of the synthesized zeolite samples were observed using a variety of conventional techniques. The phase identification of synthesized zeolite sample was determined by X-ray diffraction (XRD; Bruker, model AXS D8 Discover). The morphology of the synthesized zeolite sample was observed by scanning electron microscope (SEM; Jeol, model Jsm5410lv). X-ray fluorescence (XRF; Philips, model PW2400) was used to determine the chemical compositions of the CFA and the synthesized zeolite samples. The specific surface area, the pore size, and the pore volume of the zeolite samples and the commercial molecular sieve (types 3A and 4A) were determined by N2 adsorption-desorption technique using Brunauer-Emmett-Teller (BET) surface area and pore size analyzers (Quantachrome Instruments, model NOVA 2200e). Furthermore, the percent yield, which is one of the important parameters, was calculated in order to demonstrate the efficiency of the zeolite synthesis process.
Water adsorption
The schematic diagram of the adsorption testing experiment system is shown in . This began with loading 1 g of synthesized zeolite sample, commercial molecular sieve type 3A (molecular sieve 0.3 nm; Merck) or type 4A (molecular sieve 0.4 nm; Merck) onto glass wool to prevent the dislocation of sample from the adsorption zone into the reactor. A stainless steel tube with the length of 60 cm and the diameter of 9.8 mm was used as the adsorption reactor. Ethanol solution with 95%wt concentration in vapor phase was fed through the system at the rate of 36 mL/hr by a syringe pump through an evaporator, whereas the carrier gas (nitrogen) was introduced to the system and controlled by the mass-flow controller. These inlet gaseous mixtures were introduced to the adsorption section, in which the reactor was mounted vertically and bound with a heater. The adsorption was carried out at 90 °C.
Ethanol concentration achieved at the outlet of the adsorption process was determined using Karl Fischer titration (KF; Mettler Toledo, model C20 compact KF coulometer). The water adsorption capacity (gwater/gCFA) is the mass of water adsorbed by the zeolite (gzeolite per synthesis batch) synthesis from CFA (gCFA), and the water adsorption capacity is calculated using eq 2:
Results and Discussion
Characterization of coal fly ash
From X-ray fluorescence analysis, the results show that the main components of the original CFA were silicon and aluminium oxides, whereas the impurities consisted of metallic oxides such as Fe and Ca, as shown in . Other elements presented in trace amounts included MgO, K2O, and TiO2. High amorphous aluminosilicate (approximately 80%) content suggested a potential conversion to zeolite (Molina and Poole, Citation2004). To produce high-purity zeolite, CFA raw material was subjected to a certain pretreatment process i.e., acid-washing for removal of impurities and to enhance Si and Al compositions.
Acid-washing pretreatment
Effect of various acid types
From the preliminary results, the treatment with 10%w/w and 20%w/w HCl could raise the purity of the product to 78%wt and 85%wt, respectively. Nevertheless, this effect became less pronounced when the acid concentration increased to 30%w/w (83%wt purity). Hence, HCl concentration at 20%w/w was considered to be the most suitable concentration for acid-washing pretreatment.
presents the chemical components of CFA raw material and zeolite synthesized from CFA with and without pretreatment. The results show that most of the impurities (Fe2O3, CaO, and other impurities) in CFA can be removed by treatment with 20%w/w of these acids (HCl, H2SO4, and HNO3) at the liquid (acid solution)/solid (CFA) ratio of 25 mLacid/gCFA. These results agree with that of Shivpuri et al. (2012) who reported that heavy metals showed a high leachability in acidic conditions. Furthermore, higher specific surface area and higher pore size diameter were observed from the pretreated sample, according to the BET measurement as presented in . Zeolite synthesized from the nontreated CFA had a purity of 59% (Na2O, SiO2, and Al2O3), a specific area of 58 m2/g, and a pore size of 3.42 Å. Among the various acid species (HCl, H2SO4, and HNO3), zeolite synthesized from CFA treated with HCl provided the highest purity material (87% of Na2O, SiO2, and Al2O3), with the specific area of 261 m2/g, pore size of 4.34 Å, and pore volume of 0.8 cc/g, whereas zeolite synthesis from CFA treated with HNO3 only achieved the purity of 69%, with a specific area of 139 m2/g and pore volume of 0.12 cc/g.
2. Properties of zeolite products synthesized from CFA with various conditions
shows XRD patterns of the original CFA, the CFA after treatment with NaOH by fusion at 550 °C for 1 hr with a NaOH/CFA mass ratio of 2.25, and the CFA treated with acid-washing pretreatment prior to the fusion process. The original CFA was of amorphous phase and the diffraction peak corresponded to the presence of quartz (JCPDF no. 01-079-1906). These crystal phases were difficult to dissolve into alkali solution by hydrothermal reaction (Shigemoto et al., Citation1993). Alkali treatment by the fusion method resulted in the transformation of CFA into an amorphous material, as shown in . The alkali fusion method decomposed and converted the quartz phase into soluble phase, the conditions necessary for the formation of zeolite. The results agree with that of Wajima et al. (Citation2011) who reported the use of the alkali fusion method to convert the crystalline to soluble phase and to transform CFA into various zeolite products by varying experimental conditions.
The XRD diffraction peak corresponded to the presence of zeolite type × (JCPDF no. 01-089-8235), zeolite type A (JCPDF no. 01-089-3142), and another type of sodium aluminum silicate hydrate (JCPDF no. 00-038-0237), as shown in . It could be observed that the main phase formation of all zeolite products treated with acid was sodium aluminum silicate hydrate, which is referred to sodium aluminosilicate material and is composed of sodium, aluminum, silica, and oxygen, in many different forms, e.g., zeolite type analcime, Na-A, Na-X, etc. The percent yield of zeolite synthesis from nontreated CFA was 55%, whereas the percent yield of zeolite synthesis from samples treated with acids were in the range of 32–34%, as indicated in . The impurities contained in the treated CFA were washed away before the conversion of CFA to zeolite, therefore, producing a lower yield, but higher purity.
5. X-ray diffraction of zeolite products synthesized from CFA treated with various acids (a), various L/S ratios (b), and reusing acid (c).
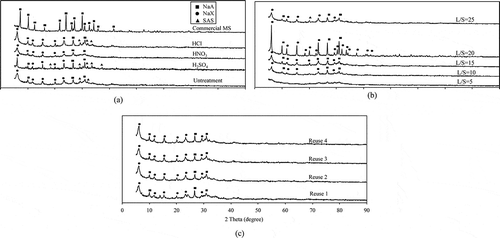
The breakthrough curve of water adsorption on zeolite products and commercial molecular sieve is plotted, as demonstrated in . The acid-washing pretreatment process had a positive effect on the water adsorption performance of the synthesized zeolite products. The samples pretreated by acid-washing prior to the fusion process demonstrated a greater adsorption performance than the samples without pretreatment. A good adsorption performance was indicated by a higher adsorption capacity, specific adsorption capacity, and outlet ethanol concentration. The zeolite with acid-washing pretreatment had higher specific surface area and pore size than the sample without pretreatment (see ), which was the main reason for a better water adsorption performance. From these studies, the highest ethanol concentration achieved at the outlet of the adsorption process was observed using the sample treated with HCl (at 98.3%wt). The samples pretreated with H2SO4 and HNO3 and the sample without pretreatment produced the highest ethanol concentration of 98.1%wt, 97.7%wt, and 96.6%wt, respectively.
6. Breakthrough curves of water adsorption by the zeolite products synthesized from CFA treated with various acid types (a), with various L/S ratios (b), and with reused acid (c).
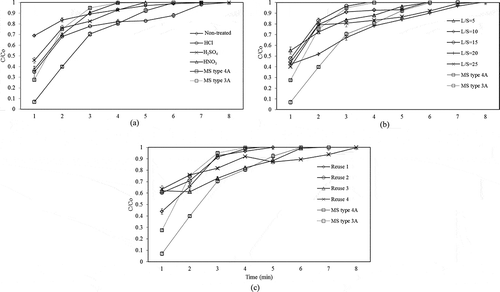
In this comparison, the adsorption capacity was calculated based on the initial weight of CFA used to produce zeolite. The water adsorption capacity (A) and the specific water adsorption capacity (asp) of the zeolite samples with and without pretreatment were calculated from eqs 2 and 3, and the results are shown in . The highest value of the adsorption capacity was observed using the samples pretreated with HCl (5.08 × 10−3 gwater/gCFA), whereas the sample pretreated with HNO3 and H2SO4 and the sample without pretreatment could only give 5.01 × 10−3, 4.22 × 10−3, and 4.03 × 10−3 gwater/gCFA, respectively, as shown .
From these preliminary results, due to the purity and the water adsorption capacity of the synthesized zeolite sample, it was recommended to perform the acid-washing process prior to the fusion process. Furthermore, among the three acid types, HCl was selected as the preferred CFA pretreatment. The commercial molecular sieve type 4A showed a higher value of the outlet ethanol concentration (99.7%wt) and the specific water adsorption capacity (2.20 × 10−2 gwater/gzeolite) than the commercial molecular sieve type 3A (98.7%wt and 1.72 × 10−2 gwater/gzeolite, respectively) and the zeolite sample treated with HCl (98.3% and 1.54 × 10−2 gwater/gzeolite, respectively). These results agree with that of Yamamoto et al. (Citation2012) who reported that zeolite with a small Si/Al ratio showed a higher water adsorption performance than zeolite with a large Si/Al. In other words, zeolite type 4A was reported to possess better water adsorption performance than type 3A. However, the water adsorption performance of the synthesized zeolite could be improved by adjusting conditions of acid-washing pretreatment (e.g., acid concentration, acid/CFA ratio) and/or zeolite synthesis (e.g., Si/Al ratio of CFA).
Effect of liquid/solid ratio
shows the chemical components of zeolite synthesized from CFA treated with 20%w/w concentration of HCl under various liquid/solid (L/S) ratios. It appeared that the quality of zeolite products was affected by the L/S ratio where most of the impurities of CFA were removed and the maximum purity of 86% (Na2O, SiO2, and Al2O3) was attained at L/S of 10 mLacid/gCFA. Similar results were observed from Kai et al. (Citation2011). However, the highest specific surface area (227 m2/g), total pore volume (0.22 cc/g), and pore size (4.09 Å) was observed from the pretreated sample with L/S ratio of 20 mLacid/gCFA (see BET results in ).
The main phase formation of zeolite product synthesized from the pretreated CFA with various L/S ratios analyzed by XRD was sodium aluminum silicate hydrate, where the diffraction peak corresponded to the presence of zeolite type × (JCPDF no. 01-089-8235) and zeolite type A (JCPDF no. 01-089-3142), as illustrated in . The diffraction peak intensity of zeolite samples increased with L/S ratio, meaning a better crystallinity of zeolites. However, the diffraction peak intensity decreased when the L/S ratio increased to 25 mLacid/gCFA, which suggested the optimal L/S of 20 mLacid/gCFA. Note that the percent yield of all zeolite products was quite similar, all in the range of 28–33%, as indicated in .
Water adsorption test from ethanol solution using zeolite synthesized from the various CFA samples along with the commercial molecular sieve was investigated with the fixed-bed column (see ). demonstrates that the zeolite synthesized from CFA treated with HCl at L/S ratio of 20 mLacid/gCFA had the largest specific surface area, pore size, and also the highest water adsorption capacity (4.51 × 10−3 gwater/gCFA and 1.42 × 10−2 gwater/gzeolite). The highest ethanol concentration at the outlet of the adsorption process was 97.9%wt, which was still lower than those from the commercial molecular sieve types 3A and 4A (98.7%wt and 99.7%wt, respectively).
Effect of reusing acid
shows the chemical components of zeolite synthesized from the CFA treated with the reused HCl (20%w/w) under the L/S of 20 mLacid/gCFA. The results indicate that there were no significant differences in the quality of the zeolite products when compared with that obtained from the use of fresh acid. This test was repeated four consecutive times and the reused acid seemed to give satisfactory results where most impurities could be removed effectively, and the products exhibited high purity (77–81%) and reasonable specific surface area (200–210 m2/g) and pore volume (0.21–0.37 cc/g), as indicated in . The percent yield of zeolite products were in the range of 28–32%.
The main phase formation of all zeolite products synthesized from CFA treated with the reused acid was sodium aluminum silicate hydrate, and the diffraction peak corresponded to the presence of zeolite type × (JCPDF no. 01-089-8235), and zeolite type A (JCPDF no. 01-089-3142), as shown in . Note that the acid volume decreased by approximately 10% after each acid-washing process, yet the concentration of the reused acid remained unchanged.
The breakthrough curve of water adsorption on commercial molecular sieve and zeolite samples synthesized from CFA treated with reused acid are plotted, as shown in . Note that the caption Reuse 1 refers to the experiment with the acid that was already used once, whereas Reuse 2, in a similar manner, refers to the experiment with the second reused acid (and so on for Reuse 3 and Reuse 4). The highest ethanol concentration at the outlet of the adsorption process using the samples treated with reused acid was in a range of 97–98%wt. This concluded that zeolite samples synthesized from CFA treated with reused acid had similar adsorption performance to those with fresh acid.
Zeolite synthesis
Effects of chemical compositions of raw materials
To remove the impurities of CFA and to make a higher purity zeolite, the acid-washing pretreatment (as stated in the previous section) was carried out prior to the fusion method. The pretreated CFA was then converted to zeolite using the fusion temperature of 550 °C with NaOH/CFA mass ratio of 2.25 for 1 hr, followed by crystallization at 80 °C for 4 hr (Ruen-ngam et al., Citation2009).
shows chemical compositions of zeolite products synthesized from the various CFAs. These results show that most impurities were removed and a higher purity (75–87%wt of purity) of zeolite product was achieved. The percent yields of the products were all in the range of 21–32%, as shown in . The same table also demonstrates the BET surface area, pore size, and pore volume of the synthesized zeolite from various CFA raw materials where the specific surface area for the zeolite products were in a range of 301–461 m2/g, and the pore sizes were in a range of 4.43–4.89 Å, with the pore volume in a range of 0.24–0.32 cc/g.
The XRD patterns () and the SEM morphological analysis () of zeolite samples synthesized from CFAs without Si/Al adjustment are demonstrated to be those of sodium aluminum silicate hydrate. The Si/Al molar ratios of CFA raw materials were in a range of 1.54–1.84 (see ), which favored the formation of zeolite type X. Similar results were obtained from Tanaka et al. (Citation2002), Purnomo et al. (Citation2012), and Izidoro et al. (Citation2013).
8. X-ray diffraction of zeolite products, synthesized from CFA with the Si/Al ratio adjustment at laboratory scale.
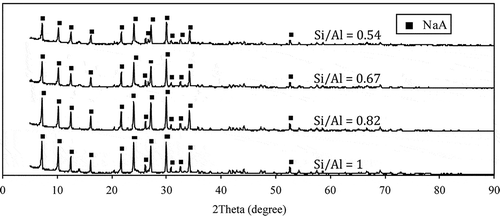
9. SEM photographs of the zeolite samples synthesized from CFA without the Si/Al ratio adjustment (a) and with Si/Al ratio adjustment (b) at laboratory-scale experimentation.
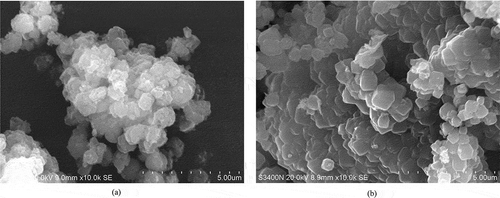
shows the breakthrough curve of water sorption on zeolite products and commercial molecular sieve. All zeolite samples synthesized using the method shown in show quite similar adsorption performance, with the highest ethanol concentration at the outlet of the adsorption process in a range of 97–98%wt, which was still lower than the commercial molecular sieve types 3A and 4A. These results suggest that the quality of the zeolite could be maintained (as sodium aluminum silicate hydrate) despite the different chemical compositions of raw CFA. However, the water adsorption performance of these zeolite samples still had to be improved to match that of commercial one. In this work, this could be achieved through the adjustment of Si/Al ratio in the CFA, as illustrated in the following section.
Effect of Si/Al ratio
CFA was pretreated with acid prior to fusion with 20%w/w HCl under the L/S ratio of 20 mL/g at 80 °C for 2 hr to remove the impurities. The Si/Al molar ratio of the treated CFA was adjusted in the range of 0.54–1 by adding alumina powder (99.9% Al2O3 powder; Sigma-Aldrich) as a source of aluminum. This was followed by the fusion at 550 °C with NaOH/CFA mass ratio of 2.25 for 1 hr and crystallization at 80 °C for 4 hr. XRF shows that, with this technique, most of the impurities were removed and a higher purity (96–97%wt of purity) of zeolite product was achieved. The yields of the products were all in the range of 63–73%, as shown in . Based on these results, the zeolite synthesized from CFA with Si/Al of 0.54 had the highest yield, which was higher than the zeolite with Si/Al of 0.67, 0.82, and 1.00, respectively. Similar results were observed from Zhang et al. (Citation2013) who reported that the yield of zeolite products decreased when the Si/Al molar ratio increased. However, a much too high Si/Al molar ratio was not found to have positive effects on the purity. illustrates that all zeolite samples had high surface area in a range of 406–418 m2/g, whereas the pore sizes of the samples fell in a range of 4.08–4.28 Å. Based on these results, the zeolite synthesized from CFA with Si/Al of 0.82 had the highest surface area (418 m2/g), large pore volume (0.76 cc/g), and the lowest pore size (4.08 Å).
The XRD patterns in suggest that all zeolite samples matched the pattern of zeolite A (JCPDF no. 01-089-3142). This finding leads to a conclusion that pure zeolite type A was synthesized when the Si/Al ratios in the reaction mixture were less than or equal to 1, whereas sodium aluminum silicate hydrate was obtained at the Si/Al molar ratio in a range of 1.54–1.84. These results agree with those of Tanaka et al. (Citation2002), Purnomo et al. (Citation2012), Izidoro et al. (Citation2013), and Zhang et al. (Citation2013) who reported that a single-phase zeolite type A was formed at the Si/Al molar ratio of not more than 1, whereas the other phases of zeolite (e.g., Na-X, Na-Y, and Na-P) was slightly formed at the Si/Al molar ratio of more than 1.
SEM of zeolite samples () revealed the presence of crystal with the cubic morphology and with even crystal size distribution. The average diameter of the zeolite cubic crystal was approximately 1 μm. No considerable amounts of amorphous material were detected with this technique, which indicates a high degree of crystallization. The process to improve the Si/Al ratio, by adding alumina prior to the fusion process, not only strongly affected the structure formation of the zeolite samples, but also dramatically affected the water adsorption performances of the products. The breakthrough curve of water adsorption on zeolite products from CFA with Si/Al adjustment and commercial molecular sieve is plotted in . All of the zeolite undergoing the Si/Al improvement process prior to the fusion process exhibited a higher water sorption performance, i.e., a higher ethanol concentration and a higher value of the specific water adsorption capacity than those of the commercial molecular sieve. Among these samples, the zeolite product with a Si/Al ratio of 0.82 presented the highest adsorption performance, with the water adsorption capacity of 1.50 × 10−2 gwater/gCFA and the specific water adsorption capacity of 2.31 × 10−2 gwater/gzeolite (the specific water adsorption of the commercial molecular sieve types 3A and 4A = 1.72 × 10−2 and 2.20 × 10−2 gwater/gzeolite, respectively).
Performance of synthesized zeolite as water sorbent
Regeneration of zeolite
In this experiment, the zeolite was regenerated using thermal swing method where the temperature was raised to 250 °C for 4 hr in order to remove moisture from the sample. It should be noted that temperature higher than 270 °C was not recommended, as this could cause extensive structural damage to zeolite (Simo et al., Citation2009). After that, the system was cooled down to the operating adsorption temperature (90 °C) where the new adsorption cycle begins. The entire adsorption cycle test was investigated without removing the sample from the bed to avoid the influence of moisture in the air. The zeolite sample synthesized from CFA treated with 20%w/w of HCl (80 °C, 2 hr) and with Si/Al molar ratio of 0.82 prior to the fusion process (NaOH/CFA = 2.25, 550 °C, 1 hr) was used to study the breakthrough behavior of the regenerated zeolite.
shows the breakthrough curve of water adsorption on zeolite product, which illustrates that zeolite deactivation was not observed under 10 adsorption-testing cycles. A similar behavior of water adsorption performance was observed in all adsorption cycles where the highest ethanol concentration at the outlet of the adsorption process was more than 99.9%wt (the commercial molecular sieve types 3A and 4A gave 98.7%wt and 99.7%wt outlet ethanol concentration, respectively).
Conclusion
This study focuses on the synthesis of zeolites from CFA and on a water adsorption potential of the synthesized zeolite products compared with commercial molecular sieve. Furthermore, the results show that acid-washing conditions (e.g., acid type, acid concentration, acid volume, and reused acid) and synthesis conditions (i.e., Si/Al molar ratio) have a significant effect on the chemical and physical properties of the synthesized zeolite products.
The results demonstrate that zeolite type 4A could be synthesized from CFA and was shown to be suitable as water adsorbent from ethanol solution. Furthermore, the quality of synthesized zeolite products could be control by adjusting the conditions of acid-washing and zeolite synthesis process. This simple conversion technique suggests a potential scale-up possibility, which could pose one of the promising solution for the management of fly ash waste.
A rough cost estimate of the synthesis based on the most suitable conditions of this work is given in and . The total expense per batch for the laboratory-scale production (approximately 13 g of zeolite product per batch) was approximately US$6.52 (US$501.43 per kilogram of zeolite). However, preliminary estimation indicates that the large-scale production of zeolite was approximately 1.5 kg/batch and the total expense per batch was approximately US$38.57 (US$19.74 per kilogram of zeolite). This considerably lower cost was due to the economy of scale, as many of the utilities could be utilized more effectively when compared with the laboratory scale. Note that the current global price of zeolite type 4A is at US$83.87 per kg (UOP: Changxing Molecular Sieves Group). Moreover, in actual industrial scenario, it might be possible to utilize waste heat from the process, which might help reduce the cost of the production.
3. Estimated electrical production cost of zeolite synthesis
4. Estimated material production cost of zeolite synthesis
Acknowledgment
The authors would like to acknowledge Inter Pacific Paper (Thailand) Co., Ltd., for providing the coal fly ash raw material.
Funding
Financial support was provided by Inter Pacific Paper (Thailand) Co., Ltd., and the Thailand Research Fund.
Additional information
Notes on contributors
Panu Panitchakarn
Panu Panitchakarn is a postgraduate student and Prasert Pavasant is a lecturer in the Department of Chemical Engineering Faculty of Engineering at Chulalongkorn University in Bangkok, Thailand.
Navadol Laosiripojana
Navadol Laosiripojana is a lecturer at the Joint Graduate School of Environment, CHE Center for Energy Technology and Environment, King Mongkut’s of Technology Thonburi, Thailand.
Nawin Viriya-umpikul
Nawin Viriya-umpikul is researcher at National Nanothecnology Center, National Science and Technology Department Agency, Thailand.
Prasert Pavasant
Panu Panitchakarn is a postgraduate student and Prasert Pavasant is a lecturer in the Department of Chemical Engineering Faculty of Engineering at Chulalongkorn University in Bangkok, Thailand.
References
- Energy Policy and Planning of Thailand. 2011. Annual Report 2011. Ministry of Energy, Thailand.
- Izidoro, J.D.C., D.A. Fungaro, J.E. Abbott, and S. Wang. 2013. Synthesis of zeolites X and A from fly ashes for cadmium and zinc removal from aqueous solutions in single and binary ion systems. Fuel 103: 827–834. doi: http://dx.doi.org/10.1016/j.fuel.2012.07.060
- Kai, H., K. Inoue, H. Harada, H. Kawakita, and K. Ohto. 2011. Leaching behavior of heavy metals with hydrochloric acid from fly ash generated in municipal waste incineration plant. Trans. Nonferrous Metals Soc. China 2: 1422–1427.
- Lalik, E., R. Mirel, J. Rakoze, and A. Groszek. 2006. Microcalorimetric study of sorption of water and ethanol in zeolites 3A and 5A. Catal. Today 114: 242–247. doi:10.1016/j.cattod.2006.01.006
- Mario, L., and A.M. Martin. 2009. Accurate correlation, thermochemistry, and structural interpretation of equilibrium adsorption isotherms of water vapor in zeolite 3A by means of generalized statistical thermodynamic adsorption model. Fluid Phase Equilibria 283: 73–88.
- Moise, J.C., J.P. Bellat, and A. Methivier. 2001. Adsorption of water vapor on X and Y zeolites exchangeable with barium. Microporous Mesoporous Mater. 43: 91–101. doi:10.1016/S1387-1811(00)00352-8
- Molina, A., and C.A. Poole. 2004. Comparative study using two methods to produce zeolite from fly ash. Miner. Eng. 17: 167–173. doi:10.1016/j.mineng.2003.10.025
- Purnomo, C.W., C. Salim, and H. Hinode. 2012. Synthesis of pure Na-X and Na-A zeolite from bagasse fly ash. Microporous Mesoporous Mater. 162: 6–13. doi:10.1016/j.micromeso.2012.06.007
- Querol, X., N. Moreno, J.C. Umana, A. Alastuey, E. Hernandez, A. Lopez-Soler, and F. Plana. 2002. Synthesis of zeolite from coal fly ash: An overview. Int. J. Coal Geol. 50: 412–423. doi:10.1016/S0166-5162(02)00124-6
- Ruen-ngam, D., D. Rungsuk, R. Apiratikul, and P. Pavasant. 2009. Zeolite formation from coal fly ash and its adsorption potential. J. Air Waste Manage. Assoc. 59: 1140–1147. doi:10.3155/1047-3289.59.10.1140
- Sapawe, N., A.A. Jalil, S. Triwahyono, M.I.A. Shah, R. Jusoh, N.F.M. Salleh, B.H. Hameed, and A.H. Karim. 2013. Cost-effective microwave rapid synthesis of zeolite NaA for removal of methylene blue. J. Chem. Eng. 299: 388–398.
- Satge, P.D.C., Z. Mouloungui, and G. Vaitilingom. 2001. Interest of combining and additive with diesel-ethanol blends for use in diesel engines. Fuel 80: 565–574.
- Shigemato, N., H. Hayshi, and K. Miyaura. 1993. Selective formation of Na-X zeolite from fly ash by fusion with sodium hydroxide prior to hydrothermal reaction. J. Mater. Sci. 28: 4693–4703.
- Shivpuri, K.K., B. Lokeshappa, D.A. Kulkarni, and A.K. Dikshit. 2011. Metal leaching potential in coal fly ash. Am. J. Environ. Eng. 1: 21–27.
- Simo, M., S. Sivashanmugam, C.J. Brown and V. Hlavacek. 2009. Adsorption/desorption of water and ethnol on 3A zeolite in near-adiabatic fixed bed. Ind. Eng. Chem. 48: 9247–9260.
- Tanaka, H., Y. Sakai, and R. Hino. 2002. Formation of Na-A and -X zeolites from waste solutions in conversion of coal fly ash to zeolites. Mater. Res. Bull. 37: 1873–1884. doi:10.1016/S0025-5408(02)00861-9
- Wajima, T., and K. Munakata. 2011. Material conversion from paper sludge ash in NaOH solution to synthesize adsorbent for remooval of Pb2+, NH4+ and PO43+ from aqueous solution. J. Environmental Science. 23: 718–724.
- Yamamoto, T., Y.H. Kim, B.C. Kim, A. Endo, N. Thongprachan, and T. Ohmori, 2012. J. Chemical Engineering. 182: 443–448.
- Zhang, X., D. Tang, M. Zhang, and R. Yang. 2013. Synthesis of NaX zeolite: Influence of crystallization time, temperature and batch molar ratio SiO2/Al2O3 on the particulate properties of zeolite crystals. J. Powder Technology. 235: 322–328. doi:10.1016/j.powtec.2012.10.046