Abstract
A hybrid selective noncatalytic reduction/selective catalytic reduction (SNCR/SCR) system that uses two types of technology, low-temperature SCR process and SNCR process, was designed to develop nitrogen oxide (NOx) reduction technology. SCR was conducted with space velocity (SV) = 2400 hr−1 and hybrid SNCR/SCR with SV = 6000 hr−1, since the study focused on reducing the amount of catalyst and both achieved 98% NOx reduction efficiency. Characteristics of NOx reduction by NH3 were studied for low-temperature SCR system at 150 °C using Mn-V2O5/TiO2 catalyst. Mn-added V2O5/TiO2 catalyst was produced, and selective catalyst reduction of NOx by NH3 was experimented. NOx reduction rate according to added Mn content in Mn-V2O5/TiO2 catalyst was studied with varying conditions of reaction temperature, normalized stoichiometric ratio (NSR), SV, and O2 concentration. In the catalyst experiment according to V2O5 concentration, 1 wt.% V2O5 catalyst showed the highest NOx reduction rate: 98% reduction at temperature window of 200~250 °C. As a promoter of the V2O5 catalyst, 5 wt.% Mn was added, and the catalyst showed 47~90% higher efficiency even with low temperatures, 100~200 °C. Mn-V2O5/TiO2 catalyst, prepared by adding 5 wt.% Mn in V2O5/TiO2 catalyst, showed increments of catalyst activation at 150 °C as well as NOx reduction. Mn-V2O5/TiO2 catalyst showed 8% higher rate for NOx reduction compared with V2O5/TiO2 catalyst in 150 °C SCR. Thus, (5 wt.%)Mn-(1 wt.%)V2O5/TiO2 catalyst was applied in SCR of hybrid SNCR/SCR system of low temperature at 150 °C. Low-temperature SCR hybrid SNCR/SCR (150 °C) system and hybrid SNCR/SCR (350 °C) showed 91~95% total reduction rate with conditions of SV = 2400~6000 hr−1 SCR and 850~1050 °C SNCR, NSR = 1.5~2.0, and 5% O2. Hybrid SNCR/SCR (150 °C) system proved to be more effective than the hybrid SNCR/SCR (350 °C) system at low temperature.
Implications: NOx control is very important, since they are the part of greenhouse gases as well as the cause of acid rain and ozone hole. A technology, so-called hybrid SNCR/SCR process, was tested using Mn-V2O5/TiO2 monolithic catalyst for NOx reduction, and the method is promising. The results of this study would provide some ideas to parties such as policy makers, environmental engineers, and so on.
Introduction
Various nitrogen oxide (NOx) control methods are necessary because NOx reduction uses different mechanisms according to the type of combustion engine. Reduction method is classified into two categories: combustion improvement method and aftertreatment method. The former reduces NOx quantity by regulating combustion point and oxygen concentration, whereas the latter achieves NOx reduction through postprocessing. Postprocessing is widely used for reduction of NOx with high concentration. Aftertreatment of NOx can be classified into SCR (selective catalytic reduction) process with low-temperature electric generation and SNCR (selective noncatalytic reduction) with high-temperature electric generation. The SCR process shows highly effective NOx reduction rate at low temperature by using a catalyst (Bosch and Janssen, Citation1988), but economic feasibility should be considered for smaller industrial facilities due to increased operation cost and shortened life span of the catalyst caused by an expensive catalyst.
On the other hand, the SNCR not only promotes easy application in coal-fired power plants and industrial boilers by reverting NO to N2 via direct injection of chemical additives in high temperature region of 900~1100 °C, but also promotes low-cost installation and operation compared with SCR (Lyon, Citation1975; Nam and Gibbs, Citation2000). The SNCR achieves approximately 30–60% NOx reduction rate, and the reduction rate increases in laboratory-sized research (Miller and Bowman, Citation1989). On the other hand, SCR can reduce NOx more than 90% depending on the catalyst volume and space velocity (Long and Yang, Citation2000; Nova et al., Citation2001). Both processes are affected by the temperature condition, degree of mixing, oxidation of reducing agent, and NH3 slip.
Research on hybrid SNCR/SCR process has been a trend to cut down the cost of business installation and operation (Roy et al., Citation2008; Wu et al., Citation2008; Chen et al., Citation2010; Koh and Park, Citation2013). Gullett et al. (Citation1994) investigated on the optimal condition of combined process of SNCR and SCR, considering the change in space velocity (SV) during SCR, NH3 injection quantity, and reaction temperature during SNCR process of pilot-scale combustor using natural gas. Urbas and Boyle (Citation1998) discussed the application of SNCR/SCR hybrid process at GPU Genco Seward Station. Furthermore, Wendt et al. (Citation2001) worked on the development of an accurate and applicable model of the hybrid process for measuring economic feasibility of SNCR/SCR hybrid process on site.
Hybrid process outperforms the independent SCR by cutting down the operation cost (Miller and Srivastava, Citation2000) and outperforms the independent SNCR by increasing the NOx reduction efficiency and reducing the concentration of NH3 slip. The state-of-the-art hybrid process uses V2O5/TiO2 catalyst, which is common in SCR. This is because V2O5/TiO2 achieves active reduction of NO generated from a fixed source by using NH3 as the reducing agent. Also, V2O5/TiO2 has superior endurance against SO2 compared with other catalysts (Chen and Yang, Citation1992). For formulation of a practical V2O5/TiO2 catalyst, WO3 (Choo et al., Citation2003), MoO3 (Lietti et al., Citation1999), SiO2 (Sorrentino et al., Citation2001), or other chemicals is added or sulfated according to the processing condition. The catalyst promoter, greater than V2O5 in quantity, is selected and added according to the emission condition and plays an important role in boosting the performance of the V2O5/TiO2 catalyst.
Although catalyst based on vanadium is highly active and durable against SO2, it has several weaknesses. Activation only occurs within narrow temperature window of 300~400 °C, and SCR is applied within such temperature window to prevent pore blocking caused by the pigmentation of ammonium sulfates such as NH4HSO4 and (NH4)2S2O7 on the catalyst surface (Choo et al., Citation2003). For such reason, much attention is drawn on the development of a catalyst with high activity during low-temperature SCR.
The purpose of this research is to study Mn-V2O5/TiO2 monolithic catalyst used in the SCR for developing a catalyst with high NOx removal activity in the low temperature region below 200 °C. The SCR process with Mn-V2O5/TiO2 monolithic catalyst only needs 150 °C for similar NOx removal efficiency compared with typical SCR processes, which require the temperature of at least 250 °C. Also, the study evaluates denitrification efficiency of the hybrid SNCR/SCR system using the prepared catalyst in order to achieve power savings and avoid catalyst poisoning.
Experimental
Catalyst preparation
V2O5 catalyst was prepared via impregnation method using NH4VO3 (99%; Aldrich, Fisher Scientific, Tustin, CA, USA) with anatase TiO2 (cell density: 36 CPI) as a supporting form. After being dried at 110 °C for 10–12 hr, it was burnt in a Maffle furnace at 500 °C for 5 hr. The catalyst content of V2O5 was set at 1 wt.%, and low-temperature catalyst was prepared by impregnating Mn(NO3)23H2O (99%; Junsei) each at 5 wt.% on the V2O5/TiO2 monolithic standard catalyst.
Catalyst characterization
X-ray diffractometer (MP-XRD, USA) was used to perform qualitative analysis on the compound precipitate of the carrier and the catalyst. CuKα was used as an X-ray source to perform X-ray power diffraction in the range of 20~80°.
Experimental equipment
The hybrid SNCR/SCR reactor used in this study was designed as shown in , and experimental conditions of SCR in hybrid SNCR/SCR are given in . Simulated gas of the hybrid SNCR/SCR reactor was composed of O2 with N2 balance (5%, 10%, 15%, 21%), 10% NO, and 81.5% NH3. The simulated gas was controlled using the MFC (mass flow controller; Brooks 5850e series; Brooks Instrument, Tokyo, Japan), and the MFC regulated flow into the reactor by GMC1000 flow and pressure controller. Simulation gas was completely mixed in the mixing chamber and then guided into both reactors to investigate the characteristics of both SNCR and hybrid SNCR/SCR reactions. Reactor tubes were made of stainless metal.
Table 1. Experimental conditions of SCR in hybrid SNCR/SCR
Simulation gas was flown into each reactor for an hour to reach steady state, and initial concentration of NOx was controlled at 500 ± 30 ppm for face-to-face comparison. Furthermore, NSR (normalized stoichiometric ratio; NH3/NOx) was altered to 1~2.5 based on NOx concentration of 500 ppm. SNCR was driven in a high-temperature reactor in the temperature range of 800~1100 °C, and reactive internal materials were manufactured using quartz. The reduction rate of NOx per reaction temperature and per NSR at 50 °C intervals was examined in the reactor (21 cm in length × 2.6 cm in diameter), and retention time was controlled at approximately 1.67 sec, with flow rate of 4 L/min. In hybrid process, SCR used a honeycomb quadrangle-shaped catalyst (cell density: 36 CPI) of sulfated V2O5-WO3/TiO2 commercialized for application at 350 °C, and the catalyst size was converted according to the SV (space velocity) from 2400 to 9000 hr−1 for analyzing reduction efficiency under the same experimental conditions of the independent SNCR. Concentration of the postreaction gaseous substances NO, NO2, and O2 were analyzed using CombuCheck single-gas monitor (TSI, Shoreview, MN).
Results and Discussions
Comparison of SCR system response between the baseline catalyst and the Mn-added catalyst
The NOx reduction efficiencies by reaction temperature and operating condition are compared between the baseline catalyst and the Mn-added catalyst. The catalyst used in this study is (5 wt.%)Mn-(1 wt.%)V2O5/TiO2, containing 5 wt.% Mn in (1 wt.%)V2O5/TiO2.
Figure presents the NOx reduction efficiencies of the baseline catalyst and the Mn-added catalyst against the change in the reaction temperature, NSR, and O2 concentration. As observed in and , it is verified that although the best NOx reduction efficiency of Mn-added catalyst is approximately 10% lower, it occurs in a low temperature region around 150 °C, which is 100 °C lower than for the baseline catalyst. Also, the NOx reduction efficiency of the Mn-added catalyst is 8% higher than that of the baseline catalyst at 150 °C for 10% O2, as shown in . This sets an important milestone for resolving the issue concerning high activity of NOx released from a fixed source around 300 °C due to the V2O5/TiO2 catalyst. The NOx reduction efficiency decreases after the temperature for the best NOx reduction efficiency, since concentration of NH3 is getting lower after this temperature because of increasing NH3 oxidation activities. As observed in , it is verified that NOx reduction efficiencies of both baseline catalyst and Mn-added catalyst per reaction temperature decrease as O2 concentration increases. This is because as O2 concentration increases and temperature rises, reduction becomes less active whereas NH3 oxidation becomes more active, reducing the NOx reduction efficiency.
NH3 shows more active self-oxidation with respect to the elevation of the reaction temperature in SCR system and reaches a maximum value as NOx conversion rate decreases. It can be verified by measuring NOx concentration at the reactor exit while providing only NH3 to the reactor. plots NOx reduction efficiency against reaction temperature and NSR for the baseline catalyst and Mn-added catalyst. NOx reduction efficiency increases or stays nearly the same when NSR is greater than 1, and it decreases when NSR is smaller than 1. Such result is due to the stoichiometric requirement of NH3 during the catalyst reaction of NOx in SCR system. According to Muzio et al. (Citation1977), NOx reduction efficiency increased to 22% (NSR = 0.3), 75% (NSR = 1.1), and 90% (NSR = 1.6) when discharge condition of combustion gas was set to 300 ppm NOx and 4% O2. Other experiment results also showed similar tendency.
SV, which is closely linked to catalyst performance, is generally defined by the catalyst quantity regarding the gas flow cleared through reaction or as the proportion of the reactor volume occupied by catalyst. In case of a catalyst with good performance, only small quantity of catalyst is required to process simulation gas, enabling high SV operation. and show decline in NOx reduction efficiency with increased SV in reaction temperature range of optimum efficiency when the operation conditions were set to 500 ppm NOx, NSR = 1.2, and 10% O2. Increase in SV forces more simulation gas passing through the catalyst layer per time unit, and NOx activation decreases as catalyst surface contact is shortened. Furthermore, it can be seen that the NOx reduction efficiency is higher in Mn-added catalyst than in the baseline catalyst at SV = 3000 hr−1. This is due to the support of Mn even in equal temperature window and increase of the activation point for reducing NOx in the low temperature region when Mn is added.
Although NOx reduction efficiency against the change in reaction temperature, O2 concentration, and NSR drops by 10% in the Mn-added catalyst, the reaction temperature of the Mn-added catalyst shifts to low temperature region of 150 °C, which is 100 °C lower than the baseline catalyst. Also, NOx reduction efficiency is 8% higher with the Mn-added catalyst than the baseline catalyst. Furthermore, it is shown that NOx reduction efficiency differs between Mn-added catalyst and the baseline catalyst according to the reaction temperature, even in temperature window of optimum efficiency with equal SV. In our study, the role of Mn is not increasing the efficiency of V2O5/TiO2 catalyst, but decreasing the temperature for NOx oxidation, since catalytic activity energy for NOx oxidations with adding Mn is lower than that with adding other components.
Although V2O5/TiO2 catalyst, the current commercial catalyst, displays optimum activation in the high temperature region, it also faces technical and economic challenges such as decreased NOx reduction efficiency due to NH3 oxidation, shortened life of the catalyst, increased overhead, and additional installation cost from heating equipment. This study can resolve such challenges by dropping the gas discharge temperature by 100 °C during SCR application of the catalyst with high activation in low temperature region. Power cost will be reduced, and the catalyst life will be extended. Therefore, hybrid system with low-temperature SCR using Mn-added catalyst seems to be more suitable than the hybrid system using the baseline catalyst.
XRD analysis
To identify the crystal structure form of V2O5/TiO2 monolithic standard catalyst applied in low-temperature SCR system, XRD patterns were analyzed and are shown in . When 1 wt.% V2O5 is contained in anatase TiO2 carrier, a peak due to V2O5 is absent, and this signifies that V2O5 is evenly dispersed. However, V2O5 peak appears at 2θ = 21.787° (110), 25.637° (210), 26.221° (101), 31.138° (400), 32.470° (011), 33.419° (111), and 34.406° (301) when V2O5 content is increased to 10 wt.%. This reflects the work by Reddy et al. (Citation1999), which illustrates that excess V2O5 in forming a single layer of the carrier causes crystallization of V2O5. The result is also similar to Serwicka’s (Citation2000) research, which verified thatthe peak at 2θ = 15~32° signified V2O5 crystal content.
shows the XRD patterns when Mn, a multivalent base metal oxide, is added to the baseline catalyst. XRD peak does not appear when Mn concentration is low; this indicates even dispersion on V2O5/TiO2 monolithic catalyst surface. However, crystal structure of Mn is present in the V2O5/TiO2 monolithic catalyst as Mn concentration increases to 15 wt.%, and XRD peak of manganese oxide (Mn2O3) appears at 2θ = 32.978° (222).
NOx removal characteristics of hybrid SNCR/SCR system with applied low-temperature SCR system
NOx reduction characteristics of hybrid system using low-temperature SCR considering economic aspect of power cost and catalyst life span are evaluated. Experimental conditions are all equivalent to former hybrid systems, with the only exception that reaction temperature of the SCR system using 5 wt.% Mn in (1 wt.%)V2O5/TiO2 was set to 150 °C.
plots NOx reduction characteristics of hybrid system against SNCR system reaction temperature and NSR change under conditions of 5% O2 and low-temperature SCR system with SV = 2400 hr−1. Reaction temperature of SNCR is within the range of 850~1050 °C, and NOx reduction efficiency of hybrid system is above 97% when NSR is greater than or equal to 1.0.
Figure 5. NOx reduction characteristics as a function of temperature and NSR in hybrid SNCR-SCR using low-temperature SCR.
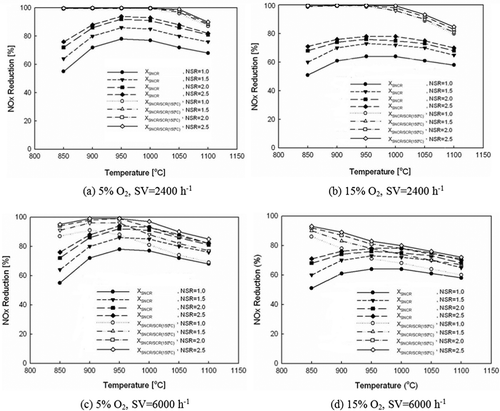
When operation temperature of SNCR system is low at 850 °C, NOx concentration increases in low-temperature SCR system, and when operation temperature of SNCR system rises to 950 °C, NOx amount to be reduced decreases in low-temperature SCR system. This achieves extension of the catalyst life span used in the hybrid system.
Furthermore, NOx reduction efficiency in SNCR system increases as NSR increases, so NOx amount to be reduced in low-temperature SCR system decreases. When SNCR system reaction temperature is 1100 °C and low-temperature SCR system reaction temperature is 350 °C, NOx reduction efficiency of the hybrid system with NSR = 1.0~2.5 drops by 10~12% when compared with 950 °C SNCR system and 150 °C SCR hybrid system. This is due to decrease in total NOx reduction efficiency as NH3 is used up through oxidation in the high temperature region above 1100 °C and lacks the capability as a reducing agent in the low-temperature SCR system.
To evaluate the effect of O2 concentration on the hybrid system, NOx reduction efficiency at 15% O2 is plotted in against the efficiency at 5% O2 in , which is the optimum condition for NOx reduction. All variables except O2 concentration are equivalent between and b. Although reduction characteristics between and b seem similar, NOx reduction efficiency shows 13~16% drop in optimum temperature region of SNCR system as O2 concentration increases from 5% to 15%, increasing NOx amount to be reduced in the low-temperature SCR system. Such variation in reduction efficiency according to the O2 concentration is suspected to have an influence on the life span of the low-temperature SCR catalyst.
For evaluating effect of low-temperature SCR system SV on the hybrid system, NOx reduction efficiencies with SV from 2400 to 6000 hr−1 are plotted in and . presents NOx reduction characteristics of hybrid system against the SNCR system reaction temperature and NSR change at 5% O2. NOx reduction efficiency of hybrid system at 850 °C SNCR system is shown as 87% when NSR = 1.0, 91% when NSR = 1.5, and 94~95% when NSR = 2.0~2.5. When SNCR system is in optimum operating temperature, NOx reduction efficiency of hybrid system is shown as 88% when NSR = 1.0 and above 96% when NSR = 1.5~2.5. So, total NOx reduction efficiency with NSR greater than 1.5 does not vary much even when low-temperature SCR system SV is increased from 2400 to 6000 hr−1.
Comparing the SV = 2400 hr−1 hybrid system of low-temperature SCR system with identical conditions, the total NOx reduction efficiency shows clear drop of 3~18% as NSR changes from 1.0 to 2.5 at SNCR system reaction temperature of 1000 °C. The efficiency clearly drops by 9~22% at 1050 °C SNCR system and 5~18% at 1100 °C SNCR system. This is speculated to be caused by NH3 oxidation occurring in high temperature region above 1000 °C, which does not occur under 950 °C for SNCR system.
and compare NOx reduction efficiency according to the low-temperature SCR system SV with O2 concentration of 15%. As NSR changes from 1.0 to 2.5, it can be seen that the total efficiency drops by 7~13% in hybrid system at 850 °C, 11~21% in 900 °C SNCR system, 17~28% in 950 °C SNCR, 20~29% in 1000 °C SNCR, 17~28% in 1050 °C SNCR, and 13~20% in 1100 °C SNCR, showing distinct differences throughout the entire temperature window of SNCR system, unlike in and . This is because there are both the effect of SV increase and more active NH3 oxidation due to increased O2 concentration.
Conclusions
Denitrification characteristics of the hybrid SNCR/SCR system using Mn-V2O5/TiO2 monolithic catalyst in SCR process are as follows.
First, although Mn-added catalyst is approximately 10% lower in NOx reduction efficiency compared with V2O5/TiO2 monolithic standard catalyst, the reaction temperature window shifts to low temperature region of 150 °C, which is approximately 100 °C lower than the standard catalyst. Also, NOx reduction efficiency is 8% higher in the Mn-added catalyst at 150 °C with 10% O2.
Second, the highest NOx reduction efficiency of Mn-added monolithic low-temperature catalyst is found in (5 wt.%)Mn-(1 wt.%)V2O5/TiO2 monolithic catalyst at 81%, which is 14% less than the standard catalyst, but the reaction temperature window shifts to low temperature region of 150 °C.
Third, after examining XRD patterns of V2O5/TiO2 monolithic standard catalyst including a multivalent base metal oxide of Mn, even dispersion on the catalyst surface is verified from absence of XRD peak in case of small amount of Mn; in case of 15 wt.% Mn, XRD peak of manganese oxide (Mn2O3) appears at 2θ = 32.978° (222) as Mn crystal structure in V2O5/TiO2.
Fourth, (1 wt.%)V2O5/TiO2 monolithic standard catalyst presents two reduction peaks at 570 and 657 °C. A major reduction peak appears at 595 °C in case of 5 wt.% Mn-added catalyst, but it still includes the reduction peaks at 570 and 657 °C present in the monolithic standard catalyst.
Fifth, NOx reduction characteristics of the hybrid system using low-temperature SCR is evaluated considering economic aspects of power cost and catalyst life span. At 5% O2 and SV = 2400 hr−1 of the low-temperature SCR system (150 °C), reaction temperature of SNCR is within the range of 850~1050 °C, and total NOx reduction efficiency of the hybrid system is over 97% when NSR is above 1.0. NOx reduction efficiency drops by 13~16% at optimum temperature in SNCR system as O2 concentration increases from 5% to 15%, increasing NOx amount to be reduced in the low-temperature SCR system. To evaluate the effect of low-temperature SCR system SV on the hybrid system, NOx reduction efficiency is measured when SV increases from 2400 to 6000 hr−1. The NOx reduction efficiency is 91~95% even when low-temperature SCR system SV is increased from 2400 to 6000 hr−1 when NSR is above 1.5.
Additional information
Notes on contributors
Sung-Woo Choi
Sung-Woo Choi is a Professor and Sang-Ki Choi is a lecturer at the Department of Environmental Science at KMU.
Sang-Ki Choi
Sung-Woo Choi is a Professor and Sang-Ki Choi is a lecturer at the Department of Environmental Science at KMU.
Hun-Kyun Bae
Hun-Kyun Bae is a Professor at the Department of Global Environment at KMU.
References
- Bosch, H., and F. Janssen. 1988. Catalytic reduction of nitrogen oxides; a review on the fundamentals and technology. Catal. Today 2:369–532.
- Chen, J.P., and R.T. Yang. 1992. Role of WO3 in mixed V2O5-WO3/TiO2 catalysts for selective catalytic reduction of nitric oxide with ammonia. Appl. Catal. A 80:135–148. doi:10.1016/0926-860X(92)85113-P
- Chen, Z.H., Q. Yang, H. Li, X.H. Li, L.F. Wang, and S.C. Tsang. 2010. Cr-MnOx mixed-oxide catalysts for selective catalytic reduction of NOx with NH3 at low temperature. J. Catal. 276:56–65. doi:10.1016/j.jcat.2010.08.016
- Choo, S.T., S.D. Yim, I.S. Nam, S.W. Ham, and J.B. Lee. 2003. Effect of promoters including WO3 and BaO on the activity and durability of V2O5/sulfated TiO2 catalyst for NO reduction by NH3. Appl. Catal. B 44:237–252. doi:10.1016/S0926-3373(03)00073-0
- Gullet, B.K., P.W. Groff, M.L. Lin, and J.M. Chen. 1994. NOx removal with combined selective catalytic reduction and selective noncatalytic reduction: Pilot-scale test results. J. Air Waste Manage. Assoc. 44:1188–1194. doi:10.1080/10473289.1994.10467313
- Koh, H.L., and H.K. Park. 2013. Characterization of MoO3-V2O5/Al2O3 catalysts for selective catalytic reduction of NO by NH3. J. Ind. Eng. Chem. 19:73–79. doi:10.1016/j.jiec.2012.07.003
- Lietti, L., I. Nova, G. Ramis, L. Dall’Acqua, G. Busca, E. Giamello, P. Forzatti, and F. Bregani. 1999. Characterization and reactivity of V2O5-MoO3/TiO2 De-NOx SCR catalysts. J. Catal. 187:419–435. doi:10.1006/jcat.1999.2603
- Long, R.Q., and R.T. Yang. 2000. Selective catalytic reduction of NO with ammonia over V2O5 doped TiO2 pillared clay catalysts. Appl. Catal. B 24:13–21. doi:10.1016/S0926-3373(99)00092-2
- Lyon, R.K. 1975. Method for the reduction of the concentration of NO in combustion effluents using ammonia. U.S. patent no. 3,900,554, 1975.
- Miller, C.A., and R.K. Srivastava. 2000. The combustion of Orimulsion and its generation of air pollutants. Prog. Energy Combust. Sci. 26:131–160. doi:10.1016/S0360-1285(99)00014-3
- Miller, J.A., and C.T. Bowman. 1989. Mechanism and modeling of nitrogen chemistry in combustion. Prog. Energy Combust. Sci. 15:287–338. doi:10.1016/0360-1285(89)90017-8
- Muzio, L.J., J.K. Arand, and D.P. Teixeira. 1977. Gas phase decomposition of NO in combustion products. Proc. Combust. Inst. 16:199–208. doi:10.1016/S0082-0784(77)80325-1
- Nam, C.M., and B.M. Gibbs. 2000. Selective noncatalytic reduction of NOx under diesel engine conditions. Proc. Combust. Inst. 28:1203–1209. doi:10.1016/S0082-0784(00)80331-8
- Nova, I., L. Dall’Acqua, L. Lietti, E. Giamello, and P. Forzatti. 2001. Study of thermal deactivation of a de-NOx commercial catalyst. Appl. Catal. B 35:31–42. doi:10.1016/S0926-3373(01)00229-6
- Reddy, B.M., I. Ganesh, and B. Chowdhury. 1999. Design of stable and reactive vanadium oxide catalysts supported on binary oxides. Catal. Today 49:115–121. doi:10.1016/S0920-5861(98)00415-5
- Roy, S., B. Viswanath, M.S. Hegde, and G. Madras. 2008. Low-temperature selective catalytic reduction of NO with NH3 over Ti0.9M0.1O2 (M=Cr, Mn, Fe, Co, Cu). J. Phys. Chem. C 112:6002–6012. doi:10.1021/jp7117086
- Serwicka, E.M. 2000. Surface area and porosity, X-ray diffraction and chemical analyses. Catal. Today 56:335–346. doi:10.1016/S0920-5861(99)00293-X
- Sorrentino, A., S. Rega, D. Sannino, A. Magliano, P. Ciambelli, and E. Santacesaria. 2001. Performances of V2O5-based catalysts obtained by grafting vanadyl tri-isopropoxide on TiO2-SiO2 in SCR. Appl. Catal. A 209:45–57. doi:10.1016/S0926-860X(00)00742-0
- Urbas, J., and J.M. Boyle. 1998. Design, optimization and economic analysis of SNCR/SCR hybrid on a utility boiler in the ozone transport region. Presented at the American/Japanese Flame Research Committees International Symposium, Washington, D.C., July 9, 1997.
- Wendt, J.O.L., W.P. Linak, P.W. Groff, and R.K. Srivastava. 2001. Hybrid SNCR-SCR technologies for NOx control: Modeling and experiment. AIChE J. 47:2603–2617. doi:10.1002/(ISSN)1547-5905
- Wu, Z.B., B.Q. Jiang, and Y. Liu. 2008. Effect of transition metals addition on the catalyst of manganese/titania for low-temperature selective catalytic reduction of nitric oxide with ammonia. Appl. Catal. B 79:347–355. doi:10.1016/j.apcatb.2007.09.039