Abstract
Commercial activated carbon is a highly effective absorbent that can be used to remove micropollutants from water. As a result, the demand for activated carbon is increasing. In this study, we investigated the optimum manufacturing conditions for producing activated carbon from ligneous wastes generated from food processing. Jujube seeds and walnut shells were selected as raw materials. Carbonization and steam activation were performed in a fixed-bed laboratory electric furnace. To obtain the highest iodine number, the optimum conditions for producing activated carbon from jujube seeds and walnut shells were 2 hr and 1.5 hr (carbonization at 700°C) followed by 1 hr and 0.5 hr (activation at 1000°C), respectively. The surface area and iodine number of activated carbon made from jujube seeds and walnut shells were 1,477 and 1,184 m2/g and 1,450 and 1,200 mg/g, respectively. A pore-distribution analysis revealed that most pores had a pore diameter within or around 30–40 Å, and adsorption capacity for surfactants was about 2 times larger than the commercial activated carbon, indicating that waste-based activated carbon can be used as alternative.
Implications:
Wastes discharged from agricultural and food industries results in a serious environmental problem. A method is proposed to convert food-processing wastes such as jujube seeds and walnut shells into high-grade granular activated carbon. Especially, the performance of jujube seeds as activated carbon is worthy of close attention. There is little research about the application of jujube seeds. Also, when compared to two commercial carbons (Samchully and Calgon samples), the results show that it is possible to produce high-quality carbon, particularly from jujube seed, using a one-stage, 1,000°C, steam pyrolysis. The preparation of activated carbon from food-processing wastes could increase economic return and reduce pollution.
Introduction
Activated carbon is used widely to remove organic pollutants from drinking water and wastewater and to remediate water, due to its high surface area (>1000 m2/g) (Cheremisinoff and Ellerbusch, Citation1978; Mahajan et al., Citation1980). Inexpensive substances with high carbon content and low inorganic content are potential raw materials for activated carbon production. The most frequently used raw materials for manufacturing activated carbon are coal (Chattopadhyaya et al., Citation2006; Jibril et al., Citation2007; Pietrzak et al., Citation2007), wood wastes (Girods et al., Citation2009), lignite, pistachio nut shells (Lua and Yang, Citation2005), corncobs (Cao et al., Citation2006), coconut shells (Achaw and Afrane, Citation2008), walnut shells (Kim et al., Citation2001; Martinez et al., Citation2006), mango pits (Elozalde-Gonzalez and Hernandez-Montoya, Citation2007), tobacco stems (Li et al., Citation2008), coffee bean husks (Baquero et al., Citation2003), cherry stones (Oilvares-Marin et al., Citation2007), olive pits (Lafi, Citation2001; Stavropoulos and Zabaniotou, Citation2005), and sawdust (Ismadji et al., Citation2005).
The adsorptive characteristics of activated carbon depend on the structure of the raw material and its production (Heschel and Klose, Citation1995). Activated carbon can be manufactured by physical or chemical activation. In general, physical activation comprises a carbonization and activation step. Steam and carbon dioxide are the most common activating reagents in physical activation, significantly influencing the porosity of the activated carbon.
Chemical activation in manufacturing activated carbon usually entails a single step, for which zinc chloride, phosphoric acid, or potassium hydroxide can be used as the activating reagent (Rodriguez-Reinoso et al., Citation2000). However, the chemical activation can introduce impurities such as Zn and P, depending on the chemical agent used, and can result in high operating cost due to the addition of chemicals. Therefore, we adapt the physical activation to make clean activated carbon without incorporation of any mineral impurities and produce essentially microporous carbon.
Many groups have examined low-cost alternatives to commercial carbon that are derived from fruit stones or agricultural by-products, because such materials are generally inexpensive (Achaw and Afrane, Citation2008; Gergova et al., Citation1993; Kim et al., Citation2001; Lua and Yang, 2001). In Korea, jujube seeds and walnut shells that are generated from food processing are discarded as waste materials. These remnants have many properties that render them potentially suitable raw materials for the production of activated carbon. However, the production of activated carbon using jujube seeds as a raw material has not been reported.
The main purposes of this study were to determine the feasibility of producing activated carbon from jujube seeds and to analyze its physicochemical characteristics. Also, we compared its performance with walnut shells verified as feasible activated carbon under the same manufacuring facility and recipe. We characterized the pore structure of our activated carbon samples to gain insight into their adsorptive properties. In addition, we examined the influence of water vapor activation, final temperature, soak time, and water dose on the characteristics of the high-surface-area activated carbon that was produced from these raw materials.
Materials and Methods
Materials samples
Walnut shells and jujube seeds were obtained from H Confectionary and Foods Co. Ltd. (Korea), where they had been produced as waste products from processing food. The starting materials were selected manually, cleaned with deionized water, dried at 110°C, and ground to particles that were smaller than 5 mm. In addition, two commercially available activated carbon products (SLS-100 and F400) were supplied by Samchully Activated Carbon Co. Ltd (Korea) and Calgon Mitsubishi Co. Ltd. (Japan), respectively, and as reference materials.
The carbon content of walnut shells and jujube seeds was 46.4% and 44.3%, whereas that of walnut shells-based and jujube seeds-based activated carbon was 89.1% and 85.5%, respectively. Also, the moisture of raw materials was 13 ± 2% and that of walnut shells-based and jujube seeds-based activated carbon was 3.4% and 4.2%, respectively.
Carbonization and steam activation
Carbonization and activation of the raw materials were performed in a fixed electric furnace that was equipped with a retort (Lindberg/Blue M, Waterton, WI). We pyrolyzed and activated a 50-g sample of raw material by heating it in a nitrogen gas atmosphere at various temperatures between 600°C and 1000°C for a carbonization time of 1 to 4 hr. After pyrolysis, the furnace was cooled to between 100°C to 200°C, and the carbonized materials were allowed to cool for several minutes and then moved to a desiccator. Experiments were conducted in triplicate to ensure a coefficient of variation (CV) of less than 5%.
The activation process was conducted by steam activation. While the furnace was maintained at the desired temperature under nitrogen gas, water was pumped into the gas flow line and carried into the retort by the nitrogen. A peristaltic pump was used to effect a constant water flow rate of 7.5 mL/min (Gilson, Model Miniplus II). High-purity nitrogen was introduced into the furnace at 400 mL/min as a carrier gas.
Iodine number
Iodine number is usually used to evaluate the adsorptive capacity of activated carbon. The adsorption of iodine from aqueous solution was used to compare the surface areas of the activated carbon samples. Iodine number is defined as the number of milligrams of iodine that is adsorbed by 1 g of adsorbent when the iodine concentration of the residual filtrate is 0.02 N (McKay, Citation1996). The residual iodine concentration was determined by titration with sodium thiosulfate solution (Gergova et al., Citation1994). Three measurements were taken for each sample, and the average values are shown; the relative CV for each mean value is shown as an error bar.
Specific surface area and pore size distribution
For the analysis of physical and adsorptive characteristics, the jujube seeds-based and walnut shells-based activated carbons prepared under the optimal production conditions (carbonization and activation temperature: 700°C and 900–1000°C) were used. Adsorption–desorption isotherms of the activated carbon samples were constructed using a Quantacrome Autosorb 1 (Quantachrome, Syosset, NY) with nitrogen gas as the adsorbate. N2-specific surface areas were determined from the isotherms by Brunauer–Emmett–Teller (BET) equation (Guo and Lua, Citation2002):
The t-plot method was used to calculate the pore volume, whereas pore size distribution was determined per the Barrett–Joiner–Halenda method (Gregg and Sing, Citation1982). The volumes and surface area of micropores at relative pressure up to were obtained using the Dubinin–Raadushkevich equation (Nguyen and Do, Citation2001):
The surface area was determined from three measurements, and the results that are shown are the average values. The relative CV values were calculated for each mean value and are indicated by error bars.
Surface morphology by scanning electron microscopy (SEM)
The surface morphology of the activated carbon that was produced from jujube seeds and walnut shells was examined by scanning electron microscopy (SEM; Stereoscan 400, Leica Cambridge Ltd.). SEM allows one to examine directly on the surface of activated carbon microstructural changes that occur as a result of the acid treatment step. Activated carbon samples were embedded in epoxy resin to prepare polished sections.
Adsorption equlibrium for phenol and surfactants
Isotherms were performed at 25°C using the batch bottle-point technique. A carbon sample of 0.5 g was placed into each bottle and 100 mL of single adsorbate aqueous solution with initial concentrations of 0.005–1 mg/L for phenol (molecular weight: 94.1 g, Junsei Co., Japan) and 0.5–3 mg/L for surfactants (dodecyl bezene sulfonic acid sodium salt, molecular weight: 345.5 g; Junsei Co., Japan). The initial pH was 6.0 for phenol and 5.8 for surfactnats. Solutions were not buffered, to avoid adsorption competition between organic and buffer. Bottles were shaken at 250 rpm for 3 days before sampling, using a shaker (J-USRC, Jisico Co., Korea). Preliminary kinetic experiments indicated that adsorption equilibrium was reached in less than 3 days for all the activated carbons. All the samples were filtered using a 0.25-μm filter syringe. For the determination of phenol in water samples, high-performance liquid chromatography (HPLC; Merck Hitachi Co., Japan) coupled with diode-array detection (DAD; L-7450A) was used. LiChrospher 100 RP-18 column (125 mm × 4 mm × 5 μm, Merck Co. USA) was used and the mobile phase was acidified distilled water (pH 2.2 using H3PO4) and acetonitrile (60:40, v/v). Also, the best HPLC detection of surfactants used in this study was achieved in the LiChrospher 100 RP-8 column (125 mm × 4 mm × 5 μm, Merck Co., USA) at a temperature of 35°C. The initial mobile phase consisted of 90% solvent A (methanol) and 10% solvent B (9.2 mg/L of NaClO4 in water). The concentration of solvent A decreased to 20% in 25 min using the elution gradient. The flow rate of mobile phase was maintained at 1 mL/min.
The Freundlich model is an empirical equation based on adsorption on a heterogeneous surface. It is given by the following equation:
Results and Discussion
Effect of carbonization time and temperature
Iodine removal by activated carbon is an indication of its ability to adsorb low-molecular-weight compounds. Carbon that removes a high percentage of iodine normally has a high surface area; thus, a greater degree of iodine adsorption reflects a higher surface area and a largely micro- and mesoporous structure (Gergova et al., Citation1993). To determine the optimal carbonization temperature and contact time to maximize adsorption, we evaluated various carbonization temperatures; the adsorption capacities of activated carbon from jujube seeds and walnut shells at various carbonization temperatures are shown in . When choosing carbon to adsorb contaminants, a high capacity for iodine adsorption is essential.
Figure 1. Effect of temperature and reaction time on carbonization: (a) jujube seeds and (b) walnut shells.
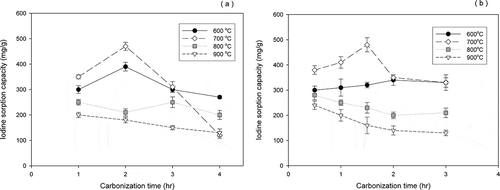
The iodine adsorption of jujube seed-based and walnut shell-based carbons declined with increasing carbonization time at 800°C and 900°C. The relatively high temperature resulted presumably in the thermal degradation of the formed activated carbon (Kim et al., Citation2001). However, both activated carbons had the highest iodine adsorption (approximately 480 mg/g) at a carbonization temperature of 700ºC. Also, the average iodine adsorption of the 2 types of activated carbon that were carbonized at 600°C was 330 mg/g, which was significantly higher than that of activated carbon that was produced at 800°C and 900°C (average 210 mg/g). High temperature adversely affects carbon structure, because the heat shrinkage of the carbon structure decreases the surface area and pore volume (Hayashi et al., Citation2000; Yang and Qiu, Citation2010).
As shown in , the increase in carbonization time did not improve iodine adsorption. At a carbonization temperature of 600°C to 700°C, the iodine adsorption of both activated carbons rose early during carbonization (within 2 hr) but plateaued or fell with time. That is, under extended activation, the microporous structure of the produced activated carbon deteriorates and turns into macropores. When iodine adsorption capacity peaked at 700°C for both types of activated carbon, the optimal carbonization time of the jujube seeds and walnut shells was 2.0 hr and 1.5 hr, respectively.
Although we cannot explain this phenomenon, a study has demonstrated that the pyrolysis of corncobs under an N2 stream has three distinct stages by carbonization temperature: low (373–523 K), medium (523–673 K), and high (673–1273 K) (Chang et al., Citation2000). The resulting chars became richer in carbon and had a fundamentally porous structure at carbonization temperatures above 673 K (or 400°C)—conditions that we adopted in this study.
Effect of activation time and temperature
An earlier report has shown that soak time and temperature during pyrolysis significantly influence the quality of activated carbon (Hayashi et al., Citation2000). However, in our study, the differences in burnoff and soak time for jujube seeds (< 10%) and walnut shells (< 8%) at a constant temperature under an N2 stream were negligible (). Burnoff rose slightly with increasing carbonization temperature for jujube seed-based and walnut shell-based carbon, indicating that high temperatures reduce the activation time of burnoff. The burnoff value for walnut shells was slightly (2%) higher than that of jujube seeds at the same temperature. Gergova et al. (Citation1994) reported that the surface structures of carbon and iodine numbers changed by soak time.
Figure 2. Effect of soak time and temperature on activation: (a) jujube seeds and (b) walnut shells.
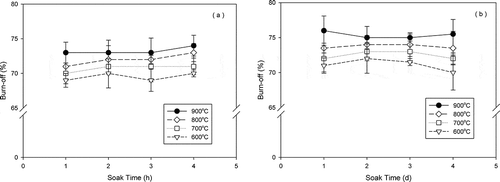
shows the burnoff and iodine number as a function of temperature for the raw materials (jujube seeds and walnut shells). A 10-mL aliquot of deionized (DI) water was prepared as an activating agent, which yielded tremendous reactivity. The burnoff and iodine number values rose with increasing carbonation temperature in the presence of DI water. Although iodine number peaked at 700°C for jujube seed (377 ± 83 mg/g)- and walnut shell (383 ± 35 mg/g)-based carbons under the N2 stream only, it climbed with increasing carbonization temperatures for jujube seed-based carbon (957 ± 125 mg/g at 1000°C) and peaked (883 ± 31 mg/g) at 900°C for walnut shell-based carbon under an N2/DI water stream. Because the reactivity of carbon increased with water evaporation at all carbonization temperatures (Gergova et al., Citation1993; Rodriguez-Reinoso et al., Citation2000; Stavropoulos and Zabaniotou, Citation2005), the adsorption of iodine rose. Also, high values of burnoff demonstrated in this study are caused by the calculation based on raw materials, not on carbonized materials.
Figure 1. Burnoff and iodine numbers at various temperatures in the production of jujube seed-based and walnut shell-based carbon
Compaing production conditions between activated carbon developed in this study and commercial activated carbons, coal- and wood-based materials pyrolize at 600–900ºC and the created char is activated at temperature above 600–1200ºC, blasted by steam. Similar to commercial activated carbon, the carbonization and activation of activated carbons in this study took place at 700ºC and 900–1000ºC, respectively.
Effect of the dose of water used for activation
The development of pore volume during activation was examined over various doses of DI water at a fixed temperature (700°C) and reaction time (2 hr and 1.5 hr). describes the characteristics of the activation for jujube seeds and walnut shells. The specific surface area and iodine number rose with increasing doses of water up to 80 mL proportionally with the amount of water vapor that was injected. This result implies that the carbonized material was highly reactive with water vapor, effecting the development of a comprehensive porous structure and a relatively large specific surface area. The disparate iodine adsorption capacities and specific surface areas for the two materials under the same processing conditions resulted from differences in reactions between the raw materials and water vapor—denser microporous structures of carbides render them more suitable as substrates for the production of activated carbon. The elemental analysis of waste-based activated carbons was significantly similar: C 98%, O 1%, H + N 1%.
Figure 1. Characteristics of activated carbon made from jujube seeds (carbonization temperature 700 °C and time 2 hr) and walnut shells (carbonization temperature 700 °C and time 1.5 hr) at various water doses
Pore size distribution
shows the distribution of pore sizes for activated carbons from jujube seeds and walnut shells and two commercial activated carbon samples from Samchully and Calgon. Few pores that were larger than 50 Å were present, except for the jujube seed-based activated carbon, which had the largest average pore size, followed by that produced from walnut shells and F-400 (Calgon) and SLS-400 (Samchully). These results indicate that steam activation creates a sufficient amount of mesopores that are 30–40 Å. The specific surface areas of the 4 activated carbon samples were 1477 m2/g for jujube seed, 1184 m2/g for walnut shell, 945 m2/g for F-400, and 952 m2/g for SLS-100.
Figure 3. Pore distributions (a) of four activated carbon samples, including two commercial activated carbon samples and (b) at various water doses.
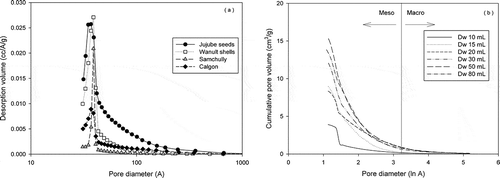
shows the cumulative pore volumes of activated carbon from jujube seeds, based on the amount of DI water, at the same carbonization temperature and activation time. As the amount of DI water increased to 50 mL, the cumulative volume of mesopores rose, because mesopores developed sharply on vigorous reaction of carbides and water vapor.
Scanning electron micrographs
The activated carbons that were prepared by water vapor pyrolysis under optimal processing conditions were examined by SEM. The microstructures that are observed by SEM can be considered extensions of the nanopores of the activated carbons. As shown in , activated carbon prepared in this study can assume a range of structures, varying in wall thickness, shape, and pore size. The activation process resulted in the creation of pores and the removal of a substantial amount of organic material.
Adsorption equlibrium for phenol and surfactants
The isotherms were described by Freundlich models; the constants obtained according to this model are listed in . All 1/n values are lower than 0.5. This shows proper adsorption equlibrium and favorable multilayer adsorption for both organics. The equilibrium constants for phenol (K) ranged from 26.8 to 36.2 (SLS-100 > walnut shells > jujube seeds > F-400). Those for surfactant ranged from 166 to 467 with the following order: jujube seeds (467) > walnut shells (363) > F-400 (224) > SLS-100 (166).
Figure 1. Estimated freundlich isothrerm constants and adsorption capacity under various concentrations of phenol and surfactants
Based on drinking-water quality standard and wastewater effluent quality standard, adsorption capacities of target contaminants were calculated from the Freundlich isotherm. The adsorption capacity of phenol using jujube seeds was 1.4 times higher than that of commercial activated carbon, and that in walnut shells was 0.8 times higher. In case of surfactant, those in all prepared activated carbons were more than 2 times higher. The adsorption isotherm test results showed that the adsorption capacities of high molecular weight (surfactant) were significantly different while those of low molecular weight (phenol) were relatively less. These results would be caused by the difference in the distribution of meso pore (50˜400 Å) depending on different activated carbons. This result implies that jujube seeds-based activated carbon has a relatively higher portion of meso pores, which is beneficial to adsorb the high-molecular-weight compounds (Hu and Srinivasan, Citation2001). The carbonization and activation process conditions critically affect on the development of pores and, thus, the adsorptive properties of the activated carbons. Activation by water vapor pyrolysis resulted in activated carbon with a high specific surface area.
Based on the results just presented, jujube seeds and walnut shells are excellent raw materials for the production of activated carbon with a high specific surface area and is an interesting alternative to commercial activated carbon commonly used for pollutants removal. From the viewpoint of cost, it is very difficult to compute the manufacturing cost because mass production can reduce significantly the selling price. Merely because the purchasing price of raw materials accounts for 15% of total price, the selling price might be saved more or less when food wastes such as jujube seeds and walnut shells are used as raw materials. However, these precursors shown in this study have demerits such as unstable supply and demand of raw materials. Becuase the jujube seeds and walnut shells are seasonal fruits, the supply of raw materials might be irregular, which can frustrate the mass production.
Conclusion
We investigated the optimal carbonization/activation conditions to produce activated carbon with a high pore volume and a high adsorption capacity by pyrolysis of food processing wastes (jujube seeds and walnut shells). To maximize the iodine adsorption capacity of activated carbon produced from food wastes, the carbonization temperature for both wastes was 700ºC. There is little difference in burnoff and soak time for the two carbons. The optimum activation temperature for the production of high-quality absorbent carbon from waste jujube seeds and walnut shells was 1000 and 900°C, respectively. Increasing the dose of water for activation had a significant impact on the pore structure and the mesopore volume. Obtained activated carbon from the jujube seeds and walnut shells was about 1.7 times larger than the commercial activated carbons such as Samchully and Calgon. Conclusively, the use of waste as adsorbent is an economic alternative and contributes to reduce the environmental contamination.
Additional information
Notes on contributors
Wookeun Bae
Wookeun Bae is a professor and Jongho Kim is a Ph.D. at the Department of Civil and Environmental Engineering, Hanyang University, Ansan, Republic of Korea.
Jinwook Chung
Jinwook Chung is a principal researcher at the R&D Center, Samsung Engineering Co., Suwon, Republic of Korea.
References
- Achaw, O.W., and G. Afrane. 2008. The evolution of the pore structure of coconut shells during the preparation of coconut shell-based activated carbons. Micropor. Mesopor. Mater. 112:284–90. doi:10.1016/j.micromeso.2007.10.001
- Baquero, M.C., L. Giraldo, J.C. Moreno, F. Suarez-Garcia, A. Martinez-Alonso, and J.M.D. Tascon. 2003. Activated carbons by pyrolysis of coffee bean husks in presence of phosphoric acid. J. Anal. Appl. Pyrol. 70:779–84.
- Cao, Q., K.C. Xie, Y.K. Lv, and W.R. Bao. 2006. Process effects on activated carbon with large specific surface area from corn cob. Bioresource Technol. 97:110–15. doi:10.1016/j.biortech.2005.02.026
- Chang, C.F., C.Y. Chang, and W.T. Tsai. 2000. Effects of burn-off and activation temperature on preparation of activated carbon from corn cob agrowaste by CO2 and steam. J. Colloid Interface Sci. 232:45–49. doi:10.1006/jcis.2000.7171
- Chattopadhyaya, G., D.G. Macdonald, N.N. Bakhshi, J.S. Soltan, and A.K. Dalai, A.K. 2006. Preparation and characterization of chars and activated carbons from Saskatchewan lignite. Fuel Process. Technol. 87:997–1006. doi:10.1016/j.fuproc.2006.07.004
- Cheremisinoff, P.N., and F. Ellerbusch. 1978. Carbon Adsorption Handbook. Ann Arbor, MI: Ann Arbor Science.
- Elizalde-Gonzalez, M.P., and V. Hernandez-Montoya. 2007. Characterization of mango pit as raw material in the preparation of activated carbon for wastewater treatment. Biochem. Eng. J. 36:230–38.doi:10.1016/j.bej.2007.02.025
- Gergova, K., N. Petrov, and S. Eser. 1994. Adsorption properties and microstructure of activated carbons produced from agricultural by-products by steam pyrolysis. Carbon 32:693–702. doi:10.1016/0008-6223(94)90091-4
- Gergova, K., N. Petrov, and V. Minkova. 1993. A comparison of adsorption characteristics of various activated carbons. J. Chem. Technol. Biotechnol. 56:77–82. doi:10.1002/jctb.280560114
- Girods, P., A. Dufour, V. Fierro, Y. Rogaume, C. Rogaume, A. Zoulalian, and A. Celzard. 2009. Activated carbons prepared from wood particleboard wastes: Characterization and phenol adsorption capacities. J. Hazard. Mater. 166:491–501. doi:10.1016/j.jhazmat.2008.11.047
- Gregg, S.J., and K.E.W. Sing. 1982. Adsorption, Surface Area and Porosity, 2nd ed. New York, NY: Academic Press.
- Guo, J., and A.C. Lua. 2002. Microporous activated carbons prepared from palm shell by thermal activation and their application to sulfur dioxide adsorption. J. Colloid Interface Sci. 251:242–47. doi:10.1006/jcis.2002.8412
- Hayashi, J., A. Kazehaya, K. Muroyama, and A. P. Watkinson. 2000. Preparation of activated carbon from lignin by chemical activation. Carbon 38:1873–78.doi:10.1016/S0008-6223(00)00027-0
- Heschel, W., and E. Klose. 1995. On the suitability of agricultural by-products for the manufacture of granular activated carbon. Fuel 74:1786–91. doi:10.1016/0016-2361(95)80009-7
- Hu, Z., and M. P. Srinivasan. 2001. Mesoporous high-surface-area activated carbon. Micropor. Mesopor. Mater. 43:267–75. doi:10.1016/S1387-1811(00)00355-3
- Ismadji, S., Y. Sudaryanto, S.B. Hartono, L.E.K. Setiawan, and A. Ayucitra. 2005. Activated carbon from char obtained from vacuum pyrolysis of teak sawdust: Pore structure development and characterization. Bioresource Technol. 96:1364–69. doi:10.1016/j.biortech.2004.11.007
- Jibril, B.Y., R.S. Al-Maamari, G. Hegde, N. Al-Mandhary, and O. Houache. 2007. Effects of feedstock pre-drying on carbonization of KOH-mixed bituminous coal in preparation of activated carbon. J. Anal. Appl. Pyrol. 80: 277–82. doi:10.1016/j.jaap.2007.03.003
- Kim, J.W., M.H. Sohn, D.S. Kim, S.M. Sohn, and Y.S. Kwon. 2001. Production of granular activated carbon from waste walnut shell and its adsorption characteristics for Cu2+ ion. J. Hazard. Mater. 85:301–15. doi:10.1016/S0304-3894(01)00239-4
- Lafi, W.K. 2001. Production of activated carbon from acorns and olive seeds. Biomass Bioenerg. 20:57–62. doi:10.1016/S0961-9534(00)00062-3
- Li, W., L.B. Zhang, J.H. Peng, N. Li, and X.Y. Zhu. 2008. Preparation of high surface area activated carbons from tobacco stems with K2CO3 activation using microwave radiation. Ind. Crop. Prod. 27:341–47. doi:10.1016/j.indcrop.2007.11.011
- Lua, A.C., and T. Yang. 2005. Characteristics of activated carbon prepared from pistachio-nut shell by zinc chloride activation under nitrogen and vacuum conditions. J. Colloid Interface Sci. 290:505–13. doi:10.1016/j.jcis.2005.04.063
- Mahajan, O.P., C. Morenocastilla, and P.L. Walker. 1980. Surface-treated activated carbon for removal of phenol from water. Separ. Sci. Technol. 15: 1733–-52. doi:10.1080/01496398008055619
- Martinez, M.L., M.M. Torres, C.A. Guzman, and D.M. Maestri. 2006. Preparation and characteristics of activated carbon from olive stones and walnut shells. Ind. Crop. Prod. 23:23–28. doi:10.1016/j.indcrop.2005.03.001
- McKay, G. 1996. Use of Adsorbents for the Removal of Pollutants From Wastewater, 39–58. Boca Raton, FL: CRC Press.
- Nguyen, C., and D.D. Do. 2001. The Dubinin–Radushkevich equation and the underlying microscopic adsorption description. Carbon 39:1327–36. doi:10.1016/S0008-6223(00)00265-7
- Olivares-Marin, M., C. Fernandez-Gonzalez, A. Macias-Garcia, and V. Gomez-Serrano. 2007. Porous structure of activated carbon prepared from cherry stones by chemical activation with phosphoric acid. Energy Fuel 21: 2942–49. doi:10.1021/ef060652u
- Pietrzak, R., H. Wachowska, P. Nowicki, and K. Babel. 2007. Preparation of modified active carbon from brown coal by ammoxidation. Fuel Process. Technol. 88:409–15. doi:10.1016/j.fuproc.2006.11.001
- Rodriguez-Reinoso, F., A.C. Pastor, H. Marsh, and M.A. Martinez. 2000. Preparation of activated carbon cloths from viscous rayon. Part II: Physical activation processes. Carbon 38:379–95. doi:10.1016/S0008-6223(99)00119-0;10.1016/S0008-6223(99)00118-9
- Stavropoulos, G.G., and A.A. Zabaniotou. 2005. Production and characterization of activated carbons from olive-seed waste residue. Micropor. Mesopor. Mat. 82:79–85. doi:10.1016/j.micromeso.2005.03.009
- Yang, J., and K. Qiu. 2010. Preparation of activated carbons from walnut shells via vacuum activation and their application for methylene blue removal. Chem. Eng. J. 165:209–17. doi:10.1016/j.cej.2010.09.019