Abstract
This paper presents an effective utilization of slag from acid leaching of coal-waste with a novel approach, namely low-temperature co-melting method, for preparation of sodium silicate (Na2O·nSiO2) using slag from acid leaching of coal-waste as feedstock. It is very interesting that the co-melting reaction temperature of the mixture of Na2CO3 and the feedstock (50˜100 μm) was as low as 850 °C, which was significantly lower than the temperature used in traditional sodium silicate production (1400 °C). The optimum SiO2/Na2O ratio was identified as 7:3 according to the results of thermogravimetry–differential scanning calorimetry (TGA-DSC), ICP-AES, and X-ray diffraction (XRD) analyses. In this condition, the main product was sodium disilicate (Na2O·2SiO2), with water solubility of 85.0%. More importantly, the impurities such as aluminum in the feedstock, which had adverse effect on subsequent treatment, were concentrated almost completely in the filter residue as insoluble sodium alumunosilicates, i.e., Na(Si2Al)O6·H2O. The lower co-melting temperature of this process demonstrates a significant energy-saving opportunity and thus a promising approach for highly effective utilization of coal-waste.
Implications:
Recently, alumina extraction from coal-waste has been extensively investigated and industrial applied in China. However, the slag-containing silica generated from the acid leaching process of coal-waste led to a secondary pollution, which hindered large-scale production. The proposed low-temperature co-melting method for preparation of sodium silicate (Na2O·nSiO2) using slag from acid leaching of coal-waste as feedstock indicated that it is an efficient approach for the recovery of silica from the acid-leached slag of coal-waste with minimal environmental impact.
Introduction
Coal-waste is the largest industrial solid wastes in China (Liu and Liu, Citation2010; Li et al., Citation2010). Nowadays, how to recycle and reuse coal-waste becomes a critical issue for effective resource utilization and environment protection. However, coal-waste has no way to be made use of except for some low-value-added products in China, such as constructive materials and road building materials. And there is still a great amount of coal-waste stack-stored in the open air, leading to land occupation and a series of environmental problems. Nevertheless, coal-waste is a useful resource, since coal-waste consists of about 20˜30% carbon, 15˜40% alumina, and 40˜60% silica. Therefore, the recovery of valuable elements from coal-waste to produce high-value-added products with minimal environmental impact is desired. In this regard, the extraction of alumina and silica from coal-waste can produce high-value chemicals and this kind of technology is in high demand. In our previously research, alumina was successfully extracted using an acid leaching process (Cheng et al., Citation2012); however, after this process, there are still a large amount of slag left, which contains a significant amount of SiO2 and would lead to a secondary pollution if discharged into environment. Therefore, this research will focus on extracting silica using the slag from the acid leaching of coal-waste as feedstock to produce sodium silicate (Na2O·nSiO2; commercially named water glass).
Typically, water glass is prepared by fusing the mixture of Na2CO3 and silica sand (SiO2) at 1100–1450 °C, followed by dissolving the liquid melts in water at 220–245 °C and 27–32 bar (Ismail et al., Citation2009; Carroll et al., Citation1998). Sometimes a hydrothermal method is also used. In this case, water glass aqueous solution is synthesized directly by the reaction of silica sand and an aqueous solution of sodium or potassium hydrate in an autoclave at 200 °C and 20 bar (Trabzuni et al., Citation2011). However, both the above methods are not suitable for sodium silicate production using the feedstock from the acid leaching of coal-waste due to a remainder of 5–10% Al2O3 after the acid leaching process. Fusing a mixture of the feedstock containing aluminum with Na2CO3 at a temperature of 1100˜1450 °C would lead to production of massive insoluble sodium aluminosilicates with high Si/Al ratios (Izumi, Citation2003), resulting in a dramatic decrease of both the solubility and the yield of the product. The other disadvantage was the high energy cost at this temperature. As for the latter method, hydrothermal reaction may lead to the difficulties on the separation of impurities and consequently influence the quality of the product.
In this work, a high-purity Na2O·nSiO2 was prepared via a novel low-temperature co-melting reaction using slag from the acid leaching of coal-waste as the feedstock (referred as “feedstock” thereafter). The co-melting reaction temperature of the mixture of Na2CO3 and the feedstock was determined by thermogravimetry–differential scanning calorimetry (TGA-DSC) combined with inductively coupled plasma atomic emission spectroscopy (ICP-AES) and X-ray diffraction (XRD) analyses. The results indicate that this new method is a promising approach for highly effective utilization of coal-waste.
Materials and Experiment
Feedstock
The coal-waste, kindly supplied by Lu’an Group (Shanxi, China), was grinded to particles with average diameter of about 200 μm and then activated in muffle furnace at 750 °C for 2 hr. The feedstock was obtained from the acidic leaching process of the activated coal-waste according to the method described in our previously published paper (Cheng et al., Citation2012). Aluminum oxide, ferric oxide, and other impurities were extracted using hydrochloric acid and poly-aluminum chloride was obtained consequently. The main composition of the feedstock measured by a PANalytical X-ray fluorescence (XRF) spectrometer (Almelo, The Netherlands) is shown in . The Cl− ions probably came mainly from the remainder of hydrochloric acid in the feedstock.
Table 1. The composition of the feedstock
Co-melting reaction mechanism
To overcome the disadvantages of the traditional water glass preparation mentioned above, a low-temperature co-melting approach was proposed for preparation of sodium silicate. It is clearly seen from the SiO2-Na2O phase diagram () (Paul, Citation1990) that the eutectic temperatures between sodium metasilicate (Na2O·SiO2) and sodium disilicate (Na2O·2SiO2) and between Na2O·2SiO2 and quartz are 840 and 789 °C, respectively. Therefore, in order to form soluble Na2O·nSiO2 (1 ≤ n ≤ 2.7) at the temperature range of 789˜840 °C, a suitable molar ratio of SiO2 and Na2CO3 is necessary to meet SiO2/Na2O ratio within range of 1:1˜7.3:2.7 (the latter ratio corresponds to the composition of the eutectic mixture of Na2O·2SiO2 and quartz).
In our case, the possible reactions are reactions 1 and 2 shown below, whereas reaction 3 could not happen because of the limitation of the SiO2/Na2O ratio (Paul, Citation1990; Kham, Citation2005; Kosminski et al., Citation2006).
In particular, a small amount of Al2O3 in the feedstock will benefit the co-melting of Na2CO3-quartz due to its strong capability of lowering the refractoriness of quartz (Kham, Citation2005). Moreover, minimal additives such as NaCl will also decrease the eutectic temperature of the above co-melting system (Paul, Citation1990; Kham, Citation2005). All these factors make it possible to prepare soluble sodium silicate by low-temperature co-melting of the mixture of the feedstock and Na2CO3.
Sodium silicate preparation
Desired amounts of anhydrous Na2CO3 and the feedstock with different SiO2/Na2O molar ratios were mixed and well grinded to fine powder (diameter ca. 50˜100 μm) in a ball mill and then put in a muffle furnace. The temperature was raised to 850 °C and then kept for 3 hr. Afterwards, the liquid melt was quenched in boiled water and became small solid fragments. Then, the small fragments and water were transferred into a high-pressure reactor and heated to 200 °C with pressure of 13 bar for 3 hr. The obtained liquid mixture was filtered; thus, a Na2O·nSiO2 solution and a filter residue were obtained, respectively.
Characterizing conditions
The chemical composition of the samples was determined by ICP using a PerkinElmer Optima 5300V ICP-AES instrument (Optima 5300V, PerkinElmer, Inc., USA). TGA and DSC analyses were carried out with a simultaneous TGA-DSC thermal analyzer (Netzsch, STA449C; Germany) in Ar atmosphere at a rising rate of 5 °C/min from room temperature to 1000 °C. Fourier transform infrared (FTIR) measurements were carried on with a Nicolet 380 FTIR spectrometer (Thermo Electron Co., USA) from 4000 to 400 cm−1 with KBr pellets. X-ray diffraction (XRD) analysis was performed using a D/max-RB diffractometer (Rigaku, Japan) with graphite crystal monochromized Cu Kα radiation. The X-ray diffraction patterns were obtained at a scan rate of 5°/min.
Results and Discussion
TGA-DSC testing and analysis
To determine the co-melting reaction temperature of the powder mixture of anhydrous Na2CO3 and the feedstock, TGA-DSC analysis of the mixed powder with SiO2/Na2O molar ratios of 1:1, 3:2, 7:3, and 7.3:2.7 was carried out. For comparison, two other samples, SiO2/Na2O 3:2 with 2% NaCl and SiO2/Na2O 7:3 with pure silica instead of the feedstock were tested as well. The samples were labeled as S-1:1, S-3:2, S-7:3, S-7.3:2.7, S-3:2+NaCl, and S-7:3 (pure), respectively. The results are shown in –.
shows the TGA-DSC curves of samples S-7:3 and S-7:3 (pure). It is obviously seen from the TGA curves that the first weight loss of both samples occurred at about 120 °C, corresponding to the weak endothermic peaks on the DSC curves. This was ascribed to the evaporation of the residual crystalline water of Na2CO3 (Kham, Citation2005).
In the case of S-7:3 (pure), the significant weight loss did not happen until 770 °C and the corresponding endothermic peaks presented at 580 and 854 °C, which were related to quartz inversion and the melting of Na2CO3, respectively (Kosminski et al., Citation2006). In addition, a solid-state reaction with release of CO2 occurred between pure SiO2 and Na2CO3 before the co-melting happened according to reaction 1 mentioned above. This was in accordance with Kosminski and the co-workers’ results (Kosminski et al., Citation2006).
It can also be seen from that the co-melting reaction temperature of S-7:3 (pure) was remarkably lower in comparison with the temperature (1100–1450 °C) used in the traditional manufacture of sodium silicate (Ismail et al., Citation2009; Carroll et al., Citation1998). This indicates that the fine particle size (50–100 μm) plays a key role in co-melting reaction at low temperatures, which might be attributed to the sufficient contact between the reactants (Paul, Citation1990). On the contrary, large particles could hardly react with each other before melting at a higher temperature.
Differed from that of S-7:3 (pure), there is no sudden weight loss observed for S-7:3; instead, the weight was lost slowly from 350 to 840 °C. Accordingly, no apparent endothermic or exothermic peak appeared during the weight loss process. The peaks corresponding to either quartz inversion at 573 °C or melting of Na2CO3 at 855 ± 5 °C were also not presented (Kham, Citation2005). This evidently indicates that the existence of the impurities promotes the decrease of both co-melting and solid reaction temperatures. It is believed that the solid-state reaction and co-melting occurred simultaneously for S-7:3. The weak endothermic and exothermic peaks observed at about 830 °C imply that a small melting process and a further reaction occurred subsequently, with no weight loss. This was probably due to the fact that reaction 2 occurred preferably at a lower temperature, whereas reaction 3 might not happen due to the SiO2/Na2O molar ratio at the range of 1˜2.7.
The TGA curves of the samples with SiO2/Na2O molar ratios at the range of 1:1 to 7.3:2.7 are shown in . It is seen that the co-melting reactions of all the samples started at much lower temperature in comparison with that of S-7:3 (pure) in , which is in well accordance to the analysis results from SiO2-Na2O phase diagram. This could also be attributed to the lower eutectic temperature at higher SiO2/Na2O ratios, apart from the influence of the impurities in the feedstock.
Among these samples, S-7:3 shows the lowest reaction temperature compared with those of S-1:1 and S-3:2. On the contrary, S-7.3:2.7 shows a higher co-melting reaction temperature than that of S-7:3, although it is the co-melting point according to the SiO2-Na2O diagram. Ideally, the co-melting of the eutectic mixture with SiO2/Na2O molar ratio of 7.3:2.7 at the eutectic point of 789 °C requires a molecular-level mixing, for instance, the mixture formed by slow-cooling of the corresponding fused liquid. However, it is difficult to satisfy the requirements in the actual system we investigated. Besides, the total weight losses of S-1:1, S-3:2, S-7:3, and S-7.3:2.7 by release of CO2 during the heating were about 23.8%, 19.9%, 16.0%, and 14.3%, respectively, which correspond to the amount decrease of Na2CO3 in the mixture.
The effect of minor addition of NaCl on the co-melting temperature of the sample with SiO2/Na2O molar ratio of 3:2 is shown in . For the sample S-3:2+NaCl, the complete weight loss occurred at 780 °C, which was 70 °C lower than that for sample S-3:2. Although NaCl does not react with silica, it could be used as the melting agent during the reaction. By addition of NaCl, the melting temperature of Na2CO3 would be dramatically decreased due to the existence of the low eutectic temperature (about 640 °C) between NaCl and Na2CO3 (Paul, Citation1990; Kham, Citation2005).
Based on the results of TGA-DSC analysis, the co-melting reaction temperature was set to rise from room temperature to 850 °C by rate of 10 °C/min and then kept for 3 hr to make sure the reaction was complete. Meanwhile, in terms of practical application, it is worth to point out that the amount of the feedstock should be well controlled in practice to satisfy the requirement of the SiO2/Na2O molar ratio in the mixture prior to the co-melting process, since the amount of silica in the feedstock may vary according to various sources of coal-waste.
The chemical composition analysis of the products
lists the chemical composition of the prepared sodium silicate and filter residue from S-3:2. The amounts of Al2O3, Fe2O3, and TiO2 in the filter residue were much higher than those in the feedstock (), and they were all below detection limits in sodium silicate solution. This illustrates that nearly all the impurities were removed and enriched in the filter residue.
Table 2. The composition of the filtrate and residue
More notably, the contents of SiO2 and Na2O in water glass are 60.97 and 36.28, respectively, indicating that Na2O·2SiO2 rather than Na2O·1.5SiO2 was formed during the low-temperature co-melting process of S-3:2. This probably was due to the formation of Na2O·2SiO2 at a lower temperature, as shown in the SiO2-Na2O phase diagram (Paul, Citation1990). Meyer et al. also reported that a glass transition temperature of 741 K existed for Na2Si2O5 synthesized from ultrapure Na2CO3 and SiO2 powders (Meyer et al., Citation2002). Another interesting finding is that titanium in the feedstock was also enriched in the filter residue (˜5%), indicating the possibility of extracting titanium as well.
The XRD analyses for the feedstock, the sodium silicate, and the filter residue of S-3:2 are shown in . The main XRD characteristic peaks for the feedstock () were attributed to α-silica, whereas the XRD patterns for the filtered slag were attributed to sodium hydroaluminosilicate (Na(Si2Al)O6·H2O; ) according to the PDF2 XRD (2004) database. However, no peak corresponding to sodium silicate was observed in , which may be due to the formation of glassy state silicate during the evaporative drying of the sodium silicate aqueous solution.
Figure 5. XRD patterns of the feedstock (a), obtained sodium silicate (b), and filter residue (c) from sample S-3:2.
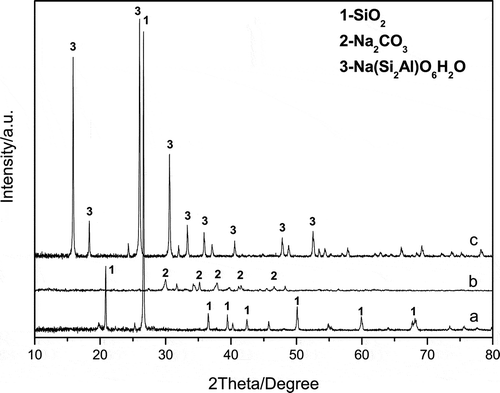
The weak diffraction peaks of Na2CO3 observed in indicate that Na2CO3 was in surplus during the co-melting reaction, which maybe because of the formation of Na2O·2SiO2 at low temperature. Besides, CO2 in ambient air absorbed during the evaporative drying of the sodium silicate aqueous solution could also produce a very small amount of Na2CO3. This is in good accordance with the ICP results in . More importantly, the impurities existed in the feedstock were concentrated in the filter residue; thus, a very pure sodium silicate could be prepared by the co-melting reaction method.
FTIR measurement and analysis
The comparative FTIR spectra of the obtained sodium silicate and filter residue from sample S-3:2 are shown as and B. The broad bands at about 3450 and 1647 cm−1 for both spectra are ascribed to absorption of O–H stretching (Giannopoulou and Panias, Citation2010; Panias et al., Citation2007; Barbosa et al., Citation2000). The bands at around 1450 cm−1 indicate the presence of Na2CO3 in both the sodium silicate and residue (Barbosa et al., Citation2000). The sharp elimination of this band in indicates the existence of some Al2O3 in the filtered residue (Giannopoulou and Panias, Citation2010; Panias et al., Citation2007). There are three main bands associated with different vibrations in the –Si–O–Si– units (Parker and Frost, Citation1996): (a) a Si–O bending vibration at about 450 cm−1 (Barbosa et al., Citation2000; Parker and Frost, Citation1996), (b) 750-800 cm−1 due to symmetric stretching vibration, and (c) the main absorption band at 1200 and 930 cm−1 assigned to the asymmetric stretching vibration. The broadness of band c of indicates the overlapping of the individual absorption bands of the SiQn structural units (where Q represents the bridging oxygen atom in the first coordination sphere of silicon atom, and n denotes the number of bridging oxygen atoms), according to the analysis by Panias and his colleagues (Giannopoulou and Panias, Citation2010; Panias et al., Citation2007). It is in good agreement with his point of view that the maximum absorption band is in the range 980–1020 cm−1 due to the predominance of SiQ2 and SiQ3 structural units over SiQ°, SiQ1, and SiQ4 ones. Besides, the band at the range 980–1020 cm−1 of shifts toward higher wavenumber as a result of the formation of insoluble Na(Si2Al)O6·H2O during the co-melting process and concentration in the filter residue. With Al incorporating in silicate gels, it improved the cross-linking in between silicate chains and favored the structural change from SiQ2 to SiQ3 units. These results are consistent with the ICP and XRD results as well.
Figure 6. Comparative FTIR spectra of sodium silicate (A) and the filter residue (B) obtained from sample S-3:2.
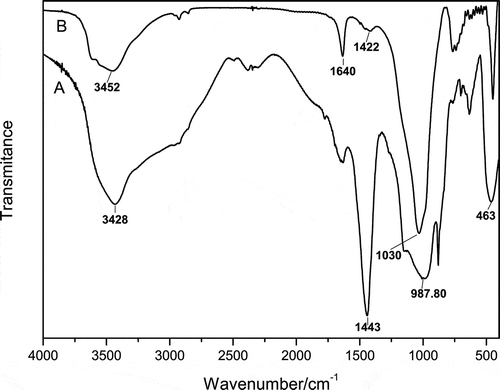
To further investigate the influence of Al on the formation of sodium aluminosilicates, the FTIR spectra of the filter residues from the samples with different SiO2/Na2O molar ratios were characterized, which are shown in . For comparison, the IR spectrum of the residue from calcined S-7:3 at 1400 °C is illustrated in as well. It is clearly seen that the peak denoting the absorption of Al–O–Si shifted from 1030 to 1054 cm−1 with the increase of the SiO2/Na2O molar ratio in the feedstock (Giannopoulou and Panias, Citation2010). It is concluded that the higher Al in the feedstock, the more sodium aluminosilicates formed, and higher temperature would make that even worse.
The solubility of the obtained water glass
The solubility of the silicates produced by the mixture of the feedstock and Na2CO3 with different SiO2/Na2O molar ratios at 850 °C together with that of S-7:3 (1400 °C) are shown in . Apparently, the solubility of the silicates decreases with the increase of the SiO2/Na2O molar ratio. This could be attributed to the formation of more sodium aluminosilicates with the amount increase of Al in the feedstock. This was confirmed by the above-mentioned results.
Table 3. The solubilities (wt.%) of the produced sodium silicates
Furthermore, it can be seen that the fusing process at 1400 °C led to a remarkable drop of the solubility of the obtained product; for instance, it dropped to 54.6% for S-7:3 (1400 °C) in comparing with the high solubility (85%) of S-7:3 (850 °C) owning to the formation of more insoluble salts at 1400 °C. It is further clarified that the temperature for industrial production of sodium silicate from pure silica sand is not suitable for the slag from acid leaching of coal-waste.
presents the XRD pattern of the filtered slag of sample S-7:3 (1400 °C). By comparing with the PDF2 XRD (2004) database, the characteristic diffractions of the residue belong to an insoluble aluminosilicate, Na3.552(Al3.6Si12.4O32)·10.656H2O, in which one Al atom almost binds four Si atoms, much higher than that of the residue obtained at 850 °C. This could be the main reason for the rapid decrease of the solubility for fusing sample S-7:3 at 1400 °C.
Conclusion
A novel approach named low-temperature co-melting reaction was used for preparation of sodium silicate using the slag from acid leaching of coal-waste as the feedstock. The results showed that the co-melting reaction temperature was as low as 850 °C, which was significantly lower than the temperature of 1400 °C used in the traditional sodium silicate production process. The existence of Al in the feedstock decreased the co-melting temperature of the fine powder mixture of the feedstock and Na2CO3 but increased the amount of the insoluble aluminosilicate, Na(Si2Al)O6·H2O. The proper SiO2/Na2O ratio of the mixture was identified to be 7:3, by which the main product was sodium disilicate (Na2O·2SiO2) and the solubility reached 85%. In particular, the impurities such as aluminum and titanium in the feedstock were concentrated in the filter residue; therefore, only trace amount of impurities was detected in the sodium silicate solution, which had no effect on the subsequent treatment. This new method is a promising approach for highly effective utilization of coal-waste.
Funding
The authors wish to thank the financial support from the National High Technology Research and Development Program of China (863 Program, grant no. 2011AA06A103).
Additional information
Notes on contributors
Li Fang
Li Fang is an associate professor, Fangqin Cheng is a professor, and Xiaofang Duan and Rongming Chen are postgraduate students at the State Environmental Protection Key Laboratory of Efficient Utilization Technology of Coal-waste Resources, Institute of Resource and Environment, Shanxi University, Taiyuan City, P.R. China.
References
- Barbosa, V.F.F., K.J.D. MacKenzie, and C. Thaumaturgo. 2000. Synthesis and characterization of materials based on inorganic polymers of alumina and silica: Sodium polysialate polymers. Int. J. Inorg. Mater. 2:309–317. doi:10.1016/S1466-6049(00)00041-6
- Carroll, J.R., W.E. Breitenbach, and W.C. Comb. 1998. Silicate reactor with submerged burners. US Patent, US 5,785,940 (July 28, 1998).
- Cheng, F., L. Cui, J.D. Miller, and X. Wang. 2012 Aluminum leaching from calcined coal waste using hydrochloric acid solution. Miner. Process. Extr. Metall. Rev. 33:391–403. doi:10.1155/2013/352157
- Giannopoulou, I.P., and D. Panias. 2010. Hydrolytic stability of sodium silicate gels in the presence of aluminum. J. Mater. Sci. 45:5370–5377. doi:10.1007/s10853-010-4586-1
- Ismail, G.A., M.M.Abd. El-Salam, and A.K. Arafa. 2009. Wastewater reuse in liquid sodium silicate manufacturing in Alexandria, Egypt. J. Egypt Public Health Assoc. 84:33–49.
- Izumi, Y. 2003. Solubility of Layered Sodium Silicate in Aqueous Solutions. Collected Papers of Nature Sciences, Sugiyama Jogakuen University, Nagoya, Japan, No. 43.http://ir.lib.sugiyama-u.ac.jp/dspace/bitstream/123456789/96/1/%E8%87%AA06%E6%B3%89.PDF.
- Kham, N.S. 2005. Development of methods for the characterization of melting batches. Genehmigte dissertation, Institut für Gesteinshüttenkunde, Aachen, Germany.
- Kosminski, A., D.P. Ross, and J.B. Agnew. 2006. Reactions between sodium and silica during gasification of a low-rank coal. Fuel Process. Technol. 87: 1037–1043. doi:10.1016/j.fuproc.2005.06.007
- Li, C., J.H. Wan, H.H. Sun, and L.T. Li. 2010. Investigation on the activation of coal gangue by a new compound method. J. Hazard. Mater. 179:515–520. doi:10.1016/j.jhazmat.2010.03.033
- Liu, H.B., and Z.L. Liu. 2010. Recycling utilization patterns of coal mining waste in China. Resour. Conserv. Recy. 54:1331–1340. doi:10.1016/j.resconrec.2010.05.005
- Meyer, A., H. Schober, and D.B. Dingwell. 2002. Structure, structural relaxation and ion diffusion in sodium disilicate melts. Europhys. Lett. 59:708–713. http://iopscience.iop.org/0295-5075/59/5/708 doi:10.1209/epl/i2002-00183-2
- Panias, D., I.P. Giannopoulou, and T. Perraki. 2007. Effect of synthesis parameters on the mechanical properties of fly ash-based geopolymers. J. Colloids Surf. A 301:246–254. doi:10.1016/j.colsurfa.2006.12.064
- Parker, R.W., and R.L. Frost. 1996. The application of drift spectroscopy to the multicomponent analysis organic chemicals adsorbed on montmorillonite. Clays Clay Miner. 44:32–40. doi:10.1346/CCMN.1996.0440103
- Paul, A. 1990. Chemistry of Glasses, 2nd ed. London: Chapman and Hall.
- Trabzuni, F.M.S., H.M. El Dekki, and C.C. Gopalkrishnan. 2011. Process for hydrothermal production of sodium silicate solutions and precipitated silicas. US Patent, US 8,057,770B2 (November 15, 2011).