Abstract
Water-emulsified diesel has proven itself as a technically sufficient improvement fuel to improve diesel engine fuel combustion emissions and engine performance. However, it has seldom been used in light-duty diesel engines. Therefore, this paper focuses on an investigation into the thermal efficiency and pollution emission analysis of a light-duty diesel engine generator fueled with different water content emulsified diesel fuels (WD, including WD-0, WD-5, WD-10, and WD-15). In this study, nitric oxide, carbon monoxide, hydrocarbons, and carbon dioxide were analyzed by a vehicle emission gas analyzer, and the particle size and number concentration were measured by an electrical low-pressure impactor. In addition, engine loading and fuel consumption were also measured to calculate the thermal efficiency. Measurement results suggested that water-emulsified diesel was useful to improve the thermal efficiency and the exhaust emission of a diesel engine. Obviously, the thermal efficiency was increased about 1.2 to 19.9%. In addition, water-emulsified diesel leads to a significant reduction of nitric oxide emission (less by about 18.3 to 45.4%). However, the particle number concentration emission might be increased if the loading of the generator becomes lower than or equal to 1800 W. In addition, exhaust particle size distributions were shifted toward larger particles at high loading. The consequence of this research proposed that the water-emulsified diesel was useful to improve the engine performance and some of exhaust emissions, especially the NO emission reduction.
Implications:
The accumulated test results provide a good basis to resolve the corresponding pollutants emitted from a light-duty diesel engine generator. By measuring and analyzing transforms of exhaust pollutant from this engine generator, the effects of water-emulsified diesel fuel and loading on emission characteristics might be more clear. Understanding reduction of pollutant emissions during the use of water-emulsified diesel helps improve the effectiveness of the testing program. The analyzed consequences provide useful information to the government for setting policies to curb pollutant emissions from a light-duty diesel engine generator more effectively.
Introduction
The diesel engine is one of the most useful tools; it has better thermal efficiency than spark-ignition engines. The diesel engine generator is widely viewed as a mean to electrify remote areas, for construction site or emergency power, and so on, when it hasn’t been connected to the centralized power stations (Lee and Scott, Citation2000; Çetinkaya and Karaosmanoglu, Citation2005). However, using fossil fuels as an energy source extensively causes significant amounts of regulated pollutants being emitted, such as carbon monoxide (CO), hydrocarbons (HC), nitrogen oxide (NOX), and particulate matter (PM). Therefore, the quest for an appropriate alternative fuel, which can improve the thermal efficiency and reduce the emission of the engine, is an important project.
Water-emulsified diesel can improve physical or chemical properties of fuel and reduce the existing diesel engine emissions (Lee et al., Citation2011; Lin and Wang, Citation2004; Ghojel and Tran, Citation2010). Water can modify the chemical kinetics and equilibrium concentrations in the combustion products. In addition, the volume of 1 mole liquid water vaporization expands about 1700 times at standard pressure and 373 K. Therefore, the combustion of emulsion droplets is usually accompanied by micro-explosions, which are different with fossil fuel droplets (Kadota et al., Citation2007). When a water-emulsified diesel droplet is heated, its temperature can maintain above the water boiling point and vaporize as in the liquid phase, which was called a “micro-explosion.” Therefore, micro-explosions lead the droplets of fuel to redisperse and then the diameter of fuel drops decreases (Kadota and Yamasaki, Citation2002; Ochoterena et al., Citation2010; Teixeira et al., Citation2013).
Several studies had tested the performance of compression ignition (CI) engines by using water-emulsified diesel as fuel. Ochoterena et al. (Citation2010) reconnoitered the spray behavior studies of emulsion fuel. This test showed that the water-in-diesel emulsion fuels had a little ignition delay, and the soot concentration in the exhaust was lower than when using pure diesel fuel. The results of Alahmer et al. (Citation2010) show that the NOx emissions decreased with increasing water content of emulsion fuels, because the addition of water leads to a local adiabatic flame temperature decline. Armas et al. (Citation2005) investigated the effects on exhaust emission via using water-emulsified fuel. The emissions of HC, NOX, soot, and PM were reduced and the brake thermal efficiency was improved.
Furthermore, some studies had tested different fuel blending, like biodiesel, or pure diesel blended with water, gasoline, or alcohol (Ashok, Citation2011). For example, Kannan and Anand (Citation2011) investigated the performance, emission, and combustion characteristics of the engine under different loading, by using diesel, biodiesel, and biodiesel–diesel–ethanol (diestrol) water micro-emulsion oil as fuel. Consequently, using diestrol–water micro-emulsion oil as fuel produced lower NO and smoke emissions than did pure diesel fuels. However, the CO, carbon dioxide (CO2), and unburned HC emissions increased compared with biodiesel (Özcan and Söylemez, Citation2005). Lin et al. (Citation2012) utilized water–butanol–diesel as fuel and then measured the NOX, PM, and polycyclic aromatic hydrocarbon (PAHs) emissions of a heavy-duty diesel engine generator. Though the PM and total PAHs emissions decreased with raising the n-butanol ratio, the specific fuel consumption and CO emissions increased.
Fine particles and ultrafine particles are the major product of engine combustion. Compared with larger particles, there are many studies that showed that small particles have higher total particle number concentrations, and they tend to absorb more toxic components, have higher deposition efficiency in the respiratory tract, and have larger surface areas (Helfenstein et al., 2008).
Mathis et al. (Citation2005) investigated the influence of diesel engine combustion parameters on primary soot particle diameter. They used a scanning mobility particle sizer (SMPS) to measure the particle number size distribution. The result shows that the soot particle number concentration of engine exhaust by using water–diesel emulsion fuel as fuel was much lower than for diesel fuel. Nevertheless, few studies have yet been carried out for the measurement of particle number concentration, size distribution, and thermal efficiency in the light-duty diesel engine generators running with emulsion fuel. Therefore, this thesis has two main objectives. First, this study investigated the different water content of emulsified diesel in terms of emissions for small diesel engine at different loading. Then it tested the thermal efficiency with different water content of emulsified diesel at different loading.
Materials and Methods
The experimental system included three major systems, the engine generator system, the exhaust gas emission measurement system, and the particle emission measurement system, as shown in . In the experiment, each sampling lasted 2 to 3 min after stabilization of the engine. When testing an engine generator in the laboratory, equivalent performance needs were achieved with the same engine generator brake power output (loading), in using any fuels.
Test engine
The test DI engine generator used for this study is a four-stroke, air-cooled, single-cylinder, direct-injection, compression-ignition, light-duty diesel engine generator (model 186FA, SHIN KOMI), testing at rated power of the generator of 900, 1800, 2700, and 3600W and at rated speed of the engine of 3600 rpm. Thus, the flow rates of exhaust gas of each fuel combustion are not being changed significantly. The properties of the test engine are shown in .
Table 1. General properties of the test engine
Test fuels
Test fuels included premium diesel (WD-0) and water-in-diesel emulsion fuels WD-5, WD-10, and WD-15; the numbers following WD indicate mass percentage of water (for example, WD-5 contains 5 wt% water, 90 wt% premium diesel, and 5 wt% surfactants). The details of the premium diesel fuels used in this study are shown in . The stability of emulsions was tested by using a centrifuge (CN-2060, Hsiangtai, 3000 rpm, 1 hr).
Table 2. Properties of premium diesel
The water-emulsified diesel tests were performed using an emulsifier mixture to prevent the phase separation. The hydrophilic–lipophilic balance (HLB) was 9; the emulsifier mixture was blended with Span 83 (sorbitan sesquioleate, HLB = 3.7) and Tween 80 (polyoxyethylene sorbitan monooleate, HLB = 15.0). The HLB of mixing surfactant is computed by the following equation:
The properties of water-emulsified diesel, including viscosity, higher heating value of fuel (HHV), and lower heating value of fuel (LHV), were measured by a dial-reading viscometer (model LVF, LV-2, Brookfield) and plain jacket bomb calorimeter (model 1341, Parr), respectively.
The viscometers measured the torque required to rotate a disk or bob in a fluid at a known speed. First, put the test liquid into the proper container; the container was in a water bath to control temperature at 25°C. Afterward, the fluid was measured for the viscosity and the values from the viscometer were recorded. The bomb calorimeter is a type of constant-volume calorimeter. The heat of the stainless-steel bomb chamber is transmitted to the water bath and then balance. Then the temperature change after 1 hr is recorded. The temperature of the water allows for calculating calorie content of the fuel.
Engine brake thermal efficiency
Thermal efficiency is the ratio of the output or work done by the working substance in the cylinder at a given time to the input or heat energy of the fuel supplied during the same time. Therefore, the brake thermal efficiency of diesel engines is expressed by eq 2 (Lin et al., Citation2010). The fuel consumption is estimated by measuring and calculating with eq 3 (Lin et al., Citation2010). And the lower heating value of fuels (LHV) and the density of fuel blend were found by following eqs 4 and 5, respectively:
Measurements of exhaust emission
In the experiment, the concentrations of CO, HC, and NO were measured by a real-time multiple exhaust analyzer (BE-1000A, Belltone Ltd.). For the particle number concentration and size distribution measurement, a sample of the tailpipe exhaust was diluted in a hundredfold dilution channel (two-stage, 10 times each stage; consult the CFR 40 Part 1065 for United States) and measured by an outdoor air electrical low pressure impactor (ELPI, Dekati Ltd.). Particles from the exhaust gas were sampled passing a unipolar corona charger. After charging, those electric particles enter a cascade low-pressure impactor, which can detect the signals of current from particle collection. Those signals of currents are converted to the particle number concentration. The size distribution was measured by a cascade impactor of different cuts of particle size. It showed the particle number counts with 12 size cuts for a particle size range of the instrument, which is between 30 nm and 10 μm (without filter stage). Otherwise, ELPI is a near real-time particle size monitor (Marjamäki et al., 2000; Lin et al., Citation2010; van Gulijk et al., Citation2001). The temperature of exhaust gas at the sampling point was the same as the exhaust temperature. However, the temperature of the diluting air was about 20ºC. Therefore, the exhaust property (temperature, pressure, velocity, etc.) was changed in this equipment setup, which might have influenced measurements. Nonetheless, by comparison with the temperature of exhaust to the atmosphere, the sampling temperature at the ELPI inlet is considered negligible.
Moreover, the artificial dilution system might have changed particle emission properties, especially the large particle. And isokinetic sampling is really difficult to do at this measurement system. Therefore, all exhaust emissions sampling were based on the similar rotational speed (3600 rpm) in this study. The flow rates of exhaust gas of each fuel combustion are not being changed significantly. Accordingly, the number concentration and volume concentration of particle emission were the only comparative analyses in this study.
Results and Discussion
Characterization of water-emulsified diesel
The results of the viscosity and the heating value of test fuels are shown in . Those values suggest that the viscosity increases as the water content of emulsified diesel increases. These trends are similar to those reported by Lin and Wang (Citation2003) and Badrana et al. (Citation2011). The viscosity of the emulsion fuels is higher than for diesel; however, the higher viscosity of fuel will not easily be atomized.
Table 3. Properties of water-emulsified diesel
In addition, the heating value of emulsified diesel is decreased as the water content of emulsified diesel increases at the generally bomb calorimeter test, because the water has no capacity to burn. In the combustion section, water is not joining the reaction. Therefore, by comparing with premium diesel, the fuel consumption compensated the loss of heating value of emulsified diesel (Ribeiro et al., Citation2007; Chiaramontia et al., Citation2003).
Fuel consumption and thermal efficiency
The fuel consumption and thermal efficiency are presented in . At a loading condition of 900 W, the fuel consumption and thermal efficiency of net diesel of fuels for WD-0, WD-5, WD-10, and WD-15 are 0.89, 0.85, 0.94, and 0.83 kg/hr and 23.65, 25.37, 25.14, and 28.06%, respectively. The fuel consumption and thermal efficiency of net diesel of fuels (without calculating the water within the emulsified diesel) for WD-0, WD-5, WD-10, and WD-15 are 1.62, 1.54, 1.58, and 1.61 kg/hr and 31.64, 33.91 35.97, and 35.07% at 3600 W, respectively. While using WD-5 as fuel, the net diesel fuel consumption is less than other fuels (WD-0, WD-10, and WD-15) at high loading conditions of the generator. Using WD-15 as fuel, the net fuel consumption is less than for other fuels (WD-0, WD-5, and WD-10) and thermal efficiency of net diesel is greater than for other fuels for low generator loads. Water vaporization will absorb the heat of the compression stroke. However, the micro-explosion leads the droplets of fuel to disperse and then the diameter of fuel drops decreases. The results of the net diesel fuel consumption of WD-5 and WD-15 seem to show no difference because water content of fuels may cause incomplete combustion of the engine at low loading. Comparing with WD-0 fuel, the thermal efficiency of net diesel might be improved about 1.2–19.9% by using water-emulsified diesel as fuel.
Figure 2. Fuel consumption and thermal efficiency of different fuels and generator loads, (a) with water content, and (b) net diesel (subtract water content); sampling time 5 min. Rotational speed was stabilized.
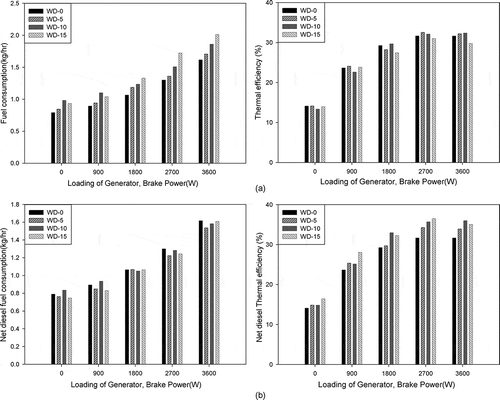
The net diesel consumption of fuel might be decreased, in spite of the fuel consumption being increased by water content of emulsified diesel over the investigated loading range. Similar results have been obtained by other studies (Alahmer et al., Citation2010; Armas et al., Citation2005; Abu-Zaid, Citation2004). When the emulsified diesel is heated, the water in the droplets is vaporized first, because the enthalpy of water vaporization is lower than diesel combustion in the CI engine (Lif and Holmberg, Citation2006). The temperature of liquid water was increased above 270ºC, while the compression stroke of the engine was applying an overpressure and raising the boiling point of liquid water, creating “superheated water.” During the compression stroke, if the temperature of liquid water was over the critical temperature (374ºC), the water-in-oil droplets might explode earlier than the combustion. This phenomenon may possibly cause better atomization of fuels by the continuous hydrocarbon phase to the micro-explosion. Besides, the micro-explosion might let the pyrolytic reaction proceed in the liquid phase. It possibly will dissolve a part of the diesel compounds, and then improve the combustion efficiency (Kadota and Yamasaki, Citation2002).
Characterization of gas emissions
shows the effect of various fuels on exhaust temperature and NO, CO, and HC emissions. The heat absorption of water vaporization can explain the exhaust temperature reduction. Before ignition, due to the evaporation of water, the cylinder temperature becomes lower as the water percentage increases. From the results shown in , suggests that the exhaust temperature of engine was decreased as water content of diesel increased. The results indicated that the exhaust gas temperature of WD-5 has had an insignificant difference with WD-0. This study yielded results similar to other research (Abu-Zaid, Citation2004). Moreover, the result shows that 10 wt% water content can provide more contribution to temperature reduction. Because lots of the heat of the compression stroke of the engine is taken up by water, the exhaust temperature of the engine drops increases with water content of diesel (Ochoterena, Citation2010).
The formation of NOX depends on the temperature of the combustion products while excess oxygen is present in the engine. In , NO emission decreased as the water content in the blend increased. When using WD-10 and WD-15 as fuel, the NO emission concentrations are less than WD-0 and WD-5 for each engine loading. While idling, the average value of NO declines to 113.4, 70.2, and 64.0 ppm for WD-5, WD-10, and WD-15, respectively, from 133.0 ppm with WD-0. The average value of NO is reduced to 1264.2, 961.4, and 874.7 ppm with WD-5, WD-10, and WD-15, respectively, from 1533.6 ppm with WD-0 as the loading was 3600 W. These trends are similar to many research studies (Lin and Wang, Citation2004; Alahmer et al., Citation2010; Ghojel, Citation2006; Qi, Citation2010; Lin, Citation2010).
According to the exhaust temperature and NO emission, the results suggested that higher water content blend fuels can reduce the adiabatic flame temperature, because the water vaporized takes heat away (Park et al., Citation2001). The mixture’s temperature at the end of the compression stroke is decreased with water vaporized, and then reduces the combustion temperature. As a result, engine exhaust NO emission is decreased. Moreover, some research also leads to the conclusion that NOX reduction from fuel injection timing delay and improved injector design is also probably due to a reduced flame temperature (Canfield, Citation1999).
As seen from , while using WD-0 as fuel, the CO concentration is less than for the other fuels (WD-5, WD-10, and WD-15) for each generator loading. CO is a product of incomplete combustion and occurs when carbon in the fuel is partly oxidized rather than fully oxidized to carbon dioxide. While idling, the average value of CO rises to 0.153, 0.152, and 0.204% with WD-5, WD-10, and WD-15, respectively, from 0.08% with WD-0. If the loading was 3600 W, the average value of CO raises to 0.056, 0.042, and 0.046% with WD-5, WD-10, and WD-15, respectively, from 0.035% with WD-0. The emission trend is similar to that reported by Lin and Chen (Citation2006).
This also happened to HC emissions (). Normally, the unburned HC in exhaust usually results in three mechanisms: misfiring, flame quenching effect, and deposits or oil membrane. Therefore, the lower temperature causes misfire and/or partial burning in the regions near the combustion chamber wall (Celik, Citation2008). When there is no load, the average value of HC rises to 56.7, 76.0, and 82.1 ppm with WD-5, WD-10, and WD-15, respectively, from 27.8 ppm with WD-0. At 3600 W, the average value of HC rises from 12.6 ppm with WD-0 to 22.2, 20.5, and 26.0 ppm with WD-5, WD-10, and WD-15, respectively.
According to the results with the exhaust temperature, CO and HC emissions suggest that when water is blended with diesel, the exhaust temperature of the engine becomes lower. Therefore, CO and HC emission were enlarged. Furthermore, the results indicate that the high viscosity of the fuel with increasing water content in the blend might cause poor fuel spray in the injection. During the compressor process, a part of the droplets of emulsified diesel might not be occurring as micro-explosions, therefore leading to CO and HC formation (Lin et al., Citation2011). On the other hand, the water content of diesel was affected by the flame that was obstructed with vaporization of water, which leads to incomplete combustion and higher CO and HC emission at lower loading (Suh and Atreya, Citation1995). If the engine is running at a lower air–fuel ratio for the same engine load, CO and unburned HC emission concentrations will get higher, for the reason that there is insufficient oxygen to convert all carbon atoms of fuel into CO2. HC might be trapped in the quench layer during the compression stroke (Abu-Qudais et al., Citation2000), and the combustion temperature was reduced as the water content increased. Therefore, the CO and HC emissions increase, especially when the combustion temperature of water-emulsified fuel is lower than for the pure diesel burning (Özcan and Söylemez, Citation2005; Lin and Chen, Citation2006; Lin et al., Citation2010). Particularly for WD-15, the exhaust temperature and NO were decreased, and CO and HC emission were increased.
Characterization of particle number emissions and size distribution
shows the feature of exhaust particle size distribution and accumulated concentration of each fuel combustion under the generator loading at 1800 W and 3600 W, respectively. While using WD-0, the total number concentration of particles is less than for the other fuels (WD-5, WD-10, and WD-15) when the loading is less than 1800 W. However, the total number concentration of particles is below that of the other fuels (WD-0, WD-5, and WD-10) when the loading is 3600 W using WD-15 (). While idling, the total number concentration of particles for WD-0, WD-5, WD-10, and WD-15 is 1.95 × 108 (σ ≊ 1.2 × 107), 1.82 × 108 (σ ≊ 5.8 × 106), 2.46 × 108 (σ ≊ 8.5 × 106), and 1.36 × 108 (σ ≊ 4.8 × 106) particles/cm3, respectively. If the loading is 1800 W, the total number concentration of particle for WD-0, WD-5, WD-10, and WD-15 is 8.91 × 107 (σ ≊ 3.9 × 106), 1.8 × 108 (σ ≊ 1.1 × 107), 2.92 × 108 (σ ≊ 4.6 × 106), and 2.27 × 108 (σ ≊ 1 × 107) particles/cm3, respectively. At high loading (3600 W), the total number concentration for WD-0, WD-5, WD-10, and WD-15 is 1.41 × 108 (σ ≊ 7.8 × 106), 1.16 × 108 (σ ≊ 6.7 × 106), 1.47 × 108 (σ ≊ 6.5 × 106), and 3.01 × 107 (σ ≊ 9.8 × 106) particles/cm3, respectively. In addition, the result sof fuel consumption, exhaust temperature, and CO and HC emission also can prove that increasing water content is not good for burning at lower loading. The total number concentration of particles might be increased if the load is low. In addition, the particle number median diameter for WD-0, WD-5, WD-10, and WD-15 is about 0.07, 0.09, 0.08, and 0.10 μm, respectively, when the loading is 3600 W. The curves of particle size distribution of particle number emission are shifted toward larger particles by using water-emulsified diesel as fuel at 3600 W ().
Figure 4. Particle number emission: (a) Accumulated number concentration of engine exhaust by using various fuels. (b) Particle size distribution and number concentration of engine exhaust by using various fuels.
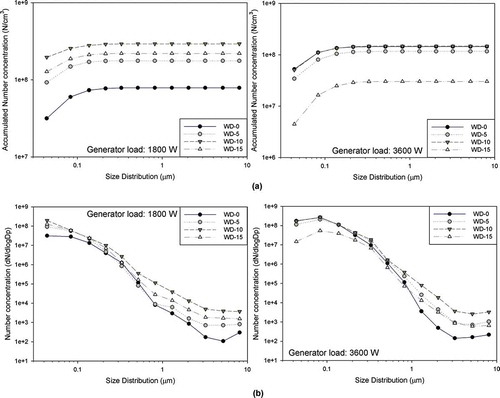
is the volume concentration distribution of particles. The value of volume concentration is determined by mathematical calculation. However, it cannot compare with particle mass concentration, absolutely. As shown in and , the volume concentration of particle emission increased when the water content increased except for WD-15. However, the results of show that the volume concentration (WD-15) of fine particles was decreased significantly. On the other hand, the condensation of semivolatile HC may cause the large particles to increase. Besides, the larger particles might also become the small particle agglomeration centers. This might change the particle size and number emission.
Figure 5. Volume concentration distribution of particle (calculated): (a) 0 W, (b) 1800 W, and (c) 3600 W of generator load.
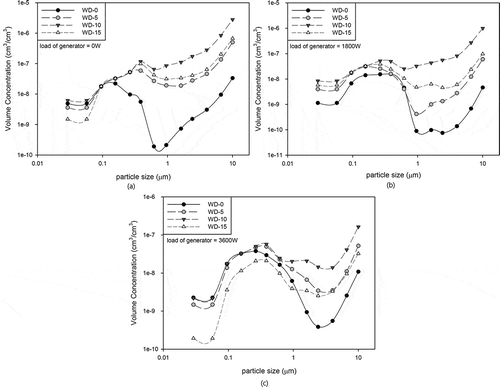
The results suggest that the number concentration of particulate emission may be diminished at high load. Most studies showed that particulate matter (PM) or soot emission was decreased by using water-emulsified diesel as fuel (Armas et al., Citation2005; Park et al., Citation2001; Lin and Chen, Citation2006; Sarvi et al., Citation2009).
Conclusion
According to the results and discussion, the water-emulsified diesel could be used in the light-duty diesel engine generator without modifications. The result shows that the net diesel fuel consumption and the exhaust gas temperature decreased with increasing water content of fuels over the investigated loading range. Comparing with WD-0 fuel, the thermal efficiency of net diesel was improved about 1.2–19.9% by using water-emulsified diesel as fuel.
Most importantly, there was a significant reduction of NO emissions of 18.3% (WD-5), 42.9% (WD-10), and 45.4% (WD-15), and the total number concentration of particle emission might be diminished if the load is high. However, using the water-emulsified diesel as fuel led to a significant increase of CO and HC exhaust emission. Furthermore, when water is added to the fuel, the injection volume is increased in order to provide enough fuel to maintain the power, and the total number concentration of particle emission might be increased.
Compared with the emission properties of WD-0 and WD-5, the NO emission of WD-10 had better reduction. Even though the NO and HC emission of WD-10 was almost the same as for WD-15, the CO emission was lower than for WD-15 and similar to results for WD-5. In addition, it provided good improvement in thermal efficiency at high load. The WD-10 fuel gave the best improvement of the exhaust emissions and engine performance.
As a final conclusion, this study accentuates the effect of water emulsion fuel in the light-duty diesel engine generator. Positive effect relates to the lower combustion temperature by using water-emulsified diesel as fuel. This study could be very useful for the government to regulate pollutant emissions from a light-duty diesel engine generator.
Additional information
Notes on contributors
Jin-Yuan Syu
Jin-Yuan Syu and Yuan-Yi Chang are doctoral students at the Graduate Institution of Engineering Technology–Doctoral at National Taipei University of Technology.
Yeou-Lih Yan
Yeou-Lih Yan is an associate professor in the Department of Safety, Health and Environmental Engineering at National United University.
Chih-Chieh Chen
Chih-Chieh Chen is a professor at the Institute of Occupational Medicine and Industrial Hygiene at National Taiwan University.
Wen-Yinn Lin
Wen-Yinn Lin and Yu-Min Chang are professors, and Chao-Heng Tseng is an associate professor in the Institute of Environmental Engineering and Management at National Taipei University of Technology.
References
- Abu-Qudais, M., O. Haddad, and M. Qudaisat. 2000. The effect of alcohol fumigation on diesel engine performance and emissions. Energy Convers. Manage. 41(4): 389–99. doi:10.1016/S0196-8904(99)00099-0
- Abu-Zaid, M. 2004. Performance of single cylinder, direct injection diesel engine using water fuel emulsions. Energy Convers. Manage. 45:697–705. doi:10.1016/S0196-8904(03)00179-1
- Alahmer, A., J. Yamin, A. Sakhrieh, and M.A. Hamdan. 2010. Engine performance using emulsified diesel fuel. Energy Convers. Manage. 51: 1708–13. doi:10.1016/j.enconman.2009.11.044
- Armas, O., R. Ballesteros, F.J. Martos, and J.R. Agudelo. 2005. Characterization of light duty diesel engine pollutant emissions using water-emulsified fuel. Fuel 84:1011–18. doi:10.1016/j.fuel.2004.11.015
- Ashok, M.P. 2011. Effect of dimethyl ether in a selected ethanol/diesel emulsified fuel ratio and comparing the performance and emission of the same to diesel fuel. Energy Fuels 25:3799–805. doi:10.1021/ef2007547
- Badrana, O., S. Emeish, M. Abu-Zaid, T. Abu-Rahma, M. Al-Hasan, and M. Al-Ragheb. 2011, Impact of emulsified water/diesel mixture on engine performance and environment. Int. J. Thermal Environ. Eng. 3(1): 1–7.
- Canfield, C.A. 1999. Effects of Diesel–Water Emulsion Combustion on Diesel Engine NOX Emissions. Master’s thesis, University of Florida, Gainesville, FL.
- Celik, M.B. 2008. Experimental determination of suitable ethanol–gasoline blend rate at high compression ratio for gasoline engine. Appl. Thermal Eng. 28:396–404. doi:10.1016/j.applthermaleng.2007.10.028
- Çetinkaya, M., and F. Karaosmanoglu. 2005. A new application area for used cooking oil originated biodiesel: Generators. Energy Fuels 19(2): 645–52.doi:10.1021/ef049890k
- Chiaramontia, D., M. Bonini, E. Fratini, G. Tondi, K. Gartner, A.V. Bridgwater, H.P. Grimm, I. Soldaini, A. Websterg, and P. Baglionia. 2003. Development of emulsions from biomass pyrolysis liquid and diesel and their use in engines-Part 1: Emulsion production. Biomass Bioenergy 25:85–99. doi:10.1016/S0961-9534(02)00183-6
- Ghojel, J., D. Honnery, and K. Al-Khaleefi. 2006. Performance, emissions and heat release characteristics of direct injection diesel engine operating on diesel oil emulsion. Appl. Thermal Eng. 26:2132–41. doi:10.1016/j.applthermaleng.2006.04.014
- Ghojel, J.I., and X.T. Tran. 2010. Ignition characteristics of diesel–water emulsion sprays in a constant-volume vessel: Effect of injection pressure and water content. Energy Fuels 24:3860–66. doi:10.1021/ef1001875
- Kadota, T., and H. Yamasaki. 2002. Recent advances in the combustion of water fuel emulsion. Prog. Energy Combust. Sci. 28:385–404. doi:10.1016/S0360-1285(02)00005-9
- Kadota, T., H. Tanaka, D. Segawa, S. Nakaya, and H. Yamasaki. 2007. Microexplosion of an emulsion droplet during Leidenfrost burning. Proc. Combustion Inst. 31:2125–31. doi:10.1016/j.proci.2006.07.001
- Kannan, G.R., and R. Anand. 2011. Experimental investigation on diesel engine with diestrolewater micro emulsions. Energy 36:1680–87. doi:10.1016/j.energy.2010.12.062
- Lee Willis, H., and W.G. Scott. 2000. Distributed Power Generation: Planning and Evaluation. New York, NY: Marcel Dekker.
- Lee, W.J., Y.C. Liu, F.K. Mwangi, W.H. Chen, S.L. Lin, Y. Fukushima, C.N. Liao, and L.C. Wang. 2011. Assessment of energy performance and air pollutant emissions in a diesel engine generator fueled with water-containing ethanol-biodiesel-diesel blend of fuels. Energy 36:5591–99. doi:10.1016/j.energy.2011.07.012
- Lin, W.Y., Y.Y. Chang, and Y.R. Hsieh. 2010. Effect of ethanol–gasoline blends on small engine generator energy efficiency and exhaust emission. J. Air Waste Manage. Assoc. 60(2): 142–48. doi:10.3155/1047-3289.60.2.142
- Lif, A., and K. Holmberg. 2006. Water-in-diesel emulsions and related systems. Adv. Colloid Interface Sci. 123– 126:231–39. doi:10.1016/j.cis.2006.05.004
- Lin, C.Y., and L.W. Chen. 2006. Engine performance and emission characteristics of three-phase diesel emulsions prepared by an ultrasonic emulsification method. Fuel 85:593–600. doi:10.1016/j.fuel.2005.09.007
- Lin, C.Y., and K.H. Wang. 2003. The fuel properties of three-phase emulsions as an alternative fuel for diesel engines. Fuel 82:1367–375. doi:10.1016/S0016-2361(03)00021-8
- Lin, C.Y., and K.H. Wang. 2004. Effects of a combustion improver on diesel engine performance and emission characteristics when using three-phase emulsions as an alternative fuel. Energy Fuels 18:477–484. doi:10.1021/ef0300848
- Lin, S.L., W.J. Lee, C.F. Lee, and S.J. Chen. 2010. Energy savings and emission reduction of nitrogen oxides, particulate matter, and polycyclic aromatic hydrocarbons by adding water-containing acetone and neat soybean oil to a diesel-fueled engine generator. Energy Fuels 24(8): 4522–33. doi:10.1021/ef100556b
- Lin, S.L., W.J. Lee, C.F.F. Lee, and Y.P. Wue. 2012. Reduction in emissions of nitrogen oxides, particulate matter, and polycyclic aromatic hydrocarbon by adding water-containing butanol into a diesel-fueled engine generator. Fuel 93:364–72. doi:10.1016/j.fuel.2011.11.042
- Lin, S.L., W.J. Lee, S.S. Chang, C.F. Lee, L.F. Lee, C.S. Lin, and H. Loong. 2011. Energy savings and emission reduction of traditional pollutants, particulate matter, and polycyclic aromatic hydrocarbon using solvent-containing water emulsified heavy fuel oil in boilers. Energy Fuels 25(4): 1537–46. doi:10.1021/ef200083g
- Mathis, U., M. Mohr, R. Kaegi, A. Bertola, and K. Boulouchos. 2005. Influence of diesel engine combustion parameters on primary soot particle diameter. Environ. Sci. Technol. 39:1887–92. doi:10.1021/es049578p
- Ochoterena, R., A. Lif, M. Nydén, S. Andersson, and I. Denbratt. 2010. Optical studies of spray development and combustion of water-in-diesel emulsion and microemulsion fuels. Fuel 89:122–32. doi:10.1016/j.fuel.2009.06.039
- Özcan, H., and M.S. Söylemez. 2005. Experimental investigation of the effects of water addition on the exhaust emissions of a naturally aspirated, liquefied-petroleum-gas-fueled engine. Energy Fuels 19(4):1468–72. doi:10.1021/ef049850g
- Park, J.W., K.Y. Huh, and J.H. Lee. 2001. Reduction of NOX, smoke and brake specific fuel consumption with optimal injection timing and emulsion ratio of water-emulsified diesel. Proc. Inst. Mech. Eng. 215:83–93. doi:10.1243/0954407011525476
- Qi, D.H., H. Chen, C.F. Lee, L.M. Geng, and Y.Z. Bian. 2010. Experimental studies of a naturally aspirated, DI diesel engine fuelled with ethanol-biodiesel-water microemulsions. Energy Fuels 24(1): 652–63. doi:10.1021/ef900814r
- Ribeiro, N.M., A.C. Pinto, C.M. Quintella, G.O.de. Rocha, L.S.G. Teixeira, L.L.N. Guarieiro, M. de C. Rangel, M.C.C. Veloso, M.J.C. Rezende, R.S. da Cruz, A.M. de. Oliveira, E.A. Torres, and L.B. de Andrade. 2007. The role of additives for diesel and diesel blended (ethanol or biodiesel) fuels: A review. Energy Fuels 21(4): 2433–45. doi:10.1021/ef070060r
- Sarvi, A., P. Kilpinen, and R. Zevenhoven. 2009. Emissions from large-scale medium-speed diesel engines: 3. Influence of direct water injection and common rail. Fuel Process. Technol. 90:222–31. doi:10.1016/j.fuproc.2008.09.003
- Suh, J., and A. Atreya. 1995. The effect of water vapor on counterflow diffusion flames. International Conference on Fire Research and Engineering, September 10–15, Orlando, FL.
- Teixeira, A.R., R.J. Hermann, J.S. Kruger, W.J. Suszynski, L.D. Schmidt, D.P. Schmidt, and P.J. Dauenhauer. 2013. Microexplosions in the upgrading of biomass-derived pyrolysis oils and the effects of simple fuel processing. ACS Sustain. Chem. Eng. 1(3): 341–48. doi:10.1021/sc300148b
- van Gulijk, C., J.M. Schouten, J.C.M. Marijnissen, M. Makkee, and J.A. Moulijn. 2001. Restriction for the ELPI in diesel particulate measurements. Journal of Aerosol Science. 32(9): 1117–30. doi:10.1016/S0021-8502(01)00045-3