Abstract
During the processing of antimony ore by pyrometallurgical methods, a considerable amount of slag is formed. This antimony waste slag is listed by the European Union as absolutely hazardous waste with a European Waste Catalogue code of 10 08 08. Since the levels of antimony and arsenic in the leachate of the antimony waste slag are generally higher than the landfilling limits, it is necessary to treat the slag before landfilling. In this study, stabilization/solidification and geopolymerization technologies were both applied in order to limit the leaching potential of antimony and arsenic. Different combinations of pastes by using Portland cement, fly ash, clay, gypsum, and blast furnace slag were prepared as stabilization/solidification or geopolymer matrixes. Sodium silicate–sodium hydroxide solution and sodium hydroxide solution at 8 M were used as activators for geopolymer samples. Efficiencies of the combinations were evaluated in terms of leaching and unconfined compressive strength. None of the geopolymer samples prepared with the activators yielded arsenic and antimony leaching below the regulatory limit at the same time, although they yielded high unconfined compressive strength levels. On the other hand, the stabilization/solidification samples prepared by using water showed low leaching results meeting the landfilling criteria. Use of gypsum as an additive was found to be successful in immobilizing the arsenic and antimony.
Implications
Despite the wide use of antimony for industrial purposes, disposal options for an antimony waste such as slag from thermal processing of antimony ore were not reported in the existing literature. This study aimed to develop a disposal strategy for the hazardous antimony waste slag. The findings of this study would contribute to understand the immobilization mechanisms of antimony and arsenic and will also be of interest to the owners of the antimony ore processing plants and to researchers investigating the efficiency of stabilization/solidification and geopolymerization technologies.
Introduction
Metal mining is the base industry in the economic development of numerous countries. Rising demands for metals from countries like China and India have caused an enormous increase in metal production in recent years. This increasing trend has carried an evolving waste management problem along with it. Therefore, it has become necessary to consider the environmental impacts of mining activities and to introduce waste management approaches. In Europe, the European Commission started to implement new directives in 2006 on the management of waste from extractive industries including mine waste (Directive 2006/21/EC and amending Directive 2004/35/EC: European Community, Citation2006).
Antimony is one of those metals that has an increasing production trend and brings environmental problems during extraction. Antimony and its compounds have a wide range of industrial applications, particularly as additives in flame retardants, which account for about 90% of global antimony trioxide consumption (Klein et al., Citation2009). Industrial uses of antimony also include the manufacture of semiconductors, diodes, lead hardener, batteries, small arms, tracer bullets, automobile brake linings, and pigments (Filella et al., Citation2002). Antimony has been produced from ores in more than 15 countries (Anderson, Citation2012). World reserves of antimony are estimated to be about 1.8 million metric tonnes (Carlin, Citation2012). Turkey is among the countries producing and exporting antimony. It has been reported that Turkey produced 50,357 tons of antimony in 2008, which had increased from 28,000 tons in 2007 (Mobbs, Citation2013).
The antimony content of the ore determines the pyrometallurgical method of antimony recovery from ore. In general, antimony trioxide (Sb2O3), which is considered to be the most important antimony compound, is produced by volatilizing antimony metal in an oxidizing furnace (Anderson, Citation2012). Antimony enters the environment during the mining and processing of its ores and in the production of antimony metal, alloys, antimony oxide, and combinations of antimony with other substances (Agency for Toxic Substances and Disease Registry [ATSDR], Citation1992). Antimony ore and impure metals can be brought for processing into the countries where antimony is not mined.
During the processing of antimony by pyrometallurgical methods, a considerable amount of slag containing antimony and other impurities is formed in the equipment such as the shaft furnace, rotary kiln, converter, or reverberatory furnace. According to the antimony production companies, 1 ton of antimony production results in the generation of approximately 4.5–5 tons of waste slag. Although part of the slag is frequently reused in the furnaces to reduce volatilization losses (Anderson, Citation2012), a larger part of it becomes waste. This antimony waste slag (AWS) is listed by the European Union (EU) as absolutely hazardous waste with a European Waste Catalogue (Citation2002) (EWC) code of 10 08 08, because of the leaching potential of the hazardous pollutants such as antimony (Sb), arsenic (As), and others that the waste may contain. The levels of pollutants such as Sb and As in the leachate of AWS are generally higher than the landfilling limits defined by the legislations.
The common AWS management practice in Turkey is to collect the AWS in the open sites near the plants without taking sufficient precautions or landfilling. Wastes from mining and smelting of antimony are reported to be generally disposed of at landfills worldwide (ATSDR, Citation1992). However, landfilling AWS is not a proper solution to the disposal problem, as the hazardous characteristics of the waste necessitate treatment before disposal at landfills. Additionally, considering the limited capacities of landfills and the waste management hierarchy recommending minimization, reuse, and recycling primarily, landfilling should be considered as the last management option.
Despite the wide use of antimony for industrial purposes, little information concerning the disposal of antimony and its compounds can be found in the literature. Cornelis et al. (Citation2012) investigated antimonate (Sb(OH)6−) leaching in hydrated cement pastes by mixing ordinary Portland cement with an aqueous KSb(OH)6solution. They reported that antimonate can interact with many minerals in hydrated cement pastes (HCP), but the most pronounced interactions occur with monosulfate, and possibly also other AFM minerals, and with C–S–H. Hale et al. (Citation2012) investigated the effects of cement or lime on the mobility of several pollutants including antimony in field-contaminated and aged soils. They found that below pH 6, Sb mobility was lower in the cement-treated soil compared to the untreated soil, but the same in the lime-treated soil as in the control soil. Cornelis et al. (Citation2008) investigated possible mechanisms that control the leaching behavior of the oxyanion forming elements including antimony in cementitious systems and alkaline solid wastes. They observed that the leachability of oxyanions usually was lower than what was expected on the basis of pure-phase solubility in alkaline wastes or cement. They suggested possible alternative mechanisms such as surface adsorption and solid solution formation with minerals containing Ca that can be found in all alkaline waste types.
Although limited studies exist in the literature on the leaching behavior of antimony, none of the studies investigated the management options for antimony waste, such as slag from thermal processing of antimony ore. This study aimed to develop a management strategy for AWS resulting from the thermal processing of antimony ore.
Stabilization/solidification (S/S) has been used to transform potentially hazardous waste, containing particularly inorganic components, into a less hazardous or nonhazardous form before disposal in a landfill (Chen et al., Citation2009). Stabilization alters hazardous waste chemically and involves chemical interactions between waste and the binding agent, while solidification converts liquid waste, sludge, or powder into a monolithic or granular form, which would be relatively easy to handle and transport to landfills (Conner, Citation1990; Glasser, Citation1997). Stabilization/solidification technology has proved to be successful in treating several industrial wastes containing zinc, lead (Salihoglu and Pinarli, Citation2008), arsenic, cadmium, chromium, copper, and nickel (Paria and Yuet, Citation2006). Dutre and Vandecasteele (Citation1995) applied S/S technology to an industrial waste containing large amounts of arsenic and originating from a metallurgical process. They used lime and cement in their experiments. Singh and Pant (Citation2006) stabilized/solidified a waste originating from arsenite removal by an activated alumina adsorption process using cement, fly ash, calcium hydroxide, and various polymeric materials.
Geopolymerization is an emerging technology for the immobilization of toxic metals in waste (Khale and Chaudhary, Citation2007). The reaction of a solid aluminosilicate with concentrated alkali hydroxide or silicate solution produces a synthetic alkali aluminosilicate material called geopolymer (Davidovits, Citation1991). Geopolymers, aluminosilicate materials that exhibit excellent physical and chemical properties, offer a diverse range of potential applications including containment and immobilization of toxic, hazardous, and radioactive wastes (Komnitsas and Zaharaki, Citation2007). Geopolymers are reported to provide performance comparable to traditional cementitious binders in a range of applications, with the added advantage of significantly reduced greenhouse emissions (Duxon et al., Citation2007). Therefore, geopolymerization has started to be a preferable waste management approach. Geopolymers have been used to immobilize heavy metals (Van Jaarsveld et al., Citation1997) and are suggested for immobilizing heavy metals by locking them within their three-dimensional framework (Davidovits, Citation1999). Khale and Chaudhary (Citation2007) reported in their review that about 90% of heavy metals get locked into the geopolymer matrix.
Promising studies conducted by the application of S/S and geopolymerization technologies in treatment of heavy metal containing hazardous wastes led the author to hypothesize that both technologies can be successful in immobilization of Sb and As in AWS. Better compressive strength and leaching results obtained with geopolymerization technology in the literature (Khale and Chaudhary, Citation2007; Komnitsas and Zaharaki, Citation2007; Pereira et al., Citation2009) compared to S/S results also led the author to hypothesize that geopolymerization may serve as a better technology than S/S in treating AWS.
In this study, S/S and geopolymerization technologies were both applied to limit the leaching potential of the Sb and As, the pollutants found to leach above the landfilling limits, from AWS. Different combinations of pastes were prepared by using Portland cement, fly ash, clay, gypsum, and blast furnace slag as S/S or geopolymer matrixes, and the efficiencies of the combinations were evaluated in terms of leaching and unconfined compressive strength.
Materials and Methods
Waste and other materials
Antimony waste slag was obtained from a thermal processing plant of antimony ore, located in Kutahya, Turkey. A composite grab sample of AWS was obtained all at once from the slag collecting container at the end of the rotary kiln. The slag was received in a dry state, and was ground and mixed thoroughly to improve the waste uniformity before use.
Low-calcium fly ash (ASTM Class F) (ASTM Standard C618-12a: ASTM, Citation2012) from the coal-fired power plant in Orhaneli-Bursa, Turkey (210 MW), was used as an aluminosilicate agent and a geopolymer precursor. Type I Portland cement (PC), clay, and gypsum, which were used as the main binders and additives, were obtained from the cement plant in Bursa. Blast furnace slag was obtained from Karabuk Iron and Steel Foundry in Turkey, and was used as an additive in one group of samples. The results of the chemical analysis of the AWS and other materials are presented in .
Table 1. Chemical composition of the AWS and the additives used (% w/w, dry basis)
Specific gravity of the AWS was 2.65 g/cm3. The waste was first ground into two fineness levels in order to see the effect of grinding on leaching. Specific surface area of ground AWS (referred as AWS hereafter) was 8060 cm2/g, and that of finely ground AWS (referred to as G.AWS hereafter) was found to be 11,050 cm2/g. The As and Sb leaching levels of the waste that was ground into two fineness levels were examined () in order to decide on the level to conduct the immobilization studies with. The As and Sb leaching levels of the G.AWS were found to be higher than those of the other material. Therefore, studies were undertaken with the coarser waste slag, AWS. Initial As and Sb concentrations of the AWS (according to the European Union’s compliance leaching test of EN 12457-4: EN Standard Store, Citation2002) were measured as 0.01 mg/L and 0.2 mg/L, respectively. According to the EU and Turkish waste acceptance criteria, the leachable As and Sb concentrations should be below 0.2 mg/L and 0.07 mg/L, respectively, in order to be accepted as non-hazardous-waste landfill. The analysis results of the necessary parameters in the AWS according to EU and Turkish waste acceptance criteria are given in . The Turkish Ministry of the Environment categorized AWS in the “10 08 wastes from other non-ferrous thermal metallurgy” group with the code of “10 08 08* salt slag from primary and secondary production,” which has an absolute hazardous entry. Therefore the waste was categorized as hazardous and subject to treatment before recovery or disposal. shows the acid neutralization capacity of the AWS studied.
Figure 1. Properties of the AWS studied. (a) The As and Sb leaching results of the AWS and ground AWS (G.AWS). (b) Acid neutralization capacity of the AWS.
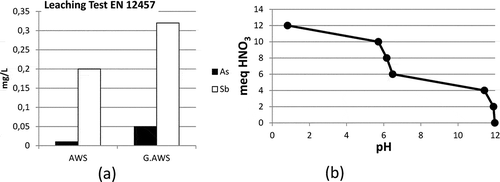
Table 2. Leaching test results of the AWS according to the EU waste acceptance criteria
All chemicals used in this study were of analytical grade, and include sodium silicate solution (Pure-Merck) (NaSil), and sodium hydroxide pellets (Pure-Merck) (NaOH). It has been reported that in order to obtain a geopolymer with maximum strength, the Si/Al ratio in general should be in the range of 1–3 (Davidovids, Citation1991; Zheng et al., Citation2010; Zhang et al., Citation2011). Therefore, the NaSilNaOH solution was prepared by keeping the NaSil/NaOH (w/w) ratio at 5 to keep the Si/Al ratio close to the ratio recommended. The Si/Al ratio ranged between 2.52 and 3.01 in this study.
Experiments
Characterization
Thermoelectron x-ray fluorescence spectroscopy with an ARL 8660 x-ray spectrometer (Switzerland) was used for the determination of chemical composition of the waste and materials. The specific surface area of the waste was measured by the fineness test air permeability method (ASTM Standard C204-11: ASTM, Citation2011) with the Blaine apparatus Tonic Technic 72071. The initial metal concentration in the waste was analyzed using a Shimadzu atomic absorption flame emission spectrophotometer (AA-6701F). The European Union’s compliance leaching test of EN12457-4 (EN 12457-4: EN Standard Store, Citation2002) was applied to determine the As and Sb concentrations. Deionized water was used as leaching fluid for EN12457-4 test (EN 12457-4: EN Standard Store, Citation2002) and a liquid-to-solid ratio of 10 L/kg was applied.
Sample preparation
Two groups of paste samples, where the AWS content was kept at 25% of the total dry weight, were prepared. All samples were prepared in triplicate. In the first group of the samples, the combinations were Portland cement alone, fly ash + Portland cement together (both used in equal weight), and fly ash alone. The samples were activated with NaSilNaOH or 8 M NaOH or water. In the second group of samples, clay, gypsum, and blast furnace slag were used as additional materials. Water or Nasil NaOH solution was used as activator. The samples activated with NaSil NaOH or 8 M NaOH were called geopolymers, and the samples prepared with water were called S/S matrixes. All additives were used in equal amounts, by weight. The contents of the samples are given in . The ingredients were mixed 5 min before the activator/liquid was added and the mixing continued for 5 min. A kitchen mixer was used for all mixing. Later, the pastes were poured into cylindrical plastic molds (45 mm diameter, 50 mm height) for air curing at room temperature of 22–23ºC for 28 days.
Table 3. Content of the S/S samples
Analysis
After 28 days of curing, the samples were subjected to unconfined compressive strength (UCS) test in compliance with ASTM C109-88 (ASTM Standard C109/C109M-07: ASTM, Citation2007). Two cylinders of each sample were used for the UCS test and the experimental values were averaged. A compressive strength testing apparatus of model SEGER-Tonindustrie was used. A stress-controlled loading velocity of 0.05 kN/sec was applied. All the samples were subjected to the EN12457-4 extraction. The As and Sb levels in the leachate after EN12457-4 were measured by a Shimadzu atomic absorption flame emission spectrophotometer (AA-6701F). The pH changes were monitored after the extraction. The samples were also subjected to the acid neutralization capacity (ANC) test. For the ANC, the samples were divided into 7 subsamples and placed in test tubes with an increased amount of nitric acid at a liquid-to-solid ratio of 10:1. The tubes were then rotated end over end for 48 hr and centrifuged before the measurement of the extract pH using a Sartorius pH meter.
Evaluation
The leaching and UCS results of different mixes were compared with each other. Leaching results were also compared with the EU and Turkish landfilling criteria.
Results and Discussion
Immobilization
shows the UCS and leaching results of the geopolymer samples prepared with 25% AWS by weight and Portland cement and/or fly ash as immobilization agents. According to the figure, the highest UCS results were obtained with the samples prepared by using NaSil NaOH as the activator. The activator NaSil NaOH gave the highest UCS result (25.2 MPa) with the sample containing fly ash and Portland cement, and the lowest result (6.5 MPa) with the sample containing fly ash alone, as seen in and , respectively. Although the UCS results obtained by using NaSil NaOH were higher than those of 8 M NaOH and of water, they were much lower than those reported in the literature. Diaz et al. (Citation2010) prepared fly-ash-based geopolymers by using an activator solution composed of 14 M NaOH solution and sodium silicate (45% by weight), and also containing sand and gravel. They reported UCS values ranging between 40 and 80 MPa for fly ashes from different power plants. The difference between their findings and findings of this study might have resulted from the effect of AWS added. The different origin of the fly ash used, a similar but still different composition of the activator solution, and the absence of sand and gravel in this study might have contributed to the difference between the results of both studies.
Figure 2. The UCS and leaching (As and Sb) results of the samples prepared by using NaSil NaOH, 8 M NaOH, and water as activators, and Portland cement and fly ash as additives.
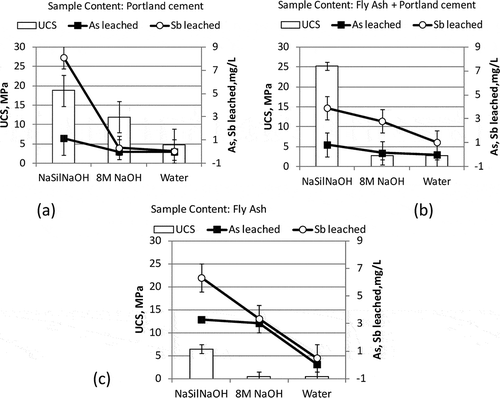
The use of 8 M NaOH yielded UCS levels varying between 0.52 and 11.92 MPa (). This result is comparable with the findings of Zhang et al. (Citation2011), who reported a UCS range of 2–15 MPa for the samples prepared with copper mine tailings, Class F fly ash (content varying between 0 and 100%), and 10 M NaOH. However, it should also be noted that the UCS of the fly ash + 8 M NaOH combination yielded a comparable but still lower UCS than the study reported by Zhang et al. (Citation2011). The difference from the literature may be caused by the difference contributed by the waste studied in both papers and different origins of the fly ash used. The researchers (Zhang et al., Citation2011) reported the SiO2 content of the mine tailings as 65% in their study, whereas the SiO2 content of AWS was 42.5% in this study. Alvarez-Ayuso et al. (Citation2008) reported higher UCS levels of fly-ash-based geopolymers of 60 MPa and 33 MPa synthesized by using 12 M NaOH and 8 M NaOH, respectively. It has also been reported by several researchers that the use of fly ashes of similar composition but from different sources may result in geopolymers with significantly differing strengths (Fernandez-Jimenez and Palomo, Citation2003; Van Jaarsveld et al., Citation2003). Fernandez-Jimenez and Palomo (Citation2003) investigated the UCS values of different alkali-activated (8 M NaOH) fly-ash mortars and reported that the compressive strength reached values higher than 30 MPa, at worst.Van Jaarsveld et al. (Citation2003) reported the UCS of alkali activated (sodium or potassium silicate) to range between 9.7 and 58.6 MPa. The possible factors that could be attributed as affecting the range in UCS levels of different alkali activated fly ash mortars by the researchers (Van Jaarsveld et al., Citation2003) include CaO content, water/fly ash ratio, alkali metal content, Al and Si content, and different solubilities of the Al and Si precursors. The effect of increasing AWS amounts on the UCS levels can be seen in Supporting . It can be inferred from the figure that the UCS levels were not considerably affected by the AWS content, which varied between 0 and 33% by weight.
Leaching results were not directly reflected in the trend in the UCS results. For example, the As and Sb leaching results of the samples containing NaSil NaOH, which yielded the highest UCS results of all samples, were higher than those of other samples, a result opposite to the expectation that elements such as As can be immobilized by being locked within the three-dimensional framework of geopolymers as suggested by Davidovits (Citation1999). Lowest As and Sb leaching results were obtained with the S/S samples prepared by using water (). The As levels leached from the samples prepared by using water varied between 0.004 and 0.045 mg/L, and the Sb levels between 0.04 and 1.04 mg/L, whereas the As levels leached from NaSil NaOH-containing samples varied between 0.83 and 3.29 mg/L, and the Sb levels between 3.91 and 8.10 mg/L. Leaching results of the samples prepared with 8 M NaOH were lower than for the NaSil NaOH-containing samples. The As leaching levels of these samples varied between 0.01 and 3.03 mg/L, and the Sb leaching levels between 0.33 and 3.35 mg/L. It was seen that the activator used was quite effective on the As and Sb leaching results of the samples.
The As leaching levels from all of the samples prepared by using water were below the regulatory As limit of 0.2 mg/L (), and below the initial As leaching from the AWS, which was 0.01 mg/L. Several researchers have shown that As immobilization is mainly controlled by the formation of Ca-As precipitates. Vandecasteele et al. (Citation2002) reported the As leaching results of a waste solidified using cement and lime, and attributed the concentration decrease in the leachate to the formation of calcium arsenate (Ca3(AsO4)2) and calcium arsenite(CaHAsO3) precipitates in the presence of Ca(OH)2. Singh and Pant (Citation2006) reported the leaching behavior of arsenic from a waste stabilized/solidified by using Portland cement, fly ash, calcium hydroxide, and various polymeric materials, and reported the formations of calcite along with precipitate formation of calcium arsenite to be responsible for low arsenic leaching from the solidified samples. Chuanyong et al. (Citation2003) also reported significant reduction in arsenic mobility with cement because of the formation of calcium arsenite. Moon and others (Citation2004) reported that lime-based S/S of As(III) resulted in a Ca-As-O as the main precipitate, while the presence of As(V) resulted in the formation of Ca4(OH)2(AsO4)2·2H2O. Low As leaching results in this study might be also attributed to the possible formation of calcium arsenite. It is expected that arsenic trioxide (As2O3) was introduced to the S/S matrix by AWS as a result of the combustion of arsenic and arsenic-containing minerals during the pyrometallurgical processing of antimony ore. The aquesous reaction of As2O3 in S/S matrix would possibly be as follows:
When the Sb leaching levels were considered, the leaching from the samples prepared by using NaSil NaOH or 8 M NaOH was found to be above the regulatory limit. Among the samples prepared with water, the one containing only Portland cement yielded Sb leaching of 0.044 mg/L, which was below the regulatory limit and initial Sb leaching from the AWS. Therefore, it can be inferred that the most feasible option in this group of samples in terms of the As and Sb leaching was Portland cement + water. The UCS level of this sample, which was 4.81 MPa, was quite low compared to the samples prepared with NaSil NaOH or 8 M NaOH.
It can be inferred from the results that UCS levels were not precursors of the immobilization performance when different activators were compared. However, when the samples prepared with the same activator were compared with each other, it was seen that high UCS results reflected lower leaching of the As and Sb. Supporting gives a comparison of the samples prepared with the same activator. For example, the highest UCS level was obtained with the sample prepared with fly ash + Portland cement and by using NaSil NaOH as activator. The leaching levels of this sample were lower than those of the other samples prepared with NaSil NaOH. The highest UCS result and the lowest leaching levels among the samples prepared with 8 M NaOH were obtained with the sample containing Portland cement along with AWS. The situation was similar with the samples prepared with water. The highest UCS and the lowest leaching levels were obtained with the same sample that contained Portland cement along with AWS.
The reason behind the high leaching levels from the samples with high UCS levels was sought by following the pH levels and acid neutralization capacities of the samples. The pH levels obtained after the EN12457 leaching test are shown in Supporting . It will be seen that all the pH levels of the samples were around 12, and not very different from each other. For example, the pH values varied between 12.10 and 12.40 in the samples activated with NaSil NaOH, and between 12.10 and 12.50 in the samples activated with 8 M NaOH. The samples prepared with water yielded pH levels varying between 11.50 and 12.30. It can be inferred that the pH levels measured after the leaching tests do not explain the trend in the leaching results.
Figure 3. The acid neutralization capacity of the samples prepared by using NaSil NaOH, 8 M NaOH, and water as activators, and Portland cement and fly ash as additives.
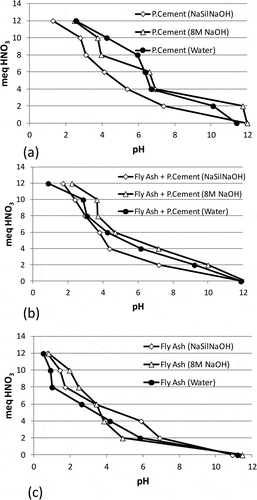
The leaching results obtained in this study agree with the findings of Alvarez-Ayuso et al. (Citation2008). The study compared the leachable content of elements of major environmental concern both in original fly ashes and in ground geopolymer samples synthesized by using 12 M NaOH. They found that geopolymer matrixes were only effective in the chemical immobilization of elements such as Co, Ni, Cu, Zn, Cd, and Pb, but not for those elements present as oxyanions, such as As, Mo, Se, Sb, or Cr. The researchers further concluded that physical entrapment does not seem to contribute in an important way to the immobilization of oxyanions. In their study, the elevated sodium levels relative to calcium in the geopolymer samples might be a reason for high leaching levels. Alvarez-Ayuso et al. (Citation2008) also noted that oxyanions generally form much more soluble compounds with sodium than with calcium. In the present study, the lower As and Sb leaching results obtained by S/S samples prepared with water, compared to the samples in which Na was added (in NaSil NaOH form or NaOH form), also agree with this fact.
Hale et al. (Citation2012) used cement or calcium hydroxide to treat soils containing Sb and other pollutants and reported a decrease in Sb mobility between pH 10 and 12. The researchers (Hale et al., Citation2012) attributed this decrease to a possible formation of solid solution, with ettringite likely to occur at high pH. Furthermore, Cornelis et al. (Citation2012) reported that dissolved Sb predominantly occurs as the pentavalent antimonite oxyanion (Sb(OH)6−) under ambient conditions, and antimonite can interact with many minerals in hydrated cement pastes (HCP). The low Sb leaching results obtained with the S/S samples prepared with water in this study, in which C-S-H formation possibly occurred, agreed with the findings of Cornelis et al. (Citation2012). Calcium-bearing minerals (particularly portlandite and ettringite) play an important role in controlling Sb leaching (Cornelis et al., Citation2006). Antimony trioxide (Sb2O3), the combustion product of the antimony ore processing, would result in the formation of pentavalent antimonite oxyanion, Sb(OH)6−, in the aquatic environment of S/S matrix according to this equation:
Ca+2 would likely form precipitates with antimonite in hydrated cement paste according to eq 4; however, calcium antimonite (Ca[Sb(OH)6]2) is reported to be too soluble to control antimonite leaching in pore solutions of alkaline matrices (Cornelis et al., Citation2006).
The acid neutralization capacities of the samples are shown in . It can be seen from the figure that the samples containing NaSil NaOH as activator, which have higher leaching levels, had slightly lower acid neutralization capacity than that of other samples. It was an unexpected finding that the acid neutralization capacity of the samples prepared with water, which showed the lowest leaching results, was found to be slightly lower than that of the samples prepared with 8 M NaOH. Therefore, it was inferred that the acid neutralization capacity did not sufficiently reflect the trend in the leaching behavior of the As and Sb.
Influence of additives: Clay, gypsum, and blast furnace slag
and show the UCS and leaching levels of the samples prepared with NaSil NaOH and water, respectively. Clay, gypsum, and blast furnace slag were used as additional additives to aid solidification and stabilization. Clay was used to provide the available alumina and silica for the possible formation of pozzolanic reaction products and to investigate its effect over leaching. Gypsum was used to provide possible interaction between sulfide and antimony, and with blast furnace slag it was intended to increase the UCS of the samples. It can be seen in that the contribution of blast furnace slag to the UCS level of the sample prepared with NaSil NaOH was higher than the contribution of clay or gypsum. However, it may also be seen that the UCS of the sample containing fly ash and Portland cement and NaSil NaOH, which was 25.2 MPa, was higher than for those samples prepared with these additives in . In other words, clay, gypsum, or blast furnace slag lowered the UCS of the samples. Addition of clay and blast furnace slag as a pair resulted in higher UCS levels than the levels obtained with the addition of clay and gypsum as a pair. The UCS levels of all samples prepared with water were rather lower than the UCS levels of the samples prepared with NaSil NaOH ().
Figure 4. The UCS and leaching (As and Sb) results of the samples prepared by using NaSil NaOH and water as activators, and Portland cement, fly ash, clay, gypsum, and blast furnace slag as additives. (a) NaSil NaOH as activator. (b) Water as activator.
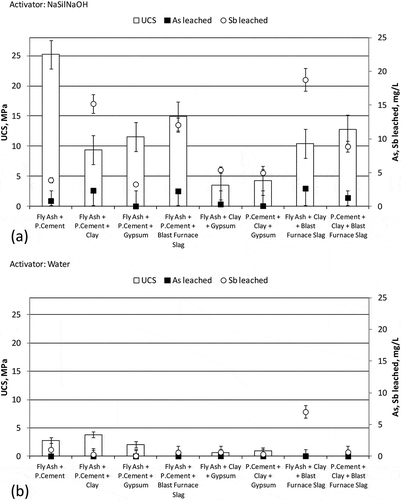
When the leaching levels were examined, the leaching trend for As and that for Sb were found to be similar. For example, the leaching of Sb from the sample containing fly ash, clay, and blast furnace slag, and prepared with NaSil NaOH was the highest of all. The leaching of As from the same sample was also the highest. The samples containing gypsum were measured to have lower leaching levels compared to other samples. In the samples prepared with NaSil NaOH, the lowest Sb leaching (3.29 mg/L) and the lowest As leaching (0.035 mg/L) were obtained with the sample containing fly ash, Portland cement, and gypsum together.
The As leaching levels from the samples prepared with NaSil NaOH ranged between 0.035 and 2.671 mg/L, and all of those samples yielded As leaching above the initial leaching of AWS, which was 0.01 mg/L. Only two samples yielded As leaching below the regulatory limit, which was 0.01 mg/L. One of these samples was the one containing fly ash, Portland cement, and gypsum together, and the other sample was the one containing fly ash, clay, and gypsum.
None of the samples prepared with NaSil NaOH yielded Sb leaching below the 0.07 mg/L regulatory limit. The Sb leaching levels of those samples ranged between 3.29 and 18.77 mg/L. All of those samples yielded higher Sb leaching than the initial leaching from the AWS.
All of the samples prepared with water resulted in As leaching lower than the regulatory limit. The As leaching levels from those samples ranged between 0.001 and 0.036 mg/L. Four of the samples yielded higher As leaching than the initial leaching from the AWS. These samples were those containing fly ash + Portland cement + blast furnace slag, fly ash + clay + gypsum, Portland cement + clay + gypsum, and fly ash + clay + blast furnace slag.
The Sb leaching from the samples prepared with water ranged between 0.057 and 6.998 mg/L. Only in one of those samples was the Sb leaching found to be below the regulatory limit. This sample was the one containing fly ash, Portland cement, and gypsum. The other samples yielded higher Sb leaching than the initial leaching from the AWS. Therefore, it could be inferred that the most feasible option in this group of samples in terms of the As and Sb leaching levels, which were 0.001 and 0.0057 mg/L, respectively, was the combination of fly ash + Portland cement + gypsum + water. However, the UCS of this sample, which was 2.05 MPa, was quite low compared to that of the samples prepared with NaSil NaOH. Cornelis et al. (Citation2006) reported that antimonite ions can substitute for sulfate during the formation of ettringite, and the sorption and/or the formation of solid solution with portlandite, calcite, and gypsum have also been suggested as possible mechanisms for the reduction of the Sb mobility. Lower Sb leaching from the samples containing additional gypsum than from the other samples in the presented study agrees with the suggestion raised by Cornelis et al. (Citation2006).
The acid neutralization capacities of the sample can be seen in and . It may be noticed that the highest acid neutralization capacity belongs to the AWS. In other words, the stabilization/solidification or geopolymerization efforts decreased the acid neutralization capacity of the raw waste.
The findings of this study do not support the hypothesis raised by the author at the beginning of the study that geopolymerization may serve as a better technology than S/S in treating an antimony waste. Although the UCS levels of the geopolymer samples were higher than that of S/S samples, which is in line with the literature, the Sb and As leaching results of geopolymer samples were worse. Elevated sodium levels brought by geopolymerization might have caused the formation of soluble compounds between oxyanions and sodium. Therefore, it can be inferred that stabilization/solidification served as a better technology than geopolymerization since it provided the formation of C-S-H where the Sb could possibly be adsorbed.
Management hierarchy for antimony waste
The antimony waste slag, which was obtained from a thermal processing plant of antimony ore in Turkey, is currently being collected in an open site near the plant. The legal authorities demand an urgent management strategy for the collected hazardous waste. The S/S and geopolymerization study presented in this paper is a part of the solution-seeking approach toward developing a management strategy for the waste.
The cost of treatment with S/S is naturally influenced by the cost of materials, volume increase, material handling and mixing, nature and concentration of contaminants, and physical properties of the waste to be treated. Therefore, treatment with S/S can be a costly process. However, when there is not a better alternative, S/S treatment can be the most feasible option. In the case of AWS in this study, the waste management hierarchy worked as follows:
Minimization: Great effort was made by the mining company to take out the antimony inside the ore because of its financial value. The mining company employed thermal processing to extract antimony from the ore. This step can be considered as a minimization step since less antimony in the waste implies less problematic waste.
Recycling: Stabilization/solidification and geopolymerization efforts undertaken in this study can be considered as steps toward recycling of the waste. However, further research is necessary to comment on the durability and mechanical strength regarding the specific purposes of the treated material.
Energy recovery: Since the waste is a thermal processing product around 1100ºC, it will not be reasonable to process it again for energy recovery.
Landfilling: In its original state, the waste cannot be disposed of at a municipal waste landfill according to the EU waste acceptance criteria (). This study can be also considered as a step toward deciding the landfill suitability of the treated waste. The S/S and geopolymerization treatment of the AWS in this study yielded a limited volume increase due to the efficient mixing and the high void ratio of the original waste. Aggregate, which would otherwise increase the volume, was not used in this study. A further pilot study by using aggregate and calculating the net volume increase is necessary before practical application.
Conclusion
This study investigated the immobilization potential of AWS, which contains As and Sb. The results indicated that the lowest leaching levels were obtained with the samples prepared by using water. Lowest UCS results were also obtained with the same samples. The highest UCS results and the highest leaching levels were obtained with the samples prepared by using NaSil NaOH as activator. In most of the samples, higher As and Sb leaching than that of the raw AWS was measured and the immobilization efforts were observed to increase the leaching of the As and Sb. The pH levels after the leaching tests and the ANC levels were found to be insufficient to explain the leaching trends. The As levels leached from the samples prepared by using NaSil NaOH varied between 0.83 and 3.29 mg/L, and the Sb levels between 3.91 and 8.10 mg/L. The As levels leached from the samples prepared by using water varied between 0.004 and 0.045 mg/L, and the Sb levels between 0.04 and 1.04 mg/L.
Two of the samples yielded As and Sb leaching below the regulatory limit, and below the initial value of the raw AWS. One of these samples was the one containing Portland cement + water, and the other was the one containing fly ash+ Portland cement + gypsum + water. Among the additives of S/S matrixes, gypsum resulted in lower As and Sb leaching levels compared to those of clay and blast furnace slag.
None of the samples prepared with NaSil NaOH or 8 M NaOH yielded As and Sb leaching below the regulatory limit at the same time. Therefore, it can be concluded that geopolymerization with these activators cannot be recommended to immobilize As and Sb, although they yielded high UCS levels. However, the S/S efforts by allowing C-S-H phase formation and use of gypsum as an additive can be recommended to immobilize the As and Sb in this kind of waste.
This study investigated the immobilization potential of Sb and As in antimony waste slag by applying S/S and geopolymerization technologies. Although UCS results of the paste samples prepared with antimony waste slag were also submitted, further research is necessary to decide whether the treated antimony waste slag satisfies material strength and durability requirements and can be used in structural systems. Possible use of the treated waste may include road pavement, concrete production, brick manufacturing, and so on. Directive 2008/98/EC (European Community, Citation2008) of the European Parliament classifies such recycling of inorganic materials with an R5 code. After immobilization studies, possible disposal routes for antimony waste slag may include recycling (R5), landfilling (D1 code of EU Directive), deep injection (D3), specially engineered landfill (D5), physicochemical treatment that results in final compounds that are discarded (D9), and permanent storage such as emplacement in a mine (D12).
This study can be considered as a step toward deciding the landfill suitability of the treated waste. Further study considering the net volume increase introduced by S/S is recommended before practical application.
Acknowledgments
The author thanks Seyma Erol, Merva Keskin, and Yeşim Köse for their efforts with the experiments.
Funding
This work was supported by Uludag University (project OUAP(M)-2013/8).
Supplemental material
Supplemental data for this article can be accessed on the publisher’s website.
Supplemental Material.pdf
Download PDF (208.8 KB)Additional information
Notes on contributors
Güray Salihoglu
Güray Salihoglu is a research and teaching professor at the Environmental Engineering Department, Uludag University Bursa, Turkey.
References
- Agency for Toxic Substances and Disease Registry. 1992. Toxicological profile for antimony and compounds. Atlanta, GA: Agency for Toxic Substances and Disease Registry.
- Alvarez-Ayuso, E., X. Querol, F. Plana, A. Alastuey, N. Moreno, M. Izquierdo, O. Font, T. Moreno, S. Diez, E. Vazquez, and M. Barra. 2008. Environmental, physical and structural characterisation of geopolymer matrixes synthesised from coal (co-)combustion fly ashes. J. Hazard. Mater. 154(1–3):175–83. doi:10.1016/j.jhazmat.2007.10.008
- Anderson, C.G. 2012. The metallurgy of antimony. Chemie Der Erde—Geochemistry 72:3–8. doi:10.1016/j.chemer.2012.04.001
- ASTM. 2007. ASTM standard C109/C109M-07, 2007. Standard test method for compressive strength of hydraulic cement mortars (using 2-in. or [50-mm] cube specimens). ASTM International, West Conshohocken, PA. doi:10.1520/C0109_C0109M, http://www.astm.org.
- ASTM. 2011. ASTM standard C204-11, 2011. Standard test methods for fineness of hydraulic cement by air-permeability apparatus. ASTM International, West Conshohocken, PA. doi:10.1520/C0204-11, http://www.astm.org.
- ASTM. 2012. ASTM standard C618-12a, 2012. Standard specification for coal fly ash and raw or calcined natural pozzolan for use in concrete. ASTM International, West Conshohocken, PA. doi:10.1520/C0618-12A, http://www.astm.org.
- Carlin, J.F. 2012. Antimony. In U.S. geological survey. USGS Minerals Information. http://minerals.usgs.gov/minerals/pubs/commodity/antimony/mcs-2012-antim.pdf (accessed July 1, 2014).
- Chen, Q.Y., M. Tyrer, C.D. Hills, X.M. Yang, and P. Carey. 2009. Immobilisation of heavy metal in cement-based solidification/stabilisation: A review. Waste Manage. 29(1): 390–403. doi:10.1016/j.wasman.2008.01.019
- Chuanyong, J., G.P. Korfiatis, and X. Meng. 2003. Immobilization mechanisms of arsenate in iron hydroxide sludge stabilized with cement. Environ. Sci. Technol. 37:5050–56.
- Conner, J.R. 1990. Chemical fixation and solidification of hazardous wastes. New York, NY: Van Nostrand Reinhold.
- Cornelis, G., T. Van Gerven, and C. Vandecasteele. 2006. Antimony leaching from uncarbonated and carbonated MSWI bottom ash. J. Hazard. Mater. 137(3): 1284–92. doi:10.1016/j.jhazmat.2006.04.048
- Cornelis, G., C.A. Johnson, T. Van Gerven, and C. Vandecasteele. 2008. Leaching mechanisms of oxyanionic metalloid and metal species in alkaline solid wastes: A review. Appl. Geochem. 23(5): 955–76. doi:10.1016/j.apgeochem.2008.02.001
- Cornelis, G., T. Van Gerven, and C. Vandecasteele. 2012. Antimony leaching from MSWI bottom ash: Modelling of the effect of pH and carbonation. Waste Manage. 32(2): 278–86. doi:10.1016/j.wasman.2011.09.018
- Davidovits, J. 1991. Geopolymers—Inorganic polymeric new materials. J. Thermal Anal. 37(8): 1633–56. doi:10.1007/Bf01912193
- Davidovits, J. 1999. Geopolymeric reactions in the economic future of cements and concretes: World-wide mitigation of carbondioxide emissions. In Proceedings of the 2nd International Conference on Geopolymer ‘99, ed. J. Davidovits, R. Davidovits, and C. James, pp. 111–121. Saint Quentin, France.
- Diaz, E. I., E. N. Allouche, and S. Eklund. 2010. Factors affecting the suitability of fly ash as source material for geopolymers. Fuel 89(5): 992–96. doi:10.1016/j.fuel.2009.09.012
- Dutre, V., and C. Vandecasteele. 1995. Solidification stabilization of hazardous arsenic-containing waste from a copper refining process. J. Hazard. Mater. 40(1): 55–68. doi:10.1016/0304-3894(94)00080-Z
- Duxon, P., A. Fernandez-Jimenez, J.L. Provis, G.C. Lukey, A. Palomo, and J.S.J. Van Deventer. 2007. Geopolymer technology: the current state of the art. J. Mater. Sci. 42:2917–33. doi:10.1007/s10853-006-0637-z
- EN Standard Store. 2002. EN 12457-4, 2002. Characterization of waste—Leaching—Compliance test for leaching of granular waste materials and sludges—Part 4: One stage batch test at a liquid to solid ratio of 10 l/kg for materials with particle size below 10 mm (without or with size reduction). http://www.en-standard.eu.
- European Community. 2006. Directive 2006/21/EC and amending Directive 2004/35/EC, Directive 2006/21/EC of the European Parliament and of the Council of 15 March 2006 on the management of waste from extractive industries and amending Directive 2004/35/EC. Off. J. Eur. Union L102/15, 11.4.2006.
- European Community. 2008. Directive 2008/98/EC, Directive 2008/98/EC of the European Parliament and of the Council of 19 November 2008 on waste. Off. J. Eur. Union L 312/3, 22.11.2008.
- European Waste Catalogue. 2002. European Waste Catalogue (EWC) And Hazardous Waste List 2002, Environmental Protection Agency, ISBN:1-84095-083-8, 49 p.Ireland.
- Fernandez-Jimenez, A., and A. Palomo. 2003. Characterisation of fly ashes. Potential reactivity as alkaline cements. Fuel 82(18): 2259–65. doi:10.1016/S0016-2361(03)00194-7
- Filella, M., N. Belzile, and Y.W. Chen. 2002. Antimony in the environment: A review focused on natural waters I. Occurrence. Earth-Science Rev. 57(1–2): 125–76. doi:10.1016/S0012-8252(01)00070-8
- Glasser, F.P. 1997. Fundamental aspects of cement solidification and stabilisation. J. Hazard. Mater. 52(2–3): 151–70. doi:10.1016/S0304-3894(96)01805-5
- Hale, B., L. Evans, and R. Lambert. 2012. Effects of cement or lime on Cd, Co, Cu, Ni, Pb, Sb and Zn mobility in field-contaminated and aged soils. J. Hazard. Mater. 199:119–27. doi:10.1016/j.jhazmat.2011.10.065
- Khale, D., and R. Chaudhary. 2007. Mechanism of geopolymerization and factors influencing its development: a review. J. Mater. Sci. 42(3): 729–46. doi:10.1007/s10853-006-0401-4
- Klein, J., S. Dorge, G. Trouve, D. Venditti, and S. Durecu. 2009. Behaviour of antimony during thermal treatment of Sb-rich halogenated waste. J. Hazard. Mater. 166(2–3): 585–93. doi:10.1016/j.jhazmat.2008.12.006
- Komnitsas, K., and D. Zaharaki. 2007. Geopolymerisation: A review and prospects for the minerals industry. Minerals Eng. 20(14): 1261–77. doi:10.1016/j.mineng.2007.07.011
- Mobbs, P.M.2013. The Mineral Industry of Turkey. In 2011 Minerals Yearbook, U.S. Geological Survey, 1–15. http://minerals.usgs.gov/minerals/pubs/country/2011/myb3-2011-tu.pdf (accessed July 1, 2014).
- Moon, D.H., D. Dimitris, and N. Menounou. 2004. Arsenic immobilization by calcium-arsenic precipitates in lime treated soils. Sci. Total Environ. 330:171–85. doi:10.1016/j.scitotenv.2004.03.016
- Paria, S., and P.K. Yuet. 2006. Solidification-stabilization of organic and inorganic contaminants using Portland cement: literature review. Environ. Rev. 14(4): 217–55. doi:10.1139/A06-004
- Pereira, C.F., Y. Luna, X. Querol, D. Antenucci, and J. Vale. 2009. Waste stabilization/solidification of an electric arc furnace dust using fly ash-based geopolymers. Fuel 88(7): 1185–93. doi:10.1016/j.fuel.2008.01.021
- Roman-Ross, G., G.J. Cuello, X. Turillas, A. Fernandez-Martinez, and L. Charlet. 2006. Arsenite sorption and co-precipitation with calcite. Chem. Geol. 233:328–36. doi:10.1016/j.chemgeo.2006.04.007
- Salihoglu, G., and V. Pinarli. 2008. Steel foundry electric arc furnace dust management: Stabilization by using lime and Portland cement. J. Hazard. Mater. 153(3): 1110–16. doi:10.1016/j.jhazmat.2007.09.066
- Singh, T.S., and K.K. Pant. 2006. Solidification/stabilization of arsenic containing solid wastes using Portland cement, fly ash and polymeric materials. J. Hazard. Mater. 131(1–3): 29–36. doi:10.1016/j.jhazmat.2005.06.046
- Van Jaarsveld, J.G.S., J.S.J. van Deventer, and G.C. Lukey. 2003. The characterisation of source materials in fly ash-based geopolymers. Mater. Lett. 57(7): 1272–80. doi:10.1016/S0167-577x(02)00971-0
- VanJaarsveld, J.G.S., J.S.J. VanDeventer, and L. Lorenzen. 1997. The potential use of geopolymeric materials to immobilise toxic metals. 1. Theory and applications. Minerals Eng. 10(7): 659–69. doi:10.1016/S0892-6875(97)00046-0
- Vandecasteele, C., V. Dutre, D., Geysen, and G. Wauters. 2002. Solidification/stabilisation of arsenic bearing fly ash from the metallurgical industry. Immobilisation mechanism of arsenic. Waste Manage. 22:143–46. doi:10.1016/S0956-053X(01)00062-9
- Zhang, L.Y., S. Ahmari, and J.H. Zhang. 2011. Synthesis and characterization of fly ash modified mine tailings-based geopolymers. Construct. Build. Mater. 25(9): 3773–81. doi:10.1016/j.conbuildmat.2011.04.005
- Zheng, L., W. Wang, and Y. Shi. 2010. The effects of alkaline dosage and Si/Al ratio on the immobilization of heavy metals in municipal solid waste incineration fly-ash based geopolymer. Chemosphere 79:665–71. doi:10.1016/j.chemosphere.2010.02.018