ABSTRACT
Stainless steel plant dust is a hazardous by-product of the stainless steelmaking industry. It contains large amounts of Fe, Cr, and Ni, and can be potentially recycled as a raw material of inorganic black pigment in the ceramic industry to reduce environmental contamination and produce value-added products. In this paper, ceramic tiles prepared with black pigment through recycling of stainless steel plant dust were characterized in terms of physical properties, such as bulk density, water absorption, apparent porosity, and volume shrinkage ratio, as well as the long-term leaching behavior of heavy metals (Cr, Ni, Pb, Cd, and Zn). The results show that good physical properties of ceramic tiles can be obtained with 8% pigments addition, sample preparation pressure of 25 MPa, and sintering at 1200 ºC for 30 min. The major controlling leaching mechanism for Cr and Pb from the ceramic tiles is initial surface wash-off, while the leaching behavior of Cd, Ni, and Zn from the stabilized product is mainly controlled by matrix diffusion. The reutilization process is safe and effective to immobilize the heavy metals in the stainless steel plant dust.
Implications: Stainless steel plant dust is considered as a hazardous material, and it can be potentially recycled for black pigment preparation in the ceramic industry. This paper provides the characteristics of the ceramic tiles with black pigment through recycling stainless steel plant dust, and the long-term leaching behavior and controlling leaching mechanisms of heavy metals from the ceramic tile. The effectiveness of the treatment process is also evaluated.
Introduction
Typically, about 20 kg stainless steel plant dust is generated per ton stainless steel produced. It is estimated that approximately 434 kt stainless steel plant (SSP) dust is produced in China based on the statistics of International Stainless Steel Forum (ISSF) (2014). These waste dusts contain large amounts of valuables in terms of Fe, Cr, and Ni, which can be present at up to 53.50%, 16.5%, and 5.42% respectively (Ma and Garbers-Craig, Citation2006), and significant levels of heavy metals, such as Cd, Zn, and Pb, which are potentially harmful to the environment and human health. In order to eliminate the impact of these heavy metals in the SSP dust, numerous treatment processes have been developed to either recover the valuables or immobilize the harmful heavy metals in the dust through a solidification/stabilization (S/S) process. The latter process provides an alternative way to reuse the wastes and can be generally recognized as an effective technology to immobilize the toxic heavy metals in the wastes and transform it into nonhazardous and value-added products (Mesci et al., Citation2009; Ma and Garbers-Craig, Citation2009; Vieira et al., Citation2013).
Black ceramic tile or brick is extensively used in building and decoration industries. The black inorganic oxide pigments used to color ceramic tile share about 25% of the inorganic pigment consumption (Yurdakul et al., Citation2011). Typical commercial inorganic black pigments are iron-chromite and Co- or Ni-containing spinels. Due to the fact that Co-containing raw materials are expensive and hazardous to human health, the iron-chromite spinels, synthesized from the mixture of iron oxides and chromium oxides at more than 1000ºC, are therefore widely concerned.
Recently, several researchers investigated the synthesis of inorganic black iron-chromite pigment with iron- or chromium-containing industrial wastes, and thereafter it was introduced into the ceramic matrix to produce black ceramic tiles (Tanisan and Turan, Citation2011; Hajjaji et al., Citation2011; Costa et al., Citation2008; Chen et al., Citation2015; Zhang et al., Citation2010; Zhang et al., Citation2014). Tanisan and Turan (Citation2011) reported that the black porcelain tile can be prepared with less expensive pigments through sintering a mixture of 40% natural chromite and 60% iron-containing oxide waste from the steel rolling mill at 1200 ºC. As the impurities oxides of Al2O3, SiO2, and MgO from the chromite will decrease the color intensity of the pigment, it is suggested to use the pigments in combination with commercial black pigments to save cost for coloration of the porcelain tile body. Moreover, Hajjaji et al. (Citation2011) and Costa et al. (Citation2008) developed a black pigment production process via sintering a mixture of galvanizing sludge from the Cr/Ni planting process and an Fe2O3-based sludge from a steel wire drawing plant. The trevorite (NiFe2O4) or nichromite (NiCr2O4) phases in the black spinel pigment can be attained when the mixture is calcined at 1000ºC for 2 hr by adjusting the Ni/Fe ratio. The coloring properties of the obtained pigment have quality comparable to those of the commercial black pigment, and the black coloration would be further enhanced with addition of minor elements such as manganese (Hajjaji et al., Citation2011; Costa et al., Citation2008). Cr-rich leather sludge from chrome-tanning processes can be used as another chromium source to prepare iron–chromium black inorganic pigments (Chen et al., Citation2015). After sintered with other metallic oxides of Fe2O3, Ni2O3, and CuO at 1200 ºC, the excellent black spinel structure and color effect of tiles can be obtained with 35–55 wt% content of chromium oxide precursor made from the washed Cr-rich leather sludge calcined at 1100ºC for 1 hr (Chen et al., Citation2015). In a previous work, iron, chromium, and nickel in SSP dust could be fully recycled into the ceramic body (Zhang et al., Citation2014). In this process, the inorganic iron–chromium pigment was synthesized through sintering SSP dust (50 wt%) and reagent-grade Cr2O3 (50 wt%) at 1200 ºC for 30 min. Then it was added into the ceramic base body to prepare black ceramic tiles. In order to fully evaluate the process, the physical properties of ceramic tiles with various sintering conditions, such as bulk density, volume shrinkage ratio, apparent porosity, and water absorption, were evaluated.
On the other hand, compared with the availability leaching tests, such as the Toxicity Characteristics Leaching Procedure (TCLP) test and the ASTM D 3987-85 test, a semidynamic leaching test is usually employed to study the long-term leachability and controlling leaching mechanisms of the heavy metals from the stabilized/solidified (S/S) products (De Groot and van der Sloot, Citation1992; Andres et al., Citation1995; Dermatas et al., Citation2004), which can be used to evaluate the effectiveness of an S/S treatment process. Several researchers investigated the long-term leaching mechanisms of the toxic substances, such as As, Pb, Cu, Cd, Cr, Zn, and Mg, from the S/S products (cements or glass) made from fly ash, ore tailings, steel foundry dust, sewage sludge, and electric furnace dust (Dutre and Vandecasteele, Citation1996; Moon et al., Citation2010; Patra et al., Citation2011; Song et al., Citation2013; Pereira et al., Citation2007). The leaching mechanisms of toxic substances are mainly controlled by diffusion, dissolution, precipitation, or diffusion and wash-off. Though the availability leaching toxicity test for the ceramic tiles showed that the leachable heavy metals meet the Chinese national limits (Zhang et al., Citation2014), the leaching mechanisms of these heavy metals from the ceramic tiles are still not clear and the effectiveness of the treatment process also requires evaluation.
The aims of this work are therefore (1) to study the physical properties of the ceramic tiles with various sintering parameters, such as bulk density, volume shrinkage ratio, apparent porosity, and water absorption, (2) to study the long-term leaching behavior and controlling leaching mechanisms of heavy metals from the colored ceramic tiles using a semidynamic leaching test, and (3) to evaluate the effectiveness of the treatment process.
Leaching models of heavy metals from the S/S products
A semidynamic leaching model for evaluating the leaching mechanisms of heavy metals from the S/S product has been developed in the past decades (De Groot and van der Sloot, Citation1992; Côtê et al., Citation1987). The controlling leaching mechanisms for heavy metals release mainly include initial surface wash-off, which is due to the soluble components on the surface of the S/S products, matrix diffusion that occurs when the components leach through the matrix of the S/S product, and dissolution or corrosion, which prevails if the solution of the matrix of the S/S product is faster than that the toxic substances diffusing through the matrix of the S/S product. Based on the leaching model established by De Groot and van der Sloot (Citation1992) and Côtê et al. (Citation1987), the initial wash-off fraction can be expressed as
where CLF(t) is the cumulative leached fraction for a species, k1 is the constant term, S is the surface area of the stabilized product, Vl is the volume of the leachant, and kl and kd are the rate constants describing the kinetics of releasing or attaching a species from the surface of the solid or from the aqueous solution, respectively. If the rate of the initial surface wash-off is fast enough, eq 1 can be simplified as CLF(t) = k1, which is the initial leached fraction of a species.
If the leaching behavior of a species is controlled by a matrix diffusion process, the cumulative leached fraction can be expressed as follows:
where V is the volume of the sample, t is the leaching time, and De is the effective diffusion coefficient.
When the dissolution process prevails, the cumulative leached fraction of a species can be derived as a linear function with leaching time:
where u0 is defined as the maximum network dissolution velocity.
Thus, the cumulative leached fraction of the toxic substances from the S/S products can be expressed as a function of leaching time, that is,
It was suggested by De Groot and van der Sloot (Citation1992) that the leaching mechanisms of a species from the S/S waste can be obtained by empirically analyzing the slope of the logarithm of cumulative leached fraction versus the logarithm of leaching time. When the slope of regression line is lower than 0.4, the leaching of a species is controlled by initial surface wash-off. The diffusion of a species from the solid matrix is the controlling mechanism if the slope of regression line is between 0.4 and 0.6, while dissolution or corrosion of the matrix may control the leaching process when the slope of the regression line is more than 0.6.
The American Nuclear Society (ANS) (1986) employed a model to evaluate the effectiveness of the S/S treatment based on Fick’s diffusion theory. According to this model, the effective diffusion coefficient (De) can be calculated as follows:
where A0 and an are the concentrations of species at the beginning and at the nth leaching period, respectively; (Δt)n is duration of the nth leaching period (tn-tn-1) and Tn is the mean leaching time of the leaching intervals ().
The value of the leaching index (LX) can be expressed as follows:
where m is the number of leaching periods and n is the nth leaching period. The value of the leaching index can also be used to evaluate the mobility of heavy metals varied from very mobile (LX = 5) to immobile (LX = 15). Typically, a treatment process can be considered as an effective method when the LX value is higher than 9, while it is not considered appropriate for disposal with an LX value lower than 8 (Dermatas et al., Citation2004).
Materials and methods
Raw materials
The stainless steel plant dust and and ceramic base body were collected from a local stainless steel plant and pigment factory, respectively. The chemical compositions and crystalline phases of these raw materials have been reported in a previous study (Zhang et al., Citation2014). The components present at more than 1% are listed in . The stainless steel plant dust mainly consists of Fe2O3 and Cr2O3 with small amounts of CaO, SiO2, MgO, MnO, and NiO, while the ceramic base body is composed of SiO2 and Al2O3 as major components and CaO, MgO, K2O, and Na2O as minor oxides. In addition, the leachable toxic Cr and Cr(VI) in the SSP dust are at 198.3 and 100.4 mg/L, which are 13 and 20 times of the national regulation limits of GB 5085.3-2007, respectively.
Table 1. Major chemical compositions of stainless steel plant dust and ceramic base body.
Preparation of ceramic tiles
The preparation process of ceramic tiles is illustrated in . The 50 wt% SSP dust and 50 wt% Cr2O3 (AR grade) were thoroughly mixed, and sintered at 1200 ºC for 30 min to prepare inorganic black pigments. Previously results have shown that good coloration properties can be obtained with addition of 8% pulverized black pigment (Zhang et al., Citation2014). Hence, approximately 20 g mixtures with 8% pulverized black pigment and ceramic base body were mixed together and pressed into cylinders with a diameter of ~2 cm. These cylinders were dried in an oven at 100ºC for 24 hr, and then sintered at 1100, 1150, 1175, 1200, and 1250ºC in a Muffle furnace (SX2-10-13) for 15, 30, 60, and 120 min, respectively. The sample preparation pressures of 20, 25, and 30 MPa and mineralizer contents of 1 and 2% were also considered. The heating rate of the furnace was ~10ºC/min and the sample was cooled down to room temperature in the furnace. The obtained ceramic cylinders were used to test the physical properties and long-term leaching behavior of heavy metals.
Physical properties test
The bulk density, water absorption, and apparent porosity of ceramic tiles were measured with the standard method of GB/T 3810.3-2006 (Test methods of ceramic tiles—Part 3: Determination of water absorption, apparent porosity, apparent relative density and bulk density). The sintered ceramic tiles were weighed (m1), and a sample was placed into the vacuum dryer with water level of 5 cm higher than the sample. The dryer was vacuumized to 10 ± 1 kPa for 30 min. Then the vacuum pump was switched off. The sample was soaked for 15 min, and weighed (m2) after being gently dried up with wet chamois leather. The buoyant weight of the vacuumized samples (m3) were also measured. The bulk density (D), water absorption (WS), and apparent porosity (AP) of ceramic tiles can be calculated as follows:
The volume shrinkage (VS) ratios of the sintered ceramic tiles were determined as follows:
where Vbs and Vas are the volume of the green and sintered ceramic samples, respectively. A field emission scanning electron microscope with an energy-dispersive spectrometer (SEM-EDS) (PhilipsXL30 TMP) was used to examine the microstructure of the ceramic tiles.
Semidynamic leaching test
For the ceramic tile with 8% pigment addition sintered at 1200 ºC for 30 min, a semi-dynamic leaching test was conducted. The chemical composition of ceramic tile with 8% pigment addition was measured by using IRIS Advantage ER/S inductively coupled plasma–atomic emission spectrometry (ICP-AES) (). The major crystalline phases in the ceramic tiles are Quartz, albite (NaAlSi3O8) and Fe1.3Cr0.7O3 (), which was determined with an x-ray diffractometer (X’Pert PRO MPD; Cu Kα radiation, 40 kV and 40 mA).
Table 2. The chemical composition of ceramic tile with 8% pigment addition.
During the leaching periods, duplicated ceramic tiles were entirely immersed into distilled water in a polyethylene bottle at room temperature. The ratio of the surface area of the cylinder ceramic samples to the volume of distilled water is 1:10 cm−1. The distilled water was replaced according to the designed intervals:
where tn is the time at the end of the nth leaching period, and t1 is the time at the end of the first leaching period, 1 hr. The concentrations of heavy metals (Pb, Cr, Cd, Ni, and Zn) in the obtained leaching solutions were determined with ICP-AES.
Results and discussion
Physical properties of ceramic tiles at various sintering conditions
Increasing temperatures can improve the sintering reaction rate of solid phases and enhance the chemical reactivity of the solid phases and diffusion capacity (Ye et al., Citation2005). shows the physical properties of ceramic tile as a function of sintering temperature with 8% pigment addition, sample preparation pressure of 25 MPa, and 30 min of sintering. It indicates that the volume shrinkage ratio and bulk density of ceramic tile increase with sintering temperature at 1100–1200 ºC, possibly due to vitrification in the presence of alkali oxides (Na2O and K2O) at elevated sintering temperature, and more melted phases would be formed to fill the pore in the ceramic tiles and therefore make it denser (Gencel et al., Citation2013). Then the volume shrinkage ratio and bulk density of ceramic tile decrease slightly above 1200 ºC. This is related to the volume expansion of closed pores in the ceramic tiles due to the improvement of gases pressure inside the closed pores (Aripin et al., Citation2014). Moreover, a higher water absorption value shows higher apparent porosity of the ceramic tiles (Baccour et al., Citation2009; Martín-Márquez et al., Citation2008). Consequently, the water absorption and porosity of ceramic tiles decrease with rising sintering temperature in the range of 1100–1250ºC. It is also found that the water absorption decreases sharply with sintering temperature, and reaches 0.23% at 1200 ºC, which is lower than the national standard of GB/T 4000.1-2006 for porcelain tiles of 0.5%.
Figure 3. Effects of sintering temperature on the physical properties of ceramic tiles: (a) bulk density and volume shrinkage; (b) water absorption and porosity (8% pigment, 25 MPa, and 30 min).
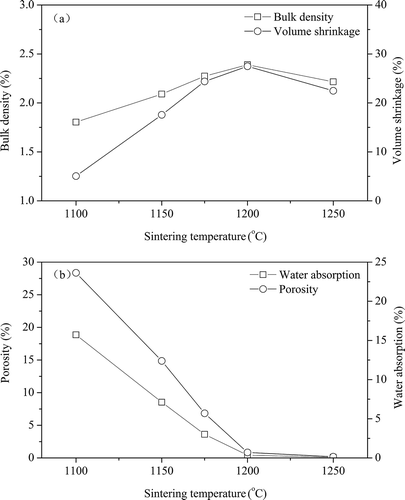
shows the results of the physical properties of ceramic tiles in relation to sintering time. It can be seen from that the bulk density and volume shrinkage of ceramic tiles initially increase within the 30 min of sintering, and reach a maximum value (2.43 g cm−3 and 27.19% respectively), then decrease with further extension of sintering time, possibly due to the slight bloating of the closed pores in the ceramic tiles ( and ). The water absorption and porosity of ceramic tiles decrease quickly from 15 min to 30 min of sintering, while there is no significant difference with sintering time longer than 30 min, and these are lower than 0.23% and 0.60%, respectively.
Figure 4. Effects of sinter time on the physical properties of ceramic tiles: (a) bulk density and volume shrinkage; (b) water absorption and porosity (8% pigment, 25 MPa, and 1200 ºC).
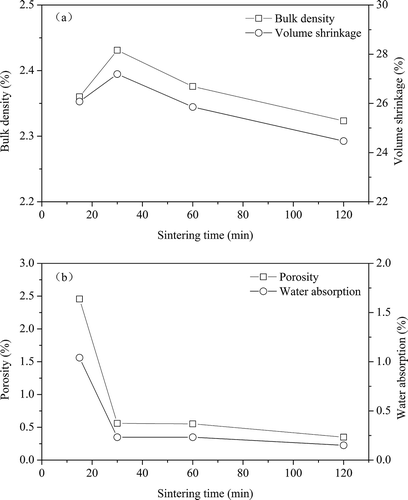
Figure 5. Microstructure of ceramic tiles sintered at various sintering periods: (a) 1200 ºC and 15 min; (b) 1200 ºC and 30 min; (c) 1200 ºC and 60 min; (d) EDS spectrum of point A.
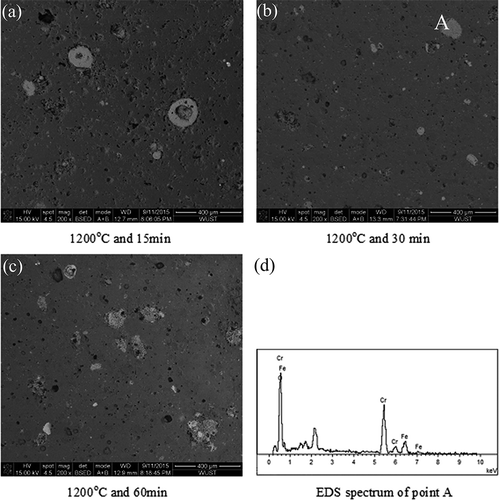
The microstructure of the ceramics tiles sintered at 1200 ºC for various periods is shown in . It illustrates that large amounts of pores are present in the ceramic tile and distribute unevenly when it is sintered at 1200 ºC for 15 min. Iron-chromium oxides (white particles as detected with EDS in ) exist in the form of agglomeration, and it is likely that the sintering reaction of pigments and ceramic body is not substantially complete due to shortage of sintering time (). However, the pores in the ceramic tiles sintered at 1200 ºC for 30 min and 60 min are relatively round, and less isolated, and the pigments are well reacted with the base body ( and ). This leads to better coloration.
presents the effects of mineralizer addition on the physical properties of ceramic tiles, when other sintering parameters keep constant. As can be seen from , increasing the mineralizer addition ratio would decrease the bulk density and volume shrinkage ratio (), while the water absorption and porosity of ceramic tiles improve (). It was observed that deformation of tile occurs when 2% CaF2 is added. This is mainly due to the fact that CaF2 can significantly decrease the firing temperature, while the excessive addition leads to enlarged high-temperature deformation of ceramic tiles (Lv, Citation2009; Zhang et al., Citation2014).
Figure 6. Effects of mineralizer addition on the physical properties of ceramic tile: (a) bulk density and volume shrinkage; (b) water absorption and porosity (8% pigment, 25 MPa, 30 min, and 1200 ºC).
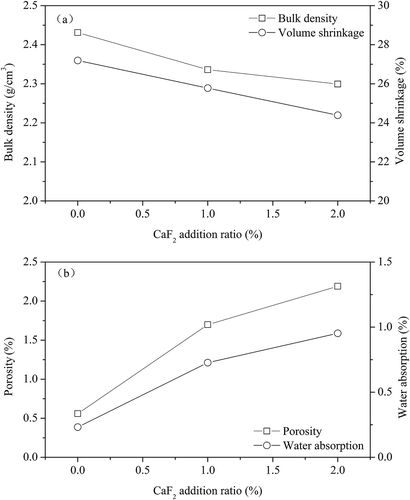
The compression strength of sample preparation has no significant effect on the bulk density of the ceramic tiles in the range between 20 MPa and 30 MPa (). However, the volume shrinkage ratio increases slightly. The water absorption and porosity of ceramic tiles decrease when the compression strength of sample preparation increases from 20 MPa to 30 MPa, due to better compacting of the green cylinder of ceramic tiles and consequently better sintering at elevated temperatures (Villanova et al., Citation2007).
Figure 7. Effects of compression strength of sample preparation on the physical properties of ceramic tile: (a) bulk density and volume shrinkage; (b) water absorption and porosity (8% pigment, 30 min, and 1200 ºC).
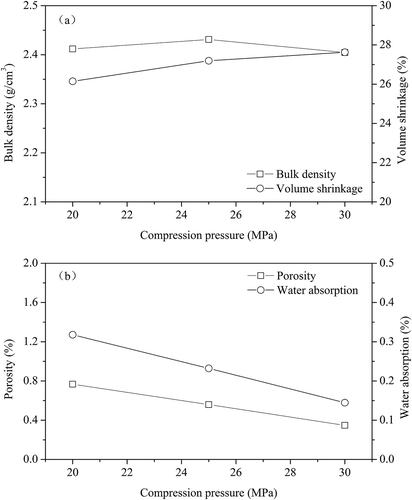
Combined with the measurements of colorimetric coordinates (L*, a*, b*) and compression strength of the sintered ceramic tiles (Zhang et al., Citation2014), good physical and coloration properties of ceramic tiles can be obtained with 8% pigments addition and sample preparation compression strength of 25 MPa with sintering at 1200 ºC for 30 min. Compared with the traditional process to synthesis black pigment with industrial-grade chemicals of Fe2O3 and Cr2O3, as well as chromite mineral, the cost of ceramic tiles produced with black pigment made from stainless steel plant dust is lower than that of the traditional production process, as part of the chemicals or minerals is replaced with stainless steel plant dust.
Leaching mechanisms of heavy metals from the ceramic tiles
The heavy metals, such as Pb, Cr, Cd, Ni, and Zn, were concerned to evaluate the controlling mechanisms and the effectiveness of the incorporation of the heavy metals into the ceramic base body according to their toxicity and contents in the ceramic tiles. Pb content in the ceramic tile is very low (0.01% in PbO), and no Pb-containing phases are detected by the x-ray diffractometer (). It is concluded that lead may be stabilized in the form of lead silicates in the matrix (Moon et al., Citation2006; Palomo et al., Citation2003). The Pb concentration in the leachate is 0.03 mg/L in 1 hr of leaching, and the relative release ratio of Pb from the ceramic tiles is 1.17%. It is under the determination limit of ICP (0.02 mg/L) in the rest of the leaching period. This suggests that it is possibly controlled by the initial wash-off.
The cumulative leached fraction (CLF) of Cr, Cd, Ni, and Zn from the ceramic tiles as a function of leaching time is shown in . It can be seen from that the cumulative leached fractions of Cr, Cd, Ni, and Zn from the ceramic tiles are 0.92%, 5.29%, 0.15%, and 18.73%, respectively. This indicates that Cr and Ni are not readily leached from the ceramic tiles (<1%). However, Cd and Zn can be easily leached during the leaching period (>5%). Moreover, the cumulative leaching concentrations of Cr, Cd, Ni, and Zn from the ceramic tiles are 0.021 mg/L, 0.014 mg/L, 0.073 mg/L, and 0.695 mg/L, respectively. These are far below the accepted safety limits of the relative heavy metals.
Figure 8. Cumulative release of heavy metals from the ceramic tile with leaching time (8% pigment, 25 MPa, 30 min, and 1200 ºC).
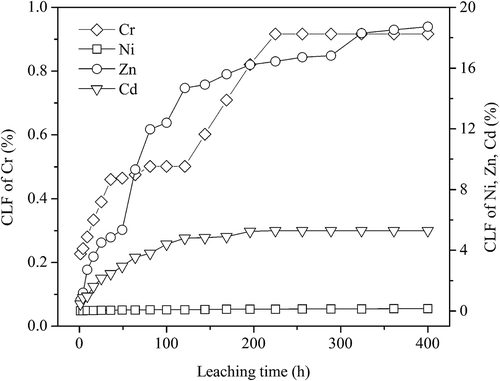
The logarithm of cumulative released ratio of heavy metals versus logarithm of leaching time of the ceramic tiles is illustrated in . This shows that the slopes of the logarithm of cumulative released fractions of Cr, Cd, Ni, and Zn versus the logarithm of leaching time are 0.28, 0.44, 0.51, and 0.59, respectively. This indicates that the controlling leaching mechanism of Cr is initial surface wash-off, because the slope of the regression line is lower than 0.4 (De Groot and van der Sloot, Citation1992). Since the slopes of the regression lines of Cd, Ni, and Zn are 0.44, 0.51, and 0.59, respectively, and are in the range of 0.4–0.6, the leaching of Cd, Ni, and Zn is mainly controlled by matrix diffusion.
Figure 9. Log cumulative release of heavy metals from the ceramic tile with log leaching time (8% pigment, 25 MPa, 30 min, and 1200 ºC).

Due to their lower contents in the ceramic tiles, no Zn-, Ni-, and Cd-containing phases in the ceramic tiles are identified with x-ray diffraction (XRD) (), and they are possibly incorporated into the glassy phases. Dalmacija et al. (Citation2010) also reported that diffusion is the controlling mechanism of Cd leached from the solidified sediment. However, Andres et al. (Citation1995) reported that Zn leaching from stabilized steel foundry dust is controlled by initial wash-off or initial wash-off followed by diffusion. Nickel leaching from the Ni-containing wastes stabilized/solidified with magnesium potassium phosphate cements could be due to the initial surface wash-off of the cylinder products (Torras et al., Citation2011).
According to the microstructure of the sintered ceramic tiles (), the chromium-bearing phase in the tiles presents as Fe1.3Cr0.7O3 in the matrix of the ceramic body (SiO2–Al2O3–Na2O based). However, during the sintering process, Fe1.3Cr0.7O3 present at the surface of ceramic tiles can be partially oxidized or reacted with lime or alkali oxides to form leachable Cr (VI)-containing phases via the following reactions (Ma and Garbers-Craig, Citation2009):
Moreover, these Cr(VI)-bearing phases can be easily leached out due to their high solubility. However, limited amounts of Cr(VI)-bearing phases will be generated as lower oxygen potential exists inside the ceramic tiles. In addition, the Cr(III)-containing phases are hardly soluble and are stabilized inside the glassy base in ceramic tile (). The chromium leaching from the ceramic tiles is therefore controlled by initial surface wash-off.
As the total leached ratios of heavy metals are lower than 20%, the leaching model can be valid to determine the effective diffusion coefficient (ANS, Citation1986). The mean values of effective diffusion coefficient (De) and leaching indexes (LX) of Cr, Cd, Ni, and Zn from ceramic tiles are presented in . The values of diffusion coefficient for the heavy metals are in the range of 5.23E-15 to 1.61E-10 cm2 s−1. This indicates that Ni is the most stabilized heavy metal in the ceramic tiles. The leaching indexes are higher than 9 for Cr, Cd, Ni, and Zn; the treatment process is therefore effective to immobilize the heavy metals and suitable for “controlled utilization.”
Table 3. Mean values of effective diffusion coefficient and leaching index of heavy metals.
Conclusions
The bulk density of ceramic tiles has no significant change with compression strength of sample preparation. However, increasing mineralizer addition ratio would decrease the bulk density of ceramic tiles. The bulk density of ceramic tiles initially increases within the 30 min of sintering, and decreases with further sintering.
The volume shrinkage ratio of ceramic tiles increase with sintering temperature of 1100–1200 ºC and compression strength of sample preparation, while it decreases with an increasing addition ratio of mineralizer.
The water absorption and porosity of ceramic tiles increase with increasing of addition ratios of mineralizer, decreasing sintering temperature, and sample preparation compression strength. They decrease quickly from 15 min to 30 min of sintering at 1200 ºC and show no significant change with extending the sintering time.
Good physical properties of ceramic tiles can be obtained with 8% pigments addition and sample preparation compression strength of 25 MPa, sintering at 1200 ºC for 30 min.
The controlling leaching mechanism of Cr and Pb is initial surface wash-off, while the leaching of Cd, Ni, and Zn is controlled by matrix diffusion. The diffusion coefficient of heavy metals ranged from 5.23E-15 to 1.61E-10 cm2 s−1, and the leaching indexes are higher than 9 for all the selected heavy metals; the treatment process is therefore effective to immobilize the heavy metals in the stainless steel plant dust.
Funding
The authors gratefully acknowledge the National Natural Science Foundation of China (50804037) and the Innovation Fund of Wuhan University of Science and Technology for financial support.
Additional information
Funding
Notes on contributors
Renbo Zhu
Renbo Zhu, Yongsheng Cai, Yuxiang Chen, Tong Yang, and Boyu Duan are students at the Wuhan University of Science and Technology.
Guojun Ma
Guojun Ma and Zhengliang Xue are professors of waste management and recycling at the State Key Laboratory of Refractories and Metallurgy, Wuhan University of Science and Technology, Wuhan, People’s Republic of China.
Yongsheng Cai
Renbo Zhu, Yongsheng Cai, Yuxiang Chen, Tong Yang, and Boyu Duan are students at the Wuhan University of Science and Technology.
Yuxiang Chen
Renbo Zhu, Yongsheng Cai, Yuxiang Chen, Tong Yang, and Boyu Duan are students at the Wuhan University of Science and Technology.
Tong Yang
Renbo Zhu, Yongsheng Cai, Yuxiang Chen, Tong Yang, and Boyu Duan are students at the Wuhan University of Science and Technology.
Boyu Duan
Renbo Zhu, Yongsheng Cai, Yuxiang Chen, Tong Yang, and Boyu Duan are students at the Wuhan University of Science and Technology.
Zhengliang Xue
Guojun Ma and Zhengliang Xue are professors of waste management and recycling at the State Key Laboratory of Refractories and Metallurgy, Wuhan University of Science and Technology, Wuhan, People’s Republic of China.
References
- American Nuclear Society. 1986. American National Standard measurements of the leachability of solidified low-level radioactive wastes by a short-term test procedure. ANSI/ANS, 16.1. La Grange Park, IL: American Nuclear Society.
- Andres, A., I. Ortiz, J.R. Viguri, and A. Irabien. 1995. Long-term behaviour of toxic metals in stabilized steel foundry dusts. J. Hazard. Mater. 40:31–42. doi:10.1016/0304-3894(94)00078-U
- Aripin, H., S. Mitsudo, B. Rahmat, S. Tani, K. Sako, Y. Fujii, K. Kikuchi, T. Saito, T. Idehara, and S. Sabchevski. 2014. Formation of porous clay ceramic using Sago waste ash as a prospective additive material with controllable milling. Sci. Sinter. 46:55–64. doi:10.2298/SOS1401055A
- Baccour, H., M. Medhioub, F. Jamoussi, and T. Mhiri. 2009. Influence of firing temperature on the ceramic properties of Triassic clays from Tunisia. J. Mater. Process. Technol. 209:2812–17. doi:10.1016/j.jmatprotec.2008.06.055
- Chen, Z., Y. Dun, Z. Li, D. Sun, and C. Zhu. 2015. Synthesis of black pigments containing chromium from leather sludge. Ceram. Int. 41:9455–60. doi:10.1016/j.ceramint.2015.04.001
- Costa, G., V.P. Della, M.J. Ribeiro, A.P.N. Oliveira, G. Monros, and J.A. Labrincha. 2008. Synthesis of black ceramic pigments from secondary raw materials. Dyes Pigments 77:137–44. doi:10.1016/j.dyepig.2007.04.006
- Côtê, P. L., T.W. Constable, and A. Moreira. 1987. An evaluation of cement-based waste forms using the results of approximately two years of dynamic leaching. Nucl. Chem. Waste Manage. 7:129–39. doi:10.1016/0191-815X(87)90007-6
- Dalmacija, M.B., M.D.J. Prica, B.D. Dalmacija, S.D. Rončević, and L.M. Rajić. 2010. Correlation between the results of sequential extraction and effectiveness of immobilization treatment of lead- and cadmium-contaminated sediment. Sci. World J. 10:1–19. doi:10.1100/tsw.2010.13
- De Groot, G.J., and H.A. van der Sloot. 1992. Determination of leaching characteristics of waste materials leading to environmental product certification. In Stabilisation and Solidification of Hazardous, Radioactive and Mixed Wastes, ed. T.M. Gillian and C.C. Wiles, 149–69. Philadelphia, PA: American Society for Testing and Materials.
- Dermatas, D., D.H. Moon, N. Menounou, X. Meng, and R. Hires. 2004. An evaluation of arsenic release from monolithic solids using a modified semi-dynamic leaching test. J. Hazard. Mater. B116:25–38. doi:10.1016/j.jhazmat.2004.04.023
- Dutre, V., and C. Vandecasteele. 1996. An evaluation of the solidification/stabilisation of industrial arsenic containing waste using extraction and semi-dynamic leach tests. Waste Manage. 16:625–31. doi:10.1016/S0956-053X(97)00003-2
- Gencel, O., M. Sutcu, E. Erdogmus, V. Koc, V.V. Cay, and M.S. Gok. 2013. Properties of bricks with waste ferrochromium slag and zeolite. J. Clean. Prod. 59:111–19. doi:10.1016/j.jclepro.2013.06.055
- Hajjaji, W., M.P. Seabra, and J.A. Labrincha. 2011. Evaluation of metal-ions containing sludges in the preparation of black inorganic pigments. J. Hazard. Mater. 185:619–25. doi:10.1016/j.jhazmat.2010.09.063
- International Stainless Steel Forum. 2014. Stainless and heat resisting steel crude steel production (Ingot/Slab Equivalent), 2014. http://www.worldstainless.org/crude_steel_ production/meltshop_production_2001_2014.
- Lv, S.Z. 2009. Study on application of fluorite tailings in low-temperature fast-firing ceramic tile for external wall. New Build. Mater. 2:86–87.
- Ma, G., and A.M. Garbers-Craig. 2006, A review on the characteristics, formation mechanisms and treatment processes of Cr(VI)-containing pyrometallurgical wastes. J. South. Afr. Inst. Min. Metall. 106:753–63.
- Ma, G., and A.M. Garbers-Craig. 2009. Stabilisation of Cr(VI) in stainless steel plant dust through sintering using silica-rich clay. J. Hazard. Mater. 169:210–16.
- Martín-Márquez, J., J.M. Rincón, and M. Romero. 2008. Effect of firing temperature on sintering of porcelain stoneware tiles. Ceram. Int. 34:1867–73. doi:10.1016/j.ceramint.2007.06.006
- Mesci, B., S. Çoruh, and O.N. Ergun. 2009. Leaching behaviour and mechanical properties of copper flotation waste in stabilized/solidified products. Waste Manage Res. 27:70–77. doi:10.1177/0734242X07082896
- Moon, D.H., and D. Dermatas. 2006. An evaluation of lead leachability from stabilized/solidified soils under modified semi-dynamic leaching conditions. Eng. Geol. 85:67–74. doi:10.1177/0734242X07082896
- Moon, D. H., D. Dermatas, and D.G. Grubb. 2010. Release of arsenic (As) and lead (Pb) from quicklime-sulfate stabilized/solidified soils under diffusion-controlled conditions. Environ. Monit. Assess. 169:259–65. doi:10.1177/0734242X07082896
- Palomo, A., and M. Palacios. 2003. Alkali-activated cementitious materials: Alternative matrices for the immobilization of hazardous wastes: Part II. Stabilization of chromium and lead. Cem. Concrete Res. 33:289–95. doi:10.1016/S0008-8846(02)00964-X
- Patra, A.C., C.G. Sumesh, S. Mohapatra, S.K. Sahoo, R.M. Tripathi, and V.D. Puranik. 2011. Long-term leaching of uranium from different waste matrices, J. Environ. Manage. 92:919–25. doi:10.1016/j.jenvman.2010.10.046
- Pereira, C.F., Y.L. Galiano, M.A. Rodriguez-Pinero, and J.V. Parapar. 2007. Long and short-term performance of a stabilized/solidified electric arc furnace dust. J. Hazard. Mater. 148:701–7. doi:10.1016/j.jenvman.2010.10.046
- Song, F., L. Gu, N. Zhu, and H. Yuan. 2013. Leaching behavior of heavy metals from sewage sludge solidified by cement-based binders. Chemosphere 92:344–50. doi:10.1016/j.chemosphere.2013.01.022
- Tanisan, B., and S. Turan. 2011. Black ceramic pigments for porcelain tile bodies produced with chromite ores and iron oxide waste. J. Ceram. Process. Res. 12:462–67.
- Torras, J., I. Buj, M. Rovira, and J. de Pablo. 2011. Semi-dynamic leaching tests of nickel containing wastes stabilized/solidified with magnesium potassium phosphate cements. J. Hazard. Mater. 186:1954–60. doi:10.1016/j.jhazmat.2010.12.093
- Vieira, C.M.F., R. Sanchez, S.N. Monteiro, N. Lalla, and N. Quaranta. 2013. Recycling of electric arc furnace dust into red ceramic. J. Mater. Res. Technol. 2:88–92. doi:10.1016/j.jmrt.2012.09.001
- Villanova, D.L., and C.P. Bergmann. 2007. Sinterability study of ceramic bodies made from a mixture of mineral coal bottom ash and soda-lime glass cullet. Waste Manage. Res. 25:77–82. doi:10.1016/j.jmrt.2012.09.001
- Ye, C., Q. Xia, W. Lu, and J. Kuang. 2005. The research of making use of the chromium salt dreg to produce the ceramic pigments. China Ceram. 41:33–36.
- Yurdakul, H., S. Turan, and E. Ozel. 2011. The mechanism for the colour change of iron chromium black pigments in glazes through transmission electron microscopy techniques. Dyes Pigments 91:126–33. doi:10.1016/j.dyepig.2011.03.014
- Zhang, L., Z. Pi, C. Yang, X. Tian, and S. Zhang. 2010. Synthesis of chromium-doped malayaite pigments from wastewater containing low chromium(VI). J. Air Waste Manage. Assoc. 60:1257–61. doi:10.3155/1047-3289.60.10.1257
- Zhang, X., G. Ma, Y. Jin, and P. Cheng. 2014. Preparation of ceramic tiles with black pigments using stainless steel plant dust as a raw material. Ceram. Int. 40:9693–700. doi:10.1016/j.ceramint.2014.02.050