ABSTRACT
A novel slow-release potassium fertilizer (SPF) was synthesized using Pidgeon magnesium slag (PMS) and potassium carbonate, which could minimize fertilizer nutrient loss and PMS disposal problems. Orthogonal experiments were conducted to determine the optimum conditions for synthesis. The potassium (K)-bearing compounds of SPF existed mainly in the form of crystalline phases Ca1.197K0.166SiO4, K2MgSiO4, and K4CaSi3O9, and in the noncrystalline phase. The active silicon content of SPF was 2.09 times as much as that of magnesium slag, and the slow-release character of SPF met the requirement for partly slow-release fertilizer in the national standard (GB/T23348-2009). The best models for describing the K release kinetics in water and 2% citric acid were the Elovich model and the first-order model, respectively. The heavy metal contents of SPF conformed to the national standard for organic–inorganic compound fertilizers, and the leaching mass concentrations of heavy metals and Fluorine were far lower than the limit values of the identification standard for hazardous waste identification for extraction toxicity (GB5085.3-2007), and also met the class II quality standard for ground water. The environmental risk of SPF is therefore very low, but because SPF is alkaline, its effect on soil pH should be taken into account.
Implications: PMS is the solid waste resulting from the production of magnesium metal by Pidgeon’s reduction process. Utilization of PMS in the high-technology and high-value areas may promote the high-efficiency development of worldwide collection metallic magnesium industry and contribute to the reduction of emissions of fine dust to air. This paper presents one of the new techniques in the use of PMS as a slow-release fertilizer by adding K2CO3. The product can serve as a very cost-effective and reliable artificial fertilizer.
Introduction
Magnesium slag is the solid waste resulting from the production of magnesium metal by the silicothermic reduction process. Silicothermic reduction processes include Pidgeon’s reduction and Magnet’s reduction, developed in Canada and France, respectively (Ramakrishnan and Koltun, Citation2004; Eli and Galid, Citation2006). Pidgeon’s reduction is the primary process used for the production of magnesium in China (Du et al., Citation2010; Brown, Citation2009), and the residue of this magnesium extraction process is Pidgeon magnesium slag (PMS). Since 1999, China has been the largest magnesium production and export country in the world, and approxiately 70% of magnesium production in China takes place in Shanxi Province. For every ton of primary magnesium produced by the Pidgeon reduction process, 6–9 tons of PMS is discharged (Cherubini et al., Citation2008). According to a 2011 report by the China Nonferrous Metals Industry Association, the primary magnesium yield worldwide was 0.78 million tons, 0.66 million tons of which was produced in China, where approximately 5 million tons of PMS were produced (China Nonferrous Metals Industry Association, Citation2012). The amount of PMS discharged is increasing with the growing demand for magnesium worldwide, and if the large quantity of magnesium slag produced does not find an effective application, it not only causes serious environmental pollution and ecological issues (Djokic et al., Citation2012b; Gao et al., Citation2008), but also results in the waste of valuable resources. Considering the sustainable development of the metallic magnesium industry, it is important to find an effective approach for the disposal of large quantities of PMS. Due to its high content of CaO and SiO2, PMS has previously been mainly used for building materials (Oliverira et al., Citation2004; Djokic et al., Citation2012a; Wang et al., Citation2011; Lu et al., Citation2013). In recent years, new ways of reusing PMS have been reported: researchers have used PMS as a heterogeneous solid catalyst of MgO–CaO/Al2O3, enabling the transesterification of vegetable oils to biodiesel (Elihann et al., 2012; Kwon et al., Citation2012; Zhang and Huang, Citation2011); based on alkali-activated and ion-exchange reactions, Zhang et al. synthesized a novel photocatalyst derived from PMS (Zhang et al., Citation2015); Fan et al. investigated the characteristics of PMS and the feasibility of PMS as a desulfurizer (Fan et al., Citation2012); Tian et al. published a study describing that the calcium hexaluminate/anorthite ceramic was prepared by magnesium slag, kaolin, and industrial alumina at different sintering temperatures (Tian et al., Citation2013); and Liang et al. reported that PMS as raw materials was applied to prepare silicon fertilizer by acid leaching and roasting with additives (Liang et al., Citation2015). Nevertheless, very large amounts of PMS are being dumped in slag disposal areas without any profit being made; in order to rectify this situation, new alternative uses need to be developed.
According to statistics published by the United Nations Department of Economic and Social Affairs, the world population will increase to 9022 billion in the year 2075 (Department of Economic and Social Affairs, United Nations, 2004), and this will necessitate the use of agricultural products that give higher levels of food productivity. High crop yields are normally achieved by improving soil properties through the addition of fertilizers, but fertilizer efficiency is usually low because of the lack of balance between the speed at which nutrients are released from the fertilizer and the speed at which nutrients are absorbed by plant roots. A large amount of nutrients are lost to the environment, causing pollution. Previous studies have shown that in China, the utilization of potassium fertilizers is 50~60%, whereas in acid soils the loss of nutrients is even greater, giving a potassium utilization level of just 40% (Department of Agriculture Science and Technology, Citation1995; Ren, Citation2010). The use of slow-release fertilizers, which release nutrients slowly, can help to avoid this problem. Preparing slow-release fertilizers using PMS, therefore, will help to alleviate the environmental hazards associated with slag stockpiling and fertilizer loss, as well as improving fertilizer efficiency.
China is an influential, agriculture-oriented, and highly populous country, and fertilizers are therefore important in order to ensure a high agricultural output. The heavy metals and radioactive elements contents in PMS meet the relevant standards, and PMS also contains large amounts of elements such as Si, Ca, Mg, and Fe, which are of nutritional value to plants (Li et al., Citation2015; Zhao, Citation2007). However, since PMS has a characteristically stable nature, these nutritional elements are bound in the form of indissoluble compounds, which cannot be absorbed by plants. In this work, a novel slow-release potassium fertilizer (SPF) was synthesized by adding potassium carbonate to PMS. Under the high-temperature condition, K2CO3 can decompose into K2O and react with CaO, SiO2, and MgO to obtain K2O-CaO-SiO2 and K2O-MgO-SiO2 in the ternary systems (Morcy et al., Citation1930; Yasuko et al., Citation2014). PMS contains CaO, SiO2, and MgO; therefore, the mixture of the K-bearing silicates can be obtained by adding K2CO3 to PMS, which will convert the rapid available potassium in K2CO3 into the slowly available potassium for increasing the utilization of potassium fertilizer, and the solubility of Si and the other nutritional elements also will be improved. This study can provide insights in terms of the preparation of slow-release fertilizers and the reuse of PMS.
Materials and methods
Materials
PMS from Hongfu Magnesium Corporation was used in this study, and the sample was obtained after exiting the furnace and cooled by air. The main chemical composition of the PMS sample is outlined in , which shows that it contained 2.46% active silicon (as SiO2); therefore, its active silicon content in total silicon (AST) was 9.01%. The X-ray diffraction (XRD) pattern of PMS is illustrated in , which shows its main constituent phases are β-Ca2SiO4, γ-Ca2SiO4, periclase, and free CaO. The standard reagents (Agilent Technologies Co., Santa Clara, CA) were of Guaranteed Reagent (GR) grade, whereas the potassium carbonate was an industrial grade reagent (purity ≥99%), and other chemical reagents used were of Analytical Reagent (AR) grade.
Table 1. The major chemical composition and the active silicon (as SiO2) content of PMS (%).
Methods
Synthesis of SPF
PMS was milled to granules of size ≤120 μm, and mixtures of varying proportions of PMS and K2CO3 were then made up (K2O content of SPF was approximately 15%, 20%, and 25%, respectively). These mixtures were then heated for different lengths of time (40, 60, and 80 min), and then cooled by different methods in order to prepare SPF. The K-bearing component in the synthesized SPF decomposed at 1400 °C, so the yield for K was lower than at 1100~1300 °C. The yields of K in the synthesized SPF at synthesized temperatures 1100~1300 °C were 83.6~94.5%, and the mean yield of K was 91.5%, which was capable of meeting the actual production demand. At a synthesized temperature of 1100 °C, the synthesized SPF contained unreacted K2O, whereas the initial release rate of K (Kin) in water was 54%, with poor slow-release property. Therefore, the heating temperature was set to 1200~1300 °C.
The effects of heating temperature (T), holding time (t), K2O content (P), cooling method (C), and blank treatment (B) on AST and Kin were investigated through orthogonal experiments with five factors and three levels. The experiments were conducted according to the orthogonal layout of L18 (37) (). Kin is the initial release rate of K, which is the accumulated release rate of K on the first day, which was determined according to the method described under the subheading “Solubility characteristics of SPF”. The average response for each factor was calculated at each level, labeled as Ai (i =1, 2, or 3) for AST and Ki (i =1, 2, or 3) for Kin, respectively, where i represents a level.
Table 2. Results of orthogonal experiments.
Solubility characteristics of SPF
PMS and SPF samples were treated according to standard NY/T797-2004 (Ministry of Agriculture of the People’s Republic of China, Citation2004), and the quantity of active silicon (as SiO2) that they contained was measured by the silicon-molybdenum blue spectrophotometric method. The chemical compositions of PMS, SPF, and SPF after leaching from 2% citric acid were determined by X-ray fluorescence (XRF) spectroscopy (PANalytical, Almelo, The Netherlands).
Microstructure and mineralogical composition of SPF
The mineralogical composition of SPF was determined using a D2 Advance X-ray diffractometer (Bruker Corporation, Billerica, MA, USA). According to the semiquantitative analysis and crystallinity analysis of DIFFRAC EVA version 3.0 software, the diffraction lines of X-ray diffraction (XRD) pattern for SPF were analyzed to obtain the composition of the major crystalline phases and the crystallinity of SPF. The morphology and microstructure of SPF were studied using a JSM7001F scanning electron microscope (JEOL Corporation, Japan) coupled with a Bruker QX200 energy-dispersive spectrometer (Bruker Corporation, Germany) (SEM-EDS).
Solubility characteristics of SPF
After the SPF samples were milled to granules of size 0.5~0.9 mm, K release rates in both water and 2% citric acid were tested according to the method proposed by Trenkel (Citation1997). Four-gram samples of fertilizer were socked in 1000-mL volumetric flasks with 1000 mL of either deionized water or 2% citric acid. At specific time intervals (1, 3, 5, 7, 14, 28, 42, and 72 days after incubation), 50 mL of the leaching solution was transferred, and the potassium content (K) of each leaching solution was determined by flame photometry. Fifty milliliters of fresh deionized water or 2% citric acid was added to each volumetric flask to ensure the volume of the solution remained at 1000 mL. The leaching residues, for 72 days in water and 14 days in citric acid, were determined by XRD. The accumulated release rates of K (v) were calculated as follows:
where v is the accumulated release rate of K (%), K is the K content in the solution (g), ∑Ki is the accumulated amount of K in the solution that has been transferred (g), and K0 is the K content in SPF (g).
The kinetic equations used to describe the rate of K release are presented as below (Jalali and Zarabii, Citation2006; Long et al., Citation2004; Sparks and Carski, Citation1985; Shariatmadari et al., Citation2006):
where a and b are model parameters, y is the amount of K released after t days, and x is the dissolution time. The goodness of fit for each kinetic equation was evaluated according to its coefficient of determination (R2) and sum of squares for error (SSE).
Environmental risk assessment of SPF
For the analysis of the heavy metal and F contents of SPF, the sample was digested according to the standard method ASTMD6357-00a (American Society for Testing and Materials, Citation2000), after which the Cd, Cr, Cu, Ni, Pb, and Zn in the digestion solution were analyzed using an inductively coupled plasma atomic emission spectrometer (ICP-AES) (Thermo ICAP6300; Thermo Electron Corporation, USA), and the concentrations of Hg and As were analyzed using a Beijing Jitian AFS-8220 atomic fluorescence spectrometer (AFS; Beijing Titan Instruments Corporation, China). The F content in SPF was determined according to standard GB/T 6730.28-2006 (General Administration of Quality Supervision, Inspection and Quarantine [AQSIQ], Citation2007b).
For the analysis of the pH value of SPF, a 5.0-g SPF sample was mixed with 50 mL deionized water in a 100-mL beaker, agitated for 1 min, and left to stand for 30 min. The pH value of the mixture was then determined using a Denver Ub-7 pH meter (Denver Instruments, Co., Arvada, CO, USA).
The leaching toxicity of SPF was tested according to the solid waste extraction procedure for leaching toxicity—H2SO4/HNO3 method, standard HJ/T299-2007 (State Bureau of Environmental Protection of China, Citation2007). The heavy metal content of the leaching solution was analyzed by ICP-AES and AFS; F was determined by the fluorine ion–selective electrode method; and the concentration of Cr(VI) was determined by the standard GB/T 15555.4-1995 (State Bureau of Environmental Protection of China, Citation1995).
Results and discussion
Process optimization for synthesizing SPF
The laboratory results of the orthogonal experiments are listed in . The Kin of SPF was 23.28~31.25%, and the AST of SPF was 1.88~2.77 times than that of PMS. This showed that Si release in PMS was improved and K release in K2CO3 was slowed down due to the reaction of PMS and potassium carbonate. The relative significance of the various factors on AST can be described in order as T > C > t > P, where T has significant influence on AST (α = 0.05). Similarly, the relative significance of the various factors on Kin could be described as T > C > P > t, where T and C had significant influence on Kin (α = 0.05). The effects of the various factors on the results are shown in , which illustrates that the holding time and the K2O content had no significant effect on the results. A higher AST and a lower Kin of SPF can be achieved by using water quenching as a cooling method and increasing the heating temperature; however, this also consumed more energy. Hence, based on comprehensive consideration of the energy efficiency and the effects of all factors on AST and Kin, it can be concluded that the optimal conditions for SPF synthesis were K2O content = 20%, T = 1300 °C, holding time = 60 min, and forced air cooling. SPF synthesized according to the above conditions was used to the following test, and the major chemical composition of the synthesized SPF is shown in , which indicates that the active silicon content of SPF was 2.09 times as much as that of magnesium slag.
Table 3. The major chemical composition and the active silicon (as SiO2) content of SPF (%)
Microstructure and mineralogical composition of SPF
The XRD pattern of SPF indicates that the major constituent phases include the K-bearing crystalline phases Ca1.917K0.166SiO4 (0.083K2O-1.917CaO-SiO2), K2MgSiO4 (K2O-MgO-SiO2), and K4CaSi3O9 (2K2O-CaO-3SiO2), and the unreacted phases Ca2SiO4 and periclase (MgO) (). The crystallinity of SPF was 37.3%, which indicated that it was composed of a greater proportion of the amorphous phase than the crystalline phase. The crystalline phase comprised 18.96% Ca1.917K0.166SiO4, 9.84% Ca2SiO4, 5.12% periclase, 1.71% K2MgSiO4, and 1.67% K4CaSi3O9. Therefore, 2.41% K2O and 11.6% SiO2 were in the crystalline phase, whereas 17.59% K2O and 10.69% SiO2 were in the amorphous phase (as calculated from ). At the process of synthesizing SPF by use of PMS and K2CO3, K2CO3 decomposed at 800~1000 °C into K2O and CO2, and K2O reacted with CaO, SiO2, or MgO in PMS to produce the potassium silicate crystalline phases (Ca1.917K0.166SiO4, K2MgSiO4, K4CaSi3O9) and amorphous phases. In previous studies, Ca1.917K0.166SiO4 and K2MgSiO4 have been found in the synthetic slow-release K fertilizer: Yamada et al. studied the preparation of a slow-release potassium fertilizer using rice husks, dolomite, and potassium carbonate, and Tokunaga et al. synthesized a slow-release potassium fertilizer using coal ash and KOH, and both studies found that K2MgSiO4 in the fertilizers was the slow-release characteristic (Yamada et al., Citation1994; Tokunaga et al., Citation1991); Shen et al. investigated the crystallizability of a slow-release potassium silicate fertilizers, the result showed that the existence of Ca1.917K0.166SiO4 and the amorphous phase in the fertilizer was the main cause for the slow-release characteristic of the fertilizer (Shen et al., Citation2005). The major constituent phases in SPF are the crystalline phases Ca1.917K0.166SiO4, K2MgSiO4, and K4CaSi3O9 and the amorphous phases, which facilitated the release of indissoluble nutrients such as Ca, Si, and Mg from the SPF, but slowed the release of K; as a result, SPF possesses the slow-release characteristic.
The SEM micrographs of PMS () and SPF (, , and ) show that, compared with PMS, SPF contained a larger proportion of the glass phase, which existed mainly in the form of layers and less granular substances with obvious edge angles, and there was no clear boundary between the granules of SPF, which were fused together. EDS microscanning of the SPF sample showed that the compositions of some points were consistent with the chemical compositions of SPF (, ; points 4 and 7 in ). In addition, it can be concluded that the potassium calcium silicate compounds Ca1.917K0.166SiO4 (points 1, 5, and 8 in ), Ca2SiO4 (points 2 and 6 in ), and MgO (point 3 in ) were present in the fertilizer by analyzing the mole ratios of atoms in SPF, which was in accordance with the XRD analysis results.
Table 4. Results of SEM-EDS analysis for SPF.
The nutrient release characteristics of SPF
The K accumulated release rates for the instant fertilizer (K2SO4) and SPF in both water and 2% citric acid are shown in . In water, the K accumulated release rate for the K2SO4 fertilizer after 1 day was approximately 90.81 ± 2.45%, and after 7 days K was released completely (the accumulated release rate of K was 99.42 ± 1.24%). However, the K accumulated release rate for SPF after 1 day was 25.56 ± 1.21% in water, and the accumulated release rate of K was 67.38 ± 2.51% in 28 days. With the sum of nutrients release slightly higher than 15% at the first day and not above 80% in 28 days, this indicated that the slow-release character of SPF met the requirement for the partly slow-release fertilizer in the national standard GB/T 23348-2009 (AQSIQ, Citation2009b). The K accumulated release rate for SPF after 1 day was 52.24 ± 2.12% in citric acid, and the accumulated release rate of K was 95.01 ± 1.21% in 14 days, which was higher than the release rate for SPF in water. This shows that citric acid can accelerate K release from such poorly soluble sources as SPF. The roots of plants can release citric acid, and the release amount of citric acid will increase as the plant grows (Miyasaka et al., Citation1991; Eitaro and Kiyoshi, Citation1974; Kochian et al., Citation2004). Therefore, the nutrients in SPF can be released effectively according to requirements for plant growth, consequently improving the utilization rate of fertilizer.
Figure 5. The accumulated release rate of potassium for SPF in water and 2% citric acid and for K2SO4 fertilizer in water.
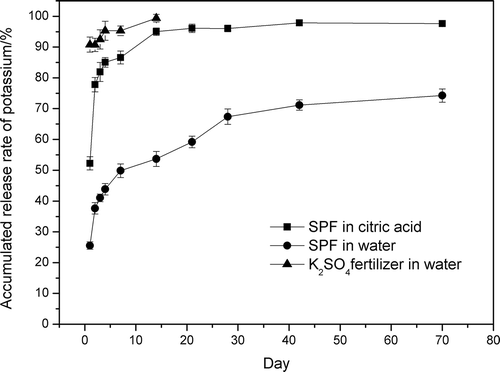
The kinetic data for K release in water and citric acid were tested using the first-order equation, the power function, the parabolic diffusion equation, and the Elovich equation, and the results are shown in . According to R2 and SSE, the relative degree of fit for the kinetic equations describing K release in water was in the order: the Elovich model > the power function > the parabolic diffusion equation > the first-order equation, and the Elovich model was a good fit for time-dependent K release in water. This indicates that the process of K release can be divided into two stages: first, K on the surface of the mineral phases is released, and then K inside the mineral phases of SPF is transferred to the surface. Hence, the kinetic function for K release from SPF in water was y = 0.277 + 0.111 ln(x), and the stated release time of SPF was 112.4 days when the release rate of K in water was 80%, which conforms to the growth cycles of many crops. The relative degree of fit for the kinetic equations describing K release in 2% citric acid was in the order: the first-order equation > the Elovich model > the power function > the parabolic diffusion equation, and the first-order model was a good fit for time-dependent K release in 2% citric acid. The kinetic function for K release from SPF in 2% citric acid was y = 0.942 − 0.942e−0.778x, which indicates that the K release from SPF in water and citric acid conformed to the different kinetic mechanisms. Wang et al. analyzed the K release kinetics of biotite in different extractants, and their results showed that the K release kinetics of biotite in weak organic acid were different from that in HNO3 (Wang et al., Citation2012). Cui et al. and Song et al. found that differences in the structure of the extractant resulted in different kinetic release mechanisms (Cui et al., Citation2002; Song and Huang, Citation1988). In the leaching process of SPF in citric acid, the citric acid with hydroxy and carboxyl groups can tend to form metal-organic complexes in solution with metal ions from mineral structures in SPF, thus accelerating the decomposition of K-bearing minerals and the release of K.
Table 5. Kinetics of K release from SPF.
The XRD pattern for SPF after leaching in 2% citric acid is shown in , which indicates that the crystal structure of SPF was destroyed and transformed into the amorphous phase after leaching in 2% citric acid; and the chemical composition of SPF after leaching in citric acid is shown in , which indicates that the citric acid could further releasing of the beneficial elements Ca, Fe, Mg, Al, as well as Si in SPF by comparison with the chemical composition of SPF (). The XRD patterns for SPF after leaching in water () show that the crystal phases of SPF almost have no change after leaching in water, whereas the relative peak intensities of the mineral phases have apparent changes. After leaching in the water, the crystallinity of SPF was reduced to 25.4% and the peak intensity for the potassium silicate crystal phase was weakened, which shows that the potassium silicate crystal phase have been partially dissolved, with the nutrients in SPF being slowly released into the water.
Table 6. The major chemical composition of SPF after leaching from 2% citric acid (%).
Environmental risk assessment of SPF
The heavy metal contents of SPF were lower than the limits for heavy metals for standard organic–inorganic compound fertilizers (GB18877-2009; AQSIQ, Citation2009a), and the traces of Cu and Zn in SPF are beneficial to the growing of crops (). The leaching toxicity of SPF was assessed by the solid waste extraction procedure for leaching toxicity (H2SO4/HNO3 method), and the results () show that the leaching mass concentrations for heavy metals and F in SPF are lower than the limit values of the identification standards for hazardous wastes (GB5085.3-2007: AQSIQ, Citation2007a) and meet the class II quality standards for ground water (GB/T 14848-93: AQSIQ, 1993). Cr(VI) was not detected in the leaching solution, which indicated that Cr in SPF is in the less harmful form of Cr(III). The heavy metals and F in SPF are therefore likely bound within stable states, greatly lowering the pollution risk of SPF. Since it is an alkaline fertilizer (pH = 13.2), when SPF is applied to calcareous and alkaline soils, the pH value of the soil could be increased, affecting plant growth and the validity of the beneficial elements in SPF. However, when SPF is applied to acid soils, it can cause an increase in the beneficial elements present in the soil. Therefore, when considering the agricultural utilization of SPF, the fertilizer effect on different pH soil should be investigated.
Table 7. Heavy metal and fluoride contents of SPF (mg·kg−1).
Table 8. Leaching toxicity of SPF (mg·L−1).
Conclusion
Orthogonal experiments were conducted to determine the optimum conditions for synthesizing SPF. After comprehensive consideration of the energy efficiency along with the effects of all the factors on AST and Kin, the optimal conditions were concluded as follows: K2O content = 20%, T = 1300 °C, holding time = 60 min, and forced air cooling. The K-bearing compounds in SPF were in the form of potassium silicate crystalline phases Ca1.917K0.166SiO4, K2MgSiO4, and K4CaSi3O9, and the amorphous phases. The active silicon content of SPF was 2.09 times as much as that of magnesium slag, and the slow-release character of SPF met the requirement for partly slow-release fertilizer in the national standard. The best models for describing the K release kinetics in water and 2% citric acid were the Elovich model and the first-order model, respectively. The heavy metal contents of SPF were lower than the limits for heavy metals for standard organic–inorganic compound fertilizers; the leaching mass concentrations of the heavy metals and F in SPF were lower than the limit values of the identification standards for hazardous wastes and met the class II quality standard for ground water. The pollution risk of SPF is therefore very low; however, since SPF is alkaline, its effect on soil pH should be taken into account. In addition, the practice application of SPF will require further investigation.
Funding
This work was supported by the National 863 High-Tech Research and Development Program of China (2012AA061602) and the Coal-Base Scientific and Technological Key Project of ShanXi Province (MC2014-06).
Additional information
Funding
Notes on contributors
Yongling Li
Yongling Li is a doctoral candidate at the State Environmental Protection Key Laboratory of Efficient Utilization Technology of Coal-waste Resources, Institute of Resource and Environment, Shanxi University, Taiyuan City, People’s Republic of China, and an associate professor at the College of Arts and Science, Shanxi Agricultural University, Taigu, Shanxi Province, People’s Republic of China.
Fangqin Cheng
Fangqin Cheng is a professor at the State Environmental Protection Key Laboratory of Efficient Utilization Technology of Coal-waste Resources, Institute of Resource and Environment, Shanxi University, Taiyuan City, People’s Republic of China.
References
- American Society for Testing and Materials (ASTM). 2000. Standard Test Methods for Determination of Trace Elements in Coal, Coke and Combustion Residues from Coal Utilization Processes by Inductively Coupled Plasma Atomic Emission Spectrometry, Inductively Coupled Plasma Mass Spectrometry, and Graphite Furnace Atomic Absorption Spectrometry. ASTMD6357-00a. West Conshohocken, PA: ASTM International.
- Brown, R.E. 2009. Magnesium in the 21st century. Adv. Mater. Process. 167:31–33.
- Cherubini, F., M. Raugei, and S. Ulgiati. 2008. LCA of magnesium production: Technological overview and worldwide estimation of environmental burdens. Resourc. Conserv. Recycl. 52:1093–1100. doi:10.1016/j.resconrec.2008.05.001
- China Nonferrous Metals Industry Association. 2012. The primary magnesium yield is 0.66 million tons which increased by 1.04% year-on-year in China. http://www.chinania.org.cn/html/hangyetongji/tongji/2012/0214/5333.html ( accessed December 4, 2012).
- Cui, J.Y., L. Ren, J.G. Wang, and F.S. Zhang. 2002. Effect of organic acids on mobilization of K from K-bearing minerals and stochastic simulation of dynamic K release. Acta Pedol. Sin. 39:341–350.
- Department of Agriculture Science and Technology, Ministry of Agriculture. 1995. Potassium in Agriculture of South China. Beijing: China Agriculture Press.
- Djokic, J., D. Minic, and Z. Kamberovic. 2012a. Reuse of metallurgical slag from the silicothermic magnesium production and secondary lead metallurgy. Metal. Int. 17:46–52.
- Djokic, J., D. Minic, Z. Kamberovic, and D. Petkovic. 2012b. Impact analysis of airborne pollution due to magnesium slag deposit and climatic changes condition. Ecol. Chem, Eng. S 19:439–450.
- Du, J., W. Han, and Y. Peng. 2010. Life cycle greenhouse gases, energy and cost assessment of automobiles using magnesium from Chinese Pidgeon process. J. Cleaner Prod. 18:112–119. doi:10.1016/j.jclepro.2009.08.013
- Eitaro, M., and K. Kiyoshi. 1974. Studies on controlled potassium fertilizers I. Relative effectiveness of various hardly soluble potassium compounds as source of slow-release. Soil Sci. Plant Nutr. 20:403–411.
- Eli, A., and G. Galid. 2006. Production Technologies of Magnesium. Berlin and Heidelberg: Springer.
- Fan, B.G., Y. Jin, X.R. Zheng, X. L. Qiao, and X.T. Wang. 2012. New investigation of magnesium slag as desulfurizer. Adv. Mater. Res. 356–360:1853–1859.
- Gao, F., Z.R. Nie, Z.H. Wang, X.Z. Gong, and T.Y. Zuo. 2008. Assessing environmental impact of magnesium production using Pidgeon process in China. Trans. Nonferrous Metals Soc. China 18:749–754. doi:10.1016/S1003-6326(08)60129-6
- General Administration of Quality Supervision, Inspection and Quarantine. 1993. Quality Standard for Ground Water. GB/T 14848-93. Beijing: Standards Press of China.
- General Administration of Quality Supervision, Inspection and Quarantine. 2007a. Identification Standards for Hazardous Wastes—Identification for Extraction Toxicity. GB5085.3-2007. Beijing: Standards Press of China.
- General Administration of Quality Supervision, Inspection and Quarantine. 2007b. Iron Ores—Determinaton of Fluorine Content—Ion-Selective Electrode Method. GB/T 6730·28-2006. Beijing: Standards Press of China.
- General Administration of Quality Supervision, Inspection and Quarantine. 2009a. Organic-Inorganic Compound Fertilizers. GB18877-2009. Beijing: China Environmental Science Press.
- General Administration of Quality Supervision, Inspection and Quarantine. 2009b. Slow Release Fertilizer. GB/T 23348-2009. Beijing: Standards Press of China.
- Jalali, M., and M. Zarabii. 2006. Kinetics of nonexchangeable-potassium release and plant response in some calcareous soils. J. Plant Nutr. Soil Sci. 169:196–204. doi:10.1002/(ISSN)1522-2624
- Kochian, L.V., O.A. Hoekenga, and M.A. Pieros. 2004. How do crop plants tolerate acid soils? Mechanisms of aluminum tolerance and phosphorous efficiency. Annu. Rev. Plant Biol. 55:459–493. doi:10.1146/annurev.arplant.55.031903.141655
- Kwon, E.E., H. Yi, and J. Park. 2012. Transesterification of used vegetable oil by magnesium slag as heterogeneous catalyst (MgO–CaO/Al2O3). J. Chem. Eng. Japan 45:850–856. doi:10.1252/jcej.11we267
- Li, Y.L., P.X. Liang, Y. Fan, and F.Q. Cheng. 2015. The resource utilization characterization and heavy metals pollution risk of magnesium slags. Environ. Chem. 34:2077–2084.
- Liang, Y.R., M.Z. Li, X.B. Liang, G.W. Wang, Y.B. Zhang, J. Mao, C.X. Ren, and X.Q. Feng. 2015. Improvement of effective silicon content in magnesium reduction slag leached by hydrochloric acid. Nonferrous Metals Extract. Metall. 7:55–59.
- Long, H.Y., Y.Z. Li, W.L. Zhang, and Y.C. Jiang. 2004. K+ adsorption kinetics of fluvo-aquic and cinnamon soil under different temperature. Sci. Agric. Sin. 37:878–885.
- Lu, F., R.Y. Bai, J.W. Cai, K. Xu, B.L. Chen, J.F. Wang, and Z.Z. Wu. 2013. Study on clinker production using magnesium slag on a 4500 line. Adv. Mater. Res. 690–693:724–727.
- Ministry of Agriculture of the People’s Republic of China. 2004. Silicon Fertilizer. NY/T797-2004. Beijing: China Agriculture Press.
- Miyasaka, S.C., J.G. Buta, R.K. Howell, and C.D. Foy. 1991. Mechanism of aluminum tolerance in snapbeans root exudation of citric acid. Plant Physiol. 96:737–743. doi:10.1104/pp.96.3.737
- Morcy G.W., F.C. Kracek, and N.L. Bowen. 1930. The ternary system K2O-CaO-SiO2. J Soc. Glass Technol. 14:149–187.
- Oliveira, C.A.S., A.G. Gumleri, A.M. Comers, and L.V. Wander. 2004. Characterizaton of magnesium slag aiming the utilization as a mineral admixture in mortar. Presented at RILEM Proceedings PRO 40 on the Use of Recycled Materials in Buildings and Structures, Barcelona, Spain, November 8–11.
- Ramakrishnan, S., and P. Koltun. 2004. Global warming impact of the magnesium produced in China using the Pidgeon process. Resour. Conserv. Recycl. 42:49–64 doi:10.1016/j.resconrec.2004.02.003
- Ren, J.M. 2010. How to improve the utilization rate of nitrogen, phosphate and potash fertilizer. Henan Agric. 2010(1):26.
- Shariatmadari, H., M. Shirvani, and A. Jafari. 2006. Phosphorus release kinetics and availability in calcareous soils of selected arid and semiarid toposequences. Geoderma 132:261–272. doi:10.1016/j.geoderma.2005.05.011
- Shen, J.G., C.Y. Guo, J.K. Yu, and M.F. Jiang. 2005. Crystallizability of potash fertilizer synthesized by desiliconized slag. J. Northeast. Univ. 26:137–140.
- Song, S.K., and P.M. Huang. 1988. Dynamics of potassium release from potassium-bearing minerals as influenced by oxalic and citric acids. Soil Sci. Soc. Am. J. 52:383–390. doi:10.2136/sssaj1988.03615995005200020015x
- Sparks, D.L., and T.H. Carski. 1985. Kinetics of potassium exchange in heterogeneous systems. Appl. Clay Sci. 1:89–101. doi:10.1016/0169-1317(85)90565-4
- State Bureau of Environmental Protection of China. 1995. Solid Waste—Determination of chrominm(VI)—1,5-Diphenylcarbohydrazide Spectrophotometric Method. GB/T15555.4-1995. Beijing: China Environmental Science Press.
- State Bureau of Environmental Protection of China. 2007. Solid Waste—Extraction Procedure for Leaching Toxicity—Sulphuric Acid & Nitric Acid Method. HJ/T299-2007. Beijing: China Environmental Science Press.
- Tian,Y., Y. Qiu, Y. Chai, P. Bai, and C. Gong. 2013. The effect of sintering temperature on the structure and properties of calcium hexaluminate/anorthite ceramics. Sci. Sintering 45:141–147. doi:10.2298/SOS1302141T
- Tokunaga, Y. 1991. Potassium silicate: A slow-release potassium fertilizer. Fert. Res. 30:55–59. doi:10.1007/BF01048827
- Trenkel. M.E. 1997. Controlled-Release and Stabilized Fertilizers in Agriculture. Paris, France: The International Fertilizer Industry Association.
- United Nations Department of Economic and Social Affairs. 2004. World Population to 2300. New York: United Nations.
- Wang, J., X.K. Li, J.W. Lu, Z. Wang, and L.P. Zhan. 2012. Study on potassium release kinetics of several K-bearing minerals by sequential extraction of different acid solution. Sci. Agric. Sin. 45:4643–4650.
- Wang, S.Y., L.G. Xiao, Q. Zhou, K. Xu, B.L. Chen, J.F. Wang, and Z.Z. Wu. 2011. Research and application on magnesium slag. Adv. Mater. Res. 280:208–211. doi:10.4028/www.scientific.net/AMR.280
- Yamada, K., L.G. Dominguez, L.A. Manalo, B.Y. Mercado, A.T. Manllilin, C.G. Pigao, H. Hosoda, H. Kuwagaki, and K. Ishibashi. 1994. Studies on the production of slow release potassium silicate fertilizer using the internal heat type fluidized bed reactor. Philipp. J. Sci. 123:313–322.
- Yasuko Y., H. Etsuo, S. Kaoru, A. Takashi, and Y. Tadakatsu. 2014. Identification of the major constituents of fused potassium silicate fertilizer. ISIJ Int. 54:990–993.
- Zhang, X., and W. Huang. 2011. Waste slag catalyst applied to transesterification of Chinese tallow kernel oil. Energy Sources Part A 33:1877–1882. doi:10.1080/15567036.2011.572120
- Zhang, Y.J., L. Kang, L.C. Liu, H.X. Si, and J.F. Zhang. 2015. Synthesis of a novel alkali-activated magnesium slag-based nanostructural composite and its photocatalytic performance. Appl. Surf. Sci. 331:399–406. doi:10.1016/j.apsusc.2015.01.090
- Zhao, H.J. 2007. Research and Application on Using Magnesium Slag to Prepare Cement. Xi’an, China: Xi’an University of Architecture and Technology.