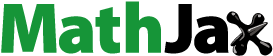
ABSTRACT
A model was developed to simulate the sewage sludge gasification in an atmospheric fluidised bed gasifier using Aspen Plus. The model here presented was based on the Gibbs free energy minimisation and the restricted equilibrium method was used to calibrate it against previously published experimental data obtained in a lab-scale gasification plant. A sensitivity analysis of the model was carried out by modifying parameters such as the temperature, equivalence ratio (ER) and the steam-to-biomass ratio. The modeled results were in good agreement with the experimental data (especially when air was used as gasifying agent) and reproduced satisfactorily the experimental trends found for the gas composition, the carbon conversion (Xc) and the cold gas efficiency (CGE) under different gasification conditions. Operating at higher temperatures increased the production of H2 and CO, as well as the Xc and the CGE. The increase in ER produced higher Xc, yet the CGE experienced slight changes due to a decrease in the lower heating value of the resulting syngas, as well as the oxidation of combustible gases. The use of air+steam as gasifying agent increased the H2 content of the produced gases but decreased the accuracy of the model.
Implications: Gasification is an available alternative to produce energy as well as several raw materials from sewage sludge. The syngas obtained from this technology totally depends on the type of gasifier and the operation conditions, which can be optimized with the help of models. In this work, a relatively simple model was built using ASPEN PLUS. Despite its simplicity, the outputs of the model are in good agreement with experimental results what makes its use interesting for assessing scaling-up possibilities from lab-scale to pilot-scale gasification processes.
Introduction
Sewage sludge is the residue, liquid or semiliquid form that is generated from the treatment of domestic and industrial wastewater (Dogru, Midilli, and Howarth Citation2002). The chemical composition of sewage sludge is determined by the origin of the raw wastewater, and its production is influenced by population growth and legislation standards (Urban Waste Water Treatment Directive 91/271/EEC [UWWTD] Citation1991). Although specific types of sludge can occasionally be used as a fertilizer, sludge is normally considered a waste that requires appropriate management or further treatment (Sewage Sludge Directive 86/278/EEC [SSD] Citation1986). The most common disposal solutions for sewage sludge are landfilling or incineration, which are restricted by the European legislation (Council Directive 99/31/CE [CD] Citation1999 ) and often have a negative public perception associated with their potential environmental risk.
An alternative to these conventional methods is the gasification of sewage sludge. This technology presents advantages such as the destruction of pathogenic bacteria and sludge volume reduction, as well as the additional benefits of energy recovery and lower-cost atmospheric emission controls (Seggiani et al. Citation2012). Gasification is a thermal process that consists of the conversion of the organic contents of sludge into combustible gas and other substances, in the presence of a gasifying agent at high temperatures under a reducing atmosphere (Fytili and Zabaniotou Citation2008). The produced gas (syngas) is mainly composed of carbon monoxide (CO), hydrogen (H2), carbon dioxide (CO2), water vapor, methane, and light hydrocarbons. In addition to the syngas, a solid carbonaceous residue (char) is produced along with a gaseous mixture of condensable organic compounds (tars). Syngas is a high-value product of the sludge gasification process, as it can be burnt in gas engines and turbines for energy production, used as a raw material in methanol synthesis, or used in the production of synthetic fuels through the Fischer-Tropsch process (Ciferno and Marano Citation2002; Holmgren et al. Citation2014; Princiotta Citation2009; Speight Citation2015).
Although gasification can be an autothermic process, most of the studies at laboratory and pilot scales have been developed allothermically by modifying independently the temperature, the air-to-biomass ratio, and the steam-to-biomass ratio (Campoy et al. Citation2008). In addition to the above-mentioned parameters, the gasifying agent and gasifier chosen are also critical aspects that influence the process and condition the quality of the obtained syngas. The most commonly used gasifying agents are air, oxygen, steam, or a mixture of these (Campoy et al. Citation2010; Meng et al. Citation2011). Regarding the type of gasifier, the most common reactors are fixed, moving, and fluidized-bed reactors (Beenackers Citation1999; Warnecke Citation2000). Among these, fluidized-bed gasifiers have a uniform temperature distribution in the gasification zone and elevated heat transfer rates, which are typical of the circulation patterns of gas-solid systems within the bed (McKendry Citation2002). Another important advantage of these gasifiers is their higher potential to be scaled up to medium and large scales, overcoming the limitations often found in smaller-scale, fixed-bed gasifiers (Kurkela, Nieminen, and Simell Citation2004).
The selection of equipment and operation conditions of a gasification system for an optimal performance needs to take into account the complex interplay between all the factors that condition the process. In this sense, models are useful tools for designing, optimizing, and assessing scaling-up possibilities for the gasification processes (Gómez-Barea and Leckner Citation2010). However, when dealing with fluidized-bed gasifiers, modeling can be difficult due to the complexity of the fluidization hydrodynamics and the complex nature of the physical and chemical phenomena occurring inside a gasifier with these characteristics (Damartzis, Michailos, and Zabaniotou Citation2012).
Three main types of modeling approaches are used for describing sludge gasification: (i) computational fluid dynamic (CFD) models, (ii) kinetic models, and (iii) equilibrium models (Champion et al. Citation2014; Gambarotta, Morini, and Zubani Citation2017). CFD models can simulate several physical phenomena, but they require very detailed information (geometry, materials, boundary conditions) and high computational resources. Kinetic models are appropriate for modeling the influence of reactor design and process parameters, but they are substantially more complex in their conceptual modeling (Petersen and Werther Citation2005a). For instance, Petersen and Werther (Citation2005b) developed a kinetic model for sludge gasification in a circulating fluidized-bed gasifier that included the hydrodynamics of the circulating bed and a comprehensive set of gasification reactions. However, this model also required carrying out axial measurements of temperature and gas concentration to develop the kinetic rate expressions.
Equilibrium models, on the contrary, are simple, easy to program, and provide a good approximation of the gasification process within a reactor (Mostoufi, Cui, and Chaouki Citation2001). These models are classified as stoichiometric and nonstoichiometric depending on the whether they are based on equilibrium constants or on the minimization of the Gibbs free energy (Gambarotta, Morini, and Zubani Citation2017). Ultimately, the choice of model depends mainly on the objectives and the experimental information available (Gómez-Barea and Leckner Citation2010).
Nonstoichiometric equilibrium models are the most common approach for the description of the performance of a fluidized-bed gasifier. As an example, Ramzan et al. (Citation2011) developed a nonstoichiometric equilibrium model for a biomass gasification process, and the model was validated using experimental results from hybrid biomass gasifier. In this paper, a comprehensive description of a nonstoichiometric equilibrium model that describes the performance of a laboratory-scale fluidized-bed gasifier is presented. The model is based on Aspen Plus and has been built to predict the output of gasification products from sludge under different operating conditions and has been validated against experimental data from the actual pilot-plant gasifier (De Andrés, Narros, and Rodríguez Citation2011). Although there are several examples of Aspen Plus being used for modeling biomass gasification processes (Baruah and Baruah Citation2014; Damartzis, Michailos, and Zabaniotou Citation2012; Doherty, Reynolds, and Kennedy Citation2013; Nikoo and Mahinpey Citation2008; Ramzan et al. Citation2011; Zheng, Kaliyan, and Morey Citation2013), scientific literature on its application in sewage sludge gasification is still scarce (Lumley et al. Citation2014; Ptasinski, Hamelinck, and Kerkhof Citation2002). Ultimately, the development of such a model is essential for finding optimal operation conditions that could inform the potential up-scaling of the gasifier to produce syngas from sewage sludge from several wastewater treatment facilities of the local water supplier (Canal de Isabel II) of the region of Madrid.
Sludge gasification model
The nonstoichiometric equilibrium model of this work is based on the fundamental chemical equilibrium problem, which is formulated as follows: given temperature T, pressure P, and molar amounts of elements i, find the equilibrium composition n that minimizes the total Gibbs free energy (G) of the system (Leal, Kulik, and Kosakowski Citation2016; Sreejith, Arun, and Muraleedharan Citation2012):
where ΔG°f,i is the standard formation free Gibbs energy of species i and R is the ideal gas constant. The calculation of the composition of syngas requires finding the values of ni that minimize the objective function G/RT. The equilibrium problem (eq 1) is a nonlinear constrained minimization problem, which requires not only the minimization of the Gibbs free energy but also satisfying the inequality constraint, which guarantees that the species have non-negative molar amounts (Gambarotta, Morini, and Zubani Citation2017; Wenger, Farouk, and Wittle Citation1996).
Modeling approach
The gasification model was constructed in Aspen Plus as a combination of different blocks and unit operations, aiming to reproduce as accurately as possible the experimental results from the laboratory-scale plant gasifier that is used for treating sewage sludge from the local wastewater treatment facilities of Madrid (De Andrés, Narros, and Rodríguez Citation2011). Once the model had been configured, analyses of the sensitivity of the yield (Ygas), composition, and lower heating value (LHVgas) of syngas, as well as the carbon conversion (XC) and cold gas efficiency (CGE), to operation variables such as temperature, equivalence ratio (ER), and steam-to-biomass ratio (S/B) were carried out.
Modeling assumptions
In order to maintain a balance between the robustness of the model, its operability, and the available information, the following assumptions were made:
Steady-state and isothermal process
Zero-dimensional and kinetic-free model
Instantaneous devolatilization of the biomass at the entrance of the reactor (Nikoo and Mahinpey Citation2008)
The main components of the syngas are H2, CO, CO2, methane (CH4), and water (H2O)
All the nitrogen and sulfur in the biomass react to give ammonia (NH3) and hydrogen sulfide (H2S) (De Jong, Andries, and Hein Citation1999; Schuster et al. Citation2001)
Tars are not modeled but are considered as a nonequilibrium component (Panopoulos et al. Citation2006)
Chemical reactions
The homogeneous and heterogeneous chemical reactions that are considered to occur in the gasification process of the unit are shown in . The hydrogen and carbon combustion reactions (R-1, R-5), as well as the water-gas shift and methanation reactions (R-3, R-7), are all exothermal and ideally provide the system with the energy needed. On the other hand, the steam-reforming, Boudouard, and water-gas reactions are endothermal (R-2, R-6, R-8), and their effect on the gasification products becomes more evident at high temperatures (González et al. Citation2008).
Table 1. Reactions considered in the model.
Model assembly and configuration
The model was developed by reproducing the gasification process with the software Aspen Plus, coupling and combining different modules to represent the parts of the plant (the resulting flow sheet is displayed in ). The gasifier was represented by multiple blocks that correspond to the different phases of the gasification process, namely, the feed drying, the decomposition of the sludge, and the gasification itself ().
Table 2. Description of the Aspen Plus reactor blocks considered in the model.
The sewage sludge was specified as a nonconventional component and the HCOALGEN and DCOALIGT algorithms were used as enthalpy and density functions, together with the LHV and the proximate and ultimate analyses of the sludge.
The drying (removal of the residual moisture) and the decomposition of the sewage sludge into elemental constituents (C, O, H, N, S, ash) occurred in RYIELD blocks (DRIER and MASSPROC, respectively). The MASSPROC block allows the user to specify the component distribution of the outlet stream, based on the proximate and ultimate analysis of the sludge. After drying and decomposition, the moisture was sent to the GASIFIER, whereas the rest of the elements were fed to a RSTOIC block (NS). The NS was configured with chemical reactions of known stoichiometry (R-4, R-9) that can be set to a determined reaction extent or conversion. In this work, this block simulated the total conversion of nitrogen and sulfur to NH3 and H2S (De Jong, Andries, and Hein Citation1999; Schuster et al. Citation2001), which were then separated from the main stream by a SEP block (ELEMSEP).
The ELEMSEP block also diverts 10% of the carbon content in the feedstock, which is the quantity of unreacted C found in the sewage sludge according to the determinations carried out in De Andrés, Narros, and Rodríguez (Citation2011). Another RSTOIC block (NONEQ) was included to consider the formation of tars. This block was not intended to estimate tar production but to exclude from the gasification process the quantity of carbon being part of tar that did not become syngas. In order to set up the production of tar in this module, temperature-dependent tar production functions from De Andrés, Narros, and Rodríguez (Citation2011) were used. In addition, the amount of carbon in the tar was set by a calculator block considering that naphthalene is the major component of tar (Panopoulos et al. Citation2006). The SEP block B2 separates tar from the rest of the reaction stream.
The modeling of the gasification process was carried out with a RGIBBS reactor block, which uses the minimization of Gibbs free energy to reach phase and chemical equilibrium. Heating demands for this module are provided by the upstream drying and decomposition processes (Ramzan et al. Citation2011). A SEP block (ASHSEP) simulated the ash removal from the gasifier.
Subsequently, the gaseous stream (GASES1) entered another RGIBBS reactor block, where restricted equilibrium was applied to adjust the gas composition to match the experimental data. A temperature profile was specified for each considered reaction in order to set a realistic syngas composition (Gumz Citation1950).
The stream of syngas then entered a mixer (MIX), together with the stream of hydrogen sulfide and ammonia (SUAM), tar (TAR), and unreacted carbon (INERTC), to simulate the final outputs from the gasifier.
Finally, the cleaning and cooling of the syngas were operated by a SEP block (SYNSEP) combined with a COOLER block. The SYNSEP simulated the removal of particulate matter from the syngas, and the COOLER lowered the temperature of the syngas to less than 100 °C, which simulates the cooling of the gases in the train of isopropanol condensers (De Andrés, Narros, and Rodríguez Citation2011) and the necessary cooling when using the syngas as fuel for internal combustion engines (Gómez-Barea et al. Citation2013). The stream “SOOTDIRT” was then composed of the remaining unreacted carbon, moisture, and tar.
Model validation
The validation of the gasification model was done against experimental results from the laboratory-scale plant under the following operation conditions (test number 5 in De Andrés, Narros, and Rodríguez [Citation2011]):
Temperature: 800 °C
Equivalence ratio (ER): 0.3
Steam-to-biomass ratio (S/B): 0
Sewage sludge input rate (Qsludge): 1.44 g/min
Air volume rate (Qair) = 0.00128 Nm3/min
The validation rationale of this work was based on the relative error (εr), which is the ratio between the absolute error (i.e., the difference between the modeled, Xm, and experimental, Xe, values) and the experimental value (eq 2). Relative errors are useful for determining model over- or underestimations based on whether the relative error is positive or negative, respectively.
The variables that were compared are (i) the syngas stream dry-basis composition in terms of hydrogen (H2), nitrogen (N2), methane (CH4), carbon monoxide (CO), and carbon dioxide (CO2); (ii) the total syngas yield (Ygas); (iii) its lower heating value (LHVgas); (iv) the total carbon conversion (XC); and (v) the cold gas efficiency (CGE). Using the performance of similar gasification systems from literature as a benchmark, the outputs of the model were considered acceptable if the relative errors for each of the variables were within ±15% (Wang and Yan Citation2009; Xiao et al. Citation2009).
Sensitivity analysis
Once the model had been validated, the sensitivity of the model to different operating conditions was evaluated through the study of the change in the performance of the gasification process against the variation of the operation variables stated in section Sludge gasification model. Model validation
The operation values of the selected operation variables for the sensitivity analysis were set according to De Andrés, Narros, and Rodríguez (Citation2011) and are as follows:
Temperature: 750, 800, and 850 °C.
Equivalence ratio (ER): 0.2, 0.3, and 0.4.
Steam-to-biomass ratio (S/B): For tests with air, 0; for tests with air and steam, 0.5.
This sensitivity analysis provides an indication of those variables that have a more significant influence on the desired yields and composition of the output streams of the system. In addition, the sensitivity analysis will be useful for selecting adequate operation conditions of a gasification system, which can then be used in plant up-scaling exercises.
Experimental
Materials
The dried sludge samples were supplied by a sludge thermal drying plant managed by the local water company of Madrid (Spain). The results of the proximate and ultimate analyses of the sludge samples are shown in (supplementary material).
Laboratory-scale plant
The plant on which this model is based mainly consists of a stainless steel fluidized-bed gasifier followed by a freeboard, both of which are electrically heated. A cyclone and a micronic filter are located downstream of the freeboard (inside a hot box) to remove any particles from the syngas. A diagram of the laboratory-scale plant is shown in Figure 1S (supplementary material).
A comprehensive explanation of the experimental procedure, tar collection, and quantification system, as well as how syngas production and composition was determined, can be found in De Andrés, Narros, and Rodríguez (Citation2011).
Results and discussion
Model validation
As previously mentioned in the section Sludge gasification model. Model validation, the gasification model of this work was validated against experimental data collected from the laboratory-scale sludge gasification plant described in De Andrés, Narros, and Rodríguez (Citation2011), operating with air (ER = 0.3) at 800 °C. As shown in , the model was in very good agreement with the experimental results (the percentage error was always below 12%), particularly as regards the syngas composition.
Table 3. Model validation: Comparison of experimental (De Andrés, Narros, and Rodríguez Citation2011) and model results.
Sensitivity analysis
Sensitivity analyses were performed to evaluate the model response to changes in temperature, ER, and SB. The following sections discuss the behavior of the parameters of interest with respect to the operation variables.
Influence of temperature
shows the influence of the gasification temperature on the gas composition, Ytar and XC, in tests with air and ER = 0.3. Within a temperature range of 750–850 °C, the model corresponded with the experimental data of gas composition, except for the CO content, which was underpredicted at 750 °C temperature and overpredicted at 850 °C. In both modeled and experimental results, the concentrations of H2 and CO in the syngas increased with higher temperatures, whereas the concentration of CO2 decreased. The concentration of methane showed a maximum around 850 °C.
Figure 2. Effect of the gasification temperature on (a, b, c, d) syngas composition, (e) gas production (Ygas), and (f) carbon conversion (XC).
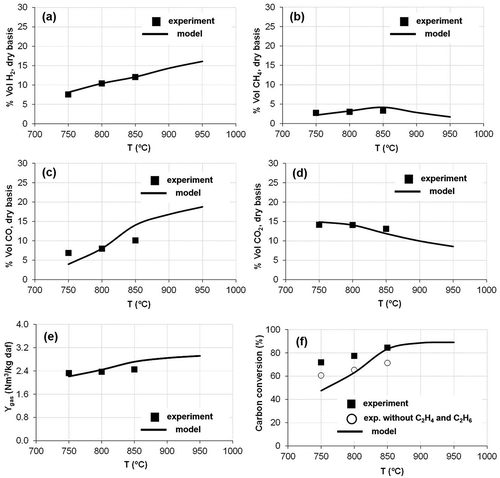
The gas production increased with temperature due to a more intense volatilization of the sludge and conversion of the char (Campoy et al., Citation2009). The highest deviations of the modeled results from the experimental values were found for carbon conversion. In De Andrés, Narros, and Rodríguez (Citation2011), the ethane (C2H6) and ethylene (C2H4) contents of the syngas were included in the estimation of XC. However, the model has not considered the CnHm gases, which would partially explain these differences. If CnHm gases are excluded from the XC calculations in De Andrés, Narros, and Rodríguez (Citation2011) (), the data fit between modeled and experimental results improved. At 850 °C, the higher CO content (Ygas and XC) modeled together with the lower CO2 content modeled may be associated with the excessive promotion of the Boudouard reaction by the model.
Influence of the equivalence ratio
The effect of the ER in the experimental and modeled results is shown in . The represented figures correspond to tests with air and at 800 °C. It can be observed that the modeled results were in good agreement with the experimental data. shows that H2, CH4, and CO contents decreased when ER increased. The oxidation reactions were stimulated with the increase in ER, which led to lower H2, CH4, and CO productions and to a slightly higher CO2 content (De Andrés, Narros, and Rodríguez Citation2011). With regards to the Ygas and XC, the effect of the ER was similar to that of the temperature, that is, higher ER increased the value of these two parameters.
Effect of air + steam as gasifying agent
shows the comparison of modeled and experimental results when a mixture of air + steam was used as gasifying agent (S/B = 0.5). As explained in De Andrés, Narros, and Rodríguez (Citation2011), the addition of steam increased hydrogen production due to the steam reforming, water-gas shift, and water-gas reactions (R-2, R-3, R-8).
Figure 4. Comparison of modeled and experimental results with air + steam as gasifying agent (S/B = 0.5): (a, b, c, d) syngas composition; (e) gas production (Ygas); (f) carbon conversion (XC).
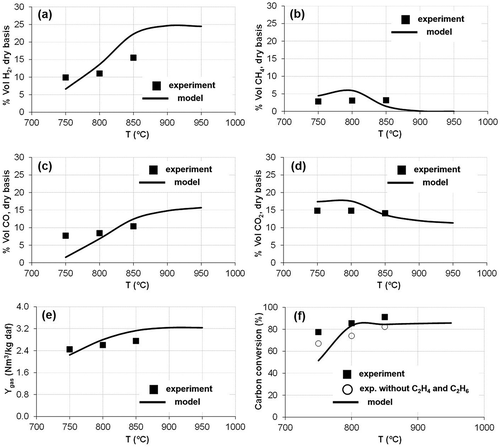
The trends obtained by the model followed experimental data satisfactorily, although with less accuracy than in tests with air. It can be explained by the fact that using air + steam decreased the residence time of the gases inside the reactor, preventing the ongoing reactions in the gasifier from reaching the chemical equilibrium assumed by the model. According to , the maximum quantitative differences were found for CO (at lower temperatures) and for H2 content (at higher temperatures), which are the main reagents and products of the chemical reactions promoted by the presence of the steam in the gasifier. In relative terms, the highest error was found for CH4 (94%). Lumley et al. (Citation2014) obtained similar results, with relative errors of 112% and 78% for modeled CH4 production for sewage sludge gasification with air and steam, respectively. According to these authors, thermodynamic equilibrium methods tend to overpredict CH4, yet they remain the best modeling choice for interrogating system designs at an early stage.
Despite the observed differences in gas composition, the modeled Ygas and XC fitted reasonably well with the experimental values (, , respectively).
Energetic evaluation
The experimental and modeled trends of the LHVgas and the CGE at different temperatures and ERs were compared ( and , respectively). According to the results obtained, both energetic parameters are more sensitive to variations of the temperature than to variations of ER. As it can be seen in , the modeled LHVgas at different temperatures agreed with the experimental data. The relative errors in modeled results were 15.2% for LHVgas and 18.0% for CGE. The operation at higher temperatures increased the production of combustible gases (H2, CO, and CH4) and therefore increased the LHVgas. At the same time, as shown in , these higher operation temperatures produced an increase of Ygas and therefore improved the CGE ().
Figure 5. Modeled and experimental results under different temperatures: (a) lower heating value (LHVgas); (b) cold gas efficiency (CGE).
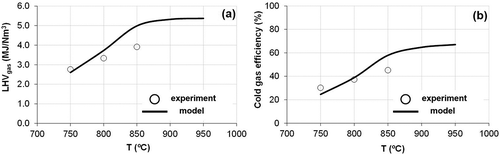
Figure 6. Modeled and experimental results under different equivalence ratios: (a) lower heating value (LHVgas); (b) cold gas efficiency (CGE).
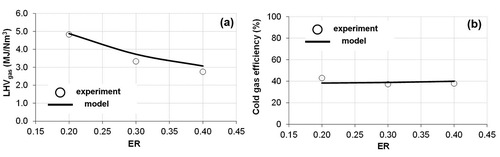
As for the LHVgas and the CGE obtained at different ERs, it can be observed in that both modeled parameters were in good agreement with the experimental data. The relative errors in modeled results were 4.2% for LHVgas and 5.6% for CGE. The ER had the opposite effect on the LHVgas than the temperature, that is, higher ER decreased the LHVgas because of the oxidation of part of the combustible gases present in the syngas (). The changes in the ER had a negligible effect on the CGE (), which can be explained by the fact that when the ER increased the Ygas rose but the LHVgas decreased.
Conclusion
Despite the relative simplicity of the model developed with Aspen Plus, its outputs were generally in good agreement with the experimental results used for model validation and sensitivity analysis.
According to the modeled results with air, increasing the gasification temperature above 850 °C may not produce large benefits regarding the syngas lower heating value (LHVgas), carbon conversion (XC), and cold gas efficiency (CGE) but would increase the H2 and CO contents of the produced gas.
The best data fit between modeled and experimental results was found when the temperature was kept at 800 °C and the equivalence ratio (ER) varied between 0.2 and 0.4. Higher ER increased both the gas production (Ygas) and the XC but had a negligible effect on the CGE because of the decrease of the LHVgas. Considering the information gathered, the optimal gasification conditions could be set at 850 °C and ER of 0.3.
The addition of steam decreased the model accuracy (specially for modeled gas composition), which can be explained by the fact that using air + steam decreased the residence time of the gases inside the reactor, preventing the ongoing reactions in the gasifier from reaching the chemical equilibrium assumed by the model. Despite this, the modeled Ygas and XC fitted reasonably well with the experimental values.
With these results in mind and despite their limitations, the thermodynamic equilibrium models may be considered as an interesting modeling choice for interrogating system designs at an early stage.
Abbreviations and acronyms
daf | = | dry and ash-free |
ER | = | equivalence ratio, defined as the ratio between the flow rate of air introduced into the gasifier and the stoichiometric flow rate of air required for complete combustion of the sludge |
LHVgas | = | lower heating value of the produced gas, MJ/Nm3, dry basis |
SB | = | steam-to-biomass ratio, defined as the flow rate of steam fed to the reactor divided by the flow rate of sludge (daf) |
Nm3 | = | cubic meter, normal conditions (0 °C, 101 kPa) |
Ygas | = | gas yield, Nm3 dry gas/kg sludge, daf |
XC | = | carbon conversion, weight of carbon in the produced gas divided by weight of carbon in the sludge introduced in the gasifier |
CGE | = | cold gas efficiency = LHV of gas divided by the LHV of sludge |
Supplemental Material
Download PDF (77.1 KB)Supplemental data
Supplemental data for this paper can be accessed on the publisher’s website.
Additional information
Funding
Notes on contributors
Juan Manuel de Andrés
Juan Manuel de Andrés, Ph.D., is an assistant lecturer at the Universidad Politécnica de Madrid (UPM).
Michel Vedrenne
Michel Vedrenne, Ph.D., is a principal technical consultant at Ricardo Energy & Environment in London.
Matteo Brambilla
Matteo Brambilla is Part-time research fellow at the Universidad Politécnica de Madrid (UPM).
Encarnación Rodríguez
María Encarnación Rodríguez, Ph.D., is a senior scientist and the head of the UPM research group on environmental technologies and industrial resources.
References
- Council Directive. 1986. Council Directive (CD) 99/31/CE, 26 April 1999, on the landfill of waste.
- Council Directive. 1991. Urban Waste Water Treatment Directive (UWWTD) (91/ 271/EEC), amended by Directive 98/15/EC.
- Council Directive. 1999. Council Directive (CD) 99/31/CE, 26 April 1999, on the landfill of waste.
- Baruah, D., and D. C. Baruah. 2014. Modeling of biomass gasification: A review. Renew. Sust. Energ. Rev. 39:806–815. doi:10.1016/j.rser.2014.07.129.
- Beenackers, A. A. C. M. 1999. Biomass gasification in moving beds, a review of European technologies. Renew. Energy. 16:1180–1186. doi:10.1016/S0960-1481(98)00469-8.
- Campoy, M., A. Gómez-Barea, A. L. Villanueva, and P. Ollero. 2008. Air−steam gasification of biomass in a fluidized bed under simulated autothermal and adiabatic conditions. Ind. Eng. Chem. Res. 47:5957–5965. doi:10.1021/ie800220t.
- Campoy, M., A. Gómez-Barea, D. Fuentes-Canoa, and P. Ollero. 2010. Tar reduction by primary measures in an autothermal air-blown fluidized bed biomass gasifier. Ind. Eng. Chem. Res. 49:294–301. doi:10.1021/ie101267c.
- Campoy, M., A. Gómez-Barea, F. B. Vidal, and P. Ollero. 2009. Air-steam gasification of biomass in a fluidised bed: Process optimisation by enriched air. Fuel Process. Technol. 90:677–685. doi:10.1016/j.fuproc.2008.12.007.
- Champion, W. M., C. David Cooper, K. R. Mackie, and P. Cairney. 2014. Development of a chemical kinetic model for a biosolids fluidized-bed gasifier and the effects of operating parameters on syngas quality. J. Air Waste Manag. Assoc. 64:160–174. doi:10.1080/10962247.2013.845619.
- Ciferno, J. P., and J. J. Marano. 2002. Benchmarking biomass gasification technologies for fuels, chemicals and hydrogen production. US Department of Energy. National Energy Technology Laboratory.
- Damartzis, T., S. Michailos, and A. Zabaniotou. 2012. Energetic assessment of a combined heat and power integrated biomass gasification–Internal combustion engine system by using Aspen Plus®. Fuel Process. Technol. 95:37–44. doi:10.1016/j.fuproc.2011.11.010.
- De Andrés, J. M., A. Narros, and M. E. Rodríguez. 2011. Air-steam gasification of sewage sludge in a bubbling bed reactor: Effect of alumina as a primary catalyst. Fuel Process. Technol. 92:433–440. doi:10.1016/j.fuproc.2010.10.006.
- De Jong, W., J. Andries, and K. R. G. Hein. 1999. Coal/biomass co-gasification in a pressurised fluidised bed reactor. Renew. Energ. 16:1110–1113. doi:10.1016/S0960-1481(98)00432-7.
- Dogru, M., A. Midilli, and C. R. Howarth. 2002. Gasification of sewage sludge using a throated downdraft gasifier and uncertainty analysis. Fuel Process. Technol. 75:55–82. doi:10.1016/S0378-3820(01)00234-X.
- Doherty, W., A. Reynolds, and D. Kennedy. 2013. Aspen plus simulation of biomass gasification in a steam blown dual fluidised bed. In Materials and processes for energy: Communicating current research and technological developments, ed. A. Méndez-Vilas, 212–220. Formatex Research Centre.
- Fytili, D., and A. Zabaniotou. 2008. Utilization of sewage sludge in EU application of old and new methods—A review. Renew. Sust. Energ. Rev. 12:116–140. doi:10.1016/j.rser.2006.05.014.
- Gambarotta, A., M. Morini, and A. Zubani. 2017. A non-stoichiometric equilibrium model for the simulation of the biomass gasification process. App. Energ. In Press, Corrected Proof. doi: 10.1016/j.apenergy.2017.07.135.
- Gómez-Barea, A., and B. Leckner. 2010. Modeling of biomass gasification in fluidized bed. Prog. Energ. Combust. 36:444–509. doi:10.1016/j.pecs.2009.12.002.
- Gómez-Barea, A., B. Leckner, A. Villanueva Perales, S. Nilsson, and D. Fuentes Cano. 2013. Improving the performance of fluidized bed biomass/waste gasifiers for distributed electricity: A new three-stage gasification system. Appl. Therm. Eng. 50:1453–1462. doi:10.1016/j.applthermaleng.2011.12.025.
- González, J. F., S. Román, D. Bragado, and M. Calderón. 2008. Investigation on the reactions influencing biomass air and air/steam gasification for hydrogen production. Fuel Process. Technol. 89:764–772. doi:10.1016/j.fuproc.2008.01.011.
- Gumz, W. 1950. Gas Producers and Blast Furnaces. New York: John Wiley & Sons, Inc.
- Holmgren, K. M., E. Andersson, T. Berntsson, and T. Rydberg. 2014. Gasification-based methanol production from biomass in industrial clusters: Characterisation of energy balances and greenhouse gas emissions. Energy 69:622–637. doi:10.1016/j.energy.2014.03.058.
- Kurkela, E., M. Nieminen, and P. Simell. 2004. Development and commercialisation of biomass and waste gasification technologies from reliable and robust cofiring plants towards synthesis gas production and advanced cycles. 2nd World Conference on Biomass for Energy, Industry and Climate Protection, Rome, 10–15.
- Leal, A. M. M., D. A. Kulik, and G. Kosakowski. 2016. Computational methods for reactive transport modeling: A gibbs energy minimization approach for multiphase equilibrium calculations. Adv. Water Resour. 88:231–240. doi:10.1016/j.advwatres.2015.11.021.
- Lumley, N. P. G., D. F. Ramey, A. L. Prieto, R. J. Braun, T. Y. Cath, and J. M. Porter. 2014. Techno-economic analysis of wastewater sludge gasification: A decentralized urban perspective. Bioresource Technol 161:385–394. doi:10.1016/j.biortech.2014.03.040.
- McKendry, P. 2002. Energy production from biomass (part 3): Gasification technologies. Bioresource Technol 83:55–63. doi:10.1016/S0960-8524(01)00120-1.
- Meng, X., W. De Jong, N. Fu, and A. H. M. Verkooijen. 2011. Biomass gasification in a 100 kWth steam-oxygen blown circulating fluidized bed gasifier: Effects of operational conditions on product gas distribution and tar formation. Biomass Bioenerg 35:2910–2924. doi:10.1016/j.biombioe.2011.03.028.
- Mostoufi, N., H. Cui, and J. A. Chaouki. 2001. Comparison of two- and single-phase models for fluidized-bed reactors. Ind. Eng. Chem. Res. 40:5526–5532. doi:10.1021/ie010121n.
- Nikoo, M. B., and N. Mahinpey. 2008. Simulation of biomass gasification in fluidized bed reactor using ASPEN PLUS. Biomass Bioenerg 32:1245–1254. doi:10.1016/j.biombioe.2008.02.020.
- Panopoulos, K. D., L. E. Fryda, J. Karl, S. Poulou, and E. Kakaras. 2006. High temperature solid oxide fuel cell integrated with novel allothermal biomass gasification: Part I: Modelling and feasibility study. J. Power Sources. 159:570–585. doi:10.1016/j.jpowsour.2005.12.024.
- Petersen, I., and J. Werther. 2005a. Three-dimensional modeling of a circulating fluidized bed gasifier for sewage sludge. Chem. Eng. Sci. 60:4469–4484. doi:10.1016/j.ces.2005.02.058.
- Petersen, I., and J. Werther. 2005b. Experimental investigation and modeling of gasification of sewage sludge in the circulating fluidized bed. Chem. Eng. Process: Process Intensification. 44:717–736. doi:10.1016/j.cep.2004.09.001.
- Princiotta, F. 2009. Global climate change and the mitigation challenge. J. Air Waste Manag. Assoc. 59:1194–1211. doi:10.3155/1047-3289.59.10.1194.
- Ptasinski, K. J., C. Hamelinck, and P. J. A. M. Kerkhof. 2002. Exergy analysis of methanol from the sewage sludge process. Energ. Convers. Manage. 43:1445–1457. doi:10.1016/S0196-8904(02)00027-4.
- Ramzan, N., A. Ashraf, S. Naveed, and A. Malik. 2011. Simulation of hybrid biomass gasification using Aspen plus: A comparative performance analysis for food, municipal solid and poultry waste. Biomass Bioenerg 35:3962–3969. doi:10.1016/j.biombioe.2011.06.005.
- Schuster, G., G. Löffler, K. Weigl, and H. Hofbauer. 2001. Biomass steam gasification – An extensive parametric modeling study. Bioresour. Technol. 77:71–79. doi:10.1016/S0960-8524(00)00115-2.
- Seggiani, M., S. Vitolo, M. Puccini, and A. Bellini. 2012. Cogasification of sewage sludge in an updraft gasifier. Fuel 93:486–491. doi:10.1016/j.fuel.2011.08.054.
- Sewage Sludge Directive (SSD) 86/278/EEC.
- Speight, J. G. 2015. Gasification for synthetic fuel production. In Synthetic liquid fuel production from gasification, eds. Luque and Speight, 1st ed. 147–174. Cambridge, UK: Woodhead Publishing.
- Sreejith, C. C., P. Arun, and C. Muraleedharan. 2012. Thermochemical analysis of biomass gasification by gibbs free energy minimization Model-Part: I (Optimization of Pressure and Temperature). Int. J. Green Energy. 10:231–256. doi:10.1080/15435075.2011.653846.
- Urban Waste Water Treatment Directive (UWWTD) (91/271/EEC), amended by Directive 98/15/EC.
- Wang, Y., and L. Yan. 2009. CFD based combustion model for sewage sludge gasification in a fluidised bed. Front. Chem. Eng. China. 3:138–145. doi:10.1007/s11705-009-0050-7.
- Warnecke, R. 2000. Gasification of biomass: Comparison of fixed bed and fluidized bed gasifier. Biomass Bioenerg 18:489–497. doi:10.1016/S0961-9534(00)00009-X.
- Wenger, A., B. Farouk, and K. Wittle. 1996. Modeling of thermal treatment of hazardous solid wastes in a DC arc melter. J. Air Waste Manag. Assoc. 46:1162–1170. doi:10.1080/10473289.1996.10467551.
- Xiao, G., M. J. Ni, Y. Chi, B. S. Jin, R. Xiao, and Y. J. Huang. 2009. Gasification characteristics of MSW and an ANN prediction model. Waste Manag 29:240–244. doi:10.1016/j.wasman.2008.02.022.
- Zheng, H., N. Kaliyan, and R. V. Morey. 2013. Aspen Plus simulation of biomass integrated gasification combined cycle systems at corn ethanol plants. Biomass Bioenerg 56:197–210. doi:10.1016/j.biombioe.2013.04.032.